GB/T38193-2019
汽车齿轮机床加工自动生产线
Machinetoolsautomaticproductionlineforautomobilegears
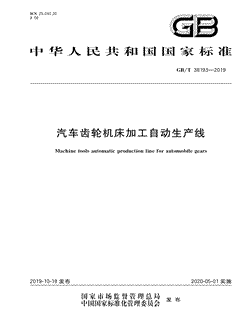
- 中国标准分类号(CCS)J56
- 国际标准分类号(ICS)25.040.20
- 实施日期2020-05-01
- 文件格式PDF
- 文本页数11页
- 文件大小716.06KB
以图片形式预览汽车齿轮机床加工自动生产线
汽车齿轮机床加工自动生产线
国家标准 GB/T38193一2019 汽车齿轮机床加工自动生产线 Machinetoolsautomatieproduetionlineforautomobilegears 2019-10-18发布 2020-05-01实施 国家市场监督管理总局 发布 币国国家标准化管理委员会国家标准
GB/38193一2019 前 言 本标准按照GB/T1.1一2009给出的规则起草
本标准由机械工业联合会提出
本标准由全国金属切削机床标准化技术委员会(SAC/TC22)归口
本标准起草单位:重庆机床(集团)有限责任公司国家机床质量监督检验中心、南京二机床有限责 任公司、天津第一机床有限公司、四川普什宁江机床有限公司宜昌长机科技有限责任公司
本标准主要起草人:曾令万、陈鹏、喻可斌、李毅、李先广,李祥文、张维、李光华、李红、柴宝连、 张勤、钟瑞龄
GB/38193一2019 汽车齿轮机床加工自动生产线 范围 本标准规定了汽车齿轮机床加工自动生产线设计、制造、检验和验收的要求
本标准适用于最大工件直径至260mm,主要完成车削、制齿,倒棱、去毛刺等工序的汽车齿轮机床 加工自动生产线(以下简称“自动线”) 规范性引用文件 下列文件对于本文件的应用是必不可少的
凡是注日期的引用文件,仅注日期的版本适用于本文 件
凡是不注日期的引用文件,其最新版本(包括所有的修改单)适用于本文件
GB/T4208一2017外壳防护等级(IP代码 GB/T5226.1一2019机械电气安全机械电气设备第1部分;通用技术条件 GB/T65762002机床润滑系统 GB/T7932-2017气动对系统及其元件的一般规则和安全要求 GB/T9061 2006金属切削机床通用技术条件 GB15760一2004金属切削机床安全防护通用技术条件 第5部分嗓声发射的确定 GB 17421.52015机床检验通则 23570一2009金属切削机床焊接件通用技术条件 GB GB T 235722009 金属切削机床液压系统通用技术条件 金属切削机床装配通用技术条件 GB/T253732010 金属切削机床清请度的测量方法 GB/T25374一2010 GB/T253762010金属切削机床机械加工件通用技术条件 工业自动化系统与集成机床数值控制数控系统通用技术条件 GB/T262202010 JB/T3736.7一1994质量管理中常用的统计工具工序能力指数 JB/T83562016机床包装技术条件 型式与组成 3.1型式 自动线按物流单元的搬运方式不同主要分为架机械手式和机器人式两种型式,示意图见图1、 图2
GB/T38193一2019 说明 -料仓1; 检测设备; 1 -加工设备1 -料仓2 加工设备2 控制单元; 衔架机械手 加工设备3. 图1析架机械手式自动线 说明 加工设备1 检测设备 加工设备2; -料仓1: -机器人; -料仓2; -加工设备3; 控制单元 图2机器人式自动线
GB/38193一2019 3.2组成 自动线一般由数控设备、物流单元、控制单元三大部分组成
其中 数控设备包括各类加工设备(车削机床,滚齿机、剃齿机、倒棱机等、检测设备以及清洗设备 a 需要时配备)等; b 物流单元包括衔架机械手或机器人.料仓、交换料道(需要时配备)等; 控制单元包括计算机、控制系统、传感器等
技术要求 4.1入线要求 自动线中的数控设备和物流单元中的惭架机械手(或机器人)在人线前应按各自相应的产品标准及 技术协议检验合格
4.2参数 自动线的参数应符合设计文件的规定
4.3布局和外观 4.3.1自动线应布局合理、造型美观、色彩和谐
4.3.2操作台应便于操作,操作按钮标志清晰,便于识别,符合人类工效学原则 4.3.3防护罩及防护装置应表面平整、匀称,不应翘曲、凹陷
4.3.4涂层颜色及光泽应均匀一致,涂层应平整,涂层表面不应有起泡及脱落等缺陷
4.3.5各种信息标志及标牌应在明显位置平整固定,清晰耐久,不歪斜
4.3.6其他应符合GB/T9061一2006中3.15及设计文件的规定
4.4性能与功能 4.4.1自动线的数控设备和物流单元之间的机械对接接口应互相适应
自动线中各工序加工设备的节拍需平衡,保证各加工设备使用率
4.4.2 4.4.3自动线控制单元的控制执行方式可采用总线集中控制或通过交互信号由物流单元的控制系统 执行
数控设备和物流单元间有上、下料请求信号,上、下料完成信号,循环,等待、故障、停机、节能模式 等信号的相互交换
自动线的数控设备应具有以下性能与功能 4,4.4 车削机床应有自动顶门,滚齿机(插齿机,剃齿机等制齿设备应有自动上下料机构 滚齿机(插齿机)应有滚(插)后去毛刺机构; b 加工设备应有刀具寿命管理及加工尺寸补偿的功能; 加工设备应具有自动排屑功能 d 工件在自动装卸夹紧放松过程中应有防止切屑黏附在定位面和夹紧部位的措施(吹气、气密检 测等)以保证定位准确和不损伤工件 各类夹具应为稳定可靠的自动夹具,必要时有工件到位检测功能
在加工两种或两种以上同 类工件时,要求的定位和夹紧部位尺寸差别不大,夹具应采用能快速且只更换最少零件的结构
GB/T38193一2019 形式
4.4.5自动线的物流单元应具有以下性能与功能 a 工件快速运行到位时应有缓冲功能; 运行应平稳,动作应准确可靠,其中析架机械手(或机器人)在抓取或放工件时应顺畅、无磕碰、 b 平稳 c 衔架机械手(或机器人)在上、下料过程中应具有缓冲功能 d 必要时,人工上料的物流单元应有防止工件放置错误的措施
4.5电气系统 自动线中的电气系统应符合GB/T5226.1-2019的规定
4.6数控系统 自动线中的数控系统应符合GB/T26220-2010的规定
液压、气动和润滑系统 4.7.1自动线的液压系统应符合GB/T235722009的规定
4.7.2自动线的气动系统应符合GB/T7932一2017的规定 4.7.3自动线的润滑系统应符合GB/T6576-2002的规定 4.7.4自动线的液压,润滑、气动系统的任何部位不应有渗漏
4.8安全卫生 4.8.1自动线的安全防护应符合GB157602004,GB/T5226.1一2019的规定
自动线的工作区应设置防护装置,同时便于操作者的观察
4.8.2 4.8.3 人工操作区域应与衔架机械手(或机器人)运动区域空间隔离,在重合区域应设置逻辑控制,并 应有硬件防护机构
气动系统应能提供稳定的正常工作的压力,当超出设定限值时,应发出警告信号或使 4.8.4液压系统、 自动线运动停止
4.8.5紧急停止后,急停按钮释放后报警解除,自动线不应自动起动
4.8.6加工设备的报警装置应设在易于观察的位置上
4.8.7析架机械手(或机器人)移动应设置可靠的限位装置,并应具备断电保护功能,防止因断电引起 的工件脱落和位移 4.8.8控制单元的电柜、操作台、操作盒等设备的防护等级应按GB/T4208一2017中IP54的规定
4.8.9在空运转条件下,自动线整线噪声声压级应不超过83dBA)
4.8.10自动线应排屑通畅,应能回收运行中产生的废油气,废油废水,确保24h以上连续正常运行
4.9加工和装配质量 4.9.1自动线的装配应符合GB/T25373一2010的规定
物流单元的机械加工件、焊接件应符合图样 工艺文件及GB/T25376一2010,GB/T23570一2009等的规定 4.9.2物流单元的齿轮齿条、导向杆,夹爪等零件应采取耐磨措施 物流单元的直线导轨等结合面,其制造及验收应符合图样、工艺文件及GB/T25376- 4.9.3 -2010和 GB/T253732010的规定
GB/38193一2019 4.9.4自动线不应有砂粒、铁屑、棉纱头等脏物
4.10空运转要求 4.10.1动作要求 动作要求一般包括下述内容 物流单元的每个工位运送工件(或工件托座)至架机械手(或机器人)抓取或放人位置的动作 aa 连续起动、停止各10次,动作应灵活、准确、无故障; 5 检验杵架机械手(或机器人)的工作进给、快速进给,检验杵架机械手(或机器人)在行程范围内 的任意给定位置的起动和停止,各检验10次,应准确可靠、无故障; 检验衔架机械手(或机器人)夹爪夹取、放置工件各10次,动作应可靠、工件无损伤 d 模拟工作状态,操纵整线“急停”按钮(或开关),连续10次,应准确无故障; 用数控程序操作,在中等速度下分别对各坐标轴进行正、反向起动、停止(或制动),工作进给、 快速进给,各进行10次,动作应灵活,准确、可靠; 按设计要求,对各坐标轴定位,进给坐标超程保护、坐标位置显示,回基准点、手动数据输人、程 序序号指示和检索、程序暂停,程序消除等功能分别进行试验,其功能应可靠、动作应灵活、 准确; 对安全防护装置进行试验,功能应可靠,动作应准确
g 4.10.2连续空运转要求 自动线模拟工作状态按设计规定的节拍进行整线连续空运转试验(带料不切削状态),其连续运转 时间不少于48h
在空运转过程中,各部分工作应正常,运行应平稳;各项功能、性能应可靠,不出现故 障,否则应重新进行连续空运转
4.11工作精度要求 自动线的工作精度有“直接评定”和“工序能力指数评定”两种评定方法,由制造厂与用户协议确定 工作精度的评定方法、评定的项目及要求 采用“直接评定”时的工作精度:自动线完成规定数量(不少于50件)被加工零件的连续切削加 a 工后,检验确定的评定项目,均应符合要求; b 采用“工序能力指数评定”时的工作精度:自动线完成规定数量(不少于50件)被加工零件的连 续切削加工后,检验并记录确定的评定项目的精度,按JB/T3736.7一1994的规定计算工序能 力指数,其结果应符合规定的要求
检验与验收 5.1概述 5.1.1每条自动线应在制造厂经检验合格后出厂
特殊情况下经用户同意可在自动线使用处进行检 验
当在自动线使用处验收时,其验收的项目由用户与制造厂商定
5.1.2自动线检验分为型式试验和出厂检验: 自动线在新试制、定型鉴定或结构、性能较基型有重大改动时,应进行型式试验
型式试验应 a 包含5.35.13的全部内容
GB/T38193一2019 D)出厂检验一般包括以下内容 参数检验(抽查); 布局与外观检验; 性能与功能检验; 自动线的空运转检验; 自动线的精度检验
5.2一般要求 5.2.1自动线检验时,应注意防止气流、光线和热辐射的干扰,应防止受环境温度变化的影响,自动线 应在常温下进行检验,检具在使用前应与自动线等温
5.2.2检验与验收前,应将自动线安置在适当的基础上,按照制造厂的使用说明书调整安装水平
5.2.3检验过程中,不应调整影响自动线精度和性能的机构和零件
自动线中用地脚螺栓紧固的部 分,在检验过程中不应重新调整安装水平
否则,应对调整后受影响的项目复检
5.2.4检验原则上是在制造完毕的成品上进行,特殊情况下可按制造厂的使用说明书拆卸某些零 部件
5.2.5自动线由于结构上的限制或不具备规定的测试工具时,可用与标准有等同效果的方法代替
5.3入线检验 检验自动线中的数控设备和物流单元中的析架机械手(或机器人)的出厂文件(使用说明书、合格证 明书、装箱单),结果是否符合4.1的要求
5.4参数检验(抽查》 按产品使用说明书或技术协议规定的参数核对自动线的参数,结果是否符合4.2的要求
5.5布局和外观检验 采用目测和图样检查方式检验自动线的布局和外观,结果是否符合4.3.1一4.3.6的要求
5.6性能与功能检验 5.6.1按工艺要求将被加工零件在数控设备和物流单元间进行交互检验,结果是否符合4.4.1的要求
5.6.2按设计规定的节拍进行自动线整线连续空运转各工序加工设备检验,结果是否符合4.4.2的 要求
5.6.3按自动线控制单元的控制执行方式检验数控设备和物流单元,结果是否符合4.4.3的要求
5.6.4在自动线整线连续空运转过程中,检验自动线的数控设备和物流单元,结果是否符合4.4.4和 4.4.5的要求
5.7电气系统的检验 -2019规定检验自动线的电气系统,结果是否符合4.5的要求 按GB/T5226.1 5.8数控系统的检验 按GB/T26220-2010规检验自动线的数控系统,结果是否符合4.6的要求
GB/38193一2019 5.9液压、气动和润滑系统的检验 检验自动线的液压、气动和润滑系统,结果是否符合4.7.1一4.7.4的要求
5.10安全卫生检验 -2019规定的方法检验自动线的安全防护装置,结果是否符 5.10.1按GB15760一2004,GB/T5226.1一 合4.8.1的要求
5.10.2采用目测方式检验自动线的工作区的防护,结果是否符合4.8.2的要求
5.10.3采用目测和实测方式检验人工操作区域与惭架机械手(或机器人)运动区域,结果是否符合 4.8.3的规定
5.10.4采用目测和实测方式在自动线整线连续空运转过程中检验液压系统、气动系统,结果是否符合 4.8.4的要求
5.10.5按下紧急停止按钮后检验自动线结果是否符合4.8.5的要求
采用目测方式检验加工设备的报警装置,结果是否符合4.8.G的要求
5.10.6 5.10.7采用目测和实测方式检验析架机械手(或机器人),结果是否符合4.8.7的规定 5.10.8按GB/T42082017中IP54规定的方法,检验控制单元的电柜、操作台,操作盒等设备的防护 等级,结果是否符合4.8.8的要求
5.10.9在空运转条件下,按GB/T17421.5-2015规定的方法检验自动线整线噪声,结果是否符合 4.8.9的要求
5.10.10采用目测和实测方式检验自动线的排屑及运行中产生的废油气、废油、废水的回收,结果是否 符合4.8.10的要求
5.11加工和装配质量检验 5.11.1采用目测和/或检查图样方式检验自动线的装配、物流单元的机械加工件和焊接件,结果是否 符合4.9.1的要求
5.11.2采用目测和/或实测方式检验物流单元的齿轮齿条、导向杆、夹爪等零件,结果是否符合4.9.2 的要求
采用实测和/或检验图样方式检验物流单元的直线导轨等结合面结果是香符合4.9.3的要求 5.11.3 5.11.4按GB/T25374一2010规定的目测法和手感法检验自动线的清洁度,结果是否符合4.9.4的 要求
5.12空运转检验 5.12.1动作检验 在自动线整线连续空运转时,检验自动线的动作,结果是否符合4.10.1的要求
5.12.2连续空运转检验 自动线模拟工作状态按设计规定的节拍,进行不少于48h的连续空运转(带料不切削状态)检验 结果是否符合4.10.2的要求
5.13工作精度检验 按符合被加工零件工序图及节拍要求的切削规范和刀具,对被加工零件进行连续切削加工,连续加
GB/T38193一2019 工不少于50件(若因故障停止,需排除故障后重新开始),检验自动线的工作精度,结果是否符合4.11 的要求
6 包装 6.1自动线在包装前,应进行防锈处理 6.2自动线的包装应符合JB/T83562016的规定
出厂的自动线包装箱内应提供一套随机技术文件
自动线随机技术文件应至少包括使用说明 6.3 书、合格证明书和装箱单,必要时还应提供自动线的维修配件目录等技术文件
自动线随机技术文件的 编制方法宜符合GB/T235712009的规定
GB/38193一2019 参 考文献 [1]GB/T23571一2009金属切削机床随机技术文件的编制
汽车齿轮机床加工自动生产线GB/T38193-2019解析
汽车齿轮是汽车传动系统中不可或缺的关键部件之一。随着汽车工业的快速发展,对于齿轮的质量和精度要求也越来越高。为了提高齿轮的制造效率和质量,越来越多的企业采用自动化生产线进行生产。
GB/T38193-2019标准发布,为汽车齿轮机床加工自动生产线的生产、检测和应用提供了更加明确的技术规范。该标准覆盖了自动生产线的各个方面,从设备选型、控制系统设计、工位布置等进行详细规定,旨在提高生产线的稳定性和生产效率。
在自动生产线的设计中,设备选型是关键的一步。GB/T38193-2019标准要求自动生产线中使用的机床、刀具、测量仪器等必须具有高精度、高效率和高可靠性的特点。此外,标准还对自动生产线的控制系统进行了规定,包括对传感器、执行器、控制器等的要求。
自动生产线的工位布置也是影响生产效率和质量的关键因素之一。GB/T38193-2019标准规定,自动生产线的各个工位应该布置得合理,使得生产过程中材料、零部件的运输路径最短,从而提高生产效率。此外,标准还规定了安全防护措施、环保要求等方面的内容。
通过将自动化生产线应用于汽车齿轮制造中,可以大幅提高生产效率和质量稳定性,同时减少对人工操作的依赖。目前国内很多企业已经开始引入自动化生产线,不仅能够有效提升生产效率,而且降低了制造成本。
总的来说,GB/T38193-2019标准的发布对于提高汽车齿轮机床加工自动生产线的技术水平、促进行业发展具有重要意义。未来,我们可以期待更多智能化、数字化的制造方案问世,为汽车制造行业的发展注入新的动力。