GB/T34907-2017
稠油蒸汽热采井套管技术条件与适用性评价方法
Technicalspecificationsandfitnessforserviceevaluationmethodforthermalwellcasingundercyclicsteamstimulationprocess
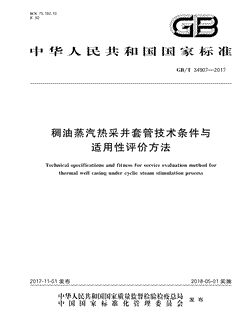
- 中国标准分类号(CCS)E92
- 国际标准分类号(ICS)75.180.10
- 实施日期2018-05-01
- 文件格式PDF
- 文本页数33页
- 文件大小2.19M
以图片形式预览稠油蒸汽热采井套管技术条件与适用性评价方法
稠油蒸汽热采井套管技术条件与适用性评价方法
国家标准 GB/T34907一2017 稠油蒸汽热采井套管技术条件与 适用性评价方法 Technicealspecifieationsandfitnessforserviceevaluationmethodfor thermalweleasingundereyeliesteamstimlatopres 2017-11-01发布 2018-05-01实施 国家质量监督检验检疫总局 发布 国家标准化管理委员会国家标准
GB/T34907一2017 次 目 前言 范围 2 规范性引用文件 3 术语和定义 符号和代号 套管钢级与类型 5.1钢级 5.2类型 套管管体 管体规格 6.1 管体性能要求 6.2 6.3检验与试验 验收与复检 6,4 6.5标记及其他 套管管端连接 7.1规格 7.2结构型式 7.3技术要求 套管适用性评价 22 8.1适用性评价流程 22 8.2试样的材料选择及加工检验 23 8.3适用性评价技术要求 24 8.4适用性评价试验 25 8.5安装要求 28 附录A资料性附录数据采集、记录及试验报告的说明 29
GB/34907一2017 前 言 本标准按照GB/T1.1一2009给出的规则起草
请注意本文件的某些内容可能涉及专利
本文件的发布机构不承担识别这些专利的责任 本标准由全国石油天然气标准化技术委员会(SAC/TC355)归口
本标准起草单位:石油集团石油管工程技术研究院、石油新疆油田分公司、石油辽河 油田分公司、中海油能源发展股份有限公司工程技术分公司、衡阳华菱钢管有限责任公司、勒海装备有 限责任公司
本标准主要起草人;韩礼红,王航、李东风、王建军、潘志勇,方伟,谢斌,田志华杨平阁、贺占国 谢凯意、陈长青
GB/34907一2017 稠油蒸汽热采井套管技术条件与 适用性评价方法 范围 本标准规定了稠油蒸汽吞吐和蒸汽驱热采井套管材料技术要求、管端连接要求、适用性评价要求与 方法
本标准适用于国内稠油蒸汽热采井套管的选用与适用性评价,包括直井,定向井等主要井型,注蒸 汽工况为井口蒸汽温度不高于400,注汽压力不高于35MIPa
同时涵盖陆地及海上稠油蒸汽热采井 作业环境
规范性引用文件 下列文件对于本文件的应用是必不可少的
凡是注日期的引用文件,仅注日期的版本适用于本文 件
凡是不注日期的引用文件,其最新版本(包括所有的修改单)适用于本文件
GB/T222钢的成品化学成分允许偏差 氢含量的测定憎气脉冲熔雕热导法 GB/T223.82钢铁 钢的脱碳层深度测定法 GB/T224 GB/T228.1金属材料拉伸试验第1部分;室温试验方法 GB/T228.2金属材料拉伸试验第2部分;高温试验方法 GB/T229金属材料夏比摆锤冲击试验方法 GB/T230.1金属材料洛氏硬度试验第1部分;试验方法(A、,B.c,D,E,F,G,H,K,N、T标 尺 GB/T2039金属材料单轴拉伸蠕变试验方法 GB/T4336碳索钢和中低合金钢多元素含量的测定火花放电原子发射光谱分析方法常规 法 GB/T5777无缝钢管超声波探伤检验方法 GB/T6394金属平均晶粒度测定法 GB/T9253.2石油天然气工业套管,油管和管线管螺纹的加工、测量和检验 GB/T10561钢中非金属夹杂物含量的测定标准评级图显微检验法 GB/T11261钢铁氧含量的测定脉冲加热惰气熔融-红外线吸收法 13298金属显微组织检验方法 GB 3299钢的显微组织检验方法 GB GB 15822无损检测磁粉检测 GB 17745石油天然气工业套管和油管的维护与使用 GB/T18052套管,油管和管线管螺纹的测量和检验方法 GB/T198302017石油天然气工业油气井套管或油管用钢管 GB/T20123钢铁总碳硫含量的测定高频感应炉燃烧后红外吸收法(常规方法 GB/T20124钢铁氮含量的测定惰性气体熔融热导法(常规方法 GB/T20657石油天然气工业套管,油管,钻杆和用作套管或油管的管线管性能公式及计算
GB/T34907一2017 GB/T21267石油天然气工业套管及油管螺纹连接试验程序 3 术语和定义 下列术语和定义适用于本文件
3.1 外加厚externalpset 在管体端部一定范围内的外径增大而内径保持不变的塑性变形工艺
3.2 接箍coupling 用于连接两根带外螺纹的套管并具有内螺纹的财简体 3.3 螺纹连接threadconneetion 外螺纹管端和内螺纹接箍的连接组件
3.4 现场端fieldend 在钻井平台上进行上扣的接箍一端
3.5 工厂端 milend 套管到达油田现场之前在工厂进行上扣的接箍一端
3.6 试样specimen 对于接箍连接的油、套管,一根试样是由一个接箍和两个外螺纹管段连接组成;对于无接箍连接的 油、套管,一根试样由一个加工有外螺纹的管段和一个加工有内螺纹的管段连接组成
3.7 泄漏leakage 压力介质通过连接螺纹或管体从试样内到达试样外(内压)或从试样外到达试样内(外压)的现象
3.8 堵头plug 用来封堵试样两端的机械装置,其主要作用是密封试样
3.9 粘扣ellm ing 金属材料接触表面在(螺纹)滑动或旋转过程中,发生冷焊而产生的撕裂现象
轻微粘扣是指使用 砂纸能够修复的粘扣,中度粘扣是指使用细纹铛刀和砂纸能够修复的粘扣,严重粘扣是指使用细纹刀 和砂纸不能修复的粘扣
3.10 工作压力operationpressure 注蒸汽压力规定的试验压力,不得超过制造商对螺纹规定的耐压额定值 3.11 工作温度operationtemperature 井口注蒸汽温度规定的试验温度 符号和代号 表1和表2中符号及代号适用于本文件
GB/34907一2017 表1套管管体符号及代号 序号 单位 符号 称 屈服强度 R MPa 抗拉强度 R MPa A 均匀延伸率 % 硬度 HRC 蠕变速率 %s-! MPa 轴向应力 表2套管管端连接符号及代号 名 称 序号 符号 单位 管体外径 D mmm 加厚管端外径 D mmm 管体壁厚 mmm 管端到加厚厚度开始减小处长度 L
mmm 管端到加厚厚度减小终止处长度 L mmm 接箍外径 w mmm 接箍最小长度 N mmm 接箍堂孔直径 Q mmm 接箍承载面宽度 mmm 套管钢级与类型 5.1钢级 按ksi表征的最小屈服强度分级,本标准包括65ksi,80ksi,90ksi、110ksi四个钢级
管体钢级代 号为“最小屈服强度+SH”,本标准规定钢级包括:65SH,80sH,90SH、110SH
5.2类型 依据管体与管端的材料性能和尺寸变化,套管可分为三种类型 第一类,管体的几何尺寸及材料性能与管端相同,标识符号为“钢级”后加“-1” 第二类,管体的几何尺寸与管端相同,但材料性能(屈服及抗拉强度)低于管端,标识符号为“钢级” 后加“一2” 第三类,管体与管端内径平齐,但后者外径采用加厚处理,管体材料性能与管端等同,其标识符号为 “钢级”后加“-3” 套管管体 6.1管体规格 稠油热采套管管体的规格同GB/T19830规定
GB/T34907一2017 6.2管体性能要求 6.2.1制造工艺要求 6.2.1.1 制造方法 套管管体推荐由热轧无缝钢管制造
若管端采用加厚处理时,应对管体管端进行整体热处理,以 保证整体管的组织均匀性
6.2.1.2热处理 套管管体的热处理工艺为“淬火十高温回火(Q&.T)”
其中钢管内外表面脱碳层厚度不超过 0.05mm. 6.2.1.3材料 套管材料宜由Cr-Mo系低碳合金钢制造,采用纯净化技术处理
按本标准供货的产品应含有至少 -种晶粒细化元素,使钢的奥氏体晶粒细化
6.2.1.4矫直 产品宜选择热矫直工艺,矫直工艺应满足GB/T19830规定
6.2.2化学成分要求 套管管体的化学成分推荐满足表3规定
表3化学成分 元素 Mn Mo NbV-T总量O-N-H总量 Cr 含量 0.30 0.l0 0.0l0 0.020 0.03 >0.40 0,6o 120×10" 质量分数/% 6.2.3拉伸性能要求 室温拉伸性能 6.2.3.1 室温下,套管管体的拉伸性能见表4所示
表4室温下套管管体的拉伸性能 屈服强度 抗拉强度 均匀伸长率 钢级 位置 R R, /MPa /MPa /% 65SH 448~586 586~689 >10 管体 管体 552655 655758 80SH 8 90sH 621758 724862 >7 管体 110SH 管体 758896 862965 5
GB/34907一2017 6.2.3.2高温拉伸性能 高温350C下,套管管体拉伸应力-应变曲线光滑,无明显屈服平台
在不高于400C高温注蒸汽 温度范围,同一批次套管管体材料的屈服强度,抗拉强度相比于室温: 350C以下,降低幅度应不大于15%; a b 350C400C温度范围,降低幅度应不大于20%
6.2.4硬度 套管管体的硬度应符合表5规定
表5套管管体硬度 65SH 80sH 90sH 110sH 钢级 硬度 HHRc 6.2.5夏比V型缺口吸收能 室温下,套管管体标准尺寸试样(10mm×10mm×55mm)的纵向冲击韧性应符合表6规定 表6套管材料冲击功 单位为焦耳 钢级 65SH 80SH 90SH 110SH 管体 >80 90 >100 >l10 6.2.6晶粒度 套管管体材料的晶粒度应为7.0级以上
6.2.7非金属夹杂物 套管管体材料的非金属夹杂物应符合表7的规定
表7夹杂物检验结果限定值 类型 原 厚 厚 悔 薄 要求 <1.5 1.5 1.5 <1.5 1.0 1.0 1.5 1.5 6.2.8蠕变性能 高温350C下,套管管体材料的蠕变速率应不高于蠕变速率本构关系[式(1)]所得的蠕变速率 =7.40×10×e十1.95×10-" 6.2.9无损检测 套管管体的无损检测应符合GB/T198302017SR2中L2检验等级标准要求,具体的检验等级要
GB/T34907一2017 求条款参照GB/T198302017SR2. 6.2.10壁厚偏差 任一检验批套管,包括单根试样套管壁厚负偏差应不高于名义壁厚的10%.
6.3检验与试验 6.3.1化学成分分析 化学分析试样应按GB/T222试样采样法采样,试样方法按GB/T4336进行,C、S元素应采用碳 硫分析仪,按照GB/T20123进行,O,N、H元素应按照GB/T20124,GB/T1l261,GB/T223.82测试
6.3.2拉伸试验 拉伸试验应按照GB/T228.1.GB/T228.2进行室温和高温试验,记录应力-应变曲线
管体及接箍应分别取3个试样进行拉伸试验,记录全部测量值,并取平均值为试验结果,单次试验 值偏差应不大于10%. 拉伸试验应采用纵向圆棒试样,在无法制备标准试样时,可以采用非标圆棒试样,标距长度应不低 于5倍直径
试验结果应标识试样直径和标距长度
拉伸试样尺寸推荐值见表8
6.3.3硬度 硬度试验应按照GB/T19830及GB/T230.1规定进行
表8拉伸试样尺寸推荐值 尺寸 规格1 规格2 直径D/mm 10,0士0.25 5.0士0.25 标距长度G/mm 50.0士0.15 25.0士0.15 最小过渡圆角半径R/. mm 10.0 6.0 6.3.4冲击试验 冲击试验试验应按照GB/T229规定进行,冲击试样为纵向夏比V型缺口试样,测试温度为室温
试验应注明试验结果及全尺寸转换值
6.3.5晶粒度及夹杂物级别评定 晶粒度试样应在垂直于套管轴向取样即套管管体横截面),在套管管体壁厚中心位置按照 GB/T6394规定评定晶粒度级别
夹杂物评定试样应在套管轴向取样(即套管管体纵截面)
非金属夹杂物检验按照GB/T10561 进行
微观组织类型及碳化物组织分布试验应沿套管及接箍轴向取样,按照GB/T13298及GB/T13299 及本标准规定进行
脱碳层深度应取管体全横截面试样,按照GB/T224执行
6.3.6蠕变试验 蠕变试验应按GB/T2039规定进行
GB/34907一2017 6.3.7无损检测 无损检测按照GB/T5777.,GB/T15822规定进行
6.4验收与复检 产品第一次检测若有不符合项,可以在同一检验批产品内随机抽取双倍数量的试样进行复检,复检 通过则可判定合格,否则为不合格
供货商对不合格产品重新处理后,应视为新产品进行检测
6.5标记及其他 6.5.1标记 套管最终产品外表面上应按本标准规定进行钢级及管端类型标识 标识位置、厂家及批次等产品溯源信息按照GB/T19830要求标记
6.5.2其他 本标准未规定事项按GB/T19830规定执行 套管管端连接 7.1规格 7.1.1总则 管端加厚处理时,管端钢级与管体相同
二次回火处理时,管端钢级高于管体,与接箍钢级相同
接箍与管体连接后,应保证整体套管为同一内径,管端、接箍内径与管体内平齐
套管螺纹连接宜采用 气密封型螺纹连接,由供货商和用户协商一致
管端规格 7.1.2 套管管端规格同GB/T19830规定,外径范围为114.30mm一244.48mm; 对于二次热处理的管体,管端内径及外径均与管体相同,管端长度不小于300mm 对于管端墩粗加厚的管体,管端外径增大,管端加厚后名义横截面积比管体增加30%或35%,管端 规格和钢级见表9,管端外加厚长度见表10
表9外加厚管端规格和钢级 管体外径 管端横截面积 管端外径 管体壁厚 管端钢级 增加的百分率 D mm mm 65SH 80SH 90SHH 110SH in mm 114.30 A 5,69 30 117.50 35 l18.02 114.30 4-1/2 ll4.30 30 6.35 117.84 35 l18,42
GB/T34907一2017 表9续) 管体外径 管体壁厚 管端横截面积 管端外径 管端钢级 增加的百分率, D % mm mm 65SHH 80SH 90SH 110SH n mm 114.30 7.37 30 118.36 么 35 l19,03 4-1/2 114.30 ll4.30 8.56 118.96 30 119.71 35 127.00 6.43 30 130.61 35 131.20 127.00 7.52 30 131.18 35 131.86 127.00 A 9.19 30 132.02 35 132.83 127.00 127.00 ll.10 30 132.94 35 133.90 127.00 人 12.14 30 133.43 134.47 35 127.00 12.70 30 133.68 D A 35 134.76 139,70 143.62 6.98 30 35 144.27 139.7 5-1/2 139.70 7.72 30 144.01 35 144.72 139,70 9.17 30 l44.75 35 145.57
GB/34907一2017 表9(续) 管体外径 管体壁厚 管端横截而积 管端外径 管端钢级 D 增加的百分率 % mm mm 65SH 80SH 90SH 110SH in mmm 139.70 5-1/2 139.70 10.54 30 145.43 D 35 146.36 168,28 7.32 172.43 30 173.1 35 A 168.28 8.94 30 173.28 A 35 174.10 6-5/8 168.28 168,28 174.13 10,59 30 A 35 175.09 168.28 A 12.06 30 174.87 35 175.94 177.80 6.91 30 181.74 35 182.39 177.8o A 人 8.05 182.35 30 35 183.10 人 177.80 人 0 A 9.19 30 182.95 人 A 35 183.80 177.8o A 177.80 183.56 l0.36 30 35 184.50 A A 177.80 11.51 30 184.15 35 185.18 口 177.80 30 A 12.65 184.72 35 185.84
GB/T34907一2017 表9续) 管体外径 管体壁厚 管端横截面积 管端外径 管端钢级 增加的百分率, D % mm mm 65SHH 80SH 90SH 110SH n mm 177.80 177.80 13.72 30 185.24 35 186.45 193.68 198.41 8.33 30 D 199.18 35 A A 193.68 9.52 30 199.04 A 人 35 199,.92 193.68 10.92 30 199.77 35 200.76 193.68 A 7-5/8 193.68 12.70 30 200.67 35 201.82 193.68 l4.27 30 201.46 35 202.72 193,68 人 15.11 30 201.87 35 203,20 193,68 15.88 30 202.24 D A 35 203.63 219,08 224.17 8.94 30 35 225.00 219.08 8-5/8 219,08 10.16 30 224.82 35 225.76 219,08 11.43 30 225,49 35 226.54 10
GB/34907一2017 表9(续) 管体外径 管体壁厚 管端横截而积 管端外径 管端钢级 D 增加的百分率 % mm mm 65SH 80SH 90SH 110SH in mmm 219.08 A 2.70 30 226.l4 35 227.30 8-5/8 219.08 219,08 14.15 226.88 30 35 228,16 A A 244,48 8.94 30 249.59 35 250,44 244.48 D 10.03 30 250,18 35 251.12 244.48 D l1.05 30 250.73 35 251.76 A g-5/8 244.48 244.48 A 11.99 30 251.23 252.34 35 244,48 30 13.84 252.19 35 253.45 244.48 15.11 252.84 人 30 35 254.21 注;“么"表示对应规格管端适用此钢级,“-"表示对应规格管端不适用此钢级 11
GB/T34907一2017 表10套管外加厚管端长度 管体外径 管端到加厚厚度 管端到加厚厚度 开始减小处长度 减小终止处长度 in mm mm mm 4-1/2 114.30 160.71 220.71 127.00 163.89 223,89 5-l/2 139.70 165.48 225.48 6-5/8 168.28 170.24 230.24 177.8o 175.00 235.00 7-5/8 193.68 179.76 239.76 8-5/8 219.08 182.94 242.94 9-5/8 244.48 182.94 242.94 7.1.3接箍规格 稠油蒸汽热采井套管采用接箍形式连接,接箍由无缝钢管加工制造,内径与管体相同
套管和接箍 连接结构见图1,接箍部分尺寸见表11 手紧 机紧 a b 图1外加厚套管和接箍 12
GB/34907一2017 表11接箍尺寸和公差 管体外径 管体 最小承载 管端横截面积 壁厚 管端外径 接箍外径 最小长度 瞠孔直径 面宽度 增加的百分率 D w NL Q b % in mm mm mmm mm mm mmm mm 1l4.30 127.00 261.42 117.86 3.18 30 5.69 117.50 129.79 261,42 120.65 3.18 35 l18.02 130,.31 261.42 121.17 3.18 127.00 261.42 3.18 14.30 117.86 6.35 30 130.13 261.42 117.84 120.99 3.18 35 118.42 130.71 261.42 121.57 3.18 4-/2 114.30 1l4.30 127.00 261.42 117.86 3.18 30 7.37 118.36 130,65 261.42 121.51 3.18 35 119,03 131.32 261,42 122.18 3.18 127.00 3.18 114.30 261,42 117.86 118.96 131.25 261.42 122.11 3.18 8.56 30 35 119.71 132.00 261.42 122.86 3.18 127.00 141.30 267.78 130.56 3.97 30 6.43 130.61 144.50 267.78 133.76 3.97 35 131.20 l45.09 267.78 134.35 3.97 127.00 141.30 267.78 130.56 3.97 7.52 30 3.97 507 131.18 267.78 134.33 35 131.86 145.75 267.78 135.01 3.97 127.00 141.30 267.78 130.56 3.97 9,19 30 145.91 267.78 132.02 135.17 3.97 35 132.83 146,72 267.78 135.98 3.97 127.00 141.30 267.78 130.56 3.97 127.00 11.1o 267.78 3.97 30 132.94 146.83 136.09 35 147.79 267.78 137.05 3.97 133.90 127.00 141.30 267.78 130.56 3.97 147.32 267.78 136.58 3.97 12.14 30 133.43 267.78 35 148.36 137.62 3.97 134.4? 267.78 127.00 141.30 130.56 3.97 12.70 147.57 267.78 30 133.68 136.83 3.97 134.76 148.65 267.78 137.91 3.97 35 13
GB/T34907一2017 表11(续) 管体外径 管体 最小承载 管端横截面积 D 壁厚 管端外径 接箍外径 最小长度 瞠孔直径 面宽度 增加的百分率 D w" N Q b % in mnm mm mmm mmm mm mm mm 139.70 153.67 270,95 143.26 3.97 6.98 30 143,62 157.18 270,95 146.77 3.97 35 144.27 157.83 270,95 147.42 3.97 139." 153.67 270.95 143.26 3.97 7.72 30 144.01 157.57 270.95 147.16 3.97 35 144.72 158.28 270.95 147.87 3.97 139.70 5-l/2 139.70 153.67 270.95 143.26 3.97 30 9.17 144.75 158.31 270.95 147.90 3.97 35 145.57 159,13 270,95 148.72 3.97 139.70 270.95 153,67 143,26 3.97 10.54 145.43 158.99 270.95 148.58 3.97 30 35 146.36 159.92 270.95 149.51 3.97 168.28 187.71 280.48 171.83 6.35 30 7.32 172.43 191.45 280.48 175.58 6.35 35 173.lm 192.13 280,48 176.26 6.35 168.28 187.71 280.48 171.83 6.35 8.94 30 280.48 70.43 73.38 192.30 6,35 174.10 193.12 280.48 177.25 6.35 35 6-5/8 168.28 168.28 187.71 280.48 171.83 6.35 10.59 30 193.15 6.35 174.13 280,48 177.28 35 175.09 194.11 280,48 178,24 6,35 168.28 187.71 280.48 171.83 6.35 74.7 280.48 78.02 6.35 2.06 30 193,89 194.96 179.09 75.r 280.8 6.35 35 177.80 290 181 7.14 200.03 l.36 6.91 181.74 203.56 290 7.14 30 184.89 35 182.39 204.21 290 185.54 7.14 177.80 177.8o 200.03 290 181.36 7.14 204.17 8.05 30 182.35 290 185.50 7.14 204.92 290 186.25 7.14 35 183.l0 14
GB/34907一2017 表11续) 管体外径 管体 最小承载 管端横截面积 壁厚 管端外径 接箍外径 最小长度 瞠孔直径 面宽度 增加的百分率 D w NL Q b % in mm mm mmm mm mm mmm mm 177.80 200.03 290 181.36 7.14 9.19 30 182.95 204.77 290 186.10 7.14 35 290 183.80 205.,62 186.95 7.14 177.80 29o 81.36 7.14 200.03 10.36 30 183.56 205.38 290 186.71 7.14 35 184.50o 206.32 290 187.65 7.14 177.80 200.03 290 181.36 7.14 30 177.80 l1.51 184.15 205,97 290 187.30 7.14 35 185.18 207.00 290 188.33 7.14 290 177.80 200,03 181.36 7.14 12.65 184.72 206.54 29o 187.87 7.14 30 35 185.84 207.66 290 188.99 7.14 177.80 200.03 290 181.36 7.14 30 13.72 185.24 207.06 290 188.39 7.14 35 186.45 208.27 290 189.60 7.14 193.68 215.90 299.52 197.23 7.94 8.33 30 198.4] 220,23 299,52 201.56 7.94 35 199.18 221.00 299.52 202.33 7.94 193.68 215.90 299.52 197.23 7.94 9.,52 30 299.52 199.04 220,86 202.19 7.94 35 199,92 221.74 299,.52 203.07 7.94 93.68 215.9o 299.52 97.23 7.914 99.77 221.59 299.52 02.92 l0.92 30 7.94 7-5/8 193.68 35 200.76 203.91 22.58 299.52 7.914 215.90 299.52 97.23 7.4 193.68 12.70 200.67 222.49 299.52 203.82 7.94 30 204.97 35 201.82 223.64 299.52 7.94 193.68 215.90 299.52 197.23 7.94 14.27 30 201.46 223.28 299.52 204.61 7.94 202.72 224.54 299.52 205.87 7.94 35 15
GB/T34907一2017 表11(续) 管体外径 管体 最小承载 管端横截面积 D 壁厚 管端外径 接箍外径 最小长度 瞠孔直径 面宽度 增加的百分率 D w" N Q b % in mnm mm mmm mmm mm mm mm 193.68 215.90 299.52 197.23 7.94 15,11 30 201.87 223,69 299,52 205.,02 7.94 35 203.20 225,02 299,52 206.35 7.94 7-5/8 193.68 215.90 299.52 197.23 7.94 193.68 15.88 30 299.52 202.24 224.06 205.39 7.94 35 203.63 225.45 299.52 206.78 7.94 219.08 244.48 305.88 222.63 9.52 30 8.94 224.17 249.16 305.88 227.32 9.52 35 225,00 249,99 305,88 228.15 9.52 219,08 244.48 305,88 222.63 9.52 10.16 224.82 249.81 305.88 227.97 9.52 30 35 225,76 250.75 305.88 228.91 9.52 219.08 244.48 305.88 222.63 9.52 30 8-5/8 219.08 1l.43 225.49 250.48 305.88 228.64 9.52 35 226.54 251.53 305.88 229.69 9.52 219.08 244.48 305.88 222.63 9.52 12.70 30 226.14 251.13 305,88 229,29 9.52 35 227.30 252.29 305.88 230.45 9.52 219.08 244.48 305.88 222.63 9.52 14.15 30 305.88 9.52 226.88 251.87 230,03 35 228.16 253,15 305,88 231.31 9,52 269.47 305.88 247.63 9.52 244.48 274.58 305.88 252.71 9.52 8.94 30 249,59 275.43 305.88 253.59 9.52 35 50.4 269.47 9.52 305.88 247.63 244.48 9-5/8 10.03 275.17 305.88 9.52 244.48 250.18 253.33 30 276.11 35 251.12 9.52 305,88 254,27 247.63 269.47 305.88 9.52 244,48 l1.05 275.72 30 250.73 305.88 253.88 9.52 251.76 276.75 305.88 254.91 9.52 35 16
GB/34907一2017 表11续) 管体外径 管体 最小承载 管端横截面积 壁厚 管端外径 接箍外径 最小长度 瞠孔直径 面宽度 增加的百分率 D w NL Q b % in mm mm mmm mm mm mmm mm 244.48 269.47 305.88 247.63 9.52 l1.99 30 251.23 276.22 305,88 254.38 9.52 35 9.52 252.34 277.33 305.88 255.49 269.47 305.88 9.52 247.63 244.48 9-5/8 30 305.88 9.52 244.48 13.84 252.19 277.18 255.34 35 253.45 278.44 305.88 256.60 9.52 244.48 269.47 305.88 247.63 9.52 30 1511 252.84 277.83 305.88 255.99 9.52 35 254.21 279,20 305,88 257.36 9.52 外径w的公差为士1%,但不大于士3.18mm
7.2结构型式 7.2.1类型 热采井套管螺纹连接可选用两种连接型式: 连接螺纹和90"直角抗扭台肩结构设计; b 连接螺纹、金属接触主密封面及台肩辅助密封面结构设计
7.2.2螺纹 套管外螺纹和接箍内螺纹宜采用API标准偏梯形螺纹,亦可采用改良的偏梯形螺纹
7.2.3密封面和台肩 密封面和台肩结构型式见表12和图2
表12密封面和台肩型式 代号 密封面型式(主密封面 对应台肩型式(辅助密封 无密封面 直角台肩 球面对柱面 柱面对柱面 逆向台肩 球面对锥面 维面对锥面 17
GB/T34907一2017 直角台肩 球面对柱面 柱面对柱面 球面对锥面 锥面对锥面 a b dD 图2密封面和台肩结构 7.2.4结构型式选用 根据井口注汽压力的不同,推荐按表13选用不同的螺纹连接结构型式
表13密封面和台肩结构型式选用 密封面和台肩结构型式 井口注汽压力/MPa 直角台肩只限于直井段3"/30m) S14 球面对柱面 柱面对柱面 >14 d 球面对锥面 锥面对锥面 注:实际使用时需经试验验证
7.2.5接箍定位槽 接箍上可加工测井时定位接箍位置的定位槽,结构及尺寸示意如图3
R 时 0 SG A50 o% 25土O.1 2.5士0.15 g时 R t0.0n 90 直角台肩 b)逆向台肩 a 图3定位槽结构及尺寸 18
GB/34907一2017 7.3技术要求 7.3.1总则 对于第二类套管产品,管端连接须采用强度错配设计,即管端、接箍的屈服强度高于管体的抗拉强 度,属于高强度匹配,保证热采服役过程中套管出现的塑性变形只发生在管体,管端与接箍连接部位始 终处于弹性状态,实现螺纹连接的气密封完整性
7.3.2制造工艺要求 7.3.2.1 制造方法 加厚管端在整体热处理之前可通过机械加工的方式进行内径平齐化处理
对管端加厚的套管应在 加厚处理后进行整体热处理,以保证整根套管的组织均匀性
7.3.2.2热处理 套管管端、接箍采用“淬火十高温回火(Q&.T)”
钢管内外表面脱碳层厚度不超过0.05mm
7.3.3化学成分 套管与接箍材料应为同一类型合金
7.3.4拉伸性能 7.3.4.1室温拉伸性能 套管管端、接箍的室温拉伸性能应符合表14或表15规定
表14一类和三类管端及接箍的室温拉伸性能 屈服强度 抗拉强度 均匀伸长率 钢级 位置 A R, R MPa MPa 448一586 586一689 >10 管端 65SH 接箍 552655 >689 5 管端 552655 655~758 8 80SH 接箍 689793 >758 >4 管端 621一758 724862 >7 90SH 接箍 862 758一896 >3.5 758896 管端 862965 >5 110SH 8961034 965 3 接箍" 19
GB/T34907一2017 表15二类管端及接箍的室温拉伸性能 屈服强度 抗拉强度 均匀伸长率 钢级 位置 R, R. A " MPa MPa 65SH 552~655 >689 >5 管端和接箍 80SH 管端和接箍 689~793 >758 >4 90SH 管端和接箍 758896 862 >3.5 l10SH 管端和接箍 896~1034 >965 >3 7.3.4.2高温拉伸性能 与套管管体材料高温拉伸性能要求相同
7.3.5硬度 套管管端及接箍材料的硬度应符合表16或表17规定
表16具有一类、,三类管端的套管硬度 65SH 80SH 90SH 110SH 钢级 管端 接箍 管端 接箍 管端 接箍 管端 接箍 -类、三类 22 二22 24 28 28 30 20 24 HRC 表17具有二类管端的套管硬度 65SH 80SH 90SH 110SH 钢级 管端、接箍 管端、接箍 管端、接箍 管端、接箍 二22 24 28 30 二类HRC 7.3.6夏比V型缺口吸收能 套管管端和接箍材料标准试样的纵向冲击韧性应符合表18规定
表18套管材料冲击韧性 单位为焦耳 钢级 6SH 80SH 90SHH l10SH 管端、接箍 >8o >90 >100 >110 7.3.7晶粒度 套管管端和接箍材料的晶粒度应为7.0级以上
7.3.8非金属夹杂物 套管管端和接箍材料的非金属夹杂物应符合表19规定
20
GB/34907一2017 表19夹杂物检验结果限定值 类型 薄 厚 厚 薄 s1.5 1.5 1.5 s1.5 1.0 <1.5 1.5 要求 l.0 7.3.9蠕变性能 高温350C下,套管管端及接头的蠕变性能与套管管体相同
7.3.10管端规格选择 套管管端规格需考虑套管柱与钻头、井眼及其他层管柱之间的间隙
7.3.11径偏差 任一检验批套管(包括单根试样),其管端外径公差为十3.18mm一0.75%D,同时管端最小外径 应保证完整螺纹最小长度
7.3.12长度偏差 管端到加厚厚度开始减小处长度L
的公差是士mm,管端到加厚厚度减小终止处长度L,的公差 是 mm
7.3.13外径不圆度 经过加厚的管端和未作加厚处理的管端外径不圆度不高于0.50%
外径不圆度由式(2)计算 2(Dm一Dmt AA 外径不圆度一 ×100% Dm十Dm 式中: D. -同一横截面上实测的最大外径值,单位为毫米(m mm; mnx 同一横截面上实测的最小外径值,单位为毫米(mm). Dm 7.3.14接箍承载面宽度 接箍最小承载面宽度应满足表11要求,且能够安全承担下井时管柱的重量
7.3.15外观检查 内外螺纹接头密封面和台肩不允许有毛刺、腐蚀坑、台肩、微裂纹、折叠、损伤以及破坏表面连续性 的凹痕、划痕、刀痕、磨痕等缺陷或缺欠,如果生产过程中或现场检测出这类缺陷或缺欠,不允许修复,需 要报废处理
密封面和台肩表面粗糙度R
不高于1.6m. 7.3.16无损检测 套管螺纹连接部分和接箍螺纹连接部分应进行磁粉检验
螺纹加工前的套管管端和接箍应按 GB/T5777要求进行超声波无损检测
7.3.17螺纹参数检测 外螺纹参数检测项目包括:;中径(或紧密距)锥度、螺距偏差、螺纹牙型高度偏差、完整螺纹最小长 21
GB/T34907一2017 度、密封直径偏差,内螺纹参数检测项目包括;中径(或紧密距),锥度、螺距偏差、螺纹牙型高度偏差、接 箍长度、密封直径偏差
7.3.18表面处理 接箍内螺纹表面处理采用镀铜或孟系磷化表面层致密、均匀光滑,无脱落现象,镀铜层厚度控制 在0.007mm一0.025mm范围内,磷化层厚度控制在0.015mm~0.03mm范围内
厂家宜提供用金相 方法检测得到的厚度和截面图检测报告,每个试样检测3个位置
7.3.19上扣扭矩 接箍现场端和工厂端应按规定的上扣位置和/或扭矩值进行上扣
接箍现场端和工厂端应使用能 控制扭矩大小的设备进行上扣,扭矩曲线应记录并保存
7.3.20实物性能 螺纹连接后的抗拉伸性能应满足GB/T20657中套管管体和接头的轴向拉伸使用性能 套管适用性评价 8.1适用性评价流程 主要针对注热蒸汽工况(井口注蒸汽温度不高于400C,注燕汽压力不高于35MPa),包括直井、定 向井等主要井型,同时涵盖陆地及海上稠油热采井作业环境
适用性评价试验流程如图4所示,其中 1井-6井,1T-3T均为试样编号
试样 螺纹参数测量 1#,2#,3#,,4#) 初始)上、卸扣试验 外压至失效试验(套管 (1#,2#,3,4销,5,6# 材料性能试验 (1T,2T,3T) 24小时用户温度下焙干 (1#,2#,3#,4#,5#,6#) 恒位移约束热应力 拉/压循环气密封 试骑(3#,4# 试骑1#,2# 温度循环气密封 试验 5#,6 内压至失效试 拉伸至失效试验 1#,2#) (3,4# 报告 图4适用性评价试验流程 22
GB/34907一2017 8.2试样的材料选择及加工检验 8.2.1试样 8.2.1.1试样的来源 试样应满足6.2管体性能要求
试样选取采用随机抽样的方式进行,可以由制造商和用户送样,也 可以由第三方到制造商或用户现场进行抽样,试样的来源方式应在报告中注明
8.2.1.2试样的数量与分组编号 所有试样均应进行分组,各组中所有试样均要进行编号
编号是为了易于区别每个试样、同时也为 了保证试验数据的正确对应
8.2.2试样的机加工 对于每个单独的试样,其长度应包括, 要求L
>D+v(见图D7 a b 用于夹持和(或)塞堵的长度; 对于第二类和第三类产品,全尺寸拉伸试样应由管体、管端及接箍连接而成
c 说明 -火持固定端 -应变片, -应变片与接头间距离;>3、D(应变片与夹持端距离;>D+3/丽); -外螺纹; -内螺纹
试样编号 "L管体最小无支撑长度 图5试样尺寸和无支撑长度示意图 23
GB/T34907一2017 8.2.3试样的检验与测量 8.2.3.1 几何尺寸 试验前测量试样的外径、壁厚,内径等几何尺寸,检验方法按GB/T19830或技术协议规定的标准 进行,在表中记录全部数据
对于破坏性试验,试验前后应按要求测量试样的几何尺寸,并记录全部数据、测量项目包括试样的 外径、壁厚、长度等几何尺寸
8.2.3.2螺纹参数 主要包括锥度、螺距齿高、密封直径等,检验方法按GB/T9253.2及GB/T18052或技术协议规定 的标准进行,记录全部数据
现场取样应提供现场螺纹检测数据,在试验过程中,根据需要可重新测量上述这些螺纹参数,并记 录全部数据
8.2.3.3无损检验 对进行压力试验的试样进行超声波,磁粉或电磁检测中的一种或两种检查其是香存在缺陷
8.2.3.4备用试样 所有用于试验的试样均应准备一定数量的备用试样,这些试样可用于预演试验、或用于替换正式试 验中途失败的正式试样
8.3适用性评价技术要求 8.3.1螺纹抗粘扣性能 按GB/T17745规定或用户推荐的上扣位置和/或最大扭矩控制,完成三次上扣、两次卸扣,在上 扣,卸扣过程中,管端外螺纹和接箍内螺纹均不能出现粘扣现象,其中高强度匹配管端的长度应不小于 300mm 8.3.2全尺寸套管实物性能 8.3.2.1拉伸至失效断裂强度 由于管体与管端十接箍采用强度错配设计,即管端十接箍的屈服强度高于管体的抗拉强度
因而 拉伸至失效试样的断裂位置应出现在管体上,管端-接箍连接部位结构保持完整
同时,管体的屈服强 度应达到GB/T20657中套管管体轴向拉伸性能要求,满足钻完井过程套管强度安全要求
8.3.2.2抗挤强度 均匀分布外载作用下,套管管体外压挤毁抗力达到GB/T20657中套管抗挤强度,满足钻完井下套 管过程中强度安全要求
8.3.2.3抗内压强度 套管的内压强度首先满足GB/T20657中套管内压屈服强度;其次,满足燕汽吞吐热采井套管注人 蒸汽压力要求,结构保持完整,不发生开裂损伤
24
GB/34907一2017 8.3.3接头气密封性能 8.3.3.1 内压保载下气密封 蒸汽热采工况工作压力下,保持压力过程中套管螺纹连接密封完整,不发生泄漏
8.3.3.2恒位移约束下套管热应力载荷测试 恒位移约束下(即保持套管试样两端相对位移不变),模拟注燕汽-焖井-采油过程中的温度变化
测试得到压缩-拉伸载荷,按照GB/T20657计算压缩应力-拉伸应力,作为燕汽吞吐热采工况下载荷循 环气密封性能评价的热应力参数依据
8.3.3.3载荷循环气密封 8.3.3.3.1室温、直井井型、工作压力下,拉伸-压缩载荷循环至少10周次,峰值载荷下保持5min 要 求载荷循环过程中套管柱内压稳定,螺纹连接密封完整,不发生气体泄漏;同时,套管柱结构完整,无明 显失效现象
室温,定向井井型(12”/30m)注蒸汽压力内压下,拉伸-压缩载荷循环至少10周次,蜂峰值载 8.3.3.3.2 荷下保持5min
要求弯曲加载下,载荷循环过程中套管柱内压稳定,螺纹连接密封完整,不发生气体 泄漏;同时,套管柱结构完整,无明显失效现象
8.3.3.4恒位移约束下温度循环气密封 8.3.3.4.1直井井型、套管两端轴向位移恒定、注蒸汽压力内压下,20350C温度循环至少10周次 降温到100即可再次升温),最高温度350C下保持5min
要求温度循环过程中套管柱内压稳定、 螺纹连接密封完整,不发生气体泄漏;同时,套管柱结构完整,无明显失效现象
8.3.3.4.2定向井(12”/30m),套管两端轴向位移恒定、注蒸汽压力内压下,20C350C温度循环至 少10周次(降温到100C即可再次升温),最高温度350C下保持5min
要求弯曲加载下,温度循环过 程中套管柱内压稳定,螺纹连接密封完整,不发生气体泄漏;同时,套管柱结构完整,无明显失效现象
8.4适用性评价试验 8.4.1上卸扣试验 8.4.1.1总则 按照GB/T17745和GB/T21267中相关操作规定,要求如8.4.1.18.4.1.5
8.4.1.2试验机 上、卸扣试验的试验机系统应带有扭矩测试仪,圈数测试仪、扭矩到位自动控制阀,同时能自动采集 并记录上扣扭矩、上扣圈数及上扣时间等参数,并能显示扭矩圈数及扭矩-时间曲线
试验机整机及所 用的载荷传感器、压力传感器等计量器具,应经过有试验机及传感器检定资格的部门进行检定和校准、 检定或校准周期不应超过一年,标定或校准载荷范围内相对误差不应超过士1.0%
8.4.1.3螺纹脂 上扣使用的螺纹脂由制造商或用户推荐
应由制造商按质量给出涂抹的最多量和最少量,或者由 制造商提供涂抹螺纹脂的图片和详细说明
如果认为螺纹性能不受涂抹的影响,应予以说明
每次上 扣前均应彻底清洗螺纹,并称出每个螺纹上应涂抹的螺纹脂量
按最大扭矩控制上扣的螺纹,应涂抹最 25
GB/T34907一2017 多量的螺纹脂;按最小扭矩控制上扣的螺纹,应涂抹最少量的螺纹脂
每次卸扣后,应重新清洗内,外螺 纹
同批试验的所有试样应使用同一种螺纹脂
8.4.1.4扭矩和速度的确定 对于符合GB/T19830的偏梯形螺纹套管,如果制造商推荐上扣扭矩,则最大扭矩、最佳扭矩和最 小扭矩按制造商推荐的扭矩确定
如果未推荐,则按三角形标记位置确定
对于特殊螺纹套管,最大扭 矩、最佳扭矩和最小扭矩应按制造商推荐的扭矩确定
对于各试样每次上扣,应按规定的扭矩大小控制 上扣
对于规定的最大扭矩,可接受最大或更大的扭矩;对于规定最小扭矩,可接受最小或更小的扭矩 如果实际扭矩在最大或最小扭矩之间,则应卸开螺纹重新施加扭矩上扣
上扣速度应按制造商或用户 的推荐值,但最快不应超过25r/min. 8.1.1.5上扣方式 推荐使用垂直上扣方式进行上卸扣试验
对于接箍连接试样,一般不应采用浮动上扣方式,即应采 用每猫分别上扣方式
对于需爱应变割量的上卸扣试验,则可采用浮动上扣方式
火具夹持接箍的位 置应尽量夹在不上扣一端,避免夹持对上扣产生不良影响
8.4.2全尺寸套管的实物性能试验 拉伸至失效试验 8.4.2.1 在复合加载试验系统上进行依据有关规定进行拉伸至失效试验
对试样施加轴向拉伸加载,拉伸 至失效破坏
拉伸过程中记录拉伸位移-载荷曲线
失效断裂应出现在套管管体上,管端接箍之间的 连接部位结构完整,同时管体断口位置附近有一定程度的颈缩现象
拉伸强度安全系数不低于1.2,安 全系数为拉伸强度试验值与强度标准值比值,其中,强度计算值是根据套管管体和接箍实测尺寸及性能 参数,引用GB/T20657中公式计算
分别记录每次试验的结果
对拉断部位拍照,明确断裂部位
8.4.2.2外压挤毁至失效试验 在复合挤毁试验系统上进行,依据规定进行外压挤毁试验
外压至失效试验应按下列步骤及要求 进行
首先,套管管端采用堵头焊接封堵,在室温下采用液体水加压,之后对试样施加均匀外压直至挤 毁失效,管体压扁或连接部位出现泄漏即为失效
8.4.2.3内压至失效试验 在静水压爆破试验系统上进行,进行内压至失效试验
在给试样加内压直至其失效期间,分别记录 每次试验的结果
8.4.3接头气密封试验 8.4.3.1内压保载试验 在内压试验系统进行,步骤如下: a采用堵头焊接封堵套管试样,对螺纹连接处的螺纹脂进行焙干; b 缓慢加压充填气体至额定内压载荷,保压10min; 检测套管螺纹连接处是否发生气体泄漏,气体泄漏依据内压泄漏检测方法
c 8.4.3.2恒位移约束下套管热应力载荷试验 通过恒位移约束下套管热应力载荷试验,测试套管受热膨胀、降温收缩产生的压缩、拉伸载荷,结合 26
GB/34907一2017 套管的规格尺寸计算得到对应的应力数值,具体步骤如下,要求见表20 a 恒位移约束通过位移传感器,轴向载荷实现 b 采用电加热带升温,热电偶测温; 依据表1程序进行试验; c d)记录试样升温过程中的载荷点
8.4.3.3载荷循环气密封试验 复合加载试验具体过程如下 对通过上卸扣试验,内压保载试验评价的套管试样进行本项目试验; a b 内压参数采用热采井口最高注汽压力,拉伸载荷、压缩载荷参数由室内模拟热循环试验获得; 工况模拟的热采井包括直井,定向井,对于定向井,选择井斜角12”/30m,施加侧向的弯曲载 荷实现 d 室温,直井/定向井,注蒸汽压力内压下,对套管柱施加轴向的拉伸-压缩循环载荷,载荷峰值保 持10 min 依据内压泄漏检测方法判断是否发生气体泄漏 e 评价完成载荷循环的试样结构完整性,是否有明显的失效现象
试验过程中不得发生泄漏现象,若发生泄漏,则终止试验,参考GB/T21267要求
表20恒位移约束套管热应力测试加载点要求 框架载荷 温度 保载时间 序号 载荷点 kN mmin 载荷 室温 位移量清零 60 载荷 150 记录位移量 150 加载荷至位移为零 记录载荷 10 载荷 250 加载荷至位移为零 250 载荷 注蒸汽极限温度 10 加载荷至位移为零 注蒸汽极限温度 加载荷至位移为零 60 室温 8.4.3.4恒位移约束下温度循环试验 具体过程如下 对通过上卸扣试验、内压保载试验评价的套管试样进行本项目试验; a b 恒位移约束通过位移传感器,轴向载荷测试仪器/设备实现,具体见相关规范 内压参数选取热采井井口的最高注汽压力,温度峰值取蒸汽吞吐工艺的上限温度350C,采用 加热带进行升温,温差控制在士5C,空气中冷却降温; 27
稠油蒸汽热采井套管技术条件与适用性评价方法GB/T34907-2017
稠油是一种石油资源,由于其黏度大、流动性差等特点,开采难度大。而蒸汽热采井套管技术则是一种应对稠油开采难题的有效手段,该技术可以在井筒内形成一定压力和温度条件,促进稠油的流动,提高采收率。
GB/T34907-2017《稠油蒸汽热采井套管技术条件与适用性评价方法》是我国针对稠油资源开发而制定的行业标准,该标准主要从以下方面进行评价:
1.套管材质与结构设计
套管材质的选择及结构的设计是决定稠油蒸汽热采技术成功的关键因素。该标准对套管材质、尺寸、厚度等进行了详细规定,并提出了结构设计要求。这些要求主要涉及套管的承载能力、耐高温性能和耐腐蚀性能等。
2.井轨迹设计
井轨迹的设计直接影响套管的施工难度和完整性,同时也会影响稠油在井筒内的流动状态。该标准规定了井轨迹的设计要求,应考虑地层的特点、采油效果、施工难度以及安全要求等方面的因素。
3.套管完整性评价
套管完整性评价是保证稠油蒸汽热采技术安全有效的重要手段。该标准主要从套管与地层、套管与套管之间、套管与井口间的联系等方面进行评价,并提出了相应的检测方法和标准。
4.稠油蒸汽热采井套管施工与管理
稠油蒸汽热采井套管施工与管理是保证技术应用效果的关键。该标准从套管施工前的检测、施工中的操作规范以及施工后的监测等方面进行了规定,并提出了相应的管理要求。
综上所述,GB/T34907-2017对稠油蒸汽热采井套管技术提供了详尽的方法和标准,这些方法和标准的运用可以帮助开发者更好、更快速地进行稠油资源的勘探开发工作。