GB/T35079-2018
多向精密模锻件工艺编制原则
Multi-wayprecisiondieforgings—Technologicaldesignprinciple
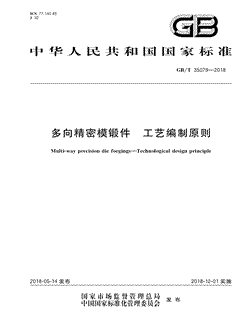
- 中国标准分类号(CCS)J32
- 国际标准分类号(ICS)77.140.85
- 实施日期2018-12-01
- 文件格式PDF
- 文本页数11页
- 文件大小817.67KB
以图片形式预览多向精密模锻件工艺编制原则
多向精密模锻件工艺编制原则
国家标准 GB/T35079一2018 多向精密模锻件工艺编制原则 Mtiwaypreecisiondieforgings一Iechnologiealdesignprineiple 2018-05-14发布 2018-12-01实施 国家市场监督管理总局 发布 币国国家标准化管理委员会国家标准
GB/35079一2018 目 次 前言 范围 2 规范性引用文件 术语和定义 编制原则 附录A规范性附录典型材料锻造温度范围要求 附录B规范性附录模具硬度要求
GB/35079一2018 前 言 本标准按照GB/T1.1一2009给出的规则起草
本标准由全国锻压标准化技术委员会(SAC/TC74)提出并归口
本标准起草单位;二十二冶集团有限公司、二十二冶集团精密锻造有限公司北京机电研究所
本标准主要起草人:刘璀、李明权、李景生、周林、金红、宋昌哲徐文翠、周丽娟、魏巍
GB/35079一2018 多向精密模锻件工艺编制原则 范围 本标准规定了采用多向模锻工艺成形的精密模锻件(以下简称“锻件”)的工艺编制原则
本标准适用于质量不大于1250kg且外形尺寸不大于1500mm的采用多向模锻工艺成形的 锻件
规范性引用文件 下列文件对于本文件的应用是必不可少的
凡是注日期的引用文件,仅注日期的版本适用于本文 件
凡是不注日期的引用文件,其最新版本(包括所有的修改单)适用于本文件 GB/T702热轧钢棒尺寸、外形、重量及允许偏差 GB/T908锻制钢棒尺寸、外形重量及允许偏差 GB/T8541锻压术语 GB13318锻造生产安全与环保通则 GB/T33879多向精密模锻件通用技术条件 术语和定义 GB/T8541界定的以及下列术语和定义适用于本文件
3.1 多向模锻工艺multiwaydieforgingprocess 采用多向模锻成形设备,在闭式模腔内对坯料进行多方向联合挤压、锻造的成形工艺
3.2 多向精密模锻件multiwaypreeisiondieforgings 在工艺温度范围内,通过专用模具,采用多向模锻技术获得的高精度、满足产品要求的精密模锻件
编制原则 4.1总则 4.1.1工艺编制应综合考虑锻件材质、锻件形状复杂程度、质量要求、形位公差、尺寸精度、设备能力、 成形方式、变形程度、模具寿命等因素
4.1.2工艺设计应遵循材料的变形规律,以锻件材料的变形抗力及流动应力为基础
可采用数值模拟 等方法对工艺过程和参数进行优化
4.1.3工艺设计应利于模具的设计、制造和成本的降低,应利于生产现场快速换模和实现自动化
4.1.4工艺设计应利于金属填充和锻件脱模
4.1.5下料质量计算应充分考虑坯料在不同加热环境下的氧化烧损情况,避免下料质量不准确造成锻 件填充不满或胀模
4.1.6应确保各个工序衔接流畅降低转运时间对坯料温度的影响
GB/T35079一2018 4.1.7应尽量减少加热次数,宜采用一次加热锻造成形
4.1.8坯料应去除氧化皮
应选择合适的润滑剂及喷涂方式,避免锻件被拉伤以及模具提前失效
4.1.9应考虑坯料在模具型腔的定位、工件的放人取出、设备的精度及偏载等
4.1.10应合理安排模具各部位参与成形的顺序,速度和位移量,防止锻件出现折叠等锻造缺陷,且应 利于圆角等过渡部位的填充
4.1.11工艺编制应充分考虑企业生产制造流程,便于物料流转,利于生产成本控制
4.1.12锻造生产车间作业环境,设备、工装及锻造过程的安全和环保应满足GB13318的要求
4.2锻件设计原则 4.2.1分模面选取 4.2.1.1 锻件分模面的选取应利于锻件脱模,金属充填型腔及模具加工 锻件分模方式可采用水平分模,垂直分模、联合分模等方式
阀门阀体(含带水平法兰),三通 4.2.1.2 弯头、变径管等锻件宜采用水平分模方式[见图1a).,b).e).d];带上(下)端面法兰的阀门阀体锻件宜 采用垂直[见图1e)]或联合分模方式[见图1]
a b) 水平分模带水平法兰阀门阀体 水平分模三通 水平分模弯头 水平分模(变径管 垂直分模(四通 联合分模(带上法兰阀门阀体 d 分模形式示意图 4.2.2机械加工余量 锻件机械加工余量应符合表1、表2的要求
GB/35079一2018 表1锻件表面单边机械加工余量 单位为毫米 锻件质量 kg 锻件部位 >560 >60300 >300700 >700~1250 端面 1015 8~10 3一5 8 其余部位 a5 底面余量可取较小值
表2锻件内孔直径的单边机械加工余量 单位为毫米 孔深 孔径 2060 >60100 >100200 >200300 >300400 >400~600 3060 >60100 23 >100~150 23 34 46 >150200 23 3~4 6 68 >200300 2 3~4 h 810 4.2.3锻件尺寸公差 锻件尺寸公差应符合GB/T33879规定的要求 4.2.4模锻斜度、圆角半径、孔深 锻件的模锻斜度、圆角半径及孔深应符合GB/T33879规定的要求
4.3主要工艺参数确定 4.3.1变形和加热温度 4.3.1.1 变形温度的选择应有利于提高锻件材料的成形性及获得良好的锻后组织
典型材料的锻造温 度见附录A 坯料加热时间以坯料均匀达到始锻温度为依据
对热传导系数较低的材料宜采用阶梯加热保 4.3.1.2 温的方法,在满足加热要求的前提下减少金属氧化和表面脱碳
4.3.2变形力 4.3.2.1可采用数值模拟方法计算各阶段变形力
4.3.2.2锻造带内孔的锻件时,应合理分配各方向挤压力,以防凸模承受过大偏载力而断裂
4.3.2.3合模力的大小应保证锻造过程中模具不胀开,锻件不形成毛刺
4.3.3锻造工步 4.3.3.1阀门阀体(含带水平法兰、三通等结构锻件一般采用合模一垂直方向穿孔(挤压)一水平方向 穿孔(挤压)的成形方式,如图2所示
GB/T35079一2018 上凸模 上凸模 上凸校 凹模 上凹模 上凹模 坏料 区件 工件 左凸模 左凸 右凸模 左凸模 右凸模 凸模 F凹校 下凹模 下凹模 b 合模 垂直穿孔 水平穿孔 a 图2三通阀体锻件锻造工步示意图 4.3.3.2变径管等锻件主要采用合模一水平方向穿孔(挤压)的成形方式,如图3所示
上凹模坯料 右凸模 左凸模上四模工件 右凸模 左凸模 工 下凹模 下凹校 合模 水平穿孔 a b 图3变径管锻件锻造工步示意图 带上(下)端面法兰的阀门闵体锻件主要采用垂直合模 4.3.3.3 -垂直方向穿孔(挤压)水平方向穿孔 挤压)的成形方式,如图4所示
上凸模 上凸模 上凸模 坯料 工件 左凹模 工件 左凹校 左凹模 右凹校 右凹模 右凹模 看凸极 左马楼 左凸模 左凸模 右凸模 右凸模 下凹模 下凹模 下凹模 垂直合模 垂直穿孔 水平穿孔 b e 图4带主法兰三通锻件锻造工步示意图 4.3.3.4锻造工步可采用数值模拟进行优化,保证锻件易于成形,无缺陷,且锻件金属流线完整
GB/35079一2018 4.4模具 4.4.1 一般要求 4.4.1.1凹模宜采用镶嵌组合结构形式,凸模宜采用分段组合结构形式
4.4.1.2应有导向机构,合模后模腔错移量应符合表3规定
表3模腔错移量 单位为毫米 锻件质量 >5200 >200700 >700l250 kg 0.3 0.5 S0.6 错移量 4.4.1.3凸模可进行TD处理、渗氮等表面硬化处理,提高模具使用寿命
4.4.1.4模具尺寸设计时应考虑热膨胀
模具精度应满足锻件的尺寸、形位公差等要求
4.4.1.5应根据工艺要求选择合适的模具材料,模具硬度等力学性能应满足工艺要求,见附录B. 4.4.2预热、润滑、冷却 4.4.2.1模具应预热,预热温度一般控制在150C200C之间
生产过程中模具温度一般控制在 00C一400C之间
4.4.2.2生产过程中应对模具表面喷涂润滑剂,润滑和冷却模具表面;润滑剂的选择应充分考虑锻件材 质、,成形方式、工况条件、模具温度变化等因素;润滑剂在使用中应易于清理且满足环保要求
4.4.2.3结构较复杂模具的润滑及冷却可通过采用半自动或自动喷涂装置实现,保证模具型腔及凸模 的充分润滑和冷却
模具冷却亦可采用模具内部冷却等方式
4.5下料 4.5.1根据锻件形状及技术经济要求,原材料宜选用棒材
棒材的尺寸、外形、质量应满足GB/T702、 GB/T908的要求
4.5.2用于生产的原材料应进行复检,复检项目应至少包括化学成分、尺寸,外形表面质量,必要时应 进行超声波检测
4.5.3宜采用锯切方式下料,应去除料头、料尾
需要时应增加去毛刺、剥皮或其他改善坯料表面质量 的方法
4.5.4坯料应称重,其下料质量允许偏差范围宜符合表4规定
表4坯料质量允许偏差 坯料质量 >5一20 >2060 >60150 >150300>300500>500~750>7501250 kg 质量偏差 02.5 01.2 01 01 01 01.5 4.6氧化皮处理 热坯料表面的氧化皮应予以清除,清除方式不应降低表面质量,宜采用高压水清理的方式
GB/T35079一2018 4.7锻造 4.7.1应根据坯料材质、形状、规格、生产批量和环保要求选取适合的加热设备
4.7.2坯料加热规范的制定应综合考虑材质,形状,规格、生产节拍、生产成本等各方面因素
4.7.3锻造过程中一般采用位移和压力联合控制的方式,凹模合模应采用压力控制,上凸模宜采用位 移控制,参与锻件最终成形的凸模宜采用压力控制方式
4.7.4应根据锻件材质、规格、最大散热面积等确定锻件合理的冷却方式
4.8锻件表面清理 锻件表面的氧化皮及工艺混合物应予以清除,清除方式不应降低表面质量,改变材料性能或金相组 织等,一般可采用抛丸、喷砂等方式
4.9锻件缺陷及处理 锻件内部不应有裂纹,折叠,穿流等影响锻件内在质量的缺陷
4.9.1 49.2锻件的表面缺陷类型一般有结疤、折叠、皱裂、凹坑、刻痕、擦伤等,合格锻件不应有集中的,连续 的或线状的表面缺陷
锻件可通过检测缺陷深崖表征表面缺陷程度
眼件的表面缺陷深度达到零件的最小壁厚时为 4.9.3 有害缺陷
锻件的主要表面缺陷及处理方法见表5
4.9.4锻件允许焊补,需要进行焊补的.焊接工艺过程应评定合格,或应得到需方同意
表5锻件的主要表面缺陷及处理方法 缺陷分类 缺陷类型 缺陷程度 处理方法 有害缺陷 全部 缺陷的深度达到零件的最小壁厚 报废 h<5%D或h<1.6mm,取较小值 不需要修复 结疤,折叠、戳裂 h>5%D或h>1.6mm,取较小值 机加工或打磨 非有害缺陷 h<1.6mm 不需要修复 凹坑、刻痕、擦伤 <锻件最小壁厚 机加工或打磨 1.6mmh 机加工或打磨的去除量应根据缺陷位置的锻件实际壁厚确定;任何情况下,锻件的实际壁厚不应小于规定的最 小壁厚值
注:h 缺陷深度;D 检验位置实际壁厚
GB/35079一2018 录 附 A 规范性附录 典型材料锻造温度范围要求 典型材料锻造温度范围要求见表A.1
表A.1典型材料锻造温度范围要求 始锻温度 终锻温度 始锻温度 终锻温度 材料牌(代)号 材料牌(代)号 20# 1250 750 Al05 1250 750 700 F11 1250 200 800 Q345B 12CrlMov F22 1200 800 200 800 30CrMo 18o 800 F91 1180 850 180 800 850 40CrNi2Mo F304 1180 40CrMnMo 18o 85o0 F321 1180 850 15-5PH 1150 850 LF2 1250 750
GB/T35079一2018 附 录 B 规范性附录) 模具硬度要求 不同材质模具的硬度要求见表B.1
表B.1不同材质模具硬度要求 模具类型 模座套 凹模 凸模 5CrNiMo 材料牌号 40Cr B2 5CrNiMo Hl3 3Cr2W8V 硬度 53(表面硬化 47 33 39 2632 43一49 37 43 47一53 HRC 处理时为5965
多向精密模锻件工艺编制原则GB/T35079-2018详解
多向精密模锻件是一种高级别的锻造技术,适用于各种规格、材质的锻件生产。在这个领域,中国也在不断加强科研力度和技术创新,提高这种锻造技术的应用水平。
2018年,国家发布了一份关于多向精密模锻件工艺编制原则的标准——GB/T35079-2018。该标准以提高产品质量、降低成本、优化生产流程为宗旨,明确了多向精密模锻件的生产工艺以及编制原则,对于推动我国锻件制造产业的高质量发展具有重要作用。
该标准规定了多向精密模锻件的定义、分类、基本要求、工艺流程、工艺参数、模具设计等方面的内容。其中最为关键的是工艺编制原则部分,主要包括以下内容:
- 材料选择:应根据锻件的特性和用途,选择适宜的材料。
- 工艺流程确定:应根据锻件的形状、尺寸以及数量确定最佳的工艺流程。
- 工艺参数设置:应根据锻件的材料、结构、形状、尺寸和数量等因素综合考虑,科学合理地设置各项工艺参数。
- 模具设计:应根据锻件的形状、尺寸、结构等特点进行模具设计,确保锻件质量稳定。
通过GB/T35079-2018标准的执行,可以保证多向精密模锻件的质量和稳定性,提高产品的市场竞争力和用户体验,同时也能促进行业的技术创新和进步。
总之,GB/T35079-2018标准的发布对于我国多向精密模锻件行业来说具有重要的意义。该标准的推广与实施,将有力推动我国锻件行业的高质量发展。