GB/T40281-2021
钢中非金属夹杂物含量的测定极值分析法
Determinationofcontentofnonmetallicinclusionsinsteel—Extremumanalyticalmethod
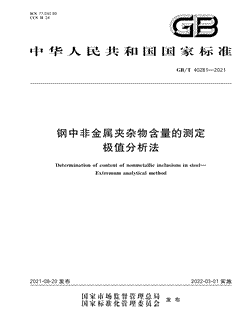
- 中国标准分类号(CCS)H24
- 国际标准分类号(ICS)77.040.99
- 实施日期2022-03-01
- 文件格式PDF
- 文本页数27页
- 文件大小1.82M
以图片形式预览钢中非金属夹杂物含量的测定极值分析法
钢中非金属夹杂物含量的测定极值分析法
国家标准 GB/T40281一2021 钢中非金属夹杂物含量的测定 极值分析法 Determinationofcontentofnonmetallicinclusionsinsteel Extremumanalyticalmethod 2021-08-20发布 2022-03-01实施 家市场监督管理总局 国 发布 国家标准花管委员会国家标准
GB/T40281一2021 目 次 前言 引言 范围 规范性引用文件 术语和定义 符号和缩略语 原理与应用 操作流程 试验报告 13 附录A资料性非金属夹杂物尺寸长度、直径或面积)极值计算公式 附录B(资料性》锯材非金属夹杂物极值分析示例 15 附录C资料性)冶炼过程铸态非金属夹杂物极值分析示例
GB/T40281一2021 前 言 本文件按照GB/T1.1一2020<标准化工作导则第1部分:标准化文件的结构和起草规则》的规定 起草
请注意本文件的某些内容可能涉及专利
本文件的发布机构不承担识别专利的责任
本文件由钢铁工业协会提出 本文件由全国钢标准化技术委员会(SAC/TC183)归口
本文件主要起草单位抚顺特殊钢股份有限公司、齐齐哈尔华工机床股份有限公司、江苏永钢集团 有限公司、首钢集团有限公司冶金工业信息标准研究院、钢铁研究总院、技术经济学会
本文件主要起草人;程丽杰、鞠新华,谷强、李继康、李涛,吴锦圆、颜丞铭、翟继龙、余超、孙继强
GB/T40281一2021 引 言 钢中大型非金属氧化夹杂物的存在会导致金属力学性能的下降,造成性能不合格
非金属夹杂物 的试验方法标准如GB/T10561等采用比较法评定级别,级别与非金属夹杂物长度是呈指数递增,是非 连续数据,很难与零件疲劳寿命相关联,而且检验到的非金属夹杂物偶然性大,数据离散
一些研究表 明,极值分析法应用统计原理,对非金属夹杂物增加了检验次数,对数据进行统计学分析,可最大程度反 映非金属夹杂物的分布状态,降低偶然性
极值分析法分析出的非金属夹杂物极值能更好体现钢材中 存在的非金属夹杂物整体状态,数值连续可比,可建立与零件寿命的关联 极值分析法可供试验人员分析出钢中内生非金属夹杂物或第二相的最大值
一般情况下,可测量 出钢试样中的最大氧化夹杂物
必要时,也可测定多种类型夹杂物的最大值,例如,同一组试样可分别 测出其中的氧化物、碗化物、硅酸盐、点状非金属夹杂物,碳氮化钛等夹杂物的最大值
极值分析法也可 用于测定其他显微组织的特征,比如球墨铸铁中的石墨球大小的极值,工具钢和轴承钢中的碳化物的最 大颗粒度以及晶粒的最大直径
钢中外来夹杂物的分布特性不易预测,应采用其他无破坏性的检测方法,例如超声波探伤来确定
GB/T40281一2021 钢中非金属夹杂物含量的测定 极值分析法 范围 本文件规定了钢中非金属夹杂物极值分析法的试样制备、夹杂物检验、极值计算、极值图绘制、数据 有效性分析,差异性评估和试验报告等 本文件适用于钢材,钢绽和连铸坯中非金属夹杂物的极值分析
其他显微结构的特征值也可参照 使用
本文件不适用于外来非金属夹杂物的极值分析
规范性引用文件 下列文件中的内容通过文中的规范性引用而构成本文件必不可少的条款
其中,注日期的引用文 件,仅该日期对应的版本适用于本文件;不注日期的引用文件,其最新版本(包括所有的修改单)适用于 本文件
GB/T10561钢中非金属夹杂物含量的测定标准评级图显微检验法 GB/T13298金属显微组织检验方法 GB/T30067金相学术语 术语和定义 GB/T30067界定的以及下列术语和定义适用于本文件
3.1 extremevaluedistribution 极值分布 特定的面积或体积上所测量的最大夹杂物特征值r的概率密度函数,符合式(1),则连续随机变数 r有一个二元参数(Gumbel)的最大值分布
-[(气云]xs[-(- f(a 其中,式(1)的后半部分为累积分布函数,见式(2)
F(.r)= =exp(-exp[-(r一A)/]
( 在式(1)和式(2)中,r代表最大费雷特(feret)直径,可为每个检验面积A
中的最大夹杂物的尺寸 长度、直径,或面积),假定 3 由式(3)则可推算出式(4)和式(5). F()=ex-esp(-y门 和 5 工=dy十入 式中: -极值分布函数的定位参数(相当于起步的夹杂物尺寸);
GB/T40281一202 极值分布函数的尺度参数(l/相当于分布曲线的斜率,代表增值速度,越大,增值越快). 3.2 约减变量 reducedvariaate Red.Var 从式(4)中可以看出,y和慨率密度函数有关系,即y=F(P),尸为概率,则从式(4)中可以推出式(6) 6 ln -ln[F(y)]》=一In(一lnP y= 3.3 排序定位sortingpsitionm 所检测的N个夹杂物尺寸数据点X,按升序进行的排列,其中,lGB/T40281一2021 At T= A 示例,当A,=160mm,A叫= =160000mm”时,丁=10o0
通过式(10)可推算出与之相对应的概率值为0.999 99.9%.
3.8 矩量法极值分布参数 distributiomparamter" extremeValue hymomentmethod 8n ,人mom 用式(12)和式(13)来表示 Sdew6 o 12 >mmn 和 13 入m=L一0.57720 mom 其中,下标mom表示依据矩形法评估的参数
3.9 最大似然法极值分布参数extremmevaluedistributionparameterbymaximumlikelihoodmethod Ml,AML 基于参数》和入的最佳值,推测出获得夹杂物尺寸测量组概率的最大值
因为夹杂物极值分布根 据双指数函数计算,则最大值求解最容易的方法是通过分布函数的对数函数,假定有特定的数组,则计 算见式(14)和式(15): LL (14 -习,in[(,A.a对 =习,L,=习,[叫()-' 二 -exp(一! 15 LL的最大值宜通过数值分析计算得出,通过电子数据表或适当的电脑分析程序都可计算得出
参数和入的数值从式(15)分析数据规划求和得出,分别被标为心和入
3.10 dictedinclusiondiensions 预测夹杂物尺寸pret X 测定出o和入的最佳值后,可根据式(16)预测不同概率下夹杂物长度的平均值 工=on.(Red.Var)十入n (l6 3.11 standarddeviationoftheinclusion 夹杂物尺寸的标准差 SE(.x 对于通过最大似然法计算得出的任何一个长度为r的夹杂物,其标准差的计算见式(17): SE(r)=o.V.I09.54y.608y7 7n (17 3.12 夹杂物尺寸的95%置信区间95%confideneeintervalsoftheineclusiom 95%CL 计算见式(18): 18 95%CL=士2SE(r) 3.13 预测的最大夹杂物尺寸(长度、直径或面积predicteddimensions(length,diammeterorarea)ofthe biggestlnclusion Lm 基于极值分布分析方法,预测到概率为P的最大夹杂物尺寸的计算见式(19):
GB/T40281一2021 19 =一wln(一lnP)十入M 当T>100时,式(19)可简化为式(20) Lm=ln(T十入Mn 20 注:在本文件中,如选定参考面积A=160000mm”面积,A
=160mm,则逆转周期T=1000
相对应的概率 p=0.999(99.9%),预测到的最大夹杂物尺寸的计算见式(21): lm,=6.91o十入m 21 3.14 最大夹杂物尺寸L的95%置信区间95%cnfideneeinteryalsofthebiggestineusionm 95%C 使用非常大的逆程周期来预测钢某一特定面积内所存在的最大夹杂物尺寸,给定或由式(10)计算 得出预测概率P,约减函数的计算见式(22),最大夹杂物尺寸的近似95%的置信区间由式(17)和 式(18给出
ln(一lnP 22 y= SE(r)=n.I09.54y千0.6O8y 95%CI=士2sE(.r) 注:在本文件中,选定参考面积A=160000mm面积,A
=160mm=.则逆转周期丁=1000
相对应的概率 p=0.999(99.9%),预测到的最大夹杂物尺寸的标准差和95%的置信区间的计算分别见式(23)和式(24) SE(r=5.80o/n (23 95%CL=士2sE(r)=士11.61on/、" (24 3.15 串状夹杂物stringerinelusions -个单独的夹杂物沿变形方向被大大地拉伸,两个或两个以上的B类和c类夹杂物在一个平面内 皇直线排列,并与热加工方问平行,做此之同的悄离不大于1m,且两个相邻夹杂物之同的间距小于 40 Mma 3.16 费雷特直径feretdiiameter 由一组两个平行的与粒子相切的切线距离确定的,不是一个实际意义上的直径,而是一组直径,如 图1所示
图1费雷特直径示意图
GB/T40281一2021 3.17 离群值 outlier 测定的一个或几个最大非金属夹杂物尺寸,离开其他尺寸较远,暗示有非正常的来源,不能参与极 值分析,需要剔除
注本文件依据格拉布斯(Grubbs)检验法确定离群值,剔除水平为1%
符号和缩略语 表1列出的符号和缩略语适用于本文件
表1符号和缩略语及说明 符号或缩略语 名称与说明 使用金相显微镜测量的每个视场的面积 A 检验面积;一个试样上每个磨光面的总观测面积
A,规定为160mm,另有规定者除外 参考面积:任意选取,以预测最大夹杂物Lm的概率确定
在本文件中建议选择Ad= A 160000mm'面积 N 检验用试样的数量,通常是6个试样 N, 检验用磨光面的次数,即一个试样检验次数,通常是4遍 每个试样抛光面上所观测到的视场数量 N N 用于分析夹杂物尺寸的总检验面数量,通常是24 个 极值分析用的检测的最大夹杂物个数 极值 分布函数的定位参数 极值分布函数的尺度参数 Red.Var 变数y称为约减变量 累计慨率 预期概率 " 所测的N个最大夹杂物尺寸(长度L、直径D或面积S)的算数平均值 Sdle 所测的N个最大火杂物长度的标准差 逆转周期 矩量法求得的极值分布函数的尺度参数 矩量法求得的极值分布函数的定位参数 o 最大似然法求得的极值分布函数的尺度参数 最大 入 大似然法求得的极值分布函数的定位参数 极值分布的自变量,本文件为最大弗雷特直径,为A类、B类或C类的长度,或为D(DS)类的 直径,或夹杂物的面积 预测不同概率下夹杂物尺寸 预测的最大夹杂物长度 lmn8 SE(.r 夹杂物尺寸的标准差 95%CL 95%置信区间 -计算得出的任何一个长度为r的夹杂物近似95%的置信区间 L的95%C1 最大火杂物长度Lm的95%置信区间 注:以光学显微镜检测的线性特征参数值均以微米为单位,特征区域面积以平方微米为单位
GB/T40281一2021 5 原理与应用 5.1极值分布参数值的测定有三种方法;线性回归预测分析法,矩量法(mom)和最大似然法(ML)
其中线性回归预测分析法是最简单的一种方法,矩量法计算简便,而最大似然法测量结果更精确
5.2线性回归预测分析法是在约减变量曲线图上绘制一条直线,作为夹杂物长度函数
但由于该方法 较长的夹杂物比较短的夹杂物权重大,所以精确度不高
最大似然法利用矩量法计算得出的m值和 值作为初始推算数据
入en 5.3本文件推荐使用最大似然法计算值和入值,采用其他方法应注明方法
如无特殊规定,最大 似然法为仲裁方法
5.4预测的夹杂物最大值Lm与采用的预测概率有关由参考面积A决定
如无相关规定,预测概 率取99.9% 6 操作流程 6.1总则 -般推荐使用6个试样进行分析,检测每个试样所需分析类型的每条(个)夹杂物的长度或直径,再 磨制试样,可重复4次以上试验过程,筛选出每个检验面上最大非金属夹杂物尺寸,判断数据有效性分 析出值和入值,计算所预测的夹杂物最大值L,绘图,出具试验报告
极值分析流程如图2所示
试样 检验数据有 差异 夹杂物 极值 极值分布 制备 检验 效性分析 计算 图绘制 评估 图2极值分析流程图 6.2试样制备 取样数量按相关检验规定,如未规定时,取6个试样
截取试样按G;B/T10561执行
试样制备按 GB/T13298执行
每个试样应具备160mm'以上的检测面积
在每次再磨光操作时,应至少去除 0.3mm的材料,以形成一个新的检验面
标注并记录每次磨面的检测面积,计算平均值,作为检验面 积A
6.3夹杂物检测 6.3.1选择检测对象 根据研究目的,确定需要分析的非金属夹杂物类型,对不同类型的夹杂物分别进行极值分析
对于 A类,B类和C类夹杂物,测定非金属夹杂物的长度,对于D类和Ds类夹杂物合并一类一点状夹杂物 分析,测定非金属夹杂物的直径
铸态夹杂物测定夹杂物直径或簇状夹杂物区域直径
注1;夹杂物长度为一条(串)夹杂物的长度,可穿越视场
注2:点状夹杂物直径为等效圆直径d.,即是椭圆的长轴d和短轴d长度的几何平均值[见式25门
椭圆最大 弦长和垂直其弦的最大弦作为椭圆长轴和短轴
25 d,=X 6.3.2选择检测方法 使用金相显微镜或扫描电镜,对非金属夹杂物进行人工检测或自动检测非金属夹杂物的长度或
GB/T40281一2021 直径
6.3.3人工检测 6.3.3.1放大倍数 设定适当的放大倍率
对于含有相对大夹杂物的试样,需要使用10倍至20倍放大倍率的物镜;如 果检验面积上仅含有相对小的夹杂物,需要使用50倍至100倍的物镜
如果检验面积上仅含有少量夹 杂物,则首先应在低倍率下观测试样,并标记出较大夹杂物的位置,然后再在高倍率下测量所观察到的 非金属夹杂物
但是,所有的检测应使用相同的放大倍率
6.3.3.2测量方法 夹杂物尺寸有三种测量方法: 直接测定 使用显微镜的刻尺,在目镜下测定夹杂物尺寸; a b) 软件测定 -使用图像分析软件的测量工具测定夹杂物尺寸 标尺测定 投影或打印图像,利用标尺.等比换算出夹杂物尺寸
c 6.3.4自动检测 6.3.4.1夹杂物分类 使用全自动金相显微镜或带有颗粒分析软件的扫描电镜自动检测非金属夹杂物
对金相显微镜 选择合适的成像方式,例如可使用偏振光或微分相衬DcC,利于二值化提取夹杂物
扫描电镜检测应在 背散射电子信号下进行,设置合适的衬度以保证准确辨识非金属夹杂物
依据非金属夹杂物的形态,成 分或特定规则对非金属夹杂物分类,对不同类别的夹杂物分别进行极值分析
6.3.4.2起始检测尺寸和放大倍数 根据夹杂物尺寸,选择适当的检测放大倍数和夹杂物的起始检测尺寸,如果没有特殊规定,放大倍 数采用500×,夹杂物起始检测尺寸采用1 m
6.3.4.3检测结果的处理 非金属夹杂物自动检测结果为检测面内所有非金属夹杂物的统计数据,包含夹杂物的尺寸、定位坐 标、化学成分,夹杂物类别或成分等信息,提取所需分析类别非金属夹杂物的相关数据,进行极值分析 注:自动检测使用样品一般较大
可将大试样划分数个区域,相当于分为数个试样检测
例如大试样的尺寸为 32mm×30mm,分割成六个区域,每160 计视为1个试样,有两种处理方式 mm a)自动逐个检测所分析的夹杂物尺寸,使用定位功能,拼接为一个大图,划分为2列3行,每个区域相当于1个 试样 设定扫描区域,扫描每个区域,得到六组数据,视为6个试样的检测结果
b 6.3.5测定和记录 测定每个试样每次磨制检验的每条(个)夹杂物的长度或直径,记录每个试样每次检验的非金属夹 杂物长度或直径的最大值
6.3.6确定检验数量 可根据样品情况确定检验试样数量(N,)和磨制的次数(N,),检验面数量(N)至少为8个
示例,对于每个视场,可通过手动或自动方式聚焦图像,并测量每个氧化夹杂物的长度
重复本操作过程,直到分
GB/T40281一202 析完整个抛光面(A>160mm')
累计数据,记录下A
面积上所检测出的最大夹杂物的长度,保存在电脑 中,以备进一步分析用
其余试样也照此程序检验,得出6个试样的非金属夹杂物最大值
再次磨光试样
重复上面的试验试样步骤3次,直至每个试样测定4次,得出一组24个检验面上非金属夹杂物最大长度
6.3.7计算 将非金属夹杂物最大尺寸填人表2.计算并填人平均值和标准差
表2非金属夹杂物最大尺寸检测结果 单位为微米 磨 面 试样 N ------ N 平均值(Mean): 标准差Sdevu: 最大值(Max): 最小值(Min): 6.4极值计算 6.4.1总则 非金属夹杂物极值计算流程如图3所示
输入检验最大 编号 计算极率 计算减约变量 排序定位 1、2 夹杂物尺寸 Redar 计算平均值 计算标准差 计算尺度公数 计算定位参数 计算对数晒数 计算对数函数和 Se Mceanm sUMu om n 计算各极率夹杂物长度 sSUM()最大值规划求和,解得 计算各概率夹杂物置信限 95%CZ ,l,AMI 计算夹杂物最大值 计算最大夹杂物的置信限 95%C 图3极值计算流程 6.4.2排序,定位、编号和计算概率 所测量的24个夹杂物长度按升序排列,然后对每个夹杂物进行编号,最小的夹杂物为1,然后依次 类推,2,3,4,填人设计好的Excel中
每个夹杂物都是依照尺寸大小确定位置,概率以编号为基
GB/T40281一2021 础,使用式(7)计算得出: ,其中1GB/T40281一202 据和信息反映出数据的检测方法以及数据分析结果包括分析用的数据点,通过最大似然法测定出的最 佳直线,以及数据的95%置信区间
以约减变量为纵坐标,夹杂物尺寸为横坐标
夹杂物尺寸由四组 数据组成,测定值Data、计算值X和其最大值最小值
也可以同时标注出夹杂物的最大值
最后一 组数据为丁=1000对应的约减变量y=6.907,夹杂物最大尺寸L及其相应的上下限,见附录 图B.1
图中曲线纵坐标上的各个位置从式(6)计算得出,即为约减变量(Red.MVar),通常纵坐标的尺度 范围从一2到+7,与之相对应的夹杂物长度的概率范围从0.87%一99.9%,逆转周期从1.0088 1000,曲线末端y=6.907对应最终预测的夹杂物最大值L
一max
6.5.2夹杂物极值分布图 协议注明时应绘制夹杂物极值分布图
纵坐标轴标y为约减变量(Red.Var),横坐标为按规定概 率下的夹杂物尺寸L,见图B2
约减变量(Red.Var)为固定值,由概率确定,约减变量与概率值和逆 转周期的对应关系见表3将om 和入L代人式(19)就可以计算得出不同概率对应的L
通常纵坐标 一max
的尺度范围;概率范围从1%一99.999%,逆转周期为1~1000o. 表3概率P,逆转周期T、约减变量》和夹杂物的最大长度L
逆转周期T 概率P/9% 约减变量y 夹杂物最大长度L/m 1.01 -1.529 1.11 10 -0.838 50 0.367 95 20 2.970 50 98.0 3.902 100 99 4.600 1000 6.907 99.9 10000 99.99 9.210 100000 99.999 11.513 99.9999 1000000 13.816 10000000 99.99999 16.118 6.6检验数据有效性分析 将最大值和最小值及其计算的平均值和标准差,代人式(27)和式(28)计算T、和T
查表4,确 定试验数对应的值,如果T、不大于值,则此夹杂物尺寸值不离群值;如果T、大于值,则此夹 杂物长度值是离群值,该数据点不予接受,意味着试验失败
将检出离群值的夹杂物试样应重新磨光 并再次检验最大夹杂物
对新组成的夹杂物数列再次进行分析,直至排除所有的离群值为止
同理,分 析T是否为离群值依此同样处理
离群值的分析应在检测完夹杂物尺寸和计算平均值和标准差 (6.4.3之后进行,及时排除异常数据,避免后续做无效分析
LN一 (27 T Sdev L一IL T=" 28 Sle 注1;本文件按显著性1%作为剔除条件,单个样本拒收参考表4
10
GB/T40281一2021 表4格拉布斯Grubhs)检验法的临界值k值 N 25 37 13 2.607 3.009 3.204 49 3.329 61 3.418 14 26 62 2.650 3.029 38 3.216 50 3.336 3.424 1.56 15 27 3.228 3.345 2,705 3.049 39 51 63 3,430 1.492 16 2.747 28 3.085 40 3.240 52 3.353 64 3.437 1.749 17 2.785 29 3.103 41 3.251 53 3.361 65 3.442 1.944 18 2.821 30 3.l19 42 3.26 54 3.368 66 3.449 19 67 2.097 2.854 31 3.135 43 3.27 55 3.376 3,454 2.221 20 2.884 32 3.150 3.282 3.383 68 56 3.46 44 2.323 221 2.912 33 3.l64 45 3.292 57 3.391 69 3.466 10 2.410 22 2.939 34 3,178 46 3.302 58 3.397 70 3,471 1r 23 2.485 2,963 35 3.178 47 3.310 59 3.405 24 12 2.550 2.987 36 3.191 48 3.319 60 3.411 147 3,727 6.7差异评估 极值分析方法可用于评估钢材的夹杂物水平
例如比较A,B两组钢材中大型非金属夹杂物的尺 寸差异
对于A钢,对SUM(LL)规划求和计算出on和入值,代人式(21)和式(24),计算出A钢的 L值和sE值
B锅同样计算
L.(A)-Lm.(B)的近似95%置信区间可使用式(29)进行计算
如 果95%置信区间的上下限包括0,则可推断出A和B中大夹杂物的特性尺寸不存在差异
如置信区间 范围大于0,则可推断出A的大夹杂物特性尺寸大于B的大夹杂物特性尺寸
如果置信区间范围小于 0,则可推断出A的大夹杂物特性尺寸小于B的大夹杂物特性尺寸
29 CI=CI-CI
=Lm.(A) -L.(B)士2/SEA十SEB 6.8极值分析示例案例 钢材非金属夹杂物极值分析示例见附录B
冶炼过程铸态非金属夹杂物极值分析示例见附录C 试验报告 试验报告可以图,表或文档形式报出报告应包括下列信息 7.1 分析检验人员姓名; a b 分析检验日期 材料类型 c d 试样取样位置以及材料规格; 本文件编号; e 放大率; f 检测的夹杂物最大尺寸L,包括任何不予接受的外围检测尺寸 g h) ! 或D,s; Sdee 11
GB/T40281一202 j on.(小数点后三位),使用非最大似然法,需要注明分析方法; k入wn.(小数点后三位),使用非最大似然法,需要注明分析方法 D L和95%置信限,计算时采用预期概率尸=99.9%,不应报预期概率尸;采用其他预期概率 应同时填报预期概率P、L和95%置信限
7.2有特殊规定时,在报告中填加下列信息 a A; b A.
; c A叫; d N. N; 钢中氧、硅、铝和钙的含量; 提供夹杂物尺寸极值数据分析图; g h)提供夹杂物极值分布图
12
GB/T40281一2021 附录 A (资料性) 非金属夹杂物尺寸(长度,直径或面积)极值计算公式 A.1预测夹杂物的长度x 测定出s和入u的最佳值后,由式(16)可预测不同概率下夹杂物长度的平均值 .r=.(Red.Var)十入 Red.Var为约减变量y,由式(6)可知 (Redl.Var -ln(一ln[F(y]》=一ln(-lnP =y=一 将y代人式(16)得式(A.l): A.1 工=-nln(一lnP )十入n 可以推师山与之相对应这的展书门-一 使用式(10),逆转周期T 则将P代人式(A.1) 可得式(A.2) -aln-n(] A.2 r=一 十AM 预测最大夹杂物长度Lmt 基于极值分析方法,在A面积上预计观测到非金属夹杂物最大值
用最大夹杂物长度L代替 代人式(A.1)可得式(19),即 r L.=-o.ln(-lnP)十入xm As 使用式(10)和式(11),逆转周期T ,可以推算出与之相对应的概率P 下一 A 代人我(可得式A).将厂” 代人式(19),可得式(A.4) ,将P=1一 =-ln [(-会 A.3 十入M L=一l [(j- A.4 -ln(-lnP)=-In[一In(1一1/T]~ln(T,当T>100时,相对误差<0.11%,则式(19)可简化 为式(20),即 L,=oln(T)十入m 将T 代人得式(A.5): 二 Lm= 十入M A.5 -iml( 在本文件中,如果无特殊规定,一般选定参考面积A=160000mm面积,A
=160mm',使用 式(11得出逆转周期T=1000
通过式(10)可推算出与之相对应的概率P=0.999(99.9%)代人式 A.5)预测最大夹杂物尺寸
-ln(一lnP=一ln(一ln0.999)=6.91 L=6.91o十An 13
GB/T40281一2021 A.3最大夹杂物长度Lm的95%置信区间 使用非常大的逆程周期来预测钢某一特定面积内所存在的最大夹杂物长度,预测到最大夹杂物尺 寸的标准差可根据式(22)和式(17)计算: -ln(一lnP y=一 sE(c)=n.,/T.I下5T可wwy元" 在本文件中,如果无特殊规定,一般选定参考面积A=160000mm'面积,A
=160mm',使用 式(I1),逆转周期丁=1000
通过式(I0)可推算出与之相对应的概率尸=0.999(99.9%),预测到最大 夹杂物尺寸的标准差为: y=-ln(-lnP)=-ln(-ln0.999)=6.91 SE(r)=owV.I090.514y0.608y =o.090.54又6.90.608又6.9万 二5.80o/厅 预测到最大夹杂物尺寸的95%置信区间可根据式(18)计算
95%C1=士2sE(r)=士11.61o/、n 14
GB/T40281一2021 附录 B 资料性) 钢材非金属夹杂物极值分析示例 B.1试样制备 一组6个试样磨制4次,测量每个磨面B类最大夹杂物长度,试样编号为16,磨光面编号为I~ N,填人表B,.1,标注并记录每次磨面的检测面积,计算平均值,作为检验面积A
B.2夹杂物检测 检测的最大夹杂物长度数据使用式(8)和式(9)计算出检测的最大夹杂物的平均长度值Mean和标 准差Sdeo,可使用ExCEL的AVERAGE和sTDEV自动计算,确定最大值和最小值,填人表B.1
表B.1非金属夹杂物最大夹杂物长度检测结果 单位为微米 试样 140 200 00 280 90 250 240 80 800 220 320 490 205 300 190 120 150 70 250 500 110 390 150 200 平均值(Mean);247.708 标准差Sew;l63.,654 最大值(Max);800 最小值(Min):70 B.3数据有效性分析 4m,平均长度 B.3.1最大夹杂物:从表B.1的数据组可得出,最大值为800Mm,最小夹杂物长度为701 值L=247.71Mm,标准差Sdev=l63.65m,代人式(27)可计算出: L、一L 800一247.708 =3.375 I63.654 SleU 根据表3.24个数据的临界值众 B.3.2 =2.987,则T
应为2.987或以下
对于最大夹杂物长度800 m 而言,T;=3.375>2.987,意味着试验失败,从表B.1可知需剔除试样3的最大夹杂物长度800"m. B.3.3将试样3重新磨光,再次检验最大夹杂物
最大夹杂物长度为530m,填人表B.1,分析最大值 5324m,最小值70m,代人式(27)和式(28)可计算出T和T均小于2.987,则最大和最小的夹杂物 长度值不是离群值,试验数据均有效 LN 532-236.542 T2 -2.272 130.017 Sleu 15
GB/T40281一202 L-L236.542-70 T= =1.281 130.017 Sde 累计概率和约减变量计算 B.4 将24个检测值输人Exeel电子数据表格的A栏,对数据按升序排列,最小数据在首位,排序定 B.4.1 位的数据见表B.2 B.4.2对所有夹杂物进行编号,最小的夹杂物编号为1,依次累计,2,3,4,,N,见表B.2中B栏
B.4.3通过式(7)计算出每个位置夹杂物的概率,填人表B.2中c栏
例如,假定一个夹杂物长度为 180m ,该夹杂物编号为9,则该夹杂物的概率可通过式7)计算得来 =0.36 月-、- B.4.4将该位置的概率代人式(6)中,可计算出每个位置的约减变量,见表B.2中D栏
例如,编号为9 的夹杂物,其长度为180m,概率值为0.36,则通过式(6)可计算出该位置夹杂物的约减变量
-ln(一ln0.36)=一0.021 y=-In(-InP,)=- B.4.5通过A栏的夹杂物长度数据可使用式(8)和式(9)计算出夹杂物的平均长度值Mean=236.542m和 标准差Sde=130.017m,也可以使用Excel计算公式AVERAGE和STDEVP直接计算
这些数据填在表 B2中B栏上方
B.5极值分布参数》和入计算分析 B.5.1将夹杂物平均长度值和标准差可分别代人式(12)和式(13)中计算出心m和入mm,计算结果分别 为心=101.3744m和入=178.0294m,这些数据填在表B.2中E栏上方
Sdlev6 130,017×6 =101.374 moea 3.1416 Amm=L一0.57720mm=236.542-0.5772×130.017=178.029 B.5.2为了采用最大似然法测定和入值,首先应通过式(1)解析出极值概率密度函数的自然对数函 数InLr(e,a.,a)],见式(15),计算出该函数的每个数据点,求和
使用》和入值规划求解出这些数值 和的最大值,就是最大似然分析法,该方法按下列步骤进行测定 (-一] exp(- 吉 f(r)一 exp 习ln[r(e,.,)] LL= 一] exp(一 [)-(巴 以矩形法分布参数心m值和入m值为推测dn和入值的初始数值,然后将这两组数据复制 a 到表B.2中H栏上方
b 使用H栏中的值和入值进行初步计算,计算出每个火杂物长度的ln((e" ;,入,数 值,填人表B.2中E栏
对每个数值ln(f(r,,A,)求和SUM(LL)
在表B.2中,sUM(LL.)值位于F栏下方
c F栏中各项总和的最大值可通过数值分析法得出,例如,在ExCEL数据表中使用sOLVER d 函数(规划求和)可进行此步操作,设置目标单元格为sUM(LL.)的值,可变单元格为和 入m的值,求解得心和入值
注,也可使用其他类型的电子数据表或分析软件程序进行相关计算
16
GB/T40281一2021 B.6极值长度计算 B.6.1通过最大似然法分析得出的o值和入值,可用在式(16)中表示最优(平均)线
在式(16)中 代人o值和入值,以及Red.Vvar值,可计算出最优(平均)线上的各个数据点,填人表B.2的G栏
r,=(Red.Var)+AxM =My十入 B.6.2与上述方法相似,通过式(17)和式(18)可测定每个数据点的95%置信区间点,分别填人表B,2 中的H栏和I栏
sE(r;)=dn..I9干O.5T45yO.8yT" 95%CL=士2sE(.r 直以一工,十2sE(r))-a.y十A姐+2dn,I.I05T5.Oy元" 2SE(r,)=oy十入w一2/.09干0.514y千0.08y Zig B.6.3假定逆转周期为1000,将o值和A
值代人式(21),则可计算出Lm、值,具体计算步骤如下 所示: Lm=6.91o十A1 一6.91×92.540十179.773=819.2 B.6.4L的95%置信区间;在L.的标准误差的计算中,概率P取99.9%,将ow和川值代人式 24),则具体计算如下所示: 11.61u11.61×92.540 95%cL一=士2sE(r)一 =士219.3 v24 m 表B.2夹杂物长度、概率和所计算出的统计参数 单位为微米 B D H Mean 236.542 ma o1.374 Mn. 92.,540 130.017 178.029 179.773 Sdev 入wm" 入. Red.Va1 Iength Y Rank Prob X) ln ro rhg Data RV f.r;,.0.A 70 0.04 一1.169 -6.616 71.59 27.9 115.3 90 0.08 -0.927 -6.196 94.03 53,4 134,6 71.2 -0.752 -6,034 100 0.12 110,23 149,2 11o -0.606 -5.899 123.72 85.6 161.9 0.16 120 0.2 -0,476 -5,789 135.73 97.9 173.6 140 0.24 -0.356 -5.635 146.86 109.0 184.7" 150 0.28 -0.241 -5.585 157.44 119.3 195.6 -0.131 -5.585 128.9 150 0.32 167.69 206.4 17
GB/T40281一2021 表B.2夹杂物长度、概率和所计算出的统计参数(续 单位为微米 E H 18o 0.36 一0.,021 一5.528 177.79 138.2 217.4 190 10 0.087 -5.534 187.86 147.2 228.5 0.4 200 0,44 0.197 -5.550 198.03 156.l 240.0 12 200 0.48 0.309 -5.550 208,40 164.9 251.9 205 13 0.52 0,425 -5.562 219,08 173.8 264.4 14 -5.610 220 0,56 0,545 230.21 182.9 277.5 0,6 -5,700 240 15 0,672 241,94 192.3 291.6 25o 16 0.807 -5.755 254.43 202.1 0.64 306.8 17 250 0,68 0.953 5.755 267.95 212.5 323.3 28o0 18 0,72 1.113 -5.949 282.79 223.8 341.7 19 -6.100 362.5 300 0,76 1.293 299,43 236.3 320 20 0.8 1.500 -6.263 318.58 250.5 386.7 390 21 0.84 1.747 -6.903 34l.4 267.2 415.7 490 22 0.88 2.,057 7.915 370,13 287.9 452. 500 0.92 2.484 -8.019 409.67 316.1 503.3 23 24 0,.96 3.199 -8.356 475,77 362.6 588.9 532 SUM(LL, -147.386 B.7绘制夹杂物长度极值数据分析图 从表B.2拷贝相关数据填人表B,3相关栏目,填人L,相关数据,使用origin软件绘制图B.1
也 可使用Excel表和Minitab绘图
表B.3夹杂物数据 单位为微米 Data Red.Var" .r rhiel -1.169 115.3 70 71.59 27.9 90 -0.927 94.03 53.4 34.6 100 -0.752 110,23 71.2 149.2 110 -0.606 123.72 85,6 161,9 120 -0.476 135.73 97.9 173.6 140 -0.356 146.86 109.0 184.7 150 -0.241 157.44 119.3 95,6 150 -0.131 167.69 128.9 206.4 18
GB/T40281一2021 表B.3夹杂物数据(续 单位为微米 Red.am Data 工lo Z'igh 18o -0.021 177.79 138.2 217. 190 0.087 187.86 147.2 228.5 200 0.197 198.03 156.1 240.0 200 0.309 208.40 164.9 251.9 205 0.425 219,08 173.8 264.4 220 0.545 230,21 182.9 277.5 240 0.672 241.94 192.3 291.6 250 0.807 254.43 202.l 306.8 250 0.953 267.95 212.5 323.3 280 1.113 282,79 223,.8 341.7 362.5 300 1.293 299,43 236.3 320 1.500 318.58 250.5 386.7 390 1.747 34l.41 267.2 415.7 490 287.9 2.057 370,13 452.4 500 409.67 316. 503.3 2.484 532 475.77 362.6 588.9 3.199 计算的L 6.907 819.2 599.9 1038.5 mnax Dwu x =92.540Keur179.773 -=150mm? 892-2193 10020030040050060070080090010001100 x/Hm 图B.1夹杂物长度极值数据分析图 B.8绘制钢-极值分布图 对照表2,按式(20)计算出不同概率对应的非金属夹杂物的最大长度Lm,填人表B.4
以 y(Red.Var为纵坐标,夹杂物最大长度L,为横坐标,做出夹杂物长度极值分布图,见图B.2
纵坐标 19
GB/T40281一202 左侧也可标注概率(%),右侧也可标注逆转周期
表B.4概率,逆转周期、约减变量和夹杂物的最大长度 P/% Lma./m 1.01 -1.529 38.25 10 -0.838 102.23 1.11 50 0.367 213.69 95 20 2.970 454.63 50 98.o 3.902 540.86 100 99 4.600 605.47 6.907 818.97 l000 99.9 0000 99.99 9,210 1032.09 100000 99.999 11.513 1245.18 1000000 99,.9999 13,816 1458,26 10000000 99.99999 16.118 1671.34 18" 6 4 12- 0 8 6 0 20040060080010001200140016001800 xum 图B.2夹杂物长度极值分布图 20
GB/T40281一2021 附录 C 资料性 冶炼过程铸态非金属夹杂物极值分析示例 C.1冶炼过程中由于取样的即时性,不能进行大量的检验,对单个试样的检验,偶然性大,分析数据离 散,不能很好反映工艺状态
使用极值分析方法,对冶炼过程铸态非金属夹杂物进行分析,可了解冶炼 过程非金属夹杂物的变化情况,可建立一种冶炼过程非金属夹杂物的分析方法,成为分析研究钢纯洁度 的有效手段
在冶炼的各关键环节取熔融状态的钢液,急冷,非金属夹杂物被固定的小钢样中,分析铸 态的非金属夹杂物
C.2在电炉样LF VD -浇注每个过程(见表C.1)取一个试样,检验每个铸态夹杂物的直径 重新磨样,再检验,对每个试样共检验8次,使用本文件进行计算
表C.1 冶炼过程说明 明 冶炼过程 说 电炉工位,铁料基体全部熔,加返回钢T>1600C后所取的试样;DL--2表示DL试样剔除一个离 DL 群数据后再检 LF LF工位,白渣,成分粗调后所取的试样 LF工位,成分微调后5min后所取的试样 LF2 VD1 VD工位,人罐,加铝前所取的试样;VD1-2表示VD1试样剔除一个离群数据后再检 VD2 VD工位,加铝后所取的试样;VD2-2表示VD2试样剔除一个离群数据后再检 VD3 VD工位,软吹,吊出前所取的试样 浇注过程中所取的试样 JZ c.3选择一炉20CrMo钢在上述环节取样分析铸态非金属夹杂物,取样见表c.1,分析结果见表c.2 极值数据分析见图C.1,各环节最大夹杂物见图C.2
从分析结果可见LF进人VD夹杂物最小随后长 大,浇注环节夹杂物最大,似乎是在VD后夹杂物逐步长大,存在问题
但是在对各个环节进行差异性 分析见表C.3)后发现只有电炉环节有实质差异,其他环节无差异
表c.2铸态夹杂物的极值计算 单位为微米 试样编号 L8 L1 2SE(.r T8 T 范围 Lmim 127.7 DL-2 85 25 53.8 1.941 l.015 27.7士53,8 74.,0 181.5 LF 30 1o 64.6 1.125 0.998 35.2 29.4 64.6士29.4 94.l 67.8 35.3 1.641 1.272 67.8士35.3 103,l LF2 30 32.5 0 VD1 25 1o 39.3 16,4 1.701 0.706 39.3士16,4 22.9 55.6 VD2 40 10 59.8 27.9 1.923 0.64] 59,8土27.9 31.9 87,7 VD3 45 10 76.3 35.1 1.875 1.042 76.3士35.1 41.3 1l1.4 JZ 85 10 129,4 67.3 1.847 0.588 129.4士67.3 62.1 1967 21
GB/T40281一2021 2.5- 2.5- 2.0- 2,0- Due 1.5 1.5 xim 1.0 1" 二品n 0.5 第" 父 D1.R37. D7.17RrI5. 0.0 0.0. =195mm2 A=256mm -0.5 -0,5 -l.0 80 10 15 20 25 30 35 40 45 20 30 40 50 70 90 60 YAxisTitle YAxisTitle 2.乐 2.5- LF2 VD1-2 2.0 2.0- 1.5 a -a xa 1.5 1.0 ,hio 1.0- 0.5 0.5- 0.0 D=8.60Redar+8.36 0.0 .9TII.73 A4=297mm32 -248mm" -0.5 -0.5 40福 5 101520 Da6百而如猫 YAxisTite YAxisTile 2.5 2.5 VD2-2 VD3 2.0- 2.0- Dua 1.5 1.5- rim tt 1.0. 1.0 .eh 0.5- 0.5- D6.8ORu+12.8 L240mn 0.0. 0.0 D8.54Ru7.可 x A256mm -0.5 -0.5 l.0. -l.0 0 30 35 40 10 15 20 25 5 2025 30 3540 550 YAxisTitle YAxisTitle 2.5 zH 2.0 .5 Dia xin .0 xm0 0.5 0.0 D16R16.T =289mm -0.5- 1.0. -10 102030405060708090 YAxisTile 图c.1各过程铸态夹杂物直径极值数据分析图 22
GB/T40281一2021 135.0 115.0 95.0 75.0 55.0 35.0 Jz VD1-2VD2-2 VD3 LF1 LF2 图c.2铸态夹杂物直径的最大值 表c.3冶炼各过程差异性评估 试样编号 cI SE(.r C`I L D12 127.7 26.9 LF1 64.6 14.7 124.4 1.8 LF2 67.8 17.65 42.7" 49.1 VD1-2 39.3 8.2 67,4 10,4 VD2-2 59.8 13.95 11.9 52.9 VD3 76.3 17.55 28.3 -61.3 JZ 129.4 33.65 22.8 -129.0 上一行与下一行的比对
钢中非金属夹杂物含量的测定极值分析法GB/T40281-2021
钢材是现代工业中最重要的结构材料之一,而其中的非金属夹杂物对于钢材的性能和质量有着重要的影响。因此,精确测定钢中非金属夹杂物的含量显得尤为重要。
目前,钢中非金属夹杂物含量的测定方法主要有显微镜法、X射线能谱法、电感耦合等离子体发射光谱法等。这些方法虽然都具有优点,但也存在着各自的局限性。
相对于传统的方法,极值分析法具有操作简单、精度高、准确度高等优点。因此,本文将介绍极值分析法GB/T40281-2021在钢中非金属夹杂物含量测定中的应用。
首先,我们需要准备一台能够进行化学成分分析的设备。接着,取钢样,进行化学成分分析,在此基础上计算出各个元素的质量分数。
然后,我们需要将钢样破碎,并进行粒度筛分,得到不同粒度级别的样品。再对不同粒度级别的样品进行氧化处理,并通过溶解等操作将其中的非金属夹杂物提取出来。
最后,根据不同粒度级别样品中非金属夹杂物的含量,采用极值分析法进行统计计算,从而得到整体钢样中非金属夹杂物的含量。
需要注意的是,在进行实验前,我们需要按照标准要求对设备进行校准,而且在操作过程中,还需注意样品的处理方式和操作过程等细节问题,以确保实验结果的准确性。
总之,极值分析法是一种可靠、高效、精准的钢中非金属夹杂物含量测定方法,其在钢材行业中具有重要意义。