GB/T30579-2014
承压设备损伤模式识别
Damagemodesidentificationforpressureequipments
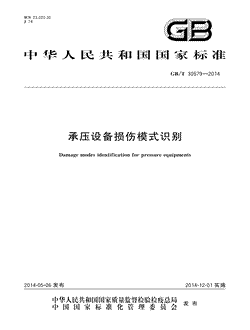
- 中国标准分类号(CCS)J74
- 国际标准分类号(ICS)23.020.30
- 实施日期2014-12-01
- 文件格式PDF
- 文本页数125页
- 文件大小2.66M
以图片形式预览承压设备损伤模式识别
承压设备损伤模式识别
国家标准 GB/T30579一2014 承压设备损伤模式识别 identifieatioforpresureequipments Damage m0deS 2014-05-06发布 2014-12-01实施 国家质量监督检监检疫总局 发布 国家标准花管理委员会国家标准
GB/T30579一2014 目 次 前言 引言 范围 规范性引用文件 般规定 腐蚀减薄 环境开裂 32 材质劣化 6 机械损伤 其他损伤 78 附录A(资料性附录)承压设备损伤模式索引 8 附录B(资料性附录)典型过程成套装置承压设备损伤分布图 92 附录c(资料性附录)常用金属材料牌号 115
GB/T30579一2014 前 言 本标准按照GB/T1.1一2009给出的规则起草
本标准第4章第8章参考APIRP571一2003《炼油设备中的失效机理第4章常见损伤机 所有工厂英文版)和APRP571一2003(炼油设备中的失效机理第5章炼油厂损伤机理》 理 英文版)编写并根据我国实际情况进行了内容调整和增加
本标准4.8“有机酸腐蚀”、4.25“甲铵腐 蚀”,5.3“硝酸盐应力腐蚀开裂”,5.9”氢氧酸致应力腐蚀开裂”,5.11“高温水应力腐蚀开裂”,6.1“晶粒长 大”、6.11“辐照脆化”、6.15“敏化-晶间腐蚀”、7.4“接触疲劳”、7.5“机械磨损”、7.6“冲刷”、7.8“过载”和8 9“微动腐蚀”根据我国实际情况起草
本标准附录A根据我国实际情况起草
本标准附录B参考APIRP5712003《炼油设备中的失效机理第5章炼油厂损伤机理>英文 版)编写,其中图B.8一图B.15根据我国实际情况起草
本标准附录C根据我国实际情况起草
本标准由全国锅炉压力容器标准化技术委员会(SAC/Tc262)提出并归口
本标准起草单位;特种设备检测研究院、合肥通用机械研究院、北京航空航天大学、华东理工大 学,石油化工股份有限公司炼油事业部、江苏省特种设备安全监督检验研究院、石油化工股份 有限公司青岛安全工程研究院、中科合资(广东)炼化公司、石油股份有限公司克拉玛依石化分公 司、石油独山子石化公司研究院、石油化工股份有限公司洛阳分公司、国家压力容器与管道安 全工程技术研究中心、云南省特种设备安全检测研究中心,山东省特种设备检验研究院
本标准起草人;贾国栋、史进,艾志斌,张峥、轩福贞、王建军,陈学东、王辉、杜晨阳、缪春生、刘小辉、 王光、梁永智,赵立凡、叶国庆、汪逸安,李光海、姜海一,王笑梅、顾望平、陈涛,邵珊珊、赵宗祥、曹怀祥
GB/T30579一2014 引 言 我国目前对于承压设备损伤模式的分类尚未系统化,本标准旨在首次建立适用于在役承压设备损 伤模式的统一分类原则和框架
损伤与失效不同之处在于损伤是一个发生过程,失效是损伤积累到 定程度,承压设备强度、刚度或功能不能满足使用要求的状态,即出现损伤时不一定失效,发生失效前 定出现了损伤
对于损伤模式的识别,有助于在役设备的检测和评估,利于在设备发生失效前及时进行 修复或报废等处理
本标准中损伤模式按照腐蚀减薄、环境开裂、材质劣化机械损伤和其他损伤模式进行分类,其中在 一大类损伤模式下又细分为着干种损伤 每 分类原则按照承压设备和其服役环境相互作用下可能发生 的损伤,是一种以材料和环境相对应的分类方法
其中服役环境指承压设备所处的介质,温度、压力等 环境
本标准目前收录的损伤主要为在役承压设备在简单环境因素影响下发生的损伤
但是承压设备实 际的服役环境有时是比较复杂的,如实际介质中含有多种腐蚀性组分,并且造成的损伤也是多种损伤耦 合作用的结果,较为复杂的损伤将在今后的标准修订中引人
本标准为承压设备损伤模式识别的基础 性标准,按照本标准进行识别的过程中,还应对损伤现象及辅助的试验结果进行综合分析,必要时可采 取失效故障树分析法,排除法或模拟试验法等方法进一步分析判断
本标准中对于损伤发生的条件和其敏感性的判断以定性描述为主,在今后的标准修订中将逐步增 加相关数据,向定量判定方向发展
GB/T30579一2014 承压设备损伤模式识别 范围 本标准给出了承压设备主要损伤模式识别的损伤描述及损伤机理、损伤形态,受影响的材料、主要 影响因索.易发生的装置或设备、主要预防措随、检测或监渊方法.相关或伴随的其他损伤等
本标准适用于承压设备损伤模式识别
本标准不适用于承压设备密封失效,安全连锁装置失效、压力泄放装置失效
规范性引用文件 下列文件对于本文件的应用是必不可少的
凡是注日期的引用文件,仅注日期的版本适用于本文 件
凡是不注日期的引用文件,其最新版本(包括所有的修改单)适用于本文件
GB150.2 压力容器第2部分材料 锅炉和压力容器用钢板 GB713 GB3531低温压力容器用低合金钢钢板 钛及钛合金牌号和化学成分 GB/T3620.l2007 高压锅炉用无缝钢管 GB5310 石油裂化用无缝钥管 GB9948 GB13296锅炉,热交换器用不锈钢无缝钢管 GB/T14976流体输送用不锈钢无缝钢管 GB19189压力容器用调质高强度钢板 GB/T21833奥氏体-铁素体型双相不锈钢无缝钢管 GB24511承压设备用不锈钢钢板及钢带 GB/T26610.1一2011承压设备系统基于风险的检验实施导则第1部分:基本要求和实施程序 JB/T4734铝制焊接容器 JB/T4745钛制焊接容器 JB/T4755一2006铜制压力容器 JB/T4756镍及镍合金制压力容器 NB/T47008承压设备用碳素钢和合金钢锻件 NB/T47009低温承压设备用低合金钢锻件 ASMElPartAASME锅炉和压力容器规范第卷材料A篇铁基材料(ASMEboiler and pressurevesselcode MaterialsPartAFerrousmaterialspecifications) AME I PartBASME锅炉和压力容器规范第卷材料B篇非铁基材料(ASMEboiler vesselcode MaterialsPartB:Nonferrousmmaterialspecificeations andpressure AsSTMUNSASTM统一编号系统(AsTMunified lnumberingsystem -般规定 3.1 本标准的损伤模式分为:腐蚀减薄、环境开裂、材质劣化、机械损伤,无法归人上述损伤模式或非单
GB/T30579一2014 -损伤的归人其他损伤 损伤是指承压设备在外部机械力、介质环境、热作用等单独或共同作用下,造成的材料性能下 a 降、结构不连续或承载能力下降 b 腐蚀减薄指在腐蚀性介质作用下金属发生损失造成的壁厚减薄
c)环境开裂指在腐蚀性介质作用下材料发生的开裂
d)材质劣化指由于服役环境作用下材料微观组织或力学性能发生了明显退化
机械损伤指材料在机械载荷或垫载荷作用下,发生的承载能力下降
3.2损伤个例之间存在差异性,有时不能完全与本标准中描述的典型损伤相吻合,当存在多种损伤或 损伤耦合时,需要更复杂的识别方法
本标准从损伤描述及损伤机理、损伤形态,受影响的材料,主要影响因素、易发生的装置和设备、主 3.3 、相关或伴随的其他损伤共8个方面进行了描述
要预防措施、检测或监测方法、 从事损伤模式识别的人员或团队应具有材料学、,腐蚀与防护化工工艺、力学、无损检测等相关基 3.4 础知识,具有承压设备(如容器、管道,锅炉,储罐等)设计,制造、安装、检验等相关专业知识,以及丰富在 役承压设备运行,检修的经验,能按照本标准提供的典型情况,结合损伤案例的个体特征,进行合理的分 析和判断
腐蚀减薄 盐酸腐蚀 4.1 4.1.1损伤描述及损伤机理 金属与盐酸接触时发生的全面或局部腐蚀 Fe十2HCI-FeCl,十H 注本标准中所有化学式中的金属一般以Fe作为代表给出
4.1.2损伤形态 碳钢和低合金钢盐酸腐蚀一般表现为均匀腐蚀,存在介质局部浓缩或露点腐蚀时也可表现为局部 腐蚀或沉积物下腐蚀
300系列不锈钢和400系列不锈钢发生盐酸腐蚀时可表现为点状腐蚀,形成直 径为毫米级的蚀坑,甚至可发展为穿透性蚀孔
4.1.3受影响的材料 碳钢、低合金钢、300系列不锈钢、400系列不锈钢 4.1.4主要影响因素 盐酸浓度;随盐酸浓度升高,腐蚀速率增大;在热交换器和管道中的氯化铵盐或盐酸胺盐沉积 a 物易从工艺物流或注人的洗涤水中吸收水分,在沉积物下可形成局部的氨化氢水溶液.水溶液 的pH值低于4.5时对碳钢和低合金钢的腐蚀性较强 温度;随温度升高,腐蚀速率增大 合金成分300系列不锈钢和400系列不锈钢耐盐酸腐蚀能力差,钛(含钛合金)和镍(含镍合 金)耐盐酸腐蚀,尤其在温度不高的稀盐酸中耐腐蚀性能强; 催化或钝化剂;氧化剂氧气、铁离子和铜离子)存在时,会加速镍基合金的腐蚀;在氧化性介 质环境中,钛具有优良的耐盐酸腐蚀能力
GB/T30579一2014 4.1.5易发生的装置或设备 炼油厂中的盐酸腐蚀多与露点腐蚀有关,即在燕憎塔,分僧塔或汽提塔塔顶工艺物料中,含水和 氯化氢的气相发生冷凝,最初析出的液滴酸性很强(pH值低),腐蚀速率很高
易发生的装置或设 备有: a)常减压装置 常压塔塔顶系统中,塔顶油气冷却形成含盐酸的冷凝液,pH值较低,可对管道和热交换 1 器包括壳体、管束和管箱)造成快速腐蚀; 2)减压塔顶真空喷射器和冷凝设备会发生盐酸腐蚀
b)加氢装置 1 原料泾或循环氢中的有机氯化物进人装置内,反应生成盐酸; 2 当氨和氯化氢同时存在时,装置中许多部位,如热进料/反应产物热交换器的反应产物侧 等,均可形成氧化铵盐,这些氧化铵盐也可能在反应产物系统的水相中聚集浓缩,详见 4.19; 氯化氨也可能随着工艺流穿过分僧单元,在注水点及其下游发生严重的酸露点腐蚀
3 催化重整装置
催化剂中被置换出来的氯化物会反应形成盐酸,流向反应产物系统、再生系统、稳定塔、脱 丁烧塔和进料/预加热热交换器 含氯化氢的蒸汽流经气分装置分僧工段,引发混合点腐蚀或酸露点腐蚀
2) 聚丙烯(聚乙烯)装置;催化剂中含有氯化物,如三氯化钛,在聚丙烯的合成工艺中,与水蒸气 或水接触的设备和管线
4.1.6主要预防措施 常减压装置;控制初塔进料中的氯化物含量,使塔顶回流罐液体中的氯化物含量不超过 20x10";改善材质适应性,可将碳钢升级为镍基合金或钛;注水稀释急冷塔顶工艺物料,降低 盐酸浓度;按pH值情况在脱盐装置下游注人适量苛性碱,控制碱液温度、浓度和注人量,避免 进料预热系统的碱应力腐蚀开裂和积垢;将缓蚀剂(氨、中和胺和成膜胺等)注人常压塔塔顶操 作温度在露点以上的管线; 加氢装置:降低上游装置中氯化物盐、盐酸胺盐的夹带量;降低氢气中盐酸夹带量,可安装专 用洗涤器或保护床;易发生盐酸腐蚀的部位采用耐蚀镍基合金 催化重整装置;采用与上述加氢装置相同的措施;降低进料中的水和/或含氧物质,减少催化剂 中氯化物脱除量;采用加装特殊吸附剂的脱氯设备
4.1.7检测或监测方法 对于均匀腐蚀,检测方法一般为目视检测和腐蚀部位壁厚测定;对于点蚀坑或蚀孔,检测方法 -般为目视检测; b腐蚀发生在内壁而只能从外部检测时,可用自动超声波扫查、导波检测或射线成像检测查找 减薄部位,并对减薄部位进行壁厚测定 c) 介质的pH值,氯化物含量的测定和监控; 设置腐蚀探针或腐蚀挂片监控实时腐蚀速率
dD
GB/T30579一2014 4.1.8相关或伴随的其他损伤 氯化铵腐蚀、氧化物应力腐蚀开裂 4.2硫酸腐蚀 4.2.1损伤描述及损伤机理 金属与硫酸接触时发生的腐蚀 Fe十Hso,(稀)-Feso十H 4.2.2损伤形态 稀硫酸引起的金属腐蚀多为均匀腐蚀或点蚀,若腐蚀速率高且流速快,不会形成锈皮
碳钢焊 缝热影响区会发生快速腐蚀,在媒接接头部位形成沟槽 储罐及铁路罐车等低流速区或滞留区会形成氢槽
b 硫酸能腐蚀焊缝的夹杂
c 4.2.3受影响的材料 按耐腐蚀性从弱到强排列,碳钢、316L不锈钢、,3904L不锈钢、合金20,高硅铸铁、高镍铸铁、合金 B2和合金C276
4.2.4主要影响因素 酸浓度:对于碳钢,硫酸浓度低于70%质量分数)时,腐蚀速率随浓度增高而减小;浓度在 a 70%~85%范围区间时,腐蚀速率随浓度增高而增大;浓度在85%98%范围区间时,腐蚀速 率随浓度增高而减小;浓度在98%~100%范围区间时,腐蚀速率随浓度增高而增大;浓度 >100%时,腐蚀速率随浓度增高而减小 流速:流速超过0.6m/s时,碳钢腐蚀速率较大; b 温度;硫酸浓度一定时,随温度升高,腐蚀速率增大;浓硫酸与水混合时产生热量,混合点温度 升高导致腐蚀速率增大; 合金成分;碳钢,3161不锈俐,.904L不锈俐、合金20,高硅铸铁,高镍铸铁,合金B2和合金 C276(按耐腐蚀性从弱到强排列); 腐蚀杂质;存在氧化剂时腐蚀速率增大
4.2.5易发生的装置或设备 a)废水处理装置可能发生硫酸腐蚀; 硫酸婉基化系统易受硫酸腐蚀,如反应器流出物管线、再沸器、脱异丁婉塔塔顶系统和苛性碱 b 处理工段; 硫酸通常在分塔和再沸器的底部蓄积,使该部位硫酸变浓,腐蚀性较强
4.2.6主要预防措施 使用合金20,904L不锈钢,合金c-276等材料时,可在表面形成一层保护性硫酸铁膜,抵抗稀 a 硫酸腐蚀; 根据硫酸的实际浓度、流速和温度等选择对应等级的材质 b 注人适量苛性碱中和酸值
c
GB/T30579一2014 4.2.7 检测或监测方法 a 检测方法一般为目视检测和腐蚀部位壁厚测定,重点应关注高温和湍流部位; b 若腐蚀发生在内壁而只能从外部检测时,可用自动超声波扫查、导波检测或射线成像查找减 薄部位,并对减薄部位进行壁厚测定; 设置腐蚀探针或腐蚀挂片,监控实时腐蚀速率 4.2.8相关或伴随的其他损伤 无 4.3氢氟酸腐蚀 4.3.1损伤描述及损伤机理 金属与氢氟酸接触时发生的腐蚀 Fe十2HF-FeF十H 4.3.2损伤形态 碳钢腐蚀表现为局部区域减薄,可能会形成明显的氟化亚铁垢皮; a b)合金400发生腐蚀时为均匀腐蚀减薄,但不会产生明显的氟化亚铁垢皮 腐蚀发生时也可能伴随氢脆,氢鼓包和/或氢致开裂以及应力导向氢致开裂,如未消除应力的 合金400在接触含氧的氟化氢潮湿蒸汽时,容易发生应力腐蚀开裂,详见5.8
4.3.3受影响的材料 碳钢,铜镍合金、合金400,合金C276; a b 低合金钢,300系列不锈钢和400系列不锈钢对氢氟酸腐蚀和/或开裂敏感,一般不能用于氢 氟酸使用环境
4.3.4主要影响因素 流速;碳钢在无水的浓氢氟酸中形成一层保护性的氟化物垢皮,在高流速或强紊流作用下垢皮 被破坏,使腐蚀速率增大
b)浓度;水的存在会破坏氟化物垢皮的稳定性,并将其转变为非保护性垢皮
根据实验室测定 的结果,低流速或滞流状态下,温度在21C一38C范围内,氢氟酸浓度不超过35%时,碳钢的 腐蚀速率随氢氟酸浓度增高而增大;浓度超过35%后,碳钢的腐蚀速率随氢氟酸浓度增高而 减小
温度;根据实验室在滞流状态的无水氢氟酸中100h内测定的数据,在60C一188温度范围 内碳钢在液态无水氢氟酸中的腐蚀速率随温度升高而增大,在188C一200温度范围内碳 钢在液态无水气氟酸中的腐蚀速率随温度升高而减小,温度超过200C时碳钢在气态无水氢 叙酸中的腐蚀速率随温度升高而增大 碳钢中残留的铜,镍铬元素可加迷氢氟酸腐蚀 d 介质受到氧污染时会增大碳钢的腐蚀速率,也会加速合金400的腐蚀和应力腐蚀开裂 4.3.5易发生的装置或设备 氢氟酸烧基化装置:临氢氟酸环境的设备和管道,以及含酸火炬气管道
常见氢氟酸婉基化装
GB/T30579一2014 置运行时酸中的含水量为1%3%,运行温度一般低于66C,在此条件下碳钢可广泛应用于 运行中配合要求不很严密的设备,如泵、阀门、仪器等,故除氢氟酸再蒸僧塔、再生塔和除酸用 中和容器通常部分或全部采用合金400外,大多数设备都可由碳钢建造
高腐蚀速率的常见部位:操作温度高于66C的管道和设备,包括泄压阀人口、小口径放气口 和排气口的盲管段,以及位于异构体汽提塔、脱丙烧塔、氢氟酸汽提塔、丙烧汽提塔塔顶部位的 管道和热交换器、酸汽化器等
4.3.6主要预防措施 监测操作温度超过66C的碳钢管道和设备的壁厚
如已发生严重减薄、不能满足使用要求, 可提高材料等级,采用合金400
整体或复合层采用合金400材料,还可避免氢鼓包、氢致开 裂或应力导向氢致开裂的问题,详见5.8
合金400也无法满足要求的部件应采用c276
b控制进料中水,氧和其他腐蚀杂质,并严格控制循环酸的含水量
控制碳钢中残存的铜、镍、铬三种元素总含量不超过0.20%(质量分数)
4.3.7检测或监测方法 检测方法一般为目视检测和腐蚀部位壁厚测定 a b)若腐蚀发生在内壁而只能从外部检测时,可用自动超声波扫查、导波检测或射线成像查找减 薄部位,并对减薄部位进行壁厚测定
4.3.8相关或伴随的其他损伤 氢氟酸致气应力开裂
4.4磷酸腐蚀 4.4.1损伤描述及损伤机理 金属与磷酸接触时发生的腐蚀 3Fe十2H,PO-一Fe,(PO)十3H 4.4.2损伤形态 碳钢发生磷酸腐蚀时多呈局部腐蚀或点蚀
4.4.3受影响的材料 按耐腐蚀能力从弱到强排列为;碳钢、304L不锈钢、316L不锈钢和合金20. 4.4.4主要影响因素 a)酸浓度:若不存在自由水,固体磷酸(如含磷酸催化剂)不具有腐蚀性; 温度;随着温度升高,腐蚀速率增大; b e)氯化物杂质可促进磷酸腐蚀 大部分腐蚀发生于停机时的水洗作业中
d 4.4.5易发生的装置或设备 a 聚合装置;水与催化剂混合的管道和设备 b)易发于介质流动低速区或流动死角,例如管道集合管、盲管、釜式再沸器底部和热交换器局部
GB/30579一2014 熔透焊缝等,在这些部位有足够的滞留时间使酸滴沉降或聚集 4.4.6主要预防措施 选材:在水分无法完全脱除的部位,选择耐腐蚀能力强的材质; a b温度;当温度不超过49,304L不锈钢在浓度为100%质量分数)的磷酸中亦具有很好的耐 腐蚀性能;温度在49C107C范围内时宜用316L不锈钢; 浓度;在沸点温度下,当磷酸浓度不超过85%质量分数)时,可选用316L不锈钢或合金20
4.4.7检测或监测方法 a)检测方法一般为目视检测和腐蚀部位壁厚测定; b 若腐蚀发生在内壁而只能从外部检测时,可用自动超声波扫查、导波检测或射线成像查找减 薄部位,并对减薄部位进行壁厚测定; c)取样分析塔顶系统首个贮罐的水溶液中铁含量 在塔顶冷凝器和再沸器的第一台排水器中设置电阻式腐蚀探针或腐蚀挂片,进行在线腐蚀速 d 率监测
4.4.8相关或伴随的其他损伤 无
4.5二氧化碳腐蚀 4.5.1损伤描述及损伤机理 金属在潮湿的二氧化碳环境(碳酸)中发生的腐蚀: H.O+CO十Fe-一FeCO十H 4.5.2损伤形态 a)形成液相的部位会发生腐蚀,二氧化碳从气相中冷凝出来的部位容易发生腐蚀; 腐蚀区域壁厚减薄,可能形成蚀坑或蚀孔 b e)在紊流区,碳钢发生腐蚀时可能形成较深的点蚀坑和沟槽 腐蚀一般发生在紊流和液体冲击区域,有时也会发生在管道焊缝根部
d 4.5.3受影响的材料 碳钢、低合金钢
4.5.4主要影响因素 a)pH值:二氧化碳分压增高,pH值下降,腐蚀性增强; 温度;温度未达到溶液中二氧化碳气体逸出温度前,随温度升高,腐蚀速率增大 b e)如果铬含量未达到12%以上,增加钢中铬含量不能明显提高耐腐蚀能力
4.5.5易发生的装置或设备 所有锅炉给水和蒸汽冷凝系统 a 制氢装置;在变换器排出气系统中,当排出气流温度降至露点(大约149C)以下时,腐蚀比较 b mm/年; 常见,根据已知检测结果,腐蚀速率可高达25.4"
GB/T30579一2014 e二氧化碳脱除装置:再生器顶部系统; d) 空分装置:;压缩空气经冷却后的低点凝液部位; 油/气田集输的油气管道
4.5.6主要预防措施 a缓蚀剂:在燕汽冷凝水系统中加人缓蚀剂 b pH值;液相的pH值提高到6.0以上可有效降低蒸汽冷凝水系统的腐蚀速率 选材:300系列不锈钢可有效抵抗二氧化碳腐蚀,能用于产生二氧化碳和脱除二氧化碳设备, c 同时应注意避免300系列不锈钢在现场焊接施工可能造成的敏化
400系列不锈钢和双相不 锈钢也具有良好的耐腐蚀性
4.5.7检测或监测方法 检测方法一般为目视检测和腐蚀部位壁厚测定,焊缝的腐蚀则应通过目视检测和焊缝尺进行 检测 b)若腐蚀发生在内壁而只能从外部检测时,可用自动超声波扫查、导波检测或射线成像查找减 薄部位,并对减薄部位进行壁厚测定; 腐蚀发生时可能沿着管道底部表面(如果存在分离的水相时、管道顶部表面(预计湿气系统中 存在凝结时),以及弯头和三通的紊流区; 水质监测分析(pH、,Fe等),以确定操作工况的变化
dD 4.5.8相关或伴随的其他损伤 锅炉怜凝水腐蚀、破酸盐应力腐蚀开裂. 4.6环烧酸腐烛 4.6.1损伤描述及损伤机理 在177C一427C温度范围内,环婉酸对金属材料的腐蚀: 2Rc0OH+Fe-Fe(RcOO)十H 4.6.2损伤形态 a)高流速区可形成局部腐蚀,如孔蚀,带锐缘的沟槽 b低流速凝结区,碳钢低合金钢和铁素体不锈钢的腐蚀表现为均匀腐蚀或点蚀
4.6.3受影响的材料 碳钢、低合金钢、300系列不锈钢、400系列不锈钢和镍基合金
按耐环烧酸腐蚀能力由弱到强大致 顺序排列;碳钢、1.25Cr-0.5Mo,2.25Cr0.5Mo,5Cr0.5Mo,12Cr、9Cr-1Mo,304L不锈钢,321不锈钢、 347不锈钢、316不锈钢、317不锈钢,6%的钼合金、合金625,合金276 4.6.4主要影响因素 酸值;腐蚀速率随姬相酸值增加而增大,酸值通常用中和值或总酸值表征;原油中不同环烧酸 a 其腐蚀性不同,腐蚀速率与总酸值的关系不能完全对应,由实际介质成分决定 当炝相介质的使用温度在218C一400C范围内,腐蚀较为常见,且随着温度升高,腐蚀 b 温度 速率增大
GB/30579一2014 硫含量;泾相中的硫可能与钢材反应生成硫化亚铁保护膜,从而减缓环炕酸的腐蚀; d)流速:随流速升高,腐蚀速率增大; e 相态;两相流(气相和液相,湍流区,蒸懈塔的气相露点部位腐蚀严重 材料;合金中钼元素可以提高耐蚀性,钼元素含量下限为2.5%(质量分数),具体钼元素含量可 f 根据原油及物料中的总酸值确定
4.6.5易发生的装置或设备 常减压装置加热炉炉管、常压和减压转油线、减底油管线、常压蜡油回路,减压重蜡油回路(有 时减压轻蜡油回路也会出现);一次加工原料为高酸原油的延迟焦化装置焦化轻蜡油回路和焦 化重蜡油回路中可能发生环烧酸腐蚀 管道高流速、湍流、流向改变的部位,如阀门、弯头、三通、减压器位置,以及泵内构件设备和 b 管道焊缝、热偶套管等流场受到扰动的部位; 常压塔、减压塔内构件在闪蒸段、填料和高酸物流凝结或高速液滴冲击的部位易发生腐蚀 c D 常减压装置的下游装置内注氢点之前热胫物料系统
4.6.6主要预防措施 掺炼;原设计不耐环婉酸腐蚀的装置或系统部件,原料油混合掺炼,降低酸值或适当提高硫 a 含量; b) 选材;使用钼元素含量高的合金来提高耐蚀性,严重腐蚀时宜采用317L不锈钢; 缓蚀剂;选用合适的缓蚀剂
c 4.6.7检测或监测方法 a 监测工艺条件;原油和侧线物流中的酸值监测,确定酸在不同僧分中的分布; b)测厚:采用目视检测十超声波测厚,检测壁厚变化; 射线检测,射线成像检测可有效检出局部腐蚀区城, C 探针或挂片;设置电阻腐蚀探针和腐蚀挂片; d 腐蚀产物监测;检测物流中的铁、镍元素含量来评估系统的腐蚀程度; 氢通量监测使用氢探针监测氢通量 f 流场分析,确定管道系统高流速或湍流部位
g 4.6.8相关或伴随的其他损伤 高温硫化物腐蚀(无氢气环境 4.7 苯酚腐蚀 4.7.1损伤描述及损伤机理 金属与苯酚(石碳酸)接触时发生的腐蚀
4.7.2损伤形态 a)碳钢发生苯酚腐蚀时可表现为均匀腐蚀或局部腐蚀; b存在流体冲刷时多引起局部腐蚀
4.7.3受影响的材料 按耐腐蚀性增强的顺序:碳钢、304L不锈钢、316L不锈钢和合金C276
GB/T30579一2014 4.7.4主要影响因素 温度:低于121C时腐蚀速率较小;碳钢、304L不锈钢在232以上的苯酚环境中腐蚀速率 a 较大; b 浓度;稀苯酚溶液(质量分数为5%~15%的苯酚溶液)对冷凝干燥器腐蚀性较强; 材质;按材料耐苯酚腐蚀性从弱到强为碳钢、硬度较低的奥氏体不锈钢(如304L、3161等 c 合金276; 流速;介质高流速可促进局部腐蚀
4.7.5易发生的装置或设备 a)润滑油装置中的苯酚提取设施; b) 苯酚丙酮装置的苯酚塔再沸器和废苯酚回收工段 e)双酚A装置的苯酚回收塔再沸器、苯酚提纯塔再沸器
4.7.6主要预防措施 a)流速;在苯酚回收工段应将苯酚介质流速控制在9m/s以下 温度;保持苯酚回收塔塔顶温度高于露点温度,至少应高出17C; b 选材:316L不锈钢可用于处理含酚水的干燥塔、苯酚闪蒸塔和各种热交换器壳体以及分离设 c 备的顶部;萃取炉中的管和联管箱应为316L不锈俐,对于316L不锈钢不能满足耐蚀要求的 场合,如介质流速较高时宜用合金C276
4.7.7检测或监测方法 检测方法一般为目视检测和腐蚀部位壁厚测定; a b)采用奥氏体不锈钢时,若腐蚀发生在内壁而只能从外部检测时,可用自动超声波扫查、导波检 测或射线成像查找减薄部位,并对减薄部位进行壁厚测定; 设置腐蚀探针或腐蚀挂片监控实时腐蚀速率
4.7.8相关或伴随的其他损伤 无 4.8有机酸腐蚀 4.8.1损伤描述及损伤机理 金属与低分子有机酸(如甲酸、乙酸、乙二酸等,不含本标准中单独列明的环婉酸等其他有机酸)接 触时发生的均匀腐蚀或局部腐蚀
以甲酸为例,腐蚀过程为 Fe十2HcOoH--Fe(HcOo)十H 4.8.2损伤形态 碳钢、低合金钢发生甲酸腐蚀时可表现为均匀腐蚀,介质局部浓缩或露点腐蚀时表现为局部腐蚀或 沉积物下腐蚀
4.8.3受影响的材料 碳钢、低合金钢
10
GB/T30579一2014 4.8.4主要影响因素 a 酸类型:甲酸和乙酸的腐蚀性最强,均可溶于姬中并在接触水分时被水萃取,形成局部高浓度 酸液; b 浓度或pH值;一般来说,随着酸浓度升高(即pH值降低),腐蚀速率增大,但浓度在50%质 量分数)左右的甲酸腐蚀性最强,浓度降低或浓度升高时腐蚀都会减缓; 温度;随温度升高,腐蚀速率增大; 合金成分;碳钢耐蚀性最差,其次为低合金钢,次之300系列不锈钢和400系列不锈俐,而钛相 D 钛合金、镍和镍合金均对有机酸具有较好的耐腐蚀能力
4.8.5易发生的装置或设备 炼油装置中的有机酸腐蚀一般由环婉酸分解或工艺添加剂加人的有机酸(如甲酸.乙酸,丙酸和丁 酸)引发,比如常加压装置燕馏塔的塔顶系统
对于某特定的有机酸来说.腐蚀一般多发生在直接输送该有机酸的物料系统.或输送可能生成该有 机酸的其他物料系统中
比如甲酸腐蚀易发生的装置或设备如下 a)甲醇装置:甲醇合成塔后含甲酸的物料系统, b) 二甲腿装置;甲醇原料系统,尤其是温度较高的部位; 其他输送或储存甲醇、甲醛或甲酸的设备及管道系统,温度越高的部位腐蚀越明显 c) 乙酸装置易发生的装置或设备如下 醋酸装置;醋酸合成系统、分离系统,尤其是温度较高的部位,以及醋酸储运系统 b)乙酸乙酯装置:反应系统和醋酸回收系统尤其是温度较高的部位 氯乙酸装置;反应系统和醋酸回收系统; 精对苯二甲酸装置:乙酸回收系统; d 其他输送或储存乙醉、乙醛或乙酸的设备及管道系统,温度越高的部位腐蚀越明显
e 二酸装置易发生的装置或设备如下 乙二醇装置;乙二醇储运系统; a 草酸装置;反应系统和草酸分离系统 b 其他输送或储存乙二醇、乙二酸的设备及管道系统
c 4.8.6主要预防措施 选材;采用含钼奥氏体不锈钢、镍基合金或钛,也可采用衬四氟乙烯的复合钢材,或者设置陶瓷 a 衬里等; b 加中和剂;炼油装置可添加中和剂来降低介质中有机酸含量,但中和剂添加需要适量,避免引 起其他损伤 工艺优化:输送醛、醇、耐等有机物的设备和管道应避免因系统密封问题混人空气,造成有机酸 浓度升高
4.8.7检测或监测方法 a 检测方法一般为目视检测和腐蚀部位壁厚测定; b若腐蚀发生在内壁而只能从外部检测时,可用自动超声波扫查、导波检测或射线成像查找减 薄部位,并对减薄部位进行壁厚测定; 介质的pH值测定和监控; 11
GB/T30579一2014 d)设置腐蚀探针或腐蚀挂片监控实时腐蚀速率
4.8.8相关或伴随的其他损伤 无
4.9高温氧化腐烛 4.9.1损伤描述及损伤机理 高温下金属与氧气发生反应生成金属氧化物的过程: 在高温下,氧气和金属反应生成氧化物膜; a 通常发生在加热炉和锅炉燃烧的含氧环境中
b 4.9.2损伤形态 多数合金,包括碳钢和低合金俐,氧化腐蚀表现为均匀腐蚀,腐蚀发生后在金属表面生成氧化 a 物膜 b)300系列不锈钢和镍基合金在高温氧化作用下易形成暗色的氧化物薄膜
4.9.3受影响的材料 碳钢,低合金钢,300系列不锈钢、400系列不锈钢和镍基合金
4.9.4主要影响因素 a)温度:碳钢随温度升高腐蚀加剧,538以上时碳钢的氧化腐蚀严重 b)合金成分铬元素可形成保护性氧化物膜故碳钢和其他合金的耐蚀性通常取决于材料的铬 元素含量,300系列不锈钢在816C以下有良好的耐蚀性
4.9.5易发生的装置或设备 加热炉、锅炉和其他火焰加热设备等高温环境中运行的设备,尤其是在温度超过538C的设备和管 道中
4.9.6主要预防措施 a 材质选用;通过材质升级可防氧化腐蚀
铬是影响耐氧化能力的主要合金元素
硅和铝等其 他合金元素也有同样效果,但因其对力学性能不利,添加量应控制
用于加热炉支架,烧嘴喷 口和燃烧设备部件的特殊合金常添加这些元素
保护层:敷设耐氧化的表面保护层
4.9.7检测或监测方法 监测工艺条件;温度监测,如使用炉管表面热电偶和/或红外热成像仪对温度进行监测,防止运 行超温; b)厚度测量;超声波测厚
4.9.8相关或伴随的其他损伤 无 12
GB/T30579一2014 4.10大气腐蚀(无隔热层 4.10.1损伤描述及损伤机理 未敷设隔热层等覆盖层的金属在大气中发生的腐蚀
阳极反应: Fe一Fe2十十2e Fe+-Fe+十e 阴极反应 O十2H.O十4e-一4OH-(中性或碱性溶液) O,十4H十十4e一2H.O(酸性溶液 4.10.2损伤形态 碳钢和低合金钢发生腐蚀时主要表现为均匀腐蚀或局部腐蚀; a b)纯铜在发生大气腐蚀时易在金属表面生成绿色腐蚀产物 铝,镁和钛等金属因新鲜金属与大气接触后可在表面生成一层氧化膜,并失去表面金属光泽 4.10.3受影响的材料 碳钢、低合金钢,铝、铜等有色金属及其合金
4.10.4主要影响因素 a)大气成分;含有氯离子的海洋大气、潮湿工业大气或含有强烈污染的环境大气易发生该腐蚀
b 湿度;干燥的大气腐蚀能力很弱,而湿度较大的大气环境,尤其是容易凝结水滴的大气环境腐 蚀能力较强
以碳钢为例,当空气中相对湿度超过60%以上时,碳钢腐蚀速率按指数关系增 大,而空气相对湿度低于50%,腐蚀速率则较低
温度;材料表面温度宜高出环境露点温度至少3C以上,否则易在材料表面形成冷凝水造成 腐蚀
4.10.5易发生的装置或设备 所有在大气环境中使用的装置和设备,特别是存在任何下列情况时 a)设备和管道操作温度比较低,足以形成湿气 b)油漆或涂层系统质量差; 设备操作温度在环境温度和较高温度之间,或在环境温度和较低温度之间循环,容易发生腐 蚀;长期停用或闲置,但又没有正确封存的设备也容易发生腐蚀; 储罐和管道都特别敏感,用管座支撑的管道由于管子和支撑点之间容易吸附水而产生腐蚀, D 朝向正对着主风向及雨势的设备,容易发生大气腐蚀; 双金属连接结构,如铜与铝导电连接
4.10.6主要预防措施 防腐涂层!;可使用有机.无机涂层和金属镀层 a 选材;可选用耐候钢、不锈钢,或者在材料冶炼过程中加人铜,磷、铬,镍等微量元素 b c 控制湿度;一般认为湿度在50%以下腐蚀速率较低,湿度在30%以下腐蚀速率极低; d)环境保护增强大气环境保护,减少大气中的污染物含量 13
GB/T30579一2014 4.10.7检测或监测方法 a 检测方法一般为目视检测和腐蚀部位壁厚测定; b自动超声波扫查或导波法可对架空管道或无支撑部位容器壁进行检测
4.10.8相关或伴随的其他损伤 大气腐蚀(有隔热层). 4.11大气腐烛(有隔热层 4.11.1损伤描述及损伤机理 敷设隔热层等覆盖层的金属在覆盖层下发生的腐蚀,又称层下腐蚀
4.11.2损伤形态 碳钢和低合金钢发生腐蚀时主要表现为覆盖层下局部腐蚀
将碳钢和低合金钢的隔热材料拆 a 除后,隔热层下腐蚀常形成覆盖在腐蚀部件表面的片状疏松锈皮
300系列不锈钢,400系列不锈钢及双相不锈钢会产生点蚀和局部腐蚀
对于300系列不锈 b 钢,尤其隔热材料为老旧硅酸盐(含氯化物),还可能发生氯化物应力腐蚀开裂,在8o C 150C范围内时尤为明显,而双相不锈钢对此开裂敏感性较低
在一些局部腐蚀的情况中,腐蚀呈现为痛状点蚀(常见于油漆或涂层系统破损处)
d)隔热层和油漆或涂层明显发生了破损的部位经常伴有隔热层下腐蚀
4.11.3受影响的材料 碳钢、低合金钢.300系列不锈钢,双相不锈钢
4.11.4主要影响因素 大气成分:在海洋环境或水汽充沛的地方,发生隔热层下腐蚀的温度上限还可能远远超过 a 121C;多雨、温暖和沿海地区的装置比干燥、寒冷和内陆地区的装置更容易发生隔热层下腐 蚀;产生空气污染物,如氧化物海洋环境,冷却塔飘落)或二氧化硫(烟囱排放物)的环境可能 加速腐蚀
结构和覆盖层质量;结构设计和/或安装不良形成积水,将会加速隔热层下腐蚀;如果覆盖层 防护不严密,覆盖层的间隙处或破损处容易渗水,水的来源比较广泛,可能来自雨水,冷却水塔 的喷淋、蒸汽伴热管泄漏冷凝等
吸湿(虹吸)的隔热材料可能会面临隔热层下腐蚀问题;从隔 热层渗出的杂质,如氧化物,会加速损伤
温度;在水露点以下运行的设备容易在金属表面结露,形成潮湿环境,增加腐蚀可能性;当金属 温度没有超过水快速燕发的温度点时,随温度升高,腐蚀速率增大;当金属温度在水的沸点 100C~121C之间时,腐蚀非常严重
在该温度范围内,水很难燕发,隔热层会长时间处于 潮湿状态
运行:冷热循环运行或间歇使用可能加速腐蚀
4.11.5易发生的装置或设备 位置;高湿度区域,如冷却塔的下风向区、蒸汽排放口附近,喷淋系统、酸燕汽或喷水加迷冷却 的附近区域
14
GB/T30579一2014 b 设计 发生隔热层下腐蚀的设备多存在隔热层、防潮层、防水层或胶黏水泥损坏的情况,或有穿 l 透隔热层的突起及隔热层终端(如法兰); 2)设备设计中将隔热层支撑圈直接焊接在容器壁上(非支撑式);扶梯和平台支架以及吊 耳、接管,加强圈附近尤为明显; 3》燕汽伴热已损坏或泄漏的设备或管道; 油漆和/或涂层系统局部发生损坏 5)蒸发之前湿气或水自然汇集(重力疏水)的部位(立式设备的隔热层支撑圈)和末端设置 不良的防火层
与竖直管段底部相连的水平管段中,靠近连接处的端部几十厘米范围内 是隔热层下腐蚀典型部位
乙烯裂解装置的碳二系统中乙烯低温管道,以及碳三系统中丙烯低温管道是损伤发生的常见 区域
4.11.6主要预防措施 防腐涂层;可使用有机、无机涂层和金属镀层,尤其对于发生隔热层下大气腐蚀的300系列不 a 锈钢管线增加涂层防护; 选材可选用耐候钢、不锈钢,或者在材料冶炼过程中加人铜、磷、铬,镍等合金元素; b 控制覆盖层质量;一般认为覆盖层良好的情况下几乎不会发生层下腐蚀,对于覆盖层破损的部 位应及时进行修复 300系列不锈钢应采用低氯隔热层,降低氯化物应力腐蚀开裂可能性 d e)环境保护;增强大气环境保护,减少大气中的污染物含量; f 操作温度:如果工艺允许,使用温度尽量避开层下腐蚀敏感温度区间
4.11.7检测或监测方法 a)检测方法一般为覆盖层目视检测和覆盖层破损部位进行壁厚测定; b 导波法可对未拆除覆盖层部位进行一定条件下的截面腐蚀减薄量检测 e)可采用脉冲涡流对不拆除隔热层的管道进行壁厚测量; d 红外热成像检测设备或管道的隔热层完好状况 4.11.8相关或伴随的其他损伤 大气腐蚀、氯化物应力腐蚀开裂、高温氧化腐蚀
4.12冷却水腐蚀 4.12.1损伤描述及损伤机理 冷却水中由溶解盐、气体、有机化合物或微生物活动引起的碳钢和其他金属的腐蚀
4.12.2损伤形态 a冷却水中存在溶解氧时,冷却水对碳钢的腐蚀多为均匀腐蚀; b)若冷却水腐蚀以垢下腐蚀,、缝隙腐蚀、电偶腐蚀或微生物腐蚀为主时,多表现为局部腐蚀 冷却水在管嘴的出人口或管线人口处易形成冲蚀或磨损,形成波纹状或光滑腐蚀 c d在电阻焊制设备或管道的焊缝区域,冷却水腐蚀多沿焊缝熔合线形成腐蚀沟槽
15
GB/T30579一2014 4.12.3受影响的材料 碳钢所有不锈钢、铜、铝,钛和镍基合金
4.12.4主要影响因素 温度:冷却水出口温度和/或工艺物料侧人口温度的升高会增加腐蚀速度和结垢倾向
工艺物 料侧的温度高于60C时,新鲜水存在结垢倾向,工艺物料侧温度继续升高或冷却水人口温度 升高时,这一倾向更明显
半咸水或盐水/海水出口温度高于46时会结垢严重,超过80C 后腐蚀逐渐下降
b氧含量:随冷却水含氧量升高,碳钢腐蚀速率增大
结垢;垢层可由矿物沉淀(硬的),淤泥、悬浮的有机材料、腐蚀产物、氧化皮,海水和微生物生长 形成,造成垢下腐蚀
流速;流速足够高时可减少结垢,并冲出沉积物,但不能过高以致引发冲刷腐蚀,流速的限制 取决于管线材质和水质
低流速时通常腐蚀严重,流速低于1m/s容易导致结垢、沉积,在冷 却水用于凝结器或冷却器的壳程时,介质流动死区或滞流区部位腐蚀加剧,比管程腐蚀严重
水质;300系列不锈钢在新鲜水、,半咸水、,盐水/海水系统中可产生点蚀、缝隙腐蚀和环境开裂, 铜/锌合金在新鲜水、半咸水,盐水/海水系统会发生脱锌腐蚀;铜/锌合金在含氨或铵化合物的 冷却水中会发生环境开裂;电阻焊接制造的碳钢设备,其焊缝或热影响区在新鲜水,半咸水中 会发生严重腐蚀
钛和其他阳极材料连接可能发生严重的钛氢化,温度高于82较为常见,低温也偶有发生
4.12.5易发生的装置或设备 所有水冷热交换器和冷却塔设备
4.12.6主要预防措施 系统改进;系统设计改进、运行优化和进行化学处理来防护,如冷换设备设计时冷却水走管程 以尽量减少滞流区: 温度:人口设计温度应低于57C; b c)流速;流速应有最小流速和最大流速范围限制,尤其是使用盐水/海水时; d 材质选用;选用耐蚀性好的材质,尤其对于在高含氯、低流速、高温度和/或水处理不当的冷却 水系统中运行的换热设备; 清洗;对换热管内外表面进行定期清洗
e 4.12.7检测或监测方法 a 水质监测:对pH值,氧含量,回流比、残存药剂量、微生物活性,冷却水出口温度、姬污染程度 和工艺泄漏情况进行监测; b)换热性能测算;定期测算热交换器换热性能,掌握结垢和沉积状况 流速监测:用超声波流速仪检测冷却水流速 d)采用涡流检测,漏磁检测、导波检测或内旋转检测系统对热交换器管束进行检查; 取样分析:对有代表性的管子进行取样,剖管分析
4.12.8相关或伴随的其他损伤 微生物腐蚀、氯化物应力腐蚀开裂 16
GB/T30579一2014 4.13土壤腐蚀 4.13.1损伤描述及损伤机理 金属接触到土壤时发生的腐蚀
4.13.2损伤形态 土壤腐蚀多表现为以点蚀为主的局部腐蚀,腐蚀的严重程度取决于局部的土壤条件和设备金属表 面环境条件的变化
4.13.3受影响的材料 碳钢、铸铁,球墨铸铁、低合金钢
4.13.4主要影响因素 土壤电阻率:电阻率大的土壤对金属的腐蚀性较低; a b)水分含量;水分含量大的土壤往往腐蚀性较强; c)溶解盐浓度;溶解盐浓度大的土壤对金属的腐蚀性较强; d)酸度;酸度大的土壤对金属的腐蚀性较强 e)温度:;随金属温度升高,土壤腐蚀性增强 位置;土壤和空气的界面区域湿度和氧气有利于土壤腐蚀的发生; 保护涂层:保护涂层良好的部位腐蚀情况轻微,保护涂层破损处或效果较差的位置腐蚀情况 较严重; h)阴极保护;保护良好的部位腐蚀情况轻微,保护效果较差的位置腐蚀情况较严重 iD 其他:土壤多样性、杂散电流、微生物、氧浓差电池腐蚀等
4.13.5易发生的装置或设备 a)埋设于地下并与土壤直接接触的设备 埋设于地上,但设备的底部或其他某部位与土壤直接接触的设备, b) e)埋地或半埋地管道; d)设立在地面上且有一部分与土壤相连的金属支撑结构
4.13.6主要预防措施 a)采用特殊回填填料或回填方式,改善设备周围的土壤条件,可减少碳钢的土壤腐蚀; b)保护涂层:保持保护涂层的质量; 阴极保护;设置有效的阴极保护设施 c) 4.13.7检测或监测方法 参比电极法;宜用结构附近的专用参比电极(电阻压降误差校正)测量结构对土壤的电位; a) 耐压试验:验证经受腐蚀后结构的强度 b e)导波检测;应用于管涌、埋地或半埋地管道检测, 对满足检测条件的管道可采用自动内检测仪进行腐蚀检测
d) 4.13.8相关或伴随的其他损伤 无 17
GB/T30579一2014 4.14微生物腐烛 4.14.1损伤描述及损伤机理 细菌,藻类或真菌之类的活性有机物造成的腐蚀,多与团簇状或泥泞状有机物有关
常见微生物有 硫酸盐还原菌(sRB),铁氧化菌(IOB)、锰氧化菌(MnOB),硫氧化细菌、铁还原细菌、酸生产菌(APB)和 胞外聚合物生产菌(EPB). 4.14.2损伤形态 a 微生物腐蚀通常表现为局部垢下腐蚀或微生物簇团处腐蚀; 碳钢的微生物腐蚀通常为杯状点蚀,不锈钢的微生物腐蚀通常为表面蚀坑
b 4.14.3受影响的材料 碳钢,低合金钢,300系列不锈钢、400系列不锈钢,铝、铜和镍基合金
4.14.4主要影响因素 水分;微生物腐蚀通常发生在水溶液或有水存在的环境中,尤其是在允许或促进微生物生长的 滞流或低流速区域
环境;微生物可在苛刻环境中生存和繁殖,典型情况有缺氧、缺光或黑暗、高盐度,pH值在0~ b 12.0之间温度在一17Cl13C之间
未对环境采取控制措施时,即使只是少量微生物混 人,经过增殖扩散,亦可形成强腐蚀性
养分;不同微生物所需养分不同,养分可以是无机物,如硫、氨、硫化氢也可以是有机物,如姬、 有机酸等
承压设备发生工艺物料内漏时,姬或硫化氢等杂质的混人可加剧微生物腐蚀
此 外碳,氮,磷是微生物生长所必需的基本元素
4.14.5易发生的装置或设备 a)热交换器,储罐底部水相,低流速或介质流动死角的管线、与土壤接触的管线等 进行水压试验的设备在排水后未及时吹干,或露天放置的设备无保护措施 b e)水质处理不良的冷却水储罐和水冷热交换器; 消防水系统
d 4.14.6主要预防措施 杀菌剂;采用杀菌剂持续处理,典型杀菌剂有氯、澳臭氧、紫外线或专用化学剂 a b)流速;限制最低流速,减少低流速或滞流区, 水分;水压试验后尽快清空,吹干并防止湿气进人;非存水系统应保持干燥清洁; 保护设施;对地下结构进行包覆和阴极保护,储罐的内表面刷涂料; D 清理;清理有机物可使用刮除、高速水流清洗、化学清洗和微生物处理
4.14.7检测或监测方法 水质监测;监测杀菌剂残余量、微生物数量,以及目视检测腐蚀状况 a 专用探针;监测结垢程度,结垢可能会先于或与微生物腐蚀同时进行; b 热交换器负荷监测;热交换器负荷能力降低表明可能存在结垢和微生物腐蚀 c d)气味监测:污水气味异常表明可能存在微生物腐蚀
18
GB/T30579一2014 4.14.8相关或伴随的其他损伤 冷却水腐蚀
4.15锅炉冷凝水腐蚀 4.15.1损伤描述及损伤机理 锅炉系统和蒸汽冷凝水回水管道上发生的均匀腐蚀和点蚀,多由溶解的气体、氧气、二氧化碳引起 4.15.2损伤形态 除氧系统工作不正常时,很少的氧气就可引发锅炉冷凝水腐蚀,多表现为点蚀,呈溃疡状,在金 a mm30 属表面形成黄褐色或砖红色鼓包,直径从1 mm不等,由各种腐蚀产物组成,腐蚀产 物去除后,可见金属表面的腐蚀坑; b)冷凝水回水系统的腐蚀多由二氧化碳引起,腐蚀后管壁形成平滑凹槽
4.15.3受影响的材料 主要为碳钢,以及一些低合金钢、300系列不锈钢和铜合金 4.15.4主要影响因素 a)关键因素为溶解的气体浓度(氧气和二氧化碳),pH值、温度、给水水质和给水处理专用系统; 生成连续的四氧化三铁保护层并保持完好,足以实现对锅炉的腐蚀防护; b e)用来除结垢和沉淀的化学处理,应与专用水设施和锅炉给水处理系统的除氧剂相匹配; d)铜锌合金应避免接触有联氨、中和胺或含氨化合物的锅炉冷凝水
4.15.5易发生的装置或设备 锅炉外部处理系统、除氧设备、给水管线、泵、冷凝水回水系统,以及级间加热器、省煤器或蒸汽发生 系统的水侧和受火侧
4.15.6主要预防措施 a)除氧处理;在进行机械除氧的同时,根据系统压力情况进行化学药剂(如催化亚硫酸钠或联氨 除氧,可减少系统含氧量
残存除氧剂被夹带进人燕汽发生系统,可除去脱氧器下游混人的 氧气
b)缓蚀剂采用结垢或沉积物控制,或者四氧化三铁保护层防护的处理方案,如果不能降低冷凝 水回流系统的二氧化碳,可能就需要添加胺类缓蚀剂 4.15.7检测或监测方法 水质监测;水质监测是常用的有效方法.监测参数包括pH值、导电率,氧含量,残留杀菌剂,以 a 及用来检测泄漏的有机固体悬浮颗粒总量 b)操作程序;根据经验制定合理的工作程序,可在复杂的锅炉水和冷凝水系统中查找即将出现 或已出现爆管及冷凝水泄漏的部位 表面检测;湿荧光磁粉检测可在停车状态下有效检测除氧器的开裂
4.15.8相关或伴随的其他损伤 二氧化碳腐蚀、腐蚀疲劳、冲蚀、冲刷
19
GB/T30579一2014 4.16碱腐蚀 4.16.1损伤描述及损伤机理 苛性碱或碱性盐引起的局部腐蚀,多在蒸发浓缩或高传热条件下发生
有时因碱性物质或碱液浓 度不同,也可能发生均匀腐蚀
4.16.2损伤形态 a多表现为局部腐蚀,如锅炉管的腐蚀沟槽或隔热垢层下的局部腐蚀, b 腐蚀坑可能因充满沉积物,损伤被遮盖,在可疑区域进行检测时可能需要使用灵敏仪器, e)水气界面介质浓缩区域会形成局部沟槽,立管可形成一个环形槽,水平或倾斜管会在管道顶端 或两侧形成纵向槽 d)温度高于79C的高浓度碱液可引起碳钢的均匀腐蚀,温度达到93C时腐蚀速率非常大
4.16.3受影响的材料 碳钢、低合金钢、.300系列不锈钢
4.16.4主要影响因素 苛性碱(氢氧化钠或氢氧化钾)浓度越高,腐蚀越严重
多数情况下工艺物料中碱液浓度很低、 但如果存在蒸发、沉积,分离等浓缩过程,可形成局部高浓度
碱的主要来源有中和或反应用工艺注碱、锅炉水加人的低浓度碱、锅炉水软化器再生期间因 b 疏忽而混人的碱、冷凝器或工艺设备泄漏而混人工艺流体的碱、中和和脱除硫化物而注人的苛 性碱液
4.16.5易发生的装置或设备 锅炉和蒸汽发生器(包括热交换器); a b 常减压装置原油进料的注碱部位可能会出现苛性碱浓缩情况,如注人的碱不能和油气有效混 合,会加剧常减压装置预热热交换器、加热炉炉管和转油线的局部腐蚀 乙烯裂解装置;压缩系统的注碱管道、碱洗塔三段碱洗段; 使用碱进行产品脱硫的装置
d 4.16.6主要预防措施 优化设计:燕汽发生设备设计时进行优化,如减少游离苛性碱的量、注人足量的水、控制加热炉 炉膛的燃烧强度以减少炉管的过热,或减少进人凝汽器的碱盐量
设计时还应考虑使注人的 碱和其他介质能进行有效混合,避免碱在器壁高温部位发生浓缩
碳钢和300系列不锈钢在66C以上的高浓度苛性碱液中会产生严重腐蚀,合金400和一些其 b 他镍基合金的腐蚀速率较低
4.16.7检测或监测方法 超声波测厚;超声波测厚可有效检测均匀腐蚀,目视检测和超声波测厚可有效检测局部腐蚀; a 对于管道和无法内检的容器,可进行超声波扫查和射线成像检测, b注人点监测:对注人点下游进行腐蚀监测,如定点测厚、导波检测和射线成像检测; c)蒸汽发生器可用内窥镜进行目视检测
20
GB/T30579一2014 4.16.8相关或伴随的其他损伤 蒸汽阻滞
4.17燃灰腐蚀 4.17.1损伤描述及损伤机理 燃油或燃煤中的杂质(主要为硫、钠、钾和/或饥),在加热炉,锅炉,燃气涡轮的金属表面沉积和熔 化,生成的熔渣熔解了表面的氧化物膜,使膜下新鲜金属裸露出来,和氧气反应再次生成氧化铁等氧化 物,如此反复,加速材料在高温下的损耗
4.17.2损伤形态 a)燃油的燃灰腐蚀表现为结渣处的严重金属损耗,金属腐蚀速率可达2.5mm/年一25mm/年
b)使用燃油的过热器和再热器沉积燃灰至少可分为两层:附着在部件上的沉积物最为重要,在 室温下呈暗灰色或黑色的外观;熔融态硫酸盐将腐蚀产物烧结并覆盖在表面,形成粘着力很强 的玻璃状硬垢
去除燃灰沉积物后,金属基体表面呈鳄鱼皮状,腐蚀浅槽纵横交错 使用燃煤时燃灰层的玻璃状硬垢层和基体金属间可见明显的平滑界面
水冷壁开裂以环向为主,轴向相对少些,整体表现为环向凹槽
熔雕灰团形成时,只能维持住一定重量的灰分
重量过大时,熔渣会脱落,使一段无甚挡的光 管暴露在燃烧室的热流下
水冷壁温度会发生跃升,估计幅度可达38C,形成类似于热疲劳 的开裂;蒸汽冷却管的机理也类似,只是温度跃升小一些,因此热疲劳损伤也轻微一些;过热器 和再热器的鳄鱼皮状斑纹和燃煤锅炉水冷壁的环向开裂也类似
4.17.3受影响的材料 a 所有加热炉和锅炉的常用材料; b50Cr-50Ni系列合金耐蚀能力强
4.17.4主要影响因素 a)温度;金属温度超过盐的熔化温度时腐蚀才会发生,温度最高的部位腐蚀最严重 b合金成分;腐蚀速率因合金成分不同而变化,镍基耐蚀合金耐蚀能力强
熔渣类型;燃油燃料的燃灰中熔渣是五氧化二饥和氧化钠的混合物,或五氧化二饥和硫酸钠的 混合物,熔点约538C;燃煤的燃灰对过热器和再热器的腐蚀是硫酸铁钠和硫酸铁钾熔渣造成 的,熔点在544C一610C间;水冷壁的燃灰腐蚀是焦硫酸钠和焦硫酸钾的混合熔渣造成的 熔点温度约371C
气相中一氧化碳,硫化氢、氢气含量较高,以及未燃烧的煤粉都会形成还 原性条件,腐蚀加速,腐蚀速率是氧化性条件中的2倍5倍
d)管子(尤其是奥氏体合金材质)表面的渗碳,会降低耐腐蚀性,加速金属的损耗
4.17.5易发生的装置或设备 所有使用含杂质(指含硫、钠、钾和/或钥)燃油或燃煤的加热炉或燃气轮机,以及使用含钥和钠 杂质的燃油或造油加热炉容易发生腐蚀,如果燃油中没有铁,燃油锅炉发生燃灰腐蚀的可能性 很小; b)加热炉金属表面温度低于熔渣熔点时不会发生腐蚀,但加热炉炉管的吊管架和支架因使用温 度高,可能发生严重的燃灰腐蚀 21
GB/T30579一2014 燃气透平机改用燃油驱动时,叶片可能发生燃灰腐蚀; c d 加热炉炉管产生结焦时,操作人员可能会增加热通量,使炉管部件温度升高,可能引起燃灰 腐蚀; 过热器和再热器中熔盐的熔点达538笔甚至更高,任何金属壁温比这些硫酸盐熔点更高的装 置都可能会发生腐蚀; f 乙烯裂解装置裂解与急冷系统的裂解部分裂解炉对流段及辐射段炉管; g水冷壁温度低于371C时,腐蚀程度最轻
因此,蒸汽压力不超过12.4MPa的部位几乎不会 发生燃灰腐蚀
4.17.6主要预防措施 燃料改性使用杂质含量低的燃料,或进行掺混,可减级燃灰腐蚀; a 设计优化燃烧器合理设计,减少火焰冲击和局部过热等可能产生高温的状况 b 工艺改进;燃烧时保持氧气过量实现燃料充分燃烧,或向燃料中注人特殊的添加剂,提高炉渣 c 熔点,并降低沉积物粘附在金属表面或熔解保护性氧化物膜的可能性;降低设备使用温度,使 温度最高的部位不超过熔渣的熔点 选材:管线吊管架和支架等容易产生高温的部件,可以改用50%Cr50%Ni合金,如合金657, 但可能需同时对吊管架的设计进行更改,以改善50%Cr-50%Ni合金低应力脆断的问题 4.17.7检测或监测方法 目视检测;检查燃灰腐蚀的最有效方法,挂渣明显的部位金属损耗可能也非常严重; a b)壁厚测定;先喷砂处理去除粘附力强的玻璃状硬垢,然后用超声波检测来测量厚度损失 e)金相检查和沉积物分析技术可用于确定是否发生了燃灰腐蚀, 4.17.8相关或伴随的其他损伤 热疲劳
4.18烟气露点腐蚀 4.18.1损伤描述及损伤机理 燃料燃烧时燃料中的硫和氯类物质形成二氧化硫、三氧化硫和氯化氢,低温(露点及以下)遇水燕气 形成酸,对金属造成腐蚀
腐蚀介质的形成过程如下 烟气中的硫或氯-sO.SO.)或HC SO十H,OHSO SO十H.O-HSO 4.18.2损伤形态 烟气露点腐蚀是亚硫酸腐蚀、硫酸腐蚀和盐酸腐蚀中某种腐蚀或几种腐蚀共同作用的综合 a 结果; 省煤器或其他碳钢或低合金钢部件发生烟气露点腐蚀时会形成宽而浅的蚀坑,形态取决于硫 酸凝结方式 对于余热锅炉中的300系列不锈钢制给水加热器,可能发生表面的应力腐蚀开裂,裂纹整体外 观呈“发丝”状
心
GB/T30579一2014 4.18.3受影响的材料 碳钢、低合金钢、300系列不锈钢
4.18.4主要影响因素 杂质;燃料中的杂质硫及氯化物)含量越高,腐蚀的可能性就越大,腐蚀程度就可能越严重; a b)温度:所有的燃料均会含有一定量的硫,如果烟气接触的金属温度低于露点温度,就会发生硫 酸和亚硫酸露点腐蚀
硫酸露点与烟气中三氧化硫浓度有关,一般大约为138C
氯化氢露 点温度与氯化氢浓度有关,一般大约为54C
4.18.5易发生的装置或设备 使用含硫燃料的加热炉或锅炉,在省煤器和烟道中都可能发生硕致烟气露点腐蚀 a 余热锅炉进水温度低于飘化氢复露点温度时,300系列不锈孵制给水加热器可能在烟气侧发生 b 叙化物应力腐蚀开裂 燃气轮机的气相含氯时,如使用氧基除菌剂的冷却塔漂溅物可能被吹进燃气轮机系统,余热回 收设备的300系列不锈钢制给水加热器可能发生氯致烟气露点腐蚀,导致余热回收设备的给 水加热器损坏
4.18.6主要预防措施 a)保持锅炉和加热炉的金属壁温高于硫酸露点温度 环境中含有氯化物时,余热锅炉的给水加热器不能用300系列不锈钢材质; b e)燃油锅炉进行水洗除灰作业时,如果仅用水进行最终清洗可能不能中和掉酸性盐,可以在最终 清洗的水中加人碳酸钠中和酸性灰份
4.18.7检测或监测方法 a)超声波测厚可监测省煤器管子的壁厚减薄速率; b) 目视检测和渗透检测可发现300系列不锈钢的应力腐蚀开裂
4.18.8相关或伴随的其他损伤 盐酸腐蚀、氧化物应力腐蚀开裂
4.19氯化铵腐蚀 4.19.1损伤描述及损伤机理 氯化铵在一定温度下结晶成垢,在无水情况下发生均匀腐蚀或局部腐蚀,以点蚀最为常见,可出现 在氧化铵盐或胺盐垢下
4.19.2损伤形态 腐蚀部位多存在白色、绿色或褐色盐状沉积物,若停车时进行水洗或吹扫,会除去这些沉积物 等到目视检测时沉积物可能已不明显; b)垢层下腐蚀通常为局部腐蚀,如点蚀; 腐蚀速率可能极高
23
GB/T30579一2014 4.19.3受影响的材料 按耐腐蚀性增加的顺序;碳钢、低合金钢,300系列不锈钢、合金400,双相不锈钢、合金800和合金 825、合金625和合金C276,以及钛
4.19.4主要影响因素 材质;见4.19.3的材料耐腐蚀性排序
a b)成垢(结晶)程度:高温物料冷却时氯化铵盐会析出成垢(结晶),其程度取决于氯化铵浓度和 温度,即使温度远远超过水的露点温度(>149),也会腐蚀管线和设备
水分氧化铵盐易吸湿潮解,少量水即可造成严重腐蚀,最大腐蚀迷率可超过2.5, mm/年
当 氧化锁在高于水露点湖度下析出时,可能需要迷人洗涨水以溶解氯化铵盐
叙化锁盐也具有 很强的水溶性和腐蚀性,在与水混合时形成酸性溶液,某些中和胺与氯化物发生反应形成具有 类似作用的盐酸胺盐 温度;随温度升高,腐蚀速率增大
4.19.5易发生的装置或设备 常压塔塔顶系统;常压塔塔顶、塔内上部塔盘、塔顶管线及热交换器可能会积垢,发生垢下腐 蚀
由于氯化铵和/或盐酸胺盐从气相凝结出来,沉积物可能出现在低流量区
塔顶循环回流 物料含有叙化铵或盐酸胺盐时可能会发生腐蚀
加氢装置;反应器流出物中氯化铵结垢,发生垢下腐蚀
若热交换器发生结垢或换热效率下 降,可能需要用水冲洗
催化重整装置;反应器流出物和循环氢系统会发生氯化铵垢下腐蚀
d)流化床催化裂化装置和焦化装置;分憎塔塔顶和塔顶回流系统会发生氯化铵垢下腐蚀
4.19.6主要预防措施 耐点蚀的合金同样具有较好的耐氧化铵腐蚀性能,但即使是耐点蚀性最强的镍基合金和钛合金,也 可能在氯化铵盐环境中发生点蚀
a)常减压装置;电脱盐和/或向脱盐后的原油中注苛性碱,降低常压塔进料中的氯化物含量,以氯 化铵盐或盐酸胺盐进行控制;对常压塔顶管线注水冲洗沉积盐;注人成膜胺型缓蚀剂缓解 腐蚀; 加氢装置:降低反应器原料经中的氯化物含量;控制补充氢中的氧化物含量;向反应产物流出 系统连续或间断注水,冲走氯化铵沉积物 催化重整;反应产物进行脱氯处理;或注水冲洗,但注水系统应精确设计;塔顶的部分设备可注 人中和胺或成膜胺型缓蚀剂缓解腐蚀
4.19.7检测或监测方法 a)氯化铵盐垢下腐蚀通常为局部腐蚀,难以检测; b壁厚测定:射线成像或超声波检测确定壁厚减薄; 监测进料和排放废水中氨和氯化物含量,可能需要通过工艺模拟来确定浓度和露点温度,若已 c 计算出氧化铵盐沉积温度,为使金属壁温始终保持在氧化铵盐沉积温度之上,温度监测和控制 可能会比较有效 监测热交换器的压力降和热效率,压力降异常增大或换热效率明显降低时,常可发现已产生 了氧化铵盐沉积垢层; 2
GB/T30579一2014 腐蚀挂片或探针,由于氯化铵盐必须能沉积在探针表面才可有效监测腐蚀,故该方法有可能 有用
4.19.8相关或伴随的其他损伤 盐酸腐蚀
4.20胺腐蚀 4.20.1损伤描述及损伤机理 胺处理工艺中碳钢发生的均匀腐蚀和/或局部腐蚀,胺腐蚀并非胺本身直接产生腐蚀,而是由胺液 中溶解的酸性气体(二氧化碳和硫化氢)、胺降解产物、耐热胺盐(HSAs)和其他腐蚀性杂质引起的
4.20.2损伤形态 a)碳钢和低合金钢发生胺腐蚀时可表现为均匀腐蚀或局部腐蚀,沉积物处表现为垢下腐蚀; b)介质流速较低时,多为均匀腐蚀,介质流速高并伴有紊流时,多为局部腐蚀
4.20.3受影响的材料 碳钢、低合金钢
4.20.4主要影响因素 介质:介质对碳钢和低合金钢的腐蚀性从大到小的次序为单乙醇胺(MEA),二甘醇胺(DGA、 二异丙胺(DIPA、二乙醇胺(DEA)和甲基二乙醇胺(MDEA)
b)胺浓度;贫胺溶液导电性差和/或pH值高,一般没有腐蚀性
胺液中耐热胺盐(HsAs)浓度 超过2%(质量分数)时,腐蚀速率显著增大,其程度取决于耐热胺盐浓度
杂质;氨,硫化氢和氮化氢等杂质会加速腐蚀,多发生于再生塔塔顶冷凝器、出口管线,以及回 流管线、阀和泵处
温度;随温度升高,腐蚀速率增大,特别是富胺环境中
若压力降足够大,温度高于104C左右 时酸性气体可能会发生闪蒸,产生严重局部腐蚀 流速;低流速区一般呈均匀腐蚀,高流速并存在强紊流时会造成局部腐蚀
4.20.5易发生的装置或设备 a各类胺处理系统,如炼油厂中用于脱除硫化氢、二氧化碳或硫醇的胺处理系统,在常减压装置、 焦化装置、流化床催化裂化装置、重整加氢装置、加氢裂化装置和尾气处理装置中常可见到这 些胺处理系统 再生塔塔底再沸器和再生器,尤其是胺液温度最高且介质紊流最强的区域,可发生严重腐蚀 b 贫胺/富胺溶液热交换器的富胺侧、高温贫胺管线、高温富胺管线、胺液泵,以及回收设备是腐 蚀易发区域, 4.20.6主要预防措施 处理量;用于吸收酸性气体的胺处理系统应控制合适的处理量,避免胺液中腐蚀性杂质浓度 a 过高
b)温度:控制再沸器的温度和流量,并控制再生塔塔顶温度,避免胺在高温下发生降解产生腐蚀 性产物
25
GB/T30579一2014 压力:控制高温部位的局部压力降,降低闪蒸程度 d)材质;无法避免闪蒸时应采用300系列不锈钢或其他耐蚀合金,在吸收塔和汽提塔中,宜采用 410不锈钢塔盘和内件 耐热胺盐浓度;控制耐热胺盐的浓度在可接受的范围内,可有效降低胺液腐蚀能力
防止氧气 窜人也会减少耐热盐的形成,胺的储罐和物料缓冲罐应充装惰性气体进行保护 设计和操作;如果设计合理,操作正确,大多数部件都可使用碳钢材质,但设计存在缺陷,或操 作不当,以及介质中有杂质时会产生腐蚀
例如过滤和工艺控制可除去胺液中的固体颗粒和 胫组分,富胺液中固体颗粒过滤效果比贫胺液更佳
流速;碳钢材质输送的富胺液速度不宜超过1.8m/s,输送贫胺液可放宽至6m/s g h)缓蚀剂可添加合适的缓蚀剂,以控制胺腐蚀
检测或监测方法 4.20.7 检测方法一般为设备内部的目视检测和腐蚀部位壁厚测定; a b)若腐蚀发生在内壁而只能从外部检测时,可用自动超声波扫查、导波检测或射线成像查找减 薄部位,并对减薄部位进行壁厚测定; 腐蚀探针或挂片;监控实时腐蚀速率,尤其是温度较高的部位,如再沸器进料管线和回流管线 高温贫胺/富胺管线、汽提塔塔顶冷凝器的管线
4.20.8相关或伴随的其他损伤 胺应力腐蚀开裂
4.21高温硫化物腐蚀(无氢气环境》 4.21.1损伤描述及损伤机理 碳钢或其他合金在高温下与硫化物反应发生的腐蚀: Fe十RSFeS十R 4.21.2损伤形态 多为均匀腐蚀,有时表现为局部腐蚀,高流速部位会形成冲蚀; a 腐蚀发生后部件表面多覆盖有硫化物膜,有的膜很厚,有的很薄,厚度跟材质、流体腐蚀性、流 b 速和是否有杂质有关
4.21.3受影响的材料 a)所有铁基材料,包括碳钢、低合金钢,300系列不锈钢、400系列不锈钢 b)镍基合金会不同程度地发生硫化物腐蚀,腐蚀速率取决于材料成分,尤其是铬含量 和碳钢相比,铜合金发生硫化物腐蚀的起始温度更低
4.21.4主要影响因素 合金元素;耐硫化物腐蚀性能,取决于反应产生的硫化物膜保护能力
一般而言,钢材和镍基 a 合金随络元素含量升高,耐魏化物腐蚀能力增强
300系列不锈钢,如304.316.321甜37,在 多数炼油工艺中耐高温硫化物腐蚀能力较强
镍基合金与不锈钢相似.铬含量相近的镍基合 金其抗硫化物腐蚀能力也相似 b温度:通常在铁基合金温度超过260C时开始发生高温硫化物腐蚀,温度越高,腐蚀越快
26
承压设备损伤模式识别GB/T30579-2014
随着我国经济的快速发展,承压设备已经成为许多企业不可或缺的重要组成部分。然而,在使用过程中,由于种种原因,这些设备也很容易出现各种损伤情况。为了保证设备的安全性和稳定性,必须对这些损伤情况进行准确的识别和分析。
针对这一问题,国家标准化管理委员会发布了GB/T30579-2014标准,其中包括了承压设备损伤模式识别的相关内容。该标准通过对设备常见的损伤类型进行系统分类,并结合实际生产环境,提出了具体的识别方法和步骤。
在具体应用时,可以根据设备的使用情况和损伤痕迹,通过以下步骤来识别设备的损伤模式:
- 观察和检查设备,确认是否存在异常情况;
- 对异常情况进行详细描述,包括位置、大小、形状等信息;
- 根据异常情况的特征,参照标准中的分类方法,确定其属于哪种损伤类型;
- 进一步分析损伤类型的原因和后果,并提出相应的解决方案。
需要注意的是,在实际操作过程中,还应该结合设备的使用环境、工作负荷等因素进行综合判断。同时,为了确保识别结果的准确性和可靠性,还应该配合使用相关的检测设备和技术手段。
总之,GB/T30579-2014标准中的承压设备损伤模式识别方法,为工程技术人员提供了重要的指导和参考。只有在实践中不断摸索和探索,才能更好地应用这些理论知识,提高设备的安全性和稳定性。