GB/T37393-2019
数字化车间通用技术要求
Digitalfactory—Generaltechnicalrequirements
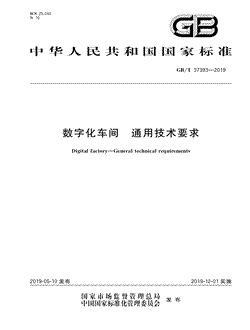
- 中国标准分类号(CCS)N10
- 国际标准分类号(ICS)25.040
- 实施日期2019-12-01
- 文件格式PDF
- 文本页数48页
- 文件大小6.59M
以图片形式预览数字化车间通用技术要求
数字化车间通用技术要求
国家标准 GB/T37393一2019 数字化车间通用技术要求 Digitalfaetory一Generalteehniealrequirements 2019-05-10发布 2019-12-01实施 国家市场监督管理总局 发布 币国国家标准化管理委员会国家标准
GB/37393一2019 目 次 前言 引言 范围 规范性引用文件 2 术语和定义 3 缩略语 体系结构 基本要求 6.1数字化要求 6.2网络要求 6.3系统要求 6.4集成要求 6.5安全要求 基础层数字化要求 7.1制造设备的数字化要求 7.2生产资源的数字化要求 工艺设计数字化要求 --+ 车间信息交互 9.I通信网络 9.2数据采集与存储 9.3数据字典 0制造运行管理数字化要求 基本要求 10.l 0.2车间计划与调度 0.2.1信息集成模型 0.2.2功能要求 0.3工艺执行与管理 信息集成模型 10 10.3.1 0.3.2功能要求 10 0.4生产过程质量管理 ll 0.4.1信息集成模型 ll 10 0.4.2功能要求 12 0.5生产物流管理 13 0.5.1信息集成模型 13 0.5.2功能要求 18 15 0.6车间设备管理
GB/T37393一2019 15 10.6.1信息集成模型 16 10.6.2功能要求 18 附录A资料性附录典型电气产品数字化车间应用案例 25 附录B资料性附录数字化车间合理化产线设计案例 28 附录C资料性附录数字化制造设备典型配置与功能 36 附录D资料性附录数字化车间的安全管理示例 39 附录E(资料性附录数字化车间信息处理案例
中
参考文献
GB/37393一2019 前 言 本标准按照GB/T1.1一2009给出的规则起草
本标准由机械工业联合会提出
本标准由全国工业过程测量控制和自动化标准化技术委员会(SAC/Tc124)归口
本标准起草单位:机械工业仪器仪表综合技术经济研究所、科学院沈阳自动化研究所、国机智 能科技有限公司、吴忠仪表有限责任公司、西安高压电器研究院有限公司,无锡职业技术学院、船舶 重工集团公司第七一六研究所、秦川机床工具集团股份公司、北京和利时系统工程有限公司、信息 通信研究院西部分院、中冶赛迪信息技术有限公司,青岛海尔工业智能研究院有限公司、江苏徐工信息 技术股份有限公司、南京大学将华南理工大学、西北工业大学、西门子()有限公司、罗克韦尔自动化 )有限公司、三菱电机自动化()有限公司、菲尼克斯()投资有限公司贝加莱工业自动化 )有限公司,施耐德电气()有限公司重庆盟讯电子科技有限公司南京优倍自动化系统有限 公司、上海自动化仪表有限公司、陕西高端装备与智能制造产业研究院有限公司、上海电器科学研究院 上海工业自动化仪表研究院有限公司,北京航天智造科技发展有限公司、广东汇兴精工智造股份有限公 ,毕恩吉商务信息系统工程(上海)有限公司
司、 本标准主要起草人:丁露,王成城、王春喜.宋宏、李放,刘暇,陶静,戴勇、钱晓忠、刘志刚、王骏 郭琼、吴慧媛、华铬、戴霁明、杨应华、周晓毅、戎罡、孙强、潘学龙、倪建军、廖良闯、玄甲辉、任洪强、全新路 张维杰、任涛林、李翌辉、赵洪武、陈长胜、张云华、范雨晓、黄振林,刘俊杰、陈菁,刘亚俊、何茂松、董健 薛晓娜、宋华振、张庆军、王震、柴熠、王英,王嘉宁、许建全、于文涛、阎新华、何军红、许光辉
GB/T37393一2019 引 言 数字化车间是运用精益生产、精益物流、可视化管理、标准化管理、绿色制造等先进的生产管控理论 和方法设计和建造的信息化车间,具有精细化管控能力,是实现智能化、柔性化、敏捷化的产品制造的基 础
数字化车间作为智能制造的核心单元,涉及信息技术、自动化技术、机械制造、物流管理等多个技术 领域
因此,统一的术语和通用的技术要求是我国实现数字化车间建设、完善智能制造标准体系所必备 的基础条件
数字化车间标准体系由一系列标准构成,标准体系架构如图1所示 智能制造 数字化车间标准体系 基础标准 术语和定义 通用技术要求 参考模型 方法标准 数字化车间 数字化车间 数字化车间 数字化车间 数字化车间系统 设计建设规范虚拟仿真要求工艺布局要求 MES/ERP技术要求 安全技术要求 应用标准 汽车制造行业数字 船舶制造行业数字 航空制造行业数字 化车间特殊要求 化车间特殊要求 化车间特殊要求 机床和机器人行业数字 轨道交通行业数学 电子制造行业数字 化车间特殊要求 化车间特殊要求 化车间特殊要求 支持标准 工业控制网络通用 智能制造装备集成 离散制造能效 技术要求 信息校型 数据型 智能化产品 智能制造安全保障 离散制造能效评估方法 通用技术要求 系列标准 图 数字化车间标准体系架构 其中,第一栏为标准体系中的基础标准,本标准为基础标准;第二栏为方法标准,是第四栏技术支持 类标准在数字化车间环境中的映射,是数字化车间标准建设的重点;,第三栏为应用标准,是基础标准和 方法标准在特定行业领域的应用,例如汽车制造、船舶航空、轨道交通等;第四栏为支持标准,不是数字 化车间标准的重点工作内容,但对本标准体系中第二栏的方法标准起到支撑作用
本标准主要用于离散制造领域数字化车间的新建、改建、验收和运营对于流程工业领域也具有一 定的参考价值
IN
GB/37393一2019 数字化车间通用技术要求 范围 本标准规定了数字化车间的体系结构、基本要求,车间信息交互、基础层数字化要求、工艺设计数字 化要求、车间信息交互、制造运行管理数字化要求等内容
本标准适用于指导离散制造领域数字化车间的规划、建设(新建或改建),验收和运营
规范性引用文件 下列文件对于本文件的应用是必不可少的
凡是注日期的引用文件,仅注日期的版本适用于本文 件
凡是不注日期的引用文件,其最新版本(包括所有的修改单)适用于本文件
GB/T20720.3一2010企业控制系统集成第3部分:制造运行管理的活动模型 术语和定义 下列术语和定义适用于本文件
3.1 控制图controlehart 为检测过程,控制和减少过程变异,将样本统计量值序列以特定顺序描点绘出的图
[GB/T3358.22010,定义2.3.1 3.2 详细生产排产detailedproduetionscheduling 组织和构造生产现场作业计划的集合,并对单个或多个产品的相关生产顺序进行排序
3.3 数字化车间digitalfaetory(digitalworkshop) 以生产对象所要求的工艺和设备为基础,以信息技术、自动化、,测控技术等为手段,用数据连接车间 不同单元,对生产运行过程进行规划、管理、诊断和优化的实施单元
注;在本标准中,数字化车间仅包括生产规划、生产工艺、生产执行阶段,不包括产品设计服务和支持等阶段
3.4 紧急插单emergeneyorder 在按订单生产模式下,客户订单要求的交货期早于正常生产运行需要的提前期,使得产品不能按照 常规业务流程进行生产,而采取的特殊措施
生产过程中发生产品品质问题,返工返修、补废等导致不 能按期交货,也会引起紧急插单
3.5 设备管理equipmemtmanagememt 以设备为研究对象,追求设备综合效率,应用一系列理论、方法通过一系列技术、经济、组织措施 对设备的物质运动和价值运动进行全过程管理
注1:前期管理;规划,设计,选型、购置将安装、验收
注2;后期管理;使用,维护,维修等过程
GB/T37393一2019 3.6 作业计划jobplan 根据企业季度、月度、日生产计划的具体规定,为各个工段,班组、个人,或每个工作地制定的以周、 日、班以至小时计,制造同一产品的计划
3.7 物流调度logisticsehedwling 在稀缺资源分配过程中所涉及的物流的调配 3.8 制造设备mnlaetwri eguipment 通过设备自身功能以及同其他辅助设备协同来执行车间具体生产工艺的设备
注:制造设备包括加工设备、物流设备、质量检测设备以及维护设备等
3.9 制造执行系统manufaeturingexeeutonsystenm 生产活动管理系统,该系统能启动、指导、响应并向生产管理人员报告在线、实时生产活动的情况
这个系统辅助执行制造订单的活动
[GB/T254862010,定义2.162 3.10 人机交互man-machineinteraetion 人与机器互相配合共同完成一项任务的过程
3.11 预测性维护pedictemanteanee 根据观察到的状况而决定的连续或间断进行的预防性维修,以监测、诊断或预测构筑物、系统或部 件的条件指标
这类维修的结果应表明当前和未来的功能能力或计划维修的性质和时间表
注:也称为基于状态的维修
[GB/T29308-2012,定义3.13] 3.12 生产求助productionhelp 作业工位上作业人员对发生的各种异常情况发出求助信息,提示相关人员及时处理
3.13 生产物流管理prdetionlogistiemanagement 发出实时、具体的物流指令,调度物流资源、驱动物流设备、控制物流状态,按排产计划与调度要求 为生产过程各个工位或区域,供应生产作业所需物料,保障车间生产的任务有效完成
3.14 生产现场可视化管理系统produetionsitevisalizationmanagementsystem 面向生产现场,采用电子看板、广播等技术手段,实现产品、设备、物流、生产状态,能源监管等信息 公开化,可视化,以提升现场管理水平、优化现场工作环境的管理系统
3.15 生产资源produetieresources 生产所需的除制造设备以外的制造资源 注:生产资源包括人员,元器件,成品、半成品、辅助工具等
3.16 质量控制qualittycontrol 质量管理的一部分,致力于满足质量要求
[GB/T190002015,定义3.3.7]
GB/37393一2019 3.17 维修repair 设备技术状态劣化或发生故障后,为恢复其功能而进行的技术活动
注:设备维修,包括各类计划维修和计划外的故障维修及事故修理
3.18 作业任务task 根据动态的现场情况,为作业计划分派人员、设备等资源后,下发给作业人员或设备的可执行的单 -产品的生产制造工作 3.19 可视化工艺流程管理 yisualprocessmmanagement 将制造过程各工序间流转关系及条件用计算机工艺软件进行管理,并以工艺流程图的方式进行 显示
3.20 作业工位workstaton 数字化车间里生产过程最基本的生产单元
缩略语 下列缩略语适用于本文件
AGV;自动导引运输车(AutomatedGuidedVehicde) ASN;预先发货清单(AdvancedsShippingNote) BOM物料清单(BillofMaterial puternumericalcontrol CNC:计算机数字控制机床(Compu DCA;文件控制与归档(DocumentControlandArchiving ERP;企业资源计划(EnterpriseResourcePlanning HMI;人机接口(HumanMaehinelnterface) 1/O输人/输出(Input/Output) Tehnology) IT:信息技术(Inform mation MBD;基于模型的设计(ModelBasedDesign) MEs,制造执行系统(ManufacturingExecutionsystem) MTB3F;平均故障间隔时间(MeanTimmeBetweenFailure) NC;数字控制(NumericealControl )verallEquipmentEffectiveness OEE:整体设备效率(Over PDA;生产数据采集(Produ DataAcquisition 1ct1Om rammableIogicControler PIC;可编程序控制器(Prog" PLM:;产品生命周期管理(ProductLifecycleManagement) PDM:产品数据管理(Pr ProductDataManagement PDCA;计划执行检查行动(Planm Check,Act equistion) SCADA:监控与数据采集(SupervisoryControlAndDataAe SIL;安全完整性等级(SafetylntegrityLevel sPC;统计过程控制(StatisticalProcessControl sQL;结构化查询语言(StrueturedQuevyL.anguage) RFID;射频识别技术(RadioFrequeneyldentification) RGV:有轨制导车辆RailGuidedVehicle)
GB/T37393一2019 ransmissionControlProtocol/Inm Protocol TCP/IP;传输控制协议/互联网协议(Tra Internet VPN;虚拟专用网络(VirtualPrivateNetworks) wLAN;无线局域网络(wirelessL.ocalAreaNetworks) wMS;仓储管理系统(warehouseManagementSystem) 5 体系结构 数字化车间重点涵盖产品生产制造过程,其体系结构如图2所示,分为基础层和执行层
在数字化 车间之外,还有企业的管理层(不在本标准范围内)
数字化车间应用案例可参见附录A,产线设计可参 见附录B 数字化车间的基础层包括了数字化车间生产制造所必需的各种制造设备及生产资源,其中制造设 备承担执行生产、检验、物料运送等任务,大量采用数字化设备,可自动进行信息的采集或指令执行;生 产资源是生产用到的物料、托盘、工装辅具,人、传感器等,本身不具备数字化通信能力.但可借助条码 RFID等技术进行标识,参与生产过程并通过其数字化标识与系统进行自动或半自动交互
数字化车间的执行层主要包括车间计划与调度、生产物流管理、工艺执行与管理、生产过程质量管 理、车间设备管理五个功能模块,对生产过程中的各类业务、活动或相关资产进行管理,实现车间制造过 程的数字化、精益化及透明化
由于数字化工艺是生产执行的重要源头,对于部分中小企业没有独立的产 品设计和工艺管理情况,可在数字化车间中建设工艺设计系统,为制造运行管理提供数字化工艺信息
本标准仅包含最基础的功能模块,可根据实际情况增加其他模块,如能效管控系统、生产安全管理 系统等,参见附录C和附录D
数字化车间信息处理方式可参见附录E
企业资源计划 产品生命周期管理 管理层 企业 企业 信息 信息 交互 造运行管理 工艺 车间计划与调度 工艺执行与管理 生产物流管理 执行层 设计* 生产过程质量管理 车间设备管理 车间 车间 信息 信息 交互 交互 基础层 制造设备 生产资源 图例 数字化车间 数字化车间 数字化车间 具备的功能 之外的功他 可选功能 图2数字化车间体系结构图
GB/37393一2019 数字化车间各功能模块之间主要数据流如下(见图3) 系统从企业资源计划承接分配到车间的生产订单,在车间计划与调度模块依据工艺路线分解 为工序作业计划,排产后下发到现场
工艺执行与管理模块指导现场作业人员或者设备按照数字化工艺要求进行生产,并采集执行 反馈给车间计划与调度
若生产过程出现异常情况,不能按计划完成,需敏捷协调各方资源, 通过系统进行调度以满足订单需求
工艺执行过程中若需进行检验控制,由生产过程质量管理模块将检验要求发送给检验员或检 验设备执行检验,并采集检验结果,进行质量监控和追溯
生产现场需要的物料,根据详细计划排产与调度结果,发送相应物料需求给生产物流管理模 块,由仓库及时出库并配送到指定位置;生产完成将成品人库,实现生产物料的管理、追踪及 防错
-生产执行过程的工艺执行、质量控制等结果反馈到车间计划与调度,进行实时监控及生产调 度,并形成完工报告反馈到更高一层企业资源计划
-数字化车间中大量的设备运维,通过车间设备管理模块统一维护,提醒和指导设备人员定期保 养,记录维修保养结果
设备维保计划与工序作业计划需相互协调,以保证生产正常进行
采购库存 车间生产计划生运行 物料消耗 等信息 /车间订单 结果反惯 物料需求 送反馈 车间计划与调度 生产物流管理 作业计划 执行反锁 数字化工艺信息 工艺执行与管理 质量控 检验指令 结果反馍 -质量要求及皮锅 生产过程质量管理 车间设备管理 制造过程质量信息 检验参数 检验数据 设备运行参数 制造设备 生产资源 图3数字化车间数据流示意图 基本要求 6.1数字化要求 数字化车间的资产和制造过程信息应数字化
GB/T37393一2019 数字化要求主要包括如下方面: -制造设备数字化;数字化车间的制造设备数字化应符合7.1的要求,数字化设备的比率应不低 于70%
各行业可根据各自身特点规定相应行业数字化车间制造设备的数字化率
生产信息的采集;:90%的数据可通过数字化车间信息系统进行自动采集
生产资源的识别应能对数字化车间制造过程所需要的生产资源的信息进行识别
生产现场可视化;可通过车间级通信与监测系统,实现车间生产与管理的可视化
工艺设计数字化;数字化车间的工艺设计宜采用数字化设计方法,符合第8章要求
6.2网络要求 数字化车间应建有互联互通的网络,可实现设备、生产资隙与系统之间的信息交互 6.3系统要求 数字化车间应建有制造执行系统或其他的信息化生产管理系统,支撑制造运行管理的功能
6.4集成要求 数字化车间应实现执行层与基础层、执行层与管理层系统间的信息集成
6.5安全要求 数字化车间应开展危险分析和风险评估,提出车间安全控制和数字化管理方案,并实施数字化生产 安全管控
基础层数字化要求 7.1制造设备的数字化要求 制造设备的数字化要求包括 应具备完善的档案信息,包括编号、描述、模型及参数的数字化描述; 应具备通信接口,能够与其他设备,装置以及执行层实现信息互通; 应能接收执行层下达的活动定义信息,包括为了满足各项制造运行活动的参数定义和操作指 等; 令 应能向执行层提供制造的活动反馈信息,包括产品的加工信息、设备的状态信息及故障信 息等; 应具备一定的可视化能力和人机交互能力,能在车间现场显示设备的实时信息及满足操作的 授权和处理相关的人机交互
数字化制造设备的典型配置与功能要求参见附录C
7.2生产资源的数字化要求 生产资源的数字化要求包括 在条码及电子标签等编码技术的基础上满足生产资源的可识别性,包括生产资源的编号、参数 及使用对象等的属性定义; -上述信息应采用自动或者半自动方式进行读取,并自动上传到相应设备或者执行层,便于生产 过程的控制与信息追溯 -识别信息可具备一定的可扩展性,如利用RFID进行设备及执行层的数据写人
GB/37393一2019 工艺设计数字化要求 根据生产过程需求,数字化车间的工艺设计宜采用数字化设计方法,并满足以下要求 采用辅助工艺设计,如三维工艺设计 能进行工艺路线和工艺布局仿真 能进行加工过程仿真和/或装配过程仿真; 建立工艺知识库,包括工艺相关规范成功的工艺设计案例,专家知识库等; 提供电子化的工艺文件,并可下达到生产现场指导生产; 向制造执行系统输出工艺BOM 车间信息交互 9.1通信网络 为执行数字化车间基础层的工作任务处理,实现控制设备与现场设备之间的通信,可采用如下通信 方式 -现场总线:可采用PROFIBUS,CC-IINK,MODBUS,CAN等协议; 工业以太网通信;可采用PROFINET,Ethernet/IP,EtherCAT,POwERRLINK等协议; -无线通信:工业无线(wIA-FA、wIA-PA)、wIFI、蓝牙,3G/4G/5G等协议
9.2数据采集与存储 数字化车间应在企业数据字典定义的数据采集内容基础上,结合数据的实时性要求,利用合理的网 络通信方式与数据存储方式进行数据的采集与存储,并与企业级数据中心实现对接
包括 应能对车间所需数据进行采集、存储和管理,并支持异构数据之间的格式转换,实现数据互通
a D)宜采用实时数据库与历史数据库相结合的存储方式: 实时数据库;采集和储存生产现场实时性较高的数据,支持执行层的各项应用,如OEE统 计等; 22 历史数据库:宜采用关系数据库,采集和储存工艺设计和制造过程所需的相关主数据及过 程数据
应具备信息安全策略,并支持更新和升级.如访问与权限管理、人侵防范、数据容灾备份与恢 复等
9.3数据字典 数字化车间应建立数据字典,具体要求如下 包括车间制造过程中需要交互的全部信息,如设备状态信息、生产过程信息物流与仓储信息、 检验与质量信息、生产计划调度信息等 描述各类数据基本信息,如数据名称、,来源、语义、结构以及数据类型等; 支持定制化,各行业可根据各自特点制定本行业的数据字典
10制造运行管理数字化要求 10.1基本要求 数字化车间制造运行管理各功能模块应满足以下基本要求
GB/T37393一2019 -能与数据中心进行信息的双向交换 -具有信息集成模型,通过对所有相关信息进行集成,实现自决策; -模块间能进行数据直接调用; -模块能与企业其他管理系统(如ERP,PDM等)实现信息双向交互
10.2车间计划与调度 0.2.1信息集成模型 车间计划与调度的功能模型及与主要数据流见图4
其中,虚框中为生产计划与调度的功能,包括 详细排产、生产调度、生产跟踪,其主要业务流程如下 -数字化车间从企业生产部门获取车间生产计划或通过接口自动接收ERP系统的生产订单), 根据生产工艺形成工序作业计划,根据生产计划要求和车间可用资源进行详细排产,派工 -将作业计划下发到现场,通过工艺执行管理模块指导生产人员/或控制设备按计划和工艺进行 加工 生产执行过程中,实时获取生产相关数据、跟踪生产进度,并根据现场执行情况的反馈实时进 行调度; -根据生产进度偏差对未执行的计划重新优化排产,并将生产进度和绩效相关信息反馈到企业 生产部门或ERP系统,完成车间计划与调度的闭环管理
车间计划与调度应支持可视化信息管理,即通过车间生产流程监测.控制系统反馈的信息.以可视 化看板的形式展现生产计划执行的节拍、工艺调整、指挥调度、物流(车间级)、产成品等信息,以辅助人 员在线实时地监控、参与、调整生产计划
企业资源计划 生产运行 车间生产计划/ 业 纱区继 车间计划与调度 车间设备管理 一-计划与调度信息 详细排产 作业计划 -运维计划- -生产进度 生产跟踪 生产物流管理 -物料需求 生产调度 -调度信息 执行反馈 -配送反惯 -作业计划 工艺执行与管理 图4车间计划与调度信息集成模型 10.2.2功能要求 10.2.2.1 详细排产 为满足车间生产计划要求,通过详细排产,根据产品工艺路线和可用资源,制定工序作业计划
排 产的过程需综合考虑当前计划完成情况、车间设备等资源可用性、实际产能及节省能源等因素,生成基 于精益化生产理念的、.以柔性制造为目标的生产排产计划
详细排产的具体功能要求见GB/T30720.3
GB/37393一2019 2010中6.6 详细排产应根据产品生产工艺制定工序计划,考虑车间设备管理、生产物流管理中设备、人员、物料 等资源的可用性进行计划排产,形成作业计划发送给生产调度
另外,排产生成的作业计划也会反馈影 响生产设备,人员、物料等生产要素的管理,比如,与设备维护保养计划相互影响
对于多品种小批量生产模式,由于从一批产品转到另一批产品生产要花费时间调整设备、更换模具 等,传统车间以减少换产次数的方式安排生产
随着多功能加工中心,柔性生产线等智能装备的提升 以及准时配送、成套配送等新物流方式的支持,数字化车间中多品种小批量生产的详细排产应实现均衡 化生产,包括 -生产总量的均衡;将连续两个时间段之间的总生产量的波动控制到最小程度,减少生产量波动 造成的设备、人员、库存及其他生产要素的高配置浪费; 产品品种数量的均衡;在生产期之间,合理安排不同产品的投产顺序和数量,消除不同品种产 品流动的波动,减小对前序工序和库存的影响
对于柔性生产线,应能实现均衡化混线生产 多品种小批量的均衡化车间计划,需与其他车间生产要素的管理相配合,最终应能达到如下效果 -能够快速地适应每月中每天的市场需求的变化,为准时化的实施提供强有力的支撑; 成品库存数量保持较低水平,并且可以及时满足客户的需求 可以使工序间的在制品数量减少到最低,并可以进一步消除,实现“零库存” 对于单件生产模式,产品品种多而每一品种生产数量很少,产品生产重复性差,生产技术准备时间 长,设备利用率较低
数字化车间中单件生产的详细排产应基于瓶颈理论,确定某时间段内的瓶颈资 源,并根据瓶颈资源排产,提高资源利用率及有效产出
10.2.2.2生产调度 为了实现作业计划的要求,通过生产调度分派设备或人员进行生产,并对生产过程出现的异常情况 进行管理
详细功能要求见GB/T20720.3一2010中6.7
数字化车间的生产调度应能实时获取生产进度、各生产要素运行状态,以及生产现场各种异常信 息,具备快速反应能力,可及时处理详细排产中无法预知的各种情况,敏捷地协调人员、设备、物料等生 产资源,保证生产作业有序、按计划完成
获取生产现场状况的方式包括设备实时数据,通过数字化工 位、可视化管理系统获取的各种生产过程信息
生产调度处理的异常情况主要包括 市场需求波动引起的紧急订单,下达到车间成为紧急插单,影响已安排的其他正常生产计划, 需采取相应措施满足计划要求: 生产计划已安排或投产后,发生客户临时变更订单要求,需采取相应措施满足要求 生产过程中进行质量检验发现不合格情况,导致返工返修需进行生产调度; 设备故障、人员等发生异常情况,采取相应措施保证生产继续进行 若异常事件导致无法通过调度满足计划要求,则需通过详细排产重新进行优化排产 10.2.2.3生产跟踪 生产跟踪包括为企业资源计划作生产响应准备的一系列活动,如总结和汇报关于产品生产中人员 和设备的实际使用、物料消耗、物料生产以及其他如成本和效益分析需要的有关生产数据信息
生产跟 踪还向详细生产排产、以及更高层的企业生产计划提供反馈信息,以使各层计划能根据当前情况进行 更新
数字化车间的生产跟踪应能自动获取生产相关数据,统计产品生产中各种资源消耗,并反馈给相关 功能/系统/或部门
生产相关数据的获取来源,包括从数字化接口(数字化设备或工位)直接采集到的, 或者经过其他功能模块加工过的信息
GB/T37393一2019 0.3工艺执行与管理 0.3.1信息集成模型 工艺执行与管理信息集成模型如图5所示,主要包括工艺执行与工艺管理两部分
工艺执行由车 间子计划/物料清单生成,派工单生成、作业文件下发等构成,工艺管理由工艺权限管理、工艺变更管理 可视化工艺流程管理等构成
工艺执行贯穿于计划质量、物流、设备等全生产过程中;工艺管理功能可 以在PDM,ERP,MES等相关系统中实现,工艺文件以计算机系统可识别的数据结构呈现
车间计划与调度 -数字化工艺信息 作业计划 执行反馈 工艺执行与管理 车间设备管理 -设备需求 派工单生成 -生产/质检数据 数据采集 生产物流管理 -物料需求- -作业执行助理 派工单 -检验指令 作业文件下发 标准工艺参数/作业程序下传 生产过程质量管理 -工艺参数/作业程序 作业执行指令 制造设备/生产资源 -执行反馈 -质景控制结果反馈- 图5工艺执行与管理信息集成模型 10.3.2功能要求 工艺执行 10.3.2.1 通过工艺的数字化与车间系统的网络化,实现作业文件、作业程序的自动下发和标准工艺精准执 行;通过生产和质检数据,现场求助信息采集,反馈工艺执行实时状态和现场求助信息,实现产品生产工 艺的可追溯与现场求助的快速响应
具体功能包括: -物料清单生成 根据产品BOM与作业计划,自动分解生成物料清单,实现生产计划细分、,物料提前备料、工序流转 自动采集、工位物料智能化配送等
-派工单生成 根据生产工艺过程,将车间子计划分解为各工序的派工单
各工序根据产品BOM、生产工艺过 程、日派工单实现生产前物料备料,车间根据产品BOM、生产工艺过程、标准工时等实现各派工单智能 化调度
作业文件下发 将各种工艺卡、工艺图纸、作业指导书等作业文件自动下载到各作业工位终端,现场作业人员可通 过工艺编码或生产计划号、工单号实时查询标准工艺参数、标准质检工艺、作业指导等工艺信息
10
GB/37393一2019 标准工艺参数、作业程序下传 通过以太网或总线方式将标准工艺参数自动下发到对应机台,防止由于人为因素导致现场机台工 艺参数设置错误
作业程序可以自动下传到现场数字化装备实现自动加工或装配等作业
数据采集 进行工艺信息在线交互式浏览、物料校验及开工条件检查 实时记录和上传生产现场出现的工艺技术问题和处理方法; 实时采集生产过程中的工艺参数,向质量控制系统提供生产,质检数据,实现生产过程质量预警,并 通过与生产现场可视化管理系统等进行集成,实现预警信息及时发布; 求助终端实时采集生产求助信息,向生产现场可视化管理系统提供现场求助信息,以便现场作业工 位获得快速响应 及时将作业指令状态信息与作业工位状态信息向系统反馈
10.3.2.2工艺管理 数字化车间应实现以工艺信息数字化为基础,借助一体化网络与车间作业工位终端实现无纸化的 工艺信息化管理;并以可视化工作流技术,实现制造流程再造、工序流转和调度的数字化管控以及工艺 纪律管理
具体功能包括 工艺权限管理 工艺执行权限主要实现组织结构管理、人员管理、访问规则管理等
一般情况下,组织结构由 Group(组别,Role(角色),User(用户)和Person(人员)构成
通过访问规则的定义,来实现对用户操 作权限的控制,控制用户,角色、工作组对数据仓库或具体文档的操作权限
根据岗位职责要求进行相应权限分配,对应授权人员可进行相关工艺的上传、下载,查询、修改等
工艺变更管理 主要实现工艺变更、工艺优化数据版本管理等
工艺变更应符合标准变更工作流程以及控制、跟踪 机制,结合产品数据的状态管理,可以在规范管理更改过程、保证更改的可追剖性的同时提供准确、及 时的更改传递机制,保证更改结果的正确性和一致性
-可视化工艺流程管理 通过可视化工艺流程实现工序间流转管理,并对工艺流程中各工序点进行属性设置,快速实现数字 化车间生产流程再造,实现数字化车间生产工艺流程快速切换
作业文件管理 作业文件包括生产流程工艺、工艺卡、工艺图纸、质检工艺标准卡、标准工艺参数卡等,并以版本号 区别
作业程序管理 作业程序通过工艺编码或生产计划号、工单号与数字化装备关联,并以版本号区别
-工艺优化管理 对采集的机台工艺参数的实际值或质检数据,进行统计分析、预警,实现工艺优化
生产求助管理 工位上作业人员针对工位发生的各种问题发出求助呼叫信息.上传生产现场可视化管理系统,可触 发声光报警、显示终端、广播等,提示相关人员注意,以便及时处理问题
0.4生产过程质量管理 0.4.1信息集成模型 生产过程质量管理各功能之间及与外部功能子系统之间的信息集成关系描述,如图6所示
1
GB/T37393一2019 生产过程质量管理 工艺、标准改进 工艺执行与管理 检测、判定标准 质量改进 开uk这然外鼎丽 质量统计、分析与评价 分析结果 -监测数据- -判定数据" 质量监控 质量检测与判定 -检测及判定结果 质量数据 过程监测数据 质量数据采集 质量追溯 质量采集数据 控制指令 设备控制系统、数据采集系统 图6生产过程质量管理信息集成模型 10.4.2功能要求 0.4.2.1质量数据采集 质量数据主要包括生产设备工艺控制参数,质量检测设备检测结果、人工质量检测结果等生产过程 数据,覆盖原材料、零部件、半成品和成品
数字化车间应提供质量数据的全面采集,对质量控制所需的 关键数据应能够自动在线采集,以保证产品质量档案的详细与完整;同时尽可能提高数据采集的实时 性,为质量数据的实时分析创造条件
10.4.2.2质量监控 10.4.2.2.1 指标监控 应对过程质量数据趋势进行监控,并对综合指标进行统计监控
过程质量数据趋势监控;主要用于独立质量指标的原始数据监控,具有采集频率高、实时性强的特 点,通过设定指标参数的报警界限,对超出界限的数据及时报警
通常由生产组态软件开发实现,以趋 势图为主要展现形式
综合指标统计监控;主要用于基于原始数据的综合质量指标的统计监控,可以融合多种监控标准和 统计算法对指标进行综合运算,并定时刷新,使监控更宏观,更有针对性
通常由MES或独立质量系 统开发实现,以SPC控制图、预控图、仪表盘等为主要展现形式
0.4.2.2.2质量监控预报警 应基于实时采集海量质量数据所呈现出的总体趋势,利用以预防为主的质量预测和控制方法对潜 在质量问题发出警告,以避免质量问题的发生
以采用SPC工具进行监控为例,其具有八种标准的判 异准则,可以基于判异规则对质量数据进行监视,对发现的异常情况应及时预报警与处理
10.4.2.3质量追溯 以产品标识(生产批号或唯一编码)作为追溯条件,以条码及电子标签为载体,基于产品质量档案 以文字,图片和视频等富媒体方式,追溯产品生产过程中的所有关键信息;如用料批次、供应商、作业人 员、作业地点(车间、产线、工位等)、加工工艺、加工设备信息、作业时间、质量检测及判定,不良处理过 程、最终产品等
12
GB/37393一2019 0.4.2.4质量改进 针对生产过程中发现的质量缺陷,应基于PDCA循环原则构建质量持续改进机制,固化质量改进 流程,提供质量异常原因分析工具,并不断积累形成完备的质量改进经验库
0.5生产物流管理 10.5.1 信息集成模型 数字化车间中的所有物料、刀具,量具、车辆、容器/托盘等都应进行唯一编码
应能自动感知和识 别物流关键数据,并通过通信网络传输、保存和利用
生产物流管理信息集成模型见图7
工艺执行管理 车间计划与调度 产品工艺 排产与调度计划 配送反饿 物料需求 生产物流管理 车间库存管理 -采购/配送需求 生产管理规范 物流规划 库存信息 物流规划执行反馈 出入库信息 物流调度及优化 训度指令 物料领取与配送 发料信息 收料及物料 异常反锁 基础层 制造设备 生产资源 图7生产物流管理信息集成模型 10.5.2功能要求 10.5.2.1 物流规划 物流规划的依据是车间计划与调度指令要求,并应遵守下列约束条件 -时间;基于物流规划中规定的时间条件,以及制造执行计划中的批次、路线及起始-到达的区位 要求,设置合理、可行的物流起始时间、运行路线和到达时间 -装载;基于车间环境与实施条件和工艺执行计划要求,确定各次物流运转所应装载的物料或在 制品
凡进人物流计划的物料均应编码,并在物料本体上附加数字化标识,标识的编码结构应符合企业产 品生命周期管理信息结构要求
物流规划应输出相应的信息文件,内容包括;物流运行的物件数量、批次组合、物流路线、物料需求 13
GB/T37393一2019 时间和送达时间等基本信息
物流方案应使物流批量与工艺指令相匹配,合理安排转序时间间隔,用准 确的物料流量来满足工艺执行岗位操作需要
10.5.2.2物流调度及优化 物流调度主要包括如下内容: 事前调度,针对供应链采购进厂物流进度及其产品信息和质量状况,按照事先设计的处理流程 应对物流计划内容的插人变更 事中调度,针对较大批次生产任务对物流计划的影响,基于生产进度执行原则和精益库存管理 原则,合理调配物流时间和运输批次,保持物流与各工艺执行工位的进度同步; -事后调度,在发生外来扰动(如插单、换单等)时,快速启动物流响应,以减轻外来扰动对生产进 度的影响,满足客户需求
调度优化主要包括如下内容 充分利用物联感知技术,获取物流调度作业执行过程中的现场实时数据,以验证当前调度执行 的流程是否合理、节约和高效 基于规定的车间时钟时间,预先制定可多时间段分散并行的物流作业方案,以应对外来扰动所 引发的制造执行指令变更,并避免时间和物理资源的浪费 积累生产过程运行管理知识,逐步形成基于制造执行系统指令的最佳物流方案 数字化基础条件好的企业,应引人虚拟化技术以提高生产物流的可视化程度,为工艺过程的仿 真试验、验证分析和节拍预测/调整提供决策支持
10.5.2.3物料领取与配送 在车间运输与库存系统的基础上,为了配合车间物流调度而进行的实物形态的运输、存储等活动 包括在仓库内外的运输活动(包括调库、移库等)进行物料领取与配送
如图8所示
物料编码 车间库存执行 -物料信息" 库存转移订单 车间运输系统定义 -路径信息
运输订单 车间仓储系统定义 -存储位置信息 运输指令运输状态反馈 物流设备 图8物料领取与配送接口示意图 在具体物流调度的需求下,车间物料请求(包括具体的物料、数量以及配送地点等)通过设备、现场 执行层或者制造执行系统提交给车间物流管理系统
借助于自动化物流设备和车间物流布局,车间物 流管理系统产生相应的物流配送作业并将指令发送给对应的车间物流设备并指导该设备完成物流作业 任务并反馈给车间物流管理系统
14
GB/37393一2019 必要时,应有一定的防错措施,用文字,语言、标识和必要的物理装置来警示、限制或隔离人的行动 及其功能作用,防止人对材料、物体和设备实施错误或不当的触摸、尝试、操纵,移动或变更
10.5.2.4车间库存管理 数字化车间的库存管理应是基于不同库存活动对车间物料形态,数量,状态等属性变化进行记录、 追溯与分析等活动
可借助于信息化手段与自动化技术,使其变得更加精确和透明
主要包括库存数 据采集与追溯、库存分析 库存数据采集是指对于库存运营和物料操作信息的汇集和报告的一系列活动
库存追溯是建立在库存历史数据基础上以满足第三方系统和企业内的查询、验证等活动
车间库 存与企业资源计划应交互库存移动、状态等信息
在企业资源计划中建立库存管理体系
在企业层对 库存管理进行企业级别库位定义、库存移动规则定义等(包括库位间不同库存类型和状态、以及库位与 库位之间)
库存移动信息一般包括 -从仓库到产线的原材料准备 生产订单状态更新,包括生产订单的执行,更改和取消等; 车间发生的非符合型成本,比如由于人为、设备和技术原因导致的原材料报废和不良品报 废等; 其他库存转移,包括: 退仓;由于生产计划的变更,多余原材料退回仓库; 退还给供应商:将车间有问题的物料转移到收货环节进行供应商退货处理
库存分析是指为了库存操作的持续改善而对于库存效率以及资源利用率进行分析的一系列活动, 如在收货环节通过提供的收货数量差异与交付时间来进行原材料供应商评估 0.6车间设备管理 0.6.1信息集成模型 车间设备管理主要功能包括设备状态监控、设备维修维护和指标运行分析
各功能之间及与外部 功能子系统之间的信息集成关系描述如图9所示 车间设备管理 设备图纸、技术资料 设备台账管理 设备维修维护 -设备运维计划 车间计划与调度 维修维护数据 维修维护指令 监控指标 设备状态监控 -监控数据 指标运行分析 设备状态数据 设备控制系统、数据采集系统 图9车间设备管理信息集成模型 15
GB/T37393一2019 0.6.2功能要求 10.6.2.1设备状态监控 10.6.2.1.1设备运行数据采集 通常由设备控制与数据采集系统实现,应能自动在线采集反映设备状态所需的关键数据
对于不 同类型的设备,数据采集方式也不同,如对于具有以太网等标准通讯接口的设备,可以直接按相应接口 协议采集;对于没有通讯接口的设备,可以通过增加专用采集终端进行采集
数据采集信息一般应包括 设备状态信息 设备状态起始时间信息; 设备运行及空闲时间 设备故障信息 设备报警信息; 设备加工及运行参数信息
0.6.2.1.2设备状态可视化 设备状态信息应采用图形化展示方式
对于具有建模需要的关键设备,应按照设备图纸构建数字化模型,结合采集数据准确模拟设备的实 时运行状态,并能够按照设备结构实现部件级的分解查询
从而增强设备监控的可视化效果
10.6.2.1.3基于事件的设备状态异常预警 依据设备运行标准和要求,应对指标参数的监控结果进行分析和判定,对有异常变化趋势的情况进 行预警,对发生异常或故障的情况进行报警
预警和报警信息应按照异常等级与类型及时通知到相应的监控人员,并采用多种形式相结合的通 知方式,如现场监控屏幕显示、报警灯声光报警、系统级消息通知、短信通知等
10.6.2.2设备维修维护 10.6.2.2.1概述 应建立以设备维修维护计划制定、工单分配、下发执行,反馈为流程的标准化维修维护体系,以计 针 划工单为主要管理形式,利用智能移动终端(如手持PDA.平板电脑)完成维修维护的执行和反馈
对典型故障,提供维护维修的经验库,能够基于采集的设备状态进行自诊断;对于维修过程,提供图文、 视频等标准作业指导,确保设备安全稳定运行
0.6.2.2.2周期性维护 根据设备类型制定相应的周期性维护计划,基于配置信息自动生成维护工单,并通知和下发给相应 岗位人员,通过执行工单的反馈信息跟踪执行状态
10.6.2.2.3预测性维护 基于对设备运行数据,特别是设备运行日志文件数据的分析,对设备的运行状态进行有效评估,进 而动态、及时地发现设备运行的潜在异常情况,并生成具有针对性的维护方案
针对设备关键零部件,能够结合其理论使用寿命和实际运行参数状态,对零部件的更换时间做出及 16
GB/37393一2019 时提醒,对超期使用的零部件做报警
10.6.2.2.4设备故障管理 设备故障管理内容如下 故障分类管理;依据管理要求,可以对故障类型按不同角度进行配置,形成类型编码与名称的 对应存储关系
如按故障发生的部位可划分为机械故障和电气故障,按故障来源可划分为人 为故障和非人为故障等 故障树管理:依据车间设备实际情况,建立设备、故障类型,故障部位,故障名称的故障树存储 结构,形成可配置的故障信息维护体系
故障分析与经验库:利用可视化分析工具,对故障现象进行原因分析,为分析人员提供故障诊 断方案
基于日常故障处理经验,建立并维护故障案例库和处理经验库,为故障处理人员提供 故障解决方案
故障处理:按照故障分析结果,以电子工单的方式对故障的处理流程进行管理,保存故障处理 的过程记录
10.6.2.3设备运行分析 基于设备实时状态采集和维护维修过程中搜集的过程数据,自动统计分析与设备相关的指标,主要 包括设备完好率,.设备利用,设备故障率、停机《或停产)时同.停机(或停产)次数、设备平均故障间临 时间(MTBF)等
注:不同类型设备的统计指标及计算方法不尽相同,按实际管理需求进行选择
17
GB/T37393一2019 附 录 A 资料性附录) 典型电气产品数字化车间应用案例 概述 A.1 数字化车间是数字化、网络化技术在生产车间的综合应用,它将制造设备与工艺设计系统、生产组 织系统和其他管理系统的信息进行集成,形成综合信息流的集成制造系统
从整体上改善生产的组织 与管理,提高制造系统的柔性,提高数字化设备的效率
本附录通过一个典型的数字化电气产品生产车间实例,展示数字化车间的实现方案及关键节点
在车间建设中,数字化制造起着非常重要的作用,提供从产品设计、工艺编制,车间计划到产品的整个加 工过程的生产活动的信息化管理
它采用当前的、精确的数据,对生产活动进行初始化,及时引导,响应 和报告车间的活动,对随时可能发生变化的生产状态和条件做出快速反应,重点削减不产生附加值的活 动,从而有效的推动车间运行
数字化制造改善运行设备的回报,并改善及时交货、库存周转,毛坯和现 金流通性能
通过双向通信,提供整个企业的生产活动以及供应链中以任务作为关键因素的信息
A.2实现方案 A.2.1体系架构 体系架构如图A.1所示 A.2.2功能和要求 实现功能:本数字化车间订单管理模块从企业资源计划承接分配到车间的生产订单,由排产模块根 据工艺路线分解为工序作业计划,排产后下发至生产现场工艺管理模块指导现场作业人员或设备按照 数字化工艺要求进行生产,工艺执行过程中,若需进行检验控制,由质量管理模块负责质量的监控和追 溯,生产需要的物料由物流管理模块负责分配,生产过程中的大量设备,通过设备管理模块进行统一管 理
生产过程中的工艺执行、质量控制等结果将会反馈到排产模块,进行实时的监控与调度,并形成报 告反馈至更高一层的企业资源计划系统
数字化要求;数字化车间的资产和制造过程信息应能够转变为被计算机识别的信息,主要包括设备 的数字化、生产资源的可识别、数据信息的可采集以及生产现场的可视化
网络要求;数字化车间的网络通信,实现设备、生产资源与系统间的互联互通
集成要求;数字化车间应能实现执行层与基础层、执行层与管理层系统间的信息传输与集成
安全要求;数字化车间应提出车间的安全控制和数字化管理方案,并实施数字化生产安全管控
18
GB/37393一2019 企业资源计划系统ERP 产品生命周期管理(PLMD 工艺管理 质量管理 排产管理 设备管理 订单管理 物流管理 来料检临 物料清单生成 设备分类 订单查询 看板系统 排产分配 派工单生成 过程检验 订单跟踪 执 信息采集 自动排产 智能仓储 作业文件下发 投诉管理 人工排产c 订单统计 物料识 设备控制 工艺权限管理 数据采集 维护计划 订单控制 工具管叫 容器管理 质量分析 工艺变更管理 订单池 数据监控 状态监控 库存分析 制造运营管理(MOM 车间 信息! 高性能注塑机 自动化装配机 智能工作站 集成设 础 组合机床 模具RFID 智能小车 智能打印 制造设备和生产资源 图A.1数字化车间体系架构 A.3基础层数字化 A.3.1制造设备的数字化 A.3.1.1数字化功能 制造设备的数字化功能主要分为数据采集和操作功能两部分 数据采集:对制造设备进行数据采集和分析,对制造进度、现场操作、质量检验、设备状态等生 a 产现场信息进行采集和跟踪,并对这些信息进行分析
数据采集的接人主要采用如下方法;条形码阅读器采集工件码标,经可编程控制器转换为可识别数 据,并通过Profinet/Profbus-DP,上传到车间MES系统sQL数据库;材料托盘全部带有RFID标签 由读出/"写人设备与PlC相联,再连接到MES系统;AGV小车,下料、切割、注塑,装配设备全部采用 PIC为控制核心的自动化设备,通过光电(光电开关、编码器)、磁感应、霍尔效应、热阻、图像识别、语音 等方式采集数据,并将工件、设备、人员、物料等信息上传给MES系统,车间设备的电压,电流、相位,功 率因索等能效参数也通过PLC采集上传给MES系统
b操作功能;MES系统负责制造设备的执行管理如订单信息、排程管理、生产信息统计、资源信 19
GB/T37393一2019 息以及HM信息;设备及生产信息、报警信息、作业及维修指导等信息
A.3.1.2网络构成与接口 PROFINET的实时通道和等时同步通道可以实现毫秒级到微秒级的响应速度,已被工业自动化业 界广泛采用
本系统采用开放实时以太网的一网到底结构,从底层1/0现场层到设备之间连接的控制 层,再到管理层MES、ERP等全部采用PROFINET实时工业以太网,包括线缆、光纤传输的 PROFINET技术,无线wI.AN传输的PROFINET技术
整体网络架构如图A.2所示
ERP MES 工业云 主服务器操作终端 打印机 数据中心 磁盘阵列 工作站 防火墙 CPIP OPcUA 防火墙交换机 oRcUA iPofinet lProfinet FV系森 Profinet |Proinet PG PC PLC IoPcU oPCU4 HMI HM们 ORcU MI 无线通讯 lProfine IProinet Profiner 安全桥 安全桥 安全桥 Proinet Pronet Profinet 远程o 远程o 远程o IProfinet 阀岛 Proinet 阀岛 Proffnet KaV小车 而间岛 Prone Profinet Profnet ..**# 注塑机 包装机 图A.2网络架构 PROFINET兼容TCP/IP协议的实时以太网,能满足过程控制、工厂自动化和运动控制实时通信 要求,已有的系统无需修改就能集成到PROFINET中,系统具有高度开放性和兼容性,为系统拓展提 供了接口,如CNC设备、机器人,RFID视觉系统、视频监控等
本案例车间已经建成了以工业交换机和工业无线AP为接人设备,并与公司办公网络有机集成的 工业以太网
通过有线的、,无线的连接,车间中的生产设备能够与网络相连,并将相关的数据传输到 MES系统中
A.3.1.3集成要求 对数字化智能制造设备的系统构成以及内在逻辑关系进行至上而下的梳理和分析,如图A.3 所示 20
GB/37393一2019 大批量产品定制 个性化客户服务 业务层 订单 智能化生产线 运作层 柔性化 可重构 精益化 敏捷化 数字化 信息系统 自动化 均衡淋 生产过程 加工参 上下料 流生产 数优化 实时监控 PDM:数据管那 功能系统 ERP:生产计划 MES:生产控制 数字化物 在线高精 设备故障 流跟踪 度检测 自动预警 自动化 柔性化 智能化 传憾 通信 功能单元 网络 软件 设备 工装 网络 传感技术,模块化、嵌八式系统设计技术,先进 控 写化技 系统协同技术,故障诊断与健 支撑技术 康维野技来,高可幕实时遥信网络技木,功能安 全技术,特种工艺与精密制造技术,识别技术 图A.3制造设备的系统集成 该架构主要包括业务层、运作层、功能系统、功能单元、支撑技术五个层次
各个层次相辅相成,紧 密联系,其中系统以需求订单为输人,以信息系统为核心,集成自动化上下料等多个子功能系统,以基本 功能单元及支撑技术为依托,推动智能制造生产线的正常运作,实现大批量产品的生产或小批量个性化 产品的定制服务,满足客户和市场的需求
A.3.1.4功能安全 设备的安全性能由机械安全防护和电气安全控制两方面组成
除了机械安全防护外,从电气安全 控制的角度,一套安全控制系统由安全输人设备,如紧急停止按钮、安全门锁、安全激光扫描仪、双手按 钮、安全地毯等;安全控制模块如安全继电器、安全桥,安全PLC,安全网络;和被控输出元件,如主接触 器、阀等三部分组成
本数字化车间根据车间个设备区域安全系统的规模大小来选择相应的方案,具体如下 简单的单功能安全应用,如急停按钮,采用单功能的安全继电器
对于2个3个安全功能的应用,如一个急停按钮、一个安全门锁和一个安全光幕,可选择多功能 的安全继电器,即简化接线、减少安装空间,又节约成本
对于4个~70个安全功能的应用,可采用可编程安全模块,使用方便,性价比高,还可以通过网关 将故障信号传到PIC或上位机,有利于故障诊断
占地面积大或长距离的自动化生产线通常采用现场总线或工业以太网,实现分布式1/0系统,其 安全控制系统可采用安全PIC十安全I/0的方案
对低成本要求较高的,采用安全桥方案
安全桥技 术自带安全逻辑处理单元,无需安全PLC,显著降低整体方案成本
智能型安全驱动设备,如,变频器,伺服控制器,采用自带安全力矩关断功能的型号
从提高生产效率方面考虑,将安全区域划分成几个不同的区域,分别进行安全控制
另外,对产线 核心的区段,采用安全速度监视继电器控制,可在满足安全要求的同时,将安全对生产效率的影响降到 最低
安全防护系统的实施,遵照相关安全标准,如IEC61508、IsO12100、IEC62061、IsO13849、 21
GB/T37393一2019 EC60204等
采用包括风险评估在内的全生命周期的安全管理体系
A.3.1.5信息安全 车间信息系统可能遇到的不安全威胁有病毒、黑客和内部人员的非授权网络操作或误操作
为了 消除以上不安全因素,整个车间网络系统采用三层纵深防御策略
第一层为物理策略层,建立车间网络操作管理规范,计算机设置相应的不同层级密码 第二层为网络安全层,对车间网络按功能区域分段,段与段之间及控制层与管理层之间设置 mGuard工业级硬件防火墙,其过滤器根据源发地址和目标地址对数据包进行过滤,阻止来自 “外部”的不需要的数据流
远程访问全部经过VPN和mGuard防火墙过滤; 第三层为系统完整性层面,采用cIFs(CommonlnternmetFilesystem)完整性检测技术可定 期扫描网络中的病毒,并可以调用第三方病毒服务器对病毒实施有效查杀
A.3.2生产资源的数字化 通过应用RFID技术,可编码原料、原料处理设备、模具等,并将收集的信息传送给生产设备控制系 统
即将产品从原料到成品整个流程的所有信息记录并连接起来
A.4工艺设计数字化 工艺设计数字化是产品设计数字化与企业管理数字化的桥梁
本数字化车间采用工艺设计、执行 与管理系统进行数字化的产品工艺设计
现场生产工程师可以通过流程框图的形式对现场的工艺进行 设计和规划
A.5车间信息交互 数字化车间的整体布局分为基础层、执行层,在数字化车间之外,还有企业的管理层,系统将收集到 的客户信息与管理层的ERP和PL.M进行信息交互,ERP与执行层的制造执行系统MES之间进行信 息交互,PLM将数字产品信息传递到执行层的工艺设计,执行与管理系统,同时MES与工艺设计,执 行与管理系统也存在信息交互,MES将生产订单等信息传递给基础层生产资源、制造设备、模具、检测 工具等,工艺设计、执行与管理系统将生产工艺、物流信息等传递给制造设备、AGV等,同时基础层又 会将收集到的信息反馈到MESs与工艺设计、执行与管理系统中
A.6制造运行管理数字化 A.6.1车间计划与调度 数字化车间通过车间计划排产模块实现车间计划与调度
根据预先定义的生产约束条件,规则矩阵,预设指标,排产产能策略等条件,实现全自动排产,半自 动排产或人工排产
结合甘特图方式,综合显示设备实时状态信息、已排产订单工序,关联关系、工具资 源分配情况,便于计划员检查现场排产情况和执行状态,实现了生产过程透明化的需求
除了生产订单排产,还可以针对设备预修、维修任务、模具换针任务等,创建MES中的工作计划工 单,调动车间生产、ToolShop、设备维护等团队完成指定任务 A.6.2工艺执行与管理 数字化车间通过车间订单管理模块完成工艺执行与管理
22
GB/37393一2019 ERP系统生产订单数据、相应BOM,routing等主数据,准实时传人MES系统,经排产后下达车间 现场
实现了无纸化信息流传递,提高了计划与车间执行层面的联动性
在HM终端上显示设备实时运行状态,支持状态转换,自动记录设备作业周期、产量,合格品/不 合格品数量
查看本工位上待生产订单,登录或退出订单工序,订单工序完成情况,订单产品BOM,工 序配套、工具资源和准备状态等信息
在HMI终端上还可以即时打开本工序订单相关的操作文档手册,方便车间现场员工使用
车间执行过程和结果信息,最终汇人MES订单管理模块,通过订单相关报表,方便获取订单完成 的各种时间状态组成,便于分析订单执行周期内的瓶颈,通过订单与质量相关报表,可以分析订单与班 组、设备、工具之间的关联关系,便于分析、定位质量问题
A.6.3生产过程质量管理 质量管理包括来料检验、过程检验、投诉管理、工具管理以及质量分析模块
它通过检验计划与生 产计划紧密的结合,实现了生产的闭环管理
它通过各测量工具等方法采集现场的相关数据
质量数据采集与监控.MES对接收到PLC发送的不合格品信号进行记录和统计,定时刷新系 统质量监控页面,通过sPC控制图方式展示每个设备每个时段的不合格品数量,并根据不合 格品的发展趋势进行预警 质量追溯与改进;质量追溯系统是数字化车间在引人质量追溯软件框架的基础上,车间自主开 发的生产软件
系统贯穿整个生产过程,其主要的功能包含追溯产品中使用的原材料状况及 记录通过每道生产工序的时间及结果
实施全面产品质量过程管控,并实现收集数据用于内 部分析改进
追溯系统如图A.4所示
追溯系统 -追溯系统的构建 手工装配实施 发货 发货追河 来料注册 追溯报告 系统架构搭建 创装 过程控制 返工分折 ATE NG 成品组装 迫溯系统 SMT制程运用 材料追溯 订单追湖 程序校验 国麻测区 Setup优化 材料证 PcB追棚 县利 o口 工 插件 图A.4追溯系统构建示意图 A.6.4生产物流管理 生产物流管理包括: 内部生产物流;包括收货和发货环节
其中,收货环节包括ASN的创建、货物的清点、货物的 上架,发货环节包括订单发货、生产发料看板及生产发货
成品物流;成品仓库物流系统主要功能部件采用模块化,标准化设计,并应用条码技术、,变频调 速、高速数据采集、人机界面,工业现场总线、以太网及PLC控制等先进控制技术,在wMS系 23
GB/T37393一2019 统的管理调度下,完成物品的包装输送及出库业务
通过核心ERP系统下达业务指令,实现业务信息流的自动传递,减少仓库对人员的需求和依赖
A.6.5车间设备管理 车间设备管理包括 设备状态监控:数字化车间采用MES制造执行系统中的设备管理模块,对设备的状态进行 a 监控
b 设备维修维护设备信息管理模块-设备维护日历可实现 -操作工及设备维修人员可在设备终端上查看设备维护内容及周期 系统自动计算维护周期,并通过图示在终端给出提示信号
设备运行分析;智能生产线的数据采集与控制系统对设备实时状态和维护维修过程中搜集的 数据进行采集,自动统计并分析与设备相关的指标
24
GB/37393一2019 附录B 资料性附录 数字化车间合理化产线设计案例 目的和概要 B.1 由于人工成本上升,人才成本提高,品质确保困难等问题的出现,机器代替人的自动化解决方案得 到广泛应用
其中一种是全自动化产线的方式(如图B.1所示),但存在以下缺点: 难以对应多品种小批量的生产方式 a 难以跟上生产规模的变动; b 设备成本较高; c 需要较大的安装空间; d 维护成本较高; ee fD 生产类型更换的准备时间长,由于设备故障造成的临时停机多发,难以保持高开工率 需要高水平的操作人员
g 按照适当的规模,将产线分割为多个工作单元可有效解决以上问题,如图B.2所示
工作单元之间 的部件搬送由人来完成
本附录给出了人和设备(机器人)的协作生产解决案例
35m 零部件供给 零部件供给 零部件供给零部件捕入 零部件插入 零部件组装 零部件供给 零部件检测 零部件组装零部件清洗 零部件组装 ”" 规格名称印刷 传送带 入口 出口 弹黄压力检测 复介组转/渊试 单体检测 锁螺丝 捆包印字 捆包 印字干燥 宰部件供给 图B.1全自动化产线的整体示意图 9m f49m 教工作单元 人员搬送部件的区域 图B.2单元式生产线的整体示意图 25
GB/T37393一2019 B.2 实现方法 B.2.1应对多品种小批量生产 包括 -自动换产:在头道工序打印QR码,在之后的各工序中通过读取该QR码,使设备执行符合该 产品的生产方式,实现自动换产 人工供给零部件;因产品型号不同所需的不同零部件,将设备中这些零部件的自动供料改为人 工供料
在数字化车间中,操作人员会因为多品种小批量的生产方式需要而频繁地变更操作 工序
为了减轻操作人员的负荷并消除人为的错误,宜导人作业辅助解决方案
即需要操作 人员供给的零部件(如图B.2所示、在数字化工作单元间的部件搬送如图B.2所示成 品取出和堆放(如图B,2所示)等操作方法都会在显示器上给出恰当的操作提示,并提供明 确的操作顺序指导,防止人为失误,以提升生产效率和产品品质
同时作业辅助解决方案还可 以和MEs/ERP/B1(Businesslntelligence)等上位系统协同,通过PDCA的持续循环改善方 法,降低操作失误,提高生 .品质和节能等,从而削减综合成本 产效率、 引进小型的单元式生产线;把生产性高(周期时间短)的全自动产线更换为周期时间较长的小 型单元式生产线,使憋体生产可应对多品种小批量生产的柔性要求
示例 全自动产线;周期时间=5s,面积=35m×8m,产线数=1条产线
单元式产线;周期时间=15s.,面积=9m×4.9m,产线数=3条产线
B.2.2节省设备的占地面积 比较大的零部件如需自动供料(排列供给)则需要大型的供料设备,因此通过人工上料大型零部件 方式可减少设备的占地面积
另外,集中操作人员的活动路线,可减少操作人数
如图B.2所示 B.2.3实现设备高运转率 包括 减少临时停机 通过削减工序数量,减少停机概率 在图B.1所示的全自动产线上排列着50道工序,只要其中一道工序发生临时停机,就会造 成整条产线停止
图B.2所示的单元式产线把工序数减少到23道,降低了整体产线的停 机概率
通过减少零部件的搬运,排除了停机的主要原因 通过把供料设备的搬送工序最小化,排除了零部件搬送时因部件堵塞所造成的停机
在 震动盘的出口处安装视觉传感器确认零部件的位置,机器人在此位置抓取零部件
削减换产时间 通过B,2.1中自动换产或人工供给零部件,实现换产时间最小化
B.2.4使用工业物联网进行运行管理/品质管理 可在如下方面使用工业物联网进行运行管理或品质管理 自动采集设备的运行状况、停止次数、停止时间、停止原因等数据,实现运行管理
a b 自动采集产品的测试结果、使用的零部件属性、操作人员属性、组装属性(具备力觉传感器的电 动螺丝刀采集锁螺丝的力矩值)等数据,实现品质管理
26
GB/37393一2019 自动采集设备使用的能耗信息和生产状况的数据,实现能源监控
c d 通过作业辅助解决方案,可将生产实绩数据、操作实绩数据(具备力觉传感器的电动螺丝刀采 集锁螺丝的力矩值)实时上传到IT系统
可将采集的数据生成以下可视化图表 锁螺丝不合格推移表; 组装台数图表; 组装节拍时间图表; 锁螺丝不合格数图表; 作业项目不合格数图表
使用可视化数据分析操作人员的人为失误原因,并将分析结果用于操作人员的教育和工序的 调整改善,并迅速地反馈到生产现场,从而实现实时的PDCA循环,如图B.3所示
可视化 锁螺丝不合格率推移表 云端 MES/ERP/B 组装台数一览表 工具
组装节拍时间一览表 2MwMw 锁螺丝不合格数一览表 作为项目不合格数一览表 网络 可视化 网络 ACION FLAN m 改许 II网关 n" CHECK DO MES/ERP/B tw小物 物f 服务器 工具 内联网 现场网络 数据生产实绩 作业实绩 手工螺丝实绩等 能渊
锁螺丝转矩 作业支拨 系统 零部件由操作人员搬运 图B.3lndustrialo自动采集数据示例 27
GB/T37393一2019 附 录 资料性附录) 数字化制造设备典型配置与功能 C.1概述 为了满足某一特定的车间工艺过程,在具体工艺定义输人的基础上,通过数字化制造设备自身功能 以及同其他辅助设备协同来执行车间具体的生产工艺
通过车间网络向执行层反馈作业执行的状态和 用户自定义的数据采集属性值
交互的数据主要包括 生产运行数据 质量运行数据; 维护运行数据; 物流运行数据 数字化制造设备应构建在工业通信网络基础之上实现与其他数字化设备及上层运作系统进行数据 交互的功能,包括 -现场设备与邻近设备联网实现协调动作、信息交换与互锁 现场设备与辅助设备联网实现协调动作、信息交换与互锁 -工厂信息网络与上位管理信息系统实现联网与数据交互
其功能模型见图C.1
应用服务器 网络设备 wsB总线 生产运行数据/质量运行数据/维护运行数据/物流运行数据 执行管理 数据采集 定义管理 运行指令接收 运行指令反馈 数字化制造设备 运行定义管理 运行结果数据 特定工序工艺要求 特定工序工艺结果 图C.1数字化车间设备功能模型图 28
GB/37393一2019 C.2数字化加工设备 C.2.1基本要求 对数字化加工设备的基本要求如下 自动化加工 加工装备具备在无人操作的情况下按照既定的逻辑(NC代码或PILC程序)实现自动加工生产 工作模式可选,如手动、自动等; 根据指令自动运行和停止 加工节拍根据工艺要求自动调节; 工件自动夹紧与松开 与辅助设备配合完成自动上下料 自动测量,定位与保护功能; 互锁功能 自动报警 安全防护功能
-网络功能 装备可作为一个网络节点接人到工厂中现场总线网络或工厂信息网络,并且在保证安全传输的前 提下,与网络中其他设备实现数据交换
网络是实现数字化工厂的前提条件,是加工装备与其他设备数据传输的基础
加工装备主要涉及 到两种网络:现场总线(如PROFIBUS)和工厂信息网络
通常加工设备与现场设备间具有逻辑互锁的信息交换多采用现场总线;而加工设备与工厂管理系 统间信息交换的采用工厂信息网络
两种网络在传输的实时性、数据量、传输方式等要求上有较大的差 别,通常不可混用 现场网络与邻近设备联网实现协调动作、信息交换与互锁; 现场网络与辅助设备联网实现协调动作、信息交换与互锁, 工厂信息网络与上位管理信息系统实现联网与数据交互
柔性加工 指装备在不停机的情况下,满足多品种的加工 丰富的人机界面,支持开放式工具对用户界面自定义; 根据指令自动选择不同的加工程序 根据指令自动选择工艺参数; 根据指令自动选择工装、夹具或托盘 根据指令自动更换加工刀具; 刀具参数根据指令自动调整; 自动测量、定位与保护功能
安全 关于安全性,从单个的加工设备角度考虑,涉及到人员安全性与设备安全性两个方面
人员安全性针对具有一定危险性的加工工艺现场,为了保证作业人员等设备周围人员的安全,加工 设备应具有以下功能 29
GB/T37393一2019 针对加工工艺中的危险环节具有警告功能
例如,利用蜂鸣器,指示灯等对危险性做出 警告
针对加工设备周围环境的安全性具有感知功能
例如,利用互锁、安全光幕等对进人危险 领域的行为具有感知功能
针对危险行为具有迅速采取安全措施的功能
例如,感知到危险行为后,迅速自动断电, 运动机构自动紧急停止等
设备安全性包括加工设备中需要使用用来加工的刀具、模具等消耗部件以及定期补充部件
此类 部件如不及时更换和补充,会影响到设备的安全性,进而发展为故障或者事故
作为数字化加工设备,对以上消耗部件的状态以及定期补充部件的交换记录,应具有数字化管理的 功能
并且通过灵活运用以上管理数据,事先起到对消耗部件以及定期补充部件维护的作用 消耗部件
例如,刀具、冲压模具、砂轮 定期补充部件
例如,油类(冷却油、润滑油),电池、密封圈
远程监视 数字化加工设备需对设备的运行状态、消耗品寿命有远程监视故障预告)功能 以往传统设备中应在车间现场才能完成的各种监视,数字化设备需能在监视室电脑上显示出与车 间HMI同样画面,并且通过移动终端支持的远程监视功能,在不同地点在任何时间实施监视 监视生产状况,例如,针对于生产计划的进展情况; 监视设备状态,例如,正常运行中,缺料(等待、异常; 监视消耗部件的损伤状况,例如,刀具的使用次数 把握报警原因,例如,缺料、安全报警(人员进人、消耗部件损伤材
C.2.2数字化功能 在数字化工厂中,加工装备不再是作为独立设备运行,而是作为工厂的一个组成部分与其他设备共 同协作运行,接受工厂管理系统的统一调度管理
频繁及大量的数据交换使得加工装备一定要具备完 善的功能和接口
实现数字化功能可分为如下两大方面 数据采集: 数字化加工装备需要具备为工厂管理系统提供用于统计,分析、监控等所需的基础数据
这些数据 根据其数据用途主要分为 加工信息
用于描述该加工装备在进行某一生产过程相关的信息,如工件名称、工艺参 数,加工时间、工件计数等; 设备状态信息
用于描述加工装备的运行状态、工作状态、组件状态等相关信息,如开机 状态,设备总运行时间、操作模式等; 故障报警及信息
用于描述加工装备异常时产生的故障和报警相关信息,如报警代码、报 警内容、持续时间、频次等, 刀具管理信息
用于描述加工装备所使用到加工刀具相关的信息,如刀具参数、刀具使用 寿命等; 能耗数据
用于描述加工装备在运行过程中消耗的能源相关信息,如电压,电流,功率等; 其他信息
用于描述各种加工装备特有的数据信息
操作功能 数字化装备需要具备相应的接口,以接收工厂管理系统的操作指令,并能够按照指令执行相应的功 30
GB/37393一2019 能,在执行结束后,将执行的结果反馈给工厂管理系统
加工装备主要的功能包括: 文件访问
支持工厂管理系统对加工装备文件类数据进行(读写、修改、删除、复制、移动 等)操作,例如,将NC程序的下载至数控机床,或者从检测设备中将测量结果文件上载至 服务器等
诊断和调试
支持远程对加工装备进行故障诊断及操作调试,以便于快速维修
操作权限
加工装备应具备权限管理功能,可以区分操作人员、维护人员、编程人员等操 作权限,避免由于误操作对设备或生产造成损失
数据缓存
支持加工装备保存一定时间的历史数据,以确保意外离线时仍然能够保持数 据的连续性完整性
操作追溯
支持记录加工装备的操作历史,便于装备发生故障时进行追溯
时钟同步
确保设备与整个工厂网络内其他设备保持同一时钟,以免发生记录混乱
归档
支持工厂管理系统定期对加工装备中的重要数据如调试数据、加工程序、配置信息 等进行归档保存进行管理,以便于由于加工装备更换、维修后,可以快速恢复生产 其他
用于实现各种加工装备特有的操作功能
C.2.3网络接口 常用的数字化加工设备的网络接口包括如下两类 -现场网络种类、安全 现场网络用于实现加工设备与其他加工设备或辅助设备之间协同工作时的通信与数据交换,应满 足实时性及安全性 支持国标所列的现场网络标准; 具备标准统一的、开放的刀具数据采集接口; 可通过MEs订单选择加工程序 可通过MEs订单自动启动加工 与辅助设备(如测量仪、机器人等)无缝集成
网络: 实现数控加工程序同CAM或MES的开放式,专用的交互接口; 实现sCADA或MES对加工设备的数据采集、数据传输和管理 通信协议应支持标准统一的、开放的数据采集协议; 用户可以自己选择采集数据的类型,可以实现高速的数据采集与传输,支持文件夹、Ftp等 方式 支持远程访问与诊断; 支持数据备份与恢复
C.2.4辅助设备 辅助设备是数字化加工设备不可或缺的部分,不直接参与加工,但对加工有重要作用的相关设备, 根据其辅助作用分类如下 上料下料设备 用于向加工设备提供物料以及从加工设备获取成品 机器人; 31
GB/T37393一2019 机械手(非标设备). 测量设备 用于监视、检测加工设备中使用的消耗部件等 力学传感系统; 刀具测量设备
识别设备 用于识别、检测物料和成品 RFID; CCD; 视觉设备 称重设备 C.3 数字化物流设备 C.3.1物料输送设备 C.3.1.1悬挂输送机 悬挂输送机系统的技术要求 应具有数字化变频调速功能,以便适合相关工艺作业节拍的要求
按照工件种类和外形特征选择合适的挂具
挂具应适合人的操作,使悬挂输送机在输送或行 走进程中,能够由人工或机械的形式实施安全的操作
悬挂输送机的架空轨道安装在厂房的屋架或其他构件上,组成有直线和转向站的空间线路,故 应配置完整的安全保障装置和管理措施
C.3.1.2辑子输送机 轭子输送机主要用来输送具有一定规则形状、底部平直的成件物品
为保证物料在辐子上移动的 稳定性,基于输送机机械组成结构,要求每个物料支撑面至少应有4个辐子支撑,辐子的间距应小于物 料/箱体支撑面长度的1/4
c.3.1.3搬运机器人 适合于工艺现场的搬运机器人,有析架机器人简称析架,用于搬运体积大、质量重的工件)、机械 臂、检测机器人等
引人搬运机器人,应先对搬运工艺现场进行合理化和规范化
包括 规划设计物流的空间轨迹、作业条件、作业顺序等技术规格和性能指标; 根据工序作业的要求,设计、制作并安装不同类型的末端执行器,以完成不同形态和状态的工 件搬运作业; -根据工件的特点选用或设计、制作适合工件物理特征的传送装置,以服务于搬运机器人的功能 效用
c.3.2自动搬运小车 自动搬运小车是在生产过程中执行物料搬运作业的重要工具,分为有轨自动小车(RGV)和自动导 32
GB/37393一2019 引AGV)小车两类
对AGV的控制要求
AGV系统应是基于计算机的现场控制系统,能够在车间内部按照规定的方向通常为顺时针 方向)在规定的轨道上移动,并能够通过位置感知实现在规定站点的定位、启动、转向或停止
AGV系统应通过自带传感器,用于检测AGV何时到达规定的站点,或越过某站点继续移动; AGV系统应与车间主信息系统保持时钟同步
基于AGV的物流系统,应含有“运行监管”和“动态显示”功能;其中,运行监管系统负责接收 外来的物流指令并实时获取车辆当前动态信息并发送至动态显示
一需要多台AGV的数字化车间,应规划,设计出基于优化控制策略的AGV系统运行监管模式, 确保多个AGV设备能够在移动指令得到层次化的控制
简单的AGV系统,其应用软件应得到分布式异步通信技术的支持;复杂的多AGV系统应具 有一定的并发实时性
c.3.3自动化立体仓库 自动化立体仓库,是自动存取、自动输送、自动识别等功能集成的自动化仓库,是通过计算机技术和 PIC控制的多技术集成的有机整体
自动化立体仓库的功能要求 具有基于计算机管理、自动控制的物料搬运设备和货物存取作业功能;能够始终准确无误地对 各种信息进行存储和管理
具有信息识别功能,包括对自动化仓库中货物识别,跟踪,堆垛机自动认址、货物位置检测和堆 垛机准停等内容
-与车间或企业的信息系统互联互通,支持加工工艺执行的需求、整机装配的齐套管理需求和库 存控制要求
采用高层货架存储货物.存储区充分利用仓库地面和空间、节省库存占地面积,提高空间利用 率;具有自动分拣、理货功能,可自动地执行物料识别、接收和分类储存管理;可自动提取和半 自动配送
可通过调节运输过程中不同运输工具间的运量差异,优化运输的匹配方案,化解不同运输设备 间能力差异
自动化立体仓库的管理软件,应具有出人库管理、盘库管理,查询、打印及显示,仓库经济技术 指标计算分析等功能
C.4数字化检测设备 C.4.1基本要求 数字化检测设备采用基于数字化的测量方式,具有在线或离线检测.记录、显示、上传,分析,故障诊 断和校准等功能,还应具有数字化接口,以支持检测设备与加工设备、检测设备与生产管理系统、检测设 备与质量管理系统之间检测数据的传输
通过网络互联各类检测设备,构建数字化检测系统,实现对检测数据的采集、分析与处理,从而有效 提高生产过程的质量控制水平 33
GB/T37393一2019 C.4.2功能要求 C.4.2.1数字化检测设备数据通信要求 数字化检测设备数据通信包括检测程序的下达和检测结果的采集,通过设备接口实现
主要的通 信形式包括基于RS232串口的数据通信,基于GPIB(GeneralPurposeInterfaceBus),VXI(VMEbus eXtensionsforlnstrumentation),PXI(PCIextensionsforInstrumentation)、LxI(LANeXtensionsfot n)和AXIe等总线标准的数据通信
lnstrumentatio1 不同类型的检测数据需按照统一的数据结构进行格式转换,以满足上层系统对数据的分析和监控 的要求
典型的检测数据协议标准有用于尺寸测量的ANSIDMIS标准、用于质量数据表达和通信的 Q-DAS标准等
C.4.2.2数字化检测系统应用要求 通过检测设备的联网构建数字化检测系统,采用数字化检测方法,将零部件真实测量状态反映到数 字化模型上,以形成设计制造一检测一控制一管理的闭环控制,事序中监控关键工序的加工或装配质 量,有效降低测试成本,提高检测效率与质量管控水平 -数字化检测技术应用规范 针对机加零件、钣金零件、复材零件,部件及大部件装配检测等工程应用环境,编制数字化检测工艺 规程编制规范、数字化检测方法选用技术规范、检测数据分析与处理技术规范和数字化检测作业流程规 范等
基于模型的检测工艺规划 -般应包括基于零部件典型结构特征的检测任务快速定义、识别与提取;基于模型环境的检测工艺 规程编制(检测设备选择、,测点规划与布局及对检测路径的优化与仿真等);检测坐标系构建;检测方案 选用;检测模型轻量化等过程
数字化快速检测 -般包括快速选择与零件检测特征模型匹配的检测方法;开发辅助自动化测试装置,构建自动化检 测系统;通过监测设备数据接口,实现检测数据的自动采集与上传等
-检测数据的处理与分析 依据检测数据分析与处理技术规范,基于统一的编码,对测试数据进行规范化处理,对测试数据文 件进行转换,并统一存放在测试数据库中
通过MBD技术,在三维模型上实现检验工艺规程、产品测 量数据和检测结果的统一标注,生成基于轻量化模型的三维可视化检验报告,对检测数据进行分类统 计,利用散点图、柱状图、分布图或趋势图等显示不同分析结果,为产品全生命周期质量追溯提供依据
数字化设备布置要求 C.4.3 数字化检测设备安装位置一般采用在机安装或现场安装
在机安装;将检测设备直接安装在加工设备上,在工序加工过程中和加工结束时对工件精度进行实 时自动检测,并自动输出检测数据
现场安装;按照加工工艺路线,在生产线现场安装检测设备,在加工结束时对工件进行自动检测,并 自动输出检测数据 注在桃安装检测,可有效诚少检测运输时间,提高检测精度和效率,并可对工件进行实时自动检测,保证了加工质 量,但对加工设备及检测仪器要求较高
现场安装检测可快速换型适用于多品种的检测,柔性高,但增加了检 34
GB/37393一2019 测运输及重新定位装夹时间
C.5数字化辅助设备 数字化辅助设备主要包括移动终端和工作站
移动终端包括但不限于PDA,平板电脑、车载电脑 等移动终端
工作站包括但不限于落地式、悬挂式、,嵌人式等形式的信息终端,以及拉绳式、按钮式等形 式的求助终端
对数字化辅助设备的基本要求如下: 具备良好的现场网络布置环境条件; 按数字化工艺流程合理布局; 具有权限管理功能,能进行作业人员身份验证管理, 具备生产数据录人功能 可查询、下载作业所需的生产指导文件; 具有呼叫请求,求助信息提示、响应确认等信息交互功能 35
GB/T37393一2019 附 录 D 资料性附录) 数字化车间的安全管理示例 目的和概要 D.1 为了确保数字化车间中的设备和人可以在安全的状态下共存,一定要考虑各种安全保障措施,以紧 急应对突发事故,并确保信息安全等
因此,需要采取以下措施 自动采集并显示与人和物的安全状态相关的重要数据
a 在实时采集安全状态相关数据的基础上,提供安全监视和风险报警
b) 实现安全的数字化管理
危险信息、风险信息、保护措施信息、安全有关的过程/设备/人员信 e' 息、管理规则信息,分析辅助信息、知识类信息等,对这些信息以计算机可以识别的形式进行采 集、保存、供应、处理、展开
dD 提高安全管理的可视化
通过安全监测和分析管理系统,全方位地观测和追踪重要的危险源 实时监测风险等级并预警,安全且全面地展开监视,同时要具备针对紧急情况的应对策略等, 以不断提高安全管理和可视化的等级
本资料提供数字化车间在多品种小批量生产方式下,频繁发生工序变更带来的安全控制,以及因连 接外部网络需要进行的信息安全处理的事例
D.2实现方法 D.2.1架构 数字化车间的生产安全管理功能模型如图D.1所示
生严安全管 人员/风险数据 事故相关数据 对危险区域的风险监测 紧急时的应对 数据的整合性 监视数据 安全相关控制系统 整合性的监视和管理 规定限制信息安全 设备信息 反惯 监视数据 机器的修理和维护 数字化制造设备/生产资源 图D.1生产安全管理的功能模型 D.2.2功能 在数字化车间开展生产安全管理,应将被数字化的各类危险源监视数据、人员状态数据、侵人危险 区域的监视数据、机器的状态数据等,与生产管理系统协同,开展实时生产安全管理
生产安全管理具备以下的功能 36
GB/37393一2019 危险区域的风险监测 a 危险源的监测: 根据危险源的分类,对机械的危险、电气的危险、热的危险、噪声产生的危险、放射线产生 的危险、材料和物资所引起的危险等进行实时监测,对于机械的伤害范围、噪声,粉尘浓度 等预先设定基准值,超过时报警,根据反馈信息及时调整,以避免危险情况发生
人员的行动和状态监测 通过识别身份、追踪位置、行为判断等对人员的行动进行监测,可以实现以下功能 判别人员活动信息,评价进人危险区域的风险状况 通过声光,对侵人危险区域、异常行为,异常状态等发出报警
必要的情况下,对人员的状态(呼吸、心跳、血压等)进行实时监视,异常时报警
风险管理和早期预警 实时收集风险参数信息,对评价计算模型进行准确的设定/分析,当有可能导致风险上升 或者超过基准值时,实时报警并提示减少和避免风险的应对措施: 自动分析导致风险上鼻和超过的原因,提示减少和回避风险的应对措施
和生产系统协同,自动判别风险要素的变化由于生产计划的改变,导致安全区域发 生变化,威胁人员安全),维持安全的环境
b)安全程度的监视和管理 安全功能必需符合安全等级标准(IsO13849-1PL、,IEC61508sIL等)所规定的相关规格
例 如类别4PL(PerformanceLevel)e规定的单一故障,在安全功能实行时或者实行前的功能诊 断时,所检测出的每小时危险侧故障的平均概率(PFH)在10-"
GB/37393一2019 录 附 E 资料性附录 数字化车间信息处理案例 E.1目的与概述 数字化车间通过从现场各生产单元采集数据上传至上层系统,以实现生产的规划、管理,诊断和优 化
本附录针对数据与现场关联性,实时反馈及数据机密性,提供了数字化车间信息处理解决方案的实 现案例
通常采用云技术将生产现场收集的各类信息上传至上层系统
但是在实际的制造业生产现场中 云技术存在如下问题 要灵活应用储存在云端上的大数据,应具备制造业生产现场的诸多专业知识 数据信息一定要实时的反馈至生产现场; 制造业现场中的核心信息具有极高的机密性
为解决以上问题,本案例采用介于生产现场与IT系统之间的中间层信息处理技术
E.2实现方案 E.2.1架构 数字化车间的信息系统架构大致可分为3个部分,即为生产现场层、,IT系统层以及连接两者的中 间层(见图E.1)
云烟 T系统 PLM ERP MES SCADAAPs 中间层 信息协同 边缘计算 信息协同处理 数据采焦分析 专用模块 专用模块 2 生产现场 LC 现场总线 图E.1数字化车间的信息系统架构 39
GB/T37393一2019 在生产现场层中,对车间产生的各种数据进行实时收集
在中间层中,为了对原始数据赋予其因果 关系并转换成有用的信息,需对收集的数据进行一次处理,又称“边缘计算”
在此得到的分析,解析的 结果将被反馈至生产现场
另外,也会与IT系统进行无逢连接
中间层不仅有助于无缝连接,也可优 化整个系统
E.2.2功能 中间层的“边缘计算”具有以下功能 生产现场数据的一次处理 制造现场采集的数据十分庞大,若将全部数据送到云端上作处理,常会发生通信负荷和响应性能恶 化的问题
因此在数据分析时,有必要对重要数据进行过滤,进而能改善负荷集中的问题
另外,对数 据做关联性处理、对控制数据做时间排序等,使数据的分析更容易
生产现场数据的分析和改善 对制造现场进行数据分析时,需要各种专业技术
能够在生产现场快速分析所采集的数据,将有助 于实现生产现场的改善
专有技术的保护 利用云技术将制造现场的数据上传到云端,无法确保专业技术的保密性
通过边缘计算,对数据进 行一次处理,可降低生产现场的专业技术流出的可能性
E.2.3实施 中间层的“边缘计算”方案的实施及系统构成可参考见图E.2
在系统中增加用于边缘计算的关键 部件FA-IT信息协同处理模块即可实现
ERP 巴LM APS MES SCADA FA-IT信息协同处理模块 边 专用模块 专用模块 专用模块 组设备 物流设备 加工设备 图E.2边缘计算方案实施及系统构成示意图 40
GB/37393一2019 E.2.4要求 为了实现以上的实施方案,对整个系统有以下基本要求 通信上需要采用满足高速、大容量通信的开放式现场总线
采用可实现多种硬件,软件与网络、阶 层,设备的无缝连接的通信协议
另外,为了满足中间层的信息处理要求,需采用编写便捷可实现传输, 数据收集功能的信息协同处理模块
E.3案例 E.3.1产品生产状态监测与反馈 以贴片机运行管理系统为例,如图E.3所示
通过运用相关信息协同处理模块,实时收集贴片机的 生产,运行,品质信息,并结合传感器收集的基板数量,赋予其产品关联性,写人信息系统数据库
通过 边缘计算分析贴片机运行数据、零部件层面的不良数据等,最终将贴片不良问题反馈至产品设计阶段, 进而降低不良率,优化产品生产
<贴片机运行管理系统 管理终端 数据库 效果 Ethermet *优化运转率 *优化品质
生产进度一元化管理 出现问题时迅速应对 产线平衡均一化 分析不良原因 信息流 提升品质 [贴片机运行管理画面 减少设备停止 节省人工 "信息收集、输出自动化
防止零部件缺货 收集、分析零部件层面i m 的Eror信息! Ethernet 信息协同处理模块[实现高安定性,高可靠性的信息收集] [模块A] 将传战器收集的基板数量写入数据库 生产信息 模块] 远行信息 运转率、停止次数、 实时收集贴片机的“生产
运行”品质信息 品信息 零部件数量 =Eror信息 Eror次数等 图E.3贴片机运行管理系统示例 E.3.2设备状态监测与反馈 以伺服电机机械诊断功能的运用为例,如图E.4所示
通过收集与伺服电机相连的机械部件的振 动、摩擦等相关数据,实现设备状态监视
进一步通过对数据的实时分析诊断,当出现异常波形时,早期 停机检修,减少因设备故障停机带来的损失
1
GB/T37393一2019 异常够知 放障预测 100 期 上下限 波形 缺油 破拟 实时监视设备状态 18 24 故障知 使用时间 相关/同归 振动上下限值 降维 触发 无需附加程序,自动实时收集 专用模块 模拟数字数据 何服电机机械诊断功能 通过对设备数据的被形解析、 统计解析、多变量解析 实施监视 wh M 提升设备运转率品质 各种传感器振动、声音等 设备故障之前更换部件,降低停机损失 机械部件 物承、丝杠等) 将机械部件寿命信息反债至设备设计层面 图E.4伺服电机机械诊断功能运用示例 42
GB/37393一2019 参 考文献 GB/T3358.2一2010统计学词汇及符号第2部分;应用统计 质量管理体系基础和术语 [[2]GB/T190002016 [3]GB/T25486一2010 网络化制造技术术语 [门 GB/T29308一2012核电厂安全重要仪表和控制系统老化管理要求 [5幻 IS(O12100 Ssafety ofmachinery Riskassessmentand Generalprinciplesfor desig riskreduction [[6]ISO13849SafetyofmachinerySafety-relatedpartsofcontrolsystems [7]IEC60204Safetyofmachinery一Eleectriealequipmentofmachines [8IEC61508 Functionalsafetyofelectrical/electronic/programmableelectronicsafety" related systems [9IEC62061 SafetyofmachineryFunctionalsafetyofsafety-relatedelectrical,electronic and programmableeleetroniccontrolsystems 43
数字化车间通用技术要求GB/T37393-2019
随着工业自动化程度的不断提高,数字化车间作为一种新型的生产方式,正逐渐得到广泛应用。然而,在数字化车间建设过程中,由于缺乏统一的标准和规范,导致许多企业在实践中遇到了各种问题。因此,制定《数字化车间通用技术要求GB/T37393-2019》这一标准对于保障数字化车间运行安全、稳定和高效具有重要意义。 该标准主要包含以下内容: 一、通用技术要求 数字化车间的基础设施要求:包括供电、供气、供水、排水等基础设施要求,同时还需要考虑到环境条件和物理结构等方面的因素。 数字化车间的数据管理要求:包括数据采集、传输、存储、处理等方面的要求,需要确保数据的安全性、精确性和可靠性。 数字化车间的网络通信要求:包括网络连接、通信协议、数据传输速率等方面的要求,需要保证通信的快速、稳定和可靠。 数字化车间的软件系统要求:包括软件平台、应用系统、信息安全等方面的要求,需要确保软件系统的高效性、安全性和易用性。 二、实施建议 在数字化车间建设过程中,应该遵循以下实施建议: 1.采用成熟的技术标准和规范,确保数字化车间运行的稳定性和可靠性。 2.充分考虑生产环节的实际需求,合理设计数字化车间的各项功能。 3.注重系统的可扩展性和兼容性,以便后续的数字化转型和升级。 4.加强对数字化车间的管理和维护,尽可能避免设备故障和数据泄露等问题。 三、总结 数字化车间是未来工业生产的趋势,其建设需要遵循统一的标准和规范。制定《数字化车间通用技术要求GB/T37393-2019》这一标准的出台,对于数字化车间建设提供了重要的规范和指导,同时也有利于提升数字化车间的运行效率和安全性。