GB/T29717-2013
滚动轴承风力发电机组偏航、变桨轴承
Rollingbearings-Windpowergeneratorsyawandpitchbearings
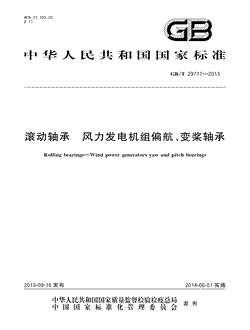
- 中国标准分类号(CCS)J11
- 国际标准分类号(ICS)21.100.20
- 实施日期2014-06-01
- 文件格式PDF
- 文本页数26页
- 文件大小1.28M
以图片形式预览滚动轴承风力发电机组偏航、变桨轴承
滚动轴承风力发电机组偏航、变桨轴承
国家标准 GB/T29717一2013 滚动轴承风力发电机组偏航、变桨轴承 Rolingbearin一windpowerenertorsyawamdpitehbearing 2013-09-18发布 2014-06-01实施 国家质量监督检验检疫总局 发布 国家标准化管理委员会国家标准
GB/T29717一2013 目 次 前言 范围 规范性引用文件 术语和定义 符号 轴承代号方法 偏航、变桨轴承结构型式和外形尺寸 技术要求 5 检测方法 检验规则 10标志 11防锈包装 12运输和贮存 20 13安装和保养 2r 附录A(资料性附录)轴承的安装与保养
GB/T29717一2013 前 言 本标准按照GB/T1.1一2009给出的规则起草 本标准由机械工业联合会提出. 本标准由全国滚动轴承标准化技术委员会(SAC/TC98)归口
本标准主要起草单位:洛阳LYC轴承有限公司
本标准参加起草单位;洛阳轴承研究所有限公司,成都天马铁路轴承有限公司、大连冶金轴承股份 有限公司、马鞍山经纬回转支承有限公司、北京京冶轧机轴承制造有限公司、西北轴承股份有限公司、瓦 房店轴承集团有限责任公司、上海斐赛轴承科技有限公司、国电联合动力技术有限公司
本标准主要起草人;董汉杰,庞碧涛、练松伟、谢兴会、徐玲玲,黄伟
本标准参加起草人;许正根、汪文革、,张宏伟、王书君、张富永、,王丽君、孙振生、赵联春、孙黎翔、 闻传涛、杨世宏
GB/T29717一2013 滚动轴承风力发电机组偏航、变桨轴承 范围 本标准规定了风力发电机组偏航、变桨轴承的代号方法、结构型式,外形尺寸、技术要求、检测方法、 检验规则、标志和包装等
本标准适用于风力发电机组偏航,变桨轴承(以下简称轴承)的生产检验和用户选型、验收
规范性引用文件 下列文件对于本文件的应用是必不可少的
凡是注日期的引用文件,仅注日期的版本适用于本文 凡是不注日期的引用文件,其最新版本(包括所有的修改单)适用于本文件
件
钢的低倍组织及缺陷酸蚀检验法 GB/T2261991 GB/T230.12009金属材料洛氏硬度试验第1部分;试验方法(A、,B,c、,D,E、F、G、H、K、 N,T标尺) GB/T231.1一2009金属材料布氏硬度试验第1部分:试验方法 GB/T308.1一2013滚动轴承球第1部分;钢球 GB/T1357一2008通用机械和重型机械用圆柱齿轮模数 GB/T19792001结构钢低倍组织缺陷评级图 GB/T41992003滚动轴承公差定义 GB/T5617一2005钢的感应淬火或火焰淬火后有效硬化层深度的测定 金属平均晶粒度测定法 GB/T63942002 GB/T6930一2002滚动轴承词汇 滚动轴承参数符号 GB/T781l2007 GB/T8597一2013滚动轴承防锈包装 GB/T97932012热喷涂金属和其他无机覆盖层锌,铝及其合金 GB/T10095.1一2008圆柱齿轮精度制第1部分;轮齿同侧齿面偏差的定义和允许值 GB/T10095.2一2008圆柱齿轮精度制第2部分;径向综合偏差与径向跳动的定义和允许值 GB/T10561一2005钢中非金属夹杂物含量的测定标准评级图显微检验法 GB/T18254一2002高碳铬轴承钢 GB/T20887.12007 汽车用高强度热连轧钢板及钢带第1部分;冷成形用高屈服强度钢 B/T5000.15一2007重型机械通用技术条件第15部分;锻钢件无损检测 大型合金结构钢锻件技术条件 JB/T63962006 JB/T70512006滚动轴承零件表面粗糙度测量和评定方法 JB/T10471一2004滚动轴承转盘轴承 HG/T23491992聚酰胺1010树脂 HG/T2811一1996旋转轴唇形密封圈橡胶材料 术语和定义 GB/T4199一2003,GB/T69302002界定的术语和定义适用于本文件
GB/T29717一2013 4 符号 GB/T7811一2007确立的以及下列符号适用于本文件
b:齿宽 D,轴承外径;对带外齿轴承为外圈外圆柱表面直径 D;外齿齿顶圆直径 D,;外圈安装孔直径 D.;钢球直径 D:外圈安装孔中心圆直径 d.轴承内径;对带内齿轴承为内圈内圆柱表面直径 d.;内齿齿顶圆直径 d.:;内圈安装孔直径 d:内圈安装孔中心圆直径 F;外齿轮对滚道的径向综合跳动 F;内齿轮对滚道的径向综合跳动 H;外圈高度 h;内圈上端面和外圈上端面的高度差 K;成套轴承外圈径向跳动 K a;成套轴承内圈径向跳动 m;模数 n,外圈安装孔个数 ;内圈安装孔个数 Sa:成套轴承外圈轴向跳动 S:成套轴承内圈轴向跳动 T:轴承高度 齿轮径向变位系数 ,Z :齿数 4;轴承单一外径偏差 A,;轴承单一内径偏差 Ar.:轴承实际高度偏差 轴承代号方法 5.1通用代号方法 5.1.1代号的构成 偏航,变桨轴承代号由前置代号、基本代号和后置代号构成,其排列顺序如下 前置代号 基本代号 后置代号 5.1.2前置代号 前置代号为“FD”,为“风电”两字汉语拼音首个大写字母的组合,前置代号与基本代号间用
GB/T29717一2013 “-”隔开
5.1.3基本代号构成 基本代号分为三部分,前部为结构型式代号和传动型式代号,中部为球直径(近似值),后部为球组 节圆直径
5.1.3.1结构型式代号 结构型式代号按表1的规定
表1结构型式代号 结构型式代号 结构型式 单排四点接触球式 0 03 双排同径四点接触球式 5.1.3.2传动型式代号 传动型式代号按表2的规定
表2传动型式代号 传动型式代号 传动型式 无齿式 渐开线圆柱齿轮外齿小模数 渐开线圆柱齿轮外齿大模数 渐开线圆柱齿轮内齿小模数 渐开线圆柱齿轮内齿大模数 5.1.3.3基本代号编制规则 基本代号编排时,结构型式代号和传动型式代号连写,前部、中部和后部之间用"”隔开 5.1.4后置代号 5.1.4.1后置代号排列顺序 后置代号分为两部分,前部表示轴承套圈材料及预先热处理方法,后部表示密封、技术要求等有 改变
5.1.4.2后置代号含义及编制规则 5.1.4.2.1套圈材料及预先热处理方法代号按表3的规定,在其代号前用“”和基本代号隔开
5.1.4.2.2当密封、技术要求等有改变时,用“K”或“K和数字组合”表示,如K、_K1、K2等,其含义用户 可咨询制造厂,代号与材料代号空半个汉字距
GB/T29717一2013 表3套圈材料及预先热处理方法代号 代号 套圈材料 预先热处理方法 调质处理 03 2CMG 调质处理 其他材料 13 5.1.5代号示例 示例 D-3.O.250.坚 Kl -密封、技术要求等改变 套圈材料为42CrMo,调质处理 -球组节圆直径为2500mm -球直径(近似值)为60mm 渐开线圆柱齿轮内齿小模数 单排四点接触球式 风电轴承 5.2其他代号 当用户对代号有特殊要求时.由制造厂与用户之间协商确定
偏航、变桨轴承结构型式和外形尺寸 结构型式 单排四点接触球式 6.1.1 单排四点接触球轴承见图1图3 图1无齿式单排四点接触球轴承
GB/T29717一2013 D 图2内齿式单排四点接触球轴承 D, 图3外齿式单排四点接触球轴承 6.1.2双排同径四点接触球式 双排同径四点接触球式见图4图6
图4无齿式双排同径四点接触球轴承
GB/T29717一2013 图5内齿式双排同径四点接触球轴承 D 图6外齿式双排同径四点接触球轴承 6.2外形尺寸 6.2.1单排四点接触球式轴承的外形尺寸见表4 2 6.2. 双排同径四点接触球式轴承的外形尺寸见表5
GB/I29717一2013 鲁 三 一 一 y 台 三 象 落 复 C 3 LO LP 9 s 昌 岛 8 园 鱼 员 9 8 品 二 品 2 路 器 3 8 品 路 司 8 2 路 路 科 一 N S N y 米 三 G 5 8 出 曾 8 三 " 8 品 品 盗 昌 8 A 一 ! 曾 曾 s
GB/T29717一2013 三 N 3 显 追 三 三 C m co o cm uo Lo un g 品 月 员 3 图 医 昌 苏 器 品 品 路 品 等 苏 品 8 路 品 路 路 路 怅 o3 3 S N m 8 乌 8 出 三 3 图 8 器 3 " 三 三 A m 义 g 曾 S s
GB/I29717一2013 的 丽 的 的 的 C ln P P in s 二 司 昌 3 贾 云 9 3 品 司 贾 司 路 易 一 S 3 二 o 盗 路 路 三 发 显 当 一 管 新 A 员 会
GB/T29717一2013 爸 一 E 可 C ln g P in LP 岛 品 品 司 三 监 送 8 品 品 品 品 品 s 路 贾 o 怅 S 三 9 三 二 出 8 多 三 8 多 三 多 一 多 三 篇 白 会 10o
GB/T29717一2013 监 多 C c ln 3 图 图 盘 贾 品 8 品 器 品 贾 苏 路 " o 怅 易 ! S 3 出 多 三 鸟 器 一 监 客 A 白 会
GB/T29717一2013 路 C n 空 n 二 uo 品 品 月 虽 E 9 s 品 兽 图 营 等 9 - 路 路 o 怅 S " 出 m 司 8 会 12
GB/T29717一2013 技术要求 7.1材料与热处理 7.1.1套圈 7.1.1.1轴承套圈一般采用42CrMo钢制造,其化学成分、,低倍组织和非金属夹杂物应符合表6一表8 的规定,其余要求符合JB/T6396一2006的规定,当用户有特殊要求时,也可采用性能相当或更优的其 他材料制造 表6材料化学成分 牌号 化学成分/% Mn s C Ni H Mo Cu 42CrMo e 0.41 0.600.17 1.00一 0.15" 0.45 0.80 0.37 1.20 0.25 0.30 0.20 0.025 0,0250,00020,0020 表7低倍组织级别 低倍组织类型 评级图 maX 第3级别图 中心疏松 2.0级 -般疏松 第3级别图 2.0级 偏析 第3级别图 2.0级 表8非金属夹杂物级别 细系 粗系 非金属夹杂物类型 mmaX 2,5级 1.5级 1.0级 2.0级 B 1.0级 1.0级 1.0级 1.0级 7.1.1.2轴承套圈调质后一40C低温冲击功KV不应低于27J,调质硬度为260HBw一300HBw. 其他力学性能指标应符合JB/T6396-2006的规定
7.1.1.3轴承套圈调质后平均晶粒度级别应符合GB/T6394一2002中6级一9级要求
轴承套圈调质后超声波检测不应低于JB/T5000.15一2007中质量等级为】级的要求
7.1.1.5轴承套圈滚道表面淬火后表面硬度为55HRC62HRC,其有效硬化层深度应符合表9的 规定
13
GB/T29717一2013 表9滚道有效硬化层深度 单位为毫米 30 50 >40一50 >3040 有效硬化层深度mimn 3.0 4.0 5.0 3.5 注,有效硬化层深度为滚道表面到硬度值为48HRc处的垂直距离
7.1.1.6轴承齿圈齿面齿根应进行表面淬火,表面硬度为50HRC60HRC,有效硬化层深度应符 合表10的规定
表10齿圈齿面和齿根有效硬化层深度 单位为毫米 模数 610 1016 1622 2228 齿面 2.5 3.2 3.6 2.0 有效硬化层深度 min. 齿根 0.6 1.0 l.4 l.8 2.2 注:有效硬化层深度为齿面或齿根表面到硬度值为40HIRC处的垂直距离 7.1.1.7轴承套圈存在软带时,软带宽度不应大于堵塞孔直径加35 将带堵塞孔套圈的软带设 mm 置在堵塞孔部位,双排同径轴承上下两排滚道软带一般放置于一处,非堵塞孔软带位置对应的非安装面 上应作明显的永久性标记“s” 7.1.2滚动体 轴承用钢球一般采用符合GB/T182542002规定的GCrl15或GCr15SiMn轴承钢制造,其尺寸、 公差等其他要求应符合GB/T308.1一2013的规定,当用户有特殊要求时,也可采用性能相当或更优的 其他材料
7.1.3保持架 偏航轴承用保持架一般采用符合HG/T2349-1992规定的聚酰胺1010树脂制造,当用户有特殊 要求时,也可采用性能相当或更优的其他材料
变桨轴承用保持架一般采用符合GB/T20887.1一2007规定的HR38oF钢板制造,当用户有特殊 要求时,也可采用性能相当或更优的其他材料
7.1.4密封圈 轴承用密封圈一般采用符合HG/T2811一1996规定的丁晴橡胶制造,在具有强酸、强碱、强紫外 线,臭氧等环境下应采用氢化丁腊橡胶制造,当用户有特殊要求时,也可采用性能相当或更优的其他 材料
7.2齿轮 7.2.1轴承套圈齿轮为渐开线圆柱齿轮
齿轮径向变位系数为.r=十0.5,当用户有特殊要求时,也可 根据用户需要选取其他系数 7.2.2轴承套圈齿轮模数应符合GB/T1357一2008的规定
7.2.3轴承套圈齿轮精度不应低于GB/T10095.1一2008和GB/T10095.2一2008规定的9级要求
当用户有特殊要求时,也可由制造厂与用户之间协商确定
14
GB/T29717一2013 7.3公差 7.3.1轴承的尺寸公差按表11的规定
7.3.2轴承的旋转精度按表12的规定
7.3.3轴承安装孔和定位孔的位置度应符合表13规定
尺寸公差 表11 单位为微米 " 士1000 H9 h9 非定位直径的4,按H12的规定
非定位直径的山,按h12的规定
表12旋转精度 单位为微米 d或D S,S K,K F、F max 1o 250 400 630 80 630 1000 100 14o 280 1000 1600 120 180 360 600 2500 60 220 420 2500 4500 200 28o 560 4500 6000 260 340 640 注1:当d或D不作为轴承的定位直径时,其K或K.可不予要求
注2:对悴火齿轮,齿轮径向跳动允许增大50%
内圈的旋转精度应按d查表确定 外圈的旋转精度应按D查表确定 表13安装孔和定位孔位置度 单位为毫米 安装孔位置度 定位孔位置度 安装孔中心圆直径 ax
2000 0.6 0.5 2000 0.7 0.5 注:带螺纹安装孔的位置度不应低于0.6mm
7.4表面粗糙度 轴承所有需防腐处理的表面粗糙度Ra不应低于3.2m
15
GB/T29717一2013 7.5游隙 轴承的轴向游隙值和径向游隙值不应大于零
7.6空载启动力矩和旋转力矩 轴承空载启动力矩和旋转力矩由制造厂与用户之间协商确定 7.7润滑 轴承初润滑时应填装用户指定的润滑脂,注脂量一般为轴承内部有效空间容积的60%一80%,也 可由制造厂与用户之间协商确定
装填的润滑脂应具备使用温度范围(一40C一150C、抗微动磨 损、极压性、抗水性、防腐性和良好的泵送性等基本性能要求
7.8润滑油孔 轴承通过油孔注油润滑,其注油螺纹孔规格一般为M10×1,排油螺纹孔规格一般为Ml4×1.5,当 用户有特殊要求时,油孔数量、位置和规格也可由制造厂与用户之间协商确定
7.9防腐处理 轴承除齿轮外的其他外露表面应按GB/T97932012进行热喷涂纯锌防处理,海用轴承应进行 喷漆处理,其具体防腐要求应满足表14的规定,当用户有特殊要求时,也可采用满足性能要求的其他防 腐方法
表14轴承防腐要求(除齿轮外) 防腐要求 轴承防腐表面 陆 地 海洋 锌层厚度为0.1 mm0." 2mm,厚度相互差锌层厚度为0.1 mm0.2 mm,厚度相互差 安装表面和配合止口 不大于0.05mm
不大于0,05mm
锌层厚度为0.1mm0.2nm,并进行喷漆 锌层厚度为0.1mm~0.2mm 非安装表面 处理,漆层厚度不应低于0.l6mm. 注,油漆品牌和喷漆操作规范的选择由供需双方依据偏航、变桨轴承具体工作环境确定 7.10寿命要求 轴承在正确安装、润滑和密封的条件下,使用寿命不应低于20年
7.11其他要求 7.11.1轴承套圈和钢球不应有白点,夹杂,表面不应有裂纹、锈蚀,烧伤、磕碰、软点等缺陷
7.11.2轴承滚道和齿面、齿根应进行无损探伤,不允许存在裂纹
在轴承齿轮最大径向跳动处标记三个齿,并在中间齿非基准端面上作永久性机械标识,其标识 7.11.3 般为数字“0” 7.11.4若有其他特殊要求时,可由制造厂与用户之间协商确定
16
GB/T29717一2013 检测方法 8.1材料检测 8.1.1化学成分的分析 套圈材料化学成分的分析应符合JB/T6396一2006的规定 8.1.2力学性能的试验 8.1.2.1取样方法 在每一调质炉中最后一个料盘锻件的中间位登放登一个加高件,在位于该加高件套圈壁厚的中间, 距端面12.5mm处沿圆周方向取一个拉伸试样和三个冲击试样,试样取样位置如图7所示 2.5mm 试样位置 图7试样取样位置 8.1.2.2 性能试验 套圈力学性能的试验方法应符合JB/T6396一2006的规定
8.1.3低倍组织的检验 套圈低倍组织的取样和检验方法应符合GB/T226一1991的规定,图片评级符合GB/T1979 2001的规定
8.1.4非金属夹杂物的测定 套圈非金属夹杂物的测定方法应符合GB/T10561一2005的规定
8.1.5平均晶粒度的测定 套圈平均晶粒度的测定方法应符合GB/T6394一2002的规定
8.2热处理检测 轴承滚道和齿面、齿根淖火后表面硬度的试验应采用里氏硬度计或超声波硬度计,其试验方法符合 GB/T230.1一2009和GB/T231.12009的规定,有效硬化层深度的测定方法应符合GB/T5617 2005的规定
17
GB/T29717一2013 3 8. 探伤检测 套圈超声波探伤和滚道、齿面、齿根无损探伤检测方法按JB/T5000.15一2007的规定
公差的测量 轴承尺寸公差、旋转精度和齿轮精度的测量方法按JB/T10471一2004的规定 8.5表面粗糙度的测量 轴承表面粗糙度的测量方法按JB/T7051一2006的规定
8.6游隙的测量 轴承游隙的测量方法按JB/T10471一2004的规定,游隙值为零即可
防腐层的检测 轴承表面防腐层厚度的测量方法和结合强度的试验方法按GB/T9793一2012的规定
8.8空载力矩的测试 空载启动力矩 8.8.1 空载启动力矩的测试方法如图8所示
将轴承内圈基准端面水平置于一平台上,将弹簧秤一端固 定在轴承外圈上,拉力方向应沿轴承切线方向且与轴承端面平行,拉动弹簧秤,当轴承从静止到开始转 动时,读出此时弹簧秤的读数,再乘以力臂(D/2)即为轴承的空载启动力矩
当用户有特殊要求时,制 造厂也可采用专用设备进行空载启动力矩的测定
8.8.2空载旋转力矩 空载旋转力矩的测试方法如图8所示
将轴承内圈基准端面水平置于一平台上,将弹簧秤一端固 定在轴承外圈上,拉力方向应沿轴承切线方向且与轴承端面平行,拉动弹簧秤.当轴承平稳运转时读出 此时弹簧秤的读数,再乘以力臂(D/2)即为牺承的空载旋转力矩
当用户有特殊要求时,制造厂也可 采用专用设备进行空载旋转力矩的测定
图8空载力矩测量方法示意图 8.9寿命试验 轴承寿命试验原理图见图9所示
一与用户之间协商确定
当用户有特殊爱家时.出可白秘边厂" 18
GB/T29717一2013 变桨轴承 偏航轴承 M 说明: F 轴承承受的轴向力 F 轴承承受的径向力; M -轴承承受的倾覆力矩
图g试验原理图 检验规则 出厂检验 9.1 轴承应经制造厂质检部门检查合格后并附有合格证方可出厂;轴承以下各项应100%检验,除防腐 和空载启动、,旋转力矩检测项目外,其余检验项目应在防腐处理前进行
检验项目应包括 -套圈的化学成分和机械性能; 套圈超声波无损探伤; 滚道和齿面、齿根硬度; 滚道和齿面、齿根有效硬化层深度 滚道和齿面、齿根探伤; 尺寸公差和旋转精度; 游隙; 防腐层厚度; 空载启动,旋转力矩; 外观质量; 用户要求检验的其他项目
9.2验收检验 验收检验的抽样方案、验收项目、接收质量由制造厂与用户之间协商确定
10 标志 10.1轴承应采用铭牌进行标志
铭牌安装在轴承软带附近的非安装表面上 10.2标志内容应包含轴承型号、编号,制造厂家和制造日期,当用户有特殊要求时,也可增加由制造厂 与用户之间协商的其他标志
防锈包装 轴承的齿轮防锈,依据用户使用要求执行
轴承的包装除不需要清洗和涂防锈油外,其余要求符合 19
GB/T29717一2013 GB/T8597一2013的规定
12 运输和贮存 12.1轴承在运输过程中,应做好防雨处理
轴承应水平放置在交通工具上固定,必要时可加辅助 支承 12.2贮存时应放于干燥、平整的室内,与化学药品及其他具有腐蚀性物品隔离开;若需多套轴承重叠 堆放时,每套轴承之间应沿圆周方向均匀放置三个以上高度相等的木垫块,且上,下层垫块的放置位置 应一致
13 安装和保养 轴承的安装与保养参见附录A
20
GB/T29717一2013 附 录A 资料性附录 轴承的安装与保养 A.1配合表面 每套轴承在安装使用前应对配合表面进行必要的检查,支承轴承的部件除应具有足够的刚度外,其配 合表面还应进行机械加工,清除表面杂物和毛刺
支承部件配合表面的技术要求应符合表A.1的规定
支承部件与轴承配合的表面平面度和在径向宽度上的倾斜度如图A.1所示
说明: 支承部件与轴承配合的表面平面度; 支承部件与轴承配合的表面径向宽度 dl -支承部件与轴承配合的安装孔中心圆直径; 支承部件与轴承配合的相邻安装孔间距 P -支承部件与轴承配合的表面倾斜度最高点 -在支承部件与轴承配合的安装孔中心圆表面上,每间距一个安装孔距离的倾斜度; S,S,S,S 支承部件与轴承配合的表面径向宽度h的倾斜度 图A.1支承部件与轴承配合的表面平面度和在径向宽度上的倾斜度 表A.1支承部件配合的表面技术要求 平面度 圆周两相邻单位长度 径向宽度6的 端面粗糙度 圆周两相邻单位长度 孔中心圆直径 L=1个安装孔距) 倾斜度 L=1个安装孔距 Ra D或d 相同方向倾斜度的变化量相反方向倾斜度的变化量 mmm S S. S. m mm mm Am m 1.25 400 630 100 50 630 1000 120 60 1.25 1000 80 1600 150 2.5 0.00013L. 0.00013L 1600 2500 200 l00 2.5 2500 120 250 2.5 4000 4000 6000 150 300 3.2 21
GB/T29717一2013 A.2安装方法 铀承的套圈一般具有淖火软带,用户在安装时应将软带位置置于非载荷区
安装时应先将轴承径 向定位,螺栓预紧时应采用星形对角多次紧固,并检查轴承的旋转情况
为保证轴承传动平稳,应在螺 栓完全拧紧之前,对齿轮进行啮合检查
拧紧螺栓时的预紧力,应为螺栓材料屈服极限的70%
安装 螺栓时应配备调质平垫圈,不允许使用弹簧垫圈
A.3安装螺栓预载荷 轴承在安装时其连接螺栓应达到一定的预载荷
常用螺栓的预载荷可参考表A.2的规定
表A.2各种螺栓的预载荷 螺栓强度等级 螺栓 8.8 12.9 10,9 直径 螺栓安装预紧载荷 拧紧力矩 螺栓安装预紧载荷 拧紧力矩 拧紧力矩 螺栓安装预紧载荷 mm N N N Nm Nm m 78 M12 38500 56000 117 66000 135 M14 53000 126 77000 184 216 90000 M16 72000 193 106000 297 124000 333 M18 91000 270 129000 387 151000 459 ME 387 166000 648 117000 558 194000 M22 146000 522 208000 747 243000 873 M24 168000 666 239000 954 280000 116 9g0 M27 221000 315000 1395 370000 1665 M3o 270000 385000 1350 1890 450000 2250 M33 335000 480000 560000 M36 395000 560000 660000 M69 475 000 670000 790000 M42 542000 772000 904000 需要采用螺 需要采用螺 需要采用螺 M45 635000 栓液压拉紧 905000 栓液压拉紧 059000 栓液压拉紧 装置 装置 装置 M48 714000 018000 l191000 857000 1221000 1429000 M52 M56 989000 1408000 648000 M6o 1156000 1647000 1927000 心
GB/T29717一2013 4 轴承的保养 A, 轴承应填充专用润滑脂
在填充润滑脂时,应边填充边转动轴承,使润滑脂不受钢球阻隔,均匀分 布,直至新润滑脂挤出油孔或密封唇为止
一般情况下,润滑脂每半年应填充新的润滑脂
在较恶劣的 环境条件下,可适当缩短注脂周期;轴承停用半年以上应加注新的润滑脂
滚动轴承风力发电机组偏航、变桨轴承GB/T29717-2013解析
随着气候变化和环保意识的提高,风力发电作为一种清洁能源得到了越来越广泛的关注。而滚动轴承作为风力发电机组重要的零部件之一,在其中也扮演着至关重要的角色。
风力发电机组通过叶片转动驱动转子旋转,进而产生电能。然而在实际运行过程中,由于多种原因(如风向变化等),风轮会相应地发生偏离方向的现象,称为偏航。这时候就需要通过滚动轴承来支撑转子,使其能够稳定转动。
除了偏航问题外,变桨轴承也是风力发电机组中需要考虑的问题。变桨是指根据叶片所处的风速和转子的运行状态,自动调整叶片的角度。这样可以使得叶片始终保持在最佳的工作状态,提高发电效率。而变桨轴承则负责支撑叶片的旋转,并确保其能够准确地调节叶片角度。
为了确保滚动轴承和变桨轴承的质量和可靠性,国家制定了GB/T29717-2013标准。该标准针对风力发电机组中常用的滚动轴承和变桨轴承进行了详细规定,包括产品结构、材料、制造工艺、检验方法等方面。这为风力发电机组的生产和使用提供了有力的技术支持。
总之,滚动轴承和变桨轴承作为风力发电机组中不可或缺的零部件,对于其性能和可靠性有着至关重要的影响。而GB/T29717-2013标准的制定,则进一步保证了其品质和安全性,为风力发电事业的发展提供了坚实的技术基础。
滚动轴承风力发电机组偏航、变桨轴承的相关资料
- 滚动轴承外球面球轴承铸造座技术条件GB/T27560-2011
- 滚动轴承机床主轴用圆柱滚子轴承GB/T27559-2011
- 滚动轴承带座外球面球轴承技术条件GB/T27555-2011
- 滚动轴承向心轴承定位槽尺寸和公差GB/T27556-2011
- 了解滚动轴承圆柱滚子轴承可分离斜挡圈外形尺寸GB/T20060-2011
- 风力发电机组设计要求GB/T18451.1-2012
- 小型垂直轴风力发电机组GB/T29494-2013:原理、特点与应用
- 低温型风力发电机组GB/T29543-2013介绍
- 风力发电复合材料整流罩GB/T29553-2013介绍
- 风力发电复合材料机舱罩GB/T29760-2013解读
- 滚动轴承风力发电机组偏航、变桨轴承GB/T29717-2013解析
- 风力发电设备用轴承钢第1部分:偏航、变桨轴承用钢GB/T29913.1-2013
- 船舶操纵性第2部分:回转和偏航纠正
- 滚动轴承风力发电机组偏航、变桨轴承GB/T29717-2013解析
- 风力发电设备用轴承钢第1部分:偏航、变桨轴承用钢GB/T29913.1-2013
- 滚动轴承风力发电机组偏航、变桨轴承GB/T29717-2013解析