GB/T38446-2020
微机电系统(MEMS)技术带状薄膜抗拉性能的试验方法
Micro-electromechanicalsystemtechnology—Testmethodsfortensilepropertymeasurementofstripthinfilms
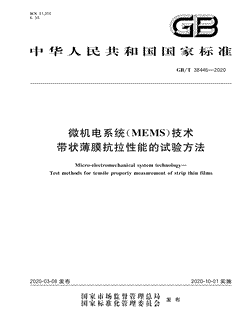
- 中国标准分类号(CCS)L55
- 国际标准分类号(ICS)31.200
- 实施日期2020-10-01
- 文件格式PDF
- 文本页数13页
- 文件大小1.19M
以图片形式预览微机电系统(MEMS)技术带状薄膜抗拉性能的试验方法
微机电系统(MEMS)技术带状薄膜抗拉性能的试验方法
国家标准 GB/T38446一2020 微机电系统(MEMS)技术 带状薄膜抗拉性能的试验方法 Miero-electromechaniealsystemtechnology- measurementofstripthinfilms Ielmethodsfortensileprpertsy 2020-03-06发布 2020-10-01实施 国家市场监督管理总局 发布 国家标涯花管理委员会国家标准
GB/T38446一2020 目 次 前言 范围 2 规范性引用文件 3 术语和定义
中,中 试验方法 数据处理 附录A资料性附录采用MEMS工艺的样品制备 附录B(资料性附录对准偏差和几何结构对性能测试的影响 附录c(资料性附浪》纳米压痕仪的测试结果误差及补偿 参考文献
GB/38446一2020 前 言 本标准按照GB/T1.1一2009给出的规则起草
本标准由全国微机电技术标准化技术委员会(SAC/Tc336)提出并归口
本标准起草单位:北京大学、中机生产力促进中心,北京智芯传感科技有限公司无锡华润上华科技 有限公司、中北大学、北京必创科技股份有限公司
本标准主要起草人:张威、李海斌、张亚婷,朱悦、夏长奉、石云波、陈得民、马书娜,程红兵、周浩楠
GB/38446一2020 微机电系统(MEMs)技术 带状薄膜抗拉性能的试验方法 范围 本标准规定了带状薄膜抗拉性能的试验方法及数据处理 本标准适用于厚度在50nm到数微米之间且长度和厚度的比值大于300的样品,也可用于MEMs 产品带状薄膜结构的质量监控
规范性引用文件 下列文件对于本文件的应用是必不可少的
凡是注日期的引用文件,仅注日期的版本适用于本文 件
凡是不注日期的引用文件,其最新版本(包括所有的修改单)适用于本文件
GB/T26111微机电系统(MEMS)技术术语 术语和定义 GB/T26111界定的以及下列术语和定义适用于本文件
3.1 弹性模量 mdlusofelastieity E 材料在弹性变形阶段时,应力与应变的比值
注:改写GB/T3102.3一1993,定义3.18,1 3.2 屈服强度yieldstrength Re 当材料呈现屈服现象时,在试验期间达到塑性变形发生而力不增加的应力点
注1;改写GB/T228.1一2010,定义3.10.2. 注2:对于屈服现象明显的材料,屈服强度就是材料发生屈服现象时屈服极限的应力;对于屈服现象不明显的材料 屈服强度为应变达到残余应变0.2%时的应力
3.3 抗拉强度tensilestrength Rm 材料拉断过程中对应的最大应力
注改写GB/T228.1一2010,定义3.10.1 3.4 挠度deflection 样品结构轴线在垂直于轴线方向的线位移或中面在垂直于中面方向的线位移
GB/T38446一2020 3.5 偏转角defleetionangle 弯曲的样品和连接样品两固定端直线间的夹角
注:本标准所指样品均为带状弯曲样品
试验方法 4.1试验环境 温度:15C35C; 相对湿度;20%一80%; 大气压力;86kPa106kPa
4.2样品要求 4.2.1样品的加工和尺寸 样品应使用和实际器件相同的加工工艺 附录A描述了一种基于MEMS工艺的样品加工方法
样品形状和符号定义分别如图1和表1所示
设计样品时,应最小化弯矩的影响,样品的长度宜大 于厚度的300倍;宽度宜大于厚度的10倍;长度宜大于宽度的10倍
样品应保证平直
图 薄膜样品 表1样品符号和定义 符号 单位 定义 2L 样品长度 m B 样品宽度 m 样品厚度 m 4.2.2样品的尺寸测量 长度(2L)、宽度(B)和厚度(h)的测量误差应在土5%之内
GB/38446一2020 4.3试验设备 试验设备是由驱动器、载荷尖端、对准装置、力和位移传感器组成的力学测试系统,如纳米压痕仪
各试验设备的详细要求如下所述: 驱动器;所有可以线性运动的激励设备均能用于此试验,如压电驱动器,音圈驱动器、伺服电机 等,分辨率应优于样品最大挠度的1/1000; b 载荷尖端;载荷尖端向样品施加线接触力,其形状就像传统的楔形压头尖端,尖端可由金刚石、 蓝宝石等硬质材料制成,尖端的半径应接近或大于样品厚度,且小于L/50(见表1) 对准装置:安装在测量设备上的载荷尖端应与位移检测的轴向和负载对准,且偏差小于1";尖 端表面还应和样品表面对齐,且偏差小于1(参见附录B中关于角度的对准偏差对性能测试 的影响),宜使用可倾斜的平台安装设备以便调整偏转角,尖端应安装在样品中心,且误差在 L/100以内; 力和位移传感器;力和位移传感器分辨率应优于1/1000,误差应在士1%之内
可以使用电容 d 式、线性差动变压器式或光学式位移传感器
4.4试验步骤 测量样品的记录长度(2L),宽度(B)和厚度(h). 4.4.1 44.2将包含有样品的衬底粘贴在样本夹具上
推荐使用如磁性粘贴、静电粘贴,胶粘剂粘合等方式 安装样品
4.4.3将样品放置于测试台上,调整位置,使载荷尖端的平面与样品的表面平行且位于样品表面的儿 何中心,并用光学显微镜进行检查
载荷尖端与样品间的位移和角度对准偏差会影响试验结果,参见附 录B
4.4.4确定样品的参考位置
参考位置是指样品的上表面的位置
这个位置可通过光学显微镜或三 次连续测试进行确定
当载荷尖端接触条带时,可通过光学显微镜观察到带状结构的微小形变
测试 条带上连接基片固定两端的表面位置和中心的表面位置,三个表面位置的平均值即视为样品条带的参 考位置,见图2
图2用于确定样品参考位置的三次连续测试 4.4.5在恒定位移速率下施加外力,直至条带断裂,见图3
根据不同样品选择施加的外力大小以及增 加步距
对应变速率不敏感的材料通常选择移动速率为L×10-/s或L×10-/s
记录所施加的外力 F)的大小和样品的挠度(w)
为了从试验结果中获得样品实际的受力和挠度,应根据所用试验设备 的具体情况做出一些补偿
例如,附录C所展示的使用纳米压痕仪时的误差和补偿
GB/T38446一2020 外力 薄膜 图3条带弯曲试验示意图 数据处理 S 5.1参数计算 通过4.4试验得到的相关参数计算以下性能参数 在弯矩可忽略和样品各处应变相同的假设基础上可以通过式(1)和式(2)计算应力和应变,见 a 图3 2 一7e" 式中 条带应力 -施加于条带的外力; tan-le/L); 3 条带应变; Z 相应的挠度
b)根据计算结果绘制应力-应变曲线,得到弹性模量,屈服强度和抗拉强度
注:当L/h大于300,式(1)和式(2)对弹性模量和屈服强度有很好的近似结果,可用附录B提供的方法进行验证 当内应力存在时,式((1)中的F会受其影响,条带应力也会发生改变 5.2试验报告 试验报告包括但不限于以下信息 a) 执行标准; b 试验环境; 样品标识号 c 样品制造工艺; d 样品材料(若为单晶体,注明晶向;若为多晶体,注明结构和晶粒尺寸) 样品尺寸和测量方法; f) 试验设备详情; g h) 测量属性和结果;弹性模量,抗拉强度和应力-应变曲线
GB/38446一2020 附 录 A 资料性附录 采用MEMs工艺的样品制备 A.1样品制造 样品可以通过MEMS工艺制备
针对不同的测试材料和器件,可以开发不同的MEMS工艺流程
图A.1介绍了一种MEMs工艺流程,详细描述如下 在Si圆片上沉积氧化物薄膜
a b 在氧化物薄膜上沉积测试材料薄膜
Au,Mo,SINr可用作测试材料
可淀积粘合剂层以增 强氧化物薄膜和测试材料薄膜间的附着力
为了最小化测量时的刚度效应,粘合剂层的厚度 -定要谨慎选择
图形化测试材料薄膜以固定样品的形状
co d) 用氧化物或光刻胶钝化层保护图形化的样品
制作独立式的薄膜,使用DRIE刻蚀S基片背面
e fD 移除光刻胶或氧化物得到独立式的薄膜
d aSi衬底和氧化物沉积 样品钝化 b 样品沉积 e刻蚀 c 样品图形化 门光刻胶或氧化物去除 (100)si 氧化硅 氮化硅 样品 光刻胶 图A.1样品的工艺流程图
GB/T38446一2020 A.2样品的尺寸测量 样品的尺寸可用多种方法进行测量
测量样品的厚度可用台阶仪或AFM原子力显微镜)测量;样 品的宽度和长度可用电子显微镜甚至光学显微镜测量
为防止薄膜由残余压应力产生屈曲,条带上连 接基片的固定两端的长度即可认为是样品的长度
GB/38446一2020 附录 B 资料性附录 对准偏差和几何结构对性能测试的影响 B.1背景 通过带状弯曲试验得到的结果会受到多种误差源的影响
其中一部分为样品的儿何结构,另外一 部分则是平移和有角度的对准偏差
使用有限元仿真,可以估算这些误差源的影响,并且提供了有帮助 的测试指导建议
样品有三个参数,长度,宽度和厚度
根据弹性模量和屈服强度误差,并在精确对准 情况下,这些参数的影响可被估计
由于平移和有角度的对准偏差而造成的误差也可被估计
B.2有限元仿真 对于带状弯曲试验样品生成了三维有限元模型,使用有限元软件对其进行了仿真
材料特性采用 了14m厚Au薄膜的抗拉实验结果,仿真的本构模型是弹性的和可塑性的
使用有限元仿真,提取了 样品的作用力和挠度数据,并且相应的应力和应变数据通过使用5.1中的公式进行计算
弹性模量和 屈服强度(0.2%误差)可通过估计的应力-应变数据进行计算
误差则通过计算值和仿真输人值的差进 行估计
B.3分析结果 在精确对准下的弹性模量和屈服强度误差通过有限元分析进行了估计,并且在图B.1中绘制
当 长度/厚度比增加时,弹性模量和屈服强度的误差减小了,所估计的特性也比真实特性略小
当长度和 厚度的比值远大于300时,误差小于1%
10 B/h=10 --0---B/h=20 B/h=30 型 -6 一8 -10 100 200 300 400 500 长厚比M a 长度和厚度的比值对弹性模量误差影响的有限元分析 图B.1基于1Hm厚Au薄膜数据误差的有限元分析
GB/T38446一2020 10 B/h=10 -O--B/h=20 B/h=30 一10- 10o 300 500 200 400 长厚比/n b)长度和厚度的比值对屈服强度误差影响的有限元分析 图B.1(续) 平移和角度的对准偏差分析如图B.2结构所示
基于仿真结果,当平移(d)未对准小于L/100时, 发现d对弹性模量和强度的影响小于0.1%
角度对准偏差中,a对结果有着最重要的影响,由a造成 的误差随着宽度B增加而增大
当B/h为10并且a小于1"时,弹性模量和屈服强度的误差小于 0.5%
当3和Y小于1时,它们对于弹性模量和屈服强度的影响小于0.1%
载荷尖端圆角半径对于弹性模量和强度估值的影响也进行了估计
当半径增加时,弹性模量和强 度的误差也增大
强度误差的增长快于弹性模量误差的增长
当半径小于L/50时,误差小于0.5%
图B.2平移(d)和角度(a,,?)未对准
GB/38446一2020 附录 C 资料性附录 纳米压痕仪的测试结果误差及补偿 误差成因 C.1 产生误差的原因主要为热漂移和试验设备的弹簧片刚度
C.2热漂移补偿 热漂移是一种常见的造成精密传感器测量误差的因素
这种误差被认为是测试系统热波动的结 果
为了测试热漂移,在负载控制条件下记录该偏差一段时间,同时样品与楔形顶部相接触
通过使用 漂移数据,修正了带状弯曲试验偏差数据
这是纳米压痕试验常见的补偿手段
由于蠕变与温度漂移 难以区分,这个补偿不能用于有蠕变特性的样品
C3弹簧片刚度补偿 许多商业纳米压痕系统利用一个弹簧片实现高可重复性的线性运动,见图C.1
该设备通过控制 电磁驱动器的电流给样品上施加作用力
该驱动器作用力的大小为电流乘以负载校准常数
样品的实 际受力等于驱动器作用力减去使弹簧片形变的力
弹簧片受力可通过驱动器在不安装样品的情况下进 行测量
为了补偿弹簧片受力,可将有样品的外力挠度数据减去无样品的外力挠度数据
条带上的 实际作用力信号可通过这个过程确定
电磁激励器 弹黄片 位移传感器 测试样品 图C.1纳米压痕仪的示意图
GB/T38446一2020 参 考文献 [1]GB/T228.1一2010金属材料拉伸试验第1部分;室温试验方法 [[2]GB/T3102.3一1993力学的量和单位 10
微机电系统(MEMS)技术带状薄膜抗拉性能的试验方法GB/T38446-2020
微机电系统(MEMS)技术是一种新兴的技术,其应用范围非常广泛,包括汽车、医疗、通信等各个领域。在MEMS制造过程中,薄膜是一个非常重要的组成部分,因此对其力学性能的测试也显得尤为重要。
为了规范带状薄膜的抗拉性能测试方法,国家于2020年发布了GB/T38446-2020《微机电系统(MEMS)技术带状薄膜抗拉性能的试验方法》标准。
该标准主要针对带状薄膜的抗拉性能进行测试,并规定了相应的测试方法、试验设备及试验环境等方面的要求。其中,试验方法包括常温下的静态拉伸试验和疲劳试验,试验设备包括拉伸试验机、载荷传感器和位移传感器等。同时,标准还对试验过程中的误差进行了分析和控制。
此外,该标准还规定了带状薄膜的测试样品制备方法和尺寸要求等方面的内容。例如,对于不同厚度的薄膜,其样品的长度和宽度应有所区别,并且在制备过程中要注意避免产生划痕、氧化等影响测试结果的因素。
总之,GB/T38446-2020标准的制定为MEMS技术中带状薄膜抗拉性能测试提供了规范,为相关行业的研究和应用提供了技术支持。