GB/T41056-2021
全断面隧道掘进机双护盾岩石隧道掘进机
Fullfacetunnelboringmachine—Doubleshieldhardrocktunnelboringmachine
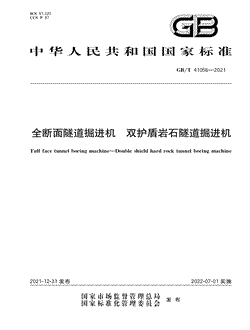
- 中国标准分类号(CCS)P97
- 国际标准分类号(ICS)91.220
- 实施日期2022-07-01
- 文件格式PDF
- 文本页数27页
- 文件大小2.15M
以图片形式预览全断面隧道掘进机双护盾岩石隧道掘进机
全断面隧道掘进机双护盾岩石隧道掘进机
国家标准 GB/T41056一2021 全断面隧道掘进机双护盾岩石隧道掘进机 Fulfaeetumnelboringmachine一Doubleshieldhardroektunnelboringmachine 2021-12-31发布 2022-07-01实施 国家市场监督管理总局 发布 国家标涯花管理委员会国家标准
GB/41056一2021 目 次 前言 范围 2 规范性引用文件 术语和定义 基本参数和型号 技术要求 试验方法 检验规则 19 随行文件 标志、包装和运输 20 刀盘理论扭矩计算方法 附录A资料性 21 22 附录B(资料性)掘进机理论推力计算方法 附录c资料性)带式输送机理论功率计算方法 24
GB/41056一2021 前 言 本文件按照GB/T1.1一2020<标准化工作导则第1部分;标准化文件的结构和起草规则》的规定 起草
本文件由机械工业联合会提出 本文件由全国建筑施工机械与设备标准化委员会(SAC/TC328)归口
本文件起草单位;石家庄铁道大学中船重工(青岛)轨道交通装备有限公司、中铁十八局集团有限 公司、北方重工集团有限公司、铁建重工集团股份有限公司、中铁工程装备集团有限公司、盾构及掘 进技术国家重点实验室、北京建筑机械化研究院有限公司,水利水电第三工程局有限公司、上海隧 道工程有限公司机械制造分公司、山东大学,中交天和机械设备制造有限公司大连理工大学、力信测量 上海)有限公司、天津大学、沈阳工业大学、沈阳建筑大学
本文件主要起草人:郭京波、杨绍普、唐希刚、王雁军、刘飞香、贺飞、丁永强、黄继敏、刘双、邓立营、 李术才,何恩光.沈建华,孙艳秋、张兵,杨辉,麻成标.霍军局,高振宅.郭志,刘振军,、宁向可,马肖丽、 潘存治杨延栋、张稳军,余辉文.刘斌,李刚、顾建江、郝如江、李福宝、吴海祥,朱福顺、周鹏
GB/41056一2021 全断面隧道掘进机双护盾岩石隧道掘进机 范围 本文件规定了全断面隧道掘进机中的双护盾岩石隧道掘进机的基本参数和型号、技术要求、试验方 法、检验规则、随行文件、标志,包装和运输 本文件适用于全断面隧道掘进机中的双护盾岩石隧道掘进机(以下简称掘进机)的设计、制造和使用
规范性引用文件 下列文件中的内容通过文中的规范性引用而构成本文件必不可少的条款
其中,注日期的引用文 件,仅该日期对应的版本适用于本文件;不注日期的引用文件,其最新版本(包括所有的修改单)适用于 本文件
GB/T150(所有部分压力容器 GB/T191包装储运图示标志 GB/T1985一2014高压交流隔离开关和接地开关 GB2893安全色 GB2894安全标志及其使用导则 GB/T3766液压传动系统及其元件的通用规则和安全要求 GB/T3956电缆的导体 GB/T4208外壳防护等级(IP代码 GB/T5226.1机械电气安全机械电气设备第1部分;通用技术条件 GB5226.3机械安全机械电气设备第11部分:电压高于1000Va.c.或1500Vd.c.但不超过 36kV的高压设备的技术条件 GB/T6388运输包装收发货标志 GB/T7932气动对系统及其元件的一般规则和安全要求 GB/T10595带式输送机 GB/T13283工业过程测量和控制用检测仪表和显示仪表精确度等级 GB T 13306标牌 GB 3384机电产品包装通用技术条件 GB l4039一2002液压传动油液固体颗粒污染等级代号 GB 4048.3低压开关设备和控制设备第3部分:开关、隔离器、隔离开关及熔断器组合电器 GB 14776 人类工效学工作岗位尺寸设计原则及其数值 GB 17301 土方机械操作和维修空间棱角倒钝 GB 9666阻燃和耐火电线电缆或光缆通则 GB T 19804焊接结构的一般尺寸公差和形位公差 GB/T20082液压传动液体污染采用光学显微镜测定颗粒污染度的方法 GB/T20840.2 互感器第2部分电流互感器的补充技术要求 GB/T20840.3互感器第3部分;电磁式电压互感器的补充技术要求 GB/T24337电能质量公用电网间谐波
GB/T41056一202 GB/T26802.1工业控制计算机系统通用规范第1部分;通用要求 GB/T34354一2017全断面隧道掘进机术语和商业规格 GB/T346522017 全断面隧道掘进机敞开式岩石隧道掘进机 GB/T346532017 全断面隧道掘进机单护盾岩石隧道掘进机 GBT37400.3重型机械通用技术条件第3部分:;焊接件 GB/T37400.10-2019重型机械通用技术条件第10部分;装配 GB/T37400.11重型机械通用技术条件第11部分;配管 GB/T37400.13重型机械通用技术条件第13部分;包装 GB50168一2018电气装置安装工程电缆线路施工及验收标准 GB501692016电气装置安装工程接地装置施工及验收规范 JB/T10205液压缸 术语和定义 GB/T34354一2017,GB/T34652一2017,GB/T34653一2017界定的以及下列术语和定义适用于 本文件
33 全断面隧道掘进机fulfacetumnelboringmachine 通过开挖并推进式前进实现隧道全断面成型,且带有周边壳体的专用机械设备
注:主要包括盾构机、岩石隧道掘进机、顶管机等
[来源;GB/T34354一2017,2.1,有修改] 3.2 岩石隧道掘进机 hardrocktunnelboringmachine 通过旋转刀盘并推进,使滚刀挤压破碎岩石,采用主机带式输送机出渣的全断面隧道掘进机
注1:包括敞开式岩石隧道掘进机、单护盾岩石隧道掘进机及双护盾岩石隧道掘进机等; 注2岩石隧道掘进机也称硬岩隧道掘进机或TBM [来源;GB/T34354一2017,2.13] 3.3 双护盾岩石隧道掘进机dobleshiedhardrektummeloringmaehne 具有护盾保护,依靠管片和/或撑靴撑紧洞壁以承受掘进反力和扭矩,掘进可与管片拼装同步的岩 石隧道掘进机
[来源:GB/T3435!一2017,2.16,有修改 3.4 公称直径nominaldiameter 开挖直径 eXcaVationdiameter 刀盘旋转一周,最外端设计初装滚刀刀刃形成轨迹的直径
[来源:GB/T34652一2017,3.4打 3.5 最大工作扭矩maximumworkingtorque 刀盘在工作转速范围内,主驱动单元能够输出的可持续工作的最大扭矩
[来源:GB/T34652一2017.3.5] 3.6 takim 脱困扭矩 brea ingouttorque 刀盘在最大工作扭矩工况下无法转动时,主驱动单元所能够短时输出的最大扭矩
GB/41056一2021 [来源:GB/T34652一2017,3.67 3.7 壁后回填系统backfillingsystem 用于填充隧道岩壁与管片外壁之间空隙的各种物料注人装置的总称
[来源:GB/T346532017,3.9 3.8 双护盾模式doubleshiedmode 通过支撑护盾内的撑靴撑紧洞壁为主推进系统提供反力和反力矩,利用主推进液压缸为刀盘提供 推力,掘进与管片拼装可以同时进行的工作模式
3.9 前护盾frntshield 盾体的前段
注在岩石隧道掘进机中又称前盾
[来源.(GB/T34354一2017,2.26,有修改] 3.10 伸缩护盾telescopicshiedl 位于前护盾和支撑护盾之间由相对运动的内,外两部分组成,可保护该区域内设备及人员安全的 环形壳体
3.11 支撑护盾supportshied 双护盾岩石隧道掘进机中用于安装撑靴、辅助推进系统的盾体部件
[来源:GB/T34354一2017,2.32 3.12 反扭矩装置reaetivetorqedeviee 位于前护盾和支撑护盾之间,用于抵抗护盾所受反向扭矩的装置
3.13 滚转调整装置rollinmgadjustmentdevice 位于支撑盾内,用于抵抗辅助推进缸所受盾体反向扭矩,控制护盾滚转角度的装置
3.14 稳定器stabilizer 安装于盾体上,通过伸出动作支撑于洞壁或地层实现稳定盾体的装置
[来源;GB/T34354一2017,2.89 3.15 撑靴系统grippersystemm 敞开式和双护盾岩石隧道掘进机中可撑紧洞壁承受掘进反力的系统
注,主要由钢结构架,液压缸,撑靴等组成 来源:GB/T34354一2017,2.33,有修改] 3.16 主推进系统mainthrustsystem 在双护盾模式下,用于推动掘进机前进的系统
注:主要由主推进液压缸、阀组、泵站、行程测量装置等组成
3.17 辅助推进系统ans uslary thrustsystem 用于双护盾岩石隧道掘进机在掘进与管片安装同步作业时顶紧管片的系统,也可作为推进系统
GB/T41056一202 注:主要由推进液压缸、组,泵站、行程测量装置等组成
[[来源;GB/T34354一2017,2.42,有修改 基本参数和型号 4.1基本参数 掘进机的主参数为公称直径/开挖直径,基本参数如下 公称直径/开挖直径,单位为毫米(mm); 总长度,单位为米(m); 总质量,单位为千克(kg); 主机长度,单位为米(m); 主机质量,单位为千克(kg); 适应管片规格,单位为毫米(mm); 最小水平转弯半径,单位为米(m); 适应最大坡度,(%); 装机功率,单位为千瓦(kw) 刀盘最大转速,单位为转每分(r/min); 刀盘驱动功率,单位为千瓦(kw); 刀盘滚刀数量,单位为把或刃; 最大推进速度,单位为毫米每分(G mm/min; 主推进系统最大推力,单位为千牛(kN); 辅助推进系统最大推力,单位为千牛(kN); 撑靴最大撑紧力,单位为千牛(kN); -最大脱困扭矩,单位为千牛米(kN
m -额定扭矩,单位为千牛米(kN m; -最小换步时间,单位为分(min); -掘进行程,单位为毫米(mm); -最大不可分割件质量,单位为千克(kg); -最大不可分割件尺寸(长×宽×高),单位为毫米(mm)
4.2型号 产品型号由产品代号和主参数组成,主参数为公称直径/开挖直径,其表示方法如下 主参数;用阿拉伯数字表示,单位为毫米(mm) 产品代号;用大写字母表示,由制造商自行规定 4.3结构示意图 掘进机结构示意图见图1
GB/T41056一2021 20 22 标引序号说明: 主机带式输送机 -刀盘; -反扭矩装置; 13 辅助推进液压缸; 18 溜渣槽; 外伸缩护盾; 14 滚转调整装置; 19 管片; 前护盾; 内伸缩护盾; 尾护盾 豆砾石注人系统 15 20 主驱动单元 10 饺接液压缸L; 16 超前钻机 221 压缩空气系统; 1 17 22 稳定器; 支撑护盾 管片拼装机; -注浆系统
12 主推进液压缸; 撑靴 图1双护盾岩石隧道掘进机示意图 技术要求 5 般要求 5.1 5.1.1公称直径/开挖直径偏差范围应为0 mm十4mm
5.1.2炽接件应符合GB/T37400.,3的规定
5.1.3装配应符合GB/T371400.10一2019的规定
5.1.4配管应符合GB/T37400.11的规定
5.1.5工地组装连接螺栓应达到设计预紧力矩要求
5.1.6 电气安全要求应符合GB/T5226.1,GB5226.3的规定 5.1.7掘进机在环境温度5C50C,相对湿度小于90%的环境条件下应能正常工作
5.1.8掘进机设计应为智能化制造、绿色环保、再制造提供条件
5.1.9部件不能满足运输或工程要求时应分块设计
5.2机械结构 5.2.1刀盘及刀具 5.2.1.1刀盘强度和刚度应符合设计要求
5.2.1.2刀盘本体尺寸公差应符合GB/T19804中B级的规定
5.2.1.3刀盘本体工作平面的平面度应符合GB/T37400.3中E级的规定
5.2.1.4刀盘应设置雾化喷水装置
5.2.1.5刀盘应具备更换刀具的吊装通道及空间
5.2.1.6刀盘正面、侧面与岩石直接接触表面应采取耐磨及保护刀圈措施
GB/T41056一202 5.2.1.7刀盘可更换刀具安装方式:刀盘直径小于4.5m时宜采用背装式,刀盘直径大于或等于4.5" 时应采用背装式 除刀盘最外端设计初装滚刀外,其他刀具的安装半径偏差范围应为 5.2.1.8 一2mm十2mm
mm十2mm
5.2.1.9中心刀及正滚刀刀刃高度偏差范围应为0n 5.2.1.10刀具与刀座结合面的间隙不应大于0.1mm. 5.2.1.11滚刀刀刃挡圈侧宜朝向刀盘中心位置
5.2.1.12铲斗和出渣槽应能满足最大掘进速度时的出渣需要
5.2.1.13刀盘刀具宜配置磨损检测装置或系统
5.2.2主驱动单元 5.2.2.1主轴承的设计寿命不应小于15000h
5.2.2.2应具有正反转功能
5.2.2.3应具有点动功能
应配置驻车制动器,驻车制动器与刀盘动作控制应具有联锁功能
5.2.2.4 5.2.2.5应具有脱困模式,脱困扭矩不应小于主驱动最大工作扭矩的1.5倍
5.2.2.6应具有良好的主驱动密封功能
工作转速应连续可调
5.2.2.7 5.2.2.8主驱动变频器、主驱动电机及减速箱宜采用水冷散热 5.2.2.9宜采用变频电机驱动
5.2.2.10刀盘实际配置的扭矩不应小于刀盘理论扭矩,刀盘理论扭矩的计算方法见附录A
5.2.3护盾 5.2.3.1护盾外径偏差和圆柱度应符合设计要求
5.2.3.2护盾强度和刚度应符合设计要求
5.2.3.3护盾结构应满足吊装、运输要求
5.2.3.4前护盾径向应配置稳定器,稳定器数量不应少于2个,各稳定器应具有独立控制功能
5.2.3.5前护盾与支撑护盾之间应设置反扭矩装置
5.2.3.6内,外伸缩护盾的结构和径向间隙应满足最小转弯半径的要求
5.2.3.7护盾外径应采用前大后小的设计
5.2.3.8护盾宜预设超前钻机作业孔,护盾内部空间应满足钻孔作业设备安装及操作要求
5.2.3.9应设置滚转调整装置
5.2.3.10内伸缩护盾应设置观察窗
5.2.3.11支撑护盾应满足撑靴移动要求
5.2.4管片拼装机 5.2.4.1应具有管片的抓持、提升,平移,回转及定位功能
5.2.4.2回转机构的小齿轮与回转轴承大齿轮啮合接触点不应低于GB/T37400.102019中6.3.4规 定的9级精度要求
5.2.4.3制动装置应能可靠制动
5.2.4.4应具备有线、无线两种控制方式,两种控制方式间应能互锁,无线遥控有效控制范围应覆盖工 作区域
GB/41056一2021 5.2.4.5沿周向顺时针,逆时针旋转角度不应小于200" 5.2.4.6当设有盾尾刷时,纵向行程应满足在隧道内至少更换一道盾尾刷的需要
5.2.4.7管片拼装平台应便于管片拼装作业
5.2.4.8在断电情况下,真空吸盘式管片拼装机应能保证吸持管片的时间不小于20min,且真空度不 低于80%
5.2.4.9采用机械锁固的管片拼装机抓取安全系数不应小于1.5,非机械锁固的管片拼装机抓取安全系 数不应小于2.5
5.2.4.10应进行载荷试验,静载试验载荷为最大管片重量的1.25倍,动载试验载荷为最大管片重量的 1.1倍
5.2.5连接桥及后配套拖车 5.2.5.1连接桥与管片拼装机行走梁的连接结构宜具有伸缩功能
5.2.5.2后配套拖车结构内净空尺寸应大于物料运输车辆最大通行截面尺寸100mm 5.2.5.3应设置作业平台
5.2.6 支撑及推进系统 5.2.6.1 双护盾模式的换步循环时间不应大于5 min
5.2.6.2撑靴接地比压不宜大于4MPa 5.2.6.3撑靴应具有防滑功能
5.2.6.4撑靴系统应具有高压撑紧缓动功能
5.2.6.5撑靴系统与主推进系统应具有联锁功能
5.2.6.6推进液压缸应符合JB/T10205的规定
5.2.6.7推进系统与主驱动单元应具有联锁功能
5.2.6.8推进液压缸分区数不应少于4组,各组应能进行独立的行程检测,推进液压缸分区的工作压力 应单独可调
5.2.6.9推进液压缸应具有快速伸缩功能,满足掘进速度的设计要求
5.2.6.10推进模式下的推进液压缸伸出速度应连续可调
5.2.6.11辅助推进液压缸的行程应满足管片拼装的需要,行程偏差范围应为-2mm~十2mm
5.2.6.12辅助推进液压缸的最大撑靴比压不应大于管片的设计强度
5.2.6.13掘进机推力应与工程地质相适应,掘进机理论推力的计算方法见附录B 5.2.7带式输送系统 5.2.7.1带式输送机应符合GB/T10595的规定
5.2.7.2主机带式输送机应具有调速功能
5.2.7.3主机带式输送机应设置防偏、除尘,张紧装置,接渣口应具有缓冲和防冲击功能
5.2.7.4宜设置主机带式输送机清渣装置
5.2.7.5主机带式输送机应设置急停开关及联锁装置,且能现地和主控室控制,并能互锁
5.2.7.6带式输送机出渣能力应满足掘进机最大掘进速度的要求,带式输送机理论功率计算见 附录c
GB/T41056一2021 5.2.8管片运输系统 5.2.8.1管片输送装置应能将管片从后部拖车区域运送至管片拼装机的抓取区域
5.2.8.2管片吊机抓取管片的安全系数应满足以下要求 采用机械锁固抓取时,不应小于1.5; a b 采用非机械锁固抓取时,不应小于2.5
5.2.8.3应进行载荷试验,静载试验载荷为最大管片重量的1.25倍,动载试验载荷为最大管片重量的 1.1倍 5.2.8.4管片吊机宜采用无线、有线两种控制方式 5.2.9壁后回填系统 5.2.9.1应满足最大掘进速度所需物料回填量要求
5.2.9.2应具有物料注人速度和流量的调节功能
5.3液压系统 5.3.1应符合GB/T3766的规定
5.3.2油液固体颗粒污染等级不应低于GB/T14039-2002规定的一/18/15
5.3.3液压油箱应设置液位及高温报警装置
5.3.4各子系统应设置测压点
5.3.5应设置滤芯堵塞报警装置
5.3.6应设置液压油冷却装置,冷却能力应能满足降温需要
5.3.7掘进机出厂前应进行液压系统的空载试验
5.4电气系统 5.4.1通用要求 5.4.1.1动力电缆及控制电缆应符合GB/T3956中5类及以上导体的规定 5.4.1.2电线电缆应符合GB/T19666的规定
5.4.1.3电线电缆敷设应符合GB501682018中6.1,6.3,6,4、7.1,7.2的规定
5.4.1.4高低压箱柜内电器设备、1kV及以下配电装置及二次回路的绝缘电阻值不应小于2MQ
5.4.1.5高压开关柜正面应留有安全操作空间,应有带电显示装置和防误操作联锁装置,能实现如下功 能要求 防止带负荷分、合隔离开关: a 防止误分,误合断路器,负荷开关、接触器 b 防止接地开关处于闭合位置时关合断路器,负荷开关 c d 防止在带电时,误合接地开关或挂接地线 防止误人带电间隔
e 5.4.1.6电气设备外壳防护等级不应低于GB/T4208规定的IP55
5.4.2供配电系统 5.4.2.1开关装置应符合GB/T1985一2014中ll.1、ll.2、ll.4、ll.5、ll.6、ll.7和GB/T14048.3的 规定
GB/41056一2021 5.4.2.2 干式电力变压器应设置三相绕组温度检测保护装置,油浸式电力变压器应设置油温保护装置
5.4.2.3变压器进线侧应设置避雷器
5.4.2.4变压器的进线侧开关应具有过载、短路保护功能
5.4.2.5变压器的进线侧开关应具有分/合闸、隔离和接地功能
5.4.2.6应在变压器的低压侧或者高压侧配置电能计量表,电能表的精度不低于GB/T13283规定的 0.5级,电压互感器的精度不低于GB/T20840.3规定的0.2级、电流互感器的精度不低于GB/T20840.2规 定的0.2s级 5.4.2.7TN电网的低压配电系统应具有漏电保护、短路保护,过载保护,缺相保护和相序保护功能
漏电保护不应少于两级,过载保护和短路保护不宜超过三级
5.4.2.8IT电网的低压配电系统应具备短路保护、过载保护功能,应采用绝缘监测系统实现漏电保护 功能
5.4.2.9低压配电系统平均功率因数不应低于0.9
5.4.2.10低压配电系统的谐波应符合GB/T24337的规定
5,4.2.11 接地系统应符合GB50169-2016中4.1~4.4的规定
5.4.3控制系统 5.43.1控制系统的电源应与动力回路隔离 5.4.3.2工控机应符合GB/T26802.1的规定
5.4.3.3人机界面语言应有中文显示
5.4.3.4功率超过30kw以上的电动机,宜采用软起动、变频起动或其他降压起动方式
5.4.3.5操作箱应具有与主控室操作的联锁功能
5.4.3.6应具有设备启、停次序和工作模式转换联锁功能
5.4.3.7继电器、接触器、电磁阀的控制回路,应配置过电压吸收器或续流回路 5.43.8控制系统中操作、指示器件的布置应符合GB/T14776的规定 5.4.3.9应具有护盾滚转极限角度报警功能
5.4.3.10控制系统应具备故障诊断与显示警示功能
5.4.4数据采集系统 应至少能采集以下掘进机数据;刀盘转速,刀盘扭矩、推进速度、掘进推力、主机倾角、推进液压 5.4.4.1 缸行程及施工环境气体含量
5.4.4.2应具有掘进数据采集,保存、查询、导出、打印功能
5.4.4.3应预留远程数据传输接口
5.4.5通信系统 5.4.5.1护盾内,壁后回填系统的设备操作箱位置,带式输送机卸渣口、主控室内、尾部拖车区域应配置 防护等级不低于IP55的电话机
5.4.5.2应预留主控室与洞外通信的接口
5.4.6视频监视系统 应在管片拼装区域、带式输送机卸渣口、尾部拖车位置、轨道铺设区域设置监视器
5.4.6.1 5.4.6.2应预留与洞外传输的接口
GB/T41056一2021 5.4.6.3应具有屏幕显示切换功能
5.4.7急停开关 5.4.7.1主控室、变压器处、后配套人员通道区域应配置急停开关,急停开关复位时不应直接恢复供电 5.4.7.2现地操作箱上应配置急停开关,急停开关复位时不应直接起动机构
5.4.8照明系统 5.4.8.1应设置独立的隔离变压器
5.4.8.2应选用密闭、防水的照明灯具
5.4.8.3人员通道和工作区域应配置应急照明设备,应急照明设备在外部断电后的照明时间不应少于 1h
5.4.8.4移动式照明电压不应大于12V
5.5导向系统 5.5.1宜采用激光靶式或棱镜式导向系统,全站仪测角精度不应低于2" 5.5.2应具有设计轴线管理功能,数据库轴线坐标列表导出功能 5.5.3应具有空间位置检测功能,包括相对设计轴线的水平和高程偏差
实际掘进姿态偏离设计轴线 最大限差时,导向系统应具有报警功能
5.5.4应具有姿态角度检测功能,包括掘进机前盾和支撑护盾的滚动角、俯仰角、方位角等姿态数据
5.5.5应配置工控机,工控机应具有图形显示功能,包括掘进机空间位置和姿态角度的实时数据 5.5.6应具有测量基点检核功能
5.5.7应具有与掘进机控制系统通信的功能
5.5.8应具有测量数据的历史查询、导出和报表功能
5.5.9应满足导向系统在直线段有效使用距离大于200m的要求
5.5.10应采取减振措施 5.6辅助系统 5.6.1通风及除尘系统 应配备二次通风系统,主机尾端的回风速度不宜小于0.5m/s
5.6.1.1 5.6.1.2储风筒风管储存长度不宜小于200m 5.6.1.3除尘器前的除尘风管应便于清理
5.6.2润滑及密封系统 5.6.2.1主驱动密封系统应采取强制润滑和冷却方式,并应设置流量报警装置 5.6.2.2主轴承润滑系统应采取强制润滑和冷却方式,并应设置温度、流量报警装置
5.6.2.3油脂注人系统应具备脉冲计数和空桶检测报警功能
5.6.2.4润滑系统宜采用逻辑控制,设置监控、联锁装置
5.6.3供排水系统 5.6.3.1主驱动电机、变频器、减速机宜采用强制水冷方式,并应设置温度、流量报警装置
5.6.3.2 应具有刀盘冷却、除尘喷水功能
10
GB/41056一2021 5.6.3.3应具有流量、压力,水位检测功能
5.6.3.4应配备管路延伸装置
5.6.3.5内循环介质宜采用软水
5.6.3.6应满足掘进作业排水需要 5.6.3.7供水能力不应低于刀盘喷水、冷却用水服务用水的压力和流量需要 5.6.4压缩空气系统 气动系统应符合GB/T7932的规定
5.6.4.1 5.6.4.2 三气压缩机额定压力不应低于0.8MPa
空 5.6.4.3应具有过滤、干燥功能
5.6.4.4应设置储气罐,储气罐应符合GB/T150(所有部分)的规定
5.7职业健康与环境安全 5.7.1应设置气体检测装置,至少能检测O.、CO.CH.CO.、HHS气体的浓度
5.7.2应在变压器、系和马达集中区域、供配电单元、控制室区域设置灭火器,并应根据可能的火灾类 型和确保掘进机安全要求选用合适的灭火剂
5.7.3声音报警装置输出的最低声压级应比施工环境噪声至少高出10dB(A). 5.7.4主控室应配置空调设备,并且具有隔热、隔音,减振功能,主控室内的噪声不应高于75dBA. 设置防护隔离装置
5.7.5电气设备应设置警告标志,高压电设备周 围 应 5.7.6易对人员造成伤害的外露运动部件应设置声光警示装置并有明确的颜色标识,标识颜色应符合 GB2893的规定
5.7.7应配置通畅的人行安全通道并有导向标志,标志应符合GB2894的规定
5.7.8日常操作和维修期间所需接触区域内的尖角和锐角应符合GB/T17301的规定
5.7.9物料易坠落的工作区域应设置安全防护装置
通道内有分支、转弯、台阶、坡道及重要出人口处均应有紧急疏散标志
5.7.10 5.7.11在后配套拖车的出人口处、主操作室内应设置醒目的紧急信息指示牌,指示牌应包括;疏散路 线、救护设备和灭火设备存放位置、灭火系统安装的示意图
试验方法 6.1试验条件 6.1.1试验场地应满足承载掘进机质量的要求
6.1.2试验环境温度5C35C,相对湿度40%70%
6.1.3试验用仪器仪表在试验前应进行检定或校准,仪器仪表包括;钢卷尺、钢直尺、游标卡尺、千分 尺,秒表、电流表,风速仪.电压表、绝缘电阻测试仪,油压表、硬度计,全站仪、声级计和温度计 6.2目测检查 6.2.1目测检查设备的布置状态、动作状态、显示状态及技术文件,目测检验项目如下: 喷水装置效果,反扭矩装置,防偏,除尘、,张紧装置,联锁、急停功能状况,回填能力,测压点设置,导 向系统精度,出口压力,空气过滤装置,电气设备警告标志,运动部件警示,安全通道标志,紧急疏散标 志,紧急信息指示牌
1
GB/T41056一202 6.2.2检查不拆解部件
6.3检测数据采集 试验检测时,单项数据采集不少于3次,并与规定值进行比对
6.4整机参数 6.4.1在刀盘安装在主机上的条件下,选定并标识水平及垂直方向基点,旋转刀盘,用全站仪或三维摄 影测量系统测量刀盘公称直径/开挖直径
6.4.2在推进模式下,用钢卷尺测量液压缸行程,用秒表计时,计算推进液压缸最大伸出速度,并与主 控室操作面板液压缸行程传感器数值及设计值比对
6.4.3推进系统最大推力按式(1)计算 F="×D'××Z×10 入 式中 F 掘进机最大推力,单位为千牛(kN); 主推液压缸无杆腔内径,单位为毫米(mm); D 主推液压缸最大压力值,单位为兆帕(MPa); 2 主推液压缸的数量
6.4.4调整刀盘从零至最大转速,在刀盘转速平稳后,用秒表记录旋转的时间,计算转速
6.5机械结构 6.5.1刀盘及刀具 6.5.1.1将刀盘本体水平放置于工作平台,用数显水平尺检查刀盘本体工作面的平面度
6.5.1.2刀具轨迹半径检测方法及步骤如下 a 将刀盘放置于水平平台上; b)将测量工装固定于刀盘中心,调整工装测量面使之水平; 直角尺紧靠刀盘刀具刀刃中心,见图2; c 测量直角尺对应工装上的刻度值; d 依次测量得出刀具轨迹半径尺寸r(i为刀具编号,i=1,2 n)值,并与设计值进行比对
12
GB/41056一2021 标引序号说明 -测量工装; -直角尺; -最外侧刀具 -刀盘本体; -水平基准面 图2刀具轨迹半径刀刃高度偏差检测示意图 6.5.1.3刀刃高度偏差检测方法及步骤如下 在刀盘水平放置状态下,将刀盘法兰面调至水平; a b)将测量工装固定于刀盘面板中心,调整工装测量面与刀盘法兰水平; 直角尺水平边紧靠测量工装,实刻线与刀具刀刃最高点中心线平齐,见图2; c d)记录直角尺对应工装上的刻度值、直角尺水平边到刀具最高点的刻度值 依次测出每件刀具的刀刃高度尺寸h值
e 6.5.1.4用塞尺检查刀具与刀座结合面的间隙
6.5.2主驱动单元 6.5.2.1空载运行刀盘,起动正转模式检查刀盘转动,用秒表测量刀盘旋转一圈所用时间,计算刀盘正 转转速,并与主控室操作面板数据比对
起动反转模式,检查是否具有反转功能
6.5.2.2点动状态下刀盘旋转,用秒表测量刀盘旋转一圈所用时间,计算刀盘转速
6.5.2.3起动停机保护制动器,在刀盘边缘施加最小5kN的偏心载荷,检查刀盘是否有转动
6.5.3护盾 6.5.3.1盾体外径偏差检测方法如下: 将盾体放置在水平平台上,初定测量中心,将测量工装安装于盾体顶部,见图3 a b 将线锤固定于测量工装上,距离盾体外圆约50mm处,使线锤方向与测量工装上的整数刻度 线重合 沿圆周每隔30"用钢直尺分别测出外圆面与线锤间距1,计算线锤对应刻度值与各测量值的差 值,得到盾体半径值,拟合盾体外圆轨迹,确定测量中心,将测量工装重新找正 d 再次测量值,计算出盾体半径值; e 计算出盾体外径
6.5.3.2盾体圆柱度检测方法如下 根据6.5.3.1的测量方法,分别测量a、b、c,d各点的值(ad位置的高度间隔约为三分之 a 盾体高度),见图3; b 根据ad各位置平面的测量值,计算最大值与最小值的差值,计算出盾体圆度:/am一/mn、 13
GB/T41056一202 -mm、lm一/am和lim,一laim,并与设计值进行比对; 根据a),b)的测量方法得出直线度和圆度的结果,计算出圆柱度
6.5.3.3伸缩护盾径向间隙检测方法如下 伸缩护盾安装前,厂内检测根据6.5.3.1和6.5.3.2的测量方法,分别测量内外伸缩护盾的沿圆 a 周每隔30°位置的外径; b 根据测量值,计算沿圆周每隔30°位置外径的差值,计算出伸缩护盾径向间隙
标引序号说明 护盾; 测量工装; -吊线锤; 水平平台面 图3护盾外径检测示意图 6.5.4管片拼装机 在空载状态下,将拼装机回转机构分别停留在0,.90,180",270"位置,进行提升、平移、支撑操 6.5.4.1 作;在抓紧管片状态下,将拼装机回转机构分别停留在0",390",18o",270"位置,进行提升、平移、支撑操 作,检查管片拼装机的功能
6.5.4.2在管片拼装机抓紧管片状态下,管片旋转过程中关闭动力源,检查制动性能
6.5.4.3纵向行程检测:用卷尺测量管片拼装机纵向最大移动距离,与设计值对比验证
6.5.4.4真空度检测:在管片拼装机抓紧管片状态下,切断动力源,20nmin后观察真空吸盘的真空表显 示值,与设计值对比验证
6.5.4.5静载试验在最不利工况下,抓持静载试件时间不应小于10min,观察管片拼装机抓取机构的 状态;动载试验抓持动载试件,分别进行全行程的提升、平移、回转及定位动作,观察管片拼装机的运行 状态,加速度和速度控制在设计范围内
6.5.5支撑及推进系统 6.5.5.1在单护盾模式下,控制和调整各分区辅助推进液压缸伸出及缩回,检查主挖室操作面板各分区 液压缸动作情况.并测量液压缸行程值
注,单护盾模式是指通过辅助推进液压缸顶紧管片端面为掘进提供推力和部分防滚转反扭矩,掘进与管片拼装不 能同时进行的工作模式
6.5.5.2在双护盾模式下,控制和调整主推进液压缸和撑靴油缸伸出及缩回,并测量主推进液压缸与撑 靴液压缸行程值
动作合格后,再检查辅助推进液压缸伸、缩动作情况
6.5.5.3在双护盾模式下,控制撑靴液压缸和主推进液压缸按换步顺序动作,测量换步循环时间
14
GB/41056一2021 6.5.5.4在双护盾模式下,分别操作主推进液压缸和辅助推进油缸全行程伸,缩,用秒表记录伸、缩时 间,计算得出伸,缩速度
6.5.5.5在推进模式下,依次伸出各分区带有位移传感器的推进液压缸,伸出过程中旋转推进速度旋 钮,观察控制面板速度显示值 6.5.6带式输送系统 带式输送系统在空载状态下,通过主控室操作面板,调节速度旋钮,检查调速性能
6.5.7管片运输系统 6.5.7.1在管片吊机的起始位置装人管片,起动行走机构,检查提升高度是否满足要求,观察行走动作 是否有卡滞现象,并检查管片吊机最终行程是否满足管片运输要求
6.5.7.2抓取静载试件,悬空高度不小于50mm,悬空时间不小于10min,观察吊机的状态;抓取动载 试件,至少观察3个吊运循环内吊机的运行状态,试验包括对各机构在整个运动范围内做反复起动和制 动,速度控制在设计范围内
分别用无线,有线控制方式操作管片吊机,检查操控动作是否与执行动作一致
6.5.7.3 6.5.8壁后回填系统 起动回填料运输系统,以水或压缩空气为介质,运行5min后,检查各回填料注人系统的压力限制 功能、速度调节功能
6.6液压系统 6.6.1液压油污染度检测按GB/T20082的方法进行
6.6.2设定温度传感器油温报警、停机试验值,起动液压系统,当油温升高至设定的报警试验值时,观 察控制面板报警指示,用温度计测量油温进行比较
当油温升高至设定的停机试验值时,检查主机停机 状况,用温度计测量油温进行比较
6.7电气系统 6.7.1供配电系统 6.7.1.1TN电网;逐一按压回路漏电保护装置的测试开关,观察开关是否跳开;合上开关后,观察是否 恢复回路供电
6.7.1.2IT电网:调定绝缘检测仪的绝缘电阻报警值,起动动力回路的电机,观察绝缘检测仪是否 报警
6.7.2控制系统 按照掘进机掘进起动次序,起动各机构,检查各机构起动状况
按正常次序按压停止按扭,检查各 机构停止状况
颠倒起动次序,检查各机构起动状况
6.7.3数据采集系统 6.7.3.1在主控室操作面板上观察掘进数据及图形,并进行查询历史数据、导出和打印的操作
6.7.3.2在掘进机掘进作业状态下,在地面监控室查看掘进数据和视频图像
6.7.4视频监视系统 6.7.4.1在主控室的监视器上,观察5.4.6.1规定区域的图像是否稳定、清晰
15
GB/T41056一202 6.7.4.2在掘进机掘进作业状态下,在地面监控室观察5.4.6.1规定区域的图像是否稳定,清晰
6.7.5急停开关 6.7.5.1在5.4.7.1规定的区域按压急停开关,观察掘进机的相应执行机构是否停止动作
急停开关复位 后,观察能否恢复系统供电;在配电柜上按压复位开关后,再合上电源总开关,观察系统是否恢复供电
6.7.5.2在5.4.7.2规定的区域按压急停开关,观察相应机构是否停止工作;急停开关复位后,观察机构 能否自行起动;在主控室或者操作箱上按下复位开关,再按机构的起动顺序起动,观察是否能正常恢复 机构动作
6.7.6照明系统 检查照明灯的配置及防护等级,灯具的防护等级查看产品说明书
6.8导向系统 6.8.1输人数据与设计数据允许的偏差值,模拟输人错误的设计轴线数据,使测量数据与设计轴线的 偏差大于允许误差,观察导向系统是否发出警告
6.8.2开始测量时导向系统是否能自动捕捉激光靶或者棱镜
6.8.3在导向系统工控机上进行数据查询、导出和生成报表的操作
6.9辅助系统 6.9.1在隧道施工及二 =次风机运行正常条件下,用风速仪检测主机尾端的回风速度 6.9.2调节油脂系排量,降低出口有效流量,观察主控室操作面板报警指示;继续调节排量,当有效流 量低于极限值时,检查主机停机状况
6.9.3调节齿轮油泵排量,增大溢流量.降低出口有效流量,观察主控室操作面板报警指示;继续调节 排量,当有效流量低于极限值时,检查主机停机状况
6.9.4将空桶接近开关动作调节至设定位置,运行密封润滑系统
当到达指定位置时,观察主控室控 制面板报警指示状况
6.10职业健康与环境安全 6.10.1使用O,CO,CH,CO.、HS标准气体对气体监测系统进行测试 6.10.2在掘进机掘进作业状态下,用声级计测量背景噪声,在距离声音警报装置1m的四周测量报警 装置的声压级
6.10.3在掘进机掘进作业状态下,用声级计测量主控室噪声
检验规则 7.1检验分类 掘进机检验分为出厂检验、工地检验和型式检验
7.2出厂检验 由制造商质量检验部门进行,检验合格后出具出厂检验合格证,出厂检验项目见表1
7.3工地检验 7.3.1工地检验包括工地组装检验和掘进检验 l6
GB/41056一2021 7.3.2工地组装完成后,进行工地组装检验
7.3.3在完成制造商和用户协议的掘进距离后进行掘进检验,检验合格后出具验收证书
7.3.4工地检验项目见表1
7.4型式检验 7.4.1有下列情况之一时,应进行型式检验 制造商或用户有需求时; a b)工艺,材料和结构有较大改变,有可能影响产品性能时 c 出厂检验与上次型式检验有较大差异时 d)国家市场监督管理部门提出型式检验要求时
7.4.2型式检验应检验表1规定的全部项目
7.5合格判定 全部检验项目合格,判定为合格
表1检验项目分类表 类别 工地检验 试验 出厂 技术 序号 检验项目 要求 方法 检验 分类 系统 工地组装检验掘进检验 公称直径/开挖直径 5.1.I 6.4.1 推进速度 6.4.2 辅助推进系统 整机参数 符合 设计值 最大推力 6,4.3 刀盘转速 6.4.4 5.2.1.3 6.5.1.1 刀盘本体平面度 喷水装置效果 6.2 5,2.1.4 刀盘及刀具 刀具安装半径偏差 5.2.1.8 6.5.1.2 刀具刀刃高度偏差 5.2.1.9 6.5.1.3 刀具与刀座间隙 5.2.1.10 6.5.1.4 查验计 10 主轴承设计寿命 5.2.2.1 算书 机 5.2.2.2 6.5.2.1 11 正反转功能 械 主驱动 12 5.2.2.3 6.5.2.2 点动功能 单元 构 13 制动功能 5,2,2.4 6.5,2.3 查验计 5.2.2.5 14 脱困扭矩 算书 护盾外径偏差 15 5,2.3.l 6.5.3.1 护盾圆柱度 5,2.3.l 6.5.3.2 1" 护盾 反扭矩装置 1 5.2.3.5 6.2 18 5.2.3.6 6.5.3.3 径向间隙 17
GB/T41056一2021 表1检验项目分类表续 类别 工地检验 技术 试验 出厂 序号 检验项目 要求 方法 检验 工地组装检验掘进检验 分类 系统 19 5.2.4.1 动作功能 6.5.4.1 5.2.4.3 6.5.4.2 20 制动功能 管片拼装机 纵向行程检查 5.2.4.6 6.5.4.3 22 真空度检测 5.2.4.8 6,5,4,4 23 载荷试验 5.2.4.10 6,5.4.5 符合设 24 撑靴行程 6,5,5,2 计值 5.2.6.8 6.5.5.2 25 主推进系统控制 5.2.6.9 6.5.5.4 26 主推进系统伸出速度 主推进系统速度连续可调5.2.6.10 6.5.5.5 支撑及推进 28 辅助推进系统分区控制 5.2.6.8 6.5.5.1 机 系统 29 辅助推进系统伸出速度 5.2.6.9 6.5.5.4 辅助推进系统速度 30 5.2.6.10 6.5.5.5 连续可调 符合设 31 换步速度 6,5.5,3 计值 调速功能 5.2.7.2 6.5.6 32 带式输送 33 防偏、除尘,张紧装置 5.2.7.3 6.2 系统 34 联锁、急停功能状况 5.2.7.5 6.2 35 管片运输 5.2.8.1 6.5.7.1 管片运输 载荷试验 36 5.2.8.3 6.5.7.2 系统 5.2.8.4 6.5.7.3 吊机控制 37 38 5.2.9.l 6.2 回填能力 壁厚回填 系统 39 5.2.9.2 6.5.8 速度和流量调节 40 油液固体颗粒污染 5.3.2 6.6.1 4 液压系统 油温报警装置 5.3.3 6.6.2 42 测压点设置 5.3.4 6.2 漏电保护功能 43 5.4.2.7 6,7.1.l 供配电系统 电 6.7.1,2 绝缘电阻报警功能 5.4.2.8 4 45 6.7.2 控制系统 联锁次序 5.4.3.6 46 数据收集功能 5.4.4.2 6.7.3.1 数据采集 系统 47 远程信息传输接口 5.4.4.3 6.7.3.2 18
GB/41056一2021 表1检验项目分类表(续) 工地检验 类别 试验 出厂 技术 序号 检验项目 要求 方法 检验 分类 系统 工地组装检验掘进检验 48 掘进机内置监控 5.4.6.1 6.7.4.1 视频监视 系统 电 49 远程监控接口 5.4.6.2 6.7.4.2 气 控制室急停开关 50 5,4.7.l 6.7.5,1 急停开关 操作箱急停开关 5 统 5.4.7.2 6,7.5.2 照明系统 2 灯具防护等级 6.7.6 5.5.1 6.2 导向系统精度 538 设计轴线管理 5.5.2 6,8,1 54 导向系统 空间位置检测 55 5.5.3 6.8.2 56 信息交换功能 5.5,7 6.8.3 7 通风、除尘 回风速度 5.6.1.l 6.9.1 58 主驱动密封润滑 5,6,2.l 6.9,2 辅 59 润滑、密封 主轴承润滑 5.6.2.2 6.9.3 助 5.6.2.3 6.9, 60 空桶检测功能 统 61 出口压力 5.6.4.2 6.2 压缩空气 62 空气过滤装置 5.6.4.3 6.2 63 气体检测 5,7.1 6.10.1 64 声音报警音量值 5,7.3 6,10,2 65 主控室噪" 5,7.4 6,10.3 电气设备警告标志 .7.5 6.2 66 安全要求 67 5.7.6 6.2 运动部件瞥示 68 安全通道标志 5.7.7 6.2 69 紧急疏散标识 5.7.1o 6.2 6.2 70 紧急信息指示牌 5.7.ll 随行文件 8.1随行文件应包括: 出厂检验合格证; 产品质量证明书 :, 品使用说明书 产品维护保养手册, 主要部件装配尺寸图 电气系统、液压系统、辅助系统原理图 外购主要部件随机资料 19
GB/T41056一202 -随机配件清单 易损,易耗件清单; 随机工具清单 8.2产品维护保养手册应包括产品的适用范围、结构功能说明、维护保养,以及操作规程等内容
标志、包装和运输 g.1标志 9.1.1警示标志 9.1.1.1警示标志应设置于醒目位置,并永久固定
9.1.1.2警示标志内容应不易被擦除
9.1.2标牌 标牌应符合GB/T13306的规定,在标牌上至少应标出如下内容 设备名称; 设备型号; 出厂编号; 整机质量; 制造商名称; 制造商地址
9.2包装和运输 g.2.1包装应符合GB/T13384及GB/T37400.13的规定.并适合陆路或水路运输及装载的要求 9.2.2包装储运图示标志应符合GB/T191及GB/T6388的规定,其主要内容包括 收货站及收货单位名称; 发货站及发货单位名称 鸡 “品名称和型号; 毛重、净重,箱号及外形尺寸; 起吊作业标志和储运图示标志
9.2.3掘进机运输应符合铁路、公路和航运的有关规定
20
GB/41056一2021 附 录 A 资料性) 刀盘理论扭矩计算方法 理论扭矩计算方法按公式(A.1) T=习(f×F×R,)+习T
A.1 式中 刀盘扭矩,单位为千牛米(kNm); 滚刀滚动阻力系数,一般取值0.1一0.15; F 滚刀额定承载能力,单位为千牛(kN) R -每把滚刀在刀盘上的回转半径,单位为米(m); T -摩擦扭矩,单位为千牛米(kNm)
21
GB:/T41056一2021 附 录 B 资料性 掘进机理论推力计算方法 B.1掘进机辅推进系统推力 掘进机辅推进系统推力理论计算方法按公式(B.1) Fr=K1×(F十F
十F十F B,1) 式中: 厂 掘进机辅推进系统推力,单位为千牛(kN) r K 储备系数,一般取K1=1.11.5; F -围岩和护盾间的摩擦阻力,单位为千牛(kN); F -后配套系统的拖动阻力,单位为千牛(kN); 厂 刀盘推进反力,单位为千牛(kN); F -盾尾刷与管片之同摩擦阻力,单位为干牛(h. B.2掘进机主推进系统推力 掘进机主推进系统推力理论计算方法按公式(B.2) F开=K,×(F,十F, (B.2 式中 掘进机主推进系统推力,单位为千牛(kN); Fzr 前护盾和外伸缩护盾受到的摩擦阻力之和,单位为千牛(kN)
Fs B.3围岩和护盾间的摩擦阻力 围岩和护盾间的摩擦阻力F按公式(B.3)计算 F=i×w B.3) 式中: 围岩与护盾间的摩擦系数,一般取0.3一0.5; A W 护盾受到围岩作用的全部径向压力,单位为千牛(kN B.4后配套系统的拖动阻力 后配套系统的拖动阻力F按公式(B.4)计算 (B,4 F
="×w. 式中 车轮和钢轨间的摩擦系数,一般取0.050.l; M2 W, 后配套系统总重,单位为千牛(kN. B.5刀盘推进反力 刀盘推进反力F
按公式(B.5)计算: (B.5 F=F×N 式中 F -滚刀额定承载能力,单位为千牛(kN); 22
GB/41056一2021 N -刀盘配置的滚刀数量
B.6盾尾刷与管片之间摩擦阻力 盾尾刷与管片之间摩擦阻力F,按公式(B.6)计算 F,=24×w B.6 式中 管片和盾尾刷之间的摩擦系数,一般取;=0.5; a W、 -环形管片的重量,单位为千牛(kN)
B.7岩石和前护盾,外伸缩护盾的摩擦阻力 岩石和前护盾,外伸缩护盾的摩擦阻力F
按公式(B.7)计算: F,=Fx 式中: 前护盾和外伸缩护盾总长,单位为米(m):; l 护盾总长,单位为米(m)
23
GB:/T41056一2021 附 录 C 资料性) 带式输送机理论功率计算方法 圆周力 C.1 圆周力按公式(C.1)计算: C.1) =CH.lg十g叫+(2A十ge刀十们,.成H十F,十F F,= 式中: F -圆周力,单位为牛顿(N); 系数; 模拟摩擦系数 -带式输送机长度,单位为米(m) 重力加速度,单位为米每二次方秒(m/s): g 承载分支托辐每米长旋转部分质量,单位为千克每米(kg/m); IRo 回程分支托辗每米长旋转部分质量,单位为千克每米(kg/m); -每米长输送带的质量,单位为千克每米(kg/m); n -每米长输送物料的质量,单位为千克每米(kg/m); ge 附加阻力,单位为牛顿(N) -提升高度,单位为米(m); P -特种主要阻力,托前倾摩擦阻力及导料槽摩擦阻力,单位为牛顿(N); F,
-特种附加阻力,清扫器,卸料器及反转回程分支输送带的阻力,单位为牛顿(N)
C.2 传动滚筒轴功率 传动滚简轴功率按公式(C.2)计算 (C.2 P八=F×u/1000 式中 P 传递滚筒轴功率,单位为千瓦(kW); 输送带速度,单位为米每秒m/s). C3 电机功率 电机功率按公式(C.3)计算 C.2 P=K×尸x/7 式中 电机功率,单位为千瓦(kw); 功率备用系数 K 传动效率
24
全断面隧道掘进机双护盾岩石隧道掘进机GB/T41056-2021
全断面隧道掘进机是目前用于隧道施工的重要设备之一。而双护盾岩石隧道掘进机则是其一个重要类型。为了规范这种设备的生产和使用,国家标准化管理委员会发布了最新版的关于全断面隧道掘进机双护盾岩石隧道掘进机的标准——GB/T41056-2021。
该标准规定了双护盾岩石隧道掘进机的基本要求、技术指标、测试方法、检验规则等内容。其中,标准明确了该机器应包括哪些部分,并对每个部分做了详细说明。同时,对于操作要求也进行了规定,以保证整个系统的安全性和有效性。
该标准还规定了双护盾岩石隧道掘进机应具备的功能和性能指标,例如:掘进机的外形尺寸、掘进直径、推进力等基本技术参数;同时还应该支持自动化掘进、高效节能、可靠性高等特点。此外,标准还对机器的可靠性、稳定性、安全性等方面做出了要求。
采用GB/T41056-2021标准的全断面隧道掘进机双护盾岩石隧道掘进机具有以下优点:
- 提高施工效率:采用自动化掘进方式,可以大幅度提高施工效率,降低人工成本。
- 降低安全风险:双护盾结构可以有效地防止坍塌和落石,提高施工安全性。
- 降低环境污染:采用高效节能的设计理念,可以减少对环境的污染。
- 适用范围广泛:该机器可用于各种类型的隧道掘进,具有很强的适应性。
总之,GB/T41056-2021标准为全断面隧道掘进机双护盾岩石隧道掘进机的制造和使用提供了明确的指导,使得该机器更加安全、可靠、高效。相信在不久的将来,这种先进的技术将会在隧道工程中被广泛应用。