GB/T23924-2009
三轮汽车和低速货车干摩擦式离合器
Tri-wheelvehiclesandlow-speedgoodsvehicles-Dryfrictionclutch
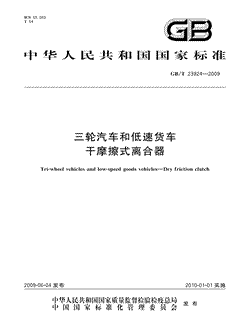
- 中国标准分类号(CCS)T54
- 国际标准分类号(ICS)65.060
- 实施日期2010-01-01
- 文件格式PDF
- 文本页数17页
- 文件大小760.65KB
以图片形式预览三轮汽车和低速货车干摩擦式离合器
三轮汽车和低速货车干摩擦式离合器
国家标准 GB/T23924一2009 三轮汽车和低速货车 干摩擦式离合器 Triwheelvehiclesamdow-speedgodsvehices一Drytrietioncuteh 2009-06-04发布 2010-01-01实施 国家质量监督检验检疫总局 发布 国家标准化管蹬委员会国家标准
GB/T23924一2009 三轮汽车和低速货车 干摩擦式离合器 范围 本标准规定了三轮汽车和低速货车干摩擦式离合器的术语和定义、技术要求、试验方法、检验规则、 标志、包装、运输与贮存
本标准适用于采用螺旋弹簧和膜片弹簧的三轮汽车和低速货车干摩擦式离合器
规范性引用文件 下列文件中的条款通过本标准的引用而成为本标准的条款
凡是注日期的引用文件,其随后所有 的修改单(不包括勘误的内容)或修订版均不适用于本标准,然而,鼓励根据本标准达成协议的各方研究 是否可使用这些文件的最新版本
凡是不注日期的引用文件,其最新版本适用于本标准
GB/T2828.1计数抽样检验程序第1部分;按接收质量限(AQL)检索的逐批检验抽样计划 (IsO2859-1:1999,IDT) JB/T5673农林拖拉机及机具涂漆通用技术条件 术语和定义 下列术语和定义适用于本标准
3.1 压缩特性eharacteristiesofcompressionm 从动盘总成厚度变化量和轴向载荷的关系
3.2 轴向压缩量axialcmpressiom 在工作压紧力下,从动盘总成厚度的变化量
3.3 分离扭转力矩releasetorque 在规定的工况下,离合器压盘达到图样规定的最小升程时,从动盘总成的旋转力矩
3 负荷特性characteristiesofloadl 在未安装从动盘总成的条件下,对压盘加载和最后减载过程中,作用在压盘上的载荷P与压盘位 移入之间的关系曲线
如图1所示
片/N '/N A/mm" 入/mm 螺旋弹簧 膜片弹氮 图1负荷特性
GB/T23924一2009 3.5 ontheworksite 工作位置压盘位移量pressureplate edispheement 入 离合器处于实际安装状态,压盘位置相对于未装从动盘总成时压盘位置的位移量
3.6 工作压紧力wnrkin" preSSure P 在负荷特性减载过程中P-A曲线上,对应于入,的载荷
分离特性releaseeharacteristies 离合器处于实际安装状态,或用相当于从动盘夹紧厚度的垫块代替从动盘,当分离和接合离合器 时,作用于分离杆(指)端的载荷P,及压盘升程随分离杆(指)端行程入变化的关系曲线
如图2 所示
P:/N P/N "a P"md 入2/mm 入2/mm 螺旋弹簧 膜片弹簧 图2分离特性 3.8 最大分离力 maximumreleaseforce 在规定的分离行程入范围内,分离特性P-入
曲线上的最大载荷值
3.9 压盘升程pressurepatetravel 在分离特性P-入
曲线上,对应规定分离行程入处,压盘上各点位移的最小量
3.10 压盘倾斜量pressureplateinclination h 在分离特性h入
曲线上,对应规定分离行程入处,压盘上各点位移中最大值和最小值之差
技术要求 一般要求 离合器应符合本标准的要求,并按经规定程序批准的图样和技术文件制造
4 离合器的滑动摩擦力矩 2 4.2.1摩擦片表面温度为250C时,单盘离合器单位面积滑动摩擦力矩应不低于表1的规定,双盘离 合器的单位面积滑动摩擦力矩不低于表1规定值的75%
GB/T23924一2009 表1双盘离合器的单位面积滑动摩擦力矩 离合器规格/mm 210 >210265 >265 单位面积滑动摩擦力矩/(Nm/cem 0.30 0.35 0,28 4.2.2摩擦片表面温度为250C时,离合器的滑动摩擦力矩应不小于常温时的70%
离合器的热负荷 离合器连续起步10次,每次起步的平均温升值应不大于10C
离合器摩擦衬片耐磨性 离合器经1.0×10'次模拟起步试验后,摩擦片单面磨损量应不大于0.65mm,摩擦片表面不应有 裂纹、气泡和铆钉露头等现象
4.5 离合器的分离扭转力矩 单盘离合器的分离扭转力矩应不大于0.2N
m 4.6离合器的静平衡 盖、压盘总成最大允许静不平衡量为6Mgcm,从动盘总成最大允许静不平衡量为12NMg”cm (M为盖、压盘总成质量千克数,M为从动盘总成质量千克数)
4.7盖总成工作压紧力 盖总成工作压紧力应符合产品使用说明书、技术文件或有关标准的规定,其偏差在工作压紧力的 土10%之内
4.8压盘升程 压盘升程应符合产品使用说明书、技术文件或有关标准的规定
盖总成动态分离耐久性能 4. 9 盖总成经4×10次动态分离耐久性试验后,应满足下列要求 a)分离轴承处载荷变化量不大于初始值的15% 压盘工作压紧力,对膜片弹簧离合器不小于初始值的85%,对螺旋弹簧离合器不小于初始值 b 的80%; e)压盘升程不小于初始值的85%; 分离杆(指)的鹰损量不小于分岗杆(指)端厚度的30% d 任何零件不应失效 e 从动盘总成夹紧厚度偏差及平行度 在工作压紧力下,从动盘总成夹紧厚度偏差及平行度分别为士2.5mm和0.2mmm
4.11从动盘总成轴向压缩耐久性能 在工作压紧力下,从动盘总成经2×10'次轴向压缩试验后应满足下列要求 a)轴向压缩量不小于初始值的80%; b)波形片无损伤、断裂,铆接无松动 任何零件不应失效 c) 4.12从动盘扭转耐久性能 从动盘总成经3.5×10次扭转耐久试验后应满足下列要求: 极限力矩不低于初始值的75%; a b)扭转减振器的摩擦力矩阻尼力矩)不低于初始值的60%; c各零件不应失效
分离杆(指)高度偏差及分离杆(指)端面跳动量 4.13.1在规定工况下,盖总成分离杆(指)端高度偏差不大于士1.5 mm
4.13.2 在规定工况下,盖总成分离杆(指)端与分离轴承接触圆周上的端面跳动量,对膜片弹簧离合器
GB/T23924一2009 不大于1 ,对螺旋弹簧离合器不大于0.5 mm mm 4.14离合器性能参数明示 离合器的下列性能参数必应在产品使用说明书和图样上明确规定 a)分离杆(指)行程及压盘升程; 压盘工作压紧力及压盘位置; b 扭转特性曲线及阻尼力矩值; d)从动盘总成轴向压缩特性 分离扭转力矩
4.15其他要求 4.15.1离合器应清洁,摩擦片表面不应粘有油污
4.15.2离合器各金属零件应经防锈处理,压盘表面允许涂防锈剂
4.15.3离合器总成表面涂漆应符合JB/T5673的规定
试验方法 5.1样品准备 试验前,按需要对样品进行针对性的原始数据测量和记录 5.2盖总成分离特性和负荷特性测定试验 5.2.1试验设备及仪表 使载荷均匀作用于分离杆(指)端、压盘摩擦表面,并与压盘摩擦表面垂直的盖总成静特性测量台 架,如图3和图4所示
测量台; 2 百分表; 垫块; 载荷测量装置; 代用分离轴承 5 代用飞轮
图3分离特性测量装置
GB/T23924一2009 支撑柱; 2 测量台; 代用飞轮 载荷测量装置 加载盘; 百分表 图4负荷特性测量装置 5.2.2试验程序 将盖总成按技术要求固定于代用飞轮上,中间装有相当于从动盘总成夹紧厚度的垫块 5.2.2.1 5.2.2.2将这套装置放于测量台中心,如图3所示
5.2.2.3操纵加载装置,使代用分离轴承行程达到规定的最大分离行程然后退回
如此动作10次后, 分离杆(指)预加规定载荷,将百分表或位移传感器调零
5. .2.2.4操纵加载机构,以适当的行程增量使离合器分离,直至达到最大分离行程为止,再以相同的行 程增量,使离合器接合,直至恢复零位,记录分离和接合时分离行程相对应的载荷及压盘位移
5 .2.2.5绘制分离特性曲线 5.2.2.6将按5.2.2.1的要求装好的试验装置放于测量台中心,如图4所示 5.2.2.7装百分表或位移传感器,使其与压就或与压盘摩擦表面援触的专用位移测量架相接触,调零
5.2.2.8对压盘施加载荷,使压盘移动 mm 1左右,取出垫块,然后减载至百分表复零
再继续减载 直至卸掉全部载荷,记录压盘从零位到全部卸掉载荷时的位移量,此值即为入6 5.2.2.9将百分表或位移传感器、负荷测量装置重新调零
5.2.2.10以适当的压盘位移增量对压盘加载,加载至超过入2.5mm左右,然后减载,直至卸掉全部 载荷,记录压盘上载荷P随压盘位移入变化的数字
5.2.2.11绘制负载荷特性曲线,注明入
5.2.2.12按图1和图2所示,确定P、Pm,h,和Mh
5. 3 从动盘总成轴向压缩特性,夹紧厚度及平行度测定试验 55 .3.1试验设备及仪器仪表 保证载荷垂直而均匀地作用于从动盘总成摩擦表面的轴向压缩特性试验台及相应的仪器仪表装 置,如图5所示
GB/T23924一2009 主框架; 位移传感器; 3 预载盘; 从动盘总成: 5 -下垫板
图5从动盘总成压缩特性测量装置 5.3.2试验程序 5.3.2.1将试验样品装于试验台上,装置状况如图5所示
5.3.2.2按工作压紧力压缩从动盘总成数次,直至轴向压缩量读数稳定,施加规定的预载荷,然后开始 测量
5.3.2.3对从动盘总成加载,直到从动盘总成上的载荷达到规定的工作压紧力,记录轴向压缩量d和 对应的垂直压力P 5.3.2.4达到规定的压紧力时,测量上下夹板间沿圆周均布三点处的距离,其平均值为从动盘总成的 夹紧厚度,最大值与最小值之差即为平行度
5.3.2.5以同样方法减载,直到载荷卸到零,记录轴向压缩量》和对应的垂直压力P
5.3.2.6绘制轴向压缩特性曲线,如图6所示,确定轴向压缩量o
"/N 6/mm 图6从动盘总成压缩特性 5.4从动盘总成减振器扭转特性测定试验 5.4.1试验设备及仪器仪表 保证摩擦衬片部分完全固定,并对盘毂施加扭转力矩的从动盘扭转特性试验台及相应的转角和力 矩测量装置,如图7所示
GB/T23924一2009 支撑板 花键轴; 从动盘总成; 夹紧板; 5 转矩测量装置; 转角测量装置 驱动装置
图7从动盘总成减振器扭转特性测量装置 5. .4.2试验程序 .4.2.1将从动盘总成装到试验台与之相配合的花键轴上,将摩擦衬片部分夹紧
5 5 4.2.2装转角指针或角位移传感器,使之能随盘毂一起转动并处于零位
4.2.3对盘毂施加扭转力矩,转动盘毂,直到与限位销接触为止 5 55 .4.2.4卸载至零
反向施加扭转力矩,转动盘毂,直到与限位销接触为止
5 .4 2. .5 5 .4.2.6卸载至零
55 4.2.7重复5.4.2.35.4.2.6两次
55 4 .2.8在中间位置检查并调整转角及扭转力矩至零位
5 2. 9 重复5.4.2.35.4.2.6,但需记录转角与扭转力矩对应数值
.4.2.10绘出扭转特性曲线,如图8所示
55 MNm" Mm Ma 当 0,0/(" M 扭转刚度:C
= 图8从动盘总成扭转特性
GB/T23924一2009 5.4.2.11按图8所示确定减振器极限转角o.,极限力矩M.m,规定转角处的摩擦阻尼力矩M, 规定转角范围a区间的扭转刚度c,对应发动机最大扭矩M.,时的转角0
5.5盖总成动态分离耐久性能试验 5.5.1试验条件 5.5.1.1盖总成转速 主轴转速为1450 r/min
5.5.1.2离合频率 离、合频率为(100士5)次/min
5.5.1.3分离行程 分离行程符合所试验离合器的使用说明书和产品图样的规定 5.5.1.4分离轴承 轴承接触表面尺寸及自由行程应符合产品图样要求,最好用使用中规定的分离轴承
分离轴承对 离合器回转中心偏心量为0.381 mm
5.5.1.5环境温度 室温或100C士10C,或根据试验性质和目的,由有关方面商定
5.5.1.6离合器安装状况及试验次数 按四种从动盘总成夹紧厚度安装,每种安装状况试验10×10'次
a) 第一种为名义夹紧厚度减去0.25 mm; b 第四种为从动盘磨损后的最薄厚度,由设计确定 第二种和第三种由第一种和第四种厚度之间的间隔等分确定
e) 试验总次数最少为4×10次
5.5.2试验设备 满足5.5.l试验条件的盖总成动态分离耐久性试验台,如图9所示 外罩; 垫板 代用飞轮 驱动装置; 盖总成 分离轴承; 曲柄连杆 曲柄驱动机构 风扇; 0 加热器 图9盖总成动态分离耐久性能试验台
GB/T23924一2009 5.5.3试验程序 5.5.3.1按5.2测总成分离特性及负荷特性,确定试验前的Pm.,h
和P
5.5.3. .2 将样品按规定装于试验台的飞轮上,在飞轮与压盘表面间装第一种厚度的垫板或垫块
5.5.3. .3 调整试验台,满足5.5.1的规定
5.5.3.4开动试验台连续动作10×10'次
5.5.3.5停机检查,如无零件损坏.将垫块厚度减至下一规定尺寸,连续动作10×10'次
5.5.3.6重复5.5.3.5直至完成第四种垫块厚度尺寸试验
5.5.3.7停机卸下样品,检查有无零件损坏,测量分离杆(指)磨损量,并按5.2测分离特性和负荷特 性,确定P.、h
和P 5.5.3.8重复5.5.3.2~5.5.3.7直至完成所要求的总循环次数或试件发生损坏为止
5.6从动盘总成轴向压缩耐久性试验 5.6. 试验条件 5.6.1.1轴向载荷;零至最大载荷往复循环,最大载荷等于与被试从动盘总成配用的盖总成工作压 紧力
5.6.1.2往复频率:(150200)次/min
5.6.1.3往复行程;与被试离合器规定的分离行程相同
5.6.1.4试验次数;(2×10'一4×10)次,可按有关规定确定
5.6.2试验设备 往复行程在(0一20)mm范围内可调,并满足5.6.1中规定的往复式试验台及与被试从动盘总成相 配套且工作压紧力符合规定的盖总成,如图10所示
-从动盘总成 代用飞轮; 芯轴 台架; 5 盖总成; 分离轴承 曲柄连杆; 曲柄驱动机构 图10从动盘总成轴向压缩耐久性能试验台 5.6.3试验程序 5.6.3.1按5.2确定盖总成的工作压紧力是否符合规定 5.6.3. 2 按5.3测量从动盘总成轴向压缩特性,确定试验前轴向压缩量d. 将被试从动盘总成和盖总成装于试验台上
5.6.3.4 调整试验台,满足5.6.1的规定
GB/T23924一2009 5.6.3.5开动试验台,使离合器分离、接合,往复循环至规定的试验次数
5.6.3.6拆下样品,按5.3规定测量从动盘总成轴向压缩特性,确定试验后的轴向压缩量d
5.6.3.7必要时取出摩擦衬片铆钉,取下摩擦衬片,检查波形片和摩擦衬片的损坏情况
5.7从动盘总成扭转耐久性能试验 试验条件 载荷:最小扭矩为25%发动机最大扭矩,最大扭矩为100%发动机最大扭矩的单向脉冲扭转 载荷,亦可按相应上述载荷的相应转角间接加载
5.7.1.2扭转频率:(420~1200)次/n min 5.7.1.3试验次数:3.5×10次或根据要求确定
5.7.2试验设备 满足5.7.1试验条件的机械式或液压式扭转疲劳试验台,如图7所示
5.7.3试验程序 按5.4规定测量从动盘总成减振器扭转特性曲线,确定试验前的扭转刚度Ca、摩擦阻力矩 M.、极限转角o和极限力矩M .7.3.2将样品装于试验台的花键轴上,将摩擦衬片部分固定
. 5 .7.3.3调整试验台后,以规定的载荷、频率,摆动减振器至规定的次数:50×10',100×10',200 1o',350×10',进行中间检查和最终检查
重复5.7.3.1并检查有无损坏、松动及磨损情况
5.8离合器分离扭转力矩测定 5.8.1试验条件 离合器总成应经过磨合,其接触面积大于80%,摩擦表面温度小于100C
5.8. 2 试验设备 能够对离合器总成的分离杆(指)施加均匀作用力,使压盘分离到规定的升程,通过芯轴转动从动盘 并测量转动力矩的装置
5.8.3试验程序 5.8.3.1将经过磨合的离合器总成安装到测量装置上
5.8.3. 2 从动盘承受工作压紧力
5.8.3.3对分离杆(指)施加均匀作用力,使压盘分离到规定的最小升程
5.8.3.4通过测力矩装置转动从动盘芯轴,使之旋转至少一周,同时测量旋转过程中转动力矩的平均 值,该平均转动力矩即为离合器分离扭转力矩
5.9离合器热负荷测定试验 5.9.1试验目的 模拟起步过程,确定离合器平均每接合一次的滑磨功及连续起步时的发热情况
5.9.2试验条件 5.9.2.1样品应经过磨合,其接触面积大于80%,摩擦表面温度小于100C
5.9.2.2起步转速一般为1450r/min. 5.9.2.3载荷相当于车辆满载,在10%坡度上,用1挡起步时的当量惯量和道路阻力矩
当量惯量按式(1)确定 wR J- 式中; 车辆1挡的当量惯量,单位为千克二次方米(kg”mi). W 车辆总质量,单位为千克(kg); R 车轮滚动半径,单位为米(m); 10
GB/T23924一2009 驱动桥减速比 变速器1挡速比
道路阻力矩按式(2)确定 WR M l11e 式中: M" 作用于离合器输出端上的道路阻力矩,单位为牛顿米(Nm). 道路阻力系数,夕-/oa+ Sina 滚动阻力系数,f=0.02; 坡路角度,tana=10%; 重力加速度,单位为米每二次方秒(m/s)
5.9.2.4每次接合的滑磨时间为1.5s士0.5s
5.9.2.5连续起步周期为30s
试验次数为10次
5.9.2.6 测量和记录的参数 需测量和记录接合过程中下列参数随时间的变化量 摩擦力矩; a b)离合器主动及从动部分转角或转速 摩擦表面温度
5.9 试验设备及测量记录装置 5.9.4.1满足5.9.2规定的试验条件的离合器综合性能试验台,其原理如图11所示
10 -- 输人转速传感器, 驱动电机; 储能飞轮" 代用飞轮; 离合器总成 分离轴承; 分离机构 输出转速转矩传感器 惯量盘 -加载,制动装置 图11离合器综合性能试验台 1l
GB/T23924一2009 5.9.4.2能实时测量和记录离合器接合过程中摩擦力矩、主动及从动部分转角或转速、摩擦表面温度 随时间变化的测量及记录装置
5.9.5试验程序 5.9.5.1按5.2和5.3的规定检查盖总成和从动盘总成,确定它们是否满足技术要求
士0.1 5.9.5.2在压盘表面中径处,距工作表面0.5mm士 1mm,埋装热电偶或其他感温元件
5.9.5.3将离合器按技术要求安装于试验台上
5.9.5.4装配当量惯量
5.9.5.5选择适当的工况磨合,满足5.9.2.1的规定
5.9.5.6按5.2和5.3的规定复验磨合后的盖总成和从动盘总成,确定夹紧厚度和对应的工作压 紧力
5.9.5.7将离合器重新装于试验台上,安装连接好温度、摩擦力矩、转角或转速的测量记录装置
5.9.5.8起动试验台上的控制装置,按5.9.2.25.9.2.6规定的条件,接合离合器,待主,从动部分同 步之后,分离离合器、制动从动部分至停止,再放松制动,依次顺序循环共10次,记录接合过程的各参 数,至少记录三次
5.9.5.9重复5.9.5.6
5.9.5.10根据记录整理出各次起步滑磨功及温升
滑磨功按式(3)处理 A=M(a一叫)dl (3 式中: -滑磨功,单位为焦耳(J); M. -摩擦力矩,单位为牛顿米(N
m); 接合过程的起、止时间,单位为秒(s); to、t 主、从动部分角速度,单位为弧度每秒(rad/s)
w、o 5.10离合器静摩擦力矩测定试验 5.10.1试验条件 5.10.1.1样品应经过磨合,磨合要求同5.9.2.1的规定
5.10.1.2在室温条件下加载至打滑
5.10.2试验设备 离合器综合性能试验台,要求同5.9.d.1. 5.10.3试验程序 让磨合好的离合器在试验台上处于完全接合状态,将主(或从)动部分固定,对从(或主)动部分缓慢 施加扭转载荷,测量并记录开始打滑时的扭矩,测量次数不少于五次,取算术平均值 5.11离合器滑动摩擦力矩测定试验 试验条件 5.11.1.1 应在完成5.9.5.8或5.10.3之后进行,否则样品应经过磨合,磨合要求同5.9.2.1 5 离合器从动盘总成固定不动,盖总成转速为摩擦片外径处线速度为17.0m/s士0.5m/s时 相应的转速 5.11.1.3摩擦表面温度从室温开始强制滑磨,直至300C
5.11.2测量和记录的参数 a 滑动摩擦力矩; b 摩擦表面温度 5.11.3试验设备 满足5.11.1试验条件的离合器综合性能试验台,同5.9.4的规定
12
GB/T23924一2009 5.11.4试验条件 5.11.4.1将磨合好并按5.2和5.3检验后的盖总成和从动盘总成或完成5.9.5.8之后的盖总成和从 动盘总成(表面用砂纸打磨去除油污或碳化物)装于试验台上 5.11.4.2调整试验台,满足5.l1.1的规定 5 .11.4.3调整摩擦力矩、温度测量记录装置
5. .11.4.4起动试验台的控制装置,按5.1l.1.2一5.11.1.3进行强制滑磨,记录对应于室温,50c、 100C、,150C,200C,250C及300C时的滑动摩擦力矩
5.11.4.5绘制滑动摩擦力矩随温度变化的关系曲线
计算250C时单位面积的滑动摩擦力矩
5. 12离合器摩擦衬片耐磨损性能试验 12.1试验条件 5 按5.9.2.15.9.2.4的规定,模拟车辆连续起步
12.1.2接合频率为(3一6)次/min
5 12.1.3摩擦表面温度不超过160c 5.12.1.4试验次数为10X10'次或根据不同要求商定
5 12.2试验设备 试验设备同5.9.4的规定
5.12.3试验程序 5.12.3.1按5.9.5.15.9.5.6的规定进行,并测量记录摩擦衬片的厚度,测量位置在每面中径处附 近均布三点,并作标记
5.12.3.2将离合器重新装于试验台上,按5.12.1规定的试验条件,模拟车辆连续起步,至规定的试验 次数 5 .12.3.3在完成2.5×10、5×10'次循环后,检查零件有无损坏
5.12.3.4在完成1×10'次循环后,拆下样品做最终检验,测量摩擦衬片标记处的厚度,确定摩擦中径 处平均磨损量 6 检验规则 6.1出厂检验 每套离合器总成,均要经质量检查合格后方可出厂,出厂时应附有产品质量合格证 6.1.2出厂检验项目如下 a)盖总成工作压紧力 压盘升程 b c离合器的静平衡, d) 分离扭转力矩; 分离杆(指)高度偏差及分离杆(指)端面跳动 f 外观质量
抽检的数量不少于三套,从企业成品库中随机抽取时,抽样基数不少于抽取数的10倍
1.4所检项目应全部合格方可判该检验批产品合格
6 6.2型式检验 有下列情况之一时,进行型式检验 6.2.1 新产品或老产品转厂生产的试制定型鉴定; a 13
GB/T23924一2009 b正式生产后,如结构、材料、工艺有较大改变,可能影响产品性能时 e)正常生产时,应定期周期性进行试验 产品长期停产后,恢复生产时 d 出厂检验结果与上次型式检验结果有较大差异时 e fD 国家质量监督机构提出进行型式检验的要求时
6.2.2型式检验项目如下 离合器的莆动摩擦力矩, a b)离合器的热负荷; c 离合器摩擦衬片的耐磨性; 离合器的分离扭转力矩; 离合器的静平衡; e 盖总成工作压紧力; 压盘升程 h)盖总成分离耐久性能; i 从动盘总成夹紧厚度偏差及平行度 从动盘总成轴向压缩耐久性能; 从动盘扭转耐久性能; k 分离杆(指)高度偏差及分离杆(指)端面跳动量; 其他要求
m 6. 2. 3 对6.2.2中a),b)e 、 hb )j),k)各项抽检一台,其余项目按6.1.3的规定抽检
6.2.4所有检验项目均合格,方可判通过型式检验
6.3用户验收 订货单位有权对收到的产品进行抽检,试验项目、抽样方案、抽样检查和判断处置规则应按本标准 和GB/T2828.1的规定,由供需双方商定
标志、包装、运输与贮存 标志 离合器出厂时,均应标示制造厂家的厂标,其上应注明离合器的型号与规格、制造日期与产品编号
7.2 包装 7.2.1离合器应包装牢靠,其包装箱内应附有产品说明书产品合格证
合格证应注明: a)制造厂名和商标; 产品名称、型号规格及总成号 b c制造厂质量检验章; d 执行标准编号; e)制造日期与产品编号
包装箱上应注明 7.2.2 a 制造厂名和商标 b)产品名称、型号规格及总成号; 包装箱内产品数量、毛重和净重 制造日期与生产批号 D 印有“小心轻放,勿受潮湿”和“向上”字样
e 14
GB/T23924一2009 7.3运输 运输过程中要小心轻放、防雨、防潮,从动盘不应粘有油污
7.4贮存 离合器应贮存于通风、干燥,无油污,无腐蚀的库房内
自出厂之日起六个月内,如有锈蚀现象应由 制造厂家负责