GB/T18442.4-2019
固定式真空绝热深冷压力容器第4部分:制造
Staticvacuuminsulatedcryogenicpressurevessels—Part4:Fabrication
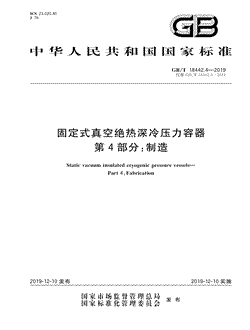
- 中国标准分类号(CCS)J76
- 国际标准分类号(ICS)23.020.40
- 实施日期2019-12-10
- 文件格式PDF
- 文本页数15页
- 文件大小1.23M
以图片形式预览固定式真空绝热深冷压力容器第4部分:制造
固定式真空绝热深冷压力容器第4部分:制造
国家标准 GB/T18442.4一2019 代替GB/T18442.42011 固定式真空绝热深冷压力容器 第4部分:制造 Staticvaeuuminsulatedcryogenicpressure veSSels Part4:Fabrieation 2019-12-10发布 2019-12-10实施 国家市场监督管理总局 发布 国家标涯花管理委员会国家标准
GB/T18442.4一2019 次 目 前言 范围 2 规范性引用文件 术语和定义 -般要求 材料复验、分割与标志移植 冷、热加工成型与组装 焊接 无损检测 热处理 1C 清洁要求 组装要求 12吸附剂的安装 13管路制造 氮质谐检漏 14 15罐体涂敷 16标志标识 1 出厂资料 18封存、装运
GB;/T18442.4一2019 前 言 18442《固定式真空绝热深冷压力容器》分为以下7个部分 GB/T 第1部分:总则; 第2部分;材料; 第3部分设计 第4部分;制造; 第5部分;检验与试验 第6部分安全防护; -第7部分;内容器应变强化技术规定
本部分为GB/T18442的第4部分
本部分按照GB/T1.l一2009给出的规则起草
本部分代替GB/T18442.4一2011《固定式真空绝热深冷压力容器第4部分;制造》,与GB/T18442.4 2011相比,除编辑性修改外主要技术变化如下 修改了一般要求; 删除了焊接援头分类内容,将其移至GBy/T18442的第1部分; -增加了材料复验的内容; 删除了冷成型的钢板加工变形率计算公式,改为直接引用GB/T150.4 -增加了冷弯成型的奥氏体不锈钢管子的铁素体测量值指标; 修改了缺陷修磨、补焊以及封头等制造技术要求 增加了内容器奥氏体不锈钢封头成型后的铁素体测量值的规定; -简化了A、B类焊接接头对口错边量、棱角以及壳体圆度的要求,改为直接引用GB/T150.4 -增加了罐体和支座的组装要求; 修改了圆简与罐体的焊接接头制造要求; 修改了焊接要求,对A,B类焊接接头的焊缝余高要求直接引用GB/T150.4 修改了产品焊接试件的制备要求; -增加了无损检测方法的选择和CR、,DR、TOFD等检测方法,完善了内容器和外壳的无损检测 技术要求,且增加了无损检测记录、资料和报告要求; 增加了热处理要求; -细化了清洁要求和组装要求 -增加了吸附剂的安装要求; 删除了管路制造中的管路焊接结构等设计要求,将其移至GB/T18442的第3部分 增加了外部管路的无损检测规定、耐压试验要求; 删除了安全附件安装要求,将其移至GB/T18442的第6部分 修改了标志与标识,出厂文件、封存和装运的要求
本部分由全国锅炉压力容器标准化技术委员会(SAC/TC262)提出并归口
本部分起草单位:张家港中集圣达因低温装备有限公司、上海市气体工业协会、南通中集能源装备 有限公司查特深冷工程系统常州)有限公司、特种设备检测研究院、江苏省特种设备安全监督检 验研究院张家港分院、苏州圣汇装备有限公司、荆门宏图特种飞行器制造有限公司、上海华谊集团装备 工程有限公司
GB/T18442.4一2019 本部分主要起草人;罗晓钟、周伟明、钱红华、膝俊华,陈来生、杨坤、陈朝晖,徐萌、张连伟、肖学文、 魏勇彪
本部分所代替标准的历次版本发布情况为 GB/T18442,4201l GB184422001
GB;/T18442.4一2019 固定式真空绝热深冷压力容器 第4部分;制造 范围 GB/T18442的本部分规定了固定式真空绝热深冷压力容器(以下简称深冷容器)制造中的材料复 验,加工成型、焊接、,无损检测、清洁、组装、标志标识、出厂资料等基本要求
本部分适用于同时满足以下条件的深冷容器 内容器工作压力不小于0.1MPa; b)几何容积不小于1m 绝热方式为真空粉末绝热、真空复合绝热或高真空多层绝热 c d)储存介质为标准沸点不低于一196的冷冻液化气体
本部分不适用于下列范围的深冷容器; 内容器和外壳材料为有色金属或非金属的; a 球形结构的" b 堆积绝热方式的; c d移动式的; 储存标准沸点低于一196C冷冻液化气体介质的, e 储存介质按GB12268规定为毒性气体的 f 国防军事装备等有特殊要求的 8 规范性引用文件 下列文件对于本文件的应用是必不可少的
凡是注日期的引用文件,仅注日期的版本适用于本文 件
凡是不注日期的引用文件,其最新版本(包括所有的修改单)适用于本文件
GB/T150-2011(所有部分)压力容器 GB/T1804一2000一般公差未注公差的线性和角度尺寸的公差 GB/T9969工业产品使用说明书总则 GB/T18442.1固定式真空绝热深冷压力容器第1部分;总则 GB/T18442.3固定式真空绝热深冷压力容器第3部分;设计 GB/T25198压力容器封头 JB/T4711压力容器涂敷与运输包装 JB/T6896 空 :气分离设备表面清洁度 NB/T47013.1承压设备无损检测第1部分;通用要求 NB/T47013.2承压设备无损检测第2部分;射线检测 NB/T47013.3承压设备无损检测第3部分;超声检测 NB/T47013.4 承压设备无损检测第4部分:磁粉检测 NB/T47013.5承压设备无损检测第5部分:渗透检测 NB/T47013.10承压设备无损检测第10部分;衍射时差法超声检测 NB/T47013.11承压设备无损检测第11部分:X射线数字成像检测
GB/T18442.4一2019 NB/T47013.14承压设备无损检测第14部分:X射线计算机辅助成像检测 NB/T47014承压设备焊接工艺评定 NB/T47016承压设备产品焊接试件的力学性能检验 NB/T47041塔式容器 NB/T47065.1容器支座第1部分:鞍式支座 NB/T47065.2容器支座第2部分;腿式支座 NB/T47065.4 容器支座第4部分:支承式支座 TsG21固定式压力容器安全技术监察规程 术语和定义 GB/T150,GB/T18442.1、GB/T18442.3界定的术语和定义适用于本文件
一般要求 深冷容器的制造应符合TsG21.GBT150.4.本部分以及经规定程序批准的设计文件的要求 4.1 4.2受压元件(封头、锻件等)以及安全附件、仪表、装卸附件等为外购、外协件时,深冷容器制造单位应 保证外购、外协件的质量满足设计文件及本部分的要求,且经检验合格后方可使用
4.3机械加工表面和非机械加工表面的线性尺寸的极限偏差,分别按GB/T18042000中的m级和e 级的要求
4.4深冷容器上的各连接管路、零部件和附件安装应牢固可靠,外表面应平整美观,无压伤、裂纹、焊渣 或漆层脱落等缺陷
阀门和仪表等应安装在便于操作或观察的位置 材料复验、分割与标志移植 5 5.1材料的复验应符合TsG21,GB/T150.4和设计文件的规定
5.2制造受压元件的材料应有可追溯的标志
在制造过程中,如原有标志被裁掉或材料分割时,制造 单位应在材料分割前完成标志移植
5.3材料分割可采用冷切割、热切割或其他适当的方法
当采用热切割方法分割材料时,应清除表面 熔渣和影响制造质量的表面层
5.4内容器受压元件不应采用硬印作为材料移植标记、焊工标记及其他标记
冷、热加工成型与组装 6.1成型 6.1.1筒体和封头可采用冷,热成型方法加工成所需形状
6.1.2奥氏体不锈钢简体和封头,采用冷加工成型后变形率超过GB/T150.4规定的控制指标时,应按 照相应的材料标准进行固溶处理
6.1.3与深冷介质接触的冷弯成型的奥氏体不锈钢管子,其成型后的铁素体测量值应不大于15%
6.1.4制造单位应根据制造工艺确定加工余量,受压元件成型后的厚度应不小于设计图样标注的最小 成型厚度
GB;/T18442.4一2019 6.2表面修磨 制造过程中应避免钢板表面的机械损伤
对于尖锐伤痕以及不锈钢表面的局部伤痕、刻槽等缺陷 应予以修磨,修磨的斜度最大为1:3
修磨的深度应不大于该部位钢材厚度的5%,且不大于2mm 否则应予补煤
6.3坡口 坡口表面质量应符合GB/T150.4的规定
6.4封头 6.4.1 封头应符合GB/T25198和设计图样的规定 6.4.2封头成型宜采用整体成型,并符合下列规定 先拼板后成型封头的拼接焊缝一般不超过3条,拼板的宽度应不小于300mm
拼接焊缝的 a 内表面以及影响成型质量的拼接焊缝的外表面,应在成型前打磨至与母材齐平
用带间隙的全尺寸的内样板检查封头内表面的形状偏差时(见图1),缩进尺寸为3%D 5%D,其最大形状偏差外凸应不大于1.25%D,内凹应不大于0,625%D
检查时应使样板 垂直于待测表面 内容器封头应采用适当的成型工艺,避免封头过渡段和直边段出现裂纹
当采用温成型工艺 时,应避开奥氏体型不锈钢的敏化温度区
d 内容器奥氏体不锈钢封头成型后其过渡段和直边段的铁素体测量值应不大于15%
封头直边部分应不存在纵向皱折
间欧样板 缩进尺视封头大小而定 间隙样板轮廓测量基准线 封头 图1凸形封头的形状偏差检查 6.5圆筒与罐体 6.5.1A,B类焊接接头对口错边量以及在焊接接头环向、轴向形成的棱角应符合GB/T150.4的规定
6.5.2不等厚钢材的B类焊接接头以及圆筒与球形封头相连的A类媒接接头的对接要求应符合 GB/T150.4的规定
6.5.3 因简直线度允差应符合GBT104的规定 6.5.4组装时,罐体上焊接接头的布置应满是下列要求 组装圆筒中,任何单个筒节的长度应不小于300mm,环向并板长度应不小于500 a mm; b 相邻简节A类接头间外圆弧长应大于钢材厚度的3倍,且不小于200" mm; 封头A类拼接接头、与封头相邻筒节的A类接头相互间的外圆弧长均应大于钢材厚度的3 倍,且不小于200mm;
GB/T18442.4一2019 d 不应采用十字焊缝,焊接接头宜避开开孔位置; 罐体上凡被补强圈,垫板等覆盖的焊缝,均应在覆盖前打磨至与母材齐平; e f 内容器附件和内容器间的焊接应尽量避开内容器上的A,B类焊接接头,且距离环焊缝边缘不 小于100mm;当与纵焊缝交叉时,应开槽避让 6.5.5内容器、外壳组焊完成后,应分别按GB/T150.4一2011中6.5.10和6.,5.l1的要求检查壳体的直 径和圆度
6.6其他组装要求 6.6.1罐体的主要几何尺寸、管口方位应符合设计图样的要求
6.6.2腿式支座的制造和装配要求按照NB/T47065.2的规定
6.6.3支承式支座的制造和装配要求按照NB/T47065.4的规定
6.6.4鞍式支座的制造和装配要求按照NB/T47065.1的规定 6.6.5裙座的制造和装配要求按照NB/T4704的规定
焊接 7.1焊前准备和施焊环境 焊前准备和施焊环境应符合GB/T150.4一2011中7.1的规定
7.2焊接工艺 7.2.1深冷容器应按NB/T47014进行焊接工艺评定且符合TsG21和GB/T150.4的规定
当焊接结构受压元件用境外牌号材料(含填充材料)时,制造单位在首次使用前应按NB/T47014进 7.2.2 行焊接工艺评定
7.2.3焊接工艺评定应包括焊缝和热影响区的低温夏比(V形缺口)冲击试验
冲击试验的取样方法 按NB/T47014的要求确定
冲击试验温度应不高于设计图样要求的试验温度
当焊缝两侧母材具有 不同冲击试验要求时,低温冲击吸收能量按两侧母材抗拉强度的较低者符合GB/T150.2或设计图样 的要求
接头的拉伸和弯曲性能按两侧母材中要求的较低者
7.2.4受压元件之间或受压元件与非受压元件组装时的定位煤,若保留成焊缝金属的一部分,应按受 压元件的焊缝要求施焊
7.2.5罐体的煤接应严格控制线能量
在焊接工艺评定所确认的范围内,宜选用较小的焊接线能量, 以多道施焊为宜 7.2.6内容器主要受压元件焊缝应在含焊缝布置图的焊接记录中记录焊工代号
焊接工艺评定技术档案应保存至该工艺评定失效为止,焊接工艺评定试样保存期不少于5年 7.2.7 7.3罐体焊缝表面的形状尺寸及外观要求 7.3.1焊缝表面的形状尺寸应符合下列规定 A,B类焊接接头的焊缝余高应符合GB/T150.4的规定
a b) c,D,E类接头的焊脚尺寸,在图样无规定时,取焊件中较薄者的厚度
当补强圈的厚度不小 于8mm时,其焊脚尺寸等于补强圈厚度的70%,且不小于8mm
7.3.2焊接接头表面质量应符合下列规定: 不应有表面裂纹、未焊透、未熔合,咬边,表面气孔,弧坑,未填满,夹渣和飞溅物等缺陷 a b 焊缝与母材应圆滑过渡,角焊缝的外形应凹形圃滑过渡; 按照疲劳分析设计的罐体,应去除A,B类焊缝的余高,使焊缝表面与母材表面平齐; c
GB;/T18442.4一2019 d)其他表面质量应符合设计图样的规定
7.3.3临时附件的焊接应符合下列规定 罐体上焊接的临时吊耳和拉筋的垫板等,应采用力学性能和焊接性能与罐体相同或相近的材 a 料,并用相适应的焊材及焊接工艺进行焊接
b 临时吊耳和拉筋的垫板割除后,留下的焊疤应打磨光滑,并按图样规定进行渗透检测或磁粉检 测,表面应无裂纹等缺陷
打磨后的厚度应不小于该部位的设计厚度或图样规定的最小成型 厚度
7.4焊接接头返修及母材缺陷补燥 7.4.1应分析缺陷产生的原因,提出相应的返修或补焊方案
7.4.2煤接接头的返修和补焊都应进行焊接工艺评定或具有经评定合格的焊接工艺支持,施煤时应有 详尽的返修或补焊记录
7.4.3焊缝同一部位的返修次数不宜超过2次
如超过2次,返修前应经制造单位技术负责人批准,且 应将返修的次数、部位和返修情况记人产品质量证明文件
7.4.4返修部位应按原要求经检测合格 7.4.5耐压试验后进行的返修,如返修深度大于1/2壁厚,应重新进行耐压试验
7.4.6氨质谱检漏后需返修的,返修部位应采用合适的检验方法检测合格,且重新进行氨质谱检漏
7.5产品焊接试件与试样 凡符合以下条件之一的、有A类纵向焊接接头的内容器,应逐台制备产品焊接试件 7.5.1 需经过热处理改善或恢复材料力学性能的内容器; a b)设计图样要求制备产品焊接试件的内容器
7.5.2制备产品焊接试件与试样应符合下列规定 产品焊接试件应在内容器简节A类纵向焊缝的延长部位与筒节同时施媒
a 试件应取合格的原材料,且与内容器用材料具有相同标准、相同牌号、相同厚度和相同热处理 b 状态
试件应由施焊内容器的焊工,采用与施焊内容器相同的条件、过程与焊接工艺施焊
有热处理 要求的内容器或部件,试件一般应随内容器或部件一起热处理
d 试件的尺寸和试样的截取应符合NB/T47016的规定
7.5.3试样的力学性能检验与评定应符合下列规定 力学性能检验的试验方法,合格指标及复验要求,应符合NB/T47016的规定; a b 夏比(V形缺口)冲击试验应包括焊缝金属和热影响区,试验温度为受压元件的设计温度或设 计图样规定的温度; 当产品焊接试样评定结果被判为不合格时,应分析原因,采取相应措施,允许按NB/T47016 的要求重新取样进行复验
当复验结果仍达不到要求时,则该试件所代表的产品应判为不 合格
无损检测 8 8.1无损检测方法 8.1.1无损检测方法包括射线检测、超声检测、磁粉检测和渗透检测
射线检测应符合NB/T47013.2、 NB/T47013.11或NB/T47013.14的规定;超声检测应符合NB/T47013.3或NB/T47013.10的规定 磁粉检测应符合NB/T47013.4的规定;渗透检测应按NB/T47013.5的规定
GB/T18442.4一2019 8.1.2制造单位或无损检测机构应按设计图样要求和NB/T47013.1的规定制定无损检测工艺
8.1.3无损检测方法的选择应满足相应的无损检测标准的规定
8.2无损检测方法的选择 8.2.1内容器及外壳的A,B类焊接接头内容器工艺人孔简体与凸面受压的工艺人孔封头的合拢B类 焊接接头和外壳的合拢B类焊接接头除外),管路对接接头,应进行射线检测或超声检测
超声检测包 括衍射时差法超声检测(TOFD),可记录的脉冲反射法超声检测和不可记录的脉冲反射法超声检测
8.2.2当采用不可记录的脉冲反射法超声检测时,应采用射线检测或衍射时差法超声检测作为附加局 部检测
8.2.3罐体的不锈钢焊接接头表面无损检测应采用渗透检测,碳钢或低合金钢焊接接头的表面无损检 测应采用磁粉检测或渗透检测
8.2.4铁磁性材料制罐体焊接接头的表面无损检测应优先采用磁粉检测
8.3内容器无损检测比例及技术要求 A.B类焊接接头应进行100%射线检测或超声检剥
8.3.1 8.3.2工艺人孔筒体与凸面受压的工艺人孔封头的合拢B类焊接接头无损检测的检测方法和要求应 符合设计图样的规定
8.3.3先拼板后成型的凸形封头上所有拼接接头还应进行100%表面检测
8.3.4内容器上D,E类焊接接头应进行100%表面检测
8.3.5内容器上临时吊耳和拉筋垫板割除并修磨后留下的焊疤,应进行表面检测 内容器无损检测的技术要求应符合下列规定 8.3.6 射线检测技术等级应不低于相应检测方法的AB级,其合格级别应不低于】级; a 脉冲反射法超声检测技术等级应不低于B级,合格级别应不低于I级 b 渗透检测合格级别应不低于I级
c 8.4外壳无损检测比例及技术要求 8.4.1A,B类焊接接头(外壳的合拢B类焊接接头除外)应进行局部射线检测,检测长度不小于各条焊 接接头长度的20%,且均不得小于250mm,其射线检测技术等级应不低于相应检测方法的AB级,合 格级别不低于皿级
8.4.2外壳的合拢B类焊接接头以及下列项目的焊缝应经无损检测,检测方法和要求应符合设计图样 的规定,其检测长度可计人外壳的局部检测长度 先拼板后成型凸形封头上的所有拼接接头; a 凡被补强圈、垫板、支座、,内件等覆盖的焊接接头; b) 对于满足GB/T150.3 中6.1.3不另行补强的管座,自开孔中心,沿外壳表面的长度等 -201l c 于1.5倍开孔直径的范围内的焊接接头
8.4.3先拼板后成型的凸形封头上所有拼接接头应进行100%射线检测及100%表面检测,其射线检测 技术等级应不低于AB级,合格级别应不低于I级,表面检测的合格级别应不低于I级
8.4.4外壳上临时吊耳和拉筋垫板割除并修磨后留下的焊疤,应进行表面检测,表面检测的合格级别 应不低于I级
8.5管路无损检测比例及技术要求 8.5.1真空夹层内及外部的管路,其B类焊接接头应按NB/T47013.2进行100%射线检测,射线检测 技术等级应不低于AB级,其合格级别应不低于级
GB;/T18442.4一2019 8.5.2真空夹层内及外部的管路,其C,D类焊接接头应按NB/T47013.5进行100%渗透检测,合格级 别应为I级
8.6重复检测 8.6.1经无损检测的焊接接头,发现不准许的缺陷时,应在缺陷清除干净后进行补焊,并对该部位采用 原无损检测方法和合格级别进行重新检测和评定
8.6.2进行局部无损检测的焊接接头,发现不准许的缺陷时,应在该缺陷两端的延伸部位增加检测长 度,增加的长度为该焊接接头长度的10%,且两侧均不小于250 若仍有不准许的缺陷,则对该条 mm
焊接接头进行100%无损检测
8.6.3渗透与磁粉检测发现不准许的缺陷时,应进行修磨及必要的补焊,并对该部位采用原无损检测 方法重新检测
8.7无损检测的实施时机 8.7.1焊接接头的无损检测,应在形状尺寸和外观质量检查合格后进行
8.7.2 拼接封头应在成型后进行无损检测
若成型前已进行无损检调,则成型后还应对圆狐过渡区至 直边段进行无损检测
8.8无损检测记录、资料和报告 制造单位应如实填写无损检测记录,正确签发无损检测报告,妥善保管射线底片和超声检测数据等 检测资料(含缺陷返修前记录),并建立无损检测档案,其保存期限应不少于深冷容器的设计使用年限 热处理 9.1罐体热处理要求应符合GB/T150.4和设计文件的规定 9.2除图样另有规定外,外壳冷成型后无需热处理
10 清洁要求 10.1与介质接触的所有零部件表面,应进行脱脂与清洁处理,合格指标应符合JB/T6896或设计图样 的规定
0.2真空夹层内表面以及夹层内的零部件,应进行脱脂、除锈、干燥等处理,合格指标应符合设计图样 的规定
10.3对不设置工艺人孔的内容器,在最后一道环焊缝对焊前,应清除容器内杂物,其清洁度满足设计 图样的要求
10.4清洁合格后,所有的零部件、管路和内容器的开口处都应立即用洁净的密封件密封好,防止污染 物,灰尘,水进人 11 组装要求 11.1内容器在耐压试验合格后方可与外壳进行组装,且应符合下列要求 高真空多层绝热的内容器应在绝热材料包扎完成后尽可能及时与外壳进行套装,以防止绝热 a 材料受潮及污染; b 套合时,应保证夹层的清洁,并防止损伤多层绝热材料、夹层管线和内容器的外表面
GB/T18442.4一2019 套合时,应尽可能减小内容器与外壳的同轴度偏差
c 11.2高真空多层绝热的绝热层应在内容器与外壳组装前完成安装,且应符合下列要求 多层绝热材料应经干燥处理 a b 层数、层密度应符合设计图样的规定; 反射屏与间隔材料之间应相互封闭; d 尽量避免出现反射屏之间直接接触(短路)及局部无反射屏的现象, e 最外层应有防止绝热层松散和脱落的相应措施
1.3真空粉末绝热材料的填充应在内容器与外壳组装完工后进行,且应符合下列要求 粉末绝热材料应经干燥处理; a 装填时,应控制粉末绝热材料的装填密度: b es 尽可能采取措施,防止粉末绝热材料沉降; 加压充填粉末绝热材料时,应有防止内容器失稳的相应措施 d 如需添加阻光剂,应保证其在粉末材料中分布均匀
e 12 吸附剂的安装" 12.1低温吸附剂应安装在内容器外壁,其包装和填充应符合设计图样的规定
12.2常温吸附剂应安装在外壳内壁,其包装和安置应符合设计图样的规定
13 管路制造 13.1管路安装前,管子,管件、阀门等管路组成件内外表面应清理干净,无杂物、油污且干燥
13.2真空夹层内的管路应进行耐压试验
13.3管路的法兰密封面及密封垫片,应无影响密封性能的划痕、斑点等缺陷
13.4法兰面应垂直于管路的主轴中心线,且保证法兰面的水平或垂直,其偏差均应不超过法兰外径的 1%(法兰外径小于100mm时按100mm计算)且不大于3.0mm
法兰的螺栓孔应与管路主轴线或铅 垂线跨中布置(见图2)
有特殊要求时,应在图样上注明
图2法兰的螺栓孔与管路主轴线或铅垂线跨中布置 3.5当管路装配间断施工时,应及时封闭敞开的管口
13.6阀门应按设计流程图确定其安装方向
螺杆式截止阀应在顺时针方向转动时被关闭
13.7管路上应清楚标明各个接口和附件的用途
管路阀门应标明介质流向,截止阀应标明开启和关 闭方向
GB;/T18442.4一2019 3.8安全阀、压力表应校验合格后才能安装使用
3.9管路宜采用管夹固定,管夹的固定不应限制管路的热胀冷缩
3.10有导静电接地要求的设备,各段管子间应导电
当每对法兰或螺纹接头间电阻值超过0.03Q 时,应设导线跨接
3.11外部管路应进行耐压试验和气密性试验
14氨质谱检漏 4.1内容器与外壳组装后,应对真空夹层进行氮质谱检漏
漏率指标应符合GB/T18442.3和设计图 样的规定
4.2泄漏处应按焊接返修工艺进行修补,按原无损检测要求检测合格后,重新进行氮质谱检漏
15罐体涂敷 罐体的涂散应符合B/Tt和设计文件的规定 16标志标识 16.1制造单位应在深冷容器的明显部位装设产品铭牌
铭牌应采用中文(必要时可以中英文对照)和 国际单位,铭牌的格式与内容应符合TsGi21的规定 6.2铭牌内容可采用压印、雕刻浮雕等永久方法进行标记,铭牌上的各种标志应清晰、易读
16.3铭牌可采用合适金属结构的防撬紧固件或焊接方法通过与垫板、支座或类似结构与容器永久 固定
6.4铭牌、支架及紧固件应采用与使用环境相适应的金属材料
16.5外壳上应设置管路流程示意图、液位对照表等标识,标识应字迹工整、清晰可见、牢固耐用
标识 不应出现折痕、皱纹、自卷撕裂等现象 6.6管路上应有标明阀门及管口用途的标识
17 出厂资料 7.1深冷容器的制造单位应向使用单位至少提供以下技术文件和资料 a 竣工图样,图样上应有设计单位设计专用章(复印章无效),并且加盖竣工图章(竣工图章上标 注制造单位名称、制造许可证编号,审核人的签字和“竣工图”字样),如果制造中发生了材料代 用,无损检测方法改变,加工尺寸变更等,制造单位应按照设计单位书面批准文件的要求在竣 工图样上作出清晰标注,标注处应有修改人的签字及修改日期 产品合格证(含产品数据表)和产品质量证明文件,包括电子文档的光盘或其他电子存储介质; b 特种设备制造监督检验证书 c 风险评估报告; d 强度计算书; e 应力分析报告(需要时; 罐体安全泄放量,安全阀排量、爆破片泄放面积,外壳防爆装置泄放面积的计算书 g h 安装及使用维护保养说明; 备件、附件清单和相应的质量合格证明
GB/T18442.4一2019 电气、仪表防爆合格证书(需要时
7.2产品质量证明文件至少应有下列内容 材料清单; a b 主要受压元件材料质量证明书; c 质量计划; 受压元件(封头、锻件等)为外购或外协件的产品质量证明文件; d 罐体外观及几何尺寸检验报告 焊接记录; 无损检测报告; g 热处理报告及自动记录曲线(需要时) h 耐压试验报告 气密性试验或其他泄漏试验报告; 产品铭牌的拓印件或复印件; 真空性能检测报告含封结真空度检测、真空夹层漏气速率检测、真空夹层漏放气速率检测) 静态蒸发率检测报告(需要时); m n 气体置换检验报告; 产品制造变更报告; O 安全附件、仪表及装卸附件的质量证明文件; p 其他必要的产品质量证明文件
a 17.3安装及使用维护保养说明除符合GB/T9969的规定外,还应有下列内容, 产品型号以及主要技术性能参数 a b 安全告知和产品使用说明 管路及阀门用途(应包括安全附件、仪表和装卸附件的型号和连接方式),流程示意图 c d 操作使用说明,至少应有操作规程,最大允许充装量的控制要求; 使用注意事项,至少应包括预冷过程和装卸过程中的注意事项 e fD 维护和保养要求; 常见故障的排除方法 8 h)起吊、装运和安装说明 8封存,装运 18.1封存 18.1.1深冷容器完工后,内容器及管路应使用干燥的氮气加压密封,密封压力一般为0.03MPa 0.05MPa,露点应不高于一25C 18.1.2充装易燃、易爆介质的深冷容器,内容器和管路的含氧量应不高于2%
8.1.3充装非易燃介质的深冷容器,内容器和管路的含氧量应不高于3%
18.1.4充装液氧介质的深冷容器,与氧接触的零部件应不存在与氧发生反应的物质 18.1.5所有管路、阀门和仪表的开口端,应进行防尘保护 18.1.6深冷容器在投人使用前如需长期封存,应放在防潮、通风的专用场地
18.1.7深冷容器封存期间,应按产品安装与使用维护说明书进行正常的维护与保养
18.2装运 18.2.1深冷容器应在空罐情况下交付用户
10
GB;/T18442.4一2019 18.2.2深冷容器可采用公路运输、铁路运输和水路运输等装运方式,吊装时应使用专用吊具 8.2.3装运过程中罐体应捆扎牢固可靠,外部管路及阀门、仪表等应包扎牢固,确保深冷容器各部位 得到有效保护
固定式真空绝热深冷压力容器第4部分:制造GB/T18442.4-2019
固定式真空绝热深冷压力容器是一种高端的容器设备,广泛应用于航空航天、国防科技、核能工业等领域。为推动该行业的发展和规范化,我国发布了一系列相关标准,其中GB/T18442.4-2019就是固定式真空绝热深冷压力容器制造方面的标准。 根据GB/T18442.4-2019标准,固定式真空绝热深冷压力容器的制造应当符合以下要求: 1.材料选择:容器的材料应当符合设计要求,并经过相应的检测和认证,以确保其质量和安全性。 2.制造工艺:在生产过程中应使用先进的加工技术和设备,严格按照标准规定的工艺流程来进行制造。 3.焊接要求:容器的连接部位应采用特殊的焊接技术,以确保其密封性和强度。焊接材料应该与容器本身材料相同或者具有相似的性能。 4.试验检测:在制造完成后,应进行各种试验和检测,包括强度试验、泄漏试验、真空试验等,以确保容器的安全可靠性。 5.质量控制:在生产过程中应严格按照标准规定的质量管理体系进行控制,确保产品的质量稳定和可靠性。 总之,GB/T18442.4-2019标准为固定式真空绝热深冷压力容器的制造提供了明确的指导和规范,有助于促进这一领域的技术创新和发展,提升我国在高端装备制造领域的竞争力。