GB/T37400.10-2019
重型机械通用技术条件第10部分:装配
Heavymechanicalgeneraltechnicalspecification—Part10:Assembling
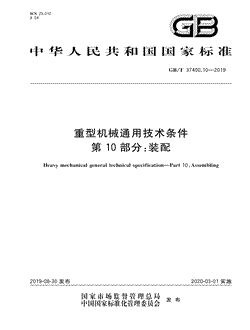
- 中国标准分类号(CCS)J04
- 国际标准分类号(ICS)25.010
- 实施日期2020-03-01
- 文件格式PDF
- 文本页数21页
- 文件大小1.78M
以图片形式预览重型机械通用技术条件第10部分:装配
重型机械通用技术条件第10部分:装配
国家标准 GB/T37400.10一2019 重型机械通用技术条件 第10部分:装配 meehamiealgeneralteehmiealspeeiffieatoa一Part10Aseming Heay 2019-08-30发布 2020-03-01实施 国家市场监督管理总局 发布 国家标准化管理委员会国家标准
GB:/T37400.10一2019 前 言 GB/T37400《重型机械通用技术条件》分为16个部分 第1部分:产品检验; 第2部分:火焰切割件 第3部分;焊接件; 第4部分:铸铁件; 第5部分:有色金属铸件 第6部分;铸钢件; 第7部分;铸钢件补焊 第8部分;锻件 第9部分;切削加工件 第10部分:装配 第11部分配管 第12部分;涂装; 第13部分;包装; 第14部分;铸钢件无损探伤 第15部分;锻钢件无损探伤; 第16部分液压系统
本部分为GB/T37400的第10部分
本部分按照GB/T1.12009给出的规则起草
本部分由全国冶金设备标准化技术委员会(sAc/Tc409)提出并归口
本部分起草单位;上海电气上重碾磨特装设备有限公司、中冶华天南京工程技术有限公司、中冶陕 压重工设备有限公司、衡阳中钢衡重设备有限公司、重型机械研究院股份公司、一重集团有限 公司、太原重工股份有限公司、二重(德阳)重型装备有限公司
本部分起草人;叶志强、沈光明姜洪涛、高梦唐保国,卫卫芦强,何家宝、王农、石雨、樊立,赵盛堪、 李勇、肖体云、苏静、韩建平、谭加、殷勇、李冬爱、王国成、许海勇、崔晓明
GB:/T37400.10一2019 重型机械通用技术条件 第10部分:装配 范围 GB/T37400的本部分规定了重型机械产品装配的一般要求,装配部件的几何公差、装配连接方 法、典型部件装配、总装、检验及试车、拆卸的通用技术要求
本部分适用于重型机械产品的装配
规范性引用文件 下列文件对于本文件的应用是必不可少的
凡是注日期的引用文件,仅注日期的版本适用于本文 件
凡是不注日期的引用文件,其最新版本(包括所有的修改单)适用于本文件
GB/T9239.1一2006机械振动恒态(刚性)转子平衡品质要求第1部分;规范与平衡允差的 检验 GB/T37400.3重型机械通用技术条件第3部分;焊接件 GB/T37400.9重型机械通用技术条件第9部分;切削加工件 GB/T37400.l1重型机械通用技术条件第1l部分;配管 JB/T6996重型机械液压系统通用技术条件 JB/T7929 齿轮传动装置清洁度 装配的一般要求 3.1进人装配的零件及部件(包括外购件、外协件),均应具有检验部门的合格证方能进行装配
3.2零件在装配前应清理和清洗干净,不得有毛刺、飞边、氧化皮、锈蚀、切屑、油污、着色剂防锈油和 灰尘等
装配前应对零,部件的主要配合尺寸,特别是过盈配合尺寸及相关精度进行复查
3.3 经钳工修整的 配合尺寸,应由检验部门复检
3.4装配过程中的机械加工工序应符合GB/T37400.9的有关规定;焊接工序应符合GB/T37400.3 的有关规定
3.5除有特殊要求外,装配前应将零件的尖角和锐边倒钝
3.6装配过程中零件不准许磕碰、划伤和锈蚀
3.7输送介质的孔要用照明法或通气法检查是否畅通
3.8装配后无法再进人的部位要先涂底漆和面漆
油漆未干的零、部件不得进行装配
3.9机座、,机身等机器的基础件,装配时应校正水平(或垂直)
其校正精度,对结构简单、精度低的机 器不低于0.1mm/m;对结构复杂、精度高的机器不低于0.05mm/m
3.10具有相对运动的零,部件上各润滑点装配后应注人适量的润滑油(或脂)
装配部件的几何公差 4.1本几何公差是指装配部件被测要素的未注几何公差,主参数L<1000 mm见表1,主参数
GB/T37400.10一2019 1 000 mm
GB:/T37400.10一2019 5.1.5双螺母紧固时,若两螺母厚度不相同时,薄螺母应置于厚螺母之内,薄螺母应按规定力矩要求拧 紧,厚螺母则应施加较大的拧紧力矩
5.1.6螺母拧紧后,螺栓、螺钉末端应露出螺母端面2个3个螺距;采用拉伸预紧方式拧紧的螺栓,螺 母拧紧后,螺栓末端应露出螺母端面的长度按照设计图样要求或不小于1个螺栓公称直径(d)
5.1.7沉头螺钉紧固后,沉头应低于表面1mm~2mm或按照设计图样要求
5.1.8严格按照图样及技术文件上规定性能等级的紧固件装配,不准许用低性能紧固件替代高性能紧 固件
5.1.9对于大直径重载预紧的螺母,在紧固时应在螺纹合部分涂防咬合剂
5.2销连接 5.2.1圆锥销装配时应与孔进行涂色检查,其接触率不应小于配合长度的60%,并分布均匀
5.2.2对定位精度要求高的销和销孔,装配前检查其接触面积,应符合图样技术文件的规定;当无规定 时,其接触率不小于总接触面积的60%
5.2.3定位销端面一般应突出零件表面
带螺尾圆锥销装人相关零件后,其大端应沉人孔内
5.2.4开口销装人相关件后,其尾部应分开,其扩角为60"90" 5.3键联接 5.3.1平键装配时,不得配制成阶梯形
平键与轴上键槽两侧面应均匀接触,其配合面不得有间隙
钩头键、楔键装配后,其接触面积应 5.3.2 不小于工作面积的70%,且不接触部分不得集中于一段
外露部分应为斜面的10%~15%
5.3.3花键装配时,同时接触的齿数不小于2/3,接触率在键齿的长度和高度方向不得低于50%
5.3.4滑动配合的平键(或花键)装配后,相配件应移动自如,不得有松紧不匀现象
5.4铆钉连接 5.4.1铆接时不得损坏被铆接零件的表面,也不得使被铆接的零件变形
5.4.2除特殊要求外,,一般铆接后不得出现松动现象,铆钉头部应与被铆零件紧密接触并应光滑圆整
5.5黏合连接 5.5.1黏结剂牌号应符合设计或工艺要求并采用在有效期限内的黏合剂
5.5.2 被黏接的零件表面应做好预处理,彻底清除油污,水膜.锈迹等杂质 5.5.3黏接时黏结剂应涂得均匀
固化的温度、压力,时间等应严格按工艺或黏结剂使用说明的规定 执行
5.5.4黏接后应清除流出的多余黏结剂
5.6过盈连接 5.6.1 压装 5.6.1.1压装时压装的方法可参考附录B选取,压人力的计算可参考附录C 5.6.1.2压装的轴或套允许有引人端,其导向锥角10"一20,导锥长度等于或小于配合长度的15%
5.6.1.3实心轴压人盲孔时允许开排气槽,槽深不大于0,5mm
5.6.1.4压人件表面除特殊要求外,压装时应涂清洁的润滑剂
5.6.1.5压装时,其受力中心线应与包容件,被包容件中心线保持同轴
GB/T37400.10一2019 5.6.1.6采用冲击压装时,应采用软金属或硬质非金属材料做防护衬垫,零件表面不应有砸痕
5.6.1.7采用压力机压装时,其压力机的压力一般为所需压人力的3倍一3.5倍
压装过程中压力变化 应平稳
5.6.2热装 5.6.2.1热装的加热方法可参考附录B选取
5.6.2.2热装零件的加热温度根据零件材质、结合直径,过盈量及热装的最小间隙等确定,确定方法参 见附录D. 5.6.2.3用油加热零件的加热温度应比所用油的闪点低20C30C
5.6.2.4热装时要求操作动作迅速准确,一次热装到位,中途不许停顿
若发生异常,不准许强迫装人 应排除故障,重新加热再进行热装
5.6.2.5热装后零件应自然冷却,不准急冷,如有必要,可以采用辅助冷却,但是要遵守厂家的材料规范 并注意最高允许的冷却温度
5.6.2.6零件热装后应紧靠轴肩或其他相关定位面,冷缩后的间隙不得大于配合长度尺寸的 0.3mm/m
5.6.3冷装 冷装时常用的冷却方法可参考附录B选取
5.6.3.1 5.6.3.2冷装时零件的冷却温度及时间的确定方法可参见附录E
5.6.3.3被冷却零件取出后应立即装人包容件
对零件表面有厚霜者,不得装配,应重新冷却
5.6.4胀套 5.6.4.1胀套与结合件的配合表面应干净无污物,无腐蚀,无损伤
装前均匀涂一层不含MoS2等舔加 剂的润滑油
5.6.4.2胀套螺栓应使用力矩扳手,并对称,交叉、逐步,均匀,逐级拧紧
5.6.4.3胀套螺栓的拧紧力矩TA值按设计图样或工艺文件规定,未规定拧紧力矩的胀套螺栓可参考 附录A并按下列步骤进行 以1/3TA值拧紧; a b) 以1/2TA值拧紧; 以TA值拧紧 c d 以TA值检查全部螺栓
6 典型部件装配 6.1滚动轴承装配 6.1.1轴承外圈与开式轴承座及轴承盖的半圆孔不准有卡住现象,装配时允许整修半圆孔,修整尺寸 不应超过表3规定值
轴承外圈与开式轴承座及轴承盖的半圆孔应接触良好,用涂色检验时,与轴承座对称于中心线 6.1.2 120?、与轴承盖在对称于中心线90`的范围内应均匀接触
在上述范围内用塞尺检查时,0.03mm的塞 尺不得插人外圈宽度的1/3
6.1.3轴承内圈端面应紧靠轴向定位面,其允许最大间隙:对圆锥滚子轴承和角接触球轴承为 0.05mm; 其他轴承为0.1 mm
GB:/T37400.10一2019 6.1.4轴承外圈装配后与定位端轴承盖端面应接触均匀
表3轴承盖(座)修整尺寸 单位为毫米 轴承外径D 图示 120 S0.10 90° >120260 s0.15 15 >260一400 s0.20 " 20 >400 <0.25 30 6.1.5采用润滑脂润滑的轴承,装配后应注人符合规定的清洁润滑脂,其注人量相当于轴承空腔容积 约50%一75%
凡稀油润滑的轴承,不准加润滑脂
6.1.6轴承热装时,其加热温度应不高于100
轴承冷装时,其冷却温度应不低于一80C 6.1.7可拆卸轴承装配时,应严格按原组装位置,不得装反或与别的轴承混装
对可调头装的轴承,装 配时应将轴承的标记端朝外
6.1.8在轴的两端装配径向间隙不可调的向心轴承,且轴向位移是以两端端盖限定时,其一端应留有 轴向间隙c(如图1)
C值的大小按式(1)计算 C=aA
L十0.15 式中: 轴向间隙,单位为毫米(m mm; -轴材料线膨胀系数,对钢:a=12×10-/C; 公t -轴最高工作温度与环境温度之差,单位为摄氏度(); -两轴承中心距,单位为毫米(mm); 0.l5 -轴热胀后剩余间隙,单位为毫米(mn m
-般情况取'=40C,故装配时只需根据L尺寸,即可按简易式(2)计算C值: C=0.0005L十0.15 图1
GB/T37400.10一2019 6.1.9单列圆锥滚子轴承,角接触球轴承,双向推力球轴承轴向游隙按表4调整
双列和四列圆锥滚 子轴承装配时应检查其轴向游隙并应符合表5和表6的要求
表4角接触球轴承、单列圆锥滚子轴承,双向推力球轴承轴向游隙 单位为毫米 角接触球轴承轴向游隙 单列圆锥滚子轴承轴向游隙 双向推力球轴承轴向游隙 轴承内径 轻系列 中及重系列 轻系列 轻宽中及中宽系列 轻系列 中及重系列 <30 0.02~0.06 0,03一0,09 0.03一0.1o 0.04~0.11 0,03~0,08 0.050.11 3050 0,03~0,09 0.04一0.10 0,040,l1 0,050,13 0.04~0.1o 0,060,12 >50~80 0.040.10 0.050.12 0.05~0.13 0.06~0.15 0.05~0.12 0.07一0.14 0.050.12 0.060.15 0.060.15 0.070.18 0.06~0.15 80一120 0.100.18 >120150 0.060.l5 0.070.18 0.070.18 0.080.20 >150~18o 0.070.18 0.08~0.20 0.09一0.2o 0.10~0.22 >180~200 0.090.20 0.100.22 0.12~0,22 0,140,24 >200~250 0.18一0.30 0.18~0.30 表5双列圆锥滚子轴承轴向游隙 单位为毫米 轴向游隙 轴向游欧 轴承内径 轴承内径 内圈比外圈温度高 内圈比外圈温度高 -般情况 -般情况 2530 2530 8o 0.100.2o 0.300.40 >225315 0.300.40 0.700.8o >80180 0.160.25 0,40~0.50 >315~580 0.400.50 0.901.00 >180~225 0.200.30 0.50~0.60o 表6四列圆锥滚子轴承的轴向游隙 单位为毫米 轴承内径 轴承内径 轴向游隙 轴向游隙 500630 >120~180 0.15~0,25 0.300.40 0.200.30 >630~800 >180315 0.350.45 315一400 0.25~0.35 800~1000 0.35一0.45 >400500 0.30~0,.40 >10001250 0,40~0.50 6.1.10滚动轴承装好后用手转动应灵活、平稳,不得有卡滞现象
6.1.11用压装法压人或压出轴承时,应用专用压具或在过盈配合环上垫以棒或套,不得通过滚动体和 保持架传递压力或打击力,也不得使用明火对轴承进行加热
6.2滑动轴承装配 6.2.1上、下轴瓦应按加工时的配对标记装配
6.2.2上、下轴瓦的接合面要紧密贴合,用0.05mm塞尺检查不得插人
6.2.3轴瓦垫片应平整无棱刺,形状应与瓦口相同,其宽度和长度比瓦口面的相应尺寸小1" mm" 2mm
2 垫片与轴颈应有1mm mm的间隙,两侧厚度应一致,其允差应小于0.2mm. 6.2.4用定位销固定轴瓦时,应在保证瓦口面和端面与相关轴承孔的开合面和端面保持平齐状态下钻
GB:/T37400.10一2019 钦,配销
销装人后不得松动,销端面应低于轴瓦内孔1 2mm. mm一 6.2.5上、下轴瓦外圆与相关轴承座孔应接触良好,在允许接触角内的接触率应符合表7要求
表7上、下轴瓦外圆与相关轴承座孔的接触要求 接触要求 项目 图示 下瓦 上瓦 稀油润滑 130°士5” 150"士5” 接触角 120°士5? 140”士5” 油脂润滑 >70% 60 a角内接触率 D <200mm时,0.05mm塞尺不准插人 瓦侧间隙/mm D>200mm时,0.10mm 塞尺不准插人 6.2.6上、下轴瓦内孔与相关轴颈接触a以外的部分均需加工出油楔(表8图示之c)
楔形从瓦口开 始由最大逐步过渡到零,楔形最大值按表8规定
表8上下轴瓦油楔尺寸 油楔最大值C 图示 稀油润滑 CC mm范围内 距瓦两端面10mm~15 C~( 油脂润滑 下瓦 中间部位C~2c 注c值为轴的最大配合间隙
6.2.7轴瓦内孔刮研后,应与相关轴颈接触良好
在接触角范围内的接触斑点按表9规定
表9上下轴瓦内孔与相关轴颈的接触要求 接触角a a角范围内接触斑点/点数/(25mm×25mm 图示 轴瓦内径/mm 轴转速/r/min <18o >360500 l80360 稀油 油脱 <300 涧滑 润滑 >300500 120”" 90”" >500~1000 >l000
GB/T37400.10一2019 6.2.8轴瓦安装在轴承体内,无论径向或轴向都不准许有位移 6.2.9整体轴套的装配可根据过盈的大小采用压装或冷装
6.2.10轴套装人相关零件后,轴套内径与轴配合应符合设计要求,必要时可以适当的修刮来保证
两 件结合面经着色研合,接触痕迹应均匀分布,其未接触部分按限定区域内不得超过表10限定的方块值 表10均匀接触限定值 单位为毫米 长度参数范围 限定方块值 长度参数范 限定方块值 25×25 >800~1600 200 80×80 >200400 40×40 >1600 100×100 >400800 60×60 注1长度参数范围系指长方形平面的长度,对于圆柱面和弧面按其展开图形的长度 注2如果结合面宽度尺寸小于或等于所选档次中限定方块值的边长时,可降到相应档次(结合面)的宽度大于 限定方块值边长的档次使用
6.2.11球面轴承的球体与球面座应均匀接触,用涂色法检查,其接触率不应小于70%
62.12合金轴承衬的刮研接触要求按6.2.7
刮削量不得大于合金轴承衬壁厚的1/30. 6.2.13合金轴承衬表面呈黄色时不准使用,在规定的接触角内不准有缝隙现象;在接触角外的缝隙面 积不得大于非接触区总面积的10%
6.3齿轮与齿轮箱装配 6.3.1装配前检查齿轮齿顶、齿端是否已修形,如未修形需进行倒棱修整
6.3.2齿轮(蜗轮)基准端面与轴肩(或定位套端面)应贴合,用0.05mm塞尺检查不得插人,并应保证 齿轮基准端面与轴线的垂直度要求 相赌合的圆杜齿轮刚,二齿宽中心平面的轴向位置偏差应符合如下规定 6.3.3 当齿宽B小于或等于10o0 a mm时,位置偏差B小于0.05B; b 当齿宽月大于100 mmm时,位置偏差B小于5mm
6.3.4齿轮蜗轮)副啮合时的齿面接触斑点不小于表11的规定
接触斑点的分布位置应趋近于齿面 中部,齿顶和齿端棱边不准许有接触
表11 齿面接触斑点 圆柱齿轮 圆锥齿轮 蜗轮 精度等级 沿齿高 沿齿长 沿齿高 沿齿长 沿齿高 沿齿长 55 80 65一85 60一8o 65 60 50 70 5575 5070 45 60 55 50 40 50 40~70 3065 30 40 45 40 25 10 30 306o 2555 20 30 30 30
GB:/T37400.10一2019 6.3.5齿轮(蜗轮)副装配后应检查齿侧间隙,并符合图样或工艺文件要求
6.3.6圆锥齿轮一般应按加工配对编号装配;若圆锥齿轮加工精度很高,可以不用配对,则在圆锥齿轮 装配时应使两齿轮分度圆锥相切,两锥顶重合
6.3.7齿轮箱与盖的结合面应接触良好
在自由状态下,箱盖与箱体的间隙不应超过表12的规定值 紧固后用0,05mm塞尺检查,局部插人不应超过结合面宽的三分之一,结合面可以涂平面密封胶 表12箱盖与箱体在自由状态下的允许间隙 单位为毫米 齿轮箱长度 1000 >l0002000 >20003000 >30004000 箱体与箱盖间隙 0.08 <0.12 s0.15 0,20 6.3.8齿轮传动装置装配后,应按设计或工艺要求进行空运转试车
应运转平稳、无异常噪音
6.3.9齿轮箱的清洁度应符合JB/T7929的规定
6.4带轮与链传动装配 6.4.1平行传动轴的带轮,两轴线平行度公差为0.15L/1000(L为两轴中心距,单位为mm),两轮的 轮宽中间平面应在同一平面上,公差为0.5mm
6.4.2主动链轮与从动链轮的齿宽中心平面应重合,其偏移量不得超过设计要求
若设计未规定,其 偏移误差不大于1.5L/1000(L为两链轮的中心距,单位为mm) 6.4.3链条与链轮啮合时,链条工作边应拉紧并应保证啮合平稳
6.4.4链条非工作边的初垂度按两链轮中心距的1%~5%调整
6.5联轴器装配 6.5.1每套联轴器在拆装过程中,应与原装配组合一致
6.5.2刚性联轴器装配时,两个半联轴器端面应紧密接触,两轴线的径向位移应小于0.03mm
6.5.3挠性、齿式、轮胎,链条联轴器装配时,其装配精度应符合表13规定
表13联轴器装配精度 两轴线的同轴度公差圆周跳动/mm 联轴器轴孔直径/mm 两轴线的角度偏差/(' <100 0.05 l00180 0.05 >180一25o 0.10 >250315 0.10 >315一450 0.15 >450~56o 0.15 0.20 >560~630 >630~710 0.25 0,20 >710~800 0,30 两个半联轴器均应做转动测量,这样可以补偿其外圆的圆度偏差
用百分表测量,两轴线间差值是表列公差之半 两轴线的角度偏差可用百分表检测,或塞尺检查联轴器两法兰间的间隙.
GB/T37400.10一2019 6.6制动器和离合器装配 6.6.1制动带与制动板铆接后应贴紧,局部间隙应符合以下要求 制动轮直径小于500mm时,局部间隙小于或等于0.31 a mm; b制动轮直径大于或等于500mm时,局部间隙小于或等于0,5 mm; 塞尺插人深度小于或等于带宽的1/3,且全长上不得多于两处
c 6.6.2制动带与制动板铆接时,铆接应牢靠,不得松动,铆钉头应埋人制动带厚度的1/3,制动带不准许 有铆裂现象
6.6.3带式制动器在自由状态时,制动带与制动轮之间的间隙为1mm一2mm
6.6.4块式制动器在自由状态时,制动块与制动轮之间的间隙为0.25nmm0.50mm
6.6.5片式摩擦离合器在自由状态时,主动盘与被动盘应彻底分离
6.6.6干式摩擦片应干燥、清洁,工作面不准许沾上油污和杂物
6.6.7离合器的摩擦片接触面积不小于总摩擦面积的75%
6.7液压缸、气缸及密封件装配 6.7.1组装前严格检查并清除零件加工时残留的锐角、毛刺和异物,保证密封件装人时不被擦伤
6.7.2装配时应十分注意密封件的工作方向,0形圈与保护挡环并用时应注意挡环的位置
6.7.3对弹性较差的密封件,应采用具有扩张或收缩功能的工装进行装配
6.7.4带双向密封圈的活塞装人盲孔油缸时,应采用引导工装,不准许用螺钉旋具等硬物硬塞
6.7.5密封件不准许强硬敲打或强行装配,以防密封件的密封性能受到破坏
6.7.6对于有填料箱的密封装置,当压装盘根时,应将填料圈的接口切成45"的坡口,相邻两圈的接口 应错开大于90"
填料压圈或压盖的压紧力应均匀分布,应无过紧使温度升高及运动阻滞或过松使泄 漏超过规定的现象
6.7.7油封装配时,油封唇部应无损伤,应在油封唇部涂抹润滑剂;油封装配方向,应使介质工作压力 把密封唇部紧压在主轴上,不得装反
6.7.8装配0形密封圈时,不得扭曲、损伤密封圈;装配V、,Y,U形密封圈时,支撑环,密封环和压环应 组装正确,且不宜压得过紧,密封圈的唇边应对着密封介质的压力方向,并注意不要损伤唇边
6.7.9液压缸、气缸装配后要进行密封及动作试验,达到如下要求: 行程符合要求; a D)运行平稳,无卡阻和爬行现象;
无外部渗漏现象,内部渗漏按图样要求
6.7.10各种密封毡圈、毡垫,皮碗等密封件装配前应浸透油;紫铜垫作退火处理
6.8管路装配 管路装配要求应符合GB/T37400.11、JB/T6996的有关规定
其他 7.1平面刮研 7.1.1平面刮研时应使用相应的精度等级的平板或平尺
推拉平板或平尺时应沿水平方向施力,不准 许在平板或平尺顶面施力
7.1.2相关两个平面需要互研时,只能在两个平面各自按平板或平尺刮研接近合格后方准互研 7.1.3被刮研表面的接触斑点不少于表14规定
10
GB/T37400.10一2019 表14刮研表面接触斑点 滑动速度 接触面积 接触面积 s0.2m >0.2m" m/s <0.5 3点数/25mm×25mm 2点数/(25mm×25mm) 4点数/(25mm×25mm) 3点数/25mmX25mm) 0.5~1.5 7.2锥面着色研合 锥轴伸与轴孔配合表面接触应均匀,着色研合检验时其接触率不低于70%
7.3平衡实验要求 7.3.1有平衡力矩要求的零、部件,装配时应按规定进行静平衡或动平衡试验
7.3.2对有静平衡试验要求而未注明具体要求时,则按GB/T9239.1一2006中Gl6级执行
7.3.3对转动零部件的不平衡质量可用下述方法进行校正: 用补焊,喷镀、黏接、铆接、螺纹连接等加配质量(配重); a b 用钻削、磨削、铁削、挫削等去除局部质量去重); 在平衡槽中改变平衡块的数量或重量
c 7.3.4用加配质量的方法校正时,应固定可靠,以防在工作过程中松动或飞出
7.3.5用去除质量的方法校正时,注意不得影响零件的刚度、强度和外观
7.3.6对组合式转动体,经总体平衡后不得再任意移动、调换零件
7.4装配标识 7.4.1机器在装配中如有不准许用户在安装时互换的零件或变更相关件的装配位置,且这些零、部件 装配后又需拆开包装的,则应打出能够容易识别原装配关系的钢印或粘贴标签
7.4.2装配中已配好的管路又需拆开包装的,在联接处应粘贴标签或牵挂钢印标牌
7.4.3同一标识组的编号应一致,同一台产品中不同标识组的编号不得重复
7.4,4标识的字迹应清晰、整齐
7.4.5标识的位置应靠近相关件联接处的非滑动面上
若是毛坯,则在磨出的平面上作标识;若在大 件上作标识,则应用红漆圈上方框
各标识处不准涂油漆或腻子,但应涂防锈油
总装、检验及试车 8 8.1产品出厂前应进行总装
对于特大型产品或成套的设备,因受制造厂条件所限而不能总装的,应 试装时应保证所有连接或配合部位均应符合设计要求 进行试装
8.2产品总装后均应按产品标准和有关技术文件的规定进行检验,并对执行过的检验作记录
检验范 围至少要满足符合图样设计的最低要求 a 检查装配件的几何公差; b 检查管路的一般公差; 检查支承面和接触面,连接点和交接点 c d 检查调整的间隙和接触面; 检查结合面的间隙(用0.05mm的塞尺); 11
GB/T37400.10一2019 检查运动和行驶路径(必要时可以使用辅助装置); f 检查缸的行程(可用适合的液压机组); 8 h)检查防锈保护和涂漆
8.3产品总装后均应按产品标准和有关技术文件的规定进行试车,试车一般要求 a 产品的运转为双向旋转的,应双向试车;运转为单向的,试车方向应与工作方向一致 b 拖动产品的试车工具的转速应符合产品工作要求,允许偏差为士10%
随机的气、液管路应按GB/T37400.11的规定进行清洗和防锈处理 d 产品试车前,随机的润滑管、液压管应先单独进行循环清洗
清洁度应符合GB/T37400.11 的相关规定; 对于特大型产品或成套的设备,因受制造厂条件限制而不能试车时,则应按有关合同或协议 执行
8.4空运转试车应符合以下规定 凡机器产品(包括成套设备中的单机),都应按相关技术文件的要求在装配后进行空运转试车 a 包精手动盘车试验 单机空运转试车,对需手动盘车设备,不少于3个全行程;对连续运转的设备,试车时间不少于 b 2h对往复运动的设备,全行程往复不少于5次 对有多种动作程序的设备,各动作要进行联动程序的连续操作或模拟操作,运转5次以上,各 c 动作应平稳、到位、无故障
8.5负荷及工艺性试车按产品标准、技术文件或合同规定进行
8.6在试车过程中轴承温度应符合图样或工艺要求,在图样及工艺未作规定时应符合表15规定 表15轴承试车时的温升要求 单位为摄氏度 项 目 最高温度 温 升 空运转试车 <35 <85 滚动轴承 负荷试车 <45 85 空运转试车 20 70 滑动轴承 负荷试车 30 <70 注1最高温度指实测最高温度 注2;运转规定时间内每相隔30min测温一次,做好记录
若30min内温度变化<0.5C,则为最终温度
8.7有压力要求的设备(如液压机),应对密封及系统进行密封耐压试验
如技术文件无明确试压要求 时,其试验压力为工作压力的100%125%
保压5minr 10min,不得渗漏
8.8产品在总装及试车过程中,应做好关键件配合尺寸,单配件尺寸及试车的各项记录并作为产品技 术档案存档
9 拆卸 9.1拆卸程度对产品设备的可运输性起到了决定作用
应注意拆卸的目的是产品设备的可运输性 g.2拆卸工作量应减少到可能的最低程度
只要发货时不会产生问题,螺栓和垫板等应尽量保留在设 备上
可更换部件(例如,管道支承部件、分体盖、分体壳等)在拆卸前做好装配标识,标识应能长久保持 并清晰可见
管路拆卸要求应符合GB/T37400.11的相关规定 9.3 12
GB:/T37400.10一2019 附 录 A 资料性附录 螺栓拧紧力矩 表A.1规定了一般连接螺栓拧紧力矩
表A.1螺栓拧紧力矩 纱规格d/mm 力学 性能 M6 M8 M10M12M14M16M18M20M24M27M30M36M42M48M56 等级 拧紧力矩TA/(N
m 3.6 17.127.2 7.4 140 9.8 41.7 81.2 206.9|281.l489.7785.711861901 22 13.122.9 55.976.9 108.8187.5277.1376.5655.910521589 547 4.6 2.6 6.8 36.4 5.6 3.3 8.5 16.528.745.6 70 96.4136.3235 347 472 822131919913192 18 61 205 73910041749280642366791 8.8 35 97 149 290 500 10.9 9.9 25,449,4 86136.8210289 409 705104214162466395759739575 12.9 11.830.459.2 103163.9252346.5490 8451249169729564742l715911477 A2一70 12.824.9 43.368,9105.8145.6205,9355 525 7131242199230084822 A280 6.6 16.9 32.9 57.31.3 140. 470 192.7272.6 694,6943,81644263839826384 螺纹规格l/mm 力学 M72×6M80×6M90×6M100×6M110×6M120×6M125×6M140×6M160×6 性能 M64 等级 拧紧力矩TA/(Nm 3.6 284l 4ll3 5703 8258 1l514 15344 20157 22480 31731 47888 4.6 3805 5508 7638 l1060 15421 20550 26996 30107 42497 64135 4769 6904 9573 13861 19327 25756 33834 37733 53263 5.6 80383 10147 14689 20368 29492 41122 54799 71988 80284 113326 171027 8.8 10.9 14307 20712 28719 41584 57982 77267 01503 113200 159790241148 12.9 17148 24824 34422 49841 69496 92610 121660135680191521289036 A270 7204 10429 14461 20939 29197 38907 51l11 57002 80461 121429 A2一80 9538 13808 19146 27722 38655 51511 67669 75467 106526 160765 注1:适用于粗牙螺栓、螺钉,不适用于细牙螺栓、螺钉膨胀螺栓以及T形螺栓和地脚螺栓
注2;拧紧力矩允许偏差为士5%
注3:所给数值为使用润滑剂的螺栓,摩擦因数为从=0.125
注4:优先选用第一系列,M14.M18,.M27.M120等第二系列尽可能不用
13
GB/T37400.10一2019 附录 B 资料性附录) 过盈连接各种装配方法的工艺特点及适用范围 过盈连接各种装配方法的工艺特点及适用范围见表B.1
表B.1过盈连接各种装配方法的工艺特点及适用范围 主要设备 装配方法 工艺特点 使用范围 和工具 适用于配合面要求较低或其长度较短、 简便,但导向性不易控制,易出 冲击压人 手锤或用重物冲击 过渡配合的连接件,如销、键、短轴等 现歪斜 多用于单件生产 适用于不宜用压力机压人的小尺寸连 螺旋式、杠杆式、 气 导向性比冲击压人好,生产率接件,如小型轮圈、轮毂齿轮、套筒,连 工具压人 F 动式压人工具 较高 杆、衬套和一般要求的滚动轴承等
多 用于小批生产 适用于中型和大型连接件,如车轮、飞 齿条式、螺旋式、杠 压力范围由10kN~1000kN 轮,齿圈,轮毂,连杆衬套,滚动轴承等 压力机压人 杆式、气动式压力机 装 配合夹具可提高导向性 易于实现压合过程自动化,成批生产中 和液压机 广泛采用 液压垫(一般用厚 用于压人行程短的大型、重型连接件, 2mm一3mm的钢 液压垫压人 压力常在10000kN以上 多用于单件或小批生产以代替大型压 板制成空心,注人压 力机 力液体) 加热温度低于350C,丙烧(或适用于局部受热和热胀尺寸要求严格 喷灯、氧乙块、丙烧其他气体燃料)
加热器热量控制的中型和大型连接件,如汽轮机 火焰加热 加热器炭炉 集中,加热温度易于控制,操作鼓风机、透平压缩机的叶轮、组合式曲 简便 轴的曲柄等 沸水槽加热晶度阶它 ~100C, 适用于过盈量较小的连接件,如滚动轴 蒸汽加热槽可达120,热油 热 沸水槽,蒸汽加热 承、液体静压轴承、连杆衬套、齿轮
对 介质加热 槽加热可达90C一320C,均 槽,热油槽 忌油连接件,如氧压缩机上的连接件 可使连接件除油干净、热胀 需用沸水槽或蒸汽加热槽加热 均 装 加热温度可达400以上,热 电阻炉,红外线牺射 适用于小型和中型连接件,大型连接件 电阻加热和 胀均匀,表面洁净,加热温度易 辐射加热 加热箱 需专用设备,成批生产中广泛应用 于自动控制 加热温度可达400C以上,加适用于采用特重型和重型过盈配合的 感应加热 热时间短,调节温度方便,热效中型和大型连接件,如汽轮机叶轮,大 感应加热器 型压榨机部件等 率高 14
GB/T37400.10一2019 表B.1续) 主要设备 装配方法 使用范围 工艺特点 和工具 干冰冷缩装置或以 适用于过盈量小的小型连接件和薄壁衬 干冰冷缩 酒精、丙酮、汽油为可冷至一78C,操作简便 套等 介质 可冷至一40一140C,
适用于配合面精度较高的连接件,在热态 冷 冷缩均匀,表面洁净,冷缩 低温箱冷缩 各种类型低温箱 下工作的薄壁套简件,如发动机气门座 温度易于自动控制,生产 圈等 率高 装 移动式或固定式液 可冷至一195'C,冷缩时间 液氮冷缩 适用于过盈量较大的连接件,如发动机 氮槽 短,生产率高 主、副连杆衬套等,在过盈连接装配自动 移动式或固定式液可冷至一 180"C ,冷缩时间 化中常采用 液氧冷缩 氧槽 短,生产率高 15
GB/T37400.10一2019 录 附 资料性附录) 压装时压入力的计算公式 C.1压人力P按式(C.1)计算 P= =户iard,L 式中 -压人力,单位为牛顿(N); -结合表面承受的最大单位压力,单位为牛每平方毫米(N/mm); 力me -结合直径,单位为毫米(mm); dd ! 结合长度,单位为毫米(mm); 结合表面摩擦因数,见表C.1
表c.1摩擦因数 摩擦因数a 摩擦因数" 材料 材料 无润滑 有润滑 无润滑 有润滑 钢-钢 0.070.16 0.050.13 钢-青铜 0.15~0.20 0.030.06 钢-铸钢 0.1m 0.07 钢-铸铁 0.12~0.15 0.05~0.10 钢结构钢 铸铁-铸铁 0.10 0.08 0.150.25 0.050.10 0.11 0.07 钢-优质结构钢 c.2最大单位压力力i,按式(C.2)计算 8e imas C.2 C d十 E 式中 o -最大过盈量,单位为毫米(mm); ma ..C 系数,见式(C.3)、式(C.4); c 分别为包容件和被包容件的材料弹性模量,单位为牛每平方毫米(N/mm=),见表c.2. E.、E C.3系数C..C按式(C.3)和式(C.4)计算 d
”十d C.3 十U dl”十l2 C.4 dl 式中 分别为包容件外径和被包容件内径(实心轴d=0),单位为毫米(n mm da、l 材料的泊松系数,见表C.2
16
GB/T37400.10一2019 表c.2弹性模量E、泊松系数、线膨胀系数a 线膨胀系数a 弹性模量E 泊松系数 10-"/C 材 料 kN/mm 加热 冷却 200235 0.300.31 -8.5 碳钢,低合金钢合金结构钢 ll 灰口铸铁HT150 7080 0.240.25 11 HT200 灰口铸铁HT250 105~130 0.24一0.26 HT300 10 8 可锻铸铁 90100 0.25 160180 0.280.29 非合金球墨铸铁 85 0.35 17 -15 青铜 18 黄铜 80 0.360.37 16 21 铝合金 69 0.320.36 20 镁铝合金 40 0.250.30 25.5 25 17
GB/T37400.10一2019 附 录 D 资料性附录) 热装时加热温度和时间的确定 热装时包容件的加热温度可按推荐式(D.1)计算 D.1 A1十么2 D.1 品十1- t
al 式中 包容件加热温度,单位为摄氏度("C); 包容件内径的热胀量(等于过盈量4,与热装时的最小间隙4:之和),单位为毫米(mm); eot 材料的线膨胀系数,单位为每摄氏度(C-1),见表C.2(加热): 结合直径,单位为毫米(mm) dd 环境温度,单位为摄氏度(C)
D.2热装时所需的最小间隙4,按表D,.1选取
表D.1热装时所需的最小间隙4a 单位为毫米 结合直径 >80 >l00 >120 >150 >180 >220 >260 >310 >360 >440 >500 100 120 150 18o 220 26o 310 36o 一440 500 560 装配间隙 0.1 0.12 0.20 0.25 0.30 0.38 0.46 0.54 0.66 0.75 0.84 结合直径 >560o >630 >710 >800 >900 >1000>1120>l250>l400>1600o>l800 710 112o12501400~1600 1800 d 630 800 -900 1000 2000 装配间隙 1.10 1.20 1.40 1.6o 1.8o 2.00 3.20 2.20 2.6o 2.90 0.94 注:热装时所需的最小间隙的A经验数据为配合直径的1/1000mm1.5/1000mm
D.3加热和保温时间的经验数据,一般可按每厚10mm需要10min的加热时间,每厚40mm需要 10min的保温时间
D.4应用举例;已知包容件为钢制件,其结合直径d=150mm,最大过盈量41=0.117mm,求热装时 加热温度
解;查表C.2,钢制零件受热时的线膨胀系数a=ll×10-/C 查表D.1,热装时所需的最小间隙4=0.20mm 取环境温度/=25 0.117十0.20 A1十A2 十!= 十25=217(C ×0"×150 al 18
GB:/T37400.10一2019 附录 E 资料性附录 冷装时冷却温度和时间的确定 E.1冷装时的冷却温度应控制合适,可按推荐式(E.1)计算 2A eit ++ E.1 adl adl 式中: -冷却温度,单位为摄氏度(C); 被包容件外径的冷缩量(按经验数据取为结合面过盈量4,的2倍),单位为毫米(mm); e 材料的线膨胀系数,单位为每摄氏度(C-I),见表C.2(冷却); -结合直径,单位为毫米(mm).
dl E.2零件的冷却时间按式(E.2)计算: T
=kd十6 E.2 式中 -零件冷却所需的时间,单位为分(min); T -被冷却零件的最大半径或壁厚,单位为毫米(mm); -与零件材质和冷却介质有关的综合系数(见表E.1),单位为分每毫米(min/mm). 表E.1综合系数k 零件材质 钢 铸铁 黄铜 青铜 液态氮 1.2 1.3 0,8 0.9 冷却 介质 液态氧 1.4 .0 1.1 .5 E.3冷却剂工作温度见表E.2 表E.2冷却剂工作温度 冷却剂 工作温度 干冰加酒精或丙酮 -78 液态氧 180 液态氨 120C -195c 液态氮 E.4应用举例:已知被包容件为钢制件,其结合直径d/=1501 mm,最大过盈量41=0.090mm. 求冷装 时冷却温度和冷却时间
解:查表c.2,钢制零件冷却时的线膨胀系数a=一8.5×10-/C 则零件的冷却温度 2×0.090 =一141('C) -8.5×10×150 adl 采用液态氮冷却,则零件冷却时间 T
=k十6=1.2×75十6=96min
重型机械通用技术条件第10部分:装配GB/T37400.10-2019
重型机械作为重要的工业制造设备,在国民经济发展中具有重要地位。为了确保重型机械的质量和可靠性,针对其生产过程中的装配环节,国家制定了《重型机械通用技术条件》标准,其中第10部分为装配标准,即GB/T37400.10-2019标准。
GB/T37400.10-2019标准概述
GB/T37400.10-2019标准规定了重型机械在装配过程中所需遵循的基本要求、技术要求及检验方法等方面的内容。
1.基本要求
GB/T37400.10-2019标准明确了装配过程中应遵循的基本要求,包括:
- 在装配前应进行必要的检查和准备工作;
- 在装配过程中,要对各组件进行清洗、涂油等预处理工作;
- 应按照相关技术文件中规定的顺序进行装配工作;
- 装配完成后,应进行必要的检查和试运行。
2.技术要求
GB/T37400.10-2019标准还规定了重型机械装配过程中的技术要求,主要包括:
- 各零部件之间应符合相应的配合要求;
- 各紧固件应满足相关的强度和可靠性要求;
- 应采用适当的工具和设备进行装配,并保证其正确、安全和有效;
- 在特殊情况下,应按照相关技术文件中的规定进行特殊处理。
3.检验方法
为确保装配质量和可靠性,GB/T37400.10-2019标准还制定了相应的检验方法,包括外观检查、尺寸检查、配合检查、紧固件检查、试运行等环节。
结语
重型机械装配是一个复杂的工程,涉及到多个零部件、紧固件等,要求严格按照相关标准进行操作,以确保装配质量和可靠性。GB/T37400.10-2019标准对于重型机械装配过程中的基本要求、技术要求及检验方法等做出了明确规定,为重型机械制造企业提供了重要的参考依据。