GB/T28573-2012
石油、石化和天然气工业一般用途汽轮机
Petroleum,petrochemicalandnaturalgasindustriessteamturbines-General-purposeapplications
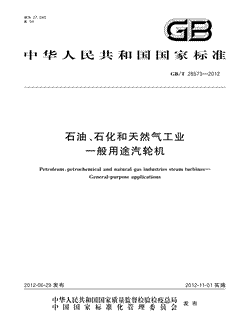
- 中国标准分类号(CCS)K54
- 国际标准分类号(ICS)27.040
- 实施日期2012-11-01
- 文件格式PDF
- 文本页数66页
- 文件大小1.39M
以图片形式预览石油、石化和天然气工业一般用途汽轮机
石油、石化和天然气工业一般用途汽轮机
国家标准 GB/T28573一2012 石油、石化和天然气工业 一般用途汽轮机 Petroleum,petrochemiealamdnaturalgasindustriessteamturbines General-purp0seapplieations 2012-06-29发布 2012-11-01实施 国家质量监督检验检疫总局 发布 国家标准化管理委员会国家标准
GB/I28573一2012 目 次 前言 引言 范围 规范性引用文件 术语和定义 主机设计 4.1总则 4.2承压缸体 4. 汽缸附件 4.4汽缸接口 4.5外力和外力矩 4.6转动部件 4.7密封件 4.8动力学 4.9轴承及轴承座 4.10润滑 .nm 15 材料 .12铭牌及转向箭头 辅助部件 5.1齿轮装置 5.2联轴器及护罩 5.3安装底板 18 26 . 控制设备和测量装置 2: 5.5管道及其附件 25 5.6专用工具 2: 5.7可拆卸式保温层 25 检验和试验 25 6.1总则 6.2检验 26 6.3试验 21 26 6.4装运准备 30 供方的资料 30 7.1总则 7.2报价书 30 31 7.3合同资料 33 附录A资料性附录本标准与APIStd61l:1997相比的结构变化情况
GB/T28573一2012 附录B资料性附录规范性引用文件中我国文件与国际文件之间的一致性程度 34 35 附录C资料性附录本标准与APIStd611:l997的技术性差异及原因 37 附录D(资料性附录 -般用途汽轮机数据表 附录E(规范性附录阻尼不平衡响应分析 E.1横向分析 4" E.2不平衡响应分析的工厂鉴定 附录F规范性附录确定剩余不平衡量的方法及作业表 F.1适用范围 F.2最大允许剩余不平衡量 45 剩余不平衡量检查 F.3 附录G(资料性附录)最简单的压力润滑油系统 56 附录H(资料性附录)检验员用的检验表 52 附录I资料性附录)供方图样和资料要求 53 I.1供方图样和资料要求示例 53 1.2说明 56 6 参考文献 图1转子响应曲线 图E.1典型振型图 42 图F.1剩余不平衡量作业表 46 图F.2剩余不平衡量计算实例 48 图G.!最简单的压力润滑油系统(有可选择的增加内容 5 表1冷却水系统参数 表2算术平均粗糙度(Ra) 表》调速器 20 表4供参考的管道材料 214 表5铸件缺陷严重程度表 26 表A.1本标准与APStd611:1997章条编号对照 33 表B.1规范性引用文件中我国文件与国际文件之间的一致性程度 34 表C.1本标准与APIStd611;1997的技术性差异及原因 35 表H.1检验员用的检验表 52
GB/I28573一2012 前 言 GB/T28574《石油、石化和天然气工业特种用途汽轮机》和GB/T28573《石油,石化和天然气工 业 -般用途汽轮机共同构成石油、石化和天然气工业用汽轮机产品标准
本标准按GB/T1.1一2009给出的规则起草
本标准使用重新起草法修改采用APIStd61l:1997《石油、化工和天然气工业一般用途汽轮机》
本标准与APIStd61l:1997相比在结构上有较多调整,附录A中列出了本标准与APIStd61l 1997的章条编号对照一览表
本标准与APIStd61l:1997的技术性差异如下 -关于规范性引用文件,本标准做了适当调整,以适应我国的技术条件,调整的情况集中反映在 第2章“规范性引用文件”中,我国文件与国际文件之间的一致性程度见附录B
具体调整 如下: 用GB/T8117(所有部分)代替IEC60953(所有部分); 用GB/T17241(所有部分)代替Iso7005-2 -除规范性引用文件外的涉及技术性差异的条款已通过在其外侧页边空白处用垂直单线()进 行了标示
附录C中给出了相应技术性差异及其原因的一览表
本标准还作了下列编辑性修改: 为与系列标准一致,并符合GB/T1.1的编写规定,将标准名称由《石油、化工和天然气工业一 般用途汽轮机)改为《石油、石化和天然气工业一般用途汽轮机》,英文名称由“General-Pur poseSteamTurbinesforPetroleum,chemicalandGasIndustryServices”改为“Petroleum., petrochemicalandnaturalgasindustriessteamturbinesGeneral-purposeapplications”; -将第1章的“适用范围”改为“范围”,对1.1的“用途”、1.2的“变通设计”和1.3的“相抵触的 规定”根据我国标准的编写格式,更改了条款编号(见章条编号对照表); 将1.1.1关于一般用途汽轮机的表述,改为“术语和定义”中的3.1,特种用途汽轮机的表述 见 GB/T28574一2012(石油、石化和天然气工业特种用途汽轮机》中的3.41 由于GB/T28573一2012和GB/T285742012是系列标准,为了表述统一,相同的术语和定 义在GB/T28574一2012规定,本标准中不重复 修正了原文中一些错误(见脚注2一脚注7): 删除标准中的“美国惯用单位”数据、公式及表格
将质量的符号由“w”改为“m”,将转速的符 号由“N”改为“n”; 所有英制单位均转化为公制单位; 依据附录"除非另外注明,所有压力均为表压”的说法,删除正文及附录中表示表压的(g); 根据GB/T1.1一2009的规定,对原附录顺序进行重新编排
本标准由电器工业协会提出
本标准由全国汽轮机标准化技术委员会(SAC/TC172)归口
本标准负责起草单位;杭州汽轮机股份有限公司
本标准参加起草单位;上海发电设备成套设计研究院
本标准主要起草人;宋思远,张琦、毛汉忠,张国强、廖小林,叶奋、刘晨 m
GB/T28573一2012 引 言 条编号后或段前标有黑点()的,表示该条或段的内容由需方决定或由需方提供进一步的信息
宜在数据表上标出这些信息和决定(见附录D),否则,宜在询价单或定购单中说明
GB/T28573一2012 石油、石化和天然气工业 一般用途汽轮机 范围 本标准规定了一般用途汽轮机设计、材料,安装、检验,试验和装运准备方面的要求
本标准还涉及 到润滑油系统、仪器仪表、控制系统和辅助设备
本标准适用于石油、石化和天然气工业一般用途汽轮机
本标准不适用于石油、石化和天然气工业特种用途汽轮机,特种用途汽轮机采用GB/T28574
注1:供方可以提出变通设计
经过供需双方同意,等值的紧固件和法兰可以替换 注2;当本标准与询价单或i订单之间出现抵触时,以订单包含的内容为准 规范性引用文件 下列文件对于本文件的应用是必不可少的
凡是注日期的引用文件,仅注日期的版本适用于本文 件
凡是不注日期的引用文件,其最新版本(包括所有的修改单)适用于本文件
GB/T152.4紧固件六角头螺栓和六角螺母用沉孔 GB/T195平健键槽的剖面尺寸 GB/T1800.1产品儿何技术规范(GPS)极限与配合第1部分:公差、偏差和配合的基础 (GB/T1800.1一2009,IS0286-1:1988,MOD) GB/T1800.2产品几何技术规范(GPs)极限与配合第2部分;标准公差等级和孔、轴极限偏 差表(GB/T1800.22009,ISO286-2:l988,MOD GB/T3098.1 紧固件机械性能螺栓、螺钉和螺柱GB/T3098.l2010,ISO898-l:2009, MOD) GB/T3852联轴器轴孔和联结型式与尺寸 GB/T4604滚动轴承径向游隙(GB/T4604一2006,Is(5753:l991,MOD GB/T6391滚动轴承额定动载荷和额定寿命(GB/T6391一2010,IsO281;2007,IDT) GB/T730755"非密封管螺纹(GB/T7307一20o1,eqIso228-1;1994) GB/T8117(所有部分汽轮机热力性能验收试验规程[GB/T8117一2008,IEC60953:1990(所 有部分),IDT] GB/T8923.1涂覆涂料前钢材表面处理表面清洁度的目视评定第1部分;未涂覆过的钢材 表面和全面清除原有涂层后的钢材表面的锈蚀等级和处理等级 钢制管法兰 GB/T91129124 GB/T9144普通螺纹优选系列(GB/T9144一2003,IsO262;1998,MOD) GB/T9239.1机械振动恒态刚性)转子平衡品质要求第1部分;规范与平衡允差的检验 (GB/T9239.1一2006,ISO1940-1:2003,IDT) GB/T10121钢材塔形发纹磁粉检验方法 GB/T1271660"密封管螺纹 GB/T13807.3腰状杆螺柱连接副螺母,受力套管
GB/T28573一2012 GB/T14383锻制承插焊和螺纹管件 GB/T17241(所有部分铸铁管法兰(IsO7005-2 GB/T20410涡轮机高温螺栓用钢 GB/T28574石油、石化和天然气工业特种用途汽轮机(GB/T28574一2012,ISO10437;2005. MOD) DL/T678电站钢结构焊接通用技术条件 JB/T1581汽轮机、汽轮发电机转子和主轴锻件超声波探伤方法 JB/T4365专用的润滑、轴密封和控制油系统 JB/T4730.2承压设备无损检测第2部分;射线检测 JB/T7927阀门铸钢件外观质量要求 JB/T8557挠性联轴器平衡分类 JB/T9559工业汽轮机用挠性联轴器 JB/T9631汽轮机铸铁件技术条件 炼油厂压力泄放装置的尺寸确定,选择和安装的推荐作法 SY/Tl0044 ANSI/AGMA9002-B柔性稠合器的孔径和键槽英制系列[Boresandkeywaysforflexible inchseries)力 uplings cOup ANNSI/ASMEB31.3工艺管道(P'roeessP'iping APIStd526钢质法兰端泄压阀(Flangedsteelpressurereliefvalves) APIstd670机械保护装置(Machineryprotectionsystems) APIStd677石油、石化和天然气工业用一般用途齿轮装置(General一Purposegearunitsforpe- troleum,chemicalandgasindustryservices) ASME锅炉和压力容器规范,第V卷 无损检测Boilerandpressurevesselcode,Section Nondestructiveexamination ASME锅炉和压力容器规范,第卷第1部分;压力容器建造规则(Boilerandpressurevessel code,Section一Division1,Pressurevessels) AsME锅炉和压力容器规范,第卷焊接和钉焊评定(EBoilerandpressurevesselcode,Sectionm X -weldingandbrazingqualifieations) andlar s,NPS1 AsMEB16.5管法兰和法兰管件NPs1/2NPS24(Pipelanges edftm angec throughNPS24 ASMEB16.42球墨铸铁管法兰和法兰管件额定级号150和300(Ductileironpipelangesand flangedfittings,Classes150and300 nancetestcode6onsteamturbines) ASMEPTC6汽轮机性能验收试验规程6(Perorm ASTMA278/A278M温度达到650下(350C)的承压灰铸铁件的标准规范[St Standard specif eationforgrayironcastingsforpressure-containingpartsfortemperaturesupto650degreesF35o DegreesC)] AsTMA320/A320M低温用合金钢栓接材料的标准规范(Standardspecificationforaloy-steel forlow-temperatureservice andstainleSS steelboltnmaterial AsTMA395/A395M高温承压件用铁素体球墨铸铁件的标准规范(Standardspecificationfor ferriticductileironpressure-retainingcastingsforuseatelevatedtermperatures) AsTMA515/A515M中温和高温压力容器用碳素钢板标准规范(Standardspeeifceationfor pressurevesselplates,carbonsteel,forintermediate-andhigher-temperatureservice ASTMA536球墨铸铁件标准规范(Standardspec ifieationforduetileironcastings)
GB/T28573一2012 ASTME125铁素体铸件磁粉显示的参照照片集(Standardreferencephotographsformagnetie particleindicationsonferrouscastings) NEMAMG1电动机和发电机(Motorsandgenerators) bteamturbinesformechanicaldriveservice) NEMASM23机械驱动用汽轮机(St NFPA70国家电气法规(Nationalelectricalcode) ssPcsP6工业喷砂清理(Commereialblasteleaning 注1:上述所列出的引用标准
在询价后,如果要改变引用标准、法规和技术规范的适用范围,须经供需双方同意
注2:为遵守任何适用于设备的政府法规、法令、条例或法律,供需双方应共同确定必须采取的措施
洼3供方有责任对每个分供方转发全部可适用的技术规范
术语和定义 GB/T28574界定的以及下列术语和定义适用于本文件
3.1 -般用途汽轮机generahpur p0seturbines EN -般用途汽轮机为卧式或立式汽轮机,用于驱动通常作为备用的、尺寸(功率)相对较小的设备或非 关键设备
一般用途汽轮机适用于进汽表压不超过4.8MPa,进汽温度不超过400C和转速不超 过6000r/min
3.2 循环油系统eireulatingoilsystem 从轴承座里抽出油,并在油返回到轴承座前,在一个外部冷油器中进行冷却 3.3 NEMA进汽和排汽条件NEMIAinletandexhaustconditons 等同于数据表上规定的最高进汽和排汽条件
正常条件normal 设备正常运行时适用的功率、转速和蒸汽条件
这些条件是达到最高效率的要求
3.5 油雾润滑oilmistlubrieation 由中央供油装置雾化产生油雾并通过压缩空气把油雾输送到轴承座进行润滑的润滑油系统
3.6 纯油雾润滑(干润滑油槽pureolmistlubrieation(drysump 油雾既润滑轴承又吹洗了轴承座
气吹油雾润滑(湿润滑油槽purgeoilmistlubricationwetsummp 油雾只用来吹洗轴承座
轴承润滑通过常规的油道、抛油环或油环进行
3.8 额定量rated 规定的汽轮机最大功率及相应的转速,包括被驱动设备技术规范要求的全部裕量
GB/T28573一2012 3.g 全跳动量totalindiceatedlrunout TIR 用千分表量得的直径或表面的跳动量,也称作总跳动量
显示读数表示不垂直度或等于读数一半 的偏心率
主机设计 总则 4.1.1按本标准设计和制造的设备(包括辅机),应至少有20年的使用寿命,并且至少能连续运行 三年
这是一个公认的设计准则
4.1.2供方应对所有设备及订单范围包括的辅助系统负责
4.1.3应在数据表中规定设备的正常运行点
4.1.4汽轮机应具备下列能力: 在正常蒸汽条件下,以正常功率和转速运行,制造厂的保证汽耗应在这些工况范围内
a 当数据表上规定的最小进汽和最大排汽参数同时出现时,应能以相应的转速发出额定功率
b 为防止机组尺寸过大,或为获得较高的运行效率,需方可以要求用规定标准值的方法或一个选 定的、替代额定功率的额定功率百分比,来限制汽轮机的最大容量
注1,在正常蒸汽条件下,通过使用一个或多个手动阀可以获得额定功率,在最低进汽和最高排汽燕汽条件 下,使用一个或多个附加手动阀也可以获得额定功率
其他运行条件下使用手动阀的情况,见5.4.1.5 的内容
以最高连续转速和任何规定范围内的转速连续运行
c 在最高进汽参数和最高及最低排汽参数下,以额定功率和额定转速连续运行
d 偏离额定蒸汽条件的运行应符合NEMAsM23的规定
注2:在未向制造厂咨询的情况下,无论汽轮机零部件的设计限值是多少,如果超出铭牌限制值,就不宜起动 汽轮机或重新确定限值
4.1.5设备的设计应确保其运行至跳闸转速和减压阀设定值时不损坏
41.6单级汽轮机不需要预暖机,就可立即起动至满负荷
需方应为进汽管道汽缸、蒸汽室和汽封装 置考虑恰当的疏水
注当单级汽轮机用于无人自动快速起动时,可能需要附加条件,因此建议就此向制造厂咨询
4.1.7单级和多级机组用的汽轮机叶轮或多个叶轮应置于轴承之间
采用其他布置形式需要得到需 方同意 4.1.8油箱和内部安装了润滑运动部件的(如轴承,轴封、高精度抛光零件、仪表和控制元件)密封壳 体,在运行和停机期间,应能最大限度减少潮气、灰尘和其他外来杂物所产生的污染
4.1.9所有设备应按能进行快速而经济的维修进行设计
主要部件如汽缸组件和轴承座应采用台肩 式或圆柱暗销连接的方法设计和制造,以确保重装时能精确对中 4.1.10订单范围内的汽轮机及其他设备应在试验台上进行试验,并按规定的验收准则在固定基础上 运行
安装后,各种设备组合起来的机组性能应由供需双方共同负责 4.1.11除非另有规定,冷却水系统按4.1.11.1和4.1.11.2的规定设计
4.1.11.1一个或多个冷却水系统按表1设计
系统应配置完全排放和疏水用的相关接口
GB/T28573一2012 表1冷却水系统参数 指 标 S单位 热交换器表面速率 1.5m/s一2.5m/s 最高允许工作压力 690kPa >1.04MPa 试验压力 最大压降 100kPa 最高进口温度 30 最高出口温度 50C 20 最大温升 最小温升 10C 水侧污垢系数 0.35m'K/kW 壳体腐蚀允许余量 3.0mm 注:如果最小温升规定同热交换器表面速率的标准相抵触,则供方应通知需方
热交换器表面速率准则意味着 最大限度地减少水侧结垢;最小温升准则意味着最大限度地减少冷却水量
需方应批准最终选择
为避免凝结,轴承座的最低进水温度宜高于环境空气温度
4.1.12 供需双方应共同保证控制全部所供设备的噪声水平
供方提供的设备应符合需方规定的最 大允许噪声限值 4.1.13 电机,电气组件和电气安装应适合需方在数据表中规定的场所类别(类别,级别和组别),并 应符合NFPA70第500,501,502和504节的规定,以及需方提供和规定的当地法规 4.1.14 需方应指明装置是安装在室内(受热或不受热),还是安装在室外(是否有顶棚),并规定保证 设备运行的环境和气候条件(包括最高和最低温度、异常的湿度和灰尘或腐蚀)
4.1.15设备布置,包括管道和辅助设备应由供需双方共同商定
布置时应为操作和维修提供足够的 空间和安全通道
4.1.16机器和全部所供辅机的备品备件均应符合本标准的所有规定
4.2承压缸体 4.2.1在规定的燕汽工况范围内,当压力和温度同时达到最恶劣情况时,所有承压件均能安全运行
4.2. 汽缸设计采用的圆周应力值在材料的最高工作温度下,不应超过ASME规范第卷第1册规 2 定的最大许用拉伸应力值
4.2.3轴向中分的汽缸应采用螺栓紧密连接的金属对金属的结合方式(使用合适的密封膏)
轴向结 合处不应使用垫片(包括缠绕式垫片
当径向中分的汽缸采用衬垫圈的连接方法时,应限制垫圈移动, 以确保连接安全
4.2.4轴向中分卧式汽轮机,应设计成在不从基础上移动汽缸或不拆卸进汽、排汽管道(规定上排汽的 除外)情况下,可以检查和替换转子及磨损的部件
轴向中分的多级汽轮机汽缸可在高压和低压区段之 间采用径向中分方式
4.2.5径向中分卧式汽轮机,应设计成在不从基础上移动汽缸或不拆卸进汽,排汽管道情况下,可检查 和更换轴承及外汽封
注,可要求在基础上移动径向中分卧式汽轮机,以便拆卸转子 4.2.6汽缸和座架应具有足够的强度和刚度,可把联轴器法兰处(许可应力、管道力和扭矩所导致的最
GB/T28573一2012 恶劣的综合作用)的轴对中变化限制在504nm以内
座架和对中螺栓应具备足够的刚度,以便通过使 用横向和轴向顶起螺钉来移动机器
轴向中分的卧式汽轮机应具有中心支架,以保持与相连接设备的 良好对中
汽轮机座架的下水平安装面机加工平行度在0.17mm/m(1;6000)以内
对应表面应在 表面间距离为0.17mm/m内共面
4.2.7蒸汽室、汽缸、汽封装置和冷却套管应设置疏水接口
对于凝汽式汽轮机,如果排汽接管或管道有取向要求,或如果需方有规定,则供方应随机提供- 个自动疏水系统
4.2.8单阀汽轮机的蒸汽室和多级汽轮机的第一级应设置仪表接口
4.2.9应提供拆卸和重装用的顶起螺钉、导柱(用于多级汽轮机)和汽缸对中暗销
如果顶起螺钉用于 分开结合表面,则该结合表面应局部下陷(加工成沉孔或凹槽),以防止擦伤表面而引起结合面出现缝隙 或贴合不良
导柱应有足够的长度,以防拆卸和重装汽缸时碰坏内部零件或汽缸螺栓
起吊搭子和吊 环螺栓只能用于起吊上半汽缸
装配完毕后,机组的起吊方法由供方规定
4.2.10承压部件应尽可能减少使用螺纹孔
为防止汽缸承压区段出现泄漏,钻孔和攻孔的底部及周 围,除了留有允许的腐蚀余量外,还应留出至少等于螺栓直径一半的金属厚度
螺纹孔深度至少是双头 螺柱直径的1.5倍
4.2. 11 按4.2.l1.14.2.11.5的规定提供螺栓
4.2.11.1螺纹应符合GB/T9144规定
4.2.11.2与螺栓相比,优先使用双头螺柱
4.2.11.3螺柱连接件应将装配好的双头螺柱、螺母一起提供
盲螺孔的钻孔深度以螺纹部分达到主 螺栓外径的1.5倍为限;每个螺柱应从两端倒角1.5个螺牙
4.2.11.4未经需方同意,不应使用带槽螺母或扳手式螺栓 4.2.11.5螺栓四周应留出合适的空间,便于使用套筒扳手或梅花扳手
4.2.12安装表面的加工粗糙度为3.24m一6.34m的算术平均粗糙度(Ra)
压紧螺栓或地脚螺栓 孔应垂直于一个或多个安装表面,并且惚孔直径按GB/T152.4的规定
4.2.13
如有规定,设备底座应设置垂直顶起螺钉
为最终销接定位,设备底脚应钻若干定位孔
4.2.14 4.3汽缸附件 所有的喷嘴或喷嘴组均可更换
所有其他的静叶均应安装在可更换的隔板或弓形块上
4.4汽缸接口
进、排汽接口为法兰连接或经机械加工并用双头螺柱连接接口,接口取向按数据表的规定,并 4.4.1 与GB/T28574中3.20和3.21规定的最大进汽和排汽条件相适应
4 焊接到汽缸上的接口应符合汽缸的材料要求,包括冲击值,而不是符合连接管道的要求
汽缸 进行水压试验前,应完成所有接口的焊接
管道连接用的汽缸开口直径至少为DN20,并采用法兰连接或机械加工后用双头螺柱连接
无 4 法采用法兰连接或机械加工后用双头螺柱连接的地方,允许采用DN20~DN40的螺纹开口
这些螺纹 开口按下面4.4.3.14.4.3.7的规定进行安装
接管的螺纹长度最好不大于150mm,并应拧人螺纹开口
44.3.2小于或等于DN25的接管(壁厚)最小应为seh'160无缝钢管,大于或等于DN40的接管(壁 厚)最小应为Sch80无缝钢管 1 管壁厚度号(schedulenumber)的缩写,为订货简便增加的一种代号
GB/T28573一2012 4.4.3.3蒸汽压力等于或大于1.2MPa的,接管应配备带颈对焊法兰或承插焊法兰 4.4.3.4螺纹接口应密封媒接;但铸铁设备、仪表接口或维修时要拆卸的接口不允许采用密封焊接
密封焊接焊缝应符合ASMEB31.3规定
4.4.3.5锥螺纹的螺孔和凸台应符合AsMEB16.5规定
4.4.3.6管螺纹应为符合GB/T12716要求的锥管螺纹
44.3.7插焊接口的开口应符合GB/T14383规定 不应使用公称尺寸为DN32、DN65、DN90、DN125、DN175和DN225的开口
,不连接管子的螺纹开口,应使用符合GB/T14383要求的实心圆头钢质螺塞堵 4.4.5除非另有规定, 住
螺塞至少应符合汽缸材料要求
可拆卸的螺塞应使用抗腐蚀材料
所有的螺纹接口均使用符合温 度要求的润滑剂
油通道用的螺塞不应使用胶带
不允许使用塑料螺塞
4.4.6法兰除了要符合下列4.4.6.14.4.6.5的规定外,还应符合GB/T17241或GB/T9112~ 9124或ASMEB16.42规定
4.4.6.1铸铁法兰应为平面法兰,公称尺寸小于或等于DN200时,应有一个符合GB/T17241规定的 最小PN50厚度
4.4.6.2所有排汽接口均允许使用平面法兰
平面法兰应有一定的凸起厚度
4. .4.6.3如果合适,容许采用比GB/T17241,GB/T9112一9124或ASMEB16,42规定更厚或外径更 大的法兰
4.4.6.4所有缸体法兰的螺栓孔节圆应与法兰同心,机加工过的垫圈座足以容纳完整的标准垫圈,使 垫圈不会伸人流道
4.4.6.5
为了制造匹配零件的需要,如果接口大于GB/T91129124或ASMEB16,42所包括的接 口时,则供方应向需方提供设备法兰详图
如有规定,匹配零件由供方提供
4.4.7法兰和接管的接触面粗糙度应符合表2规定的粗糙度要求
经需方同意,可以使用饥制法 兰面 表2算术平均粗糙度(Ra) 接触面粗糙度Ra 类 型 使用条件 m 真空 1.6一3.2 平面和突面 高于大气 3.212.5 <1.6 环状连接面 任何条件 4.4.8为便于不移动机器进行拆卸,需方的所有接口应易于接近
为加强刚性,立式汽轮机的装配法兰应为铸铁件或钢制件,并具有充分的螺栓连接和加强肋 4.4.9 条
按照规定,装配法兰应采用椎接结构或采用符合NEMAMG1或其他规定的,具正确对中结构的 平面法兰和暗销接合
4.5外力和外力矩 汽轮机的设计应能承受按NEMASM23计算的外力和外力矩
4.6转动部件 4.6.1转子 4.6.1.1转子应能无损坏地瞬时达到110%的跳闸转速
GB/T28573一2012 4.6.1.2装配完毕的转子(整锻转子除外),在任何规定的起动或运行工况下,以及一直到110%跳闸 转速范围内的任何转速情况下,均能防止轮盘相对轴产生窜动
叶轮用加热套装的方法安装到轴上并 用键固定
当叶顶速度在最大连续转速下超过250m/s,或当级进汽温度超过440C时,如果采用组合式转 子,则需要得到需方的特别许可
4.6.2主轴 4.6.2.1整个轴均应精加工,并且联轴器、轴承和碳环密封区粗糙度为Ra0.8wm或更好
当提供非接触振动探头和/或轴向位移探头,或者规定它们的结构时,径向振动探头监视的转 4.6.2.2 子主轴传感区应与轴承轴颈同心
对探头每侧的探头顶部最小直径范围来说,主轴的全部传感区(径向 振动和轴向位移)应不存在图案和划线痕迹或任何其他如油孔、键槽那样的不连续表面
这些部位不应 喷镀,加轴套或电镀
这些部位最后加工完成的表面粗糙度最大为Ra a0.8Am,最好采用璀磨或抛光的 方法
这些部位应严格退磁到AP1 Std670 规定的水平,或用其他方法进行处理,以使综合的总电气和 机械跳动量不超过最大允许的峰 峰振幅值的25%或不超过下列值,取两者中的较大值: a)径向振动探头所监测的区域为6.3umm.
-旦规定了振动探头条款,就应对轴进行抛光 b) 轴向位移探头所监测的区域为12.7Am.
4.6.2.3汽缸端部汽封采用碳环密封保护轴的,其材料应是抗腐蚀材料
数据表应说明制造厂所用的 方法、涂覆材料和最终涂层厚度
4.6.2.4键槽的圆角半径应符合GB/T1095的规定
4.6.3叶片 4.6.3.1动叶片在设备的任何运行工况范围内所产生的综合应力(稳态加循环)应足够低,以便即使出 现共振,也能确保安全运行
4.6.3.2全部叶片能在整个规定的转速范围内(包括瞬时工况)运行,并在瞬时达到110%跳闸转速时 也能运行
4.7密封件 4.7.1主轴的外汽封采用碳环或可更换的迷宫式汽封,或这两种组合的,或其他非接触式机械密封
4.7.2轴封表面的摩擦速度低于50m/s时才能使用碳环密封
在每个有效密封环最大允许平均压差 240kPa的情况下,根据运行工况和排汽要求来确定碳环数量
碳环密封用弹簧应采用镍铬一铁合金 冷卷后热处理)或相当材料制作
确定密封环的冷态间隙时要考虑运行中的蒸汽温度变化情况 另提供一套完整的带汽封体的碳环 4.7.3 4.7.4 如有规定,应提供一台独立的、与汽封连接的真空装置,以减少蒸汽泄漏
除非另有规定,否 则应由负责汽轮机安装底板的供方安装并连接真空装置
4.7.5
低于大气压工作的汽封,按引人蒸汽以封阻空气来设计结构
应提供与端部迷宫式汽封相互 连接的,带压力表、调节器和其他必需阀门的管道
管道应设置一个与需方密封燕汽源相连的公共接 口
当有规定时,在整个负荷范围内,能自动调节密封蒸汽的进汽
正常运行时的密封蒸汽供汽最好引 自汽轮机的正压区段
4.7.6轴封及真空系统的所有管道和部件按计算的新间隙泄漏量的300%确定尺寸
4.7.7多级汽轮机的级间隔板密封采用可更换的迷宫式汽封
4.7.8汽封体泄漏接口应符合4.4.3的规定
GB/T28573一2012 4.8动力学 4.8.1 临界转速 4.8.1.1当作用到一个转子一轴承支承系统的周期强迫力频率激振频率)与该系统的固有频率相一 致时,系统可能会处于共振状态
4.8.1.2处在共振状态的转子一轴承支承系统显示的是被放大的正常振幅值
放大值和相位角变化 率与系统的总阻尼值和转子振型有关 注;振型通常是指一阶刚性振型(平移型或跳动型),二阶刚性振型(锥型或摆动型)和(一阶、二阶、三阶n阶)弯 曲振型
如果径向振动探头测出转子放大系数AF(见图1)大于或等于2.5,则对应颗率称为临界转 4.8.1.3 速,对应的转子旋转频率也称为临界转速
对本标准来说,极限阻尼系统是一个放大系数小于2.5的阻 尼系统
运行转迷 CE C让 0.707峰值 川. /min 图中 转子一阶临界,中心频率,周波每分; ne 临界转速,n次阶 Ham 最高连续转速,105% n -0.707×振幅峰值处的初始(较低)转速(临界)1 H -0.707×振幅峰值处的最终(较高)转速(临界); 半功率点处的蜂宽; n AF -放大系数:AF=n/n一n). SM -避开裕量; 临界响应区 CRE -n.处的振幅 A -n.处的振幅 Am 图1转子响应曲线 4.8.1.4一个激振频率可以小于,等于或大于转子转速
系统设计时考虑到的潜在激振频率包括但不 限于下列情况 转子系统的不平衡; a b油膜振荡; 内摩擦; c d动叶,静叶,喷嘴和扩散器的通道频率; 齿轮啮合和边频带; e
GB/T28573一2012 f 联轴器不对中; g转子系统部件松动 滞后和摩擦涡动 h 边界层流动分离 i 声音和空气动力的交叉耦合力; k异步涡动, 耐磨轴承的滚珠和轴承套频率
结构支承系统的共振可能对转子振幅产生不利影响
因此,供方供货范围内的结构支承系统 4.8.1.5 在规定的转速范围或避开裕量(见附录E的E.1.4)内不应出现影响转子振幅的共振,除非共振已被大 大衰减
4.8.1.6规定对机组负有责任的供方应确定驱动轴系(汽轮机、齿轮装置、电动机和类似的机械设备 的临界转速不会激起所供机械设备的任何临界转速,并且整个轴系适合于规定的运行转速范围,包括轴 系的任何起动转速停止(保持点)要求
应提交一份从零转速到跳闸转速的所有应避开的运行转速列 表,供需方审查,并将它们列人使用手册(见7.3.6)
如有规定,汽轮机供方应把所有必须的横向和扭转振动分析数据提供给对整个机组负有责 4.8.1.7 任的供方
4.8.1.8单级汽轮机的一阶刚性振型至少是最高连续转速的120%
4.8.2横向振动分析 4.8.2.1供方需证明分析推导出的标准临界转速值以及过去制造的相同尺寸,相同转子/轴承结构的 汽轮机试验是合格的,并且应把这些数据作为报价书的一部分提交给需方
对新的汽轮机设计和转子 轴承结构,供方应按附录E提出的准则进行横向临界分析
如有规定,供方应按4.8.1.8和E.1.4的规定提供用于避开裕量的计算结果和/或有效的 4.8.2.2 支承试验数据
4.8.3扭振分析 4.8.3.1在分析中,应考虑到很多因素均可能激发无阻尼扭转固有频率,这些因素包括但不限于下列 情况: a)诸如不平衡和节圆线跳动这样的齿轮问题, b)诸如转速滞留和其他扭转振荡之类的起动工况; 液压调速器控制回路共振; e) d 运行转速 4.8.3.2对机组负有责任的供方应保证整个轴系的无阻尼扭转固有频率至少比规定运行转速范围内 从最低转速到最高连续转速)的任何潜在激振频率高10%或低10%
4.8.3.3最好避免比运行转速大两倍或更多倍数的扭转临界转速,或者证明系统中出现相应激振频率 不会产生有害影响
如果合适并且证明无害,则除了运行转速的倍数外,扭转分析还应考虑与转速无关 的或本质上为非同步的扭转激振频率
鉴别这些频率是供需双方的共同责任
4.8.3.4当所计算的扭转共振值在4.8.3.2规定的范围,供需双方一致认为已尽力了,但也无法从限 定的频率范围内移开临界值,则应进行应力分析,来确定共振对整个轴系不存在不利影响
该分析的验 收准则应经供需双方同意
如有规定,供方应对整个连在一起的机组轴系进行扭振分析,并且有责任指导必要的修改 4.8.3.5 以满足4.8.3.l4.8.3.4的规定要求
10o
GB/T28573一2012 4.8.4振动和平衡 4.8.4.1每个轮盘或推力盘安装到轴上之前应作单平面平衡
其他主要部件在安装到轴上之前,应单 独作动平衡
4.8.4.2
装配期间,旋转部件应作多平面动平衡
这个工作在加装两个主要部件后实施
平衡校正 只能在加装的部件上进行
其他部件可以在全部装配完毕后,进行最终平衡调整时作少量修正
对只 有 一个键槽的转子,应把具有一定弧度的半键(半键弧度应与轴的外圆一致)装人键槽
如有规定,装配 部件作最终平衡所用的全部半键的质量应记录在剩余不平衡作业表上(见附录F)
每面(轴颈)最大允 许剩余不平衡量按式(1)计算 Um=6350×m/" 式中: U mm -剩余不平衡量,单位为克毫米(g max -轴颈静载荷,单位为千克(kg); 2 最高连续转速,单位为转每分(r/min) 当提供备用转子时,备用转子应按主转子要求进行动平衡
4.8.4.3 如有规定,每个组装转动部件最终平衡结束后,应按附录F的剩余不平衡作业表要求作检 查和记录 4.8.4.4高速动平衡(以运行转速在高速动平衡机进行的平衡)仅在需方的特别认可下进行,其验收准 则应经供需双方同意
4.8.4.5机组装上平衡后的转子,以最高连续转速或规定运行范围内的任何其他转速进行工厂试验 时,轴颈处和相应每个径向轴承处所测得的任何平面未滤波振动峰一峰振幅不应超过由式(2)计算出的 值或50m,取较小值 12000 A =25.4 = 式中 未滤波振动振幅,测得的峰-峰值,单位为微米(m); -最高连续转速,单位为转每分(r/min)
任何大于最高连续转速的转速,在最高转速和驱动机械的跳闸转速范围以内,其振动不应超过在最 高连续转速下所记录的最大值的150%
注不能把这个限制同附录E规定的限制混消起来,附录E所规定的是工厂的不平衡响应鉴定
4.8.4.6当已经规定采用非接触探头或装置时,应确定并记录电跳动量和机械跳动量
其方法是在探 头位置中心线放置一个非接触振动探头,并在探头端部的任一侧放置一个千分表,然后转动放在V形 槽铁中的转子进行测量
机械运行试验报告应填写每个探头位置转动360°的电跳动量和机械跳动量数值
4.8.4.7如果供方能证实存在电跳动量和机械跳动量,则由式2)算出的最大检验值的25%或 6.3 Am,取较大值,然后按矢量方法,从工厂试验期间所测得的振动信号中减去
4.8.4.8如果不提供非接触振动探头,或不在轴上测量轴振动,那么,当机组以4.8.4.5所描述的转速 运行时,在轴承座上测得的运行转速频率下振动速度不应超过3.0 /s(不滤波)和2.0 mm/ mm/s 滤波 4.9轴承及轴承座 4.9.1 在下列条件下应使用液压径向轴承 耐磨轴承dN系数等于或大于300000时[dN系数是轴承尺寸(孔径毫米数)和额定转速(转每 11
GB/T28573一2012 分)的乘积]
标准耐磨轴承不能满足在额定工况下连续运行50000h(见GB/T6391)的L10额定寿命要 求,或不能满足以最大轴向、径向载荷和额定转速连续运行32000h的要求(额定寿命是指在 额定轴承载荷和转速下,同一耐磨轴承组的90%轴承出现故障迹象前所能达到或超过的小时 数) 4.9.2卧式汽轮机应安装能承受两个方向轴向载荷的推力轴承
当规定或耐磨轴承不能满足最小 的L10额定寿命要求时,多级汽轮机应装配液压推力铀承[4.9.1a)]
4.9.3立式汽轮机可采用油润滑或油脂润滑的滚珠或滚柱径向和推力轴承
推力轴承应根据数据表 规定的被驱动设备推力(上或下)的200%来设计
应防止耐磨轴承油脂过多
4.9.4耐磨轴承按GB/T1800.l1800.2的要求固定在轴上并装人轴承座内
但是,滚珠推力轴承 的锁紧装置应采用“w系列”带一个舌状止动垫圈的螺母
4.9.5角状接触型的耐磨轴承除外,耐磨轴承应有一个等于GB/T4604规定的3组径向游隙
单列 或双列轴承为Conrad型(无注油槽 4.9.6为便于装配,液压径向轴承为剖分式的、精密孔的和套简或瓦块型的,应具有钢衬浇巴氏合金 的可更换轴瓦、瓦块或壳体
液压径向轴承应设置防止转动的销子,并应可靠牢固地轴向固定
4.9.7 当设备在规定转速下,包括任何临界转速,带或不带负荷运行时,所设计的轴承应能抑制液压的 不稳定性,并在整个容许的支承间隙范围内,提供足够的阻尼限制转子振动达到4.8.4.5规定的最大 振幅
4.9.8轴瓦、瓦块或壳体应装在水平中分的轴承座内,并且可在不拆卸轴向中分机组的上半汽缸或径 向中分机组的端部,以及不拆卸联轴器轮毂的情况下,更换轴瓦、瓦块或壳体
4.9.9轴承设计应做到能防止逆向安装和/或颠倒安装
.9.10液压推力轴承应符合下列4.9.10.14.9.10.3的规定
4. 4.9.10.1液压推力轴承应为钢衬、浇巴氏合金的多瓦块型,设计成在两个方向具有相同的止推能力, 且每侧布置连续的具有压力的润滑油
两侧应为可倾瓦型,具有自动找平功能,以便在瓦块厚度出现轻 微不一致时,可确保每个瓦块分担相同的推力载荷
所设计和制造的每块瓦块尺寸精度高(厚度变化 上),个别瓦块之间可以互换或更换 4.9.10.2液压推力轴承应优先使用整体推力盘
当提供整体推力盘时,应至少留出3mm附加余量
以确保推力盘受到损坏时,可进行修复
当提供可更换的推力盘时(组装和维修用),应牢固地固定在轴 上,以防止微振磨损
4.9.10.3液压推力轴承推力盘两面的粗糙度Ra应不大于0.4m,推力盘两面的轴向全跳动量不应 超过12.7Am. 4.g.11推力轴承应以在最不利的规定运行工况下连续运行来确定尺寸
推力载荷的计算包括但不限 于下列因素: a)结污和密封间隙改变至设计的内部间隙大两倍的情况 b 所有由直径变化造成的阶梯推力; e级反动度和级压差; 进汽和排汽压力变化 dD e 4.9.12~4.9.14所述的被驱动设备的外部载荷 4.g.12对齿式联轴器,其外部推力按式(3)计算 0.25X9550×P 1 式中: 外部推力,单位为千牛顿(kN); 12
GB/I28573一2012 -额定功率,单位为千瓦(kw); 额定转速,单位为转每分(r/min); n -联轴器轴颈,单位为毫米(m D mm 注:轴颈为联轴器节圆半径的近似值, 4.9.13根据联轴器制造厂所允许的最大许可偏转计算挠性联轴器的推力
14 如果一个推力轴承(如在齿轮箱内)要承受两个或多个转子推力,如果那些推力的方向使它们 4.9 量值叠加时,即采用合力值;否则,就采用最大推力
4.9.15液压推力轴承应按不大于轴承制造厂极限载荷值的50%来选择
极限载荷值是无故障连续 运行期间,推力轴承所产生的最小油膜厚度下的载荷,或者是巴氏合金在最高温度下,不出现蠕变或屈 服变化的载荷,取较小的载荷
在确定推力轴承尺寸的过程中,对于各种特定使用条件,应考虑下列的 因素: 主轴转速; a b) 轴承巴氏合金温度; e)轴承瓦块挠度 d 最小油膜厚度 e)供油量、油黏度和供油温度; 轴承结构配置; f 巴氏合金; g h 油膜涡动
应在数据表上提供计算的推力负荷和轴承制造厂的极限额定值
4.9.16推力轴承应容许每根转子相对汽缸定位,并可以设置推力轴承的间隙和预载荷
4.9.17轴向中分的轴承座应采用金属同金属接触的方法,两半用圆柱定位销定位 4. .9.18所设计的采用压力油润滑的液压轴承轴承座应可最大限度地减少泡沫
回油系统足以保持油 位并使泡沫面低于轴端密封
在最不利的规定运行工况下,流经轴承和轴承座的油温温升不应超过 30C
轴承出口油温不应超过80C
当进口油温超过50C时,轴承设计、油流和允许温升应给予特 别考虑
推力轴承溢流油出口应是切向的,并在控制环上半,如果不使用控制环,则溢流油出口应在轴 承支架中 4.9.19进油口和排放接口应采用法兰连接或机械和双头螺柱连接的方法
螺孔可以是DN20,DNN25 和DN40
DN40螺孔的管子连接件应按下列条件安装 a)铸铁轴承座应配置长度不超过150mm,Sch40s的不锈钢管接头
b 钢制轴承座应配置长度不超过300mm,Seh80的碳钢管接头 管接头应随带碳钢松套法兰 c d)螺纹接口应密封焊接,但是铸铁轴承座或维修时要拆卸的部位不要求密封焊接
密封焊接焊 缝应符合ASMEB31.3的规定
不作密封煤接的螺纹接口连接时不应使用胶带
e DN20和DN25的管子或管子连接件不应密封焊接
4.9.20与用户管道连接的螺孔,应使用符合GB/T14383规定的实心圆头钢螺塞堵住,且不应使用 胶带
4.9.21在汽轮机轴穿过轴承座的部位,应设置可有效防止杂质、凝结水和蒸汽侵人的可更换端部密 封
设计的密封能有效保持轴承座中的油不泄漏
密封件为金属的,无火花、非接触和非磨损的材料
允许采用径向轴流式密封和磁性密封
不应采用唇式密封
4.9.22轴承座应具有足够的防止被蒸汽凝结水污染的能力,尤其在汽轮机惰走期间,更应具备这种 功能
4.9.23无压力油润滑轴承的轴承座应设置至少为DN15尺寸的注人和排放用螺纹孔并用螺塞堵住
13
GB/T28573一2012 轴承座应配置至少0.1L容量的等油位、可视供油注油器,该注油器是一个耐热玻璃容器(不能太阳直 射或受热感应或磨损,带一个正油位位置控制器(没有调节螺钉)和保护网罩
一个正常油位的永久性 标记应醒目的、准确的标记于轴承座外面,该标签用铸造或其他耐久的方法固定
4.9.24用油环润滑轴承的轴承座应设置一个被封盖住的开口,其位置为当汽轮机运行时,可目视观察 检验油环
4.9.25规定用油雾润滑时,应符合下列4.9.25.l4.9.25.5的规定
4.9.25.1在轴承座上半应设置一个DN8油雾进口
为便于油雾穿过整个耐磨轴承,纯油雾或气吹油 雾的进、出口位置应不使油雾内部通道被短路
如果轴承是套筒式轴承,那么,为了使补充油能滴人轴 承之中,凝结油雾接口应设置在轴承的上方
4.9.25.2应设置一个DN8排气接口,其位置在每个耐磨轴承和轴承座轴终端处的空隙端盖上或轴承 座上
只安装套筒式轴承的轴承座应在靠近轴承座端部的地方设置排气口
4.9.25.3不应使用有护圈或密封的轴承
4.9.25.4当规定采用纯油雾润滑时,不装配油环或抛油环(如果有)和等油位注油器,也不需要提供油 位指示器
当规定采用气吹或冷凝油雾润滑时,应提供这些设施,并且为了保持轴承座的内压,还应给 注油器加装管子
4.9.25.5需方应提供排放和供油雾用的连接件
4.9.26应在规定的运行工况和40C的环境温度下提供足够的冷却,包括结垢裕量,以保持压力系统 的油温低于70C和油环润滑或溅油润滑的油温低于80C
在必须水套冷却的场合,只能在轴承座的 上半和下半之间的水套上配置外部连接件,并且既不能装垫片,也不能装螺纹连接件接头
因这两种接 头可能使水渗人油箱中
如果采用冷却盘管(包括配件),则其材料为有色金属材料,且轴承座内部无承 压接头或连接件
盘管最小厚度至少是19伯明翰线径(1.07nmm),直径至少12.7mm.
如有规定,每个轴承座应提供两个径向振动探头安装接口,每台机组的推力端提供两个轴向 4.9.27 位移探头安装接口,以及每台机组提供一个转速探头安装接口
探头安装按APIStd670的规定,轴信 号传感区应符合有6.了规定
4.10润滑 4.10.1除非另有规定,否则,卧式机组的轴承和轴承座配备使用烙类润滑油
4.10.2抛油环或油环在其边缘或孔径边缘的最低处以上应有3mm6mm的有效浸没深度
抛油 环应安装轮毂,以保持同轴度,并且应可靠固定在轴上
当规定用一台共用系统向两台或更多设备(如压缩机、齿轮箱和汽轮机)供油时,需方应在与 4.10.3 使用该用油系统供油设备的供货商协商一致的基础上,在数据表上对油的特性作出规定
洼;共用油系统中所使用的润滑油是与GB/T3141中规定的等级32相一致的焰类油
4.10 要求宽转速范围、快速停机或慢转运行的场合,应规定合适的工况,驱动设备供方应校验在 所有规定运行工况下的汽轮机(和齿轮箱)是否得到了足够的润滑
4.10.5建议用循环系统的场合,应向需方提供详细情况,以供审查 4.10.6JB/T4365标准中所述以外的压力润滑系统应由一个带进口滤网的油泵,一个供-回油系统, 一个冷油器(当要求时),一个全流量过滤器,一个低压润滑油压力停机开关和其他必需的仪器仪表组 成
下列4.10.6.14.10.6.8提出具体要求
关于最低要求的压力润滑油系统见附录G 4.10.6.1油箱应具有下列特性和附件 容量足够大而不需要频繁加油,足以满足停机时用油需要,提供至少3min的维持时间用来沉 淀杂质和水分 b)具有清除空气和最大程度减少到泵段的漂浮杂质的结构; c)加油连接件应为带水平显示器的铠装式液位玻璃管,并有适合于室外使用的通风器; 14
GB/T28573一2012 可满足彻底排放目的的倾斜底部和排油接口; d) 一个实用的、较大的清洁开口; e f)油箱材料由供需双方商定
4.10.6.2除非另外提供压力油源,否则,由主轴驱动主油泵
惰走期间,排放从吸油管来的油不应对 无人自动起动时的泵产生危害
4.10.6.3如果供方提出要求,则应提供用于起动的手动备用泵
4. .10.6.4优先采用一台独立的管壳型冷油器
冷油器不允许置于油箱内
.10.6.5滤芯可更换的全流量过滤器,过滤精度为25Am或更高
过滤器的滤芯材料为抗腐蚀材 4. 料
不推荐使用金属网或烧结金属滤芯
过滤器不应设置减压阀或自动旁路
4.10.6.6冷油器后的温度表 10.6.7过滤器前、后测压用的压力表
4 10.6.8低油压停机装置或开关 0. 当需方规定或供方有要求时,提供一台独立驱动、自动控制的备用泵
如有规定,每个轴承油排放管上均应配置流量观察窗
如有规定,提供低压报警开关
10.6.11 4.10.6. 12 如有规定,提供低油压辅助油泵起动开关
4.10.7如果主油泵和备用油泵不封闭地装在油箱内,则应配置钢罩壳;但是,主轴驱动的油泵壳体可 以是铁制的
所有其他含油的压力部件均是钢制的(见5.5.2的内容) 4.10.8
如有规定,应在油箱外面设置一个可更换蒸汽加热元件或恒温控制的铠装式电浸人加热器 (不锈钢套壳材料为奥氏体型),用于天气寒冷时起动前加热油箱里的油
加热器具有足够的能力在 12h内,把油箱里的油从规定的最小环境温度加热到制造厂要求的起动温度
如果使用一台浸人式电 加热器,则其最大功率密度应为2.0w/cm 4.11材料 4.11.1 总则 4.11.1.1除了本标准或数据表的要求或禁止外,制造材料应为制造厂用于规定运行工况的标准材料 见5.5)
应在供方的报价书中清楚地说明所有主要部件的冶炼情况
4.11.1.2在供方报价书中应对所有主要部件的材料作出明确规定
应参考适用的国际标准对材料包 括材料等级作出标识
当无适用牌号时,供方应在报价书中给出包括材料的力学性能、化学成分和试验 要求等内容的材料规范
4.11.1.3如果最大蒸汽条件超过1.7MPa或260C,则承压部件应为钢制件
如果最高排汽压力超 过520kPa或空负荷排汽温度超过260,则非凝汽式汽轮机的排汽缸为钢制件
蒸汽最高温度超过 413C的,采用合金钢制件
只有经需方同意,才能采用球墨铸铁制件
汽轮机主轴和叶轮应为符合制造厂标准的材料,叶片和喷嘴(动叶和静叶)为11-13Cr材料 围带为11-13Cr或镍铜合金材料,蒸汽过滤器为18-8不锈钢材料
转动或滑动部件(如调节器连杆钦接头和调整机构)应为适应现场环境的耐腐蚀材料 不作鉴别的较小零件(如螺母、弹簧、垫圈、垫片和键),至少应采用在同环境中的专用零件同 样耐腐蚀的材料
需方应指出燕汽和环境中存在的腐蚀介质,包括可能引起应力腐蚀裂纹的那些成分 如果零件在制作、表面淬硬、堆焊或补焊时易受晶间腐蚀影响,则应采用低碳钢或质量稳定 的奥氏体不锈钢材料
注:除非涂上一层对晶间腐蚀不敏感的缓冲涂层,否则,含碳量超过0.10%的表面淬硬或堆焊低碳钢和质量稳定的 奥氏体不锈钢均敏感
15
GB/T28573一2012 4.11.1.9使用材料为奥氏体型不锈钢的配对零件如双头螺柱和螺母或类似具有粘结特性的材料的部 位,应使用具有良好温度性能的防粘剂进行润滑,该防粘剂能与规定的液体相兼容 注:对扭矩载荷值来说,使用和不使用防粘剂,其结果是截然不同的
4.11.1.10对于承压缸体,其材料、铸造系数和焊缝质量均应符合AsME规范第卷第1册的要求
制造厂的数据报告格式不要求同规范规定的相一致
4.11.1.11低碳钢在环境温度或低温下可能存在缺口敏感性和易脆裂,因此,全镇静正火钢须经晶粒 化处理后才能使用
禁止使用ASTMA515钢种
4.11.1.12环境温度低于一30C时,通常使用钢质缸体材料,在最低规定温度范围不具有一个足以证 明ASME规范第卷第1册UG84的夏比V型缺口冲击功要求的冲击强度
因此,供需双方应共同 协商保护要求
13 承压接口用的最低质量等级螺栓连接材料应为碳钢(GB/T3098.1),铸铁汽缸和钢质汽缸 4.11.1.1 用的螺栓连接材料为高温合金钢(GB/T20410)
螺母应符合GB/T13807.3的要求(或符合 GB/T3098.1,空间限制时,需表面淖硬),温度低于一30C的,采用符合AsTMA320要求的低温螺 栓连接材料
.11.2铸件 b 4.11.2.1铸件应完好,无疏松、热裂、缩孔、气孔、裂缝、起皮和砂眼及类似的有害缺陷
铸件表面应经 喷砂,喷丸、化学清洗或其他标准方法清理
铸造分型面的飞边和残留的浇、冒口均应铲平、挫光或 磨平 承压铸件应尽量减少使用型芯撑
型芯撑应干净无锈(允许有镀层),并且其成分应与铸件 材料相容 除了4.11.2.3.1和4 1. 2.3.2规定的要求外,铁素体铸件不应采用补焊,锤击、塞堵头,烙 . 焊或灌注的方式进行修补
2.3.1可焊接铸钢件可用补焊修复,应按ASME规范第卷第1册和第卷的规定采用鉴定合 格的焊接工艺
4.11.2.3.2灰铸铁或球墨铸铁铸件在ASTMA278、ASTMA395或ASTMA536规定的范围内进 行塞堵头修补
为塞堵头而钻的孔应采用液体渗透方法仔细检查,以确保去除全部有缺陷的材料
所 有ASTM规范未包括的修复方法应得到需方同意
4.11.2.4禁止采用全封闭的型芯内腔包括用堵头封死的内腔
4.11.2.5球墨铸铁件的生产应按JB/T9631的规定进行
4.11.3焊接 4.11.3.1管道、压力容器零件和任何不同金属之间的焊接及补焊,应由经ASME规范第卷第1册 和第卷规定考核合格的或符合我国要求的焊工进行操作和检验
4.11.3.2供方负责所有修复及补焊审查工作,以保证正确进行修复和补焊的热处理以及无损探伤,并 符合鉴定合格的工艺要求(4.11.1.10)
补焊的检验应采用与检测原始缺陷相同的无损探伤方法
对 于磁性材料,至少应按6.2.2.4要求进行磁粉检验,对于非磁性材料,应按6.2.2.5要求进行液体渗透 检验
4.11.3.3除非另有规定,否则,所有ASME规范第卷第1册及ASMEB31.3规范以外的焊接,如 底板上焊接、非承压输送管道、隔热罩和控制盘的焊接,均执行DL/T678标准
4.11.3.4由锻制或锻,铸合成的承压缸体应符合下列4.l1.3.4.14.1l1.3.4.4的规定
4.11.3.4.1钢板边缘按ASME规范第卷第1册UG-93(d)(3)规定作磁粉检验或液体渗透检验
4.11.3.4.2焊接表面应在铲平或刨平后,进行磁粉探伤检验或液体渗透检验,并作焊后热处理后再 16
GB/T28573一2012 复验 4.11.3.4.3压力容器焊缝包括水平与垂直法兰式连接的壳体焊缝均应完全透
4.11.3.4.4符合ASME规范第卷第1册规定并要求焊后热处理的焊接缸体,无论厚度多少均应进 行热处理 4.11.3.4.5所有焊缝均应按AsME规范第卷第1册Uw-10和Uw-40规定作热处理 4.12 铭牌及转向箭头 4.12.1铭牌应牢固地固定在设备及其辅助设备主要部件的可视部位
4.12.2转向箭头应直接铸人或因定在转动设备各主要部件的可视位置
铭牌和转向箭头(如果固定 的材料应为奥氏体型不锈钢或镍铜合金(蒙乃尔高强度合金钢或相同材料)
固定销钉材料为相同材 料
不允许使用媒接方法固定
需方可以指定采用sI国际单位或采用其他单位
作为一个最低要求,铭牌上应使用数据表 4.12.3 上的单位清晰地标出下列数据: a)供方名称 b) 产品序列号 e)规格及型号, 额定功率及转速; d -阶临界转速; e) 二阶临界转速 注如果通过试验没有获得临界转速值,那么,应在临界转速值后标上“计算"字样
应在试验台测出低于最 大连续转速的任何临界转速
低于一阶临界转速运行的汽轮机,可省略二阶临界转速 g最高连续转速 最低允许转速; h 超速跳闸设定值 i 正常和最高进汽温度及压力 j 正常和最高排汽压力 k 需方的设备项目号(如果规定铭牌不够大,可使用一个单独的铭牌标出
辅助部件 齿轮装置 5.1 5.1.1齿轮装置可以提高汽轮机效率时,就考虑采用齿轮装置
汽耗和性能曲线应以齿轮装置的输出 功率为根据
5.1.2被驱动设备的额定功率大于55kw的,齿轮装置不应整体装人汽轮机内
5.1.3除非另有规定,否则,达到1500kw的单独平行轴齿轮装置应符合AP1Std677的规定
5.1.4应在所有的数据表和相应设备上清晰地标出齿轮装置的输出轴转向
5.2联轴器及护罩 5 2 除非另有规定,否则,汽轮机和被驱动设备之间的挠性联轴器和护罩由被驱动设备的制造厂 提供
如有规定,则驱动设备端的半联轴器由汽轮机制造厂安装 5 .2.2联轴器一轴连接处的额定功率应至少等于驱动设备额定功率同ANS1/AGMA9002的联轴器 使用系数之间的乘积
联轴器的制造,式样和安装布置应经需方和驱动及被驱动设备供方的一致同意
除非另有规定,否则,应采用最小尺寸为125mm的隔套式联轴器
联轴器为锻钢件,且所设计的结构 17
GB/T28573一2012 能允许进行由膨胀以及其他轴端移动所产生的轴向窜动
5.2.3应把轴,键槽尺寸(如果有)和端部及热力影响产生的轴端移动这方面的数据提供给联轴器的供 货方
5.2.4 当汽轮机供方提供一台独立的齿轮装置时,应同时提供汽轮机和齿轮装置之间的挠性联轴器 5.2.5 为确保连接机器的精确对中,应按下列5.2.5.1一5.2.5.3规定来控制联轴器配对和对中面的 总显示读数
5.2.5.1对于所有的汽轮机,通常为检查对中而采用的联轴器表面与联轴器轮毂旋转轴的同轴度在下 列限制范围内:在最小25mTIR(总显示读数)允许公差和最大75mTIR允许公差情况下,每毫米 TIR
如果满足动平衡要求,则所有不用来定位、配对或对中的其他直径应符合联轴 轴直径为0.51Hm 器制造厂的标准
汽轮机与它的被驱动设备采用挠性联轴器的,其定位和对中面应在5.2.5.1的限制范围内与 轴线垂直
5.2.5.3对于汽轮机与被驱动设备之间采用刚性联轴器的立式汽轮机,联轴器配对直径的同轴度应在 5.2.5.1规定限制的范围内
在最大0.51mTIR(总显示读数)情况下,联轴器配对面与联轴器轴线 垂直度应在每10mm配对面直径lMm之内
挠性联轴器用键连接的方法安装到轴上
键、键槽及装配应符合JB/T9559规定
挠性联轴器 为圆柱形孔径的,应具备GB/T1800.2,容许公差N8所规定的过盈配合,还应符合GB/T3852规定 使用机械密封,要求可拆卸联轴器轮毂的,并且轴直径大于60mm的,轮毂应采用圆锥方法安装
采用 键连接的联轴器,其锥度应为GB 10的长系列圆锥体
其他锥度及装配方法应经供 3852规定的 需双方一致同意
联轴器轮毂上应设置便于拆卸的锥形拔出孔,其直径至少10mm
注,应采取合适的安装和维护方法,以保证圆锥配合的联轴器具有压配合能力 所制造的联轴器应满足JB/T8557中等级9的要求
运行转速等于或小于3800r/min的联轴器应作部件平衡
每个部件如轮毂、套简、挠性部件、 隔套及连接装置均应分别进行平衡
除了单独键连接轮毂的键槽,所有部件的加工均应在平衡前完成
联轴器部件应平衡到GB/T9239.1中G1.0级或平衡到7g ,取较大值
心轴质量不应超过正在 mm 作平衡的部件质量
运行转速大于3800r/min的联轴器,其部件平衡和装配平衡检查应符合JB/T9559的要求
5.2.9 5.2.10便于拆卸的联轴器护罩应全部遮盖住由供方提供的联轴器的所有暴露部分
联轴器应具备足 够的刚度,以承受弯曲变形和耐磨,并且护罩应延伸至座架内13mm
5.3安装底板 5.3.1总则 5.,3.1.1
如有规定,设备应配备底板或底盘
5.3.1.2在下列5.3.1.2.1一5.3.1.2.11中,术语“安装底板”是指底盘和底板 5.3.1.2.1安装底板制作完成后,其上所有的机械设备安装面均应进行平整和平行加工
安装面应至 少在三侧比设备底座大25mm,防止不稳定支承
设备的所有安装表面应处在同一平面,其误差在 50Am之内
最大表面粗糙度为Ra3.2Amm
3 .2.2设备支承质量超过250kg的,安装底板应设置轴向和横向顶起螺钉,其尺寸等于或大于垂 s 直顶起螺钉
为了使支承搭子不影响设备的安装或拆卸顶起螺钉或垫圈,顶起螺钉的支承搭子应附到 安装底板上
如果因为设备过重而无法使用顶起螺钉,则应提供其他方法
55 .3.1.2.3设备底部垂直顶起螺钉布置应防止衬垫表面损坏, 21 API标准原文中是5.2.6.1,按内容应是5.2.5.1
18
GB/T28573一2012 5.3.1.2.4所设计的机械支承应能把联轴器法兰处由最不利的压力、扭矩和允许的管道应力综合作用 所产生的对中变化限制在504m(见4.5关于允许管道力的内容) 5.3.1.2.5当提供中心支承时,所设计和制造的中心支承可使用水平顶起螺钉来移动机器
5.3.1.2.6除非另有规定,应使用环氧树脂薄胶泥
供方应按GB/T8923.1或SSPCSP6的规定,对 安装底板的所有灌浆表面进行喷砂处理,并预先在这些表面涂上一层无机硅酸锌
5.3.1.2.7不应使用地脚螺栓把机器固定到安装底板上
5.3.1.2.8不应在安装底板上钻用于其他设备的孔
安装底板应设置调平螺钉
被灌浆的安装底板 的外侧圆角半径为50mm(在平面图上)
不灌浆的安装表面机加工后应立即涂上防锈剂
5.3.1.2.9安装底板的供方应提供设备底座与安装底板之间用的、厚度3mm~15 mm的不锈钢垫片 组(材料为奥氏体型)
所有垫片组应骑跨在压紧螺栓和垂直顶起螺钉之上,并且比设备底座的每个边 至少大6mm
需方应提供地脚螺栓
安装底板的供方负责提供用于把设备固定到安装底板的紧固件和用于校平安装底板的顶 5.3.1.2.11 起螺钉
底盘 当规定使用底盘时,数据表上应列出安装在该底盘上的主爱设备
底盘为独立的钥制媒接构 件
底盘结构具有纵向钢梁,并在汽轮机和汽轮机驱动设备的支承面下设置全宽度横梁结构
5.3.2.2除非另有规定,为了保证底盘上的部件的任何泄漏不会流出底盘,底盘面积应根据传动轴系 部件的尺寸来扩展
如有规定,底盘应设置调整垫块或安装罩盖可拆卸的觇标
安装后,调整垫块或觇标应便 5 3.2.3 于在基础上对安装设备和底盘进行现场校平
如有规定,底盘应能在建筑构件下作不连续/浆施工的墩式安装(一种在规定的支承点上 5.3.2 具有足够刚度的安装方法)
底盘设计须供需双方一致同意
5.3.2.5底盘应设置至少四点起吊的吊耳
起吊装有全部设备的底盘时,既不会对底盘造成永久性变 形或其他损坏,也不会对底盘上的设备造成损坏
5.3.2.6构件之间的底盘底部应是敞开的
当把底盘安装到一个混凝土基础上时,应设置一个至少为 0.01nm'面积的浆孔,并且每个隔框的尺寸不小于75mm
可在所有的承重结构梁下,通过这些灌浆 口进行灌浆工作
实际设计这些部位时,对汽轮机以及所有的被驱动设备来说,这些灌浆口应便于灌 浆
灌浆口应有15mm高的凸缘边,如果灌浆口位置位于液体冲击外露浆液区域,则应提供最小厚度 为16规格的金属盖
在底盘的每个隔框的最高点,设置一个直径至少15mm的通气孔
55 .3.2.7 除 5.3.2.6规定的要求外,固定双头螺柱,如“]”(勾)形的,应焊接到最大中心线300mm的 底盘平台下,以加强灌浆中的固定
5. .3.2.8 底盘底部的安装块应在一个平面上,以允许采用一个单独的水平基础
如有规定,由供方 提供辅助底板
.2.9除非另有规定,底盘上部的所有行走面和工作区均应设置防滑金属盖板
33 5.3.3底板及辅助底板 55 .3.3.1当规定用底板时,除了要符合5.3.2规定外,还应符合下列5.3.3.1.1和5.3.3.1.2的规定
5. .3.3.1.1螺栓连接的部位应留出足够的空隙,便于使用套简扳手或梅花扳手,并且允许使用水平和 垂直顶起螺钉移动设备
5.3.3.1.2底板应具备足够的厚度,可把设备载荷从设备底座传递到基础,但是底板厚度决不能小于 40mm
19
GB/T28573一2012 5.3.3.1.3当规定采用辅助底板时,辅助底板应至少为25mm厚的钢板
辅助底板的配合面粗糙度 与5.3.1.2.1规定相同
5.4控制设备和测量装置 5.4.1总则 5.4.1.1测量装置及其安装方法应符合需方询价书或订单所列举的规定,或符合这两者的规定
5. .4.1.2如有规定,控制设备和测量装置均应适合室外安装
4 1. 在其他适用场合,控制设备和测量装置应符合AP1Std670的规定
5 3 55 .4.1.4所有导线的设计及安装应做到便于拆卸,不损坏导线;导线所处位置不会妨碍轴承、密封件或 设备内部零件的拆卸
55 4 1. .5 当有规定时,为了在正常工况以外的工况经济地运行,应设置手动喷嘴控制阀
供方应闸 明所需的手动阀数量并提供性能数据[见4.1.4b)]
.4.2控制系统 o 4.2.1应在汽轮机的调节器和速关阀前设置抗腐蚀拆卸式蒸汽滤网
燕汽滤网的最小实际有效截 5. 面应两倍于汽轮机进汽接口的横截面
拆卸燕汽滤网时不需拆卸进汽管道
.4.2.2除非另有规定,应提供一个NEMAA级液压调节器
该调节器符合NEMAsM23的规定, 5. 并具有等于或好于表3所列的特性
可提供符合上述要求的电子调节器
表3调速器 NEMAsM23等级 数 最大稳定 额定转速调节 0.5 最高转速变化正或负 0.75 0.25 最高升速 跳闸转速 115 110 注,所有数值(跳闸转速除外 转速的百分比
跳闸转速为最高连续转速的百分比
)均为懒定 除非另有规定,应采用手动转速变换器调节转速
当为转速调节规定一个信号时,供方应提供一个如下布置的转速设定机构 5.4.2. 需方所规定的控制设备信号的全部范围应同被驱动设备要求的运行范围相适用
除非另有规 a 定,最大控制信号应对应于最高连续转迷 控制信号的动作或故障,或转速设定机构故障,均不应影响调速器对最高允许转速的限制,也 b 不妨碍用手动转速变换器进行手动调节
除非另有规定,调速器和手动转速变换器的可调转速范围应为最高连续转速的20% 5.4.2.5 也 就是大于正常转速5%,小于正常转速15%
转速调节阀应符合制造厂标准,最好为平衡型的
5.4.2.6 5.4.2.7当最高进汽压力等于或大于1.7MPa时,速关阀和转速调节阀应有一个金属或其他非压缩 型阀杆密封衬套和一个中间泄漏口 5.4.2.8汽轮机应配备独立的危急超速系统,当运行转速达到跳闸转速时见表3),切断汽轮机供汽
危急超速系统应具备下列特性 容易接近; 2o0
GB/T28573一2012 b在管道最高蒸汽压力和流量情况下,可手动跳闸 汽轮机在任何负荷工况下,均能通过一个强制作用速关阀使汽轮机停机; c d能在管道最高进汽压力下复位; 零件不产生火花并适合在危险气体和室外使用
e 注,需方应在进汽管道上设置一个用于关闭汽轮机的隔离阀,超速跳闸系统复位前,应关闭该阀
5.4.2.9汽轮机排汽压力低于大气压力时,对是否需要配置跳闸系统操纵的排汽真空破坏器,应经供 需双方一致同意 注:对排汽低于大气压力的汽轮机,即使关闭汽轮机的速关阀,也会有燕汽漏人,从而使汽轮机和被驱动设备无法 完全停机
真空排汽破坏器把空气引人排汽缸,提高排汽压力,并且减少惰走时间
对于排汽到一个公用凝汽 系统的汽轮机,则不容许引人空气,为此,要求一个或多个更可靠的速关阀 5.4.3仪表板和仪表盘 仪表板 如有规定,应提供一个就地仪表柜
需方应指定所要求的仪表范围
5.4.3.2 仪表和控制盘
如有规定,应提供一个仪表板,该仪表板包括驱动和被驱动设备用的全部仪器
这类仪 5.4.3.2.1 表板应按需方的说明进行设计及安装
需方应规定仪表板是独立地安装在机组基础上,还是安装在其 他部位
操作者能从驱动设备控制点清楚地看到仪表板上的仪表
应设置一个指示灯试验按钮
应在 数据表上规定安装在仪表板上的仪表
5 ..4.3.2.2仪表柜应完成组装,只需要与需方的外部管道和线路相连即可
如果因为控制或仪器仪表 原因,要求机组有一个以上的接线点时,则应提供从一个单接线盒到每个开关或仪器的导线,该接线盒 安装在机组的接线柱上(或它的底座上,如果有底座的话)
导线应装人金属导管或盒内
所有接线盒 和端子板上的接线柱、开关和仪器均应加贴识别标签
5.4.4 仪表 5.4.4.1 转速表 如有规定,应提供一个转速表
应规定转速表是采用电子转速表,还是采用振动弹簧转速表
除非 另有规定,转速表的最小范围从0%125%的最高连续转速
5.4.4.2温度计 . .4.4.2.1刻度盘式温度计为重型设计和防腐蚀的
刻度盘直径至少l00 mm,并且是双金属型或充 液体的
温度计刻度盘采用白底黑字的标准式样
5 .4.4.2.2温度计的传感元件应处于流动的液体之中 注:这点对部分充满液体流动的管道尤为重要
5.4.4.3温度计套管 与易燃或有毒液体接触,或处于压力,充满液体的管道中的温度计应配置规格为DN20的可分离杆 式温度计套管,其材料是奥氏体型不锈钢 5.4.4.4热电偶及电阻式测温计 实际应用时,应允许在机组运行情况下更换热电偶和电阻式测温计
安装热电偶和电阻式测温计 21
GB/T28573一2012 时,温度计套管或探测器和接线盒之间的导线应是连续的导线
应提供从热电偶到底板上的一个或多 个分线盒之间的导管
5.4.4.5压力表 5.4.4.5.1压力表(不包括装在仪器内部的气压表)应配置奥氏体不锈钢波登管和不锈钢活动机件 100mm直径的刻度盘(压力超过5.5MPa的,采用150mm直径的刻度盘),以及配置DN插人式合金 钢连接件
压力表的刻度盘采用白底黑字的标准式样
应正确选择压力表的量程范围,使正常运行压力处在压力表量程的中间位置
但是,刻度盘的最大 读数在任何情况下也不能低于减压阀设定值加10%的值
每只压力表应配置一个圆片插件或放气件, 用来释放过高的表壳内压
5. 4 .4.5.2如有规定,易受振动的位置应提供注液压力表
4.4.6电磁阀 5. 只在干净、干燥的空气仪表装置中使用直接操作的电磁阀,电磁阀绝缘等级等于或大于F级,并且 具有连续工作的能力
当要求电磁阀进行其他工作时,对气动阀、液压阀和类似阀门来说,电磁阀起 一个控制阀的作用
5.4.4.7减压阀 安装在供方提供的设备或管道上的减压阀应由供方提供
其他减压阀由需方提供
所有 5.4.4.7.1 运行设备的减压阀均应符合sY/T10044以及APIStd526规定的限制要求
供方应向需方提供减压 阀尺寸选择和选型时的流量,最高允许设定压力和温度
供方的报价书应列出所有的减压阀,并清楚显 示哪些减压阀由供方提供
减压阀的设定值,包括蓄能器,应考虑到所有可能的设备发生故障的类型及 对管道系统的保护 5. 4 .4.7.2除非另有规定,否则减压阀本体为钢质材料
5.4.4.7. 3 如有规定,对通过隔离阀隔离的元件应配置温控减压阀
5 流量指示器 5.4.4.8.1 如有规定,应在每个轴承的大气压力回油管道中设置流量指示器
5.4.4.8.2除非另有规定,流量指示器为法兰连接型,有观察窗并具有钢质本体
5.4.4.8.3为便于观察通过管道的油流量,每个流量指示器应在垂直面上设置观察窗
观察窗的直径 至少等于1/2的油管内径,且能清楚显示最小油流量
5.4.5报警和停机 5.4.5.1
总则 作为规定,供方应提供并安装开关及控制装置
5.4.5.2报警哨阀 如有规定,汽轮机汽缸上应设置一个报警哨阀
凝汽式汽轮机的报警哨阀设定在35kPa
背压式 汽轮机的报警啃阀的最小设定值是最高排汽压力的10%或比最高排汽压力高出70kPa(取较大值). 注:报警哨阀只是一个声音报警装置,不是减压装置
5.4.5.3报警和跳闸开关 5.4.5.3.1为便于检验和维护,每个报警开关和停机开关应装人一个单独罩壳
应使用气密式单极双 22
GB/T28573一2012 投开关,其最小容量在120V交流电压时达到5A,120V直流电压时达到0.5A
不应使用水银开关
55. .4.5.3.2
需方应对报警和跳闸功能用的电子开关操作方式作出规定
5.4.5.3.3罩壳外面不能调整报警和跳闸开关设定值
55 .4.5.3.4压力传感部件为奥氏体型不锈钢
.4.5.3.5供方应在报价书提供完整的所供报警和停机装置的说明
S 5.4.5.4电弧型开关座 对4.1.13适用规范中所描述的有关电弧型开关座的特性要求,应给予特殊关注
5.4.6振动和位置检测器
如有规定,应提供并安装振动和轴向位移传感器,并根据APIstd670进行标定
5.4.6.1
如有规定,应提供并安装振动和轴向位移监视器,并根据APISd670进行标定
5.4.6.2 5.4.6.3 如有规定,应提供轴承温度监视器,并根据APIStd670进行标定
5.5管道及其附件 5.5.1 总则 5.5.1.1管道设计、接头制作、试验和检验应符合ASMEB31.3规定
除非另有规定,不要求进行X 射线检验 5.5.1.2下列用途的管道系统作为辅助系统 a)蒸汽,包括密封燕汽; b 仪表和控制气体; e)润滑油 d 控制油; e)冷却水; f疏水及冒汽
辅助系统应遵守表4的要求
注汽缸接口见4.4 5.5.1.3管道系统应包括管道、隔离阀、控制阀、减压阀、减压器、孔板、温度计及套管,压力表、,观察窗 和全部有关的通气及疏水装置
5.5.1.4如果汽轮机供方提供底盘,则应提供汽轮机供方所供设备需要的管道系统,包括主机基础区 域和任何控制台基础或任何辅机基础范围内安装的附件
每个基础边界处的管道末端为法兰接口
5.5.1.5管道系统的设计应达到下列要求 具有合适的支承及保护,以防止因振动或装运,运行和维修而引起的损坏 a) b)具有适当的挠性和正常的可接近性,便于运行、维修和彻底清洁 c)管道根据机组轮廓进行安装布置,做到整齐有序且不妨碍接近孔口; d消除气穴 不拆卸管道就能通过最低点达到完全排水
5.5.1.管道装配最好采用弯制或焊接方法,尽量减少使用达兰和配件
只有在设备连接处、任何基 .才允许使用焊接法兰
除了T形接头和异径接头,只有在管道密集区 础的边界处和易于维修的部位, 为简化管道布置时,才允许采用焊接连接件
最大程度减少使用螺纹接口
不应使用管外套管的方法 5.5.1.7管螺纹应为符合GB/T12716规定的锥螺纹
当要求符合当地标准时,管螺纹则应符合 GB/T7307的规定
法兰符合GB/T91129124的规定
只有经需方同意才可使用松套法兰
对于 23
GB/T28573一2012 承插焊式连接件,应在管端和插口底部之间留出1.5mm的间隙
5.5.1.8仪表、铸铁设备或维修时须拆卸的部位不允许采取媒接方法
5.5.1.9不应使用尺寸为DN32,DN65、,DN90,DN125、DN175或DN225的连接件、管道、阀门和 配件 5.5.1.10安装空间不允许使用DN15,DN20或DN25管子的地方,其无缝管配置参见表4
表4供参考的管道材料 燕 汽 冷却水 润滑油 部件名称 标准
GB/T28573一2012 5.5.1.11任何接口的最小尺寸为DN15
5.5.1.12供方提供的管道系统应在工厂进行构制和安装,并具有合适的支承
法兰连接件的螺栓孔 应跨置在平行于设备主水平或垂直中心线的直管上
5.5.2油管道 5.5.2.1 当油流速为0.了m/八时,按不超过-半流量的要求来确定排油口尺寸,并且保证做到排放畅 通(要考虑到存在泡沫的情况)
水平管道应至少有40mm/m的连续倾斜坡度(朝着油箱)
如果可能 的话,分支管(任一横截面不超过一个)沿流动方向以45"进人疏油总管
5.5.2.2不应使用非自耗的衬环和套简式接头
滤油器下游的压力管道内不应存在聚积污垢的障碍 物.不应使用承插焊管配件
5.6专用工具 5.6. 当机组要求使用专用工具和夹具进行拆卸,安装和维修时,应在报价单中列出这些专用工具,并 1 作为设备原始供货的一部分来提供
多机组安装的,其要求使用的专用工具和夹具数量应经供需双方 -致同意
在设备进行工厂安装及试验后拆卸时,应使用这些专用工具或相似的专用工具
5.6.2提供专用工具时,应将专用工具单独装人坚固的金属箱并标上“专用工具”标签/项目号)字样
每个工具均有说明用途的标签
5.7可拆卸式保温层 除非另有规定,等于或大于正常运行温度(等于或大于75C)的汽缸应装有完全遮住汽轮机的 5.7.1 可拆卸毯式保温层
毯式保温层由里面装有防护金属网格的高温纤维织物组成
扣件、金属网格和紧 固件的材料均为不锈钢材料
5.7.2正常运行工况下,保温层外表面温度保持在75以下
应按拆卸和更换时尽量不受到损坏的 原则来设计可拆卸保温层
检验和试验 总则 6 6.1.1需方预先向供方发出通知,并经供方根据合同认可后,需方代理人应能进人所有供方及分供方 正在进行设备制造,试验和检验的现场 6.1.2供方应把需方的检验和试验要求告知分供方
供方应在进行需方指定的现场见证或观察验证前,贯前飞足够的时间)通知需方作好准备 需方代理人应可接触供方的质量控制大纲,以作审查之用
需方应指定参与检验和试验的范围,并对提前通知时间提出规定
6.1.5 1.5.1当需方规定在工厂进行检验和试验时,供需双方应共同协调确定停工待检点和检验员巡 6 查点
6.1.5.2现场见证;是一个与生产进度同步的,并且在需方或其代理人到场的情况下所进行的检验或 试验的控制点
对机械运行试验或性能试验这样的现场见证,要求先提供一份初步试验良好的通知书 6.1.5.3观察验证;是指把检验和试验的时间通知需方,但是检验和试验按计划进行,如果需方或其代 理人不到场,供方可进行下一步工作(需方应预料到在工厂作观察验证比现场见证时间更长. 6. .1.6指定的检验和试验用设备由供方提供
6.1.7 如有规定,需方代理人,供方代理人或供需双方代理人应在“检验员检验表附录H)上签名, 并写明日期
装运前,把完整的清单提交给需方
25
石油、石化和天然气工业一般用途汽轮机GB/T28573-2012解读
随着国家经济的快速发展和人民生活水平的提高,石油、石化和天然气等能源的需求不断增加。而作为这些能源转换的主要设备之一,汽轮机的重要性日益凸显。针对石油、石化和天然气工业领域中汽轮机的特殊需求,国家相关部门发布了GB/T28573-2012标准,旨在规范该领域中汽轮机的设计、制造和使用。
该标准对于石油、石化和天然气工业领域中汽轮机的基本要求进行了详细规定,包括了安全、可靠、高效、节能等方面的指标。在安全方面,标准要求汽轮机必须符合国家相关安全标准,同时还提出了涉及到燃气和蒸汽两种介质的特殊要求。在可靠方面,标准对汽轮机的寿命、维护等方面进行了详细规定,并要求制造商必须提供相应的技术支持和培训服务。在高效和节能方面,标准提出了具体的技术要求和测试方法,包括功率、效率、排放等指标。
除了基本要求外,该标准还对汽轮机的设计、制造和使用进行了细致的规定。其中,标准要求制造商必须根据用户的特定需求进行设计,同时还需要提供相应的技术文件、检验报告等;对于制造过程中的关键环节,如材料选用、加工工艺、试验等,也有详细的规定。此外,标准还对汽轮机的日常维护、保养、检修等方面进行了规范,以确保汽轮机在使用期间始终保持最佳状态。
总之,GB/T28573-2012标准的发布,为石油、石化和天然气工业领域中汽轮机的设计、制造和使用提供了明确的指导,有助于提升汽轮机的安全性、可靠性和效率,进一步促进了我国能源行业的发展。