GB/T26610.3-2014
承压设备系统基于风险的检验实施导则第3部分:风险的定性分析方法
Guidelineforimplementationofrisk-basedinspectionofpressureequipmentsystem―Part3:Qualitativeapproachtorisk
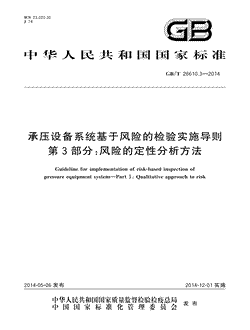
- 中国标准分类号(CCS)J74
- 国际标准分类号(ICS)23.020.30
- 实施日期2014-12-01
- 文件格式PDF
- 文本页数14页
- 文件大小509.02KB
以图片形式预览承压设备系统基于风险的检验实施导则第3部分:风险的定性分析方法
承压设备系统基于风险的检验实施导则第3部分:风险的定性分析方法
国家标准 GB/T26610.3一2014 承压设备系统基于风险的检验实施导则 第3部分:风险的定性分析方法 Guidelineforimplementationofrisk-basedlinspeetioof pressureequipentsystem一Part3:Qualitativeapproaehtorisk 2014-05-06发布 2014-12-01实施 国家质量监督检监检疫总局 发布 国家标准花管理委员会国家标准
GB/T26610.3一2014 前 言 GB/T26610(《承压设备系统基于风险的检验实施导则》分为5个部分 -第1部分:基本要求和实施程序; 第2部分基于风险的检验策略; 第3部分;风险的定性分析方法 第4部分;失效可能性定量分析方法 第5部分;失效后果定量分析方法 本部分为GB/T26610的第3部分
本部分被照GB/T1.一209给出的规则起草 本部分参考了APRP581《基于风险的检验》,并结合我国的实际情况制定
本部分由全国锅炉压力容器标准化技术委员会(SAc/Tc262)提出并归口
本部分起草单位;合肥通用机械研究院、特种设备检测研究院,福建特种设备检测研究院、 石油化工股份有限公司、石油天然气股份有限公司、石油化工股份有限公司茂名分公司、大连 西太平洋石油化工有限公司
本部分主要起草人;陈学东、艾志斌、杨铁成,胡久韶、顾望平、贾国栋、王辉、李光海、谢国山,王笑梅 张志超,何承厚,李信伟、韩建宇曲豫
GB/T26610.3一2014 承压设备系统基于风险的检验实施导则 第3部分:风险的定性分析方法 范围 GB/T26610的本部分给出了针对石油化工装置承压设备系统进行风险定性分析的方法,其他工 业承压设备系统实施的风险定性分析也可参照采用
本部分适用于GB/T26610.1所指的承压设备系统
规范性引用文件 下列文件对于本文件的应用是必不可少的
凡是注日期的引用文件,仅注日期的版本适用于本文 件
凡是不注日期的引用文件,其最新版本(包括所有的修改单)适用于本文件
GB/T26610.1承压设备系统基于风险的检验实施导则第1部分:基本要求和实施程序 术语和定义 GB/T26610.1界定的以及下列术语和定义适用于本文件
3.1 eguipmentfactor 设备因子 EF 与装置(单元或工段)中可能发生失效的设备总数相关的表征数值
3.2 损伤因子 damagefactor D 装置(单元或工段)中潜在的损伤机理种类的量化表征
3.3 检验因子 inspectionfactor IF 当前检验程序的有效性及其对识别装置(单元或工段)中潜在损伤机理的能力的量化表征
3.4 维护状态因子manteaneeconditionfaetor MCF 被评估装置(单元或工段)的设计制造水平,企业管理和维护程序运行的有效性的量化表征
3.5 factor 工艺因子 procesS Pp 装置(单元或工段)运行连续性、工艺稳定性和安全保护装置可靠性的量化表征
GB/T26610.3一2014 3.6 ealdesignfetor 机械设计因子 mechanict MDF 装置(单元或工段)设计规范的先进性及与现行标准的符合性的量化表征
燃烧与爆炸后果 damageconsequence 可燃性介质泄放到环境中引起着火与爆炸造成的各种损失的量化表征
3.8 燃烧与爆炸后果等级dam 1agecomseqencecategOry 根据化学因子、,破坏量值因子状态因子、自燃因子,压力因子和安全防护因子的组合所确定的后果 等级类别
3.9 化学因子 chemicalfactor CF 介质发生燃烧的可能性的量化表征,由可燃因子和反应因子组成 3.10 可燃因子 flashfactor FF 介质固有的可燃性的量化表征
3.11 反应因子reactionfactor RF 介质暴露于一点火源时发生反应的可能性(稳定性)的量化表征
3.12 损伤量值因子daagequantityfaetor DQF 失效事件发生后,装置中的可燃介质最大程度泄放导致的破坏程度的量化表征 3.13 状态因子 statefactor SF 介质泄放到大气中被闪蒸成蒸汽的难易度程度的量化表征
3.14 自燃因子autignmitionfactor A 介质泄漏后自行燃烧的可能性的量化表征
3.15 压力因子 pressurefactor PRF 失效事件发生后,介质泄放到环境中的快慢程度的量化表征 3.16 安全防护因子ereditfaetor CRF 装置在设计,制造过程所赋予的安全特性的量化表征
GB/T26610.3一2014 3.17 中毒后果 toxicconsegquence 有毒介质泄放到环境中引起的中毒造成的各种损失的量化表征
3.18 中毒后果类别等级toxiecnsequeneeeategory 根据中毒量值因子、扩散因子、安全防护因子以及人口因子的组合所确定的后果等级类别
3.19 中毒量值因子toxicquantityfactor Tor 失效事件发生后,装置中的有毒介质最大程度的泄放导致的破坏程度的量化表征
3.20 扩散因子dispersibilityfaector DLF 介质扩散能力的量化表征
3.21 人口因子 populationfactor PPF 失效事件发生后,可能受到某一有毒介质泄放影响的人数的量化表征
总则 定性分析的程序 4.1 分析前应首先确定被评估装置(单元或工段)的物理边界和介质特性,然后按第5章确定其失效可 能性,按第6章确定其失效后果,按第7章确定其风险等级
4.2 一般原则 4.2.1当装置(单元或工段)中有若干种主要的介质时,应根据介质种类分别计算该装置的失效后果, 并确定风险级别,以风险级别最高的结果作为该装置最终的风险级别
4.2.2在进行风险的定性分析时,为保证评估结果的一致性,当某 一问题有多种可选答案时,应选择其 中的一种,而不是使用插值
4.3定性分析的应用 风险的定性分析方法可以单独应用.也可以和定量方法结合起来使用
在受条件限制无法进行 4.3.1 全部定量风险分析时,可通过定性分析方法筛选出定性风险相对较高的部分进行定量风险分析,再依据 定量风险分析的结果制定基于风险的检验策略
4.3.2进行不同装置(单元或工段)定性风险对比时需要考虑装置(单元或工段)中的设备数量,只有设 备数量相近的装置(单元或工段)才能进行对比
失效可能性评估 5.1失效可能性的评估步骤 5.1.1根据被评估装置(单元或工段)的具体情况,分别对下列6个因子进行赋值或计算
GB/T26610.3一2014 a)设备因子(EF) b 损伤因子(DF); 检验因子(IF) c) d维护状态因子(MCF). 工艺因子(PF). e) f 机械设计因子(MDF 5.1.2将上述6个因子的值相加,计算失效可能性因子,按表1确定失效可能性等级(即图1风险矩阵 图的纵轴
表1失效可能性等级 失效可能性因子 失效可能性等级 0~15 6一25 2635 3650 51一75 5.2各因子的赋值或计算方法 5.2.1 设备因子(EF 根据被评估装置(单元或工段)中可能发生失效的设备总数对设备因子(EF)进行赋值,其最大值 为15: a)对完整的装置进行评估(可能发生失效设备数量大于150台),取EF=15; b 对装置中的某个单元进行评估(可能发生失效设备数量为20台150台),取EF=5; 对装置中的某个工段进行评估(可能发生失效设备数量小于20台设备),取EF=2
c 5.2.2损伤因子(DF) 判断装置(单元或工段)中是否存在发生某种损伤机理的可能性,并分别赋值 a)存在导致碳钢或低合金钢发生腐蚀开裂的可能性,取DF1=5 存在因低温,回火脆化或其他原因可能引起碳钢发生脆性断裂的可能性,取DF2=4: b 存在发生热疲劳或机械疲劳的可能性,取DF3 存在发生高温氢腐蚀的可能性,取DF4 d 存在由于工艺原因引发奥氏体不锈钢应力腐蚀开裂的可能性,取DF5=3; 存在发生局部腐蚀的可能性,取DF6- 存在发生全面腐蚀的可能性,取DF7=2; h)存在发生蠕变损伤的可能性,取DF8=l; 存在材料退化(如
相析出、渗碳、珠光体球化等)的可能性,取DF9=1 iD 存在已经识别的其他损伤机理的可能性,取DF10=1
j 将DF1~DF10相加,计算损伤因子(DF),其最大值为20.
5.2.3检验因子(IF 5.2.3.1根据容器检验历史对IF1进行赋值:
GB/T26610.3一2014 按要求进行定期检验,检验方案符合有关规范要求,有现场监控装置(如泄漏报警,视频监控 a 等),取IF1=一 一5 b仅进行过部分宏观(肉眼)检查和超声测厚等,取IF1=一2; 未进行过有效检验,取IF1=0.
c 5.2.3.2根据管道检验历史对IF2进行赋值: a)按要求进行定期检验,检验方案符合有关规范要求,有现场监控装置,取IF2=一5; b)仅进行过部分宏观肉眼)检查和超声测厚等,取IF2=一2; c)未进行过有效检验,取IF2=0
5.2.3.3根据检验方案对IF3进行赋值 a)已识别出设备的全部损伤机理,并全部制定了有针对性的检验方案,取IF3=一5; 仅对部分已识别的损伤机理制定了针对性的检验方案,取IF3=一2; b c)检验方案不满足上述各项要求,取IF3=0 5.2.3.4将IF1~IF3相加,计算检验因子(IF),其最小值为一15,但其绝对值不得超过损伤因子(DF). 5.2.4维护状态因子(CF) 5.2.4.1根据企业的管理水平对MCF1进行赋值 企业管理水平明显优于现行有关工业标准,规范.取MCFI=0; a 企业管理水平接近现行有关工业标准,规范,取MCF1=2; b e)企业管理水平明显低于现行有关工业标准,规范,取MCF1=5
5.2.4.2根据装置设计与制造水平对MCF2进行赋值: a)装置的设计与制造水平明显优于现行有关工业标准、规范,,同时业主提出了更严格的要求,取 MCF2=0; b) 装置的设计与制造水平接近现行有关工业标准,规范,取MCF2=2; c)装置的设计与制造水平明显低于现行有关工业标准、规范,取MCF2=5
5.2.4.3根据装置维修方案的有效性对MCF3进行赋值: a)装置的维修方案明显优于现行有关工业标准、规范,同时业主提出了更严格的要求,取 MCF3=0; 装置的维修方案接近现行有关工业标准、规范.取MCF3=2; b c)装置的维修方案水平明显低于现行有关工业标准,规范,取MCF3= s 5.2.4.4将MCF1MCF3相加,计算检验因子(MCF),其最大值为15
5.2.5工艺因子(Pp 5.2.5.1根据平均每年的计划或非计划停工次数对PF1进行赋值: 0次1次,取PF1=0:; b 次一4次,取PF1=1; 5次一8次,取PF1=3; 9次~12次,取PF1=4; 多于12次,取PF1=5
5.2.5.2根据工艺稳定性对PF2进行赋值 a 工艺非常稳定,不存在造成反应失控的可能性或其他不安全因素,取PF2=0, b)存在一定的操作异常的可能性,取PF2=1; c 存在导致设备损伤加速的可能性或其他不安全因素,取PF2=3 D 工艺本身非常不稳定,极易失控,取PF2=5
GB/T26610.3一2014 5.2.5.3根据保护装置可靠性,如是否会因为介质结垢或堵塞导致安全阀等失效,对PF3进行赋值 a)运行状况清洁,发生堵塞的可能极小,取PF3=0; b)有轻微结垢或堵塞的可能,取PF3=1 有明显结垢或堵塞的可能,取PF3=3; c d)在使用过程中,发现过保护装置损坏的情况,取PF3=5
5.2.5.4将PF1PF3相加,计算工艺因子(PF),其最大值为15
5.2.6机械设计因子(MDF) 5.2.6.1根据设备设计、制造、维护与现行标准、规范的符合性对MDF1进行赋值: 所有设备均按现行标准、规范进行设计与维护,取MDF1=0; a b 所有设备均按其建造时的有效标准,规范进行设计与维护,取MDF1=2; 设备未按现行标准、规范进行设计,取MDF1=5
c) 5.2.6.2根据工艺对MDF2进行赋值 工艺是通用的且符合现行标准与规范设计条件,取MDF2=0; a) 工艺独特或所有工艺设计条件均为极端条件,取MDF2=5
b 5.2.6.3将MDF1和MDF2相加,机械设计因子(MDF),其最大值为10
失效后果评估 失效后果的分类 6.1 失效后果分为 a)燃烧与爆炸后果; b)中毒后果
6.2失效后果评估原则 当某一介质泄漏仅产生燃烧与爆炸后果或中毒后果,仅需要针对实际存在的失效后果进行评估,作 为最终的失效后果等级(图1风险矩阵图的水平轴);当介质泄漏产生两种失效后果时,如果其中一种后 果带来的风险占明显主导地位时,只需确定主导风险的后果而不必考虑另一种后果,否则应对两种失效 后果分别进行评估,并以其中较严重的失效后果等级作为最终的失效后果等级 6.3燃烧与爆炸后果等级的评估方法 6.3.1评估步骤 6.3.1.1根据被评估装置(单元或工段)的具体情况,分别对下列6个因子进行赋值或计算 化学因子(cF) a b损伤量值因子(DQF); 状态因子(SF); c) D 自燃因子(AF); 压力因子(PRF); 安全防护因子(CRF) fD 将上述6个因子的值相加,计算燃烧与爆炸后果因子,按表2确定燃烧与爆炸后果等级 6.3.1.2
GB/T26610.3一2014 表2燃烧与爆炸后果等级 燃烧与爆炸后果因子 燃烧与爆炸后果等级 019 2034 3549 50~79 79 6.3.2各因子的赋值或计算方法 6.3.2.1化学因子(CF) 根据介质的可燃性,对可燃因子(FF)进行赋值,见表3
6.3.2.1.1 表3可燃因子FF 可 燃 性 可燃因子F 不会燃烧 需要加热才可点燃 在环境温度较高的情况下可以点燃 在各种环境温度下可以迅速点燃的液体和固体 在常温常压下迅速或完全汽化,或是可以迅速分散在空气中,可以迅速燃烧 6.3.2.1.2根据介质的反应危害,对反应因子RF)进行赋值,见表4
表4反应因子RF 反 害 应危 反应因子RF 通常情况下稳定,即使暴露于明火中也不反应,并且不与水反应 通常情况下稳定,但是可能在加热加压的条件下变得不稳定,或可以与水发生反应 在加热加压条件下发生剧烈化学变化,或与水剧烈反应,可能与水混合后发生爆炸 可以在某些条件下(如被加热或与水反应等)发生爆炸 可以在常温常压下迅速发生爆炸 6.3.2.1.3根据可燃因子和反应因子,按表5确定化学因子(CF)
若FF=0或RF=0,取CF=0
GB/T26610.3一2014 表5化学因子CF 反应因子RF 可燃因子F 12 15 10 12 15 20 12 15 18 25 25 13 15 20 6.3.2.2损伤量值因子(pop) 根据在单一失效事件中可能泄漏的可燃介质最大存量,对损伤量值因子(DQF)进行赋值,见表6
表6损伤量值因子DQF 损伤量值因子DQF 被泄放的介质量/kg <450 15 450900 20 9014500 25 450113600 28 136o136300 31 34 36301一91000 91001318000 37 3180o1一454000 39 54001908000 4! 9080014540000 45 50 >4540000 6.3.2.3状态因子(SF) 根据介质标准大气压下的沸点温度,对状态因子(SF)进行赋值,见表7
表7状态因子sF 沸腾温度/C 状态因子SF -73 一73一38 39121 122~204 >204
GB/T26610.3一2014 6.3.2.4自燃因子(AF) 若介质的工作温度低于其自燃温度,取AF=一10;否则根据标准大气压下介质的沸点温度对自燃 因子(AF)进行赋值,见表8
表8自燃因子AF 沸点温度/t 自燃因子AF -18 -18150 >150 13 压力因子(PRF) 6.3.2.5 若设备中的介质为气体且处于大于1MPa压力下或设备中的介质为液体,取PRF=一10,否则 PRF=一15
6.3.2.6安全防护因子(CRF) 根据以下条件对CRF1CRF10进行赋值 如果按相关设计规范设置了气体泄漏探测报警装置,取CRF1=一1,否则CRF1=0; a) 如果设备在惰性气氛内正常运行,取cRF2=-1;否则取CRF2=0; b 如果消防系统在重大事故中是安全的(如消防水系统在爆炸后保持完整)取cRr3= 一1,否 则CRF3=0; d)如果该区域的设备隔离能力可远程控制,取CRF4=一1,否则CRF4=0; 如果在最关键设备(一般为工作压力最高的设备周围有防爆墙,取CRF5=一1,否则 e CRF5=0:; 如果存在能在失效事件发生后5min内处理不少于75%存量介质的应急系统,且其可靠性达 90%及以上,取CRF6=一1,否则CRF6=0, 如果在结构和电缆上均已敷设了耐火材料且耐火等级符合相关技术规范,取CRF7=-l;如 果仅在结构或电缆上敷设了耐火材料,取CRF7=0.95,否则CRF7=0; 如果消防水持续供给能力超过4h,取CRF8=一1,否则CRF8=0, h 如果安装有固定式泡沫消防系统,取CRF9=一1,否则CRF9=0; iD 如果装置的所有区域设置消防水监控器,取CRF10=一1,否则CRF10=0. 将CRF1CRF10相加,计算安全防护因子(CRF). 6.4中毒后果等级的评估方法 6.4.1评估原则 在评估中毒后果时,仅考虑瞬时剧烈效应引起的后果,而不考虑较缓慢扩散可能引起的慢性中毒
6.4.2评估步骤 根据被评估装置(单元或工段)的具体情况.分别对以下4个因子进行赋值或计算 6.4.2.1 中毒量值因子TQF);
GB/T26610.3一2014 b扩散因子(DI); e安全防护因子(CRF); 人口因子(PPF d 6.4.2.2将上述4个因子的值相加,计算中毒后果因子,按表9确定中毒后果等级
表9中毒后果等级 中赤后果因子 中毒后果等级 10 1019 2029 3039 39 6.4.3各因子的赋值或计算方法 6.43.1中毒量值因子(TQFP) 6.4.3.1.1根据某单一泄漏事件中可能损失的有毒介质的最大存量对TQF1进行赋值,见表10. 表10TQF1 被泄放的介质量/lkg TQF1 <450 15 450一4500 20 27 450145000 35 >45000 6.4.3.1.2 根据介质对健康的危害,对ToF2进行献值,见表1m. 表11TQP2 介质对健康的危害 TQF2 暴露可能导致不适,但是仅可能有轻微持续性伤害 -20 高浓度或持续性暴露可能导致暂时失去行为能力或可能造成持续性伤害 10 短时间的暴露可能导致严重的暂时性或持续性伤害 20 短时间的暴露可能会导致死亡或重大持续性伤害 6.4.3.1.3将TQF1和TQF2相加,计算中毒量值因子(TQF)
6.4.3.2扩散因子(DIF) 根据标准大气压下介质的沸点温度,对扩散因子(DIF)进行赋值,见表12 10
GB/T26610.3一2014 表12扩散因子DIF 扩散因子DIF 标准沸点/C 1~29 0.5 3065 0,3 66~93 0.1 94~150 0.05 >150 0.03 6.4.3.3安全防护因子(CRF 6.4.3.2.1如果被评估装置安装了探测器,可有效及时探测出毒性介质泄漏,取CRF1=一1,否则 CRF1=0. 6.4.3.2.2根据以下条件对CRF2进行赋值 如果盛装毒性介质的主要容器可以根据有毒介质探测仪的泄漏报警而自动启动隔离,取 a CRF2=一25; b)如隔离为远程手工执行,取CRF2=一5 e)如隔离为手工执行,取CRF2=一1; d 其他情况取CRF2=0
如已安装的水幕或其他减缓系统被证明能有效减缓90%以上介质泄漏,取CRF3=一5,否 6.4.3.2.3 则CRF3=0
6.4.3.2.4将CRF1~CRF3相加,计算安全防护因子(CRF). 6.4.3.4人口因子(PPr) 根据距泄漏点400m半径范围内的日间平均人数,对人口因子(PPF)进行赋值,见表13
表13人口因子PPr 人口因子PPp 半径范围内的日间平均人数/人 400m <10 10100 1011000 15 1001l0000 20 风险等级的确定 当被评估装置(单元或工段)的失效可能性等级和失效后果等级确定后,将其组合在一个5×5的风 险矩阵图(见图1)中确定被评估装置的风险级别
GB/T26610.3一2014 图例说明 高风险 中高风险 事 中风险 低风险 图1风险矩阵
承压设备系统基于风险的检验实施导则第3部分:风险的定性分析方法GB/T26610.3-2014
承压设备是在工业生产中广泛应用的一种设备,其安全性关系到生产过程中的人员安全和生产效率。为了确保承压设备的安全可靠,需要对其进行定期检验。而在检验过程中,风险的存在可能会给检验带来不确定性和隐患。因此,必须要有合理的风险分析方法和管理措施。
GB/T26610.3-2014《承压设备系统基于风险的检验实施导则第3部分:风险的定性分析方法》就是一项非常重要的标准,它规定了承压设备检验实施过程中的风险分析方法和管理要求。
该标准中的风险分析方法主要包括以下内容:
1. 风险识别
在检验前,需要对承压设备系统进行全面地了解和排查,并确定其中可能存在的风险因素。这一过程是为后续的风险评估和控制提供基础。
2. 风险评估
风险评估是根据风险识别结果,对发生概率和影响程度进行定性分析和量化评价。这一过程可以帮助检验人员更好地了解风险的严重性和可能造成的影响,从而采取相应的控制措施。
3. 风险控制
在风险评估的基础上,需要制订相应的风险控制措施并加以实施。通过控制风险的发生和扩大,有效保障承压设备的安全运行。
总之,GB/T26610.3-2014所规定的风险分析方法是承压设备检验过程中必不可少的一个环节。它可以帮助检验人员更好地了解和掌握风险管理的方法和技巧,从而提高承压设备的安全性和可靠性。