GB/T38719-2020
金属材料管测定双轴应力-应变曲线的液压胀形试验方法
Metallicmaterials—Tube—Determinationofbiaxialstress-straincurveoftubebyhydro-bulgingtest
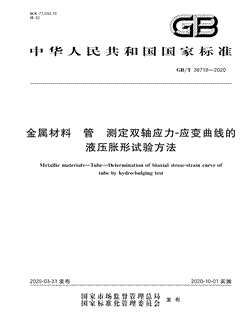
- 中国标准分类号(CCS)H22
- 国际标准分类号(ICS)77.040.10
- 实施日期2020-10-01
- 文件格式PDF
- 文本页数16页
- 文件大小2.04M
以图片形式预览金属材料管测定双轴应力-应变曲线的液压胀形试验方法
金属材料管测定双轴应力-应变曲线的液压胀形试验方法
国家标准 GB/T38719一2020 金属材料 管 测定双轴应力-应变曲线的 液压胀形试验方法 Metallicmmaterials一IubeDeterminationofbiaxialstress-straincurveof tubeyhydro-bulging test 2020-03-31发布 2020-10-01实施 国家市场监督管理总局 发布 国家标涯花管理委员会国家标准
GB/38719一2020 目 次 前言 引言 范围 2 规范性引用文件 术语和定义 符号及说明 原理 设备 试样 8 试验程序 曲率半径、应变和应力确定方法 10结果处理 1 试验报告 附录A规范性附录 试验设备 附录B(规范性附录散斑喷涂方法 双向应力状态等效应力-应变曲线的确定方法 附录C资料性附录 参考文献 12
GB/38719一2020 前 言 本标准按照GB/T1.1一2009给出的规则起草
本标准由钢铁工业协会提出
本标准由全国钢标准化技术委员会(SAC/Tc183)归口
本标准起草单位:哈尔滨工业大学,大连理工大学、江苏界达特异新材料股份有限公司冶金工业信 息标准研究院、东莞材料基因高等理工研究院、深圳万测试验设备有限公司、鞍钢股份有限公司、宝山钢 铁股份有限公司
本标准主要起草人何祝斌、苑世剑、王炜、李荣锋、董莉、林艳丽,凡晓波、黄星、吕丹、方健、侯慧宁、 张坤、胡馨予,朱海辉
GB/T38719一2020 引 言 本标准是应用管胀形试验测定金属管在双向应力状态无摩擦影响条件下的双轴应力-应变曲线的 方法
和单向拉伸试验相比,本标准所提供的试验方法可以获得更大的应变量及接近管状零件实际成 形时的应力状态
本标准是金属管胀形试样的轴向和环向曲率半径、应变、应力的测量方法和确定 方法
IN
GB/38719一2020 金属材料 管 测定双轴应力-应变曲线的 液压胀形试验方法 范围 本标准规定了金属材料管双轴应力-应变曲线液压胀形试验的术语和定义、符号及说明,试验原理、 设备、试样试验程序、双轴应力-应变曲线的计算和试验报告
本标准适用于壁厚不小于0.5mm且径厚比(外径与壁厚比)大于20的圆形截面薄壁金属管(包括 无缝管和焊管. 规范性引用文件 下列文件对于本文件的应用是必不可少的
凡是注日期的引用文件,仅注日期的版本适用于本文 件
凡是不注日期的引用文件,其最新版本(包括所有的修改单)适用于本文件
GB/T228.1金属材料拉伸试验第1部分;室温试验方法 GB/T15825.2金属薄板成形性能与试验方法第2部分;通用试验规程 术语和定义 下列术语和定义适用于本文件
3.1 DIC测量系统digitalimagecorelationmeasurementsystem 采用数字图像相关方法(DIC,digitalimagecorrelation),跟踪物体变形的散斑图像,计算出物体表 面全场的三维坐标,位移和应变的测量系统
3.2 散斑 pecke 试样表面随机分布的斑点
3.3 胀形区中间点intermediatepontofthebulgimg2one 位于胀形区中间横截面上的壁厚最薄点
注,见图1a)中P点
3.4 等效应力equivalentstres 复杂应力状态折算成单轴应力状态的当量应力
3.5 等效应变equivalentstrain 复杂应变状态折算成单轴应力状态的当量应变
3.6 双轴应力-应变曲线biaxial streSS-straincurve 在双向应力状态下得到的等效应力-应变曲线
GB/T38719一2020 符号及说明 本文件使用的符号及说明见表1
表1符号及说明 符 说 单 号 位 明 受力分析微元体中性层环向弧长 ds mm dls 受力分析微元体中性层轴向弧长 mm d0 受力分析微元体环向圆心角 rad 受力分析微元体轴向圆心角 dw rad D 试样初始外径 mm kN 轴向推力 F 合模力 kN 胀形区最高点距离试样轴线的距离 mm 胀形破裂时胀形区最高点距岗试样轴线的跑岗 mm 试样长度 mm 胀形区长度 mm 夹持区长度 mm MPa 液体介质压力 R 试样初始外半径 mm R 模具圆角半径 mm 抗拉强度 Rm MPa AR 试样胀形区中间点径向位移(外表面 试验结束后试样胀形区中间点径向位移(外表面 mm ARemd S 试样原始外周长 mm S丽 胀形破裂时试样最大截面周长 mm 试样初始壁厚 mm 试验结束后试样胀形区中间点壁厚 mm 试样胀形区中间点实时壁厚 mm 胀形区中间点轴向应变 胀形区中间点环向应变 胀形区中间点厚向应变 等效应变 % 胀形过程中某一时刻试样的膨胀率 胀形破裂时的极限膨胀率 % 胀形区长度与试样初始外径的比值 胀形区中间点环向曲率半径 mm
GB/38719一2020 表1(续 号 符 说明 单 位 胀形区中间点轴向曲率半径 p mm 胀形区中间点轴向应力 MPa 胀形区中间点环向应力 MPa C6 胀形区中间点厚向应力 MPa 等效应力 MP 6 试样与模具圆角接触部分圆弧所对应的圆心角 o 塞头的锥角 原理 将试样两端密封且轴向固定利用液体介质对试样施加内压力进行胀形,测量胀形过程中的液体压 力、位移、壁厚、应变等数据,分析获得试样在内压作用条件下变形时的等效应力、等效应变并绘制应力 应变曲线
试样应力分量可由液体压力、胀形区中间点P点的厚度、P点的轴向与环向曲率半径计算
计算所得P点的应力分量和测量所得P点的应变分量用于确定试样双轴应力-应变曲线,如图1所示
CCD-2 cD口g 受力分析示意图 应力分析示意图 b 说明 观察孔 管试样; 右塞头; -液体介质; 下模 左塞头; 上模; 玻璃板; CCD镜头 轴向 10 11 径向
图1管状试样液压胀形试验原理
GB/T38719一2020 6 设备 液压胀形试验所用设备应符合附录A的规定
试样 -段圆形截面的管材 7.1试样为- 7.2试样长度由式(1)确定,见图1a)
!=2L
十L
十5 式中 L
=(1.03.0)D.,推荐L
=1.5D
7.3试样端部应去除毛刺、打磨光滑,不应存在初始裂纹或较深、较尖锐的划痕,并且制样时保证试样 表面没有损伤(划痕、裂纹等缺陷. 7.4试样外表面应清理干净以喷涂散斑,具体喷涂方法及注意事项见附录B. 7.5制样过程中应防止试样产生变形
8 试验程序 8.1试验时应记录试验温度,试验一般在室温10C一35C下进行
8.2测量试样的初始壁厚、初始外径,沿环向等间隔测量出8个点,测量工具的分辨力不低 于0.01mm
8.3对试验所用模具、试验装置进行必要的清洗、检查,检查压力控制系统能否正常运行和压力管路是 否存在漏液
8.4试验前,空载条件下检查设备是否能够正常运行并检查塞头和模具密封段是否配合良好
8.5将准备好的试样放人模具中,合模后利用塞头进行扩口密封
8.6根据8.2测量的壁厚分布确定最薄点所在区域并做标记,以便采用DIC测量系统分析数据时找到 胀形区中间点
8.7向试样内部预加注液体(乳化液或液压油,排除试样内部的气体,然后增加塞头推力以实现管端 密封
8.8利用压力传感器测量试验过程中的液体压力
8.9利用DIC测量系统,与8.8同步测量试验过程中试样表面散斑图像
8.10按同一时间刻度,记录并保存试样内压力数据和DC测量系统所测量的变形数据
推荐每分钟 至少记录0组数据
为了保证足够的数据量,胀形测试过程中应至少拍摄100张图像
8.11按照一定的增压速率(推荐0.05MPa/s~0.1MPa/s)加载直至试样破裂,结束试验,记录胀破压 力值,保存试验数据
8.12为保证获得至少三个有效的试验结果,应准备足够多的试样
9 曲率半径、应变和应力确定方法 g.1曲率半径(p、Pn 需要求解的曲率半径为胀形区中间点的轴向和环向曲率半径
试样胀形时中间点附近区域外表面 轴向的轮廓为椭圆形,环向的轮廓为圆形
以胀形区中间点为中心在DIC测量范围中选择一个局部矩
GB/38719一2020 形区域进行分析,如图2中所示
所选区域的长度建议取值为=(0.2~0.5)D,,宽度,建议取值 为4=(0.20.4)L
,也可以根据实际视窗大小做调整
在所选区域内的轴向方向上均匀选取若干个 点(推荐至少选取5个点,点与点之间距离应大于2mm),提取所选取点的坐标信息,根据椭圆方程采 用最小二乘法拟合可确定胀形区中间点的轴向曲率半径;在所选区域内的环向方向上均匀选取若干个 点(推荐至少选取5个点,点与点之间距离应大于2mm),提取所选取点的坐标信息,根据圆的方程采 用最小二乘法拟合可确定胀形区中间点的环向曲率半径
必要时,也可以协商采用其他拟合方法或计 算方法确定曲率半径
说明 轴向 -环向; -径向
图2选择分析区域用于计算轴向和环向曲率半径 9.2应变(s. 、Ee 胀形区中间点的轴向和环向应变可以由DC测量系统直接输出,得到轴向和环向应变(e.,e),根 据体积不变原理按式(2)计算得到胀形区中间点的厚向应变(e,) e,=一E,一e
2 按式(3)计算胀形区中间点的壁厚(,)为 ,=texp(e=taexp(一e一E 'p一 9.3应力o.,o 轴向和环向的应力分量由式(4)确定
(pn一tp)9 2P一p72 (pp tP (2p一pp一tp dn tp/2) 2tp(p 0结果处理 10.1双轴应力-应变曲线计算 根据测量得到的数据(o.,o)和(e,e),确定双向应力状态下的等效应力-应变曲线
确定过程参 照附录C给出的方法进行
GB/T38719一2020 0.2加工硬化指数和强度系数 采用指数硬化模型对所得的等效应力-应变曲线进行拟合,从而确定加工硬化指数和强度系数, 参见附录C
10.3极限膨胀率 试样的极限膨胀率按式(5)计算 土2AR 2h
一D (D 一D hend emd) xI0%或 ×100% (5 7mnx5 D 式中:h和AR为试样破裂前一瞬间的数值
极限膨胀率也可以利用试样胀破后最大截面外周长与原始试样截面外周长按式(6)计算 Se 6 X100% 7 试验报告 11.1试验报告应包括以下主要内容: 本标准编号; a b 试样标识; e 试样的厚度、外径、长度、长径比,材料牌号和状态; d 拟合的双轴应力-应变曲线; e 试验的测量计算结果,包括;胀破压力、极限膨胀率,加工硬化指数和强度系数等; fD 试验日期,试验人员等
11.2试验报告还可包括下述内容 试验过程描述 a b 双轴应力-应变曲线的确定方法 c 试样准备记录; d 试验后样品整体外观照片" 试验中的其他说明
GB/38719一2020 附 录 A 规范性附录) 试验设备 A.1管状试样液压胀形试验设备示意图见图A.1
说明 -DIC测量系统 数据采集模块; -压力测量模块; -控制系统; -机身主体; -高压系统
图A.1试验设备示意图 A.2试验设备应具有向试样内部提供液体介质的装置和控制系统
所提供的液体压力力应满足 式(A.l),其中轴向抗拉强度R按照GB/T228.1测得 (A.1 A.3试验设备应提供足够大的轴向推力以满足试样端部的密封要求
所提供的轴向推力F应满 足式(A.2) > D
一 A.2 F>1.3力T A.4试验设备应提供足够大的合模力
所提供的合模力F,应满足式(A.3). 2F A.3 F>1.2(D,一2t)L力十 A.5试验设备应配备一个试样内部液体压力测量系统,也可以配备间接测量系统
从最大测量压力值 的20%起,测量误差不大于实际测量值的1%
A.6在试验过程中,采用DC测量方法获得试样外表面散斑点的X、Y、乙坐标
测试设备应保证在测 试过程中对试样外表面进行连续渊量
A.7模具和塞头应具有足够的刚度
塞头用于对试样端部密封并防止试样在胀形过程中产生轴向滑 动
塞头推力应足以使试样端部扩口密封,但不应使试样端部在扩口密封时出现裂纹
建议塞头的锥 角乡为30",也可以根据实际情况进行调整,达到密封效果即可
A.8设备应具有排气功能,以在试验前排除试样内部的气体,防止破裂时气体瞬间释放引起液体飞溅
A.9建议在镜头和灯具前放置一块玻璃板,以防止试验结束试样发生破裂时液体飞溅对设备造成损
GB/T38719一2020 坏,以保护DIC测量系统
放置的保护装置不应影响DC测量系统的测量精度
A.10上模具需要留观察孔,观察孔的设置应既便于DIC测量系统的测量又不影响模具的整体刚度
A.11模具圆角半径R
依据试样初始直径和壁厚选取
由Ra=D.t/20计算确定R
的所在范围,根 据表A.1确定R
的实际取值
A.12试验模具的结构、形状、尺寸应满足试验原理和试验条件
A.13试验设备的其他要求,可按GB/T15825.2的规定
表A.1R
的取值 单位为毫米 R计算值范围 R,建议取值 2.5 2.5 >2.5~5 5.0 >57.5 7.5 >7.5~10 10.0 >10 15.0
GB/38719一2020 附录 B 规范性附录 散斑喷涂方法 B.1概述 采用DIC测量系统测量试样胀形时的应变和几何形状时,需要在试样表面喷涂散斑,散斑的质量 决定测量系统能否进行准确测量以获得准确的数据,因此本附录对散斑喷涂做了相关规定
B.2喷涂随机散斑 B.2.1喷涂散斑的步骤如下: 第1步,首先将试样表面清理干净,确保不会出现影响散斑喷涂和粘附的油污等 -第2步,在待测试样上喷涂一层薄薄的哑光白色底漆以减小试样表面光泽的影响; 第3步,待上一步白色底漆将要晾干时喷涂黑色散斑,如图B.1所示为供参考的散斑图案
图B.1参考散斑图案 B.2.2对于喷涂用喷漆的品牌及规格不作规定,以喷涂效果和DC测量系统观测效果为准
推荐使用 哑光自喷漆进行喷涂
喷涂散斑后的试样应尽快进行试验测试,防止久置后试样变形时散斑脱落
注意;喷漆可能含有有毒溶剂,请遵守喷漆罐上的警告,不要吸入喷出的气体,一定要在良好的通风 条件下使用喷漆;避免喷漆接触皮肤和眼睛;喷出的漆雾一般具有可燃性,因此,应远离火源;在喷漆之 前检查试件表面是否适合喷漆
B.3散斑质量要求 试样表面的散斑质量会对测量产生影响因此,被测试样表面所喷涂的散斑应满足以下要求 为了获得高对比度的随机灰度分布图像,试样表面喷涂的散斑应具有随机特征,以保证参考图 aa 像中的像素区域和目标图像中对应的像素区域相匹配 b 所使用的油漆应该有足够的弹性和强度以免涂层开裂或脱落,散斑应能够随着试件一起变形 且不会过早损坏; 试样表面特征需要有良好的对比度,以保证图像匹配精度;
GB/T38719一2020 d 散斑表面宜没有面积较大的持续强光区域,例如大的斑点,图B.2分别显示了不合格的散斑和 合格的散斑
较好的高对比度散斑 不合格的低对比度散斑) 干扰点过大的高对比度散斑 图B.2散斑实例 0
GB/38719一2020 附录 C 资料性附录 双向应力状态等效应力-应变曲线的确定方法 要获得双向应力状态等效应力-应变曲线就需要先获得等效应力和等效应变
C.1 C.2由于试样为薄壁管,可忽略厚度方向的应力,应力状态可近似为平面应力状态
c.3假设试样材料为各向同性,满足Mses屈服准则,则等效应力等效应变为式(C.1): =vG;-a (C.1 b /E+E,十e C.4若试样材料为各向异性,满足Hil48屈服准则,则等效应力,等效应变为式(C.2) C.2 十r 2e
e0 式中 分别为试样沿轴向与环向的厚向异性系数
ro90 C.5若试样材料为各向异性,满足Hosford d屈服准则,则等效应力、等效应变为式(C.3) M la
一口. la"十,la"十rr 十r ** C.3 [rl十ro]M(aed.e
丽
T 十r
oM十r,ra" 式中: M-材料参数,对于体心立方M=6,对于面心立方M=8.
C.6若材料满足其他屈服准则,则按其他屈服准则计算等效应力、等效应变
C.7计算得到的等效应力、等效应变为散点,需要采用函数进行拟合得到应力-应变曲线,式(C.4)为一 种常用的拟合函数,也可以选用其他的函数利用最小二乘法进行拟合
o=Ke" C.4 式中 K 强度系数; 加工硬化指数 11
GB/T38719一2020 考文献 参 [[1]GB/T38684金属材料薄板和薄带双轴应力-应变曲线胀形试验光学测量方法 [[2]林艳丽.薄壁管液压胀形壁厚线性模型与力学性能测试方法[D].哈尔滨:哈尔滨工业大学博 士学位论文,2012. [3 HwangYM,LinYK.AnalysisandFiniteElementSimulation.oftheTubeBulgeHydro Techn6 Process[].JournalofMaterialsProces 2002,126(3):821-825. noloey forming ssing nOpenDieConsideringAniso HwangYM,LinYK.AnalysisofTabeBulgeForningin.an tropicEffectsoftheTubularMaterialJ].InternationalJournalofMachineToolsandManufacture 2006,46(15):1921-1928. 5 HwangYM.LinYK,AltanT.EvaluationofTubularMaterialsbyaHydraulieBulgeTest ].InternationalJournalofMachineToolsandManufacture,2007,47(2):343-351 HwangYM,LinYK.EvaluationofFlowStressesofTubularMaterialsConsideringAni andTehnoloey," sotropicEffectsbyHydraulicBulgeTestsJ].JournalofEngineeringMaterials 2007 129(3):414-421 HwangYM,wangCw.FlowStressEaluationofZineCopperandCarbonsteelTubesby Thar.AuisanpsJ].Jma.adMaerial HydraulicBulgeTestsConsidering ProcessingTechnology, 2009,209(9,1):4423-4428. HeZB,YuansJ,LinYL,etal.Analyticalmodelfortubehydro-bulgingtest,part [8 Models、forstresscomponentsandbulgingzoneprofile[].InternationalJournalofMechanical Sciences,201,87:297-306. HeZB,YuansJ,LinYL,etal.Analyticalmodelfortubehydro-bulgingtests,partI [9 Linearmodelforpolethicknessanditsapplication[].InternationalJournalofMechaniealSeiences. 2014,87:307-315. 12
金属材料管测定双轴应力-应变曲线的液压胀形试验方法GB/T38719-2020
随着工业技术的不断发展和进步,金属材料在各个领域得到了广泛的应用。而在实际应用中,对于金属材料的性能测试是非常关键的,其中测定双轴应力-应变曲线更是至关重要。
针对这个问题,国家标准化管理委员会于2020年发布了一项新的标准——《金属材料管测定双轴应力-应变曲线的液压胀形试验方法GB/T38719-2020》。该标准提出了一种新型的液压胀形试验方法,通过对金属材料进行液压胀形试验,可以快速、准确地测定金属材料在不同应力状态下的应变曲线。
试验原理
液压胀形试验是将金属管材放入特制的模具中,在内部加入高压液体,使管材产生径向膨胀形变,进而达到加载双轴应力的目的。同时,通过调整加压液体的压力、流量和胀形速度等参数,可以控制金属管材的应力状态,进而测定其应变曲线。
试验步骤
- 将待测金属管材经过打磨、清洗等处理后,装入液压胀形试验机的模具中。
- 在管材的两端加上密封头,并连接液压源。
- 通过调节液压源的参数(如压力、流量等),使金属管材开始沿径向胀形。
- 同时使用应变计等设备,实时测定金属管材的应变变化,记录下其应变曲线。
- 根据需要,可以对金属管材进行多次试验,以获得更加准确的应变曲线。
试验结果
通过以上试验方法,可以得到金属材料在不同应力状态下的应变曲线。这些数据可以作为评估金属材料性能、设计和制造金属构件等方面的重要参考依据,进而提高金属材料的工程应用效果。
总结
本文介绍了一种新型的液压胀形试验方法,该方法可用于测定金属材料管在双轴应力状态下的应变曲线,并为金属材料的工程应用提供重要的参考依据。通过对金属材料进行液压胀形试验,可以快速、准确地测定其应变曲线,为金属材料的工程应用提供了重要的参考依据。此外,该方法还具有试验操作简单、成本低廉等优点,因此得到了广泛的应用和推广。
总之,液压胀形试验是一种非常实用的金属材料性能测试方法,可为工程应用提供重要的参考依据。在今后的金属材料研究和开发中,液压胀形试验将继续发挥重要作用,为金属材料的进一步应用和推广提供有力支撑。