GB/T31817-2015
风力发电设施防护涂装技术规范
Specificationofcoatingforcorrosionprotectionofwindpowerequipments
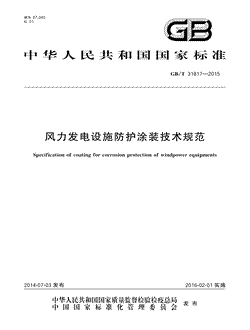
- 中国标准分类号(CCS)G51
- 国际标准分类号(ICS)87.040
- 实施日期2016-02-01
- 文件格式PDF
- 文本页数24页
- 文件大小559.73KB
以图片形式预览风力发电设施防护涂装技术规范
风力发电设施防护涂装技术规范
国家标准 GB/T31817一2015 风力发电设施防护涂装技术规范 Speeifieationofeoatingforcorrosiomprotectionofwindpowerequipments 2014-07-03发布 2016-02-01实施 国家质量监督检验检疫总局 发布 国家标准化管理委员会国家标准
GB/T31817一2015 目 次 前言 范围 规范性引用文件 术语和定义 分类 要求 试验方法 检验规则 5 安全、卫生和环境保护 验收 附录A(资料性附录)腐蚀环境分类 附录B(规范性附录涂料性能要求和试验方法 附录c规范性附录)基料中硅氧键含量测定方法 20
GB/T31817一2015 前 言 本标准按照GB/T1.1一2009给出的规则起草
本标准由石油和化学工业联合会提出
本标准由全国涂料和颜料标准化技术委员会(SAC/TC5)归口
本标准主要起草单位:中海油常州涂料化工研究院有限公司、海虹老人涂料()有限公司、阿克 苏诺贝尔防护涂料(苏州)有限公司、新疆金风科技股份有限公司、广东明阳风电产业集团有限公司、西 北永新涂料有限公司,冶建新材料股份有限公司,庞贝捷漆油贸易(上海)有限公司,立邦涂料()有 限公司、常熟三爱富中昊化工新材料有限公司,大金氟化工()有限公司、株洲时代新材料科技股份 有限公司,无锡福斯特涂料有限公司、中远关西涂料化工有限公司,河北晨阳工贸集团有限公司,无锡市 联邦涂料有限公司
本标准主要起草人;苏春海、李荣俊、刘进伟,吴、詹耀、李华明,武占海、史优良、吴慧、赵宏鑫、 钱晓锋、嵇麟、曾凡辉、索严林、郭建军、杜景恰、花东栓、马尘威
m
GB/T31817一2015 风力发电设施防护涂装技术规范 范围 本标准规定了内陆和海上风电设施用肪护涂层的技术条件,包括防护涂层的分类,爱求,试验方法 检验规则、安全、卫生和环境保护、验收 本标准适用于内陆和海上风电设施防护涂层的初始涂装及修补涂装
规范性引用文件 下列文件对于本文件的应用是必不可少的
凡是注日期的引用文件,仅注日期的版本适用于本文 件
凡是不注日期的引用文件,其最新版本(包括所有的修改单)适用于本文件 GB/T17241979涂料细度测定法 GB/T1725一2007色漆、清漆和塑料不挥发物含量的测定 漆腹、腻子膜干嫌时间渊定法 GB/T1728 1979 GB/T1732 1993漆膜耐冲击测定法 GB/T1733 1993漆膜耐水性测定法 GB/T17402007漆膜耐湿热测定法 GB/T1748一1979腻子膜柔韧性测定法 GB/T1766一2008色漆和清漆涂层老化的评级方法 cB/T1768一2o色漆和清漆耐磨性的测定旋转橡胶砂轮法 GB/T1770一2008涂膜、腻子膜打磨性测定法 GB/T17712007 色漆和清漆耐中性盐雾性能的测定 GB/T1865一2009色漆和清漆人工气候老化和人工辐射曝露滤过的饥狐辐射 GB/T3186色漆、清漆和色漆与清漆用原材料取样 GB/T5210一2006色漆和清漆拉开法附着力试验 GB6514一2008涂装作业安全规程涂漆工艺安全及其通风净化 GB/T6739一2006色漆和清漆铅笔法测定漆膜硬度 GB/T6742一2007色漆和清漆弯曲试验(圆柱轴 GB/T67502007 色漆和清漆密度的测定比重瓶法 G;B7691一2003涂装作业安全规程安全管理通则 GB7692一2012涂装作业安全规程涂漆前处理工艺安全及其通风净化 GB/T7790一2008色漆和清漆暴露在海水中的涂层耐阴极剥离性能的测定 GB/T8923.1涂覆涂料前钢材表面处理表面清洁度的目视评定第1部分;未涂覆过的钢材 表面和全面清除原有涂层后的钢材表面的锈蚀等级和处理等级 GB/T8923.2涂覆涂料前钢材表面处理表面清洁度的目视评定第2部分:已涂覆过的钢材 表面局部清除原有涂层后的处理等级 GB/T9274一1988色漆和清漆耐液体介质的测定 GB/T9286一1998色漆和清漆漆膜的划格试验 GB/T13288.1涂覆涂料前钢材表面处理喷射清理后的钢材表面粗糙度特性第1部分:用于
GB/T31817一2015 评定喷射清理后钢材表面粗糙度的IsO表面粗糙度比较样块的技术要求和定义 (GB/T13452.2一2008色漆和清漆漆膜厚度的测定 GB/T18570.3涂覆涂料前钢材表面处理表面清洁度的评定试验第3部分:涂覆涂料前钢材 表面的灰尘评定(压敏粘带法 GB/T18570.6涂覆涂料前钢材表面处理表面清洁度的评定试验第6部分:可溶性杂质的取 样Bresle法 GB/T18570.9涂覆涂料前钢材表面处理表面清洁度的评定试验第9部分;水溶性盐的现场 电导率测定法 GB/T18838.1涂覆涂料前钢材表面处理喷射清理用金属磨料的技术要求导则和分类 GB/T23987一2009色漆和清漆涂层的人工老化曝露曝露于荧光紫外线和水 cB/30790.2一304色漆和清漆防护涂料体系对钥结构的盼腐蚀保护第2部分;环境分类 GB502052001钢结构工程施工质量验收规范 GB50212一2014建筑防腐蚀工程施工规范 HG/T3668一2009富锌底漆 HG;/T37922014交联型氟树脂涂料 1so4628-1色漆和清漆漆膜老化的评定缺陷的数量和大小以及外观均匀变化程度的评定 第1部分;通则和评定体系(PaintandVarmishes一Evaluationofdegradtionofcoatings一Desingnation ofquantityandsizeofdefects,andofintensityofuniformchangesinappearance -Partl:(Generalin- troductionanddesignationsystem 色漆和清漆漆膜老化的评定缺陷的数量和大小以及外观均匀变化程度的评定 ISO4628-2 第2部分;起泡等级的评定(PaintandVarnishesEvaluationofdegradtionofcoatingsDesingnationm ofquantityandsizeofdefects,andofintensityofuniformchangesinappearancePart2:Assessment ofdegreeofblistering IsO4628-3色漆和清漆漆膜老化的评定缺陷的数量和大小以及外观均匀变化程度的评定 第3部分;生锈等级的评定(PaintandVarnishes一Ewaluationofdegradtionofcoatings一Desingnation ofquantityandsizeofdefects,andofintensityofuniformchangesinappearancePart3:Assessment ofdegreeofrusting ISO4628-4色漆和清漆漆膜老化的评定缺陷的数量和大小以及外观均匀变化程度的评定 第4部分:开裂等级的评定(PaintandVarnishes一Evaluationofdegradtionofcoatings一Desingnationm ofquantityandsizeofdefects,andofintensityofuniformchangesinappearancePart4:Assessment ofdegreeofcracking 1SO4628-5色漆和清漆漆膜老化的评定缺陷的数量和大小以及外观均匀变化程度的评定 第5部分;剥落等级的评定(PaintandVarnishes一Evaluationofdegradtionofcoatings一Desingnationm ofquantityandsizeofdefeets,andofintensityofuniformchangesinappearance一Part5;Assessment ofdegreeoflaking) ISO4628-6色漆和清漆漆膜老化的评定缺陷的数量和大小以及外观均匀变化程度的评定 第6部分:胶带纸法评定粉化等级PaintandVarnishes一Evaluationofdegradtionofcoatings uniformchangesinappearance Desingnationofquantityandsizeofdefeets,andofintensityof halkin tapemethod Part6:AssessmentofdegreeolG ingby ISO4628-7 色漆和清漆漆膜老化的评定缺陷的数量和大小以及外观均匀变化程度的评定 S 第7部分;天鹅绒布法评定粉化等级(Paintanu Varnishes一Evaluationofdegradtionof coatings ofuniform tonofquantityandsizeofdefeets,ando Desingnat intensity changesinappearance Part7:Assessment tafdeEreofchalkin ingbyvelvetmethod
GB/T31817一2015 ISO4628-8色漆和清漆漆膜老化的评定缺陷的数量和大小以及外观均匀变化程度的评定 aintandVarnishesEvaluationofde" 第8部分:划线或其他人造缺陷周边剥离和腐蚀等级的评定(Pai Desingnationofquantityandsizeofdefects, ts,andofintensityofuniformchanges gradtionofc coatingS Part8:Assessmentofdes eofdelaminationandcorrosionaroundascribe inapPpearance egree ISO4628-10 色漆和清漆漆膜老化的评定缺陷的数量和大小以及外观均匀变化程度的评定 第10部分:丝状腐蚀等级的评定PaintandVarnishesEvaluationofdegradtionofcoatings Desingnation ofquantityand ofdefects,andofintensityofuniformchanges S1Ze 1nappearanCe Part10:Assessmentofdegreeoffiliformcorrosion 色漆和清漆海上建筑及相关结构用防护涂料体系性能要求(Paintsandvarni ISO20340:2009 shesPerformancerequirementsforprotectivepaintsystemsforoffshoreandrelatedstructures 术语和定义 下列术语和定义适用于本文件
3 大气类型typeofatmsphere 以大气中含有的腐蚀介质类型和它们的浓度为基础进行大气类型的表征
3.2 耐久性durability 防护徐料体系从涂装完工后到第一次主要维护徐装前的预朋使用期限
3.3 防护涂料体系proteetivepaintsystem 已被涂装或将被涂装到基材上提供防腐蚀保护的色漆涂层或相关产品的总称 3.4 适用期potlile 多组分涂料混合后可使用的最长时间
3.5 可重涂性recoatability 每道涂层之间在一定涂装间隔内形成无缺陷的附着
分类 4.1涂层体系设计年限分类 按设计年限分为两类 -普通型,<15年; 长效型,>15年
4.2腐蚀环境分类 腐蚀环境分类符合GB/T30790.2一2014的要求,参见附录A
4.3涂装部位分类 按涂装部位分为五类: -叶片;
GB/T31817一2015 塔筒; 法兰; 基础环与桩基; 电机、机舱罩及其他
4.4涂装时期分类 按涂装时期分为两类: -初始涂装:风电设施钢结构的初次涂装; -修补涂装:风电设施在其运营全过程中对涂层进行的维修保养
要求 涂装施工单位基本要求 5.1 施工单位应具有防腐保温武级及以上资质,具备保证工程安全、质量的能力
5.1.1 5.1.2施工人员应具备正确施工的能力
关键施工工序喷射清理,喷漆、质检)施工人员应获得涂装 中级工及以上证书
特种作业人员应具备相应资格
5.2涂层体系要求 5.2.1涂层体系配套要求 5.2.1.1中等腐蚀环境(c3) 按照腐蚀环境、工况条件,涂装部位、防腐年限设计涂层配套体系
中等腐蚀环境(C3)涂层体系 配套应符合表1的要求
表1中等腐蚀环境(c3)涂层体系配套要求 设计年限为普通型涂装体系 设计年限为长效型涂装体系 涂装部位 最低干膜厚度 最低干膜厚度 涂料名称 涂料名称 m Amm 商定 腻子 腻子 商定 底漆 叶片 00 底漆 140 60 60 聚氨酯面漆 聚氨酯面漆 商定 腻子 腻子 商定 叶片 聚氨酯面漆 2×80 聚氨酯面漆 2×100 厚浆型环氧漆 厚浆型环氧漆 100 140 外表面 聚氨酯面漆 60 聚氨酯面漆 60 塔筒 内表面 厚浆型环氧漆 120 厚浆型环氧底漆 160 法兰(接触面) 无机富锌底漆 无机富锌底漆 50 50 240 240 厚浆型环氧漆 厚浆型环氧漆 外表面 聚氨酯面漆 50 聚氨酯面漆 50 基础环 内表面 厚浆型环氧漆 厚浆型环氧漆 240 240
GB/T31817一2015 表1(续 设计年限为普通型涂装体系 设计年限为长效型涂装体系 涂装部位 最低干膜厚度 最低干膜厚度 涂料名称 涂料名称 mm m 厚浆型环氧漆 s0 厚浆型环氧漆 100 碳钢 sO0 60 聚氨酯面漆 聚氨酯面漆 电机.机舱镀锌镀铝 专用环氧底漆 专用环氧底漆 60 o0 50 50 罩及其他 及合金钢 聚氨酯面漆 聚氨酯面漆 聚氨酯底漆或环氧底淡 聚氨酯底漆或环氧底漆 80 o0 玻璃钢 8o 80 聚氨酯面漆 聚氨酯面漆 C3环境若伴有风沙的条件下,则应适当增加配套涂层的厚度
基础环暴露部位的外表面应用面漆保护 注1:根据叶片的材质腻子可选择环氧腻子,聚氨酯腻子或其他类型;面漆可选择聚硅氧婉、聚脉、氟碳等面漆
注2塔简外表面要求高耐久性时,可采用氟碳面漆,聚硅氧烧面漆和底面合一聚脉体系等
注3;塔筒内表面要求高耐久性时,可加涂聚氨酯面漆
5.2.1.2高等腐蚀环境(C4) 按照腐蚀环境、工况条件,涂装部位、防腐年限设计涂层配套体系
高等腐蚀环境(C4)涂层体系 配套应符合表2的要求
表2高等腐蚀环境(c4)涂层体系配套要求 设计年限为普通型涂装体系 设计年限为长效型涂装体系 涂装部位 最低干膜厚度 最低干膜厚度 涂料名称 涂料名称 Am m 腻子 商定 商定 腻子 底漆 100 底漆 叶片 140 60 聚氨醋面漆 60 聚氨醋面漆 腻子 商定 腻子 商定 叶片 聚氨酯面漆 2×80 聚氨酯面漆 2X100 60 环氧富锌底漆 60 环氧富锌底漆 120 外表面 环氧云铁中间漆 环氧云铁中间漆 60 60 聚氨酯面漆 聚氨酯面漆 塔筒 厚浆型环氧漆 80 厚浆型环氧底漆 100 内表面 厚浆型环氧漆 8o 厚浆型环氧漆 100 50 法兰(接触面 无机富锌底漆 50 无机富锌底漆 厚浆型环氧漆 500 厚浆型环氧漆 500 外表面 50 50 聚氨酯面漆 聚氨酯面漆 基础环 内表面 厚浆型环氧漆 330 厚浆型环氧漆 500
GB/I31817一2015 表2(续 设计年限为普通型涂装体系 设计年限为长效型涂装体系 涂装部位 最低干膜厚度 最低干膜厚度 涂料名称 涂料名称 mm m 160 厚浆型环氧漆 8o 厚浆型环氧漆 碳钢 60 80 聚氨酯面漆 聚氨酯面漆 电机.机舱镀锌镀铝 专用环氧底漆 6o 专用环氧底漆 60 60 80 罩及其他 及合金钢 聚氨酯面漆 聚氨酯面漆 聚氨酯底漆或环氧底淡 聚氨酯底漆或环氧底漆 80 s" 玻璃钢 8o 80 聚氨酯面漆 聚氨酯面漆 c4环境若伴有风沙的条件下,则应适当增加配套涂层的厚度
基础环暴露部位的外表面应用面漆保护 注1,根据叶片的材质腻子可选择环氧腻子,聚氨酯腻子或其他类型;面漆可选择聚硅氧烧、聚脉、氟碳等面漆
注2塔简外表面要求高耐久性时,可采用氟碳面漆,聚硅氧烧面漆和底面合一聚脉体系等
注3:塔筒内表面要求高耐久性时,可加涂聚氨酯面漆
5.2.1.3海洋腐蚀环境(C5-M)/Im2 按照腐蚀环境、工况条件,涂装部位、防腐年限设计涂层配套体系
海洋腐蚀环境(C5-M)/Im2涂 层体系配套应符合表3的要求
表3海洋腐蚀环境(c5-M/Im2涂层体系配套要求 设计年限为长效型涂装体系 涂装部位 最低干膜厚度 涂料名称 Am 腻子 商定 叶片 底漆 180 聚氨酯面谈 60 腻子 商定 叶片 聚氨酯面漆 2×100 环氧富锌底漆 60 外表面 环氧云铁中间漆 200 聚氨酯面漆 60 塔筒 环氧富锌底漆 60 内表面 180 环氧云铁中间漆 法兰(接触面 无机富锌底漆 60 环氧玻璃鳞片漆或改性环氧漆 500 大气区 聚氨酯面漆 80 导管架 潮汐和浪溅区 环氧玻璃鳞片漆或改性环氧漆 600 及桩基 水下区 环氧玻璃鳞片漆或改性环氧漆 500 桩基内表面暴露区 环氧玻璃鳞片漆或超强环氧漆 600
GB/T31817一2015 表3(续 设计年限为长效型涂装体系 涂装部位 最低干膜厚度 涂料名称 Am 环氧富锌底漆 60 碳钠 厚浆型环氧漆 160 聚氨酯面漆 60 电机、机舱 专用环氧底漆 80 罩及其他 镀锌镀铝及合金钢 聚氨酯面漆 60 环氧底漆 100 玻璃钢 聚氨酯面漆 100 注1根据叶片的材质腻子可选择环氧腻子,聚氨酯腻子或其他类型;面漆可选择聚硅氧炕、聚脉,氟碳等面漆
注2:塔筒外表面要求高耐久性时,可采用氟碳面漆,聚硅氧烧面漆和底面合一聚脉体系等
注3塔筒内表面要求高耐久性时,可加涂聚氨酯面漆
5.2.2涂层配套体系说明 较高防腐等级的涂层配套体系也适用于较低防腐等级的涂层配套体系,并可适当降低涂层厚度
5.2.3涂层体系性能要求(不含叶片 5.2.3.1中等腐蚀环境(C3)下涂层体系性能要求 中等腐蚀环境(C3)下涂层体系性能应符合表4的要求
表4中等腐蚀环境(C3)下涂层体系性能要求 耐盐雾性" 人工加速老化缸灯 耐水性" 附着力 涂装部位 设计年限 MPa 普通型 120 240 1000 塔筒外表面 长效型 480 1000 240 普通型 塔筒内表面 长效型 120 >5 普通型 240 000 基础环 48o 长效型 2000 普通型 1000 电机.机舱罩及其他 长效型 120 1000 耐水性试验后不生锈,不起泡,不开裂、,不剥落,允许变色1级和失光1级
耐盐雾性试验后不起泡、不剥落,不生锈、不开裂
人工加速老化性能试验后不生锈、不起泡、不剥落,不开裂,不粉化,允许变色2级和失光2级;当采用高性能面 漆例如氟碳、聚硅氧烧时,人工加速老化时间为3000h
GB/I31817一2015 5.2.3.2高等腐蚀环境(C4)环境下涂层体系性能要求 高等腐蚀环境(C4)环境下涂层体系性能应符合表5的要求
表5高等腐蚀环境(C4)环境下涂层体系性能要求 耐水性" 附着力 耐盐雾性" 人工加速老化(乞灯 涂装部位 设计年限 MPa 普通型 240 1000 1000 塔简外表面 长效型 480 2000 1000 普通型 120 600 塔筒内表面 长效型 240 1000 2000 普通型 480 基础环 长效型 480 3000 120 普通型 600 1000 电机.机舱罩及其他 长效型 240 1000 l000 耐水性试验后不生锈、不起泡、不开裂、不剥落,允许变色1级和失光1级
耐盐雾性试验后不起泡、不剥落,不生锈,不开裂
人工加速老化性能试验后不生锈、不起泡、不剥落、不开裂,不粉化,允许变色2级和失光2级;当采用高性能面 漆例如氟碳,聚硅氧烧时,人工加速老化时间为3000h. 5.2.3.3海洋腐蚀环境(C5-M/Im2涂层体系性能要求 海洋腐蚀环境(C5-M)/Im2涂层体系性能应符合表6的要求
表6海洋腐蚀环境(C5-M/Im2涂层体系性能要求 耐盐水性" 耐阴极剥离 附着力 人工加速老化'(饥灯循环老化试验 耐盐雾性" 涂装部位 (3%NaCl水溶液》 MPa h 3000 1000 4200 塔筒外表面 720 塔简内表面 480 2000 >5 导管架及桩基 4200 720 3000 200 电机、机舱 480 2000 1000 罩及其他 耐盐水性试验后不生锈、不起泡、不开裂、不剥落,允许变色1级和失光1级
耐盐雾性试验后不起泡、不剥落、不生锈,不开裂
人工加速老化性能试验后不生锈,不起泡、不剥落,不开裂、不粉化,允许变色2级和失光2级;当采用高性能面 漆例如氟碳、聚硅氧烧时,人工加速老化时间为3000h
5.2.4叶片涂层性能要求 叶片涂层性能应符合表7的要求
GB/T31817一2015 表7叶片涂层性能要求 目 指 标 项 涂膜外观 平整光滑 23士2"C 弯曲试验/mm 20土2)C/1h. 耐磨性(1000g/1000r,砂轮型号:CS-10)/mg 50 附着力(拉开法) 平均值大于6MPa,单个测试值不低于5MPa 耐油性(液压油,4h 不起泡,不起皱,允许轻微变色 不起泡,不起皱,允许轻微变色 耐酸性(50g/LH.SO溶液,l68h 耐碱性(100g/LNaOH溶液,961 不起泡,不起皱,允许轻微变色 h 无起泡、开裂、剥落等现象
拉开法附着力;平均 耐盐雾性(720h 值大于5MPa,单个测试值不低于4MPa 耐湿热性(480 涂膜无明显变化 不起泡、不开裂,不脱层,允许变色2级、失光2级 人工加速老化试验(UVA-340nm),(2000h 和粉化2 级 5.3 涂料性能要求 涂料性能要求见附录B 5.4工艺要求 5.4.1表面处理 5.4.1.1钢材表面预处理 5.4.1.1.1结构预处理 钢结构在喷射清理除锈前应进行必要的结构预处理,包括 粗槌焊缝打磨光顺,焊接飞溅物用刮刀或砂轮机除去
焊缝上深为0.8mm以上或宽度小于 深度的咬边(除封闭的内表面外)应补焊处理,并打磨光顺; 锐边用砂轮打磨成曲率半径为2mm的圆角; 切割边的峰谷差超过1mm时,打磨到1mm以下
厚钢板边缘切割硬化层,用砂轮磨掉 0.3mm; 表面层叠、裂缝夹杂物,打磨处理,必要时补悍
5.4.1.1.2除油 表面油和油脂的清洁应用溶剂或专用清洗剂和干净的抹布擦洗
5.4.1.1.3除盐分 经喷射清理后,检测钢板表面水溶性盐含量,(C5-M)/Im2环境下水溶性盐(相当于NaCI)含量不 大于50mg/m',其他环境下不大于100mg/m'
表面存在的盐分超标时应采用高压淡水冲洗
GB/I31817一2015 5.4.1.1.4 除锈 除另有规定外,磨料、除锈等级、表面粗糙度要求如下 -喷射清理用金属磨料应符合GB/T18838.1的要求; 根据表面粗糙度的要求,选用合适粒度的磨料 -热喷锌、喷铝,钢材表面处理分别应达到GB/T8923.1规定的Sa3级; -无机富锌底漆,钢材表面处理应达到GB/T8923.1规定的Sa2~Sa3级; -环氧富锌底漆,钢材表面处理应达到GB/T8923.1规定的Sa2%级; -不便于喷射除锈的部位,手工或动力工具除锈至GB/T8923.1规定的St3级
5.4.1.1.5除尘 喷射清理完工后,除去喷射清理残渣,使用真空吸尘器或无油、无水的压缩空气,清理表面灰尘 清洁后的喷射清理表面灰尘清洁度要求不大于GB/T18570.3规定的3级
二次表面处理 5.4.1.2 5.4.1.2.1钢结构焊接修复预处理 按5.4.1.1要求进行
5.4.1.2.2钢结构二次表面处理 钢结构二次表面处理,包括 钢结构外表面,在涂装涂层底漆时宜采用喷射方法进行二次表面处理; 内表面无机硅酸锌车间底漆基本完好时,可不进行二次表面处理,但要除去表面油污、可溶性 锌盐,灰尘等,并对焊缝、锈蚀处打磨至GB/T8923.1规定的St3级
5.4.1.3表面处理后涂装的时间限定 当处理过的表面干燥且无油、无灰情况下,应立即喷涂预处理车间底漆作为钢材的短期防护
二次 表面处理后在无污染的情况下或者任何可见的表面损坏发生前(一般为4h),施工底漆作为防护 5.4.1.4玻璃钢表面预处理 加工后的玻璃钢要用适当的清洁剂去除脱模剂,油污、油脂等污染物,然后用高压新鲜淡水冲洗,或 者用适当的溶剂/脱脂剂进行彻底的清洁
等底材完全清洁并且干燥后,用P80或P120等级的砂纸进 行机械或手工打磨,打磨方式宜用打圈式打磨,尽量使打磨砂纸平面和玻璃钢基材平面保持基本平行, 不要打磨出半月型型面,也尽量不要打磨到玻璃纤维层
砂纸打磨以后,应彻底除去玻璃钢基材表面的 灰尘,除尘有几种方法;其一,如果有条件最好使用真空吸尘机,吸尽玻璃钢底材表面的灰尘;其二,可用 清洁的压缩空气去除玻璃钢底材表面的灰尘,然后用无尘布清洁;其三是用水冲洗玻璃钢底材,表面干 燥后用无尘布清洁
另外也应检查玻璃钢底材是否打磨到位;逆光观察玻璃钢底材,表面呈现无光/哑 光状态,表明打磨到位,否则应进行再打磨
5.4.2涂装要求 5.4.2.1施工环境要求 施工环境温度538C,空气相对湿度不大于85%,并且钢材表面温度高于露点3C以上;不应在 雨、雪,雾,大风和较大灰尘的条件下进行户外施工;低温(5以下)施工时采用相应的低温固化型涂料
10o
GB/T31817一2015 5.4.2.2涂料配制和使用时间 5.4.2.2.1涂料应充分搅拌均匀后方可施工,宜采用电动或气动搅拌装置
对于双组分或多组分涂料 应先将各组分分别搅拌均匀后,再严格按比例混合并搅拌均匀
5.4.2.2.2混合好的涂料按照产品说明书的规定时间进行熟化
5.4.2.2.3涂料的混合使用期按产品说明书规定的适用期执行 5.4.2.2.4低温施工时,涂料混合和固化的温度应符合产品说明书的规定
5.4.2.3涂装工艺 5.4.2.3.1涂装方法 涂装方法分为 大面积喷涂应采用高压无气喷涂施工及其他施工方式 -焊缝、棱角沟槽,边角、流水孔等不易涂装的角落部位应采用刷涂或辗涂进行手工预涂处理,然 后再大面积喷涂 细长、小面积以及复杂形状构件可采用空气喷涂或刷涂、涂施工 按5.4.1.4要求对玻璃钢表面预处理,用大缝腻子刮涂风电叶片表面较大空洞和缺陷的地方, 用针孔腻子刮涂风电叶片表面的细孔和小瑕疵
进行第一遍薄刮,确保腻子与玻璃钢基材紧 密结合,大缝腻子与针孔腻子配合使用,将叶片表面的缺陷进行修补,刮涂一遍膜厚在 干燥后进行粗打磨
粗打磨后,将打磨好的腻子表面粉尘清除干净,进行第 50&m250丛m, 二遍满批,要求涂刮平整,不漏底,腻子刮涂干膜厚度50m1000m,待表干后,再找补缺 陷部位进行刮涂修补,待干燥后进行细打磨,打磨完成清除腻子表面粉尘;进行第三遍薄刮,腻 子涂刮一遍干膜厚度50 )um一250um,对针眼,轻微缺陷进行再次找补,待腻子彻底干燥后进 行细打磨,打磨过程中如有细小针眼及轻微缺陷可用针眼腻子重复找补,直至腻子表面光滑平 整
腻子彻底涂刮完成并验收合格后,将表面清除干净,进行底漆或者中涂的施工
不管腻子 在任何一层漆面上刮涂或找补,在喷涂面漆之前均宜使用针眼腻子配合面漆或中涂进行找补 然后打磨及进行面漆喷涂
5.4.2.3.2涂装间隔 按照设计要求和材料工艺进行底涂、中涂和面涂的施工
每道涂层的涂装间隔时间应符合材料供 应商的有关技术要求
超过最大涂装间隔时间时,应进行表面拉毛处理后涂装
5.4.2.3.3现场末道面漆涂装 现场末道面漆涂装前应进行以下处理和检查: -对运输和装配过程中破损处进行修复处理; -采用淡水、清洗剂等对待涂表面进行清洁处理,除掉表面灰尘和油污等污染物 试验涂层相容性与附着力,整个涂装过程中要随时注意涂装有无异常情况 5.4.3涂层要求 5.4.3.1外观 涂层表面应平整、均匀一致,涂层应无漏涂,起泡、针孔、裂纹、返锈等异常现象,允许有轻微桔皮和 局部轻微流挂
11
GB/I31817一2015 5.4.3.2干膜厚度 施工中随时检查湿膜厚度以保证干膜厚度满足设计要求
干膜厚度采用“85-15”规则判定,即允许 有15%的读数可低于规定值,但每一单独读数不应低于规定值的85%
涂层厚度达不到设计要求时, 应增加涂装道数,直至合格为止
涂膜厚度测定点的最大值不能超过设计厚度的3倍
5.4.3.3附着力 当检测的涂层厚度大于250m时,附着力试验采用拉开法测试,按GB/T5210一2006的规定进 行,涂层体系与底材的附着力及层间附着力平均值不低于5MPa,最小值不小于3MPa
当检测的涂层 厚度不大于250um时,各道涂层和涂层体系的附着力试验可按GB/T9286一1998的规定进行,附着力 不大于2级
5.4.4维修涂装 5.4.4.1涂膜劣化评定 涂层投人使用后,按照风电设施运行管理单位的规定定期检查,进行涂层劣化评定,评定方法依据 ISO4628-1、ISO4628-2、ISO4628-3、ISO4628-4、ISO4628-5、,ISO4628-6、ISO4628-7、ISO4628-8 1so4628-10
根据漆膜劣化情况,选择合适的维修或重涂方式
5.4.4.2维修涂装 维修涂装要求如下 当面漆出现3级以上粉化,且粉化减薄的厚度大于初始厚度的50%,或由于外观要求时,彻底 清洁面涂层后,涂装与原涂层相容的配套面漆; 当涂膜处于2一3级开裂,或2~3级剥落,或2一3级起泡,但底涂层完好时,选择相应的中间 漆、,面漆,进行维修涂装; -当涂膜发生大于Ri2锈蚀时,打磨处理和彻底清洁表面,涂装相应底漆、中间漆、面漆
5.4.4.3工艺要点 5.4.4.3.1根据损坏的面积大小,钢结构外表面可分为以下两种重涂方式 小面积维修涂装
先清理损坏区域周围松散的涂层,延伸至未损坏区域50 mm80mm,并 应修成坡口,表面处理至Sa2级或St3级,涂装低表面处理环氧涂料十面漆; 中等面积维修涂装
表面处理至Sn2%级,涂装环氧富锌底漆十环氧(云铁)漆十面漆
5.4.4.3.2内表面维修或重新涂装底漆宜采用适用于低表面处理的环氧底漆,并宜采用浅色高固体分 或无溶剂环氧涂料
5.4.4.3.3海洋大气腐蚀环境(C5-M/Im2下的涂层修复先采用清洁剂、淡水等清洁后,再表面打磨粗 糙和除锈处理
5.4.4.3.4处于干湿交替区的钢构件,在水位变动情况下涂装时,应选择表面容忍性好的涂料.并能适 应潮湿涂装环境的涂层体系
5.4.4.3.5处于水下区的钢构件在浸水状态下施工时应选择可水下施工、水下固化的涂层体系
5.4.4.3.6玻璃钢表面涂装的维修,其表面处理及配套可按新建时的方案进行,也可根据实际使用工 况,另行提出配套方案
试验方法 6.1涂层配套体系 6.1.1耐水性试验按GB/T1733一1993甲法进行
12
GB/T31817一2015 6.1.2附着力试验按GB/T5210一2006,GB/T92861998进行 6.1.3耐盐雾性能试验按GB/T1771一2007进行
6.1.4人工加速老化性能(饥灯)试验按GB/T1865一2009中循环A的规定进行;人工加速老化性能 荧光紫外)试验按GB/T23987一2009进行,其中辐照度0.68w/m',试验条件为黑板温度(60士3)C 下紫外光照4h,黑板温度(50士3)C下冷凝4h为一个循环,连续交替进行
6.1.5耐阴极剥离性能试验按GB/T7790一2008方法A进行
6 .1.6耐盐水性,耐油性、耐酸性、耐碱性试验按GB/T9274一1988甲法进行
6.1.7循环老化试验按IsS20340:2009附录A进行
6. 1.8弯曲试验按GB/T6742一2007进行
6.1.9耐磨性试验按GB/T1768一2006进行
6 .1.10耐湿热性试验按GB/T1740一2007进行
6.1.11涂层体系试验后,漆膜表面缺陷评判按GB/T1766一2008进行
6.2表面处理 6.2.1表面处理等级评判按照GB/T8923.1、GB/T8923.2进行
6.2.2表面粗糙度评判按照GB/T13288.1进行
6.2.3表面油污检查可采用以下两种方法: -粉笔试验法(适用于非常光滑的钢结构表面);对于怀疑有油污污染的部位,用粉笔划一条直线 贯穿油污区域
如果在该区域内,粉笔线条变细或变浅,说明该区域可能被油污污染; -醇溶液试验法(适用于所有钢结构表面);对于怀疑有油污污染的部位,用蘸有异丙醇的脱脂棉 球擦拭,并将擦拭后的棉球中的异丙醉醇挤人透明玻璃管中,加人23倍的蒸馏水,振荡混合约 20min
以相同体积的异丙醇蒸水溶液为参照,如果溶液呈混浊状,表明钢结构表面有油污 污染
6.2.4表面灰尘清洁度评判按GB/T18570.3进行
6.2.5表面水溶性盐(相当于NaCI)测定按GB/T18570.6和GB/T18570.9进行
当钢材确定不接触 氯离子环境时,可不进行表面可溶性盐分的检测;当不能完全确定时,应进行首次检测
6.3现场涂层 6.3.1涂层厚度 6.3.1.1湿膜厚度按GB/T13452.2一2008中的4.2.4梳规或4.2.5轮规规定的方法进行测试
6.3.1.2干膜厚度按GB/T13452.2一2008进行测试
6.3.2涂层附着力 涂料涂层附着力按GB/T5210-2006,GB/T9286一1998进行
检验规则 7.1 取样 7.1.1产品按GB/T3186规定取样,也可按商定方法取样
取样量根据检验要求确定
现场取样应使 用专用的样品取样罐
确保现场取样罐的清洁,没有灰尘,水等杂质
7.1.2抽检的产品包装完整,标志清晰
7.1.3采用电动或气动搅拌装置,确保抽检产品均匀一致
13
GB/I31817一2015 7.2检验项目 7.2.1涂层性能的检测项目见表4,表5,表6,表7
7.2.2进场涂料检测项目由监理,施工方及涂料供应商确定 7.2.3现场涂层检测项目按照5.14.3执行
7.3判定原则 7.3.1型式检验包括涂层配套体系性能检测的全部项目,应由涂料供应商提供国家认可检测机构出具 的涂层性能的合格的检测报告
进场涂料检测结果全部符合本标准的要求为合格
检测结果有一项及以上指标不符合要求时 7.3.2 可对不符合要求的项目进行复验,复验结果仍不符合要求,则判该批产品为不合格
现场涂层检测结果全服行合本标准的要求为合格
检割结果有一项及以上指标不符合要求时 7.3.3 都应在现场处理至合格后方可进人下道工序
安全、卫生和环境保护 8.1 安全、卫生 8.1.1涂装作业安全、卫生应符合GB6514一2008、GB7691一2003,GB7692一2012和GB50212 2014的有关规定
8.1.2涂装作业场所空气中有害物质不超过最高容许浓度
8.1.3施工现场应远离火源,不可堆放易燃,易爆和有毒物品
8.1.4涂料仓库及施工现场应有消防水源、灭火器和消防工器具,并应定期检查
消防道路应畅通
8.1.5施工人员应正确穿戴工作服、口罩、防护镜等劳动保护用品,这些劳保用品应是具备相应资质厂 家生产的合格产品
8.1.6所有电器设备应绝缘良好,临时电线应选用绝缘性能良好的电缆,工作结束后应切断电源
8.1.7工作平台的搭建应符合有关安全规定
高空作业人员应具备高空作业资格
8.2环境保护 遵照国家清洁生产和文明生产的要求,保持施工现场清洁,产生的垃圾等应及时收集并妥善处理
验收 9.1涂层验收可按构件分批次验收
9.2涂装承包商至少应提交下列验收资料: -设计文件或设计变更文件; -涂料出厂合格证和质量检验文件,进场验收记录; 钢结构表面处理和检验记录 -涂装施工记录(包括施工过程中对重大技术问题和其他质量检验问题处理记录); 修补和返工记录; -其他涉及涂层质量的相关记录
14
GB/T31817一2015 附 录A 资料性附录 腐蚀环境分类 A.1大气区 大气区腐蚀种类见表A.1
表A.1大气区腐蚀种类 单位面积质量损失/厚度损失(经过一年曝露后) 温和气候下典型环境实例 锌 低碳钢 腐蚀种类 外部 内部 质量损失厚度损失质量损失厚度损失 g/mm" m g/mmr Am 加热的建筑物内部,空气 C s1o <1.3 S0,7 s0.1 洁净
如办公室、商店、 很低 学校和宾馆等 污染水平较低
大部分未加热的地方,冷凝有可 C2 1.3一25 0.1一0.7 10一200 0.7一5 低 是乡村地区 能发生,如库房、体育馆等 具有高湿度和一些空气 城市和工业大气,中邻二 污染的生产车间,如食品 C3 200~400 2550 5~15 0.7一2. 氧化硫污染
低盐度沿 中等 加工厂、洗衣店,酿酒厂 海区 牛奶场 C4 中等盐度的工业区和沿 化工厂、游泳池、沿海船 400650 50~80 15~30 2.14.2 高 海区 舶相造船" C5-l 高湿度和恶劣气氛的工总是有冷凝和高污染的 很高 650~150080~200 3060 4.2~8.4 业区 建筑物和地区 工业 C5-M 高盐度的沿海和海上总是有冷凝和高污染的 很高 650一500 80200 3060 4.2一8.4 区域 建筑物和地区 海洋 注:在沿海区的炎热、潮湿地带,质量或厚度损失值可能超过C5-M种类的界限
A.2水和土壤区 水和土壤种类见表A.2
15
GB/I31817一2015 表A.2水和土壤腐蚀种类 分类 环境 环境和结构的示例 淡水 河流设施,水力发电站 lml 海水或盐水 Im2 港口地区的构筑物,例如闸门水闸、防波堤;海上构筑物 土壤 埋在地下的槽罐,钢桩,钢管 Im3 16
GB/T31817一2015 附 录 B 规范性附录 涂料性能要求和试验方法 B.1富锌底漆 富锌底漆应符合表B.1的要求
表B.1富锌底漆的要求和试验方法 技术指标 项 目 试验方法 无机富锌底漆 环氧富锌底漆 粉末,应呈微小的均匀粉末状态
在容器中状态 液料和浆料,搅拌混合后应无硬块,呈均匀习 目测 状态 7o GB/T17252007 不挥发分(混合后/% 密度(混合后/g/ml 商定 GB/T67502007 不挥发分中金属锌含量/% 80 75 HHG/T3668一2009中5.7 HG/T3668一2009中5.8 适用期h 商定 施工性 施工无障碍 HG/T36682009中5.9 涂膜外观 涂膜外观正常 目测 表干千 GB/T1728一1979乙法 0,5 干燥时间h 24 实干 GB/T1728一1979甲法 耐冲击性/em 50 GB/T1732一1993 GB/T52102006 附着力/MPa GB5020520o1 抗滑移系数"'(初始时) 0.50 1000h划痕处单向600h划痕处单向扩 扩蚀2.0nmm,未划蚀2.0mm,未划痕 耐盐雾性 GB/T1771一2007 痕区无起泡,生锈、区无起泡、生锈,开 开裂,剥落等现象 裂、剥落等现象 无机富锌底漆用于法兰面时,测试抗滑移系数
B.2环氧漆 环氧漆应符合表B.2的要求 17
GB/I31817一2015 表B.2环氧漆的要求和试验方法 技术指标 项 目 试验方法 环氧(厚浆)漆 环氧(云铁)漆 在容器中的状态 搅拌后无硬块,呈均匀状态 目测 75 不挥发物含量 1% GB/T17252007 表干 GBT1728一1979乙法 干燥时间h 实干 24 GB/T17281979甲法 弯曲试验/ mm GB/T67422007 50 GB/T1732. -1993 耐冲击性/em 附着力7" /MPa GB/T52102006 GB/T9274一1988甲法 耐酸性0%HsO溶液, 不起泡,不生锈,允许轻微变色 l68h 甲 溶液,168" h 不起泡,不生锈,允许轻微变色 GB/T92741988 耐碱性(10%NaOH 耐盐水性(6%NaCI溶液 不起泡,不生锈,允许轻微变色 -1988甲法 168h GB/T9274 B.3面漆 面漆应符合表B.3的要求
表B.3面漆的要求和试验方法 技术指标 项目 试验方法 丙烯酸脂肪族 氟碳面沫 聚硅氧熔面漆 聚氨酯面漆 不挥发物含量9 60 55 75 GB/T17252007 GB/T17241979 细度/m 商定 35 溶剂可溶物佩含量7% 22 HG/T3792 -201附录 基料中硅氧键含量/% 附录C 15 表干 GB/T1728一1979乙法 干燥时间h 实干 24 GB/T17281979 甲法 耐弯曲性/mm GB/T67422007 50 GB/T17321993 耐冲击性/em 耐磨性(500r/500g/g GB/T1768一2006 0.05 0.03 砂轮型号:cS-10 铅笔硬度(擦伤 GB/T67392006 GB/T52102006 附着力/MPa 耐盐雾性 1000h不起泡、不开裂、不脱层 GB/T1771一2007 100h不起泡 不开裂,不脱落,3000h不起泡,不开裂,不脱落, 允许1级变色、允许2级变色、2级失光和2级 GB/T18652009 人工加速老化(气灯 1级失光和1级粉化 粉化 18
GB/T31817一2015 B.4叶片涂料 B.4.1叶片腻子性能要求 叶片腻子性能应符合表B.4的要求
表B.4叶片腻子性能要求和试验方法 指 标 项 目 试验方法 大缝腻子 针孔腻子 不挥发物含量/% 98 GB/T17252007 附着力(拉开法/MPa GB/T52102006 柔韧性/mm 100 50 GB/T1748一1979 10 适用期/min 目测 打磨性 2h可打燃 GB/T1770一2008 耐水性(72 h 不起泡,不脱落,允许轻微少色 -1993甲法 GB/T1733 GB/T17321993 耐冲击性/ em 30 刮涂性 易刮涂,不卷边 目测 B.4.2叶片面漆性能要求 叶片面漆性能应符合表B.5的要求
表B.5叶片面漆性能要求和试验方法 目 试验方法 项 耐磨性(1000g/1000r)/mg 50 GB/T1768一2006 砂轮型号;C's-1o) 耐冲击性/em 50 GB/T17321993 附着力(拉开法/MPa GB/T52102006 耐油性(液压油,4) GB/T9274一1988甲法 不起泡、不起皱,允许轻微变色、失光 耐酸性(50g/LHsO溶液,168h) 不起泡不起皱,允许轻微变色、失光 GB/T9274一1988甲法 不起泡,不起皱,允许轻微变色,失光 GB/T9274一1988甲法 耐碱性(100g/INa(OHH溶液,96h GB/ /T 23士2)C 6742一2007 弯曲试验/mm 一20士2)C/1h GB/T67422007 GB/T17402007 不起泡、不开裂、不脱落
拉开法附着 耐湿热性(480h 力;不低于4MP GB/T5210一2006 不起泡、不开裂、不脱落,允许2级变 GB/T23987一2009 人工加速老化试验(QUV-A340nm,2000h 色,2级失光和2级粉化 注当采用氧碳、聚硅氧烧面漆时,人工加速老化试验时间为3000h
19
GB/I31817一2015 附 录c 规范性附录 基料中硅氧键含量测定方法 C.1范围 本方法适用于聚硅氧婉涂料中基料中硅氧键含量的测定
原理 试样经离心分离,取清液部分将溶剂挥发完全后,粉碎成粉末
准确称取一定量的粉末,经梯度灰 化除去基料中有机物,灰分即为二氧化硅
由灰分质量计算基料中硅氧键含量
注灰分是否为二氧化硅,可采用x射线荧光光谱仪或其他具有相同功能的仪器进行定性鉴定
试剂和材料 采用混合溶剂[甲苯:丙酮=1;1(体积比)]或其他合适的溶剂
所用试剂均为分析纯
C.4仪器设备 高温炉;温度能控制在(600士20)c
C.4.1 C.4.2瓷堆蜗;高型,50ml
预先在高温炉内于600C下加热至恒重,在干燥器内冷却并存放
C.4.3分析天平;精度0.1mg c.4.4干燥器
C.4.5离心机转速5000r/min20000r/min. C.4.6烘箱:具有强制通风,温度能控制在(105士2)C
C.4.7粉碎机
c.5测试步骤 C.5.1测定次数 所有试验进行二次平行测定
c.5.2样品离心处理和粉碎 按产品明示的配比制备混合试样(稀释剂不必加人),取适量混合均匀的试样(根据试样的黏度、所 用离心机的离心管体积和离心力大小而定)于离心管内,加人适量的混合溶剂,混合均匀后,放人离心机 内,离心0mm一nm,使基料和颜填科分离,将上层游液翼于I0nL烧杯中
重复上逃洗涂,离 心操作三次,并将试管中上层游液合并于100mL烧杯中
在低温下将烧杯中的大部分游剂挥发后,取 适量烧杯内溶液试样涂在玻璃板或聚四氟乙烯板上,在(105士2)条件下烘烤使溶剂完全蒸发,然后将 烘干样品粉碎备用
20
GB/T31817一2015 C.5.3梯度灰化 准确称取约2g(精确至0.1mg)按C.5.2处理后的基料(烘干样品)到已恒重的瓷堆蜗内
将瓷堆 塌放人高温炉内,按下列条件进行梯度灰化试样:升温至200C保温2h;继续升温至300C保温2h;继 续升温至400C保温2h;继续升温至500C保温2h;最后升温至600C,保温直至完全灰化
在大多 数情况下,灰化会在600C保温3h后结束
将瓷堆蜗放人干燥器内冷却至室温,称量
注1:硅氧键含量较低的样品,为提高测试准确性,可适当增加称样量
注2;在灰化期间应供给足够的空气氧化,但瓷堆蜗内的物质不应在任何阶段发生燃烧和逸出
注3高温炉升温时应控制速度,升温过快时灰化所产生的气体可能会将灰分带出瓷堆蜗 C.6结果计算 按式(C.1)计算基料中硅氧键含量: m
一m)×0.7333 X100% C.1 e m 式中 基料中硅氧键含量; w -瓷堆蜗和灰分的质量,单位为克(g); m -瓷堆蜗的质量,单位为克(g); 基料的质量,单位为克(g); 0.7333 二氧化硅换算成硅氧键的系数
计算两次平行测定的平均值,计算结果保留小数点后一位 精密度 C.7.1重复性 同 -操作者二次测试结果的相对偏差小于5%
C.7.2再现性 不同实验室间测试结果的相对偏差小于10%.
风力发电设施防护涂装技术规范GB/T31817-2015解读
近年来,随着我国大力发展风力发电产业,风力发电设施的建设和运行越来越受到人们的关注。然而,由于风力发电设施所处环境恶劣,长期暴露在风吹日晒雨淋的自然条件下,其表面容易出现锈蚀和起泡等情况,从而影响设施的寿命和发电效率。为了解决这一问题,我国国家标准化管理委员会于2015年发布了《风力发电设施防护涂装技术规范GB/T31817-2015》(以下简称“规范”),该规范旨在规定了风力发电设施防护涂装的技术要求和检验方法,以保证风力发电设施的安全运行和长期使用。
一、规范背景
《风力发电设施防护涂装技术规范GB/T31817-2015》是我国首个针对风力发电设施防护涂装的技术标准。该规范的制定旨在加强风力发电设施的防护措施,提高其使用寿命和发电效率,推动风力发电产业的健康可持续发展。
二、规范适用范围
该规范适用于在大气环境中运行的风力发电设施及其部件的防护涂装工作,包括塔筒、机舱、机组及叶片等部位的涂装。
三、术语和定义
该规范中涉及到的术语和定义主要包括:防护涂层、底漆、中间涂层、面漆、烘干、硬度、附着力等。
四、技术要求
《风力发电设施防护涂装技术规范GB/T31817-2015》规定了风力发电设施防护涂装的技术要求,主要包括:涂层材料的选择、涂装前的表面处理、涂布工艺、烘干条件等。
五、检验方法
为保证涂装质量,该规范还规定了涂装过程中的检验方法,主要包括:涂层厚度的测量、表观质量的评定、硬度测试、附着力测试等。
总之,《风力发电设施防护涂装技术规范GB/T31817-2015》是我国风力发电产业发展的重要标准,它的出台对于提高风力发电设施的安全性和稳定性具有重要意义。风力发电设施作为新能源领域的一项重要技术,其防护涂装技术也将越来越受到关注和重视。未来,我国应该加强对风力发电设施防护涂装技术的研究和推广,不断提高其质量和效率,促进风力发电产业的可持续发展。
风力发电设施防护涂装技术规范的相关资料
- 风力发电机组设计要求GB/T18451.1-2012
- 风力发电塔用结构钢板GB/T28410-2012
- 小型垂直轴风力发电机组GB/T29494-2013:原理、特点与应用
- 低温型风力发电机组GB/T29543-2013介绍
- 额定电压1.8/3kV及以下风力发电用耐扭曲软电缆GB/T29631-2013介绍
- 钢结构防护涂装通用技术条件GB/T28699-2012解读
- 风力发电设施防护涂装技术规范GB/T31817-2015解读
- 基于J2EE的应用服务器技术规范GB/T26232-2010
- 数字电视接收设备机道分离DTV-CSI接口规范第1部分
- 国家纺织产品基本安全技术规范GB18401-2010
- 洗涤用品安全技术规范GB/T26396-2011
- 承压设备带压密封技术规范GB/T26467-2011详解
- 风力发电设施防护涂装技术规范GB/T31817-2015解读