GB/T38653-2020
核电厂常规岛高压加热器技术条件
Specificationsforhighpressurefeedwaterheaterforconventionalislandinnuclearpowerstation
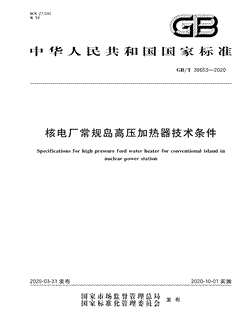
- 中国标准分类号(CCS)K54
- 国际标准分类号(ICS)27.040
- 实施日期2020-10-01
- 文件格式PDF
- 文本页数34页
- 文件大小3.23M
以图片形式预览核电厂常规岛高压加热器技术条件
核电厂常规岛高压加热器技术条件
国家标准 GB/T38653一2020 核电厂常规岛高压加热器技术条件 Speeifieationsforhighpressurefeed waterheaterforconventionalislandin nuclearpowerstation 2020-03-31发布 2020-10-01实施 国家市场监督管理总局 发布 国家标涯花管理委员会国家标准
GB/T38653一2020 次 目 前言 范围 2 规范性引用文件 术语和定义 性能及设计要求 材料 24 制造 6 检查及验收 29 性能试验 31 31 油漆、标志、包装与运输
GB/38653一2020 前 言 本标准按照GB/T1.1一2009给出的规则起草
本标准由电器工业协会提出
本标准由全国汽轮机标准化技术委员会(SAC/TC172)归口
本标准起草单位:东方电气集团东方锅炉股份有限公司、上海发电设备成套设计研究院有限责任公 司、国核电力规划设计研究院有限公司、哈尔滨锅炉厂有限责任公司、上海电气电站设备有限公司上海 电站辅机厂、哈尔滨汽轮机厂有限责任公司、东方电气股份有限公司
本标准主要起草人;邓科,陈鑫,刘军良、王锦生、赵治军、袁宁、陈辉、王琳、张彦军、许宝军、李国骥、 刘学、胡方、陈健、张义
GB/T38653一2020 核电厂常规岛高压加热器技术条件 范围 本标准规定了核电厂常规岛高压加热器(以下简称高加)的性能及设计要求、材料、制造、检验、验 收、性能试验及油漆、标志、包装与运输要求
本标准适用于U形管式高压加热器 规范性引用文件 下列文件对于本文件的应用是必不可少的
凡是注日期的引用文件,仅注日期的版本适用于本文 件
凡是不注日期的引用文件,其最新版本(包括所有的修改单)适用于本文件 GB/T150.1一2011压力容器第1部分;通用要求 压力容器第2部分;材料 GB/T150.22011 GB/T150.3一2011压力容器第3部分;设计 GB/T150.4压力容器第4部分:制造、检验和验收 GB/T151一2014热交换器 GB/T18042000 -般公差未注公差的线性和角度尺寸的公差 GB/T5310高压锅炉用无缝钢管 GB/T6479高压化肥设备用无缝钢管 GB/T8923.1一2011涂覆涂料前钢材表面处理表面清洁度的目视评定第1部分:未涂覆过 的钢材表面和全面清除原有涂层后的钢材表面的锈蚀等级和处理等级 GB/T9948石油裂化用无缝钢管 GB/T13296锅炉,热交换器用不锈钢无缝钢管 GB/T24591高压给水加热器用无缝钢管 24593锅炉和热交换器用奥氏体不锈钢焊接钢管 GB/T25198压力容器封头 GB/T26929压力容器术语 GB/T29465浮头式热交换器用外头盖侧法当 GB/T30065给水加热器用铁素体不锈钢焊接钢管 HG/T20592钢制管法兰(PN系列 HG/T20615钢制管法兰(Class系列 B/T4711压力容器涂敷与运输包装 JB/T5862汽轮机表面式给水加热器性能试验规程 NB/T47008承压设备用碳素钢和合金钢锻件 NB/T47010承压设备用不锈钢和耐热钢锻件 NB/T47013.2一2015承压设备无损检测第2部分:射线检测 NB/T47013.32015承压设备无损检测第3部分;超声检测 NB/T47013.42015承压设备无损检测第4部分;磁粉检测 NB/T47013.5一2015承压设备无损检测第5部分;渗透检测
GB/T38653一2020 NB/T47013.8一2012承压设备无损检测第8部分;泄漏检测 NB/T47013.102015承压设备无损检测第10部分;衍射时差法超声检测 NB/T47014承压设备焊接工艺评定 47015压力容器焊接规程 47018承压设备用焊接材料订货技术条件 47021甲型平焊法兰 NB/T47022乙型平焊法兰 NB/T47023长颈对焊法兰 NB/T47041塔式容器 NB/T47065.1容器支座第1部分;鞍式支座 NB/T47065.3容器支座第3部分耳式支座 TsG21一2016固定式压力容器安全技术监察规程 3 术语和定义 014和GB/T26929界定的以及下列术语和定义适用于本文件
GB/T150.1一201l、GB/T151 3.1 常规岛conventionalisland;cI 核电厂汽轮发电机组配套设施及所在厂房的总称
3.2 高压加热器highpressurefeedwaterheater 利用汽轮机高中压段的抽汽加热给水的换热器
注1,高压加热器属于管壳式换热器,是位于给水回热系统主给水系与主给水母管之间的加热器
注2:单独由过热蒸汽冷却段组成的高加可称为蒸汽冷却器
注3:单独由疏水冷却段组成的高加可称为疏水冷却器
3.3 设计压力designpressure 设定的容器顶部的最高压力
注1与相应的设计温度一起作为容器的基本设计载荷条件,其值大于或等于最高工作压力
注2:管程和壳程分别设定设计压力
3.4 管程设计温度tubesidedesigntemperature 管箱壳体(或封头)及其他受压零件设计时设定的温度
注1:管程设计温度同时也是换热管的设计温度
注2:管程设计温度与管程设计压力一起作为管程设计载荷条件
3.5 壳程设计温度shellsidedesit sigtemperature 壳程壳体、封头及其他受压零件的设计温度
注1:当具有过热段时,此温度可分区设置
注2壳程设计温度与壳程设计压力一起作为壳程设计载荷条件 3.6 终端温差terminaltemperaturedifterenee;TID 进口处抽汽压力下的饱和温度与给水出口温度之差
注终端温差也可称为“上端差”
GB/38653一2020 3.7 疏水冷却段端差drainsubeolerapproach;DcCA 疏水出口温度与给水进口温度之差
注:疏水冷却段端差也可称为“下端差” 3.8 过热蒸汽冷却段dlsuperheatng2zwne;Ds 把过热抽汽的一部分显热传给给水,从而提高给水温度的区段 3.9 凝结段cdensing Z0ne 通过蒸汽凝结加热给水的区段
3.10 ;Dc 疏水冷却段drainsubheooling ingzone; 把疏水的热量传给给水,使疏水温度降到低于饱和温度的区段 3.11 壳程压降shellside' preSSuredrop 介质流经壳程的压力损失
3.12 管程压降 tube" sidepresure drop 介质流经管程的压力损失
3.13 疏水drains 从较高压力级进人壳体的凝结水与加热器自身凝结水的总称
3.14 换热面积heattransferarea 3.14.1 计算换热面积effeetivearea 以换热管外径为基准,扣除不参与换热的换热管长度后,计算得到的外表面积
3.14.2 公称换热面积ominalarea 圆整为整数后的计算换热面积 注:公称换热面积在设计总图中列出,并在铭牌上表示 3.15 waterfiledtime 满水时间 加热器壳侧水位从最高液位上涨到顶部全充满水的时间
注满水时间取下述流量较大情况下的时间 -两根换热管破裂四个断口)的爆管量; 0%的给水流量
3.16 共用旁踏whoepu 高压加热器共用的管侧旁路系统 3.17 性能设计工况pertn rmanedesigncondition 以用户或设计委托方指定的考核性能指标进行传热计算的工况
GB/T38653一2020 注1:性能设计工况一般为汽轮机最大连续出力运行工况(TMCR工况.
注2;用户或设计委托方也可指定某一工况作为性能设计工况
3.18 condition 强度设计工况strengthdesign 以满足强度安全进行强度计算的工况
注1:强度设计工况一般为阀门全开工况(VwO工况)
注2:用户或设计委托方也可指定某一工况作为强度设计工况
3.19 污垢热阻toingre esistance 换热面上沉积物所产生的传热阻力
性能及设计要求 4.1 -般规定 4.1.1设计条件 4.1.1.1用户或设计委托方应确定设计条件(见表1. 表1设计条件 建造规范项目 要求执行的建造规范内容 安装形式(卧式,正立式、倒立式》 安装位置(室内或室外 形式(或级数 布置形式单列或多列 空间极限总长度加上检修所需空间 给水流量 给水进、出口温度 管程设计参数 给水进、出口熔值 包括运行时可能出现的各种工况 给水管道尺寸 管程设计压力 各加热燕汽流量 各加热蒸汽压力 各加热蒸汽温度 壳程设计参数 各加热蒸汽熔值 包括运行时可能出现的各种工况 各疏水进、出流量 各水进,出温度 各疏水进、出熔值 终端温差 端差 包括运行时可能出现的各种工况 疏水冷却段端差 pH9.5针对碳钢、铁素体不锈钢换热管 水质 氯离子含量<25mg/L(针对奥氏体不锈钢换热管)
GB/38653一2020 表1(续 要求执行的建造规范内容 建造规范项目 安装位置气象特征与环境条件 安装位置地震基本烈度和设计基本地震加速度 安装位置场地土类别 其他 设计使用寿命 噪声标准 4.1.1.2适宜时,用户或设计委托方可提出设计条件的补充项目(见表2). 表2设计条件补充项目 建造规范项目 要求执行的建造规范内容 壳体材质 管箱材质 材质 管板材质 换热管材质 其他部件材质 管程压降 压降 壳程压降 备用管子数量 备用管 管程设计温度 壳程设计压力 设计参数 壳程设计温度 耐压试验压力 污垢热阻 用户或设计委托方未提供污垢热阻时,换热管内表面的污垢热阻可取不低于3.52×10-》m'
C/w,过热蒸 》m”
"/w
汽冷却段、疏水冷却段换热管外表面的污垢热阻可取不低于5.28X10-" 4.1.2载荷 4.1.2.1设计时应考虑以下载荷 内压,外压或最大压差; -膨胀量不同引起的作用力; 液柱静压力液柱静压力小于设计压力的5%时,可忽略不计)
4.1.2.2适用时应考虑下列因素: 自重及正常工作条件下或耐压试验状态下内装介质的重力载荷: 附属设备及隔热材料,衬里、管道、扶梯、平台等的重力载荷; 风,地震、雪载荷; 支座及其他型式支承件的反作用力;
GB/T38653一2020 连接管道和其他部件的作用力; -温度梯度引起的作用力; -冲击载荷包括压力急剧波动引起的冲击载荷、流体冲击引起的反力等); -运输或吊装时的作用力
4.13设计压力 4.1.3.1 管程设计压力 管程设计压力应满足下列要求: -大于或等于主给水泵出口的最大压力 -大于或等于主给水系统设计压力
4.1.3.2壳程设计压力 壳程设计压力不应低于各工况壳程最高运行压力的115%
4.1.4设计温度 4.1.4.1 管程设计温度 管程设计温度不应低于壳程设计压力下的燕汽饱和温度
当具有过热蒸汽冷却段时,换热管的设 计温度还应增加20C
4.1.4.2壳程设计温度 具有过热蒸汽冷却段时,在熔图上,从强度设计工况的抽汽压力和温度处,作等饷线与设计压力 线相交,其壳体短节设计温度不应低于该交点处的温度,其余部分壳体的设计温度不应低于设计压力下 的蒸汽饱和温度
没有设置过热蒸汽冷却段时,壳程设计温度应不低于壳程介质最高工作温度
4.1.5厚度附加量 4.1.5.1厚度附加量按式(1)确定
C=C十C 式中 厚度附加量,单位为毫米(mm); C 材料厚度下极限偏差(见4.1.5.2),单位为毫米(mm); 腐蚀裕量(见4.1.5.3),单位为毫米(mm)
C 4.1.5.2板材或管材的厚度下极限偏差应符合相应材料标准的规定
4.1.5.3腐蚀裕量按下列原则考虑和选取: 对有均匀腐蚀或磨损的元件,应根据预期的设计使用年限和介质对金属材料的腐蚀速率(及磨 蚀速率)确定; 各元件受到的腐蚀程度不同时,可采用不同的腐蚀裕量; 碳素钢或低合金钢制高加,壳程筒身腐蚀裕量不小于1mm; -管板、浮头法兰和球冠形封头的两面均应考虑 -管箱平盖、凸形封头、管箱和壳体内表面应考虑 管板和管箱平盖上开槽时,可将高出隔板槽底面的金属作为腐蚀裕量,但当腐蚀裕量大于槽深 时,还应加上两者的差值;
GB/38653一2020 -设备法兰和管法兰的内径面应考虑 换热管、钩圈、浮头螺栓和纵向隔板,一般不考虑; 分程隔板的两面均应考虑; -拉杆、,定距管,折流板和支持板等非受压元件,一般不考虑
4.1.6许用应力 4.1.6.1材料的许用应力应按GB/T150.1一2011中表1、表2确定
4.1.6.2受压元件用钢材的许用应力值应按GB/T150.2一2011选取 4.1.6.3复合钢板的许用应力应按GB/T150.1一2011中4.4.3确定
4.1.6.4圆筒许用轴向压缩应力应按GB/T150.l一2011中4.4.5和相关标准确定 4.1.6.5需要考虑地震载荷或风载荷与4.1.2的载荷组合时,允许元件的设计应力不超过许用应力的 1.2倍,其组合要求按相应标准的规定
4.1.7耐压试验 4.1.7.1耐压试验的要求和试验压力应符合GB/T150.1l一201l中4.6的要求
4.1.7.2耐压试验的种类和要求应在图样上注明 4.1.7.3按压差设计的高加,应在图样上提出压力试验时升、降压的具体要求
4.1.7.4应在图样上提出管接头的试验方法和压力
4.1.7.5试验时应在试验位置的最高点设置排气孔,排气孔应是设备接头或液压试验端盖的一部分,其 位置应利于设备充人试验介质时将气体完全排出
4.1.8封口焊检漏试验 4.1.8.1换热管与管板的封口焊应进行空气检漏及氨检漏试验,氨检漏允许漏率指标小于10Pam/s 4.1.8.2检漏试验的种类和要求应在图样上注明 4.2结构设计 4.2.1结构型式 U形管高加典型结构示意见图1
GB/T38653一2020 20 19 18 说明: 16 人孔/检修孔 防冲板 -拉杆; -活动支座 1l -放气管/仪表管; 蒸汽进口管; 12 放气管; 17 固定支座; 给水出口; 8 壳程壳体; -壳程封头; 18- 13 给水进口; -管箱封头 折流板/支持板 -疏水出口管 -放水管/仪表管; 9 14 管板; 10 换热管; 15 -放水管/仪表管; 20 分程隔板
图1U形管高加典型结构示意图 4.2.2管程 4.2.2.1管板上换热管孔的布置 换热管常用排列形式示意见图2
景 b 正三角形排列30° 转角正三角形排列60° 正方形排列(90" 转角正方形排列(45° 图2换热管排列形式示意图 换热管中心距按GB/T151一2014中6.3,1.2的规定
布管限定圆直径按GB/T1512014中6.3.1.3的规定
GB/38653一2020 4.2.2.2管程分程 4.2.2.2.1 管程数一般有1、2、4、6、8、10、12共7种,常用的分程布置形式可按GB/T151一2014中 图6-12 4.2.2.2.2多管程结构应尽可能使各管程的换热管数相近、分程隔板槽形状简单、密封面长度较短
4.2.2.3管箱 管箱应符合下列要求: 多管程管箱平盖上的分程隔板槽结构尺寸应与管板的分程隔板槽一致,见4.2.2.8.3.2; 管箱平盖与管箱的连接紧固件宜采用双头螺柱 采用轴向人口接管的管箱,接管中心线处的最小深度不应小于接管内径的1/3 当o'>9000lkg/ms")时,采用轴向人口接管的管箱宜设置防冲结构 -管箱人口管的流体密度,单位为千克每立方米(kg/m'). 注:? -管箱人口管的流体速度,单位为米每秒(m/s)
-管箱可采用简节与椭圆封头组合形式,也可直接采用半球形封头形式,其计算方法按 GB/T150.32011的规定
4.2.2.4分程隔板 分程隔板及与管板的连接结构应符合下列要求 分程隔板结构要求按GB/T151一2014中6.3.6的规定; -当管箱与管板不要求分离时,分程隔板与管板可采用焊接连接
4.2.2.5检修人孔 管箱的检修人孔宜采用压力自密封人孔或半强制密封人孔
4.2.2.6给水管及其他开口设置 4.2.2.6.1管箱应设置给水进口管、给水出口管、放气管,放水管和检修孔,其要求见表3
表3管箱上管口的设置 接管 安装位置 管径要求 给水进口管 换热管流程人口 满足流速要求 给水出口管 换热管流程出口 满足流速要求 >D20 放气管 管箱顶部或顶部给水管上 管箱底部或底部给水管上 >DN 放水管 20 封头 DN400 检修孔 注:DN 公称尺寸,用于管道系统元件的字母和数字组合的尺寸标识,后跟无量纲的整数数字
4.2.2.6.2管侧安全阀接口可设置于管箱上或设置于系统管道上,其管径应大于或等于DN20
4.2.2.6.3接管与管箱的连接及其他要求按GB/T151一2014中6.13的规定 4.2.2.7换热管 换热管除应符合GB/T151一2014中6.4的I级管束的规定外同时符合下列要求 -换热管宜采用碳钢、铁素体或奥氏体不锈钢管;
GB/T38653一2020 -满足有效换热面积之外的管子数量不低于管子总数量的5% 换热管按最小或平均壁厚标注在图样及设备技术规格书中
4.2.2.8管板 4.2.2.8.1管孔 管孔按GB/T151一2014中6.5.1的I级管束管板管孔的规定
4.2.2.8.2拉杆孔 焊接连接的拉杆孔示意见图3a),拉杆孔深度L,宜大于拉杆直径的d
拉杆孔直径按式(2 确定
d=d十1.0 式中 拉杆孔直径,单位为毫米(mm); d dn 拉杆直径,单位为毫米(mm). 螺纹连接的拉杆螺纹孔示意见图3b),螺纹深度L
应大于拉杆螺纹长度L
1-2X45 2×45" 焊接连接的拉杆孔示意 螺纹连接的拉杆孔示意 b 说明: -拉杆孔直径,单位为毫米(n d mm); 2 拉杆孔深度,单位为毫米(mm); -拉杆孔螺纹深度,单位为毫米(G mm); ! -拉杆螺纹长度,单位为毫米(mm. 图3拉杆孔示意图 4.2.2.8.3法兰连接的管密封面 4.2.2.8.3.1固定管板与标准容器法兰配合时,管板密封面结构尺寸应按NB/T47021、,NB/T47022或 NB/T47023的规定确定
4.2.2.8.3.2分程隔板槽的尺寸按下列要求确定 -槽深应大于垫片厚度,且不宜小于4mm,隔板槽密封面应与环形密封面平齐 114mm; 槽宽a
宜为8mm" 多管程的隔板槽倒角不应妨碍垫片的安装;隔板槽拐角处的倒角宜为45?(见图4),倒角尺寸b 10
GB/38653一2020 宜大于分程垫片的圆角半径R
说明 分程隔板槽宽,单位为毫米(mm)1 4" 分程隔板槽倒角尺寸,单位为毫米(mm); 分程垫片的圆角半径,单位为毫米(mm). R 图4管板的分程隔板槽示意图 4.2.2.8.4管板堆焊层 管板与换热管的连接面宜堆焊,堆焊层厚度大于或等于3 mm ,材质与换热管同类或相似
4.2.2.9换热管与管板的连接 4.2.2.9.1换热管与管板的最小泄漏通道为每个角焊缝的最小泄漏通径即角焊缝厚度),单个值应大 于或等于换热管名义厚度()的三分之二, 4.2.2.9.2胀接及焊接结构尺寸按GB/T151一2014中6.6的规定或采用其他可靠的连接结构尺寸
4.2.2.10管板与管箱、壳体的焊接连接 管板与管箱、壳体的焊接连接可根据设计条件,设备结构等因素选用GB/T151-2014中附录I所 示结构,也可采用其他可靠的连接结构
4.2.3壳程 4.2.3.1管系的布置 应由过热燕汽冷却段、凝结段、疏水冷却段三段组成,适宜时可由其中各段单独或过热燕汽冷却段 加凝结段、凝结段加疏水冷却段组合而成
4.2.3.2导流和防冲设置 导流和防冲设置应符合下列要求 -导流和防冲按GB/T151一2014中6.8.1的规定; 燕汽进口接管和疏水进口接管下方应设置防冲结构,管束上的防冲板半径应大于或等于接管 11
GB/T38653一2020 中心到介质出口处发散角45"处的尺寸
4.2.3.3折流板和支持板 折流板和支持板按GB/T151一2014中6.8.2的I级管束规定
4.2.3.4防短路结构 防短路结构按GB/T151一2014中6.8.3的规定
4.2.3.5拉杆,定距管 拉杆,定距管按GB/T151一2014中6.8.5的规定 4.2.3.6滑道 滑道按GB/T151一2014中6.8.6的规定,也可采用其他可靠的结构
4.2.3.7 壳体 壳体尺寸除满足强度和结构要求外,还应满足各类燕汽和疏水进人的扩容要求,满水时间宜在 60s120s
由于场地或结构限制等原因,不能靠增大壳体尺寸保证满水时间时,应考虑增加外置式疏水箱或采 取缩短高加给水旁路阀闸阀,燕汽管路关断阀动作时间等措施保护汽轮机安全 4.2.3.8接管及其他开口 4.2.3.8.1壳体至少应设置蒸汽进口管,疏水出口管、启动放气管,运行排气管、放水管、安全阀接口;紧 急疏水管、疏水人口管根据需要设置,要求见表4
表4壳体上管口的设置 接管 安装位置 管径要求 蒸汽进口管 壳体顶部 满足流速要求 疏水出口管 壳体底部,当管道布置有特殊要求时,也可位于壳体侧面 满足流速要求 壳体顶部,当具有疏水冷却段时 >DN20 启动放气管 其段内顶部位置也需设置侧向疏水出口除外 运行排气管 按内部结构设计 排放能力为进人蒸汽量的0.5% 放水管 DN20 壳体底部 安全阀接管 壳体顶部 满足泄放量要求 紧急疏水管 壳体底部 满足疏水出口管的流速要求 满足流速要求 疏水人口管 壳体凝结段具有扩容空间的位置 液位测量接口 壳体侧面或顶部 满足仪控要求 压力,温度测点 壳体/介质出,人管口侧面或顶部 满足仪控要求 4.2.3.8.2连续运行排气管应单独与冷凝器或除氧器连接
4.2.3.8.3接管与壳体的连接及其他要求按GB/T151一2014中6.13的规定
12
GB/38653一2020 4.2.4设备及接管法兰 4.2.4.1设备法兰设计应符合GB/T150.3一2011的规定
4.2.4.2设备法兰应优先选用NB/T47021,NB/T47022,NB/T47023,GB/T29465的法兰
4.2.4.3接管法兰应优先选用HIG/T20592、HG/T20615的法兰
4.2.4.4非标设计时,应优先选用相关标准的法兰连接尺寸
4.2.5密封及垫片 4.2.5.1密封结构及垫片应根据工作条件(介质、温度、压力)按相关标准进行设计或选用
4.2.5.2管法兰垫片、管箱垫片、管箱侧垫片按相关标准选用
4.2.5.3金属平垫片、金属波齿复合垫片、椭圆垫、八角垫,透镜垫等按相关标准进行设计、选用
有成熟使用经验时,也可采用其他密封结构
4.2.5.4 4.2.6 支座 4.2.6.1 卧式高加支座 卧式高加鞍式支座布置示意见图5,布置原则如下 公称长度小于或等于3m时,鞍座间距L郎宜取公称长度的40%60%; 公称长度大于3m时,鞍座间距L;宜取公称长度50%一70% 宜使L
和L
'相近; 必要时应对支座和壳体进行强度和稳定性校核 确定鞍座与相邻接管的距离时应考虑鞍座基础及保温的影响 说明 -固定鞍座; -活动鞍座 图5鞍式支座布置示意图 鞍式支座可按NB/T47065.1选用
4.2.6.2立式高加支座 立式高压加热器支座包括耳式支座和裙式支座,立式支座布置示意见图6. 4.2.6.2.1 4.2.6.2.2耳式支座可按NB/T47065.3选用,布置原则如下 壳程壳体公称直径小于或等于DN800时,至少应设置2个支座,且应对称布置 13
GB/T38653一2020 壳程壳体公称直径大于DN800时,至少应设置4个支座,且应均匀布置
经充分考虑各种载荷及其组合载荷影响,并经强度校核确认,支座数量可少于上述要求
4.2.6.2.3裙式支座可按NB/T47041进行设计 耳式支座示意 裙式支座示意 a 说明: -耳式支座; -裙式支座
图6立式支座布置示意图 4.2.7设备附件 4.2.7.1管箱平盖宜设置吊耳等起吊附件
4.2.7.2可抽管束的固定管板上宜设置吊环螺钉孔
正常操作时,应采用丝堵和垫片保护螺孔,维修时 换装吊环螺钉抽装管束
4.2.8保温 表面温度超过50C的设备应进行保温
环境温度不高于25C时,设备保温结构外表面温度不应 超过50C;环境温度高于25C时,保温结构外表面温度可比环境温度高25C
4.3设计计算 4.3.1承压壳体与隔板 承压壳体与隔板的计算按GB/T151一2014中7.1的规定
14
GB/38653一2020 4.3.2开孔补强 开孔补强应符合GB/T150.3一2011中第6章的规定
4.3.3换热管 换热管的计算应符合GB/T151一 -2014中7.3的规定
4.3.4 管板 管板的计算应符合GB/T151一2014中7.4或其他相关标准的规定
4.3.5振动 振动计算参见GB/T151一2014附录C
4.3.6人孔密封 人孔密封计算参见G;B/T150.32011附录C
4.3.7圆筒形壳程和管程的接管荷载 文件要求 4.3.7.1 接管允许载荷应在设计文件中列出 4.3.7.2管道实际应力超过接管允许值的处理 管道实际应力或载荷超过接管允许载荷值时,应采取补强措施
4.3.7.3接管的力和力矩计算 4.3.7.3.1外加载荷作用在球形壳体或圆筒形壳体上所引起的局部力和力矩示意如图7所示
15
GB/T38653一2020 MMec 正视图或平面图 b 横截面图 说明 -壳体; -接管; Fe -最大径向合力; MR 最大周向合力矩 eM MRM -最大纵向合力矩; 接管口端部外半径; R
-壳体平均半径
图7局部力和力矩示意图 43.7.3.2无因次数87按式(3)和式(4)计算,根据8和从图8、图9和图10中查到a、习和A =0.875 (3 R T 式中: 无因次数 接管口端部外半径,单位为米(m); r' -壳体平均半径,单位为米(m); 壳体厚度,单位为米m); 无因次数 16
GB/T38653?2020 88 800o00 00 000 50000 40000 30000 20000 88 000 70 0oo 6 5000 4000 3000 2000 300 700 00 00 400 100 300 50 200 D 40 30 20 10 0.05 0.10 0.15 0.20 0.25 0.30 0.35 0.40 0.45 0.50 0.55 0.60 ?8a? 17
GB/T38653?2020 100000 B 80000 70000 60000 50000 40000 30000 300 20000 000 " 0oo 8000 6000 5000 4000 100 3000 2000 To0 00 so0 400 300 200 60 0 40 30 20 10 0.05 0.10 0.15 0.20 0.25 0,30 0.35 0.40 0.45 0.50 0.55 0.60 ?9? 18
GB/T38653一2020 7000o 60000 50000 40000 30000 20000 88 0o00 7000 000 6 5 000 4000 3000 300 2 000 8 80o0 700 00 100 00 00 300 -50 200 30 20 0.05 0.10 0.15 0.20 0.25 0.30 0.35 0.40 0.45 0.50 0.55 0.60 图10A线算图 4.3.7.3.3设计压力产生的应力应取a与[][壳体材料在设计温度下的许用应力,单位为兆帕(MPa] 中的较小值,口按式(5)计算
19
GB/T38653一2020
-半(依
- 式中 由设计压力产生的应力,单位为兆帕(MPa); 设计压力,单位为兆帕(MPa); 壳体平均半径,单位为米(n R m; T 壳体厚度,单位为米(m) 4.3.7.3.4接管的最大径向合力按式(6)计算
R FRRr (S -O 式中 F -最大径向合力,单位为牛顿(N); RRF R 壳体平均半径,单位为米(m); S -设计温度下壳体材料的屈服强度,单位为兆帕(MPa); 由设计压力产生的应力,单位为兆帕(MPa); 无因次数; 4.3.7.3.5接管的最大周向合力矩按式(7)计算
RrS MRcM= 式中 M -最大周向合力矩,单位为牛顿米(N m; RcM 壳体平均半径,单位为米( R m; 接管口端部外半径,单位为米(m); s -设计温度下壳体材料的屈服强度,单位为兆帕(MPa); -无因次数
4.3.7.3.6接管的最大纵向合力矩按式(8)计算
R品r (S,一a MRLM 式中 M -最大纵向合力矩,单位为牛顿米(N
m; .M Rm 壳体平均半径,单位为米(m); 接管口端部外半径,单位为米(m); r' s -设计温度下壳体材料的屈服强度,单位为兆帕(MPa); -由设计压力产生的应力,单位为兆帕(MPa); 无因次数
接管允许载荷应在图11所示以坐标原点、F即和M为界限的三角形面积内
F.M拨 4.3.7.3.7 式(9)和式(10)取值
20
GB/38653一2020 FR Mg 图11接管允许载荷范围 =FRee 9 Fe 式中 F郎 -最大合力,单位为牛顿(N); F 最大径向合力,单位为牛顿(N)
RRF 10 Meu=min(lMwu,|Mw.M| 式中: M8 -最大合力矩,单位为牛顿米(N m lRM 最大周向合力矩,单位为牛顿米(Nm); MRcN 最大纵向合力矩,单位为牛顿米(Nm>. MRLM 4.3.7.3.8外加载荷位于图11所示三角形区域外时,应复核外加载荷包括r、y、、各方向的力及其合 成力和合成力矩)是否均位于安全系数取1的三角形区域内
4.4安全装置 4.4.1壳程和管程的超压泄放装置 4.4.1.1管程给水进、出口之间至少应设置一只DN20的安全阀,共用旁路设置的多级高加管程可共 用一只管程安全阀,也可单独设置
4.4.1.2壳程应至少设置一只安全阀,其泄放量按下述流量的较大者,并留10%余量 给水流量的10%; 当一根换热管完全断裂产生两个断口时的给水流量G,按式(1l)计算
二64x10d、P下/ G 式中: 给水流量,单位为千克每秒(kg/) G 换热管内径,单位为毫米(mm); d 管侧设计压力,单位为兆帕(MPa); P P 壳程设计压力,单位为兆帕(MPa); 换热管内水比容,立方米每千克(m=/kg). 4.4.2液位测量装置 4.4.2.1应设置液位测量装置,除仅有过热燕汽冷却段的燕汽冷却器外,壳程宜设置五挡水位: 21
GB/T38653一2020 正常水位 -正常运行时的水位; a b) 低一水位 疏水阀完全关闭的水位; e 高一水位 -报警及危急疏水阀开始打开的水位; d) 高二水位 危急疏水阀完全打开的水位; e 高三水位 解列的水位
4.4.2.2蒸汽冷却器可仅设置解列水位 4.4.2.3高加水位控制仪表装置可采用集箱母管结构或独立接管结构,如采用集箱母管结构,设备引出 管规格应大于或等于DN50.
4.4.3压力测量装置 管程和壳程应至少各设置一个压力测量装置,宜设置于给水出口管和蒸汽进口管上 4.4.4温度测量装置 管程和壳程应至少各设置一个温度测量装置,宜设置于给水出口管和蒸汽进口管上. 4.5性能 4.5.1温度 性能设计工况下,高加总温升不应低于设计值4C
4.5.2端差 4.5.2.1上端差应符合以下要求 具有过热蒸汽冷却段时,上端差应大于或等于-1.7C -没有设置过热蒸汽冷却段时.上端差应大于或等于1C 上端差要求小于一1.7C时,应采用外置式蒸汽冷却器
4.5.2.2下端差应符合以下要求 卧式或倒立式高加具有疏水冷却段时,下端差应大于或等于5.6; 正立式高加下端差应大于或等于8C 下端差小于5.6C时,应采用外置式疏水冷却器
4.5.3流速 4.5.3.1换热管内流速 性能设计工况及平均温度(给水进口和给水出口温度的算术平均值)下,通过换热管内的给水流速 不应超过下列数值: 不锈钢换热管:3m/s; 碳钢管;2.4m/s
4.5.3.2接管介质流速 性能设计工况下,按内径选择接管,管内介质流速不应超过表5的规定
22
GB/T38653一2020 表5接管介质流速 接管 流速极限 给水进、出口 6.0m/s 过冷疏水 1.2m/s 疏水出口 水位受控 1.2nm/s 饱和疏水 水位不受控 0.6m/s 两相流体的质量流速 nmin(77.16,1220kg/m's7 疏水进口 扩容后的蒸汽质量流速及蒸汽流速 38.58kg/tm's 45.7m/s 含高湿度寨汽进口) 扩容后的液体流速 1.2m/s 混合物密度,单位为千克每立方米(kg/m');P燕汽进口绝对压力,单位为兆帕(MPa) 注:p 4.5.4 压降 4.5.4.1 管程压降 性能设计工况下,每台高加管程压降不应超过0.15MPa
4.5.4.2壳程压降 性能设计工况下每台高加壳程的总压降不应超过加热器抽汽级间压差的30%,且每段内的压降不 得超过35kPa(带疏水段正置立式高加除外
4.5.5噪声 离设备外表面1m处,噪声应小于85dB(A)
4.5.6事故工况 双列布置的情况下,因事故造成一列解列时,另一列应短时承受原单列流量的150%
材料 5 5.1选用及代用规定 5.1.1受压部件材料应符合GB/T150.22011及相关标准的规定,受压部件不应使用铸件
5.1.2制造单位对主要受压元件的材料代用,应事先获得原设计单位的书面批准,并应在竣工图上做 详细记录
5.1.3受压元件用钢应附有钢材生产单位的钢材质量证明书原件或者加盖了材料经营单位公章和经 办负责人签字(章)的复印件,容器制造单位应按质量证明书对钢材进行验收
容器制造单位应对下列 材料进行人厂复验,复验结果应符合相应材料标准的规定和设计文件的要求: 皿类压力容器的级锻件 -用于主要受压元件的境外牌号材料 -设计文件要求进行复验的材料
5.1.4焊接材料应符合NB/T47018及设计文件的规定
容器制造单位应对焊接材料进行人厂复验, 复验结果应符合制造单位规定
23
GB/T38653一2020 5.2标志及移植 受压元件的材料应有可追溯标志
制造过程中,如原标志被裁掉或材料分成几块时,应在材料分割 前完成标志移植
5.3其他要求 5.3.1换热管束应按材料牌号对应的标准分别满足GB/T5310.GB/T6479、GB/T9948 GB/T13296,GB/T24591,GB/T24593,GB/T30065或其他相关标准的要求
5.3.2主要受压元件采用未列人TsG;21一2016规定的协调标准的材料,应按照相关标准的规定通过 技术评审,方可使用
主要受压元件采用已列人TsG21一2016规定的协调标准的材料,抗拉强度下限值大于或等于 5.3.3 540MPa的材料及用于压力容器设计温度低于一40 T的低合金俐,如果材料制造单位没有该钢材的制 造或者压力容器应用业绩,应按相关标准的规定通过技术评审,方可使用
5.3.4主要受压元件用碳钢、碳缸钢,非含铬低合金钢铬含量应控制在0.15%一0.30%之间
5.4锻件要求 锻件应符合NB/T47008或NB/T47010的规定,锻件的级别应符合GB/T150.2201l中6.1.3 的规定
制造 6 6.1冷、热加工成形与组装 6.1.1封头和筒体 6.1.1.1封头应采用整块钢板制成,不应拼接
6.1.1.2封头成形,热处理,无损检测应符合设计图样和GB/T25198的要求
6.1.1.3管侧、简体的同一截面上最大直径与最小直径之差e<0.5%DN,且应符合下列规定 公称尺寸小于或等于DN1200时,其值不得大于5mm 公称尺寸为DN1200~DN2000时,其值不得大于7mm; 公称尺寸大于DN2000时,其值不得大于12mm
6.1.1.4简体直线度检查,应通过中心线的水平和垂直面,即沿圆周0",90",180",270°四个部位测量
直线度允许偏差为筒体总长度L的0.1%,且应符合下列规定 -L小于或等于6000mm时,其值应小于或等于4.5mm; -L大于6000mm时,其值应小于或等于8 mm
6.1.1.5管侧筒体上的焊接管孔不应在焊缝上,且管孔中心与焊缝边缘的距离应大于或等于0.8d d为开孔最大直径),且大于或等于0.5d部+12mm 6.1.1.6管侧封头和筒体热加工后,应清除内外表面的氧化皮,不应有裂纹、重皮等缺陷
凸起、凹陷、 疤痕等缺陷深度或高度小于或等于锅材厚度的5%且小于或等于2mm时,应将其打磨清除并平滑过 渡;深度超过上述厚度时,应在热处理前进行补焊磨平
应对补煤处进行100%表面检测 凡有碍管束拆装的壳体内壁焊缝余高及有碍垫板装配的壳体外壁焊缝余高均应磨平至与母材 6.1.1.7 表面平齐
6.1.2换热管 6.1.2.1换热管的外观和尺寸极限偏差应符合GB/T151一2014中I级管束和设计文件的要求
24
GB/T38653一2020 6.1.2.2换热管不应环向拼接
管材应无缺陷;有缺陷的管材不应修复后使用
注缺陷包括分层、撕裂,瑕疵、开裂,裂缝、凹痕,有害的划痕、环纹、裂纹、折叠和刻痕等 612换热管不宜热弯冷弯后应按GBT11一21进行热处理 6.1.2.4换热管弯制后,当R/d大于1.5及工艺稳定时,对每种通球直径抽取其最小弯曲半径管子数 的5%,且不少于2根进行通球检查,以钢球通过为合格
钢球直径按表6选取
表6钢球直径 弯管半径R R一2.5l 2.5dR<3.5d R>3.5d 钢球直径 0.75d >0.8d >0,.85l 注R为弯管半径,d为管子外径,d为管子内径
6.1.2.5U形弯管直管段壁厚与规定壁厚的允许偏差应符合换热管原材料要求,U形弯管弯头部分的 管子壁厚按设计文件的规定
6.1.2.6换热管应按相关标准或技术协议进行100%无损检测
6.1.2.7管子弯曲成形后应逐根进行耐压试验,其介质要求、试验压力、保压时间按设计文件的规定
试验合格后应将介质放尽,并使管子干燥
6.1.3管板、折流板、支持板 6.1.3.1换热管外径和管板上管孔直径极限偏差应符合表7的规定
管板钻孔后,应抽查大于或等于 60的管板中心角区域内的管孔,允许有4%的管孔直径上极限超出表7的相应值,但不得超出相应上极 限偏差的50%,未达到上述要求时应进行100%检查
表7换热管外径及管板上管孔直径极限偏差 单位为毫米 管子外径 15.88 16 19 25 换热管 极限偏差 士0.10 16.25 19.25 25.25 管孔直径 l6.08 管板 十0.05 十0,05 十0.10 极限偏差 一0.05 一0.10 一0.10 6.1.3.2孔桥宽度极限偏差应符合下列规定 管板始钻(进钻)面上相邻两管孔中心距极限偏差为士0.3mm;任意两管孔中心距极限偏差为 a 士1mm
管板终钻出钻)面,其相邻两管孔之间的孔桥宽度B,最小孔桥宽度B b ,分别按式(12和 式(13)计算
管板厚度大于或等于160mm时,按表8选取B值 12 B=(S一d)一41 41=24
+C A=0.041×/ad B=0.6(S一d 13 式中: 孔桥宽度,单位为毫米(mm); B Bmm -最小孔桥宽度,单位为毫米(m mm; S -换热管中心距,单位为毫米(n mm; 25
GB/T38653一2020 -管孔直径,单位为毫米(mm); d 换热管名义外径,单位为毫米(mm); 孔桥偏差,单位为毫米(mm),A1=2A十C; A1 钻头偏移量,单位为毫米(mm),4!=0.041×0/d:; -附加量,单位为毫米(mm): 当 1d<16mm时,C=0.51; 当 id>16mm时,C=0.76:; -管板厚度,单位为毫米(mm 终钻后应抽查大于或等于60"管板中心角区域内的孔桥宽度,B值的合格率应大于或等于 c 96%,B的数量应控制在4%之内,未达到要求时应进行100%检查
6.1.3.3管板管孔表面粗糙度Ra6.3,管板孔表面应清理干净,不应有影响胀接或媒接连接质量的毛 刺、铁屑、锈斑、油污等,且不应有贯通的纵向或螺旋状刻痕
6.1.3.4折流板和支持板的管孔直径极限偏差应符合表9的规定,最大超差0.1mm的管孔数不得超 过管孔总数的4%
抽查一块折流板或支持板大于或等于60"管板中心角区域内的管孔,未达到要求时 应进行100%检查
6.1.3.5折流板和支持板机械加工表面粗糙度Ra12.5,外圆两侧面的尖角应倒钝,应去除折流板和支 持板上的毛刺
6.1.3.6折流板,支持板与管板上的管孔应与管束同心,且管孔两侧应倒角处理
表8管束孔桥宽度 单位为毫米 换热管外径 孔中心距 管孔直径 名义孔桥宽度 允许孔桥宽度" 最小孔桥宽度 S B S一d Br 15,88 20.64 16.08 4.56 3.22 2.74 15.88 22 16.08 5.92 4.58 3.55 15.88 22.23 l6.08 6.15 4.81 3.69 21 16 16.25 4.75 3.18 2.85 22 16.25 4.17 5.75 l6 3.45 19 24 19.25 4.75 3.31 2.85 19 25 19.25 5.75 4.30 3.45 25 32 25.25 6.75 5.47 4.05 为管板厚度>l60mm时允许的孔桥宽度
表9管孔直径及极限偏差 单位为毫米 折流板和支持板 换热管外径 孔径 极限偏差 +0.20 16.28 15,.88 16 16.40 十0.30 19 19.40 25 25.40 26
GB/38653一2020 6.1.4对接 6.1.4.1封头、筒体及管板对接时,厚板的削薄量应符合GB/T150.4的规定
6.1.4.2封头,筒体及管板对接时,其纵环缝对口错边量应符合GB/T150.4的规定
6.1.5管束的组装 6.1.5.1管系立架后,穿管前应确认所有隔板与管板之间对应管孔的同轴度
6.1.5.2拉杆上的螺母应拧紧,以免在装人或抽出管束时,因折流板窜动而损伤换热管
6.1.5.3穿管时不应强行敲打,换热管表面不应出现凹瘪或划伤
6.1.5.4除换热管与管板间以焊接连接外,其他任何零件均不得与换热管相焊 6.1.5.5滑道应与折流板、支持板焊接牢靠,滑道应凸出折流板支持板外缘
6.1.5.6在壳体上设置接管或其他附件时,应避免壳体变形影响管束套装
6.2胀接 管子与管板的胀接可采用机械或液压方式 6.2.1 应根据胀接工艺试验或工艺评定制定胀接工艺规程
6.2.2 穿管前,管孔应清洁无污物
管内清理采用压缩空气
6.2.3 6.2.4换热管材料的硬度宜低于管板的硬度 穿管前,应清除管板厚度加50mm长管端外表面的锈迹,直至显示金属光泽,且不应有重皮、凹 6.2.5 痕、裂纹及纵向或螺旋沟纹等缺陷
6.2.6换热管与管板连接型式按设计图样和工艺文件规定
6.2.7胀接后,应逐根检查管子与管板,如有松动或漏胀应补胀
如胀接后管子内壁存在裂纹,应换管
若拆除确有困难,经技术负责人批准后允许堵管
堵管 6.2.8 根数不宜超过总根数1%且总数不超过2根,堵管应遵守下列规定 堵管后不影响设备的安全性; 出厂资料应标记出堵管位置,并提供给用户 堵管根数超过2根时,由供需双方协商处理
6.3焊接 6.3.1下列各类焊缝的焊接工艺应按NB/T47014评定合格 受压元件焊缝; 与受压元件相焊的焊缝 熔人上述永久焊缝内的定位焊缝 受压元件母材表面堆媒、补媒 6.3.2焊工应按焊接工艺规程或者焊接作业指导书进行施焊,做好施焊记录,并在规定部位标记焊工 代号或者在焊接记录(含焊缝布置图)中记录焊工代号,并列人产品质量证明书中
有耐腐蚀要求的不 锈钢以及复合钢板,不得在耐腐蚀面采用硬印标记 6.3.3焊前准备和施焊过程应符合NB/T47015的要求,焊件相连部位及施焊区域不得有影响焊接质 量的锈蚀、油污等杂物和宏观的裂纹,重皮等 6.3 焊条、焊剂应按要求烘干;焊丝表面不得有油污、锈迹
.4 6.3.5管子与管板焊接前,应去除管板表面及管端处油污、锈迹等杂质和水汽(可预热30C一80). 焊接部位和场地应保持清洁
6.3.6封口焊焊缝和热影响区表面不应有咬边、裂纹、气孔,夹渣或未熔合等缺陷,管口不得有焊穿和 27
核电厂常规岛高压加热器技术条件GB/T38653-2020解析
随着我国经济的快速发展,能源需求不断增长,核电成为可持续发展的一种重要能源形式。而核电厂常规岛高压加热器作为核电站的重要组成部分,对于核电站的运行和安全起着至关重要的作用。因此,制定一套科学合理的技术条件标准就显得尤为重要。
该标准规定了核电厂常规岛高压加热器的技术条件,旨在保证核电站的安全、稳定运行、提高核电站的经济效益。以下是该标准中涉及到的主要技术条件:
1.型式与基本参数
该标准规定了高压加热器的型式和基本参数,包括额定蒸发量、设计压力、设计温度、介质等级、工作介质、进出口直径、高度、外形尺寸等。
2.材料
该标准对于高压加热器的材料作出了明确规定,要求材料必须符合相应的国家标准或行业标准,同时还需要进行严格的检测和评价。
3.制造与检验
该标准对于高压加热器的制造和检验也做出了详细规定,包括焊接、金属结构、气密性、水压试验等方面的内容。要求制造和检验必须符合相应的国家标准或行业标准,并严格按照质量控制系统实施。
4.安装与调试
该标准规定了高压加热器的安装与调试步骤,包括设备基础、支撑架、连管、防振、绝缘等方面的内容。要求安装与调试必须符合相应的国家标准或行业标准,并按照相关规范进行操作。
5.运行与维护
该标准对于高压加热器的运行和维护也做出了详细规定,包括日常检查、防腐、清洗、维修等方面的内容。要求运行与维护必须符合相应的国家标准或行业标准,并按照相关规范进行操作。
总之,该标准的实施可以有效提高核电站的安全性、可靠性和经济效益,保证核电站的长期稳定运行。