GB/T34001-2016
中国修船质量标准
Chinashiprepairingqualitystandard
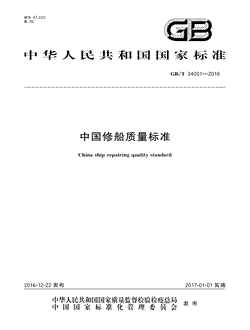
- 中国标准分类号(CCS)R30
- 国际标准分类号(ICS)47.020
- 实施日期2017-01-01
- 文件格式PDF
- 文本页数152页
- 文件大小1.76M
以图片形式预览中国修船质量标准
中国修船质量标准
国家标准 GB/T34001一2016 修船质量标准 Chinashiprepairingqualitystandardi 2016-12-22发布 2017-01-01实施 国家质量监督检验检疫总局 发布 国家标准化管理委员会国家标准
GB/T34001一2016 93 7.4吊艇架 95 装 95 8.1货舱盖 99 8.2固定钢质梯 101 8.3钢质门 103 8.4舷窗 104 8.5小舱口 8.6舷梯 105 107 管系 管路 9.1 107 9.2阀件 1l0 113 10电气工程 10.1 电缆 电机 10.2 ll6 10.3配电板 120 10.4分配电箱及控制箱 122 11空调、冷藏及通风装置 123 11.1空调及冷藏装置 123 11.2通风装置 125 消防工程 12 126 12.1水消防系统 126 12.2固定式探火和失火报警系统 128 12.3固定式气体灭火系统 128 12.4泡沫灭火系统 129 12.5细水雾、水雾和自动喷水器系统 130 12.6固定化学干粉系统 132 涂装工程 13 32 13.1钢材表面处理 132 13.2涂层 134 专用设备 14 36 14.1不锈钢液货舱 136 14.2惰性气体装置 137 14.3挖泥船泥泵装置 138 14.4挖泥船饺刀 141 14.5挖泥船泥斗 142 14.6滚装船跳板装置 143 14.7大型集装箱船引水门 144 145 14.8集装箱船绑扎桥及集装箱底座 147 参考文献
GB/T34001一2016 前 言 本标准按照GB/T1.1一2009给出的规则起草 本标准由工业和信息化部提出 本标准由全国海洋船标准化技术委员会(SAC/TC12)归口
本标准起草单位:中远船务工程集团有限公司、船舶工业综合技术经济研究院、大连中远船务 工程有限公司、广东中远船务工程有限公司、上海中远船务工程有限公司、舟山中远船务工程有限公司、 天津修船技术研究所、中船澄西船舶修造有限公司、船舶工业行业协会修船分会、船级社、山海 关船舶重工有限责任公司、上海华润大东船务工程有限公司,大连辽南船厂、友联船厂(蛇口)有限公司、 中海工业有限公司青岛北海船舶重工有限责任公司、上海船厂船舶有限公司中船澄西船舶(广州)有 限公司、大连远洋运输公司、中船黄埔文冲船舶有限公司,舟山市龙山船厂有限公司舟山万邦永跃船舶 ,天津新港船舶重工有限责任公司,舟山市鑫亚船舶修造有限公司和福建 修造有限公司,青岛前进船厂 宝中海崔工程股份有限公司
本标准主要起草人;詹树明、陈颖涛、李正建、李强、赵志坚、王治安、孙昌翎、李天煜、陈应战、 工学彬,魏洪宇,徐会超,朱雨雷,龚伟兵,赵桂开、张国翔、孙鹤,吴玉红、梁森森,白新建,万莉、王戈战 崔金环,左敬民,凌云峰、李珠其、魏崇华、王加飞、周讶若、高学峰,武晶、刘伟、隋盛华、孙琦、石长柏、 膝洪达,张勃,李忠旗,雷攀峰,刘学、周庆、尹强、王贤明、杨忠良,刘斌、李付博、顾炜、蔡玉良、赵实、 陈杰,唐家和,宋树青,孙学荣,姚军、曹际伟,赵金文,周金绪、周建华,孙书猛、方玉川,朱太原、范伟琳、 张树桐、刘敬纯、赵利家、林隆、陈新华,李振恩,刘进
m
GB/T34001一2016 修船质量标准 范围 本标准规定了船舶修理过程中的材料使用要求,船舶常规修理重点对外交验项目、勘验要点、修理 质量要求,修理过程质量控制及交验要求
本标准适用于500总吨及以上钢质海洋船舶的常规修理,其他船舶参照使用
本标准不适用于船舶的重大改装
规范性引用文件 下列文件对于本文件的应用是必不可少的
凡是注日期的引用文件,仅注日期的版本适用于本文 件
凡是不注日期的引用文件,其最新版本(包括所有的修改单)适用于本文件
GB/T1184一1996形状和位置公差未注公差值 GB/T3766一2015液压传动系统及其元件的通用规则和安全要求 GB/T6414一1999铸件尺寸公差与机械加工余量 GB/T8923.1一2011涂覆涂料前钢材表面处理表面清洁度的目视评定第1部分;未涂覆过 的钢材表面和全面清除原有涂层后的钢材表面的锈蚀等级和处理等级 GB/T8923.2一2008涂覆涂料前钢材表面处理表面清洁度的目视评定第2部分;已涂覆过 的钢材表面局部清除原有涂层后的处理等级 GB/T8923.3一2009涂覆涂料前钢材表面处理表面清洁度的目视评定第3部分;焊缝、边缘 和其他区域的表面缺陷的处理等级 GB/T8923.4一2013涂覆涂料前钢材表面处理表面清洁度的目视评定第4部分;与高压水 喷射处理有关的初始表面状态、处理等级和闪锈等级 GB/T13288.2一2011涂覆涂料前钢材表面处理喷射清理后的钢材表面粗糙度特性第2部 分;磨料喷射清理后钢材表面粗糙度等级的测定方法比较样块法 造船质量标准 GB/T340002016 所有类型船舶专用海水压载舱和散货船双触侧处所保护涂层性能标准(简 IMO/MSC.215(82 称PSPC)(Performancestandardforprotectivecoatingsfordedicatedseawaterballasttanksinall ofshipsanddouble-sideskinspacesobulkcarriers) types! 总则 3.1 修船材料 3.1.1修船使用材料的一般要求 修船使用材料的一 般要求如下: 对修理所使用的材料的要求,宜与原船的材料要求相同; a b修理中所使用的材料应由具有行业资质的工厂按照供货类型和等级生产; 修理中所使用的材料应按所属船舶检验机构的要求提供产品证书,在特殊状况下或一般限于 c
GB/I34001一2016 少量的材料,可替换其他的材料但应取得所属船舶检验机构的同意; d船用材料转船级应按船舶检验机构的要求办理手续; 修理中所使用的材料如果与原船的材料要求不同,可使用等效的材料,并向所属船舶检验机构 办理相关材料等级等效评定,应至少包括下述内容: 热处理/交货状态; 1 2) 化学成分 3) 机械性能 4 厚度负公差
3.1.2船用板材代用原则 ,等级最高到EH0)代用原则如下 船用板材限于厚度不超过50 mm、 a在同一强度级别的板材中,高等级钢可代低等级钢 高强度板材可代替普通强度板材 b e)在同一强度级别的板材中,厚板可以代用薄板; d)若低强度板材代用高强度板材,则应经过相关计算,并取得船舶检验机构的认可
3.1.3船用型材代用原则 船用型材代用原则如下 代用型材的材质应符合3.1.2的要求,代用型材的剖面模数(含带板)应不小于原型材的设计 剖面模数(含带板),并应取得船舶检验机构认可; 如型材使用焊接结构代用,剖面模数应符合上述要求
3.1.4船用管材代用原则 船用管材代用原则如下 代用管材的机械性能不低于原设计管材,高级别的管材可以代用低级别的管材,无缝压力管不 应使用焊接或者铸造压力管代替; b同级别管材,壁厚大的管材可代用壁厚小的管材,但通径应不小于原设计管材
3.1.5船用涂料代用原则 船用涂料代用原则如下 a)代用的涂料品种应使用同一类型的产品; b 高性能的涂料产品可以代替低性能的涂料产品,涂层干膜厚应根据涂料公司的要求适当调整; e相同品种不同颜色的面漆不应代用 d 特殊舱室的特殊涂料不应代用
3.1.6设备换新原则 设备换新原则如下 a新换设备相关性能应不低于原设备的设计性能; b新换设备技术标准应符合相关规范的要求; 新换设备应获得船舶检验机构认可的相关证书
3.2送审文件 常规修复性修理可不送审,局部改装或换新应按照船舶检验机构要求提交送审图纸,执行送审文件
GB/T34001一2016 的程序 3.3船舶常规修理重点对外交验项目 3.3.1说明 本标准所列的项目系送船舶检验机构和船东代表的交验项目,不同类型、不同航区、不同船旗国船 舶,可按不同要求作必要的增减
一般由制造方根据船舶修理进度要求,按下列程序通知船东代表和验 船师参加检验 “报验单”应在当天上班时提交船东代表和验船师; a b临时推迟交验,应及时通知船东代表和验船师 e)涂装交验可作例外处理 3.3.2船体工程部分 船体工程交验项目应符合表1的要求
表1船体工程交验项目 序号 验收项目 验收阶段 验船师 验收内容 船东代表 船体钢板及型材 材质报告,外观质量 施工前 船体焊接材料 结构完整性及焊缝表面质量 完工后 船体结构 全焊透区域出白交验 出白后 无损检测 完工后 安装正确性 施媒前 重要设备底座(发电机底座,舱 焊缝表面质量 完工后 口盖液压油缸座 反面结构加强 施焊前 锚机座、绞缆机座 注:“、”为交验项目
3.3.3坞修工程部分 坞修工程交验项目应符合表2的要求
表2坞修工程交验项目 验收项目 验收内容 验收阶段 验船师 船东代表 序号 划线后 尺寸检查 载重线及吃水标志 安装精度检查 安装后 牺牲阳极及外加电流保护装置 安装正确性与完整性 烟囱标志,船名标志 完工后 尺寸及安装位置检查 舷外标志
GB/T34001一2016 表2(续 序号 验收项目 验船师 船东代表 验收内容 验收阶段 安装正确性与完整性 放泄塞 完工后 清洁,研磨,各零部件检查 海底阀、出海阀 安装前 压力与密封试验 船底塞 真空密性试验 安装完整性检查 完工后 液压能机 运行试验 中间轴前、后法兰校中 中间轴承检查,间隙测量 中间轴承负荷试验 舰轴管测量,安装检查 螺旋桨轴及管轴检查测量 施工中 轴系 轴承检查测量 肌轴油封安装检查,坞内压油试验 螺旋桨轴及舰管轴下沉量测量 幌铀锥体根部及健槽无损检测 轴系效用试验 完工后 桨叶修补检查 螺距测量、静平衡试验 安装前 10 螺旋桨 锥孔拂配、健和键槽配合检查 桨叶根部无损检测 安装前 安装检查 施工中 舵、轴系拉线瞠孔检查,舵杆,舵 安装前 销、舵承检查测量 舵系 舵承间隙测量 完工后 1l 舵叶零位检查 施工中 操舵试验 完工后 12 侧推装置 各个机械部件清洁检查测量 施工中 注:“、”为交验项目,“一”为不需交验项目
3.3.4轮机工程部分 轮机工程交验项目应符合表3的要求
GB/T34001一2016 表3轮机工程交验项目 序号 验收项目 验船师 船东代表 验收内容 验收阶段 定位安装 安装前 垫片拂配/环氧浇注 曲轴臂距差测量 完工后 地脚螺栓上紧 地脚螺栓无损检测 安装前 机座轴承座孔修拂、色点检查 曲轴校调、表面修理、无损检测 主轴承、连杆轴承、十字头轴承、 推力轴承拆解检查,间隙测量 缸套检查、修理、测量 柴油机 活塞及活塞杆检查、修理、测量 安装前 活塞销/十字头销检查,测量 活塞安装、校中检查测量 气缸盖、活塞的密性试验 示功阀、启动空气阀、进排气阀、 喷油器压力或密性试验 高压油梨修理检查,定时校正 安装前 调速器修理检查,台架试验 调速器效用试验 完工后 柴油机运转,负荷试验 增压器拆解清洁测量,安装 安装前 增压器 增压器转子检查,动平衡校验 增压器效用试验 完工后 各类加热、冷却器清洁,密性 热交换器 试验 安装前 钢丝绳换新安装 行车(拆解、修理及主要零部件 运行试验,负荷试验,剃车试验 换新、安装 完工后 吊重试验
GB/T34001一2016 表3(续 序号 验收项目 验收阶段 验船师 船东代表 验收内容 炉管内场强度试验,密性试验 安装前 炉管/炉板换新装配,煤接检在 锅炉 锅炉清洁检查,水压试验 炉点火升汽效用试验 饷炉压力表检定 完工后 各类系浦(海谈水、滑油、燃油、 安装检查,效用试验 货油、液压等 拆解、修理检查 安全阀 内场试跳 安装前 拆解、修理检查、压力试验 主空气阀 效用试验 安装后 拆解、修理检查、压力试验 安装前 主蒸汽阀 效用试验 安装后 拆解,修理检查,压力试验 安装前 舷侧阀 10 效用试验 安装后 装配、媒接,压力试验或等效试 11 舷侧管 焊接前/后 临 拆解、修理检查、压力试验 安装前 遥控压载阀 系统效用试验 完工后 拆解,修理检查、压力试验 安装前 货油阀 13 效用试验 完工后 拆解、修理检查、压力试验 安装前 14 压力真空阀 效用试验 完工后 15 呼吸阀 试验台效用试验 16 内场管系制作 内场液压试验 安装前 液压管、滑油管、燃油管清洁 检查 管系安装 17 管系安装完整性检查 管畅通试验 CO 管系效用试验 完工后 效用试验 18 启动空气压缩机 19 船舶各系统 效用试验
GB/T34001一2016 表3(续 序号 验收项目 验收阶段 验船师 船东代表 验收内容 瓶头阀检查,密性试验 压缩空气瓶 强度试验 20 气密试验 安装前 21 风机 叶轮动平衡校验 密性试验 22 油柜附件修理 安装检查,效用试验 23 压力水柜 密性试验,效用试验 油污水处理装置 完工后 24 效用试验 25 分油桃 26 生活污水处理装置 效用试验 27 造水机 拆解,修理检查 安装前 28 淡水软化净化装置 注:“、”为交验项目,“一”为不需交验项目
3.3.5甲板机械及栖装工程 甲板机械及躺装工程交验项目应符合表4的要求
表4甲板机械及牺装工程交验项目 序号 验收项目 验收内容 验收阶段 验船师 船东代表 刹车试验 抛锚,起锚试验 锚,错链及附件材质报告 错机、绞缆机锚和锚链 错,锚链及附件外观质量 锚、错链及附件印标志 锚链环测量 安装正确性与完整性 系泊设备 引航员梯 安装正确性和完整性 完工后 安装完整性及炽缝质量 舱口盖 密性试验 效用试验 密性试验 水密门及风雨密门 开关试验 集装箱紧固件 安装正确性 舱室防火材料 防火材料及防火结构的完整性
GB/T34001一2016 表4(续 序号 验收项目 验收阶段 船东代表 验收内容 验船师 吊臂,筒体焊缝表面质量 焊缝无损检测 起重设备 起重设备运转试验 吊重试验 完工后 舱柜,油箱,水箱等修理和新制 密性试验 救生艇负荷及密性试验 10 救生设备 救生艇收放试验 钢丝绳换新安装 安装前 钢丝绳换新安装 起货机(拆解、检查及主要零部 效用试验 件换新、安装 完工后 负荷试验 钢丝绳换新安装 安装前 舷梯(拆解、检查及主要零部件 效用试验 12 换新、安装 完工后 负荷试验 钢丝绳换新安装 安装前 食品吊(拆解、检查及主要零部 13 效用试验 件换新、安装 完工后 负荷试验 钢丝绳换新安装 安装前 软管吊(拆解、检查及主要零部 14 效用试验 件换新,安装) 完工后 负荷试验 钢丝绳换新安装 安装前 15 开关舱绞车(拆解、修理检查 功能试验,负荷试验 完工后 注“、”为交验项目,“”为不需交验项目
3.3.6电气工程部分 电气交验项目应符合表5的要求
GB/T34001一2016 表5电气交验项目 序号 验收项目 验收内容 验收阶段 验船师 船东代表 甲板电缆管制作安装检查 安装前 气躺装件 电 电缆托架安装 安装后 电缆敷设完整性 绝缘测量 主干电缆敷设 电缆芯线通断测量 完工后 高压电缆耐压试验 防火,水密隔堵装置安装检查 安装后 电缆防火,水密隔堵装置 密封检查 安装接线 清诘,保养 绝缘电阻测量 保护装置试验 主配电板、应急配电板 主开关效用试验 仪表检定,指示正确性检查 电气连锁试验 功能试验 完整性检查 安装、接线检查 清洁,保养检t 报警装置试验 绝缘电阻测量 发电机组 负荷、特性试验 并联运行试验 完工后 自动运行(PMS功率管理)试验 完整性检查 安装、接线检查 清洁保养检查 绝缘电阻测量 报警装置试验 应急发电机组 自动启动试验 供电试验 负荷、特性试验 自动供电试验 完整性检查 报警试验 充放电板、蓄电池 效用试验 完整性检查
GB/T34001一2016 表5(续 序号 验收项目 验收阶段 船东代表 验收内容 验船师 大修电动机,发电机耐压试验、 空载及效用试验 小修电动机、发电机绝缘测量、 空载及效用试验 电动机、发电机及其控制设备 转子动平衡试验 刹车试验 报警试验 接地线检查,可靠接地检查 完整性检查 效用试验 风,油紧急切断 绝缘测量、完整性检查 10 正常照明 效用试验 完整性检查 绝缘测量,完整性检查 应急照明 效用试验 11 完整性检查 完工后 舵角指示、完整性检查 12 舵机试验 报警试验 操舵试验 内部报警系统(包括火警,co) 释放报警、通用报警、冷库报警、 效用试验/模拟试验 13 病房呼叫、水密门指示、机舱报 警灯柱等) 内部通讯系统(包括广播对讲 自动电话,声力电话、子母钟、公 14 效用试验 共天线、局域网等) 设备绝缘测量 15 厨房电气设备 功能试验 16 水喷淋系统 效用试验 报警试验 17 航行灯、信号灯 效用试验 完整性检查 旋转视窗,雨刮器 效用试验 18 10o
GB/T34001一2016 表5(续 序号 验收阶段 验收项目 验船师 船东代表 验收内容 19 外加电流阴极保护,铀接地装置 2o 测深仪 效用试验 21 计程仪 22 雾笛、电笛 23 磁罗径 误差校正,效用试验 24 电罗径 卫星导航系统 25 雷达 26 27 自动识别系统 28 电子海图 29 桥楼值班报警 30 自动舵系统 效用试验 31 航行数据记录仪 航行警告接收机 32 完工后 气象传真机 33 34 甚高频无线电话 35 无线电台 36 卫星通信站 37 雷达应答器 38 应急示位标 按期进行年度测试试验或岸基维护 报警装置试验 主机操纵系统 主机车钟试验 39 主机遥控试验 报警点效用试验/模拟试验 机舱监测报警系统 轮机员值班报警效用试验 40 无人机舱效用试验 阀门遥控、液位遥测系统 效用试验 注:“、”为交验项目,“一”为不需交验项目
3.3.7空调,冷藏及通风装置工程部分 空调、冷藏及通风装置交验项目应符合表6的要求
11
GB/T34001一2016 表6空调冷藏及通风装置交验项目 验收项目 验收阶段 船东代表 序号 验收内容 验船师 空调冷藏系统(部分管系改造或 效用试验 完工后 设备换新修理 注“、”为交验项目,"一”为不需交验项目 3.3.8涂装工程部分 涂装交验项目应符合表7的要求
表7涂装交验项目 序号 船东代表 验收项目 验收内容 验收阶段 验船师 涂料厂商 钢材表面清洁度 除锈后 除锈及涂装 涂层干膜厚度 完工后 防污漆无TBT 涂层技术文件(CTF)(PSPC适用 注“、”为交验项目,“一”为不需交验项目
船体工程 钢材 4.1 4.1.1钢材质量要求 4.1.1.1船体结构钢板厚度负偏差应符合表8的要求
表8船体结构钢板厚度负偏差 单位为毫米 项目 要求(最大值 船体结构钢板厚度负偏差 0.3 钢板测量的平均厚度应不小于钢板的名义厚度,厚度的正偏差应按有关标准或合同规定 4.1.1.2机械结构钢板厚度负偏差应符合表9的要求
表9机械结构钢板厚度负偏差 单位为毫米 钢板厚度 要 求(最大值 5" 0.4 8~15 0.5 1525 0.6 2540 0.8 >40 1.0 12
GB/T34001一2016 4.1.1.3钢板表面缺陷的限定应符合表10的要求 表10钢板表面缺陷的限定 项目 要求 0.0 >mm 区域A为所有厚度可不修整缺陷的范围 0.80 b 区域B为1<20时可不修整缺陷的范围; 0.70 D>50mm 区域c为20<50时可不修整缺陷的范 0.60 20mm<<50mm 0.50 d 区域D为1>50时可不修整缺陷的范围 0.40 区域E的缺陷应按下述方法修整: 0.30 1<20mm d<0.07i,且d,二3,磨平; 0.20 0.071
GB/T34001一2016 4.2.2划线过程质量控制 4.2.2.1对主要构件应记录材质、炉号、批号和厚度
4.2.2.2划线的质量控制要点 a)尺寸偏差; b 几何公差; e)加工符号、代号及工艺符号的标注; d)材质、炉批号在余料上的移植标注
4.3切割 4.3.1切割质量要求 4.3.1.1气割切割面粗糙度应符合表15的要求
表15气割切割面粗糙度 单位为毫米 项目 标准范围 允许极限 备注 自动气割 0.10 0.20 重要部分 手工,半自动气割 0.15 0.30 构件自由边 自动气割 0.10 0.20 a 型钢的机械切割按 非重要部分 0.50 手工,半自动气割 1.00 手工气割; 切割后应除去自由 b 自动气测 0.10 0.20 重要部分 边毛刺 手工、半自动气刚 0.40 0,8o 焊接接缝及 坡口表面 自动气刚 0.10 0.20 非重要部分 0.80 手工,半自动气割 1.50 4.3.1.2气割尺寸偏差和几何公差应符合表16的要求
表16气割尺寸偏差和几何公差 单位为毫米 标准范 备注 项目 允许极限 自动焊缝 0, 0.5 板边缘 直线度 半自动焊缝及手工焊缝 1.5 2.5 坡口面角度 士2 士4" 坡口面 坡口深度 士1.5 士2.0 尺寸 按相应船舶检验机构 过渡段长度 规范要求,l可取3da 士0.5l 士1.0d 4d或5d 15
GB/T34001一2016 表16(续) 单位为毫米 标准范 允许极限 项目 备注 例如双层底肋板、衔材 主要构件 士2.5 士4.0 等要求较高的构件 构件 次要构件 士3.5 士5.0 尺寸 4.0 面板宽度 士2.0 3.0 4.3.2切割过程质量控制 切割前应拆下有碍施工的电缆、管系和设备,并采取相应的防护措施,以便按原位装复 4.3.2.1 4.3.2.2构件切割后,剐痕处要清除氧化皮并打磨,开口边缘变形处应进行火工校正,使其平整
4.3.2.3切割的质量控制要点 切割精度; a b 坡口切割方向 数控切割设备精度定期检测
c 4.4成形 4.4.1成型质量要求 4.4.1.1折边尺寸偏差和几何公差应符合表17的要求
表17折边尺寸偏差和几何公差 单位为毫米 项目 标准范 允许极限 备 注 折边宽度b 士5.0 土3.0 腹板高度h
折边角度0 士2.5 士4.5 以每100宽计 3t, 折边弯曲半径r
2t >4.5t(适用于共同结构规范的船舶 面板的直线度 10 25 以每10m长计 腹板的直线度 4.4.1.2槽形板尺寸偏差和儿何公差应符合表18的要求
表18槽形板尺寸偏差和几何公差 单位为毫米 项目 标准范围 允许极限 备注 槽的高度h 士3.0 士6.0 槽的宽度b,b 槽的直线度 10 25 以每10m长计 16
GB/T34001一2016 4.4.1.3圆柱结构尺寸偏差应符合表19的要求 表19圆柱结构尺寸偏差 单位为毫米 项目 备注 标准范围 允许极限 士D./200 士D%/150 圆柱结构直径D 最大士5 最大士7.5 4.4.1.4型材及析材尺寸偏差和几何公差应符合表20的要求
表20型材及析材尺寸偏差和几何公差 单位为毫米 项目 标准范围 允许极限 备注 角变形
士1.5 h,以每100计 士2.0 型材 以每1m长计,相 局部弯曲入 士1.0 士1.5 对样板 00 以每10m长计 弯曲偏差 士2.0 D 士4.0 相对样板 以每100计组合 面板倾斜度 士1.5 士3.0 角材相同 衔材 面板角变形 3十b/100<5十b/100 面板和覆 以每10m长计 10 25 板的直线度 17
GB/T34001一2016 4.4.1.5外板弯曲尺寸偏差和几何公差应符合表21的要求
表21外板弯曲尺寸偏差和几何公差 单位为毫米 项目 标准范围 允许极限 备 注 曲面与样板空隙 单曲度板 5.0 三角样板检验线的直线度 拉线与样板上基准经的偏差 士2.0 士3.0 每档肋距内 双曲度板 肋位方向与样箱的空隙 4.0 二5.0 长度方向与样箱的空隙 3,0 4.4.1.6钢材加热应符合表22的要求
表22钢材加热要求 项目 标准范围 允许极限 备注 -股高强度钢AH32-EH32和加热后立即水冷时l650C以下 650C AH36-EH36)" 900" 加热后空气冷却时|p00C以下 以热机械控制工艺简称TMCP 加热后空气冷却后900以下空冷下降900(空冷 表 交货的高强度钢(AH36-EH36 c.,为碳当量 再水冷时 到500C以下水冷 500c(水冷》 面 >0.38% 其计算公式如下: 最 以TMCP交货的高强度钢 Mn 加热后立即水冷或 AH32-DH32和AH36-DH36 1000C以下 1000C 空冷时 加 s0.38% Cr十Mo十V 热 以TMCP交货的高强度钢 加热后立即水冷或 Ni+Cu EH32-EH36 l900以下 900" 空冷时 度 <0.38% 加热后空气冷却后900C以下空冷下降900C(空冷 以TMCP交货的低温用钢 再水冷时 到550C以下水冷 550c(水冷 钢材级别和牌号参见GB712一2011
4.4.2成型过程质量控制 4.4.2.1钢板与型材弯制宜采用冷弯或热弯成形,并根据钢材的材质特性按规定进行弯制
4.4.2.2成形的质量控制要点如下 a)加热温度; 加热次数 b c)冷弯弯曲半径; d) 成形精度 外观质量 4.5结构更换 4.5.1勘验要点 结构更换的勘验要点如下 18
GB/T34001一2016 检查船体构件的腐蚀、变形及破损情况 a b)对需要修理的构件做好标记; 对觞麂部和机舱范围的构件进行勘验时,应特别注意与其相关的舱、柜、电缆、管系和设备等, 以便必要时采取相应的措施
4.5.2结构更换质量要求 4.5.2.1各类焊接接头装配及构件装配应分别满足GB/T34000一2016中5.1.6.1和5.1.6.2的要求
4.5.2.2板的挖补换新应符合表23的要求
表23板的挖补换新 单位为毫米 项目 标准范围 允许极限 处理方法 焊接程序: 长度L >300 >200 宽度B 矩形挖补 >5×板厚且>100 圆角R 直径D 圆形挖补 200 4.5.2.3型材及组合件的挖补换新应符合表24的要求
表24型材及组合件的挖补换新 单位为毫米 标准范围 允许极限 项目 处理方法 焊接程序;--- 挖补长度L 300 200 4.5.2.4结构大范围更换时,宜预制船体分段,分段的装配应满足GB/T34000-2016中5.1.6.3的 要求
4.5.3结构更换过程质量控制 4.5.3.1割换板的切割线宜安排在原板缝处 4.5.3.2对线型变化较大的构件,应制作样板或进行放样,在内场加工成型后再进行装配
不得强行 19
GB/T34001一2016 装配
4.5.3.3构件采用定位焊或码板装配,定位焊或码板的数量应尽量减少,焊缝应具有足够的高度
定位 焊用的焊接材料应与施焊用的焊接材料相同
有缺陷的定位焊应在施焊前清除干净 4.5.3.4与新板对接处的板缝应先焊接
4.5.3.5新板与旧板缝连续处至少一端应延伸150 mm 4.5.3.6结构大范围更换前,应进行船体基线测量并记录其原始挠度值 4.5.3.7结构大范围更换应分期分批进行,必要时应进行强度与变形计算,并采取相应的加强措施
4.5.3.8在水上进行结构大范围更换应注意选择压载工况,尽可能减小船体所承受的外力 4.5.3.9结构更换的质量控制要点如下 构件的几何尺寸; a D 装配间隙, 结构对位精度; c d内部构件的直线度
4.5.4交验要求 结构更换的交验要求如下 a)检查钢材及焊材的外观质量、材质报告及船舶检验机构证书; b)检查零部件的加工精度 e)检查坡口及装配精度; d 检查结构完整性
4.6加强 4.6.1若采用覆板条进行结构加强,则覆板条的端部处理应符合表25的要求
表25覆板条的端部处理 标准范围 允许极限 备 注 项目 切斜角 L:/6;>3 非对称 板条 增加的岸喉厚度 圆弧R 0.1b 30mm 对称 板条 喉厚度在末端加大15% 增加的焊喉厚度 4.6.2开孔补强应符合表26及表27的要求
2o0
GB/T34001一2016 表26开孔补强条件 单位为毫米 要 项目 求 备 注 开孔位右图中4区域内不得开任何孔 200 1200 1200 200 置的若必须开孔时,,应经设计部门 限制同意 在一个肋距或纵骨间距内开 个圆孔,且满足下述任一条件 ,应补强: 甲板 d>25%Ha; 25%H
GB/T34001一2016 表27开孔补强要求 注 项目 要求 覆板与梁腹板的材质相同,且>,/>30mm; 板 梁腹板 -覆板厚度; 梁腹板厚度 加装覆板补强 -覆板与梁腹板搭接长度; -梁腹板高度; H 加强覆板 -腹板开孔下边缘距梁面板距离 c? 梁面板 开孔直径 小 若用钢板制作圆环,其材质应与梁腹板相同;若采用 甲板 无缝钢管制成,其材质应为10,15或20钢
圆环板的 轴向断面积应不小于梁腹板开孔的断面积,且t;> 圆环板 加装圆环 -圆环板厚度; 板补强 H -梁腹板高度 梁腹板 腹板开孔下边缘距梁面板距离; 梁面板 -开孔直径 d 4.7 覆板 4.7.1覆板质量要求 覆板修理应符合表28的要求
表28覆板修理要求 单位为毫米 项目 标准范围 允许极限 备 注 适用覆板修理的被覆板 厚度 覆板厚度1a i/3<1a<! 纵 覆板面积La×Ba >300×300 覆板圆角R >50 塞媒孔尺寸 80100×2n 覆板边缘至塞焊孔的距 <15a <500 塞焊孔 离d 焊接在强力构件上的覆板,当>K
十 -5时,应按1:4斜 两塞炽孔间距 二200 度加工坡口 焊脚长度K.(塞焊孔及 0.85× 周边 4.7.2覆板过程质量控制 4.7.2.1覆板修理一般只允许在临时修理时采用 22
GB/T34001一2016 4.7.2.2被覆板上应无裂纹及沟漕,修理区域钢板的表面状态及钢板的剩余厚度应能保证有效焊接
4.7.2.3应尽量采用整块覆板覆盖整个有缺陷的区域,而不应多处小块覆板
4.7.2.4覆板前,水密构件应做密性实验,确定无泄漏后方可覆板修理
4.7.2.5应预先用砂轮去除覆板部位的对接焊缝加强高度,覆板与被覆板之间的贴合表面应除锈并涂 防腐涂料
4.7.2.6覆板四周边缘进行填角焊接外,如果覆板宽度大于该区域骨架跨距,还应进行塞焊
4.7.2.7覆板修理的质量控制要点 a)覆板尺寸 b 被覆板表面质量; 被覆板剩余厚度" c d)塞焊孔尺寸及间距
4.8焊接 4.8.1焊接质量要求 4.8.1.1引弧、,应预热的环境温度及媒前板材预热温度应符合表29的要求
表29引弧及预热温度 备 项目 标准范围 允许极限 注 若已引弧应用下述方法修补, 高强度钢、铸钢 -般强度E级钢 在引狐线上面炽上一条50nmm 引弧 不允许 以TMCP交货的高强度钢 以上的焊缝; 低温用钢 用砂轮磨平硬化部 -般强度钢A,B,D,E -5C AH32" 应预热的以TMCP交货的 环境温度应预热至不低于20,除 0C EH132 环境温度高强度钢 非被认可的焊接工艺有更高的要求 AH36 常规高强度钢 5 EH36 碳当量C开算公式见表2 50
GB/T34001一2016 表33焊接接头变形 单位为毫米 项 目 注 标准范围 允许极限 6 船肿0.6L区域内 骨架间距 船长; a 的外板 当超过允许极限时,可以矫 b 正或将焊缝割开后再重新装 航艇部的外板 骨架间距内外板变形量 配媒接 其他部位 裂纹的焊接修理应符合表3孔的要求
4.8.1.6 表34裂纹的焊接修理 项目 标准范围 允许极限 备 注 对贯穿板厚的裂纹,应与板对接坡口相同 角度0=45"60", 坡口加工 R=5mm 端部形式端部坡度为1:3 对裂纹在端部终止处,焊接应延伸至引弧板上 板上裂纹最大长度板上线性裂纹最大 裂纹两端应先开设止裂孔,防止裂纹继续延伸;长度 范围 400mm,刨槽超过裂纹长度500mm,没有 超过300mm的裂纹应采用分段倒媒法修理 端50mm 分叉 4.8.2焊接过程质量控制 4.8.2.1所用焊接材料应具有合格证件并经过船舶检验机构认可
4.8.2.2所用焊接工艺规程应获得相应船舶检验机构认可
4.8.2.3当被焊接的两块板材级别不同时,除在结构不连续处或应力集中区域内应选用较高级别的焊 接材料外,一般可选用与低级别板材相匹配的煤接材料
4.8.2.4焊接工作应由持有相关船舶检验机构颁发或认可的《焊工资格证书》的焊工承担
4.8.2.5施焊前,应清除施焊区域的水分、油脂、氧化皮、铁锈及涂料等
当焊接必须在潮湿、多风或寒 冷的露天场地进行时,应对焊接作业区域提供适当的遮蔽和防护措施
4.8.2.6焊接设备应能正常使用,并在有效使用期限内
4.8.2.7对于多层煤,在进行下一层焊接前,应对熔敷金属区域表面进行敲渣及清洁
4.8.2.8进行双面接焊时,在单面焊缝完成后,应在反面进行碳弧气刨,并打磨至无裂纹、夹渣及气孔等 缺陷且表面光滑
4.8.2.9在去除临时焊缝、定位焊缝,焊缝缺陷、焊疤和清根时,均不得损伤母材
4.8.2.10在清除裂纹缺陷时,应在裂纹两端先钻止裂孔,防止裂纹扩展和延伸
4.8.2.11应采用较小直径的焊条和较小的焊接电流进行煤补
4.8.2.12焊缝坡口及焊缝金属应按照相应的工艺要求进行无损检测
4.8.2.13水密结构的焊接工作完成后,应按相应船舶检验机构规范要求进行密性试验 4.8.2.14对不符合要求的焊缝应进行修补,能够重新进行检验
25
GB/T34001一2016 4.8.2.15焊接的质量控制要点如下: a)焊工资质; b 焊接材料 c 焊接规范; 焊接设备; 预热和保温 e 焊接变形 焊缝尺寸及表面质量; g h 无损检测 iD 密性试验
4.8.3交验要求 焊接的交验要求如下 a)检查焊缝尺寸及表面质量 b)测量并记录结构变形; e)提供无损检测报告; d)提供密性试验报告
4.9修整 4.9.1脚手架眼板和吊装眼板清理应符合表35的要求
表35脚手架眼板和吊装眼板清理 目 要 备 项 求 注 油水舱内 允许全部留下 机舱内 只切除影响外观和通行的眼板 影响外观和通行的吊装眼板,切 脚手架眼板 除后应修补到与母材表面 货舱内 只切除下部和舱口围板上的眼板 样平; 外板、甲板等外侧部位全部切除 其他处可用气削,允许留有根部 b 不影响通行的吊装眼板允许全部 但对强度特别重要的部位切除后 油水舱内 留下 应补焊光顺 吊装眼板 货舱内 甲板内侧允许留根 外板、甲板等外侧部位 全部切阶除 固定眼板除外 4.9.2工艺板清理应符合表36的要求
工艺板清理 表36 要 求 备 注 项目 外板、甲板和上层外侧应全部刨平并光 舷顶列板,强力甲板的角隅板及工艺板应少设或 需要良好外观处 工艺板咬边允许深度0.5mm,超过 顺
不设,其咬边应全部焊补磨光 者应焊补磨光 26
中国修船质量标准GB/T34001-2016
中国修船质量标准GB/T34001-2016是中国海事行业规范中的重要标准之一。该标准于2016年12月29日由国家质检总局发布,并于2017年2月1日开始实施。GB/T34001-2016标准主要针对中国修船行业,在保证安全、环保等方面制定了一系列的质量标准,以提高整个行业的水平和质量。
标准内容
GB/T34001-2016标准的内容包括:修船企业的评价标准、修船合同的管理、修船现场的管理、修船产品质量和安全技术要求、修船项目的验收和后续服务等。
其中,修船企业的评价标准主要包括企业质量管理体系、职业健康安全管理体系、环境管理体系等方面的标准。修船合同的管理则着重规范了合同的签订和执行流程,以及各方责任和义务。修船现场的管理主要包括人员管理、设备管理、安全管理等方面的规定。修船产品质量和安全技术要求则针对修船过程中的各项工作进行了详细的质量和安全要求说明。修船项目的验收和后续服务则规定了对修船项目的验收标准和后续服务的要求。
标准意义
GB/T34001-2016标准的制定和实施,对中国修船行业的发展具有重要意义。其一是提高了整个行业的质量和水平。标准实施后,将为修船企业提供一套完善的质量管理体系和规范操作流程,有助于消除不合理竞争和低价竞争等现象,提升整个行业的水平和品牌效益。其二是促进了海事行业的可持续发展。标准的实施有助于保障修船项目的安全和环保,同时也能够优化资源配置,提高整体效益。
总结
GB/T34001-2016标准是中国修船行业的一项重要标准,其实施将对整个行业产生积极的影响。在今后的发展中,修船企业需要严格按照标准要求进行生产和管理,以提升整个行业的水平和质量。