GB/T14783-2009
轮胎式集装箱门式起重机
Rubbertiredgantrycrane
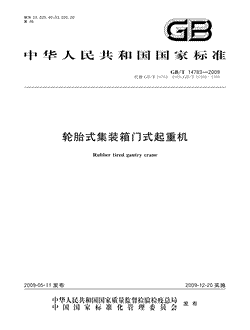
- 中国标准分类号(CCS)R46
- 国际标准分类号(ICS)53.020.20;03.220.40
- 实施日期2009-12-20
- 文件格式PDF
- 文本页数22页
- 文件大小942.90KB
以图片形式预览轮胎式集装箱门式起重机
轮胎式集装箱门式起重机
国家标准 GB/T14783一2009 代替GB/T147831993,GB/T15362一1994 轮胎式集装箱门式起重机 Rubbertiredigantryerane 2009-05-11发布 2009-12-20实施 国家质量监督检验检疫总局 发布 国家标准化管蹬委员会国家标准
GB/T14783一2009 前 言 本标准代替GB/T14783一1993《轮胎式集装箱门式起重机技术条件》和GB/T15362一1994《轮胎 式集装箱门式起重机试验方法》,将GB/T15362的内容纳人GB/T14783中
本标准与GB/T14783一1993相比主要技术差异如下 -取消了“术语” -对“齿轮和减速器”内容进行了修改和完善(见3.6.1) -对“联轴器”的选型要求进行了补充(见3.6.3); 取消原“主要部件”,将原小车轨道内容纳人“小车车轮和轨道”(见3.6.7),将原起升机构、小 车运行机构和大车运行机构内容纳人“机构”(见3.7),其他内容单列成条(见3.6); 对“动力装置”内容进行了补充见3.8); 对"试验方法"内容进行了修改和完善(见第4章》. 本标准的附录A为资料性附录
本标准由交通运输部提出
本标准由交通运输部港机标准归口单位归口
本标准起草单位:上海振华港口机械(集团)股份有限公司、上海港机重工有限公司,交通部水运科 学研究院
本标准主要起草人;李海波、胡桂军、何刚、李国辉、饶京川、李伟
本标准所代替标准的历次版本发布情况为 -GB/T147831993; -GB/T153621994
GB/T14783一2009 轮胎式集装箱门式起重机 范围 本标准规定了轮胎式集装箱门式起重机(以下简称起重机)的技术要求、试验方法、检验规则、标志 和运输等
本标准适用于装卸符合GB/1413规定的国际集装箱的起重机
规范性引用文件 下列文件中的条款通过本标准的引用而成为本标准的条款
凡是注日期的引用文件,其随后所有 的修改单(不包括勘误的内容)或修订版均不适用于本标准,然而,鼓励根据本标准达成协议的各方研究 是否可使用这些文件的最新版本
凡是不注日期的引用文件,其最新版本适用于本标准
GB/T699优质碳素结构钢 GB/T700碳素结构(GB/T700-2006,IsO630;:1995,NEQ GB/T985.1气焊、焊条电弧焊、气体保护焊和高能束焊的推荐坡口(GBT985.1一2008,ISO9692 1:2003,MOD GB/T985.2埋弧焊推荐坡口(GB/T985.2一2008,IsO9692-2;1998,MOD GB/T1184 形状和位置公差未注公差值(GB/T1184一1996,eqvISO2768-2:1989 GB/T1228钢结构用高强度大六角头螺栓(GB/T1228一2006,IsO7412;1984,NEQ GB/T1229钢结构用高强度大六角螺母(GB/T1229一2006,IsO4775:1984,NEQ) 1230钢结构用高强度垫圈(G;B/T1230一2006,ISO7416;1984,NEQ GB/T1231钢结构用高强度大六角头螺栓、大六角头螺母、垫圈技术条件 GB/T1413 系列1集装箱分类、尺寸和额定质量(GB/T1413一2008,IsO668;1995,IDT) 低合金高强度结构钢 GB/T1591 GB/T1801极限与配合公差带和配合的选择(GB/T 1801一1999,eqvIS(O1829:1975) 安全色(GB2893-2008,IsO3864-1l;2002,Graphiealsymbols-Safetycoloursandl GB2893 safetysigns一Partl:Designprinciplesforsafetysignsinworkplacesandpublicareas,MOD GB2894安全标志及其使用导则 GBy/T30r7合金结构钢 GB/T3220集装箱吊具的尺寸和起重量系列 GB/T3323金属熔化焊焊接接头射线照相(GB/T3323一2005,EN1435;1997,MOD) GB/T3766液压系统通用技术条件(GB/T3766一2001,eqvISO4413;1998) GB/T3811起重机设计规范 GB/T5117碳钢焊条(GB/T5117一1995,eqvANSI/AwSA5.1:1991 GB/T5118低合金钢焊条(GB/5118一1995,eqvANSI/AwSA5.5;1981) GB/T5293埋弧焊用碳钢焊丝和焊剂 GB/T6067起重机械安全规程(GB/T6067一1985,neqNFE52122,1975) GB/T8110气体保护电弧焊用碳钢、低合金钢焊丝(GB/T81102008,AwSA5.18M:2005 MOD) forminehoist GB8918重要用途钢丝绳(GB8918一2006,IsO3154;:1988,Sstrandedwireropes Technical delivery ,MOD ng requirements,
GB/T14783一2009 GB/T8923涂装前钢材表面锈蚀等级和除锈等级(GB/T8923一1988,eqvISO8501-1:1988) (GB/T9286色漆和清漆漆膜的划格试验(GB/T9286一1998,eqIsO2409:1992) GB/T10095所有部分圆柱齿轮精度制(GB/T10095一2008,IsO1328(所有部分),IDT GB/T10096 齿条精度 GB/T1l345钢焊缝手工超声波探伤方法和探伤结果分级 GB/T11352 -般工程用铸造碳钢件(GB/T113522009,IsO3755:1991,MOD GB/T12470埋弧焊用低合金钢焊丝和焊剂 GB/T14957熔化焊用钢丝 GB16710.1工程机械噪声限值 GB/T16710.2工程机械定置试验条件下机外辐射噪声的测定(GB/T16710.21996, ISO/DIS6393:l995,MOD GB/T16710.3工程机械定置试验条件下司机位置处噪声的测定(GB/T16710.2一1996 ISO/DIS6394:l995ADMl:l996,MOD) 动态试验条件下机外钢射噪声的测定(GB/TI6710.4 GB/T16710.4工程机械 -1996eqv ISO6395:1988) GB/T16710.5工程机械动态试验条件下司机位置处噪声的测定(GB/T16710.51996,eqv IS(O6396:l992 司机室第1部分总则(GB/T20303.12006,IsO8566-1:1992, GB/T20303.l 起重机 IDT GB/T20303.5起重机司机室第5部分;桥式和门式起重机(GB/T20303.5-2006 ISO8566-5:1992,IDT CB/T3123船用轧制钢材气割面质量技术要求 JT/T90港口装卸机械风载荷计算及防风安全要求 技术要求 3.1工作条件 3.1.1工作环境温度为-20C十40c,最大相对湿度不大于95%,有凝露
3.1.2工作时风速不大于20m/s;非工作时风速不大于44m/s
3. .1.3起重机的工作级别宜为A6、A7
起重机行走通道地面坡度应不大于1%,局部坡度不大于3%
跨度两侧行走通道地面坡度应 同向,即同为上坡或下坡
3.1. .5 如有其他特殊要求,按订货合同或技术规格书规定
3 2 整机要求 3.2.1起重机的设计,制造应符合GB/T3811和本标准的有关规定
3. .2. 2 起重机作业时的噪声应符合GB16710.1的规定,座椅处司机耳边噪声应符合GB/T20303.1 的规定
33 2. 3 起重机在做静载试验时,应能承受1.25倍额定起重量的试验载荷
试验后各构件均不应产生 裂纹,永久变形、油漆打皱及其他异常情况
3 .2.4起重机在做额定载荷试验时,应能承受额定起重量的试验载荷
试验中各机构应工作正常、,无 异常响声、结构件完好
3.2.5起重机在做动载试验时,应能承受1.1倍额定起重量的试验载荷
试验中各机构应工作正常、 无异常响声,结构件完好无损
3.2.6起重机在做可靠性试验时,应持续进行8h的作业试验,起重机不应出现因缺陷包括漏油)而
GB/T14783一2009 发生的故障
若一旦发生故障,且在15min内又不能修复,或故障出现二次以上,则可靠性试验应 重作
3.2.7起重机做金属结构应力测定时,结构强度、刚度应满足设计要求,无残余变形和损坏现象,焊缝 无裂纹,表面油漆不打皱
3.2.8起重机应完成不少于5000自然箱的起重作业工业性试验,工业性试验作业时间内包括可靠性 试验作业循环次数
试验中起重机不应发生重大损坏或性能异常现象
3.3主要技术参数的允许偏差 3.3.1起升速度的允许偏差为公称值的一3%十10%
3.3.2小车运行速度的允许偏差为公称值的一3%十10%
3.3.3大车运行速度的允许偏差为公称值的士10%
轮压和质量的允许偏差为公称值的士5%
3.3.5起升高度的允许偏差为公称值的(O一5)%. 3.3.6跨距、基距、轴距和内净空的允许偏差为公称值的士1%
3.3.7 外形尺寸的允许偏差为公称值的士2%
3.4材料 主要零件的材料应有材料生产厂的出厂合格证明书,否则应取样试验,其化学成分,机械性能应 3 符合标准
采用本标准规定之外的材料,应有可靠的理论或试验依据,并有起重机制造厂技术部门的 签证
3.4.2用于起重机金属结构中主要受力构件的材料性能不低于表1的规定
钢号Q235B,Q235C应 符合GB/T700的规定;Q345B应符合GB/T1591的规定
表1 -20 -20 工作环境温度/c 钢号 Q235B Q235C Q345B 4.3起升卷筒应采用焊接结构,其材料性能应不低于GB/T700中的Q235B 3 3. 4.4起升钢丝绳滑轮轮缘的材料性能应不低于GB/T699中的35钢
33 4 5 齿轮、小车车轮材料性能不低于GB/T699中的45钢或GB/T11352中的ZG310-570铸钢
3 .4.6联轴器材料性能应不低于GB/T699中的45钢或GB/T11352中的ZG310-570铸钢
3 .4.7齿轮轴、滑轮轴材料性能应不低于GB/T699中的35钢
3 3.4.8集装箱吊具转锁材料性能应不低于GB/T3077中的40Cr钢
3 5 结构件 3.5.1结构件制造的允许偏差应符合表2的规定
2 表 单位为毫米 序号 检查项目 允许偏差 图 简 构件的直线度 a 厂而" 垂直方向 b b 水平方向 "
GB/T14783一2009 表2(续 单位为毫米 图 序号 检查项目 简 允许偏差 F=" 梁的上拱度偏差 -图纸规定的拱度 梁的长度(L L5000 <4 5000
GB/T14783一2009 3.6.2.5装配后的制动器,各钦点应转动灵活,符合有关技术文件的规定
3.6.3联轴器 3.6.3.1联轴器的转速、转矩和安装要求等应符合相应型式联轴器标准规范的规定
3.6.3.2弹性套柱销联轴器的两个半联轴器的相对径向圆跳动AY和相对端面圆跳动X偏差值见 图1、图2和表3
图1 xB 图2 表3 单位为毫米 D AY AX 100
GB/T14783一2009 轴距 图6 3.6.7.9如采用水平导轮,则一侧两导轮之间的中心线与轨道中心线的偏差应不大于士1mm,见 图7
昌 两导轮距离中心线 两导轮距离 两导轮距岗 轨道中心线 两导轮距离中心线 图7 小车轨距K的允许偏差值公K 3.6.7.10 -轨道设在承轨梁中部,sK=士4nm,见图 -轨道设在承轨梁内侧;AK=0mm十8mm,见图9
尺十AK 图8 十AK 图9 3.6.7.11小车轨道中心线与轨道支承腹板中心线的位置偏差应不大于其腹板厚度!的1/2,见图1o.
GB/T14783一2009 s 图10 3.6.7.12同一横截面上,左右小车轨道顶面的高低误差AH应不大于轨距K的0.15%,最大值应不 超过10mm,见图ll
图11 3.6.7.13小车轨道的侧向直线度(见图12)应符合下列要求 -每2m长度内的偏差不大于1mm; 在轨道全长范围内的偏差不大于5mm. 全长范围内 图12 3.6.7.14小车轨道宜用整根轨道或用接头煤接的整根轨道,否则应满足以下要求;轨道接头处轨面的 mm2mm.
高低差应不大于1mm;侧面左右错位差应不大于1mm;间隙应为01 3.6.7.15如仅在一根轨道上采用水平导向轮,则轨距极限偏差可为3.6.7.10中的数据的3倍,对 3.6.7.13中的非导向轨道的直线度要求可以降低
3.6.8轮胎 轮胎充气压力应符合轮胎制造厂的规定,其允许偏差为士3%之内
3.7机构 起升机构 起升机构工作级别宜为M6、M7
起升机构应采用恒功率调速
电动机容量可按起吊额定起重量在工作循环内发热计算确定,但应进行过载校验 起升机构不应采用开式齿轮传动. 小车运行机构 小车运行机构工作级别宜为M6、M7
3.7.2.1 10
GB/T14783一2009 3.7.2.2运行静阻力应符合GB/T3811中的相关规定,其中等效坡度阻力应包括主梁拱度阻力、道路 坡度阻力,轮胎变形坡度阻力等 3.7.2.3小车运行机构起动或制动的加(减)速度值及相应的加(减)速时间按GB/T3811的相关规定 选取 3.7.3大车运行机构 3.7.3.1大车运行机构工作级别宜为M5、M6
3.7.3.2大车运行速度一般可分空载(仅载吊具)运行速度和满载运行速度
载箱运行是作倒箱短距 离移位,其速度值宜不小于25m/min. 3.7.3.3大车运行机构应具有保持起重机直线行驶的纠偏装置,当大车运行车轮偏离行走中心 300mmm 时,大车运行距离在9m内应能纠正 大车运行机构可转向90"后直线行驶,90"转向系在空载、大车不运行工况下,并宜在指定地点 特定路面下进行
大车运行机构制动器应有简便的机械方式能使制动器处于释放状态,以便拖运起重机
在未采用定袖转向的起重机上,应装设手拉装置使轮胎各自可转至小于的任何一角度
3.8动力装置 起重机的动力装置可为柴袖发电机组,亦可采用由电力通过电缆卷简或高架滑触线等型式为其 提供动力,或是两者的组合形式
3.8.2如采用柴油发电机组为动力装置,应满足下列要求 a在发动机附近应设置操纵发动机起动、停车装置,司机室内应设置停车装置; b) 发动机燃油油箱容量应能保证起重机36h工作的需要,并应有明显标志油位的指示器 e)发动机除自带充电设备外,另应装设可用岸电充电的设备
集装箱吊具及回转、减摇装置 33 .9.1集装箱吊具应能装卸GB/T1413规定的国际集装箱,其转锁的位置尺寸和公差应不低于 /T GB 3220的规定
3.9.2伸缩吊具本体的伸缩臂或横梁处应设有可对大宗件货进行装卸用的吊耳
3.9.3伸缩吊具宜采用具有上架的结构,吊具上架可与吊具本体分开,两者之间用易拆装的转锁或销 轴连接
3.9. 吊具转锁热处理加工后,应进行无损探伤检查,不应有裂纹,并不应修补
3.9.5吊具离地面2.4m时,吊具应在水平平面内按纵向中心线可进行回转士5
3.9.6起重机宜装设能抑制吊具或吊具与集装箱摇摆的减摇装置
3.10司机室 司机室应符合GB/T20303.5的相关规定
3. ..11液压系统 .11.1液压系统应符合GB/T3766中的规定
3. .11. 2 液压系统装配前,接头,管路及通道(包括铸造型芯孔、钻孔)应清洗干净,不许有任何污物(铁 屑、毛刺、纤维状杂质等 .11. .3 主要液压元件油泵、,油缸、阀类等)应有制造厂出具的合格证书
3.11.4液压系统应有防止过载和冲击的安全装置溢流阀调整压力应不大于系统额定工作压力 的110%.
3.11.5油箱应有足够的容量,在无冷却装置下,液压油的循环周期应不少于2 min, ,工作油温应不超 过70C 12 电气设备 3. 3.12.1电气设备设计及选择应符合GB/T3811的有关规定 1l
GB/T14783一2009 3.12.2电气设备和电气元件应适用于港口等工作环境,并符合工作级别和工作制度的要求
3.12.3电气设备应有良好的绝缘性能,用500V兆欧表测量:电动机、电阻器的绝缘电阻冷态时不低 于1MQ或热态时不低于0.5MQ;控制柜,操纵台等成套电气设备的绝缘电阻,一次回路不低于1MQ; 二次回路不低于0.5MQ;单独的电器元件绝缘电阻不低于1.5MQ
3.12.4交流和直流的不同电压等级的导线都宜分开敷设
3.12.5除动力传动控制屏与控制台等成套设备内应用聚叙乙烯塑料绝缘铜芯软线外,其余宜采用绝 缘多股铜芯电缆
动力回路的导线截面应不小于2.5mm=,控制照明回路的导线截面应不小于 1.5mm';装有电子设备控制柜的导线截面应不小于0.2mm 吊具电缆应选用特殊的挠性多芯软电缆,并应在吊具上架和吊具本体之间设置多芯插头与插 座,以便吊具快速更换
3.12.7所有连接导线两端应有与原理图、配线表一致的明显编号,标明线号、线束号、去向等
3.12.8小车供电应保证拖带电缆时轻便,灵活,并应保证电缆的弯曲半径在允许的范围内
3.12.9电气房的照明度应不低于50lx;主要通道及扶梯平台人口处的照明度应不低于20lx;作业面 的照明度应不低于50lx,司机室的照明度应不低于50lx
直流电路系统中应设有过流,过压,失磁、零位等保护 3 12.10 交流电路系统中应设有短路、过载、失压、漏电、缺相等保护
3 12.11 12.12起重机应可接岸电,以供设备预热、维修及照明等用
3 3. .13 安全保护装置 3 超速,超载限制器 13. 3. 当起升载荷达到额定起重量的100%时,应能发出提示性报警
13.1. 3. 13.1.2当起升载荷达到额定起重量的110%时应自动切断上升电源,但可下降放下物件
33. 13.1.3当升降速度超过空载额定升降速度的115%时,超速装置应能切断起升电动机电源
3.13.2极限保护装置" 3.13.2.1应装设上升终点前减速、上升终点停止、上升极限位置停止、下降终点前减速、下降终点停止 的限位位置保护
3.13.2.2小车运行机构两端均应装设终点前减速、终点停止、终点极限位置停止的安全保护装置,以 及缓冲器和车轮的车挡等
3.13.3联锁保护装置 3.13.3.1大车运行机构与大车转向机构应装设联锁保护
如车轮锁销全部退出后方可转向;车轮锁 销全部进销后方可允许大车运行等
3.13.3.2吊具着箱后,起升机构应切断下降电源,绳索不再继续下降
3.13.3.3吊具吊起集装箱后,吊具应不能伸缩、转锁应不能转动,大车应不能转向
3.13.3.4吊具转锁当未全部进人集装箱顶角件孔穴时,转锁应有防止转动的联锁装置
3. .13.3.5当吊具上架与吊具本体连接件拆卸后,吊具电缆插头仍插人吊具本体的插座时,应设有吊具 上架不能起升的联锁装置;当吊具上架与吊具本体连接件装妥后,吊具电缆插头未插人吊具本体插座 时,应设有整个吊具不能起升的联锁装置
13.4防触箱装置 起重机应设大车运行防触箱装置,当起重机与集装箱碰撞之前,应能发出讯号报警,并立即切断继 续向前运行电源,但可倒退行驶
" ..13.5防台风系拉设施和楔块 3.13.5.1起重机宜设置防台风系拉设施,抗风能力应满足JT/T90的要求,防台风系拉设施应始终 保持良好的技术状态 3.13.5.2为防止由于风载荷引起起重机沿路面滑移,应设置楔块
12
GB/T14783一2009 3.13.6报警装置 3.13.6.1起重机应设置风速报警器,并宜有瞬时风速的显示能力
3.13.6.2起重机应设置声光报警器,运行时应能发出报警声光信号 3.13.7灭火器 起重机应在电气房、发动机房,司机室附近设置灭火器 3.13.8发动机保护装置 发动机应配备冷却水温过高、机油压力过低和超速等的保护装置
3.13.9故障监视诊断装置 应设置有效的故障监视诊断装置以便及时报警,确保安全作业,缩短排除故障时间 3.13.10急停装置 在司机室、小车、电气房与发动机一侧的扶梯口,都应装有事故紧停按钮,可在紧急状态下切断动力 电源 14涂装和外观 3. 3.14.1表面处理 在涂装前构件表面应进行除铁锈、焊渣、毛刺、灰尘油脂、盐、污泥、氧化皮等预处理,以保证 3.14.1.1 表面光滑平整
除锈质量等级按GB/T8923的规定用手工方式除锈为st3级,用化学处理和抛(喷)丸(或 其他磨料)方式除锈为sSa2级 3.14.1.3表面处理后4h内应喷涂一道干膜厚度为15am~20Am的底漆,作为钢材预处理后的短期 保护,在正式涂层开始涂装时,需进行二次表面处理去除
3.14.2涂层与漆膜厚度 涂层、涂料品种、最低干膜厚及道数见表4
表4 涂层 涂料品种 最低干膜厚/am 道数 底涂层 环氧富锌底漆 60 100 环氧后浆读 中间涂层 面涂层 脂肪族聚氨酯面漆 60 总干膜厚度 220 3. 14.3涂装颜色 产品的安全标志颜色应符合GB2893,GB2894的规定
3.14.4漆膜附着力 涂层的漆膜附着力应不低于GB/T9286中规定的1级
3.14.5外观 起重机外观质量应达到 零,部件表面不应有明显变形及损伤,应平整,无粘砂和余留冒口,焊缝要均匀美观 a b油漆色泽均匀,设有涂斑、漏漆和剥落; 紧固件无松动漏装; c 管线排列整齐; 不应有油液外露; f 标牌、性能表牌、吊装标志和功能标志应齐全,安装位置应合理,表示应清楚
13
GB/T14783一2009 试验方法 4.1试验条件 4.1.1试验时风速不超过13.8m/s,环境温度为一-20C十40C,相对湿度不大于95%,有凝露
试车场地应水平坚实,坡度不大于1%,跨度两侧行走通道,地面坡度应同向,即同为上坡或 下坡 如采用轮胎原地转向,转向试验场地表面应光滑,轮胎转向处应垫钢板或采用高标号水泥路面
轮胎的工作压力应符合3.6.8的规定
燃油、润滑油、液压油和冷却液应按使用要求装至工作液面,油的品质应符合设计规定的要求
41.试验载荷应标定准确,其允许偏差为土1%. 4.2整机调试和试验准备 4.2.1试验前应进行静态检查,所有构件,机构及附属装置的安装是否准确、可靠
4.2.2所有金属结构件的焊接及高强度螺栓的连接应牢固
4.2.3各传动件、紧固件及钢丝绳端部连接应牢固可靠
4.2.4检查液压系统中液压元什与管路固定及与管路间连接时密封性和可靠性
4.2.5检测电气设备(电动机.电阻器、电器元件.电缆等)的绝缘电阻值
2.
检刮柴油机的新定转通、发电机电压,检套可机室内停车装置是否正常.灵敏
427各机糊教设计要求两试完华后,结树和传动件均能正常工作,整机无异常现象
4.2.8检查和调试所有安全保护装置
通过三次试验,确认安全保护装置的动作灵敏性、可靠性及准 确性
4.3空载试验 4.3.1几何参数测定 测量起重机有关尺寸,以三次测量的算术平均值作为测定数据 a)跨距,基距、大车行走轮轴距; b) 内净空即起重机门框内部宽度方向的通过尺寸; e)整机外形尺寸即全长,全宽、全高
4.3.2起升机构 4.3.2.1将起升机构上升到极限位置,测量起升高度
4.3.2.2将起升机构上升到极限位置,试验上升极限位置停止保护装置的可靠性
4.3.2.3测定空载起升(下降)速度和电机的电流、电压及转速值
测取空载下吊具以最高速度起升 (下降),吊具稳定运行通过10m行程所需的时间,以三次测量的算术平均值作为起升(下降)速度
4.3.2.4将起升机构上升(下降)到极限位置,检查上升(下降)终点前减速性能
4.3.2.5吊具升降时观察吊具的电缆储放情况,应保证电缆储放正常
4.3. 3 小车运行机构 4.3.3.1将小车分别运行至主梁两端终点极限位置,试验小车在主梁两端终点前减速、终点停止、终点 极限位置停止的安全保护装置的可靠性,并测量小车行程
4.3.3.2测定小车的空载运行速度和电机的电流、电压及转速值
测取空载下小车以最高稳定速度运 行通过10m行程所需的时间以三次测量的算术平均值作为小车运行速度
4.3.3.3检查小车车轮与轨道接触情况,运行时不应出现啃轨现象
检查小车供电电缆跟随小车运行情况,运行时应轻便、灵活、平稳
4.3.4大车运行机构 4.3.4.1测定大车的空载运行速度和电机的电流、电压及转速值
起重机沿轨道以最高速度运行,测 量空载下整机稳定通过10m行程所需的时间,以三次测量的算术平均值作为大车运行速度
14
GB/14783一2009 4.3.4.2测定大车运行的纠偏效果
使大车运行车轮偏离行走中心300mm,测取纠正后大车的运行 距离
试验大车防触箱装置的可靠性
4.3.4. 3 4.3.5转向机构 4. 3.5.1小车停在主梁中部,将车轮从0'一90"和90"~0"转向各两次,测定车轮转向时间与液压系统 工作压力
4.3.5.2检查大车运行机构与大车转向机构的联锁保护装置的可靠性
有定轴转向或手控分别转向的起重机,也应按其设计要求进行试验
4.3.6集装箱吊具及回转,减摇装置 4.3.6.1测定集装箱吊具转锁间距和对角线距离公差值
4.3.6.2检验吊具联锁的可靠性 检验吊具上架与吊具本体连接处和起升机构联锁的可靠性
4.3.6.4测量伸缩吊具的伸缩时间,观察转锁“开”“闭”指示的准确性
4.3.6.5测定吊具离地2.4m,吊具按其水平纵向中心线向两侧各偏转的角度,以三次测量的算术平 均值作为吊具回转角度,并测量偏转所需时间和液压系统压力
4.3.6.6观察吊具在升降过程中,减摇钢丝绳是否能及时跟踪 4.3.6.7小车运行制动后,应有明显的减摇效果,测定小车制动5s后吊具的最大摆幅
静载试验 试验前可调整超载限制器、制动器等,但试验后应调回到规定的数值
4.4.2试验时小车应停在主梁中部,先起吊额定载荷,离地100mm~200mm,然后无冲击地逐渐加载 至1.25倍额定起重量,并停留10min. 4.4. 3 测定起吊1.25倍额定起重量时主梁中部的下挠值和轮胎压缩量
4.5额定载荷试验 4.5.1测定在额定载荷下的起升速度、小车运行迷度、大车运行速度和各自电机的电流、电压及转迷 值,其试验方法可参照4.3.2.3、4.3.3.2和4.3.4.1
4.5.2测定在额定载荷下吊具回转角度,其试验方法可参照4.3.6.5
4.5. 测定在额定载荷下的减摇效果,其试验方法可参照4.3.6.6和4.3.6.7
.3 4.5.4进行额定载荷下起升、小车运行试验三次,试验过程中,起升、小车制动各三次
4.5.5测定起吊额定起重量时主梁中部的下挠值和轮胎压缩量,其试验方法可参照4.4.2
4.6动载试验 4.6.1起重机应按操作规程进行控制,各机构均为中挡速度或2/3高速运转
4.6.2起重机作升降运动三次,其中中间制动二次,小车前后运行三次、吊具回转三次,并作大车往返 运行等动作
批量生产中,应抽一台作紧忽制动试脸. 4.6.3 4.7 可靠性试验 4.7.1距起重机横行方向约30m长范围内选一试车场地,进行起重机起吊额定载荷模拟作业试验
4.7.2每连续10次作业循环后,大车空载运行30m远,再回原地继续进行作业
4.7.3每2h左右,将大车运行至转向点进行90"转向,并横向行走6m,再回至转向点,将行走轮转 回,再运行至原地,继续进行作业
作业循环中各种运动皆以最大加迷度和最大迷度进行工作
4.8轮压和质量参数测定 4.8.1非工作轮压;小车位于动力装置一侧的工作极限位置,集装箱吊具无负荷,测量各车轮负荷值
4.8.2工作轮压;小车位于动力装置一侧的工作极限位置,集装箱吊具载有额定起重量的物件,测量各 车轮负荷值
15
GB/T14783一2009 4.8.3集装箱吊具质量:如集装箱吊具系由吊具上架与吊具组合时,则应分别测出其质量
4.8.4起重机总质量:在吊具无载荷时测定
4.9噪声测定 起重机作业时,在司机室内和发动机一侧进行噪声测定,其测量方法应符合GB/T16710.2~ GB/T16710.5的规定
4.10金属结构应力测定 4.10.1 主梁,支腿、鞍梁、小车架横梁、大车平衡梁、吊具本体、吊具外伸梁等主要结构件应进行应力 测定
4.10.2分别以额定载荷、动载(1.1倍额定载荷、偏载(额定载荷重心与箱体形心距其纵向方向偏离 箱体长度的10%),在额定工作速度时进行应力测定,试验的测量次数为三次,取三次测量的算术平均 值作为测量值
以静载(1.25倍额定载荷)且各工作机构为非工作状态时进行应力测定,试验的测量次数为三 4.10.3 次,取三次测量的算术平均值作为测量值
4.11工业性试验 工业性试验中将作业日期、作业时间、吊运箱数量、故障情况等填人表A.1中 4.11.2做模拟性试生产时,每吊运10箱后,大车移动两个箱位距离且每天至少进行90"转向两次
在试验前、吊运3000箱.5000箱时,分别对起重机的主要技术性能进行阶段性的测定,测定 数据记人表A.2中
4.11.4工业性试验后应对主要易损件和运动部件以及发生异常的部分进行拆检,并对检查测量零件 的结果记人表A.3中
4.11.5工业性试验应由制造厂和用户共同负责记录数据和进行试验总结,对试验期间起重机出现的 任何不正常现象或事故应详细记录并提出分析和处理意见
检验规则 5.1型式检验 5.1.1有下列情况之一时,应进行型式检验 a)新产品或老产品转厂生产的试制定型鉴定; 正式生产后,如结构、材料、工艺有较大改变,可能影响产品性能时 b) e) 产品停产达三年以上后,恢复生产时; d 出厂检验结果与上次型式检验有较大差异时 e)国家质量监督机构提出进行型式检验要求时
5 1. 2 型式检验项目见表5
出厂检验 55 2 5.2.1每台起重机都应进行出厂检验,检验合格后(包括用户特殊要求检验项目)方能出厂,出厂产品 应附有产品合格证明书
.2.2出厂检验项目见表5
55 表! 5 检验分类 序号 检验项目 检验要求 试验方法 出厂检验 型式试验 安全保护装置可靠性 3.13 4.2.8 3.12
电气设备的绝缘电阻值 4.2.5 几何参数测定 3.3.6和3.3.7 4.3.1 16
GB/T14783一2009 表5(续 检验分类 序号 检验项目 检验要求 试验方法 出厂检验 型式试验 各机构运行速度 3.3.1、3.3.2和3.3.3 4.3.2.3、4.3.3.2和4.3.4. 起升高度及极限位置 3.3.5和3.13.2.1 4.3.2 保护 小车极限位置保护 3.13.2.1 4.3.3.1和4.3.3.2 大车运行纠偏 3.7.3.3 4.3.4.2和4.5.3 大车转向机构 3.7.3.4 4.3.5 吊具转锁间距和对角线 3.9. 4.3.6.1 距离 3.9.5 4.3.6.5和4.5.2 吊具回转角度 10 11 吊具减摇装置 3.9,6 4.3.6.6、4.3.6.7和4.5.3 12 额定载荷试验 3.2. 4.5 13 静载试验 3.2.3 14 动载试验 3.2.5 4.6 可靠性试验 15 3.2.6 4.7 16 轮压和质量参数测定 17 3.2.2 4.9 嗓声测定 18 金属结构应力测定 3.2.7 4.10 19 工业性试验 3.2.8 4.11 标志和运输 6.1标志 6. .1.1每台产品应在主梁和吊具上装设醒目的起重量标志
6.1
应在起重机支腿的适当位置装设产品标牌
产品标牌的型式及尺寸应符合有关标准的规定,并 应包括下列内容: 产品型号和名称 a 制造厂名称; D e)主要技术参数 d 产品编号; 制造日期
6 在司机室内应装设主要参数表标牌
6 各种操纵手柄、开关及信号装置近旁,应装设指示功能的标牌,并应表示位置和控制方向
运输 6.2. 产品的运输应符合铁路、公路、航运的有关运输要求
在解体运输中,对长大件和可自由移动的部件,应垫平绑扎牢固,防止运输变形、移位、碰撞
在起重机整机吊运中,应防止小车在主梁上移位和起重机在船上的移位,并应防止门架变形等
17
GB/T14783一2009 附录A 资料性附录 工业性试验记录表格 工业性运转试验日报 工业性运转试验日报见表A.1
表A.1工业性运转试验日报 吊运箱次 装载总质量 起止时间 集装箱规格 停机原因 备注 空箱 重箱 总数 纯作业时间 发动机运行时间 故障停机时间 柴油消耗量/电消耗量 lg/wh 操作人 填报人 日期 日期 A.2技术参数测量值 技术参数测量值见表A.2
表A.2技术参数测量值 时间 机构 负载 方向 设计速度 测量行程 实测速度 备注 平均 起升 空 下降 起升 起升 下降 前 空 后 小车运行 前 满 左 空 右 大车行走 左 有 8
GB/T14783一2009 表A.2(续) 时间 机构 负载 方向 设计速度 测量行程 实测速度 备注 平均 0"90° 大车转向 空 90"0 前 空 后 吊具回转 前 后 伸出 吊具伸缩 空 缩回 A.3拆检零件实测记录 拆检零件实测记录见表A.3
表A.3拆检零件实测记录 件 数 项 数 原图要求 实测数据 备 零件名称 注