GB/T9061-2006
金属切削机床通用技术条件
Generalspecificationsformetal-cuttingmachinetools
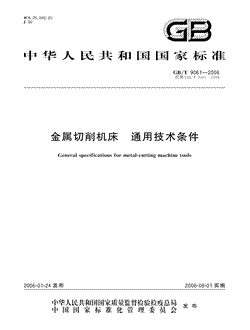
- 中国标准分类号(CCS)J50
- 国际标准分类号(ICS)25.040.20
- 实施日期2006-08-01
- 文件格式PDF
- 文本页数15页
- 文件大小542.83KB
以图片形式预览金属切削机床通用技术条件
金属切削机床通用技术条件
国家标准 GB/T9061一2006 代替GB061-198s 金属切削机床通用技术条件 Generalspecificationsformetal-cuttingmachinetools 2006-08-01实施 2006-01-24发布 国家质量监督检验检疫总局 发布 国家标准化管理委员会国家标准
GB/T9061一2006 前 言 本标准代替GB/T9061一1988(《金属切削机床通用技术条件》
本次修订按照GB/T1.1一2000 《标准化工作导则第1部分;标准的结构和编写规则》对原标准进行了编写,标准结构和技术内容有所 调整和变化,规定更加具体,提高了可操作性
本标准与GB/T9061一1988相比,主要变化如下 -按照GB/T1.1的规定,增加了“目次”“前言”和“引言”
条款表述等用词符合要求,文字措 词等力求简洁明确,内容格式和图表按编写规则进行了修改; -标准结构进行了调整,取消了原标准的第4章“加工和装配质量”及第5章“外观质量”,该两章 的技术内容并人本标准的第3章,并将第3章的原标题“基本要求”改为“技术要求”
原标准 的第6章改为本标准的第4章,原标题“验收检验”相应更改为“检验与验收”
突出了“技术要 求”和“检验与验收”两部分为本标准的主要构成; 将原标准第1章标题“主题内容与适用范围”改为“范围”,并对原标准适用范围的表述进行了 修改,使适用界限和对象更加直观明确, -本标准第3章增加了“数控系统”一条,相应在第4章增加了“数控系统的检验” 由于涉及人身健康或设备安全防护的技术要求属于强制性标准的内容,按照可直接引用原则, 对原标准3.8“安全卫生”作出了较大修改(见本版的3.9); 参照国外先进标准,并考虑国内目前制造水平和提高产品质量的原则,将原标准6.6.10“整机 连续空运转试验”中的数字控制机床连续运转时间进行了调整(见本版的4.6.12); 取消了原标准带有的“附则”,原“附则”中的有关技术要求内容写人了本标准,各项规定作了充 实和完善 增加了规范性附录“确定主轴轴承的稳定温度和温升值的方法”(见附录A); 增加了资料性附录“机床主传动系统最大扭矩的试验及近似计算法”(见附录B); 增加了资料性附录“机床最大切削抗力的试验及近似计算法)"(见附录C)
本标准的附录A为规范性附录,附录B,附录C为资料性附录
本标准由机械工业联合会提出 本标准由全国金属切削机床标准化技术委员会(SAC/TC22)归口
本标准起草单位;北京机床研究所
本标准主要起草人:徐光武、李祥文、张维
本标准所代替标准的历次版本发布情况为 -JB2278一78,GB/T90611988
GB/T9061一2006 引 言 本标准是对GB/T9061一1988《金属切削机床通用技术条件》的修订
修订时,本标准除按照 GB/T1.1一2000的要求进行了编写外,在标准结构、技术内容上作出了调整和完善
GB/T9061 1988的前身是原第一机械工业部部颁标准JB2278一78《金属切削机床通用技术条件》,已经实施近 15年
GB/T9061是机床产品基本的共同性质量要求的总规定(也称总标准),其涉及产品设计,制造 及检验验收等的技术要求比较系统、完整,促进了机床产品质量标准体系的发展,对行业的制造技术水 平和产品质量的提高具有重要作用
GB/T9061与已补充及具体化为目的而制定的各类型机床产品技术条件也称分标准)构成了评 定产品质量的技术依据
GB/T9061一2006 金属切削机床通用技术条件 范围 本标准规定了金属切削机床(以下简称机床,包括组合机床、机床附件等)基本的、共同性的技术 要求
本标准适用于机床设计、制造、检验与验收
各类型机床产品可根据其使用性能、结构等特点,编制 相应的产品技术条件标准,对技术指标,评定方法和检验项目等规定作出补充和具体化 规范性引用文件 下列文件中的条款通过本标准的引用而成为本标准的条款
凡是注日期的引用文件,其随后所有 的修改单(不包括勘误的内容)或修订版均不适用于本标准,然而,鼓励根据本标准达成协议的各方研究 是否可使用这些文件的最新版本
凡是不注日期的引用文件,其最新版本适用于本标准
GB/T191一2000包装储运图示标志(eqvIsO780:1997) GB/T3167一1993金属切削机床操作指示形象化符号(neqIsO7000:1984) GB/T3168一1993数字控制机床操作指示形象化符号(neqISO2972:1979 GB5226.1机械安全机械电气设备第1部分;通用技术条件(GB5226.1一2002/IEC60204 1:2000 GB/T6477.1一1986金属切削机床术语基本术语 GBT6t77.2一1986金属切削机床术语组合机床及组合机床自动线 GB/T6477.16一1986金属切削机床术语机床附件 GB/T65762002机床 润滑系统(so510.197.MoD》 气动系统通用技术条件(IsO4414;,1998,IDT) GB/T79322003 GB/T13306一1991标牌 金属切削机床静刚度检验通则 GB/T13574 1992 金属切削机床型号编制方法 GB T 153751994 GB15760金属切削机床安全防护通用技术条件(GB157602004y 金属切削机床振动测量方法 GB/Tl6768一1997 金属切削机床噪声声压级测量方法 GB/T16769一1997 B/T23261994机床附件型号编制方法 1999数控机床坐标和运动方向的命名(eqIsO841:1974 JB/T3051 JB/T3207一1991机床附件产品包装通用技术条件 JB/T3997一1994金属切削机床灰铸铁件技术条件 JB/T41681999组合机床型号编制方法 JB/T8356.1一1996机床包装技术条件 JB/T8356.21996机床包装箱 JB/T88322001机床数控系统通用技术条件 JB/T9872一1999金属切削机床机械加工件通用技术条件 JB/T9873一1999金属切削机床煤接件通用技术要求 JB/T9874一1999金属切削机床装配通用技术条件 JB/T9875一1999金属切削机床随机技术文件的编制
GB/T9061一2006 JB/T9877一1999金属切削机床清洁度的测定 JB/T9935一1999机床附件随机技术文件的编制 JB/T10051一1999金属切削机床液压系统通用技术条件 技术要求 3.1型号、名称和参数 机床的型号、名称宜按照GB/T15375,GB/T6477.1,GB/T6477.2,GB/T6477.16JB/T4168和 JB/T2326等的有关规定进行编制和给出
数控机床坐标和运动方向的命名宜符合JB/T3051的规 定
机床的参数宜符合各类型机床参数标准的规定
机床与工夹量具、附件等连接部位的型式和尺寸 应符合有关标准的规定
3.2布局和造型 3.2.1机床造型设计美观大方,外部结构与色彩匀称、和谐
外露的附件、配套件应与整机协调 3.2.2机床各部件及装置应布局合理、高度适中,便于操作者观察加工区域
机床应排屑方便
3.2.3机床的手轮、手柄和按钮等应布置合理,操作方便,并符合有关标准的规定
3.2.4机床应装,拆、调整和维修方便
整体或拆分运输的机床应符合运输和装载的要求
3.3性能与结构 机床性能和结构应满足用户的要求
机床的设计还宜充分考虑系列化、通用化、标准化、模块化
附件和工具 机床应备有保证基本性能的附件和工具
扩大机床使用性能的特殊附件,根据用户要求按协议供 应
附件和工具宜标有相应的标记或规格
机床的标准附件和工具,均应保证连接部位的互换性和使用性能
3.5电气系统 机床的电气系统应符合GB5226.1的规定
3.6数控系统 机床的数控系统应符合JB/T8832的有关规定
液压、气动冷却和润滑系统 机床的液压系统应符合JB/T10051的规定 3 7 .2 机床的气动系统应符合GB/T7932的规定
3.7.3机床的冷却系统应保证冷却充分、可靠
机床的润滑系统应符合GB/T6576的规定
3.7.5机床的液压、气动、冷却和润滑系统及其他部位均不应漏(渗)油、漏(渗)水,漏气
切削冷却液 不应混人液压系统和润滑系统
3.8测量装置 机床和附件的测量装置应准确、可靠,读数部分便于操作观察,视场清晰
有密封要求处应设有可 靠的密封装置
3.9安全卫生 机床上有可能对人身健康或对设备易造成损伤的部位,应采取安全措施,机床的安全防护应符合 GB15760等有关标准的规定
3. 10寿命 3. 10.1机床重要的及易磨损的导轨副应采取耐磨措施,并符合有关标准的要求
3. 10.2对机床主轴、丝杠,蜗杆副和高速,重载齿轮副等主要零件也应采取相应措施,提高其工作 寿命
3.10.3机床主轴、导轨、丝杠等易被尘屑磨损的部位宜采取防护装置
GB/T9061一2006 3.11标牌 机床上的产品标牌宜符合GB/T13306的有关规定
标牌上的内容应正确并符合有关规定,汉字 应采用国家公布的简化字
操作标志等指示形象化符号应符合GB/T3167,GB/T3168及有关标准和 技术文件的规定
3.12随机技术文件 机床随机技术文件应包括使用说明书将合格证明书和装箱单
机床随机技术文件的编制方法宜符 合JB/T9875,JB/T9935等标准的规定
3.13加工质量 3.13.1机床上各种零件材料的牌号和机械性能应符合相应标准的规定
零件的加工应符合相应标 准、图样和工艺文件的规定
3. 13.2灰铸铁件质量应符合JB/T3997的规定
3.13.3热处理件质量应符合有关标准的规定
13.4机械加工件质量应符合JB/T9872的规定
3. 3. 13.5焊接件质量应符合JB/T9873的规定
3. 14装配质量 3. 机床的装配质量应符合B/T974的规定
3. 14.2机床装配过程中清洁度检测要求和方法宜符合JB/T9877的规定
3. 15 外观质量 3.15.1机床外观表面不应有图样未规定的凸起,凹陷,粗糙不平和其他损伤 3.15.2机床的防护罩应平整、匀称,不应翘曲、凹陷 .15.3机床零,部件外露结合面的边缘应整齐、匀称,除设计允许外不应有明显的错位
错位量和错 位不匀称量宜符合表1的规定
机床的门、盖与机床的结合面应贴合,贴合缝隙值不大于表1的规定
机床的电气柜电气箱等的门、盖周边与其相关件的缝隙应均匀,缝隙不均匀值不大于表1的规定
表1 单位为毫米 二500 >5001250 >12503150 >3150 结合面边缘及门,盖边长尺寸 错位量 错位不匀称量 1.5 贴合缝隙值 1.5 缝隙不均匀值 注1;当配合面边缘及门、盖边长尺寸的长,宽不一致时,按长边尺寸确定允许值 注2:错位不匀称量指外露结合面边缘同一边或对应边最大错位量与最小错位量之差值
注3,缝隙不均匀值指门,盖间对开缝或其相对机床本体间最大缝隙值与最小缝隙值之差值
3 15.4外露的焊缝应平直、均匀
15.5装人沉孔的螺钉不应突出于零件表面,其头部与沉孔之间不应有明显的偏心
固定销(轴用固 3 定销两端均露者除外)一般应略突出于零件外表面
螺栓尾端应略突出于螺母端面
外露轴端一般应 突出于包容件的端面,突出值约为倒棱值
内孔表面与壳体凸缘间的壁厚应均匀对称,其凸缘壁厚之差 不应大于实际最大壁厚的25%
3. 15.6机床外露零件表面不应有磕碰,锈蚀
螺钉,铆钉,销子端部不应有扭伤,锤伤等缺陷
3.15.7金属手轮轮缘和操纵手柄应有防护层
3.15.8电镀件,发蓝件发黑件色调应一致,防护层不应有褪色、脱落现象
3.15.9电气、液压、润滑和冷却等管道的外露部分应布置紧凑,、排列整齐,并不应产生扭曲、折叠等
GB/T9061一2006 现象
3. 15.10机床零件未加工的表面应涂以油漆
涂漆应符合有关标准和技术文件的规定
可拆卸的零、部件装配结合面的接缝处,在涂漆以后应切开,切开时不应扯破漆面
3.15.11机床上的各种标牌应清晰、耐久
产品铭牌宜固定在机床的明显位置,并应平整牢固、不 歪斜
检验与验收 4.1概述 4.1.1每台机床应在制造厂经检验合格后出厂
某些机床需安装在整个生产线上才能进行检验,或检 验时需要大量专用毛坯及制造厂不具备特大,特重工件等情况时,经用户同意也可在机床使用处进行 检验
4.1.2机床检验分为型式试验和出厂检验
4.1.2.1属于下列形式之一,应进行型式试验 新产品试制,定型鉴定; a 机床结构、性能较基型有重大改动时
bb 4.1.2.2出厂检验一般包括以下内容 外观检验; a 附件和工具的检验; 参数检验(抽查); e d 机床的空运转试验(含抽查项); 机床的负荷试验(含抽查项); e 机床的精度检验(含抽查项); g其他
注:注明“抽查”检验的项目,在足以保证成批生产产品的质量条件下,其抽查时间、方法、台份等一般由制造 规定
4.2一般要求 4.2.1机床检验时,应注意防止气流,光线和热辐射的干扰
机床应防止受环境温度变化的影响,有恒温要求的机床应在规定的恒温条件下进行检验,检具在使 用前应与机床等温
4.2.2检验与验收前,应将机床安置在适当的基础上,按照制造厂的使用说明书调平机床,并应符合相 应的精度检验标准中所规定的安装要求
4.2.3检验过程中,不应调整影响机床精度和性能的机构和零件
用地脚螺栓紧固的机床,在检验过 程中不应重新调整安装水平
否则,应复检调整后受到影响的有关项目
4.2.4检验原则上是在制造完毕的成品上进行,特殊情况下可按制造厂的使用说明书拆卸某些零 部件
4.2.5机床由于结构上的限制或不具备规定的测试工具时,可用与标准有同等效果的方法代替
4.3外观检验 4.3.1按3.2评定机床的布局和造型仅在型式试验时进行)
4.3.2按3.15检验机床的外观质量
附件和工具的检验 按3.4检验随机供应的附件和工具是否符合规定
4.5参数检验(抽查 按3.1检验机床的参数
检验机床与工夹量具、附件等连接部位的型式和尺寸是否符合有关标准
GB/T9061一2006 的规定
4.6机床的空运转试验 4.6.1运转检验 .6.1.1机床应在无负荷状态下进行空运转
试验时,机床的主运动机构应从最低速度起依次运转 每级速度的运转时间不应少于2min
用交换齿轮、.皮带传动变速和无级变速的机床,可作低、中,高速 运转
在最高速度时应运转足够的时间(不应少于1h),使主轴轴承(或滑枕)达到稳定温度
4.6.1.2进给机构按其各项功能依次作变换进给量(或进给速度)的空运转检查,批量生产产品检验 时,可仅作低、中,高进给量(或进给速度)检查
注:对于进给机构与主运动机构有传动关系的机床应解释为“进给量”;对于进给机构与主运动机构无关系的单独 驱动系统应解释为"进给速度”" 有快速移动的机构,应作快速移动的试验
4.6.2温升试验 4.6.2.1主轴轴承达到稳定温度时,检查其温度和温升,温度和温升值不应超过表2的规定
确定主 轴轴承的稳定温度和温升值的方法见附录A
表2 单位为摄氏度 轴 式 承型 温 度 温 升 滑动轴承 60 30 滚动轴承 70 注:机床经过一定时间的运转后,其测量温度值上升幅度不超过每小时5C时,一般可认为已达到稳定温度
4.6.2.2液压系统的温升试验,宜符合JB/T10051的规定
主运动为往复运动的机床,应在最高速度 下检查运动件(滑枕、工作台等)导轨的稳定温度
其他重要部位轴承或热源的温度和温升值,应符合有 关标准和技术文件的规定
4.6.3主运动和进给运动的检验(抽查 检验主运动速度和进给速度(进给量)的准确性,并检查快速移动速度(或时间)
在所有速度下,机 床工作机构均应平稳、可靠
4.6.4动作试验 机床动作试验应包括以下内容 以一个适当的速度检验主运动和进给运动机构的起动、停止(包括制动、反转和点动等)和动作 a 是否灵活、可靠,一般应反复动作10次; 检验自动机构(包括自动循环机构)的调整和动作是否灵活、可靠; b 反复变换主运动和进给运动的速度,检查变速机构是否平稳,可靠和指示的准确性 d 检验转位,定位,分度机构动作是否灵活、可靠; 检验调整机构,夹紧机构,读数指示器和其他附属装置是否灵活,可靠; fD 检验装卸工件、刀具和附件等装置是否灵活、可靠; 与机床连接有传动关系的随机附件,应进行连接试运转,并检查相互关系是否符合设计要求; g 检验其他操纵机构动作是否灵活、,可靠; h 检验有刻度装置的手轮反向空程量和手轮、手柄的操纵力
手轮反向空程量和手轮、手柄操纵 力应符合有关标准的规定
注:数控机床除按上述各条检验外,还应按有关标准和技术文件进行动作试验
4.6.5安全防护装置和保险装置的检验 安全防护装置和保险装置应符合GB15760等有关标准的规定,检查其是否齐备、可靠
4.6.6噪声检验 机床的噪声声压级在空运转条件下测量,测量方法宜符合GB/T16769的规定,测量结果应符合
GB/T9061一2006 GB15760的规定
4.6.7空运转功率试验(抽查) 在机床主运动机构各级速度空运转至功率稳定后,检查主传动系统的空运转功率
对于进给运动 与主运动分开的机床,必要时宜检查进给系统的空运转功率 注:检验空运转功率时,应扣除电动机本身消耗的功率,但当电动机直接装在主轴上时自驱式主轴),则不扣除电 动机本身消耗的功率
空运转功率的指标由各类型机床分标准规定 4.6.8电气系统的检验 机床电气系统应符合GB5226.1等有关标准的规定,检查其工作性能是否符合要求
4.6.g数控系统的检验 机床数控系统应符合JB/T8832的规定,并检验其与主机联接后是否可靠、稳定
4.6.10液压、气动,冷却和润滑系统的检验 液压、气动、冷却和润滑系统应符合3.7的规定
4.6.11测量装置的检验 测量装置应符合3.8的规定
4.6.12整机连续空运转试验 自动,半自动和数控机床可在全部功能下模拟工作状态作不切削连续空运转试验,其连续运转时间 应符合表3的规定
连续运转试验过程中不应发生故障,如出现异常或故障,在查明原因进行调整或排 除后,应重新开始试验
试验时,自动循环应包括所有功能和全部工作范围,各次自动循环之间的休止 时间不应大于1 min
表3 单位为小时 机 床 控 制 型式 连续运转时间 机械控制 电、液控制 联动轴数3 36 数字控制 48 联动轴数>3 4.7机床的负荷试验 4.7.1机床承载工件最大重量的运转试验(抽查 在机床上装上设计规定的机床承载最大重量的工件,机床以低速及设计规定的高速运转,检验机床 运转是否平稳、可靠
4.7.2机床主传动系统的扭矩试验 扭矩试验包括: 机床主传动系统最大扭矩的试验; a bb 机床短时间超过最大扭矩25%的试验(数控机床除外). 试验时,在小于或等于机床计算转速的转速范围内选一适当转速,逐级改变进给量或切削深度,使 机床达到规定扭矩
检验机床传动系统各传动元件和变速机构是否可靠,检验机床是否平稳和运动是 否准确
机床主传动系统最大扭矩的试验及近似计算法见附录B 对于成批生产的机床,允许在2/3倍最大扭矩下进行试验,但应定期进行最大扭矩和短时间超过最 大扭矩25%的抽查性试验
4.7.3机床切削抗力试验
切削抗力试验包括: 机床最大切削抗力的试验; a b)机床短时间超过最大切削抗力25%的试验(数控机床除外
GB/T9061一2006 试验时,选用适当的几何参数的刀具,在小于或等于机床计算转速的转速范围内选一适当转速,逐 渐改变进给量或切削深度,使机床达到规定的切削抗力
检验各运动机构、传动机构是否灵活、可靠
机床最大切削抗力的试验及近似计算法见附录c
对于成批生产的机床,允许在2/3倍最大切削抗力下进行试验,但应定期进行最大切削抗力和短时 间超过最大切削抗力25%的抽查性试验 4.7.4机床主传动系统达到最大功率的试验(抽查) 根据机床的类型,选择适当的加工方式、,试件(材料和尺寸、刀具(材料和几何参数),常用进给量、 切削速度,逐步改变切削深度使机床达到最大功率(一般为电动机的额定功率),检验机床在最大功率切 削下各部分工作状态的稳定性、金属切除率及电气系统等是否可靠
注1:最大功率是指机床上主电动机的额定功率,不是设计的最大功率
某些机床如只能在设计规定的计算功率下 进行最大功率试验时, 般应在机床使用说明书中注明,此情况下可按最大设计计算功率进行试验 注2:机床设计时,如主电动机额定功率不是从生产效率的角度来确定的(如根据机床起动的要求来确定等,则该 类型机床应在分标准中规定具体的试验方法
4.7.5抗振性切削试验(抽查) 对于某些机床除进行最大功率试验外,还应进行以下试验 有限功率切削试验(由于工艺条件限制而不能使用全部功率); aa bb 极限切削宽度试验
根据机床的类型,选择适当的加工方式、试件(材料和尺寸、刀具(材料和几何参数)、切削速度和进 给量,检验机床结构的稳定性
4.8机床的精度检验 4.8.1几何精度检验 按各类型机床产品精度检验等有关标准的规定进行检验
检验时,各部分运动应手动(或用低速机 动)
负荷试验前后(不做负荷试验的机床在空运转试验后)均应检验机床的几何精度
凡与温度有关 的精度项目对机床工作精度和使用性能有影响),在中速稳定温度时进行检验
最后一次精度检验的 实测数值应记人产品合格证明书中 注中速是指机床主轴(或滑枕)最高速度的二分之一
当主轴转速级数中没有与中速相一致的级数时,要选取高 于中速的速度级数 4.8.2工作精度检验 按各类型机床产品精度检验等有关标准的规定进行检验
4.8.3运动的不均匀性检验 按有关标准的规定进行检验 4.8.4振动试验(抽查) 按有关标准的规定进行试验,振动测量方法宜符合GB/T16768的规定
4.8.5刚度试验(抽查) 按有关标准的规定进行试验,静刚度检验宜符合GB/T13574的规定
热变形试验(抽查 4.8. 按有关标准的规定进行试验
4.8.7其他精度检验 按有关技术文件的规定进行检验 注:不需全面作4.8试验的机床,可按有关标准和技术文件的规定进行
4.9其他 可按订货合同中技术要求的有关内容进行
GB/T9061一2006 包装 5.1机床在包装前,必须进行防锈处理
5.2出厂的整台机床包装箱内,一般应随机供应一套技术文件
对于结构复杂的机床,宜提供两份使 用说明书 5.3机床的包装应符合GB/T191、JB/T8356.1JB/T8356.2,JB/T3207等有关标准的规定
制造厂的保证 在符合机床的运输、保管、安装、调试、维修和遵守使用规程的条件下,用户自收货之日起一年内,因 设计,制造或包装质量不良等原因造成机床损坏或其不能正常使用时,制造厂应负责包修,包退,包换
GB/T9061一2006 附 录 A 规范性附录 确定主轴轴承的稳定温度和温升值的方法 主轴轴承温度和室温的测量 A.1 机床主轴在最高转速下运转,每间隔一定时间测量主轴轴承的温度和室温
经一定时间的运 转后,轴承温度上升幅度不超过每小时5C时,可认为已达到稳定温度
A.1.2以时间(T)为横坐标,温度()为纵坐标,将间隔一定时间测得的轴承温度和室温画成变化曲线 图,使每小时温度上升5C的斜率线与轴承温度变化曲线相切
该切点定为主轴轴承达到稳定温度时 的温度值(Gi),此值减去同一时间测得的室温值(),即为主轴轴承达到稳定温度时的温升值(e 轴 承温度和室温变化曲线示例见图A.1
温度1/ 每小时温度上升5C的斜率线 30 轴承温度变化曲线 20 蜜淋安化曲线 10 时间T/h 主轴轴承达到稳定温度时的室温值; 主轴轴承达到稳定温度时的温度值; 主轴轴承达到稳定温度时的温升值
图A.1轴承温度和室温变化曲线示例 A.2测温点的选择 A.2.1为了测得主轴轴承的实际温度,机床设计时应在结构上予以考虑测温点
A.2.2由于受机床结构的限制使直接测量轴承温度受到影响时.实际测温点的温度与轴承温度的差 值应通过试验找出规律加以修正,对于成批量生产的产品,其测温点所测温度应按温差规律修正值 检验
GB/T9061一2006 附 录 资料性附录 机床主传动系统最大扭矩的试验及近似计算法 机床主传动系统最大扭矩的试验,可用功率表和转速表分别测量机床电动机的输人功率和机床主 轴转速,宜按下面的公式近似计算出机床的扭矩,该扭矩应等于机床的最大扭矩
试验时,一般应在等 于或小于机床计算转速范围内选一适当转速,通过逐级改变进给量或切削深度,使机床达到规定扭矩
T9550(P一P/n B.1 式中 扭矩,单位为牛米(Nm); 切削时电动机的输人功率(指电网输给电动机的功率),单位为千瓦(kw) 机床装有工件时的空运转功率(指电网输给电动机的功率),单位为千瓦(kw); 机床主轴转速,单位为转每分(r/min). 机床主传动系统短时间超过最大扭矩25%的试验方法同上,可继续改变进给量或切削深度,使切 削扭矩达到额定值的125%即可
此公式仅是一种近似计算法,必要时可采用其他更精确的公式
1o
GB/T9061一2006 附 录 C 资料性附录 机床最大切削抗力的试验及近似计算法 机床最大切削抗力的试验,可用功率表和转速表分别测量机床电动机的输人功率和机床主轴转速, 宜按下面的公式近似计算出机床切削抗力的主分力,按主分力和刀具角度确定机床的切削抗力,该抗力 应等于机床的最大切削抗力
试验时,一般应选用机床重切削时最常用的刀具,在等于或小于机床计算 转速范围内选一适当转速,通过逐渐改变进给量或切削深度,使机床达到规定的切削抗力
9550(P一P, F C.1 式中 切削抗力的主分力,单位为牛(N); 切削时电动机的输人功率(指电网输给电动机的功率),单位为千瓦(kw) -机床装有工件时的空运转功率(指电网输给电动机的功率),单位为千瓦(kW); 工件或刀具的切削半径,单位为米(m); -机床主轴转速,单位为转每分(r/nin). 机床短时间超过最大切削抗力25%的试验方法同上,可继续改变进给量或切削深度,使切削抗力 达到额定值的125%即可 此公式仅是一种近似计算法,必要时可采用更精确的公式
对于某些不适用该公式的机床,可按其 他有关公式计算