GB/T23576-2009
抛喷丸设备通用技术条件
Abrasiveblastingequipment-Generaltechnicalrequirements
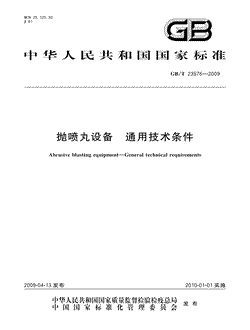
- 中国标准分类号(CCS)J61
- 国际标准分类号(ICS)25.120.30
- 实施日期2010-01-01
- 文件格式PDF
- 文本页数11页
- 文件大小653.71KB
以图片形式预览抛喷丸设备通用技术条件
抛喷丸设备通用技术条件
国家标准 GB/T23576一2009 抛喷丸设备通用技术条件 AbrsiebMlasttingequipmemt一Generaltechnicealrequirements 2009-04-13发布 2010-01-01实施 国家质量监督检验检疫总局 发布 国家标准化管蹬委员会国家标准
GB/T23576一2009 前 言 本标准的附录A是规范性附录
本标准由机械工业联合会提出 本标准由全国铸造机械标准化技术委员会(SAC/TC186)归口
本标准起草单位:济南铸锻所捷迈机械有限公司、济南铸造锻压机械研究所、青岛铸造机械集团公 司、青岛双星铸造机械有限公司,青岛开世密封工业有限公司山东开泰金属磨料股份有限公司
本标准主要起草人:王德志、邢海伟,吴正涛、丁仁相,吴寿喜、刘如伟
GB/T23576一2009 抛喷丸设备通用技术条件 范围 本标准规定了抛喷丸设备的技术要求,试验方法、检验规则等
本标准适用于对工件进行抛、喷丸加工处理的各类抛喷丸设备(以下简称为设备)
规范性引用文件 下列文件中的条款通过本标准的引用而成为本标准的条款
凡是注日期的引用文件,其随后所有 的修改单(不包括勘误的内容)或修订版均不适用于本标准,然而,鼓励根据本标准达成协议的各方研究 是否可使用这些文件的最新版本
凡是不注日期的引用文件,其最新版本适用于本标准
(GB150钢制压力容器 GB/T1184一1996形状和位置公差未注公差的规定 (GB/T1239.4一1989热卷圆柱螺旋弹簧技术条件 GB/T18042000 -般公差未注公差的线性和角度尺寸的公差 GB/T3766液压系统通用技术条件(GB/T3766一2001,eqvIsO4413:1998) GB5226.1机械安全机械电气设备第1部分;通用技术条件(GB5226.1一2002,IEC60204 l:2000,IDT GB/T7932 气动系统通用技术条件(GB/T7932一2003,IsO44l4:l998,IT GB/T79842001 输送带具有橡胶或塑料覆盖层的普通用途织物芯输送带(GB/T7984 2001,ISO/FDIS14890-1999,MOD) GB/T10095.2一2008圆柱齿轮精度制第2部分;径向综合偏差与径向跳动的定义和允许值 ISO1328-2:1997,lIDT GB/T13306标牌 GB/T17421.11998机床检验通则第1部分;在无负荷或精加工条件下机床的儿何精度 eqvISO230-l:1996 GB20905铸造机械安全要求 JB/T1644一2005铸造机械通用技术条件 JB/T3713.2双圆盘抛丸器技术条件 JB/T5365.1铸造机械清洁度测定方法重量法 JB/T5365.2铸造机械清洁度测定方法显微镜法 JB/T5548.2电动激振器第2部分;技术条件 JB/T6331.2铸造机械噪声测量方法声压级测定 JB/T6578单圆盘抛丸器技术条件 JB/T9873金属切削机床焊接件通用技术条件 JB/T9875金属切削机床随机技术文件的编制 压力容器安全技术监察规程 技术要求 -般要求 3.1.1设备应符合本标准的规定,并按经规定程序批准的图样及技术文件制造
GB/T23576一2009 1. 设备的电气系统应符合GB5226.1规定
3. 3. .1.3各电动机的负载功率不应超过其额定功率值
3.1.4工件装卸系统、弹丸循环系统、除尘系统等与抛喷丸系统应具有电气联锁装置
3.1.5设备的液压系统应符合GB/T3766的规定 3. .1.6设备的气动系统应符合GB/T7932的规定
设备的涂漆应符合技术文件的规定
3.1.8设备的各运动部位应采取安全防护措施或设胞
安全防护应符合GB20905的规定 轴承及润滑部位应润滑防尘良好
设备使用说明书中对各部位的润滑应有具体规定
3.1.10各易损件的硬度和耐磨性能应达到技术文件的规定要求,并便于更换和互换 3.1.11设备中的各减速器的清洁度限值不应超过油标下限润滑油重量的0.03%
3.1.12设备中的油缸、气缸内部清洁度应符合表l的规定 表1油缸、气缸内部清洁度数值 缸体长度/mmm" 缸体直径 >100 >200 >300 >400 >600 >800 >1000 >1500 >2000 l00 200 300 400 一60o0 800 1000 1500 2000 2500 mm 污物重量/mg 50100 200 500 800 3000 300 1000 1500 2000 2500 3500 2000 250o 100一200 500 800 1000 1500 3000 3500 4000 >200~300 500 2000 2500 3000 3500 4000 4500 l000 >300一400 2000 2500 4000 4500 3000 3500 5000 >400~500 3000 3500 4000 4500 5000 6500 >500~600 4000 4500 5000 6500 8000 >600800 5000 6500 8000 9000 8001000 8000 9000 10000 3.1.13机械加工零件的未注公差尺寸极限偏差不应低于GB/T1804一2000规定的m级公差要求
3.1.14焊接件应符合JB/T9873的规定
传动齿轮不应低于GB/T10095.2-一2008中规定的8级的精度要求
3.1.15 3.1.16设备在结构上应能保证维修方便
3. 1.17设备上各种标牌应符合GB/T1330G的规定
1.18随机附件、备件应齐全
3 3. .1.19随机技术文件应包括产品说明书、产品合格证和装箱单
随机技术文件的编制应符合 JB/T9875的规定
3.2抛丸器技术要求 ..2.1抛丸器应符合JB/T3713.2和JB/T6578的规定
3 33 .2.2抛丸器的结构参数与布置方式应能满足对工件进行抛丸加工的需要,并应达到技术文件的 规定
33 2. .3 抛丸器的抛射带、抛射速度应能满足抛丸加工工艺的要求
3.2.4每台抛丸器中的叶片,分丸轮、定向套及护板各自的硬度最大值或最小值与平均值之差应在 土3HRC范围内
3.3喷丸器技术要求 3.3.1喷嘴应耐磨,并便于更换和互换
GB/T23576一2009 3.3.2各阀、转换开关、传感器及压力表应灵敏可靠
各紧固连接件不应松动
3.3.3在使用工作压力下,各阀及管路接头处不应漏气
3.3.4喷枪及其控制装置应便于操作
喷枪的球形钞链应转动灵活
喷枪升降装置应工作平稳,升降 距离能够满足工件喷丸加工要求,并能准确的停留在升降距离内的任意位置
.3.5喷丸罐应按GB150以及《压力容器安全技术监察规程》的规定进行设计、制造、验收和使用
3 3.3.6喷丸器的喷丸量应达到技术文件的规定
3 弹丸循环系统技术要求 3 螺旋输送机 3.4.1.1螺旋输送机的结构型式应能保证输送的连续性和平稳性
3 螺旋输送机减速器输出轴与螺旋体主轴间的同轴度不应低于GB/T1184一1996中规定的 10级精度要求
3 在正常使用条件下,不应出现物料堵塞现象
3 提升机 传动滚筒不应有影响使用性能的裂纹、凹坑、焊接不良及其他缺陷
传动滚筒外径对轴线的全跳动应符合GB/T1l84一1996中规定的9级精度的要求
运输带应符合GB/T7984的规定 运输带接头处径向承受能力不应低于运输带径向扯断强度
拉紧装置调整应灵活,在牵引件安装和调整好后,未被利用的行程不应小于全行程的50%
提升机应有防逆转安全装置
提升机在正常使用条件下,最大输送量应达到技术文件的规定
2.7 2.8卸料情况良好,无显著回料现象
直线振动筛、滚筒筛 4.3. 经过排渣口排除的筛上物中含有合格弹丸的弹丸量,按重量计算不应超过循环总量的1%
4.3.2在正常使用条件下,直线振动筛槽体不应出现变形、裂纹或断裂现象
3.4.3.3弹簧的材料和热处理应符合GB/T1239.4的有关规定,弹簧的表面应进行强化处理
33 .4.3.4弹簧两端圈应并紧,磨平,弹簧与上、下支承座接触平面的贴合应紧密
33 .4.3. 5 弹簧尺寸,负荷的允许偏差与形状公差不应低于GB/T1239.4一1989中规定的2级精度的 要求
3. 4. .3. 电动激振器应符合JB/T5548.2的规定
6 3 4 .3.7在过共振区工作的直线振动筛应有可靠的制动或限幅措施,并保证停机过程快速平稳
4.3. 直线振动筛在正常工作过程中侧向偏摆量不应大于2mtm.
3 .8 33 .4.3. 9 直线振动筛在正常运转后,筛筐两侧板对称点振动方向的振幅差值不应大于在此两点所测双 振幅的平均值的20%
3 .4.3.10直线振动筛的生产率应符合技术文件的规定
33 .4.3.11滚简筛筛体锥度,圆度偏差应符合技术文件的规定
.4.3.12筛网应牢固地定在筛筒上,筛网钢丝伸出压板的长度不应小于筛孔尺寸1/3
3 33 .4.3.13滚简筛上的滚简应装配牢固,滚动轴心与圆筒轴心的同轴度不应低于GB/T1184一1996中 规定的9级精度的要求
33 .4.3.14滚筒筛的转动速度应符合技术文件的规定 3.4.4分离器 经分离器分离后的弹丸中含杂质量不应大于1%,废料中含弹丸量不应大于1%
3.4.5供丸系统 3.4.5.1供丸系统不应有漏丸现象,供丸闸门动作应灵活可靠
GB/T23576一2009 3.4.5.2供丸系统的供丸量应能满足抛丸器或喷丸器的需要
3.5工件承载体技术要求 3.5.1承载体应能满足工件在抛喷丸加工区的运行特征、特性(如进给速度、工件的运行方式等)要求
3.5.2承载体的最大承载量应符合技术文件的规定,并能满足生产率的要求
3.5.3在抛丸器抛射方向、径向散射角度或喷枪升降,前后移动、转动、对工件进行抛喷丸加工的相对 位置应能满足抛喷丸工艺参数的要求
3.5.4承载体中承受弹丸冲击的部位应采取防护措施
3.5.5承载体不应对工件质量造成损伤,承载体的结构应便于工件的装卸
3.5.6对于具体的工件承载体应符合各自的产品标雅或技术文件的规定 3.6抛喷丸加工工作区技术要求 3.6.1抛喷丸加工工作应在封闭体内进行,封闭体以及工件进出口处应具有防止弹丸飞出的装置 3.6.2封闭体内弹丸抛打区域应有安全防护措施
3.6.3在工作状态下,封闭体内应密封良好
3.6 封闭体内的空间应能满足抛喷丸加工工件的需要
3.7 工件装卸系统技术要求 工件装卸系统与工件承载体的运动节拍应协调,最大装卸量应符合技朴文件的规定 3.8除尘系统 3.8.1设备应配有除尘系统或设有与除尘系统连接的接口
设备的通风量应满足除尘要求 3.8.2除尘系统应设计合理,防止管道堵塞
3.8.3除尘器工作时各部位不应出现漏尘现象
3.8. 在工作状态下,设备所配用的除尘器向大气的粉尘排放浓度应符合国家或当地环保部门的 规定
3.9空运转、负荷运转 3.9.1空运转时间不应少于4h
在空运转之后按工件承载体最大承载量进行负荷运转
3 .9.2工件承载体运转应灵活、平稳
工件应能及时准确到位接受抛喷丸加工
3.9.3各运动机构运行应正常,相邻运动零部件之间不应有摩擦、相碰等干涉现象
抛丸器无异常 振动
3.9. 各联锁机构应可靠
3.9.5电气控制系统应协调、灵敏
3.9.6液压和气动系统的动作应灵活、准确,不应有漏油、漏气现象
9.7各紧固件及管道连接处不应松动
3 33 .9.8滚动轴承温升不应超过35C,最高温度不应高于70C 3 .9. 9 在空运转条件下,配置一台或两台抛丸器的设备,其噪声声压级不应超过90dBA);配置超过 两台抛丸器的设备,其噪声不应超过93dBA)
喷丸时噪声声压级不应超过85dB(A)
3 .g.10设备各系统应能在技术文件规定的最大负荷状态下正常工作
3.g.11设备各系统应协调配合,不应有卡阻现象
3 .g.12弹丸循环系统各部分应工作协调,并能满足抛、喷丸器的弹丸供应量
3.g.13设备的整机生产率应符合技术文件或协议要求
3.9.14在技术文件规定的生产率和使用合适的弹丸条件下,按使用目的的不同,设备的使用性能应满 足以下条款的一项或几项的规定
对于设备的使用性能在协议或技术文件中作出明确的规定
3.9.14.1工件经抛丸加工后的清理等级应达到: Sa1轻度抛喷射清理 a 在不放大的情况下进行观察时,工件表面应无可见的油脂和污垢,并且没有附着不牢的氧化
GB/T23576一2009 皮、铁锈、油漆涂层和异物
注:如氧化皮、铁锈或油漆涂层能使用腻子刮刀刮掉,则应看成附着不牢
Sa2彻底抛喷射清理 b 在不放大的情况下进行观察时,工件表面应无可见的油脂和污垢,并且没有附着不牢的氧化 皮、铁锈、油漆涂层和异物
任何残留物应是牢固附着的
Sa21/2非常彻底抛喷射清理 在不放大的情况下进行观察时,工件表面应无可见的油脂和污垢,并且没有附着不牢的氧化 皮、铁锈、油漆涂层和异物
任何残留的痕迹应仅是点状或条纹状的轻微色斑
Sa3使零件表面洁净的抛喷射清理 在不放大的情况下进行观察时,工件表面应无可见的油脂和污垢,并且没有附着不牢的氧化 皮、铁锈、油漆涂层和异物
该表面应具有均匀的金属色泽
3.9.14.2工件经抛喷丸加工后的表面粗糙度应达到规定要求
3.9.14.3工件经抛喷丸加工后的抛喷丸强度应达到规定要求
3.9.14.4如无协议规定,工件表面覆盖率不应小于98%
试验方法 4.1总则 在对本标准各项技术指标进行测定时,应按本章和测定各项技术指标所用器具的使用说明书的规 定程序操作,保证测定数据的再现性
所用器具应标定证明能够满足测定要求
4. 易损件硬度的测定 2 在易损件的被测表面随机取均布的3个点,进行磨光,磨光面积大于硬度测试仪冲头面积
然后将 该易损件固定在具有一定刚性的载体上,进行硬度测定,取3点硬度的平均值即为该易损件的硬度
对于叶片,分丸轮、定向套,护板的硬度差的测定,应分别在各自的表面随机选择3点进行测定,最 后按测定结果确定出各自的最大值和最小值与3点硬度的平均值之差
4.3清洁度的测定 清洁度按JB/T5365.1或JB/T5365.2的规定测定
精度检验 精度检验项目按GB/T17421.1的规定测定
4.5抛射带的测定 在一块合适的钢板上涂上黑墨或铺设一张厚纸并标出需要抛射的区域,将其安放在预备抛射工件 处于相同位置的工件承载体上
启动设备,人工向抛丸器的漏斗加人少量弹丸抛射
关闭设备,取下木 板检查抛射带的位置,形状和面积 4.6直线振动筛滚筒筛除的合格弹丸的弹丸量的测定 在直线振动筛、滚筒筛的排渣口处分别放置一容器,使筛上物全部流人容器中
按工件承载体允许 的最大重量装上规定的工件,开动设备使弹丸进人正常的循环后,用已放好的容器分别接收来自直线振 动筛、滚筒筛排渣口的废料,1 后关机,对容器中的废料除去大块,按规定的筛分公差进行筛分,称 min 量符合公称尺寸的弹丸质量,并按弹丸质量与直线振动筛、滚简筛实际生产率的百分比进行计算
丸中含杂质量、废料中合格弹丸含量的测定 在设备正常负荷运转已形成循环条件下,打开供丸闸门5min后,在丸砂分离器整个幕帘长度上取 样(取样应在废料挡板下方),每个样为500g,共取3个样
对每个样品用精度不低于0.01g的天平进 行称重后,将弹丸和杂质分离开,并对杂质进行称重
分别按重量百分比计算含杂质量,取3次的算术 平均值即为丸中含杂质量
在设备正常负荷运转已形成循环条件下,在丸砂分离器废料口处取样,每个样为500g,共取3个
GB/T23576一2009 样
每个样品用精度不低于0.01g的天平进行称重后,将弹丸和杂质分开
同时筛除掉弹丸中不能进 人循环使用的弹丸,对可循环使用的弹丸进行称重,按重量百分比计算合格弹丸含量,取3次的算术平 均值即为废料中合格弹丸含量
4.8粉尘排放浓度的测定 按国家或当地环境保护部门的有关规定测定
弹丸循环系统的测定 按设备允许的最大加人弹丸量加人弹丸,抛丸器电流应达到额定值 4.10整机生产率 按工件承载体允许的最大承载量装上工件,开动设备用合适的弹丸对工件进行抛喷丸加工并同时 用秒表进行计时,直到抛喷丸加工效果达到工件要求为止,按已抛喷丸加工工件的重量或等量值与所需 抛喷丸加工时间进行计算,此值即为整机生产率
4.11噪声的测定 在空运转条件下,噪声按JB/T6331.2的规定测定
4.12工件经抛喷丸加工后的清理等级的测定 清除经抛喷丸加工后待测工件表面上的所有浮尘和碎屑,不管是在散射日光下或在照度相当的人 工照明条件下对工件表面进行观察,都应凭借正常的视力进行检查,并结合对弹丸覆盖率的情况做出目 视测定的结果
4.13工件经抛喷丸加工后的表面粗糙度的测定 清除经抛喷丸加工后待测工件表面上的所有浮尘和碎屑
4.13.1 用与工件材料、粗糙度相近的抛喷丸加工表面粗糙度标准比较样块与被测工件表面进行比较, 比较时应将比较样块靠近工件的某一个被测区,依次将被测表面与比较块的四个不同方向进行对比,通 过视觉和触觉判定抛喷丸加工表面的粗糙度
4.13. .3 测定过程中,应把表面粗糙度标准比较样块与工件置于同等条件下(如温度、光线等)
4.13. 对工件表面粗糙度要求高的如Ra值为0.2Am,0.4Am,0.84m),可借助放大镜进行观察比 .4 较
如果用放大镜时,应将放大镜放置得能同时观察到被测面和比较样块表面
放大镜的放大倍数不 应超过7倍
4.13.5当无法用比较样块进行表面粗糙度的测定时,应进行表面覆盖率的测定,用与被测表面同等条 件下加工的同等规格的平板进行测定
4.13.6 当对测定结果有争议时,可采用比上述方法测定精度更商的方法进行裁定
4.14工件经抛喷丸加工后的抛喷丸强度的测定 工件经抛喷丸加工后的抛喷丸强度的测定见附录A
. 4
15工件经抛喷丸加工后的表面覆盖率的测定 4. 15.1表面覆盖率的定义 在被抛喷丸工件表面的规定部位上,弹痕占据的面积与要求抛喷丸的面积之间的比值称为表面覆 盖率
表面覆盖率以百分数表示
在受抛喷工件表面留下等于或小于2%的原始表面就定义为100%的 目测表面覆盖率
4.15.2在抛喷丸加工过的工件表面任意选取被测点,用放大倍数至少为50倍的放大镜进行目测,并 统计在受抛喷表面上留下的原始表面的面积
按102 mm×102mm或104cm”面积范围内累计存在 的所有被弹丸压痕占据的表面积进行百分比计算,计算结果即为表面覆盖率
4.15.3如有协议规定超过100%的表面覆盖率,则用抛喷丸时间计算
示例;达到200%表面覆盖率表示工件经受抛(喷)时间为100%表面覆盖率的2倍
GB/T23576一2009 检验规则 5.1 出厂检验 5.1.1每台设备应经制造厂技术检验部门进行出厂检验合格后,并附有产品质量合格证方可出厂 5.1.2如无特别协议规定,出厂前至少应按3.1.2.3.1.7、3.1.17一3.1.19,3.4.1.2,3.4.3.4 3.4.3.8、3.4.3.113.4.3.13、3.5.4,3.6.1、3.6.2,3.6.4、3.8.1、3.8.2,3.9.13.9.9的规定进行检 验,所检项目应全部合格
5.2型式检验 5.2.1有下列情况之一时,应进行型式检验 a 新产品或老产品转厂生产的试验定型鉴定时; b)正式生产后如结构、工艺、材料有较大改变可能影响产品性能时 c)停产二年以上恢复正常生产时 d)国家质量监督机构提出型式试验要求时
型式检验应对本标准中所有项目进行检验,所检验项目应全部合格 5.2.2 5.2.3型式试验时抽验样品的数量 当每批产量小于等于10台时抽检样品一台; 当每批产量大于10台时抽检样品2台
当制造厂不具备型式检验条件时,允许在用户现场做试验
5.2.4 包装、标志、储运 设备的包装、标志、储运应符合JB/T16442005中7.17.5的规定
GB/T23576一2009 附 录A 规范性附录 抛喷丸强度的测定 弧高度曲线 A.1 弧高度试片在抛喷丸弹丸冲击下,表面层发生塑性变形,导致弧高度试片向抛喷丸面呈球面状弯曲 见图A.1),特定基准面至球面最高点之间的距离,称为弧高度,即抛喷丸强度 弧高度 直径为a的基准平面 喷丸面 弧高度试片 图A.1抛喷丸后弧高度试片产生弯曲的形状及弧高度 在其他的抛喷丸强化工艺参数不变的条件下,同一类型的弧高度试片分别各自接受不同时间的抛 喷丸,获得一组弧高度值随抛喷丸时间1(或抛喷丸次数)变化的数据,用这组数据绘制出弧高度曲 线,纵坐标及横坐标分别为弧高度值及时间轴(见图A.2) 高度增加量小于10%
作图的试验点举例 0.3810 0.3556 0.3302 0.3048 0.2794 0.254o 达到和所的时面 0.2286 0.2032 0.1778 0.1524 0.1270 0.1016 0.0762 0.0508 0.0254 89101112131415161718192021 抛喷丸时间 图A.2弧高度曲线 抛喷丸强度表示方法 在弧高度曲线上找出经一定时间抛喷后的准饱和点,当抛喷丸时间再延长一倍,弧高度值增加量小 于10%时,此准饱和点即为饱和抛喷丸点
用所测得的饱和抛喷丸点弧高度值(单位为mm)表示抛喷 丸强度
GB/T23576一2009 示例;如用A型标准弧高度试片测定的弧高值为0.36mm,即表示抛喷丸强度为0.36A
抛喷丸强度检测装置 抛喷丸强度检测装置包括检测仪和试片夹具,标准弧高度试片是用70号冷轧弹簧钢制成,共有三 种尺寸规格,其符号分别为N,A.c
三种试片的主要技术规格应符合表A.1中的要求,其他技术条件 应符合有关标准的要求
表A.1 试片型号 项 目 长度/mm 76.ll士0.29 宽度/mm 18.99士0.06 0.79士0.02 2.38士0.02 厚度" mmm 1.29士0.02 士0.025 平面度偏差" mm 0.63~1.25 表而粗糙度/pm 硬度/HRC 4450 A.4当喷丸强度在0.15A一0.60A范围时,应采用A试片;当喷丸强度大于0.60A时,则应采用 C 试片;当喷丸强度小于0.15A时,采用N型试片
A.5在一些不便于放置标准弧高度试片的情况下,可采用非标准尺寸的试片,在采用之前,应先对非 标准尺寸试片与标准弧高度对比试验,并按规定采用标准弧高度试片时的抛喷丸强度来确定非标准尺 寸试片的相应抛喷丸强度
抛喷丸强度的测定 A.6.1把标准弧高度试片固定在夹具上,再把标准弧高度试片夹具分别固定在图样规定的各个抛喷 丸部位的模拟件上
把模拟件放人抛喷丸室内的工装上,进行抛喷丸,卸下标准弧高度试片以非抛喷丸 面为基准面测量其弧高度值,抛喷丸使用过的标准弧高度试片不应再次使用
A.6.2重新装上新的标准弧高度试片进行抛喷丸并测量弧高度值
用57个标准弧高度试片经不 同抛喷丸时间(或抛喷丸次数)抛喷丸之后,获得一条弧高度曲线
用该曲线确定抛喷丸强度