GB/T34882-2017
钢铁件的感应淬火与回火
Inductionhardeningandtemperingofironandsteelparts
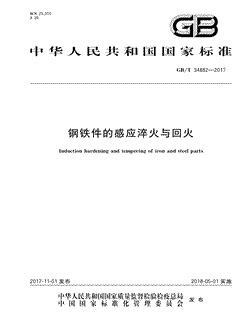
- 中国标准分类号(CCS)J36
- 国际标准分类号(ICS)25.200
- 实施日期2018-05-01
- 文件格式PDF
- 文本页数13页
- 文件大小827.10KB
以图片形式预览钢铁件的感应淬火与回火
钢铁件的感应淬火与回火
国家标准 GB/T34882一2017 钢铁件的感应淬火与回火 Inductionhardeningandtemperingofironandsteelparts 2017-11-01发布 2018-05-01实施 中华人民共利国国家质量监督检验检疙总局 发布 国家标准化管理委员会国家标准
GB/34882一2017 前 言 本标准按照GB/T1.1一2009给出的规则起草
请注意本文件的某些内容可能涉及专利
本文件的发布机构不承担识别这些专利的责任
本标准由全国热处理标准化技术委员会(SAC/T75)提出并归口
本标准主要起草单位:江苏丰东热技术有限公司、北京机电研究所、盐城高周波热炼有限公司、山东 天瑞重工有限公司,天津市热处理研究所有限公司,湖北三环锻造有限公司
本标准主要起草人:孙戍东、李俏、向建华、李永胜、宋宝敬、代合平
GB/34882一2017 钢铁件的感应淬火与回火 范围 本标准规定了钢铁件表面感应淖火与回火的质量控制、安全卫生及劳动保护的基本要求
本标准适用于钢铁件表面感应淬火与回火和感应淬火的热处理工艺
规范性引用文件 下列文件对于本文件的应用是必不可少的
凡是注日期的引用文件,仅注日期的版本适用于本文 件
凡是不注日期的引用文件,其最新版本(包括所有的修改单)适用于本文件
GB/T230.1金属材料洛氏硬度试验第1部分;试验方法(A,B,c,D,E,F,G,H,K,N,T标 尺 GB/T699优质碳素结构钢 GB/T1182产品几何技术规范(GPS)几何公差形状、方向、位置和跳动公差标注 GB/T1220不锈钢棒 GB/T1221耐热钢棒 GB/T1222弹簧钢 GB/T1298碳素工具钢 GB/T1299工模具钢 GB/T1348球墨铸铁件 GB/T3077合金结构钢 GB/T4340.1金属材料维氏硬度试验第1部分;试验方法 GB/T4341.1金属材料肖氏硬度试验第1部分;试验方法 GB/T5216保证透性结构钢 GB/T5617俐的感应痒火或火焰痒火后有效硬化层深度的测定 6967工程结构用中高强度不锈钢铸件 GB 金属热处理工艺 GB/T7232 术语 GB/T8121 热处理工艺材料术语 GB8702电磁环境控制限值 GB/T9439灰铸铁件 GB/T9440可锻铸铁件 热处理炉有效加热区渊定方达 GB/T9452 GB/T10201热处理合理用电导则 GB/T11352一般工程用铸造碳钢件 GB/T12603金属热处理工艺分类及代号 GB/T1331锻钢冷轧工作锯通用技术条什 GB/T13324热处理设备术语 GB15735金属热处理生产过程安全、卫生要求
GB/T34882一2017 GB/T15822.1无损检测磁粉检测第1部分;总则 GB/T16923钢件的正火与退火 GB/T17358热处理生产电耗计算和测定方法 GB/T18254高碳铬轴承钢 GB/T18449.1金属材料努氏硬度试验第1部分;试验方法 GB/Z18718热处理节能技术导则 GB/T19944热处理生产燃料消耗计算和测定方法 GB/T30822热处理环境保护技术要求 GB/T32541热处理质量控制体系 3593热处理状态粉末冶金铁基结构材料 JB B/T4120大型锻造合金钢支承辐 B/T6955热处理常用淬火介质技术要求 JB/T9204 钢件感应淬火金相检验 JB/T9205珠光体球墨铸铁零件感应淬火金相检验 JB/T9218无损检测渗透检测方法 术语和定义 GB/T7232,GB/T8121,GB/T13324,GB/T9452,GB/T16923中界定的以及下列术语和定义适 用于本文件
3. 感应淖火与回火indetiohardeningandtempering 以钢铁件全部或部分的表面硬化为目的,通过感应加热加热到Ae或Ae点以上温度,以适当的 冷却介质冷却(许火);随后为调节硬度和增加韧性,在回火炉中或以感应加热的方法加热到Ae点以 下的适当温度后冷却回火)
3.2 畸变distortion 相对于待处理工件,热处理后工件形状或尺寸发生的变化 感应淖火与回火工艺代号 钢铁件表面感应淬火与回火工艺代号应符合GB/T12603的规定,其工艺代号为521-04
5 待处理工件 5.1常用材料 感应淬火与回火工件常用材料应为符合表1中列出的各种牌号或与其化学成分相当的材料
5.2待处理工件的状态 5.2.1根据表2规定的项目记录待处理工件的状态,并予以保存
5.2.2根据表3规定的项目记录待处理工件的外观,形状、尺寸及精度,并予以保存
GB/34882一2017 表1感应淖火与回火工件常用材料 类 别 牌 25,30,35,40,45,50,55,60o 优质碳素结构钢GB/T699 25Mn,30Mn,35Mn,40Mn,45Mn,50Mn,6oMn,70Mn 保证淬透性结构钢GB/T5216 45H,40CrH,45CrH,40MnBH,45MnlBH,42CrMoH 30Mn2,35Mn2,40Mn2,45Mn2,50Mn2 27SMn,35SiMn,42SiMn,37SMn2MoV; 40B,45B,50B,40MnB,45MnB,40MnVB 30Cr,35Cr,40Cr,45Cr,50Cr,38CrSi,30cCrMo,30CrMoA,35CrMo,42CrMo. 合金结构钢GB/T3077 35CrMoV,38CrMoA,40CrV,50CrVA,40CrMn; 30CrMnSi,30CrMnSiA,35CrMnSiA,40CrMnMo,30CrMnTi,40CrNi,45CrNi. 50CrNi,30CrNi3,37CrNi3,40CrNiMoA,45CrNiMoVA 65,70,85,65Mn,70Mn,55SiMnVB60S2Mn,60Si2MnA,60Si2CrA, 弹簧钢GB/T1222 A.30wCGr2vA .55CrMnA,60CrMnA.50CrA.60CrMnBA
60Si2CrVA,55SiCrA GCr4,GCrl5,GCrl5SiMn,GCr15SiMo,GCr18Mo 高碳铬轴承俐GB/T182514 T7,T8,T8Mn,T9,T10,Tl1,T12,T13 碳素合金钢GB/T1298 9SiCr,8MnSi,Cr2,9Cr2; 工模具钢GB/T129 Crw2si,5Crw2si,6Ccrw2si,6CrMnSi2MolV,5Crw2siv 9Mn2V,9CrWMn,CrWMn,MnCrWV,7CrMn2Mo,7CrSiMnMoV 不锈钢棒GB/T1220 12Crl2,20Crl3,30Crl3 耐热钢棒GB/T1221 42Cr9Si2,45Cr9Si3,40Crl0Si2Mo,80Cr20S2Ni 锻钢冷轧工作GB/T13314 8Cr2MoV,9Cr2,9Cr2Mo,9Cr3Mo,9Cr2MoV -般工程用铸造碳钢GB/T11352G230-450,ZG270-500,ZG310-570,ZG340-640 中高强度不锈钢铸件GB/T6967 G20Crl3 灰铸铁GB/T9439 HT200,HT225,HT250,HT275,HT300,HT350 可锻铸铁件GB/T9440 KTZ450-06,KTZ500-05,KTZ550-04,KTZ600-03,KTZ650-02 Qr0018.Qr0015,Qr5010.Qr5007 Qr003.Qr700-2.QTr800-2 球墨铸铁GB/T1348 QT900-2 粉末冶金铁基结构材料JB/T3593Fo112,Fo113J,Fo122J,Fo123J,Fo202,Fo203 注1,保证悴透性结构钢及各种合金钢铸件参照表中所示牌号或化学成分,相当者可选用
注2:渗碳钢(牌号参照GB/T34889)经渗碳后采用感应淬火与回火处理时,也适用本标准有关内容
注3,碳素结构钢锻件参照优质碳素结构俐牌号
合金钢锻件铸件参考合金结构钢的化学成分 注4,必要时可提出特殊要求
GB/T34882一2017 表2待处理工件的状态 项 说 明 1)待处理工件的各检验记录 工件材料的类别" 化学成分 钢种代号 拉伸试验数据" 硬度测试数据" 透性试验记录 金相组织检验记录 晶粒度、脱碳层深度、碳化物、非金属夹杂物、显微组织及低倍组织 烧结密度测试数据 经过压制加工的烧结材料还应明确密度差 2)待处理工件的制造方法 铸造 烧结" 锻造 有冷、热加工之分 轧制 有冷、热加工之分 冲压 有冷,热加工之分 钣金加工 有冷、热加工之分 有冷、热加工之分 拉拔 有冷、热加工之分 型轧 有冷、热加工之分 挤压 热套 含厚度校正 焊接 机械加工 必要时还应明确加热温度、保持时间及冷却方法 3)待处理工件的预处理及工艺 正火 锻造余热火 完全退火 球化退火 去应力退火 调质 渗碳 渗氮 4)待处理工件的表面成形及其矫正程度 切削方法及条件 矫正的程度 有冷、热加工之分 确定对感应火处理无妨碍时,也可省略
关于钢铁类烧结材料,还应明确气孔大小及分布,微观组织均质程度,含油率等
也包括渗碳火回火、碳氮共渗淬火回火
GB/34882一2017 表3待处理工件的外观,形状和尺寸 有无裂纹.伤痕、锈斑、黑皮,毛刺及油污 1)工件的外观 (2)工件的质量 )工件的形状 特殊形状、厚度差异、孔穴的形状与位置 (3 4)工件的尺寸 工件尺寸及处理范围的尺寸 (5)工件的精度" 参考;精度包括尺寸公差,形状公差,方向公差,位置公差,其中形状公 差指直线度、平面度、,圆度、圆柱度、线轮廓度及面轮廓度;方向公差指 平行度,垂直度,倾斜度;位置公差指位置度,同心度,同轴度及对称度 6)处理部位的表面粗糙度 喷砂或喷丸 7)清理方法" (8)防锈剂的种类" 该项目见GB/T1182
对一般件可部分或全部省略 确定对感应淖火处理无妨碍时,也可省略 5.3待处理工件的交接验收 待处理工件在交接时应按照5.l和5.2要求的项目进行确认,必要时对重点项目进行复检
感应火与回火设备 6.1感应加热电源 6.1.1感应加热电源可采用真空管式、晶闸管式或晶体管式,应能产生适宜快速加热所需的输出功率 及频率,由配备的输出侧或输人侧的控制装置,在状态保持条件下,对应于设定的电压和功率,所控制的 输出电压和输出功率应满足表4所示的精度要求
表4感应加热电源的控制精度 电源种类 功率 电压 晶闸管式、晶体管式 士2% 士4% 真空管式及其他 士2.5% 士5% 6.1.2配备时间控制系统,对加热时间进行控制
在满足表5要求的系统精度条件下,应能保持和调 整时间参数
时间控制系统精度包含触摸屏、可编程控制器、输出继电器等
表5时间控制系统精度 时间范围/s 综合精度/s S0.10 <0.15
GB/T34882一2017 6.2感应淬火机械装置 感应淬火机械一般包括固定式淬火机械、移动式淬火机械或其他与待处理工件的形状相适应的淬 火机械,须保持或调整至表6规定的精度
表6感应淬火机械装置的精度 检验项目 精度 主轴锥孔径向跳动 S0.2mm 回转工作台面的跳动 0.2mm 顶尖连线对滑板移动的平行度 mm(夹持长度<2000mm) 0.3 士2% 工件进给速度变化范围 将检验棒插人主轴锥孔.在跑主轴端面300mm处测量
安装直径>300mm的圆盘,在150nmm半径处测量
安装直径$50mm长为500mm的圆棒时测量的结果
对不能装人长500mm试件,应等效校正至该条件
6.3淖火冷却设备 根据待处理工件的材料种类、形状、尺寸不同,可选用符合JB/T695规定的水.,油,水溶性淳火 6.3.1 剂等不同的悴火介质
各冷却系统中使用的悴火介质的温度波动应符合表7所列的许可范围
表7淬火介质的使用温度允许偏差 悴火介质 水溶性淖火剂 心 油 士1o 士20 士10 温度波动许可范围/t 6.3.2火冷却槽应有足够的容积,并应配备适当的淬火介质循环装置及温度调节装置
喷液淖火冷 却时冷却介质的压力和流量应能够调整,浸液悴火的冷却槽应配备使淬火液具有一定流速的搅拌装置 或具有同样效果的装置
6.3.3淬火冷却设备应配备冷却时间控制装置
喷液淬火时,在冷却开始继电器启动后,冷却介质应 能快速到达工件表面进行淬火冷却
6.4回火设备 6.4.1炉类回火设备按照表8选择相应等级的加热设备,其温度均匀性和系统准确度等要求应符合 GB/T3254l的规定要求
表8炉类回火设备的等级 加热设备等级 加热区温度/ 重要件 般件 MA MA 400 川A 400 6.4.2感应加热回火设备应满足6.1和6.2的规定要求
GB/34882一2017 6.5设备维护与管理 设备维护应遵守操作规程和维修保养制度,并保存相关记录,保证设备满足6.16.4的精度和使 用性能,其管理应符合GB/T32541中关于感应热处理设备中的相关要求
感应淬火与回火工艺过程及操作 7.1待处理工件 按5.2的要求对待处理工件的材料,状态、形状,尺寸和外观进行检查和确认
待处理工件的表面 不应有影响感应加热淖火与回火的氧化皮、毛刺、油污,必要时进行去氧化皮、去毛刺和洗净处理
7.2感应淬火与回火设备 7.2.1检查和确认感应电源处于通电状态,无异常报警.冷却水流通正常.处于加热待机状态
7.2.2设定设备冷却水槽温度,确认各部分冷却水流动正常无泄漏;根据制定的热处理工艺设定淬火 液槽温度,淬火液管道系统无泄漏,用手动开关或按钮确认空载淬火液流量
7.2.3检查控制和操作系统通电状态,无异常报警
7.2.4在手动模式下检查设备各部分运转机构的动作
7.2.5根据制定的热处理工艺,通过设备的控制和操作系统界面,预先设置对应于待处理工件的程序 包括淖火加热和回火加热输出功率或输出电压值、淬火和回火加热时间、位置或位移参数、淬火冷却时 间、回火冷却时间、各动作步骤等必要的参数和步骤
7.3感应器和冷却器 选用合适待处理工件的感应器和冷却器,进行安装
7.3.1 7.3.2检查确认感应器的变形、破损以及导磁体的状态是否满足加工要求
7.3.3检查感应器与输出变压器间的连接状态,确认接触良好
7.3.4检查和清理冷却器(冷却环、套)出水口,保证畅通
7.3.5安装冷却器后,在手动模式下调整和确认淬火液流量
7.4工件的装夹 7.4.1选用合适待处理工件的装夹夹具,进行安装
7.4.2检查装夹夹具(包括防变形加压夹具)的状态,并确认动作正常
7.4.3装夹时应严格保持工件与感应器的相对位置正确,特别是应当注意偏心和倾斜,以保证加热与 冷却的相对均匀,且避免因为工件的局部加热引起的膨胀、畸变导致感应器与工件间的接触放电等故 障
必要时用量具或专用检具检查工件与感应器之间的间隙
7.5感应火加热与冷却 7.5.1选取对应待处理工件的程序,根据制定的热处理工艺,确认程序中的各参数(加热输出功率或电 压、,加热时间、淖火冷却时间等)和动作步骤设置是否正确
7.5.2根据制定的热处理工艺设定和确认加热输出功率或电压、淬火液流量、移动速度等参数的监视 值范围
7.5.3在满足“全复位状态”和“电源准备完成”的状态下,按下“开始”按钮或开关进行单循环或多循环 处理
7.5.4为控制工件畸变必要时也可采用加压淬火
GB/T34882一2017 7.6回火加热与冷却 7.6.1为避免发生开裂、畸变和其他缺陷工件淬火后应及时回火,也可采用自回火的方法
7.6.2选择感应加热回火方式时,使用对应待处理工件的回火感应器和冷却器,选取对应的程序,按照 与7.5中规定的同样步骤进行操作
7.6.3选择回火炉方式时,根据制定的热处理工艺设置回火加热温度、保温时间后进行回火处理
7.6.4根据工件的技术要求,有时会省去回火
在省去回火或采用感应回火方式的情况时,为避免工 件出现裂纹等缺陷,应根据工件的材料、形状,处理条件等进行相应处理
7.7矫直处理 热处理后对需矫直的工件应确保矫直产生的残余应力不妨碍后续机械加工与使用,必要时进行去 应力处理
去应力处理应保证工件的性能
7.8记录 按规定和工艺要求对处理工艺进行记录,并妥善保管
如省去回火时,应记录此事项 质量要求与检验 8 8.1外观 已处理工件表面不应出现因感应淬火引起的微裂纹、熔融、烧伤及影响使用的划痕、磕碰等缺陷 外观检验采用目测,根据G;B/T15822.1或JB/T9218规定的任一方法检查裂纹 8.2表面硬度 已处理工件的表面硬度检查可根据GB/T230.1,GB/T4340.1,GB/T4341.1,GB/T18449.1的规 定,选择适宜的硬度计进行测试
其硬度偏差值应符合表9、表10和表11列出的允许范围
表11应 符合JB/T4120的规定,仅适用于某些大型工件
表g洛氏硬度偏差范围 表面硬度/HRc 单件 工件的类型 同一批件 50 5060 >60 50 506o >60 重要件 5 <4.5 <4 6 <5.5 5 6 -般件 6 5.5 5 6.5 表10维氏硬度或努氏硬度偏差范围 表面硬度/HV或HK 单件 工件的类型 同一批件 s500 500 500 500 二55 75 重要件 85 l05 <75 <105 C95 125 一般件
GB/34882一2017 表11肖氏硬度偏差范围 表面硬度/HS 工件的类型 单件 --批件 同 80 80 80 -80 重要件 <6 <8 <1o 8 -般件 8 <1o <10 12 注1:各硬度值是用不同的硬度计测得的结果,各表中的硬度值无直接换算关系
维氏或努氏硬度的施加载荷由委 托与受托双方协商确定
注2,单件的硬度偏差指的是工件在同样淖火回火或淖火条件下其形状、尺寸相同的部位,除了悴火范围边界的硬 化部位范围内的偏差基
注3同一批件指用同一批待处理工件在同一操作条件下处理得到的处理完成品总称
注4:具体硬化部位范围由委托方与受托双方协商确定
8.3有效硬化层深度 8.3.1感应淬火层深度一般按照有效硬化层深度要求和检验
简单形状工件的有效硬化层深度偏差 范围应符合表12的规定
8.3.2有效硬化层深度测试按GB/T5617,JB/T9205或委托受托双方协商规定执行
8.3.3复杂形状和大型工件的有效硬化层深度经双方商定,允许有较大的偏差范围
表12有效硬化层深度的偏差范围 硬化层深度波动范围/mm 有效硬化层深度/mm 单件 同一批件 0." 0.4 1.5一2.5(含2.5)>1.5<2.5 0,4 0,6 2.5~3.5(含3.5 0.6 0.8 0.8 3.55.0(含5.0 l.0 l.0 1.5 >5.0 注;有效硬化层深度在用范围的形式要求时,计算偏差使用范围的中间值
8.4金相组织 金相组织检验应根据材料在JB/T9204或JB/T9205中的规定进行
进行金相组织检验时,根据 工件材料的种类不同,其组织应是与各种使用目的相适应的正常组织,不应存在因感应加热引起的晶粒 显著长大、表层脱碳和过烧等缺陷
8.5畸变 已处理工件的尺寸变化应确保不影响随后的机械加工与使用
具体畸变量尺寸要求由委托与受托 双方协商确定
GB/T34882一2017 g 质量验收 验收时对于已处理工件的外观、表面硬度、硬化层深度、金相组织及畸变量检查应满足第7章和 第8章的规定
硬化层深度的检查允许用相同材料相似试样进行
金相组织检验可以根据委托与受托 双方协商确定
1C 安全卫生与劳动保护要求 10.1感应淬火与回火过程的安全卫生防护应符合GB15735的有关规定
10.2感应加热设备电磁辐射职业暴露限值应符合GB8702规定 11 能源消耗与环境保护要求 感应淬火与回火过程的能源消耗应符合GB/Z18718,GB/T10201,GB/T17358,GB/T19944的 有关规定
环境保护技术要求应符合GB/T30822规定
12 产品报告单 交货单或产品报告单中应包括下列内容: 工件名称和图号; 工件用材料牌号(或代号); 处理工艺代号 数量或质量; 质量检验结果; 处理单位全名或其简称; 处理日期;年月日