GB/T34370.9-2020
游乐设施无损检测第9部分:漏磁检测
Nondestructivetestingofamusementequipments—Part9:Magneticfluxleakagetesting
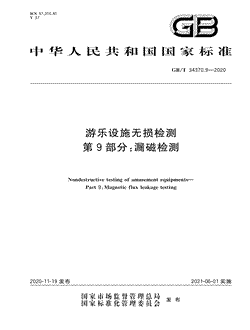
- 中国标准分类号(CCS)Y57
- 国际标准分类号(ICS)97.200.40
- 实施日期2021-06-01
- 文件格式PDF
- 文本页数17页
- 文件大小1.42M
以图片形式预览游乐设施无损检测第9部分:漏磁检测
游乐设施无损检测第9部分:漏磁检测
国家标准 GB/34370.92020 游乐设施无损检测 第9部分:漏磁检测 Nondestrctivetestingofamusementequipments Part9Magneticfluxleakagetesting 2020-11-19发布 2021-06-01实施 国家市场监督管理总局 发布 国家标涯花管理委员会国家标准
GB/T34370.9一2020 次 目 前言 范围 2 规范性引用文件 3 术语和定义 方法概要 安全要求 人员要求 6 检测设备和器材 检测工艺规程 在用管材、板材的漏磁外检测 10在用钢丝绳、拉索的漏磁检测 1 检测记录与报告 附录A(资料性附录)典型构件试件制作要求
GB;/T34370.9一2020 前 言 GB/T34370《游乐设施无损检测》分为以下11部分 第1部分:总则; 第2部分:目视检测; 第3部分;磁粉检测 第4部分;渗透检测; 第5部分;超声检测 第6部分:射线检测 第7部分;涡流检测 第8部分声发射检测 第9部分:漏磁检测; -第10部分;磁记忆检测; 第11部分;超声导波检测
本部分为GB/T34370的第9部分 本部分按照GB/T1.12009给出的规则起草
本部分由全国索道与游乐设施标准化技术委员会(SAC/TC250)提出并归口 本部分起草单位;特种设备检测研究院、华中科技大学、,爱德森(厦门)电子有限公司、北京科海 恒生科技有限公司、深圳华侨城文化旅游科技集团有限公司中山市金马科技娱乐设备股份有限公司、 华强方特文化科技集团股份有限公司、广东长隆集团有限公司、湖南省特种设备检验检测研究院、山东 瑞祥模具有限公司浙江优尔特检测科技有限公司 本部分主要起草人;沈功田,胡斌,王宝轩、,武新军,吴占稳、万强、,苑一琳、林俊明、陈谋财,邓东阁、 文红光、陈涛、刘辉、林伟明、肖化明、魏忠瑞、柳章龙
GB;/T34370.9一2020 游乐设施无损检测 第9部分漏磁检测 范围 GB/T34370的本部分规定了游乐设施的漏磁检测和结果评价方法
本部分适用于游乐设施用外径不小于38mm、壁厚不大于20mm的钢管,厚度不大于20mm的钢 板,直径不小于6mm的钢丝绳、拉索等铁磁性材料构件的漏磁检测
规范性引用文件 下列文件对于本文件的应用是必不可少的
凡是注日期的引用文件,仅注日期的版本适用于本文 件
凡是不注日期的引用文件,其最新版本(包括所有的修改单)适用于本文件
GB/T20306游乐设施术语 GB/T20737无损检测通用术语和定义 GB/T34357无损检测术语漏磁检测 GB/T34370.1游乐设施无损检测第1部分:总则 GB/T34370.5游乐设施无损检测第5部分;超声检测 GB/T34370.6游乐设施无损检测第6部分:射线检测 术语和定义 GB/T20306,GB/T20737,GB/T34357和GB/T34370.1界定的以及下列术语和定义适用于本 文件
3.1 缺陷当量defeetequivalent 与特定或俗成的数值相当的量,本部分是特指依据获得的信号特征给出缺陷的量值
方法概要 4.1基本原理 漏磁检测的原理如图1所示
当铁磁性构件被外加磁化器磁化后,在构件内可产生磁场,若构件上 存在腐蚀或机械损伤等缺陷,则磁力线会泄漏到构件外部,从而在其表面形成漏磁场,如在磁化器中部 放置一个磁场传感器(通常采用霍尔元件或线圈等磁场传感器),则可探测到该漏磁场,由于漏磁场强度 与缺陷深度和大小有关,因此可以通过对漏磁场信号的分析来获得构件上产生缺陷的信息
图2为测 量水平和持之磁场分量的典型信号示意图
GB/T34370.9一2020 磁化器 磁力线 磁场 传感器 构件 漏磁检测原理示意图 0.04 a.04 0.03 0.03 0.02 0.02 0.01 0.01 -0.01 -0.02 -0.03 -0.01 -0.04 10 50 80 90100 40 0 2030 70 10 20 30 40 50 60 80 90 100 距离/mmm 距离/mm 水平分量漏磁场信号 D 垂直分量漏磁场信号 a 图2典型漏磁信号示意图 4.2漏磁检测方法的应用 4.2.1检测时机: 制造过程中的检测; aa b)在役检测
4.2.2 主要用途: a 材料或构件制造过程产生的裂纹、机械损伤、非导磁夹杂的检测及评价 b 设备或构件服役过程中产生的开裂与腐蚀、机械损伤等金属损失的检测及评价
4.3相关影响因素 漏磁检测方法的相关影响因素有 扫查速度与方向; aa 提离值 b) 被检构件的几何形状和电磁特性; c d 检测仪器的灵敏度
5 安全要求 本章没有列出进行检测时所有的安全要求,使用本部分的用户应在检测前建立安全准则
GB;/T34370.9一2020 检测过程中的安全要求至少包括 a 检测人员应遵守被检设备现场的安全要求,根据检测地点的要求穿戴防护工作服和佩戴有关 防护设备 b 应注意避免各种安全隐患,例如碰伤,触电、跌落,挤压,剪切,缠绕、滑倒、溺水、烫伤等 在高空进行操作时,应考虑人员、检测设备器材坠落等因素,并采取必要的保护措施 c d 磁化单元在运输、存放和搬运过程中应避免强磁对人身安全、设备、仪器仪表和环境的影响 检测时,应注意磁场吸力导致的人员受伤和设备损坏及其他辅助电子设备的影响
e 人员要求 从事游乐设施漏磁检测工作的人员,应符合GB/T34370.1的有关规定
检测设备和器材 7.1漏磁检测系统 7.1.1漏磁检测系统应至少包括电源、磁化单元、磁场传感器、信号采集单元、信号显示(或报警)单元、 信号存储单元等,必要时还应有退磁单元和位置记录单元
7.1.2漏磁检测系统应具有对发现的缺陷位置和尺寸或大小进行分析和显示的功能
7.2试件 7.2.1校准试件 7.2.1.1校准试件主要用于漏磁检测仪器各个独立通道的功能测试,调节检测灵敏度、调整检测参数和 保证检测结果准确性
7.2.1.2校准试件应采用与被检测对象相同或铁磁特性相近的材料制作 7.2.2对比试件 7.2.2.1对比试件主要用于实际检测中缺陷的信号当量或量化的评价和确定验收等级
7.2.2.2 对比试件应与被检对象具有相同成相近的规格,牌号,热处理状态、表面状右和电张特性
7.2.3制作要求 试件表面不应沾有异物,且无影响测试结果的缺陷
7.2.3.1 7.2.3.2试件上加工的人工缺陷应进行测定,并满足第9章和第10章的要求 7.3垫片 应采用已知厚度的非导磁材料,推荐厚度为0.5mm的整数倍
检测工艺规程 8 8.1通用检测工艺规程 从事漏磁检测的单位应按GB/T34370.1和本部分的要求制定通用检测工艺规程,其内容至少应 包括如下要素: 工艺规程版本号; a
GB/T34370.9一2020 b 适用范围; 依据的标准、法规或其他技术文件, c d 检测人员资格要求; 被检对象的材料和几何尺寸; e 表面状态,覆盖层或覆盖层厚度; 检测时机; g 检测设备制造单位和型号; h 检测仪器的磁化能力; 检测系统软件; 检测探头制造单位和型号; k 扫查方向、扫查速度和扫查覆盖区域 提离 m 对比试件和校准试件的材料 Tn 检测的标记和原始数据记录要求, 检测后的操作要求; p 检测结果的评价及处理方式; 检测记录、报告和资料存档 编制级别、审核(级别)和批准人; S 制定日期
8.2检测作业指导书或工艺卡 对于每类结构的漏磁检测,应根据实际情况,按照GB/T34370.1,本部分和通用检测工艺规程制定 漏磁检测作业指导书或工艺卡
检测工艺卡内容应至少包括 作业指导书或工艺卡编号 a b 检测执行的标准; 被检测设备和构件的信息:名称、型号、编号、材质,规格尺寸、热处理状态、焊接型式等; 检测设备:名称,规格型号、编号等 传感器型号、励磁方式; 检测时机; 检测区域和表面要求; g 检测部位示意图; h 检测环境要求; 扫查方向、扫查速度和扫查覆盖区域 提离 对比试件和校准试件的材料 m 检测的标记和原始数据记录要求 检测后的操作要求; n 检测结果的评价及处理方式 o 检测过程的记录; p 编制(级别)和审核(级别人员签字及日期
g
GB;/T34370.9一2020 在用管材、板材的漏磁外检测 g.1检测对象 检测对象为外径不小于38mm、壁厚不大于20mm的钢管和厚度不大于20mm的钢板构件
对 于可以从内部进行漏磁检测的较大构件,参照本章执行
9.2检测系统 9.2.1检测设备 检测设备一般由电源、磁化单元、探头、扫查单元、信号处理单元和记录单元等组成
除应满足7.1 的要求外,还应满足9.2.2~9.2.9的要求
9.2.2磁化单元和探头 按不同的被检构件的曲率选用合适的磁化单元和探头
g.2.3通道 仪器和探头应具有足够的通道数,且探头应给出每个检测通道的覆盖范围
9.2.4扫查单元 扫查单元应与被检构件的曲率相匹配,可采用手动或电动的方式进行扫查,最大扫查速度不应低于 0.3mm/s
9.2.5灵敏度 对于小于或等于8mm的壁厚,当涂层厚度小于6mm时,可探测到被检对象表面厚20%深的人工 缺陷;壁厚大于8mm或涂层厚度大于6mm时,其检测灵敏度由用户与检测单位协商确定 9.2.6信号显示 应采用指示灯、屏幕等方式显示缺陷的位置、深度当量或其他信息
9.2.7 系统校准 每年应至少一次采用校准试件进行系统校准
校准通过将检测系统在校准试件上检测人工缺陷来 进行
9.2.8 系统功能核查 应在检测实施前和结束后,采用校准试件对设备进行系统功能核查
在系统遇到故障或者修理后 需进行系统功能核查
9.2.9检测设备的维护 检测实施前应对检测设备进行维护和功能检查,以保证仪器功能正常
在现场进行检测时,如怀疑 设备的检测结果,应对设备进行功能检查和调整,并对每次维护检查的结果进行记录
GB/T34370.9一2020 g.3试件 g.3.1校准试件 校准试件的制作参考附录A中A.1和A.3
9.3.2对比试件 9.3.2.1 对比试件用于对被检测缺陷深度当量的评定 9.3.2.2应选用与被检对象几何尺寸相同,电磁特性相近的材料,按照被检对象的检测要求制作对比 试件
g.3.2.3被检构件的曲率半径不大于150mm时,应采用相同曲率结构的对比试件;被检构件的曲率半 径大于150mm时,可根据检测设备的功能,采用平板对比试件代替曲率结构的对比试件
9.3.2.4对比试件的制作参考A.2和A.4 9.4检测程序 9.4.1资料审查 进行检测前应对被检设备进行资料审查,内容应包括 设备制造文件资料,产品合格证,质量证明文件,竣工图等; a) b)设备运行记录资料:开停车情况、运行参数、工作介质、载荷变化情况以及运行中出现的异常情 况等; 检验资料:历次检验报告; c d 其他资料:修理和改造的文件资料等 9.4.2现场勘查 对被检设备和构件进行现场勘查,找出并设法排除可能影响检测结果的因素
同时,对被检构件进 行定位标识
9.4.3检测工艺卡的编制 对于每个检测设备或每个被检构件,应根据使用的仪器和现场实际情况,按照GB/T34370.1,本部 分和通用检测工艺规程编制漏磁检测工艺卡
g.4.4检测条件确定 被检构件表面应无影响检测的障碍物和干扰检测的异物,如有影响检测的油脂、污物、毛刺和氧化 皮等应清除,以保证检测正常进行
g.4.5扫查方式确定 根据漏磁检测的目的和被检构件的形状和尺寸,确定磁化方向和扫查方式 9.4.6仪器调试 检测前应对仪器进行系统功能性检查和调试
9.4.7 系统校准 9.4.7.1探头,磁化单元和系统主机每次实施检测前都要进行校准,以保证检测结果的准确性,每次校
GB;/T34370.9一2020 准均应记录
系统校准包括位置校准和灵敏度校准
9.4.7.2以下情况应使用对比试件对漏磁检测设备的灵敏度进行检查 每次检测开始前和结束后 a b 怀疑检测设备运行不正常时; c 连续检测时,每8h检查1次; d)合同各方有争议或认为有必要时 9.4.8检测 9.4.8.1若以发现体积型缺陷为检测目的,可采用单一方向扫查方式,若是以发现裂纹为检测目的,应 采用正交扫查方式
9.4.8.2扫查可以采用手动或自动模式进行,扫查速度应尽量保持均匀
g.48.3扫查检测中应保证相邻扫描带之间的有效重叠(一般不低于10%,可依据现场情况适当调 整),不引起漏检
9.5检测结果评价与处理 9.5.1检测数据评价 9.5.1.1 检测时应根据用户的要求确定需报警的缺陷当量深度,在探测到超过此深度的缺陷信号时仪 器应报警
9.5.1.2对于出现报警的部位,应在垂直原扫查方向90°的方向或其他多个方向进行再扫查验证,以确 认是否为真实缺陷
9.5.1.3若确定为真实缺陷,检测人员则应将发现的缺陷位置在构件和图纸上分别做出标识,即为不可 接收信号位置
9.5.2不可接收信号的处理 首先采用目视和小锤敞击的方法进行检测,用以分辨不可接收信号是位于外表面或内表面的 9.5.2.1 缺陷
9.5.2.2对于外表面缺陷可采用深度尺直接测量缺陷的深度
9.5.2.3对于内表面缺陷,应采用超声或射线检测方法进行测量,以更精确地测量缺陷的深度,超声检 测方法按G;B/T34370.5执行射线检测方法按GB/T34370.6执行
9.5.2.4其他不可接收信号的处理方式由检测方和用户协商确定
10 在用钢丝绳拉索的漏磁检测 10.1检测对象 检测对象为直径不小于6mm的在用钢丝绳、拉索 0.2检测系统 0.2.1检测设备 -般由电源,磁化单元,探头信号处理单元和记录单元等组成,必要时可增加扫查单元 检测设备一 除应满足7.1的要求外,还应满足10.2.210.2.8的要求
GB/T34370.9一2020 0.2.2磁化单元和探头 按不同的被检构件的直径选用合适的磁化单元和探头
0.2.3扫查单元 扫查单元应与被检构件的直径相匹配,手动或电动的方式进行扫查,一般扫查速度不大于10 m/S
可采用扫查单元固定、构件运动或构件固定、扫查单元运动的方式
0.2.4灵敏度 LF检测时,可以检出缆索表面断丝对比试件中1根断丝缺陷;LMA检测时,可以检出缆索金属截 面积损失对比试件金属截面积变化1%的缺陷
10.2.5信号显示 应采用指示灯、屏幕等方式显示缺陷的位置、当量或其他信息
10.2.6系统校准 每年应至少采用校准试件进行一次系统校准 10.2.7系统功能核查 应在检测实施前和结束后,采用校准试件对设备进行系统功能核查
在系统遇到故障或者修理后 需进行系统功能核查
10.2.8检测设备的维护 检测实施前应对检测设备进行维护和功能检查,以保证仪器功能正常
在现场进行检测时,如怀疑 设备的检测结果,应对设备进行功能检查和调整,并对每次维护检查的结果进行记录
0.3附件 10.3.1校准试件 校准试件的制作参考A.5
0.3.2对比试件 0.3.2.1对比试件用于对被检测缺陷当量的评定
10.3.2.2应选用与被检对象几何尺寸相同,电磁特性相近的材料,按照被检对象的检测要求制作对比 试件
10.3.2.3对比试件的制作参考A.6
10.4检测程序 0.4.1资料审查 资料审查应包括下列内容 设备制造文件资料:产品合格证、质量证明文件; a b 设备运行记录资料:开停车情况、运行参数,载荷变化情况以及运行中出现的异常情况等 检验资料;历次检验报告; c
GB;/T34370.9一2020 d 其他资料:修理和改造的文件资料等
10.4.2现场勘查 对被检构件周围进行现场勘查,找出并设法排除振动、周围铁磁性物体等可能影响检测结果的因 素
同时,对被检构件进行定位标识
0.4.3检测条件确定 被检构件表面应无影响检测的障碍物和干扰检测的异物,如有影响检测的毛刺和氧化皮等应清除, 以保证检测正常进行
10.4.4扫查方式确定 根据漏磁检测的目的和被检构件的尺寸和安装方式,确定磁化方向、扫查方式和扫查速度
0.4.5仪器调试 检测前应对仪器进行系统功能性检查和调试
10.4.6 系统校准 10.4.6.1探头,磁化单元和系统主机每次实施检测前都要进行校准,以保证检测结果的准确性,每次校 准均应记录
系统校准包括位置校准和灵敏度校准
0.4.6.2以下情况应使用对比试件对漏磁检测设备的灵敏度进行检查 a 每次检测开始前和结束后; b 怀疑检测设备运行不正常时; 连续检测时,每8h检查1次; co 合同各方有争议或认为有必要时 d 10.4.7 检测 10.4.7.1为保证检测结果的可重复性,应进行至少2次的重复操作
10.4.7.2扫查可以采用手动或自动模式进行,扫查速度应尽量保持均匀
10.4.7.3当构件全部工作长度需要多次扫查时,每次调整磁化器磁极方向相对于构件宜前后一致,扫 查检测中应保证相邻扫描段之间的有效重叠(一般不低于1m,可依据现场情况适当调整),不引起漏 检
检测同一个构件时,宜由一台仪器按同一标准完成检测
0.4.7.4当测定金属横截面积损失的百分率时,应以构件上状态完好的位置为基准点
0.5检测结果评价与处理 10.5.1检测数据评价 10.5.1.1检测时应根据有关安全技术规范、产品设计制造使用标准的要求确定需报警的缺陷当量,在 探测到超过此当量信号时,仪器应报警
10.5.1.2对于出现报警的部位,应在磁化方向不变情况下进行双向反复扫查,以确认是否为真实缺陷 并进行目视检测
若确定为真实缺陷,检测人员则应将发现的缺陷位置在构件和图纸上分别做出标识,即为不 10.5.1.3 可接收信号位置
GB/T34370.9一2020 10.5.2不可接收信号的处理 10.5.2.1首先采用目视的方法进行检测,用以分辨不可接收信号是位于外表面或构件内部 10.5.2.2对于外表面缺陷可采用目视检测,确定受损钢丝数量或金属横截面积损失比例
10.5.2.3其他不可接收信号的处理方式由检测方和用户协商确定
1 检测记录与报告 11.1检测记录 检测记录的主要内容不应少于8.2和l1.2规定的内容
11.2检测报告 检测报告应至少包括如下内容 委托单位、报告编号 a 检测单位; b 被检构件(设备)规格、几何尺寸、使用年限、材料牌号、公称直径、涂层厚度,表面状态 c 执行标准、参考标准; d 检测仪器名称、型号、扫描模式 校准和对比试件的材料、尺寸,缺陷的形状; 标准和对比试件的校准结果 g 仪器检测状态参数的设置值 o 图示标明检测部位; 检测设置文件名称及数据文件名称; 用草图、标记或照相描述并定位超出验收标准的不可接收信号的指示及缺陷位置示意图; k 验收准则及检测结论; m检测日期、检测人员和审核人签字及资质
0
GB;/T34370.9一2020 附 录 A 资料性附录 典型构件试件制作要求 平板校准试件 A.1 校准试件应选用与被检对象铁磁性相近的钢板制作,试件的厚度可选用8mm,或其他不超过20mmm 的尺寸;试件的宽度至少为探头最大间距的2倍,试件的长度至少为1250mm
可选用62mm一66mm 范围内的钒刀在校准试件上分别加工出长为探头最大间距的1.5倍、深为板厚的20%、40%,60%和80% 的4条横槽,槽宽度与深度的误差不大于士0.2nmm,槽与槽之间的间距至少为200mm
图A.1为校准试 件的示意图
不小于300mm 200mmm" 200mm" 200mm 不小于300mm 80% 60% mmm 图A.1平板校准试件示意图 A.2平板对比试件 对比试件应选用与被检对象同种材质、相同的生产工艺和相同的组织成分的同等厚度的材料制作 试件的宽度至少为探头阵列宽度的2倍,试件的长度至少为扫查器长度的3偕再加400mm
除合同 有关各方另有约定之外,应在校准试件长轴中心线上分别加工出深度为板厚的20%,40%,60%和80% 的四个球形孔
8mm及以下的板厚选择直径为20mm的球头刀,8mm以上的板厚选择直径为 25nmm的球头刀,深度误差不大于士0.2mm;孔与孔之间的间距至少为200nmm,两端孔距试件边沿 的距离相同
图A.2为对比试件的示意图
1
GB/T34370.9一2020 不小于300mm 200mm 200mm 200mm 不小于300mm 40%球孔示意图 图A.2平板对比试件示意图 圆管校准试件 圆形管件校准试件应选用与被检测管件几何尺寸相同、铁磁性能相同或相近的材料制作,试件的厚 度为8mm或不超过20mm,最小长度为2000mm
在校准试件上从管件外表面分别加工宽度为 2mm,深为壁厚的20%、40%,60%、80%的4条周向槽,槽宽度与深度的公差不大于士0.2mm. ,槽与 槽之间的间距至少为200 mm
如有需要,也可从内壁加工
图A.3为管件校准试件的示意图
A.4圆管对比试件 圆形管件对比试件应选用与被检测管件几何尺寸相同、铁磁性能相同或相近的材料制作,试件的最 小长度为2000mm,且不得小于管件的外周长
依据被检对象在对比试件外壁(或/和内壁)上分别加 工出深为壁厚的20%、40%60%、80%的至少4个球形孔
8mm及以下的壁厚选择直径为20mm的 球头钝刀,8mm以上的壁厚选择直径为25mm的球头铁刀,深度的公差不大于士0.2mm;孔与孔之间 的间距至少为200mm,两端孔距试件边沿的距离相同,且不小于300mm 12
GB;/T34370.9一2020 内表面开槽 不不 200mm200mm200 mmk aoo 300 mm " 40% % 6mm 6 8% 外表面开槽 不 不小于 Lo0'咖200mm.200.mm200mm.30" 609% 80% 吗% 4g% 6,mm B一B 图A.3管件校准试件的示意图 A.5绳/索校准试件 A.5.1绳/索断丝校准试件 绳/'索断丝校准试件所用钢丝绳应根据检测仪所能检测绳/索外径尺寸的上限和下限规格分别选 取
试件长度不小于2.5m,弯曲度不大于15mm/m
采用人工锯断方式在绳/索上制作断丝
断丝 位置间隔0.5m左右,断丝为1根、2根、3根共3处,距离绳/索端部不小于400mm
断丝要求丝径习 1.5mm、断口间隙>2mm
A.5.2绳/索金属截面积损失校准试件 绳/索金属截面积损失校准试件所用钢管应根据检测仪所能检测绳/索外径尺寸的上限和下限规格 分别选取
钢管金属截面积与等同直径绳/索金属截面积相同
采用下述方法中的一种进行制作
方法一;试件长度不小于2.5m,弯曲度不大于15mm/m
人工缺陷为纵向槽,槽的长度不小于 300mm,间隔不小于300mm、距离管端部不小于400mm、宽度和深度按照截面积减小的百分比确定 要求金属截面积变化为1%,2%,3%、4%的位置共4处
方法二;试件长度不小于1m,弯曲度不大于15mm/m
在钢管内插人多根等直径的钢丝以增加 金属截面积的总面积
钢丝的截面积为钢管截面积的1%或更小,多根钢丝的截面积偏差小于1%
测 13
GB/T34370.9一2020 试时将钢管放人漏磁检测传感器中,并使传感器处于钢管中部,再逐根插人钢丝使金属截面总面积增 加4%.
A.6绳/索对比试件 A.6.1绳/索断丝对比试件 绳/索断丝对比试件所用钢丝绳应与被检钢丝绳相匹配
试件长度不小于2.5m,弯曲度不大于15 mm/m
采用人工锯断方式在绳/索上制作断丝
断丝 位置间隔0.5m左右,断丝为1根、2根、3根共3处,距离绳/索端部不小于400mm
断丝要求丝径> 1.5tmm、 断口间隙>2" 2mm
A.6.2绳/索金属截面积损失对比试件 绳/索金属截面积损失对比试件所用钢管应与被检钢丝绳外径相同金属截面积相同
采用下述方 一种进行制作
法中的- 方法一;试件长度不小于25m,弯曲度不大于15mm/m
人工缺陷为纵向槽,槽的长度不小于 ,间隔不小于300 300mm mm、距离管端部不小于400mm、宽度和深度按照截面积减小的百分比确定 要求金属截面积变化为1%、,2%、3%、4%的位置共4处
方法二:试件长度不小于1m,弯曲度不大于15mm/m
在钢管内插人多根等直径的钢丝以增加 金属截面积的总面积
钢丝的截面积为钢管截面积的1%或更小,多根钢丝的截面积偏差小于1%
测 试时将钢管放人漏磁检测传感器中,并使传感器处于钢管中部,再逐根插人钢丝使金属截面总面积增 加4%
方法三;在待测绳/索上选取状态良好区域,将多根等直径的钢丝插人该区域与传感器之间以增加 金属截面积的总面积
钢丝的截面积为待测绳/索截面积的1%或更小,多根钢丝的截面积偏差小于 1%,再逐根插人钢丝使金属截面总面积增加4%或最大可插人钢丝数量 14
游乐设施无损检测第9部分:漏磁检测GB/T34370.9-2020详解
随着游乐设施的不断发展和更新,对其安全性能的要求也越来越高。在使用过程中,游乐设施受到各种因素的影响,如振动、冲击、腐蚀等,这些因素会使得设备出现缺陷或损伤,危及人员安全。为了及时发现设备缺陷和损伤,保证游乐设施的安全性能,需要进行定期无损检测。
漏磁检测是游乐设施无损检测的一种重要方法,其原理是利用电磁感应法检测设备表面磁场变化,从而判断设备是否存在缺陷。漏磁检测不需要对设备进行破坏性取样,操作过程简单、快捷、无污染。在GB/T34370.9-2020标准中,漏磁检测被作为一种常用的无损检测方法之一。
漏磁检测的流程:
1. 检测前准备:根据设备类型和检测要求,选择合适的漏磁检测仪器,并对其进行校验和调试。
2. 检测区域划分:将设备表面划分成若干个区域,每个区域应保持相同的磁场特性。
3. 磁化处理:使用磁化电源对设备进行磁化处理,使得设备表面形成一定的磁场。
4. 漏磁检测:对设备表面进行扫描,利用漏磁检测仪器检测磁场变化,分析并确认缺陷。
5. 缺陷评估:根据漏磁检测结果,对设备缺陷进行评估和分类,确定后续处理措施。
漏磁检测的优势:
1. 操作简便:漏磁检测不需要取样,操作过程简单、快捷、无污染。
2. 检测范围广:漏磁检测适用于大部分金属材料和结构件的无损检测。
3. 检测效果好:漏磁检测能够发现细小的缺陷、裂纹以及表面变形等问题,检测结果准确可靠。
总结:
漏磁检测是游乐设施无损检测中一种常用的方法,其操作简便、检测效果好。在实际使用中,需要严格按照GB/T34370.9-2020标准执行,保证检测结果的可靠性和准确性。同时,在漏磁检测前需要对设备进行充分的准备工作,并根据检测结果对设备缺陷进行评估和分类,确定后续处理措施。
总之,漏磁检测是游乐设施无损检测中一种重要的方法,能够有效检测设备表面缺陷和损伤,保障游乐设施的安全性能。GB/T34370.9-2020标准为漏磁检测提供了详细的规范和要求,为专业人士提供了有力的技术指导。