GB/T12916-2010
船用金属螺旋桨技术条件
Specificationformarinemetallicpropeller
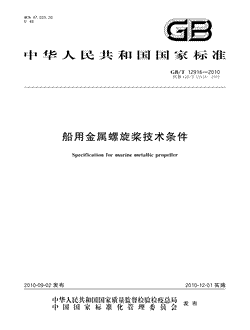
- 中国标准分类号(CCS)U48
- 国际标准分类号(ICS)47.020.20
- 实施日期2010-12-01
- 文件格式PDF
- 文本页数16页
- 文件大小540.14KB
以图片形式预览船用金属螺旋桨技术条件
船用金属螺旋桨技术条件
国家标准 GB/T12916一2010 代替GB/T12916一1991 船用金属螺旋桨技术条件 Specificationformarinemetallicpropeller 2010-09-02发布 2010-12-01实施 国家质量监督检验检疫总局 发布 国家标准化管理委员会国家标准
GB/T12916一2010 前 言 本标准代替GB/T12916一1991《船用金属螺旋桨技术条件》.
本标准与GB/T129161991相比主要变化如下 -将范围中的“技术要求,试验方法和检验规定”修改为“制造技术要求、检验方法” -将适用范围中的“整体、组装螺旋桨的制造”修改为“整体式、组装式定距螺旋桨的制造”; -将“引用标准”修改为“规范性引用文件”,修改引用标准; 重新编写了主要术语,定义,符号单位; 增加了螺旋桨按结构形式分类 调整了螺旋桨表面粗糙度、几何尺寸公差的定义和公差要求; 增加了着色探伤要求、螺旋桨清洁防护,包装和运输的要求,取消了钢字的规格; 增加立式平衡检测方法; 增加附录A,螺旋桨区域划分、缺陷检查,将正文中的表面缺陷修复内容调整到附录A 本标准的附录A为资料性附录
本标准由船舶重工集团公司提出
本标准由全国船用机械标准化技术委员会(sAc/Tc137)归口
本标准起草单位;武汉重工铸锻有限责任公司
本标准主要起草人;杜忠维、黄永强、蔡双林、黄剑平、郭雄斌,吴勇、黄丽秋
本标准所代替标准的历次版本发布情况为 -GB/T129161991
GB/I12916一2010 船用金属螺旋桨技术条件 范围 本标准规定了船用金属螺旋桨(以下简称螺旋桨)的制造技术要求、检验方法等
本标准适用于整体式、组装式定距螺旋桨的制造,可调螺距螺旋桨桨叶的制造也可参考执行
规范性引用文件 下列文件中的条款通过本标准的引用而成为本标准的条款
凡是注日期的引用文件,其随后所有 的修改单(不包括勘误的内容)或修订版均不适用于本标准,然而,鼓励根据本标准达成协议的各方研究 是否可使用这些文件的最新版本
凡是不注日期的引用文件,其最新版本适用于本标准
GB/T1176一1987铸造铜合金技术条件 GB/T7727(所有部分船舶通用术语 GJB3341一1998舰船螺旋桨用饷合金铸件规范 CB11631986钛合金螺旋桨铸件技术条件 CB3290民用船舶铜合金螺旋桨着色探伤方法及评级 术语、定义、符号、单位 GB/T7727确定的以及下列术语和定义适用于本标准
主要术语的符号和单位见表1 螺旋桨半径radiusofprpeller 螺旋桨旋转时,其叶梢轨迹圆的半径
3.2 螺旋桨截面半径radiusofbladeseetion 螺旋桨桨叶与同轴圆柱面的交切面在螺旋桨上所处的半径
3.3 螺旋桨叶截面宽度widthofbladeseetion 螺旋桨桨叶与同轴圆柱面的交切面的展开宽度
3 螺旋桨局部螺距propellerlocalpitch 螺旋桨桨叶压力面上同一半径处放射夹角为3的不同位置两点的轴向高度差
3.5 螺旋桨截面螺距ptehofbladeseeton 螺旋桨桨叶与同轴圆柱面的交切面上各局部螺距值的算术平均值
3. 6 螺旋桨叶片螺距meanpitehoflade 螺旋桨桨叶为等螺距时,为各截面螺距值的算术平均值;螺旋桨桨叶为变螺距时,一般取0.7R截 面的螺距值
3 螺旋桨总平均螺距mepiehfppeler 每片桨叶叶片螺距的算术平均值
GB/T12916一2010 3.8 螺旋桨盘面比arearatioofpropeller 螺旋桨各叶片展开面积与投影面积之比值
3.9 螺旋桨桨叶夹角angleofblades 相邻两桨叶的叶面参考线夹角
3.10 螺旋桨桨叶截面厚度thieknessofbladeseetion 螺旋桨桨叶截面上各处的厚度
3.11 stil 螺旋桨静平衡挂重addinweght ofpropellers balance 螺旋桨做静平衡时,挂在各桨叶叶梢最大厚度处使其能向下转动的挂重物最小重量 3.12 螺旋桨质量 maSS ofpropeller 螺旋桨叶片质量、桨毂质量以及圆角处填料质量之和
3.13 螺旋桨转速pedfprpetler 螺旋桨在额定功率时运转的转动速度
3.14 螺旋桨缺陷面积propellersurfaceareadiscontinuit 螺旋桨缺陷所显示区域的表面面积
3.15 螺旋桨局部螺距高差heightmarginofpropelerloealpiteh 螺旋桨相同半径上局部螺距在轴向高度上的差值 螺旋桨叶片数numberofpropellerblades 单只螺旋桨的桨叶叶片总数
3.17 nide 吸力面suction 船体前进时,螺旋桨桨叶负压吸水的一面,即为吸力面
3.18 side 压力面pressure 船体前进时,螺旋桨桨叶推水的一面,即为压力面 1g 3. V平面V-plane 垂直于螺旋桨转轴的参考平面,即为V平面
3.20 非密集缺陷non-concentrateddiscontinuity 螺旋桨表面每平方厘米内不多于4点的气孔、夹渣等缺陷,该类缺陷为非密集性缺陷
术语、符号和单位 单位 序号 符号 术语 名称 符号 螺旋桨直径 毫米 mmm R 螺旋桨半径 毫米 mmm 旋桨截面半径 R 毫米 mmm
GB/T12916一2010 表1(续 单位 序号 术语 符号 名称 符号 螺旋桨桨叶截面宽度 毫米 mm 旋桨截面距 P 毫米 mm 旋桨局部距 P 毫米 mm 螺旋桨叶片螺距 P 毫米 mm 螺旋桨总平均螺距 毫米 nmm 螺旋桨盘面比 A. /A 螺旋桨桨叶火角 度 11 螺旋桨桨叶截面厚度 毫米 mm 12 螺旋桨侧斜角 度 13 螺旋桨静平衡挂重 千克 kg 螺旋桨质量 千克 14 kg 15 螺旋桨转速 转每分钟 r/min 平方毫米 nmm 16 旋桨缺陷面积 螺旋桨局部螺距高差 毫米 1 A mm 螺旋桨叶片数 18 要求 4.1螺旋桨类型 4.1.1螺旋桨按直径可分大型螺旋桨、中型螺旋桨、小型螺旋桨3种 -大型螺旋桨;D>3500mms 中型螺旋桨;1500mm
GB/T12916一2010 理论螺距参考线 沿凡伸展的截面 图3机翼形截面局部螺距 理论螺距参考线 理论螺距参考线 沿R伸展的截面 沿R伸展的载面 图4梭形截面局部螺距 图5月牙形截面局部螺距 伸展的截而 理论螺跑参考线 螺欣浆轴线 图6截面厚度测量示意图 4.5.2螺旋桨由桨叶的0.4R开始(特殊要求螺旋桨由0.3R开始)到叶根处各截面的截面螺距P,局 部螺距P、截面宽度b和截面厚度!允许按表5规定的正负公差值加大50%
4.5.3 经设计部门或订货部门同意后,允许采用变更螺旋桨直径D的方法来补偿螺距P的超差 4.6表面缺陷 螺旋桨侧斜角区域的划分以及表面缺陷修复参见附录A
适用时,也可按各船级社规范执行
GB/T12916一2010 表5螺旋桨几何尺寸公差 序号 项目 说明 S级 1级 2级 3级 导管螺旋桨的公差在图样 士0.2% 士0.4% 半径R 士0,3% 士0.5% 中规定 截面宽度b 士1.5% 士2.0% 士3.0% 士5.0% 所列公差用直径除以桨叶 或士12 最小值 或土10mm 数(D/z)的百分数表示 或士? mmm mm 或士4mm 局部螺距P 士1.5% 士2.0% 士2.5% 士3.0% 截面螺距P 士1.0% 士1.5% 士2.0% 士2.5% 为各P值的算术平均值 叶片为等螺距时,为各P 值的算术平均值 叶片螺距P 士0.75% 士1.0% 士1.5% 士2.5% 叶片为变螺距时,可取0.7R 处P,值来衡量 士0.5% 士0.75% 士1.0% 士2% 总平均螺距" 为各桨叶尸,的算术平均值 应对0.3R.0.4R.0.6R 十4.5%或 十4.5%或 十5%或 +6%或 截面厚度! 0.8R及0.95R(或0.9R)等 0,5mm 1mm 1.5mm 2mm 以被测点的 5个截面测定,且每个截面 3.5%或 -3.5%或 4%或 -5%或 百分数计 不少于3点(特殊要求螺旋 0.5mmm 1mm 1,5mm -2mm 桨按图样要求测量 8 桨叶夹角a 0.25" 0.5” 0.5” 0.5 桨叶沿轴毂 测量各叶片中线上0.6R处 轴向位置 士0.8% 士1% 士1.5% 士2% 沿桨轴方向上离轴毂端面 以直径D计 的偏差 测量叶面中线上在0.3R和 桨叶纵斜 士(0.2%D十 士(0,5%D+ 士(0,4%D十 士(0,5%D+ 0.95R处(见图1); 10 以直径D计 两点在桨轴线上投影距离 3mm 3mm 3mm 3mm 上的偏差 相邻桨叶轴 测量各叶片中线上0.6R处 向相对位置 士0.8% 士1.0% 士1.5% 士2% 沿桨轴方向的偏差 以直径D计 检验方法 5.1测量工具精度要求 各种测量工具允许的最大误差,不应超过被测螺旋桨几何尺寸或被测量的公差的一半,或者在尺寸 测量时,大、中型螺旋桨不超过0.5mm,小型螺旋桨不超过0.25mm,两者选用大值
5.2静平衡 5.2.1螺旋桨在作静平衡之前,应先进行随遇平衡检验
当螺旋桨直径D>1500mm时,按公式(1) 计算G值作挂重试验 1 G=C× R×n 式中 -螺旋桨作静平衡时,挂在各桨叶叶梢最大厚度处使其能向下转动的挂重物最小重量,单位为
GB/T12916一2010 千克(kg); 螺旋桨叶片质量,桨毂质量以及圆角处填料质量之和,单位为千克(kg); mn R -螺旋桨旋转时,其叶梢轨迹圆的半径,单位为毫米(mm) -螺旋桨在额定功率时运转的转动速度,单位为转每分钟(r/min); 7 系数,按螺旋桨转速n及螺旋桨精度等级的系数K而定:当n>180r /min n时,C=K;当n< 180r/min时.C=K× 系数K值见表6
表6系数K值 旋桨精度等级 s级 !级 2级 3级 15 25 40 75 5.2. 当螺旋桨直径D<1500mm时,可以按公式(2)计算G值
2 G=0.025D十0.02 式中: -螺旋桨旋转时,其叶梢轨迹圆的直径,单位为毫米(mm)
5.2.3检验静平衡装置的心轴的摩擦力矩应不大于公式(3)中M值
M-是×" 3 5.2.4螺旋桨在卧式平衡仪上作静平衡检验时,将挂重分次挂于各桨叶叶梢最大厚度标记点上,然后 将挂重的桨叶叶梢最大厚度标记转到水平位置并使其静止,当去掉支承后,挂重的桨叶向下转动即为 合格
5.2.5螺旋桨在立式平衡仪上作静平衡检验时,将不大于挂重重量的挂重物挂于各桨叶叶梢最大厚度 标记点上,当去掉支承后,挂重的螺旋桨处于水平状态即为合格
5.3局部螺距 5 .3.1测量局部螺距P时,可按压力面上同一半径处放射夹角为3的O,O两点的轴向高差h来 计算(见图2) 5.3.2当机翼形截面展开后压力面为一直线,与理论螺距参考线重合时(见图3),局部螺距值P按公 式(4)计算
36o P= -×h
一h1 式中: P -螺旋桨桨叶压力面上同一半径处放射夹角为3的不同位置两点的轴向高度差,单位为毫 米(n mm; -同一半径截面压力面上不同位置两点的夹角,单位为度(") 同一半径叶片截面压力面上放射夹角为8时,起始位置处由同一基准面到理论螺距参考线 h 的轴向高度值,单位为毫米(mm); -同一半径叶片截面压力面上放射夹角为3时,终止位置处由同一基准面到理论螺距参考线 h 的轴向高度值,单位为毫米(mm 5.3.3当梭形截面展开后压力面为一曲线,位于理论螺距参考线之上时(见图4),局部螺距值P按公 式(5)计算
360 .(5 P= ×[(h
一R)一(h1一R刀 3 式中: 同一半径截面压力面上放射角为3时,起始位置处由理论螺距参考线距压力面的轴向高度 R
GB/T12916一2010 偏差值,单位为毫米(mm) R 同一半径截面压力面上放射角为3时,终止位置处由理论螺距参考线距压力面的轴向高度 偏差值,单位为毫米(mm)
5.3.4当月牙形截面展开后压力面为一曲线,位于理论螺距参考线之下时(见图5),局部螺距值P按 公式(6)计算
-3xCo十风》-十8, P 截面厚度 测量截面厚度的方法是;在压力面R,线上确定轴向各测点o[见图6a)],然后从o点所在截面的 理论螺距参考线的垂直方向上测量[见图6b)]
5.5轴孔锥度 制造厂根据锥度量规加工螺旋桨轴孔,完工后检验锥度间隙,达到制造技术要求则为合格
检测螺 旋桨轴孔加工的锥度量规的大头应刻有进线和止线,两条线的间距应不小于3mm
5.6螺旋桨压力面叶根圆角 螺旋桨压力面叶根圆角采用圆角样板做法向检查
5 边缘形状 S级、1级螺旋桨的导边及随边边缘应用样板进行检验,样板本身误差应不大于0.15mm,间隙不 大于0.75mm,长度为被检测截面宽度的10%15%,长度不超过300mm 5.8材料 5.8.1螺旋桨材料用的试样类型、检验项目等按GB/T11761987,GJB3341一1988,CB/T1163一 1986或验船部门的规定执行
5.8.2凡已合格准备出厂的螺旋桨,在材料的化学成分分析和力学性能试验的报告单上,都应有验船 部门或验船部门委托的全权代表签字认可,对于不需要经验船部门验收的螺旋桨,应由制造厂检验部门 负责人在报告单上签字认可
5.9表面着色探伤 完工后的螺旋桨应按CB3290规定的方法进行表面着色探伤检查,检查评定按各国船级社规范 执行,如无船级社规范要求的则按CB3290执行
标志,包装、贮存和运输 6.1经检验合格的螺旋桨,应在靠近桨毂小端、两叶之间的回转面上,刻印下列标志(包括商标) a)制造厂名; b 直径D; e 螺距P; d 盘面比A./A
; 旋向; 材料 D 质量; g h 炉号; 制造日期
i 叶片序号钢印打在桨毂小端的回转面上 验船部门的检验钢印应打在显眼位置
6 经检验合格的螺旋桨表面清洗干净,去除铜锈并涂刷防锈油后,用塑料布或其他包装材料将叶片
GB/T12916一2010 包装,用橡胶或其他塑性材料将叶片边缘包裹
6.5在贮存和运输过程中,作好防震、防损措施
其他 每个螺旋桨出厂时,都应附有合格证书,证书上除注明6.1的内容外,还应注明材料标准号(包括试 验项目和检验结果)及其他应说明事项
GB/T12916一2010 附 录A 资料性附录 螺旋桨区域划分及表面缺陷修复 螺旋桨侧斜角及区域划分 A.1.1螺旋桨的侧斜角由螺旋桨桨叶的侧斜角来描述
螺旋桨的最大侧斜角为;在桨叶的正投影图 上,从叶尖到桨轴中线作出与螺旋桨的桨叶截面弦长中点连线相切的直线的夹角(见图A.1)
高侧斜 螺旋桨的侧斜角大于25,低侧斜螺旋桨的侧斜角不大于25"
倒斜角 导边 随边 随边 导边 .7 0.7 0.4R 0.2h 桨叶截面 0.156 叶根 中点的连线 压力面 吸力面 图A.1侧斜角示意图 图A.2低侧斜螺旋区域划分 A.1.2为将检测要求与桨叶中的缺陷极限相联系并减少修补后疲劳裂纹的风险,将桨叶划分为A,B C三个危险区域: A区是承受最大应力的区域,因此检测要求最高
一般在该区域桨叶的厚度最大,对修补焊缝 a 的约束度最大,反过来也导致在修补焊缝内部和周围的残余应力最大
高的残余拉应力在以 后的服役中经常导致疲劳裂纹,因此在该区域的任何焊接修补必须经过消应力热处理
b B区是可能有高工作应力的区域
C区是工作应力低并且桨叶厚度相对较薄的区域
A.1.3低侧斜螺旋桨区域划分 A.1.3.1A区位于叶片的压力面,其范围为叶根至0.4R处并介于距导边0.156的界限及距随边0.2b 的界限之间的区域(见图A.2)
当桨毂半径超过0.27R时,A区为从叶根圆角至1.5倍桨毂半径之间 的区域
A区还应包括分体浇注桨毂孔处的区域(见图A.3)及可调桨桨叶的法兰及根部(如图A.4)
A.1.3.2B区为压力面叶根至0.7R范围内除A区以外的区域及吸力面叶根至0.7R的区域(见图A.2)
A.1.3.3C区为叶片两面位于0.7R以外的其他区域
整体浇铸螺旋桨桨毂的所有表面,及可调桨桨 毂除定义为A区以外的其他表面均作为c区
A.1.4高侧斜螺旋桨区域划分 A.1.4.1压力面A区的范围为叶根与随边及从导边与叶根相交处至随边0.9R处,并与0.4R弦线交 于距导边0.3M处,与0.7R弦线交于距导边0.56处的弧线所围成的区域
位于0.4R弦线以内的其余 区域也属于A区
吸力面A区的范围为沿随边,始于叶根止于0.9R,宽度为距随边0.15的区域(见 图A.5
A.1.4.2B区范围为叶片表面除A区以外的所有表面(见图A.5)
10
GB/T12916一2010 A.2缺陷检查 A.2.1无损检测 所有螺旋桨成品铸件均应在A,B,C三个区域进行表面无损检测,通常A区检测应在船检部门人 员在场下进行,对B区和C区进行检测时船检部门人员可要求在场 c区 A区 内外表面 .2x山 图A.3桨毂区域划分 A区 点 导边 时根消部 A区 一力剖面 所随边 见一h剖而> A区 包括螺栓孔 B区 B区 a一u剖面 图A.4可调桨桨叶法兰及根部区域划分 11
GB/T12916一2010 导边 导边 0.9e a.9R 0.7 S 0.7R 0.4心 压力面 吸力面 图A.5高侧斜螺旋桨区域划分 A.2.2着色渗透检测 A.2.2.1螺旋桨的表面检测通常用着色渗透检测方法进行
着色渗透检测应按船检部门认可的标准 或规则进行
着色渗透检测的显影时间应符合渗透剂生产厂的建议值或不少于10min A.2.2.2对显示进行评定时应以100cnm'大小的正方形或长方形(长边不超过250mm)作为评定区
评定区应选在显示最密集的部位
A.2.2.3渗透剂显示按图A.6划分为圆形、线形和连续形等三种
不同区域内的缺陷大小和数量应 不超过表A.1所示之值
a/心3 a/b3 0d3 圆形 线形 连续形 图A.6渗透剂显示类型 表A.1着色渗透检测判定区内显示的判定 缺陷显示的最大尺寸 区域 显示的最大数量 显示类型 每类缺陷的最大数量 圆形 线形 连续形 圆形 10 线形 14 连续形 14 圆形 20 线形 连续形 12
GB/T12916一2010 表A.1续) 缺陷显示的最大尺寸 区域 显示的最大数量 显示类型 每类缺陷的最大数量 mmm 注1,A区内小于2mm的单个圆形显示及其他区域内小于3mm的单个圆形显示可以忽略 注2:如线形或连续形显示较少或不存在,圆形显示的总数最多可达到所有显示的最大许可数量,只要保证各种 显示的数量之和不超过最大许可数量
A.2.3渗透检测 如果铸件经过修磨或焊补,修补区域应按其所处的位置和位于的区域增加渗透检测
焊缝修补过 不论其所处的位置,均应按A区域要求进行检测
A.3缺陷修复要求 A.3.1螺旋桨表面存在直径不大于1mm非密集性的气孔、渣孔等铸造缺陷时,可不作修整
A.3.2当螺旋桨的桨毂端面或内孔存在局部气孔、渣孔,对缺陷进行清洁处理,而对铸件强度无影响 时,可用合适的塑料填充这些气孔、渣孔
A.3.3发现超过表A.1验收标准的显示(如裂纹、缩孔,夹砂,夹渣、非金属夹杂,气孔以及其他可能削 弱螺旋桨安全使用的缺陷)的螺旋桨,应进行必要的修整或焊补
对于直径小于1mm的分散圆形气孔 等细小表面可以不修补
A.3.4缺陷修补一般应采用如磨、削、眈等机械方法,而不宜采用焊接的方法
若确有焊补的必要,应 事先提交详细的焊补工艺和焊补范围等资料并经验船部门同意
A.3.5不采用焊接修补的缺陷,在削钒处理后应进行打磨
并应使打磨出的凹陷轮廓尽可能光滑过 渡,以避免应力集中和减轻空泡剥蚀
A.3.6各区域可焊补的总面积和允许焊补的单个缺陷大小可参照验船部门有关标准,但应避免面积 小于5cm的焊接修补 A.3.7螺旋桨A区域的修补一般应遵循下列原则 A区一般不允许焊接修补,焊接修补只有经验船部门同意才能进行
如果同意采用焊接修补 a 则煤后应进行消应力热处理
热处理工艺应经验船部门同意
打磨后桨叶的厚度应保持图纸上批准的桨叶厚度
b 当缺陷的深度大于A.3.7b)允许修补范围时,其修补另行考虑 c A, .3.8螺旋桨B区域的修补一般应遵循下列原则 经验船部门的事先批准,B区一般允许焊接修补,但最好能够避免
每次批准均应提交缺陷 a 损坏和预期修补工艺的全部详细资料; b对深度不大于t/40 !为批准图纸上缺陷所在处的最小局部厚度)或2 的缺陷(取大 mmt mm 者)应打磨去除; 不允许用打磨去除的较深的缺陷,可用焊接方法修补
A.3.9螺旋桨C区域一般可按已认可的工艺进行焊接修补 A.3.10对每一作过修补的铸件,制造厂应保留一份记录挖修、焊补,热处理和最终检测结果的报告 该报告应经验船部门确认
A.4焊接修补 A.4.1若螺旋桨表面缺陷需要补焊时,按CB3095或各国船级社规范要求处理
A.4.2制造厂应作好缺陷及其修整的详细记录,归档备查
13
GB/T12916一2010 参考 文 献 [1]CB3095民用船舶铜合金螺旋桨补焊规则 14