GB/T34880.3-2018
五轴联动加工中心检验条件第3部分:技术条件
Inspectionconditionfor5-axissimultaneousmachiningcenter—Part3:Specifications
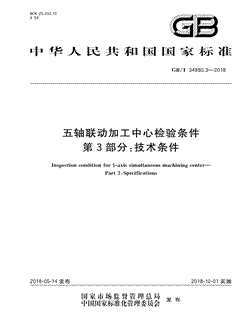
- 中国标准分类号(CCS)J54
- 国际标准分类号(ICS)25.040.10
- 实施日期2018-12-01
- 文件格式PDF
- 文本页数17页
- 文件大小1.24M
以图片形式预览五轴联动加工中心检验条件第3部分:技术条件
五轴联动加工中心检验条件第3部分:技术条件
国家标准 GB/34880.3一2018 五轴联动加工中心检验条件 第3部分:技术条件 nspeetionconditionfor5-axissimultaneowsmachiningcenter Part3Specifications 2018-05-14发布 2018-12-01实施 国家市场监督管理总局 发布 币国国家标准化管理委员会国家标准
GB/T34880.3一2018 次 目 前言 范围 2 规范性引用文件 -般要求 安全卫生 加工和装配质量 机床的空运转试验 机床连续空运转试验 机床负荷试验 最小设定单位试验 原点返回试验 10 机床精度检验 12 12包装和随机文件 13 参考文献
GB;/T34880.3一2018 前 言 GB/T34880《五轴联动加工中心检验条件》分为3个部分 第1部分:卧式机床精度检验; -第2部分:立式机床精度检验; 第3部分:技术条件
本部分为GB/T34880的第3部分
本部分按照GB/T1.1一2009给出的规则起草 本部分由机械工业联合会提出 本部分由全国金属切削机床标准化技术委员会(SAC/TC22)归口
本部分起草单位;机集团昆明机床股份有限公司,国家机床质量监督检验中心.,四川普什宁江机 床有限公司、南通航智装备科技有限公司、沈阳机床(集团)有限责任公司
本部分主要起草人何春树,朱祥、李祥文、张勤、薛佳南张维、李军、罗永华
GB;/T34880.3一2018 五轴联动加工中心检验条件 第3部分:技术条件 范围 GB/T34880的本部分规定了五轴联动加工中心的设计,制造、检验和验收要求
本部分适用于线性行程至2000mm的五轴联动加工中心(以下简称机床)
线性轴线行程超过2000mm的五轴联动加工中心也可参照使用
规范性引用文件 下列文件对于本文件的应用是必不可少的
凡是注日期的引用文件,仅注日期的版本适用于本文 凡是不注日期的引用文件,其最新版本(包括所有的修改单)适用于本文件
件
GB/T3167一2015金属切削机床操作指示图形符号 机械电气安全机械电气设备第1部分;通用技术条件 GB5226.12008 GB/T6576一2002机床润滑系统 GB/T7932一2003气动系统通用技术条件 GB/T9061一2006金属切削机床通用技术条件 GB15760-2004 金属切削机床安全防护通用技术条件 GB 16769 金属切削机床噪声声压级的测定方法 2008 18400.92007 加工中心检验条件第9部分;刀具转换和托板转换动作时间的评定 GB GB 235702009 金属切削机床焊接件通用技术条件 GB 2009 23571 属切削机床随机技术文件的编制 GB 235722009 金属切削机床液压系统通用技术条件 235752009 GB 圆锥表面涂色法检验及评定 GB 253732010 装配通用技术条件 GB 253742010 金属切削机床清洁度的测量方法 GB/T253752010 金属切削机床 结合面涂色法检验及评定 金属切削机床机械加工件通用技术条件 GB/T253762010 五轴联动加工中心检验条件第1部分;卧式机床精度检验 GB/T34880.1一2017 五轴联动加工中心检验条件第2部分;立式机床精度检验 GB/T34880.22017 -般要求 3.1概述 按本部分验收机床时,还应对GB/T9061一2006,GB/T253732010,GB/T25376一2010等标准 中未经本部分具体化的有关项目进行检验
3.2附件和工具 3.2.1应随机供应表1所列的附件和工具
GB/T34880.3一2018 表1 称 数量 调整垫铁 全套 专用调整工具 1套 3.2.2扩大机床使用性能的特殊附件,根据用户要求按协议提供
安全卫生 4.1机床的安全防护应符合GB15760一2004的有关规定
4.2机床液压系统的安全应符合GB/T23572一2009的规定
4.3机床电气系统的安全应符合GB5226.1一2008的规定 4.4按GB/T16769一2008的规定测量机床噪声,在空运转条件下噪声声压级不应超过表2的规定
表2 机床质量 >10 机床噪声声压级 80 83 dB(A 5 加工和装配质量 5.1床身、立柱、工作台,托板、主轴箱、滑座,滑鞍、主轴头体为重要铸件(焊接件,在粗加工后应进行 时效处理或采取其他消除应力措施(如;振动时效处理等)
必要时在半精加工后再进行一次时效处理 5.2机床导轨副,主轴、主轴套筒、丝杠副凸轮、高速齿轮、重载齿轮等零部件的易磨损部位应采取与 寿命相适应的耐磨措施
5.3焊接零部件应符合GB/T23570一2009的规定
重要的焊缝应进行探伤检验,不应有裂纹
5.4镶钢导轨应进行探伤检验,不应有裂纹
5.5重要固定结合面应紧密贴合,紧固后用0.04mm塞尺检验时不应插人
下列结合面为重要固定结 合面: 滚动直线导轨与其安装基面的固定结合面 a b 镶钢导轨与其安装基面的固定结合面; 滑动导轨压板的固定结合面; 前、后床身的固定结合面; d 立柱与床身的固定结合面; 立柱与横梁的固定结合面; 立柱与立柱滑座的固定结合面 g h 摆动主轴头(摇摆工作台)与其基体的固定结合面;
GB;/T34880.3一2018 电机与其相配的结合面
5.6特别重要固定结合面应紧密贴合,除用涂色法检验外,在紧固前、后用0.03mm塞尺检验时均不应 插人(与水平面垂直的特别重要固定结合面只在紧固后检验)
下列结合面为特别重要固定结合面 滚珠丝杠托架的固定结合面 a b 螺母座的固定结合面; 端齿盘的固定结合面; C 摆动主轴头与主轴箱的固定结合面 d 摇摆工作台支座与床身的固定结合面
e 5.7重要固定结合面和特别重要固定结合面,用塞尺检验时,允许局部(1处~2处)插人深度小于结合 面宽度的1/5,但不大于5mm;插人部位的长度小于或等于结合面长度的1/5,但不大于100mm则按 1处计
5.8下列导轨副应按“滑(滚)动导轨”的要求考核 各直线运动导轨副; a b)回转工作台与上滑座环形导轨副
5.9滚动直线导轨安装基面应符合设计文件的规定,组装后运动应轻便,灵活,无阻滞现象
5.10滑动导轨表面除用涂色法检验外,还应用0.04mm塞尺检验,塞尺在导轨、镶条、压板端部的滑动 面间插人深度不应大于表3的规定
表3 机床质量 塞尺插人深度 mm 10 20 25 l0 5.11两配合件的结合面均是刮研面,用配合件的结合面(研具)做涂色法检验时,刮研点应均匀
按规 定的计算面积平均计算,在每25mm×25mm的面积内,接触点数不应少于表4的规定
表4 滑滚)动导轨 每条导轨宽度 镶条、压板滑动面 特别重要固定结合面 mnm 二250 >250 抄 触 点 数 10 5.12两配合件的结合面一个是刮研面,另一个是机械加工面,用配合件的机械加工面检验刮研面的接 触点数时,不应少于表4中规定点数的75% 5.13采用机械加工方法加工的两配合件的结合面,采涂色法检验时,接触应均匀
检验与评定方法应 按GB/T25375一2010的规定进行,接触指标不应低于表5的规定
GB/T34880.3一2018 表5 滑滚)动导轨 镶条非刮研面与其相配合的结合面 重要(特别重要)固定结合面 接 触 指 标 全长上 全长上 全长上 全宽上 全宽上 全宽上 70 70 80 70 50 45 5.14当采用多段拼接的镶钢导轨,床身导轨其接合处宜留有0.02mm一0.04mm的缝隙,接合处导轨 导向面的错位量不应大于表6的规定
表6 机床质量 导轨导 向 面错位量 mm s10 0.003 >10 0.005 当采用贴塑和涂层导轨与基体应贴合紧密,粘接牢固可靠,不应有缝隙和气泡;与相配导轨的接 5.15 触应均匀,并应符合技术文件规定;导轨边缘应倒角修圆
5.16各运动坐标的滚珠丝杠副、数控回转工作台,组装后应进行多次运转,未补偿的反向间隙不宜大 于表7的推荐值 表7 线性轴线的反向间除 回转轴线的反向间除 mm 15 0,03 5.17拉刀机构及其他重要机构所用的碟形弹簧,组装后应按图样或设计文件规定进行压力试验
5.18重要的压力油缸,组装后应按系统设计压力的1.5倍进行不少于0.5h的保压试验,不应有渗漏 现象
5.19高速旋转的主轴组件,装配后应进行动平衡试验,平衡品质应符合设计文件的规定
带轮的平衡 应符合设计文件的规定
5.20机床采用电主轴、力矩电机或直线电机时,应配置恒温冷却装置,使用的介质和介质的压力、流 量、温度应符合相关的规定.不应有渗漏现象
5.21主轴箱、滚珠丝杠支撑座和螺母座等重要的定位销,其接触长度不宜少于锥销工作长度的70%, 并应均布在接缝的两侧
机床主轴装配后,其锥孔应按GB/T23575一2009用量规做涂色法检查,锥孔的接触应靠近大 5.22 端,实际接触长度与工作长度的比值不应低于80%;电主轴实际接触长度与工作长度的比值不应低 于85%
5.23按GB/T25374一2010抽查机床总装后的清洁度,其主轴箱和液压箱内部清洁度按重量法进行 检验(抽检)
单位体积中脏物的重量,冷却箱不应超过400mg/L液压箱不应超过150mg/儿L
其他部
GB;/T34880.3一2018 位用目测、手感法进行检查,不应有明显脏物
5.24机床操作指示形象化符号应符合GB/T3167一2015的规定,面板上的数字刻字及表征功能的文 字符号和标志,应清晰端正
5.25机床电气系统的装配应符合GB5226.1一2008的有关规定
5.26机床液压系统的装配应符合GB/T23572一2009的有关规定 5.27机床气动系统的装配应符合GB/T7932一2003的有关规定
5.28机床润滑系统的装配应符合GB/T6576一2002的有关规定 机床的空运转试验 6.1温升试验及主运动和进给运动检验 6.1.1机床主运动机构应从最低转速起依次运转,应做包括低、中,高速在内的不少于10种转速,各种 转速的运转时间不应少于2min,最高转速运转时间不应少于1h,使主轴轴承达到稳定温度,并在靠近 主轴定心轴承处测量温度和温升,其温度不应超过60,温升不应超过30C
在各种转速运转时,工 作机构应平稳,可靠,在最高转速运转时,不应有周期性的冲击声 6.1.2液压系统在额定工作压力下使系统连续运行,至油液达到热平衡后即油温温升幅度每小时不 大于2),检验油液的温度和温升,按GB/T23572一2009中6.2的规定其温度不应超过55C,温升不 应超过25 6.1.3在空运转条件下,机床主轴各级转速的实际偏差,不应超过公称值的士10%. 6.1.4各线性轴线和回转轴线上的运动部件,分别用低、中,高进给速度及快速进行空运转试验,其运 动应平稳、可靠、高速无振动,低速无明显爬行现象
各级进给速度的实际偏差,不应超过设计给定值的 -2%十6%
6.1.5当运动部件高速进给或快速移动时,只在除行程两端之外2/3行程上进行试验
其移动应平 稳、灵活,无明显爬行和振动,限位应可靠
6.1.6机床主传动系统的空运转功率(不包括主电动机空载功率)不应超过设计文件规定
6.2机床功能试验 6.2.1手动功能试验用手动或数控手动方式操作机床各部件进行试验 6.2.1.1对主轴连续进行不少于5次的锁刀、松刀和吹气的动作试验,动作应灵活、可靠、准确
6.2.1.2对主轴在中速时连续进行10次正、反转的启动、停止(包括制动)和定向的操作试验,动作应灵 活、可靠
6.2.1.3主轴至少应进行包括低、中、高转速在内的变速操作试验,动作应灵活、可靠
6.2.1.4各线性轴线和数控回转工作台,摆动主轴头,摇摆工作台的运动部件,用中等进给速度连续进 行各10次的正、负向启动、停止的操作试验,并选择适当的增量进给进行正向、负向的操作试验,动作应 灵活、可靠、准确
6.2.1.5对进给系统在低、中,高进给速度和快速范围内,进行不少于10种的变速操作试验,动作应灵 活、可靠
6.2.1.6对数控回转工作台,摆动主轴头,摇摆工作台的运动部件连续进行各10次的松开、夹紧,连续 分度试验,动作应灵活、可靠、准确
6.2.1.7对托板连续进行10次的交换试验,动作应灵活、可靠,托板交换时间应符合设计规定
托板交 换时间的评定应符合GB/T18400.9一2007的有关规定
6.2.1.8对刀库,机械手以任选方式进行换刀试验
刀库上刀具配置应包括设计规定的最大重量、最大
GB/T34880.3一2018 长度和最大直径的刀具
换刀动作应灵活、可靠、准确,机械手的承载重量和换刀时间应符合设计规定
刀具交换时间的评定应符合GB/T18400.92007的有关规定 6.2.1.9对机床数字控制的各种指示灯、控制按钮、DNC通信传输设备和温度调节装置等进行空运转 试验,动作应灵活,可靠
6.2.1.10对机床的液压、气动、润滑、冷却系统进行密封润滑冷却性能试验,功能应可靠,动作应灵 活、准确,各系统应无渗泄)漏现象
6.2.1.11对机床的安全、保险,防护装置以及电气系统的控制、联锁、保护功能进行试验,功能应可靠
动作应灵活、准确
6.2.1.12对机床的各附属装置进行试验,动作应灵活、可靠
6.2.2数控功能试验用数控程序操作机床各部件进行试验 6.2.2.1主轴中速运转的试验内容与6.2.1.2相同
6.2.2.2主轴变速操作的试验内容与6.2.1.3相同
6.2.2.3各线性轴线和回转轴线上的运动部件,用中等进给速度连续进行正向、负向的启动、停止和增 量进给方式的操作试验,动作应灵活、可靠、准确
6.2.2.4对各进给系统至少进行低、中,高进给速度和快速的变速操作试验,动作应灵活、可靠
6.2.2.5对数控回转工作台、摆动主轴头、摇摆工作台的运动部件连续进行各10次的松开、夹紧连绒 分度试验,动作应灵活、可靠、准确
6.2.2.6对托板进行不少于5次的交换试验,动作应灵活、可靠
对刀库总容量中包括最大重量刀具在内的每把刀具,以任选方式进行不少于2次的自动换刀 6.2.2.7 动作试验,动作应灵活、可靠
对机床的坐标联动、坐标选择、机械锁定、定位、直线和圆弧插补,螺距,间隙、刀具补偿,程序暂 6.2.2.8 停、急停等指令,刀具的夹紧、松开,以及液压、冷却、气动、润滑系统的启动、停止等数控功能逐一进行试 验,其功能应可靠,动作应灵活、准确
6.2.2.9对具有夹紧机构的运动部件应分别在各自行程范围内的任意工作位置上(一般选3个5个 位置)进行夹紧试验,动作应可靠、稳定 机床连续空运转试验 7.1用包括机床主要加工功能的数控程序,模拟工作状态做不切削的连续空运转
整机连续空运转时 间应不少于48h
每次循环时间应不大于15nmin,各次循环之间的休止时间不应超过0.5min
7.2连续空运转的整个过程中,机床运转应正常、平稳、可靠,不应发生故障,否则应重新进行运转
7.3连续空运转程序中应包括下列内容: 主轴包括低、中,高转速的正、反向运动和定位,其中高速运转时间一般不少于每个循环程序所 a 用时间的10%
各坐标上的运动部件应包括低,中,高进给速度和快速移动的正、负向运动,运行应在接近全行 b 程范围内,并可选任意点进行定位
运行中不允许使用倍率开关
高速进给速度和快速移动 时间一般不少于每个循环程序所用时间的10%
五轴联动的坐标联动运行时间,一般不少于每个循环程序所用时间的50%
d 刀库中各刀位上的刀具不少于2次的自动换刀
数控回转工作台,摆动主轴头、,摇摆工作台上运动部件的自动分度和定位
各托板不少于5次的自动交换
各坐标轴线的联动运行
8
GB;/T34880.3一2018 h 特殊附件的联机运转
机床负荷试验 8.1工作台承载工件最大重量的运转试验(抽查 可用与设计规定的承载工件最大重量相当的重物作为工件置于工作台上,使其载荷均匀,按下列规 定进行试验,运行应平稳、可靠,低速应无明显爬行现象 以最低进给速度,分别在工作台行程两端和中间位置往复进行运转,每处移动距离不少于 20mm
以最高进给速度和快速移动,在除行程两端之外的2/3行程上进行运转,分别往复 1次和5次
回转工作台B轴置于0",以最低的回转进给速度分别进行正、反方向不少于3min的运转试 b 以最高的进给速度分别向正、反向各转动一周(即360)为一次往复运转,进行5次往复运 验
转试验
回转工作台A轴置于0",最低的进给速度,分别绕A轴正、反方向摆动工作台,运行时间不少 于3min
以最高的进给速度绕A轴摆动工作台,分别在正、反向全行程范围内至少进行5次 往复摆动试验
8.2主传动系统最大扭矩的试验(适用于机械式主轴) 8.2.1在机床主轴恒扭矩范围内,选用一适当的主轴转速,采用铁削或瞠削方法进行试验
改变进给 速度或切削深度,使机床达到设计规定的最大扭矩
8.2.2切削试件材料为HT200或45钢,切削刀具硬质合金端铁刀或硬质合金瞠刀 8.2.3试验时,机床传动系统和变速机构工作应平稳、正常,可靠
8.3主传动系统最大切削抗力的试验(适用于机械式主轴 8.3.1在机床主轴恒扭矩范围内,选用一适当的主轴转速,采用钻削或锂削的方法进行试验
改变进 给速度或切削深度,使机床达到设计规定的最大切削抗力
8.3.2切削试件材料为HT200或45钢,切削刀具标准麻花钻
8.3.3试验时,机床工作应正常,各运动机构应灵活、可靠,过载保护装置正常,可靠
8.4主传动系统最大功率的试验(适用于机械式主轴抽查 8.4.1在主轴恒功率的转速范围内,选用一适当的主轴转速,采用饥削方法进行试验,改变进给速度或 切削深度,使机床达到主电机的额定功率或设计规定的最大功率
8.4.2切削试件材料为HT200或45钢,切削刀具硬质合金端铁刀
8.4.3试验时,机床工作应正常,可靠,无明显颤振现象
8.5主传动系统最大功率的试验(适用于电主轴)(抽查 8.5.1在机床主轴恒功率转速范围内,选择一适当的主轴转速,采用铁削方式进行试验,改变进给速度 或切削深度,使机床达到主电动机额定功率的1/2或设计规定的最大功率
8.5.2试件材料为铝件或45钢,切削刀具硬质合金端刀
8.5.3试验时,机床工作应正常,可靠,无明显颤振现象
GB/T34880.3一2018 9 最小设定单位试验 g.1一般要求 一抽线时,其他运动 机床最小设定单位试验包括线性和回转轴线两种时,应分别进行试验
试验某- 部件原则上置于行程的中间位置
试验时可在使用螺距误差补偿和反向间隙补偿条件下进行
9.2线性轴线最小设定单位试验 9.2.1试验方法 先以快速使线性轴线上的运动部件向正(或负)向移动一定距离,停止后,向同方向给出数个最小设 定单位的指令,再停止,以此位置作为基准位置,每次给出1个,共给出20个最小设定单位的指令,向同 方向移动,测量各个指令的停止位置
从上述的最终位置,继续向同方向给出数个最小设定单位指令 停止后,向负(或正)向给出数个最小设定单位的指令,约返回到上述最终测量位置,这些正向和负向的 数个最小设定单位指令的停止位置均不作测量
然后从上述的最终测量位置开始,每次给出1个,共给 出20个最小设定单位的指令,继续向负(或正)向移动,测量各指令的停止位置,见图1
至少在行程的中间及靠近两端的3个位置上分别进行试验
各线性轴线均应进行试验
按9.2.2 的规定计算误差,以3个位置上的最大误差值作为该项的误差
注要注意实际移动的方向
实际移动距离 数个最小设定单位指令部 件的停止位置不作测量 gooeO歌 aoo @ a O oa6 o O 测量范围 o S o aQ o 应 双 8 o o o 中 9 s 最小设定单位 9 只 图1
GB;/T34880.3一2018 9.2.2误差计算 9.2.2.1最小设定单位误差S,按式(1)进行计算 s,=|L,一 m1m 式中 最小设定单位误差,单位为毫米(mm).: S -个最小设定单位指令的实际位移值,单位为毫米(m l mm 一个最小设定单位指令的理论值,单位为毫米(mm). mn 注:实际位移的方向如与给出的方向相反,其位移量应为负值
9.2.2.2最小设定单位相对误差S,按式(2)进行计算 20m IT1X ×100% S 20m 式中: S -最小设定单位相对误差,% 连续20个最小设定单位指令的实际位移的总和,单位为毫米(mm)
9.2.3 允差 根据机床具体情况,由制造厂规定
9.2.4检验工具 激光干涉仪或读数显微镜和金属线纹尺
9.3回转轴线包括数控回转工作台、摆动主轴头、摇摆工作台)最小设定单位试验 9.3.1试验方法 先以快速使回转坐标上的运动部件向正或负)向转动一定角度,停止后,向同方向给出数个最小设 定单位的指令,再停止,以此位置作为基准位置,每次给出一个,共给出20个最小设定单位的指令,测量 各个指令的停止位置
从上述的最终位置,继续向同方向给出数个最小设定单位的指令,停止后,向负 或正)向给出数个最小设定单位的指令,约返回到上述的最终测量位置,这些正向和负向的数个最小设 定单位指令的停止位置不作测量
然后从上述的最终位置开始,每次给出一个,共给出20个最小设定 单位的指令
继续向负(或正)向移动,测量各指令的停止位置,见图2
至少在回转范围内的任意3个位置上分别进行试验
各回转轴线均应进行试验
按9.3.2的计算 方法计算误差,以3个位置上的最大误差值作为该项的误差
注:实际角位移的方向如与给出的方向相反,其角位移为负值
GB/T34880.3一2018 实际转动角度 数个量小设定单位指令部 件的停止位置不作测量 g命 eooog pc boQ a 双 9 6oo 测量范围 e a
o ao3 8 o 双 8 由 6oox 中? o 最小设定单位 o 口 图2 9.3.2误差计算方法 最小设定单位角位移误差"按式(a)进行计算 9.3.2.1 3 w
=一m|m 式中 o 最小设定单位角位移误差,单位为秒("); -个最小设定单位指令的实际角位移,单位为秒("); -个最小设定单位指令的理论值,单位为秒(") 776 9.3.2.2最小设定单位角位移相对误差u按式(4)进行计算 -20mn lmaX ×100% w 20m6 式中 最小设定单位角位移相对误差 w 连续20个最小设定单位指令的实际角位移值之和,单位为秒(")
9.3.3允差 根据机床具体情况,由制造厂规定
g.3.4检验工具 激光干涉仪或自准直仪和多面体
10
GB;/T34880.3一2018 0原点返回试验 10.1一般要求 试验某一轴线时,其他运动部件 机床原点返回试验包括线性和回转轴线两种时,应分别进行试验
原则上置于行程的中间位置
试验时可在使用螺距误差补偿和反向间隙补偿条件下进行
10.2线性轴线原点返回试验 10.2.1试验方法 线性轴线上的运动部件,从行程上的任意点,按相同的移动方向,以快速进行5次返回某一设定原 点P
的试验
测量每次实际位置P与原点理论位置P
的偏差X(j=1、2、3、4、5),见图3
至少在行程的中间及靠近两端的3个位置上分别进行试验
各线性轴线均应进行试验
按10.2.2 的规定计算误差,以3个位置上的最大误差值作为该项的误差
图3 0.2.2误差计算方法 按式(5)进行计算,误差以3个位置上的最大误差值作为该项的误差
R
=4S 式中: 原点返回误差,单位为毫米(mm); R S -原点返回偏差标准不确定度的估算值,单位为毫米(mm) 注s,根据GB/T17421.2一2016的有关公式进行计算 10.2.3允差 根据机床具体情况,由制造厂规定
10.2.4检验工具 激光干涉仪或读数显微镜和金属线纹尺
11
GB/T34880.3一2018 10.3回转轴线包括数控回转工作台、摆动主轴头,摇摆工作台)原点返回试验 10.3.1试验方法 各回转坐标上的运动部件,从行程上的任意点按相同的转动方向以快速移动进行5次返回原点 心 ”的试验
测量每次实际位置尸)与原点理论位置尸m的偏差0.( (i=1、2、3、4,5)见图4
各回转坐标均需检验,至少在回转范围内的任意3个位置进行试验,按10.3.2的规定计算误差,以 3个位置上的最大误差值作为该项的误差
图4 10.3.2误差计算方法 按式(6)进行计算,误差以3个位置上的最大误差值作为该项的误差
R0=4So 式中 R 原点返回误差,单位为秒(") -原点返回偏差标准不确定度的估算值,单位为秒(")
S 注:S根据GB/T17421.2一2016的有关公式进行计算
10.3.3允差 根据机床具体情况,由制造厂规定
10.3.4检验工具 激光干涉仪或自准直仪和多面体
1 机床精度检验 11.1机床的几何精度检验、定位精度检验、工作精度检验,五轴联动卧式加工中心按GB/T34880.1 2017进行,五轴联动立式加工中心按GB/T34880.2一2017进行,其中GB/T34880.1一2017中G14 G15,G16,G17.G18和GB/T34880.2一2017中G10,Gll,G12,G13,Gl4的检验,均应在机床主轴达到 中速稳定温度时进行
11.2机床工作精度检验时,试件铁削平面表明粗糙度Ra最大允差值为3.2Mm;试件削孔表面粗糙 12
GB;/T34880.3一2018 度Ra最大允差值为l.64m. 11.3其他精度检验可按技术文件的规定或订货合同中技术协议的有关规定进行检验
12 包装和随机文件 2.1机床在包装前,应进行防锈处理 2.2机床的包装应符合包装设计图样及技术文件的规定
2.3分箱包装的机床应符合装箱单的规定
12.4随机技术文件的编制应符合GB/T23571一2009的规定
随机出厂的技术文件应包括合格证明 书、使用说明书和装箱单 13
GB/T34880.3一2018 参 考文献 [1]GB/T17421.2一2016机床检验通则第2部分;数控轴线的定位精度和重复定位精度的 确定 14
五轴联动加工中心技术条件
五轴联动加工中心是一种高精密度、高效率的数控机床,广泛应用于航空航天、汽车、模具等领域。为确保五轴联动加工中心的性能和品质,需要对其进行严格的技术条件检验。 GB/T34880.3-2018标准规定了五轴联动加工中心技术条件的检验要求,包括机床精度、刚度和动态特性等方面的要求。其中,机床精度主要涉及到加工精度和位置精度两个方面;机床刚度则考虑了机身的稳定性和振动抑制能力;机床动态特性则包括了快速移动性、加速度和减速度等要素。 在实际检验中,需要使用一系列的检测设备和检测方法,如激光干涉仪、坐标测量仪、角度传感器、振动测试系统等。通过这些设备和方法对五轴联动加工中心的各项技术参数进行精确测量和评估,确保机床符合GB/T34880.3-2018标准要求。 在使用五轴联动加工中心时,需要严格遵守GB/T34880.3-2018标准中规定的技术参数和检测方法,以确保机床的高效稳定运行和加工质量。同时,在实际生产中也应该加强机床的维护和保养,及时发现并解决潜在问题,提高机床的可靠性和持续性能。