GB/T37584-2019
钛及钛合金制件热处理
Heattreatmentoftitaniumandtitaniumalloyparts
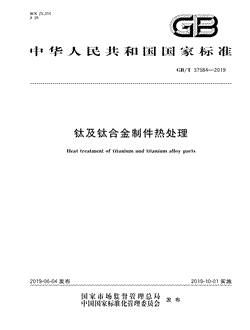
- 中国标准分类号(CCS)J36
- 国际标准分类号(ICS)25.200
- 实施日期2019-10-01
- 文件格式PDF
- 文本页数22页
- 文件大小1.64M
以图片形式预览钛及钛合金制件热处理
钛及钛合金制件热处理
国家标准 GB/T37584一2019 钛及钛合金制件热处理 Heattreatmmentoftitaniumanltitaniumalloyparts 2019-06-04发布 2019-10-01实施 国家市场监督管理总局 发布 国家标准化管理委员会国家标准
GB/T37584一2019 次 目 前言 范围 2 规范性引用文件 3 术语和定义 材料 设备与工装 热处理工艺与过程控制 生产操作与过程控制 质量控制与检验 15 技术安全与节能环保 17 10人员资质 18 19 附录A资料性附录)最大等效圆(ER)值的计算方法
GB/37584一2019 前 言 本标准按照GB/T1.1一2009给出的规则起草
请注意本文件的某些内容可能涉及专利
本文件的发布机构不承担识别这些专利的责任 本标准由全国热处理标准化技术委员会(SAC/TC75)提出并归口
本标准起草单位:航发北京航空材料研究院、北京机电研究所、山东天瑞重工有限公司、北京新 立机械有限责任公司、贵州航宇科技发展股份有限公司
本标准主要起草人:佟小军、贺瑞军、李俏、孙枫、李永胜、孙晓哲,谢撰业
GB/37584一2019 钛及钛合金制件热处理 范围 本标准规定了钛及钛合金制件(半成品及零件)热处理的材料、设备与工装、热处理工艺与过程控 制、生产操作与过程控制、质量控制与检验、技术安全与节能环保和人员资质等要求
本标准适用于钛及钛合金制件的热处理
规范性引用文件 下列文件对于本文件的应用是必不可少的
凡是注日期的引用文件,仅注日期的版本适用于本文 件
凡是不注日期的引用文件,其最新版本(包括所有的修改单)适用于本文件
GB/T228.1金属材料拉伸试验第1部分;室温试验方法 GB/T228.2金属材料拉伸试验第2部分;高温试验方法 GB/T229金属材料夏比摆锤冲击试验方法 GB/T232金属材料弯曲试验方法 GB/T3620.1钛及钛合金牌号和化学成分 GB/T4161金属材料平面应变断裂韧度Ke试验方法 海绵钛.钛及钛合金化学分析方法 GB/T4698.15 氢量的测定 GB/T4842 叙 GB/T4844纯氮、高纯氮和超纯氮 GB5226.1机械电气安全机械电气设备第1部分;通用技术条件 GB5959.4电热装置的安全第4部分;对电阻加热装置的特殊要求 GB/T6611钛及钛合金术语和金相图谱 GB/T7232金属热处理工艺术语 GB/T10066.1电热设备的试验方法第1部分;通用部分 GB/T10067.1电热装置基本技术条件第1部分;通用部分 GB/T10067.4电热装置基本技术条件第4部分;间接电阻炉 GB15735金属热处理生产过程安全、卫生要求 GB/T23603钛及钛合金表面污染层检测方法 GB/T27946热处理工作场所空气中有害物质的限值 GB/T30822热处理环境保护技术要求 GB/T30825热处理温度测量 GB/T32541热处理质量控制体系 HBZ344钛合金酸洗工艺及质量检验 JB/T6955热处理常用火介质技术要求 JB/T13026热处理用油基淬火介质
GB/T37584一2019 术语和定义 GB/T6611,GB/T7232,GB/T23603和GB/T30825界定的以及下列术语和定义适用于本文件
3.1 转变温度betatransformationtemperature 8相开始向8十a两相发生固态相变转变的温度
注,对于一种钛合金,一般依据其名义成分定义一个名义月转变温度;随着每批次钛合金的实际成分与名义成分的 偏离,实际8转变温度与名义8转变温度也会产生偏离,故每批次钛合金的实际成分确定了该批次钛合金的实 际转变温度
3.2 固溶处理soutiontreatment 在一定温度(通常为转变温度以下15C一40C)保温足够时间使可溶组分充分溶人固溶体的加 热处理
注;固溶的冷却方式通常为水冷,油冷或空冷
3.3 退火betaannealing 将钛合金加热到转变温度以上进行的退火处理
注:根据合金种类和使用目的不同,处理也可用于钛合金的固溶处理
3.4 氢污染hydrogencontamination 制件在含氢环境中加热或化学加工及酸洗处理中吸氢的过程
注:氢在钛中的扩散是可逆的,通常在700C左右的真空处理即可除氢
3.5 污染层contaminatedcease a层 制件在含氧、氮、碳的气氛中加热,当表面温度达到一定范围时,这些元素会扩散渗人产品表面,从 而产生由于a稳定剂引起的污染,形成富集氧、氮和碳的硬而脆的表层
材料 4.1常用钛及钛合金牌号及热处理 4.1.1常用合金类型及牌号 4.1.1.1钛及钛合金可以根据不同目的按不同原则分类
通常按不同退火组织形态分类,则可将钛合 金分为a合金、a-3合金、合金等几种类型
GB/T3620.1中常用钛及钛合金材料类型和牌号及名义 成分见表1
GB/37584一2019 表1常用钛及钛合金牌号及名义成分 名称 牌号 名义成分 TAl TA2 工业纯钛 TAs Ti-5AI-2.5sn TA7 TAll T-8A-1Mo-1v TA15 Ti-6Al2Zr-1Mo-1V 《钛合金 TA18 Ti3A!-2.5V TA19 Ti-6AI-2Sn-4Zr-2Mo TA21 T1A-1Mn Tc1 Ti2Al-1,5Mn Tc2 Ti3AN-1.5Mn TC4、ZTc4 Ti-6A4V TC6 Ti-6A!-2.5Mo-1.5Cr-0.3Si-0.5Fe TC10 Ti-6Al6V-2Sn-0.5Cu-0.5Fe Tc11 Ti-6.5A-3.3Mo-1.5Zr-0.25Si Tc16 Ti-3AI-5Mo4.5V Tc17 a3钛合金 Ti-5A2Sn-2Zr-4Mo-4Cr Ti-5Al5Mo-5V-1Cr1Fe Tc18 Ti6A-2Sn-4Zr-6Mo Tc19 Ti6Al2Mo-1.5Cr-2Sn-2Zr-2Nb Tc21 Tc: Ti5Al-2Sn-0,25S ZTc5 Ti-5.5AF-3.OMo-1.5V-lFe-1Cu-1.5Sn-3.5Zr TB2 T3Al-5V-5Mo-8Cn TB3 T-10Mo-8V-lFe3AI 3钛合金 T-15V-3Cr-3Sn-3A TB5 TB6 T-10V-2Fe3A 4.1.1.2钛及钛合金材料应符合相应的材料标准或规范规定,规格应满足制件需要或客户要求
4.1.2钛合金的热处理 4.1.2.1钛合金热处理通常可分为非强化热处理和强化热处理
a型钛合金的热处理一般为非强化热 处理,a-8型钛合金和8型钛合金的热处理一般为强化热处理
4.1.2.2钛合金的非强化热处理通常采用退火(包括普通退火、双重退火和等温退火等),强化热处理通 常采用固溶十时效处理
当需要消除或减少钛合金制件在铸造、冷热变形、焊接、机械加工时产生的残 余应力时,应采用非强化热处理;当需要获得设计的综合性能或某种特殊性能(如断裂韧性、疲劳性能或
GB/T37584一2019 热强性能等)时,应采用强化热处理
4.1.2.38型钛合金制件和其他经过固溶处理但未经时效处理的制件不应进行退火和去应力退火
4.2常用工艺材料 4.2.1热处理用气体 4.2.1.1钛及钛合金制件热处理用气体一般为空气和惰性气体
惰性气体通常为高纯缸、高纯氮或两 者的混合气,高纯和高纯氮应分别符合GB/T4842和GB/T4844的规定
也可以采用其他符合工 艺要求的惰性气体
4.2.1.2当采用工艺文件规定的其他气体时,其技术指标应满足工艺文件要求
4.2.2冷却介质 4.2.2.1冷却介质为油时,应符合JB/T13026的规定;介质为水或水溶液时应符合JB/T6955的要求 4.2.2.2冷却介质的使用温度应不高于产品规定的温度范围
油冷时油的起始温度应控制在15C 70范围,冷却过程中油温最高应在淬火油开口闪点以下80笔范围
4.2.2.3采用水或水溶液冷却时,介质起始温度应不高于40C
设备与工装 5 5.1设备 5.1.1加热设备 通用要求 5.1.1.1 5.1.1.1.1钛及钛合金制件可以用空气炉惰性气体保护炉或真空炉等进行热处理
不应使用盐浴炉 和流态床炉 5.1.1.1.2用于各类钛合金制件热处理的加热炉内均不应含有对制件产生不良影响的材料和/或介质
设备的加热特性应满足制件热处理工艺和工艺规范要求
5.1.1.1.3当处理的制件有炉内冷却速率要求时,设备应具有适应工艺要求的冷速控制功能和控制装 置,且冷速应满足工艺文件或客户要求
5.1.1.1.4应保证氢、氧、氮,碳对制件的污染程度最低,并保证热处理后的制件满足相应技术文件的 要求
5.1.1.1.5热处理炉设备的分类、温度均匀性检验、系统准确度校验和炉温控制与记录应符合 GB/T32541的规定
仪表配置类型应不低于GB/T3254l规定的D型配置
5.1.1.1.6用于制件退火、固溶处理的加热设备,其温度均匀性应不低于GB/T32541中类炉的规 定,用于制件时效的加热设备,其温度均匀性应不低于GB/T32541中I类炉的规定
工艺文件另有规 定的,按工艺文件规定执行
5.11.1.7各类加热设备均应具有相应的炉温均匀性测量和系统准确度校验用温度传感器插人孔或连 接结构或馈人装置温度控制的液体槽除外)
插人孔、连接结构及馈人装置不应对设备的加热保温性 能和密封性能产生不良影响
5.1.1.1.8制件加热后冷却用的真空油炉和具有自动淬火功能的其他热处理炉,其淳火转移时间应 保证满足工艺文件要求
GB/37584一2019 5.1.1.2空气电阻炉 5.1.1.2.1空气电阻炉可用于所有类型钛合金半成品件的加热
5.1.1.2.2空气电阻炉应有良好的密封性和保温性能,满足均匀加热的要求
用于低于650C时效处 理的炉子应配置炉气循环风扇
5.1.1.3惰性气体保护炉 5.1.1.3.1惰性气体炉内的惰性气体应循环流动且通畅,以使整炉钛合金制件的所有表面获得保护
5.1.1.3.2应保证惰性气体的循环合理,不对炉子的温度均匀性产生不良影响
5.1.1.4真空炉 5.1.1.4.1钛合金件在真空炉中进行加热时,真空炉的极限真空压强应不大于6.7×10-Pa,冷态压升 率应不大于0.67Pa/A
5.1.1.4.2真空炉加热室应具备回充保护气体的功能,并应配备炉气压力测量及显示仪表,对回充气体 的压力进行监测;还应配备露点仪对回充气体的露点进行监测;必要时,应配备炉气压力自动测量、控制 和记录系统
5.1.1.4.3真空高压气淬炉的气淬冷却能力应满足制件的工艺要求
5.1.2冷却设备 5.1.2.1火槽 5.1.2.1.1淬火槽的容积应能保证制件在连续生产条件下具备足够的冷却能力和制件在槽中移动的需 要,并应保证制件悴火或时效后达到规定的性能要求
必要时,淖火槽可带机械搅拌等装置(不得采用 压缩气体搅排)
5.1.2.1.2对于具有气淬功能的真空炉,其淬火冷却能力应满足工艺要求;对于具有水淬功能的真空 炉,水冷獐火槽不应对加热室以及设备的真空度产生不良影响
5.1.2.1.3对淬火槽液温度有要求时,应配备分辨力不低于3C的测温仪表
淖火槽应配置槽液冷却 装置,有要求时,应配备加热控温装置
5.1.2.2缓冷箱 缓冷箱用于要求在空气中慢冷/缓冷(即,比自然炉冷快但比空冷慢,以下均同)的制件冷却
为满 足制件的缓冷要求,缓冷箱内一般放置铁砂或石英砂或符合工艺要求的其他材料
5.1.2.3其他冷却设备或系统 采用连续式炉进行固溶处理的薄板、厚板和带材制件冷却时可采用喷雾或流体淬火冷却系统
该 系统应在制件出炉时以一定的流速将雾状或液态的淬火剂均匀地喷在制件的所有表面并使之保持一段 时间,以保证制件固溶或时效处理后能达到规定的性能要求
5.1.3清理和清洗设备 5.1.3.1制件和工装夹具的清洗和清理应采用专用设备
有温度要求的清洗设备,应配备分辨力不低 于3的测温仪表
GB/T37584一2019 5.1.3.2清洗和清理制件及工装夹具应采用符合制件清洗质量要求的设备、,喷砂和喷丸设备;选用的清 洗剂,砂和丸不应对制件和设备产生有害影响
设备应具备抽风和排污处理装置
5.2料框、料架和工装夹具 5.2.1制件热处理用的料筐、料架和工装夹具等应由耐高温材料如;钛合金、,镍基高温合金、不锈钢或 陶瓷材料)制成,且均不得与所承载的钛合金制件发生反应,也不应对热处理设备产生不良影响
不应 使用带有封闭腔体的管材制作工装夹具
如果加热过程中金属的工装火具与钛合金制件接触可能发生 不良反应时,应使用陶瓷元件隔离
5.2.2制件热处理用的料筐、料架和工装夹具应保证加热及冷却介质的循环通畅,并应能控制或减少 制件在加热和冷却过程中的畸变
6 热处理工艺与过程控制 6.1热处理工艺 6.1.1退火热处理 6.1.1.1退火 钛及钛合金制件的退火(包括普通退火,双重退火,等温退火)处理制度应符合表2的规定
保温时 间可根据制件的最大截面厚度按表2选取,也可根据制件的截面厚度按表3计算确定
表2退火制度 板材、带材及厚板制件 棒材制件及锻件 合金类型 合金牌号 加热温度 保温时间 加热温度 保温时间 冷却方式 冷却方式 min min TA2、TA3 650~720 15~120 空冷或更慢冷 650815 60~120 空冷 TA7 705845 l0120 空冷 705~845 60~240 60480 TAl1 760815 炉冷 9001000 60120 空冷" TA15 700850 15120 700850 60240 空冷 空冷 a钛合金 TA18 650~790 30~120 650~790 60~18o 空冷或更慢冷 空冷或更慢冷 TA19 870~925 10120 空冷 -(153060120 空冷" TC1 640750 15120 空冷或更慢冷 700800 60120 空冷或更慢冷 660820 15120 空冷或更慢冷 700820 60~120 空冷或更慢冷 TC2 705~870 15~60 705790 60~120 空冷或更慢冷 TC4 空冷或更慢冷" TC6 800850 60~120 空冷 TC1o 空冷或更慢冷 空冷或更慢冷 710850 15120 710850 60120 Tc11 60120 空冷 a钛合金 950980 680790 15120 770790 60~120o TC16 空冷 炉冷后空冷 TC18 740760 15120 空冷 820850 60~18o 炉冷后空冷 TC19 815915 60~120 空冷
GB/37584一2019 表2(续) 板材,带材及厚板制件 棒材制件及锻件 合金牌号 合金类型 加热温度 保温时间 加热温度 保温时间 冷却方式 冷却方式 mln mln zTc3 910 12021o 炉冷 -930 ZTC4 910~930 120180 炉冷 e月钛合金 ZTC5 910930 120180 炉冷 注:T -转变温度
炉冷到480以下
若双重退火,第二阶段应在790C保温15min,空冷 随后在595C保温8h,空冷 当Tc4合金制件的再结晶退火用于提高断裂韧度时,通常采用以下制度:在转变温度以下30C一45C,保 温1h~4h,空冷或更慢冷;再在700C760保温1h~2h,空冷
若TC4合金制件采用双重退火(或固溶处理和退火)时,退火处理制度为:在转变温度以下3045C,保 温1h~2h,空冷或更快冷;再在700760保温1h~2h,空冷
空冷后在530C580保温2h12h,空冷
以2C/nmin4C/ min的速度炉冷至550t(在真空炉中不高于500c),然后空冷 复杂退火,炉冷至740C760笔保温1h~3h,空冷,再在500C一650它保温2h一6h,空冷 表3制件厚度与保温时间之间的一般对应关系 最大截面厚度(直径 保温时间 mm mmin 1525 3 36 2535 613 3545 13一20 45一55 >20~25 >5565 >25 在厚度为25mm、保温60min的基础上,每增加5mm最少增加12min 6.1.1.2鼻退火 6.1.1.2.1对于TC4、TC4ELI、T-6A6V-2Sn和其他a-8合金,若规定进行8退火,则应在该合金3转 变温度以上25C土15C加热并保温不少于30min
制件在空气或惰性气体中冷至环境温度,不应随 炉冷却
6.1.1.2.2除合同或图样另有规定外,不应水冷
若采用水冷,TC4,TC4ELI、Ti-6AI-6V-2Sn合金水 冷后还应在730C一760C保温1h3h,进行第二次退火
6.1.1.3去应力退火 6.1.1.3.1制件可在不高于再结晶温度下进行去应力退火,以消除由于机加、冲压、焊接等工艺形成的 内应力
去应力退火所采用的加热温度和保温时间应按表4规定
制件应在真空,空气或惰性气体中
GB/T37584一2019 冷却或者随炉冷却
6.1.1.3.2对于已经固溶处理十时效强化或经过双重退火的制件,去应力退火的加热温度不应超过时 效温度或第二阶段退火温度
6.1.1.3.3对于已固溶但尚未时效处理的制件,不应进行去应力退火
表4去应力退火制度 加热温度 保温时间 合金类型 合金牌号 min TA2、TA3、TA4 480600 15~240 TA7 540650 15360 TAll 595760 10~75 600650 30~480 TAl5
钛合金 TA18 370~595 15~240 TAI9 480650 60一240 52058o Tc1 30240 545600 30~360 Tc2" Tc4" 480650 60~240 TC'6 530~620 30360 TC10 540600 30360 TC1l 500600 30~360 Tc16 550650 30240 Tc17 r月钛合金 480一650 60240 Tc18 600680 60~24o TC21 530一620 30360 ZTC3 620一800 60240 ZTC4 600800 60240 550~800 60~240 ZTC5 TB 650~700 30~60 TB3 680730 3060 钛合金 TB5 680~710 3060 TB6 675705 30~6o 与镀镍或镀铬零件接触的TC1和TC2媒接部件和零件的退火,只允许在520的真空炉中进行
去应力退火可以在760笔~790C与热成形同时进行
固溶与时效处理 6.1.2 6.1.2.1固溶处理 6.1.2.1.1对于a-8合金,制件的固溶加热应在a-区温度进行;对于8合金,制件固溶加热通常在高于
GB/37584一2019 转变温度或高于a-9区温度进行
固溶热处理制度可按表5的规定执行
制件淬火转移时间应符合 表6的规定,TC4半成品件应符合表7的规定
表5固溶处理制度 板材、带材及厚板制件 棒材制件,锻件及铸件 合金牌号 冷却方式 保温时间 合金类型 加热温度 保温时间 加热温度 min min TAll 9001010 20~90 空冷或更快冷 a钛合金 TA19 815~915 20~12o 290 900980 空冷或更快冷 TC4 890970 2~90 890~970 20120 水淬 TC6 840900 20120 水 850900 290 850900 水辫 TC10 20120 Tc16 780~830 90~15o 水消 la-钛合金 TC17 790815 20120 水淬 水浓 TC18 720~780" 60180 Tc9 815915 s15二915 20120 290 空冷或水消 870~925 870925 20120 水淬 Ti-6A-2Sn-2Zr-2Mo-2Cr-0.25Si 290 TB2 750800 030 750800 2一30 空冷或更快冷 TB5 760815 760~815 月钛合金 空冷或更快冷 230 2090 TB6 705775 60120 水" 对于复杂形状的Tc18半成品或零件,推荐可先810C一830C,保温1h一3h,炉冷,再执行本表制度,然后执 行表8的时效制度 直径或截面厚度不大于25mm时,允许空冷 表6最大淖火转移时间 最小截面厚度 转移时间 mm 0.6 >0.62.5 10 >2.525 15 -25 30 注1悴火转移时间是指从炉门打开直到整个装料完全浸人悴火剂所用的时间
注2:本表中的悴火转移时间不包括TC4合金
GB/T37584一2019 表7TC4合金半成品最大淖火转移时间 最小截面厚度 转移时间 mm >625 25 10 注:悴火转移时间是指从炉门打开直到整个装料完全浸人猝火剂所用的时间
但若能够确定炉门开启过程中 所有装料的温度下降仍在工艺温度允许的温度偏差内,则可以不将炉门开启的时间计算到转移时间内, 6.1.2.1.2对于TC4、TC4ELI、Ti-6AI-6V-2S和其他a8合金制件,若规定进行月固溶处理,则按 6.1.1.2的规定执行
6.1.2.1.3TcC16合金紧固件的强化热处理由三个必要的工序组成;退火(780×2h,以2C/min 4C/min的逃度炉冷至550,然后空冷)、※火(800C×2h,水冷)和时效[560Cx6h10h),空 冷]
注:TC16合金紧固件的强化热处理可选择下述工艺进行;加热至790810保温2h,以2C/min一4C/min 的速度炉冷至760C780,保温2h,水冷;在500C540时效,保温4h8h,空冷
6.1.2.2时效处理 固溶热处理后应按表8规定对合金制件进行时效处理
时效后,制件应在真空、空气或惰性气体中 进行冷却或随炉冷却
表8时效处理制度 加热温度 保温时间 合金类型 合金牌号 TAll 540620 824
钛合金 565620 2 TA19 TC4 480690 28 Tc6 500620 Tc1o 510一600 Tc16 50058o 4~1o a-钛合金 Tc17 480675 48 TC18 480600 410 TC19 585675 48 Ti-6Al-2Sn-2Zr2Mo2Cr0.25S 480~675 2~10 TB2 450~550 8一24 TB5 480675 月钛合金 224 TB6 480620 8~10 10
GB/37584一2019 6.2工艺过程控制 6.2.1温度控制 6.2.1.1钛及钛合金制件的热处理应在符合工艺规定满足温度均匀性的热处理炉内进行
6.2.1.2除非工艺文件特别规定,本标准所有给出的温度范围值是温度控制仪表可以设定的范围值
6.2.1.3若以载荷热电偶作为温度控制热电偶,则炉内任意其他工艺温度传感器的温度数据都不应超 过工艺设定温度允许的最大偏差上限
6.2.2保温时间及起始计算 6.2.2.1除非工艺文件另有规定,热处理保温时间的起始计算均应以炉内最后一支工艺温度传感器的 温度数据到达工艺设定温度所要求的温度均匀性下限时开始
6.2.2.2保温时间可以用实验方法确定
形状复杂制件其加热保温时间可采用等效圆(ER)法确定,计 算方法参见附录A
6.2.2.3制件在真空炉中加热时,若加热滞后时间已知,保温时间为加热滞后时间加上表3和表4对应 栏所规定的时间;加热滞后时间未知时,保温时间为表3和表4对应栏规定的保温时间的2倍
6.2.3淬火转移时间及计算 6.2.3.1淖火转移时间按表6和表7执行
对于薄壁件、片状件和细小制件,火转移时间应尽量缩 短
工艺文件对淬火转移时间另有规定的,按工艺文件执行
对于空气炉,惰性气体炉和真空炉(除单室炉)淖火转移时间的计算一般应以加热室炉门开启 6.2.3.2 时刻为起始直至装料完全没人冷却介质中为止
对于大型真空炉,应通过工艺试验和性能测试确定是 否可从装料开始移动时刻为起始进行淬火转移时间的计算
6.2.4真空热处理分压 6.2.4.1采用真空炉进行制件固溶加热时,真空工作压强应根据加热温度不同按下列规定控制 加热温度不大于750C时,真空压强不大于6.7×10-'Pa; a b 加热温度超过750C时,应向加热室回充氨气、氨气或两者的混合气或其他符合工艺要求的 气、体进行分压保护,以防止制件表面出现合金元素贫化的现象
分压压强应控制在1.33Pa~ 13.3Pa范围;工艺文件另有规定的,按工艺文件规定控制分压压强
6.2.4.2采用真空炉进行制件时效加热时,真空工作压强应控制在6.7×10-'Pa1.33×10-Pa范围
6.2.5加热介质 6.2.5.1加热介质应符合4.2.1要求,炉内加热介质需呈还原性气氛,但允许呈弱氧化性气氛
6.2.5.2在整个热处理过程中,禁止采用盐浴,吸热式或放热式气氛、氢气气氛(特殊工艺有要求的除 外)以及氨裂解后形成的气氛进行加热
生产操作与过程控制 7.1一般要求 7.1.1制件和试样表面状态 7.1.1.1待热处理的制件和试样表面应保持净洁和干燥,特别是待固溶淬火处理的制件和试样表面不 11
GB/T37584一2019 应有手印,油污、污物、涂层痕迹、铝痕及粉笔痕迹
7.1.1.2允许采用预留加工余量的方法保证热处理后能够通过机加工去除表面污染层
7.2生产操作 7.2.1热处理准备 7.2.1.1应按制件热处理工艺或工艺文件规定确定适用的热处理设备,工艺气氛和工装夹具
7.2.1.2热处理前,应彻底清除制件,试样和工装夹具表面的润滑油脂、卤化物以及其他有害的外来物
不应使用卤化溶剂或甲醇除油
7.2.1.3热处理前,应对含有热处理禁用气氛的热处理炉进行清洗
清洗用的气体为空气或惰性气体 用量至少应为炉膛容积的两倍
应对沾有有害物质的热处理炉进行清理,具体要求如下 采用空气炉进行热处理时,应在制件装炉前清理和清洗
应将之前处理的其他金属的残留物 如氧化皮、金属削末,涂层剥落等彻底清除干净;用气流清洗时,炉内的最低温度应为制件热处 理时的预定保温温度
不能用气流进行清洗时,炉内温度至少应比热处理的预定保温温度高 10C,并在此温度下至少保温4h b 采用惰性气体炉进行热处理时,制件应冷态装炉,随后进行清洗并使炉内充满惰性气体
c 采用真空炉进行热处理时,应在装炉前清洗
炉内真空工作压强应尽可能低,至少不大于6.7× 10-Pa
加热温度应比已进行过的最高热处理温度至少高10C以上,保温时间不少于1h
必要时可带随炉检验试样,清洗后按8.2.2.4检查随炉试样表面污染情况,以检验清洗是否 充分
真空钉焊炉不能直接用于钛合金制件的真空热处理,应进行彻底清理并用同种类型的材料或 d 试样进行试验验证,满足工艺要求后方可使用
7.2.1.4对于具有成品尺寸、机加工余量小的精密毛坯及具有精细尺寸的元件(如螺纹),表面有氧化控 制要求且在后续的加工中不能有效去除污染层的制件,应选用惰性气体保护炉或真空炉进行加热
7.2.1.5对于要求慢冷或缓冷的制件,应准备好适用的缓冷箱;当条件具备时,应选用具有冷速控制功 能且冷速满足工艺要求的炉子设备进行制件的加热
7.2.1.6应选择适合的工装夹具装载制件,且选用的工装夹具的热强性和耐蚀性能应满足所处理制件 的工艺要求
7.2.2热处理操作 7.2.2.1一般要求 7.2.2.1.1严格执行制件的工艺规范和设备操作规程,达到图样或工艺文件要求的制件热处理性能及 其他技术要求
7.2.2.1.2制件,试样和工装夹具在清洗、清理干净后,操作人员应戴白色脱脂棉手套或采用其他适宜 的保护方法进行装载操作,防止再次造成制件、试样和工装夹具的污染
7.2.2.2随炉试样准备 7.2.2.2.1对制件的力学性能有要求时,每热处理炉批应跟随力学性能试样,每种力学性能试样一般不 少于3个
每热处理炉批用于检验表面污染的试样应遵循;在惰性气体或真空气氛中加热时,如果加热 温度高于540C,且制件热处理后不再进行机加工,则每次装炉均需附带一个随炉试样;若加热温度低 于540,则不需放置随炉试样
12
GB/37584一2019 7.2.2.2.2表面污染检验试样应与材料或制件同牌号、同热处理状态,性能试样应与材料或制件同牌 号、同热处理状态、同炉批
试样的规格、形式应符合技术文件要求
试样通常是专门加工的,图样或技术文件有要求 7.2.2.2.3 时,试样也可以是预留在制件规定部位上的
对于小型制件,可以用无镀层的产品制件代替试样
增氛 mm×25mm 试样的规格通常为0.50 n薄片样
7.2.2.3制件和试样装载 7.2.2.3.1制件和随炉试样应以合理的方式装载摆放或吊挂,制件之间应留有合适的间隙,保证加热介 质的自由循环和所有炉料的均匀加热,最大限度地减少加热和淬火带来的变形
7.2.2.3.2禁止使用带有镀锌层、镀仞层的铁丝绑扎固定制件和试样
7.2.2.3.3若采用不锈钢制作的工装在真空炉中使用,装载时应在制件与工装接触的部位放上钛合金 垫片或陶瓷垫片
7.2.2.3.4制件和试样人炉时应确保料筐或料架放置在炉子的有效加热区内
制件及试样一般是到温 后人炉,有人炉温度要求时应按要求的温度人炉
在真空炉中加热时,制件可随炉升温
7.2.2.4淖火冷却 7.2.2.4.1制件出炉淬火冷却时应操作平稳,防止制件因碰撞或强烈晃动产生变形
应在要求的转移 时间内完成淬火操作
7.2.2.4.2制件在水,水溶液或油中冷却时,应使獐火介质充分循环搅拌和/或使所有装料在介质中适 度移动以保证冷却均匀、快速
7.2.2.4.3对于空冷的制件应散开放置或放置在流动的空气环境中;有快冷要求时,可使用风扇或鼓风 机吹风以满足制件冷却速率要求
7.2.2.4.4对于要求在空气中慢冷或缓冷的制件,若制件的加热不是在具有冷速控制功能的炉内进行, 则应使用缓冷箱进行制件的慢冷或缓冷
7.2.2.5真空热处理操作 7.2.2.5.1在升温加热前真空加热室的压力应保证在规定的工作压强,一般不大于6.7×10-?Pa,且在 真空加热过程中应按工艺规定对加热室回充惰性气体进行分压操作
当工作分压低于规定压强范围 时,应再向炉内充人规定的惰性气体
充人炉内的惰性气体露点应不高于一54 7.2.2.5.2最大截面厚度超过25mm的制件应进行预热
预热在低于最终热处理工艺温度100C 200c下进行并保温足够长的时间,预热后升温至规定的热处理工艺温度
7.2.2.5.3真空水淬时应向水淬室充人一定压力的惰性气体,充气压力一般不低于6.7×10'Pa,防止水 或水汽进人加热室同时保证水冷却效果
7.2.2.5.4真空退火或去应力处理或除氢处理等需炉冷的工艺,制件应炉冷到200C以下才能出炉
7.2.2.5.5带有密闭腔体的制件包括组合件)固溶处理时不得在真空炉内进行加热
7.3生产过程控制 7.3.1制件和试样查验 7.3.1.1热处理生产前,应对转人热处理工序的制件及试样的材料牌号、热处理状态、表面状态(包括保 护镀层或涂覆层、数量与规格以及随料或随件的工序文件等进行检查验收并应符合工艺文件和7.1的 要求,当发现有不相符的情况时,应拒收
13
GB/T37584一2019 7.3.1.2每个试样或试件均应有明显的标记并应能区分所代表的热处理炉批
7.3.2表面污染控制 7.3.2.1热处理生产过程中应严格控制炉内气氛防止制件出现表面增氢和污染,避免出现超过图样或 工艺文件规定的增氢、增氮、增碳,确保制件表面氧化程度(可通过颜色辨别)不超过工艺文件规定
7.3.2.2对真空热处理,应定时检查回充惰性气体的露点值;对惰性气体保护热处理,应定时检查气源, 防止供气中断
7.3.3重复热处理 钛及钛合金制件允许进行重复热处理
重复热处理的次数一般为1次,最多不超过两次
7.3.3.1 专 用文件或客户另有规定的按专用工艺文件或客户规定执行
7.3.3.2重复热处理时原试样和余料应跟随制件进行完整的热处理过程
检验增氢及表面污染的试样 不进行时效处理
7.3.3.3由于真空除气导致过时效而需要重新固溶,时效热处理时,应与客户协商一致
7.3.4去应力退火 7.3.4.1凡经机械校正(当允许时)的制件均应按规定进行去应力退火
对于固溶时效处理制件,去应 力退火温度应比时效温度低30C 7.3.4.2经喷丸强化的制件禁止在固溶处理后进行去应力退火
7.3.5除氢处理 7.3.5.1对于制件和试样的增氢控制应贯穿于整个工艺和生产操作过程
当最终热处理后按8.2.2.4 检验表面增氢超过规定时,应及时在真空炉内进行除氨处理,但事先应与客户协商一致
7.3.5.2除氢处理的加热温度一般比制件和试样最后一道工艺温度低30C或更多,但不低于550 若最后一道工艺温度不能满足除氢温度要求,则应当在前一道热处理工序完成后进行除氢处理;除氢处 理的极限工作真空度应不大于6.7×10-?Pa,保温足够时间后炉冷至200C以下出炉
除氢处理的保 温时间可参照表9
表9除氢处理的保温时间 保温时间 最大截面厚度(直径 mm h 20 12 >2050 23 >50 7.3.6污染层的去除 7.3.6.1当制件在非惰性气氛或非真空环境中加热到540C以上时,应留有足够的加工余量以去除表 面污染层,确保成品制件全表面清洁无污染
制件表面的清理清洗可采用酸洗(碱洗),化学髋切、喷砂(喷丸)或机械加工等方法或客户能按 7.3.6.2 受的其他方法,酸洗(碱洗)按HB/Z344规定进行
专用文件另有规定的,按专用文件执行
14
GB/37584一2019 7.3.6.3表面金属的去除应在制件热处理后立即完成,除非还有加工工序,否则不应延迟
表10给出 了制件在空气气氛中热处理后表面金属最少去除量指导值
表10制件表面金属去除量指导值 加热时间/h 不大于 加热温度/ 0.5 0.2 0 20 不大于 金属去除量/mm 不少于 600 0.01 0.01 0.01 0.01 0.03 0.05 700 0.01 0.01 0.03 0.03 0.05 0.08 0.08 760 0,01 0,03 0.03 0.08 0.08 0.08 0,15 820 0.05 0.,12 0.10 0.15 0.03 0.03 870 0.05 0.05 0.08 0.13 0.20 0.25 930 0,05 0,08 0.10 0.15 0,25 980 0,08 0,10 0.15 0.25 1040 0.,13 0.20 0.39 1100 0,15 0,25 质量控制与检验 8 8.1质量控制 8.1.1材料 8.1.1.1钛及钛合金的材质应符合对应材料规范的规定并应有相应的材质证明(质量保证书)
必要 时,应对原材料进行人厂复验
8.1.1.2热处理用油、水溶液的生产厂家应提供产品出厂检验报告及产品检验合格证,必要时,进行人 厂复验
使用过程中应按工艺材料标准或技术条件规定定期检测并合格
8.1.2设备 8.1.2.1应按GB/T30825或专用技术文件的规定对热处理设备及辅助设备、配套装置和仪器仪表(包 括温度传感器)定期进行检验、测试与校准并应符合规定
.1.2.2用于测量和监控热处理过程的所有工艺仪表和计量器具均应符合GB/T30825规定的准确度 等级要求
专用仪表或装置(如;露点仪等)应符合产品说明书规定的准确度指标
8.1.2.3应定期检测真空炉的极限真空度和冷态压升率并应满足设备技术指标要求或工艺文件规定
冷态压升率的检测方法按GB/T10066.1的规定执行,起始测试压强应不大于规定的真空压强
对于 连续使用的真空炉应每周检测一次,对于非连续使用使用间隔时间大于一周)的炉子,允许延长到每次 使用前进行检测
15
GB/T37584一2019 8.1.2.4应定期进行空气或非惰性气氛炉的增氢检测试验
每周应将炉子加热到650C以上进行一次 试样随炉装载,然后检测增氢和表面污染
8.1.3热处理后状态 8.1.3.1真空或惰性气体保护热处理后的制件表面应光亮或光洁,无磕伤、碰伤及无法去除的划痕
8.1.3.2真空热处理后的制件表面不应出现合金元素贫化现象即异常光亮且密布小坑
8.1.3.3热处理后的制件表面不应存在无法去除的污染层(厚度超过预留的加工余量或对无余量件)
若经检查发现表面增氢,应及时进行除氢处理
制件最终热处理变形应在工艺文件允许的范朋内
8.1.3.4 8.1.4热处理文档 8.1.4.1按要求填写并妥善保存热处理原始记录,建立完整的产品热处理加工档案
每台用于钛合金 热处理的加热设备的记录作为符合本标准的证据之一予以存档
除非客户文件另有规定,这些记录应 从记录之日起保存10年
8.1.4.2热处理炉设备的有效加热区测定原始记录与报告、工艺仪表系统准确度校验原始记录与报告 和设备配置的工艺仪表与传感器的检验报告或校准记录应存档并至少保存10年
8.1.4.3热处理检验结果、试样测试试验结果的记录应存档并从检验和试验之日起至少保存10年
8.1.4.4除氢处理过程应予以记录,内容至少应包括加热温度、保温时间和真空压强值
记录应存档并 至少保存10年
8.2检验 8.2.1检验项目 8.2.1.1 -般检验 应按制件图样规定和技术文件要求对热处理后的制件或试样进行相关项目的检验
专用技 8.2.1.1.1 术文件另有规定时,按专用技术文件规定执行
检验结果应满足图样,技术文件和本标准要求
8.2.1.1.2一般应对热处理后的制件及试样表面状态、外形尺寸、力学性能以及表面污染进行检验
检 验项目应在图样上注明或在技术文件中明确规定
8.2.1.2力学性能 钛及钛合金件热处理后应按工艺文件规定检测力学性能
8.2.1.3增氢和表面污染 应对最终热处理制件进行增氢和表面层污染检验并应符合图样或技术文件要求
8.2.2检验方法与评定要求 8.2.2.1 表面质量 8.2.2.1.1制件表面质量的检验一般采用目视或不大于10倍的放大镜进行观察
表面不应出现裂纹 腐蚀、无法加工消除的碰伤,划痕以及技术文件规定的其他不得出现的表面缺陷
8.2.2.1.2真空或惰性气体保护热处理制件的表面应光亮或光洁,表面呈有光泽的淡黄色是可以接受 的氧化色
16
GB/37584一2019 8.2.2.2形状和尺寸 采用规定的测量器具、专用装置对制件的尺寸和变形量进行测量与检验,并应满足图样规定或技术 文件要求
8.2.2.3性能 室温力学性能拉伸试验按GB/T228.1规定的方法执行,高温力学性能拉伸试验按GB/T228.2规 定的方法执行,冲击性能试验按GB/T229规定的方法执行,断裂性能试验按GB/T4161规定的方法 执行,弯曲性能试验按GB/T232规定的方法执行,用20倍的放大镜对试样弯曲部位进行观察,任何方 向上不得有裂纹或开裂
专用技术文件另有规定的,按专用技术文件规定执行
8.2.2.4增氢和表面污染 8.2.2.4.1氢含量的检测按GB/T4698.15的规定执行,增加的氢含量一般应不超过15×10-",或按工 艺文件规定
8.2.2.4.2表面污染层检测和评价方法按GB/T23603的规定执行
8.3检验超差的处理 当制件表面氢的增量超过本标准或工艺文件或客户要求时,可按7.3.5方法进行除复处理并按 8.3.1 8.1.4.4进行记录并归档保存
8.3.2检制件表面存在污染层时,应分别按7.3.6.2和7.3.6.3进行表面污染层和金属层的去除
8.3.3当制件最终热处理组织和性能不满足工艺或图样要求时,允许进行重复热处理
重复热处理应 符合7.3.3或客户规定 技术安全与节能环保 g.1技术安全 热处理生产过程的安全卫生按GB15735的要求执行
工作场所空气中有害物质应符合 9.1.1 GB/T27946的规定
9.1.2热处理加热设备、辅助加热设备或装置的技术安全应符合GB5226.1,GB5959.4,GB/T10067.1 和GB/T10067.4的规定
请理或清洗设备及其他铺助设备应符合国家或行业有关的标雅或技术条件,使用过程中应严格 9.1.3 按使用操作说明书执行,确保安全生产 g.1.4热处理生产使用的各种工艺气体的放置和保管应符合相应的国家或行业标准或企业技术安全 条例规定
g.1.5淬火用油和水溶液的使用、维护、存放与保管应严格按厂家提供的专用技术文件规定和国家或 行业的有关规范与安全条例执行,防止油或溶液着火,确保使用安全;油槽和使用现场应有灭火设施或 装置
9.1.6热处理现场人员应穿戴与热处理环境和热处理工艺相适应的劳动保护用品和用具
9.2节能环保 9.2.1热处理生产过程中产生的气体,液体和废油等的排放和处理应符合GB15735,GB/T30822和 17
GB/T37584一2019 国家其他相关的标准和环境保护条例要求,做到无害排放
9.2.2真空炉的机械泵排气管道应安装油气分离装置;多个真空泵可以合用一套油气分离装置
9.2.3空气电阻炉和气体保护电阻炉设备的保温层结构应采用陶瓷纤维或性能更优的节能保温材料 应符合GB/T10067.1、GB/T10067.4的规定
10人员资质 热处理操作人员应具备相应的热处理知识和操作技能,具有相关设备操作证;并应经过专业培训和 考核,获得资质后持证上岗
其他应符合GB15735或GB/T32541的规定
18
GB/37584一2019 录 附 A 资料性附录 最大等效圆(ER)值的计算方法 钛及钛合金件常见形状的最大等效圆(ER)值的计算方法见表A.1表A.2
表A.1实心体最大等效圆计算方法 下列实心体”的最大等效圆值 六角形 圆形 方形 矩形或板 ER= T ER=1.1T ER=1.25T ER=1.5T 注:T为直径或宽度H为高度;长度设为L 当L<丁时将截面看作厚度为L的板
当H>2T,且L>T时,将截面看作厚度为T的板
表A.2管状体最大等效圆计算方法 下列管状体(任何截面)的最大等效圆 -端或两端受限制或封闭" 两端开口 D<63.50mm(2.5in D>63.50mm(2.5in ER=2T ER=2.5T ER=3.5T 注,D为管子外径;丁为管子壁厚或端口受限处的厚度
当L
钛及钛合金制件热处理GB/T37584-2019
一、热处理概述
热处理是指通过加热、保温和冷却等工艺过程,改变金属材料的组织结构和性能,以达到提高其力学性能、耐腐蚀性、导热性等目的的一种金属加工技术。
钛及钛合金作为重要的航空、航天、国防等行业的结构材料,在使用过程中需要具备高强度、高韧性、高抗腐蚀性和高温稳定性等特殊性能。因此,热处理在钛及钛合金制件的生产和应用中具有重要意义。
二、热处理方法
目前,钛及钛合金制件的常见热处理方法主要包括:
- 固溶处理
- 时效处理
- 淬火处理
- 回火处理
2.1 固溶处理
固溶处理是将钛及钛合金加热至高温区,保持一定时间后,经过快速冷却获得均匀的固溶体。固溶处理可消除钛及钛合金中的α相和β相之间的残余应力,提高材料的塑性和韧性,同时改善其加工性能。
2.2 时效处理
时效处理是钛及钛合金在固溶状态下,在较低的温度下保温一段时间,使其析出出特定尺寸的强化相,从而提高其强度和硬度。时效处理也被称为人工时效,通常需要进行两次热处理,一次固溶处理和一次时效处理。
2.3 淬火处理
淬火处理是将钛及钛合金加热至高温区,然后迅速冷却到室温或以下。淬火处理可使钛及钛合金形成马氏体,从而提高其硬度和强度。但是,淬火处理会降低材料的塑性和韧性。
2.4 回火处理
回火处理是将钛及钛合金在淬火处理后进行加热,保温一段时间,然后冷却到室温以下的一种热处理方法。回火处理可以消除淬火残留应力,提高钛及钛合金的塑性和韧性,同时保持其较高的强度。
三、注意事项
钛及钛合金制件在热处理过程中需要注意以下几点:
- 掌握热处理规范和方法,严格按照标准要求进行操作。
- 严格控制热处理过程中的温度、时间和冷却速率,以避免产生不必要的残余应力。
- 加工前应对材料进行充分的热处理,以保证其性能符合设计要求。
- 热处理后需要进行必要的检测和质量控制,确保产品符合标准和客户的要求。
四、GB/T37584-2019标准
GB/T37584-2019是我国钛及钛合金制件热处理技术规范的最新标准。该标准规定了钛及钛合金制件的固溶、时效、淬火和回火等热处理方法、工艺参数、质量要求和检测方法等内容。
钛及钛合金制件生产和应用中,应严格按照GB/T37584-2019标准的要求进行热处理,以保证产品的质量和安全性能。
五、总结
热处理是钛及钛合金制件生产和应用中不可或缺的环节。通过选择合适的热处理方法和工艺参数,可以提高钛及钛合金制件的力学性能、耐腐蚀性和高温稳定性。同时,在热处理过程中需要注意控制温度、时间和冷却速率等因素,以保证产品质量。
GB/T37584-2019标准为钛及钛合金制件的热处理提供了详细的规范,生产和应用中应严格按照标准要求进行操作,确保产品质量和安全性能。