GB/T11809-2021
压水堆燃料棒焊缝检验方法金相检验和X射线照相检验
TestmethodofweldoffuelrodforPWR—Metallographicexaminationandradiographictesting
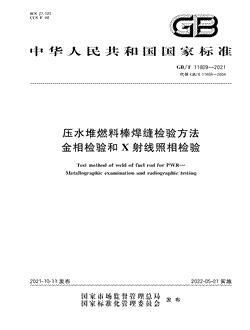
- 中国标准分类号(CCS)F48
- 国际标准分类号(ICS)27.120
- 实施日期2022-05-01
- 文件格式PDF
- 文本页数27页
- 文件大小4.87M
以图片形式预览压水堆燃料棒焊缝检验方法金相检验和X射线照相检验
压水堆燃料棒焊缝检验方法金相检验和X射线照相检验
国家标准 GB/T11809一2021 代替GB/T11809一2008 压水堆燃料棒焊缝检验方法 金相检验和x射线照相检验 TestmethodofweldoffuelrodforPwR一 Metallographicexaminationandradiographietesting 2021-10-11发布 2022-05-01实施 国家市场监督管理总局 发布 国家标涯花警理委员会国家标准
GB/11809一2021 目 次 前言 范围 2 规范性引用文件 术语和定义 金相检验 X射线照相检验方法 l3 检验报告 附录A资料性 -般燃料棒结构图 附录B(规范性》金相样品取样方法 15 18 附录C资料性浸蚀方法 19 附录D(资料性检测和照相倍数 附录E(规范性有效熔深s值的测量 20 半补偿照相法最小透照厚度计算方法 附录F规范性 22 附录G(资料性)透照布置 23 附录H(资料性燃料棒焊缝X射线照相检验补偿方法 24
GB/11809一2021 前 言 本文件按照GB/T1.1一2020《标准化工作导则第1部分;标准化文件的结构和起草规则》的规 定起草 本文件代替GB/T11809一2008《压水堆燃料棒焊缝检验方法金相检验和X射线照相检验》, 与 GB/T118092008相比,除结构调整和编辑性改动外,主要技术变化如下 将术语“环焊缝熔深”修改为“包壳环焊熔深”见3.1,2008年版的3.1),“环焊缝熔化区深度 depthofthemeltedzoneofringwelding ”修改为“环焊熔化区深度depthofthemelted zone”见3.2,2008年版的3.3) ipartofweldzone" e”修改为“ leastthickneSSotsOund minimum thicknessofsoundpartofweldzone" ”(见3.5,2008年版的3.,5) b 增加“密实区长度”V型槽”的术语和定义见3.7、3.8); 金相检验方法中增加了针对压力电阻焊焊缝的金相检验内容(见第1章、4.5.2.3、4.5.3.1、4.6.2) c d 砂纸规格修改为P120P2400见4.2.6,2008年版的4.2.5); 增加金相样品的规定(见4.4); e 将金相取样内容调整为附录B,合并了上端环焊缝及密封焊点与下端环焊缝的纵向样品取样 fD 图(见B.1,2008版的4.4.1、4.4.2),增加了压力电阻焊金相焊缝样品的取样方法,并对附录顺 序进行了调整见附录B,2008年版的4.4); 用GBZ117代替了GB16357(见5.2,2008年版的5.2) g h)修改X射线照相的检验人员资格(见5.3,2008年版的5.3); 增加了半补偿照相补偿块制作方法(见5.4.7.2),X射线胶片灰雾度要求(见5,4.5)、密度计测 量误差要求(见5.4.6)和一次透照长度计算方法(见5.5.1)等内容; 修改了工业X射线机要求(见5,4.1,2008年版的5.4.1),观片灯屏亮度的要求(见5,4.4,2008 年版的5.4.4)、像质计灵敏度的要求(见5.5.4,2008年版的5,5.3)、几何不清晰度计算公式(见 5.5.5,2008年版的5.5.4)、散射线防护要求(见5.5.6,2008年版的5.5.5)、底片密度范围(见 5.5.8,2008年版的5.5.7)和透照转角要求(见5.6.3,2008年版的5.6.3)等内容; k)合并及完善X射线照相检验报告与记录内容(见6.2,2008年版的6.2) 将热染法的温度修改为 C(见表C.1,2008年版的表B.1 I m删除存在单个气孔缺陷时有效熔深的测量示意图(见2008年版的图C.4,图c.5图C.6); n)增加金相样品检测及照相倍数(见附录 增加附录F半补偿照相法最小透照厚度计算方法(见附录F); o 增加附录H燃料棒焊缝x射线照相检验补偿方法(见附录H
P 请注意本文件的某些内容可能涉及专利
本文件的发布机构不承担识别专利的责任
本文件由全国核能标准化 技术秀 员会(SAC/TC58)提出并归口
本文件起草单位;中核建中核燃料元件有限公司
本文件主要起草人;范绍华、曹晖、,袁野、代强、马海涛、周希,黄杰,黄帆
本文件及其所代替文件的历次版本发布情况为 GB11809一1989,GB/T11809一1998 GB11851一1989,GB/T11851一1996, -2008年修订时,将GB/T11809与GB/T11851合并为GB/T11809-2008 本次为2008年合并后第二次修订
GB/T11809一2021 压水堆燃料棒焊缝检验方法金相检验和 X射线照相检验 范围 本文件描述了压水堆燃料棒(以下简称燃料棒)焊缝的金相检验和X射线照相检验方法
本文件的金相检验方法适用于采用电子束、钨极惰性气体保护进行焊接的错合金燃料棒熔化焊焊 缝(包括环焊缝和密封焊点)样品的熔深,缺陷及微观组织的检验
也适用于采用压力电阻焊进行错合 金燃料棒焊接的焊缝的密实区的检验
其中的薄膜浸蚀法仅适用于采用电子束焊接的ZrSn合金燃料 棒焊缝检验
燃料组件中错合金导向管焊缝熔深和缺陷以及采用其他焊接方式得到的焊缝的金相检验也可参照 执行
本文件的X射线照相检验方法适用于燃料棒环焊缝以及密封焊点的检查,压水堆燃料组件控制 棒、可燃毒物棒、中子源棒以及导向管部件环焊缝,其他堆型类似燃料棒环焊缝也可参照执行
规范性引用文件 下列文件中的内容通过文中的规范性引用而构成本文件必不可少的条款
其中注日期的引用文 件.仅该日期对应的版本适用于本文件;不注日期的引用文件,其最新版本(包括所有的修改单)适用于 本文件
GB/T3375焊接术语 GBT69金属平均晶粒度测定方法 无损检测术语射线照相检测 GB/T12604.2 GB18871电离辐射防护与辐射源安全基本标准 GB/T19348.12014无损检测工业射线照相胶片第1部分;工业射线照相胶片系统的分类 GB/T19802无损检测工业射线照相观片灯最低要求 GBZ117工业X射线探伤放射防护要求 术语和定义 GB/T3375和GB/T12604.2界定的以及下列术语和定义适用于本文件
3.1 包壳环焊熔深penetrationftheringwelding S 包壳管与端塞媒接熔合厚度(见图1)
GB/T11809一2021 图1环焊缝测量参数示意图 3.2 环焊熔化区深度depthofthemeltedzonme P 包壳管与端塞焊接熔化区最大深度(见图1)
3.3 密封焊点熔深penetrationofthesealweding S 密封媒点沿中心轴线方向测得的最小熔合厚度(见图2). 习 S=mintS.S 图2密封焊点测量参数示意图 3.4 lweding 密封悍点厚度depthoftheseal P 密封焊点熔合最小厚度(见图2. 3.5 ofweldzone 环焊缝有效熔深 minimumthieknessofsoundpart 环焊缝中排除缺陷影响后包壳管与端塞熔合处的焊接最小厚度
GB/11809一2021 3.6 气胀 underut 包壳管环焊缝根部咬边的现象
密实区长度continuityarealength 压力电阻焊环焊缝中焊接结合区的纵向长度(见图3)
焊缝内无缺陷 焊缝内有缺陷 a b 标引序号和符号说明: 挤出物 12 -端塞端面; 包壳管; -端塞; 焊缝密实区长度; -焊缝连续无缺陷区的长度,当焊缝内有缺陷时,L=L1十L
或L十L.,取较大值,即最长的两段 L1、L2、L 之和
图3压力电阻焊密实区长度的测量参数示意图 3.8 V型槽noteh 压力电阻焊环焊缝包壳管端部与外部挤出物之间的缺口(见图4)
GB/T11809一202 爆破后的压力电阻焊环焊缝纵截面 b)A区放大图 a 包壳管破口; 标引序号说明: -端塞端面; -包壳管; 包壳管; 焊接不连续区; -V型槽
结合线; 挤出物 -端塞与包壳管结合处; 图4压力电阻焊环焊缝缺陷检查示意图 金相检验 4.1原理 用线切割或机械加工方法从待测件上切割一块样品,镶嵌后,对待测面进行研磨、抛光和浸蚀,然后 在金相显微镜上进行测量和缺陷检查
燃料棒一般结构和焊缝位置见附录A 4.2试剂和材料 4.2.1酒精(CH,CH,OH),化学纯
4.2.2草酸(H.C,O2H.(O),化学纯
4.2.3硝酸(HNO.),质量分数为65%~68%,化学纯
氢氟酸(HF),质量分数为40%,化学纯
4.2.4 4.2.5镶样材料;环氧树脂、丙烯酸树脂、酚醛树脂或硫黄等
4.2.6金相水砂纸,P120~P2400. 42.7抛光材料抛光布和抛光剂,抛光剂粒度为0.03m一0.05pm.
GB/11809一2021 4.3仪器设备 4.3.1 金相磨抛机
4.3.2金相显微镜,测量精度0.005n mm
4.3.3游标卡尺,测量精度0.05 mm
4.3.4马弗炉,最高温度不低于800C
4.4样品 4.4.1采用线切割或机械加工等方式从待测件上切割一块作为样品,样品切割面应平整
4.4.2样品应包含熔化区及热影响区,长度以15" mm一20mm为宜,检验面应保留约0.5 mm一 1.0mm的金相磨制余量 4.4.3熔化焊和密封点的焊接样品宜采用纵向切割方式,压力电阻焊的焊接样品可采用纵向和横向 两种切割方式
样品取样拨照附录目的方法进行 4.5制样 4.5.1镶样 4.5.1.1镶样前,样品一般先用酒精清洗后晾干
除压力电阻焊环焊横截面样品外,其余样品应用环氧树脂,丙烯酸树脂、酌醒树脂或碗黄等银 4.5.1.2 嵌材料镶样
4.5.1.3如采用热染法检验组织,则样品清洗后不应镶嵌
4.5.2磨制 4.5.2.1样品应在不同粒度的金相水砂纸上进行逐步磨制,磨制过程中应用流水冲洗,最终磨面应光滑 平整 4.5.2.2纵截面样品的磨面宜平行于样品中心轴线,最终磨面应接近与中心轴线重合
4.5.2.3压力电阻焊横截面样品应磨制到检验面位置,见图5,并用游标卡尺对最终磨面进行测量
-般取1.6mm1.8mm
GB/T11809一2021 标引序号和符号说明 取样时包壳管切口 包壳管; 端塞内端面; 4、6 焊缝挤出物; 检验面位置(横截面) 端塞 端塞内蹦面到包壳管切口的距离; -检验面位置到包壳管切口的距离 -检验面到端塞内端面的距离
图5压力电阻焊横截面检验位置 4.5.3机械抛光 压力电阻焊环焊缝在浸蚀后有明显的焊接结合线,样品应机械抛光去除结合线,便于检查时确 4.5.3.1 认是否有煤接不连续区.
4.5.3.2其余样品,必要时可使用抛光布及抛光剂进行抛光
4.5.4浸蚀 可用化学浸蚀法、薄膜浸蚀法或热染法进行浸蚀
适用的浸蚀方法见附录C 4.6检测 4.6.1熔化焊焊缝的检测 4.6.1.1P
和P
的测量 样品磨面经薄膜浸蚀法浸蚀后不应擦拭,以免破坏浸蚀膜
对于正置式显微镜,可直接带水观察; 对于倒置式显微镜,吹干水迹后在显微镜上观察,在适当倍数下测量环焊缝的尸,或密封焊点的尸u 必要时照相记录熔化区图像,常用检测及照相倍数见附录D.
GB/T11809一2021 4.6.1.2s,和s,的测量 浸蚀后的样品清洗干燥后,在金相显微镜上放大适当倍数测量出环焊缝的S,或密封焊点的S 4.6.1.3s的测量 按照附录E的方法测量有效熔深s
4.6.1.4焊缝缺陷检验 浸蚀后在适当放大倍数下检验样品的熔化区,如有裂纹、气孔、夹杂、气胀等缺陷,应记录其类型尺 寸及部位
4.6.1.5悍缝微观组织检验 用热染法或其他有效浸蚀方法显示出三区后,在金相显微镜下检查焊缝熔化区、热影响区和基体的 晶粒组织,必要时照相记录,照相可采用明场或偏光照明
晶粒度的评级可按GB/T6394执行
4.6.1.6环焊缝分层检测 将分层检测样品镶嵌后磨制,每磨去约0.2mm,进行化学浸蚀后在显微镜下观察是否有气孔或气 胀等缺陷,直至磨完整个环焊缝熔化区
如有缺陷,在适当倍数下测量其大小并记录其位置,必要时照 相记录
4.6.2压力电阻焊的焊接样品检测 4.6.2.1 爆破试验破口位置检查 对爆破试验后样品检查是否沿缝结合线破裂,如图4所示
4.6.2.2V型槽缺陷检查 如果需要,按图4检查并测量V型槽缺陷的深度,超过规定值时记录测量结果
4.6.2.3焊接不连续区总长度测量 如果需要,按图4测量焊缝内部的单个不连续缺陷长度以及焊接不连续区总长度,对于内部挤出物 部分出现的不连续区可不测量
4.6.2.4焊缝密实区长度测量 如果需要,按图3测量炽缝密实区长度L,结果精确到0.1mm
4.6.2.5焊缝状态检查 如果需要,按图6所示检查焊缝状态,当出现管过熔或冷态时应记录其状态
GB/T11809一202 标准:焊缝根部与端塞端面平齐 管过熔;焊缝根部偏管子侧,包壳管过度熔合 b 冷态;焊缝未熔合长度超过约定值 标引序号和符号说明 包壳管; -端塞; 未熔合长度
图6压力电阻焊纵截面标准状态及缺陷状态示意图 4.6.2.6横截面缺陷检查 如果需要,检查横截面焊缝结合线处的缺陷并测量缺陷尺寸,横截面典型缺陷示意图见图7
当相 邻气孔间距小于3倍气孔直径时应视为一组串孔,测量其总长度
如果横截面上缺陷尺寸或数量超过 规定的标准,可继续磨抛样品进行检查,直至无缺陷或超出检验区域为止,检验位置如图5所示 标引序号说明 未焊透" 串孔 微气孔 夹杂
图7压力电阻焊横截面样品典型缺陷
GB/11809一2021 x射线照相检验方法 5.1原理 X射线在穿透过程中,强度因吸收、散射和扩散等发生衰减
环焊缝照相采用厚度补偿法,透照时 将燃料棒环焊缝插人补偿块孔内,形成一个组合体,密封焊点可与上端环焊缝共用一个补偿块,置于X 射线透照场内一起透照
燃料棒焊缝的缺陷在X射线底片上形成特征影像,通过特征影像来判断并评 价焊缝质量
燃料棒一般结构和焊缝位置见附录A
5.2防护 X射线的安全防护应符合GB18871和GBZl17的规定
5.3人员资格 5.3.1燃料棒焊缝射线检验人员应按照所从事的工作取得相应等级的民用核安全设备无损检测资格 证书
工业X射线机操作人员应参加电离辐射安全与防护培训及考核,并取得相应类别的合 5.3.2 格证
5.4设备和器材 5.4.1工业x射线机 管电压不超过320kV,焦点和焦距选择满足几何不清晰度要求
5.4.2像质计 阶梯孔型像质计,像质计对x射线的吸收系数应与被检件一致或相近,每级阶梯厚度应与该级上 两个孔的直径相等,阶梯级数一般为3级,像质计宽度H为8mm10mm,阶梯长度L不小于6mm 梯级厚度和孔径加工精度;下偏差0mm,上偏差十0.015mm
孔中心到阶梯边缘及两个孔边缘之间的 最小距离应为孔径加1mm,孔应与阶梯表面相垂直,不应有倾斜边缘
粗糙度应优于Ra1.6
像质计 分类见表1,结构见图8
表1像质计类别 单位为毫米 类别 孔径尺寸 I类 类 类 类 第1级阶梯 0,16 0.20 0.25 0.32 第2级阶梯中 0.20 0.25 0.32 0.40 0.25 0.32 0.50 第3级阶梯内 0.40
GB/T11809一2021 标引序号和符号说明 刻字区; 阶梯长度; H 像质计宽度
图8像质计结构示意图 5.4.3增感屏 铅增感屏,前屏厚度及后屏厚度为0.02mm~0.15mm
5.4.4观片灯 主要性能应符合GB/T19802的规定,亮度可调,屏亮度最小值不低于30000cd/m
灯屏应有遮 光板遮挡非评定区
5.4.5工业x射线胶片 采用符合GB/T19348.1一2014中的C3类别或更高类别胶片,灰雾度不超过0.3
5.4.6密度计 最大密度不小于4.0,误差为士0.05
5.4.7厚度补偿块 5.4.7.1要求 厚度补偿块按所检焊缝形状和尺寸制造,其对X射线的线吸收系数与被检件一致或相近,且需经 X射线检验合格
孔加工尺寸要求;pDf8歪 1,D代表被检部位直径
在保证补偿块适度刚性的前 mm, 提下,补偿块厚度尽可能小
5.4.7.2分类 按照燃料棒焊缝X射线照相检验补偿方法,厚度补偿块分为全补偿照相补偿块和半补偿照相补偿 块,厚度补偿块示意图见图9
按照附录F计算半补偿照相补偿块的最小透照厚度wmm,半补偿照相补 偿块应在焊缝区域选取合适的宽度,从补偿块的上下两面去除相同的厚度,保证焊缝有效区域的剩余厚 度大于或等于最小透照厚度wm即可
10
GB/T11809一2021 全补偿照相厚度朴偿块 C 半补偿照相厚度补偿块 图9厚度补偿块示意图 5.5照相的技术要求 5.5.1 一次透照长度 按照公式(1)计算一次透照长度
制作补偿块时,透照有效区的长度应小于一次透照长度
! -2x(一)x/KT 一1 ,
, 式中 -次透照长度,单位为毫米(mm) ffd 焦距,单位为毫米(mm); -工件至胶片距离,单位为毫米(mm); K 透照厚度比一般取1.03 5.5.2透照件布置 将燃料棒插人补偿块的圆孔内时,应使环焊缝、密封焊点处在规定的位置,使全部被透照燃料棒的 环州缝处在一条直线段上
透照时X射线发生器窗口中心指示器应对准此直线段的中点
透照时,所有补偿块的透照有效区应处于有效透照场内
像质计和铅字标识处在投影正面,其投影 不应与焊缝投影重叠
且像质计宜处在射线照相最不利的位置
透照件布置见附录G 5.5.3环焊缝和密封焊点的表面要求 环焊缝和密封焊点的表面质量应经外观检查合格
表面的不规则状态在底片上的图像不应掩盖焊 缝中的缺陷或与之相混淆,否则应做适当的修整
5.5.4像质计灵敏度 像质计灵敏度要求识别的双孔一般在阶梯孔型像质计的第2级阶梯上,同一阶梯上的双孔均可见 才认为可识别,不同透照厚度下像质计可见的双孔尺寸如表2所示: 11
GB/T11809一2021 表2透照厚度与像质计阶梯厚度及孔径关系 单位为毫米 透照厚度 像质计阶梯厚度及孔径 厚度<4 0.20 4<厚度8 0.25 8<厚度12 0.32 12<厚度l6 0,40 5.5.5几何不清晰度 几何不清晰度值应小于0.1mm,按照公式(2)计算
d×b U 式中: -几何不清晰度,单位为毫米(mm); U 焦点尺寸,单位为毫米(mm); -工件至胶片距离,单位为毫米(mm); ffd 焦距,单位为毫米(mm)
5.5.6散射线防护 应采用金属增感屏、铅板、准直器等适当措施,屏蔽散射线和无用射线
初次使用的检测工艺,以及 检测条件和环境发生变化时,应进行散射线检查
散射线检查方达;在背板与暗盒之间放置一个铅字符 号“B"B的高度为13mm,厚度为1.6mm),若在底片上出现黑度低于周围背景黑度的“B"字影像说明 背射线防护不够,底片不合格,需增大背散射防护铅板的厚度
若底片不出现“B”字影像或“B"字影像 黑度高于周围背景黑度,说明背射线防护符合要求
5.5.7标识 底片上的各种标识应清晰、完整
5.5.8底片密度 在像质计第2级阶梯上测量底片密度,底片密度应在1.8~3.5之间
5.5.9重照 不符合5.5.2,5.5.45.5.7、5.5.8的规定或发现有影响底片评定的伪缺陷时,应重新透照
5.5.10透照参数 通过工艺试验或制作被检件材质的曝光曲线来确定透照参数
5.6检验步骤 5.6.1装片 将X射线胶片和铅增感屏装人暗盒内,增感屏应保持清洁、平整
12
GB/T11809一2021 5.6.2贴片 将暗盒紧贴于工件上,保证在整个射线透照过程中胶片与增感屏始终相互贴紧,没有任何机械 损伤
5.6.3透照 环焊缝及密封焊点透照布置示意图见附录G
X射线照相检验按补偿差异分为全补偿照相法和半 补偿照相法,见附录H
在采用全补偿照相时,环焊缝应透照三次,每次透照完成后,将燃料棒转动60" 或120"
在采用半补偿照相时,环焊缝透照次数为n,=180'/0(0<60'),180"应能被/整除,/是燃料 棒转动角度 5.6.4暗室处理 按胶片说明书提供的程序和参数或其他的有效方法对透照后的胶片进行暗室处理
5.6.5底片评定 5.6.5.1 底片图像质量评定 底片应干燥后进行评定;评片时,对底片上不需要观察或透光量过强的部分应适当屏蔽,所评定的 底片质量应符合5.5,4、5.5.7、5.5,8的规定
5.6.5.2焊缝缺陷评定 焊缝缺陷评定按技术条件及检验规程相关要求进行
检验报告 6.1金相检验 金相检验报告应包括但不限于以下内容 熔深等参数的测量结果; aa b) 缺陷几何尺寸及部位; 检验人员及日期
c 6.2X射线照相检验 X射线照相检验报告包括但不限于以下内容 质量标准及版本; aa 5 X射线照相检验条件;设备型号、焦点尺寸、焦距、管电压、管电流、透照时间、像质计的选择、胶 片型号、增感屏、洗片温度、洗片时间等 燃料棒编号及对应透照日期、批次 c ) 缺陷燃料棒编号、缺陷部位及性质; 检验人员及透照日期、评片人员和复核人员签名及日期
e 13
GB/T11809?2021 ? A ) -???? ?????λ???A.1 ? -?; ?(??躸); ?; UOо; ?; ?; ; ?(??躸); 9 ?; 10 ??(?躸??? ?A.1??????? 14
GB/11809一2021 录 附 B 规范性) 金相样品取样方法 B.1环焊缝及密封焊点纵向样品 燃料棒密封焊点与环焊缝在同一端塞且在同一纵截面检验时,可一起切取
用线切割或机械加工 方法取适宜长度的样品,一般取L、为15mm一20mm,切割面距中轴线距离1为0.5mm1mm,然后 沿切割面剖开取较大块,见图B.1
标引序号及符号说明 切割面; 切割面距中轴线距离 样品长度
Ls 图B.1环焊缝及密封焊点纵截面取样示意图 B.2环焊缝横向分层检测样品 用线切割或机械加工方法将样品沿切割面切去端头,然后取适宜长度的样品,一般取L、为15mm~ 20mm,切割面距焊缝熔化区边缘的距离!为0.5mm1mm,见图B.2 15
GB/T11809一2021 标引序号及符号说明 -切割面; 熔化区; 切割面距焊缝熔化区边缘的距离; Ls -样品长度
图B.2环焊缝横向分层检测取样示意图 B.3爆破后的压力电阻焊环焊纵向样品 爆破后的压力电阻焊环焊的检验面需经过破口位置
用线切割或机械加工方法取适宜长度的样 品,一般取L、为15mm一20mm,切割面距中轴线距离1为0.5mm1mm,然后沿切割面剖开取较大 块,见图B.3
标引序号及符号说明: 1,3 破口; 切割面; 4、5未破断处 -切割面距中轴线距离; 样品长度
Ls 图B.3爆破后的压力电阻焊环焊纵向样品示意图 16
GB/T11809一2021 B.4测量密实区长度的压力电阻焊环焊纵向样品 mm20mm, 用线切割或机械加工方法取适宜长度的样品,一般取Ls为15 ,切割面距中轴线距离 1为0.5mm1mm,然后沿切割面剖开取较大块,见图B.4
标引序号及符号说明 切剂面; -切割面距中轴线距离; 样品长度
图B.4测量密实区长度的压力电阻悍环悍纵向样品示意图 B.5压力电阻焊环焊横截面样品 用线切割或机械加工方法沿切割面1及切割面2横向切断,取适宜长度的样品,一 般取Ls为 5mm~20mm,见图B.5,切割面1距端塞端面距离/由设计文件规定 标引序号及符号说明 12 -切割面; -切割面1距端塞端面的距离; -样品长度 Ls 图B.5压力电阻焊环焊横截面样品示意图 17
GB/T11809一2021 录 附 资料性 浸蚀方法 浸蚀原理 C.1 c.1.1薄膜浸蚀法 薄膜浸蚀法也称薄膜染色法
样品经选定的薄膜浸蚀剂浸蚀之后,由于浸蚀剂与磨面上组织化学 作用的结果,磨面上形成一层厚薄不均匀的化学沉积物覆盖在各组织上,在白色光的照射下,引起了光 的干涉现象
在焊缝熔化区覆盖的较浅颜色的沉积物与较深颜色基体形成明显的界限,用肉眼或显微 镜均能清晰地分辨和测量
C.1.2化学浸蚀法 化学浸蚀是选定适当的化学浸蚀液对检验面进行浸蚀,其浸蚀过程是一个化学溶解过程
浸蚀剂 首先把磨面表层的非晶形层溶去,接着就对晶界起化学溶解作用,继续浸蚀,浸蚀剂将对晶粒起溶解作 用,由于磨面上每个晶粒的位向不同,溶解速度各异
浸蚀后,每个晶粒将露出原子最密排面,并与磨面 形成不同的角度
在显微镜垂直光线照射下,将显示出阴暗不一的晶粒组织
C.1.3热染法 热染法用于检验燃料棒焊缝的熔化区、热影响区及基体组织(简称三区组织)
热染法是置抛光好 的样品于400C500C空气中加热,使磨面形成一层氧化膜,在同一温度下由于晶粒位向的差异,氧 化能力高低各异,致使不同晶粒形成氧化膜厚度不一,靠白色光在氧化膜之间产生干涉而显示出不同色 彩的晶粒组织
C.2 浸蚀方法 适用的浸蚀方法见表C.1
表C.1适用的浸蚀方法 说明 浸蚀方法 适用范围 试剂组分 焊区轮廓显示 样品磨制后直接浸人试剂中晃动约3s一8s, 过饱和草酸溶液 100ml ZrSn 薄膜法 合金电子束 取出后流水冲洗10、左右
浸蚀后熔化区 氢氟酸(40% 20ml 焊接 为白色,其他区域为黑色 硝酸(65%68% 45mL Zr-Sn合金及Zr-ND 擦拭样品表面10s一20s,流水清洗10、 氢氟酸(40% 化学浸蚀法 10ml. 合金焊接样品的浸蚀 左右 合 水 45mL 将未镶嵌的样品磨制后按化学浸蚀法处理 ZrSn合金及Zr-ND 干燥后在已升温到450C士50左右的马 热染法 合金焊缝三区组织的 弗炉中,视颜色变化,保温2nmin一5min,出 显示 炉冷至室温
热染后样品表面颜色为蓝色 偏光或明场下检查 18
GB/11809一2021 附 录 D 资料性) 检测和照相倍数 D.1检测倍数通则 金相样品检测倍数宜清晰分辨不同的金相组织接缝和焊接缺欠,测量精度宜满足样品要求
如遇 到难以判断的组织或缺欠,可放大至更高一级倍率下检测
如测量值超过当前倍数下测量范围,可通过 较高倍数确定测量位置后,使用低一级倍数进行测量
D.2照相倍数通则 金相样品照相倍数宜使视场大小包含大部分待检区域,如环焊缝、密封焊点熔化区,压力电阻焊变 形区
对焊接缺陷照相时宜显示缺陷在焊接接头中的相对位置,必要时可分别提供同一位置的低倍和 高倍照片
D.3常用倍数 常用样品检测和照相倍数见表D.1
表D.1常用样品检测和照相倍数 样品类型 放大倍数 检测倍数 环焊缝纵向样品 放大100倍及以上检测 放大50倍及以上照相 放大50倍及以上检测 放大10倍及以上照相 密封焊点纵向样品 环焊缝分层检测样品 放大50倍及以上检测 放大50倍及以上照相 压力电阻焊纵向样品 放大50倍及以上检测 放大50倍及以上照相 压力电阻焊横截面样品 放大100倍及以上检测 放大10倍及以上照相 19
GB/T11809一2021 录 附 规范性) 有效熔深s值的测量 熔化媒环炽缝有效熔深S值的测量见图E.1一图E.G
图E.1外表面凹陷 图E.2未焊透 图E.3气胀 20
GB/T11809?2021 ?E.4? ?E.5 ?E.6м? 21
GB/T11809一2021 附录 F 规范性 半补偿照相法最小透照厚度计算方法 F.1如图F.1所示,OH垂直平分AB并与之相交于H点,AB与环焊缝和端塞的交界面圆相交于c,D 两点.oH为角coD的角平分线,角cOD等于需转动的角度0,补偿块孔的半径R等于oA.环焊缝在 熔深方向上与端塞的交界面所形成的圆的半径r等于Oc,图中所示的补偿块厚度AB就是最小透照厚 度w 标引序号说明: 补偿块; -环焊缝; 燃料棒端塞
图F.1最小透照厚度示意图 F:.2根据图F.1,依据燃料棒每次转动的角度,燃料棒焊缝内圆半径、补偿块孔半径之间的关系计算最 小透照厚度,最小透照厚度计算公式(F.1). W 一2x、R=-( F.1) .( min 式中 补偿块孔半径oA,单位为毫米(mm).; R 环焊缝在熔深方向上与端塞的交界面所形成的圆的半径oc.单位为毫米(mm). 燃料棒旋转角度coD,单位为度("); 最小透照厚度AB,单位为毫米(mm)
V 22
GB/11809一2021 附 录 G 资料性 透照布置 透照布置见图G.1
像质计与底片标识一般分列补偿块两边,射线源焦点中心正对被检工件的 中心
标引序号说明 -X射线机焦点; -x射线; -补偿块; X射线胶片暗盒; 背板, -底片标识; 像质计 燃料棒
图G.1透照布置" 23
GB/T11809一2021 附 录 资料性 燃料棒焊缝×射线照相检验补偿方法 H.1全补偿照相法 H.1.1全补偿照相法是指在采用厚度补偿法时,将被检工件较薄的部位人为地增加厚度使其与工件最 厚处的透照厚度一致,达到整个工件基本一致能在同一曝光条件下进行检测的方法
H.1.2全补偿法透照示意图见图H.1
D口oQ 标引序号说明 燃料棒端塞; -环焊缝; 补偿块; 胶片; 被检部位直径 图H.1全补偿照相法示意图 H.2半补偿照相法 H.2.1半补偿照相法是指在采用厚度补偿法时,为了减少透照厚度,采用对环焊缝的中部区域进行补 偿的环焊缝弧段补偿方法
半补偿照相法通过燃料棒透照中转动一定角度,使焊缝的任意部分均进人 中部有利检测区域,保证焊缝中缺陷都能被检出
H.2.2半补偿照相法示意图见图H.2
标引序号说明: 燃料棒端塞; 2 环焊缝; 3 补偿块; 胶片; D 被检部位直径 图H.2半补偿照相法示意图 24
压水堆燃料棒焊缝检验方法金相检验和X射线照相检验GB/T11809-2021
一、引言
在核电站中,压水堆是一种常见的核反应堆类型。压水堆燃料棒作为核反应堆的重要组成部分之一,其质量直接关系到核电站的安全运行。因此,对压水堆燃料棒进行严格的检验非常必要。
二、压水堆燃料棒焊缝检验方法
焊缝是压水堆燃料棒中最容易产生缺陷的地方。目前常用的两种焊缝检验方法为金相检验和X射线照相检验。
1. 金相检验
金相检验是一种常用的金属组织分析方法,适用于焊缝的质量评定。具体流程如下:
- 制备样品:将焊接部位进行去毛刺、打磨和抛光处理,制成金相试样。
- 腐蚀显微镜观察:在腐蚀液中浸泡一段时间,然后进行显微镜观察。通过观察试样表面的组织结构来评价焊缝的质量。
- 图像分析:利用数字图像处理技术对观察到的图像进行处理和分析,得出焊缝的质量评价结果。
2. X射线照相检验
X射线照相检验可以检测焊缝内部的缺陷情况,是一种非破坏性检验方法。具体流程如下:
- 准备样品:将待检测的焊接部位置于X射线照相机的束流中。
- 照相:使用X射线照相机对焊缝进行拍摄。
- 图像分析:通过对X射线照片进行分析,检测焊缝内部的缺陷情况。
三、GB/T11809-2021标准介绍
GB/T11809-2021是我国制定的针对压水堆燃料棒焊缝检验的标准。该标准规定了金相检验和X射线照相检验的具体要求、试样制备方法、评价标准和报告书格式等内容,为压水堆燃料棒焊缝的检验提供了科学的依据。
四、总结
压水堆燃料棒焊缝的质量对核电站的安全运行至关重要。金相检验和X射线照相检验是目前常用的两种焊缝检验方法,二者结合可以对焊缝进行全面的评价。GB/T11809-2021标准为压水堆燃料棒焊缝的检验提供了详细的规范和指导,有助于保障核电站的安全运行。