GB/T37676-2019
高速精密热镦锻件工艺规范
Highspeedprecisionhotupsettingforgings—Technologicalspecification
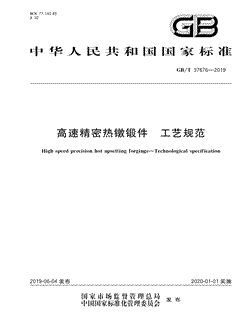
- 中国标准分类号(CCS)J32
- 国际标准分类号(ICS)77.140.85
- 实施日期2020-01-01
- 文件格式PDF
- 文本页数10页
- 文件大小1.19M
以图片形式预览高速精密热镦锻件工艺规范
高速精密热镦锻件工艺规范
国家标准 GB/T37676一2019 高速精密热徽锻件工艺规范 Highspeedpreelisionhotupsettingforgings一Technolvgitealspecifieattom 2019-06-04发布 2020-01-01实施 国家市场监督管理总局 发布 币国国家标准化管理委员会国家标准
GB/37676一2019 前 言 本标准按照GB/T1.1一2009给出的规则起草
本标准由全国锻压标准化技术委员会(SAC/TC74)提出并归口
本标准起草单位:江苏森威精锻有限公司,东风锻造有限公司、北京机电研究所有限公司、广东韶铸 精锻有限公司、浙江五洲新春集团股份有限公司、上海交通大学
本标准主要起草人:龚爱军、朱华,吴玉坚、魏巍、金红,刘梅华、刘余,胡成亮、朱卫、吴建彬、周林、 利义旭、蓝育忠、赵震、白太亮
GB/37676一2019 高速精密热徽锻件工艺规范 范围 本标准规定了高速精密热徵锻件(以下简称“锻件”)的工艺规范,包括总则、工艺参数确定、锻件坯 料的准备、坯料加热、模具的要求和设备的选择
本标准适用于生产节拍50件/min及以上、质量在7.5kg以下且外径尺寸不大于180mm,采用热 徵锻成形的钢质精密锻件的工艺编制
规范性引用文件 下列文件对于本文件的应用是必不可少的
凡是注日期的引用文件,仅注日期的版本适用于本文 件
凡是不注日期的引用文件,其最新版本(包括所有的修改单)适用于本文件
GB/T699优质碳素结构钢 GB/T700碳素结构钢 GB/T1299工模具钢 GB/T1591低合金高强度结构钢 合金结构钢 GB/T3077 GB/T5216保证淬透性结构钢 锻压术语 GB/T8541 GB13318一2003锻造生产安全与环保通则 GB/T15712非调质机械结构钢 GB/T18254高碳铬轴承钢 GB/T28417碳素轴承钢 GB/T29532钢质精密热模锻件通用技术条件 GB/T30567一2014钢质精密热模锻件工艺编制原则 术语和定义 GB/T8541界定的以及下列术语和定义适用于本文件
3. 高速精密热徵锻工艺highspeelpreeisionhotupsettingpreess 采用卧式多工位热徵锻成形机生产,节拍50件/min及以上,热徵锻精密成形的工艺
编制原则 4.1总则 4.1.1工艺设计应考虑锻件形状复杂程度、表面质量、尺寸精度、形状和位置公差、棒料尺寸、材料特 性、成形方式、变形程度、工位数、各工位许可成形力、总成形力传送要求、模具寿命、生产经济性和年产 量等因素
GB/T37676一2019 4.1.2工艺设计流程;零件图-加工余量-冷态锻件图-成形工位热态尺寸-锻件质量剪切工位 直径和长度)变形工位时间图-模具设计-模具制造一工艺试制工艺优化 4.13时间图的设计应保证各工位毛坯能被顺利搬送,并与模具不产生干涉,宜采用仿真技术进行 模拟
4.1.4各工位毛坯形状设计应考虑机械手夹持的可靠性
4.1.5工艺设计宜采用数值模拟分析成形力,填充度、温度分布,避免出现折叠和填充不足等缺陷
4.1.6变形工位的设计应考虑最小壁厚和锻造最小圆角半径等限制条件
4.1.7接触锻件的模具部件应进行冷却,模具的冷却介质一般选用水.冷却介质应避免直接喷淋锻件 4.1.8对于变形量较大的锻件宜在冷却介质中添加合适的润滑剂
4.1.9 模具的更换宜成套进行 4.1.10锻件宜利用锻后余热进行热处理
4.1.11 锻件在整个生产过程中应考虑采取防磕碰措施
4.1.12 作业环境应满足GB1331s8一203中5.2的要求,人员应请足GB1318一2003中10.2的要求 安全和环保技术措施应满足GB13318一2003中第9章的要求
4.2工艺参数确定 4.2.1变形温度 变形温度应在再结晶温度以上的奥氏体区内
为避免出现过热、过烧现象,加热料温宜在 4.2.1.1 1150c~1280内,其中轴承钢不宜超过1180C
在模具充分冷却的前提下,加热温度宜接近 上限
4.2.1.2锻后宜快速冷却到Aa以下,以避免晶粒长大 4.2.1.3利用余热进行热处理时,锻件的终锻温度应满足后续的热处理要求
4.2.2变形程度 4.2.2.1各工位的变形程度应避免最终累计变形造成大晶粒
4.2.2.2变形程度的选择应考虑变形方式对许用变形量的影响
4.2.3变形力 变形力宜采用数值模拟分析计算,也可采用诺模图或经验公式计算,可参照GB/T305672014中 4.2.1.7
4.2.4各工位参数的确定 4.2.4.1剪切工位 4.2.4.1.1棒料直径的选择应在满足长径比1/D要求1.02.0、优选1.21.7的条件下,尽可能使剪 切产生的毛刺在冲孔工序可去除或转移至加工面,具体见图la)
GB/37676一2019 单位为毫米 剪切工位 预成形工位 成形工位 冲孔工位 a b 说明: 剪切长度; D 棒料直径 D 预成形工位杆部外圆直径; 预成形工位外圆直径; 预成形工位杆部段长; 预成形工位总段长; 成形工位杆部外圆直径 成形工位外圆直径; 成形工位杆部段长 成形工位总段长; 成形工位内孔直径 D 冲孔工位撕裂面直径 冲孔工位连皮厚度; 冲孔工位内孔直径 图1各工位参数 4.2.4.1.2剪切长度宜采用计算式(1),热态下密度参考值见表1 4n ×T×D×D 式中 锻件质量; n 材料密度 圆周率
表1热态下密度和热膨胀系数参考值 锻件直径 密度参考值 钢材种类 热膨胀系数参考值 g/em mm S67 7.551 非轴承钢 1.013 >67125 7.507 1.015 非轴承钢 非轴承钢 >125160 7.485 1.016 非轴承钢 -160 1.017 7.463 轴承钢 S67 7.507 1.015 轴承钢 >67 7.474 1.0165
GB/T37676一2019 4.2.4.2预成形工位 4.2.4.2.1预成形工位成形方式有模外成形和模内成形两种,应考虑形状要求、热量损耗、模具制造、机 械手夹持等因素 4.2.4.2.2预成形工位成形应考虑体积分配,宜采用数值模拟进行
4.2.4.2.3工位具体尺寸的确定见图1b)和表2
表2预成形工位参数 单位为毫米 D. D D;一0.5一D;一8 根据体积分配确定 根据质量确定 -0.5 4.2.4.3成形工位 4.2.4.3.1成形方式可选用横向闭式模锻或横向开式模锻,应优先考虑无飞边锻造
4.2.4.3.2成形工位的连皮厚度宜采用计算式(2),其余尺寸应根据冷态锻件尺寸和热膨胀系数参考值 进行确定,具体见图le)和表1
h
=0.1×l
k 式中 经验值,一般取2~3
4.2.4.4冲孔工位 工位具体尺寸的确定见图1d)和表3. 表3冲孔工位参数 单位为毫米 D 0.15×h十l 0.1×d十 根据锻件尺寸及热膨胀系数参考值确定 人为经验值,,一般取23
4.2.5时间图的确定 4.2.5.1将剪切坯料及预成形坯料放人时间图模板中,计算出顶杆伸出长度,保证机械手打开时顶杆应 先顶住棒料(包含伸缩量至少10mm),机械手传送到位时顶杆不能接触到棒料,预成形工位时间图设 计见图2.
GB/37676一2019 单位为毫米 顶出器 凹模 前死点 AV 冲头 后死点 说明 AV 模架平面
图2预成形工位时间图 42.5.2将预成形还料及成形坯料放人时间图模板中,夹钳宽度宜大于预成形坯料宽度的一半,成形时 宜采用导向结构,机械手打开时冲头应先顶住坯料,机械手传送到位时冲头不能接触到棒料,结合设备 运动时间图和时间表算出安全距离及L
长度(机械手打开时冲头的位置),成形工位时间图设计见 图3
GB/T37676一2019 单位为毫米 顶出器 凹模 前死点 S n 冲头 后死点 说明: -成形工位冲头顶住坯料的距离; 机械手打开时冲头与前死点的距岗
2 图3成形工位时间图 4.2.5.3将成形坯料放人时间图模板中,机械手传送到位时顶杆不能接触到棒料,开始冲孔后机械手打 开,三工位时间图设计见图4
GB/37676一2019 单位为毫米 前死点 校 顶杆 冲头 后死点 图4冲孔工位时间图 4.3锻件坯料的准备 4.3.1锻件坯料优先选用棒材,应符合GB/T699,GB/T700,GB/T1299,GB/T1591、GB/T3077、 GB/T5216,GB/T15712,GB/T18254,GB/T28417等标准的规定
4.3.2原材料长度不得小于剔料系统限定的长度,宜选择9m及以上,以减少剔料浪费,且端面齐整 无毛刺,无影响使用的变形
4.3.3当锻件表面质量要求高或预成形工位选择闭式模锻时,坯料宜进行剥皮,磨削或其他方法以改 善坯料表面质量和精度,坯料直径公差通常不大于0.2mm. 4.4坯料加热 4.4.1坯料加热采用整根棒料感应加热的方式,且有温度检测和高低温报警停机功能
4.4.2感应器的规格选择应与加热坯料直径相匹配,避免加热效率低
4.4.3坯料进给节拍要根据坯料尺寸、加热温度、锻造设备等因素综合考虑,以坯料的加热温度均匀达 到工艺要求为前提
4.5模具的要求 4.5.1模具的精度应满足锻件的尺寸,形状和位置公差等精度要求
4.5.2凸模、凹模和顶杆宜采用氮化等表面处理,以提高模具表面硬度和耐磨性
模具表面粗糙度值 应不大于Ra0.8Mm
GB/T37676一2019 4.5.3凹模顶杆宜设计成中空结构,以便冷却液冷却凹模
0.30mm
4.5.4闭式成形工位的凸模、凹模应具有导向结构,双边配合间隙宜控制在0.10mm~ 4.6设备的选择 4.6.1设备的力-行程曲线及能量应满足锻件成形的力-行程曲线及变形功的要求
4.6.2设备精度应符合G;B/T29532的相关规定
4.6.3设备的选择应考虑锻件的实际产量需求、各工位载荷及允许的偏心载荷、生产成本等
4.6.4设备应具有料头、料尾自动检测和剔料系统,应考虑机械手传送系统的精确和稳定可靠模具冷 却系统的高效和模具的内冷却、模具的快速更换,顶出装置的可靠等要求
4.6.5宜组建自动化生产线,主要含上料机构、中频加热系统、高速热徵锻成形机、出料机构、控制冷却 或连续式热处理装置
4.6.6产品的出料方式可选择垂直出料和侧向出料两种,应考虑产品磕碰等要求
高速精密热镦锻件工艺规范GB/T37676-2019
随着制造业的不断发展,对于产品的精度和质量要求越来越高。高速精密热镦锻件是一种高效率、高精度、高可靠性的成形加工技术,广泛应用于汽车、机械等领域。
为了规范热镦锻件生产过程中的工艺流程和技术要求,提高产品的质量和稳定性,中国标准化协会联合相关行业单位共同制定了《高速精密热镦锻件工艺规范GB/T37676-2019》。
规范适用范围
该规范适用于高速精密热镦锻件的生产和检验,包括材料选择、热处理、模具设计、设备选型等方面的要求。
主要内容
该规范主要包括以下方面的内容:
- 术语和定义
- 材料和热处理要求
- 模具设计和加工要求
- 设备选型和操作要求
- 生产过程管理要求
- 产品检验和试验方法
工艺流程
高速精密热镦锻件的典型工艺流程如下:
- 材料选择:根据产品形状和机械性能要求,选择适宜的材料。
- 预制备:对原材料进行切割、锯断、钻孔等预制备工作。
- 热处理:对预制备好的材料进行适当的热处理,使其达到一定的软化状态。
- 模具设计:根据产品形状和尺寸要求,设计出合理的模具。
- 设备调试:选择合适的设备,并进行调试和测试。
- 热镦锻件:将软化后的材料放入模具中,在短时间内施加高压力和高温度进行成形。
- 冷却处理:将成形后的零件进行适当的冷却处理,使其达到规定的硬度和强度。
- 产品检验:对成品进行尺寸、外观、力学性能等方面的检验。
总结
高速精密热镦锻件是一种高效率、高精度、高可靠性的成形加工技术,具有广泛应用前景。通过遵循《高速精密热镦锻件工艺规范GB/T37676-2019》的要求,可以保证生产过程的规范化和标准化,提高产品的质量和稳定性。