GB/T28292-2012
钢铁工业含铁尘泥回收及利用技术规范
ThetechnicalspecificationforrecyclingandutilizationofFe-bearingdustsandsludgesinironandsteelindustry
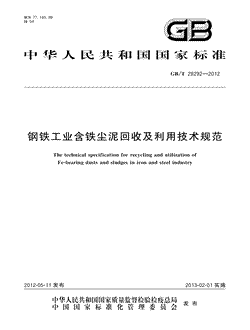
- 中国标准分类号(CCS)H54
- 国际标准分类号(ICS)77.140.99
- 实施日期2013-02-01
- 文件格式PDF
- 文本页数15页
- 文件大小453.97KB
以图片形式预览钢铁工业含铁尘泥回收及利用技术规范
钢铁工业含铁尘泥回收及利用技术规范
国家标准 GB/T28292一2012 钢铁工业含铁尘泥回收及利用技术规范 Thetechniealspeeifieationforreeyelingandutilizationof Fe-bearingdustsandsldgesinironandsteelindustry 2012-05-11发布 2013-02-01实施 国家质量监督检监检疫总局 发布 国家标准花管理委员会国家标准
GB/T28292一2012 前 言 本标准按照GB/T1.1一2009给出的规则起草
本标准由钢铁工业协会提出
本标准由全国钢标准化技术委员会(sAC/TC183)归口
本标淮起草单位;南京钢铁股份有限公司冶金工业信息标准研究院,宝钢技术研究院马鞍山钢铁 股份有限公司
本标准主要起草人刘飞、卢平,仇金辉、付伟,庄建志,廖东海、高建平,吴琳、徐海泉,贺红梅吕祥、 金德龙
GB/T28292一2012 钢铁工业含铁尘泥回收及利用技术规范 范围 本标准规定了钢铁企业含铁尘泥界定、处置、回收及利用技术的技术路线、工艺设计、,环境保护和评 价等技术原则
本标准适用于钢铁企业在原料准备、烧结、球团、炼铁、炼钢和轧钢等工艺过程中产生尘泥的回收及 利用,不包括冶金辅料尘泥、.轧锅含油尘泥和特种矿加工过程产生尘泥的回收及利用
其他行业含铁尘 泥回收及利用可参照本标准执行
规范性引用文件 下列文件对于本文件的应用是必不可少的
凡是注日期的引用文件,仅注日期的版本适用于本文 件
凡是不注日期的引用文件,其最新版本(包括所有的修改单)适用于本文件 GB/T476煤中碳和氢的测定方法 GB/T1574煤灰成分分析方法 GB/T2001焦炭工业分析测定方法 散装矿产品取样,制样通则手工取样方法 GB/T2007.l1 GB/T2007.2散装矿产品取样、制样通则手工制样方法 硫铁矿和硫精矿中铅含量的测定火焰原子吸收光谱法和EDTA容量法 GB/T2467 42 GB/T6730. 铁矿石化学分析方法双硫腺光度法测定铅量 6730.46铁矿石呻含量的测定蒸僧分离-呻钼蓝分光光度法 GB/T6730.54 铁矿石 铅含量的测定火焰原子吸收光谱法 6730.61 铁矿石碳和硫含量的测定高频燃烧红外吸收法 钙、硅、镁、钛,碑,、铝和饥含量的测定波长色散X射线荧光光谐法 GB/T6730.62 铁矿石 GB/T6730.65铁矿石全铁含量的测定三氧化钛还原重铭酸钾滴定法(常规方法) 铁矿石全铁含量的测定自动电位滴定法 GB/T6730.66 GB/T6730.67 铁矿石 碘含量的测定氢化物发生原子吸收光谱法 GB/T6730.68铁矿石灼烧减量的测定重量法 GB/T8151.1锌精矿化学分析方法锌量的测定 GB9078工业炉窑大气污染物排放标准 GB12348工业企业厂界环境噪声排放标准 GB13456钢铁工业水污染物排放标准 GB16297大气污染物综合排放标准 GB/T16597 冶金产品分析方法X射线荧光光谱法通则 GB18597危险废物贮存污染控制标准 GB18598危险废物填埋污染控制标准 GB18599 -般工业固体废物贮存、处置场污染控制标准 YB/T190.5连铸保护渣化学分析方法火焰原子吸收光谱法测定氧化钾,氧化钠含量 YB/T190.7连铸保护渣化学分析方法燃烧气体容量法和红外线吸收法测定碳含量
GB/T28292一2012 HU/T20工业固体废物采样制样技术规范 HU/T189清洁生产标准钢铁行业 H]/T426清洁生产标准钢铁行业烧结》 H]/T427清洁生产标准钢铁行业高炉炼铁 HU/T428清洁生产标准钢铁行业(炼钢 H]465钢铁工业发展循环经济环境保护导则 术语和定义 下列术语和定义适用于本文件
ofrawmaterialhandlin 原料准备尘泥 dustandsludge ingprocess 在原料场、烧结、球团、炼铁、炼钢和轧钢等工艺的原料准备过程中产生的尘泥
含铁尘泥rFc-bearingdustandsudge 含铁尘泥是钢铁企业在原料准备、烧结,球团、炼铁、炼钢和轧钢等工艺过程中进行干法除尘、湿法 除尘和废水处理后得到的固体废物,不包括冶金辅料尘泥、燃料尘泥和特种矿加工过程产生的尘泥
3.3 andsudge 烧结尘泥sinteringdust 在烧结原料准备,配料烧结与成品处理等过程中,除尘器收集下来的粉尘,主要包括烧结机机头、 机尾、成品整粒和冷却筛分等系统收集的烟尘、粉尘
3.4 球团尘泥peletizingdustandsludge 在球团原料准备、配料,熔烧与成品处理等过程中,除尘器收集下来的烟尘、粉尘
3.5 高炉瓦斯泥blastfurnaeegassludge 高炉炼铁过程中高炉煤气洗涤污水排放于沉淀池中经沉淀处理而得到的固体废物
3. 6 高炉瓦斯灰blastfurnacegasdust 高炉炼铁过程中随高炉煤气一起排出的烟尘,经干式除尘器收集得到的粉尘
3.7 高炉除尘灰blastfurnacedust 高炉炼铁过程中矿槽,筛分、转运,炉顶、出铁场等除尘工艺收集得到的粉尘 3.8 转炉尘泥converterdustandsludge 转炉炼钢过程中湿式和干式除尘器收集得到的固体废物,包括转炉尘泥(OG泥)和转炉粉尘
3.9 电炉粉尘eleetrieturnacedust 电炉炼钢过程中回收的粉尘 3.10 dstanmdsldege 轧钢尘泥steelrollin R 轧钢过程中回收的尘泥,不包括含油、含酸碱的酸洗二次尘泥
GB/T28292一2012 3.11 氧化铁皮milscale 在钢材轧制和连铸过程中剥落下来的固体物质
含铁尘泥的分类 4.1按含铁尘泥的来源,可分为原料准备尘泥、烧结尘泥、球团尘泥、高炉尘泥,炼钢尘泥和轧钢尘 泥等
4.2按含铁尘泥中锌(Zn)含量,含铁尘泥分为低锌含铁尘泥(Zn<1%),中锌含铁尘泥(1%
GB/T28292一2012 7.1.1企业外部处置方法分为企业外部露天堆放与填埋和企业外部集中处置两类
7.1.2企业内部处置方法分为企业内部直接回收利用和企业内部集中回收利用两类
7.2本标准规定了含铁尘泥在钢铁工业企业内部处置与回收利用的一般原则和技术路线 7.2.1企业内部直接回收利用是将含铁尘泥作为烧结、球团原料等在企业内部钢铁生产工艺上直接循 环利用
由于含铁尘泥品位差别较大、且含有有害杂质,长期直接循环利用会造成烧结矿铁品位降低、 有害杂质(主要为锌)含量提高,导致炉衬寿命和高炉利用系数降低
常用的直接回收利用工艺参见 9.1
7.2.2企业内部集中回收利用是将不同的钢铁生产工艺过程中收集的含铁尘泥进行集中堆放与贮存, 经过混匀、配料等工艺后,作为烧结与球团原料来使用
常用的集中回收利用工艺参见9.2 7.3企业外部集中处置与回收利用可参考钢铁工业企业内部处置与回收利用方法 含铁尘泥的回收技术 从含铁尘泥中回收铁,碳 8.1.1对于低锌含铁尘泥,可采用磁选、重选、浮选方法分离其中的铁和碳,进而得到含铁、含碳较高的 铁精矿或碳精矿
8 .1.2含铁尘泥中铁,碳回收工艺包括单一回收工艺和联合回收工艺 8.1.2.1单一回收工艺是指仅采用磁选、重选、浮选、反浮选中的一种方法进行铁、碳回收的工艺 8.1.2.2联合回收工艺是将两种或两种以上单一回收工艺进行集成的工艺,也是钢铁企业通常采用的 方法
常用的联合回收工艺有;弱磁选-强磁选(全磁选)工艺、浮选-重选工艺、粗磨-弱磁-强磁-反浮选 工艺,重选-反浮选-磁选工艺、磨矿-磁选-重选-浮选工艺等 8.1.3在应用上述单一或联合回收工艺的同时,鼓励钢铁企业根据含铁尘泥特性和企业自身条件,开 发和集成新的回收工艺,实现铁,碳资源的高效回收
8.2从含铁尘泥中回收锌 8.2.1物理法 8.2.1.1物理法锌回收技术适用于处理中锌含铁尘泥,一般只作为湿法或火法工艺的预处理方法,以 提高含铁尘泥中的锌含量
8.2.1.2物理法锌回收技术是采用机械分离离心,重选等)或磁性分离(磁选)的方式富集含铁尘泥中 的锌元索
常用的机械分离方法有浮选-重选工艺、水力旋流脱锌工艺等;常用磁性分离方法有弱磁-强 磁联合工艺等
经过物理法锌回收工艺处理后可以得到高锌含铁尘泥和低锌含铁尘泥两类物质,高锌含铁尘 泥可用作深度提锌原料,低锌含铁尘泥可回用烧结
8.2.2湿法 8.2.2.1湿法锌回收技术适用于处理高锌含铁尘泥
2 8.2.2. 湿法锌回收技术是利用氧化锌(ZnO)不溶于水或乙醇,但溶于酸、氢氧化钠或氯化铵等溶液 的性质,采用不同的浸出液,将锌从混合物中分离出来,再经过净化、电解的方法获得锌元素
8.2.2.3湿法锌回收工艺可采用酸浸、碱浸和焙烧十碱浸等方法
8.2.3火法 火法锌回收技术适用于处理中锌含铁尘泥
GB/T28292一2012 8.2.3.2火法锌回收技术是利用锌的沸点较低的特点,在高温还原条件下,锌的氧化物被还原,并气化 成锌蒸气随烟气一起排出;在气化相中,锌蒸气被氧化而形成锌的氧化物颗粒,同烟尘一起在烟气处理 系统中被收集下来
8.2.3.3火法锌回收工艺可分为直接还原法(包括转底炉法,回转窑法、循环流化床法等)和熔融还原 法(火焰反应炉还原法,等离子法等)两大类
8.2.3.4火法锌回收技术的典型工艺有转底炉法、回转窑法等
8.2.3.4.1转底炉法
该法是将中锌含铁尘泥和粘结剂等按比例配料,经造块、筛分,烘干后均布到转 底炉环形台车上,在高温加热条件下氧化锌被还原;高温球块从转底炉排出,经还原性气氛冷却后形成 金属化球团;还原的锌燕气随高温烟气一起排出,经换热器冷却后,形成细小的固体颗粒沉积在除尘 器内
采用转底炉法可将高炉瓦斯灰、转炉尘泥,氧化铁皮等通过转底炉生产出直接还原铁,供炼铁或炼 钢使用
8.2.3.4.2回转窑法
该法是把钢铁企业含锌尘泥与还原剂混合后送人还原回转窑,窑内炉料被加热 装置加热至一定温度,使得尘泥中铁和锌的氧化物被还原,其中锌元素在窑温下蒸发并与烟气一起离开 回转窑,经过收集装置得到富集锌,直接还原铁产品排人回转冷却器内,经快速冷却和筛分后得到筛上 和筛下直接还原铁,筛上物作为高炉原料使用,筛下物送往烧结使用
联合法 钢铁企业可以根据含铁尘泥的物理化学特性,将上述几种方法联合使用,找出最佳的工艺流程,以 得到最好的回收铁,碳、锌和其他有价金属的效果
含铁尘泥的利用技术 9 企业内部直接回收利用 g.1.1含铁尘泥直接返回烧结或球团工艺 烧结机头灰成品除尘灰、机尾除尘灰直接返回烧结 9.1.1.1 9.1.1.2高炉槽下除尘灰,重力除尘灰、出铁场除尘灰等随返矿通过外返矿皮带或汽车等运输方式返 回烧结
9.1.1.3转炉尘泥制成浓度15%一45%的泥浆,再加人到烧结或球团工艺的制粒机中 9.1.1.4转炉和高炉尘泥沉淀池中的污泥过筛后,采用泥浆输送管道运输到污泥搅拌罐,制成浓度为 15%一45%含尘泥浆,再经过泥浆泵输送至烧结混料机中制粒
9.1.1.5高炉瓦斯泥和转炉尘泥经过压滤、密封输送至烧结或球团工序使用
9.1.2含铁尘泥冷固结球团返回炼铁、炼钢工艺 该工艺是将低锌含铁尘泥,加人还原剂、粘结剂制成球团或压成块状,返回高炉,电炉或转炉冶炼 g.1.3转炉尘泥(0G泥)与氧化铁皮造块回用转炉造渣工艺 该工艺是将转炉尘泥、氧化铁皮和粘结剂等分别进行定量配料,经混碾、干燥、造块等工艺制成高强 度型块,作为炼钢造渣剂用于转炉炼钢
9.1.4转炉尘泥(oG泥)返回炼钢和烧结(或球团)的工艺 该工艺是将部分OG泥造块后直接返回炼钢使用或烧结工艺使用
GB/T28292一2012 g.1.5含铁尘泥金属化球团工艺 金属化球团工艺是将含铁尘泥造块后,采用回转窑或转底炉等直接还原工艺生产金属化球团,供高 炉炼铁或转炉炼钢使用
g.1.6高锌,高钾钠含铁尘泥回收利用 对于低锌含铁尘泥可采用9.1.19.1.5的工艺进行含铁尘泥的直接回收利用,而对于锌含量大于 1%、碱金属(钾钠)含量大于0.5%的含铁尘泥需经过脱锌,脱钾钠处理后才能返回钢铁生产工艺使用
9.2企业内部集中回收利用 9.2.1机械混合返回烧结工艺 该工艺是将高炉瓦斯泥、转炉尘泥、除尘灰、轧钢尘泥等经过机械混合等过程加工成松散的烧结混 合料,供烧结使用
9.2.2多种含铁尘泥均质化造粒回用烧结工艺 9.2.2.1该工艺是将来自钢铁生产各工序的含铁尘泥按照组成特性进行分类,堆放于原料场或储存于 密封料仓中,再经过混匀造粒后返回烧结工艺
多种含铁尘泥的均质化方式有综合原料场堆料混匀、混 合输送与均质化两种工艺方案
9.2.2.2综合原料场堆料混匀工艺是将多种含铁尘泥在综合原料场进行自然晾晒,再经过平铺直取等 堆料混匀后,以混匀矿进人烧结配料系统
9.2.2.3混合输送与均质化工艺是将分类堆放的尘泥从原料场取出,进行单独定量配料,配料后物料 进行混合输送和均质化处理,再经过制粒系统得到均质化的烧结颗粒料产品,最后运往烧结工艺利用 9.2.3含铁尘泥与除尘灰综合利用工艺 该工艺是将高钙灰与转炉尘泥充分混匀和消化,然后与高铁灰、高碳灰等按比例混匀,经制粒后供 烧结使用
10 环保要求 10.1技术的选择、设计,建设和运行管理应按HU465的规定进行
10.2环境保护应符合HJ/T189,HJ/T426,HJ/T427、HJ/T428的要求
10.3含铁尘泥的贮存和处置应符合GB18599的要求
对含有危险废物的含铁尘泥的填埋处置应符 合GB18597和GB18598的要求
10.4工业水污染物排放应符合GB13456的要求
10.5工业炉单元的大气污染物排放按GB9078的规定进行,其他单元的大气污染物排放应符合 GB16297要求
10.6噪声排放标准应符合GB12348的要求
11 评价指标和方法 11.1评价指标 钢铁工业含铁尘泥回收利用情况采用回收利用率R作为评价指标
GB/T28292一2012 11.2指标分级 本标准依据含铁尘泥回收利用率共给出了钢铁企业含铁尘泥回收利用的三级评价指标
一级指标 是对含铁尘泥回收利用的最高要求,三级指标是对钢铁企业含铁尘泥回收利用的基本要求
本标准的指标体系以钢铁生产各工艺过程的加权平均指标为评价依据,其他各项分类评价指标(如 原料准备、烧结、炼铁、炼钢和轧钢等工艺)为参考指标,可作为钢铁企业内部管理指标,以反映钢铁企业 工艺过程中含铁尘泥回收利用情况
钢铁企业不同工艺过程含铁尘泥评价指标如表1所示 表1含铁尘泥回收利用率的评价指标 指标等级及回收利用率/% 尘泥来源 级 二级 三级 原料准备工序 100 95 >90 烧结与球团工艺 100 >95 >90 炼铁工艺 100 >95 >90 炼钢工艺 100 >95 >90 轧钢工艺 100 >95 90 加权平均 >95 100 90 11.3回收利用率R的计算方法 11.3.1回收利用是指采用各种技术手段对含铁尘泥进行的各种合理有效的回收利用的技术路线和途 径,包括企业内部回收利用和通过企业外部加工返回利用
1.3.2回收利用率R是含铁尘泥回收利用量M占钢铁生产过程中含铁尘泥产生总量M的比率[见 式(l),式(2)和式(3]
它反映了钢铁企业在生产过程中对含铁尘泥回收利用的程度,是钢铁企业清洁 生产重要的考核指标
R=×100% x100% -(-出 M,=M十M
式中 回收利用率,%; R 回收利用的含铁尘泥量(干基),单位为吨每年(!/年) M 未回收利用的含铁尘泥量(干基),单位为吨每年(t/年); M
含铁尘泥产生总量(干基),是指钢铁企业各工艺过程达到国家排放指标要求条件下应收集 M 的含铁尘泥量的总和,单位为吨每年(t/年)
GB/T28292一2012 附 录A 规范性附录 含铁尘泥x射线荧光光谱化学分析 熔铸玻璃片法 范围 本附录适用于炼铁、炼钢含铁尘泥中全铁、二氧化硅、氧化钙,氧化镁、三氧化二、二氧化钛、氧化 、五氧化二磷和氧化锌九种组分的X荧光光谱同时测定,各组分测定范围列人表A.1
表A.1各组分测定范围 组分 测定范围/% TFe 30.0一75.0 SiO. 0.2~15.0 Cao 0.1一30.0 0,1~15.G MgO Al.O 0.15.0 TiO. 0,02~5.0 Mn(O 0,036,0 P.O 0.01l.0 ZnO 0.01一l0.0 A.2原理 将粉末样品熔制成玻璃片,用原级X射线照射,从样品中产生待分析元素的荧光光谱,经衍射晶体 分光,然后测量其强度,根据用标准样品制作的校准曲线,求出样品中分析元素的含量
A.3试剂与材料 分析中除另有说明外,应使用分析纯试剂
A.3.1三氧化二铁(Fe.O),优级纯
将三氧化二铁在700C下至少灼烧1h,然后在干燥器中冷却
A.3.2二氧化硅(SiO.),优级纯
将二氧化硅加热到1000C,至少灼烧1h,然后在干燥器中冷却
A.3.3碳酸钙(CacO,),优级纯
将碳酸钙在105C下烘1h,然后在干燥器中冷却
A.3.4氧化镁(Mg(O),优级纯
将氧化镁在1000下灼烧1h,然后置于干燥器中,冷却后,立即 称重
A.3.5三氧化二铝(A,O.),优级纯,a-型
将三氧化二铝在1000C下,至少灼烧2h(如果三氧化二 铝不是a-型,那么应加热到1250C,至少灼烧2h,使之转变成a-型),然后在干燥器中冷却
二氧化钛(To.),优级纯
将二氧化钛在1000下至少灼烧1h,然后在干燥器中冷却
A.3.6
GB/T28292一2012 A.3.7氧化(Mn,O),优级纯
将二氧化缸(MnO)置于铂金堆蜗中在1000下灼烧24h,然后 冷却
所得块状材料破碎成细粉,在550C下灼烧1h,然后在干燥器中冷却
A.3.8氧化锌(ZnO),优级纯
将氧化锌400下,至少灼烧1h,然后在干燥器中冷却
A.3.9磷酸二氢钾(KH,PO.),优级纯
将磷酸二氢钾在105C下烘1h,然后在干燥器中冷却
A.3.10碘化铵(NH.I)
碘化铵不需要烘干,但应贮存于干燥器中 注;当采用碘化铵或碘化锂时,应考虑碘对钛的干扰
A.3.11澳化铵(NHBr)
澳化铵不需要烘干,但应贮存于干燥器中
注,当采用澳化铵时,应考虑澳对铝的干扰
A.3.12氧化钻(Co.O.),优级纯
氧化钻(Co.O.)在1000下至少灼烧1h,然后在干燥器中冷却
A.3.13无水四碉酸锂(LiB,O,),优级纯
应在500C下灼烧4h,然后在干燥器中冷却、贮存
A.4仪器与设备 A.4.1波长色散X射线荧光光谱仪 仪器的校准环境应满足GB/T16597的规定
A.4.2氯甲婉气体(90%Ar十10%CH, 使用宣甲烧气体为X射线荧光光谱仪流气正比计数器专用气体时,应置于仪器室内
当钢瓶气压 低于1MPa时,应及时更换
更换后,钢瓶应稳定2h至室温后再使用
A.4.3熔融装置 熔融装置能达到1100C士50C
A.4.4墉蜗和模具 堆蜗和模具(或墉蜗兼作模具),铂金合金堆蜗(95%Pt十5%Au)加热熔融操作不易变形
堆蜗和 模具应具有足够装下熔融所需熔剂与试样的容量
模具应是平底,其厚度应足以防止变形
A.4.5瓷方舟
瓷方舟,20mL A.5试样 A.5.1试样准备 试样粒度应小于0.149mm
试样应在105C预干燥2h一4h,置于干燥器中,冷却至室温 注:应考虑研钵材质,以防止研钵材质对试样的污染
A.5.2试样灼烧 按GB/T6730.68的规定进行
灼烧后的样品用于制作玻璃样片
A.6玻璃样片的制备 A.6.1玻璃样片的配比 熔剂LiBO7.0000g士0.0005g,样品0.7000g士0.0002g,内标Co,.(O.0.0700g士0.0002g 剥离剂NH,Br0.000尽士0.0010长或NH.10.00ox士0,0010以
GB/T28292一2012 A.6.2熔融温度及时间 定量称取样品、熔剂和剥离剂至铂金墉蜗中,放人熔样装置内,在熔融温度为1100C时,熔融时间 21min(静置5min,倾动7min,倾动加旋转9 min 注:根据实验室条件试验,熔融条件应满足A.7.4玻璃样片的制备精度
A.6.3脱模 从玻璃片熔融装置中取出铂金堆蜗,放置在耐火板上,冷却至室温取出玻璃片,编号
注;大多的情况下,为了得到均匀玻璃片和从盘模具中脱出,快速冷却非常重要
也可采用水冷却金属板
A.6.4玻璃样片的制备精度 按A.6.1同一标样熔制6个样片,以建立校准曲线的分析条件进行连续测试
样片制备的重复性 按式A.1、式(A.2)计算 A.1 O 式中: 工 组分的平均测定值,CPS; i组分的j玻璃片的测定值,CPs; 工 组分的分析精度; o 组分的含量,%
当y>40时,a<0.15,并且.当8
GB/T28292一2012 A.7 R=d×R'十6 A.8 d=(Ro一Rn.)/R一RLb=Rou一d×Rm 式中: i元素的校正强度,CPS; i元素的测量强度,CPs; RoH/R1 -高、低标准化样品原始测量强度,CPS; R一R 高、低标准化样品测量强度,CPS 曲线斜率; dl 曲线截距
A.7.4.2未知样片的测量 输人试样名称(样片)、灼烧值等,在x射线荧光光谱仪上进行样片的测量 A.7.4.3测量结果的处理 根据用校准试样制作的校准曲线,求出样品中待分析元素的含量
A.8试验报告 试验报告应包括下列信息: 测试实验室名称和地址; 试验报告发布日期; 本标准的编号; 试样本身必要的详细说明; 分析结果; 与结果对应的编号 本标准中没有规定的可能对分析结果产生影响的操作及测定过程中存在的任何异常现象(如必要) A.9室内允许差 室内允许差见表A.2
表A.2含铁尘泥测定室内允许差 组 K 测定范围/% 允许差/% >56.0 0.8 TFe 30.0一56.0 0,6 <1.o 0.3 SiO. 1.0~10. 0 0.4 >10,0 0.6 S1.0 0.3 CaO 1.0~10.0 0.5 0.7 >10,0 12
GB/T28292一2012 表A.2(续) 测定范围/% 组 分 允许差/% 1.010.0 0.5 Mo >10,0 0.7 1.0 0.3 A,o >1.00 0. S1.00 0.2 TiO. >1.00 0.3 <1.00 0.1 Mno 1.005,00 0.2 >5.0 0.3 S0,5 0,2 P(O >0.5 0.3 <1.0 0.2 ZnO 1一5,0 0.3 5.0 0.4 13
钢铁工业含铁尘泥回收及利用技术规范GB/T28292-2012
随着我国钢铁工业的快速发展,其中产生的含铁尘泥问题也越来越严重。传统的处理方法多为填埋或堆放,这不仅造成了土地资源的浪费,还会给环境带来极大危害。因此,制定一套合理的含铁尘泥回收及利用技术规范显得尤为必要。
GB/T28292-2012《钢铁工业含铁尘泥回收及利用技术规范》就是中国国家标准化管理委员会于2012年发布的行业标准。该标准对含铁尘泥的回收、转化与利用进行了系统规范,并对技术指标和验收标准进行了详细说明。
该规范旨在鼓励和推广含铁尘泥的资源化利用,促进环境保护和经济可持续发展。它的发布对于解决钢铁工业中含铁尘泥问题具有重要意义。一方面,规范明确了含铁尘泥的回收、转化与利用的技术路线,指导企业在处理含铁尘泥时能够科学合理使用现代化技术手段,提高资源利用效率;另一方面,标准设定了含铁尘泥回收利用的技术指标和验收标准,规范了含铁尘泥回收利用的质量控制,提高了含铁尘泥资源化利用的水平。
总之,GB/T28292-2012标准作为行业标准,不仅指导着企业如何更好地开展含铁尘泥回收利用工作,并且推动了钢铁工业绿色发展,有效地提高了资源利用效率,降低了环境污染。未来,我们需要不断更新和完善这样的技术规范,进一步推动我国钢铁工业的可持续发展。