GB/T14560-2016
履带起重机
Crawlercranes
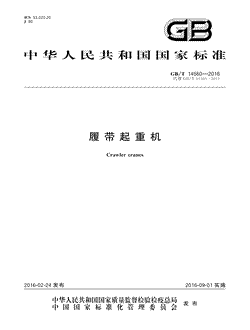
- 中国标准分类号(CCS)J80
- 国际标准分类号(ICS)53.020.20
- 实施日期2016-09-01
- 文件格式PDF
- 文本页数44页
- 文件大小816.21KB
以图片形式预览履带起重机
履带起重机
国家标准 GB/T14560一2016 代替GB7T4560-20T 履 Crawlercranes 2016-02-24发布 2016-09-01实施 国家质量监督检验检疫总局 发布 国家标准化管理委员会国家标准
GB/I14560一2016 目 次 前言 范围 规范性引用文件 术语和定义 技术要求 试验方法 检验规则 使用说明书与标志 26 26 包装、运输和贮存 附录A(资料性附录)起重机主要结构示意图 26 附录B(资料性附录)起重机臂架组合主要形式 36 附录c规范性附录)履带平均接地比压计算方法 31 附录D(规范性附录)结构试验方法 32 附录E(规范性附录)检验项目 38
GB/T14560一2016 前 言 本标准按照GB/T1.1一2009给出的规则起草
本标准代替GB/T14560一2011《履带起重机》,与GB/T145602011相比主要技术变化如下 增加了“主臂,副臂和最低稳定起升速度”的术语(见3.1,3.2和3.9) 修改了“变幅副臂”术语(见3.2.1,2011年版的3.l) “超起机构”术语修改为“超起装置”(见3.6,2011年版的3.6); 增加了“额定起重量图表”的要求(见4.2.1.3); 删除了“起重机主要部件的质量相对于公称值的误差不应大于3%”的要求和相应试验方法 见2011年版的4.2.1.6和5.3.2); 删除了“起重机在主臂工况下,起升机构、变幅机构和回转机构中任意两个机构应能同时工作” 的要求(见2011年版的4.2.1.7) 修改了“爬坡能力”的要求(见4.2.1.11,2011年版的4.2.1.12); 增加了“载荷试验”的要求(见4.2.1.13) 删除了“最短主臂工况下起吊最大起重量或最长主臂工况下起吊相应额定起重量时,发动机熄 火持续15min,载荷或臂架端部下降距离不应超过15mm或主臂变幅油缸活塞杆的回缩量不 超过2mm”的要求(见2011年版的4.2.1.14); 修改了“履带平均接地比压计算”的要求(见4.2.1.l4和附录C,2011年版的5.5.6); 修改了“司机耳旁噪声”的要求(见4.2.2,2011年版的4.2.2); 修改了“整机抗倾覆稳定性”的要求(见4,2.3,2011年版的4.2.3); “起重机可靠性试验时间和试验方法”(见4.2.4.2和5.16,2011年版的4.2.4.2和5.16) 增加了“焊缝探伤”要求(见4.2.5) 增加了“臂架头部侧向位移”的要求和试验方法(见4.2.7和附录D); 增加 “多卷扬同步单钩作业”的要求(见4.4.1.6) “气动系统”的要求(见201l年版的4.6) 删除了“起重机操纵手柄动作方向的表和布置图”见2011年版的表2和图1); 修改了“超载保护装置”的要求(见4.8.3,201l年版的4.9.4); -增加了“设置安全监控管理系统”的要求(见4.8.4.5); 修改了“最高起升速度和最低稳定起升速度”的试验方法(见5.3.3.1和5.3.3.2,2011年版的 5.3.4.1和5.3.4.4); 修改了“额定载荷试验、动载荷试验的试验工况和一次循环内容”(见表2和表3,2011年版的 表3和表4); 删除了“可靠性试验后的性能复试”要求(见2011年版的5.16.5); 删除了“工业性试验”(见2011年版的5.18); -删除了“行驶状态下的结构试验”(见2011年版的表C.1序号7); 删除了“参考文献”见2011年版的“参考文献”)
本标准由机械工业联合会提出 本标准由全国起重机械标准化技术委员会(SAC/TC227)归口
本标谁负责起草单位;中联重科股份有限公司
本标准参加起草单位:太原科技大学、浙江三一装备有限公司、徐工集团工程机械股份有限公司建 川
GB/T14560一2016 设机械分公司、辽宁抚挖重工机械股份有限公司
本标准主要起草人:杨武,罗凯,徐格宁,彭继文,孙影,张玉柱、王宪国
本标准所代替标准的历次版本发布情况为 GB/T145601993.GB/T145602011:; GB/T133301991
GB/I14560一2016 履带起重机 范围 本标谁规定了履带起重机的技术要求,试验方法、检验规则、使用说明书与标志,包装,运输和贮存
本标准适用于以内燃机为动力的液压式履带起重机(以下简称“起重机”)y 规范性引用文件 下列文件对于本文件的应用是必不可少的
凡是注日期的引用文件,仅注日期的版本适用于本文 件
凡是不注日期的引用文件,其最新版本(包括所有的修改单)适用于本文件 GB/T3323一2005金属熔化焊焊接接头射线照相 液压系统通用技术条件 GB/T3766 起重机设计规范 GB/T381l1 GB5226.2机械安全机械电气设备第32部分;起重机械技术条件 GB6067.1起重机械安全规程第1部分:总则 起重机术语第1部分;通用术语 GB/T6974.1 GB/T6974.2起重机 术语第2部分;流动式起重机 液压元件通用技术条件 GB/T7935 GB8918重要用途钢丝绳 工业产品使用说明书总则 GB/T9969 GB/T10051.!起重吊钩第1部分;力学性能,起重量、应力及材料 GB/T10051.2起重吊钩 第2部分锻造吊钩技术条件 GB12265.3机械安全 耀免人体各部位挤压的最小间距 GB12602起重机械超载保护装置 GB/T13306标牌 GB/T13384机电产品包装通用技术条件 GB15052 起重机安全标志和危险图形符号总则 GB/T19418钢的弧焊接头缺陷质量分级指南 GB20062流动式起重机作业噪声限值及测量方法 GB/T20118 -般用途钢丝绳 GB/T20303.2起重机司机室第2部分;流动式起重机 G;B20891非道路移动机械用柴油机排气污染物排放限值及测量方法(第三、四阶段》 GB/T21457 起重机和相关设备试验中参数的测量精度要求 GB/T21458流动式起重机额定起重量图表 GB/T22358土方机械防护与贮存 GB23821 机械安全防止上下肢触及危险区的安全距离 GB/T24809.2一2015起重机对机构的要求第2部分;流动式起重机 GB/T24817.2起重机械控制装置布置形式和特性第2部分;流动式起重机 GB/T24818.2起重机通道及安全防护设施第2部分:流动式起重机
GB/T14560一2016 GB/T26472 流动式起重机卷筒和滑轮尺寸 GB/T28264起重机械安全监控管理系统 工程机械用柴油机技术条件 JB/T4198.l JB/T5946工程机械涂装通用技术条件 JB/T8727液压软管总成 JB/T9737流动式起重机液压油固体颗粒污染等级、测量和选用 JB/T105592006起重机械无损检测钢焊缝超声检测 YB/T5359压实股钢丝绳 术语和定义 GB/T6974.1,GB/T6974.2界定的以及下列术语和定义适用于本文件
3.1 主臂main0om 与转台铵接,用于支撑载荷提升,可以变幅的构件
3.2 副臂jil 与主臂端部连接,以增加臂架长度和辅助起升的构件 3.2.1 变幅副臂ufingil 在作业过程中,可以改变与主臂夹角的副臂
3.2.2 固定副臂fixedjib 在作业过程中,不可以改变与主臂夹角的副臂
3.3 主臂桅杆mainboommast 与转台铃钦接,钢丝绳通过其头部的滑轮组能使主臂变幅的构件
3.4 副臂桅杆lyjibmast 与主臂端部或附近部件铵接,用于支撑副臂的构件
3.5 超起桅杆superlifmast -端与转台较接,另一端通过连接件与主臂和超起配重连接,能改变臂架工作幅度、提高起重性能 的构件
3.6' 超起装置superlirtdevice 通过增设超起桅杆,超起平衡重和辅助机构,改善构件受力状况及整机稳定性,从而提高起重性能 的装置 3.7 超起工况superli operatingmode 带有超起装置的起重机作业工况
GB/T14560一2016 3.8 标准工况standardoperatingmode 不带超起装置的起重机作业工况
3.g 最低稳定起升速度nminimunstablelifspeet 起升机构能持续稳定运行的最低速度
技术要求 工作条件 4.1 4.1.1工作环境温度为一20C~十 0C,工作场地海拔一般不应超过1000m 0 4.1.2工作风速要求如下: a)臂架长度不大于50m时,风速不应超过14.1m/s, 臂架长度大于50m时,风速不应超过9.8m/s
b 注,均为3太瞬时风迷 4.1.3在下列风速时,应将整个臂架放倒在地面上 主臂工况:主臂长度不小于50m,风速大于或等于21m/s时; a b)副臂工况:主臂加副臂组合长度不小于50m,风速大于或等于15m/s时
4.1.4工作地面应坚实,平整,地面倾斜度不应大于1%
若制造厂允许回转平面的倾斜度更大,应提 供相应的额定起重量图表
工作过程中支撑地面不应下陷
必要时根据不同地面允许的静载荷采取相应措施,以满足工作地 面的承载要求
地面或支撑面的承载能力应大于起重机当前工况下最大接地比压 注:超过上述范围时,应与用户协商解决
4.2整机 -般要求 4.2.1 4.2.1.1300t以上起重机宜带超起机构,带超起和不带超起的起重机结构形式参见附录A,起重机常 见臂架组合形式参见附录B. 4.2.1.2起重机的设计计算应符合GBy/T3811的有关规定
起重机的额定起重量图表应符合GB/T218的规定 4.2.1.3 起重机应具有在规定条件下的带载行走性能
4.2.1.4 4.2.1.5起升、变幅,回转和行走等机构的运行应平稳,其运行迷度与设计值的相对误差不应大于5%
4.2.1.6起重机的主要外形尺寸误差不应大于1%
4.2.1.7起升机构卷扬钢丝绳的单绳微动速度不应大于5m/min.
4.2.1.8在没有人为干预的情况下,空载行走状态的起重机以最低稳定速度前进或后退行走20m,其 跑偏量不应大于士250 mm
起重机作业过程中液压油箱内的相对温升不应超过40C,且最高油温不应超过80c
4.2.1.9 4.2.1.10主臂,副臂、桅杆等有后倾可能时,应设置防后倾装置
4.2.1.11空载,带基本臂的起重机在平整坚实、干燥的地面上直线行驶时,设计爬坡能力应满足 -最大起重量为450t及以下的起重机不带超起装置时不应小于15%,带超起装置时不应小 于5%; -最大起重量大于450t的起重机不带超起装置时不应小于10%,带超起装置时不应小于5%
GB/T14560一2016 4.2.1.12发动机的技术要求应符合JB/T4198.1的规定,排气污染物排放限值应符合GB20891的 规定
4.2.1.13起重机在空载和额定载荷各工况下,应动作平稳,无异响或抖动
工作速度达到技术文件的 要求
制动可靠且在任何提升操作条件下载荷均不应出现明显的反向动作
在动载和静载试验过程中或试验结束后,起重机的结构件不应产生裂纹、永久变形,油漆剥落
零 部件不应产生对起重机的性能与安全有影响的损坏,连接处无出现松动或损坏
4.2.1.14起重机的履带平均接地比压计算见附录C
4.2.2噪声 起重机在正常工作条件下运行时,司机耳旁噪声和机外辐射噪声声功率级限值应符合GB20062 的规定
4.2.3整机抗倾覆稳定性 4.2.3.1起重机在进行静态稳定性试验过程中,应不倾覆
4.2.3.2起重机在进行抗后倾覆稳定性试验时,分别测量或计算臂架一侧倾覆线上的总载荷,不应小于 起重机总质量重力的15%
4.2.4可靠性 4.2.4.1可靠性试验时,起重机的作业率不应低于85%
4.2.4.2可靠性试验时,最大起重量小于800t的起重机可靠性试验总时间不应超过350h;最大起重 量等于或大于800t的起重机,可靠性试验总时间不作规定
4.2.5焊接 4.2.5.1结构件的焊缝质量应满足机械性能设计计算的要求,焊缝缺陷质量分级应符合GB/T19418 中的“B”级
4.2.5.2主要受力构件的对接焊缝,应进行探伤检测
射线探伤时,不应低于GB/T3323一2005中的 质量等级级;超声波探伤时,不应低于JB/T10559一2006中质量等级1级
4.2.6涂装 起重机涂装技术要求应符合JB/T5946的规定
4.2.7臂架头部侧向位移 臂架头部最大侧向位移附录D的测试工况),应满足下列要求: a)臂架组合的头部侧向水平位移不应大于整个臂架组合长度的2%; b)单个臂架的水平侧向位移不应大于单个臂架长度的2%
每个臂架的水平侧向位移不包括由 连接部件变形倾斜或扭转)所引起的水平位移
如果主臂上只安装了一节副臂,应满足式(1)(见图1. Z<0.02L十Z十tan/ nZ'Lcos3)十tan(Lsin3) 式中: Z -副臂头部侧向水平位移(需测量),单位为毫米(n mm; L -副臂长度,单位为毫米(mm); 1 -主臂头部侧向水平位移(需测量),单位为毫米(nm mm
GB/I14560一2016 臂架倾斜角,单位为度() -副臂与主臂夹角,单位为度(") 臂架扭转角度,单位为度("). tanZ'计算见式(2. anz'=(Z,一Z/(L1 式中: Z在主臂头部下方的距主臂头L,处的主臂侧向水平位移(需测量),单位为毫米(n mm; 主臂沿Y轴任意投影长度,单位为毫米(n mm tan/计算见式(3)
tan/=(Z一Z/L? 式中 Z -副臂撑杆顶部侧向水平位移需测量),单位为毫米(mm) 副臂撑杆沿Y轴投影长度,单位为毫米(mm)
额定起重量 图1侧向位移计算示意图 4.3结构 4.3.1一般要求 起重机结构件材料和结构型式应满足使用过程中的强度、刚性、稳定性、防腐和有关安全性方面的 要求
选用新材料应进行工艺验证
4.3.2臂架 4.3.2.1起重机臂架材料的选择应符合GB/T3811的规定
4.3.2.2当臂架截面高度大于2m时,臂架的上表面应设置臂架的安装、拆卸、维修和保养的通道及安 全防护设施,通道及安全防护设施应符合GB/T24818.2的规定
GB/T14560一2016 4.3.3下车 履带的张紧程度应可调
对于具有伸缩平移功能的履带架,其伸缩运动应平稳
4.3.4司机室 4.3.4.1司机室应符合GB/T20303.2的规定 4.3.4.2司机室工作面上的照度不应低于50lx
4.4机构及零部件 4.4.1起升机构 4.4.1.1起重作业时,载荷起升或下降动作应平稳,载荷在任何位置均能可靠停稳
4.4.1.2载荷在空中停稳后,再次启动提升载荷时,在任何提升操作条件下,载荷均不应出现明显的反 向动作 4.4.1.3严禁起重机带载自由下降,应通过动力来控制载荷的下降速度
若采用动力下降,可参考 GB/T24809.2一2015中4.2.6的要求
4.4.1.4起升机构宜配置卷筒旋转指示器或监视装置,将其设置在操作人员易于观察的位置
起升机构应设置常闭式制动器,制动器的制动力矩不应小于1.5倍的最大工作扭矩
4.4.1.5 在紧急状态下制动不应导致结构、钢丝绳、卷筒及机构的损害 4.4.1.6对于采用多卷扬同步单钩作业的起重机,应具有同步功能
4.4.2变幅机构 臂架变幅采用卷扬机构时,卷扬机构应设置常闭式制动器,制动器的制动力矩不应小于1.5倍的最 大工作扭矩
4.4.3卷筒 4.4.3.1多层缠绕的卷筒,应有防止钢丝绳从卷简端部滑落的凸缘,凸缘超出最外层钢丝绳的高度不应 小于钢丝绳直径的1.5倍
4.4.3.2起升卷筒的容绳量应满足 当采用制造厂推荐的穿绳法和钢丝绳尺寸时,能完成制造厂规定的任何工况下的起重作业; a b 吊具下降到制造厂规定的最低极限位置时,钢丝绳在卷筒上的剩余安全圈(不包括固定绳端 所占的圈数)至少应保持2圈
4.4.3.3变幅卷筒的容绳量应满足 当采用制造厂推荐的穿绳法和钢丝绳尺寸时,臂架在0"到最大仰角的所有位置上都应能使臂 a) 架准确变幅 臂架下降到制造厂规定的最低极限位置时,钢丝绳在卷筒上的剩余安全圈(不包括固定绳端 b 所占的圈数)至少应保持2圈
卷简绳槽表面和绳槽棱边应光洁平滑,不应损伤钢丝绳的表面
4.4.3.4 4.4.3.5卷筒的卷绕直径与钢丝绳公称直径的比值应符合GB:/T26472的规定
4.4.3.6卷简宜设置钢丝绳不跳出卷筒,甚至在钢丝绳松弛状态时也不能跳出卷简的防护装置
4.4.4滑轮 4.4.4.1滑轮轮槽应是光滑的,且表面不应有可能造成钢丝绳损坏的缺陷
GB/T14560一2016 4.4.4.2滑轮上应配备防止钢丝绳脱槽的保护装置,该装置表面与滑轮最外缘间的间隙不应超出钢丝 绳直径的1/3或10mm中较小值
4.4.4.3所有滑轮的支承处均应设有润滑装置
4.4.4.4起重作业时人手可触及的滑轮组,应设置滑轮罩壳
对可能滑落到地面的滑轮组,其滑轮罩壳 应有足够的强度和刚度
4.4.4.5起升滑轮和变幅滑轮的卷绕直径与钢丝绳公称直径的比值应符合GB/T26472的规定
4.4.5钢丝绳 4.4.5.1钢丝绳的选择应符合GB/T3811的规定
起升钢丝绳宜选用阻旋转的钢丝绳
4.4.5.2钢丝绳应符合GB8918,GB/T20118和YB/T5359的规定
4.4.5.3钢丝绳端部的固定和连接应符合GB/T3811的规定
4.4.6吊钩和吊钩滑轮组 4.4.6.1吊钩的选用应符合GB/T10051.1的规定
吊钩的制造、质量及检验应符合GB/T10051.2的 规定
4.4.6.2吊钩应设置防脱装置
吊钩滑轮组应设置挡绳装置
回转机构 4.4.7 4.4.7.1回转机构应能随着起重机正常工作的要求而启动或停止,启动和停止应平稳
4.4.7.2回转机构宜设置回转自由滑转系统,该系统应具有减少或消除由起升载荷重心与钢丝绳不在 同一条铅垂线上而引起的对臂架产生的侧向力的功能
4.4.7.3回转机构应设置制动器,制动器的制动力矩不应小于1.25倍的最大工作扭矩,最大工作扭矩 包括风载荷和允许的倾斜载荷
制动器在所有允许的回转位置应都能起作用
4.4.8行走机构 4.4.8.1行走机构应具有向前和向后行走及单侧转向和原地转向的功能
4.4.8.2起重机以最高运行速度行走时,应保证启动和制动时的安全
4.4.9超起装置 4.4.9.1超起系统应设置检测超起配重(不含配重小车)离开地面状况的装置,采用超起配重小车时应 能显示超起配重利用率
4.4.9.2超起配重采用液压油缸提升时,提升油缸应具有单独调整功能,保证超起配重底板的水 平度
在操作位置,应有让操作人员方便了解在特定工况下所需匹配的超起配重重量的提示装置或 4.4.9.3 措施
4.5液压系统 4.5.1一般要求 4.5.1.1液压系统的设计,制造,安装和配管等的技术要求应符合GB/T3766的规定
4.5.1.2液压元件应能保证在最大工作压力(包括超载试验时的压力)和最大运行速度时,正常工作而 不失效
液压元件的技术要求应符合GB/T7935的规定
GB/T14560一2016 4.5.1.3平衡阀与被控元件之间应采用刚性连接,且间距尽量短
每个液压回路都应有压力限制装置以防止超压,限制压力值不应超过最大工作压力的110%
4.5.1.4每个液压回路应配有一个显示压力的装置或一个压力检测接口
4.5.1.5液压钢管末端有接头时,其安全系数不应小于2.5
液压系统中,液压油阁体颗粒污染等级应符合JBT9737的规定 4.5.1.6 4.5.1.7起重机在正常工作时包括性能试验过程),液压系统不应有渗漏油现象
4.5.2液压软管 4.5.2.1液压软管的技术要求应符合JB/T8727的规定,其安全系数不应小于4
4.5.2.2液压软管最小弯曲半径应符合软管制造厂的规定
4.5.2.3 当液压软管的工作压力大于5MPa或温度高干50c,且与操作人员距离小于】m,又设有其 他遮挡时,应采取保护措施以免软管失效对操作人员造成伤害 4.5.3液压油缸 4.5.3.1承载液压油缸(如支腿油缸、枪杆顶升油缸)应装有与之采用刚性连接的安全装置(如液压锁、 平衡阀等),以防止因液压管路意外破裂而导致安全事故
4.5.3.2两并联同步油缸应设置防过载液压阀,当一个油缸失效时,另一个油缸可避免过载, 4.5.3.3液压油缸的端口和阀(如保护阀)之间的焊接或装配连接件,爆破压力与工作压力的安全系数 不应小于2.5
4.5.4液压油箱 液压油箱应有满足液压系统正常工作的有效容积
液压油箱的结构至少应满足如下要求 -良好的密封性能.憎封效果应符合45.1了的要求 -应设置降低液压系统颗粒污染的过滤器和检测最高,最低油位的装置; -应设置排放口和清洗孔以便于液压油箱内部清洗
4.6电气系统 4.6.1电气系统应符合GB5226.2的规定
4.6.2采用无线遥控操作方式的起重机,无线遥控的电气系统应具有监控和故障自诊断功能,在任何 非正常工作状态下应能实现自动关闭、停止工作,并应具有抗同频干扰信号的能力
4.6.3起重机要求多点控制时,应有互锁功能,每一控制点均应设置紧急停止开关 4.7操纵系统与控制系统 4.7.1操纵手柄、操纵踏板,按钮,指示器及信号等装置应安装在便于操纵或观测的位置,并在其附近 配置清晰的符号及图形标识,以说明它们的用途和操纵方向
操纵手柄的动作方向与被操纵机构的运 动方向应符合GB/T24817.2的规定 4.7.2操纵手柄和操纵踏板的操纵力及行程应符合表1的规定
GB/T14560一2016 表 操纵手柄和操纵踏板操纵力及行程 操纵力 操纵行程 项目 mm 安装在控制台上 <50 操纵手柄 安装在地板上 <16o <260 操纵踏板 225 260 注1:由于载荷变化而影响操纵力的大小时,应在额定起重量下测量
注2:行程是指从空挡中间位置)到前、后或左、右位置移动的直线距离
4.7.3操纵手柄或按钮动作应灵活,不互相干扰
各操纵手柄和操纵踏板在中位时,不得因振动而 离位
4.7.4 起重机应设置紧急停止装置
当遇到紧急情况时,紧急停止装置的按钮应保持在接通位置.直 到紧急情况解除
4.7.5起重机处于非工作状态时,控制系统应能可靠地防止起重机意外启动
4.7.6为防止误操作,控制系统中应设有附加的保护装置(如钥匙开关). 4.7.7起重机开始作业时应有音响报警,警示起重机附近的人员
4.7.8支腿操纵机构应设置在使操作人员能清楚地看见活动支腿运动方向,否则,应有音响报警 4.8安全要求 4.8.1一般要求 起重机应按照GB6067.1的要求设置相应的安全防护装置
4.8.2限制运动行程与工作位置的安全装置 4.8.2.1起升高度限位器 起重机应配置起升高度限位器
当取物装置上升到设计规定的上极限位置时,应能立即切断起升 动力源
在此极限位置的上方,还应留有足够的空余高度,以适应上升制动行程的要求
下降深度限位器 4.8.2.2 起重机应配置下降深度限位器
当取物装置下降到设计规定的下极限位置时,应能立即切断下降 动力源,确保在卷筒上缠绕的钢丝绳满足4.4.3.2的要求
4.8.2.3变幅限位器 起重机应配置变幅限位器
臂架在极限位置时,控制系统应自动停止变幅向危险方向动作,并确保 在卷筒上缠绕的钢丝绳满足4.4.3.3的要求
4.8.2.4防后倾装置 起重机的防后倾装置可吸收钢丝绳或吊具因故障突然释放载荷造成的冲击,防止臂架或桅杆向后 运动
4.8.2.5角度限制器 起重机应设置角度限位器
角度限位器可有效限制主臂,副臂的最大,最小工作角度
GB/T14560一2016 4.8.2.6水平显示器 水平显示器应安装在起重机的司机室中或操作者附近的视线之内
水平显示器的显示误差不应大 于士0.1
4.8.3防超载的安全装置 起重机应配置力矩限制器,力矩限制器的技术要求应符合GB12602的规定并至少具备以下功能 a)操作中能持续显示额定起重量或额定起重力矩,实际起重量或实际起重力矩、载荷百分比,并 应通过指示灯显示载荷状态: 绿灯亮:表示实际起重量或实际起重力矩小于实际幅度所对应的相应额定起重量或额定 起重力矩的90%; 黄灯亮:表示实际起重量或实际起重力矩在实际幅度所对应的相应额定起重量或额定起 重力矩的90%~100%之间,同时蜂鸣器断续报警; 红灯亮;表示实际起重量或实际起重力矩大于实际幅度所对应的相应额定起重量或额定 起重力矩的100%,同时蜂鸣器连续报警; 报警消音功能; b 显示工作幅度、臂架仰角 d)当实际起重量在100%~110%额定起重量之间时,自动停止起重机向危险方向的动作; e)允许强制作业功能.打开强制作业开关,起重机应允许在额定起重量的100%110%之间操 作,工作速度应满足 -电控系统;速度小于最大允许工作速度的15% -液控系统;速度小于最大允许工作速度的25%; fD 在达到起升高度、下降深度、超载将角度限位等极限状态时,应显示相应的报警指示
即使打开 强制作业开关,上述报警指示不应自动解除
4.8.4安全防护装置 4.8.4.1故障显示装置 起重机应设置故障显示装置,故障显示方式应使用文字,图形或语音等
故障显示装置至少应具有 以下功能 故障显示 a -控制系统通讯故障; 超载保护装置系统故障
b)报警功能 机油压力过低; 水温过高; 液压滤清器堵塞
4.8.4.2三色指示灯报警装置 应在司机室外明显位置设置三色(绿色,黄色、红色)指示灯报警装置
三色指示灯指示起重机实际 载荷状况应符合4.8.3a)的规定
4.8.4.3警示灯 起重机应设置臂架顶端警示灯 10o
GB/T14560一2016 4.8.4.4风速仪 起重机臂长超过50m时应设置风速仪
起重机风速仪的安装应符合GB6067.1的规定
4.8.4.5安全监控管理系统 起重机应设置符合GB/T28286l规定的发全监控管理系统 4.8.4.6防护装置 4.8.4.6.1控制装置位置的设计应确保安全距离符合GB12265.3和GB23821的规定
4.8.4.6.2在正常工作或维修时,为防止异物进人或防止其运行对人员可能造成危险,应设置保护装 置
起重机上外露的、有可能伤人的零部件,如开式齿轮、链轮、链条等,均应装设防护置/栏 4.8.4.6.3防护罩/栏应牢固可靠
防护罩/栏应能承受一个90kg重的力而不会发生永久变形 4.8.4.6.4如果安全通道只可能带个人保护装置(如安全带)和/或移动通道系统(如移动平台或移动梯 子),应在说明书中提供选择、安装及安全使用的说明
4.8.4.7安全警示标志 应在起重机的可能发生危险的部位或工作区域设置明显可见的安全警示标志,安全警示标志应符 合GB15052的规定
试验方法 5.1试验条件 5.1.1根据试验工况,起重机应装上设计规定的全部工作装置
5.1.2燃油箱内应有1/32/3之间的油量,液压油箱的油面应在油面指示器规定的刻度范围内
5.1.3地面应坚实、平整,倾斜度不大于0.5%
5.1.4作业性能试验时,风速不应大于8.3m/s;结构试验时,风速不应大于4m/s 5.1.5试验时的环境温度在一20C十40C之间
5.1.6试验载荷应标定准确,相对于标定值的误差应符合GB/T21457的规定
5.1.7在不影响试验效果的情况下,试验项目可按试验内容和载荷情况相互穿插或组合进行
5.2 试验准备 5.2.1资料 试验时,应准备试验大纲和试验记录等 5.2.2测量精度 试验中参数的测量精度应符合GB/T21457的规定
5.3主要参数测定 5.3.1主要尺寸 测定项目为(见图2) a)主臂长度和副臂长度; b 最大起升高度; 11
GB/T14560一2016 卸去臂架后的起重机外廓尺寸:总长(L)、总宽(B.)和总高(H); c d 履带的相关尺寸;履带长度(L)、履带接地长度(L),履带宽度(B和两履带总宽(伸/缩 B,/B 图2起重机外形尺寸 5.3.2操纵力及操纵行程 操纵手柄和操纵踏板的操纵力;测量点为操纵手柄和操纵踏板中央点
操纵手柄和操纵踏板的操纵行程:测量操纵手柄和操纵踏板中央点的直线移动距离
5.3.3工作参数 5.3.3.1最高起升速度 基本臂为70"仰角、空载工况时,测量吊钩通过2m(主钩)行程所需要的时间,计算起升速度
试验 重复3次,取其平均值作为最高起升速度 5.3.3.2最低稳定起升速度 最长主臂、额定载荷工况时,测量吊钩通过1m(副钩)行程所需要的时间,计算起升速度
试验重 复3次,取其平均值作为最低稳定起升速度
5.3.3.3最高回转速度 基本臂为70"仰角,空载工况时,以最高速度左、右回转,测量回转360"所需要的时间,试验重复 3次,计算回转速度,取其平均值作为最高回转速度
5.3.3.4变幅时间 基本臂、空载工况时,测量臂架在0°至最大仰角范围内以最高速度全程起臂、落臂所需要的时间, 12
GB/T14560一2016 试验重复3次,取其平均值作为变幅时间
5.4外观检查 外观检查一般为目测检查,这种检查应不拆卸任何零部件或打开遮蔽物,可包括某些必要的手动操 作
同时还应检查全部必备的证书是否提供并经过审核
目测检查不少于如下项目 a)焊缝质量 表面涂装质量; b) 主臂上的维修通道 c 司机室地面防滑、门窗定位,安全玻璃使用、第二出口 d 安全防护装置; 防止钢丝绳跳出卷筒的装置 滑轮的防止钢丝绳脱槽装置 滑轮支承处的涧滑装置; 起重作业时人手可触及的滑轮组的滑轮罩壳; 吊钩的标记和防脱装置
吊钩滑轮组的挡绳装置; 液压管路、线束的敷设及保护; 操纵件的操作、标牌和标志; 安全防护装置; m 液压油油位; n 起重机标牌和额定起重量图表 0 5.5行走性能试验 5.5.1最高行走速度 试验工况为 -空载; 基本臂为45°仰角; 起升和回转制动器均处于制动工况
分别测量起重机以最高速度前进和后退各20m所需的时间,计算起重机的最高行走速度 试验重复3次,分别取前进或后退3次试验的平均值作为起重机的最高行走速度
5.5.2跑偏量 试验工况为 空载; 基本臂为45"仰角 起升和回转制动器均处于制动工况
起重机在没有人工干预的情况下,以最低稳定速度前进和后退行走各20m的跑偏量
试验重复3次,取最大值作为起重机的跑偏量
5.5.3行走制动功能 试验工况为 空载; 13
GB/T14560一2016 基本臂为最大仰角 起升和回转制动器均处于制动工况
起重机在低速挡行走状态,以允许最高速度行走,能够可靠制动,试验重复3次 5.5.4履带架伸缩功能 履带架可以伸缩的起重机,履带架距离由最小调整到最大,再由最大调整到最小,观察履带架伸缩 平稳性,试验重复3次
5.6空载试验 5.6.1试验目的 检查起重机各机构能否在规定的工作范围内正常动作,各种指示和限位装置是否能工作正常
5.6.2试验方法 分别进行吊钩起升及下降,过放,回转,变幅和臂架防后倾的功能试验,试验方法如下 吊钩升降 基本臂,主臂十固定副臂或主臂十变幅副臂的臂架组合时,起升吊钩,当吊钩达到设计 规定的极限位置时高度限位器报警,并自动停止吊钩起升动作
操作强制开关后可继续向相 同方向动作
试验重复3次
起升卷筒上钢丝绳过放 吊钩以低速下降,当起升卷筒上缠绕的钢丝绳还剩2圈时(除固定绳尾的圈数外)下降深度限 位器报警,并自动停止向危险方向运动
操作强制开关后可继续向相同方向动作
试验重复3次
回转 基本臂分别以高速和低速进行全程范围内左右各回转360",左有右回转过程各制动1次
试验重复3次
变幅 主臂十变幅副臂或主臂十固定副臂时,分别对主臂,副臂和桅杆进行全程范围内的变幅 变幅到中间位置时制动1次
幅度达到设计规定的上下限制位置时,变幅限位器报警,并自动 停止变幅
操作强制开关后可继续向相同方向动作
试验重复3次
防后倾 对主臂十变幅副臂和超起装置的臂架组合形式,分别操作主臂,变幅副臂或桅杆的防后倾 装置
臂架或枪杆的后倾角度到限制位置时,系统自动报警,并自动停止向危险方向运动,可 向安全方向动作
试验重复3次
额定载荷试验 5.7.1 试验目的 验证起重机各机构在起吊相应工况100%额定起重量的试验载荷时的性能
验证超载保护装置、三色指示灯和安全监控管理系统的报警功能
5.7.2试验方法 5.7.2.1起吊额定载荷 额定载荷试验的臂架组合,试验工况和试验循环内容见表2 每种工况按表2规定的一次循环内容重复试验3次 14
GB/T14560一2016 表2额定载荷试验 类别 臂架组合 序号 试验工况 -次循环内容 最大起重量,相应工作幅度 载荷起升到最大高度后,再下降到地面,载 基本臂 最大工作制度、相应额定起重量荷在下降过程中制动1次 载荷起升到臂架可以回转的离地高度,在作 业区范围内左右回转360",在左右回转过程中 最小工作幅度,相应额定起重量各制动1次,2 载荷起升到最大高度后,再下降到地面,载 中长主臂 荷在升降过程中各制动1次 载荷起升离地,起臂至最小工作幅度,再落 臂至最大工作幅度,再将载荷下降到地面,在 最大工作幅度、相应额定起重量 起、落臂过程中各制动1次 载荷起升到臂架可以回转的离地高度,在作 业区范围内左有回转360",在左有回转过程中 最小工作幅度、相应额定起 各制动1次2次
重量 载荷起升到最大高度后,再下降到地面,载 最长主臂 荷在升降过程中各制动1次 载荷起升离地,起臂至最小工作幅度,再落 最大工作幅度、相应额定起重量 臂 至最大工作幅度,再将载荷下降到地面,在 起,落臂过程中各制动1次 载荷起升离地,起臂至最小工作幅度,再落 标 最大工作幅度,相应额定起重量臂至最大工作幅度,再将载荷下降到地面,在 起、落臂过程中各制动1次 载荷起升到臂架可以回转的离地高度,在作 基本臂十最短副臂" 况 业区范围内左右回转360'",在左右回转过程中 最小工作幅度、相应额定起重量 各制动1次、2次
载荷起升至最大高度后,再下降到地面,载荷 在下降过程中制动1次 载荷起升离地,起臂至最小工作幅度,再落 最大工作幅度、相应额定起重量 臂至最大工作幅度,再将载荷下降到地面,在 起,落臂过程中各制动1次 载荷起升到臂架可以回转的离地高度,在作 中长主臂十中长副臂 业区范围内左右回转360",在左右回转过程中 10 最小工作幅度、相应额定起重量各制动1次.2次 载荷起升至最大高度后,再下降到地面,载 荷在下降过程中制动1次 载荷起升离地,起臂至最小工作幅度,再落 最大工作幅度,相应额定起重量 1 臂至最大工作幅度,再将载荷下降到地面,在 起、落臂过程中各制动1次 载荷起升到臂架可以回转的离地高度,在作 最长主臂十最短副臂" 业区范围内左右回转360",在左右回转过程中 最小工作幅度、,相应额定起重量 12 各制动1次、2次
载荷起升至最大高度后,再下降到地面,载 荷在下降过程中制动1次 15
GB/T14560一2016 表2(续 类别 臂架组合 序号 试验工况 -次循环内容 载荷起升离地,起臂至最小工作幅度,再落 最大工作幅度、相应额定起重量臂至最大工作幅度,再将载荷下降到地面,在 13 起、落臂过程中各制动1次 准 载荷起升到臂架可以回转的离地高度,在作 最长主臂十最长副臂 业区范围内左右回转 ,在左右回转过程中 360 14 最小工作幅度、相应额定起重量 各制动1次,2次
载荷起升至最大高度后,再下降到地面,载 荷在下降过程中制动1次 15 最大起重量、相应工作幅度 载荷起升到最大高度后,再下降到地面,载 最大工作幅度和相应的超起配 基本臂 重、超起配重回转半径、相应额荷在下降过程中制动1次 16 定起重量 载荷起升到臂架可以回转的离地高度,在作 最小工作幅度和相应的超起配业区范围内左右回转 360
,在左右回转过程中 重,超起配重回转半径,相应额各制动1次,2次
17 载荷起升到最大高度后,再下降到地而,载 定起重量 中长主臂 荷在升降过程中各制动1次 最大工作幅度和相应的超起配 载荷起升离地,起臂至最小工作幅度,再落 18 重、超起配重回转半径、相应额臂至最大工作幅度,再将载荷下降到地面,在 定起重量 起落臂过程中各制动 1次 载简起升到臂架可以回转的离地高度,在作 最小工作幅度和相应的超起配业区范围内左有回转360",在左右回转过程中 19 重、超起配重回转半径、相应额各制动1次、2次
定起重量 载荷起升到最大高度后,再下降到地面,载 最长主臂 荷在升降过程中各制动1次 最大工作幅度和相应的超起配 载荷起开离地,起臂至最小工作幅度,再落 重,超起配重回转半径,相应额臂至最大工作幅度,再将载荷下降到地面
心 20 工 定起重量 起,落臂过程中各制动1次 况 载简起升离地,起臂至最小工作幅度,再落 最大工作幅度和相应的超起配 重,超起配重回转半径,相应额臂至最大工作幅度,再将载荷下降到地面,在 21 定起重量 起、落臂过程中各制动1次 载荷起升到臂架可以回转的离地高度,在作 基本臂最短副臂" 相应的超起配重、超起配重回转业区范围内左右回转360",在左右回转过程中 22 半径、最小工作帮度、相应额定各制动1次.2次
起重量 载荷起升至最大高度后,再下降到地面,载 荷在下降过程中制动1次 相应的超起配重、超起配重回转 载荷起升离地,起臂至最小工作幅度,再落 23 半径、最大工作幅度、相应额定臂至最大工作幅度,再将载荷下降到地面,在 起重量 起,落臂过程中各制动1次 载荷起升到臂架可以回转的离地高度,在作 中长主臂十中长副臂”" 相应的超起配重、超起配重回转业区范围内左右回转360",在左右回转过程中 半径,最小工作幅度、相应额定各制动1次.2次
24 载荷起升至最大高度后.再下降到地面载 起重量 荷在下降过程中制动1次 16
GB/T14560一2016 表2(续 类别 臂架组合 序号 试验工况 -次循环内容 相应的超起配重、超起配重回转 载荷起升离地,起臂至最小工作幅度,再落 半径,最大工作幅度、相应额定 臂 至最大工作幅度,再将载荷下降到地面,在 25 起重量 起、落臂过程中各制动1次 载荷起升到臂架可以回转的离地高度,在作 最长主臂十最短副臂 相应的超起配重、超起配重回转业区范围内左右回转 ,在左右回转过程中 360° 26 半径,最小工作幅度、相应额定各制动1次、2次
起重量 载荷起升至最大高度后,再下降到地面,载 荷在下降过程中制动1次 相应的超起配重、超起配重回转 载荷起升离地,起臂至最小工作幅度,再落 27 半径、最大工作幅度、相应额定臂至最大工作幅度,再将载荷下降到地面,在 起重量 起,落臂过程中各制动1次 载荷起升到臂架可以回转的离地高度,在作 最长主臂最长副臂 相应的超起配重将超起配重回转业区范围内左右回转360",在左右回转过程中 28 半径,最小工作幅度、相应额定各制动1次.2次
起重量 载荷起升至最大高度后,再下降到地面,载 荷在下降过程中制动1次 副臂分为固定副臂和变幅副臂 5.7.2.2带载行走 5.7.2.2.1标准工况试验 中长主臂、最小工作幅度,臂架位于行走方向的正前方,起吊带载行走时相应工况100%额定起重量 的试验载荷,载荷起升到离地高度500mm左右,起重机以最低稳定速度直线前进和后退行走各201 m
前进或后退行走过程中各制动1次
试验重复3次
5.7.2.2.2超起工况试验 相应的超起配重、超起配重回转半径、中长主臂、最小工作幅度,臂架位于行走方向的正前方,起吊 带载行走时相应工况100%额定起重量的试验载荷,载荷起升到离地高度500mm左右,起重机以最低 稳定速度直线前进和后退行走备20m
前进或后退行走过程中各制动1次
试验重复3次
5.7.2.3安全装置验证 在试验过程中,验证超载保护装置、三色指示灯和安全监控管理系统的报警功能 5.8动载荷试验 5.8.1试验目的 验证起重机的各机构在起吊相应工况110%额定起重量时各机构和制动器的功能
验证超载保护装置、三色指示灯和安全监控管理系统的报警功能
在试验过程中或试验结束后,检查起重机的零部件是否产生对起重机的性能与安全有影响的损坏, 连接处是否出现松动或损坏
17
GB/T14560一2016 5.8.2试验方法 5.8.2.1起吊110%额定载荷 动载荷试验的臂架组合、试验工况、试验循环内容见表3, 每种工况按表3规定的一次循环内容重复试验3次 表3动载荷试验 类别 臂架组合 序号 试验工况 -次循环内容 1l0%最大起重量、相应工作 幅度 载荷起升到最大起升高度后,再下降到地 基本臂 面,载荷在下降过程中制动1次 最大工作幅度,相应110%额定 起重量 载荷起升到臂架可以回转的离地高度,在作 业区范围内左右回转360'",在左右回转过程中 最小工作幅度、相应110%额定 各制动1次、2次
起重量 载荷起升至最大高度后,再下降到地面,载 中长主臂 荷在下降过程中制动1次 载荷起升离地,起臂至最小工作幅度,再落 最大工作幅度、相应110%额定 臂至最大工作幅度,再将载荷下降到地面,在 起重量 起、落臂过程中各制动1次 载荷起升到臂架可以回转的离地高度,在作 业区范围内左有回转360",在左有回转过程中 最小工作幅度、相应110%额定 t 各制动1次、.2 起重量 载荷起升至最大高度后,再下降到地面,载 标 最长主臂 荷在下降过程中制动1次 准 载荷起升离地,起臂至最小工作幅度,再落 最大工作幅度、相应110%额定 臂至最大工作幅度,再将载荷下降到地面,在 起重量 起,落臂过程中各制动1次 载荷起升离地,起臂至最小工作幅度,再落 最大工作幅度及相应110%额 臂至最大工作幅度,再将载荷下降到地面,在 定起重量 起、落臂过程中各制动1次 载荷起升到臂架可以回转的离地高度,在作 基本臂十最短副臂" 业区范围内左右回转360",在左右回转过程中 最小工作幅度、相应110%额定 各制动1次、2次
起重量 载荷起升至最大高度后,再下降到地面,载 荷在下降过程中制动1次 载荷起升离地,起臂至最小工作幅度,再落 最大工作幅度及相应110%额定 臂 至最大工作幅度,再将载荷下降到地面,在 起重量 起落臂过程中各制动1次 载荷起升到臂架可以回转的离地高度,在作 中长主臂十中长副臂" 业区范围内左右回转360'",在左右回转过程中 最小工作幅度、相应110%额定 各制动1次,2次
10 起重量 载荷起升至最大高度后,再下降到地面,载 荷在下降过程中制动1次 18
GB/T14560一2016 表3(续 类别 序号 试验工况 臂架组合 -次循环内容 载荷起升离地,起臂至最小工作幅度,再落 最大工作幅度及相应110%额定 臂至最大工作幅度,再将载荷下降到地面,在 1l 起重量 起落臂过程中各制动1次 载荷起升到臂架可以回转的离地高度,在作 最长主臂十最短副臂" 业区范围内左右回转 ,在左右回转过程中 360 最小工作幅度、相应110%额定 12 各制动1次,2次
起重量 载荷起升至最大高度后,再下降到地而,载 标 荷在下降过程中制动1次 准 载荷起升离地,起臂至最小工作幅度,再落 最大工作幅度及相应110%额定 况 13 臂至最大工作幅度,再将载荷下降到地面,在 起重量 起、落臂过程中各制动1次 载荷起升到臂架可以回转的离地高度,在作 最长主臂十最长副臂 业区范围内左右回转360",在左右回转过程中 最小工作幅度、相应110%额定 14 各制动1次2次
起重量 载荷起升至最大高度后,再下降到地面,载 荷在下降过程中制动1次 最小工作幅度和相应的超起配 重,超起配重回转半径、相应 15 10%额定起重量 载荷起升到最大高度后,再下降到地面,载 基本臂 最大工作幅度和相应的超起配荷在下降过程中制动1次 重、超起配重回转半径、相应 16 110%额定起重量 载荷起升到臂架可以回转的离地高度,在作 最小工作幅度和相应的超起业区范围内左右回转360°,在左右回转过程中 17 配重、超起配重回转半径、相应各制动1次,2次 l10%额定起重量 载荷起升至最大高度后,再下降到地面,载 中长主臂 荷在下降过程中制动1次 载荷起升离地,起臂至最小工作幅度,再落 最大工作幅度和相应的超起配 起 重,超起配重回转半径、相应臂至最大工作幅度,再将载荷下降到地面,在 18 110%额定起重量 起、落臂过程中各制动1次 况 载荷起升到臂架可以回转的离地高度,在作 最小工作幅度和相应的超起配业区范围内左右回转360",在左右回转过程中 19 重、超起配重回转半径、相应各制动1次、2次
110%额定起重量 载荷起升至最大高度后,再下降到地面,载 最长主臂 荷在下降过程中制动1次 载荷起升离地.起臂至最小工作幅度,再落 最大工作幅度和相应的超起配 重、超起配重回转半径、相应臂至最大工作幅度,再将载荷下降到地面,在 20 1l0%额定起重量 起、落臂过程中各制动1次 最大工作幅度及相应的超起配 载荷起升离地,起臂至最小工作幅度,再落 重、超起配重回转半径、相应臂至最大工作幅度,再将载荷下降到地面.在 基本臂十最短副臂" 21 1l0%额定起重量 起,落臂过程中各制动1次 19
GB/T14560一2016 表3(续 类别 臂架组合 序号 试验工况 -次循环内容 载荷起升到臂架可以回转的离地高度,在作 相应的超起配重、超起配重回转业区范围内左右回转360",在左右回转过程中 基本臂十最短副臂 半径,最小工作幅度,相应110%各制动1次.2次
22 额定起重量 载荷起升至最大高度后,再下降到地面,载荷 在下降过程中制动1次 最大工作幅度及相应的超起配载荷起升离地,起臂至最小工作幅度,再落 重、超起配重回转半径、相应臂至最大工作幅度,再将载荷下降到地面,在 23 110%额定起重量 起、落臂过程中各制动1次 载荷起升到臂架可以回转的离地高度,在作 中长主臂十中长副臂" 相应的超起配重、超起配重回转业区范围内左右回转360",在左右回转过程中 半径,最小工作幅度,相应110%各制动1次,2次
24 额定起重量 荷起升至最大高度后,再下降到地面,载 荷在下降过程中制动1次 超 载荷起升离地,起臂至最小工作幅度,再落 最大工作幅度及相应的超起配 起 重、超起配重回转半径、相应臂至最大工作幅度,再将载荷下降到地面.在 25 110%额定起重量 起、落臂过程中各制动1次 载荷起升到臂架可以回转的离地高度,在作 最长主臂十最短副臂 相应的超起配重、超起配重回转业区范围内左右回转360",在左右回转过程中 半径,最小工作幅度,相应110%各制动1次,2次
26 额定起重量 载荷起升至最大高度后,再下降到地面,载 荷在下降过程中制动1次 最大工作幅度及相应的超起配 载荷起升离地,起臂至最小工作幅度,再落 重,超起配重回转半径、相应臂至最大工作幅度,再将载荷下降到地面,在 27 110%额定起重量 起、落臂过程中各制动1次 载荷起升到臂架可以回转的离地高度,在作 最长主臂十最长副臂 相应的超起配重、超起配重回转业区范围内左右回转360",在左右回转过程中 半径,最小工作幅度、相应110%各制动1次、2次
28 额定起重量 载荷起升至最大高度后,再下降到地面,载 荷在下降过程中制动1次 副臂分为固定副臂和变幅副臂
5.8.2.2带载行走 5.8.2.2.1标准工况试验 中长主臂、最小工作幅度,臂架位于行走方向的正前方,起吊带载行走时相应工况110%额定起重 量的试验载荷,载荷起升到离地高度500mm左右,起重机以最低稳定速度直线前进和后退行走各 20 m
试验重复3次
心
GB/T14560一2016 5.8.2.2.2超起工况试验 相应的超起配重、超起配重回转半径、中长主臂,最小工作幅度、臂架位于行走方向的正前方,起吊 带载行走时相应工况110%额定起重量的试验载荷,载荷起升到离地高度500mm左右,起重机以最低 稳定速度直线前进和后退行走各20m 试验重复3次
5.8.2.3起升机构制动性能 基本臂、最小工作幅度时,起吊相应工况110%额定起重量的试验载荷,载荷起升到离地3m高处 停留至少5min,起升机构未见打滑
5.8.2.4安全装置验证 在试验过程中,验证超载保护装置、三色指示灯和安全监控管理系统的报警功能 试验载荷在相应工况100%110%额定起重量之间时,额定起重量限制装置应连续报警,并 a 自动停止向危险方向运动,允许间安全方向动作,操作强制开关后可继续向相同方向动作 b)试验载荷超过相应工况100%额定起重量时,三色指示灯的红灯亮,并报警
5.9 静载荷试验 5.9.1试验目的 验证起重机及其各部分结构的承载能力
在试验过程中或试验结束后,检查起重机的结构件是否产生裂纹,永久变形,油漆剥落;零部件是否 产生对起重机的性能与安全有影响的损坏,连接处是否出现松动或损坏
5.9.2试验方法 在标准工况和超起工况时分别进行如下试验 起重机在基本臂,基本臂十最短副臂组合,臂架处于最不利的方向,起吊相应工况额定起重量最大 值的1.25倍试验载荷,载荷起升到离地高度200mm左右,停留10min后,再下降到地面
5.10整机抗倾覆稳定性试验 5.10.1试验目的 验证起重机的静态稳定性、抗后倾覆稳定性
5.10.2静态稳定性 5.10.2.1基本臂 臂架处于起重机稳定性最不利位置,臂架仰角处于产生最大倾覆力矩的工作幅度、起吊相应工况 1.25Pa+0.1F)的试验载荷
慢速起升载荷到一定的离地高度,停留10min. 注1:Pa -由起重机制造厂规定的在不同幅度下起重机的额定起重量的重力
注2:F -将主臂质量或副臂质量换算到主臂端部或副臂端部的质量重力
5.10.2.2最长主臂 臂架处于起重机稳定性最不利位置,臂架仰角处于产生最大倾覆力矩的工作幅度,起吊相应工况 21
GB/T14560一2016 (1.25Pa+0.1F)的试验载荷
慢速起升载荷到一定的离地高度,停留10min
5.10.2.3最长主臂+最长副臂含固定副臂或变幅副臂 臂架处于起重机稳定性最不利位置,臂架仰角处于产生最大倾覆力矩的工作幅度,起吊相应工况 1.25Pa十0.1F)的试验载荷,分别对不同的臂架组合形式进行试验
慢速起升载荷到一定的离地高 度,停留10n min 5.10.3抗后倾覆稳定性 按设计工况配置对基本臂进行试验
臂架位于最大仰角,分别处于起重机的正侧方、正前方和正后 方,吊钩和其他取物装置放在地面上
当试验条件不具备时,可采用计算法 5.11 密封性能试验 在空载试验、额定载荷试验,动载荷试验和静载荷试验过程中或试验结束后15" min内,检查液压油 箱、油泵、油马达、液压油缸、液压阀、管接头,油堵等连接部位有无渗漏
5.12噪声测量 司机室内噪声和机外辐射噪声功率级的测量方法应符合GB20062的规定
5.13发动机排气污染物测量 发动机排气污染物的测量方法按GB20891的规定进行
5.14液压油固体颗粒污染测量 在5.5一5.11规定的试验结束后,检查液压油箱中液压油的固体颗粒污染,检测方法按JB/T9737 的规定进行
5.15结构试验 5.15.1试验目的 验证起重机在起吊相应工况的试验载荷时主要结构件的应力、测试应力的安全判别、结构动特性测 试和结果处理方法
5.15.2试验方法 起重机的结构试验方法见附录D.
5.16可靠性试验 5.16.1试验目的 评定起重机在规定条件和预定的时间内强化作业状态下的工作能力、考察起重机在作业时整机和 零部件的可靠性、主要零部件的耐磨性、整机基本性能的稳定程度和液压油的温度等
5.16.2一般要求 5.16.2.1起重机应在规定的时间内完成表4规定的循环次数
规定的试验时间包括作业时间和有效 停机时间,不包括臂架和超起装置的安装时间
如果样机超出规定时间,则不计可靠性指标
22
GB/T14560一2016 5.16.2.2试验期间,样机若出现致命故障,如:主要结构件永久性变形,重要焊接开裂、翻车等,本次试 验应终止,不计可靠性指标 5.16.2.3试验完成后,应对关键焊缝进行探伤检测
5.16.2.4操作要求如下: a)操作人员应严格执行使用说明书规定的操作规程,应平稳操作,确保设备和人身安全 b)按使用说明书的要求完成每日(班)的正常保养; 试验期间不允许带故障作业 c d)试验样机每天作业时间一般不少于8h. 5.16.3试验方法 可靠性试验的臂架组合、循环次数、试验工况、一次循环内容和试验总时间见表4
表4可靠性试验 循环次数 臂架 试验工况 -次循环内容 类别 组合 A B C D E F 最小工作幅度、最大起 50 40 15 30 重量 载荷起升到最大起升高度后,再下降 基本臂 到地面,载荷在下降过程中制动1次 最大工作幅度、相应额定 50 30 40 15 起重量 载荷起升到臂架可以回转的离地高 度,在作业区范围内左右回转360",在 最小工作幅度、相应额定 20o15o35 20 10 左右回转过程中各制动1次.2次 起重量 载荷起升到最大起升高度后,再下降 到地面,载荷在升降过程中各制动1次 中长主臂 载荷起升离地,起臂至最小工作幅 最大工作幅度,相应额定度,再落臂至最大工作幅度,再将载荷 20 0 20015o35 起重量 下降到地面,在起、落臂过程中各制动 1次 载荷起升到臂架可以回转的离地高 在 度,在作业区范围内左右回转360°, 最小工作幅度,相应额定 100 80 35 20 15 左右回转过程中各制动1次,2次
况 起重量 载荷起升到最大高度后,再下降到地 最长主臀 面,载荷在升降过程中各制动1次 载荷起升离地,起臂至最小工作幅度, 最大工作幅度、相应额定 15 10o8o35 20 再落臂至最大工作幅度,再将载荷下阵 起重量 到地面,在起、落臂过程中各制动1次 载荷起升离地,起臂至最小工作幅度 固定副臂工况/副臂起臂至最小工作 最长主臂十 最大工作幅度、相应额定 15 20015o3525 幅度(变幅副臂工况),载荷起升至最大 最长副臂 起重量 高度后,再下降到地面
载荷在下降过 程中制动1次 中长主臂、最小工作幅 试验载荷起升到离地高度500mm左 带载 20 度、臂架位于行走方向的右,起重机以最低稳定速度直线前进和 10080 50 10 行走 正前方,相应额定起重量后退行走各20m 23
GB/T14560一2016 表4(续 循环次数 臂架 类别 试验工况 -次循环内容 E 组合 T B 最小工作幅度和相应的 10040 30 超起配重,超起配重回转 半径、相应额定起重量 载荷起升到最大起升高度后,再下降 基本臂 最大工作幅度和相应的到地面,载荷在下降过程中制动1次 超起配重、超起配重回转 30 5 40 15 100 半径、相应额定起重量 载荷起升到臂架可以回转的离地高 最小工作幅度和相应的度,在作业区范围内左右回转 360°,在 S0 10 100 3520 超起配重、超起配重回转左右回转过程中各制动1次、2次
半径,相应额定起重量 载荷起升到最大高度后,再下降到地 中长主臂 面,载荷在升降过程中各制动1次 载荷起升离地,起臂至最小工作幅 最大工作幅度和相应的 度,再落臂至最大工作幅度,再将载荷 100 80 35 20 10 超起配重、超起配重回转 下降到地面,在起、落臂过程中各制动 半径、相应额定起重量 1次 载荷起升到臂架可以回转的离地高 最小工作幅度和相应的度,在作业区范围内左有回转360",在 T 超起配重,超起配重回转左有回转过程中各制动1次.2次
15 100803520 半径、相应额定起重量 载荷起升到最大高度后,再下降到地 ,载荷在升降过程中各制动1次 面 最长主臂 载荷起升离地,起臂至最小工作幅 最大工作幅度和相应的 度,再落臂至最大工作幅度,再将载荷 10080 35 20 15 超起配重,超起配重回转 下降到地面,在起、落臂过程中各制动 半径、相应额定起重量 1次 载荷起升离地,起臂至最小工作幅度 相应的超起配重、超起配固定副臂工况/副臂起臂至最小工作 最长主臂十 15 重回转半径,最大工作幅幅度(变幅副臂工况),载荷起升至最大 100803530 最长副臂 度、相应额定起重量 高度后,再下降到地面
载荷在下降过 程中制动1次 相应的超起配重、超起配 重回转半径,中长主臂、 试验载荷起升到离地高度500mm左 50 20 10 带载行走 10o80 最小工作幅度、臂架位于右,起重机以最低稳定速度直线前进和 行走方向的正前方,相应后退行走各20m 额定起重量 试验总时间/h 350350350 注1:A -最大起重量P<150t的起重机;B 最大起重量 -最大起重量1501
GB/I14560一2016 5.16.4作业率计算方法 作业率按式(4)计算
R= -下x100% 式中: R 作业率; T -总作业时间,单位为小时(h) T 故障排除总时间,单位为小时(h). 检验规则 6.1 分类 起重机的检验分出厂检验和型式检验 6.2出厂检验 起重机应逐台进行出厂检验,检验合格后由质量检验部门签发产品合格证
出厂检验项目及各项目缺陷等级见附录E,载荷试验时至少应选取3个工况
6.3型式检验 6.3.1进行型式检验的样机应是出厂检验的合格产品,型式检验项目见附录E
检验样机采用随机方 法抽取1台抽样基数不眼
6.3.2凡属下面情况之一者,应进行型式检验: a)新产品或老产品转厂生产的试制定型时; b)产品停产3年后恢复生产时; 已定型或批量生产的产品,如主要结构,工艺和材料有较大改变,可能影响产品性能时,应对相 应试验进行补充试验; 出厂检验结果与上次型式检验有重大差异时; dD e)当国家质量监督机构提出进行型式检验要求时
属于a),b)和e)的情况时,应按表E.1规定的项目进行检验;属于e),d)两种情况时,可仅对受影响 的项目进行检验
6.3.3起重机的合格判定见表5
首次样机不合格,允许对其缺陷项目进行修复,调试或更换易损件后,重检其缺陷项目
如重检仍 不合格,应重新抽取样机
第二台样机再不合格,则判样机不合格
制造厂应对该型号的产品进行整 改,整改完成后再进行型式检验
表5合格判定表 缺陷数量及组合 缺陷等级 致命 关键 25
GB/T14560一2016 表5(续 缺陷数量及组合 缺陷等级 重要 -般 注1:在四组组合中,任一组合的判定数被达到,则产品或样机为不合格
注2:重复的检验项目其故障只计算一次
使用说明书与标志 7.1使用说明书 使用说明书应符合GB/T9969的规定
使用说明书的主要内容至少应包括以下内容 a)安全说明: b 技术特性说明; e)使用、操作说明 d)装配,起吊、拆卸和运输的说明 故障分析与排除说明; e f 维修和保养说明
7.2标志 7.2.1起重机标志和各种指示信息应包含中文
7.2.2应在起重机机身明显位置固定标牌,标牌应符合GB/T13306的规定
7.2.3标牌应至少包括以下内容 产品型号和名称 a) b 最大起重量 额定功率, e d 出厂编号; e)生产日期, f 制造厂名称 包装、运输和贮存 8.1包装 8.1.1起重机应按使用说明书规定的运输图要求进行解体,被解体的部件要有识别标志,以免发生 混淆
8.1.2解体后的零部件应按照GB/T13384的规定进行包装
包装时应合理摆放垫木,下车、履带、配 重,吊钩滑轮组、臂架臂节等基本处于水平状态,并使机件的表面不受损伤
8.1.3起重机应至少附有如下随行文件: 产品合格证 a 26
履带起重机GB/T14560-2016介绍
一、定义
履带起重机,是指具有行走装置和变幅机构的起重机,能够在不同地形条件下进行移动和起重作业。根据国家标准GB/T14560-2016,履带起重机可以分为以下几种类型:
- 全回转履带起重机
- 全伸展履带起重机
- 爬式履带起重机
- 斜臂履带起重机
- 桁架式履带起重机
二、分类
根据其结构特点和应用范围,履带起重机可分为以下几个类别:
- 工业起重机
- 港口起重机
- 桥梁施工起重机
- 船舶起重机
- 矿山起重机
三、结构
履带起重机的主要结构包括:行走系统、起重机构、变幅机构和电气控制系统。其中,行走系统由履带、驱动设备、制动器等组成;起重机构由起重钩、卷扬机、钢丝绳等组成;变幅机构由变幅机构本体、滑车、支架、导轮等组成。
四、工作原理
履带起重机的工作原理是通过行走装置移动到作业位置后,启动起重机构进行起重作业。其具体步骤如下:
- 行走系统将起重机移动到作业位置,并对其进行固定
- 通过变幅机构调整起重机的幅度,达到所需高度和距离
- 启动起重机构进行起重作业,完成后将起重机移动到下一个作业位置
五、使用注意事项
在使用履带起重机时,需要注意以下几点:
- 操作人员必须经过专业培训,掌握其结构和工作原理
- 在使用前应进行全面检查,确保设备正常运行
- 严禁超载和操作不当等危险行为
- 在使用过程中,要注意并避免起重机的倾斜和侧翻
- 及时做好维护保养工作,延长设备寿命