GB/T37400.14-2019
重型机械通用技术条件第14部分:铸钢件无损探伤
Heavymechanicalgeneraltechnicalspecification—Part14:Nondestructivetestofsteelcastings
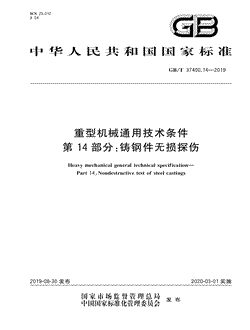
- 中国标准分类号(CCS)J04
- 国际标准分类号(ICS)25.010
- 实施日期2020-03-01
- 文件格式PDF
- 文本页数51页
- 文件大小4.67M
以图片形式预览重型机械通用技术条件第14部分:铸钢件无损探伤
重型机械通用技术条件第14部分:铸钢件无损探伤
国家标准 GB/T37400.14一2019 重型机械通用技术条件 第 14部分;铸钢件无损探伤 Hleavy mechanealgenerltechmieallspecifieationr Part14:Nondestructivetestofsteeleastings 2019-08-30发布 2020-03-01实施 国家市场监督管理总局 发布 币国国家标准化管理委员会国家标准
GB:/T37400.14一2019 目 次 前言 范围 2 规范性引用文件 3 术语和定义 3.1超声检测 射线检测 3.2 3,3渗透、磁粉检测 -般要求 - 4.1总则 .2检测档案 4.3检测人员 铸钢件超声检测 5.1订货时应明确的内容 5.2受检铸件的准备 5. 检测系统 5.4 检测仪的校准 5.5 超声可探性的确认 5.6 检测 5.7 缺陷分析 5.8 缺陷尺寸测定 5.9质量等级 13 5.10检测报告 14 铸钢件射线检测 14 6.1检测前应明确的内容 14 6.2像质级别 14 6.3设备与器材 16 6.4透照方法 6.5底片质量要求 21 6.6底片观察 6.7散射线屏蔽 6.8缺陷影像质量评级方法 6.9检测报告 26 铸钢件渗透检测
-
26 7.1检测前应明确的内容 26 7.2安全防护 26 7.3检测要求
GB/T37400.14一2019 27 7.4检测材料及灵敏度 28 7.5检测工艺 7.6显示的评定与质量等级 37 32 7.7检测报告 8 32 铸钢件磁粉检测 8.1检测前应明确的内容 32 2 8.2安全防护 32 8.3方法概述 32 8.4表面状态和表面准备 33 8.5设备和器材 33 8.6磁化方法 8.7 电流种类 34 8.8磁场方向和有效区 34 8.9磁化验证 35 8.10磁粉检测操作 36 8.11观察条件 36 8.12退磁 36 8.13显示的评定与质量等级 37 8.14检测报告 37 附录A规范性附录)补媒区的检测 39 附录B(资料性附录)传输修正及衰减系数 附录c(资料性附录DGS(AVG)曲线应用 13 附录D(规范性附录)常用灵敏度试片(块
GB:/T37400.14一2019 前 言 GB/T37400《重型机械通用技术条件》分为16个部分 第1部分:产品检验; 第2部分:火焰切割件 第3部分;焊接件; 第4部分:铸铁件; 第5部分:有色金属铸件 第6部分;铸钢件; 第7部分;铸钢件补焊 第8部分;锻件 第9部分;切削加工件 第10部分:装配; 第11部分配管 第12部分;涂装; 第13部分包装 第14部分;铸钢件无损探伤 第15部分;锻钢件无损探伤; 第16部分液压系统
本部分为GB/T37400的第14部分
本部分按照GB/T1.12009给出的规则起草
本部分由全国冶金设备标准化技术委员会(sAc/Tc409)提出并归口
本部分起草单位;二重(德阳)重型装备有限公司,太原重工股份有限公司、中冶陕压重工设备有限 公司、重型机械研究院股份公司、一重集团有限公司
本部分主要起草人;周澄、,邵鞠民,苏静、张广勇、许常青、范靳科、阎颖、闵利峰、张辉、张林
GB:/T37400.14一2019 重型机械通用技术条件 第14部分铸钢件无损探伤 范围 GB/T37400的本部分规定了铸钢件的超声检测、射线检测,渗透检测和磁粉检测等无损检测方 法、一般要求及其相应的质量等级 本部分适用于 厚度<600mm经热处理的合金和非合金铁索体钢铸件的A型脉冲反射法超声检测
对于厚 度>600mm的铸件,如果没有其他规定,也可参照执行 厚度>5 mm 铸钢件的射线检测; -铁磁性铸钢件表面及近表面缺陷的磁粉检测; -铸钢件表面开口性缺陷的渗透检测 -缺陷挖补处的磁粉检测和渗透检测
本部分不适用于奥氏体铸钢件的超声检测
规范性引用文件 下列文件对于本文件的应用是必不可少的
凡是注日期的引用文件,仅注日期的版本适用于本文 件
凡是不注日期的引用文件,其最新版本(包括所有的修改单)适用于本文件
GB/T5097无损检测渗透检测和磁粉检测观察条件 GB/T9445无损检测人员资格鉴定与认证 GB 12604.1无损检测术语超声检测 /T GB/T12604.2无损检测术语射线照相检测 GB/T12604.3无损检测术语渗透检测 GB/T12604.5无损检测术语磁粉检测 GB12664便携式X射线安全检查设备通用规范 GB/ /T 14058Y射线探伤机 GB/T15822.1无损检测磁粉检测第1部分;总则 GB/T15822.2无损检测磁粉检测第2部分;检测介质 GB/T15822.3无损检测磁粉检测第3部分;设备 无损检测渗透检测第2部分;渗透材料的检验 GB 1885l.2 GB 无损检测渗透检测第3部分;参考试块 1885l.3 2008 GB 18851.4 无损检测渗透检测第4部分;设备 GB 8851.5无损检测渗透检测第5部分;温度高于50C的渗透检测 GB/T18851.6无损检测渗透检测第6部分;温度低于10C的渗透检 GB/T19348.1 无损检测工业射线照相胶片第1部分工业射线照相胶片系统的分类 GB/T19799.1一2015无损检测超声检测1号校准试块 GB/T19799.22012 无损检测超声检测2号校准试块 GB/T19802无损检测工业射线照相观片灯最低要求
GB/T37400.14一2019 GB/T19803一2005无损检测射线照相像质计原则与标识 GB/T20129无损检测用电子直线加速器 GB/T20737无损检测通用术语和定义 GB/T23901.12019无损检测射线照相检测图像质量第1部分;线型像质计像质值的测定 GB/T23907一2009无损检测磁粉检测用试片 GB/T27664.1无损检测超声检测设备的性能与检验第1部分:仪器 GB/T37400.7重型机械通用技术条件第7部分;铸钢件补煤 术语和定义 3 GB/T12604.l、GB/T12604.2、GB/T12604.3、GB/T12604.5、GB/T20737界定的以及下列术语 和定义适用于本文件
3.1超声检测 3.1.1 底波降低量reductionofbackwallecho 在缺陷附近完好区域内第一次底波幅度与缺陷区域内第一次底波幅度的比值
注:比值需换算为dB 3.1.2 扫查灵敏度scanmingsens sitivity 在检测灵敏度的基础上,根据表面状况、检测缺陷要求及探头类型等适当提高波幅(增益)进行实际 检测的灵敏度
3.1.3 回波动态波形eehod小ynamtcpaters" 探头移动距离与对应反射体回波波幅变化的包络线
3.1.4 非延伸性缺陷refleetorswithnomeasurablesize 实际尺寸小于探头在缺陷处声束直径(一6dB)的缺陷
注:非延伸性按缺陷峰值点最大间距判定,若测出的峰值点最大间距小于或等于探头声束直径(-6dB),则该缺陷 定义为非延伸性缺陷
3.1.5 延伸性缺陷releetorswithmeasurablesize 实际尺寸大于或等于探头在缺陷处声束直径(一6dB)的缺陷 注:延伸性缺陷按缺陷峰值点最大间距判定,若测出的峰值点最大间距大于探头声束直径(一6dB),则该缺陷定义 为延伸性缺陷 3.2射线检测 3.2.1 公称厚度nominalthickness T 受检工件名义厚度
注;公称厚度不考虑材料制造偏差和加工减薄
GB:/T37400.14一2019 3.2.2 透照厚度penetratedthickness 射线照射方向上材料的公称厚度
注:多层透照时,透照厚度为通过的各层材料公称厚度之和
3.2.3 射线源至工件距离souree-to-objeetdistancee 沿射线束中心测定的工件受检部位射线源与受检工件近源侧表面之间的距离
3.2.4 射线源尺寸soureesize 射线源的有效焦点尺寸
3.2.5 缺陷评定区defeetevaluationzone 在缺陷最严重的部位,为评价缺陷数量和密集程度而设置的一个圆形区域
3.3渗透、磁粉检测 3.3.1 线性显示linearindieatiom 长度大于3倍宽度的显示
3.3.2 非线性显示non-linearindieatiom 长度小于或等于3倍宽度的显示
3.3.3 'defectindications 成排缺陷显示array 至少有三个线性或非线性缺陷显示,且相邻两缺陷显示间的距离小于2n mm
注:成排缺陷显示的长度为第一个缺陷显示开始到最后一个缺陷显示末端之间的距离
3.3.4 缺陷评定框defeetevaluationzone 在缺陷最严重的部位,为评价缺陷数量和密集程度而设置的150mm×105 nmm的一个长方形 区域
-般要求 4.1总则 4.1.1检测方法和质量验收等级的选择应依据铸钢件的具体使用和种类确定,并符合相应技术文件的 要求
4.1.2合同、订货技术条件或图样中应给出检测方法 -超声、射线、渗透和磁粉
注:奥氏体材料只能选用射线检测和渗透检测
4.1.3凡要求有表面检测的铁磁性铸件,应优先选用磁粉检测方法
若因结构形状及资源条件等原因 不能使用磁粉检测时,才选用渗透检测
4.1.4铸钢件不同区域的质量等级,应在合同、订货技术条件或图样中予以规定
质量等级的选择应 根据负荷的大小,方式和分布考虑下列各项: 对于铸件的不同区域可选用不同的质量等级
在这种情况下,应明确规定有关的区域,即 给出具体的位置和尺寸范围(长度和宽度);
GB/T37400.14一2019 22 对于待焊区域和特殊边缘区,还要给出深度范围
b 对于不同区域的质量,可以选择相同的质量等级也可以选择不同的质量等级
4.1.5若订货时没有规定质量等级,且材料标准也没有其他规定,则应按最低质量等级验收
4.1.6在特殊情况下,对于机加面的边缘区(见图4)的外层区域或称特殊边缘区),可选用较高的质量 等级
注;选用较高质量等级的原因是机械加工后内部缺陷可能暴露到精加工表面
4.1.7对于铸件补焊区域的无损检测,应依据GB/T37400.7执行
补焊区域质量要求与基体材料应 相同
补焊区的检测见附录A
4.2检测档案 4.2.1检测档案至少应包括: 无损检测委托单或检测合同 a b 无损检测工艺文件 c 无损检测原始记录; d 无损检测报告 4.2.2合同有要求时,检测前应准备一个书面检测工艺规程,必要时需经用户认可
检测程序及结果应正确、完整并有相应人员签名认可
检测记录、报告等保存期不应少于5年
4.2.3 4.3检测人员 4.3.1实施检测的人员,应按GB/T9445或其他等效标准、法规进行资格鉴定,并取得相应检测方法等 级的资格证书
4.3.2 cGB/T945所规定的各级资格人员所从事的工作应与其资格等级和方达相适应
4.3.3凡从事无损检测工作的人员,视力应满足下列要求 矫正视力不应低于5.0(小数记录值为1.0); a b)从事表面检测工作的人员不应有色盲
4.3.4从事射线检测的人员上岗前应进行辐射安全知识的培训,并取得放射工作人员证
5 铸钢件超声检测 5.1订货时应明确的内容 订货时应明确以下事宜: 检测部位及范围; -铸件各区域的质量要求或等级 是否要求书面检验规程; 要求进行的特殊检测方法
5.2受检铸件的准备 在超声检测之前,铸钢件应至少进行一次奥氏体化热处理
最终验收的超声检测的检测应安排在最终热处理之后进行
铸件超声检测应安排在外观检查合格后进行,铸件的检测面及底面应无影响超声检测的异物,机加 工表面粗糙度应至少达到Ra6.3,非加工的表面粗糙度应至少达到Ra12.5
GB:/T37400.14一2019 5.3检测系统 5.3.1超声检测设备 超声检测设备至少应具有下列性能: 可使用单晶或双晶探头,其工作频率至少为1MHz一6MHHz; -增益范围>80dB,调节精度>1dB 增益线性应满足表1要求,时基线性误差最大允许值为全屏宽度的士2%,测试方法按 GB/T27664.1
表1增益线性 增益 预定的全屏幅度 限值 dB 十2 01 >95% 80 基准线 -6 40 37%43% 12 20 17%23% 10 18 8%12% <8%,可见 -24 5.3.2探头 5.3.2.1频率 探头公称频率应在1MHz一5MHz之间
对于以发现缺陷为目的进行的初始扫查,应在规定范围 内尽可能选用低频;需进一步弄清缺陷特性需要提高分辨力时,可使用较高的频率
本部分推荐使用2MHz~2.5MHz
5.3.2.2探头种类及角度 根据铸件不同的几何形状和需检出缺陷类别的差异,可分别采用直探头或斜探头,或两种探头同时 采用,近表面区也可使用SE(双晶)直探头或(双晶)斜探头
双晶探头建议用于近表面缺陷以及深度小 于50mm的缺陷检测,双晶探头聚焦区域应能覆盖所要求进行检测的区域
横波检测时,斜探头折射角宜在35一70"之间
5.3.2.3晶片尺寸 晶片尺寸应依据检测声程和频率选择
声程较短时,应使用晶片直径6nmm一12nmm(或面积相当 的方晶片)小探头
声程较长(如单晶直探头大于200mm,单晶斜探头大于100mm)时,宜使用晶片尺 寸12mm一25mm的探头
5.3.2.4曲面扫查探头匹配 圆柱形或球形表面可按式(1)计算 探头与检测表面之间的间隙(g)不应大于0.5 mm
=a2/D + ( g=a
GB/T37400.14一2019 式中 -检测方向上的探头尺寸,单位为毫米(mm); D -工件直径,单位为毫米(mm)
若g>0.5mm,应使探头楔块与工件表面吻合,并重新设置灵敏度和扫查范围
5.3.3检测系统灵敏度 检测系统的灵敏度应至少保证能调整到5.6.4所要求的检测灵敏度
5.3.4耦合剂 耦合剂应能润湿整个受检表面,并且具有足够的导声性能
可以用水、机油、耀糊或其他性能相当 的介质
调整仪器和检测工件时应采用同一种稠合剂. 5.3.5参考试块 参考试块的声学特性应与被检铸件相同或相近
应测量参考试块与受检材料的材质衰减系数差异,以便后续对检测灵敏度及缺陷当量进行修正
5.4检测仪的校准 采用按照GB/T19799(所有部分)规定的校准试块,检测仪线性的校准应使用直探头或斜探头在 校准试块上进行
必要时,还应考虑铸件与校准试块的声速差异
如果可行,线性的校准尽可能直接在铸件本体上进行
5.5超声可探性的确认 检测前应进行可探性判断,符合要求后才能进行检测
可探性条件;先将仪器“抑制”旋钮置于零 位,使用频率2MHz一2.5MHz中某一频率的纵波直探头,对铸钢件的最大探测距离处(最厚处)或反 射杂波最多处进行探测;在最大被检深度处的平底孔的回波高度为示波屏高度的2/5时,若噪声信号反 射幅度比选定为纵波同声程检测灵敏度的反射回波低6dB以上,则该铸件适合超声检测(即可探性符 合要求) 著不能满足要求,可降低频率至1MHz,再进行可探性测试,若满足要求,可以采用该懒率检测,但 应在检测报告中加以说明
若降低频率仍不具可探性,则应对铸件重新进行热处理改善透声性,可探性满足要求后才能进行检 测
超声可探性要求按表2
表2超声检测可探性要求 最小平底孔直径 壁厚 mmm mm 300 300400 400600 600
GB:/T37400.14一2019 5.6检测 5.6.1检测范围 铸件受检部位,只要形状允许,整个受检区域都应进行检测
5.6.2检测工艺 应根据铸件的形状、尺寸、可能产生的铸造缺陷类型和可能在焊接时发生的缺陷等因素,选择合适 的声束人射方向和探头
最合适的检测工艺应由制造厂确定
应注意铸件的关键部位,必要时可编制 书面的检测工艺
焊接与制造过程中可能会产生危害性缺陷的部位,可采用斜探头检测
铸件受检部位应至少用直探头尽可能从两相对面进行检测
对于只能从一面进行检测的,应采用 直探头和双晶直探头检测
对于只能从一面进行检测,而且壁厚小于60mm的部位,只用双晶直探头 即可
铸件采用单面检测时,若需要发现靠近探头的近表面缺陷,则应使用近表面分辨力高的探头
对于单直探头扫查不能完全覆盖的部位,以及订货时规定的特殊区域,应补充横波斜探头扫查
5.6.3扫查速度 探头扫查速率应不大于150mm/s,进行全体积检测的,相邻两次扫查至少应有15%的重叠
5.6.4检测灵敏度 5.6.4.1基本原则 尽可能用铸件本体调节检测灵敏度
在不能用铸件本体的情况下,方可使用试块
采用试块时,除非不可行,则应测定传输修正AV,在测定传输修正时,既要考虑耦合面的表面质 量,还要考虑底面的表面质量,因其影响反射波高度(用作基准)
传输修正测定方法参见附录B,只有 AV,>4dB时才进行该修正
扫查时,应把增益提高到在示波屏能见到干扰背景(扫查灵敏度)
扫查过程中,要监视底面反射信 号的幅度是否有明显的降低
底面反射波幅的降低,不仅可能表明存在缺陷,也可能表明探头与铸件表 面鹏合不良,底面反射面不平行或铸件中局部的衰减变化
如果怀疑由于缺陷的存在引起底波降低会 超过应记录的值,则应对该部位在降低增益的情况下重新检测,并测定底波降低量
垂直于检测面的平面状缺陷的回波幅度可能较小,甚至可能小于3mm平底孔当量直径的记录限
若检测过程中,发现此类缺陷信号,因提高检测灵敏度,使这种反射体在示波屏上能清晰地见到其动态 回波图形(见图3 若受检部位表面质量情况有所变化,可能造成检测灵敏度的急剧变化
这种情况下,应遵守5.6.4.1 条第三段所述的调节扫查灵敏度的条件
采用双晶直探头检测时,灵敏度应在铸件上合面与底面尽可能平行的部位内进行调整
如果不 可能,则要使用有平行面的试块或钻孔的试块
用底面调节灵敏度时,若底面为曲面,其灵敏度修正与计算法相同
5.6.4.2DGS法 宜选用DXGS系统调节灵敏度,适用于直探头和斜探头检测
可使用铸件本体或参考试块,根据相应探头的DGS系统,调节检测灵敏度
应测量材料的声衰减,材质衰减系数(a)测量方法参见附录B
只有在衰减量影响超过4dB时才 进行该修正
DGS系统有DGS曲线、DG;S面板以及DGS软件等,DGS曲线应用参见附录C
GB/T37400.14一2019 5.6.4.3DAc距离-波幅曲线)法 用一组能覆盖受检铸件厚度的参考试块,找出各反射体的反射波最高点,将最高的反射波调至满屏 高的80%左右,在不动增益的情况下,依次连接各反射体反射波的最高点,由此形成一条光滑的曲线 该曲线一般应采用至少3个点进行绘制
如果在受检铸件厚度以内,超声波衰减量超过检测系统的动 态范围,则允许制作分段曲线
另外,只要能计算出超声波声衰减特性,也可采用DGS(5.6.4.2)或计算 法(5.6.4.4)原理,补充或确定DAC曲线
5.6.4.4计算法 计算法适用于检测厚度或声程大于或等于探头3倍近场的场合
灵敏度也是以仪器上设定的某一基准高度为基础来调节的
应按式(2)计算不同距离的平底孔与 大平底的分贝差值,按式(3)计算不同直径与不同距离处平底孔的分贝差值 2入.r .(2 =20lg 十2a(Er- 一rB T'.r 式中 -分贝差值,单位为分贝(dB); 入 波长,单位为毫米(mm); -所需的检测声程,单位为毫米(mn .Z m; -用以调节基准波高处的工件厚度,单位为毫米( mm .ZB 平底孔当量直径,单位为毫米(mm) 一十2a(a A --l .工 式中 平底孔当量直径,单位为毫米(mm); d1,d 平底孔埋深,单位为毫米(mm); Z1,.Z2 -衰减系数,单位为分贝每毫米(dB/mm)
材料的声衰减应进行测量,测量方法参见附录B
只有在材质衰减系数影响超过4dB时才进行 该修正
对于空心圆柱形工件,灵敏度修正所需增加的分贝差值应按式(4)计算 上-主a觉 式中 -分贝差值,单位为分贝dB); 工件内径,单位为毫米(G mm; D -工件外径,单位为毫米(mm) 注;“+”表示外圆径向检测,内孔凸柱面反射;“-"表示内孔径向探测,外圆凹柱面反射
也可以使用带有横孔(横孔长度应大于一20dB声束宽度)的参考试块
式(5)可用于平底孔和横 孔的直径转换(仅适用于D
>2A、r>5倍近场长度、单晶探头): 4.935Dm1 Do= (5 式中: 横孔直径,单位为毫米(mm); Da 平底孔直径,单位为毫米(mm)7 D FBH
GB:/T37400.14一2019 -波长,单位为毫米mm); -声程,单位为毫米(mm) 5.6.5 各类回波 有下列两种回波可能在铸件检测时出现 缺陷回波; 缺陷引起的底波衰减
以上两种回波既可单独出现,也可同时出现,均应注意并分别予以评定
回波高度以平底孔当量直径大小表示;底波衰减量是由底波高度的下降量以dB表示
5.6.6记录限及应记录的回波 达到或超过表3所规定的记录限的缺陷回波均应记录
不论回波高度大小如何,下列回波也均应予以记录 -带有深度方向或其他方向延伸的连续缺陷回波 认为对声束反射不利的铸造缺陷回波
所有探出应记录的缺陷部位均应做出标记,并应在检测报告中加以说明,可以草图或照片的形式
表3超声检测记录限 非延伸性缺陷 延伸性缺陷 壁厚 底波衰减量 区域 平底孔当量直径 dB mnm mm 300 >300400 边缘和中心区域 >400600 >12 >600 特殊边缘区 5.7 缺陷分析 所有应记录的缺陷均需进行详尽的分析
可以通过增加其他超声检测方法(其他频率角度和尺寸 的探头)或其他无损检测方法(如射线检测)辅助检测
5.8缺陷尺寸测定 5.8.1概述 超声检测,只有在特定条件(例如,已知缺陷类型、缺陷几何形状,声束能以最佳的角度人射到缺陷 等)下才有可能准确测定缺陷尺寸
通常,铸钢件中的缺陷不能满足这些条件
大的缺陷有时可能会看 成许多小的应记录缺陷
通过改变扫查方向或探头角度,有助于全面了解缺陷
5.8.2缺陷分类 根据缺陷实际尺寸与探头在缺陷处的声束直径相比较,缺陷分为非延伸性缺陷和延伸性缺陷
声 束直径可以从相应的探头说明书或声波曲线图中查出
声束直径(一6dlB)与声程的关系,对于最常用 的探头见图1,或用式(6)得出
GB/T37400.14一2019 近场区长度 品片尺寸 纵 波S mm MMIMMMIM 0 48.O 5.6 15 24 8X9 28 150 7 0X2卫 150 MHHz,L,10 2MHzL,10 ML,24 MHz,T,8×9 5 4MMtz,L,10 2MIz,L,24 4MHz,T,8×9 100 2Mz,T,8×9 4MHz.L.24 105MHz,L,24 1 4MIHz,T,20×22 70 60 50 40 30 20 I 100 200 300 400 00 说明: 声束直径,单位为毫米(mm); -声程,单位为毫米(mm). 图1近场区长度和常用单晶片探头远场区声束直径(一6dB)与声程关系的近似值 ASDs D;之 6 D 4N 式中 D 声束直径(一6dB),单位为毫米(mm); 入 -波长,单位为毫米(m nm; 声程,单位为毫米(mm) D 晶片直径,单位为毫米(mm); " ,单位为毫米(mm)
N 近场区长度(N- 5.8.3平行于受检面的缺陷尺寸的测定 在确定缺陷尺寸时,应尽可能选用近场区长度与缺陷声程相近的探头
移动探头,根据波幅降低程度,按以下方法测量缺陷尺寸 达到表3规定记录限的缺陷,应以记录限降低6dB测量 -5.6.6中所述的其他两类缺陷,应以最大回波高度降低6dB(半波高法)测量
在底波降低的情况下,应以缺陷处的底波相对于完好部位底波下降6dB的方式测量
尽可能准确地对这些探测点做出标记(例如;直探头的探头中心,斜探头的人射点)
将各标记点连 成一条外形轮廓线即给出缺陷的尺寸
对于斜探头,只要被检工件的儿何外形允许,将缺陷的各边沿点 10
GB:/T37400.14一2019 利用距离投影原理将其投影到检测面上
5.8.4垂直于受检面的缺陷尺寸的测定 推荐采用在缺陷部位声束直径尽可能小的探头(探头的近场点或双晶斜探头的聚焦区)
依据缺陷种类不同,可采用下列方法 -采用直探头测量:从两相对面采用垂直人射声束测量(图2); 采用斜探头测量;缺陷在深度方向上的延伸尺寸,通过斜角人射声波可以在缺陷上、下边沿上 各自测得的声程差而求得
说明: -缺陷在深度方向上的延伸尺寸,单位为毫米(m mm; 工件壁厚,单位为毫米(mm) S,S. -声程,单位为毫米mm
图2直探头测量深度方向上的缺陷尺寸 对于深度约为50mm左右或以内的近表面缺陷,可采用以下方法测量其深度方向上的延伸尺寸 采用双晶斜探头,把被测缺陷深度方向的最大回波高度调至100%示波屏高度,通过探头对缺陷的 垂直移动,找出回波高度下降至10%示波屏高度处,从声程S和S.以及折射角即可算出缺陷在深度方 向上的延伸尺寸(见图3).
回波高迷 100% 10% 断断续续的缺陷 图3斜探头测定垂直于受检面的延伸性缺陷的延伸尺寸和回波动态波形 1
GB/T37400.14一2019 回波高度 100% 109% b) 连在一起的缺陷 说明 -沿壁厚方向上的缺陷尺寸,其值为(s-s)cosa,单位为毫米(mm); cd S,S. 声程,单位为毫米(n mm; 折射角,单位为度("). 图3(续) 5.9质量等级 凡是达到或超过记录限的缺陷,均应按表4评定铸件质量等级
表4铸件超声检测质量分级 质量等级 特性 单位 区域" 受检区域内的 >100 >100 >50 >100 >50 50 50 50 50 mm 铸件壁厚 l00 l00 100 600" 600 600 非延伸性缺陷" 边缘 最大平底孔当量 mm 直径 中心 边缘 不作为验收依据 100mm×100mnm 表面中需记录的 中心 不作为验收依据 缺陷个数 最大底波降低量 dB 延伸性缺陷" 边缘 最大平底孔 mm 当量直径 中心 边缘 区域厚度的15% 缺陷在壁厚 方向上的最大 中心 壁厚的15% 延伸范围 12
GB:/T37400.14一2019 表4(续 质量等级 特性 单位 区域" 75 75 75 75 75 75 75 75 边缘 75 缺陷宽度<6dB声 束直径时缺陷 mmm 75 75 100 50 75 中心 00 75 20 100 最大长度 边缘 600 10001000 600 2000200020002000 2000 最大单个缺陷 mm 面积 中心 100001000o1500015000150002000o150001500020000 边缘 100001000010000100001000010000100001500015000 每个评定框内 mm 最大总面积 中心 100001500015000150001500020000150002000020000 150000 100000 评定框 nmm 390mm×390mm (320mm×320mm 2MHz -2.5MH 时,非铸件形状或 dB 12 稠合不良引起的 底波降低量 区域划分;边缘区=d/3,但最大30mm,中心区=剩余的其他区域,l=检测部位的壁厚,见图4
质量等级1级仅用于待媒区域和特殊边缘区
若无其他要求,当壁厚超过600mm时,记录和允许极限为8mm平底孔当量直径,但信噪比至少为6dB 发生争议时,缺陷当量和尺寸,应以晶片直径为24mm,2MHz的直探头检测结果为准,或与其声束特性相同 的探头
延伸性缺陷尺寸测量时,尽可能用缺陷处声束直径最小的探头,如双晶探头的焦点,或探头的近场
间距小于25mm的缺陷显示应当作为一个缺陷评定 d6.最大30mm 边缘区 中心区 边缘区 d3.最大30mm 说明;壁厚方向区域划分以铸件最终尺寸为基准
图4铸件壁厚方向区域划分 5.10检测报告 检测报告至少包括下列内容 13
GB/T37400.14一2019 工件信息 a 名称、图号,炉号、工件号等 2 被检部位; 材料 3 表面状况 ! 5 检测时机; 6 检测标准和验收标准或等级
检测范围
b 检测仪型号、探头型号,试块型号(若使用
c d 检测部位和检测方法
灵敏度
e fD 缺陷当量、尺寸和位置(例如:草图或照片),以及其他描述缺陷的信息,例如:平底孔当量直径、 底波衰减量、深度位置和深度方向上的延伸尺寸,长度和面积
检测日期和检测人员姓名
6 铸钢件射线检测 6.1检测前应明确的内容 订货时需明确以下事宜 检测范围; 像质级别、照相方法; 铸件各区域各部分的质量等级, 是否要求书面检验规程; 要求进行的特殊检测方法
6.2像质级别 射线照相像质分为A级和B级
A级适用于结构复杂、检测区厚度差较大的工件,一般照相技术即可达到A级要求;B级适用于检 测区厚度差小,近似于平板的工件,适用于A级照相检出能力不够充分的场合
除非订货时有明确规定,一般使用A级即可
6.3设备与器材 6.3.1透照设备 可使用便携式X射线机(X光机)电子加速器和7射线装置
便携式X射线机应符合GB12664的要 求,直线加速器应符合GB/T20129的要求,Y射线机应符合GB/T14058的要求
6.3.2感光材料 采用GB/T19348.1规定的工业射线照相胶片,选用金属箔增感屏
A级或B级照相适用的胶片 与增感屏组合按表5规定
14
GB:/T37400.14一2019 表5胶片等级与增感屏 胶片等级" 金属箔增感屏种类和厚度 射线装置 透照厚度 A级照相 B级照相 A级照相 B级照相 不使用,或使用厚度0.03mm的铅箔增 <10kx 感前屏及后屏 T3 T2 >100kV150kV s0.15mm, ,铅前屏及后屏 >150kV250kV 0.02mm0.15mm,铅前屏及后屏 T配2 50mm 0.02mm0.2mm,铅前屏及后屏 T: >250kV500kV 0.1nmm一0.3mm,铅前屏" >50mm T3 0.02mm一0.3mm,铅后屏 0.02mm~0.2tmm. 0.lmm一0.2mm, 铅前屏 铅前屏" 12Ir T3 T2 0.02mm~0.2mm铅后屏 <100mm "Co T3 T3 前屏及后屏,0.25mm0.7mm钢或铜 100mm S100mm 前屏及后屏",0.25mm一0.7mm俐或铜 1MeV4MeV T3 T2 l00mmm T <100mm T2 前屏'
GB/T37400.14一2019 6.3.4像质计 使用GB/T198032005以及GB/T23901.12019规定的一般选用R20的FE型像质计
6.3.5观片灯 应满足GB/T19802的规定,或具有同等性能
观片灯的最大亮度应能满足评片的要求
6.4透照方法 6.4.1透照方向 射线束应对准检测区中心,并与工件表面垂直(但当认为从别的方向进行透照更有利于缺陷的检出 时,则不受此限制)
尽量采取单壁透照方法
6.4.2像质计放置 6.4.2.1如图5图7所示,将含有应识别钢丝见表6)在内的像质计置于工件源侧表面,与工件一起 被透照
如果像质计难于放置在源侧表面,则可以紧贴胶片侧表面放置,但透照时像质计至胶片的距离 应为应识别钢丝线径(见表6)的10倍以上,同时要在像质计上放置标记“F”且其影像应出现在底片上
射线源 胶片侧像质计 源倒像质计 射线讽 胶片测像质计 源侧像质计 胶片测像质 工件 射线源 源侧像质计 胶片 胶片 胶片倒像质计 工件 胶片他像M让 像质计 激侧像质让 胶片侧像质让 简形工件照相布置(源在内单壁透照)》 平板形工件 图5照相布置 16
GB:/T37400.14一2019 射线源 工件 源侧像质计 胶片 胶片侧像质计 图6筒形工件照相布置(双壁单影法) 射线逐 像质计 工件 胶片 图7筒形工件照相布置双壁双影法 表6应识别的像质计最小线径 透照厚度 透照厚度 应识别的最小线径 应识别的最小线径 mm mm mm mmm A级 A级 B级 B级 6.4 0.10 >10~13 >13~16 0,.25 >56.4 >6.4一8 0.125 >13~16 >16~20 0.32 为 6.4 8~10 0.16 >l620 >2025 0.40 >10~13 0.20 >2026 2532 0.50 810 17
GB/T37400.14一2019 表6(续 透照厚度 透照厚度 应识别的最小线径 应识别的最小线径 mm mmm mm mm A级 A级 B级 B级 >2632 >32一45 0.63 >140180 >150190 2.5o >3250 >45一56 0.8o >180~225 >190~240 3.20 >50~63 >56~70 1.00 >225280 >240~300 4.00 >6380 >7090 1.25 >280360 >300~380 5.00 >80~100 90~120 1,60 >360 >380 6.30 100140 >120~150 2.00 6.4.2.2透照厚度变化较小时,在能代表透照厚度的部位放置1个像质计
6.4.2.3透照厚度变化较大时,在能代表透照厚度较厚的部位和较薄的部位分别放置1个像质计
6.4.2.4简形工件按图5进行周向全景照相时,一般放置4个像质计,分布在圆周的4等份位置
6.4.3照相布置 射线源将像质计,胶片间的相对位置见图5~图7
射线源至工件的最短距离(L),由焦点尺寸f、工件源侧表面至胶片的距离L决定,应满足式(7) 或式(8)的要求
,2s A级照相一 7.5L 式中 射线源至工件的距离,单位为毫米(mm); I 焦点尺寸,单位为毫米(mm); -工件源侧表面至胶片的距离,单位为毫米(n mm .,2/3 B级照相: 15L" 式中 -射线源至工件的距离,单位为毫米(mm); 焦点尺寸,单位为毫米(mm); 工件源侧表面至胶片的距离,单位为毫米(mm)
L小于公称厚度的1.2倍时,式(7),式(8)及图8中的L值取公称厚度值
射线源至工件的最短距离L值可由图8查出
上述几何条件不能满足时,若像质要求能够满足,则可不受该最短距离L值规定的限制
18
GB/T37400.14一2019 -500 -400 300 200 5000 10 2000 3000 100 2000 1000 80 -60 1000 500 50 40 30o 500 30 200 300 -20 200 100 -10 50 100 30 50 20 30 10 20 0.5 10 图8 由工件表面至胶片的距离(4.)和射线源尺寸()决定源至工件表面最短距离(L)的诺模图 6.4.4透照区标记 照相时,检测区表面应放置标记,其影像应出现在照相底片上
照相底片应与检测区一一对应
6.4.5胶片搭接 需要2张或2张以上胶片对工件进行分割照相检测时,胶片间应有一定的重叠区,此时,在工件表 面放置的搭接标记应出现在底片上
6.4.6x射线管电压及射线源的选择 最高允许X射线管电压不应超过图9规定
此外,Y射线和1MeV以上X射线适用透照厚度范围 19
GB/T37400.14一2019 见表7规定
如果表6的像质要求能够满足,则可不受此限制
00 400 300 200 100 7飞 6o 0 40 30 20 10 2加 304607o0 透照厚度/mm 图9500kV以下x射线装置最高管电压与透照厚度的关系图 表7?射线和1MeV以上x射线适用透照厚度 适用透照厚度 射 线 源 A级检验 B级检验 192Ir 20mm~l00mm 20mm90mm 60mm150mm Co 40mm一200mm X射线1MeV~4MeV 30mm~200mm 50mm180mm x射线4MeV~12MeVy 50mm以上 80mm以上 x射线12MeV以上 80mm以上 100mm以上 6.4.7胶片与增感屏 X射线、Y射线与不同透照厚度对应的胶片及增感屏组合由表5规定
但如果满足表6的像质要 求,则可不受此限制
6.4.8多层胶片法 工件形状复杂、厚度变化较大时,可以采用图10所示的多层胶片法进行照相
该方法是将2张或 2张以上感光度相同或不同的胶片装人同一暗盒进行照相
20
GB:/T37400.14一2019 射线源 像质计 工件 胶片 图10多张胶片照相法 6.5底片质量要求 6.5.1应识别的像质计最小线径 射线底片上像质计至少应识别表6规定的最小线径
如底片黑度均匀部位能够清晰地看到长度不 小于10 mm 的连续金属丝影像时,则该丝认为是可识别的
6.5.2底片黑度 检测区内缺陷影像外的底片黑度应在表8规定范围内
但若能达到6.5.1所规定的像质要求,也可 不受此限制
表8黑度范围 检 验 级别 黑度范围 A级 l.04.0 1.54.0 B级 多张胶片照相法,单片观察时底片黑度应满足表8要求;迭片观察时单片黑度最低应在0.8以上、 迭片黑度最高应在4.0以下
6.5.3胶片处理 不应产生妨碍缺陷评定的伪缺陷影像
6.6底片观察 6.6.1观片灯 根据底片黑度,按表9类别,使用6.3.5规定的观片灯对底片进行观察
21
GB/T37400.14一2019 表9观片灯的适用范围 观片灯亮度 底片黑度 cd/m 最大1.5 最小100o 最小10000 最大2.5 最大3.5 最小30000 最大4.5 最小300000 6.6.2观察方法 在暗室使用适合底片尺寸的遮光罩对底片进行观察
6.7散射线屏蔽 降低散射线影响的方法如下 在X射线装置窗口放置照射筒或准直装置,将射线束控制在检测区所需的最小范围内
另 a 外,在暗盒背面、侧面放置1 n厚铅板,以屏蔽来自物体反射的散射线
mm一4mm 周向全景曝光中无法使用限制射线束的装置时,在尽可能在宽敞的透照室内进行照相
工件 b 尽可能远离周围物体,相距较近的物体应覆盖上铅板 用铅字“B"验证背散射的影响
铅字“B”高10mm、最小厚度1.5mm,紧贴暗盒背面放置
若 在底片上出现黑度低于周围背景黑度的“B”字影像,则说明背散射防护不够,应增大背散射防 护铅板的厚度
若底片上不出现“B"字影像或出现黑度高于周围背景黑度的“B"字影像,则说 明背散射防护符合要求
6.8缺陷影像质量评级方法 6.8.1评级步骤 缺陷影像(以下简称缺陷)的质量评级按如下步骤进行 按6.6规定观察底片
a b) 确认底片符合6.5的象质要求
c 确定缺陷性质,缺陷分为气孔、夹砂及夹渣、缩孔,裂纹 d 确认被检铸件的公称厚度值
评定视野由公称厚度值决定,且取最小公称厚度值
e f 测量缺陷尺寸,并规定 观片后,仅对判断为缺陷的影像进行测量,不明阴影排除在外; 1 2 仅对影像的清晰部分进行测量,虚影部分不计人; 3) 两个或两个以上缺陷在底片上重叠时,分别进行测量
缺陷评级方法如下 g 气孔类缺陷按6.8.2.1换算出缺陷点数,然后按表10评级; 1 2 夹砂及夹渣类缺陷按6.8.2.1换算出缺陷点数,然后按表10评级; 3)缩孔类缺陷,先按其影像形状分为线状缩孔或树枝状缩孔,线状缩孔按6.8.2.2测量长度 然后再按表10评级;树枝状缩孔按6.8.2.2测量面积,然后按表10评级 4)气孔、夹砂及夹渣、缩孔类缺陷评级时,表11和表12给出了不计人评定的最大缺陷尺寸
当按表中“1级”对应尺寸去除不计缺陷后评定结果为1级时即定为1级;按表中“1级”对 22
GB:/T37400.14一2019 应尺寸去除不计缺陷后评定结果为2级或2级以上、按表中“2级和2级以上”对应尺寸去 除不计缺陷后评定结果为1级时,则应定为2级;评定结果为2级或以上时,其结果即为 最终级别 5)如果同时存在2种或以上缺陷,就应当分别评级
在有必要确定其综合级别时,可取其中 级别数较大(等级低)者为其综合级别
在同一评定视野内,最低等级包括2种以上缺陷时,综合级别应降低1级
但是,在各种缺陷都独 自为1级时只有超过缺陷点数、缺陷长度或缺陷面积允许限度1/2的缺陷在2种以上时,综合级别才 定为2级
此外,按表11和表12中“2级和2级以上”对应尺寸去除不计缺陷后评为1级、但按“1级”对应尺 寸去除不计缺陷后评为2级时,如果还有混合存在的缺陷定为2级,则综合级别应降低到3级
表10射线检测缺陷影像的最大允许值 质量等级 公称厚度 缺陷类型 mm 14 <10 14 21 >l0~20 >2040 l0 22 32 15 气孔" >40~80 16 24 32 42 80120 19 28 38 49 42 56 >120 22 32 14 <10o >10一20o 14 21 >20~40 10 15 22 32 夹杂(夹砂,夹渣" >4080 16 24 32 42 19 38 49 >80120 10 28 22 32 120 12 42 56 <20 12 23 75 120 45 >20一40 18 36 63 100 145 线状缩孔 >40120 30 63 110 160 230 120 50 l10 145 180 250 20 250 450 800 1600 3600 >2040 6300 600 900 1650 2700 树枝状缩孔 800 1350 2700 5400 9000 >40~120 120 1000 2000 3000 8000 12000 缺陷位于评定框边界时,框外部分应计算
不应有裂纹.内冷铁未完全熔合和泥芯撑未完全熔合性质的缺陷
气孔,夹砂和夹渣类缺陷以点数计
线状缩孔以毫米为单位计
树枝状缩孔以平方毫米为单位计
23
GB/T37400.14一2019 表11不计点数的缺陷的最大尺寸 单位为毫米 公称厚度 评定级别 <10 >10一20 >2040 >80120 >120 4080 1级 0,.4 0.5 1.0 1.5 2级和以上 0.7 1.,0 1.5 2.0 表12不评定缺陷的最大长度或面积 公称厚度 mm 评定级别 >80120 l0一20 20一40 4080 120 线状 5,0mm 1级 树枝 10mm 线状 5.,0tmm 10mm 20mm 2级和以上 树枝 30mm 50mm" 90mm 6.8.2缺陷点数、缺陷长度和面积 6.8.2.1缺陷点数 换算气孔、夹砂及夹渣类缺陷点数时,应将表13规定的评定框置于检测区内缺陷点数最多的区域
单个缺陷,根据其尺寸按表14换算其点数
表1l规定了不计点数的缺陷尺寸,在测量缺陷尺寸以确定 是否计人其点数时,仅测量缺陷影像黑度较高区域的尺寸,不包括周围的虚影部分
评定框内存在多个缺陷时,将各单个缺陷的点数相加,换算其总点数
评级时,只计算评定框内缺陷的总点数,但如果评定框外的缺陷正好位于评定框的边界上,则该缺 陷的点数应计人总点数中
表13气孔、夹砂夹渣类缺陷评定框要求 单位为毫米 公称厚度 10 >1020 >20~40 >4080 >80~120 >120 评定框直径 20 30 50 70 表14缺陷尺寸与点数 -25.0~ 缺陷尺寸 >2.0一 >4.0 >6,0一 >8,0 >10,0 >15.0 >20.0一 2.0 4.0 6.,0 8.0 10,0 15,0 20.0 25.0 30.0 mm 缺陷点数 12 16 20 40 24
GB:/T37400.14一2019 6.8.2.2缺陷长度和面积 评定框应置于检测区内缩孔长度或面积最大的区域
2个以上缩孔密集分布时,评定框内应尽可 能多地包括最长的和面积最大的缺陷
当大缺陷的尺寸超过评定框的直径时,最大缺陷置于评定框的 中心位置
评定框的尺寸见表15规定
不评定缺陷的最大长度或面积见表12规定 线状缩孔的长度,取连续状态的缺陷的最大长度
2个以上的缩孔,取各自长度的总和为该组线状 缩孔的总长度
如果评定框外的缺陷正好位于评定框边界上,框外缺陷也应测量进去
树枝状缩孔的面积,应取连续状态缺陷的最大长度与垂直方向上最大宽度的乘积
如果评定框外 的缺陷正好位于评定框边界上,测量时框外缺陷应包括在内
当树枝状缩孔中混存有线状缩孔时,将线 状缩孔当作树枝状缩孔处理,但只取其1/3长度值,以毫米(mm)为单位并圆整为整数值
表15缩孔类缺陷评定框要求 单位为毫米 <10 >1020 >20一40 >40~80 >80~120 >120 公称厚度 50 70 评定框直径 6.8.3缺陷影像质量等级 6.8.3.1气孔类缺陷 根据气孔缺陷的点数,按表10评级
此外,不应存在单个气孔尺寸超过1/2公称厚度或15mm的 情况 6.8.3.2夹砂及夹渣类缺陷 根据夹砂或夹渣缺陷的点数,按表10评级
此外,不应存在单个夹砂或夹渣的尺寸超过公称厚度 值或30mm的情况
6.8.3.3缩孔类缺陷 线状缩孔和树枝状缩孔按表10评级
6.8.3.4裂纹类缺陷 不应存在裂纹类缺陷
6.9检测报告 检测报告中应记录以下事项: 检测实施部门; a b 产品名称; 照相日期 c d) 底片编号; 材质; ee f 公称厚度; 透照厚度 g h) 照相设备; 射线源尺寸; 管电压或丫源类别; 25
GB/T37400.14一2019 管电流或丫源活度; k D 曝光时间; m胶片等级; 增感屏 n 像质计 P 源至胶片距离 底片像质(像质计可识别的最小线径、黑度范围); 检测部位及相关事项 rr s 检测人员资格及签名; t 其他事项
铸钢件渗透检测 7.1检测前应明确的内容 订货时需明确以下事项: 检测范围 铸件各区域的质量等级; 是否要求书面检验规程; -要求进行的特殊检测方法
7.2安全防护 对于有毒、易燃,易爆、易挥发的材料、用电安全及有害的紫外线辐射等,均应注意防护 渗透检测一般都是使用有毒、易燃和易挥发材料,对此应采取一定措施防护
应避免这些材料长时 间、反复直接接触皮肤和黏膜
工作场所应通风良好,远离热源,火花和明火
应始终严格按制造商说 明书小心使用渗透检测材料和设备
若使用UV-A紫外源,要保证滤光器始终完好,只能使用经过滤的安全紫外线,避免紫外线直接照 射眼睛
7.3检测要求 7.3.1方法概述 渗透检测前,检测面应进行预处理(见7.5,1)
然后在检测区施加合适的渗透剂,让其渗人表面开 口缺陷
经过适当的渗透时间后,去除多余渗透剂,再施加显像剂,吸出缺陷中的渗透剂,形成清晰可见 的放大缺陷显示
同一检测部位要实施多种无损检测时,应首先进行渗透检测,以免污染物进人开口缺陷
假如在其 他无损检测之后再进行渗透检测,则在检测前应彻底清理掉进人缺陷中的所有污染物
7.3.2操作程序 -般情况下的操作程序,见图11
26
GB:/T37400.14一2019 准备和预清洗 干燥 施加后乳化型渗 海加水洗型渗酒 施加溶剂去除型 剂和允许的渗透 渗透剂和允许的 透剂和允许的涉 时间 透时间 渗透时间 水和溶剂 水喷洗 水洗 施加溶剂去除剂 施加亲油性孔化 剂和允许的乳化 时间 施加亲水性乳化 擦洗 剂和允许的乳化 时间 允许千燥 水洗 水洗 多余渗透剂去除效果检查 千燥 干燥 施加水溶性显像剂 施加水悬浮显像剂 施加干粉显像剂 干燥 允许千饮 显像时间 观察 后清洗 若有要求,则做防护 图 11渗透检测的主要步骤 7.3.3设备 渗透检测设备,取决于受检件的数量、尺寸和形状,见GB/T18851.4
7.4检测材料及灵敏度 7.4.1材料族 渗透检测有各种不同的检测系统 一个材料族由渗透剂、乳化剂(需要时清洗剂和显像剂组成 使用一族材料时,其渗透剂乳化剂清沈剂和显像剂应来自同一制造商
7.4.2检测方法分类 根据渗透剂的种类、渗透剂的去除和显像剂的种类不同,渗透检测方法按表16进行分类
27
GB/T37400.14一2019 表16渗透检测方法分类 渗透剂 渗透剂的去除 显像剂 分类 分类 名称 方法 名称 名称 荧光渗透检测 水洗型渗透检测 干粉显像剂 着色渗透检测 亲油性后乳化渗透检测 水溶解显像剂 荧光、着色渗透检测 溶剂去除型渗透检测 水悬浮显像剂 亲水型后乳化渗透检测 溶剂悬浮显像剂 自显像 7.4.3灵敏度 -族材料的灵敏度等级,应用1型参考试块(GB/T18851.3一2008)进行测定
等级评定应按材料 型式试验方法进行
要能检出更小的缺陷,所用材料的灵敏度就应越高
根据表17中要求的质量等级,质量等级01和 1级(见7.6.2),应使用符合GB/T18851.2的高灵敏度渗透检测材料
7.4.4其他要求 检测时,若某一制造商的渗透材料不够用,不应用其他制造商的材料补充或代用
特定情况下使用的渗透检测材料,应按GB/T18851.2需要满足特殊要求,如可燃性、硫、卤素、钠 和其他污染物含量
7.5检测工艺 7.5.1受检表面的预处理 受检表面应清理,去除污垢、铁锈油、油脂或油漆等污染物,保证检测面无残留物,渗透剂容易渗人 缺陷
清理面积至少为检测部位四周向外扩展25mm. 根据铸件要求的不同质量等级,各质量等级要求的表面粗糙度见表17
受检表面应彻底干燥,以免缺陷中残留有水或溶剂
7.5.2施加渗透剂 7.5.2.1 施加方法 渗透剂可采用喷、刷浇、浸等方法施加到受检工件表面上
在整个渗透时间内,应一直保持渗透剂完全湿润检测表面
7.5.2.2温度 检测面温度应保持在10C50C范围内
特殊情况下,温度不低于5C时也可以使用
温度低于10C或高于50C时,应按GB/T18851.6或GB/T18851.5的规定,对渗透材料族和检 测工艺进行验证,满足要求后才能使用
7.5.2.3渗透时间 渗透时间取决于渗透剂性能、检测温度、受检零件的材料和受检缺陷特性
渗透时间可在5min 1一60min范围内
渗透时间应不少于灵敏度测定所用时间,或不少于渗透剂 28
GB:/T37400.14一2019 制造厂商推荐的时间
任何情况下,在渗透时间内渗透剂不能变干
7.5.3 多余渗透剂去除 7.5.3.1水和溶剂 用水去除多余渗透剂时,可喷水冲洗或用湿布擦
冲洗时要尽量减小机械作用的影响
水温不应 超过50C
用溶剂去除多余渗透剂时,首先应使用干净不起毛的布擦去多余渗透剂,然后再用干净不起毛的 布,蘸少许溶剂进行擦洗
不应将溶剂直接喷到受检表面上进行清洗
7.5.3.2乳化剂 7.5.3.2.1亲水性(可水稀释 施加乳化剂之前,宜先进行水洗
应使用浸泡或起泡设备施加乳化剂
乳化浓度和接触时间,应由使用者根据制造商说明书通过预 先试验来确定
乳化剂接触时间不应超过预试验确定的时间
乳化后,应进行最后水洗
7.5.3.2.2亲油性(油基》 采用浸没法施加乳化剂,接触时间应由使用者根据制造商说明书或通过预先试验来确定
乳化后,应进行水洗
7.5.3.3水-溶剂 应首先使用水除去多余的水洗型渗透剂
随后用干净的不起毛的布,蘸少许溶剂进行清洗
7.5.3.4多余渗透剂去除效果检查 去除多余渗透剂时,应目视检查检测表面的渗透剂残留状况,工件上不应出现过度背景
荧光渗透 剂,应在Uv-A光源下检查
检测面上UV-A的最低辐照强度不应小于3w/m(300w/em=)
7.5.3.5干燥 除水基显像剂外,去除多余渗透剂后,应尽快采用下述方法之一干燥检测面 用清洁、干燥、不起毛的布擦; aa b 在环境温度下蒸发; 升高温度蒸发; c d 强制空气循环; a)d)方法的组合
干燥时,表面温度不应超过50C
7.5.4施加显像剂 7.5.4.1概述 显像剂施加应在去除多余渗透剂后尽快进行
使用时显像剂应搅拌均匀,检测面上显像剂厚度要 均匀
7.5.4.2干粉 干粉显像剂只可与荧光渗透剂一起使用
显像剂应采用下述方法之一均匀地施加到检测面上: 29
GB/T37400.14一2019 喷粉 静电喷涂,聚束喷枪; 流化床或喷粉舱 应在检测表面上形成薄薄的涂层,不应有局部堆积 7.5.43水悬浮显像剂和水溶性显像剂 使用浸没在搅动的悬浮液中或使用适当的装置喷洒,使其在工件表面覆盖一层薄而均匀的显像剂
显像剂的浸没时间和温度,应由使用者根据制造商说明书或通过预先试验来确定
只要能确保得到最 适宜的结果,浸没时间应尽可能短
检测工件可通过蒸发或空气循环烘箱干燥
7.5.4.4溶剂型显像剂 用喷洒方法均匀施加,使显像剂刚好润湿检测面,形成均匀的薄膜
7.5.4.5特殊用途的水基或溶剂型显像剂(如可剥离显像剂 渗透检渊过穆中,发现需记录的显示时,应按以下方法处理! 用干净、干燥、不起毛的布擦去显像剂 施加相同的渗透剂,然后从预清洗到施加显像剂,严格按原来的工艺方法操作; 去除多余渗透剂和工件干燥后,按制造商推荐的方法施加可剥离显像剂 等推荐的显像时间过去后,小心剥下显像剂薄膜
在与工件直接接触的薄膜表面就会呈现出 显示
7.5.4.6显像时间 显像时间宜在10min一30min之间
显像开始时间要求 干显像剂施加后立即进行 湿显像剂完成干燥后立刻进行
7.5.5观察 7.5.5.1概述 初次观察宜在施加显像剂后或在显像剂干燥后立即进行
最终观察应在刚过显像时间后立即进行
观察时可使用反差眼镜或2倍10倍放大镜协助观察
7.5.5.2观察条件 7.5.5.2.1荧光渗透 不应佩戴光敏眼镜 进人暗室的操作人员,眼睛应有足够的黑暗适应时间,一般至少5nmin UV辐射不应直接照射操作者眼睛
操作者要观察的所有表面,不应发荧光
操作者视野内不应有在UV光下发荧光的纸或布
如有必要,检测室可安装UV-A背景灯,以便操作者能自由移动
检测表面应在UV-A光源下观察,光源应符合GB/T5097的要求
检测表面的UV-A辐射强度 不应小于10w/m(1000w/cm=),可见光照度不应大于20lx 30
GB:/T37400.14一2019 7.5.5.2.2着色渗透 应在自然光或白光灯下检测,检测面的白光照度不小于500lx
观察现场避免阴影和反光
7.5.6后处理和防护 7.5.6.1 后处理 完成检测后,只有渗透检测材料可能影响后续工序或使用功能时,才对工件进行后处理
7.5.6.2防护措施 如有要求,应对工件做适当的腐蚀防护
7.5.7重新检测 不能明确评定显示,需要重新检测时,应从预处理开始,重复整个检测工艺过程
7.6显示的评定与质量等级 7.6.1显示评定 显示尺寸的最终评定应在规定的最短显像时间之后,缺陷显示衰退之前的时间段内进行
显示分为以下3种 相关显示;缺陷中渗出的渗透剂所形成的痕迹显示,一般也称为缺陷显示; 非相关显示:与缺陷无关的外部因素所形成的显示 伪显示;由于渗透剂污染及检测环境等所引起的渗透剂显示 仅对相关显示进行评定
7.6.2质量等级 铸件渗透检测质量等级见表17
表17渗透检测质量分级(评定框尺寸150mm×105mm 非线性缺陷显示 线性缺陷显示或成排缺陷显示 应记录的《成排缺陷显示除外单个线性|全部线性单个线性全部线性|单个线性全部线性 表面粗糙 或成排缺和成排缺或成排缺和成排缺或成排缺和成排缺 最小缺陷 质量度Ra的最 陷显示 陷显示陷显示 显示的直 陷显示 陷显示 陷显示 缺陷显示 等级 大值 缺陷显示 径或长度 受检部位的铸件厚度 的长度 HAm 个数 mmm <16mm >16mm50mm >50mm mm 最大允许长度/mm 01 0.3 6.3 1.5 10 6 10 20 12 12.5 9 10 10 18 18 30 12 18 18 21 30 45 20 1" 10 70 32 21" 18 25 27 45 注:表中所列尺寸是指痕迹显示尺寸,而不是缺陷的实际尺寸
质量等级可仅用于承受高负荷的小铸件和机械加工面 在缺陷评定框内,同时存在线性显示和非线性显示时,尺寸应满足各自要求,缺陷个数为两者之和
GB/T37400.14一2019 7.7检测报告 检测报告应至少包括以下内容 检测工件信息 a 名称、图号,炉号、工件号等 2 被检部位; 33) 材料 表面状况 4! 57 检测时机 检测标准和验收标准或等级 66 所用渗透材料型号,制造商名称,材料名称及其批号 b c 检测方法
d 检测结果(发现缺陷的描述和位置) 检测日期和操作者姓名
e 8 铸钢件磁粉检测 8.1检测前应明确的内容 订货时需明确以下事项: 检测范围; 铸件各区域的质量等级; 是否要求书面检验规程; 退磁及其要求
8.2安全防护 对于有毒、易燃,易爆、易挥发的材料、用电安全及有害的紫外线辐射等,均应注意防护 8.3方法概述 磁粉检测基本步骤有: 磁化被检区域; 施加磁介质; 观察和评定磁痕显示
8.4表面状态和表面准备 受检表面应干净,油、油脂、沙粒和氧化皮及其他妨碍缺陷磁痕辨认的物质均不应存在
所需的表 面状态可通过喷丸、打磨或机械加工的方法予以达到
各质量等级要求的铸件表面粗糙度Ra的最大值见表19
覆盖非铁磁性涂层(油漆)的表面也可检测,但涂层不能有戳拱,且厚度不超过50wm
超过这个尿 度,则应在检测前进行检测灵敏度验证
当使用非荧光磁粉时,磁粉的颜色应与被检表面的底色有足够的反差
也可通过采用彩色磁粉或 在被检表面涂反差剂来达到
干法检验时,铸钢件检测表面应干燥
32
GB:/T37400.14一2019 8.5设备和器材 8.5.1设备 磁粉检测设备应符合GB/T15822.3的规定
当使用便携式电磁轭时,在磁轭最大间距情况下,交流电磁轭至少应有4.5kg的提升力,直流包 括整流电)电磁轭或永久性磁轭至少应有18kg的提升力,交叉磁轭(旋转磁场)至少应有ll.8kg的提 升力磁极与试件表面间隙为小于或等于0.5mm). 8.5.2磁介质 8.5.2.1磁介质要求 磁介质性能应符合GB/T15822.2的要求
检测介质可以用干粉,也可以用磁悬液
可以是荧光 也可以是非荧光 磁粉应具有高磁导率、低矫顽力和低剩磁,非荧光磁粉应与被检工件表面颜色有较高的对比度
当选择质量等级01级时(见8.13.2),宜采用荧光的磁悬液 磁悬液浓度应根据磁粉种类、粒度、施加方法和被检工件表面状态等因素来确定
一般情况下,磁 悬液浓度范围应符合表18的规定
测定前应对磁悬液进行充分的搅拌
表18磁悬液浓度 配制浓度 沉淀浓度(含固体量 磁粉类型 ml/100ml 1025 1.22.4 非荧光磁粉 荧光磁粉 0.53.0 0.10.4 8.5.2.2磁介质应用 8.5.2.2.1干粉 干粉通常用于交流和半波整流的磁化电流或磁轭进行连续法检测,通电时间至少0.5s
当零件被 磁化时,磁粉可采用手动或电动喷粉器以及其他合适的工具均匀地撒在工件被检面上
磁粉不应施加 过多,在施加磁粉之后和切断电源、观察缺陷之前,应吹去多余磁粉
在吹去多余磁粉时,不应破坏缺陷 磁痕
8.5.2.2.2磁悬液(湿法 湿法主要用于连续法和剩磁法检测
采用湿法时,应确保整个检测面被磁悬液润湿
磁悬液在使用前,应进行充分搅拌
磁悬液的施加可采用喷,浇、浸等方式,不能采用刷涂法
采用湿法时,检测前应进行水断试验,验证磁悬液在工件表面的润湿性
将磁悬液施加于被检表 面,若磁悬液液膜在工件表面均匀连续而没有断开时,即表明润湿性良好
8.5.3试片块) 常用试片(块)见附录D. 8.6磁化方法 磁化方法通常有(见GB/T15822.1) 33
GB/T37400.14一2019 -通电磁化(轴向通电、触头通电以及感应通电) -通磁磁化(穿棒法、通电导体感应磁化、便携式电磁轭、固定式磁设备、刚性线圈以及柔性 线圈 上述磁化方法可以结合使用,构成复合磁化方法,例如旋转磁场
可以采用上述一种或几种磁化方法,对零件进行局部或整体磁化
选用合适的磁化方法应考虑铸钢件的表面状态、形状、最易发生缺陷的方向、仪器设备条件等
8.7电流种类 磁粉检测常用的电流类型有;交流、整流电流(全波整流、半波整流)和直流
各种磁化方法所要求的交流磁化电流为有效值,整流电流值为平均值
磁化电流的波形电流表指 示及换算关系符合G;B/T15822.1的规定
通常情况下,对于表面缺陷,交流电的检测灵敏度最高
若需发现近表面缺陷,应使用直流或整 流电
进行干磁粉检测时,宜采用交流电或半波整流电,当采用全波整流电或直流电时,应有足够的磁化 时间
8.8磁场方向和有效区 缺陷的可检测性取决于其主轴与磁场方向的夹角a
图12对此进行了说明
-30 说明: 磁场方向 2 灵敏度最高; 灵敏度逐渐降低 -灵敏度不足; 显现缺陷的最小角度; 《en 缺陷方向的一个实例
图12可检出缺陷的方向 被检部位应在接近相互垂直的两个方向进行磁化,角度最大偏差不超过30"
这也可通过一种或 多种磁化方法来实现
若另有规定,也可以仅进行一个磁化方向的检测
使用磁轭或触头检测时,其有效区范围见图13阴影区域
34
GB/T37400.14一2019 d/" b 说明 触头电极; 磁轭电极; 磁极间距,mm;75
GB:/T37400.14一2019 8.13显示的评定与质量等级 8.13.1 显示评定 显示分为以下3种: 相关显示:磁粉检测时由缺陷产生的漏磁场吸附磁粉而产生的磁痕显示,一般也称为缺陷 显示; 非相关显示;磁粉检测时由截面变化或材料磁导率改变等产生的漏磁场吸附磁粉的磁痕显示; 伪显示:不是由漏磁场吸附磁粉形成的磁痕显示 仅对相关显示进行评定
8.13.2质量等级 铸件磁粉检测质量等级见表19
表19磁粉检测质量分级(评定框尺寸150mm×105mm) 线性缺陷显示或成排缺陷显示 非线性缺陷显示 成排缺陷显示除外单个线性全部线性单个线性全部线性单个线性全部线性 应记录的 表面粗糙 或成排缺和成排缺或成排缺和成排缺或成排缺和成排缺 最小缺陷 质量度Ra的 陷显示陷显示陷显示 陷显示陷显示陷显示 单个缺陷 显示的直 等级 最大值 显示的 总面积 径或长度 受检部位的铸件厚度 Am 长度 mm mm <16mm l6mm50mm 50mm mmmm 最大允许长度/mm 01 3.2 0.3 6.3 1.5 10 1C 10 20 12.5 35 12 10 30 15 25 70 18 l0 18 18 27 30 45 200 10 500 18 25 27 45 70 40 注表中所列尺寸是指磁痕的显示尺寸,而不是缺陷的实际尺寸
质量等级01仅用于承受高负荷的小铸件和机械加工面, 在评定框内最多可以有两个都达到最大允许长度的缺陷显示 8.14检测报告 检测报告至少包括以下内容: 检测工件信息 a l)名称、,图号、炉号、工件号等 22 被检部位; 33 材料; 表面状况; 4) 5 检测标准
37
GB/T37400.14一2019 b 检测时机和范围 磁化方法种类,检测装置、磁粉、磁化的校验等
c d 检测方法
检测结果(发现缺陷的描述和位置 e fD 检测日期和操作者姓名
38
GB:/T37400.14一2019 附 录 A 规范性附录 补焊区的检测 检测时机 A.1 补焊区的验收检测应在铸件消除应力处理之后进行
A.2表面检测 按基材检测方法,根据第7章和第8章进行渗透或磁粉检测
验收要求,除满足基材要求外,不应 有裂纹及未融合性质的缺陷
A.3射线检测 按基材检测方法,应根据第6章进行射线检测
验收要求,除满足基材要求外,不应有裂纹及未融 合性质的缺陷
超声检测 A.4 A.4.1 应先按第5章基材检测的方法进行超声检测,另外还应按A.4.2和A.4.3进行额外检测
验收要 求除满足基材要求外,不应有裂纹及未融合性质的缺陷
A.4.2补焊区范围 图A.1所示a区和b区
补娜区 基材 侧视图 俯视图 图A.1补焊区检测范围及扫查示意图 A.4.3扫查面及探头 扫查面见图A.1侧视图,斜探头扫查方向见图A.1的俯视图
探头要求应符合5.3.2的规定.并根据补焊深度d,按表A.1选择合适的探头
39
GB/T37400.14一2019 表A.1探头及灵敏度 探头选用 检测灵敏度设置 mm 60"70"双晶斜探头十双晶直探头 一20 2050 45"斜探头十双品直探头 见5.6. 5"斜探头十双晶直探头十单晶直探头 50 A.4.4其他 也可采用平底孔以外的其他参考反射体制作DAC曲线
若不能换算成平底孔当量,则记录要求 及验收条款,由供需双方另行商定
40
GB:/T37400.14一2019 附录 B 资料性附录) 传输修正及衰减系数 B.1 传输修正 B.1.1 直探头 分别在试块以及被检工件(上、下底面平行上完好部位找出一次底波,调节仪器,使一次底波达到 同样的满屏高
分别记录此时的dB值和V以及对应的声程s和s
B.1.2斜探头 使用两个相同的斜探头,一个作为发射探头,一个作为接收探头,分别在试块以及被检工件(上、下 底面平行上找出一倍跨距的反射回波,调节仪器,使回波幅度达到同样的满屏高
记录此时的dB值 V和V以及对应的声程S和s
B.1.3传输修正计算 传输修正可用式计算按式(B.1). V=V-V一AV (B.1 式中 V. -对应声程为S
时仪器的读数,单位为分贝(dB): V -对应声程为S时仪器的读数,单位为分贝(dB); -不同声程大平底反射的回波dB差,可以通过DGs曲线查出,当s大于或等于三倍近场 V
时,也可以通过AV,=2olg(s:/S)计算得出,单位为分贝(dB); -声程,单位为毫米(rmm); S s. -声程,单位为毫米mm) B.2衰减系数 B.2.1 直探头 在被检工件(上、下底面平行)上,用第一次底波和第二次底波,或找两处厚度不同部位,分别找出不 同声程底波,调节仪器,使底波达到同样的屏高
分别记录此时声程S,S,对应的dB值和V
B.2.2斜探头 B.2.2.1在受检工件上,找两处厚度不同部位,两部位的声束反射面应足够大(至少大于一20dB声束 宽度),将探头对准尖角处,移动探头找出其最大反射波幅,分别记下最大波幅时两端角处声程S,S 对应的dB值V和V
B.2.2.2或采用一收一发两个同样的探头,在受检工件上,获得两个不同声程s',S'的反射波,调节仪 器,使反射波幅达到同样的屏高,记录仪器的读数、V
B.2.3衰减系数计算 衰减系数a可通过式(B.2)或式(B.3)计算 1
GB/T37400.14一2019 B.2 a=[lV-V|一|AV.|]/2ls-S 式中 材料衰减系数,单位为分贝每毫米(dB/mm); 声程,单位为毫米(n mm 声程,单位为毫米(mm). V 对应声程为S,时仪器的读数,单位为分贝(dB); V 对应声程为s.时仪器的读数,单位为分贝(dB). 或者 团=[Iv'-'|一l4v.1]s'-s B.3 式中 材料衰减系数,单位为分贝每毫米(dB/mm); vV 对应声程为S'时仪器的读数,单位为分贝(dB) 对应声程为s:时仪器的读数,单位为分贝(dB). V' AV -不同声程大平底反射的回波dB差,可以通过Ics曲线查出,当s大于或等于三信近场 一2og(s:/s)计算得出,单位为分贝(dB) 时,也可以通过V, 声程,单位为毫米(mm; S s" 声程,单位为毫米(mm)
B.3衰减修正注意事项 采用校准试块时,应将校准试块的衰减系数全部按零进行计算
斜探头进行衰减修正时,要按声程计算,不应按厚度或深度计算
42
GB:/T37400.14一2019 录 附 C 资料性附录 DGsAVG)曲线应用 C.1概述 DGS系统有DGS曲线,DGS面板以及DGS软件等,包括直探头和横波斜探头GS(AVG)系统
其具体用法可参照相应系统使用说明书
DGS曲线的使用要求,同工件大平底调灵敏度差不多,相对面应平行或为圆柱形,只是该曲线可适 用于3倍近场区以内
C.2纵波直探头GS(AG)曲线 C.2.1灵敏度设置 如图C.1所示B4S探头的DGS(AVvG)曲线,将工件完好部位的第一次底波(B1)调到某一基准波 高[如B1=40%FSH(全屏高度],然后在曲线中查出对应厚度(如800mm)某一平底孔(如p2mm)曲 线,与大平底(o)曲线的dB差值(AdB)如45dB),那么,灵敏度为800/p2( mm)=40%FSH十45dB 增益
灵敏度调节具体为;在横坐标上找出代表800mm的垂线,该线与p2mm线相交于61dB处,与大 平底(co)曲线相交于16dB处,两者差值为45dB,将基准波高提高(增益)45dB,这样800mm(厚度 处的p2mm灵敏度就调好了 C.2.2缺陷当量确定 在上述基准灵敏度下,在某深度(如300mm)处,发现一缺陷信号波幅比基准波幅(如40%FSH)高 出AdB(十21dB),那么该缺陷当量大小确定如下;在800mm处基准灵敏度如p2)曲线交点(800 更2=61dB)向上数AdB(21dB),此时纵坐标值为40dB,然后根据40dB水平线与缺陷深度(如 00mm)交点读出该缺陷当量(p3-2dB)
43
GB/T37400.14一2019 " x=0dB/m 0 10 B4s SerieE12/86 20 " 0 R r/aB 40 吵 9 o 50 50 60 60 70 70 80 80 mm 20 3040 6080100 2003004006008001m 2m3m4m6m8m 图c.1B4S纵波直探头DGSAG)曲线 C3横波斜探头cs(AvG)曲线 横波斜探头DGS(AvG)曲线的用法与纵波直探头相似
只是此时的大平底不再是工件本体,而是 GB/T19799.1一2015中的“1号校准试块”的R100mm圆弧面,或GB/T19799.2一2012中的“2号校 准试块”的R25mm圆弧面
此时的厚度应为横波传播的声程
如图C.2所示WB45-2的DGs(AVG)曲线,假如检测声程为400 mm, 灵敏度为p1.5 mm
将探 头声束对准“1号校准试块”的R100 mm圆弧面,移动探头,找到圆弧的最大反射波幅,将其调到某一 基准被高(如40%FsH)
然后,在图中找到横坐标上代表10mm刻度处的垂线,该出该线与大平底 (co)曲线相交点处的dB值(如2.5dB);再找到横坐标上代表400 刻度处的垂线,读出该线与 mm p1.5mm平底孔曲线交点处的dB值(如55.0dB),两者相减得出分贝差值为4=52.5dB. 此时需注意,由于用的是试块圆弧,所以还需要修正圆弧面与平面差异、表面传输和材质衰减差异, 计算方法见式(c.1) 灵敏度400/p1.5(mm)=40%FSH十52.5dB(增益)十AV十A ++++ (C.1 式中 试块圆弧面与平面的dB差值,图c.2DGs(AvG)曲线右上角,此处AV=一0.5dBB VK 士0.5dB
单位为分贝(dB)
传输修正dB差值,单位为分贝(dB).
V 缺陷当量确定的方法与纵波直探头相同
44
GB/T37400.14?2019 -0.5dB0.5dB A'x= x=0dB/m 10 10 wB45-2o SerieE12/84 20 20 30 30 v/aB 40 OI 50 50 60 60 70 70 R0 80 s/mm 2030 6080100 200 300400 6008001m 2m 6m ?c.2wB45-2?б??DGs(AVG) 45
GB/T37400.14一2019 附 录 D 规范性附录 常用灵敏度试片(块 灵敏度试片 D.1 D.1.1灵敏度试片主要用于检测磁粉检测设备、磁粉和磁悬液的综合性能,了解被检工件表面有效磁 场强度和方向、有效检测区以及磁化方法是否正确
标准试片有A,型,C型,D型和M型,其规格、尺 寸和图形见表D.1
A型,C型和D型标准试片应符合GB/T23907一2009的规定
表D.1灵敏度试片的类型,规格和图形 图形和尺寸 规格,缺陷槽深/试片厚度 类型 m mm A-7/50 A1-15/50 A1-30/50 A型 A1-15/100 7/50 Ai-30/100 20 A-60/100 C-8/50 分割线 C型 8/50o 人工缺陷 5×5 C-15/50 D-7/5o s D型 D-15/50 10 7/50 7/50 12mm 7/50 15/50 M型 9mm 20 6mn 30/50 C型标准试片可剪成5个小试片分别使用
D.1.2磁粉检测时,一般选用A-30/100型标准试片
当检测铸件狭小部位,A型标准试片使用不便 时,可选用C-15/50型标准试片
为了更准确地推断出被检工件表面的磁化状态,可选用D型或M型 标准试片
D.1.3灵敏度试片使用方法 46
GB:/T37400.14一2019 灵敏度试片适用于连续磁化法使用时,应将试片无人工缺陷的面朝外
为使试片与被检面接 a 触良好,可用透明胶带将其平整粘贴在被检面上,并注意胶带不能覆盖试片上的人工缺陷
b 灵敏度试片表面有锈蚀、褶折或磁特性发生改变时不应继续使用
D.2磁场指示器 D.2.1磁场指示器是一种用于表示被检工件表面磁场方向、有效检测区以及磁化方法是否正确的一种 粗略校验工具,不能作为磁场强度及其分布的定量指示
其几何尺寸见图D.1
继败最大0.8mm 无磁性手柄 人工缺陷 8块饼形低碳钢片和铜板 用炉内纤接媒在一起 ,mm的蝌板 -厚度为0.25mm士0.025 图D.1磁场指示器 D.2.2磁场指示器使用时,应将指示器镀铜的一面朝外,同时磁化以及施加磁介质,当指示器的铜面上 没有形成清晰的磁粉显示时,则应根据需要改变磁化方法
47
重型机械通用技术条件第14部分:铸钢件无损探伤GB/T37400.14-2019
随着工业技术的不断发展,越来越多的机械设备开始采用铸造技术来生产各种零部件。而铸造出来的零部件在使用过程中存在一些潜在的缺陷,例如气孔、夹杂等,这些缺陷如果没有及时发现和处理,将会给设备的安全性和可靠性带来严重的影响。 为了确保铸钢件的质量和可靠性,我国制定了《重型机械通用技术条件》(以下简称“通用条件”)作为指导标准,其中第14部分GB/T37400.14-2019详细规定了铸钢件无损探伤的技术条件和要求。 根据国家标准,铸钢件无损探伤应该采用以下几种方法:磁粉探伤、超声波探伤、射线探伤和涡流探伤。这些方法各有特点,可以根据具体的检测要求进行选择。 不过需要注意的是,在进行铸钢件无损探伤时,必须按照国家标准GB/T37400.14-2019的相关规定执行,包括对探伤设备和人员的要求、探伤方案的制定和实施、探伤结果的判定和报告等方面,以确保检测结果的可靠性和准确性。 此外,通用条件还规定了铸钢件无损探伤的缺陷评级标准,根据缺陷类型和严重程度进行分级。对于一些重要部位的零部件,如机械轮毂、机架等,只有在经历了严格的无损探伤检验后才能够投入使用,以保障设备的安全性和可靠性。 总之,铸钢件无损探伤是保证铸造产品质量和可靠性的重要手段,通过遵循国家标准GB/T37400.14-2019中的相关规定,可以有效地预防和排除铸造缺陷,提高产品的使用寿命和稳定性。