GB/T40410-2021
金属材料多轴疲劳试验轴向-扭转应变控制方法
Metallicmaterials—Multiaxialfatiguetesting—Axial-torsionalstrain-controlledmethod
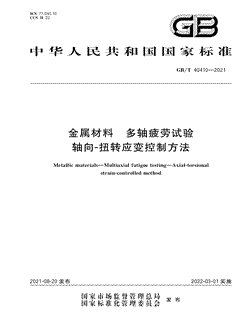
- 中国标准分类号(CCS)H22
- 国际标准分类号(ICS)77.040.10
- 实施日期2022-03-01
- 文件格式PDF
- 文本页数15页
- 文件大小1.04M
以图片形式预览金属材料多轴疲劳试验轴向-扭转应变控制方法
金属材料多轴疲劳试验轴向-扭转应变控制方法
国家标准 GB/T40410一2021 金属材料多轴疲劳试验 轴向-扭转应变控制方法 Metaliematerials一Mwtasitaiguetestng- -Axial-torsional strain-eontrolledmethod 2021-08-20发布 2022-03-01实施 国家市场监督管理总局 发布 国家标涯花管理委员会国家标准
GB/40410一2021 目 次 前言 范围 2 规范性引用文件 术语和定义 符号和说明 原理 试样 试验设备 试验程序 数据处理和分析 10试验报告 l0 附录A资料性 数据处理公式 12 参考文献
GB/40410一2021 前 言 本文件按照GB/T1.1一2020<标准化工作导则第1部分:标准化文件的结构和起草规则》的规定 起草
请注意本文件的某些内容可能涉及专利
本文件的发布机构不承担识别专利的责任
本文件由钢铁工业协会提出 本文件由全国钢标准化技术委员会(SAC/TC183)归口
本文件起草单位:北京工业大学、冶金工业信息标准研究院、深圳万测试验设备有限公司、中航工业 沈阳飞机设计研究所,力试(上海)科学仪器有限公司,航发北京航空材料研究院、航发商用航 空发动机有限责任公司、钢铁研究总院
本文件主要起草人;尚德广,董莉、李芳代、李道航、左林玄,曲林锋、刘建中陈勃、张成成、童第华 高怡斐、王斌、黄星、侯慧宁
GB/40410一2021 金属材料多轴疲劳试验 轴向-扭转应变控制方法 范围 本文件规定了应变控制下金属材料轴向扭转复合疲劳试验的原理,试样,试验设备、试验程序、数 据处理分析和试验报告
本文件适用于金属薄壁管试样在室温及高温下施加恒幅对称、平均应变为零的加载波形及轴向与 扭向波形具有相同频率的轴向-扭转复合疲劳试验
规范性引用文件 下列文件中的内容通过文中的规范性引用而构成本文件必不可少的条款
其中,注日期的引用文 件,仅该日期对应的版本适用于本文件;不注日期的引用文件,其最新版本(包括所有的修改单)适用于 本文件
GB/T228.1金属材料拉伸试验第1部分;室温试验方法 GB/T228.2金属材料拉伸试验第2部分;高温试验方法 GB/T6394金属平均晶粒度测定方法 室温压缩试验方法 GB/T7314金属材料 金属材料力学性能试验术语 GB/T10623 金属材料单轴试验用引伸计系统的标定 GB/T12160 GByT1243金属材料扭矩控制疲劳试验方法 GB/T16825.1静力单轴试验机的检验第1部分拉力和(或)压力试验机测力系统的检验与 校准 GB/T25917.1单轴疲劳试验系统第1部分:动态力校准 GB/T26077金属材料疲劳试验轴向应变控制方法 JJG556轴向加力疲劳试验机 JG762引伸计检定规程 术语和定义 GB/T10623和GB/T26077界定的以及下列术语和定义适用于本文件
3.1 轴向应变axialstrain 引伸计标距长度的伸长量AL
与引伸计标距长度L,的比值,用式(1)计算
e=AL/L 注:参考工程应变中的轴向应变定义
GB/T40410一2021 3.2 剪切应变 shearstrain 剪切位移AL,与引伸计标距长度L
的比值,用式(2)计算
y=AL,/L
注1由加载在圆柱试样上的扭矩产生,参考工程剪切应变
除剪切位移不一样,其他都类似于轴向应变,剪切位 移与引伸计标距方向垂直而不是平行(见图1), 注图中符号及其说明见表1
图1扭矩作用下圆柱试样引伸计标距内的扭转截面 注2:剪切应变与相对引伸计标距方向的扭转角之间的关系见式(3). Y=tan 3 式中: -沿着引伸计标距方向的扭转角
注3:式(4)给出了用弧度表达的圆柱试样外径d,以及引伸计标距长度L
表达的剪切应变: y=(d/2)0/L
式中: -剪切位移L
对应的扭转角
L
通过使用校准的扭转引伸计可以直接测量,或者由弧长公式AL
=(ad/2)0求得,0值通过旋 转变量差动变压器直接测量
3.3 双轴应变幅值比biaxialstrainamplituderatio 剪切应变幅值入与轴向应变幅值e,的比,用式(5)计算
.(5 入=入./e
3.4 轴向应变和剪切应变之间的相位角phaseanglebetweenaxialandshearstrains 轴向应变波形与剪切应变波形之间的相位夹角,这两个波形为相同类型,如同为三角波或同为正 弦波
3.5 同相比例)轴向-扭转复合疲劳试验in-phase(proportional)axial-torsionaltatiguetest 在相同频率下,轴向应变和剪切应变相位角为零(9=0")的试验(见图2)
注对于对称循环作用的轴向和勇切应变波形,如果轴向应变波形的最大值与剪切应变被形最大值同时达到,则相 位角必=0",
GB/40410一2021 /厅 应变路径 0.0 声0 时间/s 1周或360”" S 标引序号说明 -剪切应变 轴向应变
图2轴向、剪切应变波形同相比例)加载 3.6 非同相非比例轴向-扭转复合疲劳试验 out-of-phasenon-proportionalaxial-torsional fatigetest 在相同频率下,轴向应变和剪切应变相位角不为零(90')的试验
注1对于对称循环作用的轴向和剪切应变波形,如果轴向应变波形的最大值与剪切应变波形最大值不同时达到 则相位角9夫0
注2:图3给出了必=90"的非同相轴向-扭转复合疲劳试验加载波形
+ /5 应变路径 0.0 声=90°" 时间/ 1周或360" 标引序号说明 -剪切应变; -轴向应变 图3轴向、剪切应变波形非同相(非比例)加载
GB/T40410一2021 3.7 剪切应力 shearstress 由于薄壁管试样受到扭矩T的作用而产生的与轴向正交的切线方向上的应力分量
注1:推荐采用剪切应力均匀分布假设,作用在中径的剪切应力r与扭矩T的关系见式6): 16T T(;一Fd
十d 式中 试样的外径与内径
d.,d 注2:弹性加载情况下,在引伸计标距段内,试样内外径范围内直径为d的位置,其剪切应力
可以由式(7)计算 得到 16Td
(7 T(d
一d 注3,为了建立材料的循环剪切应力-应变关系曲线,可以在相同的加载条件下,在薄壁管的同一个位置通过测定 剪切应变和剪切应力来确定
符号和说明 本文件所用符号、说明及单位见表1
表1符号,说明和单位 单位 符号 说明 轴向疲劳强度指数 b 扭转疲劳强度指数 向疲劳延性指数 扭转疲劳延性指数 试样引伸计标距段内直径 mm 试夹持端的外径 mm 试样引伸计标距段的内径 d mm d 试样引伸计标距段的外径 mm GPa 杨氏弹性模量 N 轴向力 剪切弹性模量 GPa K MPa 轴向循环强度系数 K" 扭转循环强度系数 MPa 试样全长 mm 试样夹持端长度 LoG mm L1 夹持端和过渡段总长度 mm 引伸计标距长度 L mm 引伸计标距长度的变化量 A mm L 试样中间平直段的长度 mm
GB/40410一2021 表1符号,说明和单位(续》 符号 说明 单位 L 剪切位移 mmm 轴向循环应变硬化指数 n," 扭转循环应变硬化指数 失效时的循环数(疲劳寿命 N 过渡弧段半径 mm Ra 表面粗糙度 m R7 剪切应变比 R 轴向应变比 R 轴向循环应力比 R 剪切循环应力比 S 试样有效横截面积 mnm 扭矩 Nm 试样引伸计标距段的壁厚 mm 剪切应变 Y 剪切应变幅值 剪切应变范围值 AY Y 剪切弹性应变 A
剪切弹性应变范围值 扭转疲劳延性系数 剪切塑性应变 7” 剪切塑性应变范围值 心 轴向应变 轴向应变幅值 轴向应变范围 Ae 轴向弹性应变 轴向弹性应变范围值 Ae
轴向疲劳延性系数 轴向塑性应变 轴向性应变范围值 AE, 试样引伸计标距部分两端两个平面的扭转角 双轴应变幅值比 轴向应力 MPa A 轴向应力范围值 MPa a 轴向疲劳强度系数 MPa MP 剪切应力 A 剪切应力范围值 MPa
GB/T40410一2021 表1符号,说明和单位(续 符号 说明 单位 扭转疲劳强度系数 r MPa 轴向应变和剪切应变之间的相位角 试样引伸计标距方向的扭转角 5 原理 以应变作为控制量,对金属管薄壁试样同时施加以轴向和扭向循环载荷,进而测定该材料疲劳性 能,可用于获取均匀材料在同相(比例)与非同相(非比例)轴向与扭转组合载荷条件下的疲劳寿命和循 环变形数据
注1:多轴载荷通常所导致的变形与损伤机制较为独特,与简单单轴加载条件下的损伤机制有很大不同
由于大 多数工程构件都受到多轴循环载荷作用,因此有必要描述这种模式下材料的变形和疲劳行为
掌握多轴损 伤特性可以可靠地预测工程部件的疲劳寿命
轴向-扭转复合载荷是多轴力系统中的几种可能类型之 质上是双轴载荷
注2:由于薄壁管试样的应力状态在整个试验截面上是恒定的,在主应力或应变空间,轴向与扭转组合加载比平面 双轴加载更为方便
试样 o 6.1一般要求 本文件以圆形截面的薄壁管为试样进行试验
为了避免循环载荷下的不稳定性,试样的壁厚应满 足平均直径与壁厚的比值为10:1的薄壁管准则
对于多晶体材料,应保证壁厚部分至少存在10个晶 粒来保持各向同性
注试样平均直径dm=(d,十d)/2.
6.2材料要求 应预知试样的拉伸和压缩性能
设计试样时,可按GB/T228.1.、GB/T228.2和GB/T7314测定 拉伸和压缩性能
如需要测定材料的平均晶粒尺寸,应按GB/T6394进行测定
推荐试样形状如图4所示
试样设计时,应保证同心度,避免附加弯曲应力
注;图中符号及其说明见表2. 图4薄壁管轴向-扭转疲劳试验试样
GB/40410一2021 6.3尺寸要求 试样的具体尺寸要求见表2. 表2薄壁管试样的尺寸要求 单位 尺寸要求 名称 试样引伸计标距段的壁厚1 0.5(d
一d mmm 试样引伸计标距段的外径d
4士31 mm 试样引伸计标距段的内径d mm 0.85d
士0.04d. 试样夹持端的外径d
mm 1.6l.士0.4ad 45 倒角c 3.2ud
士0.4d 过溅弧段半径R mmm 试样全长L 8.5d.士1.5d mm 夹持端长度L
2d.士0.3d
mm 夹持端和过渡段总长度L 3.5d
士0.5d
mm 试样中间平直段的长度L 1.5dl.士0.5d mm 试样中间引伸计标距段的长度L mm 0.9d
士0.3d
士0.015 d
和d的同心度 mm 2.0士0.5 壁厚1的典型取值范围 mmm 6.4附加说明 非多晶体材料(如单晶材料和定向凝固材料)管状试样的壁厚应足够大,以保证充分包含该材料 6.4.1 的典型微观结构
6.4.2通常在包含扭转的循环载荷下,疲劳寿命与管状试样的内外径之比d/d
有关
因此,应注意 比较材料相同但具有明显不同内外径比值试样的疲劳寿命
承受轴向-扭转复合载荷时,在内外径比值 的标准取值范围内试样疲劳寿命的差别不应过大
6.5试样制备 试样内表面应研磨,以防止疲劳裂纹在试样内表面萌生
试样的引伸计标距部分的内表面与外表 面应从一端到另一端一次性加工成型
试样平行段内外表面粗糙度Ra应小于0.2m
试验设备 7.1试验机 所有的试验要在能够施加拉压和扭转载荷的试验系统上进行
试验系统应具有足够的轴向刚度和 扭转刚度,使得试验系统能够减小试验框架在额定最大轴向力和扭矩下的变形
试验机应满足 GB/T26077中轴向疲劳试验要求及GB/T12443中扭转疲劳试验要求
7.2固定夹具 用于夹持试样的夹具应具有一定使用耐久性
夹具的设计很大程度上取决于试样的设计
典型的 液压夹头装置和具有光滑圆柱形夹持部位的试样结合使用,能够较好地满足对中性和轴向刚度要求
GB/T40410一2021 对于其他类型的固定装置(如具有螺纹连接端试样固定的装置),若符合对中性准则,也可使用
但是相 对于具有光滑圆柱形夹持部位的试样,具有螺纹连接端的试样较难满足对中性准则的要求
因此,应优 先选择具有光滑圆柱形夹持部位的试样
7.3力和扭矩传感器 试验机测力系统应按GB/T16825.1进行静态校准,其准确度应为1级或优于1级
应确保动态力 测量误差不超过所需测力范围的士1%
推荐使用GB/T25917.1或JJG556作为检查方法 7.4引伸计 引伸计应按GB/T12160或JJG762进行检定/校准,并符合1级引伸计要求
7.5数据采集系统 轴向和扭向滞后环及轴向力/应变和扭矩/剪切应变随时间的变化,应采用数字采集系统对循环试 验数据进行采集
数据采集应根据具体加载路径确定采集频率,以避免四个通道响应信号削峰损失
8 试验程序 8.1试验条件 8.1.1对于室温试验,一般在10C35C范围内进行
对温度要求严格的试验,试验温度应为23C士 5 ?C
8.1.2对于高温试验,温度一般不超过1200C,试样引伸计标距段内的温度变化应不超过5C,或在 名义试验绝对温度的1%以内,取两者中的较大者
8.1.3如有任何超出试验要求极限的温度冲击,应将所有这些温度值记录在试验报告中
8.2试样尺寸测量 8.2.1薄壁管试样引伸计标距部分的内径和外径应至少进行三次测量两端和中间)
为确保同心度 应附加三次相应的测量
由测量结果计算得到的平均值作为试样的计算尺寸用于试验控制和试验数据 的后处理
8.2.2对于高温试验,由室温下的测量数据算得的平均值应利用热膨胀系数修正得到试验温度下的试 样尺寸
并用计算得到的高温下尺寸评估试验控制参数以及用于试验数据的后处理
热膨胀系数可以 在进行疲劳测试前通过测量每个试样得到,或通过材料手册查得
8.3试样安装 试样应在不受任何轴向或扭向预载荷的情况下安装在试验机上
在安装接触型引伸计或其他接触 型仪器时应尽量避免划伤试样内外表面 8.4轴向和剪切应变的计算 为精确控制试验,轴向应变和剪切应变值都应以试样的引伸计标距段为准计算得出
剪切应变在 试样的薄壁截面沿径向成线性变化,应以试样的外径为准,用式(4)计算得出
8.5加载控制模式 单轴拉压、扭转和轴向-扭转复合(同相和非同相)疲劳试验应在应变控制下进行
为进行应变控制 下单轴拉压疲劳试验,扭转通道控制器应在零扭矩状态
在进行应变控制下的扭转疲劳试验时,轴向通
GB/40410一2021 道控制器应在零载荷状态
8.6指令波形 8.6.1轴向与扭转应变的指令波形可为三角波或正弦波
对于室温试验,为防止薄壁管试样由于塑性 变形而过热(即滞后加热),加载波形的应变速率(三角波)或频率(正弦波)应足够低
试验中所采用的 应变率或频率一般不能使试样温度增高超过5,或超过名义绝对试验温度的1%,取两者较大者
对 于非同相轴向-扭转复合试验,轴向波形与扭转波形之间应有一定的相位角,且扭转波形滞后于轴向 波形
8.6.2对于金属材料,疲劳寿命可能与应变速率或频率相关
例如,应变速率相差10倍或以上,可能 会产生不同的疲劳寿命数据
因此,为建立上述情况下的疲劳寿命关系,试验中所采用的应变速率或频 率应和其他数据一并列出
8.6.3在一定温度下,一些材料的疲劳寿命可能与加载波形比如三角波或正弦波)有一定的相关性
由于三角波波形能够产生恒定的有效应变速率,因此为了准确描述轴向-扭转复合加载下材料的循环变 形行为,一般认为三角波比正弦波更为合适
8.7试验开始 材料所表现的初始循环变形取决于试验开始时的试验加载程序
同一系列的所有疲劳试验都应从 相同的方向开始
例如,在轴向扭转复合加载试验中,轴向加载波形通常开始于拉伸方向正向)扭转 加载波形通常开始于剪切应变正方向
图2和图3分别给出了轴向-扭转同相、非同相试验开始时的加 载波形
对于较大应变幅度试验,为防止产生过冲现象或者引伸计与试样之间产生滑动,轴向与剪切应 变分别在10周次内达到各自最终的稳定应变幅即可
8.8试验监测 试验监测在试验过程中需监测各试验控制变量(试样温度,轴向与扭向通道指令波形),且各控制变 量应满足以下要求 所控制的应变幅度变化范围不能超过各自通道名义值的1% aa b)在轴向-扭转复合加载疲劳试验中,轴向与扭向应变波形之间的相位角相对于预设值的偏移量 不能超过3; 试样温度变化范围不应超过5C,或名义试验温度的1%,取两者中的较大者
c 若试验过程中任一控制变量偏离其相应的规定极限范围,则畸变数据应在试验报告中进行说明
8.9数据记录 8.9.1在疲劳试验最初的10个循环周次内,应记录其轴向力、轴向应变、扭矩和剪切应变,来研究材料 的初始循环硬化/软化
在整个疲劳试验过程中,上述控制变量都应以对数循环间隔的方式进行相应记 录(如,循环数1020,50、100200,500、1000、2000,5000等 8.9.2通常在试验的最后阶段,当试样表面出现目视可见裂纹时,应适当减小数据记录的循环间隔以 更好地检测试样失效现象
8.10试样失效的确定 与单轴拉压试验不同,纯扭转疲劳试验中试样通常不会分离成两块
载荷下降百分比方法或基于 循环应力-应变行为硬化或软化)的方法都可用于定义试样失效
载荷下降百分比方法:当试样加载载荷相对于先前记录的轴向或扭向数据峰值下降5%或 a 10%时,认为试样已失效
GB/T40410一202 b 基于循环应力-应变行为硬化或软化)方法;通过考虑材料的循环硬化或软化行为来定义试样 失效
通常对于恒幅轴向-扭转复合疲劳试验,在绝大部分疲劳寿命内,载荷范围相对于循环 数曲线关系的斜率是一个常数(零或者对于循环硬化材料为一较小的正数,对于循环软化材 料为一负数)
此时失效定义为轴向载荷或扭转载荷范围相对于循环数的曲线与比实际硬化 或软化曲线低10%的曲线相交时的载荷值
注表面复型技术也可用于定义试样失效;用乙酷纤维素薄膜复制试样引伸计标距内表面,以预定的循环间隔中断 疲劳试验后检查薄膜是否存在表面裂纹
通过观察到的最长裂纹通常为0.1mm或1.0mm)来确定试样 失效
数据处理和分析 g.1弹塑性载荷条件下的轴向和剪切应力-应变关系曲线 在弹塑性加载条件下,轴向和剪切应变由弹性和塑性部分组成
常用来描述循环轴向或剪切应力 应变关系的数据处理公式参见附录A
9.2轴向、剪切应变幅值与疲劳寿命关系 通过分别使用轴向及剪切的应力幅值范围和弹性模量计算总的轴向应变范围/剪切应变范围可以 区分为弹性和塑性部分
在拉压和纯扭转载荷条件下,描述轴向或剪切应变与疲劳寿命的关系函数参 见附录A
这些轴向和扭转疲劳寿命的关系可分别或结合起来使用,预测轴向-扭转复合载荷下的疲劳 寿命
10 试验报告 试验报告应包括以下内容 本文件编号; a b) 材料牌号和规范编号、生产厂家、炉批号、材料规格,热处理制度; 材料微观结构和沿着长度方向以及薄壁管厚度方向的晶粒尺寸、化学成分和常规力学性能等 c 如适用: 试样的形状、尺寸表面状态等; d 试验设备的基本信息; e 试验控制变量:试验温度,频率,应变速率,应力比或应变比,载荷或应变最大、最小值和波形 轴向,扭向应变波形之间的相位角; 试验过程中不符合本文件的任何情况 8 h 试验结果;轴向应力,应变,扭向应力,应变随时间变化关系;典型循环的迟滞回线;轴向应变 与轴向应力关系,扭向应变与应力关系;试样失效的确定方法;导致试样失效的主裂纹方向; 与引伸计和试样的接触点有关联的裂纹以及所有超出规定界限外的控制变量差值
0
GB/40410一2021 附 录 A 资料性 数据处理公式 A.1轴向应力-应变公式 轴向循环应力-应变关系可由轴向的Ramberg一Osgood公式描述,见式(A.1)和式(A.2): A "“ A.1 N 羡 学 A.2 丽 A.2扭转循环应力-应变曲线 剪切循环应力-应变关系可由扭向的Ramberg-Osgood公式描述,见式(A.3)和式(A.4) AY AY A.3 2 Ar立 A.4 2 2C大 轴向应变幅-疲劳寿命关系 轴向应变与疲劳寿命的关系可由轴向的Manson-Coffin公式表达,见式(A.5): 学-N)'十t(eN A.5 A.4剪切应变幅疲劳寿命关系 剪切应变与疲劳寿命的关系可由扭向的Manson-Coffin公式表达,见式(A.6). (A.6 cw)>十yicN 11
GB/T40410一2021 考文献 参 [[1]GB/Z40387一2021金属材料多轴疲劳试验设计准则 [2]ASTME2207-15Strain-ControlledAxial-Torsiona nlFauigueTestingwithThimwaledTw bularSpeeimens [3 SoeeDF,MarquisGB,.MarquisG.B,MltiaxialFatigue SAE,Warrendale,2000 12
金属材料多轴疲劳试验轴向-扭转应变控制方法GB/T40410-2021解读
随着现代工业的快速发展,对金属材料的性能和耐久性等要求也越来越高。而多轴疲劳试验作为一种重要的金属材料测试方法,在实际应用中起到了至关重要的作用。为了进一步提高多轴疲劳试验的精度和可靠性,我国于2021年发布了《金属材料多轴疲劳试验轴向-扭转应变控制方法》GB/T40410-2021标准。
该标准主要涉及到了轴向-扭转应变控制方法的试验环境、设备以及试验过程中的控制要点等方面。其中,试验环境包括温度、湿度、气氛等因素,这些环境对多轴疲劳试验的结果影响极大,需要在试验前进行充分考虑和调整。
同时,在设备方面,该标准也明确规定了试验机的选用、校准以及试验夹具的设计和制作等要求。试验过程中的控制要点则主要包括应变控制、载荷控制、变形控制等方面,这些控制能够确保试验数据的精度和可靠性。
另外,该标准还对多轴疲劳试验中常见的试验方法进行了详细介绍,例如正弦波加载、随机加载、响应谱加载等。这些方法能够更好地模拟实际工况下的应力状态,从而提高多轴疲劳试验的真实性。
总的来说,GB/T40410-2021标准的发布为金属材料多轴疲劳试验的开展提供了更加科学的方法和指导,有助于提高试验数据的精度和可靠性,推动金属材料的发展和应用。