GB/T32974-2016
钢铁行业蓄热式工业炉窑热平衡测试与计算方法
Methodsofdeterminationandcalculationofheatbalanceinregenerativefurnaceofironandsteelindustry
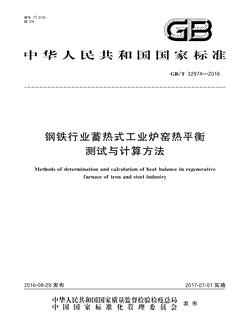
- 中国标准分类号(CCS)H04
- 国际标准分类号(ICS)77.140.99
- 实施日期2017-07-01
- 文件格式PDF
- 文本页数22页
- 文件大小453.83KB
以图片形式预览钢铁行业蓄热式工业炉窑热平衡测试与计算方法
钢铁行业蓄热式工业炉窑热平衡测试与计算方法
国家标准 GB/T32974一2016 钢铁行业蓄热式工业炉窑热平衡 测试与计算方法 Methodsofdeterminationandealeulationofheatbalanceinregenerative furnaceofironandsteelindustry 2016-08-29发布 2017-07-01实施 国家质量监督检验检疫总局 发布 国家标准化管理委员会国家标准
GB/T32974一2016 钢铁行业蓄热式工业炉窑热平衡 测试与计算方法 范围 本标准规定了钢铁行业蓄热式工业炉窑热的热平衡测试的术语和定义,基准、设备及炉子概况、炉 子近期生产情况,测试的准备,测试步骤,测试内容与方法、计算方法、热平衡测试报告主要内容
本标准适用于钢铁行业使用气体燃料连续生产的蓄热式工业炉窑热平衡测试与计算
规范性引用文件 下列文件对于本文件的应用是必不可少的
凡是注日期的引用文件,仅注日期的版本适用于本文 凡是不注日期的引用文件,其最新版本(包括所有的修改单)适用于本文件 件
YB/T4209钢铁行业蓄热式燃烧技术规范 术语和定义 YB/T4209界定的以及下列术语和定义适用于本文件
3.1 /ai 气体预热温度gas/ ”preheattemperature 供热过程中,气体流经蓄热体的温度
3.2 蓄热室排烟温度regeneratorexhaussmoketemperature 排烟过程中,烟气流经蓄热体的温度
热平衡测试与计算基准 基准温度 4.1 采用环境平均温度,即蓄热式工业炉窑车间内距离炉墙外1m处的环境平均温度
4.2燃料发热量 采用湿煤气的收到基低(位)发热量
4.3热平衡测试范围 根据测试要求,做全炉(包括蓄热回收装置)或(和)炉膛热平衡的测试与计算
4.4热平衡测试时间 在人炉物料品种及规格不变,炉子工况稳定的情况下连续测定
热平衡测定限定在8h内完成,测 定次数不能少于2次,每次为1h
其中温度、压力、流量等参数的测定每小时不少于4次,然后取平
GB/T32974一2016 均值 4.5热平衡计算单位 以每吨人炉物料消耗的热量为计算单位,即kJ/t 设备及炉子概况、炉子近期生产情况 5.1 设备及炉子概况 设备及炉子概况参照附录A填写
5.2 炉子近期生产情况 被测炉子前一个月的平均技术经济指标参照附录B填写
测试的准备 6.1 熟悉设备状况 熟悉炉子及有关设备的结构、性能、操作与运行情况.并了解生产工艺流程等
制定测试方案 6.2 根据测试要求制定测试方案,并选择能够代表炉子实际生产情况的测试部位和测试点
组织测试人员 6.3 根据测试方案组织测试人员
测试工作由专业技术人员指挥,按工作需要对测试人员进行分工.,并 根据情况进行必要的技术培训与安全教育
6.4检修设备与准备测试仪器和工具 在测试前对炉子及相关设备进行必要的检修,以保证测试工作的顺利进行
准备好所需测量工具
对现场已有仪表及各种便携的测量仪器进行校正,满足测试要求
工厂无计量装置时,在测试前应安装 计量装置
6.5选择测试时机 测试前及测试过程中,炉况及其上下游工序工作情况应正常
测试过程中,炉内物料因下游工序非 正常停留超过0.5h,应在下游工序工作情况稳定0.5h以后重新开始测试
6.6预备性测试 正式测试之前对其中的儿项或全部项目进行必要的预备性测试,验证测试手段的可靠性
测试步骤 按测试内容进行测试与记录
采用以测量为主,控制中心记录数据为参考的方法,对所测数据进行 分析整理,并按本标准的计算方法进行计算
对测试结果进行分析并提供测试报告
GB/T32974一2016 测试内容与方法 主要测试内容 按附录C进行
8.2 测试内容与方法 8.2.1燃料 8.2.1.1燃料量测试 燃料量可由工厂现有的计量装置读取
8.2.1.2燃料的取样分析及发热量测试 取样;在燃烧器前煤气管道上的取样孔进行取样,一般每小时取一次,如果煤气成分波动较大,可适 当缩短取样间隔时间 成分分析;用气相色谱进行
含水量;用吸水法或露点法测试
发热量;根据气体分析成分及含水量换算成湿成分,然后计算出气体燃料低(位)发热量
8.2.1.3燃料压力测试 从现场接近燃烧器前管道上的仪表读取
8.2.1.4燃料温度的测试 燃料无预热时从现场接近燃烧器前的管道上仪表读取
燃料预热时,应取从现场接近燃烧器前的 未预热管道上仪表读取
8.2.2助燃空气 8.2.2.1空气流量的测试 从现场接近燃烧器前的管道上仪表读取
若无法计量可用皮托管和U型压力计测出动压后,用公 式计算出来
8.2.2.2空气湿度测试 用干湿球温度计测出相对湿度,再换算成绝对湿度
8.2.2.3空气预热温度的测试 在空气预热管路上开孔用热电偶进行测定
8.2.3物料 8.2.3.1物料重量测试 物料重量采用现场计量装置读数,也可根据理论计算
GB/T32974一2016 8.2.3.2物料温度测试 采用热电偶测温法进行测量
也可采用红外热像仪或红外测温仪对人炉、出炉物料表面温度进行 测量
测量应在物料进炉前和出炉后3s内完成
8.2.3.3氧化烧损测试 氧化烧损率采用称量法或重量比表面积相似法测试(见附录D)
8.2.4烟气 8.2.4.1烟气取样和分析 出炉烟气的取样位置应分别在空烟总烟道和煤烟总烟道进烟囱前的烟气直管道上取有代表性的试 样
建议采用便携式或在线烟气分析仪
亦可采用直接取样装袋送实验室进行成分分析
8.2.4.2烟气量测试 可用皮托管与微压计配合测量多点烟气流速后算出 8.2.4.3出炉烟气温度测试 采用现场计量装置读取,在换向阀后和烟囱之间接近换向阀的烟气直管道上用热电偶测量出炉烟 气温度
8.2.5炉膛温度和压力 8.2.5.1炉膛温度测试 采用现场计量装置读取,应按炉体结构分为预热段、加热段,均热段等分别测试
8.2.5.2炉膛压力测试 由现场仪表直接读取或用便携式微压计测量,测点位置按热工测试相关规定确定
8.2.6炉体,排烟装置、炉膛、管道表面温度与热流量 测量炉体、排烟装置和炉膛至排烟装置间空气、煤气(或烟气)管道等表面温度时,可将表面温度相 近的地方分成若干部分,然后用热流计直接测出各部分的平均热流量和平均温度,或用红外热像仪,表 面温度计等测出各部分平均温度,计算出热流量
每平方米测点不少于5个
8.2.7 炉门及孔洞 记录炉门及孔洞在1h内的开启时间,测量出炉门及孔洞的高度,宽度,孔洞炉气的成分取样分析 温度与压力的测试方法分别与烟气取样的分析及炉温、炉压测试方法相同
8.2.8冷却水 8.2.8.1冷却水耗量测量 在人炉或出炉应尽量安装流量计测试,也可用体积法测试计算
8.2.8.2冷却水温度测试 在人炉和出炉处采用温度计测试
GB/T32974一2016 8.2.9汽化冷却 8.2.9.1蒸发量测试 由现场计量仪表直接读取
8.2.9.2蒸汽温度、压力及给水温度测试 蒸汽温度、压力及给水温度由现场计量仪表直接读取
计算方法 9.1热收入项目的计算 9.1.1燃料燃烧的化学热的计算按式(1)计算: Q =BQ net.an 式中: -燃料燃烧的化学热,单位为千焦每吨(kJ/t); Q 每吨人炉物料的燃料用量,单位为千克每吨(kg/t)或立方米每吨(m/t) B -燃料收到基低(位)发热量,单位为千焦每吨(kJ/t)或千焦每立方米(kJ/m')
Q.n 气体燃料的收到基低(位)发热量的计算按式(2)计算 一126cO十108H十358CH十598C,H十234H,s Qm net..ar 式中: 出 cO、H,CH,C,H,H,s 气体燃料各湿成分的体积含量,用百分数(%)表示,见式(3). 100 .(3 Zs=2Z" 100十0.124g 式中: Z及Z 气体燃料中任意湿成分及对应的干成分体积含量,用百分数(%)表示; 干气体燃料的含水量,单位为克每立方米(g/m'
昌" 9.1.2燃料带人的物理热量的计算按式(4)计算 Ct Q.=B(C,l 式中: -燃料带人的物理热量,单位为千焦每吨(k/t); Q -环境温度,单位为摄氏度(C); t -燃料的温度,单位为摄氏度(); C,及C -燃料在0至1,及
间的平均比热容,单位为千焦每千克摄氏度[k/kgC)]或千 焦每立方米摄氏度[k/m
C],见式(5)
对于气体燃料 (5 C=(CcoCO+Cco.CO:+CH+ 100 式中: 湿气体燃料中cO,cO.、H,成分的平均比热容,单位为千焦每立方 Cco、Cco、C Hg." 米挺氏度[/(m它刀
g.1.3助燃空气带人的物理热量的计算按式(6)计算 Q. =baL.:(c.-cde
GB/T32974一2016 式中: Q -助燃空气带人的物理热量,单位为千焦每吨(k/t); L 理论湿空气量,单位为立方米每立方米(m'/m)或立方米每千克(m'/kg)见式(7). (7 L;=L"(1十0.00124g) 式中: 干空气的含水量,单位为克每立方米(g/m') g L -理论干空气量,单位为立方米每立方米(m'/m')或立方米每千克(m'/kg),见式(8) L”=0.0238(H!十cO)十0.0952CH十0.0476m lCH +" 十0.0714H.ss一0.0476o 8) 式中: -空气温度,单位为摄氏度(C); -空气在0至及
间的平均定压比热容,单位为千焦每立方米摄氏度[kJ/m
C] -空气系数,见式(9) 21 9 O一0.5CO'一0.5H一2CH吧" 21一79 NCO+cO+CH+SO丽 N" OOFC干C.E 十HS 式中: O',cO',cO:'H',SO:',CHH'及Ng 干烟气中各成分的体积含量,用百分数(%)表示; N,co:,cO,CHH,C.H,H.s,H及o 燃料的各湿成分的体积含量,用百分数(%)表示
g.1.4物料带人的物理热量计算按式(10)计算 10 Q=1000(Cpdp-Cl. 式中: 物料带人的物理热量,单位为千焦每吨(k/): Q 物料在0至,及,间的平约均比热,单位为千熊每千克摄氏度[kI/(k区七] Cp及Cp -物料人炉温度,单位为摄氏度()
9.1.5物料氧化反应热量计算按式(11)计算 Q=5645160a (11) 式中: Q -物料氧化反应热量,单位为千焦每吨(k/t); -物料氧化烧损率,单位为千克每千克(kg/kg)
9.1.6收人热量总和习Q按式(12)计算 习Q=Q十Q十Q+Q十Q 12 式中: 习Q -收人热量总和,单位为千焦每吨(kJ/t)
热支出项目的计算 9.2 9.2.1出炉物料带出的物理热量计算按式(13)计算 Q=1000(1一a)(c',t',-c't. (13 式中: Q' -出炉物料带出的物理热量,单位为千焦每吨(kJ/t); 物料在0至',及,
间的平均比热容,单位为千焦每千克摄氏度[kJ/(kgC] 物料出炉温度,单位为摄氏度()
GB/T32974一2016 9.2.2烟气带出的物理热量计算按式(14)计算 习 BV 14 ? Cet,-C,/. G 式中 Q" 烟气带出的物理热量,单位为千焦每吨(k/); -不完全燃烧时烟气修正系数,见式(15)和式(16); V 炉门、孔洞逸气量,单位为立方米每小时(m'/h)(见9.2.8); 每小时人炉物料量,单位为吨每小时(t/h); G C,及C 烟气在0至l,及间的平均比热容,单位为千焦每立方米摄氏度[k/m
C] 烟气出炉或出蓄热室的温度,单位为摄氏度(C)
lg 当a>1时 l100 (15 100一0.5C(O)" 0.5H5” 当a<1时 100 b= (16 100+1.88CO十1.88H十9.52CH二4.76O 完全燃烧时的实际湿烟气量,见式(17),单位为立方米每立方米(m'/m)或立方米每千克 m'7/kg) 对气体燃料 (17 V;=V
十[a(10.00124gi)一1]L" 式中: V 实际烟气量,单位为立方米每立方米(m'/m'). 理论烟气量,单位为立方米每立方米(m'/m'),见式(18)
V,=0.01cO十3CH十m十"CH》十cO;十H》十2H,Ss十N十H,O+0.79L (18 烟气平均比热容计算按式(19)计算 C, SCa,co+ca,co 十 * 19 2一 100" 式中: C, -烟气平均比热容,单位为千焦每立方米摄氏度[k/m
C] CS,C 湿烟气中cO.cO.的平均比热容,单位为千焦每立方米摄氏度 LkJ/(m'
C] cO,co -湿烟气中CO,CO,的含量,用百分数(%)表示 9.2.3化学不完全燃烧损失的热量计算按式(20)计算: Q,一BbV;(126CO'十108HH:'十358CH'十) 20 式中: Q -化学不完全燃烧损失的热量,单位为千焦每吨(k/t)
9.2.4机械不完全燃烧损失的热量Q':机械不完全燃烧损失为烟气中残炭损失热量
由于采用了蓄 热式燃烧技术,烟气中残炭极少,故可以忽略不计
9.2.5炉子附件的吸热量计算按式(21)计算 Q'=G,(c''-c (21)
GB/T32974一2016 式中: Q" -炉子附件的吸热量,单位为千焦每吨(k/t); G 人炉吨物料加热附件(链带等)的重量,单位为千克每吨(kg/t); t' 及! -附件出炉及进炉时温度,单位摄氏度(C); c'及c 附件在0至及间的平均比热容,单位为千焦每千克摄氏度[k/(kgC门
9.2.6炉体表面散热量计算按式(22)计算 g.A Q. 22 式中: Q -炉子附件的吸热量,单位为千焦每吨(/t) -第i部分炉体表面散热面积,单位为平方米(m') -第i部分炉体表面平均面积热流量,单位为千焦每平方米小时[kJ/nm'h)],如不能直接 9n 测量,可按式(23)计算
[(273十 (273十 aa(t一t (23 g,=20.4le 100 100 式中: 炉体表面黑度; -第i部分炉体表面平均温度,单位为摄氏度(C); -对流给热系数,单位为千焦每平方米小时[k/(nmh],见式(24),式(25)式(26)和式(27). ad 无风时: a
=AG一.) 24) 式中 系数,散热面向上时A=11.7,向下时A=6.3,垂直时A=9.2
横置圆柱时 aa=8.8 25 式中: 圆柱直径,单位为米(m
dl 当风速w<5m/、时 a
=22,2十15.1W (26 当风速w>5m/、时 ,0.,8 =27.1W" (27 炉门及孔洞辐射的热量计算按式(28)计算 9.2.7 273十1
[(273十t 28 Q',=20.1一习A'声 W[ 100 100 式中 Q' -炉门及孔洞辐射的热量,单位为千焦每吨(k/t) 炉门及孔洞处温度,单位为摄氏度(C); A'" -炉门、孔开启面积,单位为平方米(m'); 角度系数; lh内开启门,.孔时间,单位为秒(s) r 炉门及孔洞逸气损失热量计算按式(29)计算 9.2.8 29 Q
=Q+Q
GB/I32974一2016 式中: Q 炉门及孔洞逸气损失热量,单位为千焦每吨(k/t); -逸气带出的物理热量,单位为千焦每吨(J/t); Q山 Q. -逸气带出的化学热量,单位为千焦每吨(kJ/t)
逸气物理热量和化学热量计算公式如下 逸气物理热量计算按式30)计算: a -习V(C,t,-C,te Q 30) G 式中: 通过炉门、孔洞的逸气量,单位为立方米每小时(m/h),见式(31)和式(35). V 炉门及垂直孔洞的逸气量 十P 281b 9.8 P V= 一r,)H 31) H中" 9.8 r
.273十t、 一ry 式中: P -炉门、孔洞底部的炉气表压,单位为帕斯卡(Pa); 大气压,单位为帕斯卡(Pa) P
炉门、孔洞的平均宽度,单位为米(m); 炉门、孔洞1小时内的开启时间,单位为小时(h); 炉门、孔洞的平均开启高度,单位为米(m); H 流量系数,厚墙=0.82,薄墙=0.62(当心<3.5l时为薄墙,0为炉墙的厚度,d为炉 4 门、孔洞的当量直径)
-环境温度下的空气密度,单位为千克每立方米(kg/mi),见式(32). 1.293 32 101325 27 ,下炉气密度,单位为千克每立方米(kg/m'),见式(33). P1十P 33) 101325 1十 27 式中: 44CO,十18H.O十64SO,十28N,十32O,十 (34) 22.4×100 式中: CO.,H.O,sO.,O -炉门、孔洞逸出气体成分,用百分数(%)表示; 水平空洞的逸气量 421uArP十PD V= 35) 9.8r 9.8×273十, 式中 A 孔洞的逸气面积,单位为平方米(m'); P 孔洞处的平均表压,单位为帕斯卡(Pa) -炉门,孔洞处的炉气温度,单位为摄氏度(C); C及C -炉门、孔洞处的炉气在0至,及
间的平均比热容,单位为千焦每立方米摄氏 度[kJ/m=
C)]
GB/T32974一2016 b逸气化学热量计算按式(36)计算 Q= 十108H
十358CH十589CH, (36 v1aco 9.2.9冷却水的吸热量计算按式(37)计算 .(37 Q,=G,(c''-C 式中: -冷却水的吸热量,单位为千焦每吨(kJ/t) Q -每吨人炉物料的冷却水用量,单位为千克每吨(kg/t); G c',c 冷却水在/'、!下的比热容,单位为千焦每千克摄氏度[kJ/(kgC] -冷却水出、人炉温度,单位为摄氏度(C)
9.2.10汽化冷却的吸热量计算按式(38)计算 rw Q'=Gh,-c"?" (38 100 式中 Q' 汽化冷却的吸热量,单位为千焦每吨(kJ/); 人炉每吨物料的产汽量,单位为千克每吨(kg/t)1 G 一给水的比热容,单位为千焦每千克摄氏度[k/(kC)], 给水温度,单位为摄氏度(C); 蒸汽的比烙,单位为千焦每千克(/kg); 汽化显热,单位为千焦每千克(J/kg) 燕汽湿度,用百分数表示(%). 9.2.11氧化铁皮带出的物理热量计算按式(39)计算 C.l 39 Q'=1000a(C'/' 式中 c"h 及C -氧化铁皮在0至'及
温度下的平均比热容,单位为千焦每千克摄氏度[k kg.C刀 -氧化铁皮温度,单位为摄氏度(C). g.2.12蓄热室表面散热量Q'e计算方法同9.2.6
9.2.13炉膛至蓄热室间的烟道散热量Q的计算
若蓄热室同炉膛之间有一定距离,此项需要计算
计算方法同9.2.6
若蓄热室安装在炉墙上,此项不需要计算
9.2.14预热空气(或煤气)管道及燕汽管道散热量Q'计算方法同9.2.6
9.2.15其他工质带走的热量Q'包括回收后外供的水燕气、保护气体,及雾化燕汽、压缩空气等
具体 项目和计算方法,可根据炉窑的特点和工艺要求具体计算
9.2.16热平衡各项收人热量总和Q与已测各项支出热量总和之差即为差值AQ,按式(40)计算 Q=习Q-(Q'十Q十Q,十十Q' 40) 差值包括未测出的支出热量及误差
热平衡允许相对误差值为士5%以内,见式(41): .(41 ×100<5 9.2.17支出热量总和计算按式(42)计算 >Q'=Q'+Q Q.'十十Qs’十Q 42 式中 支出热量总和,单位为千焦每吨(klI/ 习Q 及其总和 9.2.18计算回收并用于加热炉上的(例如预热空气或煤气的)循环热量Q.,Q. -** he 10o
GB/T32974一2016 习Qa,同时算出其占收人热量总和的百分数
9.2.19将全炉(包括蓄热回收装置)或炉膛热平衡各收,支项热量的计算结果列人表1中
表1热平衡表 收人 支出 热量 热量 符号 项目 符号 项目 0kJ/t % 10kJ/t Q 燃料燃烧的化学热量 Q' 出炉物料带出的物理热量 Q 燃料带人的物理热量 Q" 烟气带出的物理热量 化学不完全燃烧损失的热量 O 助燃空气带人的物理热量 Q" 物料带人的物理热量 机械不完全燃烧损失的热量 Q Q 物料氧化反应热量 炉子附件的吸热量 Q 炉体表面散热量 Q 炉门、孔洞辐射热量 Q 炉门、孔洞逸气损失热量 Q 冷却水的吸热量 Q1 汽化冷却的吸热量 Q 氧化铁皮带出的物理热量 Q 蓄热室表面散热量 炉膛至蓄热室间烟道散热量 Q 预热空气(或煤气)管道及 Q 蒸汽管道散热量 Q' 其他工质带走的热量 Q 差值 合计 100习Q 合计 00 注1;百分率精确到小数点后一位 注2:热量值取4位有效数字
9.3热效率 全炉热效率计算按式(43)计算 Q" Q ×100% (43 n Q 式中: 全炉热效率,用百分数(%)表示
7 炉膛热效率计算按式(44)计算: Q1一Q ×100% (44 =! Q-Q 式中 炉膛热效率,用百分数(%)表示
7 11
GB/T32974一2016 9.4主要技术经济指标 主要技术经济指标按表2计算和填写
表2主要技术经济指标 数值 序号 指标 符号或算式 单位 小时产量 t/h 乌 炉底强度 1000 kg/m'h) 供热强度 10kk/h 10"QG 单位热耗 "O 0 10 热平衡测试报告主要内容 热平衡测试报告主要内容包括: a)前言 b)主要设备概况及生产状况 e)主要测定数据 D 物料平衡表; 热平衡表; e f 主要技术经济指标; 分析及改进意见; g 测定单位,负责人.,报告执笔人、审核人(签字) h 12
GB/T32974一2016 附 录A 资料性附录 设备及窑炉概况 设备及炉窑概况见表A.1
表A.1设备及窑炉概况表 厂车间名 加热炉炉型 炉子设计单位 炉子施工单位 加热炉编号 项目 单位 数值或内容 轧机概况 型号 作业率 设计年产量 实际年产量 主要产品规格 加热炉概况 座数 设计 每座年加热量 额定 实际 设计 每座小时加热量 额定 实际 炉底有效尺寸(有效炉长×炉内宽 各部位所用耐火材料种类 平均发热量 种类 燃料 燃烧器前温度 燃烧器前压力 平均小时用量 形式 尺寸 额定能力 燃烧装置 个数 供热点装置 供热比例 13
GB/T32974一2016 表A.1(续 厂(车间)名 加热炉炉型 炉子设计单位 炉子施工单位 加热炉编号 项目 单位 数值或内容 材质 尺寸 单顶 物料 加热温度 炉底强度 装料排数 冷却方式 小时耗水量或产汽量 根数 纵横水管 直径 炉底管 管底比 包扎施工方法 包扎部位及面积 寿命(包扎使用寿命) 节能效果(包扎前,后对比 类型 蓄热介质 蓄热室 蓄热面积 蓄热温度 使用寿命 类型 座数 每座小时产气量 产汽利用效率 余热锅炉 进水温度 燕汽压力 蒸汽温度 燕汽湿度 型号 台数 鼓风机 压力 风量 14
GB/T32974一2016 表A.1(续 厂(车间)名 加热炉炉型 炉子设计单位 炉子施工单位 加热炉编号 项目 单位 数值或内容 型号 台数 引风机 吸力 引风量 绝热情况 炉体 密封情况炉门数 台数 物料推进机构 能力 出料方式 型式 升降步进行程 步进机构 水平步进行程 步进周期 配置 囱 高度 上、下部内径 温度 热工仪表测试时记录 压力 流量 大修年限 修炉情况 年修炉次数 额定 热量单耗 上年平均 最低年平均 15
GB/T32974一2016 附 录 B 资料性附录 炉子工作月报 炉窑工作月报见表B.1
表B.1炉子工作月报表 序号 项目 单位 数值或内容 加热时间 升温时间 保温时间 停炉时间 月加热物料量 平均小时加热物料量 主要加热物料规格 加热物料月平均单重 使用燃料种类及低发热量 月耗燃料量 10 平均单位热耗 1l1 12 炉子交替作业情况 13 炉子是否正常生产 16
GB/T32974一2016 附 录 C 规范性附录 主要测试内容 主要测试内容见表C.1
表C.1主要测试内容 车间)名 加热炉编号: 测试日期及起止时间 序号 项目 单位 数值或内容 大气压力 Pa 车间平均气温 气象状况 相对湿度 % 风速 m/s 均热段用量 kg/t或m'/t 上加热段用量 kg/或m'/t kg/t或m'/t 下加热段用量 燃料 压力 Pa 温度 成分 低发热量 kJ/t或/m 均热段用量 kg/t或m'/t 上加热段用量 kg/或m'/t kg/t或m'/t 空气 下加热段用量 压力 Pa 蓄热后温度 物料量 尺寸长×宽×高 mmXmmXmm 物料 每块(根)重量 人炉温度 出炉温度 重量 氧化铁皮 温度 出炉温度 进热室温度 出蓄热室温度 烟气 出炉成分 进蓄热室成分 出蓄热室成分 17
GB/T32974一2016 表C.1(续》 厂车间名 加热炉编号 测试日期及起止时间: 序号 项目 单位 数值或内容 散热面积 m" 炉体各部 表面温度 表面热流 /m'h 时间 Aw 高×宽× mmnm Pa 开启炉门孔 静压 温度 炉气成分 耗水量 kg/t 人炉温度 冷却水 出炉温度 压力 Pa 蒸发量(或用水量 kg/ Pa 燕汽压力(表压) 10 汽化冷却 蒸汽温度 燕汽湿度 % 进水温度 重量 附件 人炉温度 l 出炉温度 均热段 上加热段 12 各段炉气成分 下加热段 蓄热室 与炉尾(进料口)距离 mmm 沿炉长方向温度及 炉温 13 压力分布 炉压 Pa 18
GB/T32974一2016 附 录 D 规范性附录 烧损率的测定(重量比表面积相似法 D.1操作方法 加工一定数量的与加热物料同钢种的试样,儿何形状便于测量及确定其外表面积为宜(立方体),重 量在1kg左右
另加工与试样数量相同的盛放试样的托盘;试样外表面及托盘上的表面粗糙度均在 12.5以上,确保试验中与托盘上表面接触的试样外表面部分在炉内加热过程中不被烧损
根据加热炉的热工工作特点,试验选取正常轧制与保温待轧两种典型工况
D.1.1正常轧制工况 在正常轧制工况的测试期内,每隔1h即在炉尾人炉钢坯上部放一试样;试样在人炉前称重(秤精 度在十分之一以上),试样与钢坯在炉内同步行进,待出坯时从出钢口取出,记录每一块试样在炉内的停 留时间
试样出炉后立即强制冷却,将其表面的氧化铁皮清除干净后上天秤称重
D.1.2保温待轧工况 由于上下游工序等原因,加热炉经常会处于保温待轧状况
在进行保温待轧期间的加热炉钢坯烧 损率测试试验时,可将试样在保温开始时直接放人均热段,至保温结束时再取出
试样在加热前后的称 重方法与在正常轧制工况下进行的试验相同
所测得的结果可作为在均热段和加热段停留的全部钢坯的最大烧损率
D.2计算方法 D.2.1 烧损率计算 烧损率计算按式(D.1)计算 mn 1 ×100% (D.1 式中: 烧损率,用百分数%)表示; 钢坯或式样人炉前的重量,单位为千克(ke): n 钢坯或式样出炉并除去氧化铁皮后的重量,单位为千克(ke). D.2.2重量比表面积S 重量比表面积按式(D.2)计算 D.2 n 式中: -重量比表面积,单位为平方毫米每克(mm/g); S 钢坯或式样受热表面积,单位为平方毫米(mm=')
A
GB/T32974一2016 D.2.3单位受热面上的烧损量 单位受热面上的烧损量按式(D.3)计算: m二 "-二 D.3) = m= A A 式中: -单位受热而上的烧损量,单位为克每平方米(w/mmr)
1 D.2.4钢坯烧损率与式样烧损率的关系 在试验条件下,认为钢坯单位受热面上的烧损量与试样单位受热面上的烧损量相等 即m= D.4 D.5 发 或号 4s S D.6 所以d, 式中: 钢坯烧损率,用百分数(%)表示; l 试样烧损率,用百分数(%)表示
s
钢铁行业蓄热式工业炉窑热平衡测试与计算方法GB/T32974-2016
随着钢铁行业的不断发展,蓄热式工业炉窑在生产过程中起到了至关重要的作用。而热平衡测试是保证蓄热式工业炉窑正常运行的关键之一。本文将详细介绍GB/T32974-2016标准下蓄热式工业炉窑热平衡测试与计算方法。
1. GB/T32974-2016标准概述
GB/T32974-2016是我国钢铁行业蓄热式工业炉窑热平衡测试与计算方法的标准。该标准规定了蓄热式工业炉窑热平衡测试的基本原理、测试方法、数据处理方法和结果表示方法。
2. 蓄热式工业炉窑热平衡测试的基本原理
蓄热式工业炉窑是通过加热蓄热材料来保持高温状态,从而达到节能目的的一种设备。在蓄热式工业炉窑的生产过程中,需要对其进行热平衡测试,以保证其正常运行。
蓄热式工业炉窑热平衡测试的基本原理是:测量炉窑内各部位的温度,并根据测得的温度计算出炉窑内的热平衡状态。在测试过程中,需要对炉窑内各部位的温度进行多次测量,确保数据的准确性。
3. 蓄热式工业炉窑热平衡测试方法
GB/T32974-2016标准规定了蓄热式工业炉窑热平衡测试的具体方法:
- 选择合适的测试时间和测试地点。
- 确认测试仪器的精度和准确性,进行标定。
- 安装测试仪器,对炉窑内各部位的温度进行多次测量,并记录数据。
- 根据测得的温度数据,计算出炉窑内的热平衡状态。
- 对测试结果进行分析和评估,确保炉窑内的热平衡状态符合要求。
4. 蓄热式工业炉窑热平衡计算方法
GB/T32974-2016标准规定了蓄热式工业炉窑热平衡计算的具体方法:
- 确定炉窑内各部位的热阻值。
- 测量炉壁表面和炉内气体温度,并计算出散热损失。
- 根据蓄热材料的热容量和温度变化,计算出其在炉中吸收和释放的热量。
- 根据测得的各部位温度、热阻值、散热损失和蓄热材料的热量变化,计算出炉窑内的热平衡状态。
5. 结论
钢铁行业蓄热式工业炉窑是生产过程中不可或缺的设备之一,而热平衡测试是保证其正常运行的重要手段。GB/T32974-2016标准下蓄热式工业炉窑热平衡测试与计算方法提供了详细的操作指南和计算方法,有助于保证炉窑的正常运行和提高生产效率。