GB/T26067-2010
硅片切口尺寸测试方法
Standardtestmethodfordimensionsofnotchesonsiliconwafers
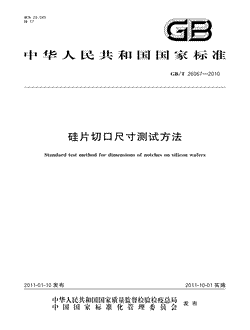
- 中国标准分类号(CCS)H80
- 国际标准分类号(ICS)29.045
- 实施日期2011-10-01
- 文件格式PDF
- 文本页数8页
- 文件大小330.20KB
以图片形式预览硅片切口尺寸测试方法
硅片切口尺寸测试方法
国家标准 GB/T26067一2010 硅片切口尺寸测试方法 Standardtestmethodfordimensionsofnotchesonsiliconwafers 2011-01-10发布 2011-10-01实施 国家质量监督检验检疫总局 发布 国家标准化管理委员会国家标准
GB/I26067一2010 前 言 本标准由全国半导体设备和材料标准化技术委员会材料分技术委员会(sAC/TC203/sC2)归口 本标准起草单位:有研半导体材料股份有限公司、万向硅峰电子股份有限公司 本标准主要起草人;杜娟、孙燕、卢立延、楼春兰
GB/T26067一2010 硅片切口尺寸测试方法 范围 本标准定性的提供了判定硅片基准切口是否满足标准限度要求的非破坏性测试方法
本方法的 测试原理同样适用于其他切口尺寸的测量
1.2本标准中物体平面尺寸为0.lmm时,通过20倍的放大后会在投影屏上形成2.0mm的影像,通 过50倍放大后会产生5.0mm的投影
本方法可以发现切口轮廓上的最小尺寸细节
1.3本标准不提供切口顶端的曲率半径的测试
规范性引用文件 下列文件对于本文件的应用是必不可少的
凡是注日期的引用文件,仅注日期的版本适用于本文 件
凡是不注日期的引用文件,其最新版本(包括所有的修改单)适用于本文件 GB/T2828.1计数抽样检验程序第1部分;按接收质量限(AQL)检索的逐批检验抽样计划 GB/T14264 半导体材料术语 术语和定义 GB/T14264界定的术语和定义适用于本文件
方法概述 本方法是利用一系列轮咪模板在显示屏上的投影与载物台上的特粥哇片的切口投影相比较,从而 得到待测硅片的切口是否满足规定要求
使硅片切口边缘的投影与定位硅片位置的定位销投影相切
此时,切口底部的投影应位于或者低 于切口和深度模板的一条已设定基准线,并且硅片边缘的投影位于或高于轮廓板上的另外一条基准线
4.3重新定位硅片,使硅片的边缘和轮廓模板中“硅片外围线”重合,此时切口底部的投影应在轮廓模 板上切口最深线和切口最浅线之间
切口边缘的投影与切口角度轮廓模板上一系列切口角度相比较,其中选择轮廓模板中与切口边缘 吻合最好的那个角的角度值作为切口的角度
4. 5 还可以使用边缘轮廓仪对于切口形状进行精确测量,具体参见附录A
干扰因素 5.1切口边缘处任何其他材料的沾污或者粗糙通过光路会产生扭曲的投影图像,导致检测出错误的切 口尺寸 5 2 切口位置相对于硅片中心点的校准是得到准确切口参数的重要环节
3 5. 磨削工具的磨损以及过程变差可能导致切口边缘不直,使切口顶点的半径不唯一
在这种情况 下,要特别关注定位切口投影图像在轮廓模板上的正确位置
5 按照特定晶向滚磨硅片边缘形成的切口是对硅片正确定位的方法
因此切口临界尺寸的精度直
GB/T26067一2010 接影响定位精度
设备 mm×51 光学投影仪:放大倍数20倍和50倍,可以显示51 mm区域放大20倍或者2mm×2mm 区域放大50倍投影图像的显示屏
6.2支架;用于固定待测试的硅片
支架确保硅片的表面与投影屏垂直,并且硅片可以以中心点为轴 旋转
沿硅片直径的水平或垂直运动必须通过切口所在区域
6.3轮廓模板;测试硅片时需要两个模板
6.3.1对于切口的定义包括切口形状和切口深度两部分,模板标有切口定义尺寸限度的线段 切口底部和硅片边缘相对于定位点中心的位置; 2 切口底部相对于硅片边缘的位置
不同直径的待测试片需要两个单独的模板
切口形状和深度模板例子见图1
单位为毫米 152.4(实际尺 152.4(实际尺 定位销 3.000 切口形状和深度模板 20x 一硅片外围线 切口底部界限 -硅片外围线 哥 切口最深线 -切口最浅线 标称硅片曲率半径 中355.6(实际尺寸) 注使用时逆时针转动90" 图1切口形状和深度模版
GB/T26067一2010 6.3.2测量切口角度的模板的角度范围从88"一96°,分刻度为1
6.3.3建立模板的方法见第8章
6.4校准板或精度棒;带有刻度,尺寸与切口的深度大致相同
用于精确建立设备的放大倍数
6.5尺子;长度为150mm,分刻度小于等于0.5; mm 放大倍数的确定 调整光学投影仪至理想的放大倍数
使用已知精确尺寸的校准板或精度棒,按照生产厂商的说明 书确定物像放大倍数,用三位有效数字表示
轮廓模准备 用放大倍数与每一个选定的轮嘴模板尺寸相来 8.1 8.2准备一个透明材料的模板,其尺寸与8.1要求的尺寸相同
投影图像的精度应高于士0.51 mm
8.3如图1,在切口形状和深度模板上标注水平和垂直轴
抽样 按照GB/T2828.1的规定进行,检查水平由供需双方协商确定
需方对抽样有特殊要求时由供需 双方协商解决
10测量步骤 10.1将放大倍数设定为20倍
10.2将支架固定在载物台上,确保切口在9点的位置
支架在载物台上垂直和水平方向的运动分别 平行和垂直于通过切口的直径
10.3将切口形状和深度模板放在投影仪屏幕上
调整水平线和垂直线,使固定销的轮廓在9点位置
10.4将第一个待测样品放在支架上,正面向上
10.5通过平面横向移动(水平)及定位旋转来调整支架,使模板上固定销的边缘与切口边缘的投影 相切
10.6确保切口底部的投影图像重合或者低于“切口底部界限”
如果切口底部的投影图像落在该界限 的上面,该硅片的切口不合格
10.7确保硅片边缘的投影与“硅片外围线”重合或在其下面
如果硅片边缘的投影图像落在硅片外围 线的上面,该硅片的切口不合格 10.8将支架向右延平面横向移动,直至硅片边缘的投影图像与标记为“硅片外围线”重合
10. 确保切口底部落在“切口最深线”和“切口最浅线”之间
若切口底部的投影图像落在两条线之 g 外,该硅片的切口不合格
10.10重复10.410.9,测量余下所有样品
10.11移开切口形状和深度模板,使用切口角度模板
10.12将放大倍数调到50偕
10.13将第一个待测样品放在支架上,正表面向上
10.14将支架平面横向移动并旋转,使得硅片切口边缘投影图像与切口角度轮廓模板中的每一个角度 比较
轮廓模板中与切口投影图像角度吻合最好的那个角的角度,定义为切口的角度
如果切口的角
GB/T26067一2010 度小于89°或大于95",硅片的切口不合格 10.15重复10.4对其余样品进行测试
11 报告 报告应包含以下信息 a)测试日期 操作人姓名; D 批号或者材料的其他标识; c 每批的硅片数量, d e) 已测试的硅片数量 f 不合格的硅片数量
12 精密度和偏差 本方法没有进行多个实验室评估
因此不推荐用于商业谈判,也不推荐用于仲裁
12.1 12.2物体平面尺寸为0.1mm的物体通过20倍的放大后会在投影屏上形成2.0mm的影像,通过 50倍放大后会产生5.0mm的投影
GB/I26067一2010 附 录A 资料性附录 硅片切口形状的精确测量 A.1除上述方法外,还可以使用边缘轮廓仪对于切口形状进行精确测量
其方法原理是使用激光投 影的方法对于硅片边缘的投影进行测量,得到边缘的形状和几何尺寸
这种方法不仅可以测量硅片的 切口形状、尺寸,还可对硅片参考面形状、尺寸及硅片的直径进行测量
A.2图A.1为标准切口图,图A.2为边缘轮廓仪对于切口的测量
单位为毫米 定位销直径3 定位销中心 90"5 T 切口边缘 曲奉半径0.9 通过硅片的基准线 图A.1硅片切口
GB/T26067一2010 h1.148m 3.191mm 片2.014mm 内3.162mmm r1.125mm Ang:89.4" 197.54mm O DiuaB:196,39mm Ang 切口角度 AngV V 切口深度; 切口宽度; V, 切口曲率半径; P=P-; 定位销顶端到切口底端的距离; P Dia 硅片直径; 直径
DiaB 图A.2切口轮廓图 A.3由于以激光投影方法为原理制造的边缘轮廓仪价格相对较高,而且目前对于切口尺寸的测试多 为定性测量,不必要精确测试结果,因此,本标准仍存在广泛的适用性