GB/T34886-2017
无损检测复合材料激光错位散斑检测方法
Non-destructivetesting—Testmethodforlasershearographyofcompositematerials
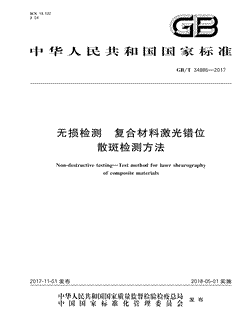
- 中国标准分类号(CCS)J04
- 国际标准分类号(ICS)19.100
- 实施日期2018-05-01
- 文件格式PDF
- 文本页数13页
- 文件大小9.82M
以图片形式预览无损检测复合材料激光错位散斑检测方法
无损检测复合材料激光错位散斑检测方法
国家标准 GB/T34886一2017 无损检测复合材料激光错位 散斑检测方法 Non-destruetivetesting一Iesmethodlforlasershearography fcompsitematerials 2017-11-01发布 2018-05-01实施 国家质量监督检验检疫总局 发布 国家标准化管理委员会国家标准
GB/34886一2017 前 言 本标准按照GB/T1.1一2009给出的规则起草
本标准由全国无损检测标准化技术委员会(SAC/TC56)提出并归口
本标准起草单位;北京航空材料研究院、上海大学、广州一道注塑机械股份有限公司航天材料及工 艺研究所、北京卫星制造厂、上海航天精密机械研究所、上海卫星装备研究所、北京嘉盛智检科技有限公 司、航空综合技术研究所
本标准主要起草人:郭广平、杨党纲、唐佳、张东升、曾启林、程茶园、毕丽、涂俊、周莉、帅家盛、 李慧娟、张于北
GB/34886一2017 无损检测复合材料激光错位 散斑检测方法 范围 本标准规定了复合材料构件的激光错位散斑检测方法
本标准适用于检测复合材料层压板、蜂窝夹芯胶接构件、泡沫夹芯胶接构件,可检测的缺陷类型包 括脱粘、分层、冲击损伤等
其他材料的胶接缺陷检测,可参照使用
规范性引用文件 下列文件对于本文件的应用是必不可少的
凡是注日期的引用文件,仅注日期的版本适用于本文 件
凡是不注日期的引用文件,其最新版本(包括所有的修改单)适用于本文件
GB7247.1激光产品的安全第1部分:设备分类、要求 GB/T9445无损检测人员资格鉴定与认证 GB/T20737无损检测通用术语和定义 术语和定义 GB/T20737界定的以及下列术语和定义适用于本文件
3.1 离面位移out-of-planedisplacement 垂直于物体表面(法线方向)的位移分量
激光错位散斑技术直接测量的参数本质上是物体的离面 位移 3.2 错位量shearveetor 剪切量 激光错位散斑检测系统的光学成像装置将物体的两个错位像叠加成像,两个图像之间的距离和相 对方向,见图1
3.3 散斑图speeklegram 激光照射物体表面时由于漫反射在物体表面形成的斑点状图像,见图2a)
随机分布的斑点随物 体表面变形同步移动,成为表面位移信息的载体
3.4 干涉条纹图fringepatterm 变形前后两幅散斑图数字相减得到的黑白相间的条纹状图像,见图2b),条纹图包含物体表面的 位移信息
3.5 相位图phasemapshearogram 通过激光错位散斑系统中的相移装置获得的多幅散斑图进行运算获得的对应点光学干涉光学相位
GB/T34886一2017 差的图像,见图2b)
相位图分为包裹相位图和解包裹相位图两种
包裹相位图的相位以2开为周期变 化,黑白条纹存在灰度突变,见图2e)
解包裹相位图通过相位补偿算法使相位连续变化,表现在图像 上为灰度的连续变化,见图2d)
错位图像 原始图像 原始图像 错位图像 +1 + 错位量(45" 错位量(一60 图1激光错位散斑检测技术中错位量 干涉条纹图 包裹相位图 解包裹相位图 b 散斑图 图2激光错位散斑检测技术获得的不同图像 人员资格 教照木标唐实能检渊的人员,应拨照GB/T45或合同各力同意的体系进行资修整定与认证.开" 由雇主或代理对其进行岗位培训和操作授权
方法概要 5 5.1激光错位散斑检测方法的原理图如图3所示
激光器发出的相干光经过扩束经照射被检测物体 其漫反射表面产生散斑场
分束镜和两个反射镜产生的两束光(两幅错位的图像)在cCD处叠加成 幅图像
物体上的两个点P1和P2(简称“对点”),成像后叠加为一点P,形成散斑图,可通过计算机看 到
采集加载前后两个变形状态下的散斑图做数字相减,得到包含表面离面位移信息的干涉条纹图,其 条纹图P点处的条纹级次代表“对点”的离面位移差
采用相移技术,多次移动相移镜,采集变形前后 具有特定相移量的多幅图像,计算后得到相位图[见图2c)]
相位图的图像质量和测量灵敏度都有显 著提高,图像的物理意义依然是“对点”的离面位移差
相位图进一步进行解包裹运算可以得到表征离 面位移一阶微分无条纹图像即解包裹图[见图2d)]
如果有缺陷则表面会产生异常的离面位移,在图 像对应位置处也会出现异常的条纹图或相位图
通过条纹异常区的特征可识别缺陷的位置和大小
GB/34886一2017 观察方向 错位散斑 成像镜 照相机 图像 微调 采集卡 反光镜 中心枝 分束镜 变形量 相移镜 计算机图 像软件 测量矢量 试验板 照射方向 扩束镜 激光器 显示屏 注,P.P是物体上的两个点,通过成像系统在成像面合成一个点P 图3激光错位散斑检测技术原理 5.2检测时加载方法取决于被检工件材料对加载产生的反应
最合适的加载方法和加载大小主要取 决于缺陷类型和缺陷深度,同时应考虑材料及结构形式
因此在连续检测前应对被检工件试样进行试 验性测试
注意应在确保加载不会对被检测对象产生损坏的情况下进行测试
5.3图3所示的激光错位散斑检测系统采用了迈克尔逊光路,这是目前主流的光路
也有采用双折射 梭镜或分光镜剪切干涉仪等光路的系统
由于激光错位散斑检测系统通过测量表面离面位移来判断内部的缺陷,其灵敏度随着缺陷深度的 5.4 增加而逐渐降低
因此,激光错位散斑技术特别适合检测复合材料层压板的分层及泡沫或蜂窝等夹层 结构的脱粘缺陷
5.5激光错位散斑技术测量离面位移的范围理论上可达到10nm一5004m
受环境影响和不同硬件 性能的影响,实际检测中离面位移的测量范围通常在0.1 m一100,Am
对于复合材料结构,可检测的 缺陷大小和深度与蒙皮材料/厚度、芯材材料以及加载方法等密切相关 5.6选择激光错位散斑方法检测前,应对采用不同加载方法时被检工件可能产生的离面位移进行分 析,估算检测灵敏度是否满足要求
真空加载下激光错位散斑方法检测能力的定量分析方法参见附录 A
理论分析可行后,应制作带有要求检出的最小缺陷的对比试块进行实验验证,以确定检测方法的可 行性,在此基础上编制产品的检测工艺规程
检测系统 6.1系统组成 检测系统应能满足激光错位散斑检测的基本要求,通常包括激光器、错位散斑照相机、调节与控制 装置、图像处理计算机和加载装置等
GB/T34886一2017 6.2激光器 激光器应具有良好的相干性、,均匀性和稳定性
激光器的功率决定了每次检测面积的大小
6.3错位散斑照相机 错位散斑照相机应具备发现被检工件中最大容许缺陷的能力
宜使用像素数不低于1024又× 1024、模数转换(A/D)不低于12位的cCD摄像机
错位散斑照相机应具有设定错位量的功能
激光 器宜集成在错位照相机上,改善检测系统的整体性
6.4调节与控制装置 错位散斑照相机应有四个基本调节功能
能够实现镜头在水平和垂直两个方向的摆动以方便镜头 对准被检测区域;能够调节镜头光圈的大小以获得合适的光强和散斑效果;能够调整镜头焦距并对焦, 获得适当大小的检测面积和清晰的散斑图像;能够控制错位量,产生所设定角度和距离的一对错位图 像
激光控制器能够控制激光束水平和垂直方向的变化,使其对准被测表面,同时采用适当的滤波及扩 束光学装置使被测表面获得均匀的激光照明
6.5图像处理计算机 图像处理计算机用于数字图像的获取、处理和存储,通过软件的不同运算功能得到各种检测图像
计算机应具有连续获取和处理图像的能力以产生检测所需的全场实时图像
软件宜具有图像拼接功 能,拼接局部的分区图像,获得被检测件的整体检测结果
6.6加载装置 6.6.1加载装置用于对被检测工件进行加载,使工件产生微小的非破坏性变形
可包含多种类型,如 真空加载装置、热加载装置、声加载装置、机械振动加载装置等,以适应检测需求
6.6.2真空加载装置由密封真空室、抽真空装置以及位于真空室与大气压之间的真空阀组成
真空室 中的压强差变化范围宜在1kPa14kPa之间
6.6.3热加载装置对工件检测区域加热,使工件表面温度升高的装置
常用的有高强度石英灯和热吹 风机 6.6.4声加载装置利用声学装置如喇叭)对被检工件产生激振,此装置由信号发生器、信号放大器和 声学驱动三部分组成
6.6.5机械振动加载装置
机械固定或真空吸附的压电陶瓷(PZT)可以作为振动加载装置
该装置 由信号发生器,功率放大器和PZT组成
该装置是由信号发生器产生正弦或其他波型,通过功率放大 器驱动PzT,产生所需振幅的振动,并将该振动传至被检工件
检测准备 7.1对比试块 7.1.1对比试块的制作应采用与被检工件相同或相近的材料,结构和工艺,并根据验收条件所限定的 缺陷类型及大小确定人工缺陷的类型和尺寸
激光错位散斑检测用对比试块常见制作方法参见附 录B
7.1.2对比试块应做编号和登记,建立管理档案,并保存图纸等资料
7.1.3对比试块使用后应妥善保管
7.1.4对比试块宜采用超声C扫描和射线照相等方法进行验证,评定预制缺陷的位置,大小及状态,识
GB/34886一2017 别并标识出制造过程中产生的非预制缺陷
7.2检测环境要求 7.2.1环境温湿度应满足检测设备所有仪器对工作温湿度的要求
7.2.2应尽量避免在露天环境下进行检测,宜在机库、大厂房等室内环境下检测
若检测只能在露天 环境下进行,应避免雨雪天和刮风天工作,并应对阳光进行有效的遮挡
7.2.3室内检测时,若周围光线较强,也应进行有效的遮挡
7.2.4应避免电磁,振动、气流等干扰
7.2.5检测环境条件适宜与否可通过对对比试块的检测进行验证
7.3安全要求 7.3.1严格执行GB7247.1的有关规定,严禁直视激光源,避免长时间看激光束
使用声波激振时,所有在场人员应戴防护耳机
7.3.2 实验室门口和相关工作区域应有激光防护,嗓声防护的警示标识
7.3.3 检测程序 根据检渊工件的特点和检渊要求选用适当的加载方法
宜采用的加载方法参见附录c. 8.1 8.2将被检工件放置或固定在安全、稳定的位置
错位散斑照相机应摆放在合适的位置 8.3被检测表面应清洁,对水迹、油污、反光点等应做擦除或喷漫反射涂料等处理
8.4对大型工件检测时,应根据单次检测区域的大小做适当的检测区域划分,并对划分的区域做好标 记和编号
例如在区域的四个角分别做分区标记,便于确认检测区域覆盖范围,以及对缺陷准确定位
8.5按厂家提供的操作说明书依次开启计算机、激光器和错位散斑照相机的总控电源,运行错位散斑 检测计算机程序
8.6调整激光器和错位散斑照相机 对准被检工件,调节视场缩放功能键,使视场覆盖检测区域; aa 调整焦距,使成像清晰; b 设定错位量,建议设为假定缺陷尺寸(或允许最大缺陷尺寸)的50%~100%.通常在5mm~ 15mm之间; 尽量提高检测区域激光光强,调整照相机光圈,使成像在实时采集后接近于(但不要达到 饱和3 如被检工件表面过于光滑,出现反射光进人照相机、局部图像亮度饱和的情况,可调整照相机 视角,避免反射光直接射人镜头 对大型被检工件,划分检测区域的分区标记应全部出现在计算机的检测视场中,以保证相邻被 检区域之间有适当的重合,避免结合部位漏检 8.7校准检测系统;放置一个两点间距已知的标志物在被检工件视场中
可以采用间隔已知、平行人 射的两束激光产生的点实现自动校准;也可以用一把经过标定的尺子进行人工校准
通过标识物对检 测的水平方向,垂直方向进行调整;并对被检工件图像做尺寸定量,设定错位量的大小和方向
自动校 准方式能够在视野距离等检测参数发生变化时随时校准,并能自动检测缺陷尺寸,有利于提高检测 效率
8.8将对比试块放置在被检区域进行检测,调整仪器设置参数,确保要求检测的最小缺陷可以被检出
记录设备参数、检测条件、检测步骤及检测图像,用于实际检测对比
8.9设定加载时间、图像采集时间(包括初始状态图像与加载后的最终图像采集时间间隔)等参数
应
GB/T34886一2017 根据工件材质、结构尺寸,缺陷可能的大小,形状和深度等因素设置加载时间
当材料尺寸厚、缺陷尺 寸小,缺陷位置深时,可适当选择较长的加载时间
初始状态的图像采集时间一般可开始于加载后干涉 图像刚进人稳定状态的时刻
8.10检测过程中,针对不同检测部位,应根据实际检测图像质量确定是否调整检测参数
参数调整后 需重新检测对比试块以确认检测灵敏度满足检测要求
检测结果评价 9.1根据检测图像判断是否有缺陷
常见缺陷的图像显示参见附录D. 9.2检测图像中出现下列情况需要重点关注 干涉条纹图局部密集,增大载荷后条纹密集加剧 a b 干涉条纹图方向或趋势改变,出现异常; c 图像中或清晰的蜂窝格中出现局部变形; d 图像中出现蝶形特征条纹
9.3通过观察干涉条纹动态变化过程,判断缺陷位置及类型
9.4结合工件内部结构信息及其在图像显示中的连续性判断是否存在缺陷
g.5大尺寸缺陷导致的离面位移大,可能覆盖附近小尺寸缺件的检测图像 9.6检测过程持续的时间越长,信号的强度就越强,同时噪声也会增加
9.7实际检测中因结构变化、材料不同、材质差异等因素的影响也会出现异常的条纹走向和局部条纹 的密集,在检测前应充分了解被检工件的结构和材料构成
9.8根据蝶形特征条纹的轮廓尺寸和两椭圆同心圆的中心距之差判断缺陷大小,并与对比试块中相同 类型、尺寸相近的预制缺陷图像进行比对,修正缺陷尺寸
对于具有自动校准功能的设备,可通过视频 卡尺或线轮廓法在解包裹图像上直接进行缺陷尺寸测量
10 检测报告 10.1检测记录应包括以下内容: 被检工件名称、图号、零件编号和检测序号 a b) 复合材料构件详细信息,如蒙皮、芯材的厚度,蒙皮、芯材的材料类型,蜂窝芯格边长 检测工艺参数.包括分区信息、检测工作距离、错位量、加载方法及参数等 c 检测日期检测地点、,记录者、检测结果 d 必要时,注明所采取的改善检测条件措施,如遮光、屏蔽等
e 0.2检测报告应包括以下内容 委托单位; a 被检工件名称、图号、材料、零件编号、检测任务序号以及分区信息; b 采用的对比试块,检测结果和结论、检测标准名称; c 报告编号、报告日期 d 编写人、审核人及批准人
GB/34886一2017 录 附 A 资料性附录 真空加载下检测能力的定量分析 航空航天领域广泛采用的蜂窝夹层结构的蒙皮厚度一般在1mm左右
分层和脱粘缺陷分布的深 度也在这一范围
而要求检测的最小缺陷直径一般在6mm~25mm
上述参数基本符合固体力学弹 性薄板小挠度理论的要求
因此,在研究缺陷的变形特征时,用受法向均布载荷的周边固支的圆形薄板 作为缺陷的力学模型图A.1)
周边固支模拟正常部位,均布载荷很好地模拟了真空加载下缺陷的受 力状态
图A.1缺陷的受力模型 周边固支的圆形薄板在均匀载荷作用下的变形有解析解,中心层的挠度见式(A.1) qoa" A.1 6D 式中 -距离圆心r处的挠度,单位为米(m); w -载荷值(在真空加载中是压力差),单位为兆帕(MPa) go -缺陷的半径,单位为米(m). D 弯曲刚度,见式(A.2)
E D A.2 12G 式中 材料的弹性模量,单位为兆帕(MPa) 泊松比,无量纲 -薄板的厚度,单位为米(m)
错位量达到周边固支圆板直径的一半时,检测灵敏度达到极限
在无损检测应用中,为了得到最高 的检测灵敏度,只要使错位量达到要求检测的最小缺陷的尺寸一半,即可获得最高检测灵敏度
一般认 为在所选择的真空加载产生的压差下,当中心变形量达到微米以上时可在图像中分辨出缺陷
GB/T34886一2017 附录 B 资料性附录) 复合材料对比试块制作方法 对比试块的材料、制造工艺和缺陷类型应与实际被检测工件相同或相近,缺陷特征应具有代表性 激光散斑检测常见缺陷类型为脱粘和冲击伤
脱粘缺陷常采用背面打孔,双层聚四氟乙烯薄膜封闭空气法和插片法
打孔法是将蜂窝材料、泡沫材料等内芯去除,不损伤上蒙皮
打孔直径应覆盖验收标准要求并在检 测灵敏度之内
双层聚四氟乙烯薄膜封闭空气法是采用双层聚四氟乙烯薄膜先封闭一定量的空气,然后在与被检 工件相同的制造工艺中放置于上蒙皮下进行制造 插片法是采用在薄金属片双面涂敷脱模剂,在与被检工件相同的制造工艺中放置于上蒙皮下,靠近 外边缘的位置进行制造,制造结束后,将薄金属片抽出,形成脱粘缺陷
冲击伤采用验收标准的要求进行制作,然后进行验证实验
制作的对比试块在制作后要进行验证实验
标识出制造过程中产生的新缺陷和未做成功的缺陷位 置,修改对比试块设计图使之一致,与对比试块一起保存备用
对比试块应定期(1年为宜)进行验证实验,确保缺陷状态未发生变化
对工件进行检测时,应先用对比试块采用相同条件验证检测灵敏度,确认符合要求
GB/34886?2017 ? C ?? ?????? üλ???????,????C.1 c.1?????? ? ? ?? ?о ? ? ? ? ? о? ? ? ? ? о? ? о? ? ? ?? ? ? о? о? о?
GB/T34886一2017 附 录 D 资料性附录) 复合材料的典型缺陷图像 激光错位散斑检测技术判定缺陷的基本方法是采用图像局部差异的比较
如果某一局部所对应的 被检工件表面或其内部结构并无特殊之处,而检测干涉图像中该局部变化异于其他部位,则意味着缺陷 的存在
这些异常表现为干涉条纹局部变密见图D.1),改少方向或趋势(见图D.2、图像局部出现凹 凸见图D.3,图D.4,图D.7、图D.8,图D.10)及蝶形条纹等
在激光错位散斑检测结果中,蝶形条纹是缺陷最为典型的特征
与缺陷的全息干涉条纹图不同,缺 陷的错位散斑干涉条纹图呈现出成对的椭圆同心圆(见图D.5,图D.6、图D.9)
这种成对的椭圆同心 圆为缺陷的蝶形特征条纹
图D.1某复合材料舵面缺陷 图D.2某复合材料分层缺陷 图D,3蒙皮蜂窝夹芯板中的缺陷 图D.4某蒙皮蜂窝夹芯结构件中的脱粘缺陷 10
GB/34886?2017 OO ?D.5?????? ?D.6?? ?D.7??о?? ?D.8??о?? ?D.9??ое?? ?D.10?λ
无损检测复合材料激光错位散斑检测方法GB/T34886-2017
复合材料具有轻质、高强度等特点,广泛应用于航空、汽车等领域。在生产和使用过程中,需要进行无损检测以保证其安全性和可靠性。其中,激光错位散斑检测是一种常用的无损检测方法。
GB/T34886-2017是我国制定的复合材料激光错位散斑检测标准,该标准规定了采用激光错位散斑技术对复合材料进行无损检测的方法和要求。
激光错位散斑检测利用激光束通过被检测物体时,受到不同部位反射光的干涉效应,在接收器上形成错位散斑图案。通过对错位散斑图案的分析,可以确定被检测物体表面的缺陷情况。
GB/T34886-2017中规定了激光错位散斑检测的仪器和设备、样品制备、检测方法、数据处理等方面的要求。其中,样品制备是非常重要的一环,样品应该去除污垢、空气泡等杂质,并且表面不能有反射镜面。检测时需要根据不同的缺陷进行合理的参数调整,以保证检测的准确性。
总之,GB/T34886-2017标准的制定为复合材料激光错位散斑检测提供了可靠的技术规范,这种无损检测方法在复合材料生产和使用过程中具有重要的应用价值。