GB/T31213.2-2014
无损检测铸铁构件检测第2部分:声超声检测方法
Non-destructivetesting―Testingofcastironequipmentsandcomponents―Part2:Testmethodforacousto-ultrasonic
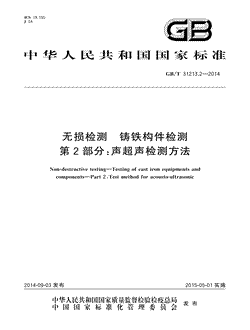
- 中国标准分类号(CCS)J04
- 国际标准分类号(ICS)19.100
- 实施日期2015-05-01
- 文件格式PDF
- 文本页数10页
- 文件大小402.87KB
以图片形式预览无损检测铸铁构件检测第2部分:声超声检测方法
无损检测铸铁构件检测第2部分:声超声检测方法
国家标准 GB/T31213.2一2014 无损检测铸铁构件检测 第2部分:声超声检测方法 Non-destruetivetestimg一Iestinmgofeastironequipmentsamd omponents一Part2:Testmethodforacoust0-ultrasonie 2014-09-03发布 2015-05-01实施 国家质量监督检验检疫总局 发布 国家标准化管理委员会国家标准
GB/T31213.2一2014 前 言 GB/T31213《无损检测铸铁构件检测》分为三个部分 -第1部分;超声检测方法; 第2部分:声超声检测方法; 第3部分;声发射检测方法
本部分为GB/T31213的第2部分
本部分按照GB/T1.1一2009给出的规则起草
本部分由全国无损检测标准化技术委员会(SAC/TC56)提出并归口
本部分起草单位;特种设备检测研究院、北京航空航天大学,北京声华兴业科技有限公司,河南 省锅炉压力容器安全检测研究院,杭州市特种设备检测院、保定市特种设备监督检验所、山东瑞祥模具 有限公司,硕德(北京)科技有眼公司
本部分主要起草人沈功田,李丽菲,梁琳,昊占稳、董屹彪、党林贵、王旭辉、陈海云、万海涛、 张君娇、王珊珊、苑一琳、香勇、刘延雷、张海营
GB/T31213.2一2014 无损检测铸铁构件检测 第2部分:声超声检测方法 范围 GB/T31213的本部分规定了铸铁构件的声超声检测方法
本部分适用于铸铁构件(包括铸铁烘缸、铸铁管道元件、铸铁阀门、铸铁结构件等)表面/近表面裂纹 缺陷和内部治金缺陷的快速检测
注:本部分未建立评价判据,具体的判据由合同各方协商确定
规范性引用文件 下列文件对于本文件的应用是必不可少的
凡是注日期的引用文件,仅注目期的版本适用于本义 件
凡是不注日期的引用文件,其最新版本(包括所有的修改单)适用于本文件
GB/T9445无损检测人员资格鉴定与认证 GB/T12604.1无损检测术语超声检测 GB/T12604.4无损检测术语声发射检测 GB/T19800无损检测声发射检测换能器的一级校准 GB/T19801无损检测声发射检测声发射传感器的二级校准 GB/T20737无损检测通用术语和定义 GB/T31213.1 无损检测铸铁构件检测第1部分;超声检测方法 术语和定义 GB/T12604.1,GB/T12604.4和GB/T20737界定的以及下列术语和定义适用于本文件
3.1 声超声 acOIst0-ultras0nic -种利用诱发应力波检测和评估被检构件弥散缺陷状态,损伤状况以及机械性能变化的无损检测 方法
注:声超声检测是声发射信号分析与超声波材料表征方法的结合 3.2 检测间隔testinginteral 声超声检测时,接收探头以相同间隔扫查的移动距离
3.3 最大容许缺陷maximumpermittedartirieinldefeet 不超过铸铁构件设计或制造相关标准规定的最大尺寸的缺陷
3.4 mmaximmumtestingdistanc 最大检测间距 在一定灵敏度条件下,激励探头与接收探头之间可达到的最大检测距离
GB/T31213.2一2014 方法概要 4.1 方法原理 声超声检测方法是一种根据超声波在构件中传播时产生的衰减变化对构件损伤实施检测的方法 其检测原理见图1
将检测探头放置在待测构件表面,信号发生器产生激励信号使激励探头发射超声 波,该超声波在构件内部与材料(包括各种内在的或外部环境作用产生的缺陷/损伤)相互作用并经历界 面的多次反射与波型转换后,到达接收探头,由于接收信号携带了材料内部信息,采集和分析接收信号 提取出能反映材料有无损伤变化的参量,从而根据该参量的变化情况对材料内部缺陷/损伤作出判断 存储 波形信号处理器 信号发生器 激励 前置放大器 信等 激励探头 按收探 图1铸铁构件声超声检测原理示意图 4.2检测方式 声超声检测方法有同侧和异侧两种检测方式
同侧检测方式如图2a)所示,激励探头与接收探头(一个/多个)位于被检构件的同一表面上
异侧检测方式如图2b)所示,激励探头与接收探头(一个/多个)分别位于被检构件上下相对的两 个表面上 激励探头 激励探头 接收探头 接收探头 同侧检测方式 异侧检测方式 b 图2铸铁构件声超声检测方式示意图 4.3扫查方式 检测时,检测探头的扫查方式包括如下三种类型 激励探头位置固定,接收探头以一定检测间隔沿激励-接收探头连线延长线移动,如图3 a 所示;
GB/T31213.2一2014 b激励-接收探头间距固定,二者同时以一定检测间隔在被检构件表面移动,如图3b)所示; 激励探头位置固定,多个接收探头按照一定阵列排布,如图3e)所示
激励探头固定,接收探头移动 激励-接收探头同时移动 多个接收探头 说明: 激励探头 接收探头
图3铸铁构件声超声检测探头扫查方法示意图 安全要求 本章没有列出进行检测时所有的安全要求,使用本部分的用户应在检测前建立安全准则
检测过程中的安全要求至少包括: 检测人员应遵守被检件现场的安全要求,根据检测地点的要求穿戴防护工作服和佩戴有关防 护设备 若有要求,使用的电子仪器应具有防爆功能; b 在封闭空间内进行操作时,应考虑氧气含量等相应因素,并采取必要的保护措施; c 在高空进行操作时,应考虑人员、,检测设备器材坠落等因素,并采取必要的保护措施 d 在极端环境下进行操作时,如低温、高温等条件下,应考虑冻伤,烫伤,中暑等因素,并采取必要 e 的保护措施; 如果存在有毒有害气体等其他可能损害人体的各种环境因素,在实施检测时,应仔细加以辨 识,并采取必要的保护措施 人员要求 采用本部分进行检测的人员应按GB/T9445的要求或有关主管部门的规定取得相应无损检测 人员资格鉴定机构颁发或认可的超声或声发射检测等级资格证书,从事相应资格等级规定的检测 工作
GB/T31213.2一2014 检测工艺规程 7.1通用检测工艺规程 从事声超声检测的单位应按本部分的要求制定通用检测工艺规程,其内容至少应包括如下要素: a)适用范围 执行标准、法规; b 检测人员资格 c d)检测仪器设备;鹏合剂,激励探头,接收探头,信号线,前置放大器、信号发生器,波形信号处理 器、检测数据采集和分析软件等; 被检件的信息:儿何形状与尺寸、材质、设计与运行参数; 检测覆盖范围及探头扫查部位; 被检件表面状态; g 检测时机 灵敏度测量、距离-幅度曲线绘制; 检测过程和数据分析解释; 检测结果的评定; k 检测记录、报告和资料存档 编制审核和批准人员; m n)编制日期
7.2检测作业指导书或工艺卡 应按9.1.3执行
检测设备和器材 声超声检测系统 8.1 8.1.1声超声检测系统包括超声信号激励和接收两部分
8.1.2超声信号激励部分包括信号发生器、信号线和激励探头,信号发生器经由信号线向激励探头发 送激励信号,激励信号的频率、幅值,周期数,重复频率应连续可调
8.13超声信号接收部分包括接收探头、信号线,前置放大器.波形信号处理器以及信号显示和存储设 备,该部分应具有信号波形采集、显示、分析与存储的功能 8.1.4声超声检测系统至少满足以下要求 a)激励探头和接收探头的工作频带宜在30kHz一500kHz的范围内,应根据实际被检件的材 料、几何尺寸和检测灵敏度要求来选择, 激励探头和接收探头应适用于被检构件材料和作业的工作温度; b 数据采集频率不低于激励信号最高频率的10倍.且与激励信号具有同步功能 c D 应具有绘制和存储距离-幅度曲线的功能; 应具有信号波形和信号波形特征参数两种信号采集方式,且可实现波形局部放大; 应具有实时存储检测信号的功能
GB/T31213.2一2014 8.2试件 8.2.1校准试件 校准试件用于对检测仪器进行灵敏度和各种功能的测试
校准试件应选用铸铁构件常用材料制 作,宽度不小于100cm,有深度为3mm和10%校准试件厚度的矩形切槽各一个,如图4所示
切槽的 长度为30 ,宽度在0.5 1,深度方向的公差为士0.2! 校准试件的长度、厚度和切槽位 mm mm一lmm, mm 置的要求见表1 厚度 宽度 深3mm 深109%校准试件厚度 长度 图4校准试件 表1校准试件的要求 单位为毫米 矩形切槽的位置 序号 厚度T 长度L L L T>20 L>1400 400 400 200 T>40 1>1200 300 300 200 T>60 L>1000 300 300 200 8.2.2对比试件 对比试件用于对被检件上缺陷损伤程度进行评定
对比试件应采用与被检件材料性能及几何形状 相同或相近的材料制作,并在对比试件上制作铸铁构件的最大容许人工缺陷
如进行裂纹性质的缺陷 检测,最大容许人工缺陷可以以人工刻槽来代表;如进行冶金性质的缺陷检测,对比试件可采用直接铸 造的方式来制作,也可选择带缺陷的实际工件
8.3检测设备的维护和校准 仪器使用单位应制定校准作业指导书,对检测设备进行周期性维护、检查和校准,以保证仪器功能, 校准结果应有相应记录和报告
在进行现场检测之前,应在实验室内选择相应规格的校准试件对检测仪器进行校准,若检测结果与 已知试件缺陷分布相符,则表明仪器正常
在现场进行检测时,如怀疑设备的检测结果,应对设备进行功能检查和调整,并对每次维护检查的 结果进行记录
传感器、前置放大器和系统主机每年应至少进行一次校准
传感器的校准按GB/T19800和 GB/T19801的要求进行,其他部件的校准按仪器制造商规定的方法进行
GB/T31213.2一2014 检测程序 9.1 检测前的准备 9.1.1资料审查 资料审查应包括下列内容 铸铁构件制造文件资料:产品合格证、质量证明文件,竣工图等; a b)铸铁构件运行记录资料;运行参数、工作环境、载荷变化情况以及运行中出现的异常情况等 检验资料;历次检验与检测报告; c d)其他资料:维护,保养,修理和改造的文件资料等 9.1.2现场勘察 在勘察现场时,应找出所有可能出现的噪声源,如脚手架的摩擦、内部或外部附件的移动、电磁干 扰、机械振动和流体流动等
应设法尽可能排除这些噪声源
9.1.3检测作业指导书或工艺卡的编制 对于每个铸铁构件,根据使用的仪器和现场实际情况,按照通用检测工艺规程编制声超声检测作业 指导书或工艺卡,确定激励探头和接收探头耦合的部位和表面条件
探头耦合部位应避开支吊架,内部 或外部附件的影响,同时对每个被检件进行测绘,对探头的稠合部位进行编号,画出被检件结构示意图
9.2探头的耦合 按照被检构件的规格选择合适的探头,并按照仪器说明书的要求合探头
探头耦合部位表面应去除涂层、防腐层或保温层,并进行打磨处理使之露出被检构件本体材料.,同 时,检测区域范围内应无液体或污垢等固体残留物以及可能影响检测的其他障碍物
距离-幅度曲线的绘制 9.3 应根据被检件的材料和规格,在实验室内选择相应符合8.2.2规定的对比试件绘制距离-幅度曲线, 曲线的纵坐标采用归一化的信号幅度
绘制对比试件上无人工缺陷部位的距离-幅度曲线(图5实线). 并存储
绘制激励-接收探头最大检测间距时人工缺陷部位的距离-幅度曲线(图5虚线),并存储,计算 出两条曲线相应纵坐标的最大差值H
00 距离/enm 图5对比试件的距离-幅度曲线示意图 9.4检测仪器系统的调试 根据构件的材料、尺寸和需要检测的缺陷类型,在仪器允许的激励频率范围内选取适当的激励
GB/T31213.2一2014 频率 通过调节仪器的参数设置使激励探头与接收探头处于最大检测间距时,检测仪器测量的对比试件 有和无人工缺陷部位波幅的最大差值H大于或等于10%,并进行记录
9.5检测信号的采集和分析 移动检测探头,绘制被检件的距离-幅度曲线,曲线的纵坐标采用归一化的信号幅度,将该曲线与存 储的对比试件无人工缺陷部位的距离-幅度曲线进行比较
当两条曲线相应纵坐标的最大差值H大 于50%H,时,则在激励探头与接收探头连线之间为声超声检测缺陷指示区域
此时,减小激励探头与 接收探头之间的检测间隔,再次绘制被检件的距离-幅度曲线,确定出该曲线与对比试件无人工缺陷部 位的距离-幅度曲线相应纵坐标的最大差值所对应的横坐标,确定出缺陷指示在被检件上的具体位置 并在被检件示意图和实物上做出标识
n至仅器激励与接收探头可达的最大检测 检测间隔应根据检测目的和缺陷大小确定,一般在10cm 距离的范围内
9.6影响检测结果的因素 9.6.1超声波传播特性 超声波固有的反射,波型转换和频散现象的存在会影响检测结果
9.6.2激励频率 在选择的激励频率范围内,激励频率越高,检测精度越高,有效检测距离越短;反之,则检测精度低, 有效检测距离长
9.6.3激励能量 激励能量越大,有效检测距离越长;反之,有效检测距离越短
9.6.4被检件工况 保温层、内部流动介质,支撑物等构件表面状态和构件温度,承载状态,焊缝以及腐蚀程度等因素均 影响到最大检测间距.并增加信号分析难度
l 检测结果的评价和处理 10.1检测结果的评价 10.1.1检测时应根据用户的要求确定不可接受的衰减信号幅度
10.1.2若确定为不可接受的衰减信号幅度,检测人员则应将发现的信号衰减部位在构件和图纸上分 别做出标识,即为不可接受信号部位
10.2检测结果的处理 对于声超声检测确定的不可接受信号的部位,可按照GB/T31213.1、NB/T47013.2 NB/T47013.4所规定的超声,射线或磁粉检测方法进行表面和(或)内部缺陷检测验证
GB/T31213.2一2014 11 检测记录和报告 11.1记录 11.1.1应按检测工艺规程的要求记录检测数据或信息,并按相关法规、标准和(或)合同要求保存所有 记录
11.1.2检测时如遇不可排除因素的噪声干扰,应如实记录,并在检测结果中注明
11.2报告 检测报告至少应包括以下内容 a 设备名称,编号,制造单位、设计载荷、温度、介质、最高工作载荷、材料牌号、公称壁厚和几何 尺寸; b)缺陷情况; 执行与参考标准; c 检测仪器名称,型号; 被检件表面状态,传感器型号,稠合剂,固定方式、检测频率; 对比试件的材料、尺寸,缺陷的形状 对比试件的距离-幅度曲线; 仪器检测状态参数的设置值; 被检构件及其缺陷位置示意图; 检测软件名称、检测设置文件名称及数据文件名称; k)结论; 检测人员、报告编写人和审核人签字及资格证书编号; 检测日期
m
无损检测铸铁构件检测第2部分:声超声检测方法GB/T31213.2-2014
无损检测是一种非破坏性检测技术,可以对材料内部缺陷进行检测,广泛应用于各种工业领域。而铸铁构件是常见的机械零部件,在制造和使用过程中可能存在各种缺陷,因此需要进行无损检测。
声超声检测是一种重要的无损检测方法之一,它利用高频声波在材料内部的传播特性来检测材料的缺陷。这种方法具有检测速度快、灵敏度高、定位准确等优点,在铸铁构件的检测中得到了广泛应用。
据中国国家标准GB/T31213.2-2014《无损检测 铸铁构件检测 第2部分:声超声检测方法》规定,声超声检测可以用于检测铸铁构件中的各种缺陷,例如夹杂、气孔、瘤子、裂纹等。其检测原理是:将高频声波引入被检测材料中,声波会在材料内部反射、折射和散射,这些反射、折射和散射信号会被接收器接收并转化为电信号,经过信号处理后,就可以确定材料中是否存在缺陷。
在实际应用中,声超声检测需要根据被检测材料的具体情况选择合适的探头、工作频率和检测模式。例如,在对铸铁结构件进行检测时,通常会使用低频段(0.5 MHz~1 MHz)的探头,以获得较大的穿透深度和较好的检测灵敏度。
总之,声超声检测是一种重要的无损检测方法,广泛应用于铸铁构件的检测中。通过合理选择探头和检测模式,可以获得较准确的检测结果,提高铸铁构件的质量和安全性。