GB/T39207-2020
锚处理系统安装与调试规程
Codeofpracticeforinstallationandcommissioningofanchorhandlingsystem
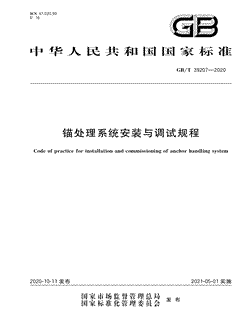
- 中国标准分类号(CCS)U16
- 国际标准分类号(ICS)47.020.99
- 实施日期2021-05-01
- 文件格式PDF
- 文本页数17页
- 文件大小1.17M
以图片形式预览锚处理系统安装与调试规程
锚处理系统安装与调试规程
国家标准 GB/T39207一2020 锚处理系统安装与调试规程 Codefpractieeforinstallationamdeommisiomingofanehorhandlmgystemm 2020-10-11发布 2021-05-01实施 国家市场监督管理总局 发布 国家标涯花管理委员会国家标准
GB/T39207一2020 次 目 前言 范围 2 规范性引用文件 3 术语和定义 安装前准备 .文件 人员 4.2 4.3工装、工具和设备 4.4安装条件 安装质量 5 5.1安装精度 5.2完整性 5.3媒继质量 5.!紧固性 5.5密性 安装程序 .1错处理绞车安装 6.2导链器安装 6.3导链槽安装 6.4尾滚筒安装 6.5鲨鱼钳、挡缆桩安装 6.6锚链转移绞车安装 6.7液压设备、电气设备、管路等安装 安装检验 调试 8.1调试目的 8.2调试用文件 8.3调试用仪表、仪器和工具 8.4调试人员 8.5调试环境 8.6调试条件 8.7调试 8.8调试数据整理和报告提交 附录A资料性附录螺栓扭矩参考表 附录B(资料性附录调试记录表
GB/39207一2020 前 言 本标准按照GB/T1.1一2009给出的规则起草
本标准由全国海祥船标准化技术委员会(SAC/TC12)提出并归口 本标准起草单位:中船黄埔文冲船舶有限公司、船舶工业综合技术经济研究院、广州黄船海洋 工程有限公司
本标准主要起草人:陈祥荣、陈遵清、聂黎军、练博强、刘伟,黄家勇,罗玫田,何、蒋巍、孙忠良、 梁毓坚、黄建军、宋义彬
GB/39207一2020 锚处理系统安装与调试规程 范围 本标准规定了锚处理系统的安装前准备、安装质量、安装程序,安装检验及调试要求
本标准适用于锚处理系统的安装与调试
规范性引用文件 下列文件对于本文件的应用是必不可少的
凡是注日期的引用文件,仅注日期的版本适用于本文 件
凡是不注日期的引用文件,其最新版本(包括所有的修改单)适用于本文件
GB/T34000造船质量标准 GB50661钢结构焊接规范 CB/T31902019钢质船体结构焊接坡口型式及尺寸 CB/T3619船舶系统和动力管路安装及密性试验质量要求 CB/T3802船体焊缝表面质量检验要求 术语和定义 下列术语和定义适用于本文件
3.1 锚处理系统anchorhandlingsystem 为其他船舶/平台进行起锚、抛锚作业服务的系统
注,锚处理系统由锚处理绞车、尾滚简、,鲨鱼钳、挡缆桩、导链器、导链槽、锚链转移绞车等设备组成,布置示意图见 图1
3.2 at 锚处理绞车 anchorhan ingwinch 为其他船舶/平台进行起锚、抛锚作业提供拉力的绞车
3.3 鲨鱼钳sharkjaw 将钢丝绳或锚链抱紧钳住的设备
GB/T39207一2020 说明: 锚处理绞车 导链器; 导链槽; 尾滚筒 -鲨鱼钳; 挡缆桩 错链转移绞车
图1锚处理系统各设备布置示意图 安装前准备 4.1文件 锚处理系统安装前应准备好下列图样和工艺文件 错处理系统设备资料; a 错处理系统安装图 b c 锚处理系统安装工艺文件; d 安装部位船体结构图船体基座图; e 锚处理系统主要受力设备地脚螺栓强度校核计算分析文件 f 吊装安全文件
4.2人员 从事锚处理系统安装的人员应: 熟悉相关的图样和工艺文件 a) b)具备认定的相关专业技能资质,并持证上岗
4.3工装、工具和设备 4.3.1锚处理系统安装用的主要工装包括 吊运工装; a 定位调整工装
b) 4.3.2错处理系统安装用主要工具和设备包括:
GB/39207一2020 顶升螺栓; a b 千斤顶; 扭力扳手; e d) 钻孔工具; 精度测量工具; e D 洋冲; 打磨工具
g 4.4安装条件 4.4.1安装区域船体结构装焊和火工矫正结束,并检验合格,避免后续动火施工作业 4.4.2安装区域船体结构面安装精度应符合相关技术文件的要求
4.4.3检查设备的完整性和外观,设备文件和证书应齐全,并做好记录
4.4.4需要安装的设备及其附件应通过检验并合格
安装质量 5.1安装精度 锚处理系统安装精度要求应符合表1的要求,其他安装精度要求符合GB/T34000的规定
表1锚处理系统安装精度要求 单位为毫米 允许极限 标准范围 备 注 项目 船体基座上丧面平面度 允许局部,分散,少量超差 基座 1:100 垫片外倾斜度 1:50 <0.0063 <0.0125 垫片表面粗糙度 垫片 钢垫片厚度 >12 环氧垫片厚度 按产品说明书 20 0.06mm塞尺允许插人 垫片与船体基座间的间隙(错处理绞车)》 0.06 深度不大于10mm 对应塞尺允许插人 垫片与船体基座间的间隙(其他设备 0.10 0.2 深度不大于10mm 垫片间接触比处理绞车 >60% >50% 安装 垫片间接触比(其他设备 >40% >50% 错处理绞车滚筒两端轴承的同轴度 0.5 或按产品说明书 尾滚筒两端轴承的同轴度 或按产品说明书 0.5 s士6 导链槽与拉线确定的安装位置的偏差 或按产品说明书 士4 5.2完整性 锚处理系统安装的完整性应符合图样和工艺文件的要求
5.3焊缝质量 5.3.1焊缝尺寸应符合图样或CB/T3802的要求,焊缝表面应成形均匀,焊道与焊道,焊道与母材之间
GB/T39207一2020 应平滑过渡
5.3.2焊接坡口应满足CB/T3190-2019第2章,第3章或相关技术要求
5.3.3装配定位焊的焊脚高度应与正式焊接大小一致,焊点长度及间距应均匀
5.3.4焊缝应按照GB50661中的相关要求进行无损检测,焊缝内部质量应符合对应等级要求
5.4紧固性 按图样要求拧紧安装螺栓
5.5密性 管系密性应符合图样或CB/T3619的要求,在管系内压力升高到规定值时,应无泄漏情况
6 安装程序 6.1 锚处理绞车安装 6.1.1船体基座安装 6.1.1.1将预制的错处理纹车船体基座吊至定位位置,并确定船体基座位置符合图样要求 检查船体基座与基座加强对位情况,应符合GB/34000中重要结构对位精度要求
6.1.1.2 6.1.1.3按图样要求焊接船体基座 6.1.2锚处理绞车定位 6.1.2.1将锚处理绞车吊运至船体基座上的安装位置,如图2所示
6.1.2.2通过顶升螺栓、千斤顶等工具微调锚处理绞车位置满足图样的要求,在船体基座上用洋冲标记 出连接螺栓孔的位置,并根据锚处理绞车的实际安装位置在船体基座面上媒好临时限位定位块
主视图 俯视图 日 说明: 船体基座; -垫片; 底座; 止推块; 主轴; -错链轮
图2锚处理绞车示意图 6.1.2.3将锚处理绞车吊离船体基座并放置妥当,对锚处理绞车底座的垫片接触位置进行打磨除锈,并
GB/39207一2020 涂黄油保护 6.1.2.4按船体基座上的螺栓孔洋冲点位置进行钻孔,然后对船体基座的垫片位置进行打磨除锈,并涂 黄油保护 6.1.3锚处理绞车安装 6.1.3.1将锚处理绞车吊运回船体基座上,借助临时限位定位块进行定位,并焊接止推块
6.1.3.2对垫片区域进行清洁
6.1.3.3按图纸要求安装钢质垫片或环氧垫片,精度满足表1的要求
6.1.3.4用扭矩扳手紧固底座连接螺栓,螺栓扭矩参照附录A中表A.1
6.1.3.5拆除临时限位定位块
6.1.3.6根据图样要求完成相关管子,电缆的安装工作
6.2导链器安装 按图样要求安装导链器及其附件
6.3导链槽安装 6.3.1根据锚处理系统的锚链走向进行划线或拉线,并结合相关图样要求对导链槽的安装位置进行划 线,划线精度应符合GB/T34000中相关精度要求
6.3.2吊运导链槽至划线安装位置进行安装
6.4尾滚筒安装 6.4.1将尾滚筒两端的轴承座拆卸下来,吊运至船体基座上进行预安装
6.4.2预安装时,使用工装螺栓调整轴承座的中心位置,两个轴承座的中心偏差应不大于0.5mm(或 根据图样要求). 6.4.3轴承座定位后,标记好螺栓孔的位置
6,4.4 吊离轴承座,在船体基座上根据标记配钻螺栓孔
6.4.5将轴承座回装至尾滚筒上,对轴承座的安装面进行清洁
6.4.6整体吊运尾滚筒至船体基座上,按预安装时的标记进行定位,并按图纸要求安装钢质垫片或环 氧垫片,然后紧固连接螺栓,螺栓扭矩参照表A.1
6.5鲨鱼钳、挡缆桩安装 6.5.1根据鲨鱼钳、挡缆桩的安装图在甲板上划线并在相应位置进行开孔
将鲨鱼钳、挡缆桩吊运至安装位置进行安装并焊接 6.5.2 根据图样要求完成管子、电缆的安装工作
6.5.3 6.6锚链转移绞车安装 6.6.1按图样要求安装锚链转移绞车的船体基座,精度应满足表1的要求
6.6.2吊运并安装锚链转移绞车,锚链转移绞车的定位安装应满足设计图样要求
参照表A1扭矩挖紧螺栓,紧周件安装紧固后,螺栓至少应伸出1个 6.6.3 3个螺牙
螺栓头和螺母 应与机脚和基座面板紧密贴合
6.6.4按图样要求安装管子、电缆等附件
液压设备、电气设备、管路等安装 按图样要求安装液压设备电气设备、管路、电缆等
GB/T39207一2020 安装检验 7.1检查设备型号,规格的正确性及设备的完整性
7.2用全站仪检查所有设备定位情况,用塞尺检查垫片间隙,用全站仪检查锚处理绞车主轴的水平,用 全站仪检查尾滚筒轴承的同轴度,以上结果应满足5.1的相关要求
7.3目视检查焊缝外观质量,用焊角尺检验焊缝高度,无损检测焊缝内部质量应满足5.3的相关要求
7.4用扭力扳手检查连接螺栓的扭矩,应符合图样要求
调试 8 8.1调试目的 在系泊状态下,检查锚处理系统及其附属设备的安装正确性,完整性以及主要功能、性能指标等是 否符合规定的使用要求
8.2调试用文件 调试用文件主要如下: a 锚处理系统布置安装图; 锚处理系统动力系统原理布置图, b 错处理系统润滑系统原理布置图; c 错处理系统电气原理图; d 错处理系统遥控和监测、报警项目汇总表 e 错处理系统遥控和监测、报警电气线路图; 锚处理系统使用说明书; 8 其他有关调试技术文件
h 8.3调试用仪表、仪器和工具 调试用仪表,仪器和工具包括测力计、兆欧表,电压表,电流表,转速表,秒表,便携式测温仪.通 8.3.1 信设备及携带式对讲机等工具
8.3.2调试使用的各种测试仪器和仪表,其精度等级应满足检验需求,并具有国家有关主管机构鉴定 的合格证明
8.4调试人员 调试的人员要求如下 从事锚处理系统调试人员应熟悉相关的图样和调试文件 a 调试人员应具备认定的相关专业技能资格,并经考核合格后持证上岗
b) 8.5调试环境 调试环境应满足如下要求 码头系缆设施安全可靠; a b 设备附近区域格栅、铺板、扶手等铺设完整,垃圾和油污水清理干净,无安全隐患; 调试前,油、气、水等辅助系统完整性、密性、清洁度等应验收合格
c
GB/39207一2020 8.6调试条件 8.6.1锚处理系统所在的船舶 调试开始前锚处理系统所在的船舶应达到如下条件 锚处理系统所在的船舶的状态符合调试要求 a b 所有为锚处理系统服务的辅助系统应能可靠工作,调试期间冷却水、供气及供电应正常 根据设备技术要求的预紧力完成了所有钢丝绳的缠绕
c 8.6.2锚处理系统 错处理系统的调试条件如下 a 锚处理系统安装检验合格,相关电缆敷设、管路安装验收合格; b 为锚处理系统服务的辅助机械装置、泵及管系已经调试合格 调试用的滑油液压油,油脂等,应符合设备使用说明书的要求并加注完毕,系统试压、串油清 洁工作结束; d 错处理系统的动力、遥控、监测,.报警装置应调试完毕
8.7调试 8.7.1调试项目 调试项目主要包括 电气装置调试 aa 液压系统调试; b 锚处理绞车空转调试; c 锚处理绞车静载荷调试; d 尾滚筒空转调试; e 鲨鱼钳、挡缆桩效用调试; 锚链转移绞车效用调试:; g 报警及监测功能调试
h) 8.7.2电气装置调试 电气装置调试主要过程如下 a 在运转调试前、后,测量各电动机及控制设备冷、热态绝缘电阻,其值不小于1Mn(或根据设 备厂家要求); 在效用调试的情况下,测量和记录电动机的起动电流、工作电流及电压 b 检查各控制设备中的联锁装置、信号,报警装置及安全保护工作的可靠性
c 参照附录B中表B.1填写调试记录
8.7.3液压系统调试 液压系统调试主要过程如下: 利用绝缘表测量各液压泵组电气设备调试前、后的冷、热态绝缘电阻 a b 各液压泵组起、停各3次,测量电动机的起动电流和电压; 各液压泵组空载运转时间不少于30min,调试中测量电动机的工作电流、电压和转速,并记录 液压泵的工作压力;
GB/T39207一2020 d 按要求调试液压系统的溢流阀、缓冲阀、程序阀等安全阀起跳压力,连续调试3次均应合格; e 对温度、液位等开关进行模拟调试 fD 对电磁阀等的电信号进行正确性调试 各液压泵组管系和仪表应无异常的振动、响声,发热和泄漏现象
8 参照表B.2填写调试记录
8.7.4锚处理绞车空转调试 锚处理绞车空转调试主要过程如下 a 调试前确认:驱动系统正常,控制系统正常,动力系统正常 b)操作绞车分别进行正、反向空转约30min,检查绞车的噪声、振动、发热、速度、电流、电压等是 否正常
参照表B.3填写调试记录 8.7.5锚处理绞车静载荷调试 锚处理纹车静载荷调试主要过程如下 根据绞车静载荷调试布置图(如图3所示)进行连接锚处理绞车、钢丝绳、测力计、卸扣,缆 a 桩等; 说明: -处理绞车; -错处理绞车自带的钢丝绳; 测力计 钢丝绳; 缆桩或吊码
图3锚处理绞车静载荷调试布置示意 b)对绞车进行静载荷测试;运转绞车,使得绞车拉力按额定载荷的20%,50%、80%、100%逐级 提升,并在每个级别的拉力时检查绞车、钢丝绳、测力计,卸扣、缆桩等是否正常 使用测力计对绞车的测力元件进行校准:运转绞车,直至测力计显示的拉力为绞车的额定载 荷,然后校准绞车的测力元件; 对绞车进行刹车测试;测试刹车是否正常,检查卷简在刹车刹紧状态下是否出现打滑现象; d 对绞车出绳长度进行模拟测试
e
GB/39207一2020 参照表B.4表B.7填写调试记录
8.7.6尾滚筒空转调试 尾滚筒安装完成后,往尾滚筒的滑动轴承内注人润滑油,然后转动滚筒体,要求尾滚筒转动时阻力 均匀,无卡阻、停顿现象
参照表B.8填写调试记录
8.7.7鲨鱼钳、挡缆桩效用调试 鲨鱼钳、挡缆桩效用调试主要调试过程如下 空载运行调试:启动油泵机组,至少进行3次鲨鱼钳、挡缆桩的升起和回收调试,检查其动作的 可靠性,不应出现动作卡滞、异常噪声或振动等异常情况 b)失电调试;在失电的情况下,应能通过蓄能器回收鲨鱼钳、挡缆桩
参照表B.9填写调试记录 8.7.8 锚链转移绞车效用调试 错链转移绞车效用调试过程如下 空载运行调试启动电机(或油泵机组),进行空载正反转空载运转时间各不少于30min调试 和刹车调试,检查其动作的可靠性,不应有异常情况 b)负荷调试;分别进行静负荷调试、刹车调试
参照表B.10填写调试记录
8.7.9报警及监测功能调试 模拟检测系统温度、压力、液位的高低位报警、过载报警、失电报警等
参照表B,.11填写调试记录
8.8调试数据整理和报告提交 将调试的相关系统功能、数据整理形成报告,提交相关方
GB/T39207一2020 附 录 A 资料性附录) 螺栓扭矩参考表 螺栓扭矩参考表见表A.1
表A.1螺栓扭矩参考表 单位为牛米 组l(8.8级 组2(不锈钢 组3(10.9级 组4(12.9级 螺栓 干式 湿式 干式 湿式 干式 湿式 干式 湿式 M3×0.5 l.25 0.9 0.87 0.66 1.75 1.3 2.l 1.55 3.6 M4X0.7 2.85 2.l l.5 4.8 M5×0.8 5.6 2.95 7.8 4.2 3.9 5.8 9.4 10 12 M6×1 9.7 7.3 6.8 5.2 13.5 16.5 M8×1.25 17 33 24 29 23.5 16.5 12.5 39 M10×1.5 47 35 33 25 66 49 79 59 M12×1.75 81 60 57 43 115 86 135 100 M14×2 130 95 90 68 180 135 215 160 M16×2 195 185 135 240 275 145 200 330 M18×2.5 270 255 38o 280 190 200 460 340 M20×2.5 38o 28o 35o 265 530 390 640 480 M24×3 650 490 610 460 920 690 1100 800 M27×3 950 700 890 660 1350 1000 1600 1200 M30×3.5 1300 950 1200 910 1800 1360 2200 600 2400 M36×4 2250 1650 2100 1550 3200 3800 2800 2900 2000 4100 3000 4900 3600 M39×4 2150 2700 2700 2500 M42×4.5 3600 3400 5100 3800 6100 4500 M48x×5 4000 5100 3800 7600 6700 9100 6800 5400 注:或符合设备厂的栓扭矩要求
0
GB/39207一2020 附录 B 资料性附录) 调试记录表 B.1电气装置调试数据记录见表B.1 表B.1电气装置调试记录表 序号 调试内容 调试结果 电动机调试前的绝缘电阻/Mn 电动机调试后的绝缘电阻/Mn 控制设备调试前的绝缘电阻/Mn 控制设备调试后的绝缘电阻/Mn 起动电流/A 工作电流/A 工作电压/八V 联锁装置,报警装置工作的可靠性 调试人员: 调试日期 B.2液压系统调试数据记录见表B.2
表B.2液压系统调试记录表 序号 调试内容 调试结果 液压系统是否存在泄漏现象 溢流阀、缓冲阀、程序阀等安全阀设定压力/MPa 高温报警温度厂" 1C 高液位报警是否正确 低液位报警是否正确 电磁阀电信号是否正确 调试人员 调试日期 B.3锚处理绞车空转调试数据记录见表B.3 表B.3锚处理绞车空转测试记录表 序号 调试内容 调试结果 调试前确认驱动系统正常 调试前确认控制系统正常 调试前确认动力系统正常 正反空转各运行约30min,检查噪声、振动、温度、速度、密封性等是否正常 调试人员 调试日期 1
GB/T39207一2020 B.4锚处理绞车静载荷测试数据记录见表B.4
表B.4锚处理绞车静载荷测试记录表 序号 项目 记录 检查绞车、钢丝绳、测力计、卸扣、缆桩等是否 测力计显示拉力为锚处理绞 正常 车额定载荷的20%时 记录电流(A/压力(MPa) 检查绞车、钢丝绳、测力计,卸扣,缆桩等是香 测力计显示拉力为锚处理绞 正常 车额定载荷的50%时 记录电流(A)/压力(MPa) 检查绞车、钢丝绳、测力计、卸扣、缆桩等是否 测力计显示拉力为锚处理绞 正常 车额定载荷的80%时 记录电流(A)/压力MPa 检查绞车、钢丝绳、测力计、卸扣、缆桃等是否 测力计显示拉力为锚处理绞 正常 车额定载荷的100%时 记录电流(A/压力(MPa) 调试人员 调试日期 锚处理绞车测力元件校准数据记录见表B.5
B.5 表B.5锚处理绞车测力元件校准记录表 测力计读数 锚处理绞车显示 序号 调试内容 的读数/kN kN 测力计显示的拉力为锚处理绞车额定载荷的1倍时,对锚处理绞 车进行校准 测力计显示的拉力为错处理绞车额定载荷的80%时,记录数据 测力计显示的拉力为处理绞车额定载荷的50%时,记录数据 调试人员: 调试日期: 锚处理绞车刹车调试数据记录见表B.6
B.6 表B.6锚处理绞车刹车调试记录表 序号 调试内容 调试结果 处理绞车拉力达到额定载荷的20%时,刹车是否正常 处理绞车拉力达到额定载荷的50%时,刹车是否正常 锚处理绞车拉力达到额定载荷的80%时,刹车是否正常 错处理绞车拉力达到额定载荷的1o0%时,刹车是否正常 调试人员 调试日期 B.7 锚处理绞车出绳长度调试数据记录见表B.7
12
GB/39207一2020 表B.7锚处理绞车出绳长度调试记录表 序号 显示绳长/ 项目 /m 卷筒收绳若干圈,记录下显示的绳长 卷简放绳若干圈,记录下显示的绳长 调试人员: 调试日期 B.8尾滚筒转动调试数据记录见表B.8
表B.8尾滚筒转动调试记录表 序号 调试内容 调试结果 尾滚简转动时阻力均匀,无卡阻现象 检查尾滚筒是否存在异常漏油 调试人员 调试日期 B.9鲨鱼钳、挡缆桩效用调试数据记录见表B.9
表B.9鲨鱼钳、挡缆桩效用调试记录表 调试内容 调试结果 序号 鲨鱼钳、挡缆桩升起、回收是否顺畅 在失电的情况下,通过蓄能器回收鲨鱼钳,挡缆桃 液压系统是否存在泄漏现象 泵站工作油压/MPa 泵站工作电流/A 泵站工作电压/V 调试人员: 调试日期 B.10错链转移绞车效用调试数据记录见表B.10
表B.10锚链转移绞车效用调试记录表 序号 调试内容 调试结果 空载运行调试;锚链转移绞车正反空转分别约301 min, 检查噪声、振动、温度、速度、密封性等是否正常 静负荷调试:运转错链转移绞车,使得绞车拉力按额定载荷 的20%,50%,80%,100%逐级提升,并在每个级别的拉力时 检查绞车,钢丝绳,测力计,卸扣,缆桩等是否正常 刹车调试;锚链转移绞车的拉力达到额定载荷的20%,50%、 80%、l00%时刹车是否正常 调试人员 调试日期 B.11报警及监测功能调试数据记录见表B.11. 13
GB/T39207一2020 表B.11报警及监测功能调试记录表 序号 名称 报警 数据 备注 系统油位低 系统油位高 系统油压高/MPa 系统油压低/MPa 过载/kN 失电 调试人员: 调试日期 14
锚处理系统安装与调试规程GB/T39207-2020详解
锚处理是一种经常用于土木工程和岩石工程中的技术,具有牢固和耐久的特点。但是,为了保证锚处理系统的安全和可靠性,需要遵循一定的安装和调试规程。
为了规范锚处理系统的安装与调试流程,国家质量监督检验检疫总局、中国国家标准化管理委员会于2020年发布了GB/T39207-2020《锚处理系统安装与调试规程》标准。
该标准主要规定了锚处理系统的安装和调试要求,包括设备安装、管路安装、电气和仪表安装、设备调试等方面。
在设备安装方面,该标准要求进行地基处理、设备基础制作、设备组装、设备安装、设备支撑、管路安装、电气线缆布置等工作,以确保设备的稳定性和安全性。
在管路安装方面,该标准要求进行管路设计、支撑系统设计、管线安装、阀门和附件安装等工作。特别是对于高压管路的安装,需要严格遵循相关规定,确保安全可靠。
在电气和仪表安装方面,该标准要求进行电气线路设计、设备接地、仪表安装和调试等工作,以确保设备的正常运行和安全性。
在设备调试方面,该标准要求进行设备功能检查、设备参数调整和设备运行试验等工作,以确保设备符合设计要求和技术规范。
该标准的发布,对于规范锚处理系统的安装与调试流程具有重要意义。同时,该标准的应用也需要专业人士的全力支持和投入。