GB/T28762-2012
数控剪板机
NCshears
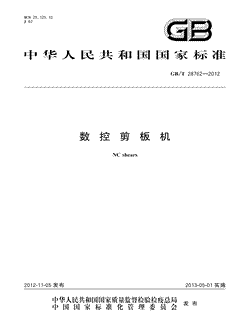
- 中国标准分类号(CCS)J62
- 国际标准分类号(ICS)25.120.10
- 实施日期2013-05-01
- 文件格式PDF
- 文本页数16页
- 文件大小617.67KB
以图片形式预览数控剪板机
数控剪板机
国家标准 GB/28762一2012 数控剪板机 NCshears 2012-11-05发布 2013-05-01实施 国家质量监督检监检疫总局 发布 国家标准花管理委员会国家标准
GB/T28762一2012 前 言 本标准按照GB/T1.1一2009给出的规则起草 本标准由机械工业联合会提出 本标准由全国锻压机械标准化技术委员会(SAC/TC220)归口
本标淮起草单位;佛山市南海力丰机床有限公司,天水锻压机床有限公司南京埃斯顿自动化股份 有限公司、沈阳锻压机械制造有限公司安徽省三力机床制造股份有限公司
本标准主要起草人;周建军,紫礼泉、,吴波、岳春娟,陈道宝、陈木胜
GB/T28762一2012 数控剪板机 范围 本标准规定了数控剪板机的术语和定义、技术要求、精度,试验方法,检验规则、标志、标牌,包装,运 输和贮存
本标准适用于数控剪板机,具有数控送料装置的剪板机也可参照使用
规范性引用文件 下列文件对于本文件的应用是必不可少的
凡是注日期的引用文件,仅注日期的版本适用于本文 件
凡是不注日期的引用文件,其最新版本(包括所有的修改单)适用于本文件 包装储运图示标志(Iso780) GB/T191 GB/T1184一1996形状和位置公差未注公差值(Is02768-2,1989 GB/T1348球墨铸铁件(Iso1083) -般公差未注公差的线性和角度尺寸的公差(Is2768-1:1989) GB/T18042000 GB2893安全色(ISO3864-1 安全标志及其使用导则 GB2894 GB/T3766液压系统通用技术条件(Iso4413 GB5226.1一2008机械电气安全机械电气设备第1部分;通用技术条件(IEC602041;2005) GB/T6576 机床润滑系统(1so.3170) GB/T7932 气动系统通用技术条件(4so41n) 液压元件通用技术条件 GB/T7935 GB/T9969 工业产品使用说明书总则 GB/T100891988圆柱蜗杆、蜗轮精度 圆柱齿轮精度制第1部分;轮齿同侧齿面偏差的定义和允许值(Iso1328-1) GB/T10095.1 GB/T10095 2 圆柱齿轮 ;径向综合偏差与径向跳动的定义和允许值 精度制第2部分: (ISO1328-2 GB/T10923-2009锻压机械精度检验通则(IsO230-l;1996 GB/T11365-1989锥齿轮和准双曲面齿轮精度 GB/T13306标牌 GB/T14404201l 剪板机精度 G;B17120锻压机械安全技术条件 GB/T23281锻压机械噪声声压级测量方法(ISOl1202 GB/T23282锻压机械噪声声功率级测量方法(ISO3746 GB24389剪切机械噪声限值 JB/T1826剪板机型式与基本参数 JB/T1826.1剪板机名词术语 JB/T1828.1剪板机用刀片型式与基本参数 JB/T1828.2剪板机用刀片技术条件
GB/T28762一2012 JB/T1829锻压机械通用技术条件 JB/T3240锻压机械操作指示形象化符号 JB/T5775锻压机械灰铸铁件技术条件 JB/T8356.1机床包装技术条件 JB/T8609锻压机械焊接件技术条件 JB8781剪板机安全技术要求 JB/T8832机床数控系统通用技术条件 JB/T9954锻压机械液压系统清洁度 术语和定义 JB/T1826.1界定的以及下列术语和定义适用于本文件
3.1 数控剪板机Ncshear 刀架和/或挡料装置采用数控系统控制的勇板机
3.2 退让retract -种控制功能,挡料装置在剪切过程中向远离刀口的方向运动一段距离,以避免挡料、刀具与工件 之间发生干涉
3.3 寻参考点rindreferenee -种控制功能,用于确定数控轴相对于其坐标原点的位置
3 示教leadthrough -种控制功能,数控系统接受人工输人的数值,并将其作为当前位置,用于代替寻参考点操作
3.5 计数eount -种控制功能,累计剪切加工次数
3.6 手动 种数控系统执行模式,由用户手工输人目标位置,然后启动定位和加工
? 自动manual 种数控系统执行模式,由用户输人加工程序,数控系统按照程序要求执行定位和加工 8 ? sition 单向定位unidireetional lp0s -种控制功能,通过某种定位操作消除丝杆、螺母之间的间隙,提高定位精度
3 安全区 SafeZOne 在运动部件行程上的某些区域,在这些区域内运动部件只能以安全速度运行
3.10 数控剪板机的各数控轴NCaxisofNCshears 控制数控剪板机运动的数控轴
GB/T28762一2012 3.10.1 X轴Xaxis 控制挡料装置前后运动的数控轴
3.10.2 A轴 A aXxis 控制剪板机刀架剪切角度的数控轴
3.10.3 G轴Gaxis 控制剪板机上下刀片剪切间隙的数控轴
3.10.4 S轴Saxis 控制勇板机刀架剪切行程的数控轴
技术要求 般要求 4.1.1数控剪板机的图样及技术文件应符合本标准和技术文件的规定,并应按照规定程序经批准后, 方能投人生产 4.1.2数控剪板机出厂时应保证其完整性,并备有正常使用和维修所需的配套件和工具;特殊附件由 用户和制造厂共同商定,随机供应或单独订货
外购件(包括电气、液压、气动元件等)应符合技术文件 的规定,并须与主机同时进行运转试验
4.1.3数控剪板机的工作机构和操作、调整机构动作应准确、协调;当一个操作循环完成时,刀架应可 靠地停在上死点
操作用手柄、脚踏装置等动作应安全、灵活、可靠
4.1.5数控剪板机设计时应满足在两班制工作且在遵守使用规则的条件下,其至第1次计划大修前的 使用时间应不低于5年
4.1.6使用说明书应符合GB/T9969的规定,使用说明书的内容应包括安装、,运输、贮存,使用维修和 安全方面的要求及说明
4.2参数 数控剪板机的参数应符合JB/T1826或产品设计文件的规定 4.3刚度 数控剪板机的刚度应符合技术文件的规定
安全与防护 数控剪板机的安全与防护应符合GB17120和JB8781的要求
4.5铸、锻、焊件 灰铸铁件应符合JB/T5775的规定;球墨铸铁件应符合GB/T1348的规定;焊接件应符合 4.5.1 JB/T8609的规定;锻件和有色金属件应符合JB/T1829和技术文件的规定,对不影响使用和外观的缺 陷.在保证质量的条件下,允许按技术文件的规定进行修补
4.5.2机架、刀架、工作台,缸体、活塞、调节螺杆、活塞杆、刀具等重要的铸、锻件和焊接件应进行消除 内应力处理
GB/T28762一2012 4.6零件加工 4.6.1零,部件的加工应符合设计、工艺技术文件的要求,已加工表面不应有毛刺、斑痕和其他机械损 伤,除特殊规定外,均应将锐边倒钝 4.6.2刮研的轴瓦、轴套、导轨的滑动面和重要平面,其接触情况应在工作位置检验(如轴瓦应压人瓦 座内)
轴瓦、轴套和导轨工作表面的刮研点应均匀,用配合件(或检验平板、检验棒)做涂色检验时,在 300cnm'面积内平均计算(不足300cmm按实际面积平均计算),每25mm×25mm 面积内的接触点数 不应小于表1的规定;移置导轨接触点数允许相应降低2点
轴瓦、轴套和导轨表面刮研点数 表 1 导轨宽度/mm 轴承直径/mm 接触点数/点 150 <120 >150 >120 注1:不适用于复合材料轴承
注2:一组不同宽度的导轨按宽导轨的规定点数检验
数控剪板机的主要导轨、刀架、缸体、活塞杆等主要摩擦副应采取耐磨措施
4.6.3 4.6.4用金属制造的操作手轮轮缘和操作手柄应抛光镀铬或采取其他防锈措施,但不得涂漆
刀片应符合JB/T1828.1、JB/T1828.2的规定 4.6.5 4.7装配 4.7.1数控剪板机应按装配工艺规程进行装配,装配到数控勇板机上的零、部件均应符合质量要求,不 允许装人图样上未规定的垫片、套等零件
4.7.2机架、导轨、工作台等重要的固定结合面应紧密贴合,紧固后,用0.04mm塞尺进行检验,只许 塞尺局部插人,其插人深度一般不应超过接触宽度的20%,且可插人部分的累计长度一般不应超过可 检长度的10%
4.7.3啮合齿轮安装后的轴向错位不应大于表2规定
表2齿轮啮合轴向错位允差 单位为毫米 较宽的齿轮轮缘宽度 中心错位小于 二50 l.5 >5015o >150 4.7.4渐开线圆柱齿轮、锥齿轮、圆柱蜗杆、蜗轮精度不应低于表3的规定
表3齿轮,圆柱蜗杆,蜗轮精度等级 标准号 精度等级 GB/T10095." 渐开线圆柱齿轮 GB/T10095.2 锥齿轮 GB/T11365一1989 9-9-8 圆柱蜗杆、蜗轮 GB/T100891988 注:不适用于手动传动
GB/T28762一2012 4.7.5数控剪板机部件的温升应符合下列规定 滑动轴承的温升不应超过35C,最高温度不应超过70C; a b)滚动轴承的温升不应超过40C,最高温度不应超过70C 滑动导轨的温升不应超过15C,最高温度不应超过50 4.8 电气设备和数控系统 4.8.1数控剪板机的电气设备应符合GB5226.1的规定
4.8.2数控系统应符合JB/T8832的规定,数控系统的平均无故障工作时间不小于5000h,并应具有 以下基本功能: 单向定位功能; a b)限制数控轴线可以运行的范围, c) 具有接受补偿数据,修正误差的功能; d)具有自动退让的控制功能; 为挡料装置的最小和最大行程位置保留安全区设置,挡料在安全区内应以低速运行 具备记录加工次数的功能,计数方向应可以选择 f 计数完成后的处理可以采用下述方法之 计数到达设定值后停机(增计数).; 计数到达0后停机(减计数); h)具有自动寻参考点的功能,寻参考点速度应采用低速; 提供示教功能代替寻参考点操作; 至少应具备手动、自动操作模式 j k 断电后,数控系统应能保存加工相关数据 D 提供监控数字量1/0端口状态的方法; nm至少应为下述系统部件提供诊断的方法 输人端口 输出端口 按键; 显示部件(LED,.LCD); 数据存储器
4.9液压和气动系统 4. .g.1数控剪板机的液压系统应符合GB/T3766的规定,液压元件应符合GB/T7935的规定,气动 系统应符合GB/T7932的规定
4.9.2工作部件在规定的范围内不应有爬行、停滞、振动,在换向和卸压时不应有明显的冲击现象
4.9.3对于有比例或伺服阀的液压系统,液压泵的出油口应设置高压滤油器
4.9.4液压、气动系统的油、气不应有渗漏现象
4.9.5数控剪板机的液压系统的清洁度应符合JB/T9954的规定 4.9.6液压泵进口的油液温度不应超过60C
4.10润滑系统 4.10.1数控剪板机应有可靠的润滑装置,润滑管路的润滑点应有对应的编号标志,保证各运转部位得 到正常润滑,润滑系统应符合GB/T6576的规定
4.10.2 重要摩擦部位的润滑一般应采用集中润滑系统,只有当不能采用集中润滑系统时才可以采用
GB/T28762一2012 分散润滑装置,分散润滑应单独设置润滑标牌,标牌上应注明润滑部位
4.10.3润滑系统的油不应有渗漏现象 4.10.4转动部位的油不得甩出,对非循环稀油润滑部位应有集油回收装置
4.11噪声 数控剪板机的齿轮传动机构、电气、液压部件等工作时的声音应均匀,不得有不规则的冲击声和周 期性的尖叫声,其噪声应符合cB21389的规定
4.12外观 4.12.1数控剪板机的外表面,不应有图样未规定的凸起、凹陷或粗糙不平
零、部件结合面的边缘应 整齐、匀称,其错偏量和门盖缝隙允差应符合表4的规定
表4零、部件结合面及门盖缝隙允差 单位为毫米 结合面边缘及门盖边缘尺寸 错位不匀称量 缝隙不匀称量 错位量 贴合缝隙量 <500 1.5 1.0 1.0 2.0 >500l250 1.0 1.0 1.5 3.5 >1250一3150 1.0 l.5 2.0 4.0 3150 注:边缘尺寸是指长边尺寸
4.12.2数控剪板机的防护罩应平整、匀称,不应有翘曲、凹陷
4.12.3埋头螺钉不应突出于零件外表面,固定销一般应略突出于零件外表面,突出值约为倒角值,螺 栓尾端应突出于螺母之外,突出值不应大于其直径的1/5,外露轴端应突出其包容件端面,突出值约为 袖端倒角值
4.12.4需经常拧动的调节螺栓和螺母及非金属管道不应涂漆
412.5非机械加工的金属外表面应涂漆,或采用其他方法进行防护
涂漆应符合技术文件的规定,漆 膜应平整,色泽应一致、清洁,无明显突出颗粒和粘附物,不允许有明显的凹陷不平、砂纸道痕、流挂、起 泡,发白及失光
部件装配结合面的漆层,必须牢固、界限分明,边角线条清楚、整齐
不同颜色的油漆 分界线应清晰,可拆卸的装配接合面的接缝处,在涂漆后应切开,切开时不应扯破边缘
对于已经过表 面防锈处理(如发蓝,镀铬、镀镍,镀锌,喷塑等)的零,部件表面,不允许再涂漆
4.12.6外露的焊缝要平直、均匀
4.12.7各种系统的管、线路安装应整齐,美观,并用管夹固定,不应与其他零、部件发生磨擦或碰撞
管子弯曲处应圆滑,并应符合其最小弯曲半径的要求
4.12.8数控剪板机的主要零、部件外露加工表面不应有磕碰,划伤、锈蚀痕迹 精度 5.1 -般要求 5.1.1应符合GB/T14404一2011中第3章的规定
1. 2 S 允许不拆除刀片检查刀片垂直平面对上刀架行程的平行度
5.1.3对上刀架做倾斜往复运动的数控剪板机,不检查5.2.3 5.1.4对数控摆式剪板机,不检查5.2.3,5.2.4
GB/T28762一2012 5.2几何精度及检验方法 5.2.1刀片刃口间隙的均匀度 5.2.1.1 允差 刀片刃口间隙的均匀度允差应符合表5的规定
表5 单位为毫米 剪板机型式 可剪板宽 允差(在全长上 0.02 二2.5 >2.5~8 0.04 闸式剪板机 >816 0.06 >16 0.08 2.5 0.04 >2.5一8 0.05 摆式剪板机 8l6 0.08 >1625 0.14 >25 0.22 5.2.1.2检验方法 在两端间隙相等的情况下,将刀架运行至上下刀片刃口相叠位置,从距刀片端面50 mm处起用塞 尺测量刃口间隙(见图1),每隔150mm测量一次
其误差以最大、最小间隙差值计 图 5.2.2下刀片和挡料器的平行度 5.2.2.1允差 下刀片和挡料器的平行度允差应符合GB/T14404一2011中4.1.2.1精度等级的I级
GB/T28762一2012 5.2.2.2检验方法 下刀片和挡料器的平行度的检验方法应符合GB/T14404一2011中4.1.2.2的规定
5.2.3与下刀片贴合的垂直支承面对上刀架行程的平行度 5.2.3.1 允差 与下刀片贴合的垂直支承面对上刀架行程的平行度允差应符合表6的规定
表6 单位为毫米 可勇板厚 允差 s10 在100行程长度上为0.18 >10 在100行程长度上为0.22 注:上刀架向下运动时,与上刀片和下刀片贴合的两垂直支承面间的距离,只许增大
5.2.3.2检验方法 按照GB/T10923一2009中的5.4.2.2.1,将指示器依次紧固在上刀架A,B及c点上,使指示表测 头顶在与下刀片贴合的垂直支承面上,当上刀架向下运行时进行测量(见图2),误差以指示表的最大读 数差值计
检验时允许不拆掉刀片而检验下刀片贴合的垂直支承面对上刀架行程的平行度
百奋面 图2 5.2.4与上刀片贴合的垂直支承面对上刀架行程的平行度 5.2.4.1 允差 与上刀片贴合的垂直支承面对上刀架行程的平行度允差应符合表7的规定
单位为毫米 可剪板厚 允 s10 在100行程长度上0.18 >10 在100行程长度上0,22 注:上刀架向下运动时,与上刀片和下刀片贴合的两垂直支承面间的距离,只许增大
GB/T28762一2012 5.2.4.2检验方法 按照GB/T10923一2009中的5.4.2.2.1,将指示表依次放在工作台的A、B及C点上,使指示表测 头顶在与上刀片贴合的垂直支承面上,当上刀架向下运行时进行测量(见图3),误差以指示表的最大读 数差值计
检验时允许不拆掉刀片而检验上刀片贴合的垂直支承面对上刀架行程的平行度
图3 5.2.5挡料装置的定位精度 5.2.5.1挡料装置的定位精度允差 挡料装置的定位精度允差为士0.1 mm
5.2.5.2挡料装置的定位精度的检验方法 在数控挡料装置行程全长范围内,至少选定五个目标位置,各目标位置的间隔不应相同(见图4). 以工作速度沿正,负方向各五次趋近每个目标位置,用深度尺或大量程百分表或数字式位移测量装置记 录每次测量到的实际位置数值;计算每次实际位置与目标位置之差,并保留差值的正负号;以所有差值 中的最大正差值和最小负差值作为数控挡料装置的定位精度
目标位置(m=5) 4
GB/T28762一2012 5.2.6挡料装置重复定位精度 5.2.6.1挡料装置重复定位精度允差 挡料装置重复定位精度为0.04 mm
5.2.6.2挡料装置重复定位精度检验方法 在数控挡料装置行程全长范围内,至少选定五个目标位置,各目标位置的间隔不应相同(见图4). 以工作速度沿正,负方向各五次趋近每个目标位置,用深度尺或大量程百分表或数字式位移测量装置记 录每次测量到的实际位置数值;计算每个目标位置测量到的最大实际位置减去最小实际位置之差,以所 有差值中最大值作为数控挡料装置的重复定位精度
5.3工作精度及检验方法 5.3.1试件的直线度 5.3.1.1允差 试件的直线度允差应符合GB/Tl4404一201l中4.2.1.1精度等级的I级
5.3.1.2检验方法 试件的直线度的检验方法应符合GB/T14404一2011中4.2.1.2的规定 5.3.2试件的平行度 5.3.2.1允差 试件的平行度允差应符合GB/T14404一2011中4.2.2.1精度等级的I级
5.3.2.2检验方法 试件的平行度的检验方法应符合GB/T14404一2011中4.2.2.2的规定 试验方法 6.1 般要求 6.1.1数控剪板机试验时应注意防止气流、光线和强磁场的影响
6.1.2数控剪板机在试验前应安装调整好,一般应自然调平,其安装水平在纵、横向均不应超过0.20o 000
6.1.3试验应在装配完毕的整机上进行,除在试验时需拆卸、调整的零、部件外,不得拆卸、调整其他 零、部件
6.1.4试验时电、气、液的供应应正常
.1.5试验时应接通数控剪板机的所有执行机构
6. .1.6数控剪板机因结构限制或不具备标准所规定的测试工具时,可用与标准规定等效的其他方法和 o 测试工具进行检验
6.2参数检验 6.2.1采用剪切钢板的方法检验主参数,应符合4.2或产品设计文件的规定
10
GB/T28762一2012 6.2.2用通用量检具测量基本参数,应符合4.2或产品设计文件的规定
6.2.3成批生产的数控剪板机允许抽样检验,每批检验数量不低于3台
6.2.4数控剪板机的参数偏差不应超过表8的规定
表8 检验项目 单位 偏差 曲轴传动 士1% mm 十3% 刀架行程量 杠杆传动 mm -2% 行程量 士2% 其他传动 mm 十3% 辅助机构行程量 mm -1% +10% 刀架和辅助机构的调节量 mmm 调节量 十3% 刀架和辅助机构的角度调节量 十10% 行程次数 次/min 注1:在电源正常情况下进行检验
注2偏差折算结果(长度,次数)小于1,仍以1计算 6.2.5基本参数中未注公差尺寸的极限偏差,对于两个切削加工面间的尺寸按GB/T1804一2000 的中等m级计算,对于两个非切削加工面或其中只有一个切削加工面的尺寸,按GB/T1804一2000 的粗糙c级计算(涂漆腻子及油漆厚度不计);基本参数中未注形位公差值,对于两个切削加工面间的尺 寸按GB/T1184一1996中的K级计算,对于两个非切削加工面或其中只有一个切削加工面的尺寸,按 GB/T1184一1996中的1级计算(涂漆腻子及油漆厚度不计). 6.3刚度 按技术文件的规定对数控剪板机加载,测定其刚度,并应符合4.3的要求
6.4空运转试验 数控剪板机应进行空运转试验,带动刀架运动的连续空运转时间不少于4h,其中连续行程的运转 时间不少于2h,单次行程的运转时间为1.5h
在试验过程中,由于故障造成停机,需重新进行4h连 对于可调迷的数控剪板机应分档进行试验,最高速度运转的时间 续空运转试验,直至试验能连续完成
在空运转试验时间内,用温度计测量温升与最高温度,其温升与最高温度应符合4.7.5 不得少于0.5h
和4.9.6的规定
6.5 负荷试验 6.5.1满负荷试验 每台数控剪板机应进行满负荷试验,试验次数不应小于2次
满负荷试验时所加载荷应为公称力 11
GB/T28762一2012 的100%
满负荷试验时各机构及辅助装置应工作正常
6.5.2超负荷试验 型式试验时应进行超负荷试验,机械传动的剪板机一般应按其公称力的120%,液压传动的剪板机 -般应不大于公称力的l10%,进行超负荷试验,试验次数不少于3次
各机构、工作系统动作应协调、 可靠,带有超负荷保护装置、联锁装置的,应灵敏可靠
6.5.3负荷试验加载方法 采用下列加载方法之一,对数控剪板机加载进行负荷试验: 完成剪板机所应完成的剪板工序之一 安装执行机构挡块; -其他模拟加载方法
6.6基本性能检验 在空运转试验前或空运转试验过程中应按4.1和下列项目进行基本性能检验 a)检验各种安全装置的性能和功能; 刀架运行的各种操作规范试验,检验刀架运行动作的性能和功能; b 检验各种调整机构的性能和功能 d)检验附属装置的性能和功能; 检验各种指示器、计数器的性能和功能; 检验液压、气动、润滑、电气装置的性能和功能" f g检验各种联锁保护装置的性能和功能
6.7安全与防护检验 数控剪板机的安全与防护的检验按4.4的规定,用试验、,测量,计算、目测检查
6.8铸、锻、焊件检验 试验和目测检验铸、锻、焊件,应符合4.5的规定
6.9零件加工检验 按4.6的规定,用通用量具检验卷板机的零件加工质量
6. .10装配检验 按4.7的要求检验数控剪板机的装配质量,用目测和通用量具检验
6.11电气设备和数控系统检验 电气设备和数控系统检验按4.8的规定进行
6.12液压和气动系统检验 液压和气动系统的检验按4.9的要求进行
6.13润滑系统检验 按4.10的要求试验和检验润滑系统 12
GB/T28762一2012 6.14噪声检验 剪板机的噪声检验按4.11和GB/T23281.GB/T23282的规定进行 6.15外观检验 数控剪板机的外观按4.12的规定,用目测检验或用相应精度的量具检验 6.16精度检验 数控剪板机的精度检验按第5章的规定在满负荷试验后进行
6.17标志、标牌检验 试验和目测检验标志、标牌,应符合8.1的规定 6.18 包装检验 弯管机的包装检验应符合8.2的规定
检验规则 检验分类 数控剪板机检验分为型式检验和出厂检验
7.1.1型式检验 7.1.1.1有下列情况之一时,应进行型式检验 -新产品定型鉴定时; -设计、工艺、材料有较大改变后可能影响产品性能时; -国家质量监督机构提出型式检验的要求
7.1.1.2型式检验项目为本标准要求的全部检验项目 7.1.1.3型式检验时,从出厂检验合格的产品中随机抽样,每次检验不少于1台
7.1.2出厂检验 7.1.2.1每台数控剪板机均应由制造厂检验部门进行出厂检验,合格后方能出厂
若因特殊原因不能 在本单位进行检验时,可在用户处检验,检验合格后方可交付使用
7.1.2.2数控勇板机应按下列项目进行出厂检验或试验 参数 a b 装配; c)安全与防护; d 基本性能" e)空运转试验; f 噪声; 电气、数控系统(可靠性试验除外); g h液压、气动,润滑系统 iD 满负荷试验; 精度; 13
GB/T28762一2012 k外观; D 包装
标志,标牌,包装,运输和贮存 标志、标牌 8.1.1包装储运图示标志应符合GB/T191的规定
数控剪板机的操作危险区、喉口部分,电气装置、传动装置和侧面、后部应有明显的警告性标志, 警告性标志应符合GB2894和GB5226.1一2008中l6.2的规定
刀架、挡料装置等运动部件应按GB2893的规定涂以黑色与黄色相间的安全色条纹,根据需 8.1.3 要,亦可只涂成黄色
数控剪板机的产品标牌上的内容应包括生产厂名、厂址、产品型号、基本参数、出厂日期或出厂 编号
8.1.5数控剪板机应有指示润滑、操纵和安全等要求的各种标志、标牌,标牌的要求应符合GB/T13306 形象化符号应符合BT32的规定
的规定
8.1.6标志、标牌应端正牢固地固定在明显、合适的位置
包装 8.2 8.2.1应符合JB/T8356.1的规定
数控勇板机的零件,部件、附件和备件的外露加工面,应涂防锈剂 并敷上防锈油纸后再予以包装,非涂封表面应清理干净
8.2.2包装应附随机附件,随机工具,使用说明书(包括编程,操作手册,合格证明书装箱单
8.2.3电气系统、数控系统应有防锈、防潮措施
8.3运输 数控剪板机在运输过程中应避免振动、冲击,防止日晒、雨淋,电器部分防止受潮
8.4贮存 数控剪板机应贮存在无腐蚀性介质,防水、防潮的场所,数控系统应贮存在050C,相对湿度不超 过85%的室内
贮存期超过1年,应对数控系统进行重新检验 14
数控剪板机GB/T28762-2012介绍
数控剪板机是一种用于切割金属材料的机械设备,可实现高精度、高效率的金属加工。GB/T28762-2012是我国发布的对数控剪板机产品质量的标准规范,其中规定了数控剪板机的分类、技术要求、试验方法和检验规则等内容。
数控剪板机的分类
按切割方式分,数控剪板机主要有齿轮式、液压式、气动式、机械式等不同的结构类型;按机身结构分,数控剪板机主要有单臂式、双臂式和门型式等不同的结构形式。
数控剪板机的技术要求
- 1. 精度要求高:数控剪板机的切割精度应达到GB/T1184-1996的B级或以上标准;
- 2. 切割速度快:数控剪板机应具有高效率、高速度的切割功能,可满足不同材料和不同厚度的加工需求;
- 3. 操作方便:数控剪板机采用数字化控制技术,操作简单、精确,且可根据实际需要进行编程;
- 4. 安全性高:数控剪板机应具有完善的安全保护装置,包括紧急停机、缺相保护等安全功能。
数控剪板机的试验方法
GB/T28762-2012规定了数控剪板机的试验方法,包括外观质量检验、电气安全性能试验、切割精度试验、稳定性试验和噪声试验等。生产企业应按照标准要求对产品进行相关试验,并出具检测报告。
数控剪板机的质量控制
数控剪板机的质量控制主要包括原材料检测、零部件装配、出厂检验等环节。生产企业应建立健全的质量管理体系,确保产品质量符合GB/T28762-2012标准规范。
数控剪板机的应用领域
数控剪板机广泛应用于金属材料切割加工领域,例如钢铁、船舶、汽车、桥梁等行业中的加工制造。特别是对于大批量、高精度、高效率的金属加工,数控剪板机具有明显优势。