GB/T33898-2017
膜生物反应器通用技术规范
Generaltechnicalspecificationformembranebioreactor
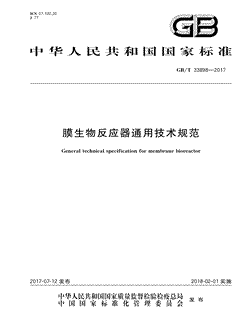
- 中国标准分类号(CCS)J77
- 国际标准分类号(ICS)07.100.20
- 实施日期2018-02-01
- 文件格式PDF
- 文本页数18页
- 文件大小1.47M
以图片形式预览膜生物反应器通用技术规范
膜生物反应器通用技术规范
国家标准 GB/T33898一2017 膜生物反应器通用技术规范 Generalteehniealspeeiieationfor membranebioreact0r 2017-07-12发布 2018-02-01实施 国家质量监督检验检疫总局 发布 国家标准化管理委员会国家标准
GB/33898一2017 前 言 本标准按照GB/T1.1一2009给出的规则起草
本标准由全国分离膜标准化技术委员会(SAC/TC382)提出并归口 本标准起草单位:天津膜天膜科技股份有限公司、天津市兴源环境技术工程有限公司、北京碧水源 膜科技有限公司,山东招金膜天股份有限公司、南京九思高科技有限公司、杭州求是膜技术有限公司、 三达膜科技(厦门)有限公司、天津森诺过滤技术有限公司、杭州天创环境科技股份有限公司、南京大学 宜兴环保研究院、苏州立升净水科技有限公司、国家海洋局天津海水淡化与综合利用研究所浙江津膜 环境科技有限公司、省部共建分离膜与膜过程国家重点实验室(天津工业大学,深圳市澳洁源环保科技 有限公司、天津膜天膜工程技术有限公司
本标准主要起草人;戴海平、刘明轩,朱高雄,刘彬、王乐译,邢卫红、张星星、方富林、,张磊,谢柏明 任洪强、陈清、潘献辉、唐小珊、许以农、何本桥、赵莹、范云双、李天玉、赵岳轩、范益群洪海云、杨山港、 邱晖、徐娅、王旭亮、全新路、丁晓斌、杨依柠、杨燕
GB/33898一2017 膜生物反应器通用技术规范 范围 本标准规定了膜生物反应器的总则、膜生物反应系统设计、安装、调试与检验,运行、清洗与维护等 技术要求
本标准适用于中空纤维膜生物反应器
规范性引用文件 下列文件对于本文件的应用是必不可少的
凡是注日期的引用文件,仅注日期的版本适用于本文 件
凡是不注日期的引用文件,其最新版本(包括所有的修改单)适用于本文件
GB/T700碳素结构钢 GB/T709热轧钢板和钢带的尺寸、外形,重量及允许偏差 GB/T1220不锈钢棒 GB/T3280不锈钢冷轧钢板和钢带 GB 3797 电气控制设备 GB 4237 不锈钢热轧钢板和钢带 GB 5836.1建筑排水用硬聚氯乙烯(PVC-U)管材 GB 5836.2建筑排水用硬聚氯乙烯(PVC-U)管件 GB 9866焊接工艺规程及评定的一般原则 20207.1丙烯脖-丁二烯-苯乙烯(ABS)压力管道系统第1部分;管材 GB/T20207.2丙烯睛-丁二烯-苯乙烯(ABS)压力管道系统第2部分:管件 GB50014室外排水设计规范 GB50141给水排水构筑物工程施工及验收规范 GB50231机械设备安装工程施工及验收通用规范 GB50235工业金属管道工程施工规范 GB50268给水排水管道工程施工及验收规范 GB50275风机、压缩机、泵安装工程施工及验收规范 GB50334城市污水处理厂工程质量验收规范 CJ60城镇污水处理厂运行,维护及安全技术规程 HU/T353水污染源在线监测系统安装技术规范(试行 HUJ/T354水污染源在线监测系统验收技术规范(试行 HU2010膜生物法污水处理工程技术规范 HU2527环境保护产品技术要求膜生物反应器 JB/T2932水处理设备技术条件 术语和定义 下列术语和定义适用于本文件
GB/T33898一2017 3.1 膜生物反应器mebranebioreactor;MBR 以膜为载体,把生物反应(作用)和分离相结合,能改变反应进程和提高反应效率的设备或系统
[GB/T20103一2006,定义6.3.3] 3.2 生物反应池biologicalproesstank 污水处理工程中承载具有生化功能的构筑物
3.3 膜池membranetank 放置膜组器及固定装置的构筑物
3.4 混合液回流比relxratioofmixture 膜池中混合液回流到生物反应池的流量与进人生物反应池的原污水流量的比值
3.5 膜分离系统 spuration membrane 1system 由膜组器、膜池,进水单元、产水单元、曝气单元、反冲洗单元、混合液回流单元、剩余污泥排放单元、 清洗单元、起吊装置和自控与检测装置等组成的,用于固液分离的系统
3.6 膜组器 membraneunit 由若干膜组件、曝气装置、集水管路、框架等组装成的,利用膜进行固液分离的水处理单元
3.7 膜污染membranefouling 料液中的某些组分在膜表面或膜孔中沉积导致膜性能下降的过程
[GB/T201032006,定义7.2.21 3.8 化学清洗chemiealcleaming 利用化学药剂去除膜的污染物的过程
[GB/T20103一2006,定义7.2.8] 3.9 跨膜压差 trans-membranepreSSure 膜进水侧与产水侧之间的压力差值,单位为MPa
[H2527一2012,定义3.3 3.10 维护性清洗 nmaintenancecleaning 为诚缓膜污染,使用低浓度化学药剂进行膜组件清洗的过程
3.11 恢复性清洗restoratiecleaning 为恢复膜性能,使用较高浓度化学药剂进行膜组件清洗的过程
3.12 完整性检测integritytest 用于判断膜组器、膜分离系统有无渗漏的检测过程
GB/33898一2017 3.13 反冲洗baekwashing 用流体对过滤介质或膜进行反向冲洗的过程
[GB/T20103一2006,定义7.2.10 3.14 物理清洗physicalcleaning 利用机械方法来清除膜表面污染物的过程
3.15 在线清洗o-linecleaning 在膜池内利用清洗装置,采用一定配比的化学药剂对膜组件进行清洗的过程 3.16 离线清洗or-line.ceaming 从膜池内取出膜组器,在独立的化学清洗池中对膜组件进行清洗的过程 [GB/T201032006,定义7.2.7] 总则 4.1膜生物反应器的总体布置应根据厂址地形、气象,地质条件,运行和环境安全等因素,统一考虑整 体布局,便于施工、维护和管理,并符合GB50014的有关规定 4.2膜生物反应器的工艺选择应满足设计进水与产水水质的要求
4.3在水质和(或)水量变化较大的污水处理系统中,应根据水质和(或)水量的变化设置自动调节系 统,保证运行的安全性
4.4当膜生物反应器用于寒冷地区时,应符合以下规定 处理工艺流程的选择应通过技术经济比较确定,并充分考虑温度的影响; a 易出现冰冻的设备,如室外污水管道、污泥管道、空气管道、闸门、计量堰等,设计中应考虑防寒 b 保温等需要; 沉砂池、沉淀池、曝气池等构筑物位于永冻地区时,应根据实际情况确定是否加盖; c 供氧宜采用鼓风曝气形式,不宜选用散热量大的表面曝气器
d 膜生物反应系统设计 5 5.1膜生物反应系统工艺流程示意图 膜生物反应系统基本工艺流程示意如图1所示
混合液回流 出水 污水 预处理 生化处理 膜分离 回用/排放 后处理 污泥处理 膜生物反应系统基本工艺流程示意图
GB/T33898一2017 5.2预处理 5.2.1 一般规定 污水在进人膜生物反应器之前应进行预处理,预处理设施包括格栅、沉砂池以及初沉池等
5.2.2格栅 格栅的选择与进水水质、生化处理工艺、膜分离技术要求有关,其设计应符合以下要求 粗格栅和细格栅的设计和选择应符合GB.50014的有关规定 a b mm1.5mm
超细格栅与膜分离技术要求密切相关,通常设置在沉砂池后,棚距为0.5n 5.2.3沉砂池 沉砂池设计和选择应符合GB50014的有关规定
5.2.4初沉池 初沉池设计应符合以下要求 初沉池设计和选择应符合GB50014的有关规定; a b 要求节省碳源且有较高的脱氮除磷效果的设计,可以设置为短时初沉池或不设初沉池
5.2.5除油装置 污水含油较高时(如动植物油30mg/L或矿物油>3mg/L),应设置除油装置,如隔油池或气浮 池等
5.2.6其他装置 当常规预处理不能满足膜分离水质要求时应增加特别处理设施,例如污水硬度及难溶盐较高时,应 采取除硬软化及阻垢措施,避免膜结垢
5.3生化处理 5.3.1一般规定 根据要求,生化处理通常选择厌氧,缺氧、好氧等工艺组合
5.3.2生物反应 生物反应池的设计应符合GB50014的有关规定 5.3.2.1 5.3.2.2根据处理目标的不同,生物反应池可采用不同的工艺配置: a 去除有机物为主要目标时,可采用单一的好氧工艺; b 去除有机物和生物脱氮为主要目标时,可采用缺氧/好氧组合工艺 去除有机物的同时还要脱氮除磷,应采用厌氧/缺氧/好氧组合工艺或各种厌氧/缺氧/好氧改 进工艺,并增加对厌氧区(池)容积以及相应混合液回流比的设计; 当污水中的BOD/cOD小于0.3时,应采用相关措施提高污水的可生化性
d 5.3.3混合液回流 混合液回流路线及回流比的设置,应综合考虑其对污染物降解、溶解氧水平与污泥浓度的影响
GB/33898一2017 5.3.4好氧曝气 好氧区(池)的供氧,应满足污水需氧量、混合以及处理效率要求
5.4膜分离系统 5.4.1 -般规定 5.4.1.1膜分离系统运行方式宜采用恒通量和周期性间歇运行模式
min3min
5.4.1.2膜分离系统过滤一个运行周期宜为7" min~9min;间歇期宜为1 5.4.2膜组器 5.4.2.1 -般规定 膜组器的整体设计应符合以下要求: 膜组器的吊架应安全可靠,便于安装和检修 a 膜组器的曝气装置、集水管路,框架和吊架等部件应布局合理,便于安装和检修,并满足工艺和 b 安全要求; 膜组器设计与选型应充分考虑集水均匀,结构紧凑,能耗低,其设计应符合H2527的有关规 定,管道和阀门等组件均应符合相应的标准和规范要求 膜组器与管路之间应由连接可靠、密封性好、耐负压、安装拆卸方便的连接件固定,通常采用不 锈钢快速接头或管道连接器固定 5.4.2.2膜组件 膜组件设计应符合以下要求 中空纤维膜组件宜采用超滤或微滤膜组件; a b 膜的平均产水通量宜在12L/(m'h)一25L/mh) 膜组件的保存、使用、安装与拆卸应根据膜组件制造商的要求进行 c d)膜组件应采用耐污染、,耐腐蚀性材料
5.4.2.3曝气装置" 曝气装置主要由进气管路和曝气部件组成,其设计应符合以下要求 进气管路应确保密封无泄漏,各通道应连接可靠 a b 曝气部件宜布置在膜组器下方,保证出气均匀并能有效减缓膜污染 曝气方式通常采用穿孔式
c 5.4.2.4集水管路 集水管路主要由连接各个膜组件产水的集水支管和总管等组成
5.4.2.5框架及附属部件 框架是将膜组件、曝气装置,集水管路连接在一起的支撑体,其设计应符合以下要求: 框架通常应使用不锈钢、带有防腐层的碳钢等金属型材或使用有足够刚度及强度的非金属材 a 料,能满足框架整体强度和刚度要求及耐腐蚀性等性能要求 b 框架主体和其附属部件使用的钢材应符合GB/T700,GB/T709,GB/T1220,GB/T3280、 GB/T4237的有关规定,使用的硬聚氧乙烯应符合GB/T5836.1,GB/T5836.2的有关规定,使用
GB/T33898一2017 的AEBS应符合GB/T20207.1,GB/T20207.2的有关规定,使用的其他材料应符合JB/T2932的 有关规定; 框架主体和其附属部件使用的焊接材料以及粘接材料应符合现行国标所规定的技术要求,焊 接质量应符合G;B/T19866的有关规定; d 金属管道焊接与安装应符合GB50235的要求
5.4.3膜池 5.4.3.1 -般规定 膜池整体设计应符合以下要求: 膜池应设置有进水口、回流口以及排泥管,每个膜池应能单独隔离、放空和检修 a b 膜池上部宜设置能覆盖膜池、化学清洗池,走道和检修平台的起吊设备; 膜池均应满足在线化学清洗的要求
进行恢复性清洗的膜池、离线清洗池应做防腐处理 d 应根据膜组器的数量设计膜池数量,膜池数量宜采用偶数 膜池内的膜组器平面布局应合理,平均分布,间距相等; 每个膜池应能独立运行且宜设置独立的进水系统、产水系统和回流系统 膜池形状宜为矩形,池深应与膜组器尺寸匹配并留有富余空间 8 膜池底部应留有排水通畅的空间和便于底部排泥的设施; h 膜池宜有膜组器的定位设置,并保证膜组器的安装水平精度在士10mm以内 在寒冷地区,宜将膜池设置于室内,室内宜考虑设置供暖,通风、除雾措施; k 膜池宜留有10%~20%备用膜组器空位
5.4.3.2 膜池深度 膜池深度的设计可参考以下因素: 膜组器高度; aa b) 膜组器底部排水排泥区高度,不宜小于200n mm; c 膜组器顶部浸没水深和膜池水位调节范围,不宜小于500 mm d 膜池水面距池壁顶部高度,不宜小于500" mm
5.4.4膜进水单元 5.4.4.1 膜池进水水质宜达到表1的要求
表1进水水质表 水温 动植物油 矿物油 指标 pH mg/L mg/1 要求 1040 30 5.4.4.2膜分离系统进水可采用重力自流进水,也可采用压力提升进水,进水宜均匀分配至各个膜池, 进水宜采用自动闸门或自动阀门调节水量
5.4.5膜产水单元 5.4.5.1膜池产水水质应符合以下要求 产水浊度小于1NTU; a
GB/33898一2017 D)产水固体悬浮物(SS)浓度小于2mg/L 5.4.5.2膜产水单元设计应符合以下要求 膜产水单元设施包括膜产水泵、各集水管路设施、辅助及监控设施 a b 膜产水单元可采用负压抽吸,也可采用静压重力自流 c 膜产水单元通量与混合液污泥浓度、温度等性能相关,宜通过实验确定; d 跨膜压差不宜大于0.05MPa; 产水泵宜采用变频控制,流量可根据对应的膜组器数量、膜设计通量和膜有效工作时间确定 产水泵应考虑备用; f 小型膜生物反应器工程中,产水泵可采用自吸泵;大中型工程中,产水泵宜采用离心泵,配合真 空泵系统使用; 集水总管应采用可调节的控制阀门,真空节点应设在各组集水总管最高点处 g h)集水管路应保证连接的密封可靠性,应满足使用时的压力和耐化学清洗剂的腐蚀等要求
5.4.6膜曝气单元 膜曝气单元由膜组器曝气设备、鼓风机、空气管路及附件等组成
管路包括供气总管和每个膜 5.4.6.1 池设置的独立的供气管,供气管连接应方便,.可靠 膜曝气单元设计应符合以下要求 5.4.6.2 膜曝气量应根据膜组器性能设计确定,同时满足生物处理需氧量和膜丝抖动需气量的要求,不 a 应造成浪费及膜损坏; 平均曝气强度应按膜池内膜面积计算,通常为0.1m'/m'h)~0.5m'/(m'); b 膜曝气单元可采用连续曝气、交替曝气、脉冲曝气等方式 c 曝气管应均匀布气; d 鼓风机可采用罗茨风机或离心风机(空气悬浮风机、磁悬浮风机等),曝气设备应考虑备用 e 应设置膜吹扫风量,风压,风机运行状态等监控系统,保障膜吹扫系统与膜产水系统的联动控 f 制,防止出现膜吹扫系统故障或风量过低的情况
5.4.7膜反冲洗单元 膜反冲洗单元设计应符合以下要求 膜反冲洗水应采用膜产水或优于膜产水水质的水源 a b)膜反冲洗频率应根据进水水质、膜设计通量等因素确定,宜通过实验确定,也可参照膜供应商 提供的类似工程参数; 膜反冲洗流量应根据膜组器的性能、产水量和产水方式综合确定,通常可按产水流量的0.5倍 1.5倍设计
5.4.8混合液回流单元 混合液回流单元设计应符合以下要求 膜池内的混合液污泥浓度宜为6g/L12g/L; aa b 混合液污泥回流比应根据膜池混合液污泥浓度、工艺脱氮除磷要求确定,通常为进水流量的 00%一400%; 混合液污泥回流泵宜采用离心泵、混流泵、潜水系或螺旋泵等; c d 回流系泵数量不应少于2台,并设有备用 混合液回流泵宜有调节流量的措施,通常设备采用变频控制 e 膜池混合液应部分回流至前面的生化反应池、部分作为剩余污泥定期排放
GB/T33898一2017 5.4.9剩余污泥排放单元 剩余污泥排放单元设计应符合以下要求 a)膜池内的污泥泥龄通常取20d30d b)膜池内的剩余污泥的排放量可按照污泥泥龄计算,也可参照H2010的有关规定执行
5.4.10清洗单元 5.4.10.1 -般规定 清洗单元由清洗泵、加药罐、管路及附件等组成
5.4.10.2维护性清洗 维护性清洗设计应符合以下要求 应定期对膜组器进行维护性清洗,通过化学药剂的杀菌、溶解、调节pH等作用,减缓膜表面的 a 生物污染和化学污染,维持膜通量 b)药液浓度由实验确定,也可参照膜供应商提供的相关资料确定
常采用的化学药剂有次氯酸 钠溶液、柠檬酸溶液等
5.4.10.3恢复性清洗 恢复性清洗设计应符合以下要求 应定期对膜元件进行充分的恢复性清洗,清除中空纤维内外表面的生物污染和化学污染物,恢 a 复膜通量; b 常采用的化学药剂有次氯酸钠溶液、氢氧化钠溶液、柠檬酸溶液等
药液浓度由实验确定,也 可参照膜供应商提供的相关资料确定; 恢复性清洗采用在线清洗或离线清洗
小型膜生物反应器工程,宜采用离线清洗;大中型工 程,宜采用在线清洗
5.4.11起吊装置 膜池顶部应设起吊装置,便于膜组器的安装与维护
5.4.12自动控制与检测 5.4.12.1膜分离系统应设置完整的自动化控制与检测系统,设置应稳定可靠,便于调整,其设计符合 GB/T3797的有关规定
5.4.12.2每个膜池的进水系统宜设置独立的液位在线监测仪表,产水系统宜设置独立的流量、跨膜压 差以及完整性检测的在线检测仪表,膜曝气单元宜设置独立的流量和压力的在线监测仪表
5.4.12.3自动控制系统宜采用可编程控制器和上位机或触摸屏进行控制,并可根据工艺要求实现设定 和调整,满足膜分离工艺参数调整的要求
5.4.12.4自动控制系统应设有可供操作人员手动操作的人机界面以及远程就地系统
5.4.12.5自动控制系统应设有报警装置
5.4.12.6自动控制系统宜设有报表系统,根据现场需求产生年、月、日报表
5.4.12.7自动控制系统中的在线检测仪表应按相应规范要求定期进行检测,对仪表进行校正
5.4.12.8自动控制系统应设有不间断电源
5.4.12.9自动控制系统应遵循“集中管理,分散控制”的原则,宜根据工程的重要等级设置系统冗余
GB/33898一2017 5.5后处理 5.5.1当对产水的除臭和脱色有严格要求时,可增加活性炭吸附或化学氧化处理设施
5.5.2 当对产水卫生安全有严格要求时,可增加消毒设施
消毒的具体方式、程度与设备配置应根据 要求的膜出水性质、排放标准或再生水要求确定
5.5.3消毒设施的设计及安全措施,应符合GB50014的有关规定
5.6剩余污泥处理 5.6.1膜生物反应系统的剩余污泥主要由膜池排出
5.6.2剩余污泥处理与处置方法应符合GB50014的有关规定 安装、调试与检验 6.1安装前准备 6.1.1膜组件或膜组器安装前,应确保预处理,生化处理、膜分离系统、后处理、剩余污泥处理的土建工 程按GB50141的有关规定检验合格,并将其内的残留杂物清洗干净,膜池按规定进行渗水试验
对已 安装好的管路按GB50268的有关规定进行检验,检验合格后将管路清洗干净,与膜组器或膜组件相连 的端口密封
6.1.2采用独立气洗系统的膜池,应在膜组件或膜组器安装前进行布气均匀性试验,试验合格后进行 膜组件安装
6.1.3 膜组件应存放在环境温度5c一40c之间的仓库内,避免冰冻、阳光直射和风吹
存放期间不 应弯曲、褶皱、重物覆盖,且不应与经、酚、酮和酸等有机溶剂接触
6.1.4安装前,所有材料、设备、零件和专用工具应准备齐全
6.2安装 6.2.1机电设备的施工与安装应符合GB50231和GB/T3797的有关规定,在线监测仪器设备的安装 应符合HJ/T353的有关规定
6.2.2系和风机的安装应符合GB50275的有关规定
6.2.3膜组件或膜组器应按顺序逐个安装,与管道连接牢固且密封良好
6.2.4膜组器管道安装完成后进行安装检验,合格后装膜组件
6.2.5向膜池注人洁净的水,保证膜组件放人后完全浸人水中
6.2.6装膜过程中不应出现膜丝皱折,受拉、挤压,碰撞和破损现象
6.2.7单架膜组件装完后通常放到充满水的清洗池中进行气检,检查修复漏点
气检合格后再放人膜 池,连接好管路
6.2.8安装完成后,应将安装过程中落人膜池内或粘附在膜组件上的杂物清理干净
6.3调试 6.3.1生化系统应满足膜分离系统的调试要求
6.3.2膜分离系统的调试应预先编制调试大纲
6.3.3通水调试前首先对水泵、风机等需要加油的设备进行注油
对泵、风机、自动阀门进行手动确 认,确认无误后进行程控确认,对仪表进行通电检查并完成自控系统的参数设置
确认无误后进行所有 机电设备的空载单机调试
6.3.4对系统管路、阀门,池体等各个环节进行清理检查,确认无污堵和损伤膜丝的残留物,并对出水
GB/T33898一2017 管及反冲洗水池进行消毒
6.3.5通水调试启动前应按A.1的有关规定进行膜分离系统完整性检测
6.3.6当发现膜组件有破损时,应按A.1.2的有关规定进行膜组件完整性检测,按A.2的有关规定对膜 组件进行修补
检测合格后应采用气洗方式对膜丝表面进行清洗,清洗干净后通水调试
6.3.7通水调试应从单个膜组器或膜池扩大至整个膜分离系统,控制方式应从手动控制逐步过渡到自 动控制;调试内容应包括过滤和清洗;调试过程的产水宜循环使用,不应进人水厂清水池
6.3.8通水调试应先进行初始调试,初始调试的产水量宜为设计产水量的1/3
待产水水质达到要求 后,可逐渐加大产水量至设计产水量,并维持该水量连续调试运行不少于72h
6.3.9化学清洗单元调试可采用达标后的膜产水模拟进行
6.3.10所有调试过程均应有记录
如果产水浊度不合格,应停机后按A.1.2的步骤执行,重新进行膜 组件完整性检测 6.4检验 6.4.1 膜系统工程质量的检验按GB50334的有关规定执行;机电设备的检验应符合GB50231和 GB/T3797的有关规定,泵和风机的检验应符合GB50275的有关规定,在线监测的检验应符合HU/T354 的有关规定
凡有自动控制装置的,应设有手动控制装置,各报警装置齐全,运行灵敏、准确,检验应符 合GB/T3797的有关规定
6.4.2检验时应检查下列项目 供水管网水压达到设定值时,系统的可靠性; a 水泵机组运行状况和扬程、流量等参数; b 管道、管件、设备的材质与设计要求的一致性; 水池的材质与设施; 供水设备的排水、,通风、保温等环境状况; 防回流污染设施的安全性; 供水设备的减振措施及环境噪声的控制; g 设备接地、防雷等保护功能; h 电源的可靠性 设备控制与数据传输的功能; kk 设备显示仪表的准确度; 消毒设备的安全运行
6.4.3膜分离系统运行检验应在相应设计产水量下连续稳定运行72h
6.4.4膜分离系统的产水量检验应达到设计产水量,产水水质检验应符合5.4.5.1的要求
6.4.5环境保护检验参考《建设项目竣工环境保护验收管理办法》的有关规定进行
6.4.6所有检验过程应作质量检验记录,检验合格后应将有关设计,施工及检验的文件立卷归档
运行、清洗与维护 7.1 -般规定 运用膜生物反应器技术进行污水处理时,其运行、维护及其安全应符合CI60的有关规定 7.1.1 7.1.2膜分离系统的操作和管理人员应进行岗前培训,熟悉膜生物反应器技术处理工艺,设施,设备的 运行要求与技术指标 7.13应建立岗位责任,操作规程,巡检、安全生产,设备维护等运行管理制度
10
GB/33898一2017 7.2运行 7.2.1膜分离系统启动前,应确认阀门、管路及设备等处于正常状态
膜分离系统启动时,应逐渐加大 供(产)水负荷
7.2.2关闭膜分离系统时,宜逐渐减小供(产)水负荷直至泵完全停止和阀门完全关闭
7.2.3膜分离系统运行过程应对水质和运行状态进行监测,按需调整系统运行参数和维护计划
7.2.4运行过程中主要监测项目如下 进水温度、压力 a b 膜池污泥浓度、污泥沉降比、膜曝气量、混合液回流比、pH值、溶解氧 产水流量、悬浮物、浊度,以及其他必要的水质分析,如化学需氧量、五日生化需氧量、氨氮含 量、总氮含量总磷含量 反冲洗水量、反冲洗时间 d 膜曝气量和鼓风机压力; e 化学清洗的周期、药量、浓度、温度和历时
f 7.3膜清洗 7.3.1物理清洗 7.3.1.1物理清洗通常是在系统运行状态下按预先设定的程序自动进行
物理请洗包括停歇睡气.水 反冲洗和冲洗三种清洗方式,应视不同污染情况而定
人工强制清洗时,依次逐个膜组器进行,并按规 定的步骤操作
7.3.1.2停歇曝气:膜分离系统产水一段时间后进行停歇曝气,此时系统先停止产水,保持鼓风机开启
让膜分离系统持续曝气
7.3.1.3水反冲洗;用膜产水或更优质的水对膜丝进行反向(即与过滤过程相反)冲洗,用反向透过膜丝 的水来冲洗膜丝表面的污染物
水反冲洗时反冲洗压力不应过高,反冲洗压力过高或者操作不当会造 成膜组件损坏
7.3.1.4冲洗:将膜组件吊出膜池或将膜池内的水排干净,用洁净的水冲刷膜组件表面附着污泥的方式 清洗膜组件
冲洗膜组件时避免冲洗水压力过高对膜组件造成损伤
7.3.2化学清洗 7.3.2.1维护性清洗具体操作时应符合以下要求 化学清洗前应制定清洗方案,配制清洗剂时,应对所接触设备、化学试剂认真检查并做好各项 a 安全防护工作; 维护性清洗药剂根据现场情况而定,通常为次叙酸钠、柠檬酸或二者交替使用,清洗药液的药 b 量根据清洗罐容积的大小和污染程度实验确定
7.3.2.2在线化学清洗指膜组件不离开膜池在膜组器原位进行清洗,清洗药剂宜为次氯酸钠、盐酸、柠 檬酸、草酸和氢氧化钠等,清洗药剂的选择可通过实验确定
7.3.2.3离线化学清洗指取出膜组器,在独立的化学清洗池中对膜组件进行清洗的过程
具体操作时 应符合以下要求: 将膜组器放在清洗平台上,先用洁净的水将膜组器上附着的污泥冲洗干净,后将冲洗干净的膜 组器吊人已配制清洗液的清洗池中进行化学清洗; b 离线清洗药剂的用量根据清洗池的容积和膜组件的污染程度通过实验确定,清洗过程中,应定 期监测药剂浓度是否满足要求,不满足时及时增加药量
1
GB/T33898一2017 7.3.2.4清洗周期根据水质和系统运行状态确定,维护性清洗周期一般为7d~15d,恢复性清洗周期 -般不小于3个月
7.3.2.5清洗温度应在膜组件生产商规定的最高温度控制范围内化学清洗温度宜控制在20C- 35C
7.3.2.6化学药剂的储存量应大于1次化学清洗所需的用药量,其中次氯酸钠的储存天数不宜大于 周到10天
与药剂直接接触的管路,应满足防化学腐蚀要求
7.3.2.7化学清洗完成后,应对被清洗部件进行彻底的物理清洗,避免系统重启后残留的清洗剂对产水 造成污染,所有清洗废液应先排人化学清洗池,处理达标后排放
7.4维护 7.4.1运用膜生物反应器技术进行污水处理时,其维护应包括膜分离系统完整性检测、膜组件破损的 封堵修复、膜组件更换、管道及其他配套机电设备与土建构筑物的维护与保养 7.4.2膜分离系统完整性主要维护项目如下 运行过程中,当产水水质不能满足5.4.5.1的要求时,应进行完整性维护 a b 完整性维护采用检漏的方法进行排查,逐个膜组器依次进行
待排查的膜组器应先停止运行, 该膜池内水位浸没膜组器顶部10cm,每个膜组件应充分浸润
每个膜架上除气检阀处于开 启状态外,其他阀门均处于关闭状态,由产水管通人检测气体,观察如有气泡出现,可判断该部 位膜组件或连接处有渗漏,将确定的破损膜组件或框架拆除并移出膜池,按附录A的方法对 膜破损部位或框架进行检测和修补,渗漏部位的拆卸应在膜组器停止运行和膜池中的水排放 干净后进行,并采用专用工具拆卸; 修复后膜组件的重新安装应符合6.2的有关规定
c 7.4.3当满足下列条件之一时,应进行膜组件更换 经恢复性清洗后膜组件通量仍不能达到要求时; a b 经检测膜组件膜老化而严重影响产水水质时
7.4.4更换组件应在所属膜组器停止运行和膜池中水排放干净后进行,并采用专用工具和材料,新组 件的安装应符合6.2的有关规定
7.4.5膜分离系统的管道,其他配套机电设备与土建构筑物的维护与保养应按CJ60的有关规定 执行
7.5停运保护 7.5.1膜分离系统停运时应对膜组件进行停运保护
7.5.2膜分离系统的停运保护应按停运时间分为短期停运和长期停运,短期停运的时间通常为小于 7d,长期停运的时间通常为大于或等于7dl 7.5.3短期停运保护主要项目如下 停运之前先进行物理清洗; a bh 物理清洗之后用清水将膜组件及系统管路充满水并排尽其中的气体,同时关闭相关阀门:
每天对膜池内的膜组件进行一次曝气擦洗; 膜池内投加次氯酸钠药液,浓度控制在30mg/L~100mg/L,以防止生物菌滋生污染膜组件
d 7.5.4长期停运保护主要项目如下: 首先应进行7.5.3的保护项目; a 对膜组件进行化学清洗; b 膜分离系统的膜组件应进行湿态保存; c d) 每隔5d按7.5.3中a)和b)的有关规定对膜组件及系统管路进行一次清洗、注水和排气
7.5.5膜组件进行湿态保存时应定期更换消毒液(如次氯酸钠),温度低时可延长更换周期,温度高时 应缩短更换周期
12
GB/33898一2017 录 附 A 规范性附录 完整性检测和修补 A.1膜分离系统的完整性检测 A.1.1要求 A.1.1.1膜分离系统的管道,膜框架安装完成后,应对其进行冲洗、水压和密闭性试验,具体操作和要 求可按照GB50268的有关规定执行
A.1.1.2膜分离系统的阀门、压力表等附件,应满足检定要求和相关标准
A.1.1.3检测时,将膜组件卸下,并清除覆盖在膜表面的污染物
A.1.1.4膜组件的外观可采用目视检测的方法,要求无划伤,无残缺
A.1.2膜组件完整性检测步骤 膜组件完整性检测步骤如下 a 检测前应确保检验所需的压力表、安全装置、阀门等附件配置齐全,且检验合格
压力表的准 确度等级不应小于1.5级,且在检定周期内; b 在水槽中加人清水,按图A.1的方式将膜组件连接到完整性检测装置,使膜组件完全浸没于水 槽中并低于液面20nmm; 压 说明 -压缩空气; -减压阀 进气阀 -压力表 排气阀 -膜组件; 水槽 图A.1膜组件完整性检测装置示意图 打开气源,调节减压阀至膜组件标称压力后,缓慢打开进气阀,从集水管的一侧进行充气所用 气体为压缩空气或氮气),充气压力0.02MPa~0.05MPa,同时将另外三个端口密封,保持压 13
GB/T33898一2017 力1min; d 观察集水管与浇铸槽粘接处和膜丝是否有连续气泡出现,若无气泡出现,即判定被检测膜组件 无渗漏;若有连续气泡出现,则判定被检测膜组件需要修补
测试结束后,关闭减压阀,打开排气阀排气,待压力表的压力降至0MPa时,关闭进气阀,拆卸 膜组件 fD 对测试合格的膜组件应进行保护性处理:短期存放浸泡清水中,长期存放应在清水中加人一定 比例的甘油溶液
A.2膜组件修补 A.2.1集水管与浇铸槽粘接修补,应使用膜组件生产厂家规定胶水进行修补
膜丝破损修补,应先将破损段截断,再用堵漏针将膜丝密封;如果浇铸层泄漏,则用胶修补 A.2.2 A.2.3将修补好的组件按照A.l.2的方法重新进行检测,直至完整性合格或报废
14
GB/33898一2017 参考文献 [1]GB/T20103一2006膜分离技术术语 [[2]建设项目竣工环境保护验收管理办法(国家环境保护总局令第13号