GB/T32958-2016
流体输送用不锈钢复合钢管
Stainlesssteelcladpipesforfluidtransport
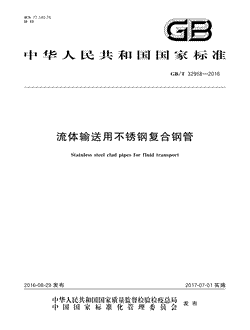
- 中国标准分类号(CCS)H48
- 国际标准分类号(ICS)77.140.75
- 实施日期2017-07-01
- 文件格式PDF
- 文本页数23页
- 文件大小688.24KB
以图片形式预览流体输送用不锈钢复合钢管
流体输送用不锈钢复合钢管
国家标准 GB/T32958一2016 流体输送用不锈钢复合钢管 Stainlesssteeleladpipesforfuidtransport 2016-08-29发布 2017-07-01实施 国家质量监督检验检疫总局 发布 国家标准化管理委员会国家标准
GB/T32958一2016 前 言 本标准按照GB/T1.1一2009给出的规则起草 本标准由钢铁工业协会提出
本标准由全国钢标准化技术委员会(SAC/TC183)归口
本标准起草单位:浙江金洲管道工业有限公司、云南昆钢新型复合材料开发有限公司、江苏武进不 锈股份有限公司、江苏众信绿色管业科技有限公司、绍兴市水联管业有限公司、浙江德威不锈钢管业制 造有限公司、山西太钢不锈钢钢管有限公司
本标准主要起草人:沈沧荣、杨伟芳、杜顺林、宋建新、孟宪虎、冯志琴、沈根荣、陆风辉、张淮、 刘尚华
GB/I32958一2016 流体输送用不锈钢复合钢管 范围 本标准规定了流体输送用不锈钢复合解管的订货内容.尺寸,外形,重量及允许偏差,技术要求.试 验方法、检验规则包装、标识和质量证明书
本标准适用于一般流体和化工弱腐蚀环境流体饷送用的以不锈钢为复层,碳钢或低合金钢为基层 的内覆或衬里复合钢管(以下简称复合钢管. 规范性引用文件 下列文件对于本文件的应用是必不可少的
凡是注日期的引用文件,仅注日期的版本适用于本文 件
凡是不注日期的引用文件,其最新版本(包括所有的修改单)适用于本文件 钢的成品化学成分允许偏差 GB/T222 GB/T223.3钢铁及合金化学分析方法二安替比林甲烧磷钼酸重量法测定磷量 GB/T223.5钢铁酸溶硅和全硅含量的测定还原型硅钼酸盐分光光度法 GB/T223.11 钢铁及合金铬含量的测定可视滴定或电位滴定法 GB/T223.12钢铁及合金化学分析方法碳酸钠分离-二苯碳酰二耕光度法测定铬量 钢铁及合金化学分析方法钮试剂萃取光度法测定饥含量 GB/T223. GB/T223
钢铁及合金化学分析方法变色酸光度法测定钛量 钢铁及合金化学分析方法碗代硫酸钠分离-秧量法测定铜量 GB/T223.18 GB/T223 钢铁及合金化学分析方法新亚铜灵-三氯甲炕萃取光度法测定铜量 223.23钢铁及合金镍含量的测定 丁 二酮肪分光光度法 GB GB/T 钢铁及合金化学分析方法丁二酮厉重量法测定镍量 223.26钢铁及合金钼含量的测定硫氧酸盐分光光度法 GB GB/T223.28钢铁及合金化学分析方法a-安息香厉重量法测定钼量 GB/T223.32钢铁及合金化学分析方法次磷酸钠还原-碘量法测定呻量 钢铁及合金化学分析方法蒸分离-中和滴定法测定氮量 GB/T 223.37钢铁及合金化学分析方法燕僧分离-惋酚蓝光度法测定氮量 223.40钢铁及合金钯含量的测定氯瞒酚s分光光度法 GB GB/T223.58钢铁及合金化学分析方法亚呻酸钠-亚硝酸钠滴定法测定孟量 GB/T223.59钢铁及合金磷含量的测定泌磷钼蓝分光光度法和锄磷钼蓝分光光度法 GB/T223.60钢铁及合金化学分析方法高氯酸脱水重量法测定硅含量 GB/T223.61钢铁及合金化学分析方法磷钼酸铵容量法测定磷量 GB/T223.62钢铁及合金化学分析方法乙酸丁酯萃取光度法测定磷量 GB/T223.63钢铁及合金化学分析方法高碘酸钠(钾)光度法测定量 GB/T223.64钢铁及合金钰含量的测定火焰原子吸收光谱法 GB/T223.67 钢铁及合金硫含量的测定次甲基蓝分光光度法
GB/T32958一2016 GB/T223.68钢铁及合金化学分析方法管式炉内燃烧后碘酸钾滴定法测定硫含量 GB/T223.69钢铁及合金碳含量的测定管式炉内燃烧后气体容量法 GB/T223.71钢铁及合金化学分析方法管式炉内燃烧后重量法测定碳含量 GB/T223.72钢铁及合金硫含量的测定重量达 GB/T223.84钢铁及合金钛含量的测定二安替比林甲婉分光光度法 GB/T223.85钢铁及合金硫含量的测定感应炉燃烧后红外吸收法 GB/T223.86钢铁及合金总碳含量的测定感应炉燃烧后红外吸收法 GB/T226钢的低倍组织及缺陷酸蚀检验法 金属材料拉伸试验第1部分;室温试验方法 GB/T228.1 GB/T229 金属材料夏比摆锤冲击试验方法 GB/T241 金属管液压试验方法 金属管压扁试验方法 GB/T246 GB/T699一2015优质碳素结构钢 GB/T700-2006碳素结构钢 GB/T983不锈钢焊条 GB/T1591一2008低合金高强度结构钢 GB/T2102 钢管的验收、包装、标志和质量证明书 GB/T265o焊接接头冲击试验方法 GB/T2651焊接接头拉伸试验方法 GB/T2653焊接接头弯曲试验方法 钢及钢产品力学性能试验取样位置及试样制备 GB/T2975 GB/T3091低压流体输送用焊接钢管 GB/T4241焊接用不锈钢盘条 GB/T4334一2008金属和合金的腐蚀不锈钢晶间腐蚀试验方法 碳素钢和中低合金钢火花源原子发射光谱分析方法(常规法 GB/T4336 GB/T5117非合金钢及细晶粒钢焊条 5118热强钢焊条 GB GB/T5293埋弧焊用碳钢焊丝和焊剂 GB/T6396复合钢板力学及工艺性能试验方法 气体保护电弧焊用碳钢、低合金钢悍丝 GB/T81l0 GB/T8163输送流体用无缝钢管 不锈钢复合钢板和钢带 GB/T8165 GB/T9711一2011石油天然气工业管线输送系统用钢管 GB/T11170不锈钢多元素含量的测定火花放电原子发射光谱法(常规法) GB/T12470埋弧焊用低合金钢焊丝和焊剂 GB/T12771流体输送用不锈钢焊接钢管 直缝电焊钢管 GB/T13793 GB/T14957熔化焊用钢丝 GB/T14976流体输送用不锈钢无缝钢管 GB/T16957复合钢板焊接接头力学性能试验方法
GB/T32958一2016 GB/T17219生活饮用水输配水设备及防护材料的安全性评价标准 GB/T17395无缝钢管尺寸,外形、重量及允许偏差 GB/T17854埋狐焊用不锈钢焊丝和焊剂 GB/T20066 钢和铁化学成分测定用试样的取样和制样方法 GB/20123 钢铁总碳硫含量的测定高频感应炉燃烧后红外吸收法(常规方法 GB/T20124 钢铁氮含量的测定惰性气体熔融热导法(常规方法 奥氏体-铁素体型双相不锈钢媒接钢管 GB/T21832 GB/T21833奥氏体-铁素体型双相不锈钢无缝钢管 GB/T21835焊接钢管尺寸及单位长度重量 NB/T47013.2一2015承压设备无损检测第2部分;射线检测 NB/T47013.5一2015承压设备无损检测第5部分;渗透检测 sY/T6423.1一2013石油天然气工业钢管无损检测方法第1部分;焊接钢管焊缝缺欠的射 线检测 sY/T6423.2一2013石油天然气工业钢管无损检测方法第2部分;焊接钢管焊缝纵向和/或 横向缺欠的自动超声检测 YB/T4204供水用不锈钢焊接钢管 压力容器用热轧不锈钢复合钢板 YB/T4282 YB/T5092焊接用不锈钢丝 订货内容 按本标准订货的合同或订单应至少包括下列内容 a)本标准编号, b)产品名称 牌号;基层牌号十复层牌号; 尺寸规格:外径×总壁厚(基层壁厚十复层壁厚),单位为毫米; 订购的数量总重量或总长度); 制造要求(成型方法,焊接工艺,复合方式) g交货状态 用途; h 其他特殊要求
尺寸,外形、重量及允许偏差 4.1外径和壁厚 复合钢管的外径(D)应为21.anm 1626mm,总壁厚()不小于2.8mm,复层厚度()应不小于 各种制造工艺的钢管外径,壁厚应符合表1的规定,其具体尺寸规格应符合GBy/T17395或 0.25mm
GB/T21835的规定
根据需方要求,经供需双方协商,可供应GB/21835或GB/T17395规定以外 规格的复合钢管
GB/T32958一2016 表1各种制造工艺复合钢管外径、壁厚范围 单位为毫米 总壁厚(G) 复层壁厚( 外径范围(D 制造工艺 不小于 不小于 复层厚度不小于复合管总壁 总要求 厚的8%,且不小于0.25mm(炸 2.8 21.31626 接连接时不小于0.5mm 衬里复合钢管 21.31422 2.8 0.25 螺旋缝埋弧(SAwH 219.11626 3.0 0,50 内覆 406.41626 6.4 直缝埋弧媒(SAWL 1.00 复合 直缝高频(HFW 219.1711 2.8 0.50 钢管 热压熔合,堆媒,离心铸造等 21.31422 2.8 0,25 4.2外径和壁厚的允许偏差 复合钢管的外径和壁厚允许偏差应符合表2的规定
根据需方要求,经供需双方协商并在合同中 注明,可供应表2规定以外允许偏差的复合钢管
表2外径和壁厚允许偏差 单位为毫米 外径允许偏差 壁厚允许偏差" 公称外径(D) 管体 复层厚度(G 管端 总壁厚( 十0.4 21.3<60.3 -0.8 +1.6 >60.3~168.3 士0.75%D 一0.4 -10%1, 士0.75%D 士0.5%D. 士9%t >168.3一610 正公差不限 但最大为士3.2 但最大为士1.6 士0.5%D >6101422 士1.6 但最大为士4.0 协议 协议 422 壁厚正偏差不适用于焊缝
管端包括钢管每个端头100mm长度范围内的钢管
无缝钢管作为基管时,总壁厚允许偏差士12.5%1
4.3不圆度 4.3.1管端不圆度 管端不圆度应不超过公称外径的1%,且最大不超过5mm;D/>75或外径不小于1016mm复 合钢管的管端不圆度由供需双方协商确定
GB/T32958一2016 4.3.2管体不圆度 管体不圆度应不超过公称外径的1.5%,且最大不超过10mm;D/>75或外径不小于1016mm 复合钢管的管体不圆度由供需双方协商确定
4.3.3内径不圆度 当复合钢管采用焊接连接时,其内径不圆度应不大于公称外径的0.5%,且不超过2" mm
4.4弯曲度 复合钢管全长弯曲度应不大于复合钢管总长度的0.2%
4.4.1 根据需方要求,经供需双方协商并在合同中注明,可规定其他弯曲度指标 4.4.2 4.5长度 4.5.1通常长度 复合钢管的通常长度为3000 mm12000mm
4.5.2定尺长度 根据需方要求,经供需双方协商,并在合同中注明,复合钢管可以定尺长度交货
定尺交货时,定尺 长度允许偏差为+”mm. 4.6管端 4.6.1管端切斜 复合钢管的两端面应与轴线垂直切割,切口毛刺应予清除
管端切斜应不大于1.6mm,如图1 所示
复层 管端 基层 管塑切斜 图1管端切斜示意图 4.6.2坡口 除另有协议规定外,外径不小于60.3mm且以焊接方式对接的复合钢管应机械加工坡口
坡口角 度,钝边尺寸由供需双方协商确定
4.6.3封焊和堆焊 4.6.3.1以焊接连接的衬里复合钢管管端的复层与基层间应进行封焊或堆焊(基层为镀锌钢管除外)
4.6.3.2如采用堆焊,钢管轴向的缝宽度应不小于钢管壁厚的两倍,且不小于25 mm
GB/T32958一2016 4.7 重量 4.7.1复合钢管按理论重量交货,也可按实际重量交货
4.7.2复合钢管的理论重量按附录A计算
4.7.3以理论重量交货的复合钢管,每批或单根复合钢管的实际重量与理论重量的允许偏差为 士7.5%
技术要求 5.1 原材料 5.1.1基层材料 5.1.1.1基层的牌号和化学成分应分别符合GB/T699一2015中10.20或GBy/T700一2006中Q195、 Q215A、Q215B、Q235A、Q235B、Q235C、Q275A、Q275B或GB/T15912008中Q345A、Q345B的 规定
5.1.1.2根据需方要求,经供需双方协商,并在合同中注明,可供应其他基层牌号和/或化学成分的复合 钢管
5.1.1.3化学成分应按熔炼成分验收
当需方要求进行成品分析时,应在合同中注明,成品化学成分的 允许偏差应符合GB/T222的规定 5.1.1.4用于衬里、,热压熔合(旋压或挤压)内覆复合的基层材料选用直缝高频电焊钢管时,复合前基层 钢管应分别符合GB/T3091.,GB/T13793或GB/T9711的规定,钢管应去除内毛刺,内毛刺残留高度 应不大于0.2nmm;选用无缝钢管时,复合前基层钢管应分别符合GB/T8163或GB/T9711的规定
复合前应进行表面预处理,去除基层钢管内表面的铁锈、毛刺和污垢
根据需方要求,经供需双方协议,并在合同中注明,可采用其他符合相关标准的钢管作为基层钢管
5.1.2复层材料 5.1.2.1复层材料的牌号和化学成分(熔炼分析)应符合表3的规定
根据需方要求,经供需双方协商, 并在合同中注明,可供应复层为其他不锈钢牌号和化学成分的复合钢管
5.1.2.2化学成分按熔炼成分验收
当需方要求进行成品分析时,应在合同中注明,成品化学成分的允 许偏差应符合GB/T222的有关规定
5.1.2.3除外形尺寸外,用于衬里、热压熔合旋压或挤压)内覆的复层钢管复合前应分别符合 GB/T12771,GB/T14976,GB/T21832,GB/T21833或YB/T4204的规定
根据需方要求,,经供需 双方协议,并在合同中注明,可采用其他符合相关标准的钢管作为复层钢管
5.1.3复合板(卷 采用经轧制或爆炸方法生产的复合板卷)作为制管原材料时,复合板(卷)应符合GB/T8165或 YB/T4282的规定
5.1.4焊材 用于基层焊接的焊丝、焊剂应分别符合GB/T5293,GB/T8110,GB/T12470或GB/T14957的规 定,焊条应符合GB/T5117或GB/T5118的规定
用于复层焊接的焊丝、焊剂应分别符合GB/T4241、GB/T17854或YB/T5092的规定,焊条应符 合GB/T983的规定
GB/T32958一2016 包 2 三 n A 撤 案 出 邱 p Gc 性
GB/T32958一2016 5.2 制造方法 5.2.1 内覆复合 内覆复合钢管的制造方法如下 a 采用复合板(卷)为原料,通过钢管成型和采用熔化极气体保护电弧焊(GMAw)钨极惰性气 体保护焊(GTAw),等离子弧焊(PAw),焊条电弧焊(SMAw),HFw,SAwH、sAw的一种 或多种组合焊接方法制造
内衬复层通过热压熔合(旋压或挤压)与基层钢管形成冶金结合的方法制造
b 在基层俐管内表面采取堆媒和离心铸造等工艺使复层与基层钢管形成冶金结合的方法制造
c 5.2.2衬里复合 复层钢管嵌人基层钢管内,通过水压,旋压或缩径,冷拔等工艺使复层与基层形成机械结合的方法 制造
5.3冷定径和冷扩径 5.3.1除基层在定径后整体进行正火、淬火,回火或消除应力热处理外,基层的定径率应不超过1.5%
5.3.2如未进行后续热处理或去应力热处理的冷定径或冷扩径钢管用作基层,除非另有协议,基层在 各制造环节中的总形变率应不超过2%
5.3.3扩径或定径率D,应采用式(1)计算 D.-DL D= D 式中: 指供方设计的扩径/定径后外径,单位为毫米(mm); D. D -指供方设计的扩径/定径前外径,单位为毫米(mm); 指外径差的绝对值,单位为毫米(mm). ID.一Dl 5.4 交货状态 5.4.1采用复合板(卷)成型焊接的复合钢管按焊接或热处理状态交货;其余类型钢管可在复合前分别 对基层和复层材料进行热处理,复合后不要求进行热处理
5.4.2根据需方要求,经供需双方协商,并在合同中注明,复合钢管的复层也可经磨(抛)光或酸洗后 交货
5.4.3根据需方要求可对复合钢管外表面涂层.涂层要求由供需双方协商规定 5.5力学性能 5.5.1总则 复合钢管基层的力学性能应符合表4的规定,可采用基层或包括复层在内的全壁厚试验试样
当 采用全壁厚试样时,可参照附录B计算对应的屈服强度和抗拉强度标准值
采用衬里、热压熔合(旋压或挤压),离心铸造的复合钢管力学性能试验应在复合以前进行
GB/T32958一2016 表4复合钢管的力学性能 断后伸长率A/% 下屈服强度" 抗拉强度 R/MPa Rm/MPa 基层材料 D168.3mm D>168.3mm 不小于 195 315 22 235 390 19 20 Q195 195'" 315 15 20 Q215A、Q215B 215 335 15 20 Q235A.Q235B 235 370 15 20 18 Q275A,Q275B 275 410o 13 13 18 Q345A,Q345B 345 470 屈服现象不明显时,按R Rm.2" Q195的屈服强度值仅供参考,不作交货条件
5.5.2拉伸 5.5.2.1复合钢管管体拉伸试验应测定屈服强度、抗拉强度、断后伸长率
煤接接头拉伸试验只测定抗 拉强度,其值应符合表4的规定
当采用全壁厚试样时,如断后伸长率不合格,允许剖去复层仅对基层 进行拉伸试验,其断后伸长率应不小于基层标准值
5.5.2.2外径不小于219.1mm的复合钢管拉伸试验应截取管体横向试样和焊缝试样
采用SAwL、 HFw工艺的复合钢管管体拉伸试样应在复合钢管上距焊缝180°的位置截取,SAwH钢管管体拉伸试 样应在复合钢管上距螺旋焊缝至少1/4个板宽位置处截取
焊缝(包括SAwL,HFw钢管的焊缝 SAwH钢管螺旋焊缝以及钢带对接焊缝)拉伸试样应在复合钢管上垂直于焊缝截取,且焊缝位于试样 的中间
外径小于219.1nmm的复合管管体应取纵向试样,或选择使用钢管全截面纵向试样
5.5.3冲击试验 根据需方要求,经供需双方协商,并在合同中注明,对质量等级为B级、基层壁厚不小于6mm且能 制取10mm×5mm×55mm及以上尺寸冲击试验试样时,基层的管体,焊缝及热影响区可做冲击试 验,焊缝及热影响区的冲击吸收能量KV,应符合基层对应厚度材料的规定
衬里复合钢管基层管体、 焊缝及热影响区冲击试验可在复合以前进行
5.5.4硬度试验 根据需方要求,经供需双方协商并在合同中注明,复合钢管可按GB/T16957规定进行硬度试验
取样方法、硬度指标由供需双方协商确定
5.5.5复合界面结合强度或夹持力试验 内覆复合斜管应进行复合界面结合强度试验,其值应不小于10MPa
试验试样的截取按 5.5.5.1 5.5.2规定截取管体试样并压平
经供需双方协商,并在合同中注明,可用压扁试验代替结合强度试验
压扁试验复层与基层结合面分离或开裂长度的验收条件由供需双方协商确定
5.5.5.2衬里复合钢管应按附录C规定测量复层和基层之间夹持力,其值符合表5的规定
GB/T32958一2016 表5衬里复合钢管的夹持力 塌陷试验后夹持力/kN 夹持力/kN 外径(D/mm1 不小于 <114.3 30 15 50 >114.3<219.l 25 >219.1<323,9 70 35 >323,.9 供需双方协商确定 5.5.6塌陷试验 5.5.6.1根据需方要求,经供需双方协商,并在合同中注明,衬里复合钢管完成管端堆焊或封焊后可进 行塌陷试验
整根复合钢管加热到240,恒温15min后,对衬里复合钢管进行内窥镜检查,应无鼓 包、波痕,弯曲和裂纹 5.5.6.2衬里复合钢管塌陷试验后,应在塌陷试验后的管子上截取试样,按附录c的规定测量复层和 基层之间夹持力,结果符合表5的规定
5.6工艺性能 5.6.1压扁试验 基层钢管为无缝钢管、HFw钢管的内覆或衬里复合钢管应进行压扁试验
对无填充金属的焊接 钢管,由制造厂选择,可用导向弯曲试验代替压扁试验
将长度不小于63.5mm的管段放置在两平行 压板之间.焊缝与载荷方向垂直,分两步进行压扁试验
第一步,延性试验
将试样压至两平板间距离为H,试样的内、外表面以及边缘不允许出现裂纹、 断裂和复层剥离(衬里复合钢管除外)
H应按式(2)计算 l.09 H= 0.09十 式中: -两平板间的距离,单位为毫米(mm); 钢管的总壁厚,单位为毫米(mm); D -钢管的外径,单位为毫米(mm) 第二步,完整性(闭合压扁)试验
继续压扁直至试样断裂或两管壁贴合
在第二步的压扁试验中
除衬里复合钢管外,不允许出现复层和基层的剥离现象
5.6.2焊缝导向弯曲试验 对有填充金属的焊接复合钢管应进行室温导向弯曲试验
由制造厂选择,可对无填充金属的焊接 复合钢管进行导向弯曲试验
试验应参照5.5.2规定截取管体焊缝和钢带对头焊缝弯曲试样,衬里复 合钢管可去除复层,内覆复合管应保留复层,弯曲试样的焊缝位于试样中间,试样上不应有补焊焊缝,焊 缝余高应去除
试样在弯模内弯曲约180",弯芯直径为总壁厚的8倍,其中一个为焊缝正面弯曲,另 个焊缝背面弯曲
试验后,应符合如下规定: 试样不允许完全断裂; a b试样上焊缝金属中不允许出现长度超过3.2mm的裂纹或破裂,不考虑深度; 10o
GB/T32958一2016 基层,复层,热影响区或熔合线上不允许出现长度超过3.2mm的裂纹或超过壁厚10%的裂纹 或破裂 试验过程中,出现在试样边缘且长度小于6.4mm的裂纹和结合面裂纹,不应作为拒收的依据
5.6.3液压试验 内覆复合锅管应逐根进行液压试验
试验压力拨式(s)计算,修约到最邻近的01MPa,最大试验 压力为5.0MPa
试验压力保持时间应不少于10s,在试验过程中,复合钢管不允许出现渗漏现象
p2IR (3 D 式中: -试验压力值,单位为兆帕(MPa); -复合钢管的总壁厚,单位为毫米(mm); 允许应力,5.5.1规定屈服强度的60%,单位为兆帕(MPa); R -复合钢管的外径,单位为毫米(n mm 基层钢管按相应标准要求进行了液压试验,复合钢管可不再进行液压试验 5.6.4晶间腐蚀试验 根据需方要求,经供需双方协商并在合同中注明,复合钢管的复层,复层焊缝可做晶间腐蚀试验
晶间腐蚀试样宜采用热固性丙烯酸树脂镶嵌,镶嵌后试样仅露出复层,复层焊缝表面;或在试样基层,基 层焊缝表面涂抹一层耐高温环氧树脂,试验方法应符合GB/T434一2008中方法E的规定或按合同规 定采用其他耐腐蚀试验方法,试验后试样不允许出现晶间腐蚀倾向
无损检测 5.7 5.7.1内覆复合钢管 5.7.1.1内覆复合焊接钢管应按sY/T6423.1一2013或NB/T47013.22015的规定进行射线检测, 或按照sY/T6423.2一2013的规定进行超声波检测,或经供需双方协商确定的其他检测方法和验收标 准进行焊缝全长检测
手工或自动超声检测前应采用超声波方法检测焊缝两侧50mm区域的未结合 缺欠,对未结合缺欠应予记录
5.7.1.2采用射线检验法对焊缝的均匀性进行检测
X射线直接透过焊缝材料,在射线检验的胶片上 产生适合的影像,或者在证实具有要求的灵敏度条件下,在其他X射线成像介质上产生适合的影像
图像质量级别分别达到sY/T6423.1一2013规定的A级或NB/T47013.2一2015规定的AB级
射线 检验合格判定按sY/T6423.1一2013或NB/T47013.2一2015执行,其中NB/T47013.2一2015按质量 等级】级验收 5.7.1.3热压熔合(旋压或挤压)内覆的复合钢管,应使用超声波纵波对基层与复层的未结合缺欠进行 检测,结果满足GB/T9711-20附录E或满足相应的钢管检验验收标准的要求
如果钢管进行热处 理和扩径,则无损检测应在所有热处理和扩径后进行,但可以选择在切头、平端和定径之前进行
5.7.1.4内覆复合钢管管端100mm应进行超声波检测,不允许存在超过6.4mm的未结合缺欠
5.7.2衬里复合钢管 5.7.2.1封焊和堆焊焊缝应进行目视检测,并按NB/T47013.5一2015的要求进行着色渗透检查,渗透 检查验收等级应不低于I级
5.7.2.2每工作班应抽取一根,以及生产工艺参数调整后前10根钢管以及随后20根钢管中应各抽取 -根,对封焊或堆焊焊缝进行全长X射线拍片检测
经协商,也可采用超声检测替代X射线拍片检测 1l
GB/T32958一2016 判定规则与验收要求由供需双方协商确定
5.7.2.3如检测发现任一封焊或堆焊焊缝不合格,则随后生产的钢管应逐根检测,直至连续20根钢管 全部合格,此前生产的20根钢管也应逐根检测
5.8表面质量 5.8.1基本要求 复合钢管的内外表面应光滑,不允许有折叠、裂纹、结疤、扭曲、气泡、断弧及其他深度超过总壁厚或 复层壁厚允许偏差的缺陷存在
允许有深度不超过总壁厚或复层壁厚下偏差的轻微麻点、轻微划伤,凹 坑和辐印等局部缺欠存在
对于衬里复合钢管,基层与复层结合面的复合前的处理、基层焊接钢管焊缝余高由双方协商约定
5.8.2咬边 埋弧焊钢管上的咬边应按照下列规定进行核查、分类和处置 深度0.4mm应接收(不考虑咬边长度. a 深度>0.4 且<0.8mm咬边,只要同时满足以下条件应接收 b mm 单个长度<0.5t; 单个深度<0.1t; 在任意300mm长度的焊缝上,这样的咬边不多于两个
所有超过b)规定的咬边应判为缺陷,应切除或整管拒收
c 5.8.3电弧烧伤 5.8.3.1电弧烧伤应判为缺陷 5.8.3.2电弧烧伤应修磨清除、切除或整管拒收;当修磨清除缺陷后,应采用10%过硫酸铵溶液或5% 的硝酸乙醇腐蚀液检查损伤材料是否已经完全清除
5.8.4内覆复合钢管的钢带(卷)对头焊缝 5.8.4.1SAwL和HFw钢管上不应有钢带/钢板对头焊缝
5.8.4.2sAwH钢管允许有钢带对头焊缝,但钢带对头焊缝与螺旋焊缝的连接点距管端的距离应大于 150mm,当钢带对头焊缝位于管端时,与相应管端的螺旋焊缝之间至少应有150mm的环向间隔
对 头焊缝应采用以下方法焊接和检验 a)采用SMAw或SMAw与GTAw组合焊接方法焊接; b 采用与螺旋媒缝相同的验收极限进行检验
5.8.5几何尺寸偏离 5.8.5.1除摔坑外,由于钢管成型工艺或制造操作而造成钢管实际轮廓相对于钢管正常圆柱轮廓的几儿 何尺寸偏离(如扁平块或撅嘴等),其极端点与钢管正常轮廓延伸部分之间的间距超过3.2mm应判为 缺陷
超过上述规定的缺陷应切除或拒收
5.8.5.2摔坑在任何方向上的长度应不大于0.5D,且深度应不超过下列规定 冷态成型并带有尖底划伤的摔坑,深度3.2" a mm; b其他摔坑,深度6.4mm. 超过规定极限值的摔坑应判为缺陷,应切除或拒收
12
GB/T32958一2016 5.8.6其他表面缺欠 外观检查发现的其他表面缺欠应按下列方法核查、分类和处置 深度不大于1/8.且不影响最小允许壁厚的缺欠,应判为可接受的缺欠 a b)深度大于1/8,且不影响最小允许壁厚的缺欠,应判为缺欠,并应采用磨削法修磨清除; 剩余壁厚小于最小允许壁厚的缺欠应归为缺陷,应切除或整管拒收
c 5.8.7焊缝高度 5.8.7.1内外焊缝应完全媒透和熔合,基层为埋弧焊钢管的复合钢管,焊缝高度应符合表6的规定
表6埋弧焊允许悍缝高度 单位为毫米 媒缝高度最大值 基层厚度! 内焊缝 外焊缝 S13.0 3.5 3.5 >l3.0 3.5 4.5 5.8.7.2距管端100mm范围内,内焊缝应磨平,剩余高度应控制在0mm0.5mm(焊缝的磨平部位 需用与复层材料相匹配的焊丝并采用GTAw堆煤一层盖面焊缝,盖面焊缝厚度不小于复层公称厚度 的90%,此处剩余高度不受0mm~0.5mm规定限制)
5.8.7.3复合钢管的内外焊缝与邻近钢管表面平滑过渡,除咬边处外,熔敷的内外焊缝顶部应不低于邻 近钢管表面
5.8.7.4当复合钢管总壁厚不大于15mm时,焊缝处钢带边缘的径向错边应不大于1.5mm;当复合钢 管总壁厚大于15mm时,焊缝处钢带边缘的径向错边最大值为总壁厚的0.1倍,且不允许超过2.5 mm
当复合钢管总壁厚不大于20mm时,焊缝最大焊偏量应不超过3 5.8.7.5 ,当复合钢管总壁厚大于 mm, 20mm时,烬缝最大媒偏量应不超过4 mm 内覆复合钢管缺陷的修补 5.9 缺陷的修补应符合如下规定 a)基层管体不允许进行焊接修补 b 经供需双方协商,可对复层的缺陷进行修复; c 基层钢管管端200mm范围内焊缝不允许进行焊接修补,其余焊缝可修补;管端200mm范围 内焊缝如需进行焊接修补,应得到需方同意
5.10卫生性能 用于生活饮用水输送的复合钢管,其卫生性能评价按GB/T17219的规定执行
5.11特殊要求 根据需方要求,经供需双方协商,并在合同中注明,复合钢管可增加复合界面结合强度或夹持力试 验频次,提高液压试验压力值等要求
试验方法 钢管的化学成分分析取样按GB/T20066的规则进行
化学成分的光谱分析方法按GB/T4336 13
GB/T32958一2016 和GB/T11170的规定进行,化学成分的化学分析方法按GB/T223.3.GB/T223.5,GB/T223.11 GB/T223.12,GB/T223.14,GB/T223.16,GB/T223.18,GB/T223.19,GB/T223.23,GB/T223..25 GB/T223.26,GB/T223.28,GB/T223.32,GB/T223.36,G;B/T223.37,GB/T223.40,GB/T223.58 GB/T223.59,GB/T223.60,GB/T223.61,GB/T223.62,GB/T223.63,GB/T223.64,GB/T223.67、 .GB/T223.84,GB/T223.85.GB/T223.86 GB/T223.68,GB/T223.69,GB/T223.71,GB/T223.72 GB/T20123,GB/T20124的规定进行,但仲裁分析时应按化学分析方法的规定进行
6.2复合钢管的尺寸和外形应采用测径卷尺、游标卡尺、千分尺光学测量仪等符合精度要求的量具或 仪器逐根测量
复层厚度的测量可在复合前进行
6.3复合钢管的内外表面应在充分照明条件下逐根目视检查,内外焊缝偏差等应采用GB/T226进行 宏观检验
复合钢管其他检验项目的取样数量,取样方法及试验方法应符合表7的规定
6.4 复合钢管其他检验项目的取样数量.取样方法及试验方法 表7 序号 检验项目 检验频次 取样数量 取样方法 试验方法 技术要求条款 熔炼分析 次/炉 1个 GB/T20066 5. 产品分析 1次/批 1个 GB/T228.l 5.5.1 2个(1个管体 拉伸试验 1次/批 GB/T2975 GB/T2651 1个焊缝 5.5.2 GB/T16957 GB/T229 2组(HAZ热影 冲击试验 1次/批 响区适用时为 GB/T2975 GB/T2650 5.5.3 3组),l组3 个 GB/T16957 硬度试验 协议 协议 GB/T2975 协议 5.5,4 GB/T6396 结合强度试验 1次/批 1个 GB/T63962008 5.5.5.1 2008 1次/批 个 5.5.5.2 夹持力试验 附录C 附录C 5.5.6 5.5.6 协议或生产 塌陷试验 1个 5.5.6 工艺评定时 附录C 附录C GB/T246 GB/T246 压扁试验 1次/批 5.6.1 媒缝和钢带对 GB/T2653 焊缝导向 10 次/批 头焊缝各 GB/T2653 5.6.2 弯曲试验 GB/Tl6957 1组,l组2个 11 液压试验 逐根 GB/T241 5.6.3 GB/T4334 协议或生产 12 晶间腐蚀试验 GB/T4334一2008 5.6.4 -2008 工艺评定时 sY/T6423.1l 射线 逐根 5.7 NB/T47013.2一2015 无损 13 检测超声波 逐根 SY/T6423.2 5.7 渗透 1次/批 NB/T47013.52015 5.7.2 14
GB/T32958一2016 表7(续 序号 检验项目 检验频次 取样数量 取样方法 技术要求条款 试验方法 协议要求 按规定抽取 卫生性能 或型式试 l4 GB/T17219 GB/T17219 5.10 个试样 验要求时 检验规则 7.1检查和验收 复合钢管的检查和验收应由供方质量技术监督部门进行
7.2组批规则 复合钢管应按批进行检查和验收
每批应由同一组合炉号,同一组合牌号,同一规格和同一制造和 复合工艺的复合钢管组成
每批复合钢管的数量应不超过以下规定: a)外径不大于168.3mm,200根 外径大于168.3mm且不大于355.6mm,100根; b 外径大于355.6mm,50根
7.3复验和判定规则 钢管的复验和判定规则应符合GB/T2102的规定
包装、标识和质量证明书 8.1标识 距管端150mm处开始,采用模板漆印或喷印等方法在复合钢管内表面或外表面做标志
标志内 容和顺序应符合如下规定: 制造厂名称或标识、标记; a b 标准编号; 外径×公称总厚度(复层厚度)×长度,单位为毫米(mm)7 c 复层材料牌号/基层材料牌号 d 管号或批号, e 其他附加标志
8.2包装和质量证明书 包装和质量证明书应符合GB/T2102的规定
15
GB/T32958一2016 附 录A 规范性附录 复合钢管理论重量计算方法 复合钢管理论重量按式(A.1)计算 W= (A.1 [D一2t一)p十t(D一)p T 000 式中: W 复合钢管的重量,单位为千克每米(kg/m); 3.1416; T D 复合钢管的外径,单位为毫米(mm); 复合钢管复层的壁厚,单位为毫米(mm); t -复合钢管复层的密度,单位为千克每立方分米(kg/dnm'),复层不锈钢的密度按表A.1 o 规定; 复合钢管基层的壁厚,单位为毫米(mm); t 复合钢管基层的密度,单位为千克每立方分米(kg/dm),基层碳素钢或低合金钢的密度按 02 7.85kg/dm" 表A.1典型复层不锈钢牌号的密度 密度,20 序号 牌号 统一数字代号 kkg/dm S30210 12Crl8Ni9 7.93 S30408 06Crl9Nil0 S30403 022Crl9Nio 7.90 06Cr25Ni20 S31008 7.98 S31608 06Crl7Ni12Mo2 8.00 S31603 022Cr17Ni12Mo2 06Cr18Ni11T S32168 8.03 S34778 06C18Ni11Nb S41008 06Crl3 7.75 10 S11863 022Crl8Ti 7.70 019Crl9Mo2NbT S11972 12 s11348 o6Crl3Al 7.75 13 s11163 022Crl1T 14 S11213 022Crl2Ni 15 S25073 022Cr25Ni7Mo4N 7.80 16 S22253 022Cr22N5Mo3N 16
GB/T32958一2016 附 录 B 资料性附录 复合钢管屈服强度和抗拉强度的计算 B.1复合钢管的屈服强度下限值可按式(B.1)计算 R十R" (B.1 Rp一 十t 式中: -复合钢管的屈服下限值,单位为兆帕(MPa); Rp -复合钢管复层材料的屈服点下限值,单位为兆帕(MPa); Rp -复合钢管基层材料的屈服点下限值,单位为兆帕(MPa); Rp -复合钢管复层材料的厚度,单位为毫米(nmm); t -复合钢管基层材料的厚度,单位为毫米(mm. B.2复合钢管的抗拉强度可按式(B.2)计算 R十Re (B.2 R;=- t十1a 式中: 复合钢管的抗拉强度下限值,单位为兆帕(MPa) Rm -复合钢管复层材料的抗拉强度下限值,单位为兆帕(MPa); Rm1 -复合钢管基层材料的抗拉强度下限值,单位为兆帕(MPa); R2 -复合钢管复层材料的厚度,单位为毫米(mm); -复合钢管基层材料的厚度,单位为毫米(mm)
17
GB/T32958一2016 附 录c 规范性附录 衬里复合钢管的夹持力试验 C.1夹持力试验 从检验的每批复合钢管中,任取1根管段并机械加工至300mm(340mm、430mm)长作为本试验 的试样,试样表面应清洁干净,管端平整且应与管道轴向垂直
注:试样方法由试验人员根据复合钢管的外径、复层壁厚及试验条件综合评估后确定,试样长度根据试验方法 确定
C.2试验准备 C.2.1万能试验机 C.2.2试验拉伸速率:3 mm/min
C.2.3试样: a 方法I;在抽取的整根复合钢管上截取适宜长度试样,机械加工至试样长度300mm,详见 图C.1
钢压头:D略小于复合钢管基层钢管内径D且D
尺寸的宽度为101 mm
单位为毫米 钢压头 说明 D -基层钢管内径,单位为毫米(mm); D 俐压头直径,单位为毫米(m (mm); 复合钢管外径.单位为毫米(mm)
D 图c.1方法I b 方法;在抽取的整根复合钢管上截取适宜长度试样,机械加工后试样符合图C.2要求,复合 钢管复层与基层结合长度为300mm.
钢压环;D略大于复合钢管外径D,D,略大于D
18
GB/T32958一2016 单位为毫米 说明: D -基层钢管内径,单位为毫米(mm) D. 俐压环内径,单位为毫米( mm); D 钢压环内径,单位为毫米(mm); D 复合俐管外径,单位为毫米(n mm
图c.2方法I 方法l:在抽取的整根复合钢管上截取适宜长度试样,机械加工后试样符合图c.3要求,复合 钢管复层与基层结合长度为300mm
复合钢管试样上与销轴配合的通孔尺寸应略大于销轴.上下通孔中心线应处于钢管截面的同一中 心线
选用的销轴直径分为15mm.25mm,35mm等3种规格,长度在钢管试样外径基础上增加60mm,由 试验人员根据复合钢管的外径和试验条件综合评估后选取
万能试验机能锁紧上下销轴两端部的夹具工装,销轴两端部试验受力与试样轴线相同
单位为毫米 销轴 -1525/35 2 鼻 复层 说明 F -施加在试样上的拉力,单位为千牛(N); D 基层钢管内径,单位为毫米(n mm); 复合钢管外径,单位为毫米(mm)
D 图c.3方法皿
GB/T32958一2016 C.3操作方法 c.3.1试验操作方法I;按图cC.1所示,把试样放置于万能试验机平台上,用内径略大于D且宽度不 小于10mm的钢环垫在试样底部并对中,找正试样上部钢压头的对中位置,给钢压头以压力,使试样的 基层钢管和复层钢管分离,记录分离10mm时的最大压应力F
C.3.2试验操作方法I:按图C.2所示,把试样放置于万能试验机平台上,钢压环放置于试样顶端并对 中,给钢压环以压力,使试样的上部分基层钢管和复层钢管发生分离并向下滑动,记录分离和移动 10 nmm时的最大压应力F c.3.3试验操作方法I;按图C.3所示,把销轴穿人试样上下端部的两个通孔内,试样放置在万能试验 机上后用夹具工装锁紧销轴两端,然后启动试验机通过两根销轴施以试样上下分离的拉力,基层钢管和 复层钢管在两根销轴的拉动下开始分离
记录分离10mm时的最大拉应力F C.3.4在装件过程中应保证试样位于试验机压板,夹具工装的中心位置,试样轴线与压板压下或拉伸 力方向一致
c.3.5压下或拉伸分离过程保持同一速率 试验结果的判定 最大压应力或拉应力F即为衬里复合钢管的夹持力,按所对应的规格符合表5规定即为合格
流体输送用不锈钢复合钢管GB/T32958-2016介绍及应用
随着工业领域的快速发展,对于流体输送管道的技术要求也越来越高。不锈钢复合钢管作为一种新型管材,具有优异的防腐、耐磨、高温高压性能,被广泛应用于各个领域的流体输送中。
我国在这方面的标准化工作也得到了加强,其中GB/T32958-2016《流体输送用复合钢管》就是其中之一。该标准规定了不锈钢复合钢管的材料、结构、制造工艺、试验方法等方面的要求,保证了其质量和可靠性。
相比于传统的输送管道,不锈钢复合钢管具有更好的经济效益和环境保护性。首先,在使用寿命上,不锈钢复合钢管的寿命是普通钢质管道的2-3倍,维护费用也更低。其次,在输送质量上,不锈钢复合钢管能够保证物料不受污染、不掉色、不变质,保证了输送效果和品质。
目前,不锈钢复合钢管已经被广泛应用于石油、化工、制药、食品等多个领域的液体输送中。同时,随着技术不断升级和完善,不锈钢复合钢管在未来的应用前景也将更加广阔。