GB/T34370.6-2017
游乐设施无损检测第6部分:射线检测
Nondestructivetestingofamusementequipments—Part6:Radiographictesting
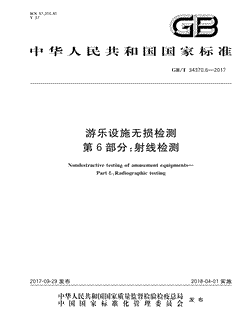
- 中国标准分类号(CCS)Y57
- 国际标准分类号(ICS)97.200.40
- 实施日期2018-04-01
- 文件格式PDF
- 文本页数31页
- 文件大小2.86M
以图片形式预览游乐设施无损检测第6部分:射线检测
游乐设施无损检测第6部分:射线检测
国家标准 GB/34370.62017 游乐设施无损检测 第 g6部分:射线检测 Nondestrctivetestingofamusementequipments Part6Radiographietesting 2017-09-29发布 2018-04-01实施 中华人民共利国国家质量监督检验检疙总局 发布 国家标准化管理委员会国家标准
GB;/T34370.6一2017 前 言 GB/T34370《游乐设施无损检测》分为以下6部分 第1部分:总则 第2部分:目视检测; 第3部分:磁粉检测; 第4部分:渗透检测; 第5部分:超声检测 第6部分:射线检测 本部分为GB/T34370的第6部分
本部分按照GB/T1.1一2009给出的规则起草
本部分由全国索道与游乐设施标准化技术委员会(SAc/TC250)提出并归口
本部分起草单位特种设备检测研究院.山东科捷工程检测有限公司,天津市特种设备监督检 验技术研究院,温州南方游乐设备工程有限公司、中山金马科技娱乐设备有限公司、江苏省特种设备安 全监督检验研究院
本部分主要起草人沈功田,胡斌,梁玉梅,刘欢.张劲松,赵欣、周葛、吴占稳、王伟华、徐达 林金贵.廖绪文,黄班
GB;/T34370.6一2017 游乐设施无损检测 第6部分:射线检测 范围 GB/T34370的本部分规定了游乐设施的熔化焊对接接头的X射线和y射线检测技术和质量分级 要求
本部分适用于游乐设施厚度为2mm200mm的碳素钢低合金钢和不锈钢对接焊接接头的射线 检测
规范性引用文件 下列文件对于本文件的应用是必不可少的
凡是注日期的引用文件,仅注日期的版本适用于本文 件
凡是不注日期的引用文件,其最新版本(包括所有的修改单)适用于本文件 GB/T11533标准对数视力表 GB/T12604.2无损检测术语射线照相检测 GB18871电离辐射防护与辐射源安全基本标准 GB/T19348.1无损检测工业射线照相胶片第1部分工业射线照相胶片系统的分类 GB/T19348.2无损检测工业射线照相胶片第2部分;用参考值方法控制胶片处理 GB/T19802无损检测工业射线照相观片灯最低要求 GB 20306游乐设施术语 GB/T20737无损检测通用术语和定义 GB/T23910无损检测射线照相检测用金属增感屏 GB/T34370.1 第1部分:总则 游乐设施无损检测 GBZ117工业X射线探伤卫生防护标准 GBZ132工业丫射线探伤卫生防护标准 JB/T7902无损检测射线照相检测用线型像质计 术语和定义 GB/T12604.2,GB/T20306和GB/T20737界定的以及下列术语和定义适用于本文件 netratedthickness 透照厚度penm w 射线照射方向上材料的公称厚度
多层透照时,透照厚度为通过的各层材料公称厚度之和
3.2 工件至胶片距离objeet-to-filmdistanee 沿射线束中心测定的工件受检部位射线源侧表面与胶片之间的距离
GB/T34370.6一2017 3.3 射线源至工件距离source-to-objeetdistanee 沿射线束中心测定的工件受检部位射线源与受检工件近源侧表面之间的距离
3.4 焦距foealdistanee F 沿射线束中心测定的射线源与胶片之间的距离
3.5 射线源尺寸soureesize 射线源的有效焦点尺寸
3.6 penetratedthieknes 透照厚度比ratioofmax
andmin. -次透照长度范围内射线束穿过母材的最大厚度与最小厚度之比 33.7 底片评定范围filmevaluationscpe 规定底片上必须观测和评定的范围
3.8 圆形缺陷roundlaw 长宽比不大于3的气孔、夹渣和夹鸽等缺陷
3.9 条形缺陷strpynaw 长宽比大于3的气孔,夹渣和夹等缺陷
方法概要 射线检测是利用物质对射线吸收的原理,通过获得缺陷部位导致物体对射线的吸收改变,引起透射 射线强度的变化,来判断工件中是否存在缺陷以及缺陷的位置,大小,如图1所示
按照射线源可分为 X射线检测、7射线检测等;按照成像方式可分为胶片射线检测成像、计算机辅助胶片成像(CR)和数字 射线成像(DR);按照检测方式可分为固定式检测和移动式检测
GB;/T34370.6一2017 射线议 x射线胶片 相对曝光量少 相对曝光量多 显影处理后胶片的俯视图 图1射线检测原理示意图 安全要求 检测过程中的安全要求至少包括 检测人员应遵守被检件现场的安全要求,根据检测地点的要求穿戴防护工作服和佩戴有关防 a 护设备
游乐设施运行后进行检测,应注意被检件的温度状态.以免烫伤
b 放射卫生防护应符合GB18871GBZ117和GBZ132的有关规定
c d 现场进行X射线检测时,应按GBZ117的规定划定控制区和管理区,设置警告标志
检测工 作人员应佩戴个人剂量计,并携带剂量报警仪
现场进行y射线检测时,应按GBz132的规定划定控制区和监督区、,设置警告标志
检测作 业时,应围绕控制区边界测定辐射水平
检测工作人员应佩戴个人剂量计,并携带剂量报 警仪 本章没有列出进行检测时所有的安全要求,使用本部分的用户应在检测前建立安全准则 人员要求 从事射线检测人员除应符合GB/T34370.1的有关规定外,上岗前应进行辐射安全知识的培训,并 取得放射工作人员证
射线检测人员的未经矫正或经矫正的近(距)视力和远(距)视力应不低于5.0(小 数记录值为1.0),测试方法应符合GB/T11533的规定
从事评片的人员应每12个月检查一次视力
检测设备和器材 7.1成像系统 成像系统可采用胶片成像,也可采用计算机辅助胶片成像(CR)和数字射线成像(DR). 7.2射线胶片 7.2.1胶片系统按照GB/T19348.1分为六类,即c1,c2,c3,C4,c5和c6类
C1为最高类别.C6为
GB/T34370.6一2017 最低类别 7.2.2胶片应按制造商推荐的温度和湿度等条件予以保存
7.2.3采用x射线检测时,应选用C5类或更高类别的胶片;采用射线检测时,应选用C4类或更高类 别的胶片
7.3观片灯 观片灯的主要性能应符合GB/T19802的有关规定
7.4黑度计(光学密度计)和标准密度片 7.4.1黑度计可测的最大黑度应不小于4.5,测量值的误差应不超过士0.05
7.4.2黑度计应使用标准密度片至少每6个月校验一次
7.4.3标准密度片应每两年检定一次
7.5增感屏 射线检淌一般应使用金属蜡感屏或不用增感屏
增感屏的迭用应符合GBT238a0和表1的 规定
表1增感屏的材料和厚度 单位为毫米 前屏 后屏 射线源 材料 材料 厚度/mm 厚度/mm x射线(<100k) 不用或 铅 0.03” 0,03 X射线 铅 S0.15 铅 0.15 (>100kV~150kV X射线 0.02~0.15 0.020.15 铅 铅 (>150kV250kV) x射线 铅 0.02~0.2 铅 0.02~0.2 (>250kV300kV Se75 铅 0.1一0.2 铅 0.1一0.2 铅 Ir192 铅 0.10.2 0.10.2 0.25~0,7" 0,25~0." 钢或铜 钢或铜 Co60 铅 0.5~2.0 铅 0.5~2.0 使用前屏0.03mm的真空包装胶片,应在工件和胶片之间加0.07mm" 0.15mm附加铅屏
7.6像质计 78.】底片影像质量采用线型像质计谢定
线型像质计的型号和规格应符合BT7902的规定
7.6.2应选择像质计材料代号为Fe,其材料为碳钢或奥氏体不锈钢的像质计
检测工艺规程 8 8.1通用检测工艺规程 从事游乐设施射线检测的单位应按GB/T34370.1和本部分的要求制定通用检测工艺规程,其内
GB;/T34370.6一2017 容至少应包括如下要素: 文件编号; a 适用范围 b 执行标准、法规; c 检测人员资格; d 检测仪器设备;名称、型号、源尺寸等; e f 被检件的信息:名称、编号、规格、材质、坡口型式、焊接方法、热处理状况 工件透照部位示意图; g h 透照规范:技术等级、透照布置、胶片,增感屏、射线能量、曝光量、焦距、暗室处理方式和条 件等; 检测时机 检测过程和数据分析解释; j k)检测结果的评定和分级; 检测记录,报告格式; m资料存档; n)编制(级别、审核(级别)和批准人员签字及日期
8.2检测工艺卡 对于每个被检件,根据使用的仪器和现场实际情况,按照GB/T34370.1,本部分和通用检测工艺规 程编制射线检测工艺卡,确定检测的部位和实施条件,如工件透照部位、源安装的部位和表面条件
应 对每个被检件进行测绘,画出被检件结构示意图和透照部位示意图
透照方法和部位的确定,应保证工件被检部分均能得到充分检查
游乐设施制造安装和在用射线检测中,检测时机及抽检率的选择等应按法规、产品标准及有关技术 文件的要求和原则进行
检测工艺卡内容应至少包括 a 工艺卡编号; 检测执行的标准和质量等级要求 b 被检测工件的信息;名称、编号、材质、规格尺寸、热处理状态、焊接型式等; d 检测设备;名称,规格型号、编号/源尺寸或有效焦点尺寸)等; 透照规范:检测技术等级、,透照布置、胶片(牌号及其分类等级)、增感屏(类型、数量和厚度)、像 质计,滤光板、背散射屏蔽铅板、射线能量、曝光量或透照时间、射线源与胶片的相对关系、射线 源至工件表面的距离、源侧工件表面至腔片的距离、暗室处理方式和条件等 检测时机 检测区域和表面要求; 8 h) 检测部位示意图 检测比例; 检测环境要求; j 评片记录; k D 编制(级别)和审核(级别人员签字及日期
GB/T34370.6一2017 9 检测 g.1检测前的准备 9.1.1资料审查 资料审查应包括下列内容 a 被检设备制造文件资料:被检部件的竣工图(含焊缝布置图、有关设计文件对无损检测的要 求、相关的无损检测报告等; b 被检设备运行记录资料:开停车情况、使用环境、使用条件、载荷变化情况以及运行中出现的异 常情况等; 检验资料;历次检验检测报告 d 其他资料维护保养、修理和改造的文件资料等
g.1.2现场勘察 应对被检件现场进行勘察,找出所有可能影响检测的因素,如表面条件、结构形式等
在检测时应 尽可能避免这些因素的干扰
9.1.3检测工艺卡的编制 按8.2执行
9.1.4表面要求 在射线检测之前,对接焊接接头的表面应经目视检测并合格
表面的不规则状态在底片上的影像 不得掩盖或干扰缺陷影像,否则应对表面作适当修整
9.1.5检测时机 除非另有规定,射线检测应在焊接完工后进行
对有延迟裂纹倾向的材料,至少应在焊接完成24h 后进行射线检测
9.2透照布置 g.2.1透照方式 应根据工件的特点和技术条件的要求选择适宜的透照方式
在可以实施的情况下应选用单壁透照 方式,在单壁透照不能实施时才允许采用双壁透照方式
典型的透照方式参见附录A
9.2.2透照方向 透照时射线束中心一般应垂直指向透照区中心,需要时也可选用有利于发现缺陷的方向透照 9.2.3一次透照长度 -次透照长度以透照厚度比K控制
不同类型焊缝的透照厚度比应符合表2的规定
整条环向 焊接接头所需的透照次数可参见附录B的曲线图确定
GB;/T34370.6一2017 表2允许的透照厚度比K 纵向炽接接头 K<1.03 环向焊接接头 K1.1" mm的环向媒接接头(包括曲率相同的曲面媒接接头),允许采用K<1.2
D为公称 对100mm
GB;/T34370.6一2017 方反比定律对曝光量进行换算
9.5.2采用y射线源透照时,总的曝光时间至少应不小于输送源往返所需时间的10倍
9.6曝光曲线 9.6.1对每台在用的X射线设备均应做出游乐设施常用材料的曝光曲线,依据曝光曲线确定曝光 参数
9.6.2制作曝光曲线所采用的胶片,增感屏,焦距、射线能量等条件和底片应达到的灵敏度、黑度等参 数均应符合本部分的规定
9.6.3对使用中的曝光曲线,每年至少应校验一次
射线设备更换重要部件或经较大修理后应及时对 曝光曲线进行校验或重新制作
9.6.4采用射线源时,可选用曝光尺等方式计算曝光时间
9.7无用射线和散射线屏蔽 9.7.1应采用金属增感屏、铅板、滤光板和准直器等适当措施,屏蔽散射线和无用射线,限制照射场 范围 9.7.2对初次制定的检测工艺或检测工艺的条件,环境发生改变时,该检测工艺在应用于正式检测时 应进行背散射防护检查
检查背散射防护的方法是;在暗盒背面贴附“B”铅字标记,一般B铅字的高度为13mm,厚度为 1.6mm,按检测工艺的规定进行透照和暗室处理
若在底片上出现黑度低于周围背景黑度的“B”字影 像,则说明背散射防护不够,应增大背散射防护铅板的厚度
若底片上不出现“B"字影像或出现黑度高 于周围背景黑度的“B”字影像,则说明背散射防护符合要求
9.8像质计的使用 9.8.1像质计一般应放置在工件源侧表面焊缝的一端(在被检区长度的1/4左右位置),金属丝应横跨 焊缝,细丝置于外侧
当 -张胶片上同时透照多条焊接接头时,像质计应放置在透照区最边缘的焊 缝处
9.8.2像质计放置原则 a 单壁透照规定像质计放置在源侧
双壁单影透照规定像质计放置在胶片侧
双壁双影透照像 质计可放置在源侧也可放置在胶片侧
b 单壁透照中,如果像质计无法放置在源侧,允许放置在胶片侧
单壁透照中像质计放置在胶片侧时,应进行对比试验
对比试验方法是在射源侧和胶片侧备 放 一个像质计,用与工件相同的条件透照,测定出像质计放置在源侧和胶片侧的灵敏度差异, 以此修正像质指数规定,以保证实际透照的底片灵敏度符合要求
当像质计放置在胶片侧时,应在像质计上适当位置放置铅字“F”作为标记,F标记的影像应与 像质计的标记同时出现在底片上,且应在检测报告中注明
9.8.3原则上每张底片上都应有像质计的影像
当一次曝光完成多张胶片照相时,允许减少使用的像 质计数量 环向焊接接头采用源置于中心周向曝光时,至少在圆周上等间隔地放置3个像质计 a 次曝光连续排列的多张胶片时,至少在第一张、中间一张和最后一张胶片处各放置一个像 b 质计
9.8.4小径管可选用普通线型像质计或附录D规定的专用(等径金属丝)像质计时,金属丝应横跨焊缝
GB/T34370.6一2017 放置
像质计应置于源侧,当无法放置在源侧时,可将像质计置于胶片侧
9.8.5底片上,在黑度均匀区(一般是邻近焊缝的母材金属区)能够清晰地看到长度不小于10mm的连 续的金属丝影像时,则该丝认为是可识别的
专用像质计应能识别不少于两根金属丝
g.9标记 9.9.1透照部位的标记由识别标记和定位标记组成
标记一般由适当尺寸的铅(或其他适宜的重金 属)制数字、拼音字母和符号等构成
9.9.2识别标记一般包括;制造单位(和/或检测单位)标识、产品编号、焊接接头编号,部位编号和透照 日期
返修后的透照还应有返修标记,扩大检测比例的透照还应有扩大检测标记
9.9.3定位标记一般包括中心标记和搭接标记
中心标记指示透照部位区段的中心位置和分段编号 的方向,一般用十字箭头“伞”表示
搭接标记是连续检测时的透照分段标记,可用符号“个”或其他能 显示搭接情况的方法表示
9.9.4标记一般应放置在距焊缝边缘至少5mm以外的部位,搭接标记放置的部位还应符合附录E的 规定
所有标记的影像不应重叠,且不应干扰有效评定范围内的影像
9.10胶片处理 9.10.1可采用自动冲洗或手工冲洗方式处理,推荐采用自动冲洗方式处理
9.10.2胶片处理一般应按胶片使用说明书的规定进行
g.11评片要求 9.11.1评片一般应在专用的评片室内进行
评片室应整洁、安静,温度适宜,光线应暗且柔和
9.11.2评片人员在评片前应经历一定的暗适应时间
从阳光下进人评片的暗适应时间一般为5min 10min;从一般的室内进人评片的暗适应时间应不少于30s
9.11.3评片时,底片评定范围内的亮度应符合下列规定: aa 当底片评定范围内的黑度D<2.5时,透过底片评定范围内的亮度应不低于30cd/m'; b) 当底片评定范围内的黑度D>2.5时,透过底片评定范围内的亮度应不低于10cd/m g.11.4底片评定范围的宽度一般为焊缝本身及焊缝两侧5mm宽的区域
因结构或焊接方法等原因 需要增大焊缝两侧评定宽度的,评定范围的宽度由合同各方商定
9.12底片质量 9.12.1底片上的标记影像应显示完整、位置正确
9.12.2底片评定范围内的黑度D应符合下列规定 2.0
GB;/T34370.6一2017 表4像质计灵敏度值单壁透照,像质计置于源侧 单位为毫米 应识别丝号 公称厚度丁范围 丝径 18(0.063 17(0.,080) 2.0 16(0.100y >2.0~3.5 15(0.125) >3.5~5.0 14(0.160 >5.07 13(0.20) >710 12(0.25) >10~15 1(0.32) >l5一25 10(0.40 >25一32 9(0.50) >324o 8(0.63) >4055 7(0.80) >55~85 >85150 6(1,00) 5(1.25 >150~250 4(1.60) >250~350 3(2.00 >350 2(2.50 表5像质计灵敏度值 -双壁双影透照、像质计置于源侧 单位为毫米 应识别丝号(丝径) 透照厚度w范围 18(0.063 170.080 2.0 16(0.100 3.5 15(0.125 >3.55.0 14(0.160) >57 >712 13(0.20 12(0.25 >1218 11(0.32 >1830 10(0.40 >3040 9(0,.50) >4050 >50~60 8(0.63 7(0.80 6085 6(l.,00 >85120 5(1.25 1
GB/T34370.6一2017 表6像质计灵敏度值 -双壁单影或双壁双影透照、像质计置于胶片侧 单位为毫米 应识别丝号(丝径 透照厚度W范围 18(0.063 17(0.080 2.0 16(0.100y >2.03.5 15(o0.125 >3.55.0 14(0.160) >51o 13(0,20 >1015 12(0,25 >1522 11(0,32) >22~38 10(0,40) >38~48 g(0.50 一48~60 8(0.63)y >6085 7(0.80) >85~125 6(1.00 >125225 5(1.25) >225~375 4(1.60 >375 32.00 g.13检测记录 应按检测工艺规程的要求记录检测数据和有关信息,除此之外,还应至少包括8.2和第12章中的 内容
10钢制熔化焊对接接头射线检测质量分级 10.1质量分级条件 本条规定适用于厚度为2mm一200mm,材质为碳索素钢、低合金钢、奥氏体不锈钢的熔化焊对接接 头射线检测的质量分级
10.2缺陷类型 煤接接头中的缺陷按性质区分为裂纹,未熔合、未煤透、条形缺陷和圆形缺陷五类
10.3质量等级的划分 根据焊接接头中存在的缺陷性质、数量和密集程度,焊接接头的质量等级划分为I、I、、爪级 10.4质量分级一般规定 10.4.1I级焊接接头内不允许存在裂纹,未熔合、未焊透和条形缺陷
10.4.2级和皿级焊接接头内不允许存在裂纹、未熔合和未焊透
12
GB;/T34370.6一2017 10.4.3焊接接头中缺陷超过级者为级
10.4.4当各类缺陷评定的质量级别不同时,以质量最差的级别作为焊接接头的质量级别
10.5圆形缺陷的分级评定 0.5.1圆形缺陷用评定区进行质量分级评定,缺陷评定区为一个与焊缝平行的矩形,其尺寸见表7 缺陷评定区应选在缺陷最严重的区域
表7缺陷评定区 单位为毫米 母材公称厚度T >25一100 100 10×1o 评定区尺寸 10×20 10×X30 10.5.2在缺陷评定区内或与缺陷评定区边界线相割的缺陷均应划人评定区内
将评定区内的缺陷按 表8的规定换算为点数,按表9的规定评判焊接接头的质量级别
表8缺陷点数换算表 缺陷长径/mm 68 25 缺陷点数 15 表9各级允许的圆形缺陷最多点数 评定区/mm×mm 10×10 10×20 10×30 母材公称厚度T/n /mm 1015 1525 2550 50100 100 I级 级 12 15 18 级 12 18 24 30 36 级 缺陷点数大于级或缺陷长径大于T/2 注:当母材公称厚度不同时,取较薄板的厚度
10.5.3由于材质或结构等原因,进行返修可能会产生不利后果的焊接接头,经合同各方同意,各级别 的圆形缺陷点数可放宽1一2点
10.5.4当缺陷的尺寸小于表10的规定时,分级评定时不计该缺陷的点数
I级接头和母材公称厚度 T<5nmm的l级接头,不计点数的缺陷在圆形缺陷评定区内不得多于10个,超过时接头质量应降低 -级
表10不计点数的缺陷尺寸 单位为毫米 母材公称厚度T 缺陷长径 25 S0.5 25
GB;/T34370.6一2017 1.4.3焊接接头中缺陷超过级者为级
11.4.4当各类缺陷评定的质量级别不同时,以质量最差的级别作为焊接接头的质量级别
11.5圆形缺陷的分级评定 按10.5的规定进行质量分级评定
但对D,<100mm小径管缺陷评定区取10mm×10mm. 11.6条形缺陷的分级评定 按10.6的规定进行质量分级评定
11.7不加垫板单面焊的未焊透缺陷的分级评定 管公称直径D.>100mm时,不加垫板单面焊的未焊透缺陷按表12的规定进行质量分级评定 管公称直径D.<100mm的小径管的不加垫板单面媒的未媒透缺陷按表13的规定进行质量分级评 定
未焊透深度应采用附录下规定的未焊透专用对比块进行测定,测定时未焊透专用对比块应置于管 的源侧表面、靠近被测未焊透缺陷附近部位
表12管公称直径D.>100mm时不加垫板单面焊未焊透的分级 单位为毫米 未焊透最大深度 单个未媒透 级别 未焊透累计长度 最大长度 与壁厚的比 最大值 不允许
GB/T34370.6一2017 允许存在的根部内凹和根部咬边应符合表15的规定
根部内凹和根部咬边深度应采用附录F规定的 沟槽对比块进行测定
测定时沟槽对比块应置于管源侧表面、靠近被测根部内凹或根部咬边缺陷附近 部位
单位为毫米 表14管公称直径D.>100mm时根部内凹和根部咬边的分级 根部内凹和根部咬边最大深度 级别 根部内凹和根部咬边累计长度 与壁厚的比 最大值 不允许 <15% <1.5 在任意3T长度区内不大于T; 总长度不大于100 二20% 二2.0 大于川级 注:对断续根部内四和根部咬边,以根部内凹和根部咬边本身的长度累计计算总长度
表15管公称直径D,<100mm时根部内凹和根部咬边的分级 单位为毫米 根部内凹和根部咬边最大深度 根部内凹和根部咬边最大总长度 级别 与焊缝总长度的比 与壁厚的比 最大值 不允许 <1.5 15% 30% <20% <2.0 30% 大于叩级 注对断续根部内凹和根部咬边,以根部内凹和根部咬边本身的长度累计计算总长度
11.9综合评级 11.9.1对公称直径D.>l00 mm的管道焊接接头,在条形缺陷评定区内同时存在条形缺陷和未焊透 根部内凹或根部咬边时,应进行综合评级;在未焊透累计长度的评定区(即6T或3T长度区)同时存在 未焊透、根部内凹或根部咬边时,应进行综合评级
11.9.2综合评级的级别如下确定:对各类缺陷先分别评定级别,取质量级别最差的级别作为综合评级 的级别;当各类缺陷的级别相同时,取降低一级后的级别作为综合评级的质量级别
12射线检测报告 检测报告应至少包括下述内容 制造单位、检测单位或委托单位; a b 被检工件名称和编号; 检测标准和验收等级; d 被检工件材质,坡口型式,焊接方法,热处理状况及表面状态 检测部位和比例; e 检测设备:名称,型号,源尺寸(或有效焦点尺寸); 透照规范:检测技术等级,透照布置、胶片牌号及其分类等级,增感屏(类型、数量和厚度,像 8 16
GB;/T34370.6一2017 质计,滤光板、背散射屏蔽铅板、射线能量,曝光量或透照时间,射线源与胶片的相对关系,射线 源至工件表面的距离、源侧工件表面至胶片的距离、暗室处理方式和条件等; 工件透照部位示意图; h) 底片评定;底片黑度、底片像质计灵敏度、缺陷位置和性质; 检测日期 j kk 检测结果及质量等级评定; 检测人员和审核人员签字、日期及其资格
17
GB/T34370.6一2017 附 录 A 资料性附录) 典型透照方式示意图 A.1典型透照方式示意 图A.1图A.8给出了常用的典型透照方式示意图,可供确定透照布置时参考
图中d表示射线 源,F表示焦距,b表示工件至胶片距离,表示射线源至工件距离,丁表示公称厚度,D.表示管子公称 直径
图A.1纵、环向焊接接头单壁透照方式(1 图A.2纵、环向悍接接头单壁透照方式(2) 图A.3环向焊接接头源在中心周向透照方式 图A.4环向焊接接头源在外双壁单影透照方式(1 图A.5环向焊接接头源在外双壁单影透照方式(2 图A.6纵向焊接接头源在外双壁单影透照方式 图A.7小径管对接环向焊接接头倾斜透照方式 图A.8小径管对接环向焊接接头垂直透照方式 注;图A.1,图A.3,图A.5和图A.7为椭圆成像;图A.2,图A.4,图A.6和图A.8为重叠成像 18
GB;/T34370.6一2017 附录 B 资料性附录 环向对接焊接接头透照次数确定方法 B.1透照次数曲线图 对公称直径D.>100mm的对接环向焊接接头进行100%检测,所需的最少透照次数与透照方式 和透照厚度比有关,这一数值可从图B.1图B.4中直接查出
图B.1为源在外单壁透照对接环向焊接接头,透照厚度比K=1.1的透照次数曲线图 aa 图B.2为用其他方式(偏心内透法和双壁单影法)透照对接环向焊接接头,透照厚度比K=1.1 b 的透照次数曲线图; 图B.3为源在外单壁透照对接环向焊接接头,透照厚度比K=1.2的透照次数曲线图: c 图B.4为用其他方式(偏心内透法和双壁单影法)透照对接环向焊接接头,透照厚度比K=1.2 d 的透照次数曲线图
B.2由图确定透照次数的方法 从图中确定透照次数的步骤是;计算出T/D.、D./f,在横坐标上找到T/D
值对应的点,过此点 画一垂直于横坐标的直线;在纵坐标上找到D./对应的点,过此点画一垂直于纵坐标的直线;从两直 线交点所在的区域确定所需的透照次数;当交点在两区域的分界线上时,应取较大数值作为所需的最少 透照次数
19
GB/T34370.6一2017 3.5 2.5 S 1.5 0.5 0.25 0.05 0.15 T/D 图B.1源在外单壁透照对接环向焊接接头,透照厚度比K=1.1时的透照次数 20
GB;/T34370.6一2017 1.2 0.8 0.6 0.2 0.05 0.2 0.25 T/D 图B.2其他方式透照对接环向焊接接头,透照厚度比K=1.1时的透照次数 21
GB/T34370.6一2017 N=15 3.5 2.5 0.5 0.05 0.15 0.25 T/D 图B.3源在外单壁透照对接环向焊接接头,透照厚度比K=1.2时的透照次数 22
GB;/T34370.6一2017 1.8 1.6 0.8 0.6 0.2 0.25 a.05 O.5 0.1 D 图B.4其他方式透照对接环向焊接接头,透照厚度比K=1.2时的透照次数 23
GB/T34370.6一2017 附 录 规范性附录) 焦点尺寸计算方法 射线源焦点形状,按图c.1所示划分为正方形、长方形、圆形、椭圆形四类,其有效焦点尺寸d分别 按式(C.1)、式(C.2)和式(C.3)计算
正方形焦点: a (C.1) d 长方形、椭圆形焦点: =(a十b)/2 C.2 d 圆形焦点 C.3 dl 正方形 长方形 因形 椭圆形 图C.1焦点形状分类 24
GB;/T34370.6一2017 附 录 D 规范性附录 专用像质计的型式和规格 D.1专用像质计的样式 专用像质计的样式如图D.1所示,丝的数目一般为5根,有特殊要求时也可为3根
D.2专用像质计的型式、规格、材料 专用像质计的型式、规格、材料等应符合7.6的规定
FEA 图D.1专用像质计的基本样式 25
GB/T34370.6一2017 附 录 规范性附录) 搭接标记的摆放位置 E.1搭接标记的摆放位置 搭接标记的摆放位置应符合图E.1一图E.5所示的规定
不应在胶片倒 应在射线源的一倒 应在射线源一侧 不应在胶片倒 图E.1平面工件或纵焊接接头 图E.2射线源到胶片距离F小于曲面工件的曲率半径 应在射线源- 侧 不应在射线源 不应在胶片侧 应在胶片侧 图E.3凸面朝向射线源的曲面部件 图E.4射线源到胶片距离F大于曲面工件的曲率半径 两种都以采用 的位置标记 图E.5射线源在曲面工件的曲率中心 26
GB;/T34370.6一2017 附录 F 规范性附录 对比试块的型式和规格 F.1对比试块 对比试块分为未焊透专用对比试块和沟槽对比试块两种
制作对比试块的材料应与被检工件的材 料相同
F.2未焊透专用对比试块的型式,规格和尺寸 未焊透专用对比试块的型式、规格和尺寸应符合图F.1和表F.1的规定
F.3沟槽对比试块的型式,规格和尺寸 沟槽对比试块的型式,规格和尺寸应符合图F.2和表F.2的规定
单位为毫米 c一(旋转 4一4旋转 B一旋转 b 图F.1未焊透专用对比试块 表F.1未焊透专用对比试块的尺寸 单位为毫米 第一阶厚度 第二阶厚度 第三阶厚度 管壁厚T 偏差 偏差 偏差 T T 3.5 0.65 0.5 0.6 0,4 十0.025 十0.025 -0.6 0.5 0.25 0. 27
游乐设施无损检测第6部分:射线检测GB/T34370.6-2017
在游乐设施的设计、制造、使用和维护过程中,安全问题一直是最重要的考虑因素。然而,由于游乐设施结构的复杂性和特殊性质,安全隐患常常难以发现。
为了确保游乐设施的安全运行,无损检测成为了一个必不可少的环节。射线检测作为其中一种重要的方法,可以有效地检测出隐藏在结构中的缺陷,并提供必要的修复建议。
射线检测主要使用X射线和伽马射线进行测试。通过对设备的辐射后,利用相应的传感器和软件对辐射图像进行分析,就能够确定结构内部的缺陷位置和大小。
与其他无损检测方法相比,射线检测具有以下优点:
- 可以检测出小到0.1mm的缺陷;
- 适用于各种结构,包括混凝土、金属、玻璃等材料;
- 对被测设备没有影响,无需停机维修。
此外,射线检测还具有一定的局限性。由于辐射会对人体造成伤害,因此必须采取必要的防护措施。同时,设备和材料的厚度也会对检测结果产生影响。
为了保证射线检测的准确性,国家标准化管理委员会发布了GB/T34370.6-2017《游乐设施无损检测第6部分:射线检测》标准。该标准规定了射线检测的技术要求、仪器设备要求、操作规程以及安全防护要求。
总之,射线检测作为游乐设施无损检测的重要方法之一,能够有效地发现结构内部的缺陷,提供必要的修复建议,从而保障游乐设施的安全运行。同时,遵守相应的标准也是射线检测必不可少的要素。