GB/T34895-2017
热处理金相检验通则
Generalrulesformetallographicexaminationofheattreatment
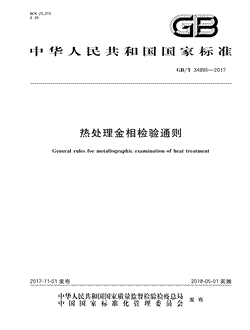
- 中国标准分类号(CCS)J36
- 国际标准分类号(ICS)25.200
- 实施日期2018-05-01
- 文件格式PDF
- 文本页数19页
- 文件大小1.47M
以图片形式预览热处理金相检验通则
热处理金相检验通则
国家标准 GB/T34895一2017 热处理金相检验通则 Generalrulesformetallographiceaminationofheattreatment 2017-11-01发布 2018-05-01实施 国家质量监督检验检疫总局 发布 国家标准化管理委员会国家标准
GB/34895一2017 目 次 前言 范围 2 规范性引用文件 术语和定义 金相检验人员 相关设备 检验过程 现场金相检验 8 检验报告 安全及环保 试样磨光用砂纸标记及粒度组成 附录A资料性附录) 附录B资料性附录抛光织物、抛光磨料及化学抛光选用 附录c(资料性附录常用化学侵蚀试剂 附录D(资料性附录)常用电解侵蚀试剂及规范 12 附录E(资料性附录)部分热处理工艺金相检验标准 13 附录F(资料性附录侵蚀剂配制及使用的安全事项 16
GB/34895一2017 前 言 本标准按照GB/T1.1一2009给出的规则起草
本标准由全国热处理标准化技术委员会(SAC/Tc75)提出并归口
本标准主要起草单位:国家刀剪及日用金属工具质量监督检验中心、北京机电研究所、上海市机械 制造工艺研究所有限公司、北京市特种设备检测中心,大连交通大学、天津热处理检测中心有限公司、长 春轨道客车股份有限公司、江苏丰东热处理及表面改性工程技术研究有限公司、广东世创金属科技股份 有限公司、北京恒智友科技开发中心 本标准主要起草人:毕革平、李俏、任颂赞、谭文华、雷闽、李志强,诬连文,宋宝敬、史有森、董小虹、 向建华黄文妞、陈小煜
GB/34895一2017 热处理金相检验通则 范围 本标准规定了工件热处理前后及热处理过程中金相检验的人员、相关设备、试样的取样制样、组织 显示、组织检验、金相照片制作原始记录、样品处置、现场金相检验、检验报告及安全环保等技术要求
本标准适用于用光学金相显微镜对热处理金相检验
规范性引用文件 下列文件对于本文件的应用是必不可少的
凡是注日期的引用文件,仅注日期的版本适用于本文 件
凡是不注日期的引用文件,其最新版本(包括所有的修改单)适用于本文件
GB/T7232金属热处理工艺术语 GB/T13298金属显微组织检验方法 GB 15749定量金相测定方法 GB 17455无损检测表面检测的金相复型技术 GB 27476.1检测实验室安全第1部分:总则 GB 27476.2检测实验室安全第2部分;电气因素 GB 27476.3检测实验室安全第3部分;机械因素 GB/T27476.5检测实验室安全第5部分;化学因素 YB/T4377 金属试样的电解抛光方法 术语和定义 GB/T7232中界定的以及下列术语和定义适用于本文件
3.1 金相检验 metallographice%amination 采用金相显微镜对金属或合金的宏观组织或显微组织进行分析测定,以得到各种组织的尺寸、数 量、形状及分布特征的方法
3.2 金相复型技术 metallographicreplica 通过将预制的复型材料与试样贴合的方法取得部件金属微观组织形貌的复型(负面)技术
[DL/T652一1998 3.3 定量金相 quantitativemetallography 采用体视学和图像分析技术等对材料的显微组织进行定量表征的一类金相技术
注:定量金相包括测估品粒尺寸,各相的含量,第二相的大小,数量,形状及其分布特征等
3.4 图像分析 imageanalysis 从图像中提取的几何信息和光密度等定量数据的实验技术
GB/T34895一2017 3.5 工件现场金相检验 workpiecesitemetallographicexamination 在工件上直接进行金相制样,直接用现场显微镜或用金相复型技术进行组织检验
金相检验人员 4.1金相检验人员需经专业培训,并取得相应上岗证
4.2从事热处理工件金相检验人员应具有金属材料及热处理的基本知识(包括相应安全、环保及质量 控制等),要熟悉相关金相检验标准,并应具有与侵蚀剂相关的化学试剂、侵蚀剂配制的基本知识
4.3金相检验人员应接受包括相应金相检验标准、安全及环保等更新信息在内的继续教育,并保存 记录
5 相关设备 5.1金相检验相关设备包括制样设备(金相切割机、镶嵌机、预磨机、抛光机、电解腐蚀设备等、金相显 微镜及照相系统等,均应满足相关的安全要求,都应纳人设备管理体系
500 5.2金相预磨机、抛光机应具有可变速功能,预磨机转速一般为300r/min~ r/min,抛光机转速 般为1000r/min,并配有进水及下水通道
也可选用全自动制样设备
5.3金相显微镜的选择及配置(包括总放大倍率选择、物镜的数值孔径、成像清晰范围、摄像头,暗场、 偏光器等附件)选择均应满足金相检验的技术要求
5.4光学金相显微镜不能与制样设备(包括侵蚀场地)同处一房间
6 检验过程 6.1取样 6.1.1基本要求 取样方案应依据相关国家标准、行业标准,或技术协议、技术文件来确定
选取样品时,应明确数 量,部位以及取向
热处理件金相检验一般采用随炉试样或在产品上切割试样
取样遵循以下原则: 代表性原则:在热处理工件上具有代表性的部位取样; a b) 完整性原则:在热处理工件上能够全面反映出组织分布
如表面热处理应包括表面组织,过渡 区组织,基体组织等; 重要性原则:在热处理工件上使用最重要的部位或缺陷最容易出现的部位; c d 无变化原则:在取样过程中,不应造成热处理组织发生变化,如过热、畸变、特殊表面的损伤 e 唯一性原则:在取样过程中要及时对试样进行标识,并确保在取样,分组、检验、留样等各环节 具唯一性并能追溯
无法在热处理工件上取样或要求对实物检测的,可以直接在工件上按相关标准选取检验区域
6.1.2试样大小及数量 6.1.2.1试样大小和数量应满足热处理工艺、热处理质量检验要求
6.1.2.2试样大小应满足对边长,视场直径或面积有要求的技术条件
对某些测试面总面积有特殊要 求的,应根据面积大小决定试样数量
6.1.2.3试样一般应以能正常握持为宜,一般磨面面积不大于400mm,高度宜为15 mm20mm,过
GB/34895一2017 小或形状复杂的难以握持进行制样的试样,可采用机械夹持或镶嵌的方法
6.1.3试样检验面的确定 6.1.3.1试样检验面应具有代表性,应符合相关标准或技术文件规定
6.1.3.2试样检验面可以有以下几种选择 横截面垂直于锻轧方向的横截面可以检验金属材料从表层到中心的显微组织分布,晶粒度级 a 别、碳化物网、表层缺陷深度、氧化层深度,脱碳层深度、表面改性层深度等
b)纵截面:平行于锻轧方向的纵截面可以检验非金属夹杂物的变形程度及分布、晶粒畸变程度、 塑性变形程度、变形后的各种组织分布形貌、热处理后显微组织在纵向分布形貌
斜截面:用于表面薄的改性层试样,可加工成斜截面,与试样表面的夹角可根据改性层深度 确定
6.1.4试样截取 大多数情况下应根据工件的硬度、形状及检测要求切割取样,可选用剪切、手锯、砂轮机切割、电火 花切割,机加工设备等截取,必要时也可用火焰气割法截取
不论用哪种方法,应采取水冷等预防措施、 并在切剐边去除畸变、过热、过烧等影响区
6.1.5镶嵌或夹持 试样过小或形状特殊,或要求检验试样表层组织而不需要棱边倒角的,可采用试样夹持或镶嵌方 法
镶嵌方法分为热镶嵌和冷镶嵌,可根据试样及检验要求选用,具体操作方法见GB/T13298
6.2制样 6.2.1试样的磨抛工序过程应有作业指导书,并应按规定执行
6.2.2试样通过磨抛过程,获得平整、光亮,无划痕,可进行显微观察的镜面
6.2.3 每 一道磨抛工序应消除上道工序产生的表层损伤痕迹
为便于辨别,下一道磨抛方向应与上一 道磨抛方向垂直
6.2.4对于需要检验表层组织及深度等试样,磨抛过程中要保证试面与外表面垂直,或保持设定的斜 角,并且保证检验边的棱边不受倒角等损伤
6.2.5机械磨抛过程中应注意对试样的施力、冷却及清洗,避免引发变质层
6.2.6对硬度较低的铝、镁等金属应施加轻压力,且不能同硬度高的试样采用同一张砂纸,抛光布
6.2.7人工磨抛操作时,试样应从盘中心至盘边缘来回移动
6.3磨光 6.3.1除金相砂轮切割机加工的试面,用其他方法截取的试面均应经砂轮磨加工,直至上道加工道痕 去除,并且平整
6.3.2磨制时可采用手工或机械方法干磨或湿磨
一般推荐用金相旋转预磨机配水砂纸的加工方法
6.3.3磨削速度与加工效率有关,更与具体试样可能产生变质层的敏感性有关,因此,不同材质、不同 工艺状态的试样应采用不同的磨光转速
磨削转速可选300r/nin一500r/nin,细磨时可选高速 6.3.4磨光一般由粗磨到细磨分多道完成
初始选用P180一P220粗水砂纸粗磨,最终选用P1000~ P1200水砂纸细磨后进人下道抛光工序
中间一般再均分两道水砂纸加工,如P320~P400及P600 P800等
同时,应注意砂纸的磨削能力,,一旦变钝应及时更换,以免造成磨面增添扰乱层
有关砂纸标 记及粒度组成参见附录A
6.3.5经最后一道细磨的试面,应只留有最终砂纸的均匀平行磨痕,才能进人抛光阶段
GB/T34895一2017 6.4抛光 6.4.1试样抛光可用机械抛光、化学抛光和电解抛光的方法
一般推荐用机械抛光法
6.4.2对于机械抛光,还应在抛光盘上覆上抛光织物(除抛光机外),并喷涂适量的抛光磨料
相关抛 光织物及抛光磨料的选用参见附录B 6.4.3机械抛光工序分为粗抛及精抛,个别情况下也可采用一次精抛光
6.4.4机械抛光时,压力要轻,试样来回移动,若检验夹杂物,石墨等时,试样还应适当转动,并不时喷 加抛磨料
抛光织物的湿度以将试样从盘上取下观察时,表面水膜能在2s3s内完全蒸发消失为宜
抛光到磨面的磨痕完全去除,达相当镜面时为止
抛光后用清水或酒精洗净吹干,使表面不致有水迹或 污物残留
6.4.5对于铝合金、铜合金、奥氏体不锈钢、耐热钢等试样采用化学抛光或电解抛光效果较好
化学抛 光可参考附录B,电解抛光方法按YB/T4377进行
6.5组织显示 6.5.1基本要求 金相试样侵蚀过程应制定相应作业指导书,并按技术文件要求执行
6.5.1.1 6.5.1.2对于非金属夹杂物、石墨、孔隙、晶界内氧化,部分相对硬质相和部分镀层等应在抛光态下直接 观察
6.5.1.3显微组织一般要通过化学或物理等方法显示出来
常用的方法为化学侵蚀、电解侵蚀、,薄膜干 涉等方法
首选化学侵蚀法,具体侵蚀方达的选择应以能满足金相分析且安全、经济为依据
6.5.1.4金相试样侵蚀处理后应充分清,吹干
6.5.2化学侵蚀 6.5.2.1 -定的化学试剂与一定的金属试样表面通过化学或电化学过程对不同组织的不均匀溶解而显 示金相组织
常用侵蚀试剂及侵蚀条件参见附录C 6.5.2.2侵蚀过程主要与试剂温度、侵蚀时间有关
侵蚀程度的控制,以能正确显示相关组织满足检 验要求为依据
6.5.3电解侵蚀 金相试样作为电路的阳极,浸人合适的电解侵蚀液中,通人较小电流进行侵蚀,以显示金属显微组 织
侵蚀条件由电压,电流、温度,时间来确定
部分电解侵蚀试剂及侵蚀条件见附录D. 6.5.4其他显示方式 薄膜干涉显示、,恒电位侵蚀、,热染法等组织显示方法见GB/T13298. 6.6组织检验 6.6.1基本要求 6.6.1.1金相显微镜目镜测微尺、物镜测微尺均应进行计量溯源
当接有电脑显示器时,应保证显示器 图像的尺寸可追溯性
6.6.1.2根据检验项目合理规范地操作光学金相显微镜,包括选择合适的目镜、物镜、数值孔径光栏,视 场光栏,光源,滤色片等以满足放大倍率,分辨力,衬度,景深等要求
6.6.1.3金相组织观察时应从低倍起到高倍率观察,先选择具有代表性视场,再放大到适当的或规定的
GB/34895一2017 放大倍率
6.6.2金相组织评定 6.6.2.1对于金相组织的判定,评级均应按国家标准、行业标准或相关的技术文件规定
部分热处理金 相检验标准参见附录E 6.6.2.2金相组织形态、粗细、分布的评级应对照相关标准中相应的评级图
6.6.2.3金相组织评级时,放大倍率,视场大小,区域、视场数应与相应标准保持一致
6.6.2.4金相组织评级时,金相组织级别的评定应按相关标准规定的方法执行
6.6.2.5当需要定量测量组织几何尺寸时,应在一定的倍率下进行,以保证一定的测量精度
测量的区 域、范围、次数以及数据处理,应按相关技术文件或相关标准执行
6.6.2.6需要用定量金相方法或图像分析方法进行组织评级测量的可按GB/T15749或相关的图像分 析软件应用说明进行
图像分析软件使用前应经证实能够达到预期使用目的
6.7金相照片制作 6.7.1 金相检验报告一般应有典型金相照片
金相照片的放大倍率、视场大小应与相应标准中的图谱相适应
金相照片应能清晰显示金相检 6.7.2 验指出的组织信息,应有放大倍率信息,要附带组织显示条件
相关组织信息可用1张或多张金相照片 表达
金相照片可通过与金相显微镜匹配的电子摄像头摄取,也可通过金相显微镜配置的感光胶片照 6.7.3 相机摄取
为摄得规范、良好的金相照片,应控制金相照片拍摄过程中的各个环节质量
金相试样应制备良好,侵蚀程度应适应放大倍率,高倍率观察试样应浅侵蚀 6.7.4 金相显微镜观察、摄像时应注意镜头组合选择、孔径光栏及视场光栏调节、照明调整等条件对成 6.7.5 像的分辨力、景深、衬度、亮度均匀性等质量的影响 6.7.6金相图像转移至显示器过程中,应注意摄像头的图像传感器类型像素、信号传输速度的影响
对拍摄前屏幕上图像不应采用电子放大手段再次放大图像,并应保持图像尺寸、倍率的可追溯性
在电 子图像拍摄前,不宜过度调整图像对比度、亮度、饱和度等,以免金相组织图像变形、细节丢失或叠加假 象等
6.7.7电子图像形式的金相照片一般采用电子打印机打印,也可通过感光相纸印制
为能表达金相照 片的层次,建议采用彩色打印机或专用图片打印纸,应保证组织的真实性、一致性
6.8原始记录 6.8.1金相检验原始记录可以是纸质的,也可以是电子文本,但应明确规定
原始记录的保存期应列 人管理体系,一般不少于一年
6.8.2热处理金相检验原始记录应包含但不限于以下内容, 委托单位或部门; 委托及检测日期 样品名称,标识号(图号等)以及主要尺寸; 样品材质及工艺;包括热处理前成型工艺; 取样及制样;取样部位,实验室内运行编号,侵蚀条件及取样需说明信息; 选用的标准,包括图谱信息 显微镜及使用条件;放大倍率(物镜、目镜),标尺等; 照片拍摄;包括存储文件夹,打印条件等; 有关数据计算处理过程
GB/T34895一2017 检验结果及说明,若校核过程中有纠正意见也应列人
6.9样品处置 金相试样在金相检验全过程中,应保证试样标识清晰可辨
金相试样保留时间应有明确规定,一般 不少于3个月
必要时,金相试样检验结束后应存放在干燥的容器内
现场金相检验 7.1现场金相检验的检验区域选择应按6.6.1的规定
7.2 -般采用专用的现场磨抛设备对所选现场金相检验区域进行磨抛、制样 7.3 -般采用化学侵蚀法显示组织
侵蚀后应注意及时用酒精冲洗观察面 7.4组织观察可使用便携式现场金相显微镜,并可用数码摄像头摄取图像
7.5 对于现场不便观察或不便拍摄的试样区域,可按照cB/T171455中的金相复型技术将所需检验部 位复制出来,带到实验室观察检验 现场金相检验除按第9章执行相关安全、环保要求外,还应遵守现场的安全,环保要求
7.6 8 检验报告 8.1金相检验报告的格式、报告的编制、校核、批准等形成过程及保存期等均应有相应的程序规定,并 纳人管理体系
8.2金相检验报告的编制者、校核者应具有相应资质
8.3金相检验报告的信息应包括但不限于以下内容 报告编号、委托日期及检验日期 委托方信息; 样品信息(名称、标识、材料牌号,炉次,取样部位,试样规格等); 热处理工艺信息; 检验依据的标准及结论 如配有金相照片,应有放大倍率及使用的侵蚀试剂说明 编制、校核及批准人签字
安全及环保 O g.1金相检验的全过程,包括取样、制样等环节,应制定相应的安全制度和配备确保安全必要的设施 并应纳人相关体系
安全制度的制定、设施的配备需符合GB/T27476.1.GB/T27476." 2 GB/T27476.3,GB/T27476.5的规定
9.2金相试样在截取,磨制时,或强酸,强碱侵蚀时,应按规定配备并穿戴好相应的安全防护用品
9.3配置侵蚀剂用的化学试剂,应从有资质供应商采购,应有采购,验收、储存、使用等相关的安全规 定,并有相应记录
g.4金相侵蚀试剂配制使用及储存的有关安全事项参见附录F,或参考GB/T27476.5
9.5金相检验的全过程,包括取样、制样等环节,应制定相应的环保制度和配备必要的设施,并应纳人 相关体系
侵蚀剂使用后废弃时,应经中和处理或经收集统一处理后排放
GB/34895一2017 录 附 A 资料性附录 试样磨光用砂纸标记及粒度组成 金相试样磨光工序目前一般采用水砂纸,金相试面从粗磨到细磨要分多道工序,相应要选用不同标 号的砂纸
有关水砂纸技术要求见JB/T7499,砂纸粒度标记及粒度组成与GB/T9258.1一致,见表 A.1和表A.2
表A.1粗磨粒砂纸粒度标记及粒度组成 第一层筛 第二层筛 第三层筛 第四层筛 第五层筛 底盘中 第 ,二层 第 -至三 第 -至四 第 -至五层 筛下物 粒度 筛孔第一层筛筛孔 筛孔 筛孔 筛孔 筛筛上物 层筛筛上 层筛筛上 筛筛上物 标记 最大 尺寸筛上物尺寸 尺寸 尺寸 尺寸 之和最小 之和最大 物之和 物之和 % % 4m 4m 4m Am Am 名 % % 18o P80 355 250 212 26士6 75士9 150 96 P100 300 212 180 l4士4 150 61士9 125 92 P120 212 50 125 42士8 106 86士6 90 96 96 P150 80 125 106 26士6 90 75士9 75 75 P180 150 106 90 63 90 10 l5士5 62士12 P220 125 75 15士5 63 62士12 53 90 90 10 表A.2细磨粒砂纸的粒度标记及粒度组成 d
最大值 d最大值 中值粒径de d最小值 粒度标记 Am Am Am Am P240 ll0 81.7 58.5士2.0 44.5 P28o 101 74.o 52.2士2.0 39,.2 94 66.8 .5 34.2 P320 46.1士1. P36o 87 60,3 40.5士1.5 29.6 P400 81 53.9 35.0士1.5 25.2 77 P500 48.3 30,2士1.5 21.5 72 P600 43.,0 25,8士1.0 18.0 67 P800 38.l 21.8士1.0 15.1 P100o 63 33." 2.4 18.3士l.0 P1200 58 29.7 15.3士1.0 0.2 58 P1500 25.8 12.6士1.0 8.3 注:这些值仅适用于GB/T2481.2中的沉降管粒度仪测定
GB/T34895一2017 附录 B 资料性附录) 抛光织物、抛光磨料及化学抛光选用 B.1抛光织物的选用 抛光织物除支承抛光磨料并与试样接触外,还应容纳抛光磨料使之不致太快地从磨盘上甩出
编 织结构和绒毛有吸收抛光磨料的作用
织物上的纤维或绒毛与试样表面的湿润摩擦,可使试样面平滑 光亮
无绒织物上的编织图案、绒毛结构、纤维长度和密度以及回弹能力等,是影响织物抛光性能的重 要因素
抛光织物的选用可参考表B.1
表B.1抛光织物的选用 抛光用材料 材料的性能 适用 质地致的呢料或有短茸毛的这类呢料或绒布耐用,抛光效果和抛光速度 般金属材料粗抛、精抛均可使 绒布、毛呢等 也较好 用,适用面厂 这类丝绒织物抛光,速度快,但容易产生浮 -般金属材料都可使用,尤其适于 带有长毛的丝绒一类的织物,如 雕现象;长毛容易将试样检验面上的夹杂物 天鹅绒、长毛绒 软金属抛光
检查夹杂物时慎用 拖出 质地坚硬致密不带茸毛的丝织这类织物可最大限度与磨料接触,切削率适用于粗抛或检验火杂及表面层 物,如帆布、丝绸、尼龙 高,可降低浮凸现象 质量的试样 B.2抛光用磨料的选用 金相试样抛光用磨料有多种,如氧化铝、氧化镁、氧化铬、氧化铁等,但目前广泛使用金刚石磨料组 成的研磨膏或喷雾剂
磨料的粒度,即颗粒尺寸是其重要指标,具体使用可在表B.2中选择
表B.2抛光磨料粒度号、尺寸及抛光后粗糙度 颗粒尺寸 抛光后粗糙度Ra 粒度号 m Am 0.40.2 w20 20 WI 14 0,2~0,1 w1o 10 0.20.1 w7 0.1~0.,05 W5 0,10,05 w3.5 0.05~0.025 3.5 w2.5 2.5 0.050.025 w1.5 1.5 0.050.025
GB/34895一2017 表B.2(续 颗粒尺寸 抛光后粗糙度 Ra 粒度号 丛m Am WI 0.0250.012 wo.5 0.5 0,0250,012 B.3化学抛光选用 不同材质的热处理工件试样采用化学抛光时,应选择不同的化学抛光试剂及抛光条件,常用化学抛 光方法及条件见Ys/T449,具体使用可在表B.3中选择
表B.3化学抛光液及条件 抛光条件 材质 试剂成分 纯铜 正磷酸33ml,硝酸33mL,冰醋酸33ml 温度:60C70C,时间:122nmin 正磷酸10mL 硝酸303ml 盐酸10ml. 冰腊酸温度,70C一80C,时间,l min一 铜合金 50ml 2min 温度;95~125,时间;2nmin 磷酸70ml,醋酸12mlL,水15ml 6min 铝及铝合金 温度;80C~90C.,时间;2 2min一 磷酸80ml,醋酸15mL,硝酸5ml 5min 甘油(98%)20mlL 盐酸(36%一38%2mL. 硝酸 擦拭 65%68%)3ml,乙酸99%5ml 镁及镁合金 硝酸10%,甲醇90% 擦拭 不锈钢 盐酸30%,碗酸40%,四氯化钛5.5%,水2A.5% 温度;55C一8o 双氧水17ml.,草酸34ml,盐酸1ml~1.5ml.,水加 合金钢 室温 至 100mL 双氧水17nml.,草酸34ml,盐酸1ml1.5ml,水加 低合金钢 室温 至 100ml 碳钢 双氧水1%,草酸70%,水20% 温度:35"C,时间:l5min
GB/T34895一2017 附 录 资料性附录) 常用化学侵蚀试剂 常用化学侵蚀试剂见表C.1
表c.1常用化学侵蚀试剂 序号 侵蚀剂名称 组成及成分 侵蚀说明 适用范围 侵蚀时间数秒至约1min,与温度有关
天或侵蚀高合金钢可适当加热 40C广泛用于碳素钢及 60); 合金钢,显示退火、 硝酸酒精 lml~5ml硝酸、100ml 显 硝酸含量高,侵蚀加剧; 正火火组织
溶液 酒精 高合金工模具钢.硝酸量可达5ml10ml;示碳化物应采用深 加人一定量水可加速侵蚀; 侵蚀 加人一定量甘油可延缓侵蚀作用 适用于碳钢及低合 苦昧酸酒精 金钢各种热处理条 l4【苦味酸.100ml酒精 侵蚀性较弱,侵蚀时间长,主要侵蚀相界面 溶液 件下的组织,能清晰 显示组织推节-相整 显示淬火及济火回 盐酸苦味酸g苦味酸、5mL盐酸、100 室温下侵蚀数分钟 火后钢的晶粒和 酒精溶液 ml酒精 组织 100ml饱和苦味酸水溶 饱和苦味酸 显示高合金俐悴、 、回 试剂加热到80C后侵蚀约5min10min 液,0.5【~lg 溶液 火后的晶界 十三熔基碱酸钠 氯化铁 氯化铁盐酸 显示马氏体类及大 盐酸50mL 侵蚀约3s~10 水溶液 多数不锈钢组织 水100ml
氯化铁5g 氯化铁盐酸 显示一般铜、铅、镁、 盐酸2 mL 浸人或用棉球擦拭几秒至数分钟 酒精溶液 镍等合金组织 酒精96ml. 巍散制盐酸随散铜4x 显示奥氏体类不锈 盐酸20ml 侵蚀约3s 钢的组织,氮化俐泼 10s 水溶液 水20ml 氮层深度测定 硫酸铜1.5g" 硫酸铜盐酸 显示高温合金、镍基 盐酸40ml 侵蚀数分钟 酒精溶液 合金组织 酒精20ml 铁氮化钾10g 显示不锈钢中的 双试剂 氢氧化钾10g 在60C90或煮沸的试剂内浸泡数分钟相和铁素体奥氏体 水100mL 不锈钢中
相 高 显示高合金钢、 10 王水 硝酸:盐酸=1:3(体积比l侵蚀数分钟 速钢、铁-钻和镍基 高温合金 10
GB/34895?2017 c.1 ? ÷Χ ?? ?? ? 0.5ml ? 11 ?15s ? ?99.5ml ? 0.5ml ?1.5ml 12 ?10s?20 ?? ? 2.5mL ?95.5m 1ml. lKroll? ?? 13 2ml6ml |??3s10s?10s30s ? 100mL ? ?ζ20mL 10mL ??? ? ? ? 20 ml ?50ml A?:4%ζ?1 %?? ζ? ??, 1.2; ?A??20s,???, 15 ? ???, B?4%ζ1.5B??10" ?? ?1%?? ?1?? ?2:????? ?3:?????? 11
GB/T34895一2017 附 录 D 资料性附录) 常用电解侵蚀试剂及规范 常用电解侵蚀试剂及规范见表D.1
表D.1常用电解侵蚀试剂及规范 规范 序号 电解液成分 用途说明 电解条件 时间/s 阴极 硫酸亚铁3g" 电流密度 中碳钢及低合金结构 硫酸铁0.1lg 1060 不锈钢 钢,高合金钢,、钰铸铁 0.1A/em~0.2A/em 水100mL 铁化娜10g 电流密度: 不锈钢高速钢 4080 水90ml 0.2A/enm一0.3A/em 4060淬火钢 草酸10g 电流密度 不锈钢、耐热钢 水100mL 0.1A/em'0.3A/em 5一20(退火,回火 除铁素体晶粒晶界外 三氧化铬10g 多数组织均能显示,渗 电压;6V 3090 不锈钢 水90ml 碳体最易腐蚀,奥氏体 次之,铁素体最慢 硫酸5ml 0V4.5V 510 纯镍及! 电压;3.0 Inconel合金 水95ml 三氧化铬1g 电压;6v 锁青铜及铝青铜 水99ml 电压;20V一45V 1180 氧棚酸1.8 铝合金覆膜偏光下可 ml 智 电流密度 水100ml (<40C 见晶粒 0.lA/cmm”一0.5A/cmm" 硫酸38ml. 电压:20V~30V 1180 纯铝、铝-镁,铝-缸等覆 磷酸43mL 智 电流密度 (<40C) 膜偏光下可见晶粒 水19ml 0.1A/em=一0,5A/em 高氯酸60ml 铅,铅锄合金,铅锡 10 电压:2V 铂 水 40ml 合金 注1:所用试剂为分析纯
注2;所用酒精为无水乙醉 注3配制用水为燕僧水或纯净水
12
GB/34895一2017 录 附 E 资料性附录 部分热处理工艺金相检验标准 E.1热处理前常规检测 热处理前常规检测部分标准见表E.1
表E.1热处理前常规检测标准 标准名称 应用说明 序号 GB/T10561《钢中非金属夹杂物含量的测定标准评适用于轧制或锻制钢材中的非金属夹杂物的显 级图显微检验法》 微评定 采用品粒面积,晶粒直径、截线长度的单峰分布 GB/T6394《金属平均晶粒度测定方法》 来测定试样的平均晶粒度 YS/T347《铜及铜合金平均晶粒度测定方法》 采用晶粒直径d表示 JB/T7946.4《铸造铝合金铸造铝铜合金品粒度》 铸造铝铜合金的晶粒度评定 第 GB/T3246.1《变形铝及铝合金制品组织检验方法 铝及铝合金铸键(或锭坯)及加工制品的显微组 1部分:显微组织检验方法》 织及晶粒度评定 GB/T224《俐的脱碳层深度测定法 用于原材料或热处理后表面脱碳层测定 适用于低碳、中碳钢评定;带状组织、魏氏组织、 GB/T13299《钢的显微组织评定方法》 游离渗碳体 E.2碳化物不均匀性评定 碳化物不均匀性评定部分标准见表E.2
表E.2碳化物不均匀性评定标准 序号 标准名称 应用说明 适用于莱氏体型高速工具钢、合金工具钢、高碳 GB/T14979《钢的共品碳化物不均匀度评定法》 铬不锈轴承钢和高温不锈轴承钢中共晶碳化物 不均匀习度的显微评定 适用于高碳铬轴承钢原材料的碳化物网状及带 GB/T18254《高碳铬轴承钢》 状评定 JB/T1255《滚动轴承高碳铬轴承钢零件热处理技适用于高碳铬轴承零件热处理后网状碳化物的 术条件》 评定 适用于合金及非合金工模具俐网状碳化物的 GB/T1299《工模具钢》 评定 13
GB/T34895一2017 E,3球化退火球化组织评定 球化退火组织评定部分标准见表E.3 表E.3球化退火组织评定标准 序号 标准名称 应用说明 低碳及低碳合金结构钢中碳及中碳合金结构钢 JB/T5074《低、中碳钢球化体评级》 的球化退火评级 GB/T1299《工模具钢 适用于合金及非合金工具钢球化组织评定 JB/T1255《滚动轴承高碳铬轴承钢零件热处理技 适用于高碳铬轴承钢球化组织评定 术条件》 E.4淬火、回火后组织评定 淬火、回火组织后组织评定部分标准见表E.4
表E.,4淬火,回火组织后组织评定标准 序号 标准名称 应用说明 JB/T9211《中碳钢与中碳合金结构钢马氏体等级》 中碳钢与中碳合金钢淖火后马氏体评级 JB/T8420《热作模具钢显微组织评级》 常用热作模具钢淬火后马氏体评级 高碳高合金钢制冷作模具淬火后的马氏体,碳化 JB/T7713《高碳高合金钢制冷作模具显微组织检验》 物评级 E.5表面改性热处理组织评定 表面改性热处理组织评定部分标准见表E.5
表E.5表面改性热处理组织评定标准 序号 标准名称 应用说明 渗碳或碳氮共渗并、回火后,表层组织中马氏 GB/T25744《俐件渗碳悴火回火金相检验 体、残留奥氏体、碳化物级别评定,心部铁素体含 量级别,表层内氧化深度的测定 汽车齿轮渗碳层的马氏体、残留奥氏体、碳化物 QC/T262《汽车渗碳齿轮金相检验》 级别评定 汽车齿轮碳氮共渗层马氏体、残留奥民体及碳氮 QC/T29018《汽车碳氮共渗齿轮金相检验》 化合物评级 JB/T7710《薄层碳氮共渗或薄层渗碳钢件显微组织 层碳氮共渗或渗碳钢件表层及心部组织评级 检测 14
GB/34895一2017 表E.5(续 序号 标准名称 应用说明 GB/T11354《钢铁零件渗氨层深度测定和金相组织钢件表层原始组织评级、渗氨层的疏松级别及氮 检验》 化物级别、渗层深度等 JB/T9204《钢件感应火金相检验》 钢件感应淬火后的马氏体评级 珠光体球墨铸铁零件经高、中频感应祚火低温回 GB/T9205《珠光体球墨铸铁零件感应火金相检验》 火后的硬化层金相组织检验 适用于俐铁零件表面渗铬、渗铝,渗锌,渗饥、 渗 JB/T5069《钢铁零件渗金属层金相检验方法》 钛、渗处理后的渗层组织检验 适用于碳俐,合金俐及铸铁等材料的渗棚层组织 JB/T7709《渗猬层显微组织,硬度及层深测定方法》 检验 E.6铝合金热处理过热评定 铝合金热处理过热评定部分标准见表E.6
表E.6铝合金热处理过热评定标准 标准名称 应用说明 序号 适用于铸造铝硅合金热处理过烧金相组织检验 JB/T7946.2《铸造铝合金金相铸造铝合金过烧》 适用于铝硅系和铝铜系合金铸件固溶处理后的 Q1676《铸造铝合金过烧金相试验方法 过烧金相组织检验 GB/T3246.1《变形铝及铝合金制品组织检验方法 铝及铝合金铸锭(或锭坯)及加工制品的热加工 第 1部分;显微组织检验方法》 中过烧组织的检验 o1675《变形铝合金过烧金相试验方法 适用于变形铝合金的过烧金相组织检验 15
GB/T34895一2017 F 附录 资料性附录 侵蚀剂配制及使用的安全事项 F.1侵蚀剂、抛光剂配制时的安全事项 F.1.1侵蚀剂配制人员应具有相关药品及化学溶剂配制操作的基本知识,了解所涉及的危害和应遵守 的安全防护揩施
F.1.2侵蚀剂配制人员应仔细阅读所选试剂的试剂瓶上注明的注意事项清楚认识到所使用药品可能 有的毒性和危害性,包括短期的、长期的、可见及不可见的、有气味及无气味的,了解相应的安全预防 措施
F.1.3倒注、配制侵蚀剂使用相应的防护用具,一般在通风橱内操作
干燥的苦味酸具有振动敏感性下的高度的爆炸性,尤其是与类似于铜铅、锌和铁等金属混合到 F.1.4 -起之后,应保存在水中,或注意保持其处于潮湿状态
F.1.5尽量使用低浓度的氢氟酸,如皮肤不慎接触到氢氟酸,应涂抹葡萄糖酸钙乳霜或其他适当的氢 氟酸中和剂
F.1.6三氧化铬是一种剧毒的致癌物质,人体反复接触会引起难以治愈的溃疡
溶于水中形成铬酸溶 液
铬酸溶液以及高孟酸钾溶液、铁化钾溶液等强氧化剂,在特定条件下会释放出很多氧气,应防范 由此引发的危害
高氯酸和无水醋酸混合时有潜在的爆炸性,使用时存在很多不可预见的危险性
因此,非特殊 F.17 需要,并无特殊措施,应禁止使用该种侵蚀剂
F.1.8配制侵蚀剂时,如无特殊说明,应把溶质加人溶剂中,不断搅拌并要防止溶液飞溅
多种溶质时 要按正确的顺序溶解配制
F.1.9碱性氢氧化物如NaOH在水中溶解时会放出大量热量,每次要少量添加并不断搅拌,若溶液温 度过高应使其冷却至室温后再添加
F.1.10大多数侵蚀剂、电解液应在干净的玻璃容器中混合或存放
含氟化物和强碱的侵蚀剂电解液 应在聚乙烯或其他适当材料的容器中混合或存放
侵蚀剂存放时应避免蒸发,但存放容器不能用螺旋 盖,以免可能气体产生造成炸裂
F.1.11侵蚀剂电解液尽可能按需适量配制,一般条件下随配随用
配制后即时做好标识,标注配制 日期
F.1.12对侵蚀剂、抛光剂等废液要集中进行无害化处理
F.2金相试样侵蚀时安全事项 F.2.1金相试样侵蚀前,操作者应正确选择侵蚀剂,了解试剂特性及侵蚀条件
F.2.2侵蚀时,应使用试样夹等工具进行操作,避免徒手与侵蚀剂直接接触,必要时要佩戴防护用品
用含硝酸裕液侵蚀试样时,若用棉花擦拭,该椭花应在水中冲洗后丢弃,以免因硝酸与棉花在 F.2.3 定条件下可能形成具爆炸性的硝化棉
F.2.4当用强酸、强碱侵蚀试样时,或侵蚀过程反应剧烈的,应在通风橱内操作
16
热处理金相检验通则GB/T34895-2017
1. 适用范围
本标准规定了热处理金相检验的一般要求和试验方法。
2. 定义
热处理:材料在固态下加热到一定温度并保温一段时间后,以适当速率冷却至室温的过程。
金相组织:材料经显微镜观察所能显示出的结构和组成。
3. 分类
热处理金相检验分为普通碳素钢、合金钢、不锈钢、高温合金、钛合金、铝合金、镁合金、铜合金、未淬火钢铸件等多个类别。
4. 试样制备
试样制备应符合GB/T231.1-2018中有关试样的规定,并根据材料的不同特点进行相应处理。
5. 试验方法
试验方法包括:试样的金相制备、显微镜观察、组织图像分析等内容,具体可参照本标准中的相关要求。
6. 结果表示
试验结果应当采用相应的标识符来表示,如普通碳素钢应使用“C”;合金钢应使用“W”;不锈钢应使用“S”等。同时,结果应当注明试验方法、试验条件等详细信息。