GB/T34370.11-2020
游乐设施无损检测第11部分:超声导波检测
Nondestructivetestingofamusementequipments—Part11:Ultrasonicguidedwavetesting
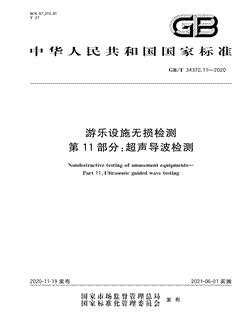
- 中国标准分类号(CCS)Y57
- 国际标准分类号(ICS)97.200.40
- 实施日期2021-06-01
- 文件格式PDF
- 文本页数17页
- 文件大小4.07M
以图片形式预览游乐设施无损检测第11部分:超声导波检测
游乐设施无损检测第11部分:超声导波检测
国家标准 GB/T34370.11一2020 游乐设施无损检测 部分.超声导波检测 第 Nondestruetivetestingofamusementequipments Part11:Ultrasonicguidedwavetesting 2020-11-19发布 2021-06-01实施 国家市场监督管理总局 发布 国家标涯花管理委员会国家标准
GB/T34370.11一2020 次 目 前言 范围 2 规范性引用文件 3 术语和定义 方法概要 安全要求 人员要求 6 检测设备和器材 检测工艺规程 检测程序 检测结果分级和处理 1C 1 13 检测记录与报告
GB:/T34370.11一2020 前 言 GB/T34370《游乐设施无损检测》分为以下11个部分 第1部分:总则; 第2部分:目视检测; 第3部分;磁粉检测 第4部分;渗透检测; 第5部分;超声检测 第6部分;射线检测 第7部分;涡流检测 第8部分声发射检测 第9部分漏磁检测 第10部分;磁记忆检测 第11部分;超声导波检测
本部分为GB/T34370的第ll部分
本部分按照GB/T1.12009给出的规则起草
本部分由全国索道与游乐设施标准化技术委员会(SAC/TC250)提出并归口 本部分起草单位;特种设备检测研究院、华中科技大学、浙江大学、杭州浙达精益机电技术股份 有限公司、深圳华侨城文化旅游科技集团有限公司、山东省特种设备检验研究院有限公司、广东省特种 设备检测研究院、浙江优尔特检测科技有限公司
本部分主要起草人;沈功田,吴占稳、沈永娜、武新军、唐志峰、吕福在、张鹏飞、陈会明、李坚、 邹易清、陈红军、邱治国、柳章龙、万强、王宝轩、张文君
GB:/T34370.11一2020 游乐设施无损检测 第11部分:超声导波检测 范围 GB/T34370的本部分规定了游乐设施超声导波检测和结果评定方法
nmm80mm 本部分适用于游乐设施壁厚为4n 的金属板(含槽钢、方形梁,直径为16 mm一 mmmm185mtm 1的钢管,直径为12 n的钢丝绳和拉索,直径为16 2000mm、壁厚为2mm80mm mm一 80mm 的拉杆等构件的超声导波检测及结果评定 规范性引用文件 下列文件对于本文件的应用是必不可少的
凡是注日期的引用文件,仅注日期的版本适用于本文 件
凡是不注日期的引用文件,其最新版本(包括所有的修改单)适用于本文件
GB/T12604.4无损检测术语声发射检测 GB/T20306游乐设施术语 GB/T20737无损检测通用术语和定义 GB/T28704无损检测磁致伸缩超声导波检测方法 GB 31211无损检测超声导波检测总则 34370.1游乐设施无损检测第1部分;总则 GB 34370.3游乐设施无损检测第3部分;磁粉检测 GB 34370.4游乐设施无损检测第4部分;渗透检测 GB 34370.5游乐设施无损检测第5部分;超声检测 GB GB/T34370.6游乐设施无损检测第部分;射线检测 GB/T34370.7游乐设施无损检测第7部分;涡流检测 GB/T34370.9游乐设施无损检测第9部分;漏磁检测 GB/T34370.10游乐设施无损检测第10部分;磁记忆检测 术语和定义 GB/T12604.4.GB/T20306.GB/T20737.,GB/T28704和GBT31211界定的术语和定义适用于 本文件
方法概要 4.1超声导波检测原理 根据被检构件特征,采用一定的方式在构件中激励出沿构件传播的超声导波,当该导波遇到缺陷 时,会产生反射回波,采用接收传感器接收到该回波信号,通过分析回波信号特征和传播时间,即可实现 对缺陷位置和大小的判别
GB/T34370.11一2020 磁致伸缩超声导波检测方法是利用磁致伸缩效应在构件中产生的超声导波,对构件实施检测的 种方法
压电式超声导波检测方法是利用压电效应在构件中产生的超声导波,对构件实施检测的一种方法
板的超声导波检测方法 板类的超声导波检测一般采用SH波或L.amb波进行检测,sH模态的超声导波一般采用薄片式磁 致伸缩换能器进行激励,Lamb波一般采用压电式超声导波换能器进行激励
板类压电式超声导波的 检测原理见图1,板类磁致伸缩超声导波的检测原理见图2
工字钢、槽钢及方形梁等构件的超声导波 检测方法可采用板的超声导波检测方法
压电超声导波换能器 图1板类压电式超声导波的检测原理 激励线圈 磁致伸缩带材 图2板类磁致伸缩超声导波的检测原理 4.3管的超声导波检测方法 管件等被检测工件主要特征为中空型圆柱体结构,直径大于20mm以上,一般采用磁致伸缩超声 导波(间接法)或压电式超声导波进行检测
磁致伸缩超声导波一般采用扭转剪切模态对管件进行检 测,压电式超声导波一般采用纵波模态对管件进行检测
磁致伸缩超声导波为基于磁致伸缩效应在磁致伸缩带上产生机械振动,通过干耦合或胶耦合的方 式将振动从磁致伸缩带传递到被检构件上形成导波,实现导波激励;并通过相同的耦合方式将导波从被 检构件传递回磁致伸缩带,并基于逆磁致伸缩效应实现导波接收
该方法既适用于铁磁性材料的检测 也适用于非铁磁性材料的检测,其检测原理如图3所示
这种方法的超声导波传感器包括线圈和磁致 伸缩带两部分,磁致伸缩带需要在使用前进行预磁化
GB:/T34370.11一2020 激励线圈 -一 磁致伸缩带材 图3管件磁致伸缩超声导波的检测原理 压电式超声导波是基于逆压电效应在压电材料上产生机械振动,通过干耦合或胶合的方式将振 动从压电晶片传递到被检构件上形成导波,实现导波激励
通过相同的耦合方式将导波从被检构件传 递回压电晶片,并基于正压电效应实现导波的接收
该方法既适用于铁磁性材料的检测,也适用于非铁 磁性材料的检测,其检测原理如图4所示
压电式超声导波管件检测通常由圆周均布的阵列化压电探 头组成
压电超声导波换能器 -一 - 图4管件压电式超声导波的检测原理图 4.4杆、索、绳的超声导波检测方法 杆,索、绳类构件主要特征为小直径实心钢构件,横截面外轮廓曲率很小,一般超声导波换能器难以 安装在被检测工件的外表面,且被检工件一般长度很长
杆,索、绳类构件宜利用磁致伸缩超声导波检测方法(直接法)激励纵向模态的导波进行检测
该方 法是利用材料本身的磁致伸缩效应在构件中直接激励和接收导波,该方法只适用于被检对象为铁磁性 材料的检测,其检测原理图如图5所示
这种方法的传感器由激励线圈、检测线圈和磁化器三部分组 成
磁化器用以提供磁致伸缩效应的偏置磁场,可采用电磁或永磁的方式加载
宜用收发分离、脉冲回 波式的检测方式
检测线圈 张励找国 M 磁化器 图5杆、索、绳类超声导波检测原理
GB/T34370.11一2020 5 安全要求 本章没有列出进行检测时所有的安全要求,使用本标准的用户应在检测前建立安全准则
检测过程中的安全要求至少包括 在实施检测前,应对检测过程中可能伤害检测人员的各种危险源加以辨识,并对检测人员进行 a 培训和采取必要的保护措施 b) 检测人员应遵守被检件现场的安全要求,穿戴防护工作服和佩戴有关防护设备 应注意避免各种安全隐患,例如碰伤、触电、跌落、挤压、剪切、缠绕、滑倒、溺水、烫伤等; c 在高空进行操作时,应考虑人员、检测设备器材坠落等因素,并采取必要的保护措施 d 在游乐设施运行状态下进行检测时,应制定有针对性的安全措施
e 人员要求 6 从事游乐设施超声导波检测工作的人员,应符合GB/T34370.1的有关规定
检测设备和器材 7.1检测仪器系统构成和工作原理 超声导波检测仪器系统构成如图6所示
其工作原理为;根据被检构件计算其频散曲线,选择导波 模态和激励信号频率;计算机控制信号发生单元,产生所需频率的信号源,经功率放大单元放大后驱动 传感器产生所需模态的导波并在被检构件内传播;当导波在构件内传播遇到腐蚀等缺陷时会产生反射 回波被传感器接收到;前置放大器将传感器接收到的信号放大后传输到信号主放大器,通过A/D转换 输人计算机,计算机进行信号分析处理后,得到检测信号波形及结果 激励单元 频散曲线软件 传感器 功放单元 信号发生单元 信号采集 前置放大器 主放大器 计算机 分析软件 信号处理单元 图6超声导波检测仪器系统构成 7.2导波模态与频率的选择 7.2.1概述 在导波检测中,首先要得到被检测对象的频散曲线,部分构件需要考虑导波在被检构件截面上的波 结构,然后根据频散曲线和波结构选择合适的导波模态和正确的检测频率,才能够保证检测的正确实 施
由于不同频率的导波波长不同,对不同损伤有不同的灵敏度,导波检测过程中宜采用多种频率或扫 频的方式
GB:/T34370.11一2020 7.2.2频散曲线计算方法 对于频散曲线的求取,一般是首先建立被检测对象的Navier波动方程,求出波在被测构件中传播 的位移和应力表达式,然后根据被检构件的位移应力等边界条件建立频散方程,该方程为超声波频率 /)与波传播速度(u)的函数,求解频散方程即得到/关于u的曲线,即频散曲线
应根据被检构件选择合适的计算方程和下列参数,计算超声导波在构件中传播时的频散曲线 材料密度; a b 材料弹性模量; c 材料泊松比; d)构件的内径和外径对于管材、直径(对于棒材和缆索)或壁厚(对于板材)
图7是一典型管类频散曲线示意图
对于L(O,l)模态,在频率区城1是非频散的
对于L(0,2) 模态,在频率区域2是非频散的
对于TO,l)模态,在整个频率区间是非频散的
图8为典型的板类 频散曲线示意图
L(0,2) L(O,1) 频率区域1 频率区域2 T(O,1) 频率 图7典型的管类频散曲线示意图
GB/T34370.11一2020 频散曲线相速度 8000 SH2 7000 iSHn 6000 S0 5000 00o0 SH0 3000 A0 2000 1000 wo7To0 100 频率/Hz 图8典型的板类频散曲线示意图 7.2.3检测波形模式选择 7.2.3.1板类被检构件 对于板类构件的检测,可根据壁厚选择超声导波的检测频率,首先应根据频散曲线选择模态,导波 模态一般为SH0,、A0,S0波,然后根据波结构分析超声导波在板厚度方向的位移分布情况,一般情况整 个板厚度方向的位移分布差异不超过20%,对于宽度大于300nmm的板,宜采用超声导波B扫检测 方式
7.2.3.2管类被检构件 对于管类构件根据直径和工况的不同,可选择不同形式的超声导波,其选择方法如下 对于充液的管件,宜采用扭转模态的超声导波进行检测 a D)公称直径DN20DNI00的管件,宜采用T(0,l、,L(0,l、L(0,2)模态的超声导波,检测方式 宜采用A扫方式; 公称直径DNI00DN800的管件,宜采用T(0,l)L(0,l)、L(0,2)以及T(n,1)模态的超声 导波,检测方式宜采用A扫或B扫方式,必要时可采用上述多种方式的组合进行检测 公称直径大于DN800的管件,宜采用T(n,1)模态,检测方式为超声导波B扫
d 7.2.3.3杆、索、绳等被检构件 在低频区域,弯曲模态导波频散严重,不适于作为检测模态;纵向模态和扭转模态频散较小,适宜作 为检测模态
扭转模态不适宜作为该类构件的检测模态
纵向模态导波的轴向振动位移远大于径向振动位移 且在构件的截面分布均匀,适合作为检测模态
对于端面无法安装换能器的杆,索,绳类被检构件,宜采用磁致伸缩换能器(直接法)进行导波检测
对于直径为12mm以上,长度为1000m一2000m的金属绳索类多丝构件,该类构件常作为支撑和牵 引结构,构件的两个端面一般不可触及,可重点检测两端锚固区,中间区域采用多次移动分段检测法;对 于直径大于16mm,长度大于10m的拉杆,换能器布置方案与绳索构件相同,宜选择纵向模态进行 检测
GB:/T34370.11一2020 对于长度小于1m的棒、轴,销、螺栓,地脚螺栓等端面可安装换能器的被检构件,宜首先采用压电 换能器在被检构件的端面进行激励,检测模态一般为纵波模态
7.3超声导波传感器 7.3.1传感器的分类 按照不同的搐触方式,产生超声波的工作原理.激励与接收传感器的导波模态、检测方式,传感器分 类如下 按传感器与被检构件的接触方式分为干鹏合式传感器、粘结式传感器、非接触式传感器,其中 a 干耦合式传感器和粘结式传感器统称为接触式传感器 5 按传感器产生超声波的工作原理分为压电式、磁致伸缩式、电磁超声式,激光超声式 按传感器激励与接收的导波模态分为纵向导波传感器、扭转导波传感器、弯曲导波传感器、复 合导波传感器; d 按检测方式分为A扫描传感器、B扫描传感器
7.3.2传感器的选择 由于不同的传感器对不同的模态导波和缺陷的检测精度不同,选择传感器应考虑如下因素 构件的材料特性,如是否导电或导磁等; aa b) 构件的几何形状,如管材、棒材、线材、型材、板材等 构件的外部状况,如表面可接近状况,包覆层材料等; c 构件的工作环境状况,如工作温度、工作介质和承载状态等; d 检测目的和检测缺陷的类型等
e 7.3.3传感器的安装 根据传感器的不同类型,其安装中主要考虑以下因素 对于接触式传感器,被检构件表面应清理干净、平整,以提高耦合效率 对于压电式传感器,其安装可参考常规超声检测中对传感器的要求; b 对于非接触式传感器,应尽可能靠近被检构件,以减小外界电磁、振动等干扰 c 7.4激励单元 激励单元的功能主要是产生相应的激励信号,进而驱动激励传感器在构件中激发出相应模态的导 波
应根据构件状况、传感器类型、频散曲线计算结果及检测的缺陷类型选择合适的激励单元
7.5信号处理单元 信号处理单元是将接收传感器接收到的信号进行放大,滤波等调理后,通过A/D转换将信号输人 到计算机
信号处理单元主要包括前置放大器,主放大器和A/D转换器
前置放大器将来自传感器的信号转换成低阻抗信号,便于信号传输 主放大器是将来自前置放大器的信号再次放大,同时采用带通滤波器去除干扰噪声
A/D转换器是将模拟信号转换成数字信号,输人到计算机
A/D转换器的采样频率应至少大于激 励频率的10倍
信号处理单元应与传感器、激励单元、采用的导波模式和检测目的相匹配
7.6信号采集与分析软件 超声导波信号采集与分析软件应至少包含以下功能
GB/T34370.11一2020 频散曲线的计算; a b 信号采集; 信号存储; c d)信号分析; e 距离-波幅(DAC)曲线的绘制 fD 频率-距离-波幅云图的绘制; 信号回放; 8 信号定位
h 对于B扫描检测方式,还需包含B扫描信号成像功能
7.7试样 7.7.1校准试样 校准试样用于对检测设备进行灵敏度和各种功能的测试
校准试样应选用压力管道常用的无缝钢 管制作,应具有2%、4%,8%和10%截面损失率的横向环形切槽各 -一个,切槽的宽度在0.5mm2mm 的范围内,深度方向的公差不大于士0.2mm
校准试样的长度、厚度和切槽位置的要求见表1
校准试样的要求 横向环行切槽的位置(距试样左端 外径D 厚度T 长度L 序号 m mm mm m 2% 10% 4% 8% 50>D>10 >2 >18 13 17 150>D50 >4 >24 13 18 23 11 18 32 1000>D>150 >10 34 25 7.7.2对比试样 对比试样用于对被检构件上缺陷截面损失率当量的评定
对比试样应采用与被检测构件材料性能及几何形状相同或相近的材料制作,试样的长度至少为仪 器可探测9%截面损失率人工缺陷距离的1.2倍,且不小于12m.
除合同有关各方另有约定之外,应按如下要求加工对比试样 对于管材构件,在对比试样上至少4个部位外表面分别加工出多个直径相同、深度为壁厚 a 40%的平底孔;每处平底孔的数量应分别按截面损失率的2%、4%,8%和10%进行计算,平底 孔在环向间距应均匀分布,在纵向间距的距离应大于1m,深度的公差不大于士0.2mm;试样 两端的平底孔应至少距试样端部1 md 对于板类构件,在对比试样上 个部位外表面分别加工出多个直径为5mm~10mm、深 b 至少 度为2mm5mm的平底孔;每处平底孔的数量应分别按截面损失率的2%、4%、8%和10% 进行计算,平底孔在环向间距应均匀分布,在纵向间距的距离应大于1m,深度的公差不大于 士0.2mm;试样两端的平底孔应至少距试样端部lm 对于线状捆扎的钢索、钢丝绳或拉杆等构件,在对比试样上4个部位分别加工出线状材料的断 口;每处断丝的数量应分别按截面损失率的2%、4%、8%和10%进行计算,同一处断丝应紧密 相邻;试样两端的断口应至少距试样端部1m,不同部位断口的间距应大于1m,在环向应均 匀分布
GB:/T34370.11一2020 7.8检测设备的维护和校准 应制定书面规程,对检测设备进行周期性维护和检查,以保证仪器功能
在现场进行检测之前,应在实验室内选择相应规格的校准试件对检测仪器进行校准,若检测结果与 已知试件缺陷分布相符,则表明仪器正常
在现场进行检测时如怀疑设备的检测结果,应对设备进行功能检查和调整,并对每次维护检查的 结果进行记录
检测工艺规程 8.1通用检测工艺规程 从事游乐设施超声导波检测的单位应按GB/T34370.1和本部分的要求制定通用检测工艺规程 其内容至少应包括如下要素 文件编号 a 适用范围 b 引用标准、法规 c d 检测人员资格; 检测仪器设备:传感器、传感器夹具、信号线、前置放大器、电缆线、仪器主机、检测数据采集和 分析软件等; 被检件的信息;几何形状与尺寸、材质、设计与运行参数 f 检测覆盖范围及传感器型号的确定; g 被检件表面状态及传感器安装方式 h 检测时机 对比试件及距离-波幅曲线的绘制, j k 检测过程和数据分析解释; 检测结果的评定; m检测记录、报告和资料存档; 工艺规程的编制审核和批准人员; n 编制日期
o 8.2检测工艺卡 对于每类构件的超声导波检测,应根据实际情况,按照GB/T34370.1,本部分和通用检测工艺规程 制定超声导波工艺卡
检测工艺卡内容应至少包括 工艺卡编号 a 检测执行的标准; b 被检测构件的信息,包括;设备名称、编号、材料和几何尺寸等 c 检测仪器设备;名称,规格型号、编号等; d 检测方式、传感器型号; 检测时机 被检件表面状态及传感器安装方式 g h 检测示意图; 对比试件及距离-波幅曲线的绘制;
GB/T34370.11一2020 检测过程和数据分析解释; k 检测结果的分级及处理方式; D 检测记录、报告和资料存档; 工艺规程的编制审核和批准人员 m 编制日期 n g 检测程序 9.1检测前的准备 9.1.1资料审查 资料审查应包括下列内容 a 被检构件制造文件资料;产品合格证、质量证明文件、竣工图等,重点了解其类型、结构特征和 材质特性等; b 被检构件运行记录资料;运行参数、工作环境载荷变化情况以及运行中出现的异常情况等; c 被检构件检验资料;历次检验与检测报告; d 被检构件其他资料:维护、保养、修理和改造的文件资料等
9.1.2现场勘察 在期察现场时应找出所有可能影响检测的障碍和可能出现的噪声源,如内部或外部部件的移动、 电磁干扰和机械振动等;应设法尽可能排除这些干扰源
9.1.3检测工艺卡的编制 对于每个被检构件,根据使用的仪器和现场实际情况,按照8.1和8.2的规定,编制被检构件超声导 波检测工艺卡;确定超声导波传感器型号、安装的部位和表面条件,画出被检构件结构示意图,确定检测 的次序等
9.1.4检测条件确定 根据被检件材料特性、结构特征、几何尺寸的大小,被检件对比试件的距离-波幅曲线以及检测的目 的,确定传感器安装的部位和表面条件要求
9.2距离-幅度曲线的绘制 应采用7.7.2规定的对比试样在实验室内经过实测绘制距离-波幅曲线
该曲线族由记录线、评定 线和判废线组成;记录线由2%截面损失率的人工缺陷反射波幅直接绘制而成,评定线由4%或8%截 面损失率的人工缺陷反射波幅直接绘制而成(评定线指标可根据检测现场情况选择4%或8%),判废线 由10%截面损失率的人工缺陷反射波幅直接绘制而成
记录线以下(包括记录线)为I区,记录线与评 定线(包括评定线)之间为I区,评定线与判废线之间为区,判废线及其以上区域为N区,如图9所示
10
GB:/T34370.11一2020 V区 区 1废 评定生 I区 起生 I区 背景噪声线 距离/mm 图9距离-波幅曲线示意图 9.3传感器的安装 传感器的安装应满足如下要求: 按照确定的检测方案在被检件上确定传感器安装的具体位置,传感器的安装部位尽应可能远 a 离被检件连接,支座等结构复杂部位; b 对传感器的安装部位进行表面处理,使其满足传感器的安装要求 c 将传感器压在被检件的表面,使传感器与被检件表面达到良好的声鹏合状态 采用机械夹具,磁夹具或其他方式将传感器牢固固定在被检件上,并保持传感器与被检件和固 d 定装置的绝缘
9.4检测 9.4.1检测仪器调试 检测仪器的调试包括下列步骤 将传感器前置放大器与仪器主机连接 a b 打开仪器开关通电,并按仪器制造商规定的时间预热,使仪器达到稳定工作状态; c 按照被检件的具体情况和频散曲线计算确定的检测频率等设定仪器的工作参数 d)对被检构件发射超声导波信号,观察构件的端头,接头,焊缝、外部支撑等部位产生的超声导波 反射信号,测量被检件超声导波传播的波速; 进一步调节仪器工作参数,使仪器处于良好的工作状态
9.4.2A扫描检测信号的分析和解释 检测信号的分析和解释通常需要参考相关试验建立的数据库,至少应包括如下内容 采用调节好的仪器,对被检构件进行检测,观察和记录出现的超声导波反射回波信号 a b)对于出现的超声导波反射回波信号,首先确定这些信号是否是由构件的端头、接头、焊缝、外部 支撑等部位产生的,如确定即可排除 对于被检件上无明显几儿何形状变化部位的超声导波回波信号,可以确定为材料损失缺陷引起 11
GB/T34370.11一2020 的超声导波回波信号,应首先确定这一回波信号的反射部位,并加以标识,然后进行检测结果 评价和处理
g.4.3B扫描成像检测信号的分析和解释 B扫描检测相对A扫描检测增加一个垂直于导波传播方向的位置信息,其检测信号的分析和解释 至少包含如下内容 采用调节好的仪器,采用B扫描传感器,对被检构件进行B扫描检测,观察和记录出现的超声 a 导波反射回波信号并绘制B扫描图像; b 对于绘制的B扫描图像信号,结合增加的位置信息,可首先进行特征定性分析,然后确定这些 信号是否是由构件的端头,接头、缝,外部支撑等部位产生的,如确定即可排除; 对于被检件上无明显几何形状变化部位的超声导波回波信号,可以确定为材料损失缺陷引起 的超声导波回波信号,对于同一声程位置含有多个反射回波颜色块,可以首先确定该位置处疑 似缺陷的数量,并加以标识,然后进行检测结果评价和处理
表2列举了管件采用B扫描检测时,部分管件特征的定性分析
一管件采用B扫描检测时的导波检测成像图,图中可以通过管件特征的周向信息分析 图10为某 出管件上的焊缝特征和缺陷特征,并且可以分辨同一轴向上的两个缺陷
表2管件中B扫描检测特征定性分析 类别 B扫描成像特点 典型特征结构 全周向特征 在同一轴向距离下管件所有周向位置均有回波 焊缝、法兰等 对称性周向特征 在同一轴向距离下管件周向均匀间隔特征 对称性焊接支撑架等 单 周向特征 在某一轴向距离下管件周向含有某一特征 腐蚀缺陷、单一焊接支架、仪表三通等 焊缝 焊缝 盲区 300 3 200 100 0.5 1.5 声程/m 图10管件采用B扫描检测时的导波检测成像图 检测结果分级和处理 10 0.1检测结果分级 将超声导波检测发现的缺陷信号与距离-波幅曲线进行比对分级,反射波幅在I区的为I级,在I 区的为I级,在区的为级,在区的为级,在V区的为V级
12
GB:/T34370.11一2020 10.2不可接收信号的确定与处理 10.2.1概述 超声导波检测给出的是缺陷当量,由于腐蚀、机械损伤等金属损失缺陷的大小和形状与人工缺陷不 同,且被检构件的实际几何尺寸与对比试样间存在差异,导致检测结果显示的缺陷当量值与其真实缺陷 会存在一定的差异,因此不可接收信号的水平的确定应根据被检件的具体情况由用户和检测人员协商 确定
0.2.2基于距离-波幅曲线分级的确定 用户参与确定的,以用户的要求为准确定不可接收信号的等级;用户不参与确定的,由检验员确定 不可接收信号的等级,一般检测结果判为II级、IV级和V级的信号,即为不可接受的信号
10.2.3基于被检件上真实缺陷的确定 可以首先对检测发现的前三个最大的缺陷信号部位,按10.2.4规定的方法进行复检,根据复检结 果来逐步确定不可接收缺陷信号的水平
0.2.4不可接收信号的处理 对于确定的不可接收信号,需要采用以下方法进行复检 首先,采用目视和小锤敲击的方法进行检测,用以分辨是位于外表面或内部的缺陷 aa b 对于外表面缺陷可采用深度尺直接测量缺陷的深度; 对于管状或板状的内表面缺陷,应采用双晶直探头进行超声检测测量,以更精确的测量缺陷的 深度,超声检测方法按GB/T34370.5执行; d 对于其他形状构件的内表面缺陷,按照GB/T34370.3GB/T34370.7,GB/T34370.9 GB/T34370.10规定,选择合适的无损检测方法进行复检 必要时,经用户同意,也可采用解剖抽查的方式进行验证
检测记录与报告 11.1检测记录 检测记录的主要内容不应少于8.2和l1.2规定的内容
11.2检测报告 检测报告应至少包括下列内容 委托单位的信息; a b 检测单位的信息; 被检构件的信息,包括:设备名称、编号、材料和几何尺寸等; c d 执行的标准、规范和相关规定文件; e 检测仪器型号、检测方式、传感器型号及固定方式; 检测仪器工作参数设置; 距离-波幅曲线; 8 h 检测示意图; 检测软件名及数据文件名; 13
GB/T34370.11一2020 检测结果分析及分级; k检测结论; D 检测人员、报告编写人和审核人签字及资格; 检测日期
m 14
游乐设施无损检测第11部分:超声导波检测GB/T34370.11-2020
作为一种高风险、高安全要求的设备,游乐设施的安全问题一直备受关注。无损检测技术是保证其安全性的重要手段之一。而超声导波检测则是这些技术中的一个重要组成部分。
超声导波检测是利用超声波在固体材料中传播的特性进行缺陷检测的一种方法。它可以检测出各种形状、大小和方向的缺陷,包括裂纹、毛刺、夹杂等。同时,该方法还具有检测速度快、精度高等优点。
GB/T34370.11-2020是我国在此方面最新发布的标准。该标准规定了超声导波检测在游乐设施中的应用范围、试验方法和评定标准等内容。其中,重点介绍了以下几个方面:
- 检测设备及其性能要求
- 试验方法与评定标准
- 缺陷的分类、评定与记录
- 检测报告的编制
在实际应用中,超声导波检测已经得到了广泛的应用。例如,在游乐设施的安全检测中,该方法可以对轮毂、轴承、螺栓等关键部位进行无损检测,以确保设施的安全可靠。
总之,超声导波检测作为一种高效、精准的无损检测技术,可以为游乐设施的安全监测提供有力支持,同时也必须按照GB/T34370.11-2020的标准来进行操作。