GB/T34350-2017
输油管道内腐蚀外检测方法
Externalinspectionmethodologyforinternalcorrosionofliquidpetroleumpipelines
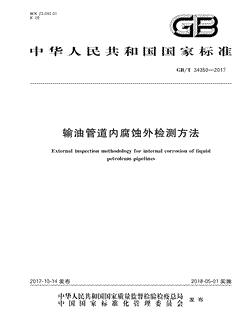
- 中国标准分类号(CCS)E29
- 国际标准分类号(ICS)23.040.01
- 实施日期2018-05-01
- 文件格式PDF
- 文本页数29页
- 文件大小4.04M
以图片形式预览输油管道内腐蚀外检测方法
输油管道内腐蚀外检测方法
国家标准 GB/T34350一2017 输油管道内腐蚀外检测方法 Externalinspeetionmethodolosyforintermalcorrsionofliquid petroleupipelines 2017-10-14发布 2018-05-01实施 国家质量监督检验检疫总局 发布 国家标准化管理委员会国家标准
GB/34350一2017 前 言 本标准按照GB/T1.1一2009给出的规则起草
本标准由全国锅炉压力容器标准化技术委员会(SAC/TC262)提出并归口
本标准起草单位:特种设备检测研究院、西安交通大学、石油化工股份有限公司茂名分公 司、石化销售有限公司、石化管道储运有限公司、石化上海石油化工股份有限公司、石 油天然气股份有限公司长庆油田分公司第三输油处、石油天然气股份有限公司长庆油田分公司第 -输油处、石油化工股份有限公司上海高桥分公司、石油化工股份有限公司巴陵分公司、上海 石油化工股份有限公司公用事业公司、石油天然气股份有限公司塔里木油田分公司、石油天然 气股份有限公司青海油田分公司、石油天然气股份有限公司长庆油田分公司油田开发处
本标准主要起草人;孟涛、马红莲、何仁洋,王跃社、栗学勇、卜文平、张惠民、吴海东金强、李保荣 张建昌、李佩、顾雪东、蔡建平、邵珊珊、何俊、杨辉、顾为敏、张中放、马晓斌、何毅
GB/34350一2017 输油管道内腐蚀外检测方法 范围 本标准规定了埋地钢质输油管道内腐蚀外检测的内容、方法及程序,包括总则、数据收集、腐蚀位置 预测、开挖检测、检测周期确定、记录和报告及附录等内容
本标准适用于满管流动的液态石油管道
地面敷设输油钢质管道内腐蚀外检测可参照本标准 执行
规范性引用文件 下列文件对于本文件的应用是必不可少的
凡是注日期的引用文件,仅注日期的版本适用于本文 件
凡是不注日期的引用文件,其最新版本(包括所有的修改版)适用于本文件
GB/T19285埋地钢质管道腐蚀防护工程检验 GB/T19624在用含缺陷压力容器安全评定 GB/T30582基于风险的埋地钢质管道外损伤检验与评价 TSGD7003 长输(油气)管道 压力管道定期检验规则 术语和定义 下列术语和定义适用于本文件
3.1 管道内腐蚀外检测extermalinspeectionforpipelineinternalcorrosion 从管道外部对输油管道内壁腐蚀情况进行检测的方法,包含数据收集、腐蚀位置预测、开挖检测及 检测周期确定等步骤
3.2 检测区段inspeetonregiom 开展内腐蚀外检测的输油管道,其流体特性、缓蚀剂措施以及其他化学处理没有显著变化的一段连 续管道(包括焊缝),同一区段有相似的物理特征和运行参数
3.3 油水分散流oil-waterdispersedflow 油水多相流的一种流态,即油相和水相以均一稳定的油水乳状液流动 3.4 油水分层流oil-waterstratifiedlow 油水多相流的一种流态,即流体可以按层分;轻流体(油相)浮在较重流体(水相)上面的流动 3.5 真实水速insituwatervelocity 油水分层流中底层水的平均流速
GB/T34350一2017 3.6 最大液滴直径 maximumdropletsize dm 悬浮在油包水分散系中,不因湍流剪切力而破碎的水滴的最大直径
3. 临界液滴直径 eritteldroplesixe dert 在水平或近水平流的油包水型分散系中,不因重力而发生沉降的水滴的最大直径
3.8 临界流速eriticalveloeitsy Vm 最大液滴直径d,等于临界液滴直径da时的流速;当实际流速大于临界流速时,管线不会形成 积水
3.9 实际倾角inelinationangle C 管道上两点间高程变化形成的角度
3.10 临界倾角eritiealinelinationangle 由输油管道内腐蚀外检测流体模型确定的积聚水或固体杂质的最小倾角
3.11 接触角 contactangle 在气、液、固三相交点处所作的气-液界面的切线穿过液体与固-液交界线之间的夹角,是润湿程度 的量度 3.12 管段segment 整根管道或管道的一段,可包括一个或多个检测区段
3.13 润湿weting 液体在与固体接触时,沿固体表面扩展的现象,通常用接触角来反映润湿的程度
总则 4.1输油管道内腐蚀外检测工作应满足TsGD7003等国家相关法规标准的规定
4.2本标准提供一套流程化的管道内腐蚀检测方法,从管道外部对无法开展内检测的管道进行检测
在检测过程中如果发现第三方破坏,外部腐蚀、机械损伤,应力腐蚀开裂等其他威胁管道安全的因素,检 测人员应依据GB/T30582、GB/T19285,GB/T19624等相应标准开展其他的检测评价工作
4.3在应用本标准开展检测工作前,应评价本标准方法对计划检测管道的适用性
检测管道至少应满 足以下条件: 管道正常运行期间不存在连续水相 a b 管道应无连续完好的内涂层; 管道可以进行开挖检测; c d) 对于有清管作业史的管道,检测人员应对本方法的适用性进行技术论证
GB/34350一2017 4.4实施检测前,检测单位应充分收集管道的内腐蚀数据,特别是与内腐蚀相关的事故情况,制定检测 技术方案
在实施检测过程中,负责解决检测过程中的技术问题
管道使用单位应负责协调检测过程 涉及的相关单位或部门关系,提供检测需要的相关数据
4.5检测单位及人员应在许可范围内从事检测工作,并对检测结论的真实性,准确性和有效性负责
注:真实性表示报告,结论以客观事实为基础,不作假证;准确性表示报告、结论所涉及到的检测数据符合相关要 求;有效性表示检验机构的资质、检验人员的资格符合要求,所使用的仪器设备在检定校准有效期内,检验依据 合法,报告审批程序符合要求
4.6内腐蚀外检测方法实施的主要步骤及流程如图1所示
4.7内腐蚀外检测方法具有局限性,当使用过程中无法获取第5章需要的数据时,应选择其他方法进 行内腐蚀评价
确定管道范围 数据收集 香 停止本方法 判断适用性 制定方案 划分检测区段 管道实际倾角计算 临界倾角计算 开挖位置初步选择 开挖检测 下次检测周期确定 出具报告 图1内腐蚀外检测主要步骤及流程 5 数据收集 5.1检测工作开始前至少应收集表1所列数据
5.2数据可从设计文件,安装资料,运行维护记录、计量台账和腐蚀检查记录、油品分析报告及前期完 整性评估或维护活动的检测报告中获取
5.3开展内腐蚀外检测工作应保证检测过程中需要的数据可收集并满足要求
5.4检测人员可根据相似管道系统的经验和掌握的信息,对个别无法获得的非计算过程直接使用的数 据,进行保守处理并应做好书面记录
GB/T34350一2017 表1内腐蚀外检测需要的基本数据 数据名称 需收集的数据 类别 管径、壁厚和材质 管道公称直径、壁厚以及材质 管道本体 地形数据,包括管道埋深
选择测量设备时应确保设备精确、准确 高程 度满足要求 油品分析 油品的密度、黏度等物性 液态石油中水、固体杂质的含量液态石油中沉积物(油渣和水)的含量 介质条件 碗化氢(HS),二氧化碳(co)液态石油中硫化氢(Hs),二氧化碳(co.)和氧气(o.))的含量,管道 各位置的化学分析 和氧气(O.)的含量 其他介质 有机酸,微生物、叙离子等 最大,最小流速 所有出人支管的最大,.最小流速 压力 最小和最大运行压力 操作工况 温度 介质温度
除特殊管段如穿河、或架空)外的运行温度 流向变化(正反输、输送方式(连续、断续等、投用时间、管道短期 操作记录 停输历史等 确认管道当前及历史注人和分输位置 输人或输出注人或分输位置 缓蚀剂 加注位置,化学药剂类型,方式(批次/连续),剂量 清管操作 清管器类型、清管频率、清出的水或固体杂质的体积 内检测或宏观检测(内腐蚀》 内检测或宏观检测确认的内腐蚀位置和严重程度 其他内腐蚀记录 其他已知的内腐蚀位置、严重程度和机理如CO. 泄谢/失效 内腐蚀引起的泄漏/失效的位置和性质 其他数据 包括监测方式[如检查片,电阻(ER)/线性极化(LPR)探针,场图法 腐蚀监测 FSM]、位置、时间、壁厚变化,记录腐蚀速率 内涂层 具有内涂层的位置 加注位置、化学剂类型及减阻、降凝或增凝等流体物理特性改变 其他化学处理 方式 其他内腐蚀数据 由检测人员确定 当沉积物油渣和水),CO、H.O,O含量等介质组分相关数据未知时,应通过采集样品测试分析得出
腐蚀位置预测 6.1概述 6.1.1腐蚀位置预测是通过流动模型计算结果识别管道中潜在积水或固体杂质的位置,并以此预测各 检测区段最可能发生内腐蚀的位置
6.1.2腐蚀位置预测工作包括检测区段划分、内腐蚀影响因素分析、水或固体杂质积聚的临界倾角计 算、管道实际倾角计算,内腐蚀位置识别
GB/34350一2017 6.2检测区段划分 6.2.1现场检测工作开始前,依据第5章所收集的数据划分检测区段
应将以下位置作为划分检测区段的分界点 6.2.2 输送介质注人点、分输点; a 缓蚀剂或化学药剂加注点; b 经过加温或加压站后导致温度和压力等工艺参数发生变化的点; c d 特殊地形地貌起止点; 管道规格发生改变的点
当存在介质正反输送工况时,应在正反输送工况的每个输送方向上分别划分检测区段
6.2.3 6.3内腐蚀影响因素 6.3.1积水因素 6.3.1.1积水因素是内腐蚀的主要影响因素之一,管道积水预测方法参见附录A 6.3.1.2积水对管道的腐蚀的影响取决于金属表面润湿状况油湿表面的管道与腐蚀物隔离不发生腐 蚀;水湿表面的管道与腐蚀物接触极易发生腐蚀;中性湿表面的管道与腐蚀物接触倾向取决于是否存在 水等竞争相
通常假设所有位置的润湿性相同,润湿性的确定方法参见附录B
6.3.1.3管壁润湿由憎水(油湿)变为亲水(水湿)所需的时间取决于姬的性质、添加剂表面活性及流动 运行条件
6.3.1.4通常假设水的化学性质在整个管道长度上保持相对稳定,但也应考虑以下情况 随距离增加,因内腐蚀等原因溶解的铁离子会影响水的pH值; aa 管道中氧气含量较小时,由于上游管段的消耗,导致下游管段无氧气
b 6.3.2固体杂质积聚因素 6.3.2.1固体杂质积聚是内腐蚀的主要影响因素之一,固体杂质积聚预测方法参见附录C
6.3.2.2积水处的腐蚀受有机或无机固体杂质的影响
固体杂质主要来源于液体中沉淀物或管道表面 氧化产物
6.3.2.3腐蚀产物、沉积物及夹带物中的有机和无机物质均会对固体杂质积聚引起的内腐蚀产生影响
应考虑以下因素 长输管道清管的有效性; a b 固体杂质各组分的潜在内腐蚀机理; 腐蚀产物、黏附性沉积物或有机沉淀物等保护性沉积物可降低管壁内腐蚀速率及程度, c 管道内表面结蜡和稳定沥青层的形成可有效抑制腐蚀
d 6.3.3流动条件因素 6.3.3.1水和固体杂质输送滞后 重新夹带沉积水和固体杂质所需的速度大于稳态下维持夹带物流动的速度
短期停输和降低输量 均影响腐蚀凤风险程度
6.3.3.2紊流和流动扰动 紊流和流动扰动的影响取决于流速、流动方式,液态石油性质和沉积物油渣和水)含量 弯头和焊缝结构引起的附加紊流可加强水相夹带作用,降低内腐蚀速率 aa b 紊流可促使水滴冲破薄油膜,润湿管壁导致局部腐蚀
GB/T34350一2017 6.3.4其他因素 6.3.4.1 破乳 两种不相溶液体(如油和水)充分混合时.其中一种液体会以液滴形态分散于另一种液体中
当混 合等作用停止时混合液会随时间推移而分离成不同的相
6.3.4.2缓蚀剂 缓蚀剂对管道各段腐蚀的影响规律与加注点距离和加注方式有关
分批加注和连续加注的效果不 同,且与清管频率有关,具体的影响规律如下 分批加注缓蚀处理管段的腐蚀更易发生于上游管段
下游管段可将上游管段析出的部分缓蚀 a 剂再吸收,缓蚀作用时间更久
应于下游监测确定批次频率
b 连续加注缓蚀处理管段的腐蚀更易发生于下游管段
缓蚀剂残留浓度随距离而降低,保护效 果减弱
加注点间距较长的管道应在上游管段作腐蚀监测
6.3.4.3微生物 对于存在微生物腐蚀的长距离管道,预测腐蚀严重程度时存在较大的不确定性
以微生物腐蚀为 主要腐蚀机理的管道系统需进行附加检查
微生物腐蚀普遍发生在以下位置 可积水的位置; a b) 可积聚固体杂质的位置; e 长输管道的低点; d 介质流动性差或不流动的管段、管件(如盲管); 焊缝和已发生点蚀的位置
e 6.4水和固体杂质积聚的临界倾角计算 6.4.1应对每个检测区段采用流动模型计算可能产生水或固体杂质积聚的临界倾角 6.4.2积水处的腐蚀受有机或无机固体杂质的影响
固体杂质主要来源于液体中沉积物或管道表面 氧化产物
针对每个确定的检测区段,检测人员应采用流动模型预测水、固体杂质积聚的临界倾角和速 度
水积聚临界倾角的计算方法参见附录A,固体杂质积聚临界倾角的计算方法参见附录C
6.4.3已通过机械清管验证无沉积的管道不需进行固体杂质积聚分析
6.4.4同一个检测区段内的临界倾角不一定是常数值应基于该位置的局部压力和温度等工艺参数计 算),通常可将各临界倾角数值逐段标注于倾角与高程图上
6.5管道实际倾角计算 6.5.1应对收集的管道高程图进行检测验证,管道埋深检测误差应不大于实际埋深的10%埋深小于 lm的以1m计算),高程测绘测量中误差不得大于士3cm(相对于邻近控制点);不满足精度要求时 应重新检测
依据管道高程计算管道的实际倾角,绘制成管道实际倾角剖面图
6.5.2根据管道走向位置与地形等因素,确定管道高程测量点的水平间距,该间距应能反应管道所有 实际倾角变化
6.5.3检测人员应书面记录管道高程测量方法、高程数据及检测过程中所作的假设等
6.5.4实际倾角可由式(1)计算 18o AH -arcSIn 4L 式中 实际倾角,单位为度()
GB/34350一2017 公H -测点间的高程差,单位为米(m); L -测点间的直线距离,单位为米(m 6.5.5高程测量点的间距设定应能捕捉到所有倾角分布的变化
根据待评估管道及地形等确定最小 间距
倾角纵面图的准确度主要取决于高程数据的精度
6.5.6高程数据的采集方法,所获取的高程数据、获取过程中所作的假设,倾角分布不确定性及其确定 方法均应记录并归档
6.6内腐蚀位置识别 6.6.1通过比较临界倾角与管道实际倾角大小,识别可能发生内腐蚀的位置,管道实际倾角大于临界 倾角的沿流向上坡部位易发生水或固体杂质积聚导致内腐蚀(腐蚀位置预测应用举例参见附录D)
6.6.2管道走向、管件或管径改变易引发局部紊流变化、固体杂质积聚,导致依附录A方法确定的非腐 蚀位置具备腐蚀条件
应对截断阀,管道变径处和液态石油注人点的下游接头以及地形或管道走向改 变引起过度弯曲处下游等可能发生局部固体杂质沉积的位置,进行开挖检测
6.6.3若前期已识别出有内腐蚀存在,则与内腐蚀位置具有相似特性的位置可定为内腐蚀易发位置
6.6.4当预测的内腐蚀可能发生位置与历史数据严重不符时,则应确认所收集的数据的准确性以及所 进行的计算结论的正确性
开挖检测 7.1概述 7.1.1开挖检测的目的是通过对开挖段管道壁厚的检测判断开挖检测位置是否存在内腐蚀,并以检测 结果评估管道的整体内腐蚀情况
7.1.2需开挖检测的位置包括腐蚀位置预测阶段识别到的可能腐蚀位置和开挖检测过程中确定可能 存在腐蚀的位置
开挖检测的一般流程如图2所示,与图2流程不符的变动或更优化的开挖检测流程 包括概率统计法)应先经技术论证合理,可行后实施,并做书面记录
7.1.3应至少选择一处内腐蚀可能性较小的位置进行开挖检测
开挖检测过程中应依据相应标准或作业指导书开展管体壁厚无损检渊工作
7.1.4 7.1.5对开挖检测过程发现的除内腐蚀之外的外腐蚀、机械损伤、应力腐蚀开裂等缺陷,应选择其他方 法进行检测评估
7.2开挖检测实施过程 7.2.1根据图2开挖检测流醒,应从检测区段的起始处向下游顺序检测实际倾角大于临界倾角的管道 位置
结束开挖检测的条件是连续两个检测位置未发现内腐蚀,并用下游第三个实际倾角大于临界倾 角的检测位置进行验证
检测位置的选择还应遵守以下规定 当实际倾角都小于临界倾角时,应检测最大实际倾角位置
当存在内腐蚀时,选择下游的最大 a 实际倾角部位进行检测;当没有内腐蚀时,检测下一个最大实际倾角位置作为验证
应在每个检测区段至少选取2处实际倾角最大的位置进行开挖检测
流体和固体杂质在长距 b 离输送中可能分层,应将5km以上的检测区段等分为三个子区段,并分别对每个子区段中实 际倾角最大的2处位置进行开挖检测
子区段是指存在腐蚀的两个倾角之间或检测区段起始 点与第一个倾角之间的连续管段 对每个检测区段,应对基于积水模型确定实际倾角最大的2处位置进行开挖检测
对存在 2处以上实际倾角最大位置的区段或子区段应增选检查点
对因流动扰动导致固体杂质积聚的管道,对每个检测区段或子区段选取实际倾角最大的2处 d 位置进行开挖检测
管径或泾类密度增大均会加剧因流动扰动引起的固体杂质积聚
GB/T34350一2017 选取位置时应考虑现场检查的可实施性,维修维护历史及内部泄漏/失效历史;开挖检测位置 应比对维修历史记录选取,以确定是否存在钢质或复合材料修复套管增加检查难度
由于内 腐蚀与时间相关,应避免所选的位置位于曾换管的区段
有正反输送历史的管道,应对正反输送两个方向分别进行检测区段划分和开挖检测,考虑流向 改变对所选择位置处腐蚀分布的影响
如果存在多处腐蚀,要重新考 “确定开挖点" 虑内腐蚀外检测方法的适用性 第6章 每个检测区段开 挖的先后顺序 第;个检测区段的第1个 第个检测区段的第/个 内腐蚀预测位置 可能内腐蚀预测位置 存在内腐蚀 存在内腐蚀 否 否 存在其他 第个检测区段的第+1个 腐蚀机理 内腐蚀预测位置 存在内腐蚀 是 存在集水器 检测装置 已检查所有区段 根据需要计算剩余强度 完成必要的修复 开挖检测报告 下次检测周期确定 说明:图中i,分别为从1n
图2开挖检测流程图 7.2.2应采用如下准则之一来判断是否存在严重的内腐蚀: 当管道壁厚小于管道的最小安全壁厚时,认为管道存在内腐蚀金属损失并发生了严重的内腐 a
GB/34350一2017 蚀(考虑外腐蚀造成的壁厚减薄); b 针对具体管道应考虑以前的金属损失和管道使用年限,制定具体的严重内腐蚀判别标准 也可使用其他经过技术论证的严重腐蚀判定准则
c 7.2.3检测人员认为必要时,可增加开挖位置进行验证检测
7.2.4当开挖检测过程中发现了大范围的严重内腐蚀时,检测人员应返回到数据收集阶段确认本标准 的可行性
7.2.5开挖检测时,应当对管道壁厚进行详细,准确的测量,应确定腐蚀减薄缺陷尺寸及相对位置
壁 厚减碱薄的轴向长度超出开挖范围时应对检测位置进行扩挖
7.2.6确定腐蚀区段管道剩余壁厚的无损检测工作应依据相应标准或作业指导书进行
7.3管体开挖检测 7.3.1管道开挖、检测及回填过程中,应遵守相关规范及标准,满足健康安全环保相关要求
7.3.2管体内腐蚀检测时,可采用外壁漏磁、外壁远场涡流等无损检测手段,结合超声波测厚仪对内腐 蚀情况进行检测
应使用超声波测厚仪对开挖出的螺旋焊缝或直焊缝边缘处其他检测手段无法检测的 部位进行管道壁厚检测
7.3.3上游管段的内检测结果可用于评估内检测器无法通过的下游管道的状态,但应结合开挖检测结 果对内检测结果进行验证
7.3.4管道开挖后,可安装腐蚀监测装置,根据监测的腐蚀速率数据,确定检测周期
7.3.5当最有可能因积液而发生内腐蚀的位置未发现内腐蚀时,则可认为本评估管段其他部位不存在 内腐蚀
7.3.6对于检测过程中发现的缺陷的处理应按照相关标准执行
7.4其他设施部件检测 7.4.1无临界倾角的无流动管件(如盲管等)也可能存在水或固体杂质积聚
例如三通位置因流向突 然改变积聚水和固体杂质
7.4.2应至少检查一处因流动效应可能存在水或固体杂质积聚的管件
8 检测周期确定 8.1应根据内腐蚀程度、腐蚀速率、维修情况及输送压力等参数确定下次检测周期
可用下列方法之一确定腐蚀迷率 8.2 按一定周期连续监测同一位置的管道壁厚损失确定腐蚀速率(即监测管道的腐蚀量)3 aa b 在基于流动模型预测的有水和固体杂质积聚的管道位置或典型的管道位置,安装腐蚀监测装置; 基于操作条件,液体组分等关键因素,建立数学模型进行腐蚀速率计算 c d)基于操作条件、液体组分等关键因素,通过实验室试验确定输送介质的腐蚀性
8.3可通过剩余寿命预测或剩余强度计算确定下次检测周期
未发现内腐蚀缺陷时不需计算内腐蚀 剩余寿命,即管道不存在内腐蚀危险;存在内腐蚀的管道可依据发现的最严重缺陷计算内腐蚀剩余寿 命
剩余强度可依据GB/T19624,GB/T30582等相关标准计算
8.4下次检测周期应不大于剩余寿命的一半 9 记录和报告 9.1记录 9.1.1数据收集、腐蚀位置预测,开挖检测及检测周期确定各步骤相关的资料,包括所有决策和支持性
GB/T34350一2017 的评价数据,都应清楚、简洁、可用的记录在案,在管道使用期内应妥善保存
g.1.2数据收集阶段应记录所有表1要求数据及数据来源
g.1.3腐蚀位置预测阶段应记录检测区段的特征、边界(地理参考位置)及管道实际倾角剖面图的测绘 过程数据
g.1.4开挖检测阶段应记录所有检测的措施和决策,包括但不限于以下内容 开挖前、后收集的数据,包括金属腐蚀损失几何尺寸、用于识别其他可能腐蚀位置的数据,以及 a 用于估算腐蚀速率的数据; b 内腐蚀减缓措施; c 开挖检测点的增加及其排序的依据和相关描述
9.1.5检测周期确定阶段应记录评价方法、评价依据、剩余寿命、剩余强度计算参数的确定及下次检测 周期
9.2报告 g.2.1检测报告的内容应以记录为依据 检测报告应包括以下内容,但不仅限于这些 9.2.2 管道基本情况 a 数据收集;应简要说明数据来源,并特别注明有怀疑或矛盾的数据; b 检测区段划分情况;包括划分依据,边界的地理位置参考, c 管道实际倾角剖面图绘制:包括现场高程测量、管道埋深的检测数据及数据计算; d 临界倾角计算;包括计算使用的参数、计算过程及结果, 开挖检测位置;包括开挖检测位置的选择依据及结果, 开挖检测:包括检测过程、使用的仪器设备及检测数据 g 下次检测周期;包括剩余寿命或剩余强度的计算以及确定的下次检测周期; h 维护建议:需要时,对发现的严重腐蚀问题提出维护建议
0
GB/34350一2017 附 录 A 资料性附录 管道积水预测 概述 A.1 A.1.1管道积水预测应考虑管道系统运行条件,如液体石油组分,压力,温度、流量、沉积物油渣和水) 等,选择适用的判定指标
A.1.2临界倾角和临界流速是管道积水预测的一个重要判定指标
计算临界倾角时应考虑稳定油包 水分散溶液中最大液滴直径,重力以及流速等因素
在给定流动条件下,存在在紊流力作用下不会破裂 的最大液滴直径,以及在重力作用下不会沉降、可以悬浮的临界液滴直径
这两个液滴直径数值相等时 的流速/倾角,被定义为油包水分散系的临界速度/倾角
将管道的实际流速/倾角同该临界速度/倾角 相比较,以确定稳定的油包水分散溶液是否会分离成为油层位于水层之上的分层流
A.2临界倾角计算过程 A.2.1最大液滴直径 根据水相在油相中的分散特性,分别通过以下两种计算流程确定稀分散系与稠分散系的最大液滴 直径,见式(A.1)(A.20) 稀分散系 在稀分散系流动条件下,水滴悬浮于连续油相中独立运动,油水间作用力占主导地位,应满足 式(A.1): pe 1一e 1 (A.l 式中: 含水率; E -油水混合物密度,单位为千克每立方米(kg/m=); pm -连续相(油)密度,单位为千克每立方米(kg/m n o. 最大液滴直径(dm)根据Brauner模型可以表示为式(A.2) /dmnx p,(l一E .a.og =1.88 we"Re" D 式中 D 管道内径,单位为米(m); we, -混合相的韦伯数,见式(A.3); 混合相的雷诺数,见式(A.4)
Rem o,DU. We
A.3 G0 pmDU A.4 Re叫 式中: U 混合相人口速度,单位为米每秒(m/s); 1
GB/T34350一2017 -油-水表面张力,单位为牛每米(N/m); 口 混合相运动黏度,单位为平方米每秒(m'/s)
Vm 尽管管流中的紊流区段不均匀且呈各向异性但经论证,当d.<0.1D时,可依式(A.2)计算 两相流系统中稀分散相的d
对于液体系统,当连续相与分散相的密度近似相等时,e<1 d计算所需参数包括流体参数和几何参数
其中,流体参数有水相流量、油水混合物密度、 姬相或油相流量;几何参数有管径和横截面积
稠分散系 b 当经相内携带的水滴未完全悬浮.且存在相互作用力时,分散系应考虑采用稠分散系方法分 析
稠分散系方法适用于任何原因导致含水率升高或油水混合物密度与油密度差别较大时
在此情况下,油相流量Q具有足以阻断水滴流量为Q.)聚结的紊流能量
在聚结水相中,表 面能量产生的速度与流动油相提供的紊流能量的生成速度成正比,见式(A.9)
表面能量的变化主要分为以下四部分,见式(A.5)(A.8): 增加的油-水界面表面能(E)为 E,= -L1口 (A.5 TD?4 Ew 失去的油-水界面表面能(Ea)为 A.6 Ea -Tdo /6 Tdl im 增加的水-钢界面表面能(E)为: E, (A.7 2o E.RD74 失去的油-钢界面表面能(E)为: A.8 E Lg口w -.(D丽 油相紊流能量等于四种表面能的变化,可得式(A.9): A.9 口4."'Q.=一E
十E
一E
十E 其中Q.和Q,分别按照式(A.10)和A.l1)计算 Q (A.10
=U、A=U.e.A (A.11 Q,=UmA=U.(1一e)A 以上各式中: 水相体积流量,单位为立方米每秒(m'/s); 油相体积流量,单位为立方米每秒(m'/s); Q. 油-水界面的宽度,单位为米(m); L 水-钢界面的圆弧长度,单位为米(m); L 油-钢界面张力,单位为牛每米(N/m);
0 水-钢界面张力,单位为牛每米(N/m).; w 紊流脉动速度,单位为米每秒(m/s); l 油层的折算速度,单位为米每秒(m/s); U U 水层的折算速度,单位为米每秒(m/s); 管道的横截面积,单位为平方米(m). 根据Young方程,见式(A.12): 12
GB/34350一2017 (A.12 =d,,com" d 一ow 式中: -油水接触角,单位为度('). 在各向同性均匀紊流中,紊流脉动速度与紊流能量耗散率e的关系为式(A.l3) o =2(ed. A.13 紊流耗散率与摩擦压降的关系为式(A.l4): AP DL APU2/U用 A.14 D pm 忐 一xD'Lpm 式中: AP -摩擦压降,单位为帕(Pa) 湍流摩阻系数; 管道长度,单位为米(m 最大液滴直径(da)用可以表示为式(A.15) s0.( ,-品-告]品监 A.15 -口.cosd 在给定的流体系统和运行条件下,可存在的最大液滴直径为通过稀分散系或稠分散系方法(A.2.1.1 和A.2.1.2)计算所得的两个值中的较大者,见式(A.l6) d ()
("). A.16 =max A.2.2临界液滴直径 通过重力和紊流力平衡,可得出重力作用导致液滴发生沉降的临界液滴直径(d),见式(A.17). 儿
" 一 F A.17 rm IApDgcosa Ap 公式中弗劳德数(Fr.)可由式(A.18)得出 U Fr A.18 Dgcosa 油水密度差可由式(A.19)得出: A.19 lAp|=lp
一p
以上各式中 管道的倾角,单位为度("); 油水密度差,单位为千克每立方米(kg/m); Ap 重力加速度,取9.81,单位为米每平方秒(m/、P) 水的密度,单位为千克每立方米(kg/m') p 湍流摩阻系数,由式(A.20)可计算
/=0.046/Re" A.20 当油相紊流强度足以维持水相最大液滴直径dm.(该尺寸应小于临界液滴直径d,即d.
GB/34350一2017 水层所占的横截面积,单位为平方米(m'); Aw 管壁上油的剪切力,单位为牛每平方米(N/m'):; T
管壁上混合物的剪切力,单位为牛每平方米(N/m'); Tm -管壁上水的剪切力,单位为牛每平方米(N/m=) 相界面的剪切力,单位为牛每平方米(N/m=) 纯水-混合物界面的剪切力,单位为牛每平方米(N/m'); 纯油-混合物界面的剪切力,单位为牛每平方米(N/m=). S 管道圆周与油相的接触长度,单位为米m) S 管道圆周与混合层的接触长度,单位为米(m); S 管道圆周与水相的接触长度,单位为米(n m; 相界面的接触周长,单位为米(m): S 纯水-混合物相界面的接触周长,单位为米(m); S 纯油-混合物相界面的接触周长,单位为米(m); Um -中间混合层的折算速度,单位为米每秒(m/s); U 人口油相折算速度,单位为米每秒(m/s); U -人口水相折算速度,单位为米每秒(m/s). wi p心P 图A.2微元柱体力学模型示意图 依据Tatel和Dukler模型,勇切应力可由Blasiustype公式估算,见式(A.24)和式(A.25) .U A.24 =f
T
ae T
=f
A.25 式中,f
和f.分别为油相和水相与管壁之间的摩阻系数,由式(A.26)和式(A.27)确定
A.26 D.U
A.27 fw=C 式中: 油的运动黏度,单位为平方米每秒m/s); -水的运动黏度,单位为平方米每秒(nm'/s); D. -油的水力直径,单位为米(m): 水的水力直径,单位为米(m): D. 油的真实速度,单位为米每秒(m/s). U
-水的真实速度,单位为来每秋(四/) U
常数C和取值为;层流时,C=l6,n=l;紊流时,C=0.046,n=0.2.
层间界面剪切力(,)可由式(A.28)得出
15
GB/T34350一2017 p(U-U.)|U-U
(A.28 r,= 式中 流速较快层的密度,单位为千克每立方米(kg/m'); 流速较快层的摩阻系数
动量平衡方程中的所有参数均可表示为界面高度的函数
因此,在油,水流速给定的条件下,对方 程求解即可得出界面高度,并计算积水量和压降
A.3补充说明 本附录主要针对输油管道内腐蚀外检测区段,依据管道运行条件(如输送介质组分,压力、温度、流 速等)选取适用的模型,计算积水临界倾角和携带水最小速度
模型主要包括四部分: a 最大液滴直径dm计算 计算在油水体系中所能存在的最大液滴尺寸,将油水体系按照稀分散系和稠分散系区别对待 1) 当水滴单独存在、悬浮于连续泾相中,视为稀分散液 22 当水滴非完全悬浮、存在明显相互作用力时,视为稠分散液
b 临界液滴直径d计算 计算在油水体系中因重力影响导致水滴发生沉降分离的临界液滴直径
积液评判 1 最大液滴直径dm小于携带水临界值da时出现油包水分散流; 最大液滴直径大于d时,水滴会在水平流动中因重力作用或在垂直流动中因变形、乳化 22 而分层分离,进而形成积液
d 临界倾角与临界流速确定 对于临界倾角的计算,使最大液滴直径d,等于携带水临界值d,将实际流速带人模型 1 中,求得管道倾角a ,该数值即计算工况下的临界倾角
对于临界流速的计算,同样使最大液滴直径d,等于携带水临界值da,而将实际管道倾 2 角带人模型中,求得实际流速,该数值即计算工况下的临界流速
分层流模型主要用于计算最大液滴直径和临界液滴直径所需的流速参数
16
GB/34350一2017 附录 B 资料性附录 润湿性测定 B.1接触角法 -液滴油)附着在浸泡于另一液体(水)中的平滑且无空隙的均质固体表面上,与固体表面形成一 个接触角
通过考虑所涉及界面的相对表面能量,可以预测钢管表面水取代胫的趋势
如果系统能量 因该作用而降低,则烽-钢界面会被水-钢界面取代
当测得的水接触角介于90"和180"之间时,宜预测姬取代水发生,为油润湿;当水接触角介于0'"和 90"之间时,宜预测水取代姬发生,为水润湿
测量接触角的方法有光学投影法,吊板法、圆简法以及washburn法
实验室测量主要步骤包括: 试件打磨(600目:; a b 将试件置于盛有燕水的烧杯中; 用注射器向水中注人油,使油黏附在试件表面 c d)测量接触角并留取影像资料
B.2扩散法 利用以不同间距放置的两个探针测得乳化液的电导率
水湿润表面由于油与钢无亲和力,会在所 有探针之间测得良好的电导率(通常1kQ2kQ);油湿润表面由于油与钢有亲和力,则探针之间测量 不到电导率;混合湿润表面则会在部分探针之间测量到电导率
17
GB/T34350一2017 附 录 资料性附录) 固体杂质积聚预测 C.1固体杂质积聚模型 C.1.1概述 应考虑管道系统运行条件,如液体石油组分、压力、温度、流量、沉积物油渣和水)等,选择适用的 模型
沉降出的固体颗粒通常所含杂质如细菌和有机氯化物)浓度较高,且杂质会紧密黏附在管道底部
通常部分固体物质的亲水性表面会携带一定量的附着水,即使无连续水相也可能引发腐蚀
因此,需对 固体材料沉积机理有所了解
固体杂质积聚应考虑连续流动分析与流动扰动两类影响因素
连续流动分析用于评估理想管道流 动条件及积聚沉淀物的敏感性;而部分管道则因流动扰动导致的内腐蚀破坏程度更高
C.1.2连续流动分析 基于混合物流速识别各类流动模式
如果流速足够快,固体颗粒会因为紊流而悬浮
当流速降低 时,密度大于流体密度的固体颗粒会沉降并聚集在管道底部,形成移动的沉积层
当作用在固体颗粒上 的总驱动力小于阻止固体颗粒运动的总阻力时,固体颗粒就会在管道底部聚集形成静止的沉积层
为确定固体是否沉积于管道底部,应计算其在沉积层中的最小速度
沉积层颗粒最小速度可由作 用在移动沉积层最底层固体颗粒上的驱动力矩和反力矩的平衡得出
通常以停留于静止沉积层上部相 邻移动沉积层且处于临界运动状态的颗粒为典型颗粒,示意图见图C.1
此时,由流体对颗粒的拖拽力 产生的驱动转矩应与由颗粒和位于移动沉积层上颗粒的浮力产生的反抗转矩应相互平衡
非均匀混合物 r" 移动沉积层 流向 静止沉积层 图c.1三层模型示意图及移动沉积与静止沉积层间界面颗粒上作用力的示意图 18
GB/34350一2017 驱动力矩为F,Lp,其中Fp为介质所施加的驱动力,Lp是驱动力作用线与转动中心图C.1中的O 点)的垂直距离
驱动力可由式(C.1)计算 C.1 Fp=0.5p.UiCnA 式中: 液相密度,单位为千克每立方米(kg/m'); n U -液相速度,单位为米每秒(m/s); -流动平面上颗粒的投影面积,单位为平方米(m'); N -颗粒阻力系数,取决于颗粒的雷诺数Re,,见式(Cc.2)~(C.4. Cp Re,=p,Un.dp/" 一0s Cp=18.5Re" 0.1Re,500 C.3 Cn=0.44500之Re,之2×10 Lp穿过A,的质心,见式(C.5): A C.5 LD= H(m警+0037 式中 颗粒与流体的相对速度,单位为米每秒(m/s); U 流体的黏度,单位为帕秒(Pas); l 固体颗粒的直径,单位为米(m)
d 反作用力矩与颗粒浮重(w,L)及施加在移动沉积层上固体颗粒的作用力相反
颗粒的浮重w,由式(C.6)得出 W,=- p)gd3 C.6 r(w" 式中: W -颗粒的浮重,单位为牛(N); -固体的密度,单位为千克每立方米(kg/m) ps 浮重作用线与转动中心o的垂直距离L可由式(C.7)得出 sm(贺十 c.7) L1=" 式中 管道倾角单位为弧度(rad). 所考虑的颗粒上其他颗粒所施加的法向力(F、)由式(C.8)得出 y一4 F、=w,Ncos=w,C -cos/B C.8 dlp 式中: N 纵向颗粒的平均数; -移动层的高度,单位为米(m) ymb 移动层的浓度比(对于立方体堆积假设为0.52)
C 法向力的作用线与转动点o的距离L由式(C.9)得出 C.9 L
=“ 尝 (层 通过驱动力矩等与反作用力矩的平衡关系式,即可得出最小沉降速度(U.),见式(c.10) coS .559(s一pL)gdsinl -十+ A BC偿- U一 (C.10 oLCD 19
GB/T34350一2017 C.1.3流动扰动的影响 由管道管件、阀门、直径变化、流向变化及注人位置等引起的流动扰动会对运行管道产生紊流变化 最易受影响的管段的此类扰动可能会影响流体输送沉积层的能力,引起固体物质沉淀,从而加速 腐蚀
最易受影响的管段特征如下 管径大(>4001 mm; -高密度石油介质(>900kg/m'); -中低流速(<1.2m/s); -可测量底部沉淀量低于0.05%) 上述管段应依据引起扰动的原因来选择直接检查位置 -阀门下游接头或最小5m范围内) 管径增大(下游接头或最小5m范围内); -过度弯曲(过度弯曲位置下游5m范围内) 加注点(加注点下游5m范围内).
c.2补充说明 由于本附录中移动沉积层高度和固体颗粒的直径变化很大,而且实际操作存在局限性,现场很难测 得,其对腐蚀的影响程度没有积水对腐蚀的影响显著,因此,本附录仅作为参考,腐蚀位置预测主要依靠 积水预测来完成 20
GB/34350一2017 附 录D 资料性附录) 输油管道内腐蚀外检测腐蚀位置预测应用举例 D.1管道基本情况 所评价管道全长302.2km,外径426mm,壁厚8mm,内径410mm,管道为X52螺旋埋弧焊钢管 输送介质为含水原油
管道的相关参数见表D.1,原油和水的物性参数见表D.2
表D.1管道相关参数 设计压力 设计温度 运行压力 运行温度 混合相人口速度 参数 MPa MPa m/s 数值 6.27 37 0.31 表D.2原油和水的物性参数 水的密度 油的密度 油相运动黏度 水相运动黏度 参数 kg/m m'/s kg/m nm'/s 841.5 988.1 5.47×10-" 数值 3.94×10-" D.2临界倾角计算 D.2.1最大液滴直径 根据水相在油相中的分散特性,分别通过以下两种计算流程确定稀分散系与稠分散系的最大液滴 例中计算临界倾角所需的参数为管道内径(D),油水混合物密度(Pw),油相体积流量(Q.),水相 直径
体积流量(Q.),重力加速度(g)和含水率(e.);其中重力加速度(g)取9.81m/s",含水率(e、)为30%
稀分散系 a 在稀分散系流动条件下,水滴悬浮于连续油相中独立运动,油水间作用力占主导地位
需满足 以下条件,见式(D.1). pm 1一E 1 (D.1 油水混合物密度如式(D.2)所示 pm=ep
十(l e)p. D.2 代人相关参数得: P.=30%×988.1十(1一30%)X841.5=885.48kg/m 885. 48 1-e-)"=(-30%)x =0.737 841.5 计算结果小于95%,不能近似等于1,所以采用稠分散系计算最大液滴直径
b 稠分散系 稠分散系方法适用于任何原因导致含水率升高或油水混合物密度与油密度差别较大时
在此 21
GB/T34350一2017 情况下,油相体积流量Q,具有足以阻断水滴(水相体积流量为Q.)聚结的紊流能量
在聚结 水相中,表面能量产生的速度与由流动油相提供的紊流能量的生成速度成正比
表面能屋的变化主要分为以下四部分,见式D.337 (D.6): 增加的油-水界面表面能(E,)为 (D.3 Em -Li口 E(rD2/4 失去的油-水界面表面能(E.)为 D.4 Ea -rd,口
rd./6 增加的水-钢界面表面能(E.)为 E D,5 -( Lg E.rD?/4 失去的油-钢界面表面能E为 E= D.6 -l口
e.rD?/4 油相紊流能量等于四种表面能的变化,见式(D.7): (D.7 -p."'Q.=一Ea十Ea一E
十E 以上各式中: -油-水界面的宽度,单位为米(m); -水-钢界面的圆弧长度,单位为米(m); 油-钢界面张力,单位为牛每米(N/m), 水-钢界面张力,单位为牛每米(N/m); ow 紊流脉动速度,单位为米每秒(m/s)
根据Young方程,见式(D.8) D.8 d
一口=口...cos 式中 油水接触角,单位为度() 在各向同性均匀紊流中,紊流脉动速度与紊流能量耗散率e的关系见式(D.9): (D.9 u'=2(ed.) 紊流耗散率与摩擦压降的关系
见式(D.10): xDL 4p 2fU. PUm D.10 P工 -DL"-是 式中 -湍流摩阻系数,无量纲,由式(D.11)计算
f=0.046/Re"3 D.11 最大液滴直径(dm)见式(D.12): "总["
-告--%品一时a 式中;L和Lg由A.2.3.2三相分层流模型计算确定,L和L取值分别为0.20338m和0.22m;a 取值为2.036×10-"N/m;0取值为120" A-03Xw.a1×于x04r Q
=UA= m'/s=0.01228m'/s 22
GB/34350一2017 -U.A07x0a1x-义0.m'/=00sGm/5 Q
=U.A =ywe
十,(1一e、)=5.47×10"×0.3十3.94×10"×(1一0.3)=4.399×10" DU 0.41×0.31 一28892.93>2000,则处于紊流状态
Re, 4.39910" 0.046 0.046 =5.897×10 0.2 28892.9303 Rem 2×0.31×5.897×10" 0.4 0.01228 4×0.20338 4×0.22 -cos120" ×2.036×10" 后-3nO示十可.3又T 84.5×0.02865 =1.258×10-m
使用Matlab计算上列方程,解得:(d)一 =(d =1.258×10-m
则dm= mnx)树 D.2.2重力的影响 计算临界倾角时应考虑稳定油包水分散溶液中最大液滴直径、重力以及流速等因索
在给定流动 条件下,存在在紊流力作用下不会破裂的最大液滴直径,及在重力作用下不会沉降、可以悬浮的最大液 滴直径
这两个液滴直径数值相等时的流速,被定义为油包水分散体的临界速度,从而推算出临界 倾角
通过重力和奈流力平衡,可得出重力作用导致液滴发生沉降的临界液滴直径dat,见式(D.13): fU d" - D.13 Fr 8 IpDgcosad 公式中弗劳德数(Fr.)可由式(D.14)得出 (D.14 Fr Dgcosar 油水密度差可由式(D.15)得出 D.15 Ao|=lp
一p
式中: -管道的倾角,单位为度("); 油水密度差,单位为千克每立方米(kg/m
A0 U." 0.31” 0.024 Frm 0.41×9.8×cosa Dg cosQ cosQ =dei,则 l maX demm 1.258×10 841.5 0.024 Frm,即 ×5.897×10了× 0.4l cosa Ap 146.6 解得cosa=0.9928,则a=6.9" 则该管道在此输量下的管道临界倾角是6.9 D.3实际倾角检测计算 将管道实际倾角和临界倾角叠加在一张图中,以便确定直接检测/检查相关位置点
海拔高度剖面 由全球卫星定位系统GPs和管道检测仪共同确定
GPS可确定具体位置和地面海拔,管道检测仪可确 定管道埋深
管道实际倾角大小可由这些数据计算得来
对于每一段,实际倾角可由式(D.16)得到: 80 AH -arcsin D.16 a 23
GB/T34350一2017 式中 管道实际倾角,单位为度("); a H 测点间的高程差,单位为米(m); 测点间的直线距离,单位为米(m). 根据现场所测高程数据绘制腐蚀管段和实际倾角剖面图
以起始点和终止点分别为283km和 285km的实际检测管段为例,管段高程剖面和实际倾角示例图见图D.1
20 200 管道高程 实际倾角 10 临界倾角 150 1100 -10 20 1050 30 000 -40 283000 283500 284000 284500 285000 距离/m 图D.1高程剖面和实际倾角示例图 D.4临界倾角与实际倾角比较 根据实际现场检测结果以及腐蚀位置预测结果知,283km一285km区段为严重腐蚀区段,图D.1 详细标识出了严重腐蚀区段的实际倾角值大于临界倾角值的位置点
表D.3列出了该区段具体的定性 检测结果
表D.3示例-检测结果 检测区段 位置/km 倾角/(" 是否腐蚀 检测序号 283km一285km 是 283.50 9,88 283km285 283.52 10.99 km 283km285km 283.56 7.37 是 283km~285km 283,88 11.29 283ktm一285km1 是 283.88 1l.12 283km285km 283,.92 7.67 否 283km~285km 284.22 10.97 否 24
GB/34350一2017 D.5实测理论对比分析 在上述所测严重腐蚀区段,实际倾角数据如图D.1所示,临界倾角线是6.9"的虚线
本例中,超过 临界倾角的部位与实际检测的腐蚀部位做了对比如表D.3所示
管道沿线大于此角的位置是积液发生 最有可能的位置,也是该管线运行的危险位置,应重点加大检测比例,而表中大于6.9°的个别位置未发 生严重腐蚀是由于为了保证尽可能地不遗漏易发生腐蚀的点,临界倾角计算模型中对临界倾角的取值 较保守,因此个别预测位置未出现严重腐蚀,但是这样可保证发生腐蚀的点都在预测的位置范围内
根据高程检测及流场分析结果,管线高程变化出现“V”字形变化的区段更容易出现腐蚀,应将高程 相对低洼点和顺流向上坡部位作为重点部分进行开挖检测
25
GB/T34350一2017 参 考 文献 [1]NACEsP0208一2008InternalCorrosionDirectAssessment MethodologyforLiquidPe- troleumPipelines. 26
输油管道内腐蚀外检测方法GB/T34350-2017
随着我国经济的快速发展,能源行业的需求量在不断增加。而输油管道作为重要的供应途径,其使用安全问题日益成为人们关注的焦点。然而在管道运行过程中,由于各种原因,如介质腐蚀、机械损伤等,都可能导致管道内部腐蚀,进而对输送介质造成直接或间接危害。因此,对输油管道进行内部腐蚀外检测至关重要。
一、GB/T34350-2017标准介绍
GB/T34350-2017标准是我国输油管道内腐蚀外检测的重要标准之一。该标准规定了输油管道内腐蚀外检测的技术要求、试验方法和评定规则,适用于输油管道内腐蚀外检测。
二、常用的外检测方法及其原理、优缺点
目前,常用的输油管道内腐蚀外检测方法主要包括磁粉探伤法、超声波探伤法和射线探伤法等。下面就这几种方法分别进行介绍:
1. 磁粉探伤法
磁粉探伤法是一种基于电磁感应原理的无损检测技术。该技术利用电磁铁产生的磁场,在被测材料表面撒布磁粉,通过观察磁粉在材料表面的分布情况,判断出材料表面是否存在裂纹、变形等缺陷。
该方法的优点在于能够对不易被发现的微小缺陷进行检测,同时操作简单,检测效率高。但是由于该方法只能检测到材料表面的缺陷,对于深部缺陷无法检测,因此需要结合其他技术进行综合检测。
2. 超声波探伤法
超声波探伤法是一种基于声波的无损检测技术。该技术利用超声波在材料内部传播的特性,通过反射和衍射现象来检测材料内部缺陷。
该方法具有灵敏度高、能够检测到深部缺陷等优点,同时对于不同材料也具有较好的适应性。但是,由于该方法受到材料密度、孔隙度等因素影响比较大,因此需要在实际应用中根据具体情况进行调整。
3. 射线探伤法
射线探伤法是一种基于射线的无损检测技术。该技术利用射线在材料中的穿透性,通过对射线穿过材料后被接收器测量到的强度进行分析,来检测出材料内部的缺陷和异物等。
该方法具有灵敏度高、能够检测到深部缺陷等优点,同时可以对材料进行整体检测。但是由于射线辐射对人体健康有一定危害,因此需要采取相应的防护措施。
三、适用范围
根据GB/T34350-2017标准规定,输油管道内腐蚀外检测方法适用于以下情况:
- 输油管道运行时间超过5年,或者输送介质发生了重大变化;
- 输油管道出现泄漏或者其他异常情况;
- 输油管道经过装修或改造,需要重新检测。
四、结论
综上所述,针对输油管道内部腐蚀的问题,GB/T34350-2017标准提供了一系列的外检测方法。在实际应用中,需要根据具体情况选择合适的方法进行综合检测,以确保输油管道的安全运行。
输油管道内腐蚀外检测方法的相关资料
- 输油管道内腐蚀外检测方法GB/T34350-2017
- 输油管道环境风险评估与防控技术指南GB/T38076-2019解读
- 输油管道内腐蚀外检测方法GB/T34350-2017
- 输气管道内腐蚀外检测方法GB/T34349-2017详解
- 钢质管道内腐蚀控制规范GB/T23258-2020解析
- 塑料薄膜和薄片水蒸气透过率的测定红外检测器法GB/T26253-2010
- 化妆品中维生素B5的测定方法
- 使用γ干扰素法GB/T32945-2016进行牛结核病诊断体外检测
- 牛结核病诊断体外检测γ干扰素法GB/T32945-2016
- 输油管道内腐蚀外检测方法GB/T34350-2017
- 输油管道内腐蚀外检测方法GB/T34350-2017