GB/T6823-2008
船舶压载舱漆
Ballasttankspaintforship
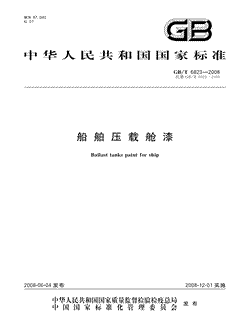
- 中国标准分类号(CCS)G51
- 国际标准分类号(ICS)87.040
- 实施日期2008-12-01
- 文件格式PDF
- 文本页数14页
- 文件大小808.64KB
以图片形式预览船舶压载舱漆
船舶压载舱漆
国家标准 GB/T6823一2008 代替GB/T68231986 船舶压载舱漆 Ballasttankspaintforship 2008-06-04发布 2008-12-01实施 国家质量监督检验检疫总局 发布 国家标准化管蹬委员会国家标准
GB/T6823一2008 前 言 本标准对应于《船舶专用海水压载舱和散货船双舷侧处所保护涂层性能标准》简称PSPC [2006年12月8日国际海事组织IMO)海事安全委员会MsC)根据修订的海上生命安全公约 (sOLAS)条款I-1/3-2通过],与其一致性程度为非等效 本标准代替GB/T68231986《船舶压载舱漆通用技术条件》 本标准与GB/T6823一1986相比主要技术差异如下 -标准名称改为《船舶压载舱漆》; -增加了适用范围; 增加了规范性引用文件章节; 增加了产品的分类; 技术要求分为“涂料的要求”和“涂层的要求”
在“涂料的要求”中增加了“基料和固化剂组分 鉴定、密度、不挥发物、贮存稳定性”的要求;在“涂层的要求”中取消了“耐冲击性、耐盐雾性、耐 ,增加了“外观与颜色、名义干膜厚度、模拟压载舱条件试验、冷凝试验”的要求; 热盐水性" -增加了对“取样"和“试验样板的制备"的详细规定 ,不挥发物、储存稳定性、外观与颜色、名义干膜厚度,模 增加了“基料和固化剂组分鉴定、密度、 拟压载舱条件试验、冷凝试验”等试验方法内容; 在附录A“模拟压载舱条件试验”和附录!“冷凝试验”中增加了“起泡和锈蚀、针孔数量、附着 力、内聚力按重量损失计算的阴极保护需要电流、阴极剥离、划痕附近的腐蚀蔓延.U型条" 等检测试验内容 在“检验规则”中增加了检验分类,按检验方式分型式检验和出厂检验二种; -增加了“附录A模拟压载舱条件试验”、“附录B冷凝试验”、“附录C人工海水配方” “附录D牺牲阳极 锌合金的组成成分” 本标准的附录A,附录B,附录C和附录D为规范性附录
本标准由石油和化学工业协会提出
本标准由全国涂料和颜料标准化技术委员会归口
本标准起草单位:;船舶重工集团公司第七二五研究所、中海油常州涂料化工研究院、中远佐敦 船舶涂料有限公司、海虹老人牌()有限公司、中涂化工(上海)有限公司、江苏海耀化工有限公司、上 海国际油漆有限公司、船级社、海洋化工研究院、上海开林造漆厂、宁波飞轮造漆有限责任公司、 浙江飞鲸漆业有限公司、江苏冶建防腐材料有限公司
本标准主要起草人;黄淑珍、苏春海、王健、徐国强、王玉压,刘才方、王一任、吴海荣、钱叶苗、 杜伟娜、袁泉利、严杰、史优良
本标准于1986年首次发布
GB/T6823一2008 船舶压载舱漆 范围 本标准规定了船舶压载舱漆的分类、要求、试验方法、检验规则、标志、包装、运输和贮存
本标准适用于不小于500t的所有类型船舶专用海水压载舱和船长不小于150m的散货船双触侧 处所保护涂层
规范性引用文件 下列文件中的条款通过本标准的引用而成为本标准的条款
凡是注日期的引用文件,其随后所有 的修改单(不包括勘误的内容)或修订版均不适用于本标准,然而,鼓励根据本标准达成协议的各方研究 是否可使用这些文件的最新版本
凡是不注日期的引用文件,其最新版本适用于本标准
GB190危险货物包装标志 GB/T191包装储运图示标志(GB/T191一2000,eqIs0780;1997) GB712船体用结构钢 GB/T1725色漆、清漆和塑料不挥发物含量的测定GB/T1725一2007,IsO3251:2003,IDT GB/T1765测定耐湿热,耐盐雾、耐候性(人工加速)的漆膜制备法 GB/T1766色漆和清漆涂层老化的评级方法 GB/T3186 色漆、清漆和色漆与清漆用原材料取样(GB/T3186一2006,ISO15528:2000,IT GB3097海水水质标准 GB/T5210一2006色漆和清漆拉开法附着力试验ISO4624:2002,IDT) GB/T6747船用车间底漆 GB/T6750色漆和清漆密度的测定比重瓶法(GB/T6750一2007,ISO2811-l:1997Paints mmethod.,IDT andvarnishes=determination 1odensitypartl:pyknometer GB/T6753.3涂料贮存稳定性试验方法 GB/T8923涂装前钢材表面锈蚀等级和除锈等级(GB/T8923一1988,eqIso8501-1;1988) GB/T9271 色漆和清漆标准试板(GB/T9271一2008,ISO1514:2004,MOD GB/9278涂料试样状态调节和试验的温湿度(GB/T9278一2008,ISO3270:1984,Pai intsand varnishesandtheirrawmaterialsTemperaturesandhuniditiesforconditioningandtesting,IDT) GB/T9750涂料产品包装标志 GB/T13288涂装前钢材表面粗糙度等级的评定比较样块法GB/T132881991. eqvIsO8503:1995 GB/T13452.2色漆和清漆漆膜厚度的测定法(GB/T134522008,IsO2808:2007,IDT GB/T13491涂料产品包装通则 GB/T13893 色漆和清漆耐湿性的测定连续冷凝法(GB/T138932008,IsO6270-l:1998 IDT GB/T18570.3涂覆涂料前钢材表面处理表面清洁度的评定试验第3部分;涂覆涂料前钢材 表面的灰尘评定(压敏粘带法)(GB/T18570.3一2005,IsO8502-3:1992,IDT G;B/T18570.9涂覆涂料前钢材表面处理表面清洁度的评定试验第9部分:水溶性盐的现场
GB/T6823一2008 电导率测定法(GB/T18570.g2005,ISO8502-9l999,IDT) HG/T2458涂料产品检验、运输和贮存通则 分类 产品按基料和固化剂组分分为两种类型 a 环氧基涂层体系 b 非环氧基涂层体系
要求 4.1 -般要求 4.1.1产品涂层的目标使用寿命为15a. 4.1.2产品配套体系的组成由涂料供应商确定
4.1.3产品应能和无机硅酸锌车间底漆或等效的涂料配套,车间底漆与主涂层系统的相容性应由涂料 供应商确认
产品应能在通常的自然环境条件下施工和干燥 4.1.5产品应适应无空气喷涂,施工性能良好,无流挂
涂料的要求 4. 2 涂料的性能应符合表1的要求
表1涂料的要求 检测项目 环氧基涂层体系 非环氧基涂层体系 基料和固化剂组分鉴定 环氧基体系 非环氧基体系 密度/g/ml) 商定 商定 不挥发物/% 自然环境条件,1a 通过 通过 储存稳定性 50士2)C条件,30d 通过 通过 3 4
涂层的要求 涂层的性能应符合表2的要求
表2涂层的要求 检测项目 非环氧基涂层体系 环氧基涂层体系 漆膜平整
漆膜平整 外观与颜色 多道涂层系统,每道涂层的颜色要 多道涂层系统,每道涂层的颜色要 有对比,面漆应为浅色
有对比,而漆应为浅色
名义干膜厚度 涂层在90/10规则下达到320pm" 商定 模拟压载舱条件试验 通过 通过 冷凝舱试验 通过 通过
GB/T6823一2008 试验方法 取样 除另有规定,船舶压载舱漆应按GB/T3186的规定抽样
样品分为两份,一份密封储存备查,另 份作检验用样品
5.2试验样板的制备 5.2.1试验样板基材 除另有规定外,试验板材应采用GB712中的热轧普通碳素钢
5 .2.2样板基材的表面处理 5.2.2.1试验样板钢板应在下列环境条件下,采用喷砂或抛丸进行钢板表面处理: a) 空 气相对湿度不超过85%; 钢板表面温度高于露点温度3C以上 b 5.2.2.2试验样板钢板经表面处理后,在进行车间底漆涂装前按GB/T8923规定方法检测钢板表面 除锈等级应达到Sa2'%;按GB/T18570.3规定方法检测表面清洁度应达到灰尘分布量为1级、灰尘尺 寸不大于2级,目视检查无油污;按GB/T13288规定方法检测表面粗糙度应达到Ra30m754m. 5.2.2.3试验样板钢板经表面处理后,应按GB/T18570.9规定方法进行钢板表面水溶性盐检测,当 钢板表面水溶性盐含量不大于50mg/mNaCl时,方可进行车间底漆的涂装
5.2.3车间底漆的涂装 除另有规定或商定,应按GB/T1765的规定采用喷涂方式进行涂装
应选择由涂料供应商确认的 无机硅酸锌车间底漆或等效涂料,车间底漆的厚度和性能应符合GB/T6747规定的要求
5 .2.4车间底漆的老化 已涂装车间底漆的试验样板应放在露天环境中自然老化至少2个月 5.2.5二次表面处理 采用低压水清洗或其他温和的方法,对老化后的试验样板表面进行清洁处理,然后将其置于通风干 燥环境中干燥
不可采用扫掠式喷射或高压水清洗等其他去除底漆的方法
5.2.6压载舱漆的涂装 5.2.6.1除另有规定或商定,应在已经做过露天环境自然老化的试验样板上,采用喷涂方式进行压载 舱涂层涂装
涂层配套体系,涂装道数,涂装间隔等按相关产品技术要求或涂料供应商要求进行
5.2.6.2涂层体系中每道涂层干膜厚度都应进行测量,直到上道涂层厚度达到规定要求,方可进行下 -道涂装(不含车间底漆涂层厚度). 2.6.3试板背面应涂适当的保护涂料或受试涂料,试板的四周应以适当的方法封边,避免对试验结 5. 果产生影响
5.2.7涂层厚度的检测 5.2.7.1最后一道压载舱涂层完全干燥后,应使用非破坏性的测厚仪,按GB/T13452.2规定的方法 测定压载舱涂层的总干膜厚度,以在150cm×150em的平面上均匀地分布9个测量点的方式进行
5.2.7.2环氧基涂层体系的名义干膜厚度在90/10规则下应达到320m(不含车间底漆涂层厚度). 非环氧基涂层体系的名义干膜厚度应符合供应商产品技术要求
注,90/10规则意指所有测点的90%测量结果应不小于名义干膜厚度,余下10%测量结果应大于0.9倍的名义干 膜厚度
5.2.7.3用90V低压湿海绵针孔检测仪,检测压载舱涂层针孔数量应为零
5.2.8试验样板的状态调节 除另有规定,应按GB/T9278规定条件状态调节7d后,方可投人试验
基料和固化剂组分鉴定 采用红外法进行鉴定
GB/T6823一2008 4 5. 密度的测定 按GB/T6750规定方法进行
5.5不挥发物的测定 按GB/T1725规定的方法进行
5.6储存稳定性的测定 按照GB/T6753.3规定方法进行试验
原封、未开桶包装的涂料在自然环境条件下贮存1a或在 50士2)C加述条件下贮存30d后,开封检查涂料应满足下列要求 a)用机械混和器搅拌,在5min之内很容易成均匀的状态; b)无硬块或胶质沉淀物
5.7外观与颜色 目视检查 5.8干膜厚度的测定 按照5.2.7规定方法进行检测
5.9模拟压载舱条件试验 按附录A《模拟压载舱条件试验》规定的试验方法,进行试验和合格性判定
5.10冷凝舱试验 按附录B(冷凝舱试验》规定的试验方法,进行试验和合格性判定 检验规则 检验分类 6.1.1检验分为型式检验和出厂检验
出厂检验项目包括密度,不挥发物、外观与颜色
6.1.3型式检验包括本标准所列的全部要求
有下列情况之一时,应进行型式检验 正常生产时,每四年应进行一次型式检验; a b) 当产品新投产时; 当材料、工艺有改变足以影响产品性能时; c d 产品停产一年以上后重新恢复生产时
6.2合格判定 在对产品进行检验时,如发现产品质量不符合本标准技术要求规定时,供需双方应按照GB/T3186 的规定重新取双倍量进行复验,如仍不符合本标准技术要求规定时,产品即为不合格品
标志,包装、,运输、贮存 标志 产品的标志应符合GB/T9750的要求
7.2包装 产品的包装应符合GB190GB/T191和GB/T13491的要求
运输 产品的运输应符合HG/T2458的要求,防止雨淋、日光暴晒
7 贮存 产品应符合HG,/T2458的要求,贮存在通风、干燥的仓库内,防止日光直接照射,并应隔绝火源
产品在原包装封闭的条件下,自生产完成之日起,贮存期为一年(或按照产品技术要求)
超过贮存期的 产品可按本标准规定的出厂检验项目进行检验,如检验合格,仍可使用
GB/T6823一2008 附 录A 规范性附录 模拟压载舱条件试验 A.1适用范围 附录A提供了本标准第4章、第5章所涉及的模拟压载舱条件试验程序的详细步骤,包括试验条 件,试验程序、验收标准和试验报告等
附录A适用于不小于500t的所有类型船舶专用海水压载舱保护涂层
A.2试验条件 A.2.1试验期为180d
A.2.2试验样板五块,每块样板尺寸为200mm×400mmX3mm A.2.3模拟压载舱条件试验装置 压载舱涂层试验波浪舱的技术要求和1=4试验样板放置情 况如图A.1所示 循环加热 50c12h 20c12h 试板 冷却 温度梯度 35C海水 加热 波浪运动 图A.1压载舱涂层试验波浪舱 A.2.4模拟真实压载舱的条件,一个试验循环为二个星期装载天然或人工海水,一个星期空载
海水 温度保持在(35士2)C
A.2.5试验海水为符合GB/T3097中第一类经过滤的天然海水或人工海水,人工海水配方见附录c 规范性附录). A.2.6样板1=;模拟上甲板的状况,试板背部(50士2)C/12h加(20士2)C/冷却12h循环;试验样板 周期性的用天然或人工海水泼溅,模拟船舶纵摇和横摇运动,泼溅间隔为3s或更短;板上有划破涂层 至底材的、横贯宽度的划线
A.2.7样板2*;固定锌牺牲阳极以评估阴极保护效果,锌牺牲阳极尺寸为中20mm×25mm,锌牺牲 阳极材料应符合附录D的要求;试验样板上距离阳极100mm处开有直径为8mm的至底材的圆形人
GB/T6823一2008 工漏涂孔;试验样板循环浸泡在天然或人工海水中
A.2.8样板3=;背面冷却,形成一个大约为20C温度梯度,以模拟一个压载舱的冷却舱壁;用天然或 人工海水泼溅,模拟船舶纵摇和横摇运动,泼溅间隔为3s或更短;板上有划破涂层至底材的、横贯宽度 的划线
A.2.9样板4”;用天然或人工海水循环泼溅,模拟船前后颠簸和摇摆的运动,泼溅间隔为3或更短; 板上有划破涂层至底材的、横贯宽度的划线
A.2.10在样板3”和4”各上一条U型条见图A.2),U型条距一条短边120mm,距长边各 80mm
25mm长 2mm厚 仪在试版与U型条 15mm 外侧焊按 40mm 图A.2U型条 A.2.11样板5”:模拟双层底加热的燃料舱和压载水舱之间的隔板,放在干燥且温度为(70士2)C条 件下暴露180d
A.3试验程序 A.3.1试验样板制备 按5.1一5.2要求制备模拟压载舱条件试验的五块试验样板
A.3.2试验样板放置 将已制备完成的1*一4”试验样板按图1所示放人模拟压载舱条件试验装置- -压载舱涂层试验 波浪舱中规定位置并固定牢固;将5"样板另外放人干燥且温度为(70士2)C的恒温试验箱中
A.3.3试验 A.3.3.1开启压载舱涂层试验波浪舱和恒温试验箱,按试验条件要求设定各系统试验运行参数
试 验过程中应随时检查、,调整和记录各系统试验参数 A.3.3.2试验过程中,在每个试验循环周期结束时,应检查并记录所有试验样板表面的锈蚀、起泡、开 裂情况必要时拍照片记录
A.3.3.3试验结束时,应小心取出所有试验样板,用自来水冲洗去除盐迹,用滤纸或软布擦干,必要时 拍照片记录
A.3.4试验结果检测 A.3.4.1起泡和锈烛 按GB/T1766规定的试验方法对1#5"试验样板进行检测和评级 A.3.4.2针孔数量 采用90V低压湿海绵针孔检测仪对1=5*试验样板进行检测
A.3.4.3附着力和内聚力 按GB/T5210中9.4.2规定的方法对1=一5*各试验样板进行检测
A.3.4.4阴极保护需要电流 按重量损失计算阴极保护需要电流 A.3.4.5阴极剥离 A.3.4.5.1仔细检查2样板涂层并记录漆膜起泡情况,若样板反面也涂装了受试涂料,那么也应对 样板反面进行检查
按照GB/T1766规定的评级标准,记录下样板的起泡等级及起泡与人造孔之间的
GB/T6823一2008 距离
注意区分因人造孔所致的起泡及人造孔之外的起泡
A.3.4.5.2在人造孔处用锋利的小刀在基材与漆膜之间划两道痕(交叉于人造孔)以评估人造孔处漆 膜附着力的降低情况
用小刀尽可能地把人造孔周围的漆膜剥起
记录下漆膜与基材的附着力是否降 低,以及被剥离漆膜与人造孔之间的最大距离(mm). A.3.4.6划痕附近的腐蚀蔓延 仔细检查1=、3=、4=样板划痕处附近涂层锈蚀、起泡、脱落情况按照GB/T1766规定的评级标 准,记录下样板的锈蚀、起泡等级及与划痕处之间的距离(mm)
测量每块样板沿划痕两边的腐蚀蔓延 并确定腐蚀蔓延的最大值,三个最大值的平均值作为验收值
A.3.4.7U型条效应 仔细检查并记录焊接在3”、4"样板上的U型焊条的所有角落或焊缝处是否存在缺陷、开裂或剥离 等情况
验收标准 船舶压载舱漆涂层的模拟压载舱条件试验的试验结果应满足下表A.1要求
表A.1验收标准 项 目 环氧基体系 非环氧基体系 起泡 0级 0级 锈蚀 0级 0级 针孔数量 >3.5MPa >5.0MPa 附着力 基材和涂层间或各道涂层之间的脱 基材和涂层间或各道涂层之间的脱 开面积在60%或以上 开面积在60%或以上 >3.0MPa >5.0MPa 内聚力 涂层中的内聚破坏面积在40%或 涂层中的内聚破坏面积在40%或 以上 以上 阴极保护需要电流 5mA/m <5mA/m" 阴极保护;人工漏涂处的剥离 8mmm 5mm 二5mm 划痕附近的腐蚀蔓延 8mm 若在角上或焊缝处有缺陷、开裂或剥 若在角上或焊缝处有缺陷、开裂或剥 U型条 离都将判定系统不合格 离都将判定系统不合格 A.5试验报告 试验报告应包括下列内容 a)生产商名称
试验日期
b c)涂料和底漆的产品名称/标识 d 批号
ee 钢板表面处理的数据,包括 表面处理方式; 水溶性盐含量;
GB/T6823一2008 灰尘和磨料嵌人物
涂层体系涂装的数据,包括下列数据: -车间底漆; 涂层道数; 涂装间隔; 试验前的干膜厚度; 稀释剂; 气温、湿度、钢板温度 模拟压载舱条件试验的试验结果,包括 样板起泡; 样板锈蚀; 针孔数量; 附着力; 内聚力; 按重量损失计算的阴极保护需要电流; 阴极保护,人工漏涂处的剥离 划痕附近的腐蚀蔓延; U型条
按验收标准判断的结果
h
GB/T6823一2008 附 录 B 规范性附录 冷凝舱试验 B.1适用范围 附录B提供了本标准第4章、第5章所涉及的冷凝舱条件试验程序的详细步骤,包括试验条件、,试 验程序、验收标准和试验报告等
附录B适用于不小于500t的所有类型船舶专用海水压载舱及船长150m及以上散货船的双舷侧 处所(非专用海水压载舱)的保护涂层
B.2试验条件 冷凝舱试验依据GB/T13893标准进行,试验条件如下 a)暴露时间为180d 1×150 b)两块试板,每块试板尺寸为150mm mm×3mm; 冷凝舱条件试验的试验装置技术要求和试验样板放置情况如图B.1所示 室温23c士2c 试板 室内湿度100% 水温40c士2C 图B.1冷凝舱试验 B.3试验程序 B.3.1按51,5,2要求制备冷凝舱试验的2块试验样板
B.3.2将已制备完成的样板按图B.1所示放人冷凝舱中规定位置
B.3.3开启冷凝试验舱,按试验条件要求设定各系统试验运行参数
试验过程中应随时检查并记录 各系统试验参数的运行情况
B.3.4试验过程中,要定期检查并记录所有试验样板表面的锈蚀、起泡、开裂等情况,必要时应拍照片 记录
B.3.5试验结束时,应小心取出所有试验样板,用滤纸或软布轻轻擦干,然后按下列规定试验方法进 行试验结果检测
B.3.5.1起泡和锈蚀的检测 按GB/T1766规定的试验方法进行检测和评级
GB/T6823一2008 B.3.5.2针孔数量的检测 采用90V低压湿海绵针孔检测仪板进行检测
B.3.5.3附着力和内聚力的检测 按GB/T52102006中9.4.2规定的方法进行检测
B.4验收标准 船舶压载舱漆涂层的冷凝舱试验的结果应满足表B.1要求
表B.1验收标准 环氧基系统 非环氧基系统 项 目 0级 0级 起泡 锈蚀 0级 0级 针孔数量 >3.5MPa >5.0MPa 附着力 基材和涂层间或各道涂层之间的脱开面 基材和涂层间或各道涂层之间的脱开面 积在60%或以上 积在60%或以上 >3.0MPa >5.0MPa 内聚力 涂层中的内聚破坏面积在40%或以上 涂层中的内聚破坏面积在40%或以上 B.5试验报告 试验报告应包括下列内容: a)生产商名称
试验日期
b) e)涂料和底漆的产品名称/标识
批号
d 钢板表面处理的数据,包括: 表面处理方式; 水溶性盐含量 灰尘和磨料嵌人物
f 涂层体系涂装的数据,包括下列数据: 车间底漆; 涂层道数; 涂装间隔; 试验前的干膜厚度; 稀释剂; 气温、湿度、钢板温度 压载条件试验的试验结果,包括 -样板起泡; 样板锈蚀; 针孔数量; 附着力; 内聚力
h按验收标准判断的结果
10
GB/T6823一2008 c 附 录 规范性附录 人工海水配方 用下列分析纯级试剂溶于蒸馏水并稀释至总量为1L 24.53g氯化钠(NaCI); 11.11g六水合氯化镁(MgCl6H.,O); .09g无水硫酸钠(Na,SO); 1.16g无水氯化钙(CaCl,); 0.70【氯化钾(KCI): 0.20g碳酸氢钠(NaHcO); .10g溴化钾(KBr) 0.
GB/T6823一2008 附 D 录 规范性附录 牺牲阳极 -锌合金的组成成分 合金中各成分的质量分数(%) 铅 0.006 铁 0.005 钙 0.025~0.070 铜 0.005 错 0.100.50 其他 <0.10 锌(纯度99.99%) 余下部分