GB/T31032-2014
钢质管道焊接及验收
Weldingandacceptancestandardforsteelpipingsandpipelines
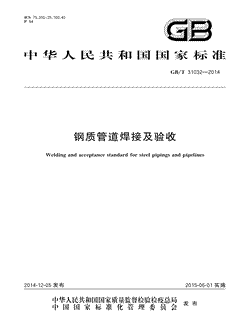
- 中国标准分类号(CCS)P94
- 国际标准分类号(ICS)25.160.40;75.200
- 实施日期2015-06-01
- 文件格式PDF
- 文本页数98页
- 文件大小1.53M
以图片形式预览钢质管道焊接及验收
钢质管道焊接及验收
国家标准 GB/31032一2014 钢质管道焊接及验收 wedingandaeptaneestandardtorsteelpipingsamdpipelines 2014-12-05发布 2015-06-01实施 国家质量监督检验检疫总局 发布 国家标准化管理委员会国家标准
GB/T31032一2014 目 次 前言 范围 规范性引用文件 术语和定义 焊接一般规定 4.1设备 4.2材料 焊接工艺评定 5.1工艺评定 5.2记录 5.3工艺规程 5.4焊接工艺规程的基本要素 5.5试验管接头的焊接 对接媒 10 5.6焊接接头的试验 对接焊 10 5.7试验管接头的焊接 角媒 5.8接接头的试验 角焊 焊工资格 8 概述 18 6.1 6.2资格考试 18 6.3上岗考试 1 6.4单项资格 6.5全项资格 20 6.6考试焊口外观检查 20 破坏性试验 6.7 26 6.8射线检测 仅用于对接焊 2: 6.9补考 2: 2: 6.10记录 施工现场焊接接头的设计和准备 2: 7.1 概述 2 7.2管口组对 7.3对接焊缝对口器的使用 7.4坡口 7.5气候条件 7.6作业空间 2 7.7层间清理 22 ? 7.8固定焊
GB/I31032一2014 25 7.9旋转焊 7.10焊口标记 25 25 7.11预热及焊后热处理 25 焊缝检验与人员资格 25 8.1检验内容 25 8.2检验方法 26 8.3检测人员的资格审定 26 8.4无损检测人员的资格 26 无损检测验收标准 26 9.1概述 26 9.2拒收权 26 9.3射线检测 32 9.4磁粉检测 3: 9.5渗透检测 3: 9.6超声检测 34 9.7咬边的外观检查标准 35 10缺陷的清除和返修 35 10.1返修权限 35 10.2返修规程 35 l0.3验收标准 35 10.4监督 35 10.5焊工 35 11无损检测 35 11.1射线检测方法 11.2磁粉检测方法 1.3渗透检测方法 1.超声检测方法 12有填充金属的机动焊 45 45 12.1适用的焊接方法 卫2.2焊接工艺评定 45 卫2.3记录 45 卫2.!焊接工艺规程 卫2.5焊接工艺规程的变更 12.6焊接设备和操作人员的审定 49 4s 12.7,合格机动梆操作工的记; 12.8现场焊缝的检查和试验 49 2.9无损检测验收标准 49 49 12.10缺陷的返修和切除 50 12.11射线检测 5d 12.12超声检测 附录A资料性附录本标准与APIStd1104:2010相比的结构变化情况
GB/T31032一2014 54 附录B资料性附录本标准与APIStd1104:2010技术性差异及其原因 59 附录C规范性附录环焊缝的附加验收标准 59 C1概述 c应力分新 60 C 爆接工艺 6 C 媒工资格 65 C 检测及验收标准 65 记录 74 返修 75 C.8术语 75 附录D(规范性附录)在役管道焊接技术 76 76 D.1概述 7? D.2在役管道系统的焊接工艺评定 D.3在役焊接焊工资格 81 8: D.4在役管道系统焊接的推荐操作 85 D.5在役管道焊缝的检测与试验 D.6无损检测验收标准包括外观检查) 86 缺陷的清除和返修 D.7 86 附录E(资料性附录 焊工考试记录 87 参考文献 92 图1对接接头焊接工艺评定试验的试样位置 10 图2拉伸试样 12 图3刻槽锤断试样 12 图4背弯和面弯试样(壁厚<12.7mm) 13 13 图5侧弯试样(壁厚>12.7 mm 图
刻槽锤断试伴的缺欠尺寸测量 l4 图" 导向弯曲试验胎具 图》冲击试样 图》刻槽锤断试样的位置,角焊焊接工艺及焊工粪格考试 图0 刻槽锤断试样的位置:角焊焊接工艺评定及焊工资格考试(包括支管连接焊工资格考试 图1对接焊焊工资格考试试验的试样位登 21 图1根部未即透 21 13错边未焊透 2 图 14中间未焊透 图 28 图 15焊道根部或接头顶部表面未熔合 28 图 16夹层未熔合 28 图17根部内凹 28 图18气孔最大分布;壁厚<12.7mm 30 图19气孔最大分布;壁厚>12.7 mm 3 图20线型像质计 38 43 图21手动超声参考试块
GB/I31032一2014 图22确定距离、折射角及声速 44 44 图23转换程序 62 图C.1横向拉伸试样 63 图C.2热影响区的夏比冲击试验取样及V型缺口开口位置 63 图c3croD试样的取样位置 64 图c.tcToD试样加工与管壁厚关系示意图 64 图C.5 焊缝金属试样的开缺口位置 64 图c.
热影响区试样的开缺口位置 66 n时的缺陷极限曲线 图c了方法-cToD>0.2万m 图C.8方法一o.10mm
GB/T31032一2014 钢质管道焊接及验收 范围 本标准规定了原油,成品油、燃气、二氧化碳、氮气等介质的输送管线、管网,阀室和站场的碳钢和低 合金钢管及管件的对接接头,角接接头和承插接头的气焊和电弧焊工艺,也包括集输系统的焊接工艺
适用的焊接方法为焊条电弧焊,埋弧焊,熔化极及非熔化极气体保护电弧焊、药芯焊丝电弧焊,等离 子弧焊、气焊或其组合
焊接方式为手工焊、半自动焊、机动焊、自动焊或其组合
适用的接位置为固 定煤,旋转焊或其组合
本标准还规定了射线检测,磁粉检测、渗透检测和超声检测的工艺以及采用破坏性试验或采用射 线、磁粉、渗透、超声和外观检测的现场焊缝的验收标准
本标准适用于新建管线、在役管线和返修管线的焊接
规范性引用文件 下列文件对于本文件的应用是必不可少的
凡是注日期的引用文件,仅注日期的版本适用于本文 凡是不注日期的引用文件,其最新版本(包括所有的修改单)适用于本文件
件
金属材料夏比摆锤冲击试验方法(GB/T2292007,ISo148-1;2006,MoD) GB/T229 GB/T3091低压流体输送用焊接钢管(GB/T30912008,ISO559:1991,NEQ 金属材料维氏硬度试验 GB/T4340 GB/T5117非合金钢及细晶粒钢焊条(GB/T51172012,IsO2560;2009.MOD) GB:/T5118热强钢焊条(GB/T5118一2012,1IsO3580;2010,MOD) GB/T5293埋弧煤用碳钢煤丝和媒剂(GB/T5293一1999,ANs1/AwsA5.17;1989,EQV GB/T8110气体保护电弧焊用碳钢、低合金钢焊丝(GB/T81102008,AwsA5.18M:2005. MOD) 石油天然气工业管线输送系统用钢管(GB/T9711 GB/T9711 -201l1,IS(O3183;2007,MOD GB/T10045碳钢药芯焊丝(GB/T10045一2001,ANSI/AwSA5.20:1995,MOD) GB/T12459钢制对焊无缝管件(GB/T124592005,AsMEB16.9;2001,MOD) GB/T12470埋弧焊用低合金钢焊丝和焊剂 GB/T13793直缝电焊钢管(GB/T137932008,ASTMA53/A53M;2005JISG3444;:2004. MOD) GB/T14957熔化焊用钢丝 低合金钢药芯焊丝(GB/T17493一2008.AwsA5.29M;,2005.MoD GB/T17493 SY/T0510钢制对焊管件规范 SY/T4109石油天然气钢质管道无损检测(sY/T41092005,AP1Std1104:1999,NEQ) sY/T5037普通流体输送管道用埋弧焊钢管 sY/T5038普通流体输送管道用直缝高频媒钢管 sY/T5257油气输送用钢制感应加热弯管(sY/T5257一2012,Iso15590.1;2001,NEQ) JB/T7902无损检测射线照相检测用线型像质计JB/T7902一2006,IsO19232-1:2004 NEQ
GB/I31032一2014 TsGZ6002:2010《特种设备焊接操作人员考核细则)国家质量监督检验检疫总局 APIRP2201石油石化行业不停输封堵安全操作规程Safehottappingpracticesinthe petroleum&.petroehenmicealindustries AsTME92金属材料维氏硬度测试方法(Standardtestmethodforvickershardnessofmetallie materials) AwsA5.!碳钢药皮电狐媒媒条(coveredcarbon.stelarcweldingeletrodes) AwsA5.2铸铁和钢质氧乙炔气焊焊丝(Ironandsteeloxyfuelgasweldingrods》 AwsA5.5低合金钢药皮电弧焊焊条(Lowalloysteelcoveredarcweldingelectrodes) AWSA5.17埋弧焊用碳钢焊丝及焊剂Carbonsteelelectrodesandfluxesforsubmerged-arc welding2) AwSA5.18气体保护电弧焊碳钢填充材料(Carbonsteelfllermetalsforgasshiededarcweld ing AwsA5.28气体保护电弧焊低合金钢填充材料(L.ow-alloysteelfilermetalsforgasshieldedl welding》 arc AwSA5.29低合金钢药芯电弧焊焊丝(L.ow-alloysteeleleetrodesforluxcoredarcwelding BS7448断裂韧性试验第二部分焊缝金属K临界CToD及临界」积分取值方法(Bs7448 Pt2Fracturemechanicstoughnesstest一Part2,MethodfordeterminationofKccriticalCT(ODand criticalJvaluesofweldsinmetallicmaterials Bs7910金属结构裂纹验收评定方法指南(Guidetomethodsforassesingthe.acceptablityof lawsinnmetallicstructures) NACEMRo175油田设备用抗硫化物应力开裂金属材料(Sulfidestresscrackingresistant metallicmaterialsforoilfield euipmm 1ent 《特种设备无损检测人员考核与监督管理规则》国家质量监督检验检疫总局 术语和定义 下列术语和定义适用于本文件
业主copany 工程的主管单位或建设单位,或由其委派或授权的单位或代表 3.2 承包商 cOntract0r 从事本标准中所述工程任务的承包单位和分包单位
机动焊mechanizedwelding 焊接参数和焊炬导控均由机械或电子控制,也可采用手动操控,以保持规定的焊接工艺 半自动焊 emiautommaticwelding 控制填充材料传送速度的设备进行的电弧媒
焊炬的移动由手动控制 3.5 根燥rootbead 连接管与管管与管件或管件与管件之间焊接的第一层焊道
GB/T31032一2014 3.6 热焊hotpass 根焊完成后立即快速进行的第二层焊道
填充烽ingwelding 根焊或热焊完成后,盖面焊之前的焊道 3.8 welding 盖面焊eap 最外面一层的成型焊道
3.9 返修repair 对经外观检查或无损检测发现的缺陷进行的修补焊接
3.10 旋转焊rolwelding 焊接时焊接热源位置固定,并位于或接近其顶部中心,被焊管或管件旋转
3.11 固定焊p0sitionwelding 焊接过程中管或管件固定不动
3.12 焊缝wed 焊件焊接后所形成的结合部分
3.13 支管焊缝branehweld 采用骑坐式、嵌人式方法或管件(支管座或三通)连接支管或管件到主管的完整坡口焊缝或角焊缝
3.14 缺欠imperfeetionm 按本标准中的检测方法检测出的焊缝的不连续性,不均匀性以及其他不健全等欠缺
3.15 缺陷defeet 达到本标准拒收要求的缺欠
3.16 显示indieation 通过无损检测获得的证据
3.17 内凹internalconeavity 焊道已经良好的熔合并且已经完好渗人沿坡口两侧的管壁厚度,但焊道中部比管壁的内表面低,形 成的内陷即为内凹
3.18 合格焊工qualifielwelder 按照第5章或第6章的要求考核合格的工 3.19 alificationtest 焊工考试welder qun 焊工经过培训或一定工作时间后,按标准规定对其专业理论知识和实际操作技能进行的考试
GB/I31032一2014 3.20 weldin ificatiom 预焊接工艺规程(PwPS)preiminarywe ingprocedurespeci 按照工程设计要求,根据已有的焊接试验结果或其他类似工程经验,由业主委托的焊接试验单位编 制的用于焊接工艺评定的焊接工艺指导性文件
3.21 焊接工艺评定wedingpwedwrequalriceatimn 在工程焊接前,为制定焊接工艺规程,通过对焊接方法,焊接材料,媒接参数等进行选择和调整的 系列工艺性试验,以确定获得标准规定焊接质量的正确工艺
3.22 焊接工艺规程weldingprocedurespeeification 根据焊接工艺评定报告,并结合实践经验而制定的直接指导工程焊接的技术细则文件
包括对焊 接接头、母材、焊接材料、焊接位置、预热、电特性、操作技术等内容进行详细的规定,以保证焊接质量的 再现性
焊接一般规定 4.1 设备 焊接所用设备应能满足媒接工艺要求,且应具有良好的工作状态和安全性
几不符合要求的烬接 设备应予修复或更换
4.2材料 4.2.1管材及管件 本标准适用于焊接符合下列最新版本的标准中的管材和管件 GB/T3091 GB/T9711(APISpec5L,IsO3183) GB/T12459 GB/T13793 sY/T0510 SY/T5037 SY/T5038 SY/T5257 适用的AsTM标准 本标准也适用于未按照上述标准制造,但其化学成分和力学性能满足上述标准规定的材料
4.2.2填充材料 4.2.2.1类型和规格 所有填充材料应符合下列任一标准,使用本标准的各方应探讨使用下列标准的最新版本 GB/T5117 GB/T5118 GB/T5293 GB/T81l0 GB/T10045
GB/T31032一2014 GB/T12470 GB/T14957 GB/T17493 AwsA5.1 AwsA5.2 AwsA5.5 AwsA5.17 AwsA5.18 AWSA5.28 AWSA5.29 不符合上述标准要求的填充材料,如经过娜接工艺评定合格后也可使用
4.2.2.2填充材料及焊剂的保管,搬运 填充材料及焊剂在保管和搬运时,应符合生产厂家的规定,并应避免损坏填充材料,焊剂及其包装
包装开启后,应保护其不致变质,药皮焊条应避免受潮湿
凡有损坏或变质迹象的填充材料和焊剂不应 使用
4.2.3保护气体 4.2.3.1类型 保护气体分为惰性气体、活性气体及惰性气体和活性气体的组合
保护气体的纯度和干燥度,应满 足媒接工艺规程要求
4.2.3.2保管和使用 保护气体应存放在容器中,并应远离高温或低温等极端环境,其他气体不应混人容器中
若保护气 体的质量和容器存在问题,则不应使用
焊接工艺评定 5.1工艺评定 5.1.1在焊接生产开始之前,应制定详细的预焊接工艺规程,并对此焊接工艺进行评定
工艺评定目 的在于验证用此工艺能否得到具有合格力学性能,如强度、塑性、韧性和硬度等的完好焊接接头
其中 环焊缝的附加验收标准见附录C,在役管道的焊接见附录1 5.1.2应使用破坏性试验检验焊接接头质量
应依据评定合格的工艺编制焊接工艺规程
5.2记录 评定的焊接工艺的各项细节和焊接工艺评定试验的各项结果的记录见表E.1和表E.2,并在该焊 接工艺规程使用期间内应保存好记录
5.3 工艺规程 5.3.1概述 工艺规程应包含5.3.2中的适用内容
GB/I31032一2014 5.3.2规程说明 5.3.2.1焊接方法 应指明所使用的焊接方法,或其方法的组合
5.3.2.2管子及管件材料 应指明适用的管子材料和管件材料
适用的管子和管件材料分组见5,4.2.2,评定试验应选择该组材料中具有最高规定屈服强度的材料 进行
5.3.2.3外径和壁厚 应规定焊接工艺规程适用的外径和壁厚范围,其分组见6.4.2中d)和e)
5.3.2.4接头设计 应画出接头的简图
简图应指明接头形式,坡口形式,坡口角度,钝边尺寸和根部间隙等
角焊缝 应指明形状和尺寸
如使用垫板时,还需指明其尺寸和材质
5.3.2.5填充材料和焊道数 应指明填充材料的种类和规格、焊缝最少层数及焊道顺序
5.3.2.6电特性 应指明电流种类和极性,规定所使用的每一种焊条或焊丝的电弧电压和焊接电流值的范围
5.3.2.7火焰特性 应指明使用的火焰类型中性焰、碳化焰或氧化焰),并应规定每种规格的焊丝适用的焊炬喷嘴的 规格
5.3.2.8焊接位置 应指明旋转焊或固定焊
固定焊应指明水平固定焊接位置(5G),垂直焊接位置(2G)或45"倾斜固 定管位置(6G). 5.3.2.9焊接方向 应指明上向焊或下向焊
5.3.2.10焊道之间的时间间隔 应规定完成根焊道后至开始第二焊道及完成第二焊道后至开始其他焊道之间的最长时间间隔
5.3.2.11对口器的类型和撤离 应规定是否使用对口器,使用内对口器或外对口器
如使用对口器,应规定在撤离对口器时完成根 焊道长度的最小百分比
5.3.2.12焊道的清理及打磨 应指明使用电动或手工工具进行焊道的清理和打磨
GB/T31032一2014 5.3.2.13预热和焊后热处理 应规定预热和焊后热处理的加热方法,温度,温度控制方法及需预热和焊后热处理的环境温度的范 围,且应符合7.1l的规定
5.3.2.14保护气体及流量 应规定保护气体的成分及流量范围
5.3.2.15保护焊剂 应规定保护焊剂的类型
5.3.2.16焊接速度 应规定各焊道的煤接速度范围
5.3.2.17层(道)间温度 应规定煤接时煤层(道)之间的温度范围
5.4焊接工艺规程的基本要素 5.4.1概述 当焊接工艺规程有5.4.2中规定的基本要素变更时,应对焊接工艺重新评定
当焊接工艺规程有 5.4.2中规定的基本要素以外的变更时,应修订焊接工艺规程,但不必对焊接工艺重新评定 5.4.2基本要素 5.4.2.1焊接方法 焊接工艺规程中焊接方法的变更,其方法见5.3.2.1
5.4.2.2母材 焊接两组不同材料时,应采用强度较高材料组别的焊接工艺单独评定
本标准所有材料的分组 如下: a)规定最小屈服强度小于或等于290MPa; b 规定最小屈服强度大于290MPa,且小于448MPa; e规定最小屈服强度大于等于448MPa的各级碳钢及低合金钢均应进行单独的评定试验; d 以上分组并不表示上述每组中母材可任意替代已做过焊接工艺评定的母材或填充材料,还应 考虑母材和填充材料在冶金特性、力学性能,预热和焊后热处理要求上的不同
5.4.2.3接头设计 接头设计的重大变更(如V型坡口改为U型坡口,或反之)
坡口角度或钝边的细小变化不属于基 本要素
5.4.2.4焊接位置 由旋转焊变为固定煤,或反之
固定焊应指明水平固定焊接位置(5G),垂直固定焊接位置(2G)或 45"倾斜固定焊接位置(6G)
6G位可替代5G位和2G位,其他不得相互替代
GB/I31032一2014 5.4.2.5壁厚 从 -种壁厚分组到另一种壁厚分组的变更[管壁厚分组见6.4.2e)]
5.4.2.6填充材料 5.4.2.6.1填充材料的变更 从 -组填充材料变为另一组填充材料应符合表1的规定 表1填充材料分类 焊条(焊丝) 组别 标准 焊剂 GB/T5117 E4310,E4311 GB/T5118 E5010,E5011 AwSA5.1 E6010,E6011 AwSA5.5 E7010,E7011 GB/T5118 E5510E551l AWSA5.5 E8010E8011E9010 E5o15,E5016,5018 GB/T5117或GB/T5118 GB/T5118 E5515,E5516,5518 AwSA5.1或AwSA5,5 E7015,E7016,E7018 E8o15,E8016,E8018 AwsA5.5 E9018E10018 GB/T5293 Ho8 H401 GB/T12470 HloMn2 HJ402 EL.8 P6X2 EL8K F6xo EL12 F6X2 AwSA5.17 EM5K F7XZ EM12K F7XO EM1l3K F7X2 EM15K ER50-6 GB/T8110 ER50-G ER70S-2 AwSA5.18 ER70s-6 ER55-6 GB/T811o ER80S-D2ER90S-G AWSA5.28 E70C××E80c×x
GB/T31032一2014 表1(续 焊条(媒丝) 组别 标准 炽剂 AwsA5.2 RG85 RG60, E61T-GS" AWSA5.20 E71T-GS GB/T17493 E501T8-K6 AwSA5.29 E71T8-K6,E71T8-Ni1 AWSA5.29 E81T8-Ni2E81T8-GE91T8-G 其他型号的媒条、填充材料和媒剂也可以使用,但需要进行单独的焊接工艺评定
在4组中可使用其他焊丝和焊剂的组合进行焊接工艺评定,此组合应用完整的Aws型号表示,如F7A0-EL12 或F6A2-EM12K
只有用同一Aws型号的材料允许不重新进行焊接工艺评定
国内材料亦同
当焊接或焊 后热处理时,焊剂型号中的X可以为A或P
在5组中的媒丝应使用保护气体 7组的焊丝仅用于根烨
规定最小屈服强度大于或等于448MPa的管材填充材料型号的变更(见5.4.2.2) 5.4.2.6.2 可在5.4.2.2a)和5.4.2.2b)中规定的分组内变更填充材料,但应从力学性能的角度保持母材和填 充材料的一致性
电特性 5.4.2.7 直流焊接时焊条(焊丝)接正极变更为接负极或反之;直流电变为交流电或反之
5.4.2.8焊道之间的时间间隔 根焊道完成后至第二焊道开始前所允许的最长时间间隔的增加
5.4.2.9焊接方向 从下向媒改为上向媒,或者反之
5.4.2.10保护气体和流量 -种气体换成另一种气体,或一种混合气体换成另一种混合气体,或保护气体流量范围较大地增加 或减少
5.4.2.11保护焊剂 保护焊剂的选用可参照表1
5.4.2.12焊接速度 焊接速度范围的变更
5.4.2.13预热 降低焊接工艺规程的最低预热温度
GB/I31032一2014 5.4.2.14焊后热处理 增加焊后热处理工艺或改变焊接工艺规程中焊后热处理的范围或温度 5.5试验管接头的焊接对接焊 应将两个管段按照预焊接工艺规程规定的要求进行组对和媒接 5.6焊接接头的试验对接焊 5.6.1试样制备 5.6.1.1试件取样应按图1指定的位置进行,试样的最少数量及试验项目见表2
管顶 -刻槽锤断 背弯 见注2 小于60.3mm a 管顶 背弯或侧弯 刻槽锤断 刻糟悸断 背弯或侧弯 b)大于60.3mm,小于或等于114.3mm; 当壁厚大于12.7mm,小于或等于114.3mm 管顶 面弯或侧弯 拉伸 刻槽锤斯 背弯或侧弯 背弯或侧哼 刻槽倾断 面弯或侧弯 拉伸 大于114.31 mm; 小于或等于323.9mm" 图1对接接头焊接工艺评定试验的试样位置 10o
GB/T31032一2014 管顶 背弯或侧弯 面弯或侧弯 刻槽锤斯 拉伸 拉伸 背弯或侧弯 面弯或侧弯 刻槽锤断 背弯或侧哼 面弯或侧弯 刻槽锤斯 刻槽锤断 拉伸 拉伸 背弯或侧弯 面弯或倒哼 d)大于323.9mm 说明 根据业主的意见,位置可以旋转,只要试件在圆周上间距相等即可
但试件不能包含有纵向焊缝 对直径小于或等于33.4mm的管子,可用全尺寸拉伸试件
图1(续 表2焊接工艺评定试验的试样类型及数量 试样数量 管外径 拉伸 刻槽锤断 背弯 面弯 侧弯 总数 mmm 壁厚<12.7mm 60.3 60.3114.3 114.3一323.9 16 >323.9 壁厚>12.7mm l14.3 ll4.3一323.9 323.9 16 对外径小于60.3mm的管子媒接两个试验媒缝,各取一个刻槽锤断试样及一个背弯试样
对外径小于或等于 33.4mm的管子,应做一个全尺寸的拉伸试样
对于规定最低屈服强度大于290MPa的材料至少应进行一次拉伸试验
5.6.1.2试样应按图2,图3,图4或图5的要求制备
试样的试验应在试样空冷至室温后进行
5.6.1.3对于外径小于60.3mm的管子,应焊接两个试验焊口以获得所需的试样数量
5.6.1.4对于外径小于或等于33.4mm的管子,可用一个全尺寸试样的拉伸试验代替两个刻槽锤断试 样和两个背弯试样
1l
GB/I31032一2014 5.6.1.5全尺寸试样的试验应按5.6.2.2的规定进行,且应符合5.6.2.3的要求
试件可以机械或氧气切割, 但两侧必须光滑平行 约230mm 原 在试件的两侧不 去除焊缝加高 图2拉伸试样 用偶锯切槽,试样可以机械或佩 气切割,但两倒必须光滑平行 约3mm 19mm 约3mm 约230mm 壁厚 在媒件的两侧不 去除烨缝加厚度 约3mm mm 横向槽深度不能超过1.6mm 用于自动和半自动 焊的刻槽锤断试样 图3刻槽锤断试样 12
GB/T31032一2014 所在圆角半径最大3.2mm 机械切割或火焰切剂 约25mm 约230mm 郑缝 壁厚 说明:内外表面的焊缝余高应去除至与试样表面平齐
试样在试验前不应压平
图4背弯和面弯试样(壁厚<12.7mm 壁版 约230mm 所在圆角半径最大3.2mm 试件宽度 壁厚 13mm 说明 内外表面的焊缝余高应去除至到试样表面平齐
试样在试验前不应压平 试样应机械切割到13mm宽,或氧乙炔焰切割到约19mm宽,然后再机加工或平滑打磨到13mm宽
切割表 面应光滑和平行
图5侧弯试样(壁厚>12.7mm) 5.6.2拉伸试验 5.6.2.1准备 拉伸试样(如图2所示)约230mm长,25mm 宽,制样可通过机械切割或氧气切割的方法进行
除有缺口或不平行外,试样不必进行其他加工
如有必要,应进行机加工处理使试样边缘光滑和平行
5.6.2.2方法 拉伸试样应在拉伸载荷下拉断,且使用的拉伸机应能测量出拉伸试验时的最大载荷
用拉伸试验 时的最大载荷除以试样在拉伸前测定的最小横截面积计算出抗拉强度
5.6.2.3要求 5.6.2.3.1焊缝的抗拉强度,包括每个试样熔合区的抗拉强度应大于或等于管材的规定最小抗拉强度, 13
GB/I31032一2014 但不需要大于或等于管材的实际抗拉强度 5.6.2.3.2如试样断在母材上,且抗拉强度大于或等于管材规定的最小抗拉强度时,则该试样合格 5.6.2.3.3如试样断在焊缝或熔合区,其抗拉强度大于或等于管材规定的最小抗拉强度,且断面缺陷符 合5.6.3.3的要求,则该试样合格
5.6.2.3.4如试样是在低于管材规定的最小抗拉强度下断裂,则该焊接接头不合格,应重新试验
5.6.3刻槽锤断试验 5.6.3.1试样制备 刻槽锤断试样如图3所示)约230" 长,25mm宽,制样可通过机械切割或氧气切割的方法进 mm 用钢锯在试样两侧焊缝断面的中心(以根焊道为准)锯槽,每个刻槽深度约为3 行
mm
用此方法准 备的某些机动焊及半自动焊(有时也包括焊条电弧焊)的刻槽锤断试样,有可能断在母材上而不断在焊 缝上
当前一次试验表明可能会在母材处断裂时,为保证断口断在焊缝上,则可在焊缝外表面余高上刻 槽,但深度从焊缝表面算起不超过1.6 mm
如业主要求,采用半自动焊或机动焊工艺的焊接工艺评定的刻槽锤断试样可在刻槽前进行宏观金 相试验
5.6.3.2方法 刻槽锤断试样应在拉伸机上拉断;或支承两端,打击中部锤断;或支承一端,锤断另一端
断口暴露 面宽至少应达到19mm 5.6.3.3要求 每个刻槽锤断试样的断裂面应完全焊透和熔合,任何气孔的最大尺寸应不大于1.6mm,且所有气 孔的累计面积应不大于断裂面积的2%,夹渣高度应不超过0.8mm,长度应不大于钢管公称壁厚的 1/2,且小于3mm,相邻夹渣之间至少应有13mm,测量方法如图6所示
最深0.8mm 最小13mm -最长3mm或1/2mm壁厚 说明:此图为断裂的刻槽锤断试样
也适用于断裂拉伸和角焊试样
图6刻槽锤断试样的缺欠尺寸测量 14
GB/T31032一2014 5.6.4背弯和面弯试验 5.6.4.1试样制备 背弯和面弯试验试样(如图4所示)约230mm长,25mm宽,且其长边缘应磨成圆角
制样可通 过机械切割或氧气切割的方法进行
焊缝内外表面余高应去除至与试样母材表面平齐
加工的表面应 光滑,加工痕迹应轻微且垂直于焊缝轴线
5.6.4.2方法 背弯和面弯试样应在导向弯曲试验模具上弯曲,模具如图7所示
试样以焊缝为中心放置于下模 面弯试验以焊缝外表面朝向下模,背弯试验以焊缝内表面朝向下模,施给上模压力,将试样压人下 上
模内,直到试样弯曲成近似U形 mm,胎具厚度C=50mm. 说明:图无比例,压头半径A=45 胎具半径B=601 mm, 图7导向弯曲试验胎具 5.6.4.3要求 弯曲后,在试样拉伸弯曲表面上的焊缝和熔合线区域所发现的焊缝任何方向上或焊缝和熔合区之 同发现的征一裂皱或其他缺欠尺寸应不大于公称壁厚的12.且不大于a0mm
若木发现其他明显缺 欠,由试样边缘上产生的裂纹长度在任何方向上均小于6.0mm,应视为合格
弯曲试验中每个试样均 应满足评定要求
5.6.5侧弯试验 5.6.5.1试样制备 侧弯试样如图5所示)约230mm长,13 宽,且其长边缘应磨成圆角
试样可通过机械切割 mm 15
GB/I31032一2014 或氧气切割的方法制成宽度约19mm的粗样,并用机加工或磨削制成13mm宽的试验试样
试样各 表面应光滑平行
焊缝的内外表面余高应去除至与试件表面平齐
5.6.5.2方法 侧弯试样应在类似于图7所示的导向弯曲试验模具上弯曲
将试样以焊缝为中心放在下模上,焊 缝表面与模具成90°
施给上模压力,将试样压人下模内,直到试样弯曲成近似U形
5.6.5.3要求 每个侧弯试样应符合5.6.4.3的规定 5.6.6夏比冲击试验 5.6.6.1试样制备 当规定做冲击试验时,应对每一种焊接方法(或媒接工艺)的平焊位置和立焊位置的煤继区和熔合 线各取3个冲击试样,对两侧母材不同的焊缝,每侧熔合线均应取3个冲击试样 冲击试样(如图8所示)应采用机械加工,其标准尺寸应为10mm×10mm×55mm;若无法制备标 准试样时,可采用厚度为7.5mm或5.0mm的小尺寸试样
V型缺口位置 1/2 壁厚 1/2r 图8冲击试样 5.6.6.2方法 冲击试验应符合GB/T229的规定
5.6.6.3要求 冲击试验的合格指标应满足设计的技术要求
5.6.7其他试验 5.6.7.1试样制备 当进行金相、硬度、抗腐蚀(HICsCC)和断裂韧性(cTOD)试验时,应满足试样制备相关标准的 要求
5.6.7.2方法 执行试样相关试验标准的规定 16
GB/T31032一2014 5.6.7.3要求 合格指标应满足设计的技术要求
5. 试验管接头的焊接 -角焊 应按图9所示的任一结构进行角焊 -角焊 5.8焊接接头的试验- 5.8.1试样制备 试样取样应按图9指定的位置进行
试样应至少4件,并按图10进行准备
制样可通过机 械切割或氧气切割的方法进行
试样应至少25mm宽,并有足够的长度使之能在焊缝处断裂
对于外径小于60.3mm的管子,为满足所需的试样数量,应焊接两个试验焊口
试样应在空冷至 室温后进行试验
两个试样从直角处截取 另两个从相隔90”截取 X 3 习 六 双 说明:;图中所示的试样位置适用于直径大于或等于60,3mm的接头,对于外径小于60.3mm的接头,试样应从大致 相同的位置切取,但应从两个试验媒口上各切取两个试样
图9刻槽锤断试样的位置:角焊焊接工艺及焊工资格考试 17
GB/I31032一2014 约25mm 可以锯槽 约45 药5mm 火焰 锯割 切割 约30"坡口 约25mmm 灭焰切刚 约50mm 约50mm 图10刻槽锤断试样的位置;角焊焊接工艺评定及焊工资格考试(包括支管连接焊工资格考试) 5.8.2方法 可采用任何一种适当的方法使角焊试样在焊缝处断裂
5.8.3要求 每个角焊试样的断裂表面应完全焊透和熔合,且满足以下要求 最大气孔尺寸不大于1.6mm:; a b)所有气孔的累计面积不大于断裂面积的2% 夹渣高度不大于0.8mm,长度不大于公称管壁厚的1/2,且小于3.0n c mm; d)相邻夹渣之间应至少有13mm的无缺陷焊缝金属,测量方法如图6所示
焊工资格 6.1概述 焊工考试分资格取证考试和上岗取证考试,焊工上岗考试前应具备国家质监部门颁发的资格证书
赏格考试机构必须是国家质量监督检验检疫总局颁布的管道焊接操作人员考试机构 考试机构应 严格按照国家质量监督检验检疫总局公布的考试类别,考试项目和《特种设备焊接操作人员考核细则》 TsGZ6002组织进行焊工考试
6.2 资格考试 从事管道焊接工作的焊工必须持有质监部门颁发的《特种设备作业人员证》,且焊工上岗考试项目 应在其所持的《特种设备作业人员证》合格项目范围内 18
GB/T31032一2014 6.3上岗考试 6.3.1焊工在上岗考试前应持有质量技术监督部门颁发的《特种设备作业人员证》
6.3.2在进行管道安装煤接之前应按照6.4或6.5中的规定对焊工进行上岗考试
6.3.3焊工在上岗考试时,应使用和管道安装焊接时相同的焊接工艺
6.3.4焊工应按6.4.1的要求焊接一个完整的管接头或管接头的扇形段
当焊接管接头扇形段时应将 其支承在具有典型的平煤、立焊和仰焊的位置
6.3.5当焊接工艺规程中有6.14.2和6.5.2中规定的基本要素变更时,应重新对焊工进行上岗考试
需 重新进行焊工上岗考试的基本要素与焊接工艺评定的基本要素不尽相同
6.4单项资格 6.4.1概述 6.4.1.1取单项资格时,每个媒工应使用评定合格的焊接工艺规程,焊接一个完整的管接头或一个管接 头的扇形段作为考试帮口 6.4.1.2当取对接管资格时,应选择旋转焊接位置或固定焊接位置进行
当选择固定焊接位置时,管轴 线应平行于水平线(代号5G),或垂直于水平线(代号2G),或倾斜于水平线约45"(代号6G) 6.4.1.3当取支管连接资格、角接头资格或其他类型接头的单项资格时,应按专用的焊接工艺规程进 行
取得的资格范围应限定在该工艺规程规定的范围内
6.4.1.4当使用的焊接工艺规程有6.4.2中所述的基本要素变更时,应重新对煤工资格进行考试
6.4.1.5若考试焊口经检验和试验满足6.6,且满足6.7或6.8中的要求,则应给焊工颁发相应的单项资 格证
6.4.2资格范围 除了焊接工艺规程有以下基本要素的变更外,按6.4.!规定取得资格的焊工可以进行规定范围内 的焊接工作
当焊接工艺规程有下列基本要素变更时,焊工应重新进行资格考试
a)由一种焊接方法变为另一种焊接方法或其他焊接方法的组合 b)焊接方向由上向焊变为下向焊,或反之; 填充材料组别从l组或2组变为3组,或从3组变为1组或2组(见表1) 从一种管外径分组变为另一种管外径分组,管外径的分组如下 dD 外径小于60.3 mm; -外径大于或等于60.3mm且小于或等于323.9mm; 外径大于323.9mm
从 -种管壁厚分组变为另一种管壁厚分组,管壁厚分组如下: 公称管壁厚小于4.8mm; 公称管壁厚大于或等于4.8mm且小于或等于19.1mm 公称管壁厚大于19.1 lmm
焊接位置的变更(如从旋转焊变为固定焊;或从垂直焊接位置(2G)变为水平焊接位置(5G). 或反之)
若工已取得45"倾斜固定管资格(6G),则可焊接任意焊接位置的对接焊和角焊 接头设计的变更(如由无垫板变为有垫板;或由V型坡口变为U型坡口,或反之)
19
GB/I31032一2014 6.5全项资格 6.5.1概述 6.5.1.1取全项资格时,焊工应使用评定合格的焊接工艺进行下述两项考试 a 固定焊接位置对接焊
管位置可以是水平固定(5G),或是倾斜固定(6G)
管外径应不小于 68.3mm, ,公称管壁厚应不小于6.4 ,焊口内表面无垫板
考试焊口的试样应从图10所 mm, 示的位置上取样或按图10所示的顺序,在相对位置上取样
对于各种外径的管子,相邻试样 试验类型的顺序应与图10中所示的顺序相同
若考试焊口经检验和试验符合6.4和6.5或 6.6的要求,则焊接该焊口的焊工获得固定焊接位置对接焊资格 支管连接 b 考试用管的外径应不小于168.3mm,公称管壁厚应不小于6.4mm
在主管上切 焊接时,应使主管管轴线在水平位置,支管管轴线与主管管轴线垂直,支管在 全尺寸孔 割一 主管下方
焊接完成后,焊缝外观应整齐均匀
6.5.1.2在整个圆周上,焊缝应完全焊透
根焊道不应有任何超过6mm的烧穿
在焊缝任何300 mm 的连续长度中,未经修补的烧穿,其最大尺寸的累积长度应不超过13mm
6.5.1.3按照图10所示位置从管接头上切取4块刻槽锤断试样
试样应按照5.8.1和5.8.2的规定进 行准备和试验,其断裂面上缺陷应符合5.8.3的要求
6.5.1.4若考试焊口满足上述要求,则焊接该焊口的焊工获得支管连接资格
6.5.2资格范围 6.5.2.1如煤工已按6.4.1.2和6,4.1.3中所述的方法通过对接媒和支管连接两项考试,且考试用管的 外径大于或等于323.9mm,则该焊工取得全项资格,可以焊接所有焊接位置、管壁厚、管外径,接头形式 和管件的煤口
6.5.2.2如焊工已按6.4.1.2和6.4.1.3中所述的方法通过对接焊和支管连接两项考试,且考试用管的 外径小于323.9mm,则该煤工取得全项资格,可以焊接所有焊接位置、管壁厚,接头形式和管件的煤口, 但管外径应小于或等于其考试用管的外径
6.5.2.3如焊接工艺规程中有下列基本要素的任一变更,焊工应重新进行资格考试 a)从一种焊接方法变为另一种焊接方法或其他焊接方法的组合; 焊接方向由上向焊变为下向焊,或反之 b 填充材料类别由l组或2组变为3组,或从3组变为1组或2组(见表1).
c 6.6考试焊口外观检查 6.6.1考试媒口的焊缝,除盖面焊道的咬边外,应无裂纹,未焊透,烧穿及其他缺陷
6.6.2焊缝应整齐均匀,盖面焊道的咬边深度应不大于管壁厚的12.5%,且不超过0.8mm
6.6.3在焊缝任何300mm的连续长度中,累计咬边长度应不大于50mm 6.6.4当采用半自动焊或机动焊工艺时,应将填充金属对管内壁的损伤降到最小
6.6.5如考试焊口不符合本节要求,则该焊口不应再做其他的试验和检验
6.7破坏性试验 6.7.1对接焊试样 当考试焊口是完整环焊缝时,应按照图10中所示的取样位置在每个考试焊口上取样;当考试焊口 是管接头的扇形段时,则应从每一扇形段上截取数量相等的试样
试验项目和试样数量要求见表3
试样应空冷至室温后试验
20
GB/T31032一2014 表3试验项目和试样数量 试样数量 管外径 mm 刻槽锤断 拉伸 背弯 面弯 侧弯 总数 60.3 60.3114.3 壁厚 <12.7mm >1l4.3323.9 12 >323.9 <114.3 厚 >114323,9 12.7mm 12 >323.9 外径小于60.3mm的管子应焊接两个试验焊缝,各取一个刻槽锤断试样及一个背弯试样
对外径小于或等于 33,4mm的管子,应做一个全尺寸试样的拉伸试样
该表适用于对接管资格考试和工程焊接要求的破坏性试验 当考试用管外径小于或等于33.4mm时,可用一个全尺寸管试样的拉伸试验代替背弯和刻槽锤断 试验
拉伸试验除应按5.6.2.2的要求进行,并应符合5.6.2.3的要求
管顶 刻糟锤斯 背弯 见注2 小于60.3mm a 管顶 背弯或侧弯 刻槽锤断 刻神锤期 背弯或侧弯 b 大于60.3mm.小于或等于114.3mm 当壁厚大于12.7mm,小于或等于114.3mm 图11对接焊焊工资格考试试验的试样位置 21
GB/I31032一2014 管顶 面弯或倒弯 拉伸 刻糟锤断 背弯或侧鸡 背弯或侧鸡 刻槽锤斯 面弯或侧弯 拉伸 大于114.31 mmm; 小于或等于323.9mm" 管顶 背弯或侧弯 拉伸 刻槽锤期 刻槽倾斯 拉伸 面弯或刻弯 拉伸 刻槽锤断 面弯或侧弯 刻槽锤断 背弯或侧弯 拉伸 d大于323.9mmm 说明: 根据业主的意见,位置可以旋转,只要试样在圆周上间距相等即可
但试样不能包含有纵向焊缝
对于直径小于或等于33.4nmm的管子,可用全截面拉伸试样
图11(续 6.7.2对接焊的拉伸,刻槽锤断和弯曲试验 试样的制备及试验应按5.6的规定进行,对于焊工上岗考试而言,不必计算出试样的抗拉强度
用 于拉抽试验的试样可改做刻槽锤断试验
6.7.3对接焊拉伸试验验收要求 如拉伸试样或全尺寸管试样拉伸断口在焊缝处或熔合线处,且断口缺欠无法满足5.6.3.3的质量要 求,则该焊工不合格
22
GB/T31032一2014 6.7.4对接悍的刻槽锤断试验验收要求 如任一刻槽锤断试样断口的缺欠超出5.6.3.3的规定范围,则该焊工不合格
6.7.5对接焊的弯曲试验验收要求 6.7.5.1如任一弯曲试样拉伸弯曲面的缺欠超出5.6.4.3或5.6.5.3的规定范围,则该焊工不合格
6.7.5.2对级别较高的钢管焊口的弯曲试样允许没有弯曲到完全的U型
如试样断裂,且其断面满足 5.6.3.3的要求,则该试样合格
6.7.5.3如只有一个弯曲试样因缺欠造成不合格,且考试机构和考试监督认定该试样中的缺欠不是该 焊缝的典型缺欠,允许在紧邻该试样的地方再取一个替换试样试验,如替换试样仍不合格,则该煤工不 合格
6.7.6角焊缝试样 应从每个考试焊口上取样
当考试焊口是一道完整的环焊缝时,应按照图9所示位置取样;如考试焊口是管接头的扇形段时 则应从每个扇形段上截取数量相等的试样
试样在试验前应空冷至室温
6.7.7角焊缝试样的试验方法和要求 角焊缝试样应按照5.8的规定进行准备和试验
6.8射线检测仅用于对接焊 6.8.1概述 在对接管资格考试时,若业主许可,可用射线检测代替6.7中规定的试验
6.8.2检测要求 应对每个焊工的全部考试焊口进行射线检测,如任何一段焊缝不满足9.3的要求,则该焊工不 合格
6.9补考 因焊工不能控制的条件或环境所造成的不合格,经考试机构和考试监督同意,可给该媒工一次补考 机会
其他不合格的焊工在未经考试机构和考试监督认可的培训前,不允许补考
6.10记录 应使用附录E所示的表格(该表格可进行修改以适合不同考试的要求,但其记录内容必须充分翔 实,满足本标准对焊工考试的要求),将每名煤工的试验和每次试验的详细结果进行记录
合格焊工的名单和考试使用的焊接工艺规程应存档
如对某个合格焊工的能力有疑问时,可要求 重新进行资格考试
施工现场焊接接头的设计和准备 7.1概述 管道工程的焊接应使用评定合格的焊接工艺规程,焊工应取得相应资格
管口表面在焊接前应均 23
GB/I31032一2014 匀光滑,无起鳞、裂纹、锈皮,夹渣、油脂、油漆及其他影响到焊接质量的有害物质
接头设计及对口间隙 应符合所采用的焊接工艺规程的要求
7.2管口组对 组对同一公称壁厚的管口时,当壁厚小于等于14mm时,错边量不大于1.5mm;当壁厚大于 且小于等于17mm时,错边量不大于2.0mm;当壁厚大于17mm且小于等于2Imn时,错边 14mm ;当壁厚大于mm且小于等于26mm时,饿边量不大于么了mm当壁厚大于等于 量不大于2.2mm; 26mm n时,错边量不大于3.0 mm
如果由于尺寸偏差造成一处较大的集中错边,应沿管口圆周将其均 匀分布
不宜直接用锤击法校正错口 7.3对接焊缝对口器的使用 按照焊接工艺规程的要求,对接焊应使用对口器
当允许在根焊道焊接完成前撤离对口器时,则在 卸下对口器前,完成的根焊道应均匀分布于管口圆周,且每段焊道长度和间距近似相等
如使用内对口 器,焊完的部分焊道难于阻止管子位移或应力过大,则应在卸去内对口器张力前焊完全部根焊道
在外 对口器撒离前,完成的根焊道应均匀分布于管口圆周,媒道累计长度应不少于管周长的50%
7.4坡口 7.4.1工厂加工 所有管端坡口应符合焊接工艺规程中对接头设计的要求
7.4.2现场加工 管端坡口现场加工宜用坡口机或自动氧气切割机进行
如业主同意,也可用手工氧气切割方法进 行
坡口加工后应光滑均匀,尺寸应符合焊接工艺规程要求
7.5气候条件 当恶劣气候条件影响焊接质量时,应停止焊接
恶劣气候条件包括(但不限于)大气潮湿、风沙或大 风
如有条件,可使用防风棚焊接
焊接工艺规程应规定适于焊接的气候条件
7.6作业空间 当管道在沟上媒接时,管口周围焊接作业空间距离应不小于400mm
沟下媒接时,媒接工作坑的 大小应使焊工操作容易
7.7层间清理 坡口和每层焊道上的锈皮及焊渣,在下一步焊接前应清除干净
清理工具可使用无动力工具或动 力工具
若媒接工艺规程规定使用动力工具,则应使用动力工具
当采用机动焊或半自动焊时,在下一焊道焊接前,应用砂轮磨除已完成焊道表面的密集气孔、引狐 处、高凸处及熔渣
7.8固定焊 7.8.1工艺 管道在焊接时应可靠固定,并在管口周围有足够的焊接作业空间 24
钢质管道焊接及验收GB/T31032-2014
钢质管道广泛应用于石油、化工、天然气等领域。在管道的生产、安装和使用过程中,焊接是一个非常关键的环节,对焊接质量的要求也非常高。
GB/T31032-2014是钢质管道焊接及验收的国家标准,该标准规定了钢质管道焊接的要求和方法,以及焊缝的检验、评定和验收标准。
焊接工艺
钢质管道的焊接工艺主要包括电弧焊、气体保护焊、埋弧焊和激光焊等多种方法。不同的焊接方法适用于不同的管道材料和规格,在选择焊接方法时需要根据实际情况进行选择。
此外,在焊接前还需要进行预热、清洗、除毛刺等工作,以确保焊缝的质量。
焊接的检验与评定
钢质管道的焊接质量检测是对焊接工艺和材料控制的一个重要环节,其主要目的是发现和排除潜在的质量问题。GB/T31032-2014标准中规定了以下几种焊缝检验方法:
- 外观检验:通过目视检查焊缝表面的瑕疵、裂纹、气孔等缺陷。
- 尺寸检验:测量焊缝的高度、宽度、厚度等尺寸参数是否符合标准要求。
- 无损检测:包括超声波探伤、射线检测等技术,可用于检测焊缝内部的缺陷,例如裂纹、气孔等。
- 力学性能检验:根据标准要求进行拉伸试验、冲击试验等,以确定焊缝的强度、韧性等力学性能是否符合要求。
根据焊缝的检验结果,可以将其分为合格、不合格和待修复三类。
焊接的验收标准
钢质管道焊接的验收标准是对焊缝质量进行评价,确定其是否符合设计要求和标准要求的过程。GB/T31032-2014中规定了以下几种焊缝验收标准:
- 静态水压试验:通过给管道施加一定压力来测试其是否能够承受设计压力。
- 磁粉或荧光检测:用于检测焊缝内部的裂纹、气孔等缺陷。
- 射线检测:用于检测焊缝是否存在未焊透、夹渣、未熔合等缺陷。
- 超声波检测:用于检测焊缝内部的裂纹、气孔等缺陷。
- 可视检测:通过对焊缝进行目视检查,判断其表面是否存在明显的瑕疵或裂纹。
根据验收结果,可以将焊缝分为合格和不合格两类。如果焊缝在验收过程中未出现明显缺陷且经过水压试验、尺寸检验、力学性能检验等各项检验均符合标准要求,则该焊缝可认为是合格的。
总结
钢质管道的焊接及验收是保证管道质量和安全运行的关键环节。GB/T31032-2014提供了一套完整的钢质管道焊接及验收标准,从焊接工艺、焊缝检验评定到焊缝验收标准都有详细规定,有效地保证了管道的质量和安全性。在进行钢质管道焊接及验收时,需要按照标准操作,并使用适当的工具和设备,以确保焊缝的质量和管道的安全运行。