GB/T14541-2017
电厂用矿物涡轮机油维护管理导则
Guideformaintenanceandsupervisionofin-servicemineralturbineoilusedforpowerplants
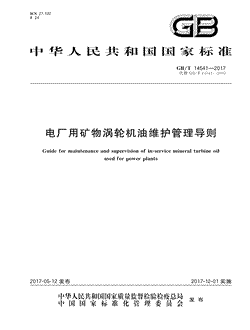
- 中国标准分类号(CCS)F24
- 国际标准分类号(ICS)27.100
- 实施日期2017-12-01
- 文件格式PDF
- 文本页数26页
- 文件大小2.01M
以图片形式预览电厂用矿物涡轮机油维护管理导则
电厂用矿物涡轮机油维护管理导则
国家标准 GB/T14541一2017 代替GB/T145412005 电厂用矿物涡轮机油维护管理导则 Guideformaintenanceandsupervisionofin-seryieemineralturbineoil lsedforpowerplants 2017-05-12发布 2017-12-01实施 国家质量监督检验检疫总局 发布 国家标准化管理委员会国家标准
GB/14541一2017 前 言 本标准按照GB/T1.1一2009给出的规则起草
本标准代替GB/T1454l1一2005《电厂用运行矿物汽轮机油维护管理导则》,与GB/T14541一2005 相比,除编辑性修改外主要技术变化如下: -修改了标准的名称及范围,将汽轮机油修改为涡轮机油 在规范性引用文件中,增减了引用文件; 删除了正文中的“汽轮机油运行寿命的影响因素和汽轮机油严重度”,将此部分内容移人附 录中; -增加了涡轮机油的性能; 修改了新油验收时旋转氧弹的质量指标; -增加了新油验收时应进行检测的项目; 修改了运行油的质量指标及检验周期 修改了关于补油的要求; 增加了关于换油的要求; -修改了运行竭轮机油的维护中关于油处理及漆加剂的内容 别除了附录C润滑油氧化安定性测定法(旋转氧弹法) 本标;准由电力金业联合会提出. 本标准由全国电气化学标准化技术委员会(sAC/Tc322)归口
本标准起草单位;西安热工研究院有限公司,国网安徽省电力公司电力科学研究院、国网福建省电 力有限公司电力科学研究院、内蒙古电力科学研究院
本标准主要起草人;王媚、李烨峰、祁炯、郑东升、乌日娜
本标准所代替标准的历次版本发布情况为: GB/T14541一1993,GB/T14541一2005
GB/T14541一2017 电厂用矿物涡轮机油维护管理导则 范围 本标准规定了电厂汽轮机、水轮机和燃气轮机系统用于润滑和调速的矿物涡轮机油的维护管理;调 相机及给水泵等辅助设备所用的矿物涡轮机油的维护管理也可参照执行
本标准适用于电厂汽轮机、水轮机和燃气轮机系统用于润滑和调速的矿物涡轮机油的维护管理 本标准不适用于各种用于汽轮机润滑和调速的非矿物质的合成液体
规范性引用文件 下列文件对于本文件的应用是必不可少的
凡是注日期的引用文件,仅注日期的版本适用于本文 件
凡是不注日期的引用文件,其最新版本(包括所有的修改单)适用于本文件
GB/T264石油产品酸值测定法 GB/T265石油产品运动粘度测定法和动力粘度计算法 GB/T267石油产品闪点与燃点测定法(开口杯法 GB/T3536石油产品闪点与燃点测定法克利夫兰开口杯法 GB/T7596电厂用运行中汽轮机油质量标准 GB/T7597电力用油(变压器油、汽轮机油)取样方达 GB/T7600运行中变压器油水分含量测定法(库仑法 GB/T7602.1变压器油、汽轮机油中T501抗氧化剂含量测定法第1部分:分光光度法 GB/T7605运行中汽轮机油破乳化度测定法 GB/T8926在用的润滑油不溶物测定法 GB1l120涡轮机油 11143加抑制剂矿物油在水存在下防锈性能试验法 GB GB/T12579润滑油泡沫特性测定法 DL/T429.1电力系统油质试验方法 透明度测定法 电力系统油质试验方法运行油开日杯老化剥定试 DL/T429.6 DL/T429.7电力系统油质试验方法 油泥析出测定法 DL/T432电力用油中颗粒污染度测量方法 SH/T0168石油产品色度测定法 SH/T0193润滑油氧化安定性测定法(旋转氧弹法 SH/T0308润滑油空气释放值测定法 erospacefluidpower Contaminationclassificationfor SAEAS4059F颗粒污染度分级标准(Ae hydraulicfluid ASTMD6971用线性扫描伏安法测量无锌涡轮机油中受阻酚和芳香胺抗氧化剂含量的标准试验 tandardtestmethodformeasurement 方法(Sta ofhinderedphenolicandaromaticamineantioxidantcon tentinnon-incturbineoilbylinearsweepvoltammetry 涡轮机油的性能 3.1多数涡轮机油由高度精炼的石蜡基矿物油复合抗氧化和防锈剂而成,依据其质量等级的不同,也
GB/T14541一2017 可能存在少量的其他添加剂,如金属钝化剂、极压添加剂和消泡剂
涡轮机油的主要功能是润滑和冷却 轴承及齿轮
在有些设备中,涡轮机油也可充当调速液压油
3.2新涡轮机油应具有良好的抗氧化性,并提供足够的防锈性、抗乳化性以及抗泡沫特性,同时能抑制 油泥和漆膜沉积物的形成
影响涡轮机油使用寿命的因素有:系统的类型和设计、油系统运行前条件、 原始油的质量、系统的运行条件、油品受污染状况、补油率以及油品的处理和存储条件(参见附录A)
对于给定的涡轮机,所有上述影响因素的组合决定其严重程度
汽轮机系统的严重程度越高,给定油的 运行寿命越短
确定汽轮机严重程度的有效方法参见附录B. 取样 4.1取样点的设置及选择 4.1.1应在冷油器出口,油箱底部、油系统过滤器的前、过滤器后及回油母管的管道上设置取样点
4.1.2油箱底部除应有放油口外,应单独设置专用取样点
4 .1.3取样点应支持重复性及代表性取样,测定结果与采样位置有关
4.2取样容器 4.2.1常规试验取样容器宜为500ml 1000mL磨口具塞玻璃瓶,参照GB/T7597要求准备 4.2.2颗粒污染等级取样容器应使用250mL专用取样瓶,参照DL/T432要求准备
4.2.3非玻璃的容器应使用耐油的材料(包括衬垫,铝笋制成的瓶盖衬垫)
4.3新油交货时的取样 43.1新油以桶装形式交货时取样桶数和方法应按GB/T7597方法逃行
应从可能污染最严重的底 部取样,必要时可抽取上部油样;如怀疑大部分桶装油有不均匀现象时,应对每桶油逐一取样,并应核对 每桶的牌号、标志,同时对每桶油进行外观检查
4.3.2新油以油槽车方式交货时,应从下部阀门处取样
取样时应先擦净阀门处导管
必要时还应抽 检上、中部的油样
4.3.3船装交货时,应用外接软管或从船舱下部取样,也可采用从专用船装油箱中取样的方式
4.3.4用外接软管取样或从油箱底部的阀门导管处取样,应在取样前将这些管道用油冲洗后才能进 行,同时取样时应维持一定的流速
4.3.5新油验收,一般应取两份以上样品,除试验所需用量外,应保留存放一份以上样品,以备复核或 仲裁用
4.3.6用于颗粒污染等级测试的样品不得进行混合,应对单一油样分别进行测试
4.4运行油的取样 4.4.1用于监督试验的运行油应从冷油器出口取样;检查油中杂质和水分时,应从油箱底部取样;当系 统进行冲洗时,应增设管道取样点
4.4.2从回油母管中取样时,管道中的油应能自由流动而没有死角
取样前,取样口应用油进行冲洗 冲洗用的油量取决于取样管道的长度和直径,应不低于取样管道容积的两倍
冲洗油应收集到废油桶 中统一处置
4.4.3若发现所取样品有异常情况时,应从不同的取样位置再次取样,以跟踪污染物的来源或查找其 他原因
出现下述几种情况的样品不具有代表性 a 所取样品与系统中油温度相差较大; b 油液颜色与所取油样颜色不一致或差异较大;
GB/14541一2017 取自储油箱的样品,在同一温度下黏度差异较大
4.5样品标记 取样瓶上应贴好标签,标签应至少包括下述内容;单位名称、机组编号、油的黏度等级、取样部位、取 样日期、取样人以及备注
4.6样品保存 如果取样后不能立即测试,所取样品应避光,且在阴凉处存放
新油的验收 5.1在新油交货时,应按照GB11120标准对油品进行验收
此外,旋转氧弹还应符合表1的规定
表1新涡轮机油旋转氧弹质量标准 项目 质量指标 试验方法 旋转氧弹(150C)/min 溶剂精制矿物油 >300 SH/T0193 加氢矿物油 >1000 检验项目至少包括;外观,色度,运动黏度、黏度指数,倾点,密度,闪点,酸值,水分、泡沫性、空气释 5.2 放值、铜片腐蚀、液相锈蚀、抗乳化性、旋转氧弹和清洁度(颗粒污染等级)
同时应向油品供应商索取氧 化安定性、,承载能力及过滤性的检测结果,并确保其符合GB11120标准要求
5.3应向油品供应商索取抗氧化剂的类型信息,并按照GB/T7596或ASTMD6971中要求的试验方 法进行抗氧化剂含量的测试,以此作为基准值,指导运行中抗氧化剂的监督以及添加
5.4也可按照有关国际标准或双方合同约定的指标验收
5.5所有样品应于取样后立即检查外观,验收试验应在设备注油前全部完成
运行油质量标准 6.1运行中涡轮机油的质量标准应符合GB/T7596的要求,具体见表2的规定
表2运行中涡轮机油质量标准 序号 项目 质量指标 检验方法 外观 DL429,1 透明,无杂质或悬浮物 色度 <5.5 GB/T6540 32 运动黏度"(40C)/mm'/s 46 不超过新油测定值士5% GB/T265 68 ,且比前次测定值不低 e180, GB/T3536 闪点(开口杯)/c 10C 颗粒污染等级 DL/T432 SAEAS4059F,级
GB/T14541一2017 表2(续 序号 项目 质量指标 检验方法 GB/T264 酸值(以KOH计)/mg/ 0.3 液相锈蚀" GB/T1l143A法 无锈 抗乳化性"(54/min 30 GB/T7605 水分"/mg/L) <100 GB/T7600 24 500/10 泡沫性泡沫倾向/泡沫稳定 GB/T12579 93,5 100/10 性)/mL/mL 500/10 后24 SH/T0308 空气释放值(50C)7 1l /min 10 不低于新油原始测定值的5%. 且汽轮机用油、水轮机用油 12 旋转氧弹值(150)/min SH/T0193 l00 燃气轮机用油>200 GB/T7602 T501抗氧剂 抗氧剂含量/% 不低于新油原始测定值的25% 受阻酚类或芳香 AsTMD697 胺类抗氧剂 32,46,68为GB/T3141中规定的ISO黏度等级
对于100Mw及以上机组检测颗粒污染等级,对于100Mw以下机组目视检查机械杂质
对于调速系统或润 滑系统和调速系统共用油箱使用矿物涡轮机油的设备,油中颗粒污染等级指标应参考设备制造厂提出的指标 执行,SAEAs4059F颗粒污染分级标准参见附录A
对于单一燃气轮机用矿物涡轮机油,该项指标可不用检测
6.2油系统检修后机组启动前,涡轮机油的颗粒污染等级应不大于SAEAS4059F标准中7级的要求 运动黏度、酸值,水分、抗乳化性及泡沫性应符合表2要求
运行中涡轮机油的监督 7.1新油注入设备后的试验 7.1.1当新油注人设备后,应在油系统内进行油循环冲洗,并外加过滤装置过滤
在系统冲洗过滤过程中,应取样测试颗粒污染等级,直至测试结果达到sAEAs1059F标准中 7.1.2 7级或设备制造厂的要求,方能停止油系统的连续循环
取样化验颗粒污染等级合格后可停止过滤,同时取样进行油质全分析试验,试验结果应符合表2 7.1.3 要求,如果新油和冲洗过滤后的样品之间存在较大的质量差异,应分析调查原因并消除
此次分析结果 应作为以后的试验数据的比较基准
7.2运行中油的检测项目及周期 7.2.1新机组投运24h后,应检测油品外观、色度、颗粒污染等级,水分,泡沫性及抗乳化性
7.2.2油系统检修后应取样检测油品的运动黏度、酸值、颗粒污染等级,水分,抗乳化性及泡沫性
7.2.3运行人员每天应记录油品外观、油压,油温、油箱油位,定期记录油系统及过滤器的压差变化情况
GB/T14541一2017 7.2.4 正常运行过程中的试验项目及周期应符合表3的规定
表3试验室试验项目及周期 投运一年内 投运一年后 序号 试验项目 燕汽轮机 燃气轮机 水轮机 燕汽轮机 燃气轮机 水轮机 外观 1周 2周 周 2周 色度 1周 2周 1周 2周 运动黏度 3个月 6个月 6个月 1年 酸值 3个月 1个月 6个月 3个月 2个月 1年 必要时 闪点 必要时 个月 颗粒污染等级 3 1个月 6个月 1年 年 2年 泡沫性 空气释放值 必要时 必要时 水分 1个月 3个月 抗乳化性 6个月 6个月 10 11 液相锈蚀 6个月 6个月 12 旋转氧弹 1年 6个月 1年 1年 6个月 1年 6个月 1年 1年 13 抗氧剂含量 1年 1年 6个月 如发现外观不透明,则应检测水分和破乳化度
如怀疑有污染时,则应测定闪点、抗乳化性能、泡沫性和空气释放值
7.2.5补油后,应在油系统循环24h后进行油质全分析
7.2.6运行中系统的磨损,油品污染和油中添加剂的损耗状况,可以结合油中元素分析进行综合判断
7.2.7如果油质异常,应缩短试验周期,必要时取样进行全分析
7.3油质异常原因及处理措施 应根据表2运行涡轮机油质量标准的规定,对油质试验结果进行分析
如果油质指标超标,应查明 原因,采取相应处理措施
运行涡轮机油油质指标超标的可能原因及参考处理方法见表4
在原因分 析时还应考虑到补油(注油)或补加防锈剂等因素及可能发生的混油等情况
表4运行中涡轮机油油质异常原因及处理措施 序号 项目 警戒极限 异常原因 处理措施 1 油中含水或被其他 1D 脱水处理或换油 乳化不透明 2) 液体污染 过滤处理 外观 2 有颗粒悬浮物 油被杂质污染 3 投人油再生装置或 2 有油泥 3 3) 油质深度劣化 必要时换油 有其他污染物 迅速变深 换油 颜色 油质深度劣化 2 颜色异常 投人油再生装置 3) 添加剂氧化变色
GB/T14541一2017 表4(续 序号 项目 警戒极限 异常原因 处理措施 运动黏度 油被污染 如果黏度低,测定闪点 比新油原始值相差士5%以上 油质已严重劣化 40) 2 必要时进行换油 3)加人高或低黏度的油 mmm'/s 闪点 查明原因,结合其他试验 开口7 比新油高或者低出15以上 油被污染或过热 结果比较,考虑处理或 换油 补油时带人颗粒 2) 系统中进人灰尘 系统中锈蚀或部件查明和消除颗粒来源,检 3 颗粒污染 有磨损 查并启动精密过滤装置、 8 等级SAE 精密过滤器未投运清洁油系统,必要时投人 AS4059级 或失效 油再生装置 油质老化产生软质 5 颗粒 采取措施控制油温 1油温高或局部过热 并消除局部过热 酸值 2) 抗氧化剂耗尽 补加抗氧剂 3 以KOH增加值超过新油0.1以上 3)油质劣化 投人油再生装置 H)/(mg/ 油被污染 结合旋转氧弹结果 必要时考虑换油 液相锈蚀有锈蚀 防锈剂消耗 添加防锈剂 抗乳化性" 进行再生处理,必要时 54" >30 油污染或劣化变质 换油 min 检查破乳化度,启用过滤 1)冷油器泄漏 水分" 设备,排出水分,并注意 l00 2 油封不严 观察系统情况消除设备 mg/I 3) 油箱未及时排水 缺陷 24及后 倾向性>500 投人油再生装置 1 油质老化 1 24 稳定性>10 泡沫性" 2 消泡剂缺失 2 添加消泡剂 10 ml 倾向性>100 油质被污染 必要时换油 93.5 稳定性>10 空气释 l0 油污染或劣化变质 必要时考虑换油 放值/minm 旋转氧弹 添加抗氧剂 小于新油原始测定值的25%,或小于 抗氧剂消耗 150C 再生处理,必要时 100min 2)油质老化 换油 nmin 添加抗氧剂 抗氧剂 抗氧剂消耗 13 小于新油原始测定值的25% 检测其他项目,必要 含量 错误补油 时换油 表中除水分,液相锈蚀和抗乳化性试验项目外,其余项目均适用于燃气涡轮机油
GB/14541一2017 油的相容性(混油 8.1需要补充油时,应补加经检验合格与原设备中相同黏度等级及同一添加剂类型的涡轮机油
补油 前应对运行油、补充油和混合油样进行油泥析出试验,混合油无油泥析出或混合油样的油泥不多于运行 油的油泥方可补加
8.2不同品牌、不同质量等级或不同添加剂类型的涡轮机油不宜混用,当不得不补加时,应满足下列条 件才能混用 应对运行油、补充油和混合油进行质量全分析,试验结果合格,混合油样的质量应不低于未混 a 合油中质量最差的一种油 b)应对运行油、补充油和混合油样进行开口杯老化试验,混合油样无油泥析出或混合油样的油 泥不多于运行油的油泥,酸值不高于未混合油中质量最差的一种油
8.3油泥析出试验应按照L./T429.7或GB/T8926(方法A)进行测试
当无法用DL/T429.7方法对 比不同油样油泥析出量时,应按照GB/T8926(方法A)进行油泥含量的测试
8.4试验时,油样的混合比例应与实际的比例相同;如果无法确定混合比例时,则试验时宜采用1:1 比例进行混油
8.5不同黏度等级的油不应混合使用
8.6矿物涡轮机油与用作润滑、调速的合成液体(如磷酸酯抗燃油)有本质上的区别,不应将两者混合 使用
换油 9.1涡轮机油运行中因油质劣化需要换油时,应提高油温至60C,进行油系统循环
循环24h后,停 止油系统运行,并立即将油系统中的劣化油排放干净
9.2检查油箱及油系统,应无杂质、油泥,必要时清理油箱
9.3用冲洗油将油系统彻底冲洗,冲洗方法参见附录D g.4冲洗过程中应取油样化验,冲洗后冲洗油质量不得低于运行油标准
9.5将冲洗油排空,应更换油系统及旁路过滤装置的滤芯后再注人新油,进行油循环,直到油质符合表 2的要求
0运行涡轮机油的维护 0.1油系统在基建安装阶段的维护 对制造厂供货的油系统设备,交货前应加强对设备的监造,确保油系统设备尤其是具有套装式 10.1.1 油管道内部的清洁 10.1.2对油系统设备验收时,除制造厂有书面规定不允许解体者外,都应解体检查其组装的清洁程 度,包括有无残留的铸砂、杂质和其他污染物,对不清洁部件应 -进行彻底清理
清理常用方法有人 工擦洗、压缩空气吹洗、高压水力冲洗、大流量油冲洗和化学清洗等
清理方法的选择应根据设备结构 材质、污染物成分、状态,分布情况等因素而定
擦洗只适于清理能够达到的表面,对清除系统内分布较 广的污染物常需用冲洗法;对牢固附着在局部受污表面的清漆、胶质或其他不溶解污垢的清除,需用有 机溶剂或化学清洗法
如果用化学清洗法,事前应同制造厂商议,并做好相应措施准备
10.1.3油系统设备验收时,应检查出厂时防护措施是否完好
在设备停放与安装阶段,对出厂时有保 护涂层的部件,如发现涂层起皮或脱落,应及时补涂,保持涂层完好;对无保护涂层的铁质部件,应采用
GB/T14541一2017 喷枪喷涂防锈剂油)保护
对于某些设备部件,如果采用防锈剂油)不能浸润到全部金属表面,可采用 或联合采用)气相防锈剂油)保护
实施时,应事先将设备内部清理干净,放人的药剂应能浸润到全部 且有足够余量,然后封存设备,防止药剂流失或进人污物
对实施防锈保护的设备部件,在停放期内每 月应检查一次
10.1.4油系统在清理与保护时所用的有机溶剂、涂料、防锈剂油)等,使用前应检验合格,不含对油系 统与运行油有害成分,应与运行油有良好的相容性
有机溶剂或防锈剂在使用后,其残留物应可被后续 的油冲洗清除掉而不对运行油产生泡沫、乳化或破坏油中添加剂等不良后果
0.1.5各部件验收时应注意下列问题 油箱验收时,应检查其内部结构是否符合要求,如隔板和滤网的设置是否合理、清洁、完好,滤 a 网与框架是否结合严密,各油室间油流不短路等
油箱上的门、盖和其他开口处应能关闭严 密
油箱内壁应涂有耐油防腐漆,漆膜如有破损或脱落,应补涂
油箱在安装时做注水试验 后,应将残留水排尽并吹干,必要时用防锈剂油)或气相防锈剂保护 安装齿轮装置前 金查其防护装置的密封状况,如有损坏应立即更换,如发现防锈剂损失 i.应检命 应及时补加并保持良好密封
阀门滤油器、冷油器、油泵等验收检查时,如发现部件内表面有一层硬质的保护涂层或其他污 物时,应解体用清洁(过滤)的石油溶剂清洗,禁用酸、碱清洗
清洗干净后应用干燥空气吹干 涂上防锈剂油)后安装复原,并封闭存放 0.1.6安装前应对轴承箱上的铸造油孔、加工油孔、盲孔、轴承箱内装配油管以及与油接触的所有表 面进行清理,清理后用防锈油或气相防锈剂保护,并对开口处进行密封
0.1.7对制造厂组装成件的套装油管,安装前仍应复查组件内部的清洁程度,有保护涂层者还应检查 涂层的完好与牢固性
现场配制的管段与管件安装前应经化学清洗合格,并吹干密封
已经清理完毕 的油管不得再在上面钻孔、气割或焊接
油系统管道未全部安装接通前,对油管敞开部分应临时密封 0.2油系统的冲洗 10.2.1新机组在安装完成后、投运之前应进行油系统冲洗
油系统冲洗技术要求参见附录D,油系统 全部设备和管道冲洗应达到合格的颗粒污染等级
10.2.2运行机组油系统的冲洗,其冲洗操作与新机组基本相同,新机组应强调系统设备在制造、贮运 和安装过程中进人污染物的清除,而运行机组油系统则应重视在运行和检修过程中产生或进人的污染 物的清除
0.2.3冲洗油应具有较高的流速,应不低于系统额定流速的两倍,并且在系统回路的所有区段内冲洗 油流都应达到紊流状态
应提高冲洗油的温度,并适当采用升温与降温的变温操作方式
在大流量冲 洗过程中,应按一定时间间隔从系统取油样进行油的颗粒污染等级分析,直到系统冲洗油的颗粒污染度 达到SAE分级标准的7级
0.2.4对于油系统内某些装置,系统在出厂前已进行组装清洁和密封的则不参与冲洗,冲洗前应将 其隔离或旁路,直到其他系统部分达到清洁为止 检修工作完成后油系统是否进行全系统冲洗,应根据对油系统检查和油质分析后综合考虑而 10.2.5 定
如油系统内存在一般清理方法不能除去的油溶性污染物及油或添加剂的降解产物时,宜采用全系 统大流量冲洗
冲洗时,还应考虑污染物种类,更换部件自身的清洁程度以及检修中可能带人的某些杂 质等
如果没有条件进行全系统冲洗,应采用热的干净运行油对检修过的部件及其连接管道进行冲洗, 直至油的颗粒污染等级合格为止
10.3运行油系统的防污染控制 0.3.1运行中 对运行油油质进行定期检测的同时,应将汽机轴封和油箱上的油气抽出器(抽油烟机)以及所有与
GB/T14541一2017 大气相通的门、孔、盖等作为污染源来监督
当发现运行油受到水分、杂质污染时,应检查这些装置的运 行状况或可能存在的缺陷,如有问题应及时处理
为防止外界污染物的侵人,在机组上或其周围进行工 作或检查时,应做好防护措施,避免系统部件暴露于污染环境中
运行中应连续运行净化装置,运行油 的颗粒污染等级和水分含量应符合运行油标准
为保持运行油的颗粒污染等级合格,应对油净化装置 进行监督,当运行油受到污染时,应采取措施提高净油装置的净化能力
0.3.2油转移时 当油系统某部分检修,系统大修或因油质不合格换油时,应进行油的转移
如果从系统内放出的油 还需再使用时,应将油转移至内部已彻底清除的临时油箱
当油从系统转移出来时,应尽可能将油放 尽,特别是将油加热器、冷油器与油净化装置内等含有污染物的大量残油设法排尽
放出的全部油可用 大型移动式净油机净化,待完成检修后,再将净化后的油返回到已清洁的油系统中
油系统所需的补充 油也应净化合格后才能补人
10.3.3检修时 油系统放油后应对油箱,油管道、滤油器、油泵、油气抽出器、冷油器等内部的污染物进行检查和取 样分析,查明污染物成分和可能的来源.提出应采取的措施 10.4油处理 10.4.1油净化处理在于除去油中颗粒杂质和水分等污染物,保持运行油的颗粒污染等级及水分含量 符合油的有关标准要求
净化处理方法有机械过滤,重力沉降、离心分离、聚结分离和真空过滤
机械 过滤用于滤除油中的机械杂质,其截污能力决定于过滤介质的材质及其过滤孔径
聚结分离和真空过 滤用于除去油中的水分,一般与机械过滤联合使用,其中真空脱水方式因脱水效率低适用于油中含水量 较少的情况
重力沉降和离心分离可同时除去油中的机械杂质和水分,重力沉降特别适合运行系统 采用 10.4.2油再生处理是采用吸附剂,借净油器的渗滤吸附作用,除去油中老化产物,恢复并保持油品化 学性能的措施,常用吸附剂的性能参见附录E
这种处理可能会除去油中某些添加剂,处理后应及时检 测并进行补加
10.4.3油处理系统的配置方式常用的有全流量净化、旁路净化和油槽净化3种
全流量净化是获得 与维持油颗粒污染等级合格最有效的方式,但常会受到过滤工序的制约
对于旁路净化,虽其效率不如 全流量净化,但易于安装,可连续使用,不会受到运行限制
旁路净化效率与旁路分流流量比率有关,分 流比越高,对污染物清除效率越高
旁路分流比率一般为10%~75%
油槽净化方式不适用于运行系 统
但当运行油在主油箱与贮油系统之间进行转移时,常需要油槽净化方式
10.4.4油处理系统与油系统的连接方式,应考虑有利于向机组提供最纯净的油;当油净化系统或管路 事故可能危及机组安全时,应能提供最大的保护
0.5油品添加剂 10.5.1添加油品添加剂是油质防劣化的一项有效措施
对于矿物涡轮机油,适合运行油使用的有抗 氧化剂和金属防锈剂二类
0.5.2添加剂对运行油和油系统应有良好的相容性,对油的其他使用性能无不良影响;对油系统金属 及其他材质无侵蚀性
10.5.3新涡轮机油应检测T501抗氧化剂,芳香胺类或其他酚类抗氧剂的类型及含量,并以此作为添 加依据
含有不同类型抗氧化剂的涡轮机油添加应按下述要求进行 仅含T501抗氧化剂的新涡轮机油或再生油,其中T501含量不应低于0.3%0.5%,运行中 a
GB/T14541一2017 应不低于0.15%,否则应该进行补加
D)含有其他抗氧化剂或与T501复合抗氧化剂的新涡轮机油,如果抗氧化剂含量低于新油的 0%,则应进行补加
补加的抗氧化剂的类型与数量应咨询油品供应商或生产商
0.5.4T746防锈剂是常用的一种金属防锈剂,如油质检测液相锈蚀不合格,则应进行补加,对矿物涡 轮机油的补加剂量一般为0.02%~0,03%
10.5.5补加添加剂时,用待补加添加剂的油将添加剂配成5%~10%的母液通过滤油机加人油中
添 加后应对运行油循环过滤,使添加剂与油混合均匀,并对运行油油质进行检测
10.5.6T501抗氧化剂与T746防锈剂的药剂质量应按附录E进行验收合格,并注意药剂的保管,以防 变质
技术管理和安全要求 1 1.1库存油的管理 11.1.1库存油管理应严格下述要求做好油的人库、储存和发放3个环节 对新购进的油,应先验明油种、牌号,并按新油的相关标准检验油质是否合格
经验收合格后 a 的油方可人库
b 库存备用的新油和合格的油,应分类,分牌号分质量进行存放
所有的储油桶,油罐应标志 清楚,挂牌建账,并应做到账物相符,定期盘点无误
严格执行库存油的油质检验
除按规定对每批人库、出库油作检验外,还要加强库存油移动时 的检验与监督
油的移动包括倒罐、倒桶以及原来存有油的容器内再进人新油等
凡是油在 移动前后均应进行油质检验,并作好记录,以防油的错混与污染
对长期储放的备用油,应定 期(一般为每年)检验外观、水分及酸值,以保持油质处于合格的备用状态
取样工具等应保持清洁,一旦发现内部积水、脏污或锈蚀以及 油桶、油罐、管线、油系以及计量、 11.1.2 接触过不同油品或不合格油时,应及时清除或清洗干净
11.1.3应尽量减少倒罐、倒桶及油移动次数,避免油品意外的污染
11.1.4应定期检查管线、阀门开关情况,严防串油、串汽和串水
11.1.5准备再生的污油、废油,应用专门容器盛装并单独存放,其输油管线与油泵均与合格油品严格 分开
11.1.6油桶应严密上盖,油罐装有呼吸器并应经常检查和更换吸潮剂
11.2建立技术管理档案 11.2.1主要用油设备台账;包括设备铭牌上的主要规范、油种,油净化装置配备情况、设备投运日期等 记录 11.2.2主要用油设备运行油的质量检查台账:包括换油、补油和防劣措施、运行油处理等情况记录
1.2.3主要用油设备大修检查情况记录 1.2.4旧油,废油回收处置或再生处理记录
1.2.5库存备用油及油质检验台账;包括油种,牌号、油量及油品转移等情况记录
11 1.2.6汽(水)轮机油系统图、油库、油处理站设备系统图等
1.3安全与卫生 11.3.1油库、油处理站设计应符合消防与工业卫生、环境保护等有关要求,油罐安装间距及油罐与周 围建筑物的距离,应符合相关防火标准的规定,且应设置油罐防护堤
油罐及其连接管线应装设良好的 接地装置,必需的消防器材和通风、照明油污废水处理等设施均应合格齐全
油再生处理站还应根据 10
GB/T14541一2017 环境保护规定,妥善处理油再生时的废渣,废气、残油和污水等
1.3.2油库,油处理站及其所辖储油区,应严格执行防火防爆制度
杜绝油的渗漏和泼洒,地面油污 应及时清除,严禁烟火
对使用过的沾油棉织物及一切易燃易爆物品均应清除干净
油罐输油操作应 注意防止静电放电
查看油罐油箱时,应使用低压安全行灯并注意通风等
1.3.3从事接触油料工作时,应注意采取有关保健防护措施,避免吸人油雾或油蒸气;避免皮肤长时 间过多地与油接触,必要时需带防护手套防护服,操作完后应将皮肤上的油污清洗干净,油污衣物应及 时清洗等
11
GB/T14541一2017 附 录 A 资料性附录) 影响涡轮机油使用寿命的运行因素 系统的设计和类型 A.1.1汽轮机润滑系统大多数型式是用主油泵直接将油压出进人润滑系统
其余组成部分为储油箱、 油冷却器、滤网、油管道和旁路净化装置或过滤设备等
A.1.2主油箱;油在主油箱内的滞留时间至少要有8min
可用加隔板的办法在主油箱内形成一个狭 长的通道,设计上还应尽量减小回油进口处的紊流
.1. 润滑油管道:润滑油管道应严密、结实可靠
要求最大限度地减少污染和泄漏,以及避免外在热 A
源对局部油管道加热;并要为检查、清理和冲洗创造条件
A.1.4旁路净化装置:旁路净化装置应该连续运行,以减少油中杂质的积累和达到可接受的颗粒污染 等级
A.2油系统投运前的条件 A.2.1润滑系统各部件通常在系统安装前运到现场
现场的存储和保护措施决定在此期间引发的污 染数量
A.2.2启动前涡轮机油系统污染通常包括防腐剂、颜料、锈蚀颗粒、以及施工过程中遇到的各种固体 如灰尘和泥垢、破布片,瓶和罐)
这些污染物对涡轮机油系统具有明显的影响
A.2.3需要连续运行净化装置,以减少运行油的颗粒污染等级和水分含量符合运行油标准,从而确保 润滑和控制系统的可靠运行
A.3原始油的质量 A.3.1使用高品质的油是保证其长期运行的最好保证
选用油应满足公认标准的要求,且满足汽轮机 制造商的要求
推荐新油测试见第5章 A.3.2应从油供应商处索要完整的试验数据
新油购进后,对油样进行全面的质量验收
A.4系统的运行条件 系统运行条件是影响指定润滑油在指定汽轮机系统中预期运行寿命的最重要因素
在某种程 A.4.1 度上,空气(氧气、升高的工作温度、金属和水分(湿气)总是存在于这些油系统中,这些因素均会影响油 的降解
A.4.2油箱油温应维持在较低温度(<60C)运行
尽管油体温度较低仍存在局部的热点(如轴承 气体密封件及油门控制装置中),导致油降解并最终造成系统油显示出劣化的迹象
A.4.3在高温条件下,特别是燃气轮机中会加速热氧化裂解,生成各种树脂状物质和产生难溶的沉积 物
应加强运行油的监督,减少局部过热点的存在
12
GB/14541一2017 A.5系统受污染情况 A.5.1涡轮机油污染往往是影响油运行寿命的最显著因素
污染可以来自系统外,也可以源自系统内 部发生的油降解和水分凝结或泄漏
在机组启动时建立一个洁净的油系统或其后的维护至关重要
A.5.2外部污染可以通过轴承密封件和通风口进人系统,也可能是错误的补油
内部污染物则在运行 过程中持续产生
这些污染物包括水、污垢、粉煤灰、磨损颗粒和不溶性微粒油降解产物
无论来源如 何,应根据油质定期使用再生、净化或脱水装置除去
A.6补油率 补油量和频率是决定系统中油运行寿命的重要因素
补油率大小不一,从每年<5%到高达30% 某些极端情况下)
如果汽轮机的补油率高于油降解率,油的降解程度得到补偿,预期运行寿命也相对 延长
如果汽轮机的补油率较低(<5%),则可以观察到更真实的油降解情况
然而,这类系统应予以 仔细查看,因其油的运行寿命儿乎完全取决于原始质量
正常情况下,平均补油率每年应小于10% 油中添加剂的含量 A.7 油中添加剂的含量影响着油的性能,应根据油质的状况适时添加适宜的添加剂,以维持油的品质
A.8油的处理和存储 A.8.1油处理可以除去油中的杂质,水分及因老化产生的酸性化合物及各种胶质等老化产物,恢复油 的性能,选择适宜的油处理方式及频率可以有效延长油的使用寿命
A.8.2存储过程中,油品应正确标注,并防止润滑油的物理和化学性质发生降解,以确保正确选择和 使用
13
GB/T14541一2017 录 附 B 资料性附录) 汽轮机严重度的测定和计算方法 “汽轮机严重度”这一概念被定义为;油每年丧失的抗氧化能力占原有新油抗氧化能力的百分率
B.1 B.2汽轮机严重度将考虑以下因素 为增加油的抗氧化能力每年注人系统的补充油量 油的运行时间的长短; 用旋转氧弹(RBOT)试验方法测定的抗氧化能力
B.3汽轮机严重度的计算公式如式(B.1). 二M(1一了/10o)/1一eMn) B B1) 式中 汽轮机严重度,以百分率表示; M 每年注人系统的补充油率,以占初始装人系统新油总量的百分率表示 -油中残余抗氧化能力的数量,以占初始装人系统新油的抗氧化能力的百分率来表示; -最初装人系统中新油已使用了的年数
B.4测定涡轮机油的氧化安定性的方法很多,但这些方法用时较长,有的约需2000h以上(约3个多 月),而旋转氧弹(RBoT)方法只需几个小时就可得出结果
图B.1表示的是一台有每年为25%严重度 的汽轮机,油补充率M对油变质r的影响关系曲线
0 40 30 20 N=30% 吴 10 16 1820 101214 使用年数 图B.1油补充率M对油变质的影响 汽轮机严重度B=25%/年) B.5对一个特定的润滑系统的严重度,从最初装人新油开始运行起,经过一段时间后,就应该进行测 定
同时完整的保存补充油量的准确记录,是这一工作开展的重要环节
一般在运行的头一,二年内每 隔3个月16个月就进行一次旋转氧弹法试验
当知道了每年的补充油量和随运行时间而变化的油 变质的程度后,则可从图B.2中查到该台汽轮机的严重度
图B.2中虚线表示查找汽轮机严重度B的 数字顿序
14
GB/T14541一2017 丸r 150一 2.0 60 100 次 50 0- 0 40 0 30- 30 0.9 三 0.8 25 0.7 20 0.6 1 " 0.5 5 0.4 12 A=30% 25% 20% 0.2 15% 10% 10 1214161820 年数 图B.2汽轮机严重度B和油补充率M对油变质的影响 B.6在这个例子中,涡轮机油已使用了5年,年补充油率为15%
油的变质的旋转氧弹试验从起始时 的1700min降到仅为350min,氧化寿命的丧失率为79.5%
从时间坐标轴上的第5年开始,向上与 15%的补充油率的曲线相交于一点,再向左投影到B/(100一r)坐标轴线上的一点,从这点与油变质坐 标轴线上的79.5连一直线,直线与汽轮机严重度B标尺线相交在22%点上,即为该台汽轮机严重度 B 值
> B.7 一个有着高严重度的涧滑油系统,需要经常补充油或更换油
反之,一个只有低严重度的润滑油 系统,则只需作例行的油补充就可以了
B.8现在设计的汽轮机组比以前安装的机组有较高的汽轮机严重度
润滑系统温度的增高被认为是 汽轮机组存在较高严重度的原因
现存大容量机组的主轴、盘车齿轮和联轴器都较大,主油箱的容量又 较小,这些都增加了单位体积的油量每小时必须向冷油器传送的热量
另外,运行现场的环境影响也很 大,如煤灰,灰尘侵人油系统,造成对油的污染变质也是一个因素
15
GB/T14541一2017 录 附 C 规范性附录) sAEAs4059颗粒污染度分级标准 SAEAS4059F颗粒污染度分级标准(差分计数)见表C.1
SAEAS4059F颗粒污染度分级标准(累积计数)见表C.2
表C.1SAEAS4059F颗粒污染度分级标准(差分计数 项目 最大污染度极限/颗粒数/100ml 寸范ISO4402校准 5m~15m5m~25m25m50m0m100m" 一l00丛m 尺寸范围(ISO11171校准 6m~14丝m1 14丝m2lm21m一38丝m384m70m" >70m 125 00 2 250 89 500 16 1000 178 82 3 ln 2000 356 4000 712 126 1425 253 8000 等级 06 16000 2850 l6 8o 2 32000 5700 1012 G4 1400 64000 2025 360 128000 22800 4050 720 128 256000 45600 8100 144o 10 256 1n 512000 91200 16200 2880 512 12 1024000 182400 32400 5760 024 表C.2SAEAS4059F颗粒污染度分级标准累积计数 项目 最大污染度极限(颗粒数/100ml 尺寸范ISO >50m l00m 4402校准 4m >5mm >15m >25m >38m >70nm 尺寸范围(IsO11171校准 44m 6m 14Am 21m 000 195 76 14 00 390 52 27 5 10 780 304 156o 609 109 3120 1217 217 2432 6250 432 13 864 12500 4864 2t 52 53 等级 25000 9731 1731 306 50000 G12 06 19 4602 3462 38924 6924 1224 212 100000 2 77 200000 849 13849 2449 400000 155698 27698 4898 848 128 256 800000 311396 9796 1696 55396 l 622792 110792 9592 3392 12 600000 12" 3200000 221584 39184 6784 245584 1024 16
GB/T14541一2017 SAEAS4059F是NAs1638的发展和延伸,代表了液体自动颗粒计数器校准方法改变后颗粒污染 分级的发展趋势,不但适用于显微镜计数方法也适用于液体自动颗粒计数器计数方法
与NAs1638相比较,SAEAS4059F具有以下主要特点: 计数方式中增加了累积计数,更贴合自动颗粒计数器的特点
a b 计数的颗粒尺寸向下延伸至1m(Iso402校准方法)或者4pm(Iso 11171校准方法),并 且作为一个可选的颗粒尺寸,由用户根据自己的需要自己决定
在颗粒污染度分级标准(累积计数)中增加了一个000等级
17
GB/T14541一2017 附 录 D 资料性附录) 油系统冲洗技术措施 准备工作 D.1 D.1.1冲洗前对系统的准备 D.1.1.1冲洗前,油系统包括冲洗增设的全部设备)所有可检查的区域均应彻底检查与清理
为冲洗 装配的临时管道,事前须化学清洗合格,增设的油容器应配上临时防尘盖,全部系统须经承压检查无 渗漏
D.1.1.2拆除供油系统原有的一切不必要的限制油流的部件,如节流孔板,过滤器滤芯等
所有通向 轴承的油管路应隔断,并装上临时旁路,系统上所有其他不予介人冲洗的区域均用挡板隔断
所有拆除 部件与隔断用挡板均应编号或记录,冲洗结束后,再按编号与记录分别进行装复或拆除
.1.1.3在冲洗油泵的吸人侧加装0.18 孔径临时滤网;在重力与压力系统卸油侧加装 D mm mm 细滤网;通向轴承箱供油管道及齿轮箱进口油管等处也应装设0.15mm孔径或更细的滤网
冲洗过程 中,还可用不起毛的布滤袋或磁性分离元件临时放人油系统原有滤网的内侧
D.1.1.4冲洗中尽可能采用全流量的油净化方式 -般采用带有全流量过滤器的大流量冲洗设备
全 流量过滤器分二级,一级为粗过滤器,装有0.15mm孔径滤网,可滤除50Mm以上尺寸的杂质颗粒;二 级为精密过滤器,装有精滤芯,可滤除5Mm以上尺寸的杂质颗粒
两级过滤器均可在不停止冲洗情况 下更换滤元
冲洗过滤设备与系统连接方式举例如图D.1
安全阀 附属油热交换器 全流量u悄号过油网 锥维形谜网 全流量5m过滤芯 大容量油泵 流量表 截止网 逆止刚 图D.1大流量冲洗装置的连接管道布置方式示意图 当冲洗油装人系统后,冲洗过滤设备应完成投运准备
在冲洗油系统的主系统前,应首先将冲洗过 滤设备及油箱都冲洗干净,以便为系统供给干净的冲洗油
为使油箱内油充分过滤,必要时需装设再循 环管路
为操作安全与方便,冲洗设备系统还应装设流量控制阀、防超压安全阀和手动旁路阀等 D.1.1.5为加热冲洗油,应增设油的热交换器
如未配热交换器,可采用油系统的冷油器,利用低压蒸 汽(P<34kPa)作热源,通人冷油器水侧进行加热的方法,但应注意,冷油器不超压而且不会使冲洗油 18
GB/14541一2017 过热
为方便冲洗油的变温操作,热交换器应兼有加热和冷却运行功能,最好是配置两台,一台用作升 温,一台用作降温
如果使用电加热的热交换器,应特别不得超温,对加热元件表面温度应使加热循环 油流不超过120C;加热循环的静止油则其表面温度不超过66,以防油质过热裂解
D.1.1.6为监督冲洗过程,需监测冲洗油的颗粒污染等级
由于正常运行时用的固定取样点并不一定 适合冲洗过程,因此,应增设临时取样点
取样点位置最好是选在被冲洗的饷承或其他部件的上游或下 游,直接监测被冲洗部件的颗粒污染等级
例如轴承冲洗增加的临时旁路及取样点如图D.2所示
临时管路 “B" 临时管路 采样滤网 采样滤网 进油管路 通过基础的套管 标有“A”和“B”的管路、管径应一致,或“最小不低于76" mmm
图D.2旁路轴承进油的管道布置示意图 在轴承旁路或轴承处取样不可能时,可在回油旁路上取样,但回油旁路有时油压低时取不出样,则 只能在油箱或滤油器上游取样,此时应考虑油箱的稀释作用特别是油箱在开始冲洗时装的是干净油
-般情况下,在滤油器下游取样,只反映直接进人冲洗部件的油的颗粒污染等级,对系统中污染物究竟 除去多少无法知道
为此,应根据具体情况增设多个取样点,使取样具有代表性 D.1.2冲洗作业用料和工具的准备 备足符合制造厂要求并经检验合格的涡轮机油或其他合适的特殊冲洗油
D.1.2.1 D.1.2.2油系统清理用工具与材料,包括擦洗海绵,不起毛擦拭布,吸油剂、覆盖轴承箱用胶合板,塑料 板等
D.1.2.3冲洗用辅助工具与备件,包括管道机械振动器,木质或铜质手锤,空气扰动喷管、清洗用喷枪、 不同过滤精度的不锈钢滤网、磁棒或磁性滤网、备用滤芯、油泵备用密封垫与配件、轻便气动抽油泵,充 气压膨胀管塞及油管路配件等
D.1.2.4检查与监测仪器、工具,包括挠性管道内窥镜便携式颗粒计数仪或镜检仪,取样瓶,取样用滤 网等
19
GB/T14541一2017 D.1.3消防、环保与其他安全注意事项 D.1.3.1油系统设备、管道表面及周围环境清理干净,无易燃物,工作区域周围无明火作业
D.1.3.2备好砂箱灭火器等消防工具
D.1.3.3油系统上的排油烟机经空载运行检查,情况正常
3.4检查事故排油系统连接正确,阀门操作灵活并关紧后加上保护罩,事故排油井内清理干净
D.1.3.5冲洗系统管道布置留有进人通道,便于工作人员操作
3.6备有工作人员防热油飞溅、泄漏而引起伤害的安全防护用具,等等
D.1.3.7油系统冲洗后的废液,应集中存放处理,严禁随意排放
D.1.3.8冲洗后的废渣及其他污物也应集中销毁,防止污染环境
D.2冲洗油的选择与使用 D.2.1冲洗用油可以是系统运行油,也可以使用特殊的冲洗油,应由有经验的专业人员根据油系统结 构特点与污染物情况作出选择,并征得制造厂同意
-般悄说均采用系能运行油作为冲洗油
在实际应用中,系统运行油用作冲洗后,不能再用作 D.2.2 系统运行油,而需要换上合格的备用油
D2特殊冲恍油一般是防锈型的
这种冲洗油由于舍有金属防锈剂与能除去一些难游性污染物(如 防锈剂降解产物、油泥等)的添加剂成分而兼有良好的溶解能力
禁止使用掺混含有水、苛性碱、四氯化 碳或其他活性物质成分的冲洗油
特殊冲洗油的选择,应严格考虑冲洗油与全部油系统以及可能被油 充满的机组的其他部件都应具有相容性,包括润滑系统与冲洗系统的所有部件、注油管线、所有冲洗用 永久性与临时性的软管管线、轴承箱、套装油管,油箱等内部的防锈涂层,用作油管在安装阶段保护而在 冲洗前不予拆除的防护物等
D.2.4冲洗油注人油箱前,须经精密过滤器净化
冲洗过程中也应在循环中不断过滤
应采用单程过 滤,防止净化后的油再与脏油混合
净油加热后过滤,可延长滤元使用寿命
油箱最低油位要足以保障 油泵的正常运行
D.2.5油系统冲洗后,冲洗油应趁热排放
排放时,应选在油管路最低点阀门处将油排尽,然后将油 箱、轴承箱、滤油器等内部残油放尽,并对设备内部残留污染物进行清理
用过的冲洗油用油箱收集进 行彻底净化,净化后油如仍具有防锈性能与溶解能力还可用作冲洗油的备用油
D.3冲洗油洁净度监测与评定 D.3.1监测冲洗油的颗粒污染等级是监督冲洗过程的重要手段的依据
D.3.2冲洗油的颗粒污染等级应不大于SAEAs7级的要求或符合制造厂的要求
D.4冲洗操作 D.4.1冲洗程序应根据油系统具体情况而定
一般可分为3个阶段,即反冲洗、正冲洗和油循环
反 冲洗是冲洗进油管,其流向为冲洗油由主油箱经冲洗设备反向流经进油管再返回油箱,目的是清除油管 路中易脱落的大颗粒杂质;正冲洗是冲洗整个油系统(轴承等部件除外),其流向按正常运行线路,即冲 洗油经冲洗设备过滤流人油管,经过回油管再返回油箱,目的是彻底清除润滑油系统中>2504m颗粒 尺寸的杂质,使油颗粒污染等级达到最低标准要求;油循环则是在恢复正式系统后,加上系统自身的动 力对油进行循环和精密过滤,进一步清除残留杂质,使油洁净度达到更高标准,以满足正常运行要求
20
GB/T14541一2017 为加大冲洗油流,提高冲洗效果,可有顺序地对管路进行分段冲洗,每段冲洗时还可按正常流向的反向 冲洗
D.4.2冲洗油的变温操作条件,一般规定;高温75C左右,但不超过80C,低温为30C以下,高、低温 阶段各保持2h3h,交替变温时间为1 1h~2h,冷,热交变冲洗时间以8h为一个循环周期
如果制造 厂家对变温操作条件有不同规定,应按制造厂家规定执行
D.4.3实践表明在冲洗过程的前几个小时,系统内进人的杂质颗粒绝大部分会被临时滤网或过滤器捕 获
在这段时间内,应加强对过滤装置的检查,一旦发现滤网压降明显增加时应立即进行清扫或更换
-般每15min间隔检查一次
其他净油装置也应定期检查与清理
D,4.4为加速冲洗进程,除在冲洗管路中对油管焊口、弯头、死角等处进行振动敲打和用压缩空气扰 动等辅助措施外,还应注意冲洗后对冲洗死角采用辅助措施清洗以及在冲洗每一阶段结束时对油箱进 行彻底清理
D,4.5油系统冲洗所需有效时间可能要几个到几十个工作日
特别是对于新系统冲洗,由于系统内一 些杂质被冲洗油浸润和冲刷后,从管壁上剥离脱落需要时间,不可能在较短时间内全部剥落,因而冲洗 所需时间较长,一般为一个月或更长
D.5油系统冲洗后投运前工作 D.5.1油漂洗、置换:采用系统内运行油冲洗时不需要油漂洗;当使用轻质油作冲洗油或使用特殊冲洗 油后,系统内尚有一定的残留时,则应用油漂洗,以清除这些含有油溶性污染物的残留污油
漂洗油应 对设备有相容性
漂洗油充人系统前,须对油净化装置(滤网滤芯等)进行清理,充人后尽快启动循环 泵,并将油加热至60C一70首先对油循环净化至少2h,然后再在系统中继续循环24h以上,直至 滤网、滤袋元件无污染物为止
漂洗结束后,放出漂洗油并对油系统再次进行检查与清理后,尽快换上 新涡轮机油,做好投运准备 D.5.2临时性防锈措施:如果机组在油系统冲洗与投运间有较长闲置时间,可采用含有气相防锈剂的 油作为系统的运行油,保护期间应随时检查,特别是对新充人油不能浸润到的系统部件或区域,必要时 还应对可能发生锈蚀的部位采用喷枪喷涂防锈剂油)
21
GB/T14541一2017 录 附 资料性附录) 涡轮机油维护所用材料性能和质量标准 E.1常用吸附剂性能(见表E.1D 表E.1常用吸附剂性能 活性 最佳使 活化 形状 名称 型号 化学成分 表面积 用温度 能吸附的组分 温度/ tm"/g) 水分、气体、有机酸 干燥时呈乳白色 等氧化产物细孔硅 mSiO.rH.o 块状或球形结晶 450600 细孔 胶多用于吸水,粗孔 硅胶 微孔 变色硅胶没有 孔径:粗孔为300500 变色硅 3050 硅胶多用于油处理
COC 变色 nm,细 胶为120 8nm101 变色硅胶作吸附剂 孔为2nm 吸水性指示用 块状,球状或粉状 活性 有机酸及其他氧化 mAl.OrH.O 结晶,孔径为 180370 300 5070 氧化铝 产物 2.5nm- 一5,5nm 通式为 la(M/nO)Al.O 水、气体、不饱和, A型 b(SiO.c(H.O 有机酸等氧化产物 分子筛 常用 条状或球形孔径 450一55025~1503A.4A.5A型分子 M一般为K、Na、 l3A10A 沸石) x型 Ca 筛多用于吸水,5A Y型 为阳离子价数 型还可用于油处理! n la、b、均为系数 通式为 不饱和焰、树脂及沥 MsoNA.o无定形或结晶状 活性 青质有机酸,水分等 含少量Fe(O,Fe.(O、的白色粉末或100300450600100150 用于油接触法再生 白土 Mg(G等)M.N为粒状 处理 系数 SiOAl,O 除去酸性组分及其 高铝 801 担体为稀土Y型微球状 530 20 5060 他氧化产物(用于接 微球 分子筛 触法再生油 22
GB/14541一2017 E.2I501抗氧化剂质量标准(见表E.2) 表E.2I501质量标准 专业标准sH0015 项目 试验方法 -级品 合格品 外状 白色结品 白色结晶" 目测 不大于 0.,015 0.03 附录 游离甲酚的含量/% 初熔点/C 69,070.0 68,570,0 GB/T617 灰分/% 不大于 0,01 0.03 GB/T606'" 水分/% 不大于 0.06 GB/T261 报告 闪点(闭口7 贮存后允许变为淡黄色,但仍可使用. 测定水分时,手续改为取3ml一4ml溶液甲,以溶液乙滴定至终点不记录读数,然后迅速加人试样1g(称准至 0.01g)在不断搅拌下使之溶解,用溶液乙滴定至终点 E.3十二烯基丁二酸防锈剂(I746)质量标准(见表E.3) 表E.3I746质量标准 专业标准SH0043 项目 试验方法 -级品 合格品 外观 琥珀色粘稠液体 琥珀色粘稠液体 目测 GB/T2540 密度(G0C)/(kg/m'y 报告 报告 4060 0~100 GB/T265 黏度(100C)/ mm/s 15o 100 GB/T267 闪点(开口杯)/t 不低于 酸值以KOH计/mg/g 235~280 235340 GB/T264 pH值 4.2 4.2 SY2679 5080 5090 碘值(以l计)/g/100g SY2301 铜片腐蚀"(100C)/3h GB/T5090 蒸僧水 无锈 无锈 GB/T1l143 液相锈蚀" 人工海水 无锈 无锈 坚膜韧性 通过 通过 试验用油均为32号或46号油;未加添加剂的汽轮机油其防锈剂添加量为0,03%士0,01%,
电厂用矿物涡轮机油维护管理导则GB/T14541-2017
随着电力工业的快速发展,矿物涡轮机油在电厂中扮演着越来越重要的角色。矿物涡轮机油作为一种高温、高压下运转的关键润滑剂,对于保证电厂的正常运转和延长设备寿命具有重要意义。
因此,在日常运行中,电厂需要采取一系列的维护管理措施来确保涡轮机油的质量和性能。GB/T14541-2017作为国家标准,规定了矿物涡轮机油的技术要求、试验方法和标志、包装、运输、储存等方面的要求,是电厂进行涡轮机油维护管理时不可或缺的参考标准。
涡轮机油的技术要求
根据GB/T14541-2017,矿物涡轮机油应具备以下技术要求:
- 粘度指数高,具有较好的粘温性能;
- 氧化安定性好,对高温和氧化环境下稳定性良好;
- 抗泡性强,避免油泡对机械部件的直接和间接损害;
- 过滤性好,保持油路畅通;
- 抗磨性好,降低机械部件的摩擦和磨损。
涡轮机油的试验方法和标志
GB/T14541-2017规定了矿物涡轮机油的试验方法和标志,其中包括动态粘度、闪点、倾点、氧化安定性、蒸发残留物等指标的测试方法。
在涡轮机油使用前,应注意查看其标志是否符合产品质量要求和相关标准的要求。一般来说,标志应包括产地、品牌、型号、粘度等信息。
涡轮机油的储存和使用
在涡轮机油的储存和使用过程中,需要注意以下问题:
- 保持油品清洁,并避免杂质进入油路;
- 避免阳光直射和高温环境,防止氧化降解;
- 避免油品接触酸、碱、盐等腐蚀物质;
- 控制油品使用量和更换周期,避免过度使用或过长使用时间。
结论
维护管理导则GB/T14541-2017为电厂使用矿物涡轮机油提供了重要的参考标准和指导,能够帮助电厂制定科学合理的涡轮机油维护管理方案。在实际运行过程中,电厂应严格按照GB/T14541-2017的要求进行涡轮机油的选择、使用、储存和更换,确保涡轮机油的质量和性能,保障设备的正常运转和延长设备寿命。