GB/T34370.5-2017
游乐设施无损检测第5部分:超声检测
Nondestructivetestingofamusementequipments—Part5:Ultrasonictesting
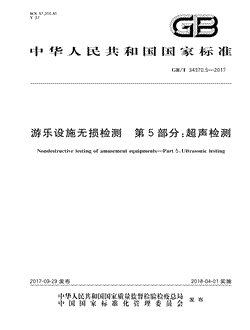
- 中国标准分类号(CCS)Y57
- 国际标准分类号(ICS)97.200.40
- 实施日期2018-04-01
- 文件格式PDF
- 文本页数89页
- 文件大小7.88M
以图片形式预览游乐设施无损检测第5部分:超声检测
游乐设施无损检测第5部分:超声检测
国家标准 GB/34370.5一2017 游乐设施无损检测第5部分;超声检测 Nondestruetivetestingofamusementequipents一Part5:UItrasonietesting 2017-09-29发布 2018-04-01实施 国家质量监督检验检疫总局 发布 国家标准化管理委员会国家标准
GB/T34370.5一2017 次 目 前言 范围 2 规范性引用文件 3 术语和定义 方法概要 安全要求 人员要求 检测设备 检测工艺规程 检测前的准备 1C 原材料、零部件的超声检测和质量分级 游乐设施焊接接头超声检测 12在用游乐设施超声检测 13脉冲反射式超声测厚 45 超声检测报告 14 16 附录A(规范性附录)双晶直探头性能要求 47 附录B(规范性附录游乐设施用钢板横波检测 19 附录C规范性附录游乐设施用钢锻件横波检测 51 附录D(资料性附录)工件底波调整灵敏度的方法 53 附录E规范性附录)游乐设施用用钢锻件超声斜探头检测 54 附录F规范性附录)游乐设施用无缝钢管轴向横波检测 56 附录G(规范性附录铸铁部件超声检测方法和质量分级 58 附录H(规范性附录奥氏体不锈钢对接焊接接头超声检测 64 附录1(规范性附录声能传输损耗差的测定 68 附录J(资料性附录)回波动态波形 70 73 附录K规范性附录)相控阵超声波检测方法 附录L规范性附录)一6dB法测定缺陷自身高度 82 附录M规范性附录典型的测量用校准试块 84
GB;/T34370.5一2017 前 言 GB/T34370《游乐设施无损检测》分为11个部分 第1部分:总则; 第2部分:目测检测; 第3部分;磁粉检测 第4部分;渗透检测; 第5部分;超声检测 第6部分:射线检测 第7部分;涡流检测 第8部分声发射检测 第9部分:漏磁检测; -第10部分;磁记忆检测; 第11部分;超声导波检测
本部分为GB/T34370的第5部分 本部分按照GB/T1.12009给出的规则起草
本部分由全国索道与游乐设施标准化技术委员会(sAc/TC250)提出并归口
本部分起草单位;特种设备检测研究院、河北省特种设备监督检验院,山东科捷工程检测有限 公司、天津市特种设备监督检验技术研究院、上海希都游乐设备制造厂、山东瑞祥模具有限公司、北京实 宝来游乐设备有限公司
本部分主要起草人;胡斌、沈功田,张君娇、,刘文贞,赵欣、张劲松、刘佳璐、吴占稳、梁玉梅、刘宏臣、 周晓君、沈永娜、万海涛、张庆柱、马建民
GB;/T34370.5一2017 游乐设施无损检测第5部分:超声检测 范围 GB/T34370的本部分规定了游乐设施的超声检测方法及质量分级和超声测厚方法要求
本部分适用于游乐设施用金属原材料、零部件和焊接接头的超声检测,也适用于在用游乐设施金属 材料零部件和焊接接头的超声检测
规范性引用文件 下列文件对于本文件的应用是必不可少的
凡是注日期的引用文件,仅注日期的版本适用于本文 件
凡是不注日期的引用文件,其最新版本(包括所有的修改单)适用于本文件 GB/T7233.1铸钢件超声检测第1部分;一般用途铸钢件 GB/Tl1344无损检测接触式脉冲回波法测厚方法 GB 12604.1无损检测术语超声检测 GB 20306游乐设施术语 GB 20737 无损检测通用术语和定义 GB 27664.1无损检测超声检测设备的性能与检验第1部分:仪器 GB 761.2无损检渊超声检测设备的性能与检验第2部分;探头 GB 29302无损检测仪器相控阵超声检测系统的性能与检验 GB 34370.1游乐设施无损检测第1部分:总则 8428无损检测超声试块通用规范 JB/T9214 无损检测A型脉冲反射式超声检测系统工作性能测试方法 JB/T10062超声探伤用探头性能测试方法 JB/T11604 无损检测仪器超声波测厚仪 JB/T11731无损检测超声相控阵探头通用技术条件 JB/T11779无损检测仪器相控阵超声检测仪技术条件 术语和定义 GB/T12604.1,GB/T20306,GB/T20737和GB/T34370.1界定的以及下列术语和定义适用于本 文件
3.1 由缺陷引起的底波降低量BG/BF(dB) lossofbackrefleetioncausedbyflawsBG/BF(aB 在靠近缺陷处的无缺陷完好区域内第一次底波幅度BG与缺陷区域内的第一次底波幅度BF之比 用声压级(dB)值来表示
3.2 基准灵敏度和扫查灵敏度basieandscanningsensitivities 基准灵敏度一般指记录灵敏度,它通常用于缺陷的定量和缺陷的分级
扫查灵敏度则主要指实际
GB/T34370.5一2017 检测灵敏度
为了不漏掉记录缺陷或某些特定的缺陷,确保游乐设施的安全,实际检测时通常采用较高 的检测灵敏度进行扫查
原则上扫查灵敏度不应低于基准灵敏度
3.3 聚焦斜探头focusingangleeamprobe 采用透镜式、发射式和曲面晶片等聚焦方法,使超声波束会聚以提高检测灵敏度的超声斜探头
3.4 端点衍射tipdifraetion 超声波在传播过程中,当波阵面通过缺陷时,波阵面会绕缺陷边缘弯曲,并呈圆心展衍的现象
3.5 端点最大反射波maximumtip reflecedwave 当缺陷的端部回波的幅度达到最大时也即缺陷端部回波峰值开始降落前瞬时的幅度位置),该回 波称为缺陷端点最大反射波
3.6 回波动态波型echdynamicpatterns 动态波型是探头移动距离与相应缺陷反射体回波波幅变化的包络线
3.7 工件厚度 basematerialnominalthicknesses 对于平板对接接头,焊缝两侧母材厚度相等时,工件厚度为母材厚度;焊缝两侧母材厚度不 a 等时,工件厚度!为薄侧母材公称厚度; 对于T型焊接接头,工件厚度去为腹板公称厚度 b 3.8 管子直径tuhediameter D 管子的外径
3.9 轴直径axisdiameter 实心轴的轴直径指轴外径,有台阶时,指工作面的直径
空心轴的直径包括内外径,外径D.,内径D
有台阶时,按照工作面的直径确定内外径
3.10 缺陷密集区aeusteroflaws 在荧光屎扫描线相当于50mm声程范围内同时有5个或5个以上的缺陷反射信号;或是在 50mm×50mm的检测面上发现在同一深度范围内有5个或5个以上的缺陷反射信号
其反射波幅 均大于某一特定当量缺陷基准反射波幅
3.11 缺陷自身高度lawheight 缺陷在壁厚方向的尺寸
3.12 缺陷评定区lawevalwationzone 在质量分级评定时,为评价缺陷数量和密集程度而设置的一定尺寸区域
可以是正方形或长方形 缺陷评定区应选在缺陷最严重的部位
GB;/T34370.5一2017 3.13 检测距离inspectiondistanee 超声波直探头检测时,检测距离是指一次声程
方法概要 4.1超声波是频率高于20kHz的机械波,工业无损检测中超声检测常用的频率为0.5MHHz5MHz 4.2超声波在材料中以一定的速度和方向传播,遇到声阻抗不同的异质界面如缺陷或被测物件的底 面等)就会产生反射或衍射
4.3反射式超声检测就是利用这种反射现象来进行缺陷检测或厚度测量,图la)c)分别是为A型脉 冲斜人射超声检测、A型脉冲直人射超声检测、A型脉冲反射式超声测厚示意图,图2为相控阵超声检 测示意图
计算 T始波 B底波 放大器 电路 电路 [缺陷波 探头 内 指示 工件 超声波传播时间 B B2 缺陷 B3 底面 探头 被检工件 .L A型脉冲直入射超声检测 A型脉冲斜入射超声检测 A型脉冲反射式超声测厚 a b 图1A型脉冲反射式超声检测示意图 声束控制 聚焦 a 常规超声检测示意图相控阵检测示意图 相控阵B扫图 检测效果对比图 d 图2相控阵超声检测示意图
GB/T34370.5一2017 5 安全要求 5.1本章没有列出进行检测时所有的安全要求,使用本部分的用户应在检测前建立安全准则 5.2检测过程中的安全要求至少包括 检测人员应遵守被检件现场的安全要求,根据检测地点的要求穿戴防护工作服和佩戴有关防 a 护设备; 检测时被检件的壁温应在稠合剂正常工作的温度区间 b 应注意超声检测时,耦合剂会引起绝缘不良,电器短路 c d 游乐设施运行后进行检测,应注意被检件的温度状态,以免烫伤
人员要求 6 从事游乐设施超声检测工作的人员,应符合GB/T34370.1的有关规定 检测设备 7.1基本要求 7.1.1超声检测设备应至少包括检测仪器和探头
7.1.2超声检测设备均应具有产品质量合格证或合格的证明文件
7.2检测仪器 7.2.1A型脉冲反射式超声检测仪的基本要求 A型脉冲反射式超声检测仪,其发射脉冲重复频率实测值与标称值误差不大于10%,发射脉 a 冲电压实测值与标称值误差不大于20%,发射脉冲宽度实测值与标称值误差不大于10%,发 射脉冲上升时间不大于25ns A型脉冲反射式超声检测仪,其工作频率按一3dB测量至少应包括0.5MHz10MHa的范 b 围,每个频带上、下限实测值与标称值误差不大于20%; A型脉冲反射式超声检测仪应具有80dB以上的连续可调衰减或增益,最小步进级每档不大 于2dB,其精度为任意连续20dB的累积误差不大于1.7dB,任意连续60dB的累积误差不大 于3dB d 各项性能指标按GB/T27664.1的要求进行测试
7.2.2超声波测厚仪的基本要求 超声测厚仪用于壁厚小于10mm的厚度测定时,最大允许示值误差为士0.1mm;用于壁厚大 a 于10mm的厚度测定时,最大允许示值误差为士(0.1十H/100)mm,其中H为标准厚度块 的标称值; 超声测厚仪的示值稳定度不大于0.2mm b 各项性能指标按JB/T11604的要求进行测试
c 7.2.3相控阵超声检测仪的基本要求 相控阵超声检测仪,其发射脉冲重复频率实测值与标称值误差不大于10%,发射脉冲电压实 测值与标称值误差不大于20%,发射脉冲宽度实测值与标称值误差不大于10%,发射脉冲上
GB;/T34370.5一2017 升时间应小于可能使用的最高探头标称频率周期时间的0.25倍; b 相控阵超声检测仪,其工作频率按一3dB测量至少应包括1MHz10MHz的范围,每个频带 上、下限实测值与标称值误差不大于20%; 各项性能指标按JB/T11779的要求进行测试
7.3探头 7.3.1单换能器或双换能器探头,包含聚焦或非聚焦式的接触式或液浸式探头
圆形晶片直径一般不 应大于40mm,方形晶片任一边长一般不应大于40mm,其性能指标按GB/T27664.2的要求进行 测试 7.3.2超声相控阵探头的中心频率一般在0.5MHz15MHz范围内,阵元数应不少于8个,其性能指 标按JB/Tl11731的要求进行测试 7.4超声检测仪器和探头的系统性能 7.4.1A型脉冲反射式超声检测仪和探头的系统性能要求: 水平线性不大于1%,垂直线性不大于5%; a 仪器和探头的组合颗事与公称颗率谈差不应大于土10% b 在基准灵敏度下,对于标称频率为5MHHz的直探头,盲区不大于10mm;对于标称频率为 c 2.5MHz的直探头,盲区不大于15mm: 仪器直探头组合的灵敏度余量应不小于32dB,仪器斜探头组合的灵敏度余量应不小于 42dB 仪器直探头组合的远场分辨力应不小于20dB,仪器斜探头组合的远场分辨力应不小于 12dB 在达到所探工件的最大检测声程时,其有效灵敏度余量应不小于10dB; 各项性能指标按JB/T10062和JB/T9214的要求进行测试
g 7.4.2超声测厚仪和探头的系统性能要求 仪器和探头的组合频率与公称频率误差不应大于士10%; aa 各项性能指标按JB/T10062的要求进行测试
b 7.4.3相控阵超声检测仪和探头的系统性能要求 相控阵超声检测系统性能包括;测定声束轮廓、声束偏转范围、阵元有效性、软件计算功能、接 a 收器增益线性; 各项性能指标按GB/T29302的要求进行测试
b 7.4.4发生以下情况时应测定检测仪器和探头的组合性能 新购置的超声检测仪器和(或)探头; a b 检测仪器和探头在维修或更换主要部件后; 检测人员有怀疑时
c 7.5试块 7.5.1 型脉冲反射式超声检测试块 1 7.5.1.1标准试块 7.5.1.1.1标准试块指具有规定的化学成分,表面粗糙度、热处理及几何形状的材料块,用于评定和校 准超声检测设备,即用于仪器、探头,系统性能校准的试块
7.5.1.1.2标准试块的制造应满足JB/T8428的要求,制造商应提供产品质量合格证
GB/T34370.5一2017 7.5.1.2对比试块 7.5.1.2.1对比试块是指与被检件或材料化学成分相似,含有意义明确参考反射体的试块,用以调节超 声检测设备的幅度和声程,以将所检出的缺陷信号与已知反射体所产生的信号相比较,即用于缺陷评定 的试块
7.5.1.2.2对比试块的尺寸精度在本部分有明确要求时应提供相应的证明文件,无明确要求时参照 JB/T8428的规定
7.5.1.3模拟试块 7.5.1.3.1模拟试块是指用于验证检测工艺和无损检测人员的检测能力、评价和验证仪器探头系统的 检测能力的试块
77.5.1.3.2模拟试块一般含模拟缺陷或真实缺陷的试块,可以是模拟工件中实际缺陷而制作的样件,或 者是在以往检测中所发现含自然缺陷的样件
7.5.2超声测厚试块 接触式超声脉冲回波测厚方法采用阶梯试块进行测厚校准
7.5.2.1 7.5.2.2校准试块应符合GB/T11344的规定
7.5.3相控阵超声检测试块 相控阵超声检测试块分为标准试块、对比试块和模拟试块
7.6超声检测设备和器材的校准、核查、期间核查和检查的要求 7.6.1 一般要求 7.6.1.1校准、核查和期间核查应在标准试块上进行
7.6.1.2校准、核查和期间核查时应使探头主声束垂直对准反射体的反射面,以获得稳定的和最大的反 射信号
7.6.2校准、核查、期间核查或检查 7.6.2.1每年至少对超声检测仪器进行一次校准,校准要求应满足超声波检测仪校准规程的规定
7.6.2.2每年至少对试块的表面腐蚀和机械损伤进行一次核查
7.6.2.3每6个月至少对超声检测仪器和探头的系统性能进行一次期间核查并记录,测试要求应满足 7.4的规定
7.6.2.4每次检测前应检查仪器设备器材外观、线缆连接和开机信号显示等情况是否正常
7.6.2.5校准、期间核查和检查时,任何影响仪器线性的控制器(如抑制或滤波开关等)都应放在“关”的 位置或处于最低水平上
7.7新购探头、检测过程的复核 7.7.1新购探头测定 7.7.1.1新购探头须有探头性能参数说明书,新探头使用前应进行前沿距离、K值,主声束偏离,灵敏 度余量和分辨力等主要参数的测定
7.7.1.2测定方法应按JB/T10062的有关规定进行测定,并满足其要求
GB;/T34370.5一2017 7.7.2检测前仪器和探头系统测定 7.7.2.1使用仪器-斜探头系统,检测前应测定前沿距离、K值和主声束偏离,调节或复核扫描量程和扫 查灵敏度
每次检测前应设定时基线和灵敏度,并参考温度的影响
时基线和灵敏度设定时温度与检 测工件的温度差不超过15C
使用仪器-直探头系统,检测前应测定始脉冲宽座、灵敏度余量和分辨力,调节或复核扫描量 7.7.2.2 程和扫查灵敏度
7.7.3仪器和探头系统的复核 7.7.3.1检测过程中如遇到以下情况应进行仪器和探头系统的复核 探头、合剂和仪器调节发生改变时 a b) 怀疑扫描量程或扫查灵敏度有变化时 连续工作4h以上时; c 工作结束时
d 7.7.3.2如果任意一点在扫描线上的偏移量超过扫描线该点读数的10%或全扫描量程的5%,则扫描 量程应重新调整,并对上一次复核以来所有的检测部位进行复检
7.7.3.3复核时,在检测范围内如发现扫查灵敏度或距离-波幅曲线上任一深度人工反射体回波幅度下 降2dlB,则应对上一次复核以来所有的检测部位进行复检;如上升2dlB,则应对所有的记录信号进行重 新评定
8 检测工艺规程 8.1通用检测工艺规程 从事游乐设施超声检测的单位应按GB/T34370.1和本部分的要求制定通用检测工艺规程,其内 容至少应包括如下要素: 文件编号; a 适用范围 b 引用标准、法规 c d 检测人员资格; 检测仪器设备;耦合剂、探头、信号线、探伤仪、检测数据采集和分析软件等 e f 被检件的信息:几何形状与尺寸、材质、设计与运行参数; 检测覆盖范围及探头安装部位; g h 被检件表面状态及检测探头布置和检测方式 检测时机 灵敏度测量、距离-波幅曲线绘制, 检测过程和数据分析解释; k 检测结果的评定; m检测记录、报告和资料存档 n)编制(级别,审核(级别)和批准人员签字及日期
8.2检测工艺卡 8.2.1对于每个被检件,根据使用的仪器和现场实际情况,按照GB/T34370.1、本文件和通用检测工艺 规程编制超声检测工艺卡,确定检测的部位和表面条件
对每个被检件进行测绘,画出被检件结构示意
GB/T34370.5一2017 图和探头的覆盖区域
8.2.2检测面的确定,应保证工件被检部分均能得到充分检查 8.2.3游乐设施制造安装和在用过程的超声检测中,检测时机及抽检率的选择等应按法规、产品标准 及有关技术文件的要求和原则进行
8.2.4检测工艺卡内容应至少应包括 检测工艺卡编号; a b 检测执行的标准和质量等级要求 c 被检测工件的信息:名称、编号、材质、规格尺寸,热处理状态、焊接型式等; d 检测设备和器材;检测仪器的名称,规格型号、编号,探头型号和编号,标准试块等 灵敏度设置、仪器调试、参数设置; f 检测时机; 检测区域和表面要求; g h 检测部位示意图; 检测比例; 检测环境要求; 检测方法; k D 扫查方式 m 朋合方式 编制(级别和审核(级别人员签字及日期
n 检测前的准备 9.1资料审查 资料审查应包括下列内容 被检设备制造文件资料;对在制设备应包括设计图样和设计说明文件,对于在用设备应包括质 a 量证明文件、竣工图等; b)被检设备运行记录资料;开停车情况、使用环境、使用条件、载荷变化情况以及运行中出现的异 常情况等; 检验资料:历次检验检测报告 c d 其他资料;维护保养、修理和改造的文件资料等
9.2现场勘察 9.2.1对于在用游乐设施,在实施检测前,应对被检设备现场进行勘察,确定实施检测的辅助条件,找 出所有可能影响检测的因素,在检测时应尽可能避免这些因素的干扰
9.2.2被检件的表面质量应经外观检查合格
所有影响超声检测的锈蚀、飞溅和污物等都应予以清 除,其表面粗糙度应符合检测要求
表面的不规则状态不应影响检测结果的正确性和完整性,否则应做 适当的处理
9.3扫查覆盖率的要求 g.3.1应确保检测时超声声束能扫查到工件的整个被检区域 9.3.2探头的每次扫查覆盖率应大于探头直径的15%或优先满足相应章节的检测覆盖要求
GB;/T34370.5一2017 g.4探头的移动速度的要求 g.4.1探头的扫查速度不应超过1501 mm/s
9.4.2当采用自动报警装置扫查时,扫查速度应通过对比试验进行确定
9.5扫查灵敏度的要求 g.5.1扫查灵敏度通常不应低于基准灵敏度且应符合相关章节的规定
9.5.2 每次检测前,时基线,灵敏度设定温度与检测工件温度差不超过15C
9.6耦合剂 9.6.1应采用透声性好,且不损伤检测表面的合剂,如机油,浆糊,甘油和水等
9.6.2 稠合剂的选取应考虑使用条件和环境要求
9.7灵敏度补偿 稠合补偿
在检测和缺陷定量时,应对由表面粗糙度引起的稠合损失进行补偿
9.7.1 在检测和缺陷定量时,应对材质衰减引起的检测灵敏度下降和缺陷定量误差进行 9.7.2 衰减补偿
补偿
曲面补偿
对探测面是曲面的工件,应采用曲率半径与工件相同或相近的参考试块,通过对比 9.7.3 试验进行曲率补偿
9.8检测工艺卡的编制 9.8.1应确定超声检测时机及检测比例的选择等符合相关法规、标准及有关技术文件的规定
检测工艺卡的内容按8.2执行
9.8.2 10原材料、零部件的超声检测和质量分级 0.1游乐设施用板材超声检测和质量分级 0.1.1板材超声检测适用范围 10.1.1.1板材超声检测方法适用于板厚为6mm一250mm的碳素钢、低合金钢游乐设施用板材及板 材制成的零部件的A型脉冲超声检测和质量分级
10.1.1.2铝及铝合金板材的A型脉冲超声检测方法和质量分级参照10.1.1.1执行
10.1.1.3奥氏体不锈钢板材以及奥氏体-铁素体双相不锈钢板材的A型脉冲超声检测方法和质量分级 也可参照10.1.1.1执行
10.1.2检测原则 0.1.2.1板材一般采用直探头进行检测
10.1.2.2在检测过程中对缺陷有疑问或双方技术协议中有规定时,可采用斜探头进行检测
10.1.2.3可选板材的任一轧制表面进行检测
若检测人员认为需要或技术条件有要求时,也可选择板 材的上、下两轧制表面分布进行检测
10.1.3探头选用 10.1.3.1探头的选用应按表1的规定进行
GB/T34370.5一2017 表1游乐设施用板材超声检测探头选用 公称频率/NMH 探头晶片尺寸/mm 板厚/mm 采用探头 620 双晶直探头 圆形品片直径中10一体30 方形晶片边长10~30 >20250 单晶直探头 10.1.3.2当采用液浸法检测板厚小于或等于20mm的板材时,也可选用单直探头进行检测
0.1.3.3双晶直探头性能应符合附录A的要求
10.1.3.4斜探头的选用应按附录B的规定进行
0.1.4试块 0.1.4.1用双晶直探头检测壁厚不大于20mm的钢板时,应采用CBI标准试块如图3所示 10.1.4.2用单直探头检测板厚大于20mm的钢板时,应采用CBl标准试块,且应符合图4和表2的 规定
试块厚度应与被检钢板厚度相近
单位为毫米 全部 8×40 注:尺寸误差<0.05mm.
图3CBI标准试块 0
GB;/T34370.5一2017 单位为毫米 100 团 5 0.1 图4 CBI标准试块 表2CBI标准试块 单位为毫米 试块编号 被检钢板厚度 检测面到平底孔的距离s 试块厚度T CBI-1 2040 20 CBI -2 30 >40 4060 CBI-3 >60100 >65 50 CB-4 >100160 90 >l10 CB-5 >l60200 140 >170 >200250 CBl-6 190 >220 10.1.5 灵敏度的确定 10.1.5.1板厚不大于20mm时,用CBI试块将工件等厚部位第一次底波高度调整到满刻度的50%, 再提高10dB作为基准灵敏度
10.1.5.2板厚大于20mm时,应将CB试块5mm平底孔第一次反射波高调整到满刻度的50%作 为基准灵敏度
10.1.5.3板厚大于探头的3倍近场区时,也可取钢板无缺陷完好部位的第一次底波来校准灵敏度,按 照底波计算法达到5mm平底孔的灵敏度
10.1.6检测 10.1.6.1检测面可选钢板的任一轧制表面进行检测
若检测人员认为需要或设计上有要求时,也可选 钢板的上、下两轧制表面分别进行检测
0.1.6.2稠合方式可采用直接接触法或液浸法
0.1.6.3扫查方式 在板材边缘或剖口预定线两侧范围内应作100%扫查,扫查区域宽度在板厚小于等于60n a mm 1
GB/T34370.5一2017 时为50mm,板厚大于6o 小于100mm 时为75mm,板厚大于或等于100 mm时为 mm 100t mm; b 在板材中部区域,探头沿垂直于板材压延方向,间距不大于50mm的平行线进行扫查,或探头 沿垂直和平行板材压延方向且间距不大于100mm格子线进行扫查,扫查示意图见图5 根据合同、技术协议书或图样的要求,也可采用其他形式的扫查 c d 双晶直探头扫查时,探头的移动方向应与探头的隔声层相垂直
锅板中部扫查 边缘100%扫查区域 剖口预定线 边缘100%扫查区城 100 锅板中部担查 剂口预定线 图5探头扫查示意图 10.1.7缺陷的测定与记录 在检测过程中,发现下列3种情况之一者即判定为缺陷并记录 10.1.7.1 缺陷第一次反射波(F1)波高大于或等于满刻度的50%,即FI多50%者; a b 当底面第一次反射被(B)被高未达到满刻度,此时,缺陷第一次反射波(H)波高与底面第 次反射波(B1)波高之比大于或等于50%,即B1<100%,而F1/B1>50%者; c 底面第一次反射波(B1)波高低于满刻度的50%,即B1<50%者
缺陷的边界范围或指示长度的测定方法 10.1.7.2 a 检出缺陷后,应在它的周围继续进行检测,以确定缺陷的延伸
b)用双晶直探头确定缺陷的边界范围或指示长度时,探头的移动方向应与探头的隔声层相垂直, 并使缺陷波下降到基准灵敏度条件下荧光屏满刻度的25%或使缺陷第一次反射波高与底面 第一次反射波高之比为50%
此时,探头中心的移动距离即为缺陷的指示长度,探头中心点 即为缺陷的边界点
两种方法测得的结果以较严重者为准
用单直探头确定缺陷的边界范围或指示长度时,移动探头使缺陷波第一次反射波高下降到基 准灵敏度条件下荧光屏满刻度的25%或使缺陷第一次反射波与底面第一次反射波高之比为 50%
此时,探头中心的移动距离即为缺陷的指示长度,探头中心即为缺陷的边界点
两种方 法测得的结果以较严重者为准
确定10.1.7.1c)中缺陷的边界范围或指示长度时,移动探头(单直探头或双直探头)使底面第 次反射波升高到荧光屏满刻度的50%
此时探头中心移动距离即为缺陷的指示长度,探头 中心点即为缺陷的边界点
12
GB;/T34370.5一2017 当板厚较薄,确需采用第二次缺陷波和第二次底波来评定缺陷时,检测灵敏度应以相应的第二 次反射波来校准
10.1.8缺陷的评定方法 10.1.8.1缺陷指示长度的评定规则: 单个缺陷按其指示的最大长度作为该缺陷的指示长度 a b)若单个缺陷的指示长度小于40mm时,可不作记录
10.1.8.2 单个缺陷指示面积的评定规则 一个缺陷按其指示的面积作为该缺陷的单个指示面积 a b)多个缺陷其相邻间距小于100mm或间距小于相邻小缺陷的指示长度(取其较大值)时,以各 块缺陷面积之和作为单个缺陷指示面积
10.1.9质量分级 钢板质量分级见表3
10.1.9.1 10.1.9.2在坡口预定线两侧各50mm(板厚大于100mm时,以板厚的一半为准)内,缺陷的指示长度 大于或等于50mm时,则应评为I级
0.1.9.3在检测过程中,检测人员如确认钢板中有裂纹等危害性缺陷存在时,应评为皿级
表3钢板质量分级 在任一1mx1m检测面积内缺陷最大允许个数 最大允许单个缺陷指示面积s(mm) 等级 单个缺陷指示面积或 或当量平底孔直径Dmm) 最大允许个数 当量平底孔直径评定范围 双晶直探头检测时;s<5o 双晶直探头检测时;20
GB;/T34370.5一2017 单位为毫米 全部 2 L0.05 图7CsI标准试块 表5csI标准试块尺寸 单位为毫米 试块序号 CSI CSI-2 CSI-3 CSI-4 50 100 150 200 50 60 80 80 单位为毫米 200 必 25 3 品 250 上正上 图8CS标准试块 15
GB/T34370.5一2017 表6cs标准试块尺寸 单位为毫米 检测距离L 试块序号 孔径 csI-1 2 CsI-" 小3 10 15 20 25 45 30 35 40 CSI-3 4 CS-4 6 10.2.5灵敏度的确定 10.2.5.1 基准灵敏度的确定 a 单直探头基准灵敏度的确定:当被检部位的声程大于或等于探头的3倍近场区长度,且检测面 与底面平行时,原则上可采用底波法确定基准灵敏度
对由于几何形状所限,不能获得底波或 声程小于探头的3倍近场区时,可直接采用试块法确定基准灵敏度
b 双晶直探头基准灵敏度的确定;使用相应的试块,依次测试一组不同检测距离的2平底孔试 块(至少3个)
调节衰减器,作出双晶直探头的距离-波幅曲线,并以此作为基准灵敏度 10.2.5.2扫查灵敏度一般不应低于最大检测声程处的p2mm平底孔当量直径 10.2.6检测 10.2.6.1合方式一般可采用直接接触法
10.2.6.2灵敏度补偿;检测时应根据实际情况进行耦合补偿,衰减补偿和曲面补偿 10.2.6.3扫查方式: a 径向检测应尽可能选择晶片尺寸较小的探头; b 应按螺旋线或沿圆周进行扫查,行程应有重叠,扫查面应能包括整个圆柱表面; c 轴向检测应从棒材的两端面进行扫查,尽可能避免边缘效应对检测结果的影响
10.2.7缺陷的测定和记录 10.2.7.1缺陷的判定以反射波幅值为判定依据,一般应采用距离-波幅曲线法或计算法确定缺陷当量
10.2.7.2采用计算法时,若材质衰减系数超过4dB/m,应考虑修正
衰减系数的测定按10.3.6.3的 规定
10.2.7.3发现以下情况之一的缺陷均应记录其波幅和位置 反射波当量大于2mm的单个缺陷; a b 底波降低量大于8dB的缺陷
10.2.8质量分级 10.2.8.1单个缺陷的质量分级见表7
10.2.8.2由缺陷引起底波降低量的质量分级见表8,表8仅适用于声程大于近场区长度的缺陷质量 分级
10.2.8.3按表7和表8评定缺陷等级时,应作为独立的等级分别使用
10.2.8.4当缺陷被检测人员判定为危害性缺陷,棒材的质量等级为V级
0.2.8.5 当密集型缺陷的当量值大于2且任意两个缺陷的间距小于25 棒材的质量等级为 mm, 16
GB;/T34370.5一2017 V级
表7缺陷的质量分级 单位为毫米 等级 单个缺陷当量直径 2 5 3 币4 5 <2 3 二4 -4 密集型缺陷当量直径 长条形缺陷2 二25 >25 表8由缺陷引起底波降低量的质量分级 单位为分贝 等级 底波降低量 BG/BF 8 >81l4 >l4一20 >20~26 >26 0.3游乐设施用钢锻件超声检测 10.3.1钢锻件超声检测适用范围 10.3.1.1钢锻件超声检测方法适用于最小尺寸大于250mm以上的游乐设施用碳钢和低合金钢锻件 的超声检测和质量分级
10.3.1.2钢锻件超声检测方法不适用于奥氏体钢等粗品材料锻件的超声检测,也不适用于内、外半径 之比小于65%的环形和筒形锻件的周向横波检测
10.3.1.3最小尺寸小于或等于250mm的碳钢和低合金钢锻件的检测参照10.2执行
10.3.2检测原则 10.3.2.1检测一般应安排在热处理后,孔、台等结构机加工前进行,检测面的表面粗糙度Ra<6.3pm
10.3.2.2锻件应进行纵波检测
10.3.2.3锻件一般应使用直探头进行检测,对简筒形和环形锻件还应增加斜探头检测
10.3.2.4锻件检测方向厚度超过400mm时,应从相对两端面进行检测
10.3.2.5对筒形和环形锻件的横波检测参照附录C执行,扫查部位和验收标准由合同双方商定
10.3.3探头选用 直探头的选择应满足下列要求 10.3.3.1 应采用单晶直探头,探头标称频率应在1MHz5MHz范围内: a b) 单晶直探头晶片有效直径应在为克10mm一克40mm范围内
0.3.3.2斜探头的选择应满足下列要求 探头与被检工件应保持良好的接触 aa 探头标称频率主要为2MHl么一5MHz.探头晶片面积为80mmi一625mm
b) 10.3.4试块 0.3.4.1试块的制作应符合7.5的规定
10.3.4.2对比试块可由以下材料之一制成 a 被检材料的多余部分(尺寸足够时); b 与被检材料同钢种,同热处理状态的材料; 17
GB/T34370.5一2017 与被检材料具有相同或相似声学特性的材料
0.3.4.3采用单晶直探头检测时,对比试块应至少包含能覆盖整个检测深度的3个p4mm平底孔
10.3.4.4检测面是曲面时,应采用CS对比试块来测定由于曲率不同而引起的声能损失,其形状和 尺寸按图9所示
工件曲率半径在试块曲率半径的0.9倍1.5倍范围内
单位为毫米 会船 85 图gcs皿曲面对比试块 0.3.5灵敏度的确定 10.3.5.1基准灵敏度的确定 当被检部位的厚度大于或等于探头的3倍近场区长度,且探测面与底面平行时,原则上可采用 a 底波计算法确定基准灵敏度 b 对由于几何形状所限,不能获得底波或壁厚小于探头的3倍近场区时,可直接采用试块法确定 基准灵敏度,参照附录D. 10.3.5.2扫查灵敏度一般不应低于最大检测距离处的4mm平底孔当量直径
0.3.6检测 10.3.6.1耦合方式一般可采用直接接触法
10.3.6.2检测时应根据实际情况进行耦合补偿、衰减补偿和曲面补偿
10.3.6.3工件材质衰减系数的测定 在工件无缺陷完好区域,选取3处检测面与底面平行且有代表性的部位,调节仪器使第一次底 a 面回波幅度(B或Bn)为满刻度的50%,记录此时衰减器的读数,再调节衰减器,使第二次底 面回波幅度(2或Bbm)为满刻度的50%,两次衰减器读数之差即为(B1一2)或(Bn-Bm)的 dB差值(不考虑底面反射损失); b 衰减系数的计算公式(T<3N,且满足n>3N/T,m=2n): m一n)T [(Bn一Bm)一6]/2(" 18
GB;/T34370.5一2017 式中: -单程衰减系数,单位为分贝每米(dB/m) Bn一Bm -两次衰减器的读数之差,单位为分贝(dB):; T 工件检测厚度,单位为毫米( mm; N 单直探头近场区长度,单位为毫米( mm; -底波反射次数
m1、n 衰减系数的计算公式T>3N) a=[(B1一B2)一6]/2T B1一B2 -两次衰减器的读数之差,单位为分贝dB); 式中其余符号意义同式(l)的规定; d 工件上3处衰减系数的平均值即作为该工件的衰减系数
10.3.6.4扫查方式 直探头扫查原则上应从两个相互垂直的方向进行检测,尽可能地检测到锻件的全体积
主要 检测方向如图10所示
其他形状的锻件也可参照执行;根据合同技术协议书或图样的要求 也可采用其他形式的扫查,如一定间隔的平行线或格子线扫查
来 T 桌 b 来 dD) 来 注:个为应检测方向;※为参考检测方向
图10检测方向(垂直检测法 b)斜探头检测应按附录E的要求进行
19
GB/T34370.5一2017 10.3.7缺陷的测定和记录 10.3.7.1采用距离-波幅曲线或计算法确定缺陷当量
10.3.7.2计算缺陷当量时,若材质衰减系数超过4dB/m,应考虑修正
10.3.7.3发现以下情况之一的缺陷均应记录 当量直径超过中4mm的单个缺陷的波幅和位置; a b 密集性缺陷:记录密集性缺陷中最大当量缺陷的位置和缺陷分布
应记录大于或等于中4mm 当量直径的缺陷密集区
缺陷密集区面积以50mm×50mm的方块作为最小量度单位,其边 界可由6dB法决定; 底波降低量应按表9的要求记录
10.3.7.4衰减系数;若合同双方有规定时,应记录衰减系数
10.3.8质量分级 当缺陷被检测人员判定为裂纹等危害性缺陷时,锻件的质量等级为V级 10.3.8.1 10.3.8.2 其他缺陷质量分级见表9. 10.3.8.3表9中采用由缺陷引起的底波降低量划分等级的方法仅适用于声程大于近场区长度的缺陷
不同种类的缺陷分级应独立使用
表9锻件超声检测质量分级 等级 <4 <4十6dB <4十18dB >4十18dB 单个缺陷当量平底孔直径 二4十12dB 由缺陷引起的底波降低量 <6dB <12dB <18dB 24dB >24dB BG/BE 二4十6dB 二64十12dE 密集区缺陷当量直径 二4+18dB 10.4游乐设施用无缝钢管超声检测 10.4.1无缝钢管超声检测适用范围 10.4.1.1无缝钢管超声检测适方法于外径不小于40mm,最小厚度为4 的游乐设施用碳钢、低合 mm 金钢、奥氏体不锈钢及奥氏体-铁素体双相不锈钢无缝钢管的接触式超声检测方法和质量分级
无缝钢管超声检测方法不适用于内外径之比小于65%的钢管周向直接接触法斜探头检测 10.4.1.2 也不适用分层缺陷的超声检测
10.4.1.3钢管轴向超声模波检测按照附录F执行
10.4.2检测原则 除非要求检测横向缺陷时,一般可只对纵向缺陷进行检测
10.,4.2.1 10.4.2.2经双方协商,纵向、横向缺陷的检测也可只在钢管的一个方向上进行 10.4.3探头选用 可使用线聚焦或点聚焦探头
10.,4.3.1 10.4.3.2单个探头压电晶品片边长或直径应不大于25mm
20
GB;/T34370.5一2017 10.4.4试块 10.4.4.1 对比试块 10.4.4.1.1对比试块应选取与被检钢管规格相同,材质,热处理工艺和表面状况相同或相似的钢管 制备
10.4.4.1.2对比试块的长度应满足检测方法和检测设备要求
10.4.4.2人工反射体 10.4.4.2.1人工反射体形状 检测纵向缺陷和横向缺陷所用的人工反射体应分别为平行于管轴的纵向槽和垂直于管轴的横 向槽,其断面形状均可为矩形或V形,人工反射体示意图见图1l
b 矩形槽的两个侧面应相互平行且垂直于槽的底面
当采用电蚀法加工时,允许槽的底面和底 面角部略呈圆形
V形槽的夹角应为60°
检测时人工反射体形状的选用由供需双方商定
全部 横向人工反射体示意图 图11人工反射体示意图 21
GB/T34370.5一2017 单位为毫米 全前 40 b)纵向人工反射体示意图 说明 -人工反射体深度,mm 人工反射体宽度,mm.
图11续 10.4.4.2.2人工反射体位置 纵向槽应在对比试块的中部外表面和端部区域内、外表面处各加工一个,3个槽的公称尺寸相 a 同,当钢管内径小于25mm时可不加工内壁纵向槽; 横向槽应在试样的中部外表面和端部区域内、外表面处各加工一个,3个槽的名义尺寸相同 b 当内径小于50mm时可不加工内壁横向槽
0.4.4.2.3人工反射体尺寸 人工反射体的尺寸按表10分为三级,人工反射体最大深度为3.0mm,具体级别按有关的钢管 a 产品标准规定执行; b)如产品标准未作规定应由供需双方商定
0.4.4.2.4制作与测量 人工反射体可采用电蚀、机械或其他方法加工
对比试样上应有明显的标识或编号
a b) 人工反射体深度可用光学方法、覆形方法或其他方法测量
22
GB;/T34370.5一2017 表10人工反射体尺寸 单位为毫米 深度 长度 级别 宽度b 最小 允许偏差 纵向 横向 h/1 士15% 5% 0.20 不大于深度的两倍 40或周长的50% I 0.40 士15% 40 8% 最大为1.5 取小者 m 10% 0.40 士15% 10.4.5 灵敏度的确定 10.4.5.1 直接接触法检测时,可直接在对比试块上将内壁人工反射体的回波幅度调到显示屏满刻度的 80%,再移动探头,找出外壁人工反射体的最大回波在显示屏上标出连接两点即为距离-波幅曲线作 为检测时的基准灵敏度
由于管径的原因,对比试块上无内壁人工反射体时,可用外壁人工反射体的一 次回波和二次回波制作距离-波幅曲线 10.4.5.2扫查灵敏度一般应比基准灵敏度高6dB 10.4.6 检测 10.4.6.1用试块调节检测时,应考虑试块和被检钢管表面的耦合差
10.4.6.2采用斜探头在探头和钢管相对移动的状态下进行检测
检测时均应保证声束对钢管全部表 面的扫查
10.4.6.3检测纵向缺陷时声束在管壁内沿圆周方向传播(见图12);检测横向缺陷时声束在管壁内沿 管轴方向传播见图13)
纵向、横向缺陷的检测均应在钢管的两个相反方向上进行
10.4.6.4探头相对钢管螺旋进给的螺距应保证超声波束对钢管进行100%扫查时,有不小于15%的覆 盖率 图12管壁内声束的周向传播 图13管壁内声束的轴向传播 10.4.7缺陷的测定和记录 采用回波幅值判定缺陷
10.4.7.1 10.4.7.2应记录回波幅度大于或等于相应的对比试块人工反射体距离-波幅曲线50%高度的缺陷
23
GB/T34370.5一2017 0.4.8质量分级 无缝钢管质量分级按表11的规定 表11无缝钢管超声检测质量分级 允许缺陷回波幅度 等级 直接接触法 液浸法 低于相应的对比试块人工反射体距离-波幅曲低于相应的对比试块内、外表面人工.反射体所产生的 线50% 回波幅度50% 低于相应的对比试块人工反射体距离-被幅曲线低于相应的对比试块内,外表而人工反射体所产生的 且大于等于其50% 回波幅度且大于等于其50% 大于或等于相应的对比试块人工反射体距离-波大于或等于相应的对比试块内、外表面人工反射体所 m 幅曲线 产生的回波幅度 0.5其他类型原材料、零部件超声检测 0.5.1游乐设施用铸钢件超声检测可按照GB/T7233.1执行
0.5.2游乐设施用铸铁件超声检测按照附录G执行
0.5.3结构不规则的游乐设施用零部件可采用相控阵超声检测
游乐设施焊接接头超声检测 11.1焊接接头超声检测适用范围 11.1.1游乐设备焊接接头超声检测方法规定了游乐设施焊接接头缺陷的A型脉冲超声检测和质量 分级
mm500 11.1.2游乐设备焊接接头超声检测方法适用于母材厚度为8m mm全焊透熔化焊的对接焊接 接头、T型焊接接头、角接接头、钢管对接接头的超声检测
奥氏体不锈钢对接焊接接头超声波检测参 照附录H的规定进行
11.13游乐设备焊接接头超声检测方法不适用于铸钢焊接接头,外径小于159mm的钢管对接焊接接 头、内径小于或等于200mm的管座角焊缝的超声检测,也不适用于外径小于250mm或内、外径之比 小于70%的纵向焊接接头超声检测
11.2检测技术等级 11.2.1检测技术等级的划分 超声检测技术等级分为A,B,C级
11.2.1.1 1.2.1.2超声检测技术等级的选择应符合制造、安装等有关规范标准及设计图样规定,应根据游乐设 施部件的重要程度和相关产品标准的规定进行选用
游乐设施焊接接头的制造、安装时的超声检测
一 般应采用B级超声检测技术等级进行检测
对特别重要的零部件焊接接头,可采用c级超声检测技术 等级进行检测
24
GB;/T34370.5一2017 11.2.2不同检测技术等级的检测要求 11.2.2.1适用于平板对接焊接接头,其他形式的焊接接头可参照执行
11.2.2.2A级检测: 40 a A级适用于工件厚度为8mm mm焊接接头的检测
b)可用一种折射角(K值)斜探头采用直射波法和一次反射波法在焊接接头的单面双侧进行检 测
如受条件限制,也可以选择双面单侧或单面单侧进行检测
-般不要求进行横向缺陷的检测
c 11.2.2.3B级检测: B级适用于工件厚度为8mm200mm 焊接接头的检测
a b 检测纵向缺陷时,当母材厚度为8<40mm,用一种K值探头采用一次反射法在焊接接头 的单面双侧进行检测;当母材厚度大于40mm<1<100mm,用一种K值探头在焊接接头的 双面双侧进行检测,也可采用两种K值探头在焊接接头的单面双侧(双面单侧)进行检测 当 母材厚度为100mm200mm ,应采用两种K值探头采用直射波在焊接接头的双面双侧进行 检测
斜探头检测时,可在焊接接头两侧边缘使探头与焊接接头中心线 B级应进行横向缺陷检测
成10"20"作斜平行扫查,母材厚度8<100mm可采用1种探头在单面斜平行扫查,母材 厚度100<1<200mm应采用2种探头在单面斜平行扫查
11.2.2.4C级检测 级适用于工件厚度为8mm一400mm焊接接头的检测
C a b)采用c级检测时应将焊接接头的余高磨平
对焊接接头斜探头扫查经过的母材区域要用直 探头进行检测,检测方法按11.4.4.7的规定进行
检测纵向缺陷时,当母材厚度为8<15mm,用一种K值探头采用一次反射法在焊接接头 的单面双侧进行检测,也可采用两种K值探头在媒接接头的单面双侧(双面单侧)进行检测; 当母材厚度大于15mm/<40nmm,应采用两种K值探头在媒接接头的双面双侧进行检测; 当母材厚度为40mm<1<100mm,应采用两种K值探头采用在焊接接头的双面双侧进行检 测;当母材厚度为100mm<1<400nmm,应采用两种K值探头采用直射波在焊接接头的双面 双侧进行检测
C级应进行横向缺陷检测
斜探头检测时,可在煤接接头两侧边缘使探头与焊接接头中心线 d 成10°20°作斜平行扫查,母材厚度8<15mm应采用1种探头在单面斜平行扫查,母材 厚度15<1<400mm应采用2种探头在单面斜平行扫查
母材厚度40<400mm应采用直探头在单面扫查
1.2.2.5用两种或两种以上不同折射角(K值)斜探头检测时,探头间折射角相差不应小于10
1.3试块 11.3.1采用cSK-IA为标准试块,采用CSK-IA.,CsK-A和cSK-A为标准试块和对比试块 其形状和尺寸应分别符合图14图17和表12的规定
25
GB/T34370.5一2017 单位为毫米 其会兴 125 110 95 2.02.53.0 .5 35 2七 K1.01.5 105 9 140 200 来 300 有机玻璃 注尺寸误差不大于士0.05mm 图14CSK-IA试块 单位为毫米 其余 2×2 说明 试块长度,由使用的声程确定
注:尺寸误差不大于士0.05 mm
图15CSK-IA试块 26
GB;/T34370.5一2017 单位为毫米 其余 品 品 7×p1x6短横孔 40 RI0 R0 300 注:尺寸误差不大于士0.05mm
图16cSK-皿A试块 单位为毫米 全部" 说明 一试块长度,由使用的声程确定
注,尺寸误差不大于士0.0mm 图17CSK-VA标准试块 表12CSK-VA试块尺寸 单位为毫米 CSK- 被检工件厚度 对比试块厚度T 标准孔位置6b 标准孔直径d >120150 135 T/4、T/2 6.4(1/4in) >150200 175 T/4、T/2 7.9(5/16in) >200250 T/4、T/2 9.53/8in) 225 >250300 275 T/4、T/2 11.17/16in >300350 325 T/4、T/2 12.71/2in) >350400 375 T/4、T/2 14.3(9/16in 27
游乐设施无损检测第5部分:超声检测GB/T34370.5-2017
游乐设施作为消费者娱乐休闲的场所,其安全问题受到广泛关注。因此,对游乐设施进行定期检测是非常必要的。而无损检测技术可以在不破坏结构完整性的情况下检测出可能存在的缺陷和隐患。其中,超声检测是一种较为常用的无损检测方法之一。
超声检测利用超声波在被检测物体中的传播和反射来检测物体内部的缺陷和材料性质等信息。由于其操作简单、检测速度快、检测深度大等特点,被广泛应用于各个领域中。
在游乐设施无损检测中,超声检测可以应用于轮胎、管道、焊接部位、连接件等方面的缺陷检测。其可检测材料种类广泛,包括金属、非金属、复合材料等。超声检测可以检测出各种常见的缺陷,如裂纹、气孔、夹杂、异物等。
GB/T34370.5-2017是游乐设施无损检测的标准之一,其中包括了超声检测的方法和要求。该标准规定了超声检测设备的参数、检测技术流程以及结果判读等方面的要求,确保了超声检测的可靠性和准确性。
总之,超声检测作为游乐设施无损检测的一种有效方法,在GB/T34370.5-2017标准中得到了明确的规范。在游乐设施的安全检测中,超声检测可以发挥重要作用。
游乐设施无损检测第5部分:超声检测的相关资料
- 无动力类游乐设施儿童滑梯GB/T27689-2011
- 游乐设施安全防护装置通用技术条件GB/T28265-2012
- 无动力类游乐设施术语GB/T28622-2012详解
- 无动力类游乐设施秋千GB/T28711-2012
- 游乐设施安全使用管理GB/T30220-2013
- 无损检测射线照相底片数字化系统的质量鉴定第2部分:最低要求GB/T26141.2-2010
- 无损检测射线照相底片数字化系统的质量鉴定第1部分:定义、像质参数的定量测量、标准参考底片和定性控制GB/T26141.1-2010
- 了解无损检测仪器周向X射线管技术条件GB/T26595-2011
- 无损检测仪器工业用X射线CT装置性能测试方法GB/T26593-2011
- 小型部件声发射检测方法GB/T26646-2011
- 无损检测超声检测设备的性能与检验第2部分:探头GB/T27664.2-2011
- 无损检测超声检测设备的性能与检验第1部分:仪器GB/T27664.1-2011
- 无损检测超声检测仪电性能评定GB/T27669-2011
- 无损检测超声检测设备的性能与检验第3部分:组合设备GB/T27664.3-2012
- 了解无损检测超声检测2号校准试块GB/T19799.2-2012
- 游乐设施无损检测第5部分:超声检测GB/T34370.5-2017