GB/T31213.1-2014
无损检测铸铁构件检测第1部分:超声检测方法
Non-destructivetesting—Testingofcastironequipmentsandcomponents―Part1:Testmethodforultrasonic
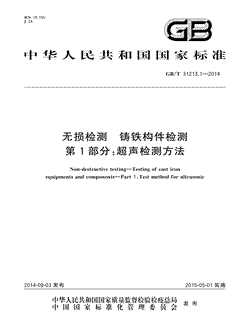
- 中国标准分类号(CCS)J04
- 国际标准分类号(ICS)19.100
- 实施日期2015-05-01
- 文件格式PDF
- 文本页数13页
- 文件大小441.75KB
以图片形式预览无损检测铸铁构件检测第1部分:超声检测方法
无损检测铸铁构件检测第1部分:超声检测方法
国家标准 GB/T31213.1一2014 无损检测铸铁构件检测 部分:超声检测方法 Non-destructivetesting一Iestingofeastiron equipmentsandcomponenmts一Part1:Testmethodforultrasonie 2014-09-03发布 2015-05-01实施 国家质量监督检验检疫总局 发布 国家标准化管理委员会国家标准
GB/T31213.1一2014 前 言 GB/T31213《无损检测铸铁构件检测》分为三个部分 -第1部分;超声检测方法; 第2部分:声超声检测方法; 第3部分;声发射检测方法
本部分为GB/T31213的第1部分
本部分按照GB/T1.1一2009给出的规则起草
本部分由全国无损检测标准化技术委员会(SAC/TC56)提出和归口
本部分起草单位;特种设备检测研究院、硕德(北京)科技有限公司、杭州市特种设备检测院,保 定市特种设备监督检验所,河南省锅炉压力容器安全检测研究院,山东瑞样模具有限公司,北哀声华兴 业科技有限公司
本部分主要起草人沈功田、香勇,昊占稳、胡斌,李伟忠,余兵、目亚弟、孔祥夷、臧福恒,魏忠瑞、 高广兴、张君娇、苑一琳、王珊珊、刘时风,彭波、彭春
GB/T31213.1一2014 无损检测铸铁构件检测 第1部分;超声检测方法 范围 GB/T31213的本部分规定了铸铁构件的超声检测方法
本部分适用于厚度为10mm一500mm铸铁构件(包括铸铁烘缸、铸铁管道元件、铸铁阀门、铸铁结 构件等)制造过程中的铸造缺陷检测、球墨铸铁构件球化级别的检测和厚度为10 mm50mm在用铸 铁构件的缺陷检测
规范性引用文件 下列文件对于本文件的应用是必不可少的
凡是注日期的引用文件,仅注日期的版本适用于本文 件
凡是不注日期的引用文件,其最新版本(包括所有的修改单)适用于本文件 GB/T9441球墨铸铁金相检验 GB/T9445无损检测人员资格鉴定与认证 GB/T12604.1无损检测术语超声检测 GB/T19799.1无损检测超声检测1号校准试块 GB/T19799.2无损检测超声检测2号校准试块 无损检测通用术语和定义 GB/T20737 无损检测超声检测用试块 GB/T23905 术语和定义 GB/T12604.1和GB/T20737界定的术语和定义适用于本文件
安全要求 本章没有列出进行检测时所有的安全要求,使用本部分的用户应在检测前建立安全准则
检测过程中的安全要求至少包括 a)检测人员应遵守被检件现场的安全要求,根据检测地点的要求穿戴防护工作服和佩戴有关防 护设备; 若有要求,使用的电子仪器应具有防爆功能; b 在封闭空间内进行操作时,应考虑氧气含量等相应因素,并采取必要的保护措施 在高空进行操作时,应考虑人员、检测设备器材坠落等因素,并采取必要的保护措施, D 在线检测或在极端环境下进行操作时,如低温、高温等条件下,应考虑冻伤、烫伤、中暑等因素, 并采取必要的保护措施; 如果存在有毒有害气体等其他可能损害人体的各种环境因素,在实施检测时,应仔细加以辨 识,并采取必要的保护措施
GB/T31213.1一2014 人员要求 采用本部分进行检测的人员应按GB/T9445的要求或有关主管部门的规定取得相应无损检测人 员资格鉴定机构颁发或认可的超声检测等级资格证书,从事相应资格等级规定的检测工作
检测工艺规程 6.1通用检测工艺规程 从事超声检测的单位应按本部分的要求制定通用检测工艺规程,其内容至少应包括如下要素: 适用范围 a b)引用标准、法规; 检测人员资格 c 检测仪器设备;合剂、探头、信号线、检测仪器主机,检测数据采集和分析软件等; D 被检件的信息;几何形状与尺寸、材质、设计与运行参数等; 检测覆盖范围及探头扫查部位 被检件表面状态及检测探头扫查方式; g 检测时机 灵敏度测量,距离-幅度曲线绘制 检测过程和数据分析解释; 检测结果的评定; 检测记录、报告和资料存档 编制审核和批准人员 m 编制日期
n 6.2检测作业指导书或工艺卡 应按8.1.2执行
检测设备和器材 仪器 7.1 超声检测仪至少应符合以下要求 a)水平线性<0.5%,垂直线性<3%; b适用于探头标称频率在0.5MHz~5MHz的范围 接收带宽应至少在探头标称频率一6dB带宽的0.5~2倍,并有与探头标称频率相适应的窄带 滤波器; 发射脉冲宜是方波激励,激励电压大于500V,脉冲上升时间不应超出标称探头频率对应周期 D 的0.25倍,且脉冲宽度至少在100ns一1000ns的范围内可调; 探伤时可以观察到背面回波(底波)的衰减 e) 设备宜具备球墨铸铁球化率测量(声速测量)的能力
7.2探头 对于铸铁构件铸造过程中产生的治金缺陷,应采用单晶直探头进行检测,当检测铸件近表面缺陷时
GB/T31213.1一2014 可使用双晶直探头;对于特殊几何形状的铸铁构件,可使用斜探头进行检测
对于铸铁构件在役使用过程中产生的缺陷,应采用斜探头进行检测
对于斜探头,声程不超过100mm,标称折射角度在45"~70"的范围内 两种探头的频率均应当在0.5MHz~5MHz的范围之内,在检测厚度小于20 的铸件或是靠 mm 近表面的部位时可以选择较高的频率 由于超声在钢和铸铁中的传播速度是不同的,实际的折射角度与用于钢材料的探头标称折射角度 也是不同的
可以按式(1)计算: a
=arcsin[.sina. /, 式中 铸铁中的折射角度 钢中的标称折射角度(探头标称折射角度); a 铸铁中的横波声迷,单位为米每秒(m/s) 钢中的横波声速,单位为米每秒(m/s)
如果工件材料是球墨铸铁,可以参照图1根据声速确定探头在球墨铸铁中的折射角度
90” 90" 85” 80” 75” 70 70” 5" 0”
Or 55 50 50° 宿 40 40” 35? 30 p 240025002600270028002900300031003200o 3255 说明: 球墨铸铁中的折射角度; 横波声速,单位为m/s 钢材料中的标称折射角度; 此区域同时存在纵波和横波 图1钢材料中与球墨铸铁中探头折射角度的关系 在实际应用中,如可以使用两个相同的斜探头时,可按图2所示的方法测定探头的折射角度,按 式2)计算 retan[A/(2×T)] a
=ar 式中: 铸件中的折射角度" a 在信号最大情况下,两个斜探头人射点间的距离 A 壁厚
T
GB/T31213.1一2014 图2利用两个相同斜探头测定铸铁构件中探头折射角度的示意图 7.3标准试块 标准试块应采用GB/T19799.1规定的1号试块或GB/T19799.2规定的2号试块
7.4对比试块 7.4.1 概述 对比试块应使用与被检工件类似的材料制成(例如声速、晶粒噪声和表面条件),壁厚应等于或大于 被检工件的标称壁厚
试块中制作人工参考反射体,一般有平底孔和横通孔两种,平底孔用于直探头纵波探伤,横通孔用 于斜探头横波探伤
对比试块的形状和尺寸应符合7.4.2和7.4.3的规定,其他要求应符合GB/T23905的规定 7.4.2单晶直探头对比试块 单晶直探头检测采用单晶直探头对比试块调节检测灵敏度,人工参考反射体为平底孔,其形状和尺 寸应符合图3和表1的规定 单位为毫米 全抓 0.05A 图3单晶直探头对比试块
GB/T31213.1一2014 表1单晶直探头对比试块尺寸 单位为毫米 平底孔直径克=3 平底孔直径=8 平底孔直径中=5 平底孔直径多=I0 检测距离 试块直径D 检测距离L试块直径D检测距离L 试块直径D 检测距离L试块直径D 50 20 50 20 20 20 50 50 40 50 50 50 50 50 50 50 50 80 50 00 60 100 60 60 80 50 120 60 150 80 150 80 16o 80 200 80 200 80 200 80 250 00 250 100 300 100 300 100 400 150 500 150 7.4.3双晶直探头对比试块 工件检测距离小于50nmm时,应采用双品直探头对比试块
双晶直探头试块的人工参考反射体为平底孔,其形状和尺寸应符合图4和表2的规定
单位为毫米 200 250 品 - 图4双晶直探头对比试块 表2双晶直探头对比试块尺寸 单位为毫米 检测距离L 平底孔直径 15 25 35 45 10 20 30 40 10
GB/T31213.1一2014 7.4.4斜探头对比试块 斜探头检测采用斜探头试块调节检测灵敏度,其人工参考反射体为横通孔,其形状和尺寸应符合 图5的规定 单位为毫米 300 品 0.05 说明 -横孔直径,分别为3mm、5mm.8mm和10mm. 图5斜探头对比试块 7.5检测设备的维护和核查 仪器使用单位应制定设备核查作业指导书,对检测设备进行周期性维护、核查,以保证仪器功能,核 查结果应有相应记录和报告 在进行现场检测之前,应在实验室内选择相应规格的对比试块对检测仪器进行核查,若检测结果与 已知试块人工参考反射体分布相符,则表明仪器正常
在现场进行检测时,如怀疑设备的检测结果,应对设备进行功能检查和调整,并对每次维护检查的 结果进行记录
检测程序 检测前的准备 8.1 8.1.1被检件材料 首先需要确定待检铸铁构件材料是否适用于超声检测,应至少保证对比试块中人工缺陷反射波信 噪比高于6dB
否则检出能力会降低
应对被检铸铁构件壁厚方向按照最终使用状态划分成不同的检测区域,其剖面如图6所示
GB/T31213.1一2014 说明 边缘区域; 中心区域 壁厚; -T/3最大30mm). 图6壁厚分区 8.1.2检测作业指导书或工艺卡的编制 对于每个铸铁构件,根据使用的仪器和现场实际情况,应按照通用检测工艺规程编制超声检测作业 指导书或工艺卡,确定探头和表面条件
同时对每个被检件进行测绘,对检测部位进行编号,画出被检 构结构示意图
8.2表面条件和耦合要求 所有扫查面应清除污物、氧化皮等,并保证平整以便超声耦合
另外,在检测前应消除工件表面状 况(例如铸造毛坯、喷砂/丸、机加工等)可能造成的评估误差
检测面的表面粗糙度<12.5umm 可使用不同的耦合介质,但是它们的类型应适合被检材料
例如;水、含添加剂的水(润湿剂,防冻 剂防腐剂,连结剂、油、脂、含水的纤维素浆糊等
合介质的特性在整个检查过程中应保持稳定并满足使用温度范围
8.3检测 8.3.1概述 探头的选择在很大程度上依赖于铸件的形状以及缺陷的特点和位置
对于铸造过程中产生的缺 陷,通常使用的方法为利用纵波直探头垂直人射,对于使用过程中产生的缺陷,可以使用横波探头斜 人射
8.3.2扫查覆盖与扫查速度 为了能覆盖到所有规定需要进行检测的部位,相邻探头移动覆盖区可以是有效声束的10%
扫查 速度不应超过150nmm/s
8.3.3仪器调试 8.3.3.1概述 应使用GB/T19799.1.GB/T19799.2的标准试块和7.4规定的铸铁对比试块进行仪器调试
GB/T31213.1一2014 8.3.3.2量程设定 量程的设定可以利用对比试块或标准试块进行,然后用铸铁构件自身进行检验,如果铸件厚度已 知,并且具有平行曲面,可以直接使用铸件进行设定
8.3.3.3系统最小灵敏度(检测灵敏度)设定 依次测试一组不同检测距离的平底孔或横通孔,制作探头的距离-波幅曲线,并以此作为灵敏度
如果无法达到上述方法设定的灵敏度,则在检测报告中应记录下能探测到的最小平底孔直径
8.3.3.4扫查灵敏度设定 扫查灵敏度的设置应保证在屏幕上可以看到噪声
通常扫查灵敏度不应低于最小灵敏度 8.3.4信号指示的分析 如果不是由于铸件结构或者棚合条件变化,而造成回波指示变化,下面类型的回波信号需要进行 评估 面回波(底波)衰减; -缺陷回波
各种类型的波形指示有可能单独出现,也可能同时出现
背面回波衰减表现为背面回波的减弱(单 位为dB),缺陷回波的高度以平底孔或横通孔的直径来表示
除非另有规定或协议,否则当达到或超过表3给出的数值时,都应当进行评估,并且如果超过表4 和表5给出数值的75%,应进行记录
表3需要评估的超声指示 壁厚T 背面回波的衰减 最小平底孔或横通孔直径 反射波高于噪声" mm dB mm dB 12 10
GB/T31213.1一2014 9.2夹渣缺陷的质量分级 采用直探头进行检测,夹渣缺陷的质量分级见表5
面型和线型缺陷的质量分级 9.3 采用斜探头进行检测,发现面型和线型缺陷的质量分级见表6
表4体积型缺陷的质量分级 质量等级 类别 50一 50一 50一 5o >50 壁厚/mm 50 200 200 50 200 50 200 200 200 20 30 壁厚百分比/% 25 35 未超过 边缘区域最大不 1000 表3的600 10001000 20002000 连续"b/ /mm 指示 未超过 中心区域最大不 表3的100001500o1500015000200003000020000 连续/mm 指示 不连续总面积占未超过 检测表面的百表3的 10 15 15 15 20 20 15 20 30 30 40 分比/% 指示 关于夹渣参见表5
边缘区域,参见图6 表5夹渣缺陷的质量分级 质量等级 15 25 厚百分比/% 未超过表4的指示 10 20 表6面型和线型缺陷的质量分级 质量等级 壁厚T/mm 10
GB/T31213.1一2014 金相法和声速测量对比试验,可以得到球化率和材料声速的关系曲线,金相法球化率的检测及分级方法 按GB/T9441执行
球化率的超声检测结果应按测量到的声速给出球墨铸铁材料的球化率等级,检测结果应满足球墨 铸铁构件设计要求 11 检测记录和报告 1.1 记录 应按检测工艺规程的要求记录检测数据或信息,并按相关法规、标准和(或)合同要求保存所有 记录
检测时若遇不可排除因素的噪声干扰,应如实记录,并在检测结果中注明 11.2报告 超声检测报告至少应包括以下内容 a)铸铁构件使用单位、编号; 规格、几何尺寸、工作环境及使用年限 b 材料牌号,表面状态; 执行标准、参考标准 D 对比试件的材料、尺寸,缺陷的形状; 对比试件的距离-幅度曲线; 被检件的特征; 检测区域范围; h 检测设备;检测仪器名称、型号、探头、耦合剂等; 探伤工艺 灵敏度设置所需的必要数据 k 关于超声检测适用性的详细信息, lD 对不连续的特征(例如;背面回波衰减、壁厚方向的位置和尺寸、长度,面积以及当量)和位置 m 草图或照片)的描述及其缺陷位置示意图: n)球墨铸铁件球化率等级和材料声速 o结论 p)检测人员、报告编写人和审核人签字及资格证书编号 检测日期
q
无损检测铸铁构件检测第1部分:超声检测方法GB/T31213.1-2014
铸铁构件是工业生产中常用的一种零部件,其质量直接影响着机械设备的安全性和可靠性。因此,在生产和使用过程中需要对铸铁构件进行质量检测。
超声检测作为一种常用的无损检测方法,被广泛应用于铸铁构件的缺陷检测。在进行超声检测时,会使用超声波探头对被测物体进行扫描,并通过接收和处理反射回来的超声信号来判断物体内部是否存在缺陷。
国家制定了GB/T31213.1-2014《无损检测 铸铁构件检测 第1部分:超声检测方法》标准,该标准规定了铸铁构件超声检测的方法、设备和工具的选择,以及检测过程中需要注意的问题等。遵循该标准进行检测可以保证检测结果的准确性和可靠性。
除了遵循标准进行操作外,还需注意一些超声检测中常见的问题,如探头与被测物体表面的接触、杂音的干扰等。合理的操作方法和经验对于检测结果也有着至关重要的作用。
总的来说,超声检测是一种非常实用的无损检测方法,在铸铁构件的质量检测中具有重要应用价值。在进行检测时需要严格遵守国家制定的标准,并留意操作过程中可能出现的问题。