GB/T37368-2019
埋地钢质管道检验导则
Guidelineforinspectionofburiedsteelpipelines
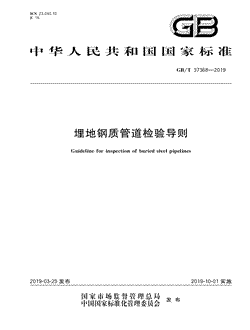
- 中国标准分类号(CCS)E16
- 国际标准分类号(ICS)23.040.10
- 实施日期2019-10-01
- 文件格式PDF
- 文本页数44页
- 文件大小3.26M
以图片形式预览埋地钢质管道检验导则
埋地钢质管道检验导则
国家标准 GB/T37368一2019 埋地钢质管道检验导则 Guidelineforinspectionofburielsteelpipelines 2019-03-25发布 2019-10-01实施 国家市场监督管理总局 发布 国家标准化管理委员会国家标准
GB/37368一2019 目 次 前言 范围 2 规范性引用文件 术语、定义和缩略语 总则 数据收集的要求 检验方案制定 检验实施 适用性评价 基于风险的检验 10记录和报告 28 29 附录A规范性附录)站场内压力管道的检验 埋地钢质管道检验有效性 附录B规范性附录 35 附录c(规范性附录)金属损失漏磁内检测器最低要求 40
GB/37368一2019 前 言 本标准按照GB/T1.1一2009给出的规则起草
本标准由全国锅炉压力容器标准化技术委员会(SAC/TC262)提出并归口
本标准起草单位:特种设备检测研究院、石油化工股份有限公司天然气分公司、石化 销售有限公司华南分公司、上海市特种设备监督检验技术研究院、江苏省特种设备安全监督检验研究 院、广东省特种设备检测研究院、福建省特种设备检验研究院、安徽省特种设备检测院、中油管道检测技 术有限责任公司、中石化长输油气管道检测技术有限公司、石油天然气股份有限公司管道分公司管 道科技研究中心,石油勘探与生产分公司,深圳市燃气集团股份有限公司,石油天然气股份有 限公司塔里木油田分公司油气运销部、中石油管道联合有限公司西部分公司、上海金艺检测技术有限公 司石油长庆油田分公司、石油大庆油田特种设备检验中心,沈阳市特种设备检测研究院、重庆 市特种设备检测研究院、陕西省天然气股份有限公司
本标准主要起草人何仁祥,吉建立、杨绪运、杨永、王笑梅、马义来、宗照峰、田中山、汤晓英 缪春生、杨树斌、姚钦、李志宏、门建新,孙明、刘保余,王富祥、苗文成、王晨、周卫军,李安军,李杰 梁德平、单洪翔、徐勇、周军、宋益民、闵海鹏
GB/37368一2019 埋地钢质管道检验导则 范围 本标准规定了在用埋地钢质管道检验的工作流程、数据收集、检验方案制定、检验实施、适用性评 价、基于风险的检验、记录和报告等方面的主要内容及基本要求
本标准适用于陆上长输、集输、公用管道中埋地钢质管道的检验,其他埋地钢质管道可参照执行
规范性引用文件 下列文件对于本文件的应用是必不可少的
凡是注日期的引用文件,仅注日期的版本适用于本文 件
凡是不注日期的引用文件,其最新版本(包括所有的修改单)适用于本文件
GB/T16805输送石油天然气及高挥发性液体钢质管道压力试验 GB/T19285埋地钢质管道腐蚀防护工程检验 GB/T19293对接焊缝X射线实时成像检测法 GB/T19624在用含缺陷压力容器安全评定 GB 21246埋地钢质管道阴极保护参数测量方法 GB 2664 无损检测磁记忆检测总则 GB 27512埋地钢质管道风险评估方法 GB 27699钢质管道内检测技术规范 GB 28704无损检测磁致伸缩超声导波检测方法 GB 28705无损检测脉冲涡流检测方法 GB/T30582基于风险的埋地钢质管道外损伤检验与评价 GB/T31211无损检测超声导波检测总则 GB/T31212无损检测漏磁检测总则 GB32167油气输送管道完整性管理规范 GB 32563无损检测超声检测相控阵超声检测方法 GB 34346基于风险的油气管道安全隐患分级导则 GB 84349输气管道内腐蚀外检测方法 GB 34350输油管道内腐蚀外检测方法 GB 35013承压设备合于使用评价 GB/T36676埋地钢质管道应力腐蚀开裂(sCC)外检测方法 GB/T36701埋地钢质管道管体缺陷修复指南 GB/T37369埋地钢质管道穿跨越段检验与评价 GB50028城镇燃气设计规范 GB50057建筑物防雷设计规范 GB50251输气管道工程设计规范 GB50253输油管道工程设计规范 GB50350油田油气集输设计规范 GB/T50698埋地钢质管道交流干扰防护技术标准
GB/T37368一2019 GB/T50818石油天然气管道工程全自动超声波检测技术规范 GB50991埋地钢质管道直流干扰防护技术标准 CJ34城镇供热管网设计规范 CJJ61城市地下管线探测技术规程 NB/T47013(所有部分承压设备无损检测 sY/T4109石油天然气钢质管道无损检测 埋地钢质管道外防腐层保温层修复技术规范 SY/T5918 含缺陷油气管道剩余强度评价方法 SY/T6477 TsGD7005压力管道定期检验规则 -工业管道 术语、定义和缩略语 3 3.1术语和定义 下列术语和定义适用于本文件
3.1.1 外检测externalinspeetionm 通过仪器设备从外部对管道本体、腐蚀防护系统等进行的检测
包括内腐蚀外检测,外腐蚀外检 测、应力腐蚀外检测等方法
3.1.2 内检测in-lineimspetionm 通过内检测装置从内部对管道本体进行的检测
包括几何内检测、漏磁内检测、超声内检测电磁 超声内检测等方法
3.1.3 适用性评价fitnessforservieeassessment 对含有缺陷或损伤的管道进行的一种评价,以确定在预期的工作条件下是否可以继续安全运行
3.1.4 定期检验periodieinspeetionm 按照国家特种设备安全相关法律、法规和安全技术规范的要求,对在用管道开展的周期性检验 活动
3.1.5 自行检查independentinspection 管道使用单位在定期检验的要求以外,自主开展的其他检验、检测活动
3.1.6 检验有效性inspeetionefreetiveness 对检验效果的定性分级评价,从高度有效到无效分为5个等级
3.2缩略语 下列缩略语适用于本文件
ACcvG;交流电位梯度法(AlternatingCuremtVolage(Gradient) CIPS;密间隔电位法(CloseIntervalPotentialSurvey DcvG直流电位梯度法(Drercuremtvolage Gradient) IR降;电压降(IRdrop LNG;液化天然气(LiquefiedNaturalGas)
GB/37368一2019 PEARsoN音频检漏法(PearsonSurvey SCADA;监控和数据采集系统(SupervisoryControlandDataAcquisitionSystems) nCrieking) sCC;应力腐蚀开裂(StressCorrosion sSMYS;规定的最低屈服强度(SpecifiedMinimumYieldsStrength TOFD:衍射时差法超声波检测TimeOfFlightDifraction) 总则 4.1本标准规定的检验是指对在用埋地钢质管道安全状态进行的一种验证活动
按检验性质分为定 期检验和自行检查两种类型,按检验方法分为传统检验和基于风险的检验两种模式
4.2自行检查和定期检验均可按照本标准规定的方法进行检验,定期检验过程除满足本标准的相关要 求外,还应符合国家特种设备相关法律法规、安全技术规范和有关标准的要求
-般采用传统检验的模式进行检验
满足9.1.1条件的管道使用单位,也可根据管道的损伤模式 4.3 和危害因素,结合管道的实际使用情况,采用基于风险的检验模式
本标准规定的检验的流程如图1所示 4.4 数据收集 风险评估 检验策略制定 风" 险! 检验方案制定 再! 评! 检验实施 您 适用性评价 风险缓减 记录和报告 注实线框中的内容为传统检验的内容,虚线框中的内容仅在基于风险的检验时执行
图1检验的流程 管道使用单位应根据管道的实际情况,制定检验计划
首次检验应在管道投用后3年内完成
4.5 4.6检验一般由管道使用单位负责组织,由具有资质和能力的检验机构负责实施
管道使用单位应为 检验顺利开展提供必要的条件,并协助完成检验工作
4.7从事管道定期检验的检测机构应取得国家特种设备安全监督管理部门核准的检验、检测资质,检 验、检测机构及人员应在资质范围内从事检测与评价工作,并对检验结论的真实性、准确性和有效性 负责
注,真实性表示报告、结论以事实为基础,不作假证;准确性表示报告,结论所涉及的检测数据符合相关要求;有效 性表示检验机构的资质、检验人员的资格符合要求,所使用的仪器设备在检定校准有效期内检验依据合法,报 告审批程序符合要求
4.8检验的全过程包括计划准备,实施和后期处置等,并应全过程记录
GB/T37368一2019 4.9对于管道较长且具有多个站场的管道,定期检验宜分段进行
具体的分段办法,由检验机构和使 用单位根据实际情况确定
4.10站场管道检验相关要求见附录A,埋地钢质管道穿跨越段的专项检验按照GB/T37369执行
4.11鼓励采取本标准中未列出的检测新技术,但应对新技术的应用效果进行有效验证
定期检验中 应用新技术时,应按照相关法律法规要求开展新技术评审
4.12检验过程中应遵守管道使用单位和检验机构关于健康、安全,环保的相关要求 4.13检验过程所使用的设备、仪器和测量工具应在有效的检定或校准期内
5 数据收集的要求 5.1数据基本要求 数据基本要求如下 a 采用各类检测方法在检验前,需要收集的基本数据要求见表1
检验过程中,应按照相关标准 要求进一步收集所需的数据
b 收集的数据应真实有效
必要时,可对收集到的各类数据进行对比、分析及整合,保证数据 质量
在数据收集过程中,当发现有数据不完整时,可通过现场检测或测试对重要数据进行补充
表1各类检测方法要求收集的基本数据 外检测 基于风险 序号 分类 数据 内检测 应力腐 的检验 外腐蚀 内腐蚀 蚀开裂 规格 材质 长度 输送温度 输送压力 输送介质 管道 安装日期 基本属性 投用日期 外防腐层类型 1C 内涂层类型 阴极保护类型 是杏有sACDA系统 是否有收发球筒 13 地理坐标 15 纵断面及高程 管道路由 及地表情况 地表状况 17 环境变化
GB/37368一2019 表1(续》 外检测 基于风险 序号 分类 数据 内检测 应力腐 的检验 外腐蚀 内腐蚀 蚀开裂 18 介质成分 1s 最小输量流速 20 入口压力 出口压力 2 运行数据 2 压力波动 2 清管历史 24 内检测历史 5 阴极保护有效性 26 漏点地理坐标 27 距压缩机、泵站的距离 2 时间 2s 漏点周向钟点位 30 压力波动 事故/事件 31 流速 数据 32 温度 33 倾角 34 元件类型 应力状况 35 36 土壤腐蚀性 37 管理制度 38 管理信息 应急预案 39 检维修记录 注;Y表示应收集的数据
元件类型是指管道具体泄漏部位的元件类型,如直管(高频电阻烬管,直缝埋弧媒管、螺旋缝埋狐炽管),弯管、 弯头、三通等
5.2数据来源 5.2.1设计、制造、安装资料,其中包括: 设计文件(包括计算书、施工图、说明书、强度计算书等)、设计变更 a b 管道元件制造质量证明文件监督检验报告; 管道安装验收资料、管道安装监督检验报告、工程质量检验和评定报告
c 5.2.2使用及运行管理资料,其中包括 运行日志及工艺记录含介质成分分析和异常情况处理记录等) a
GB/T37368一2019 D)改造或修理资料,包括施工方案和竣工资料,以及改造、修理监督检验资料 注b)仅限于特种设备安全技术规范要求进行监督检验的改造和修理,才需要收集改造或修理监督检验资料
c 应急预案; d 管理变更记录; e 运行管理制度及程序文件
5.2.3检测与评价报告,其中包括: 安全附件的校准、校验资料; a b 定期检验周期内的年度检查报告 c 历次定期检验报告; d 企业自行检查、检测及评价报告和记录
5.2.4失效数据文件,其中包括: 泄漏数据; a 腐蚀数据 b 外力破坏数据; c 地质灾害数据 d 5.2.5现有的完整性管理系统或地理信息系统
5.2.6相关法规和标准
5.3数据质量 5.3.1应考虑下列影响数据有效性的主要因素 过期图纸及文件; a b) 检测错误; c 笔误 d)检测设备和工具的准确性不足
5.3.2应考虑管道设计时采用的规范标准是否依然是有效版本,并考虑版本变化对检验结果的影响
5.4数据更新 检验后,管道使用单位应对管道数据进行完善和更新,并补充到管道数据库中 检验方案制定 6 6.1现场工作开展前,检验机构应在数据收集的基础上,根据使用单位的检验计划以及相关安全技术 规范和标准的要求,制定检验方案
6.2检验方案应至少包括以下内容要求: 管道基本情况及检验范围; a 所依据的法规标准; b 参与人员及分工 c 检验流程 d 检验项目、检验内容、检测方法、检测比例或检测数量等 f 记录与报告要求
6.3检验方案应征询管道使用单位意见,并经过检验机构授权审批人批准后,方可实施
6.4检验方案现场实施不适用或存在其他特殊情况时,检验人员应根据实际情况,按照有关质量管理
GB/37368一2019 程序办理方案变更,并且按照变更后的方案开展检验
检验实施 7.1检验实施的总体要求 7.1.1管道现场检验实施内容主要包括宏观检验,内检测、外检测、耐压试验和专项检测,其中,宏观检 验为必检内容
内检测、外检测、耐压试验和专项检测按以下原则选择 具备内检测条件的管道,优先选择内检测
对不具备内检测的管道,可通过改造管道使其具备 a 内检测条件,对不能改造或不能清管的管道,按照b),c)d)执行
选用内检测时,还需要对外 防腐保温)层和阴极保护系统状况进行检测评价
不具备内检测条件时应选择外检测
b 内、外检测均不可实施的管道,应进行耐压试验
c 必要时,对管道穿跨越段、特殊部位和特殊工况管段开展专项检测,专项检测包括管道穿跨越 d 段的检测,特殊工况下的管道材质理化检验,以及特殊部位环焊缝检测和特殊部位腐蚀检 测等
7.1.2检验实施前,管道使用单位应配合做好检验前的准备工作,确保管道处于待检状态
7.1.3检验实施过程中应严格按照法规、标准和检验方案要求执行,并做好记录
7.2宏观检验 7.2.1宏观检验的内容 宏观检验一般包括地面环境及设施检查、阴极保护系统测试,电性能测试、地质条件调查,以及安全 附件、安全保护装置与仪表检验等
7.2.2地面环境及设施检查 地面环境及设施检查应包括以下内容: 位置与走向;对管道位置,埋深和走向等进行检测
对浮管、露管、浅埋管段进行统计,并核对 aa 设计施工和竣工验收资料,确定管道埋深是否合格
b 管道沿线防护带:检查管道与其他建(构)筑物净距和占压状况;按照管道设计标准核对管道地 区等级的变化情况;按照《石油天然气管道保护法》的相关要求对管道周边建(构)筑物进行调 查统计,并记录相关情况
泄漏检查;目视检测地面是否存在泄漏情况,对疑似泄漏处采用泄漏检查仪进一步确认
对阀 室、阀井、三通、开挖点、地质灾害影响段、施工造成的管道悬空段,以及管道经过水面处有油泄 漏、有异常气味等处重点检查
地面装置;检查里程桩,标志桩、转角桩、交叉桩和警示牌等标识以及围栏等是否完好,是否存 在丢失等情况
管道穿跨越段;检查跨越段管道防腐(保温)层,补偿器、错固墩等是否完好,钢结构及基础、钢 丝绳索具及其连接件等是否存在腐蚀或其他损伤;检查穿越处的保护工程是否稳固,穿越处 的埋深及穿越段两端的标识桩、锚固墩是否完好;调查是否存在河道变迁等情况
水工保护设施;查验挡土墙、护岸,护坡、截水墙、淤土坝,排水沟等管道水工保护设施是否 f 完好
管道覆土:查验管道附近覆土是否存在塌陷,沉降、滑移等情况
GB/T37368一2019 h)检验人员认为有必要的其他检查
注:e)和b)中穿越处的保护工程,水工保护设施等的检查和河道变迁调查为企业自行检查的项目 7.2.3阴极保护系统测试 对于有阴极保护的管道,应进行以下检查和测试: 阴极保护系统运行状况,检查管道阴极保护率和运行率、排流效果,阴极保护系统设备及其排 a) 流设施; b)辅助阳极床和牺牲阳极接地电阻(适用于管道采用牺牲阳极保护,且管道保护电位异常时. 7.2.4电性能测试 当发现管道阴极保护电流及电位异常时,应对以下部位的电绝缘性和电连续性进行测试 a 测试绝缘法兰、绝缘接头,绝缘短管、绝缘套,绝缘固定支墩和绝缘垫块等电绝缘装置的绝缘 性能 b) 采用法兰和螺纹等非媒接件连接的阀门等管道附件的跨接电缆或其他电连接设施,测试其电 连续性
7.2.5地质条件调查 7.2.5.1对有危险的矿产地下采空区,黄土湿陷区、潜在崩塌滑坡区、泥石流区、地质沉降区、风蚀沙埋 区、膨胀土和盐溃土、活动断层、冻土区等,一般由管道使用单位委托专业机构定期开展地质条件变化的 调查,管道检验机构应对地质条件发生变化部位的管道进行重点检查和检测
725.2地质条件调查为金业自行检查的项目
管道检验机构拨照了.22p)开展的管道覆土状况调在 不能替代地质条件调查
7.2.6安全附件、安全保护装置与仪表检验 7.2.6.1安全附件检验主要包括以下内容: a 安全阀是否在校验有效期内; b 爆破片装置是否按期更换; 紧急切断阀是否完好
c 7.2.6.2安全保护装置和仪表检验一般由管道使用单位委托专业机构,按照国家或行业相关标准要求 进行检验或校核 7.3内检测 7.3.1基本要求 7.3.1.1内检测实施前应对检测过程可能产生的风险进行识别并制定控制措施 7.3.1.2开展内检测的管道应具备以下条件 a 收发球简除满足管道工艺设计的要求外,还应满足GB/T27699的要求; b 管道三通的挡条或挡板设置、开孔要求应符合GB/T27699的要求; 管道弯头的曲率半径应满足检测器的通过性能指标;相邻弯头间的直管段长度应大于管道 外径, 管道沿线阀门应满足检测器通过要求,阀门指示器指示准确 管道变形量满足检测器通过要求
GB/37368一2019 7.3.1.3应根据管道实际情况选用适当的内检测技术,各种内检测技术有效性见附录B 7.3.1.4由管道使用单位和检验机构共同商定选择适用的内检测技术,确定内检测数据可接受准则;内 检测器的能力和性能应满足管道检测的要求
选择内检测器时应考虑的因素包括但不限于 检测概率; a b 检测闵值; 缺陷识别能力; c 量化精度; d 特征定位精度 ee f 置信度; 数据采样频率; 8 壁厚范围 h 速度范围 温度范围; k 压力范围; 可通过的最小弯头半径; m可通过的最小内径; 检测器长度,重量和节数, n oo 单次运行检测器所能检测的管道长度
7.3.1.5首次应用的内检测技术、新设备,在检测前应至少对以下性能进行验证 整体承压能力; a b 通过性能 缺陷识别能力
c 7.3.1.6内检测实施程序按照GB/T27699相关规定执行
7.3.2内检测实施 7.3.2.1检测前准备 检测前准备工作如下 调查包括管道物理属性及附属设施改造、维修记录; a b 确认收发球简、三通、弯头、阀门及收发球指示器等设置满足内检测检测要求; 确定检测器包括检测概率、检测值、缺陷识别能力、量化精度、特征定位精度、置信度、数据采 样频率满足检测的要求等
金属损失漏磁内检测器的最低要求见附录C 7.3.2.2踏线选点 检测人员应在管道使用单位的配合下对管道沿线进行现场勘察,了解路况并选择设标点位置,确定 管道穿跨越位置和管道走向变化
设标间距宜不大于1km
在高程落差比较大或穿跨越区域应加密 设置
应记录定标点的地理信息
7.3.2.3清管作业 管道清管作业应符合以下规定 清管器的发收作业按GB/T27699的要求执行; b 运行泡沫清管器时,宜设置必要的监听点(坑),收球筒处宜设置收球笼
GB/T37368一2019 运行机械清管器,首次运行一种类型清管器,宜对清管器加装发射机(装置),并对清管器的运 行进行跟踪监视; 首次运行机械清管器,清管器应加装测径板; d 清管次数及效果以清出杂质少于5kg或满足检测器运行要求为合格 e 7.3.2.4 变形检测 变形检测应符合以下规定: 变形检测器发送前应对检测器进行标定; a 变形检测器的发收作业按GB/T27699的要求执行; b c 变形检测设标、跟踪应满足数据分析的要求 小 变形检测检测数据不满足质量(数据分析)要求,应分析原因,并及时进行复检
7.3.2.5缺陷检测 缺陷检测应符合以下规定 aa 缺陷检测器发送前应对检测器的性能进行标定 缺陷检测器的发收作业应按GB/T27699的要求执行; b 缺陷检测设标,跟踪应满足数据分析、评价的要求 c 若检测数据不完整,且不满足数据分析的要求或不满足管道适用性评价要求,应分析原因,并 d 及时进行复检 7.3.3检测数据的预处理 内检测收球后应对检测数据进行预处理,并及时向管道使用单位报告发现的以下问题 变形量超过管道外径5%以上的变形点的相关信息; a b金属损失大于管道公称壁厚的50%以上的金属损失点的相关信息
7.3.4开挖验证 7.3.4.1开挖验证的时机 应在内检测数据分析完成之后,正式检验报告出具之前,进行开挖验证
7.3.4.2开挖验证点选取原则 开挖验证点的选取原则应满足以下要求 每个检测管段,应选取不少于5个开挖验证点; a b 宜选择量化精度较低的缺陷进行开挖验证 宜选择使用单位关注的缺陷类型或被检测管道的主要缺陷点进行开挖验证; c d 宜选择最严重的缺陷点进行开挖,若因穿越等客观条件最严重的缺陷位置无法开挖时,应与使 用单位协商处理; 开挖数量、比例应考虑管道敷设地区等级、介质类型等因素
e 7.3.4.3开挖检测的项目及要求 开挖检测的项目包括;土壤腐蚀性检测、防腐《保温)层检查和探坑处管地电位检测,管道本体检测、 管道焊缝无损检测等,具体要求如下 10
GB/37368一2019 土壤腐蚀性检测,检查土壤剖面分层情况以及土壤干湿度,必要时可以对探坑处的土壤样品进 a 行理化检验
防腐(保温)层检查和探坑处管地电位检测,检查防腐(保温)层的物理性能以及探坑处管地电 b 位,必要时收集防腐(保温)层样本,按照相关标准进行防腐(保温)层性能分析
管道本体检测,包括金属腐蚀部位外观检查、管道壁厚测定,腐蚀区域的描述,以及凹陷、变形 等损伤检查;必要时还应进行腐蚀产物分析
管道焊缝无损检测,采用目视、磁粉、渗透等方法对开挖出的环焊缝进行焊缝外观检查和表面 缺陷检测,对外观检查和表面检测中发现存在错边、咬边严重,或存在表面裂纹的焊接接头,应 按照7.6.2.2.2的要求,对内部缺陷做进一步检测
7.3.4.4开挖验证结果处理 将开挖验证点的现场测量结果与检验报告结果进行比对,确认实际检测精度是否满足方案规定的 数据可接受准则,并按以下原则进行处理 若验证合格,应按方案要求出具验证报告和检验报告
a 若验证不合格,应及时分析原因,增加开挖验证数量或重新分析内检测数据;若仍不合格,应 b 重新运行内检测器
7.4外检测 7.4.1基本要求 外检测包括外腐蚀外检测、内腐蚀外检测及应力腐蚀开裂外检测三种,应根据管道的实际情况,结 合以下原则选择适当的外检测方法 当管道不具备内检测条件时,应进行外腐蚀外检测; a b 当管道发生过内腐蚀损伤、类似管道发生过内腐蚀损伤或管道使用单位认为需要时,应进行内 腐蚀外检测; 对发生过应力腐蚀开裂或具有应力腐蚀开裂倾向的管道应进行应力腐蚀开裂外检测
7.4.2外腐蚀外检测 7.4.2.1 -般规定 外腐蚀外检测的一般规定如下: a 外腐蚀外检测的一般程序,项目及内容等按照GB/T30582的相关内容执行; b)外腐蚀外检测的内容主要包括数据收集、腐蚀防护系统检测和开挖检测,其检测流程如图2 所示 在开展管道外腐蚀外检测时,一般还需结合发观检验的结果,对存在机械破坏、.地质条件不良 位置的管道进行开挖检测,对管道几何变形和机械损伤进行检测;必要时还需对开挖出的环焊 缝质量进行检测
11
GB/T37368一2019 数据收集 腐蚀防护系统检测 开挖检测 环境 外防 阴极保 排流系 腐蚀 腐层 护系统 统有效 性检 质量 有效性 性检测 测 检测 检测 土壤腐蚀 杂散电流 大气腐蚀 性检测 检测 调查 图2外腐蚀外检测的流程 7.4.2.2仪器设备 检测仪器设备应符合相关标准要求,并满足以下规定 管道埋深及水平位置检测仪器测量误差,不大于实际埋深的10%(埋深小于1m的以1m计 a 算). 外防腐层质量状况检测仪及阴极保护电位检测仪在非开挖状态下实施检测,外防腐层局部破 b 损地面定位误差不大于0.5m,密间隔电位检测仪应具有自动记录功能且测量误差不大于 0.001V; 管体腐蚀缺陷尺寸测量仪器检测误差不大于士0.1mm
7.4.2.3数据收集的附加要求 管道外腐蚀外检测需要收集的数据,除满足第5章的要求外,还需要满足检测仪器选择、检测信号 接人点选取及开挖位置确定等工作的要求
7.4.2.4腐蚀防护系统检测 7.4.2.4.1环境腐蚀性检测 环境腐蚀性检测一般包括土壤腐蚀性检测和杂散电流检测
对可能存在大气腐蚀环境的跨越段与 裸露管段,还应进行大气腐蚀调查
具体如下 a 土壤腐蚀性检测 土壤腐蚀性主要考虑土壤电阻率检测
必要时可测试管道自然腐蚀电位、氧化还原电位、土壤 pH值、土壤含盐量、土壤质地、土壤含水量、土壤氧离子含量等7个参数的测试
土壤腐蚀性 检测项目、常用检测方法、检测参量及依据标准等见表2
首次检验时应检测管道环境土壤腐蚀性
当地物地貌环境和土壤无较大变化时,土壤腐蚀性 数据可采用工程勘察或上次定期检验报告的数据
12
GB/37368一2019 表2土壤腐蚀性检测 常用检测 序号 检测项目 检测参量 依据标准 备注 方法 平均电阻率,单位为欧米 按电极间距,可分为等距法 GB/T19285 四极法 土壤电阻率 nm GB/T21246 和不等距法 自然腐蚀 GB/T19285 参比法 自然腐蚀电位,单位为伏(w -般使用地表参比法 电位 GB/T21246 氧化还原 氧化还原电位,单位为毫伏 -般铂电极为工作电位,参 GB/T19285 去极化法 电位 mV 考电极为甘汞电极 土壤pH值 电位法 pH值 GB/T19285 土壤含盐量干渣称重法土壤含盐量,质量分数(% 取样后实验室内测试 GB/T19285 -般分为以下几类: 手测法 砂土 a 土壤质地 土壤质地 GB/T19285 揉条法) b 壤土(轻、中,重壤土); 黏土(轻黏土,黏土 土壤含水量,质量分数(% 取样后实验室内测试 土壤含水量 烘干法 GB/T19285 土壤 硝酸银 土壤氯离子含量,单位为毫克每 GB/T19285 取样后实验室内测试 氯离子含量 滴定法 千克(mg/kg 杂散电流检测 当管道附近存在杂散电流干扰源或管地电位异常时,应进行杂散电流检测
常见的杂散电流 干扰源见表3
杂散电流检测的项目、方法、检测参量及依据标准等见表4
表3常见的杂散电流干扰源 序号 分类 常见干扰源 直流电气化铁路、直流电车装置、直流电网、直流电话电缆网络、直流电解装置、电焊机 直流干扰源 及其他建(构)筑物阴极保护系统等 高压交流电力线路设施和交流电气化铁路设施等 交流干扰源 表4杂散电流检测 序号 类别 检测项目常用检测方法 检测参量 依据标准 备注 干扰管地 管地直流 自然电位可测量时,测量 GB/T19285 直流电位,单位为伏(V 电位 电位测量 GB50991 值用来计算电位偏移 直流杂 散电流 电位梯度,单位为伏每米 可测量土壤电位梯度及 土壤表面 GB/T19285 十字交叉法 电位梯度 V/m GB50991 土壤中电流方向 管道交流 管地交流 GB/T19285可测量管道交流干扰电 交流电位,单位为伏(V 干扰电压 电位测量 GB/T50698 压值 交流杂 散电流 检查片交流交流电流密度,单位为安每 交流电 GB/T19285 般需埋预设腐蚀检 流密度 电流测量 平方米(A/m') GB50698 查片 13
GB/T37368一2019 表4续 序号 类别 检测项目常用检测方法 检测参量 依据标准 备注 管中电流 感应法 感应电流,单位为安(A GB/T19285 -般使用专业仪器进行 特殊情 况下杂 管地电位波动值,单位为毫 散电流 管地电位管地电位测量 GB/T19285 -般使用专业仪器进行 伏mV 大气腐蚀调查 c 调查当地环境气体类型、相对湿度、大气环境、管道所处地区钢材大气腐蚀速率
7.4.2.4.2外防腐层质量检测 外防腐层质量检测包括外防腐层整体状况和局部破损点的不开挖检测
常用外防腐层质量检测项 目、检测方法、检测参量及依据标准见表5
表5外防腐层质量检测 序号检测项目 检测方法 检测参量 依据标准 备注 la ACVG操作简单; 交流电位 地表电位梯度、 b) 难以检测硬质地面下及深水中的管段 GB/T19285 单位为分贝 局部破损 梯度法 GB/T21246 无法检测具有电屏蔽的防腐层剥离 ACVG) dB) d)不适用金属套管内、冻土下的管段 直流电位 地表电位差, DvG一般与密间隔电位法配合使用 梯度法 单位毫伏 b 适用于外加电流法阴极保护系统; DCVG mV GB/T19285 难以检测水泥、沥青硬化地面下的管段 局部破损 d 下管段 密间隔 管地极化电位, GB/T21246 难以检测深水 无法检测具有电屏蔽的防腐层剥离; 电位法 单位为毫伏 不适用金属套管内.冻土下的管段 (CIPS) mV 难以检测水田、沼泽地、水泥和沥青硬 地表电位差
GB/T19285 音频检漏法 化地面下及高压交流电力线附近管段 局部破损 单位为毫伏 b) PEARSON GB/T21246 无法检测具有电屏蔽的防腐层剥离 mV 不适用金属套管内.冻土下管段 不适用金属套管内及高压交流输电线 路附近的管段; GB/T19285 交流电流 电流衰减率、 整体质量 b) 管道附近金属物会造成干扰; 衰减法 % GB/T21246 土壤电阻率较大时局部破损难以检出; D 无法检测具有电屏蔽的防腐层剥离 7.4.2.4.3阴极保护系统有效性检测 阴极保护系统有效性检测包括通/断电位、管地电位、密间隔电位、阳极地床接地电阻、电绝缘性、阴 极保护电源运行情况调查等
通/断电位、管地电位、密间隔电位、阳极地床接地电阻和电绝缘性的检测 方法、检测参量及依据标准见表6
阴极保护电源运行情况调查内容包括阴极保护电源的基本情况调 查、阴极保护电源运行数据分析
应检测管道对地的阴极极化电位以判断管道阴极保护有效性
强制电流保护系统及可断电的牺牲 14
GB/37368一2019 阳极保护系统应检测断电电位,不可断电的牺牲阳极保护系统应使用极化探头等检测管地电位
保护 电位接近该管道最低保护电位或存在过保护,杂散电流干扰的管段及首次开展定期检验的管道应实施 密间隔电位检测
强制电流保护设备输出电位、电流异常时,应检查阴极保护设备的运行状况,必要时 应检测阳极地床的接地电阻、管道连接电阻及绝缘装置的绝缘性能
牺牲阳极电位闭路电位明显升高 或是输出电流过小时,应开挖确认消耗情况
表6阴极保护系统有效性检测 常用检测 序号检测项目 检测参量 依据标准 备注 方法 GB/T19285 保护电位, 通电电位 参比法 含IR降 单位为伏(V GB/T21246
消除了由保护电流所引起的IR降的 影响
保护电位、 GB/T192852.以下情况不可用3 断电电位 参比法 单位为伏(V GB/T21246 采用多组牺牲阳极保护或牺牲阳极与管 a 道直接连接时 b 外接阴极保护电源无法中断时 电位差, GB/T19285 管地电位近参比法 单位为伏(V GB/T21246 1 以下情况不可用: 阴极保护电流不能同步中断 b 套管内的管段
2.以下情况检测结果受外部条件影响 密间隔 管地极化电位 覆盖层导电性很差的管段,如铺砌路面 GB/T19285 a 密间隔 电位法 电位 单位为毫伏mV GB/T21246 冻土、钢筋混凝土、含有大量岩石回 (CIPS 填物; b 剥离防腐层下或绝缘物造成电屏蔽的 位置,如破损点处外包覆或衬垫绝缘物 的管道 适用于强制电流辅助阳极地床(浅埋式或深井 长接地 接地电阻 式阳极地床)、对角线长度大于8m的棒状牺 阳极地床 GB/T19285 电阻测试 单位为兆欧 牲阳极组或长度大于8m的锌带 GB/T21246 接地电阻 MQ 短接地 适用于当对角线长度小于8m的棒状牺牲阳 电阻测试 极组或长度小于8m的锌带 电位, 适用于定性判别有阴极保护运行的绝缘法兰 电位法 单位为毫伏(mV) (接头)的绝缘性能 漏电电阻 电阻 当采用电位法测试其绝缘性能可疑时,可漏电 单位为兆欧(MQ) 测试法 电阻测试法进行补充 电绝缘性 GB/T19285 电流衰减法 管内电流, 测试漏电率 单位为安(A 接地电阻仪 接地电阻 测量法 单位为欧(Q 15
GB/T37368一2019 7.4.2.4.4排流系统有效性检测 具有杂散电流排流装置的,应依据GB/T19285检测排流装置的有效性
7.4.2.5开挖检测 7.4.2.5.1开挖位置选择原则 开挖位置选择原则如下: 应综合考虑防腐层破损、腐蚀活性、阴极保护有效性、杂散电流及土壤腐蚀性等因素,对可能存 a 在外腐蚀损伤的位置进行排序,优先选择外腐蚀概率较高的位置进行开挖 b 开挖数量比例应满足相关安全技术规范和GB/T30582的要求 优先选择位于高后果区内的防腐层破损处进行开挖,高后果区的识别方法按照GB32167 执行; d 优先选择杂散电流的流出点,以及阴极保护失效或曾经发生过腐蚀泄漏的管段 开展内检测的管道,开挖位置与数量的选择宜与内检测结果相结合; e fD 当开挖检测发现管道存在严重外腐蚀时,应适当增加开挖检测点数量
开挖检测的项目及方法 7.4.2.5.2 开挖检测的项目及方法如下 开挖检测的项目除应满足7.3.4.3的规定外,还应满足GB/T30582的要求;定期检验的开挖 a 项目还应满足相关安全技术规范的要求; 对宏观检验中发现对存在机械破坏,地质条件不良位置的管道进行开挖检测,重点对管道几何 b 变形和机械损伤进行检测; 除目视检测常规无损检测和超声波测厚外,常用的管道本体缺陷外检测技术的检测能力及依 据标准见表7
根据检测目标和现场客观条件,选择适当的外检测方法对开挖处管体的质量 进行检测
表7金属管道管体和焊接接头缺陷外检测技术 序号 检测技术 检测能力 依据标准 备注 la 表面需光滑平整,无需去除防腐层 GB/T31212 外壁漏磁可对检测处管体金属损失进行定 难以检测针孔、焊缝边缘、弯头及大小 检测 性检测 NB/T47013.12 头有形状改变位置的缺陷 可对检测处管体金属损失进 表面需光滑平整 低频 b) GB/T31212 磁场较弱,容易受到周围环境的干扰产" 行快速定性检测 电磁检测 b 适用于直管段和弯头 生虚假信号 磁记忆 表面需光滑平整; 管体应力集中定性检测 GB/T26641 检测 仅能定性检测 满足以下条件的覆盖层,可不用拆除: 适用于大面积的均匀腐蚀 金属保护层厚度不大于1nmm 脉冲涡流 减薄; GB/T28705 对于不锈钢或铝保护层,覆盖层厚度不 Ib 检测 不适用于点蚀、裂纹等局部缺NB/T47013.13 b 大于200mm;对于铁保护层,覆盖层厚 陷检测 度不大于100 mm 16
GB/37368一2019 表7(续 序号 检测技术 检测能力 依据标准 备注 mm的 可对防腐层厚度不大于5 要求探头检测过程运行要平稳、被检测面光 远场涡 管道实现100%检测检测灵敏 汁,抖动或震动都会产生虚假缺陷信号,检 流检测 度高 测效率低,标定要求较高 在线状态下仅适用于DN200 x 射线数 以下公称直径的液相管道管 GB/T19293 无需胶片,迅速成像,检测效率高 a 字成像 体和焊接接头缺陷检测; NB/T47013.11b)无需拆除保温层,无需清空管内介质 检测 适用于气相管道管体和焊按 接头缺陷检测 可对检测处管体金属损失 超声波c 效率较低; 00%检测,形成直观的三维 扫描成像 NB/T47013.3 扫描图像" 检测处需打磨光滑 b 检测 适用于直管段和弯头 b 单点激励可实现管道的长距 离检测 低频 较短或螺旋焊缝管道检测有效性差 GB/T31211 适用于管体内外缺陷检测 b GB/T28704 导波检测 直埋及带防腐层管道检测距离较短 b 适用于穿越涵洞、铁路等带套 管的管体检测 适用于测点附近约前后1m 范围内的体积型缺陷的精确 高频 检测距离短 la 检测 导波检测 b) 检测精度高于低频导波 适合于管道支、吊架下的腐蚀 b 检测 相控阵 GB/T32563 适用于管体和焊接接头的内部缺 10 超声检测陷检谢 GB/T50818 TOFD mm的管道对 可实现缺陷成像显示; 适用于壁厚大于12" 1 NB/T47013.10 接接头的检测 检测处需打磨光滑 b 检测 三维激光扫描管道外壁凹陷、腐蚀等外部缺 无法直接检测缺陷剩余壁厚,需通过基准点 2 扫描技术陷轮席尺寸 计算缺陷情况 7.4.3内腐蚀外检测 7.4.3.1 -般规定 内腐蚀外检测应满足以下要求 内腐蚀外检测技术主要用于对不能进行内检测的管道的内腐蚀评价; a b 净化天然气输送管道的内腐蚀外检测程序、项目及内容等按照GB/T34349进行检测,含水天 然气管道的内腐蚀外检测可参照国外相关标准进行检测;输油管道内腐蚀外检测程序,项目及 内容等按照GB/T34350进行检测 内腐蚀外检测的主要步骤包括数据收集、内腐蚀位置预测管道高程图绘制、介质多相流计算、 腐蚀位置判断)及开挖检测
17
GB/T37368一2019 7.4.3.2仪器设备 内腐蚀外检测仪器设备性能应能符合相关标准要求,并满足以下规定 管道埋深检测仪器测量误差不大于实际埋深的10%(埋深小于1m时,按1m计算). a) b) 高程测绘仪器测量误差不得大于士3cemm(相对于邻近控制点). 7.4.3.3数据收集的附加要求 管道内腐蚀外检测需要收集的数据,除满足第5章的要求外,还需要满足GB/T34349和 GB/T34350等有关标准的要求
7.4.3.4内腐蚀位置预测 内腐蚀位置预测应符合以下要求 a 腐蚀预测工作主要内容包括检测区段划分、积液或固体沉积的临界倾角计算、管道实际倾角计 算及内腐蚀位置识别
内腐蚀外检测区段划分原则根据介质不同有所区别,初次应用外检测时应尽量细分 b e 临界倾角可依据相应标准提供的计算模型或使用商业软件计算
依据不同输送介质中腐蚀性 物质(凝析水、沉淀物)及其聚积特点,选择适用的多相流计算方法确定腐蚀性物质最可能聚集 位置
应用腐蚀预测软件计算腐蚀速率时宜对计算结果进行实际验证
d 管道实际倾角计算依据的管道高程数据测绘及管道埋深精度应满足CJJ61的规定;净化天然 气管道内腐蚀位置预测应遵守GB/T34349的有关规定,输油管道内腐蚀位置预测应遵守 GB/T34350的有关规定
7.4.3.5开挖检测 7.4.3.5.1开挖位置选择 开挖检测的位置选择,可依据不同介质,分别按照GB/T34349或GB/T34350规定的流程执行 也可采用其他可行的开挖程序
7.4.3.5.2开挖检测的项目及方法 开挖检测的项目及方法如下 开挖后,一般采用超声波C扫描成像检测、外壁漏磁检测等方法对内腐蚀缺陷进行定性检测 a 然后使用超声波测厚方法对剩余壁厚进行量化检测;也可选用表7中适用的其他方法对管道 内腐蚀缺陷进行检测 开挖后,如果发现管道存在外腐蚀、机械损伤及sCC等缺陷,应采用其他相应的方法对这些缺 b 陷进行检测和评价; 应使用超声波测厚仪对开挖出的螺旋焊缝或直焊缝附件母材壁厚进行检测 d 若管道安装有内腐蚀监测设备,应对监测数据与开挖实际检测数据进行对比;在内腐蚀严重处 宜修建检测探坑定期检测壁厚或安装内腐蚀监测设备 当开挖检测发现管道存在大范围的严重内腐蚀时,检测人员应对该管道开展内腐蚀外检测的 可行性进行重新评估
7.4.4应力腐蚀开裂(SCC)外检测 7.4.4.1 -般规定 7.4.4.1.1管道可能出现的应力腐蚀开裂分为;内部输送介质诱导和外部环境诱导两种,外部环境诱导 18
GB/37368一2019 的外壁应力腐蚀开裂有高pHSCC和近中性pHSCC两种形式
7.4.4.1.2应结合管道实际情况,开展SCC敏感因素分析,根据分析结果,决定是否开展应力腐蚀开裂 外检测
7.4.4.2内部输送介质诱导应力腐蚀开裂外检测 对曾发生过输送介质诱导的应力腐蚀开裂的管道,应定期进行排查,对可能发生应力腐蚀开裂的管 段按照相关标准进行开挖检测
7.4.4.3外部环境诱导应力腐蚀开裂外检测 7.4.4.3.1数据收集的附加要求 管道外部环境诱导应力腐蚀开裂外检测需要收集的数据,除满足第5章的要求外,还需要满足 GB/T36676等有关标准的要求 7.4.4.3.2位置预测 对存在外部环境诱导应力腐蚀开裂倾向的管道,按照GB/T36676开展scC敏感管段筛选,并确 定开挖位置
7,4,4.3.3开挖检测的项目及方法 开挖检测的项目及方法如下 开挖原则和开挖检测要求按照GB/T36670执行; a b 开挖检测主要包括防腐层状况检测管地电位检测及管体裂纹无损检测;应首先选择磁粉、渗 透等方法进行表面裂纹检测,当发现存在表面裂纹时,应采用超声波检测法对裂纹尺寸进行测 量;必要时应进行现场金相检测,确定应力腐蚀开裂的类型; 开挖后,如果发现管道存在外腐蚀、机械损伤等缺陷,应采用其他相应的方法对这些缺陷进行 检测和评价
7.5耐压试验 7.5.1基本要求 耐压试验应满足以下基本要求 耐压试验分为峰值试验、强度试验和严密性试验三类,三类试验可以单独或组合使用,应根据 a 试验目的确定合适的试验类型, 耐压试验一般由使用单位负责准备和操作;检验单位负责对耐压试验的过程进行现场监督,并 b 对试验结果签字确认; 使用单位应结合管道的实际情况,制定专门的耐压试验方案 耐压试验实施前,应评估试验风险,包括试验过程中管道的载荷情况,试验过程失效可能引发 后果;并制定预防措施; 四类地区不得使用有毒、易燃易爆介质进行耐压试验
注:e)中管道地区等级的划分参照GB50251的相关规定执行
7.5.2仪器设备 试验用的压力表、压力天平和温度计等计量器具应在检定或校准有效期内
19
GB/T37368一2019 7.5.3试验要求 耐压试验的过程应符合以下规定 a)试验过程应遵守GB/T16805及相关施工验收标准的规定
b 试验压力一般根据下一周期管道的拟运行压力确定
对于服役年限大于30年小于40年的长 输管道宜按照运行压力的1.25倍进行试压,对于超过40年以上的管道宜按照拟运行压力的 1.1倍进行试压
长输管道推荐的试验压力、稳压时间和合格标准见表8
管道的最高试验压力不得超过sMYS的90%
c -般采用洁净水作为试验介质
采用空气或输送介质进行耐压试验时,应符合相关法规及标 d 准要求,且应开展安全风险分析,相关安全措施应满足要求 试验过程中应对管道压力变化情况进行全程监控和记录,同时安排线路巡护人员重点观察沿 线地面有无介质泄放,地面附着物有无异常,以确定是否有管材破裂、穿孔等泄漏情况发生
.应拆除安全阀,阀门或安装盲板 f 试验期间,试验压力超过管道系统上安全阀的整定压力时, g 系统中的试验介质易产生热膨胀时,应在压力保持期间采取预防措施避免超压
h)试验完成后,管道系统应排空试压介质、进行吹扫或干燥处理
表8长输管道的试验压力、稳压时间和合格标准 输送介质 分类 试验压力及稳压时间 压力,MPa 拟运行压力1.1倍 -般地段 稳压时间,h 输油 压力,MP 拟运行压力1.25倍 管道 高后果区 稳压时间,h 24 合格标准 压降<1%试验压力,且s0.1MPa 压力,MPa 拟运行压力1.1倍 一般地区 稳压时间,h 24 拟运行压力1.25倍 压力,MPa 高后果区I级 稳压时间,h 24 输气 压力,MP 拟运行压力1.4倍 管道 高后果区级 稳压时间,h 24 压力,MPa 拟运行压力1.5倍 高后果区川级 24 稳压时间,h 合格标准 压降<1%试验压力,且<0.1MPa 7.6专项检测 7.6.1管道穿跨越段的检测 管道穿跨越段应按照穿跨越的类型进行分类并识别各类穿跨越段面临的风险因素和损伤模式,按 照GB/T37369等相关标准对管道本体和附属设施分别进行检测和评价
20
GB/37368一2019 7.6.2特殊工况和特殊部位检测 7.6.2.1特殊工况下材质理化检验 对以下管道宜按照GB/T30582的有关要求进行管道材质理化检验 有可能发生硫化物应力腐蚀开裂的管道; a D)材料状况不明的管道
7.6.2.2特殊部位环焊缝检测 7.6.2.2.1抽检部位 对以下环向焊接接头应重点抽检 内检测发现管道存在危险性超标缺陷的焊接接头; a 外检测开挖坑检中发现错边、咬边超标或存在表面裂纹的焊接接头 b 阀门、膨胀器连接的第一道焊接接头 穿跨越部位、出土与人土端的焊接接头; d 支吊架损坏部位的焊接接头; f 管道制造、安装中返修过的或连头、碰死口的焊接接头; 不同材质,不同壁厚对接的焊接接头 g h使用中发生泄漏部位附近的焊接接头
7.6.2.2.2无损检测要求 无损检测的方法选择、执行标准应符合以下规定 无损检测一般按照sY/T4109或NB/T47013(所有部分)执行
a b 管道的表面缺陷检测应优先采用磁粉检测,埋藏缺陷检测一般采用射线检测或超声检测等常 用方法;当检验现场无法实施射线检测或超声检测等方法时,也可采用TOFD,相控阵超声检 测、X射线数字成像检测等方法
首次检验时应进行埋藏缺陷检测,再次检验时,一般不再进行埋藏缺陷检测;当存在内部损伤 机理并且发现损伤迹象,或上次检验发现危险性超标缺陷时,则应进行埋藏缺陷检测
7.6.2.3特殊部位腐蚀检测 7.6.2.3.1抽检部位 腐蚀检测应重点抽检以下部位 滞流末端管道滞流末端管道与相邻管道的连接处及盲管位置 a 防腐层补口处的局部腐蚀位置, b c 土壤-空气界面处的外腐蚀位置; 高程落差较大的液体管道相对高点位置; d 控制阀、孔板、泵出口的下游易产生冲刷腐蚀位置 e 仪表插孔和法兰等结构件下游产生湍流的部位 f 7.6.2.3.2检测要求 特殊部位腐蚀检测的要求如下 -般采用目视检测,超声检测,射线检测、涡流检测和外壁漏磁检测等方法对以上腐蚀位置进 a 21
GB/T37368一2019 行检查或检测,也可采用表7中其他适用的方法进行检测; b 当检测发现存在严重腐蚀时,应加大抽检比例,对类似工况和部位进行重点检测
8 适用性评价 8.1基本要求 8.1.1检测工作结束后,应对发现问题的管道进行适用性评价,以确定管道许用工作参数、维修计划与 下次定期检验日期
8.1.2适用性评价分为应力分析、强度评估、剩余寿命预测和材料适用性评价
8.1.3开展适用性评价时,应综合考虑缺陷类型,载荷类型,失效模式,材料性能、缺陷扩展量、环境变 化、管道建造及运行历史等因素和数据,选择合理的评价方法和可接受准则
8.1.4适用性评价应考虑获取缺陷数据的检测设备的检测精度误差
8.1.5管道常见的缺陷可分为体积型、平面型和几何变形等3类,具体分类如下 体积缺陷;局部减薄(含腐蚀)、划痕、气孔、夹渣,深度小于1mm的咬边等; a b 平面缺陷;裂纹、未熔合、未焊透、深度大于或等于1mm的咬边等; 几何变形凹陷、皱褶、屈曲、鼓胀、椭圆变形等
c 当无法区分体积缺陷或平面缺陷时,宜按照平面缺陷进行评价
8.2应力分析 有下列情况之一的管道,应进行应力分析计算 a 存在较大变形、挠曲、破坏,以及支撑件损坏等现象且无法复原的 b 整体减薄量超过管道公称壁厚30%的; 需要设置而未设置补偿器或补偿器失效的; d 机械连接处(法兰或接头)经常性泄漏、破坏的 输送过程中发现管道存在振动、移位或敷设环境改变等异常情况的 e 注;e)中敷设环境改变主要指管道敷设地区等级发生变化的
f 检验人员或使用单位认为有必要的
应力分析计算应结合实际工况,呆用数值模拟或应力测试方法,分析管道的应力状态
8.3强度评估 8.3.1耐压强度校核 有下列情况之一的管道,应进行耐压强度校核 a)工作压力提高,或工作温度改变的 b)输送环境发生重大改变,管道地区等级升级的
耐压强度校核一般按照表9中标准进行,穿跨越段的耐压强度校核应按照穿跨越管道设计规范对 相关参数进行修正
也可采用行业认可的其他标准方法进行强度校核
表9管道耐压强度校核依据标准 管道类型 依据标准 输油 GB50253 长输管道 输气 GB5025 22
GB/37368一2019 表9(续》 管道类型 依据标准 燃气 GB50028 公用管道 热力 cJ34 GB50350 集输管道 8.3.2含缺陷管道剩余强度评估 按照以下要求,对检测发现的含缺陷管道进行剩余强度评估,确定管道最大允许工作压力 a 直管上体积缺陷的剩余强度评估按照GB/T30582,GB/T19624和GB/T35013等标准进行 弯头和弯管上体积缺陷按照GB/T30582和GB/T35013等标准进行 b 直管段上平面缺陷的剩余强度评估按照GB/T19624进行; 凹陷的剩余强度评估按照GB/T30582、GB/T35013进行,椭圆变形可按照GB/T35013进 行,其他管道儿何变形可采用有限元分析方法进行仿真计算 对于含对接焊缝错边和斜接等缺陷管道的剩余强度评价,可按照GB/T35013和SY/T6477 等标准进行; 对于含弥散损失缺陷、分层缺陷等缺陷管道的剩余强度评价,可按照sY/T6477进行
8.4剩余寿命预测 对检测发现的含腐蚀等与时间有关的缺陷管道,应考虑管道投用时间、缺陷致因等信息,建立管 8.4.1 道缺陷增长预测模型,对管道进行剩余寿命预测,根据寿命预测结果,确定下次检验时间
腐蚀管道的 剩余寿命预测按照GB/T30582进行
8.4.2对裂纹类缺陷的剩余寿命预测按照GB/T19624等相关标准执行
8.5材料适用性评价 8.5.1有下列情形之一的,应进行材料适用性评价 输送介质种类发生重大变化,改变为更危险介质的 aa b) 外部腐蚀环境发生显著改变的
8.5.2材料适用性评价可按照GB/T30582进行
8.6问题处理与检验周期确定 8.6.1问题处理 8.6.1.1问题处理应符合以下规定 对检验中发现的管体缺陷、防腐层缺陷和附属设施损毁等问题均应及时进行修复或处理" aa b -般由管道使用单位负责组织,由专业的施工单位负责实施; 修复或处理前,应制定详细的修复计划;对重大问题的处理应编制专项方案
c 8.6.1.2管体缺陷修复的原则如下 管体缺陷的修复计划一般包括立即修复、限期修复和监控使用;应对可能发生立即失效的管体 a 缺陷立即进行处理,其他缺陷应根据其严重程度限期修复或监控使用 b 管体缺陷修复应按照GB/T36701等标准进行
8.6.1.3防腐层修复的原则如下: 23
GB/T37368一2019 对检测发现的管道防腐层破损,应根据严重程度结合实际情况有计划地进行修复 a b)管道防腐层修复应按照sY/T5918等标准进行
8.6.1.4附属设施修复和处理原则如下 对发现的水工保护,地面标识和阴极保护设施等附属设施存在的向题,宜在检验后一年内完成 a 处理 管道附属设施的修复应按照相关设计及施工验收标准进行
b 8.6.2检验周期确定 8.6.2.1检验周期确定的原则 确定下次周期时,应考虑以下因素 a)法律法规的要求; b) 管道企业的安全管理规定和安全运行策略 检验的性质、检验的方法; c d 适用性评价结果,以及缺陷和问题的修复和处理情况
8.6.2.2 内、外检测的周期确定 确定内、外检测的下次周期时,应符合以下规定 定期检验周期应符合特种设备安全技术规范相关规定 a) b) 企业自行检查的周期不宜超过管道预测剩余寿命的一半 在确定管道下次检验周期时,可不考虑已修复缺陷和局部个别缺陷的影响;局部存在的个别缺 c 陷可在整条管道的检验周期到期前单独进行检验
8.6.2.3耐压试验的周期 以耐压试验为主要检验方法的管道,其检验周期最长不超过3年
9 基于风险的检验 g.1基本要求 g.1.1申请应用基于风险检验的管道应依据国家标准实施了完整性管理,且管道使用单位应满足以下 条件 具有完善的管道完整性管理体系和较高的管理水平; a b) 建立健全应对各种突发情况的应急预案,并且定期进行演练 管道运行良好,能够按照有关规定进行检验和维护; c 管道资料完整、准确 d e 工艺操作稳定; fD 管道采用sSCADA系统,并且有可靠的安全联锁保护系统
9.1.2从事基于风险检验的人员经过相应的培训,熟悉基于风险检验的有关国家标准和专用分析 软件
9.1.3基于风险的检验包括数据收集、风险评估、检验策略制定、检验方案制定、检验实施、适用性评 价、风险减缓、风险再评估及报告出具等工作内容
9.2数据收集 开展基于风险的检验时,数据收集除应满足表1规定的要求外,还应补充管道周边自然气候、地质 24
GB/37368一2019 状况、人口,建(构)筑物、水源及其他公共基础设施分布情况等数据,且应满足相关标准的要求
g.3风险评估 g.3.1风险评估应给出管道的失效可能性、失效后果、风险等级,为检测方法、项目、比例和重点检测管 段的选择以及为采取维修、维护等风险减缓措施提供依据,并能评价风险减缓措施产生的效果
9.3.2风险评估方法的选择应符合以下要求 管道风险评估方法包括但不限于专家评价法、安全检查表法风险矩阵法、指标体系法、场景模 型评价法和概率评价法等
b 所采用的风险评估方法应能识别出威胁管道安全的主要潜在危险或状态,能评价管道失效发 生的可能性和后果,能给出达到评价目标的风险结果及风险精度,能对检验、维修等风险减缓 措施效果进行评定
应根据风险评价目标,结合现有数据的完整程度以及经济投人等因素,选择适用的管道风险评 估方法
d 可以采用一种或多种风险评价方法来实现管道风险评价目标 埋地钢质管道风险评估一般包括如下步骤 9.3.3 a 数据收集和整合分析; 管道区段划分; b 失效可能性评价 ce 失效后果评价; d 风险值计算及级别划分; e 提出风险碱缓措施建议 9.3.4风险评估过程中管道危害因素和损伤模式识别、管段划分、高后果区识别,按照GB32167的相 关规定执行
依据收集的数据情况,可选择定量或半定量的风险评估方法
半定量风险评估按照 9.3.5 GB/T27512进行
采用GB/T27512开展评估时,风险评估人员可在基本模型评估的基础上,使用修 正模型开展风险评估
定量风险评估按照GB/T34346执行
9.4检验策略制定 9.4.1检验策略一般由承担基于风险检验的检验机构负责制定
9.4.2检验策略制定应综合考虑国家法规要求、使用单位管理制度、风险评估结果、安全管理或检验目 标、待检管道特征、服役工况和环境条件、检验有效性及资源投人等因素,一般包括以下内容: 潜在危险及损伤模式:; a 检验的时间; b 检验的管道范围; co 检验的项目、方法及依据标准
d 9.4.3确定管道检验时间时,应遵守以下原则 a 高风险管道、位于高后果区内的管道应优先检验
检验时间确定时应考虑检验仪器工具与工况、季节、路由状况的匹配性
开展内检测时应考虑 b 到管道不同时期的压力,温度及输量因素;开展外腐蚀防护系统检测时应考虑冻土,地面种植 物生长周期的影响;开展杂散电流检测时应考虑干扰源的运行周期;采用地电场原理检测时应 考虑土壤电阻率变化的影响
下次检验前的风险应低于较高风险等级
9.4.4检验项目及检验方法的选择,应符合以下要求 25
GB/T37368一2019 对高、较高风险等级的管段及风险超过风险可接受水平的管段应选择检验有效性为中高度及 a 以上级别的检验方法;对于中、较低及低风险等级的管段,可选择中度有效的检验方法
检验 有效性分级见附录B 选择适当的检验方法,且应保证被选用的检验方法的检验有效性能够满足检验目标要求
b 确定检验项目时,应选择检验管段对主要损伤模式及缺乏历史数据的重要项目开展检测,应重 c 点关注可能造成管道立即失效的历史问题及与时间相关的风险因素
采用外检测时,开挖检测位置应包含风险等级最高的管段
d 应根据各种检测方法的局限性,对检测难点提出有效的质量控制措施
必要时,应组合多种检 测技术进行综合检测
埋地钢质管道常用检测方法检测项目及推荐标准见表10,具体检测程序及内容依据相关标 f 准执行
表10常用检测方法 检测方法 潜在危险 损伤模式 检测项目 依据标准 金属损失 内外腐蚀 腐蚀减薄 应力腐蚀 环境开裂 裂纹 内检测 管材制造缺陷 制造缺陷 金属损失、裂纹 GB/T27699 焊缝缺陷 制造缺陷 金属损失、裂纹 外力破坏 机械损伤 金属损失,裂纹、儿何尺寸变形 腐蚀防护系统有效性、 外腐蚀 腐蚀减薄 管体金属损失 GB/T30582 外腐蚀 外检测 GB/T19285 路由环境、地面标识、埋地深、 外力破坏 机械损伤 管体金属损失和几何尺寸变形 外 GB/T34349 检测 内腐蚀 多相流计算、高程测绘 GB/T34350 内腐蚀 腐蚀减薄 外检测 管体金属损失 GB/T31211 GB/T28704 应力腐蚀 应力腐蚀 腐蚀防护系统有效性 GB/T36676 环境开裂 开裂外检测 开裂 管体金属损失和裂纹 埋深 机械损伤 GB/T19285 极端低温 管道位置和埋深 检测 冰胀 防雷 雷击 GB50251 其他 接地电阻等 电流过大) GB50057 检测" 检测" 管道位移 不良地质 管道位置和 暴雨、洪水 机械损伤 GB/T30582 条件检测 儿何尺寸变形 及土体移动) 仅在风险评估认为具有相应的潜在危险时应用
防雷检测一般由使用单位委托有防雷检测资质的专业机构负责
9.4.5检验策略中应明确适用性评价要求及检验周期的确定方法
9.5检验方案制定 g.5.1基于风险的检验工作开展前,应依据检验策略制定检验方案
方案中应至少包括以下内容 26
GB/37368一2019 管道基本情况; a b 依据规范、标准; 参与人员要求与分工; c d 基于风险的检验流程; 风险评估 e 检验策略制定; g 检验实施; h)适用性评价; 风险减缓的要求; j 风险再评估的要求; k 记录与报告要求
9.5.2基于风险的检验方案应与管道使用单位进行充分沟通,取得使用单位的认可后方可实施
9.6检验实施 9.6.1依据检验策略和检验方案规定范围,时间、方法,项目及比例开展现场检测工作
9.6.2现场检测过程应符合相关标准、操作指导书或仪器说明书等文件的要求,相关标准见表2、表4、 表5,表6,表7和表10中给出的依据标准
9.7适用性评价 现场检测结束后,应按第8章开展管道适用性评价
9.8风险减缓 应采取相应的风险减缓措施将管道风险控制在可接受水平以下,确保管道能够安全、可靠运行到 下一检验周期
风险减缓措施一般包括;降低失效可能性和降低失效后果两类
风险减缓的措施按照 GB/T34346等标准执行
9.9风险再评估 9.9.1基于风险的检验是个持续动态过程,应通过风险再评估,掌握管道最新的风险分布和水平
管 道使用单位应根据最新的检测、,运行维护和环境数据,对管道的风险评估结果进行更新
风险再评估的时机包括" 9.9.2 适用性评价及风险减缓措施实施后 a b 在管道的运行工况发生重大改变前; c 当管道的外部环境发生重大改变后; d 当发生地震、洪水等自然灾害后; e 检验到期前
g.9.3基于风险的检验确定下次检验周期时,应遵循以下原则 采用基于风险的检验方法时,可依据管道的风险等级对8.6,2确定的检验周期进行调整,原则 a 上低、较低风险的管道可适当延长检验周期,高、较高风险的管道应适当缩短检验周期 b)定期检验采用基于风险的检验方法时,其检验周期最长不得超过预测剩余寿命的一半,且不超 过9年
9.9.4对于风险等级超过风险可接受水平的管道,应分析产生较高风险的原因,采用针对性的方法和 措施来降低风险使风险控制在使用单位可接受范围内 27
GB/T37368一2019 10记录和报告 0.1记录 0.1.1所有的检测都应有完整的现场记录,记录至少应包含以下内容 a 检测管段或部位; b 检测设备的唯一识别标识
对检测结果会造成影响的环境条件; d 对检测结果会造成影响的管道检测部位状况或运行状况 表征管道状况的检测数据; e f 检测时间; 检测人员
日 10.1.2当记录为电子文档时,应有纸质的检索记录,记录检测时间、检测人员及电子文档名称等
0.2报告 传统检验报告至少包括以下内容 10.2.1 a) 项目概况 b 数据收集;应简要说明数据来源,并特别注明有怀疑或矛盾的数据 e 检验实施;包含检验检测的管道区段、时间、环境条件、技术方法与设备、数据等, 适用性评价;包括评价参照的法规标准、参数选取、评价过程,评价结论及维修维护建议 d e 结论建议;许用参数、下次检验日期,缺陷修复或其他安全措施建议,管道安全运行建议
10.2.2基于风险的检验报告至少包括以下内容 项目概况; a 数据收集;应简要说明数据来源,并特别注明有怀疑或矛盾的数据 b 风险评估包括所依据的评价标准、主要的原始信息、失效可能性、失效后果、风险值、风险级别 c 及风险消减措施建议等; 检验策略:至少包括9.3要求的内容 d 检验实施:包含检验检测的管道区段,时间、检测时的环境条件、使用的技术方法与设备,相关 单项检测的结论 适用性评价;包括评价参照的法规标准参数选取、评价过程、评价结论及维修维护建议 D 风险减碱缓风险减缓的措施方法和过程描述等; 日 风险再评估;包括所依据的评价标准、主要的原始信息、失效可能性、失效后果、风险值、风险级 h 别及风险消减措施建议等; 结论建议:;许用参数、下次检验日期,缺陷修复或其他安全措施建议,管道安全运行建议 iD 0.2.3内检测的报告内容及格式应符合GB/T27699的规定
10.2.4定期检验的检验报告内容及格式还应满足相关安全技术规范要求
0.2.5报告中所有的检测数据应能在记录中追溯
28
GB/37368一2019 附录 A 规范性附录) 站场内压力管道的检验 A.1范围 本附录适用于陆上长输,集输、公用管道系统中站场内钢质管道(以下简称“站内管道”)的检验,阀 室内压力管道的检验按照本附录执行
本附录不适用于LNG接收站内压力管道的检验
A.2基本要求 A.2.1站内管道的企业自行检查按本附录执行;站内管道的定期检验除满足本附录相关要求外,还应 满足相关特种设备安全技术规范的要求
A.2.2站内管道的检验机构应取得国家特种设备安全监督管理部门核准的资质
A.2.3站内管道包括架空和埋地两部分,其检验的一般流程如图A.1所示
A.2.4站内管道检验应遵守国家及管道使用单位的相关安全规定
确定检验范围 数据收集/更新 检验方案制定 宏观检验 埋地管道 架空管道 壁厚测定 非开挖检# 无损检测 开挖检测 安全状况等级评价 记录与报告 注非开挖检测是指在地面对埋地管道腐蚀防护系统进行检测
图A.1检验的流程 A.3数据收集/更新 检验前,使用单位应提交以下资料 29
GB/T37368一2019 设计资料,包括设计单位资质证明,设计,安装说明书,设计图样,强度计算书等; a b 安装资料,包括安装单位资质证明,竣工验收资料,以及管道安装监督检验报告等; 改造或修理资料,包括施工方案和竣工资料,以及改造、修理监督检验资料:; e d 使用管理资料,包括运行记录,运行中的异常及处理的情况记录等 检验、检查资料,包括安全附件的校准、校验资料,定期检验周期内的年度检查报告和上次的定 期检验报告; fD 有关法规要求以及检验人员认为定期检验所需要的其他资料
检验人员应根据检验的需要,对上述资料进行审查
a)项e)项所列资料,在管道投用后首次全 面检验时应进行审查,以后的检验视需要(如发生改造及重大修理等)进行审查 检验方案制定 A.4 A.4.1在收集数据的基础上,根据待检管道的敷设特征、损伤模式,并结合现场实际情况,确定检验项 目、方法和比例要求,并制定检验方案
A.4.2制定检验方案时,应按7.6.2.2和7.6.2.3的相关要求,加强对特殊部位环焊缝和特殊部位腐蚀 的检测
A.4.3检验方案的内容应符合第6章的相关要求
A.4.4检验方案应充分征求使用单位的意见,尤其是站场管理人员的意见
A.5宏观检验 A.5.1宏观检验内容 A.5.1.1架空管道 架空管道的宏观检验一般包括以下内容 管道有无泄漏 aa b 绝热层和防腐层是否完好、是否存在层下腐蚀现象; 管道的异常振动、变形(挠曲、下沉)以及位移情况 c d 管道组成件及其焊缝接头的腐蚀、裂纹、泄漏、鼓包、变形、机械损伤 支吊架的松动、变形脱落、断裂、腐蚀、焊接接头开裂,以及稳定情况; 支承件的断裂、损坏,弹簧支承失效,支承底板移位或其他非正常情况 阀门表面的腐蚀、裂纹、严重缩孔等缺陷,以及连接螺栓是否松动、阀杆操作是否灵活 8 h 法兰是否偏口,紧固件有无松动和腐蚀情况,有无泄漏迹象,以及法兰面有无异常挠曲,变形 膨胀节表面的划痕、凹陷、腐蚀穿孔、开裂等,以及异常变形偏心或位移等 排放(疏水、排污)装置的堵塞、腐蚀等 A.5.1.2埋地管道 埋地管道宏观检验一般包括以下内容: 管道有无泄漏; a 埋深、走向位置信息; b 地面标识和标志是否完好; c d 出土人土点防腐层状况; 地表沉降
e 30
GB/37368一2019 A.5.1.3补充规定 当宏观检验发现有地基沉降的,应补充测量管道变形、位移情况,必要时还应进行应力检测和应力 分析
A.5.2重点检查部位 宏观检验应对以下部位进行重点检查 承受疲劳载荷的管段; a b 曾经发生过事故或异常的管段; 经过重大修理或改造的管段 A.5.3单线图(或路由图)测绘 宏观检验时应绘制管道单线图(或路由图),且应符合以下规定 单线图(或路由图)应至少包括,管道规格,走向或路由、标高或埋深,管段长度、介质流向、管道 a 组成件、管道元件、支吊架位置及类型、安全保护装置,防腐(保温)层类型等信息 若管道使用单位能够提供清晰、准确的单线图(或路由图)时,则无需重新测绘 b 再次检验时,若管道未经过改造,一般不重新测绘
c A.6架空管道检验 A.6.1壁厚测定 A.6.1.1壁厚测定,一般采用超声测厚方法
A.6.1.2测定位置应具有代表性,有足够的壁厚测定点数
测定点位置选择和抽查比例应符合以下 要求 测定点的位置,重点选择易受腐蚀、冲蚀,制造成型时壁厚减薄和使用中易产生变形、积液、磨 aa 损部位,低频导波检测,外壁漏磁检测以及其他方法检查发现的可疑部位,支管连接部位等; 弯头(弯管)、三通和异径管等的测定抽查比例不得低于20%;每个被抽查的管道组成件.测定 b 位置一般不得少于3处;被抽查管道组成件与直管段相连的焊接接头直管段一侧的测定位置 -般不得少于3处;检验人员认为有必要时,还可以对其余直管段进行壁厚测定抽查; 管道支吊架处防腐层存在破损,或发生支吊架下腐蚀穿孔的,应采用高频导波等检测技术进行 支架下管体内外腐蚀检测,检测比例不低于20%; 在检验中,发现管道壁厚有异常情况时,应在壁厚异常部位附近增加测点,并且确定壁厚异常 区域,必要时,可适当提高整条管线测定的抽查比例 采用低频导波、外壁漏磁等检测方法进行长距离检测时,可仅抽查信号异常处的管道壁厚
A.6.1.3壁厚测定应在单线图中标注测定点位置和测定值 A.6.1.4对于局部内腐蚀的管道,可采用表A.1中的组合方法进行检测,对腐蚀位置和腐蚀深度进行 精确检测
31
GB/T37368一2019 表A.1管道腐蚀检测的组合方法 序号 腐蚀部位 初步检测方法 精确检测方法 外壁漏磁检测 相控阵超声检测 X射线数字成像检测 直管 超声测厚检测 脉冲涡流/远场涡流检测 超声波C扫描成像检测 高频导波检测 超声被C扫描成像检测 弯头 超声测厚检测 x射线数字成像检测 A.6.2无损检测 A.6.2.1表面缺陷检测 表面缺陷检测应采用NB/47013中规定的检测方法
铁磁性材料管道的表面缺陷检测应优先采 用磁粉检测
表面缺陷检测的要求如下: 宏观检验中发现裂纹或有怀疑的管道,应在相应部位进行外表面无损检测 a 对于保温层破损或可能渗人雨水的奥氏体不锈钢的管道,应在相应部位进行外表面无损检测 b e 检验人员认为有必要时,应对支管角焊缝等部位进行外表面无损检测抽查; d 碳钢、低合金钢低温管道,Cr-Mo钢管道,标准抗拉强度下限值大于或等于540MPa的低合金 钢管道,长期承受明显交变载荷的管道,应在焊接接头和应力集中部位进行外表面无损检测抽 查,抽查比例不少于焊接接头数量的5%,并且不少于2个; 检测中发现裂纹时,应扩大表面缺陷检测的比例
A.6.2.2埋藏缺陷检测 埋藏缺陷检测一般采用NB/T47013中的射线检测或超声检测等规定的方法
首次检验时,应进 行埋藏缺陷检测,检测比例为焊接接头数量的10%且不少于2个,再次检验时,一般不再进行埋藏缺陷 检测
当存在内部损伤机理并且发现损伤迹象,或上次检验发现危险性超标缺陷时,仍应进行埋藏缺陷 检测
埋藏缺陷检测的重点部位要求如下 安装和使用过程中返修或补焊部位; a) b 错边、咬边超标的焊接接头 表面缺陷检测发现裂纹的焊接接头 c 泵、压缩机进出口第一道或相邻的焊接接头; d 地基沉降、支吊架损坏部位附近的焊接接头; 不同钢级的焊接接头; 使用中发生泄漏的部位附近的焊接接头 g 对于温度、压力循环变化和振动较大的管道应加倍抽检,并且对所抽查的煤接接头的焊缝进行 100%无损检测 32
GB/37368一2019 埋地管道检验 A.7.1检测方法选择 应根据管道实际情况,按照以下原则选择合适的检测方法
a 对于具备条件的管道,可按照7.4进行检测, b)对于管道周围干扰严重,无法严格按照7.4进行检测的管道或埋地敷设长度小于100m的管 段,可进行腐蚀防护系统非开挖检测或开挖检测
A.7.2非开挖检测 首先应按照GB/T19285相关规定开展外防腐层质量与阴极保护系统有效性检测
防腐层质量检 测应排除各种管道接地点的电干扰 采用牺牲阳极作为阴极保护时,应使用极化探头等仪器或技术消除IR降影响; a b 采用强制电流阴极作为保护系统保护时,应检测断电位消除IR降影响,必要时还应检测阳极 地床接地电阻; 具有绝缘装置的管道,应参照GB/T19285检测绝缘性能
A.7.3开挖检测 A.7.3.1开挖位置选择 应综合考虑防腐层破损、腐蚀活性、阴极保护有效性、杂散电流及土壤腐蚀性等因素,对可能存在外 腐蚀损伤的位置进行排序,开挖检测应优先选择以下位置 站内低点排水位置的管段; a b 与汇管相连的排污管段、放空管段; c 出土人土端低频导波检测显示异常信号或存在破损的下弯头; d 地表存在明显沉降迹象的管段 环境腐蚀性强且防腐层存在破损的管段; e fD 类似结构位置发生过泄漏的管段 A.7.3.2开挖比例 站内埋地管道开挖检测时,开坑的数量和比例应满足以下原则 存在A.7.3.1情况的,每类开挖的数量应不少于1处; a b 长度超过100m且无分支的埋地管道应开挖1处进行低频导波检测 站内埋地管道总长度不足500m的,开挖坑数量应不少于2处 d 站内埋地管道总长度超过500m不足1000m的,开挖坑数量应不少于4处; 站内埋地管道总长度超过1000m的,开挖坑数量应不少于6处; e 抽查时若发现危险性超标缺陷的,应增加抽查比例,增加量由检验人员与使用单位结合管道运 行参数和实际情况协商确定
A.7.3.3开挖检测内容 开挖检测应按照7.3.4.3的要求,开展土壤腐蚀性检测防腐保温)层检查和探坑处管地电位检测、 管道本体检测和焊缝的无损检测,并采用专项检测技术对以下特殊部位开展补充检测 具有局部内腐蚀的管道,可采用表A.1中的组合方法,对腐蚀位置和腐蚀深度进行精确检测 a 33
GB/T37368一2019 b 可能存在应力集中的部位,可采用X射线衍射检测等方法进行应力状态检测 套管内的无缝管,可用低频导波对管道本体状况进行整体检测
A.8安全状况等级评价 站内管道按照TsGD7005的相关要求开展安全状况等级评价,并确定检验周期
A.9记录与报告 记录及报告应满足第10章的相关要求
34
GB/37368一2019 录 附 B 规范性附录 埋地钢质管道检验有效性 B.1检验有效性分级 B.1.1检验有效性应考虑下列因素 检验类型 a b 管道和元件的结构类型; 损伤模式及失效模式; d 损伤扩展速率或敏感性; 检测方法和频次; e fD 受检部位的可检程度
B.1.2检验有效性分为5个级别,见表B.1
表B.1检验的有效性分级 检验有效性级别 描述 某种检验方法准确识别某种损失实际状态的置信度在80%~100%之间 高度有效 中高度有效 某种检验方法准确识别某种损失实际状态的置信度在60%一80%之间 中度有效 某种检验方法准确识别某种损失实际状态的置信度在40%一60%之间 低度有效 某种检验方法准确识别某种损失实际状态的置信度在20%40%之间 无效 某种检验方法准确识别某种损失实际状态的置信度在020%之间 B.2各类检测方法的检验有效性级别 各种内检测方法的检验有效性分级见表B.2,各种开挖无损检测方法的检验有效性分级见表B.3 各种防腐层漏点检测方法的检验有效性分级见表B.4 35
GB/T37368?2019 3 紧 ? ? 3 ? ? ? Go d G0 G e ? 3 ? R 3 ??? s T 36
GB/37368?2019 X 3 ? 6m m m o m ? ? ? 37
GB/T37368一2019 起 欢 异 紧 邀 米 人 大 一 室 一 因 田 蛋 g 妈 没 卡 38
GB/37368一2019 表B.4各种防腐层质量检测方法的有效性分级 检测方法 检测对象 电位梯度法 音频检漏法 密间隔电位法 交流电流 ACVG,DCVG) PEARSON CIPS) 衰减法 带防腐层漏点的管段 1.2 裸管的阳极区管段 近河流和水下穿越管段 无套管的穿越管段 1,2 1,2 带套管的管段 短套管 铺砌路面下的管段 1,2 冻土区的管段 1,2 相邻金属构筑物的管段 ,2 ,2 相邻平行管段 杂散电流区的管段 1,2 1,2 高压交流输电线下方管段 1,2 管道深埋区的管段 湿地区(有限的)管段 1,2 l,2 石方带、岩礁,回填区 注,1为高度有效;2为中高度有效;×为低度有效或无效 39
GB/T37368一2019 录 附 规范性附录) 金属损失漏磁内检测器最低要求 金属损失漏磁内检测器的最低要求见表C.1
表c.1金属损失漏磁内检测器最低要求 项目名称 技术指标 轴向采样间隔 2mm 传感器周向间距 6mm 最小检测深度 10%t 检测能力 深度检测精度 士10%1 最大检测速度 5m/s 最小检测深度 10%t -般金属损失缺陷 深度检测精度 士10%1 长度检测精度 士20mm 10%t 最小检测深度 坑状金属损失 士10%t 深度检测精度 长度检测精度 士10mm 最小检测深度 20%t 缺陷长度(轴向 深度精度 轴向凹沟 深度检测精度 士15%" 长度检测精度 士20mm 10%t 最小检测深度 士15%! 周向凹沟 深度检测精度 士10mm 长度检测精度 轴向凹槽 最小检测深度 可检测 周向凹槽 最小检测深度 10%t 深度检测精度 士15%1 周向凹槽 长度检测精度 士10mm 士15mmmr 长度检测精度 环焊缝上的腐蚀 士15%t 深度检测精度 士10mm 宽度精度(周向)》 距离最近的参考点 士1%定标距离 定位精度 距离最近的环焊缝 士0.1m 40
GB/37368一2019 表c.1续 项目名称 技术指标 80% 置信水平 注1:1 管道壁厚
注2管道金属损失类型一股分为一般金属损伤、,坑状金属损失,轴向凹沟金属损失,轴向凹槽金属损失、周向四 沟金属损失和周向凹槽金属损失,金属损失类型定义见NB/T47013.12.
埋地钢质管道检验导则GB/T37368-2019解读
埋地钢质管道作为一种广泛应用于城市供水、燃气、暖通和输油输气等领域的管道材料,其安全性和可靠性对于保障人民群众生产生活的正常进行至关重要。然而,由于埋藏在地下,管道的运行状态难以直接观察和检测,存在泄漏、腐蚀、破坏等风险,给工程安全带来极大的挑战。
为了确保埋地钢质管道的安全运行,我国制定了一系列相关标准和规范。其中,埋地钢质管道检验导则GB/T37368-2019是最新发布的一项标准,该标准于2019年正式实施,旨在规范埋地钢质管道的检验和评估。
首先,该标准要求对埋地钢质管道进行分类评估,根据其所处环境、使用年限、材质等因素,确定不同等级的检验要求。例如,对于新建的高压输气管道,将采用全面、细致的检验方案,包括内部和外部的检测措施,确保管道的安全可靠性。
其次,该标准还规定了埋地钢质管道的检验方法和技术要求。例如,检验过程中应当采用无损检测技术,通过超声波、磁粉探伤、液体渗透等方法对管道的壁厚、腐蚀程度等参数进行检测,发现隐患并及时处理。同时,标准还明确了检验人员的资格要求和考核机制,确保检验过程的专业性和准确性。
此外,该标准还规范了埋地钢质管道的修复和强化措施。例如,如果在检验过程中发现管道存在腐蚀或破裂等问题,应当及时采取针对性的修补措施,而对于老化、损伤较严重的管道,则应当考虑增加支撑、改进环境等强化方案,确保管道的安全稳定运行。
总的来说,埋地钢质管道检验导则GB/T37368-2019是我国在工程建设领域中的一项重要进展,其实施将有助于提高埋地钢质管道的安全性和可靠性,减少因管道事故而带来的人员伤亡和经济损失。此外,该标准还具有推动技术创新、提升检测能力的积极意义。